Трубная мельница Ø3,2х15м




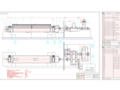
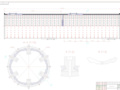
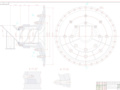
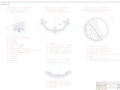
- Добавлен: 25.10.2022
- Размер: 1 MB
- Закачек: 7
Описание
Состав проекта
![]() |
![]() ![]() ![]() ![]() |
![]() ![]() ![]() ![]() |
![]() ![]() ![]() ![]() |
![]() ![]() ![]() ![]() |
![]() ![]() ![]() |
- Архиватор zip файлов
- AutoCAD или DWG TrueView
- Microsoft Word
Дополнительная информация
Патентные исследования.dwg

-Наклонная грань 2-Закладные элементы 3-Болты 4-Головка 5-Образные пазы 6-Верхняя грань 7-Продольные каналы 8-Продольные и поперечные пазы 9-Нижняя поверхность 10-Отверстия 11-Втулка 12-Гайка 13-Шайба 14-Фитинги
-Барабан мельницы 2-Полочные лифтеры 3-Футеровочные плиты 4-Крепежные болты 5-Материал различной крупности 6-Шары 7-Внелифтерная зона 8-Материал различной крупности
-Корпус 2-Металлический лифтер 3-Футеровочные плиты 4-Пустотные полосы 5-Болтовые соединение 6-Болтовые соединение
КП МО-08 802 00 00 00 ПИ
Бронефутеровка для мельниц полусамоизмельчения
Футеровка мельниц с помощью лифтеров
Футеровка для мельниц самоизмельчения
Барабан.dwg

Трубная мельница 3,2х15м.dwg

Частота вращения барабана
Мощность электродвигателя
по известняку и глиняному шлаку
КП МО-08 802 00 00 00 СБ
Перегородка межкамерная
КП МО-08 802 00 00 00 ПЗ
КП МО-08 802 01 00 00
КП МО-08 802 02 00 00
КП МО-08 802 03 00 00
КП МО-08 802 04 00 00
КП МО-08 802 05 00 00
КП МО-08 802 06 00 00
КП МО-08 802 07 00 00
КП МО-08 802 08 00 00
КП МО-08 802 11 00 00
КП МО-08 802 12 00 00
КП МО-08 802 13 00 00
КП МО-08 802 14 00 00
КП МО-08 802 15 00 00
КП МО-08 802 16 00 00
Привод вспомогательный
Пояснительная записка
КП МО-08 802 09 00 00
КП МО-08 802 10 00 00
КП МО-08 802 00 00 01
КП МО-08 802 00 00 02
КП МО-08 802 00 00 04
КП МО-08 802 00 00 05
КП МО-08 802 00 00 06
КП МО-08 802 00 00 07
Гайка М16 ГОСТ 15526-70
Гайка М30 ГОСТ 15526-70
Гайка М36 ГОСТ 15526-70
Гайка М48 ГОСТ 15526-70
Гайка М64 ГОСТ 15526-70
Гайка М72 ГОСТ 15526-70
Шайба 16 ГОСТ 6402-70
Шайба 30 ГОСТ 6402-70
Шайба 36 ГОСТ 6402-70
Шайба 48 ГОСТ 6402-70
Шайба 64 ГОСТ 6402-70
Шайба 72 ГОСТ 6402-70
Гайка М12 ГОСТ 15526-70
Шайба 12 ГОСТ 6402-70
КП МО-08 802 00 00 03
КП МО-08 802 00 00 00
Загрузочная часть.dwg

Пояснительная записка.doc
Сущность модернизации13
1 Расчет производительности мельницы14
2 Расчет мощности привода мельницы14
3 Расчет угловой скорости вращения барабана16
4 Частота вращения рабочего органа мельницы18
5 Определение массы мелющих тел19
6 Расчет корпуса мельницы на прочность19
Развитие процессов измельчения клинкера и добавок определяется необходимостью расширения строительно – технических свойств цемента: повышенными требованиями к его качеству и стабильности в значительной степени гарантируемых рациональными дисперсными характеристиками цемента. Повышение этих характеристик сопровождается ростом удельных энерго – металлозатрат что предопределяет создание эффективных энерготехнологических изделий.
В цементной промышленности затраты на энергию составляют наибольшую стать расходов. Обычно 60 и более процентов электроэнергии используются для помола цемента в шаровых мельницах. Шаровая мельница является традиционным агрегатом в цементной промышленности. Она проста в эксплуатации обеспечивает высокий коэффициент использования нетребовательна к обслуживанию и обеспечивают широкое распределение частиц по размеру что часто благоприятно с точки зрения свойств цемента. Однако эффективность шаровых мельницах достаточно низкая: только 3 – 6% подаваемой электроэнергии действительно идет на измельчения материала. Остальная часть в форме тепла износа вибрации и шума просто теряется. Поэтому возможностям оптимизации и модернизации помольных циклов шаровых мельниц уделяется большое внимание.
Описание конструкции и принципа действия
Трубная мельница 32х15м изготовлена из цельносварного корпуса толщиной 46 мм загрузочного и разгрузочного устройств камеры разгрузки главного и вспомогательного приводов и системой жидкой смазки. Главный привод включает в себя цилиндрический двухступенчатый редуктор соединенный цилиндрическим валом с мельницей и эластичной муфтой с электродвигателем. Вспомогательный привод служит для ремонтных работ для проворачивания мельницы. С торцов барабан закрыт днищами переходящими в пустотелые цапфы. Цапфы опираются на цапфовые подшипники воспринимающие собственный вес барабана и передающей его на фундамент. Днища крепятся к цилиндрической части барабана болтами по всему диаметру и с внутренней стороны футеруются броневыми плитами из марганцовистой и хромистой стали. Для загрузки мелющих тел монтажа и замены бронеплит в корпусе барабана имеются люки. Барабан по длине разделен прутковой межкамерной перегородкой на две камеры: шаровую и цильпебсную.
Междукамерная перегородка препятствует перемещению мелющих тел по длине барабана. В торце барабана со стороны разгрузочного устройства установлена разгрузочная выходная решётка.
Загрузочное устройство мельницы состоит из стальной наклонно расположенной питательной течки с внутренней бронефутеровкой. Течка расположена на металлической тумбе прочно прикрепленной к фундаментной плите.
Течка входит в торцовую часть входной цапфы в которой установлена и вращается вместе с мельницей загрузочная втулка (трубошнек) представляющая собой трубу с винтовыми ребрами (лопастями). Между течкой и загрузочным трубошнеком проложены пропитанные густой смазкой уплотнения. Материал поступает в течку и из неё направляется лопастями разгрузочного трубошнека в барабан мельницы.
Разгрузочное устройство мельницы имеет выходное днище отлитое вместе с цапфой.
К днищу прикреплены болтами радиальные сварные секторы выходной решётки с отверстиями через которые проходит размолотый материал в разгрузочную полость ограниченную днищем и решёткой.
Между решёткой и днищем установлена литая диафрагма с направляющим конусом и радиальными лопастями. При вращении барабана измельченный материал захватывается лопастями и ссыпается с них на конус после чего поступает в разгрузочный трубошнек выходной цапфы который перемещается к разгрузочному патрубку расположенному между цапфой и приводным валом мельницы.
В патрубке выполнены отверстия через которые цемент попадает на цилиндрическое контрольное сито.
Крупные частицы металлические включения и др. задерживаются ситом а готовая продукция направляется в приемный бункер пневмокамерного насоса. Задержанные ситом металлические включения крупные частицы поступают в патрубок разгрузочной камеры и удаляются из мельницы.
Цапфовые подшипники предназначены для опирания барабана мельницы и состоят из рамы корпуса вкладыша и крышки. Корпус подшипника и вкладыша сопрягается по сферическим поверхностям что обеспечивает самоустановление подшипника при работе машины. Внутреннюю поверхность вкладыша заливают баббитом. Вкладыш выполнен с углом обхвата цапфы 120ºС имеет два встроенных термодатчика. Один из них сигнализирует о нагреве баббитовой заливки до температуры 65С второй при нагреве до 80С дает сигнал на остановку мельницы.
Для защиты от пыли и предотвращения вытекания смазочного материала через зазоры крышка подшипника литой конструкции соединена болтами.
Цапфовые подшипники смазываются с помощью циркуляционной смазочной системы. Масло в подшипник подается патрубком.
Поступивший смазочный материал равномерно распределяется по цапфе а затем затягивается при вращении в зазор между цапфой и вкладышем.
Отработанное масло удаляют из подшипника по патрубку.
Для охлаждения вкладыша в его теле установлен змеевик. В него по трубе поступает холодная вода которая нагреваясь выходит наружу. Охлаждено способствует так же принудительно - циркуляционная смазочная система.
Футеровка сырьевых мельниц предохраняет внутренние поверхности барабана мельницы от изнашивания. Барабан мельницы облицован продольными а днище поперечными плитами.
В качестве мелющих тел в шаровых мельницах применяются шары и цилиндрики. Шары могут изготовляться из углеродистой марганцовистой или хромистой стали а в ряде случаев и из отбеленного чугуна. Шары изготовляются коваными штампованными или литыми. Для помола сырьевых материалов угля цементного клинкера применяются шары диаметром от 30 до 100 мм.
В многокамерных мельницах шары загружаются в первые камеры в то время как в последних камерах применяются цилиндрики (цильпебс) диаметром 16—25 мм при длине равной 15 диаметра.
Броневые плиты крепятся к барабану мельницы или болтами с потайной головкой или по способу. Плиты крепятся в шпунт с последующим расклиниванием при помощи клина затягиваемого болтами. Толщина плит колеблется в пределах от 30 до 60 мм.
Рисунок 1.1 – Трубная шаровая мельницы 32х15м
-Тумба; 2-Течка; 3-Лопасти; 4-Загрузочное устройство; 5-Люк; 6-Бронеплиты;
-Межкамерная перегородка; 8-Разгрузочное устройство; 9-Патрубок;
-Промежуточный вал; 11-Главный редуктор; 12-Муфта; 13-Электродвигатель; 14-Цапфовый подшипник; 15-Цапфа; 16-Барабан; 17-Вспомогательный электродвигатель; 18- Вспомогательный редуктор;19-Муфта;
Бронефутеровка для мельниц полусамоизмельчения
Бронефутеровка для мельниц полусамоизмельчения содержащая лифтеры расположенные рядами вдоль оси барабана мельницы и направленные к центру по радиусу отличающаяся тем что бронефутеровка содержит смонтированные на внутренней поверхности барабана мельницы футеровочные плиты с наклонными полочными лифтерами установленными под углом 10°-80° к горизонтали направленным в сторону противоположную вращению барабана мельницы с соотношением их длины к толщине от 15 до 6 причем высота лифтеров составляет 03-06 а расстояние между соседними рядами составляет не менее 11 от максимального размера куска исходного материала при этом расстояние между лифтерами составляет не менее 11 максимального диаметра шара.
Недостатком известных полочных лифтеров для мельниц полусамоизмельчения является низкая эффективность размола шаровой загрузкой из-за смещения шаровой загрузки в сторону разгрузочной решетки под воздействием загружаемого в мельницу крупнокускового исходного эффективность размола (шарами).
Рисунок 2.1- поперечный разрез мельницы
- барабан мельницы; 2- футеровочные плиты; 3- полочные лифтеры; 4- крепежные болты; 7- 8 – материал различной крупности; 9- шары;
- внелифтерная зона;
Барабанная мельница содержащая вращающийся корпус равнорасположенные по его внутренней поверхности одинаковые продольные металлические лифтеры деформированные футеровочные плиты из упругого материала уложенные между лифтерами с натягом и находящиеся в плотном контакте с внутренней поверхностью вращающегося корпуса и средства удерживающие футеровочные плиты из упругого материала в деформированном состоянии отличающаяся тем что лифтеры выполнены в виде рельсов при этом каждая футеровочная плита плотно контактирует с боковыми поверхностями рельсов и с внутренней поверхностью корпуса а средства удерживающие упругие футеровочные плиты в деформированном состоянии выполнены в виде жестко укрепленных на внутренней поверхности корпуса штифтов со сферическими головками и предусмотренных в футеровочной плите со стороны ее поверхности подлежащей контактированию с внутренней поверхностью корпуса барабанной мельницы соответствующих им сферических гнезд с запорным отверстием охватывающим сферическую головку штифта.
Недостатком данной конструкции является низкая прочность резиновых лифтеров при высоких нагрузках возникающих в крупных мельницах диаметром от 36 до 5 метров. В таких мельницах как правило происходят надрывы резиновых лифтеров подбивка в место надрыва осколков шаров с последующим разрушением как лифтеров так и футеровки.
Рисунок 2.2- Поперечный разрез футеровочной плиты
- вращающийся корпус; 2- металлические лифтеры; 3- футеровочные плиты;
Футеровка барабанной мельницы самоизмельчения
Футеровка барабанной мельницы самоизмельчения содержащая чередующиеся наборы лифтеров в виде брусьев из эластомерного материала разной высоты с многогранными рабочими поверхностями образующими волновую рабочую поверхность футеровки нижние части которых армированы установленными в пазах закладными элементами соединенными с помощью крепежных элементов с барабаном мельницы отличающаяся тем что каждый набор брусьев состоит из двух крайних брусьев одинаковой высоты и выступающих над ними двух средних брусьев одинаковой высоты рабочие поверхности которых выполнены двугранными расположены зеркально относительно плоскости симметрии набора брусьев и образуют ступенчатые восходящую и нисходящую ветви волны рабочей поверхности набора брусьев при этом каждый брус каждого набора выполнен с несколькими сквозными продольными каналами в средней части а армирующие его закладные элементы соединены с контактирующей поверхностью пазов посредством вулканизации.
Рисунок 2.3- Футеровка и элементы его крепления к барабану
- барабан; 4- брусья; 6- рабочая поверхность;
- 10- продольные и поперечные пазы;
-12- закладные элементы; 14- крепежные элементы; 15- т-образные пазы;
- болты; 17- втулка; 18- шайба; 19- гайка; 20- фланцы; 21- отверстия;
- головка; 27- продольные каналы; 28- верхняя грань; 29- наклонная грань;
- нижняя поверхность;
Барабанная мельница включающая вращающийся корпус продольные металлические лифтеры равнорасположенные и жестко прикрепленные к внутренней поверхности корпуса и футеровочные плиты отличающаяся тем что каждый лифтер снабжен двумя продольными параллельными пазами а футеровочные плиты выполнены из упругого материала и с помощью ряда болтовых соединений проходящих по их продольной оси уложены между лифтерами с натягом так что боковые края футеровочных плит входят в продольные пазы лифтеров а тыльная поверхность каждой футеровочной плиты образует две продольные полости.
Недостатком данной конструкции является относительно малая высота гребней волновой рабочей поверхности мельницы которая обеспечивает подъем только мелких частиц и не позволяет сообщать большую кинетическую энергию для размола крупных кусков руды. Следствием этого является низкая производительность и недостаточная эффективность мельницы на первых стадиях помола руды из-за преобладания процесса взаимного истирания частиц над процессами соударения.
Рисунок 2.4 - Поперечный разрез футеровочной плиты
- корпус; 2- металлический лифтер; 3- футеровочные плиты;
-7- болтовые соединения; 8- пустотные полосы;
Сущность модернизации
Принимаем в качестве аналога патент № 2165295
Барабанная мельница работает следующим образом. В корпус 1 с лифтерами 2 и установленными футеровочными плитами 3 загружают рудно-шаровую смесь т.е. руду подлежащую размолу и мелющие тела - шары. Мельница приводится во вращение по стрелке А. При вращении мельницы рудно-шаровая смесь за счет центробежных сил и лифтеров 2 поднимается на определенную высоту и скатывается вниз по этой поверхности измельчаясь за счет соударений и истирания в так называемом "каскадном режиме".
Лифтеры 2 поднимают шары и крупные частицы руды которые не только падают или скатываются вниз но и с дополнительным ускорением отбрасываются к центру попадая на упругие участки футеровочных плит 3 образуемые пустотными полостями 8 и отражаясь от них.
Это создает благоприятные условия для дробления и измельчения материала причем мельница переводится из каскадного режима в каскадно-водопадный режим работы.
В процессе помола основные нагрузки и усилия среза испытывают металлические лифтеры 2. Благодаря Т – образному сечению лифтера вместо усилий на срез действующих на болтовые соединения в традиционных конструкциях на лифтер 2 воздействует опрокидывающий момент относительно оси вращения приходящийся на край полки. Однако этот опрокидывающий (вращающий) момент уравновешивается болтовыми соединениями 4 и 7 испытывающими при этом только осевые нагрузки.
Благодаря заявляемой конструкции достигается соединение в одной мельничной системе двух процессов: дробления крупных кусков в водопадном режиме дезинтеграции и истирания мелких частиц рудной массы в каскадном режиме что обеспечивает повышение эффективности процесса увеличение производительности мельницы и снижение числа мельниц в технологической цепочке.
1 Расчет производительности мельницы
С достаточной для практических расчетов точностью значение определяют из зависимости:
где - полезная мощность;
b - удельная производительность [ткВтч] определяется по характеристике размалываемости; принимается равной 0035 ткВтч;
- коэффициент эффективности процесса; для открытого цикла . С учетом модернизации принимаем ;
-поправка на тонкость помола. При оценке по
где m – параметр уравнения кинетики определяют по результатам определения характеристики измельчаемости.
Далее проводятся исследования основных факторов на эксплуатационно-технологические параметры и строятся графические зависимости.
2 Расчет мощности привода мельницы
Расходуемая мельницей мощность является важнейшим показателем поскольку производительность мельницы прямо пропорционально величине полезной мощности - а мощность двигателя близка к потребляемой - .
Мощность на оси барабана определяется:
где - полезная мощность;
- потери на холостой ход;
- дополнительные потери в подшипниках цапф возникающие под действием мелющей загрузки и материала.
Потери на приводе учитываются введением механического КПД передачи . С учетом этого коэффициента мощность на валу электродвигателя:
Для определения на практике удобнее использовать формулу:
где - полезный диаметр мельницы;
- относительная скорость вращения;
- степень заполнения;
- насыпная плотность мелющих тел;
Значения и рассчитывается по приблизительным эмпирическим зависимостям:
3 Расчет угловой скорости вращения барабана
Угловая скорость барабана определяет характер траектории движения мелющих тел от которой зависит эффективность помола в мельницах. При небольшой угловой скорости барабана загрузка повернется на определенный угол и будет циркулировать. Мелющие тела будут подниматься вращаясь с барабаном на некоторую высоту и затем скатываться по подстилающим слоям не производя удара. При слишком большой угловой скорости центробежная сила инерции превысит силу тяжести G и мелющие тела не будут отрываться от стенок даже в самой верхней точке С. Минимальная при которой шар не отрывается от барабана в верхней точке называется критической. Ее определяют из условия:
Откуда критическая угловая скорость радс
где g – ускорение свободного падения мс2;
R – радиус вращения мелющих тел м;
Оптимальная угловая скорость барабана находиться из условия обеспечения максимальной высоты падения шара которая определяется координатами точек отрыва шара от стенок и точек соприкосновения его с барабаном после падения. В точке А на шар действует сила тяжести G сила инерции и сила трения F. Учитывая что будет иметь место подпор верхних частиц нижними то скольжением тел по стенкам барабана можно пренебречь тогда отрыв тел от стенок барабана будет обеспечен при условии:
Угловая скорость радс
Рисунок 4.1- Схема для расчета параметров шаровой барабанной мельницы
После отрыва шара от стенок барабана он движется по параболе которая описывается системой уравнений:
где v - окружная скорость мс;
t - время с момента отрыва шара с.
Подставив в эти уравнения значения окружной скорости мс
Получим значение текущей ординаты
Траектория окружности стенок барабана описывается уравнением:
Подставив значения X и Y в формулу и решив совместно уравнения найдем ординату точки:
Для определения максимальной высоты падения необходимо иметь первую производную от предыдущей функции и приравнять ее к нулю:
Очевидно что и R не равны нулю тогда
Из уравнения следует что можно найти наивыгоднейший угол отрыва шаров который будет равен .
4 Частота вращения рабочего органа мельницы
Для каждой трубной шаровой мельницы имеется так называемая критическая частота вращения. Рабочая частота вращения должна быть меньше чем критическая. Оптимальная частота вращения мельницы n (с-1) определяется по формуле:
где - коэффициент запаса учитывающий условия сочетания максимально полезной мощности с минимальным износом бронефутеровки и мелющих тел;
D - условный диаметр мельницы в "свету" м; D = (094 - 095)
D0- внутренний диаметр корпуса мельницы м.
Фактическая частота вращения корпуса мельницы устанавливается после расчета и выбора параметров привода. Отклонение фактической частоты вращения от расчетной не должно превышать одного процента.
5 Определение массы мелющих тел
Масса загружаемых в барабан мельницы мелющих тел рассчитывается по формуле:
где - коэффициент разрыхления загрузки для шаров
- объемная масса мелющих тел ;
При коэффициенте загрузки
6 Расчет корпуса мельницы на прочность
После отработки и выбора кинематической схемы привода мельницы производится ее силовой расчет который является основой для дальнейшего прочностного расчета основных деталей машины.
Корпус мельницы представляет собой цилиндрическую оболочку нагруженную распределенными и сосредоточенными силами и установленную на две опоры. Распределенной нагрузкой являются: мелющие тела и сырьевые материалы; сила тяжести межкамерных перегородок и разгрузочных устройств; сила тяжести корпуса мельницы и т.п. При расчете распределенной нагрузки действующей на корпус за расчетную длину принимают полную его длину.
Рисунок 4.2 – Расчетная схема нагрузок трубной мельницы
Динамические нагрузки вызваны центробежной силой благодаря давлению падающих масс мелющих тел и сырьевых материалов.
После определения этих нагрузок по общеизвестным правилам строятся схема нагрузок в вертикальной плоскости и эпюры перерезывающих сил и изгибающих моментов.
В соответствии с полученными эпюрами нагрузок определяют величину и строят эпюры перерезывающих сил и изгибающих моментов действующих на корпус мельницы в вертикальной и горизонтальной плоскостях. Нагрузка в горизонтальной плоскости создается только горизонтальной составляющей центробежной силы которая приложена по длине корпуса в виде равномерно распределенной нагрузки.
Определяем реакции опор поперечные силы в сечениях и изгибающие моменты:
Участок 1 (0 x1 127)
Участок 3 (0 x3 077)
Участок 4 (0 x4 1502)
Участок 5 (0 x5 5244)
Участок 7 (0 x7 072)
На участке от муфты до первого (со стороны муфты) подшипника действует полный крутящий момент подводимый к барабану кНм:
где N-мощность двигателя кВт;
-угловая скорость радс;
Вследствии трения в подшипнитке крутящий момент уменьшается на величину
где Rв-нагрузка на подшипник кН;
-коэффициент трения в подшипнике;
По длине корпуса крутящий момент изменяется по наклонной прямой. Наиболее опасное сечение будет в середине пролёта где приведенный момент кН м
где Мz – максимальный изгибающий момент кН м
Напряжения в этом сечении кН м
где k = 08- коэффициент учитывающий ослабление сечения вырезами и отверстиями для болтов;
W-момент сопротивления сечения корпуса м3 который равен
где S- толщина стенки барабана м
R-наружный радиус корпуса равный 164 м.
Подставляя полученное значение в формулу получим
Наиболее нагружены болты со стороны приводного устройства. Болты работают на срез и растяжение.
Срез болтов происходит под действием равнодействующей Рр веса вращающихся частей мельницы и центробежной силы инерции а также окружного усилия создаваемого крутящим моментом который передается от двигателя. Окружное усилие приложенное по окружности проходящей через центры болтов направлено по касательной к этой окружности Н
где – крутящий момент кН× м
– радиус окружности центров болтов м
N – мощность электродвигателя кВт
n – частота вращения мельницы
Суммарная сила среза будет равна:
Величина напряжения в болтах под действием суммарной силы среза:
где т – число болтов шт
т = 16 ( плотнопригнаных )
F – сечение болта м2
Допустимое напряжение среза для стали Ст 3 [] = 48 МПа
Растягивающее усилие действия изгибающего момента (рисунок 4.3) будет равно;
где т1 – количество равномернозатянутых болтов шт;
Рисунок 4.3 - Схема к расчету болтов
Усилие затяжки ботов Т Н.
– напряжение затяжки МПа
F1 – сечение нарезанной части болта м2
Т = 120× 00085 =1020 кН
Суммарная величина растягивающего усилия Н равна
где к – коэффициент учитывающий упругость болта;
Крутящий момент необходимый для затягивания болта определяют по формуле;
где – диаметр стержня болта м
– коэффициент запаса прочности;
Касательное напряжение МПа возникающее в нарезанной части болта определяется по уравнению;
где т2 – общее количество болтов шт
– диаметр нарезанной части м
– диаметр стержня м
Соединение приводного вала мельницы с центральным приводом с редуктором и днищем барабана осуществляется посредством шлицевых и зубчатых муфт.
В шлицевых муфтах расчету подвергаются шлицы которые рассчитываются на изгиб срез и смятение от действия окружного усилия.
где к1 – коэффициент запаса;
к2 – коэффициент учитывающий тяжелые условия работы муфты;
Окружное усилие определяем по формуле;
где – диаметр шлицевой муфты;
Проводим проверку шлицев на смятие изгиб и МПа
где – наружный диаметр муфты м
– внутренний диаметр муфты м
– коэффициент учитывающий что не все шлицы работают одновременно;
Допустимое напряжение на смятие и растяжение [s] = 240 МПа на срез
[ t ] не более 100 МПа.
На основании выше приведенного анализа можно определить направление совершенствовании трубной шаровой мельницы.
Чтобы повысить эффективность процесса измельчения и качества продукции следует интенсифицировать процесса измельчения и повысить производительность трубной шаровой мельницы.
Банит Ф.Т. Несвижский О.А. Механическое оборудование цементных заводов. – М.: Машиностроение 1975. – 180 с.
Бауман Л.А. Клушанцев Б.В. Мартынов В.Д. Механическое оборудование предприятий строительных материалов изделий и конструкций. – М.: Машиностроение 1981. – 160 с.
Богданов В.С. Ильин А.С. и др. Дипломное и курсовое проектирование механического оборудования и технологических комплексов предприятий строительных материалов изделий и конструкций: Учебное пособие под редакцией В.С. Богданова и А.С. Ильина. – М.: Издательство Ассоциации строительных вузов 2006. – 784 с.
Клушанцев Б.В. Косарев А.И. Муйземнек Ю.А. Дробилки. Конструкция расчет особенности эксплуатации. – М.: Машиностроение 1990. –320с.
Лоскутов Ю.А. и др. Механическое оборудование предприятий по производству вяжущих строительных материалов. – М.: Машиностроение 1971 –376 с.
Сапожников М.Я. Механическое оборудование предприятий строительных материалов изделий и конструкций. – М.: Высшая школа 1971 –382с.
Сапожников М.Я. Дроздов Н.Е. Справочник по оборудованию заводов строительных материалов. – М.: Изд-во литературы по строительству
Сапожников М.Я. Механическое оборудование предприятий строительных материалов изделий и конструкций. Атлас конструкций. – М.: Машиностроение 1978 –111 с.