Цилиндрический резервуар для хранения нефтепродуктов




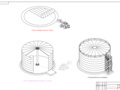
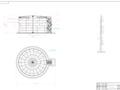
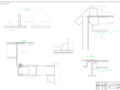
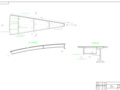
- Добавлен: 25.10.2022
- Размер: 625 KB
- Закачек: 0
Описание
Состав проекта
![]() |
![]() ![]() ![]() ![]() |
![]() ![]() ![]() ![]() |
![]() ![]() ![]() ![]() |
![]() ![]() ![]() ![]() |
![]() ![]() ![]() |
Дополнительная информация
ПСК(лист2).dwg

ПСК(лист4).dwg

ПСК(лист1).dwg

ПСК(лист3).dwg

Рекомендуемые чертежи
- 27.04.2022
- 24.01.2023
- 22.12.2024
Свободное скачивание на сегодня
- 22.08.2014
- 29.08.2014