Бакалаврская работа - Паровой котел Е-35-2,5-250




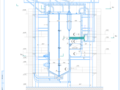
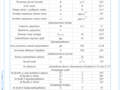
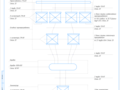
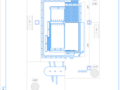
- Добавлен: 04.11.2022
- Размер: 3 MB
- Закачек: 1
Описание
Бакалаврская работа - Паровой котел Е-35-2,5-250
Состав проекта
![]() |
![]() ![]() ![]() |
![]() ![]() ![]() ![]() |
![]() ![]() ![]() ![]() |
![]() ![]() ![]() ![]() |
![]() ![]() ![]() ![]() |
![]() ![]() ![]() ![]() |
![]() ![]() ![]() ![]() |
Дополнительная информация
Сводная таблица результатов расчета.cdw

Гидравлическая схема.cdw

вид сверху.cdw

циркуляционный контур.cdw

главный вид правильный.cdw

вид сбоку.cdw
