Технология сборки и сварки опорной балки



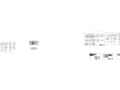
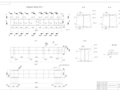

- Добавлен: 25.10.2022
- Размер: 2 MB
- Закачек: 0
Описание
Состав проекта
![]() |
![]() |
![]() ![]() ![]() ![]() |
![]() ![]() ![]() |
![]() ![]() ![]() |
![]() ![]() ![]() ![]() |
![]() ![]() ![]() |
![]() |
![]() ![]() ![]() |
Дополнительная информация
rryirsrrs-rrrryer-rr-1-srsrrs-r1.frw

rryirsrrs-rrrryer-rr-1-srsrrs-r1-rrrrrrsrrrer-srrsryere.dwg
и благоустройством территории
- датчик магнитоконтактный
- извещатель пожарный автоматический дымовой
- извещатель пожарный автоматический тепловой
- извещатель пожарный ручной
- извещатель пожарный автоматический пламени
- камера передающая телевизионной установки с поворотным устройством
- камера передающая телевизионной установки бех поворотного устройства
- датчик целостности стекла
- кодонаборное устройство (КНУ)
- считыватель радиокарт (СРК)
- кнопка тревоги (КТ)
Болт М30х100.10.9.ХЛ
Первичная применяемость
rrrryer11.dwg
налившегося раствора
Болт М30х100.10.9.ХЛ
Ведомость элементов Бл-1
Таблица отправных марок
Визуально-измерительный контроль
Ультразвуковая дефектоскопия
Просвечивание проникающим излучением
Контролируемые швы сварных соединений
тавровых и нахлесточных соединений всех элементов
Швы стыковых и тавровых соединений со сплошным проплавлением
Швы стыковых соединений
результаты проверки которых ультрозвуковой дефектоскопией требуют уточнения
м и объединены по верхним поясам пятью блоками 1П1-15 и ПК 1-15) металлической ортотропной плиты проезжей части. Плита состоит из листа настила толщиной 14мм
продольных ребер из полосы сечением 180x14мм и поперечных тавровых ребер
поставленных с шагом 3000мм по длине пролета По осям опор поставлены сварные двутавровые домкратные и поперечные балки (БЛ1
БП2). Металлические балочные строение автодорожных мостов 15 метровые пролеты -устанавливаются на опорные балки 1Бл-1). Все монтажные соединения металлоконструкций
включая соединение ортотропных плит проезжей части
на высокопрочных болтах М22 из стали 40Х (кроме оговоренных) "Селект" с пескоструйной обработкой контактирующих поверхностей. Все заводские соединения - сварные. Пролетные строения устанавливаются на тангенциальные металлические опорные части. 2.2. Профиль для ограждения автомобильных дорог согласно ТУ 14-2-341-78 из СтЗ (сп5)ГОСТ380-71. 2.3. Сборку опорных балок и приемку конструкции выполнять в соответствии с требованием и СТО-ГК "Трансстрой"-012-2007 Стальные конструкции мостов. Заводское изготовление. 2.4. Болты М12 в деформационных швах
в томе КМД-не учтены. 3. Антикоррозионная защита стальных конструкций. 3.1 0чистку
грунтовку и окрашивание стальных конструкций следует выполнять в соответствии с требованием СТО 001-2009 Защита металлических конструкций мостов от коррозии методом окрашивания" и "Рекомендации по применению полимерных материалов для защиты конструкций транспортных сооружений". Срок службы покрытия не менее 15 лет при условии эксплуатации в холодном макроклиматическом районе. 3.2 Соприкасающиеся поверхности в местах стыков и соединений но высокопрочных болтах не грунтовать и не красить. 3.3 Для защиты от коррозии мостовых конструкций использовать грунт "эпоксидное покрытие Iпterseo 670HS (серый)" и краску "эпоксидное покрытие Inter seal 670HS серый" и "полиуретановая эмаль Inter thane 990 (серый) РА Л 7038". Согласно СТО 001-2009. 4. Указания по изготовлению стальных конструкций. 4.1 Изготовление конструкции должно производиться в соответствии с требованиями СТО-ГК "Трансстрой "-012-2007 и в соответствии с требованиями чертежей настоящего проекта 4.2 Качество свободных или не полностью проплавляемых при сварке кромок деталей конструкций пролетного строения должно удовлетворять требованиям табл. 4 СТО-ГК "Трансстрой"-012-2007. 4.3 Все элементы из листовой стали подлежат проверке на отсутствие расслоения. Допускается контроль по состоянию кромок после резки
механической обработки
правки и других технологических операций. 4
Перед сборкой и сваркой главных и дом к ратных балок
блоков опорной плиты проезжей части должна быть выполнено автоматическая сварка вертикальных и горизонтальных листов
продольных ребер плит но полную длину элемента с учетом припуска на усадку при сварке. Начало и конец стыковых швов надлежит выводить на планки
удаляемые после сварки с тщательной зачисткой мест их установки. 4.5 Форма подготовки кромок стыков и соединений должно соответствовать указаниям на чертежах
требованиям СТО-ГК "Трансстрой"-012-2007
ГОСТ5264-80* заводским нормалям. 4.6 Сварочные материалы должны соответствовать СТО-ГК "Трансстрой"-012-2007. 4.7 Конструкции предназначены для восприятия динамических воздействий в условиях высоких напряжений. В соответствии с этим l0
- все угловые виды должны быть выполнены вогнутыми
с плавным переходом к основному металлу (допускается отступление с обеспечением требований п. 8.3.г СТО-ГК "Трансстрой "-012-2007 в части возможности выпуклости не более 15% катета шва)
- все угловые швы должны быть непрерывными
- все поперечные угловые швы
прикрепляющие поперечные (вертикальные) ребро жесткости к нижним поясам главных балок
выполняются ручной - сваркой с соотношением катетов 12 (больший катет на поясе) и СТО-ГК "Трансстрой"-012-2007
- все стыковые соединения (в том числе и не предусмотренные чертежами КМ) подлежат механической обработке по СТО-ГК - "Трансстрой "-012-2007; - качество механической обработки подлежит контролю ОТК и заводской инспекции. l7.3335
8 На заводе-изготовителе должны быть выполнены общие и контрольные сборки пролетного строения в соответствии с г лов ой 13 СТО-ГК "Трансстрой "-012-2007. 4.9 Методы и объемы контроля сварных швов
rryirsrrs-rrrryer-rr-1-srsrrs-r1-rrrrrrsrrrer-srrsryere.frw

rryirsrrs-rrrryer-rr-1-srsrrs-r1.dwg
и благоустройством территории
- датчик магнитоконтактный
- извещатель пожарный автоматический дымовой
- извещатель пожарный автоматический тепловой
- извещатель пожарный ручной
- извещатель пожарный автоматический пламени
- камера передающая телевизионной установки с поворотным устройством
- камера передающая телевизионной установки бех поворотного устройства
- датчик целостности стекла
- кодонаборное устройство (КНУ)
- считыватель радиокарт (СРК)
- кнопка тревоги (КТ)
Болт М30х100.10.9.ХЛ
Первичная применяемость
РПЗ.docx
2 Характеристика металла технические требования и его свариваемость 8
3 Разработка технических условий на изготовление сварной конструкции . ..10
3.1 Технические условия (ТУ) на изделие ..11
3.2 ТУ на контроль качества изделия 11
3.4 ТУ на сборку . . .11
3.5 ТУ на основной и сварочные материалы 11
3.6 ТУ на углекислый газ и Аргон 12
3.8 ТУ на изготовление деталей 12
3.9 ТУ на сварку .. 13
Технологическая часть .14
2 Выбор способа сварки 14
2.1 Автоматическая сварка под флюсом 14
2.2 Сварка в углекислом газе .17
3 Выбор сварочных материалов . .. .. 18
3.1 Сварочная проволока .. . 18
2.2 Флюс сварочный 19
2.3 Углекислота .. 19
4 Расчёт параметров режима сварки 20
5 Выбор сварочного оборудования . 28
6 Разработка технологии сборки и сварки . . 31
7 Обоснование выбора оснастки . 34
Выбор метода контроля . 34
Список использованных источников .. .38
Сварные конструкции давно нашли свое применение в строительной отрасли в машиностроении в автомобильной промышленности и в других сферах производства. С каждым годом производство сварных конструкций показывает все увеличивающиеся темпы развития — и причина этого состоит в том что потребители поняли все преимущества металлических конструкций произведенных с помощью сварки.
К достоинствам сварных конструкций относится: высокое качество и прочность соединения надежность удобство применения долгий срок службы небольшой вес экономия металла.
Если же говорить о недостатках сварных металлических конструкций то к ним можно отнести неустойчивость металла к коррозии. Но современные технологии изготовления металлоконструкций и способы обработки металла позволяют легко справиться с этой проблемой.
Сварные конструкции характеризуются максимально прочным соединением отдельных деталей между собой так как технология производства сварных конструкций основана на слиянии частей конструкций в единое целое на молекулярном уровне. Металл на краях деталей расплавляется до жидкого состояния и таким образом происходит обмен молекулами. В результате получается конструкция по своей прочности максимально близкая к прочности цельной детали.
Для изготовления сварных конструкций требуется меньше метала чем для изготовления конструкций соединенных с помощью заклепок или литых соединений. Причем экономия может достигать довольно значительных объемов — до 20% а это значит что сварное соединение можно считать эффективным не только с точки зрения расхода материалов но и с точки зрения стоимости всей металлоконструкции. То есть получается что изготовление металлоконструкций с помощью сварного соединения экономически обладает большей рентабельностью чем любые другие конструкции.
Имеется у сварных конструкций и еще одна отличительная черта логично вытекающая из предыдущей особенности — они весят меньше чем конструкции сделанные методом литья или собранные с помощью заклепочного соединения. И при этом по своей прочности они ничуть не уступают а даже превосходят эти виды конструкций.
В заключении нужно отметить что разработка технологии производства сварной конструкции производится индивидуально для каждой отдельной подобной конструкции в соответствии с технической документацией требованиями предъявляемыми к готовому изделию а также имеющимся в распоряжении производителя оборудованием.
1 Описание конструкции
Мост — искусственное сооружение возведённое через реку озеро овраг пролив или любое другое физическое препятствие. Мост возведённый через дорогу называют путепроводом мост через овраг или ущелье — виадуком. Мост является одним из древнейших инженерных изобретений человечества.
Как правило мосты состоят из пролётных строений и опор. Пролётные строения служат для восприятия нагрузок и передачи их опорам; на них может располагаться проезжая часть пешеходный переход трубопровод. Опоры переносят нагрузки с пролётных строений на основание моста.
Пролётные строения состоят из несущих конструкций: балок ферм диафрагм (поперечных балок) и собственно плиты проезжей части. Статическая схема пролётных строений может быть арочной балочной рамной вантовой или комбинированной; она определяет тип моста по конструкции. Обычно пролётные строения прямолинейны однако в случае необходимости (например при постройке эстакад и дорожных развязок) им придают сложную форму: спиралеобразную кольцевую и т. д.
Пролётные строения поддерживаются опорами каждая из которых состоит из фундамента и опорной части. Формы опор могут быть весьма разнообразными. Промежуточные опоры называются быками береговые — устоями. Устои служат для соединения моста с подходными насыпями.
Балочные мосты — самый простой вид мостов. Предназначены для перекрытия небольших пролётов. Пролётные строения — балки перекрывающие расстояние между опорами. Основная отличительная особенность балочной системы состоит в том что с пролётных строений на опоры передаются только вертикальные нагрузки а горизонтальные отсутствуют. Балочные мосты разделяют на следующие типы:
Разрезная система — состоит из ряда балок причём одна балка перекрывает один пролёт. Система статически определима и может применяться при любых типах грунтов. Недостатки: большое количество деформационных швов и обязательное наличие двух опорных частей на каждой промежуточной опоре.
Неразрезная система — одна балка пролётного строения перекрывает несколько пролётов или сразу все. Таким образом пролётное строение неразрезной системы рассчитывается как многоопорная статически неопределимая балка с использованием метода сил метода перемещений или других методов расчёта статически неопределимых систем применяемых в строительной механике. Неразрезная система хороша меньшим чем в разрезной количеством деформационных швов и меньшей строительной высотой. Недостаток такой системы — чувствительность к деформации основания.
Консольная система — состоит из двух типов балок. Одни балки опираются на две опоры и имеют консольные свесы. Другие балки называются подвесными поскольку опираются на соседние балки. Соединение балок осуществляется при помощи шарниров. Достоинством консольной системы является её статическая определимость а следовательно лёгкость расчёта и нечувствительность к грунтам. К недостаткам системы можно отнести большое количество и сложность устройства деформационных швов шарнирного типа а также нарушение комфортности проезда в зоне шарниров. В настоящее время мосты такой системы строятся редко.
Температурно-неразрезная система — состоит из двух опорных балок объединённых в цепь с помощью верхней соединительной плиты. Под действием вертикальных нагрузок такая система работает как разрезная а под действием горизонтальных — как неразрезная. Её достоинством является меньшее количество деформационных швов а недостатком — обязательное наличие двух опорных частей на каждой промежуточной опоре.
Во всех вышеперечисленных схемах мостов пролётные строения могут изготавливаться как в виде сплошных балок различного сечения так и в виде решётчатых конструкций то есть ферм.
Опорная балка является элементом моста и представляет собой жесткую сварную металлическую конструкцию двутаврового сечения.
По взаимному положению свариваемых элементов различают стыковые угловые тавровые и нахлёсточные соединения (рис. 1). По расположению в пространстве на момент сварки швы могут быть в нижнем горизонтальном вертикальном и потолочном положениях (рис. 2).
Независимо от пространственного положения и типа шва монтажные сварные соединения в мостах должны обеспечивать передачу всех расчетных усилий действующих в соединяемых элементах. Прочность сварных соединений при статических испытаниях должна быть не ниже прочности основного металла ; показатели ударной вязкости относительного удлинения и твердости по метал шва и по линии сплавления должны отвечать требованиям СТП.
Рисунок 1 . а – стыковые односторонние и двусторонние; б - угловое; в - тавровое; г - нахлёсточное
Типы сварных монтажных соединений:
Рисунок. 2. а - нижнее; б -горизонтальное; в - вертикальное; г - потолочное
Пространственное положение швов при монтажной сварке:
При проектировании сварных конструкций предпочтение следует отдавать стыковым соединениям (С) выполняемым механизированными способами. Угловые (У) тавровые (Т) и нахлесточные (Н) соединения если они необходимы на монтаже должны выполняться преимущественно в нижнем положении и тоже механизированными способами. Следует избегать протяженной потолочной горизонтальной и вертикальной ручной дуговой сварки узлов и конструкций.
Стыковые односторонние соединения в нижнем положении (рис.1а слева) должны выполняться автоматической сваркой с применением различных типов подкладок с обратным формированием корня шва.
Стыковые соединения с двусторонними швами (рис.1а справа) допускаются вконструкциях которые в процессе сборки и сварки могут быть перекантованы или в местах требующих сплошного проплавления в вертикальном или горизонтальном положениях(стыки ребер со вставками соединения ребер опорных диафрагм с продольными ребрами и т.д.).
Для стыковых односторонних или двусторонних соединений поясов балок при соответствующем обосновании допускается полуавтоматическая или ручная сварка взамен автоматической .
Форму подготовки кромок тип соединения пространственное положение шва и способ сварки следует указывать в чертежах КМ. При последующей разработке ППСР форма подготовки кромок должна уточняться в соответствии с назначаемой технологией сварки.
2 Характеристика металла технические требования и его свариваемость
Материалы для изготовления опорных балок и их элементов должны применяться в соответствии с государственными стандартами и другими нормативными документами.
Выбор материала должен производиться с учетом нижних предельных значений температуры окружающей среды для рабочего и нерабочего состояний балки степени нагруженности элементов и агрессивности окружающей среды.
Для определения склонности стали к хрупкому разрушению материала также необходимо учитывать вязкость металла как показатель склонности стали к старению. Одной из основных задач которые необходимо решить в процессе изготовления конструкции является определение группы свариваемости применяемого материала (10ХСНД) химический и механический состав стали приведен в таблице 1и 2.
Характеристика материала 10ХСНД
ХСНД ( другое обозначение 10ХСНД-Ш )
Сталь конструкционная низколегированная для сварных конструкций
Сталь хромокремненикелевая с медью
Элементы сварных металлоконструкций и различные детали к которым предъявляются требования повышенной прочности и коррозионной стойкости с ограничением массы и работающие при температуре от —70 до 450 °С
Зарубежные аналоги:
Для изготовления опорной балки выбираем сталь 10ХСНД-3.
Таблица 1 Химический состав. ГОСТ6713-91прокат листовой горячекатаный ГОСТ19903-74
Примечание: Также хим. состав указан в ГОСТ 6713 - 91 ГОСТ 19282-73
Технологические свойства материала 10ХСНД .
Механический состав стали10ХСНД .
Механические свойства при Т=20oС материала 10ХСНД .
Прокат ГОСТ 6713-91
Физические свойства материала 10ХСНД .
ХСНД - Сталь конструкционная низколегированная для сварных конструкций
Технологические свойства: температура ковки °С: начала 1200 конца 850.
Свариваемость материала: без ограничений.
Способы варки: РДС АДС под флюсом и газовой защитой ЭШС
Обрабатываемость резанием: в нормализированном и опущенном состояниив= 560МПа Kv б.ст= 112 Kv тв.опл= 14.1750. Охлаждение на воздухе.
Эта сталь менее склонна к старению и отличается меньшей реакцией на сварочный нагрев.
Сталь обыкновенного качества поставляют без термической обработки в горячекатаном состоянии. Изготовленные из нее конструкции также не подвергают последующей термической обработке.
Рассматриваемая сталь обладает хорошей свариваемостью. При сварке рассматриваемых сталей состав металла шва незначительно отличается от состава основного металла. В металле шва меньше углерода для предупреждения образования структур закалочного характера при повышенных скоростях охлаждения. Возможное снижение прочности металла шва вызванное уменьшением содержания углерода компенсируется легированием металла через проволоку покрытие или флюс марганцем и кремнием.
Повышенные скорости охлаждения металла шва способствуют увеличению его прочности однако при этом снижаются пластические свойства и ударная вязкость. Пластическая деформация возникающая в металле шва под действием сварочных напряжений также повышает предел текучести металла шва. Свойства сварного соединения зависят не только от свойств металла шва но и от свойств основного металла в около шовной зоне. Структура а значит и свойства основного металла в около шовной зоне зависят от его химического состава и изменяются в зависимости от термического цикла сварки.
Механические свойства металла шва и сварного соединения зависят от его структуры которая определяется химическим составом режимом сварки и предыдущей и последующей термической обработкой. Химический состав металла шва зависит от доли участия основного и электродного металлов в образовании шва и взаимодействий между металлом и шлаком и газовой фазой. При сварке рассматриваемых сталей состав металла шва незначительно отличается от состава основного металла. Возможное снижение прочности металла шва вызванное уменьшением содержания углерода компенсируется легированием металла через проволоку покрытие или флюс марганцем и кремнием.
Свариваемость стали зависит от нескольких параметров таких как удельное содержание углерода в стали толщина металла окисляемость металла при сварке сопротивляемость образованию трещин при нагревах.
Для оценки склонности металла к появлению холодных трещин чаще всего используется углеродный эквивалент который определяется по формуле:
При Сэ=04% а S≤04% холодные трещины не образуются подогрев не нужен.
3 Разработка технических условий на изготовление сварной конструкции
Конструкция должна изготавливаться в соответствии с чертежами. Отступления от чертежа не допускаются. В случае необходимости они должны быть согласованы с составителями чертежа. Изготовление конструкции производится в соответствии с разработанным технологическим процессом инструкциями и руководствами. При изготовлении конструкции должен быть обеспечен контроль над выполнением работ чертежей производства работ с занесением результатов контроля в сдаточную документацию или в журналы промежуточной приемки а также в исполнительную документацию.
3.1 Технические условия (ТУ) на изделие
Точность сварных конструкций должна соответствовать ГОСТ 25345. Если точность не удовлетворяет требованиям то целесообразно повышать ее посредством химической обработки механической обработки.
Допуск овальности и угловатости цилиндрических изделий после сварки и калибровки не должен превышать норм. Допуск прямолинейности цилиндрических изделий не должен быть более 2мм на метр длины.
3.2 ТУ на контроль качества изделия
Все швы сварных конструкций должны подвергаться техническому осмотру производимому методом визуального осмотра и измерений.
Контроль выбирается в зависимости от условий эксплуатации изделия. После термической обработки сварных конструкций должен быть проведен визуальный осмотр всех швов и при необходимости контроль наличия внутренних трещин и несплошностей швов а также в зависимости от сложности конструкции по назначению служб технолога должны быть проверены ее размеры.
Сварные жесткие конструкции включающие замкнутые швы включающие их свободную усадку и выполненные из сталей содержащих углерода более 0.22% и элементов эквивалентных углероду более 06% при толщинах более 25 мм необходимо подвергать термической обработке или другому виду стабилизации напряжений.
Точность изготовления деталей в зависимости от сложности и габаритов сварных металлоконструкций должна назначаться на 1-2 квалитета выше точности чистовой механической обработки.
Размеры деталей сварных металлоконструкций должны устанавливаться с учетом усадки от сварных швов.
Допуски на детали образующие общий размер не должны превышать допуски на этот размер.
Качество поверхности необработанных кромок деталей должно соответствовать данным приведенным в ГОСТ 14792.
3.5 ТУ на основной и сварочный материалы
Качество и марка материала стали 10ХСНД должны соответствовать требованиям ГОСТ и удостоверяться сертификатами. При отсутствии соответствующих сертификатов или сомнениях по качеству и марке стали проводятся лабораторные испытания. Вся сталь должна быть проверена на соответствие действующему ГОСТу замаркирована сложена по профилям. Перед подачей в производство выправлена очищена от окалины ржавчины масла влаги и других загрязнений. При транспортировке необходимо применять приспособления исключающие образование деформации и смятие стали.
Для автоматической и механизированной сварки применить проволоку сплошного диаметра удовлетворяющую требованиям ГОСТ 2246-70 Поверхность сварочной проволоки должна быть чистой и гладкой без окалины ржавчины масла и других загрязнений.[1]
3.6 ТУ на углекислый газ и аргон
Углекислый газ применяемый для сварки углеродистой и низкоуглеродистой стали должен соответствовать ГОСТ 8050-85
Аргон предназначен для использования в качестве защитной среды при сварке сталей различных марок должен соответствовать ГОСТ 10157-79
Флюс для сварки металлоконструкций должен соответствовать ГОСТ 9087 . Флюс перед сваркой для удаления влаги следует прокаливать при температуре 350 градусов в течение 2-3 часов перевозить из цеха в цех в закрытой таре.
3.8 ТУ на изготовление деталей
Метод изготовления деталей должен выбираться в зависимости от допусков на их размеры наличие оборудования и экономической целесообразности. Все готовые детали подвергаются внешнему осмотру и обмеру.
Правка должна осуществляться в листоправильных машинах прессах обеспечивающих плавность нагрузки. Если необходима разметка то она должна осуществляться по шаблонам и с помощью материального инструмента.
Резку необходимо проводить по технологическим картам в которых указывается способ резки и разметка.
При гибке необходимо учитывать особенности технологии и поведения металла при гибке зависящего от механических свойств металла. В горячем состоянии гибка должна проводится при температурах 700-1100 градусов. При этом скорость охлаждения должна исключать закалку коробление трещины и надрывы материала. Гибку необходимо проводить поперек волокон проката. Во избежание складок на внутренней поверхности место сгиба надо хорошо подогревать. Брать припуск на гибку по технологическим картам.
Сварку производить на установленных режимах по разработанному технологическому процессу. Сварку должен производить электросварщик или оператор автоматической или механизированной сварки имеющий соответствующее удостоверение. Сварку производить после проверки правильности сборки узлов и конструкции в целом. Зажигать дугу и выводить кратер на основной металл запрещается. Сварные швы должны быть не ниже качества основного металла. Швы сварных соединений по окончании сварки должны быть очищены от шлака брызг и натеков металла. Выполнение каждого валика многослойных швов допускается после зачистки предыдущего валика и прихваток от брызг металла и шлака конструктивные размеры сварных швов должны соответствовать ГОСТ 14771-76 и ГОСТ 8713-70. [67]
Маркировка окраска упаковка хранение и транспортирование.
Маркировка должна проводится в цехах по ГОСТ 14192 ГОСТ 23170. Для защиты от коррозии сварные конструкции должны быть окрашены. Сварные конструкции отправляемые заказчику должны быть подвергнуты консервации. Консервация должна предусматривать быстрое и легкое удаление консервирующего слоя.
Требования безопасности.
Конструкция должна соответствовать нормам безопасности труда по ГОСТ 12.3.003 ОСБТ. Не превышать уровень шума установленный по ГОСТ 12.1.003.
Технологическая часть
1 Подготовка конструкции к сварке
Элементы конструкций должны быть обработаны под монтажную сварку в соответствии с требованиями настоящего стандарта и чертежей.
Поступившие на монтаж конструкции должны быть подвергнуты тщательному внешнему осмотру с целью определения правильности подготовки кромок соединяемых элементов.
В монтажных условиях при необходимости скос кромок свариваемых элементов следует выполнять механизированной зачисткой (шлифовкой) абразивным инструментом.
Свариваемые элементы в местах наложения швов и прилегающие к ним кромки должны быть зачищены до металлического блеска с удалением окалины ржавчины жиров и т.д.
Процесс сборки сварных соединений должен включать следующие операции: временное закрепление монтируемых элементов и подгонку соединения под сварку. Конструкция сварного соединения должна обеспечить возможность последовательного выполнения этих операций.
Сборку нужно производить на стенде используя специальные приспособления. В условиях специального производства расположение деталей в узле нередко задается разметкой; для их фиксации используют струбцины планки скобы с клиньями и другие простейшие универсальные приспособления.
Для сборки балки крана мы будем использовать сборочное приспособление- жесткий каркас с упорами и прижимами. При сборке детали заводят в приспособление укладывают по упорам и закрепляют прижимами.
Сборку производим на прихватках пооперационно каждый отдельный узел. За фиксированные собранные узлы на прихватках должны обладать жесткостью и прочностью.
Прихватки должны быть протяженностью не менее чем 20-З0 мм и располагаться в местах где они будут переварены при укладке основных швов. При использовании сборочно-сварочных приспособлений сварку выполняют после сборки не вынимая из приспособления.
2 Выбор способа сварки.
Выбор способа сварки является одним из наиболее важных аспектов в процессе производства сварной конструкции поскольку этот выбор определяет решение следующих задач технологичности сварной конструкции:
обеспечение сварного шва требуемыми механическими технологическими и другими свойствами.
высокую производительность производства.
снижение трудозатрат за счет возможной автоматизации сварочных процессов.
использование менее квалифицированных рабочих сварщиков за счет автоматизации процесса что как следствие влияет на затраты производства.
Рассматривая конструкцию опорной балки можно определить что поясные швы имеют достаточную протяженность сварных швов что позволяет применить автоматизированный процесс сварки как например дуговую сварку под флюсом сварочная консоль (ESAB-IT).
Также следует отметить что приварка ребер жесткости в процессе производства приходится делать на цепном кантователе то есть на готовый стержень приваривают ребра жесткости и из этого следует что автоматизация процесса весьма затрудняется и предпочтительней воспользоваться полуавтоматической сваркой в среде защитного газа (WEGA 600mig).
Производительность по сравнению с ручной сваркой увеличивается в 5-10 раз. При сварке под флюсом ток по электродной проволоке проходит только в ее вылете (место от токоподвода до дуги). Поэтому можно использовать повышенные (25-100 Амм2) по сравнению с ручной дуговой сваркой (10-20 Амм2) плотности сварочного тока без опасения значительного перегрева электрода в вылете и отслаивания обмазки как в покрытом электроде.
Использование больших сварочных токов резко повышает глубину проплавления основного металла и появляется возможность сварки металла повышенной толщины без разделки кромок. При сварке с разделкой кромок уменьшается угол разделки и увеличивается величина их притупления т.е. уменьшается количество электродного металла необходимого для заполнения разделки. Металл шва обычно состоит приблизительно на 23 из переплавленного основного металла (при ручной дуговой сварке соотношение обратное). В результате вышесказанного растут скорость и производительность сварки. Под флюсом сваривают металл толщиной 2-60 мм при скорости одно дуговой сварки до 70 мч. Применение многодуговой сварки позволяет повысить её скорость до 300 мч.
Высокое качество металлов шва и сварного соединения достигается за счет надежной защиты расплавленного металла от взаимодействия с
воздухом его металлургической обработки и легирования раздавленным шлаком. Наличие шлака на поверхности шва уменьшает скорость кристаллизации металла сварочной ванны и скорость охлаждения металла шва. В результате металл шов не имеет пор содержит пониженное количество неметаллических включений. Улучшение формы шва и стабильности его размеров особенно глубины проплавления обеспечивает постоянные химический состав и другие свойства на всей длине шва. Сварку под флюсом применяют для изготовления крупногабаритных строительных конструкций из сталей.
В настоящее время сварка в среде углекислого газа широко применяется при изготовлении изделий из углеродистых конструкционных сталей.
Особенностью сварки в углекислом газе является сравнительно сильное выгорание элементов обладающих большим сродством к кислороду (С Al Ti Si Mn и др.).
Окисление происходит за счет как углекислого газа так и атомарного кислорода который образуется при диссоциации С02 под действием температуры дуги.
Поэтому для получения качественных соединений необходимо при сварке в среде углекислого газа иметь в сварочной ванне достаточное количество раскисляющих элементов.
Элементы -раскислители вводятся в сварочную ванну обычно за счет проволоки (Св-08Г2С Св-08ГС).
Химический состав металла шва зависит не только от основного и электродного металла но и от параметров режима сварки особенно от Uд (напряжение дуги) и I св(сварочный ток).
При повышении сварочного тока и уменьшении напряжения увеличивается температура дуги и уменьшается время пребывания капель электродного металла в контакте с газом т.е. уменьшается время накапливания капли на конце электрода. Вследствие этого уменьшается степень выгорания раскислителей из сварочной проволоки.
Наоборот повышение напряжения на дуге приводит к значительному обеднению металла шва раскислителями так как процент выгорания их в столбе дуги повысится за счет того что увеличится время контакта капли электродного металла с газом.
Если количество водорода содержащегося в сварочной ванне превосходит предел его растворимости в металле к началу кристаллизации ванны то поры в шве неизбежны что снижает механические свойства сварного соединения.
Для получения плотных швов в углекислом газе должно быть не более 004% растворенной воды и не более 01 % воды в свободном состоянии поэтому необходимо тщательно осушать углекислый газ предназначенный для сварки.
При недостаточном расходе углекислого газа в зону сварки проникает воздух. Из-за этого в металл шва попадает азот что приводит к образованию пор как и при попадании водорода. Кроме того азот увеличивает твердость и хрупкость металла шва т. е. снижает пластичность соединения. Азот в металл шва может попасть и из углекислого газа загрязненного им поэтому содержание азота в углекислом газе не должно превышать 01%.
Углекислый газ имеет следующие особенности:
при повышении давления превращается в жидкость;
при охлаждении без давления переходит в твердое состояние — сухой лед;
сухой лед при повышении температуры переходит непосредственно в газ минуя жидкое состояние.
Для сварки применяют углекислоту по ГОСТ 8050 — 76 поставляемую в баллонах в жидком состоянии. При испарении 1 кг жидкой углекислоты при 0°С и 760 мм.рт.ст. образуется 5068 л газа. В стандартный баллон емкостью 40 л заливают 25 кг жидкой углекислоты что составляет 1267 м3 газа. Вредными примесями в углекислом газе являются азот и влага.
Влага удаляется из газа осушителем который заполняется силикагелем алюминием или медным купоросом которые перед заправкой в осушитель необходимо прокалить при температуре 250 —300°С в течение 2 — 25 ч.
Конструкция сварных соединений в первую очередь зависит от расчетных показателей полученных при процессе проектирования определяется катет шва и протяженность.
В сварных швах возникают напряжения: связующие - в следствии совместной деформации наплавленного и основного металла и рабочие - передающие усилия с одного элемента на другой. Связующие напряжения при расчете сварных конструкций не учитывают.
Угловые швы доминирующие в сварной конструкции имеют треугольную форму. В результате проплавления основного металла их форма изменяется. Минимальные размеры катетов определяются толщиной основного металла и классом стали по пределу текучести согласно СНиП П-23-81.
Далее согласно ГОСТу на сварные соединения в зависимости от способа сварки подбирается конструкция сварного соединения с основными элементами разделки или без кромок в зависимости от выбранной технологии сварки и условий свариваемости данной марки стали.
Как было сказано выше при производстве сварной конструкции используется низкоуглеродистая конструкционная сталь. И при анализе свариваемости в совокупности со способом сварки а также с применением сварочных проволок было обосновано что легирование целесообразнее осуществлять за счет флюса что исключает необходимость использование более дорогих сварочных материалов.
При рассмотрении вопроса выбора способа сварки было определено что поясные соединения будут свариваться автоматической сваркой под флюсом а все остальные свариваться в среде углекислого газа.
Типы сварных соединений назначаем в соответствии с ГОСТ 14771-76 и ГОСТ 8713-79 «соединения сварные» при сварке в среде углекислого газа и автоматической сварки под флюсом соответственно[13].
Автоматическая сварка под флюсом:
Принимаем тип Т3 - тавровое соединение с двухсторонним швом.
Катет шва согласно проекту принимаем 10мм для всех поясных швов
Подробно списывать целые разделы из литературы о сущности способов сварки нет смысла нужно просто перечислить возможные способы для сварки Вашей конструкции описать процесс (применительно к конструкции и конкретным швам) достоинства и недостатки каждого способа и обосновать выбор способов которые будут применены.
2.1 Автоматическая сварка под флюсом.
Создание автоматической сварки под флюсом является крупнейшим достижением современной сварочной техники. Первоначальная идея способа сварки под флюсом принадлежит изобретателю способа дуговой сварки Н. Г. Славянову. В качестве флюса он применял дробленое оконное стекло.
При сварке под флюсом сварочная дуга между концом электрода и изделием горит под слоем сыпучего вещества называемого флюсом.
Флюс насыпается слоем толщиной 50-60 мм; дуга утоплена в массе флюса и горит в жидкой среде расплавленного флюса в газовом пузыре образуемом газами и парами непрерывно создаваемыми дугой. При среднем насыпном весе флюса около 15 гсм2 статическое давление слоя флюса на жидкий металл составляет 7-9 гсм2. Этого незначительного давления как показывает опыт достаточно чтобы устранить нежелательные механические воздействия дуги на ванну жидкого металла разбрызгивание жидкого металла и нарушение формирования шва даже при очень больших токах.
В то время как при открытой дуге механическое воздействие цуги на ванну жидкого металла делает практически невозможной сварку при силе тока выше 500 – 600Аа вследствие разбрызгивания металла и нарушения правильного формирования шва погружение дуги во флюс дало возможность увеличить применяемые токи в среднем до 1000-2000 а и максимально до 3000-4000 п. Таким образом появилась возможность при сварке под флюсом повысить сварочный ток в 6-8 раз по сравнению с открытой дугой с сохранением высокого качества сварки и отличного формирования шва. Производительность сварки при этом растет значительно быстрее увеличения тока меняется самый характер образования шва.
Маломощная открытая дуга лишь незначительно расплавляет кромки шва который образуется главным образом за счет расплавленного электродного металла заполняющего разделку кромок. Мощная закрытая дуга под флюсом глубоко расплавляет основной металл позволяет уменьшить разделку кромок под сварку а часто и совсем обойтись без разделки. Снижается доля участия электродного металла в образовании шва; в среднем наплавленный металл образуется на 23 за счет расплавления основного металла и лишь на х3 за счет электродного металла. Производительность сварки определяемая числом метров шва за час горения дуги при сварке под флюсом значительно выше (до 10 раз) чем при сварке открытой дугой на одинаковых сварочных токах. Таким образом производительность сварки под флюсом возрастает как за счет увеличения сварочного тока так и за счет лучшего его использования.
Возможность резкого увеличения силы сварочного тока составляет главное неоценимое преимущество сварки под флюсом. Заключение дуги в газовый пузырь со стенками из жидкого флюса практически сводит к нулю потери металла на угар и разбрызгивание суммарная величина которых не превышает 2% веса расплавленного электродного металла. Сварные швы получаются равномерного и очень высокого качества. Отсутствие потерь на угар и разбрызгивание и уменьшение доли электродного металла в образовании шва позволяют весьма значительно экономить расход электродной проволоки. Лучшее использование тока заметно экономит расход электроэнергии. Так как дуга горит невидимо под толстым слоем флюса не требуется защиты глаз работающих.
К недостаткам сварки под флюсом можно отнести невидимость места сварки закрытого толстым слоем флюса и довольно значительные расход и стоимость флюса. Невидимость места сварки повышает требования к точности подготовки и сборки изделия под сварку затрудняет сварку швов сложной конфигурации. Расход флюса по весу в среднем равняется весу израсходованной проволоки и стоимость его оказывает существенное влияние на общую стоимость сварки.
Применение для сварки под флюсом дуговых автоматов особых осложнений не вызывает дуга под флюсом обычно устойчивее открытой дуги. Переход на сварку под флюсом потребовал лишь увеличения сварочных токов и соответственного увеличения размеров и усиления конструкции автоматов. Сварка под флюсом в большинстве случаев ведется на токе высоких плотностей поэтому широко применяются автоматы с постоянной скоростью подачи электродной проволоки.
2.2 Сварка в углекислом газе.
Обычно выполняют на постоянном токе обратной полярности плавящимся электродом. Основными параметрами режима сварки в СО2 и его смесях являются полярность и сила тока напряжение дуги; диаметр скорость подачи вылет и наклон электрода; скорость сварки; расход и состав защитного газа.
Сварочный ток и диаметр электродной проволоки выбирают в зависимости от толщины свариваемого металла и расположения шва в
пространстве. Стабильный процесс сварки с хорошими технологическими характеристиками можно получить только в определенном диапазоне силы сварочного тока который зависит от диаметра и состава электродной проволоки и рода защитного газа.
Величина сварочного тока определяет глубину проплавления и производительность процесса сварки. Величину сварочного тока регулируют изменением скорости подачи сварочной проволоки.
Одним из важных параметров режима сварки в СО2 является напряжение дуги. С повышением напряжения увеличивается ширина шва и улучшается его формирование. Однако увеличивается и угар полезных элементов кремния и марганца повышается чувствительность дуги к магнитному дутью увеличивается разбрызгивание металла сварочной ванны. При пониженном напряжении дуги ухудшается формирование сварочного шва. Оптимальные значения напряжения дуги зависят от величины сварочного тока диаметра и состава электродной проволоки а также от рода защитного газа.
Другие параметры режима сварки в СО2 находятся в сложной зависимости от различных факторов влияющих на сварочный процесс.
Режим сварки в СО2 подбирают на основании обобщенных опытных данных.
Перед началом сварки необходимо отрегулировать расход газа и выждать 20-30 секунд до полного удаления воздуха из шлангов. Перед зажиганием дуги необходимо следить чтобы вылет электрода из мундштука не превышал 20 - 25 мм. Движение горелки должно осуществляться без задержки дуги на сварочной ванне так как эта задержка вызывает усиленное разбрызгивание металла. Сварка в нижнем положении производится с наклоном горелки под углом 5 - 15° вперед или назад. Предпочтительнее вести сварку углом назад т.к. при этом обеспечивается более надежная защита сварочной ванны. При механизированной сварке металла малой толщины 1-2 мм поперечных колебательных движений не производят. Сварку ведут на максимальной длине дуги с максимальной скоростью. При достаточной газовой защите избегают прожогов и обеспечивают нормальное формирование шва. Горелку ведут углом назад при этом угол наклона составляет 30-45°.
Стыковые соединения при толщине металла 15-3 мм сваривают на весу. Более тонкий металл сваривают в вертикальном положении на спуск (сверху вниз) провар достигается за один проход. Сварку соединений внахлестку при толщине металла 08-20 мм чаще производят на весу и реже — на медной подкладке. При качественной сборке нахлёсточных соединений представляется возможным значительно увеличить скорость сварки. Колебательные движения горелкой при сварке больших толщин те же что и при ручной сварке. При сварке с перекрытием для уменьшения пор применяются продольные колебания горелки вдоль оси шва что обеспечивает более полное удаление водорода из сварочной ванны.
Сварка в среде СО2 является высокопроизводительным процессом. В массовом и крупносерийном производстве работают слесари-сборщики которые освобождают сварщика от сборочных операций. Сварочный пост в этом случае оборудуется кроме сварочной аппаратуры специальными приспособлениями для обеспечения высокой производительности сварочных работ при гарантированном качестве сварных узлов.
Требования к качеству сборки и подготовки деталей под сварку в СО2 сварочной проволокой (08 - 25) мм должны соответствовать ГОСТ 14771-76.
3 Выбор сварочных материалов
Для того чтобы сварка получалась качественной главное чтобы шов был надежным. Нужно не только соблюдать технологию процесса но и подбирать т.е. правильно делать выбор сварочных материалов для сварки. Сварочные материалы выбираются в зависимоcти от основного материала от способа сварки используемой при изготовлении конструкции. В нашем случае мы используем автоматическую сварку под флюсом и сварку в СО2 применительно к сварке низкоуглеродистой стали Ст3сп а значит необходимо выбрать: проволоку флюс углекислоту.
3.1 Сварочная проволока Св08А
Сварочная легированная проволока марки Св08А изготавливается согласно ГОСТ 2246-70* химический состав приведен в таблице 3.
Таблица3 - Химический состав проволоки Св08А
Марка сварочной пров.
Массовая доля химических элементов в пределах или не более %
Диаметр сварочной проволоки: 120 - 60 мм;
Допуски по диаметру согласно ГОСТ 2246-70;
Поверхность сварочной проволоки – неомеднённая
Сварочная проволока Св-08А применяется для :
сварки в среде защитных газов
сварки конструкции ответственного и общего назначения
сварки углеродистых и легированных сталей: конструкционной стали стали для сосудов под высоким давлением и судостроительной стали.
3.2 Флюс сварочный АН-348А
Флюс сварочный АН-348А ГОСТ9087-81 химический состав которого приведен в таблице 4 предназначен для автоматической и полуавтоматической сварки и наплавки углеродистых нелегированных и низколегированных сталей углеродистой и низколегированной сварочной проволокой: СВ08 СВ-08ГА S1 S2.
Сварочно-технологические свойства.
При влажности превышающей допустимую флюс перед употреблением подвергают в сушке при температуре 300-400 0С в течение 1-2 часов.
Таблица 4 - Химический состав флюса АН-348А в %
Цвет зерен - от желтого до коричневого всех оттенков; размер зерен 025-28 мм; строение зерен - стекловидное; объемная масса 13-18 кгдм3
3.3 Углекислота высшего сорта 99.8%
Требования к качеству сборки и подготовки деталей под сварку в СО2 сварочной проволокой (08 — 16) мм должны соответствовать ГОСТ 14771-76.
4 Расчёт параметров режимов сварки
катет шва – 10 мм. Диаметр электродной проволоки – 4 мм:
Вычисление общей площади наплавки по формуле:
Fно= FА + FB [мм2] (2.1)
FA – площадь треугольника с катетом К=10мм.
FB – площадь выпуклой части шва.
FА= = 50мм2 = 050 см2
где в – коэффициент формы валика (в=5-8).
FB = egM [см2] (2.5)
где М-коэффициент полноты М=075
FB = 15016075=018 см2
Fно= 050 + 018=068 см2
Определяем силу тока по формуле:
где i – плотность тока принимаем i=48
Напряжение дуги принимаем – 34В
Определяем коэффициент наплавки αн
αн = А + В [ ] (2.7)
где АВ – значения для флюса в зависимости от рода тока.
Находим действительный коэффициент наплавки
αн.д= αн + Δαн [ ] (2.8)
где Δαн – находим по графику
αн.д= 1602 + 02 = 1604
Определяем скорость перемещения дуги:
где у – плотность металла.
Находим скорость подачи сварочной проволоки:
Полуавтоматическая сварка в среде углекислого газа:
К параметрам режимов сварки в защитных газах относятся род и полярность тока диаметр электродной проволоки величина сварочного тока напряжение на дуге скорость подачи проволоки.
Механизированная сварка в среде защитного газа на переменном токе не применяется так как процесс сварки затрудняется из-за нестабильного горения дуги.
Сварку в среде СО2 плавящимся электродом производят на постоянном токе обратной полярности. Это объясняется тем что при токе прямой полярности процесс сварки характеризуется большим разбрызгиванием даже при сварке значительно меньшим током. Это в свою очередь приводит к уменьшению глубины провара. Хотя коэффициент плавления электродной проволоки при сварке на обратной полярности в 15 - 18 раза меньше чем при сварке на прямой полярности это преимущество в большинстве случаев не удается использовать так как при сварке на прямой полярности ширина шва значительно меньше а высота выпуклости больше чем при сварки на обратной полярности. Кроме того сварка на токе прямой полярности характеризуется увеличением окисления элементов и повышением склонности шва к образованию пор.
При сварке в углекислом газе обычно применяют постоянный ток обратной полярности т.к. ток прямой полярности приводит к неустойчивому
горению. Переменный ток также приводит к неустойчивости процесса горения дуги и худшему формированию шва можно применить только при сварке осциллятором.
Катет шва - 12мм; 8мм; Диаметр эл. проволоки – 12мм.
Силу сварочного тока рассчитываем по формуле:
Jсв =j Aэл [А] (2.11)
где j - плотность тока Амм"=175
АЭЛ - площадь поперечного сечения электродной проволоки мм (Расчёт режимов является ориентировочным и на практике требует уточнения).
Определяем скорость подачи электродной проволоки по формуле:
Vnn = рэл [ммс] (2.12)
где: Vnn - скорость подачи проволоки ммс
λр - коэффициент расплавления электродной проволоки гАч
Рэл - плотность металла электродной проволоки гмм (0.0078 гмм ).
1 Коэффициент расплавления определяем по формуле:
Vnn = = 4719ммс = 1698мч
Определяем скорость сварки по формуле:
VCB= или VCB=0.9 (2.14)
где VCB - скорость сварки ммс
λн - коэффициент наплавки гАч
Ан - площадь поперечного сечения шва мм2
Рн - плотность металла гмм“
9 - коэффициент учитывающий потери металла на угар и разбрызгивание
1 Коэффициент наплавки определяется по формуле:
λн = λр(1- )[ гАч] (2.15)
где - потери электродного металла вследствие окисления испарения и разбрызгивания % (= 7-15 % принимаем = 10%)
λн= 00032(1- ) = 000288 гАс =1036 гАч
2 Площадь поперечного сечения шва мм2
Fно=Fа + Fb [мм2 ] (2.1)
где FА - площадь треугольника с катетом К=12мм.
FB - площадь выпуклой части шва.
Fa= = 72мм2 = 072см2.
FB = 17016075= 0204 см2.
Fно = 072+0204= 0924 см2
Так как сварку катетом 12мм мы варим в 3 прохода то
Fa= = 32мм2 = 032см2
FB= 113018075= 015см2.
Fно = 032+015 = 047 см2
Vсв=36*099=36мч при катете шва 8мм.
Напряжение на дуге принимают в интервале 16-34 В
Напряжение принимаем Ud=28В. Большее значение соответствуют большей величине тока. Данные расчетов параметров и режимов сварки сведены в таблицу 5.
Напряжение на дуге предварительно подбирается и может быть установлено при настройке например по напряжению холостого хода источника тока.
Таблица 5 – Данные расчетов параметров и режимов сварки
Автоматическая сварка под флюсом
Механизированная сварка в среде СО2AR
5 Выбор сварочного оборудования
Установка для сварки балок
ЭСАБ обладает необходимым оборудованием и ноу-хау для высокопроизводительной и качественной сварки
- Т- или L-образных балок балок с широкими полками балок переменного сечения и балок несимметричного профиля
Установки для сварки балок выпускаются двух типов: IT-установки в которых балка сваривается при вертикальном положении стенки и BW-установки сваривающие балку в горизонтальном положении стенки
Основным достоинством установки для сварки балок помимо ее высокой производительности является то что во время процесса сварки
стенка балки прижата к полке так что зазор в стыке исключен
Это гарантирует высокое качество сварки
Установка IT имеет встроенное устройство правки грибовидности которое предотвращает изгиб при сварке (см Рисунок 4)
Программа выпуска установок ЭСАБ для сварки балок позволяет выбрать оборудование для выполнения ваших конкретных требований
Свариваемые балки имеют следующий диапазон размеров:
Где полный состав сварочного оборудования (для каждого способа включая сборку – источник питания автомат (полуавтомат) подающий механизм и т.д. техническая характеристика и краткое описание?
Стержень балки имеет достаточную протяженность поэтому сварку производим на автоматической консоли под слоем флюса.
Рисунок 4 – Сварочная консоль
Для приварки ребер жесткости будет предпочтительней воспользоваться полуавтоматической сваркой в среде защитного газа. WEGA 600mig (см.рисунок.5). Аппараты WEGA - это отличные характеристики зажигания дуги отсутствие брызг в зоне короткой и капельной дуги мелко ступенчатое регулирование 4-х роликовый механизм подачи сварочной проволоки продуманная конструкция корпуса с улучшенным воздуховодом для увеличения ПВ. Аппараты WEGA предназначены для сварки полуавтоматом на токах до 600 А обладают идеальным зажиганием дуги и мощной системой охлаждения сварочной горелки.
Аппараты MIGMAG сварки металлов компании EWM - это стабильность режимов сварки (даже при значительных перепадах сетевого напряжения) высокая надежность и мобильность простота в использовании лаконичность дизайна и прочность корпуса. Все аппараты оснащены дополнительными функциями и удобными панелями управления значительно облегчающими работу сварщика. Сварочный аппарат полуавтомат EWM также позволяет значительно увеличить производительность.
Благодаря инновационным разработкам в сфере сварочных технологий и собственному производству компания EWM лидирует на европейском рынке. Мы хотим чтобы Вы знали что купить сварочный полуавтомат EWM может каждый желающий. В нашем каталоге Вы легко найдёте необходимое Вам оборудование для сварки полуавтоматом.
Технические характеристики полуавтомата WEGA 600mig приведены в таблице 5.2
Таблица 5.2- технические характеристики полуавтомата WEGA 600mig
Технические характеристики
Диапазон регулирования сварочного тока А
Количество ступеней переключения
Скорость подачи проволоки ммин
Температура окружающей среды град. С
Сила тока при ПВ 60% А
Сила тока при ПВ 100% А
Сетевое напряжение (допуски) В
Частота тока в сети Гц
Сетевой предохранитель А
Максимальная потребляемая мощность кВА
Рекомендуемая мощность генератора кВА
Емкость бака (охлаждающая жидкость) л
Максимальный расход лмин
Максимальное давление на выходе бар
Габариты сварочного аппарата (Д×Ш×В) мм
Габариты устройства подачи проволоки (Д×Ш×В) мм
Масса сварочного аппарата кг
Масса устройства подачи проволоки кг
Аппарат имеет два вида панелей:
oКлассическая панель управления.
o2-х и 4-тактный режимы.
oСовременная концепция с цифровым дисплеем показывающим все параметры сварки.
o2-х. и 4-тактный режимы бестоковая проверка газа и заправки проволоки;
Возможность выбора режима работы: Job (однокнопочное управление) и Manuаl (двухкнопочное управление)
Рисунок 5 – Тележка и блок управления для полуавтоматической сварки
При оснащении кондуктора отдельными единицами оборудования и приспособлениями выбор производится по наиболее важными показателями оборудования. При сборке опорной балки углы между стенкой и полками должен составлять 90º.
Эффект использования сборочного кондуктора существенно зависит от быстрого действия и надежности механизма зажатия элементов. Закрепление и освобождение элементов балки по всей длине с помощью винтов занимает много времени. Значительно производительнее и удобнее в работе приспособления оснащенные пневматическими зажимами с питанием от заводской сети сжатого воздуха. В этом случае зажатие и освобождение балки осуществляется переключением крана подачи воздуха. Обеспечение взаимной перпендикулярности полки и стенки при сборке требует поступательного перемещения зажимающего элемента. Это можно осуществить либо путем жесткого крепления прижимов на штоках цилиндров либо прямолинейными направляющими прижимов с шарнирным креплением последних к штокам цилиндров показано на рисунке 5.
После сборки опорной балки с помощью мостового крана грузоподъемностью 10т перевозим балку на сварку. Для сварки поясных швов используем автоматическую сварку под слоем флюса. (см. рисунок 6)
После сборки и заварки поясных швов автоматической сваркой балку с помощью мостового крана грузоподъемностью 10т перевозим на сборку для установки на балку ребер жесткости. Ребра жесткости на балку устанавливают сборщики вручную. Для установки используют ручные приспособления. После сборки балка отправляется на сварку но уже полуавтоматическим способом. Для сварки используют полуавтоматы wega 600 mig (см.рисунок 5) в качестве газа используется смесь углекислоты и аргона сварочная проволока толщиной 12 мм.
По окончании сварки балка отправляют на зачистку от окалин брызг и др. Затем отправляют готовое изделие в покрасочный цех где балка проходит пескоструйку грунтовку покраску и сушку а затем её складируют.
6 Разработка технологии сборки и сварки
Сварку на монтаже мостов применяют главным образом для соединения основных несущих конструкций стальных пролетных строений сплошностенчатых двутавровых иL-образных балок составных из цельноперевозимых блоков коробчатых сечений настильных листов ортотропных плит ребристых плит .
Конструкция монтажных соединений должна обеспечивать беспрепятственное выполнение сварки на всей длине шва.
Монтажные стыки двутавровых L-образных и коробчатых сплошностенчатых балок могут быть цельносварными комбинированным и фрикционно-сварными. На выбор типа стыка в определенной степени влияет способ монтажа пролетных строений. При сборке пролетных строений на берегу с последующим перемещением их на опоры предпочтение отдается цельносварным стыкам; при навесной полунавесной и уравновешенно-навесной сборке целесообразно применение комбинированных стыков.
В комбинированных фрикционно-сварных стыках главных балок стыковые сварные соединения верхнего пояса рекомендуется проектировать без вставки т.е. "совмещенными" с расположением стыковых швов поясов в одном сечении с осью симметрии болтового соединения стенки. Величина требуемого зазора в соединении верхнего пояса обеспечивается как правило при заводском изготовлении.
Допускается в отдельных случаях проектировать монтажные блоки главных балок сприрезаемым на монтаже припуском длины верхнего пояса на одном из торцов блока. Прирезка припуска выполняется в этом случае без дополнительного монтажа блока.
Непонятно о чем идет речь? У Вас тема – монтажная сварка? Не видя чертежи трудно оценить правильность записки необходимы чертежи (графическая часть).
При подготовке деталей под сборку и сварку необходимо контролировать:
наличие маркировки и документации подтверждающей приемку полуфабрикатов деталей сборочных единиц и изделий при входном контроле;
наличие маркировки изготовителя материала на деталях подготовленных под сборку сварку;
наличие удаления механическим путем зоны термического влияния в месте термической (огневой) резки заготовок (необходимость должна быть указана в конструкторской или технологической документации);
геометрическую форму обработанных кромок в том числе при подготовке деталей с различной номинальной толщиной стенки;
чистоту (отсутствие визуально наблюдаемых загрязнений пыли продуктов коррозии влаги масла ржавчины) подлежащих сборке сварке кромок и прилегающих к ним поверхностей а также подлежащих неразрушающему контролю участков материала.
При сборке деталей под сварку визуально необходимо контролировать:
правильность установки временных технологических креплений;
правильность сборки и крепления деталей в сборочных приспособлениях;
правильность расположения и количество прихваток и их качество;
чистоту кромок и прилегающих к ним поверхностей деталей.
Измерительный контроль при подготовке деталей под сварку осуществляется для проверки:
размеров разделки кромок (углы скоса кромок толщина и ширина притупления кромок разделки);
ширины зоны механической зачистки наружной и внутренней поверхностей деталей и шероховатости поверхностей кромок и прилегающих поверхностей деталей в том числе места зачистки шва разъема остающейся подкладной пластины (кольца).
Измерительный контроль соединений собранных под сварку включает проверку:
размеров швов приварки временных технологических креплений;
величины зазора в соединении.
размера смещения кромок (внутренних и наружных) собранных деталей;
размеров (длина высота) прихваток и их расположения по длине (периметру) соединения (при необходимости в случае если это оговорено технической документацией также расстояния между соседними прихватками);
размеров ширины зоны нанесения защитного покрытия на поверхностях деталей;
геометрических (линейных) размеров узла собранного под сварку (в случаях оговоренных ПКД).
Объем выборочного контроля качества подготовки и сборки деталей под сварку может быть увеличен или уменьшен в зависимости от требований заказчика.
7 Обоснование выбора оснастки
Швы сварных соединений выполненные на укрупнении и монтаже подлежат контролю по всей длине. Снижение объемов контроля не допускается.
Отклонения размеров сечения швов от проектных не должны превышать величин указанных вГОСТ.
В сварных соединениях обозначенных в проектной документации как "нестандартные" всвязи с применением специальных технологий сварки допускаются отклонения размеров сечения швов от параметров предусмотренных в вышеуказанных стандартах но в пределах допусков указанных в чертежах КМ и ППСР.
При автоматической сварке мы получаем абсолютную защиту сварочной ванны от окружающей среды что дает чистый металл шва без пор и включений. Эта сварка наиболее подходящая для длинных стыковых швов.
Выбор метода контроля
После сварки необходим контроль изделия. Проверяют его геометрические размеры. Также необходимо провести полный осмотр швов визуальным методом. При необходимости проверить ультразвуком 100%.
Визуальный и измерительный контроль сварных соединений выполняется при производстве сварочных работ и на стадии приемосдаточного контроля готовых сварных соединений.
Послойный визуальный контроль в процессе сварки выполняется с целью выявления недопустимых поверхностных дефектов (трещин пор шлаковых включений прожогов свищей усадочных раковин несплавлений грубой чешуйчатости западаний между валиками наплывов) в каждом слое валике шва. Выявленные при контроле дефекты подлежат исправлению перед началом сварки последующего слоя валика шва.
В выполненном сварном соединении визуально следует контролировать:
Отсутствие (наличие) поверхностных трещин всех видов и направлений;
Отсутствие (наличие) на поверхности сварных соединений дефектов: (пор включений скоплений пор и включений отслоений прожогов свищей наплывов усадочных раковин подрезов непроваров брызг расплавленного металла западаний между валиками грубой чешуйчатости а также мест касания сварочной дугой поверхности основного материала);
Качество зачистки металла в местах приварки временных технологических креплений;
Качество зачистки поверхности сварного соединения изделия (сварного шва и прилегающих участков основного металла) под последующий контроль неразрушающими методами (в случае если такой контроль предусмотрен ПТД);
Наличие маркировки (клеймения) шва и правильность ее выполнения.
В выполненном сварном соединении измерениями необходимо контролировать:
- Размеры поверхностных дефектов (поры включения и др.) выявленных при визуальном контроле:
- Высоту и ширину шва а также вогнутость и выпуклость обратной стороны шва в случае доступности обратной стороны шва для контроля;
- Высоту (глубину) углублений между валиками (западания межваликовые) и чешуйчатости поверхности шва;
- Подрезы (глубину и длину) основного металла;
- Отсутствие непроваров (за исключением конструктивных непроваров) с наружной и внутренней стороны шва;
- Размеры катета углового шва;
- Ультразвуковой контроль выполняется в соответствии с требованиями "Правил устройства и безопасной эксплуатации грузоподъемных кранов" ГОСТ 14782 ГОСТ 20415 РД РОСЭК-001-96.
Ультразвуковому методу контроля в равной степени как и рентгенографическому должны подвергаться стыковые сварные соединения несущих (расчетных) элементов металлоконструкций.
Ультразвуковой контроль стыковых сварных соединений несущих (расчетных) элементов металлоконструкций проводится только после устранения дефектов выявленных внешним осмотром.
При этом обязательному контролю подвергают начало и окончание сварных швов стыковых соединений поясов и стенок коробчатых металлоконструкций балок.
При любом методе контроля суммарная длина контролируемых участков сварных соединений устанавливается нормативными документами и должна составлять не менее:
% от длины стыка — на каждом стыке растянутого пояса металлоконструкции;
% от длины стыка — для всех остальных стыковых соединений;
% от длины шва — для других видов сварных соединений указанных в рабочих документах.
Основными задачами контроля качества сборочно-сварочных работ являются:
- обеспечение соблюдения технологии сборочно-сварочных работ и требований нормативной документации;
- своевременное предупреждение и выявление дефектов;
- повышение ответственности непосредственных исполнителей за качество выполняемых работ.
Для выполнения всех требований по обеспечению качества сварных монтажных соединений в строительной организации должен проводиться трехступенчатый контроль качества: входной пооперационный и приемочный.
Результаты контроля фиксируются в исполнительной документации (журналах и актах) составленной по утвержденным формам. В этих документах должны быть отражены результаты наблюдений на всех стадиях входного пооперационного контроля контроля готовых монтажных соединений и контроля конструкции в целом.
Исполнительной документацией по качеству сварных конструкций являются: журналы монтажных работ постановки высокопрочных болтов сварочных работ; проект производства сварочных работ или технологическая инструкция по монтажной сварке; заключения по результатам неразрушающих методов контроля швов(ультразвуковой магнитопорошковый проникающим излучением) с указанием всех обнаруженных дефектов (допустимых и недопустимых); протоколы испытаний технологических проб; протоколы аттестации сварщиков монтажной организации; акты проверки соблюдения технологии монтажной сварки; материалы по выявлению причин появления дефектов швов и т.п.
Для создания сквозной системы контроля за качеством сборочно-сварочных работ строительная организация разрабатывает маркировочную схему в которой присваивается наименование и порядковый номер каждому сварному шву выполненному на монтаже а также наименование порядковый номер швам и плитам прошедшим укрупнительную сборку. Марки швов и элементов принятые в маркировочной схеме едины для записи во всей исполнительной документации. Маркировочную схему разрабатывают на каждое пролетное строение и прикладывают к исполнительной документации.
Укрупненным монтажным блокам одного типа многократно повторяющимся в пролетном строении после укрупнения присваивают марку содержащую в себе тип плит из которых блок укрупнен и порядковый номер в ряду блоков этого типа. Маркировку укрупненных блоков наносят несмываемой краской на крайнее поперечное ребро у его правого конца. При установке укрупненного блока имеющего порядковый номер в пролетное строение на маркировочной схеме в месте установки этого блока ставят его порядковый номер. Плиты не требующие укрупнения или однократно устанавливаемые в пролетном строении маркируют по маркам заводских блоков без присвоения порядкового номера.
В данном курсовом проекте была разработана технология сборки и сварки опорной балки моста через реку. Было подобранно сборочно-сварочное приспособление для сборки и сварке балки. Были выбраны сварочные материалы.
Для сборки балки использовался самоходный портал а для кантовки концевой балки крана применили цепной кантователь для поворота детали.
Для сварки поясных швов использовался автоматический сварочный стенд под слоем флюса.
Для приварки ребер жесткости и подошв использовалась полуавтоматическая сварка в среде защитного газа.
Исправить все грамматические и орфографические ошибки еще раз проверить содержание ссылки на использованную литературу отправьте чертежи (лучше в PDF).
СПИСОК ИСПОЛЬЗОВАННЫХ ИСТОЧНИКОВ
Акулов А.И. Алешин В.П. Ермаков С И. Полевой Г.В. Рыбачук A.M. Чернышов Г.Г. Якушин Б.Ф. Технология и оборудование сварки плавлением и термической резки. - М.: Машиностроение 2003. - 560 с.
Думов С.И. Технология электрической сварки плавлением – Л.: Машиностроение. Ленингр. отд-ние 1987. – 461 с.
Хромченко Ф. Справочное пособие электросварщика – М.: Машиностроение 2005. – 416 с.
Технология сварки металлов и сплавов плавлением. Под ред. акад. Б.Е. Патона М.: Машиностроение 1974. – 768 с.
Стандарт предприятия СТО ИрГТУ. 005-2009. – Иркутск: ИрГТУ 2008.
ГОСТ 14771-76. Дуговая сварка в защитном газе. Соединения сварные. Основные типы конструктивные элементы и размеры.-введ.01.07.1977.-М: Издательство стандартов 1991. - 39 с.
ГОСТ 2246-70. Проволока стальная сварочная. Технические условия. – введ. 01.01.1973.- М: Издательство стандартов 1987. – 28 с.
ГОСТ 380-2005. Межгосударственный стандарт. Сталь углеродистая обыкновенного качества. Марки. - М: Издательство стандартов 2008. – 24 с.
Технология монтажной сварки стальных конструкций мостов. Стандарт предприятия СТП 005-97. – М: Корпорация «ТрасСтрой» 1997. – 67 с.
Методические рекомендации по проектированию опор мостов. Всесоюзное научно-техническое общество железнодорожников и транспортных строителей.: - Ленинград 1988.