Завод железобетонных конструкций для инженерного оборудования улиц




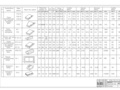
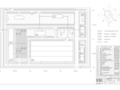
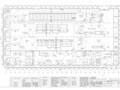
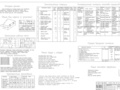
- Добавлен: 25.10.2022
- Размер: 1 MB
- Закачек: 0
Описание
Состав проекта
![]() |
![]() |
![]() ![]() ![]() ![]() |
![]() ![]() ![]() ![]() |
![]() ![]() ![]() ![]() |
![]() ![]() ![]() ![]() |
![]() ![]() ![]() ![]() |
![]() ![]() ![]() ![]() |
![]() ![]() ![]() ![]() |
![]() ![]() ![]() ![]() |
![]() ![]() ![]() ![]() |
![]() ![]() ![]() ![]() |
![]() |
![]() ![]() ![]() |
![]() ![]() ![]() |
![]() ![]() ![]() |
![]() ![]() ![]() |
![]() ![]() ![]() |
![]() ![]() ![]() |
![]() ![]() ![]() |
![]() ![]() ![]() |
![]() ![]() ![]() |
![]() ![]() ![]() |
![]() ![]() ![]() |
![]() ![]() ![]() |
![]() ![]() ![]() |
Дополнительная информация
Пропар. камера.dwg

Тех схема 2.dwg

План Такранов.dwg

тех карта готовая.dwg

Разрезы.dwg

Экон.часть.dwg

номенклатура.dwg

Мех обор.dwg

Генплан 1.dwg

Автомат Напольная камера.dwg

Рекомендуемые чертежи
- 26.01.2021
- 20.08.2014
- 23.08.2014
- 23.08.2014
- 20.08.2014
- 20.08.2014