Шаровая мельница МШЦ 2100х3000




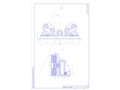
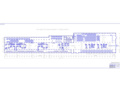
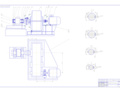
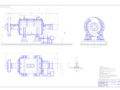
- Добавлен: 25.10.2022
- Размер: 1 MB
- Закачек: 6
Описание
Состав проекта
![]() |
![]() |
![]() ![]() ![]() ![]() |
![]() ![]() ![]() ![]() |
![]() |
![]() ![]() ![]() |
![]() ![]() |
![]() ![]() ![]() |
![]() ![]() ![]() |
![]() ![]() ![]() ![]() |
![]() ![]() ![]() ![]() |
![]() |
![]() ![]() ![]() ![]() |
![]() |
![]() ![]() ![]() |
![]() ![]() ![]() |
![]() ![]() ![]() |
![]() ![]() ![]() ![]() |
![]() ![]() ![]() ![]() |
![]() |
![]() ![]() ![]() |
Дополнительная информация
2 Мельница ВО (2).cdw

3 Привод СБ.cdw

2 Мельница ВО (1).dwg
*-Размер для справок
При сборке (монтаже) необходимо контролировать:
- Боковые зазоры открытой зубчатой передачи. Допустимый боковой зазор между
зубьями - 0.7-1.5 мм.
- Пятно контакта в зацеплении открытой зубчатой пары. По высоте не менее 30%
по длине не менее 40%
- Прилегание поверхностей катания опорных колец к роликам.
Допустимый клиновой зазор не более 0.5 мм.
Смазка подшипников мельницы - густая централизованная
редукторов - жидкая заливная.
При сборке (монтаже) привода и опорных роликов необходимо выполнять все технические
требования к монтажу
указанные в узловых чертежах.
КП 1 1504.04 111 520 01 ВО
1 План.dwg
Выпускаемая продукция: медно-цинковый концентрат
КП 1 1504.04 111 520 01 ВО
ПЛАН ОБОГАТИТЕЛЬНОЙ ФАБРИКИ ( ГЛАВНЫЙ КОРПУС )
1 План.cdw

Выпускаемая продукция: медно-цинковый концентрат
КП 1 1504.04 111 520 01
ПЛАН ОБОГАТИТЕЛЬНОЙ ФАБРИКИ ( ГЛАВНЫЙ КОРПУС )
КП 1 1504.04 111 520 01 ВО
2 Мельница ВО (1).cdw

*-Размер для справок
При сборке (монтаже) необходимо контролировать:
- Боковые зазоры открытой зубчатой передачи. Допустимый боковой зазор между
зубьями - 0.7-1.5 мм.
- Пятно контакта в зацеплении открытой зубчатой пары. По высоте не менее 30%
по длине не менее 40%
- Прилегание поверхностей катания опорных колец к роликам.
Допустимый клиновой зазор не более 0.5 мм.
Смазка подшипников мельницы - густая централизованная
редукторов - жидкая заливная.
При сборке (монтаже) привода и опорных роликов необходимо выполнять все технические
требования к монтажу
указанные в узловых чертежах.
КП 1 1504.04 111 520 01 ВО
2 Мельница ВО (2).frw

Болт М16 х 50 ГОСТ 7798-70
Болт М18 х 60 ГОСТ 7798-70
Болт М16 х 40 ГОСТ 7798-70
Гайка М48 ГОСТ 5915-70
Гайка М16 ГОСТ 5915-70
Гайка М18 ГОСТ 5915-70
Шайба 20 ГОСТ 6402-70
Шайба 48 ГОСТ 3695-72
Шайба 16 ГОСТ 6402-72
Шайба 18 ГОСТ 6402-72
Шпонка 28х16х90 ГОСТ 8789-68
Муфта втулочно-пальцевая
Электрический двигатель
АИР112МВ6 N=4кВт n=1000обмин.
Редуктор 2ЦТ2-100Н u=6.3
2 Мельница ВО (2).dwg
Болт М16 х 50 ГОСТ 7798-70
Болт М18 х 60 ГОСТ 7798-70
Болт М16 х 40 ГОСТ 7798-70
Гайка М48 ГОСТ 5915-70
Гайка М16 ГОСТ 5915-70
Гайка М18 ГОСТ 5915-70
Шайба 20 ГОСТ 6402-70
Шайба 48 ГОСТ 3695-72
Шайба 16 ГОСТ 6402-72
Шайба 18 ГОСТ 6402-72
Шпонка 28х16х90 ГОСТ 8789-68
Муфта втулочно-пальцевая
Электрический двигатель
3 Привод СБ.frw

2 Мельница ВО (1).frw

ПЗ.docx
ФГАОУ ВПО «Уральский федеральный университет
имени первого Президента России Б.Н.Ельцина»
Механико-машиностроительный факультет
Кафедра «Металлургические и роторные машины»
ПЕРЕЧЕНЬ ЛИСТОВ ГРАФИЧЕСКИХ ДОКУМЕНТОВ 4
ТЕХНОЛОГИЧЕСКАЯ ЧАСТЬ 6
1 Краткое описание технологического процесса (ОФ) 6
2 Технологические расчёты 13
КОНСТРУКТОРСКАЯ ЧАСТЬ 17
1 Описание конструкции мельницы 17
2 Литературный обзор 19
3 Конструкторская разработка узлов машины 20
1 Расчёт нагрузок и мощности привода мельницы 21
2 Кинематические расчёты 26
3 Прочностные расчёты основных узлов и деталей машины 31
4 Расчёты унифицированных деталей и узлов машины 37
БИБЛИОГРАФИЧЕСКИЙ СПИСОК 40
СПЕЦИФИКАЦИИ ВЫПОЛНЕННЫХ ЧЕРТЕЖЕЙ
В проекте рассмотрена мельница МШЦ 2100х3000 предназначенная для измельчения рудных материалов. Приведена техническая характеристика.
В конструкторской части приведено описание конструкции машины принцип действия основные узлы конструктивные достоинства и недостатки выявившиеся при эксплуатации. Приведено обоснование выбора конструкции (на основе вопросов надёжности и экономичности).
В расчетной части произведен расчет мощности привода мельницы расчет бандажа мельницы расчет шпонки на смятие и выбор подшипников.
В данном курсовом проекте была произведена модернизация опор мельницы и замена привода. Электродвигатель СДМ 21526-32У4 мощностью данный электродвигатель имел высокую частоту оборотов и большой запас по мощности поэтому была произведена замена его на электродвигатель АИР112МВ6 мощностью имеющий меньшее число оборотов что привело к уменьшению энергозатрат.
Курсовой проект выполнен в объёме 4х листов А1 и пояснительной записки 41 лист.
Перечень листов графических документов
Наименование документа
Обозначение документа
Обогатительная фабрика
КП 1 1504 111 520 01 ВО
Мельница МШЦ 2100х3000
КП 1 1504 111 520 02 ВО
КП 1 1504 111 520 03 СБ
В данной курсовом проекте будет рассмотрена обогатительная фабрика в частности мельница МШЦ 2100х3000 а также её привод и основные узлы.
Шаровая мельница машина для измельчения различных материалов. От дробилок мельницы отличаются более тонким помолом материала (до частиц размерами мельче 5мм).
В качестве мелющих тел в шаровых мельницах используются металлические шары диаметром 30 125 мм заполняющие до 45% объёма барабана.
Мельницы предназначены для сухого и мокрого помола.
Приведём описание и принцип работы данной мельницы с указанием её основных характеристик. Проанализируем её достоинства и недостатки и возможность усовершенствования а также сравним с более современными аналогами. Предоставим расчёты мощности приводов подшипникового узла и некоторых других узлов и деталей.
ТЕХНОЛОГИЧЕСКАЯ ЧАСТЬ
1 Краткое описание технологического процесса обогатительной фабрики
В состав обогатительной фабрики входят: дробильное отделение отделение измельчения и флотации отделение обезвоживания и сушки концентратов участок обжига извести и приготовления известкового молока реагентное отделение участок хвостового хозяйства и очистки промышленных сточных вод.
В дробильном отделении руда доставленная в корпус приема руды в железнодорожных думпкарах выгружается в первичные бункера снабженные решетками с отверстиями 300х300 мм. Рудная пыль выделяемая при выгрузке руды из думпкаров улавливается при помощи циклонов ЦН-15. Рудная пыль уловленная в системе аспирации разгружается на ленточный конвейер № 3 объединяется с рудой и поступает в корпус средне-мелкого дробления. Материал крупностью -300 мм транспортируется при помощи конвейеров в корпус средне-мелкого дробления и подвергается предварительному грохочению на грохоте CVB 1845-3P с выделением готового по крупности продукта -12 мм который поступает во вторичные бункера отделения измельчения и флотации. Рудная пыль выделяемая при транспортировке руды в корпус средне-мелкого дробления улавливается при помощи аспирационной системы пылеуловителем КМП-40. Рудная пыль уловленная пылеуловителем в виде пульпы перекачивается насосами в технологический процесс отделения измельчения и флотации.
Верхний продукт грохочения подвергается дроблению в дробилках среднего и мелкого дробления типа HP-400 с последующим грохочением на грохотах TS 302N. Продробленная руда по системе конвейеров поступает во вторичные бункера отделения измельчения и флотации. Рудная пыль выделяемая при грохочении дроблении и транспортировке в корпусе средне-мелкого дробления улавливается при помощи аспирационной системы в пылеуловителе КМП-71. Рудная пыль уловленная пылеуловителем в виде пульпы перекачивается насосами в технологический процесс отделения измельчения и флотации.
Дробленая руда после корпуса средне-мелкого дробления с помощью разгрузочных тележек на конвейерах № 11 12 пересыпается во вторичные бункера секции измельчения. Рудная пыль выделяемая при разгрузке руды с разгрузочных тележек во вторичные бункера улавливается циклонами марки СИОТ. Уловленная в системах аспирации рудная пыль разгружается во вторичные бункера объединяясь с дробленой рудой.
В отделении измельчения и флотации дробленая руда проходит через четыре технологических процесса: измельчение классификация флотация и мокрая магнитная сепарация. Все технологические процессы в отделении связаны с использованием воды поэтому выделение рудной пыли исключено.
На секциях № 1 2 4 и 5 перерабатывается Волковская руда Сафьяновcкая - «Промсырье» Тарньерская медная руда и конвертерный шлак. На секциях № 6 7 и 8 перерабатывается медно-цинковые руды Сафьяновского и Тарньерского месторождений.
Секции № 1 2 4 и 5 работают по следующей технологической схеме. Руда или конвертерные шлаки из вторичных бункеров посредством тарельчатых питателей и ленточных конвейеров поступает на I стадию измельчения в стержневые мельницы МСЦ 2700х3600. Измельчение ведется в водной среде. Измельченный продукт по системе трубопроводов направляется на II стадию измельчения в шаровые мельницы МШЦ 2700х3600 и далее насосами подается на первую стадию классификации в гидроциклоны ГЦ-500. Слив гидроциклонов первой стадии классификации поступает на межстадиальную флотацию. Пенный продукт межстадиальной флотации является готовым медным концентратом камерный продукт поступает на вторую стадию классификации в гидроциклоны ГЦ-500 для разделения на слив и пески. Пески гидроциклонов второй стадии классификации поступают в шаровые мельницы третьей стадии измельчения с последующим возвратом на вторую стадию классификации. Слив второй стадии классификации направляется в процесс основной медной флотации с последующим обогащением на перечистной медной флотации для получения готового медного концентрата и промпродукта. Хвосты основной флотации подаются на контрольную флотацию. Концентрат контрольной флотации и хвосты перечистной флотации подаются на II стадию классификации. Хвосты контрольной флотации являются отвальными хвостами складируются в Сорьинское хвостохранилище.
Готовый медный концентрат перечистной флотации объединяясь с готовым медным концентратом межстадиальной флотации перекачивается насосами в отделение обезвоживания и сушки концентратов. Процесс флотации ведется в водной среде с использованием флотомашин ФМР-25 и применением следующих реагентов: известковое молоко ксантогенат бутиловый калия флотомасло Т-80 (вспениватель-«Оксаль»).
При обогащении руды Волковского месторождения хвосты контрольной флотации поступают на основную магнитную сепарацию которая осуществляется на магнитных сепараторах ПБМ-ПП 150200. Хвосты основной магнитной сепарации являются отвальными и складируются в хвостохранилище а концентрат основной магнитной сепарации поступает на перечистку после чего концентрат является готовым железным концентратом хвосты перечистки возвращаются в голову основной магнитной сепарации.
На секциях 6 7 8 осуществляется обогащение медно-цинковых руд по коллективно-селективной схеме.
Узлы измельчения секций № 78 однотипны. Дробленая руда поступает в стержневую мельницу МСЦ-2700х3600 на первую стадию измельчения. Разгруз стержневой мельницы поступает на первую стадию классификации в спиральный классификатор 1КСН-20. Слив классификатора вместе с разгрузом второй стадии измельчения (шаровая мельница МШЦ-2700х3600) поступает на вторую стадию классификации (рудные гидроциклоны ГЦ-500). Пески гидроциклонов и спирального классификатора поступают на вторую стадию измельчения. Слив второй стадии классификации подается вместе с разгрузом третьей стадии измельчения в шламовые гидроциклоны ГЦ-500 на III стадию классификации. Пески гидроциклонов поступают в шаровую мельницу МШЦ-2700х3600 на третью стадию измельчения а слив гидроциклонов подается на коллективную флотацию.
Узел измельчения секции № 6: дробленая руда подается на I стадию измельчения в стержневую мельницу (МСЦ-2100х4500). Разгруз стержневой вместе разгрузом II стадии измельчения (шаровая мельница МШЦ-2100х3000) подается на классификацию в гидроциклоны ГЦ-350. Пески гидроциклонов поступают в шаровую мельницу в слив поступает в пульподелитель. Здесь пульпа разделяется на два потока которые поступают в зумпфы слива II стадии классификации секций 78.
При коллективной флотации пульпа с узла измельчения поступает в агитационные чаны КЧР-50 емкостью по 50 м3. В первый чан подается известковое молоко для создания щелочной среды. Во втором чане происходит агитация с медным купоросом после чего пульпа поступает в цикл коллективной флотации. В качестве собирателя используется бутиловый ксантогенат калия.
Основная коллективная флотация состоит из 10-ти флотомашин ФПМ-16 контрольная флотация –из 4-х ФПМ-16.
Концентрат основной коллективной флотации подается на секцию измельчения № 6 где подвергается классификации в гидроциклонах ГЦ-360. Пески поступают на доизмельчение в шаровую мельницу МШЦ-2100х3000 разгруз которой возвращается на классификацию. Слив гидроциклонов подается на перечистку (14 флотомашин ФПМ-32). Хвосты основной коллективной флотации поступают на контрольную флотацию. Хвосты контрольной флотации являются отвальными хвостами и складируются в хвостохранилище.
Концентрат контрольной флотации вместе с хвостами перечистки подается на флотацию промпродуктов (26 флотомашин ФМР-25). Концентрат флотации промпродуктов поступает на доизмельчение вместе с концентратом основной коллективной флотации. Хвосты флотации промпродуктов являются отвальными хвостами и складируются в хвостохранилище.
На разделительную флотацию поступает разгруз сгустителей. В контактном чане КЧР-25 (емкость 25 м3) ведется агитация с сернистым натрием и цинковым купоросом для депрессировки цинковых минералов.
Затем материал поступает на основную флотацию которая ведется при помощи 4-х флотомашин ФПМ-16. Концентрат основной флотации поступает на перечистку ведущуюся флотомашинами (I перечистка – 6 ФПМ-32 – 6 шт.; II перечистка – ФПМ-32 – 2 шт.). Хвосты основной флотации поступают на контрольную флотацию (12 флотомашин ФПМ-16). Хвосты контрольной флотации – готовый цинковый концентрат.
Хвосты I перечистки и концентрат контрольной флотации поступают на классификацию в гидроциклоны секции №6. Пески гидроциклонов поступают в шаровую мельницу МШЦ-2100х3000) и после доизмельчения возвращаются на классификацию. Слив классификации подается в сгустители вместе с коллективным концентратом.
В процессе сгущения и фильтрации медный концентрат из отделения измельчения и флотации поступает в пульподелитель где разделяется на потоки направляемые в радиальные сгустители П-30 с периферическим приводом диаметром 30 м. Слив сгустителей поступает в тюбинг. Разгруз сгустителей (пульпа) с помощью песковых насосов 4"НП подается в чан КЧР-63А из которого с помощью перистальтических насосов VF 80 перекачивается в чаны КЧР-50А корпуса фильтрации медного концентрата. Из чанов пульпа насосами Warman 64 DD-AH подается на пресс-фильтры фирмы Diemme модели ME.1500.3500N. Здесь происходит обезвоживание пульпы до влажности 5-10%. Фильтрат с помощью насосов Warman 32 CC-AH возвращается в сгустители а готовый медный концентрат по ленточному конвейеру поступает в кагат отделения подготовки шихты металлургического цеха.
Вторым вариантом получения обезвоженного медного концентрата является его сушка. В этом случае слив сгустителей поступает в тюбинг разгруз сгустителей с помощью песковых насосов 4"НП подается в пульподелитель в котором разделяется на два дисковых фильтра ДУ-68-25. Фильтрат с помощью насосов возвращается в сгустители а медный концентрат с содержанием влаги 20% по системе ленточных конвейеров поступает в сушильные барабаны. Все перечисленные технологические процессы в отделении кроме сушки медного концентрата связаны с использованием воды поэтому выделение пыли исключено.
Сушка медного концентрата происходит за счёт тепла вносимого в сушильные барабаны горячими (600-700 0С) топочными газами. Воздух необходимый для горения подводится к горелкам через воздухопроводы от вентилятора. Очистка отходящих газов от пыли осуществляется в циклонах марки СИОТ. Уловленная в системах аспирации пыль (пыль медного концентрата) объединяется с просушенным медным концентратом (содержание влаги 10%) и направляется на склад готовой продукции ОФ поэтому данная пыль не учитывается на предприятии в качестве отходов.
Сгущение цинкового концентрата ведется в радиальных сгустителях. Разгруз сгустителей поступает в чан КЧР-63А откуда с помощью насосов подается на фильтрацию на пресс-фильтры ФКМг8030. Фильтрат возвращается в сгустители. Обезвоженный продукт по конвейерам поступает на склад готовой продукции ОФ.
Процесс обжига извести ведется в шахтных печах при температуре 1100-11500 С в зоне обжига. Известняк доставляется железнодорожным транспортом на участок обжига извести и приготовления известкового молока и выгружается в приёмные бункера. Далее по системе конвейеров известняк поступает в бункера складирования известняка откуда при помощи лотковых питателей дозируется и транспортируется на грохочение. При этом выделяется два класса крупности. Известняк крупностью - 40 мм отправляется в металлургический цех где используется в качестве шихты. Класс +40 мм направляется в скиповые бункера откуда при помощи скипов-подъемников подается в шахтные известеобжигательные печи (2 шт.) футерованные огнеупорным шамотным кирпичом. Печь работает на природном газе подаваемом центральной горелкой. Воздух подается при помощи вентилятора. Выгрузка обожженной извести осуществляется при помощи выгрузочного механизма на конвейер. Отходящие газы от обжиговых печей поступают на очистку в групповой циклон типа ЦН-15. Уловленная в циклоне известковая пыль объединяется с обожженной известью после чего готовый продукт отправляется на резервный склад извести.
В процессе приготовления известкового молока обожженная комовая известь дозируется из бункера с помощью вибропитателя на ленточный конвейер. Далее для измельчения подается в шаровую мельницу МШЦ-2100х3000 загруженную шарами диаметром 60 мм. Известковая пыль выделяемая при транспортировке извести (перепады ленточных конвейеров № 12 13) из бункера в шаровые мельницы улавливается при помощи циклонов марки СУОТ. Уловленная в системах аспирации пыль объединяется с обожженной известью и поступает в загруз шаровых мельниц.
В загрузочную горловину мельницы подается вода. После измельчения в шаровой мельнице материал поступает в двухспиральный классификатор 2КСП-12. Пески классификатора поступают в питатель мельницы. Для транспортировки песков подается вода. Слив классификатора насосами 2330 перекачиваются в контактные чаны в которые также может подаваться вода для разбавления известкового молока. Известковое молоко насосами по двум трубопроводам подается в отделение измельчения и флотации обогати-тельной фабрики. Часть извести автомобильным транспортом перевозится на участок хвостового хозяйства для нейтрализации оборотной воды и очистки дебалансовых сточных вод.
Приготовление растворов реагентов применяемых в технологическом процессе обогащения: ксантогената бутилового калия вспенивателя – Оксаль цинкового и медного купороса гидросульфида натрия.
Ксантогенат в металлических барабанах (бочках) вспениватель-Оксаль в специальных емкостях многоразового использования медный и цинковый купорос в мягких контейнерах (бигбегах) доставляются в реагентное отделение автомашиной с центрального склада; гидросульфид натрия – в железнодорожных цистернах.
Водные растворы реагентов готовятся в чанах после чего при помощи насосов перекачиваются в расходные баки расположенные на дозировочных площадках отделения измельчения и флотации. Пыль и аэрозоли выделяемые в процессе загрузки и растворения реагентов улавливаются при помощи пылеуловителя КМП 32 и в виде водного раствора насосами перекачиваются в зумпфы хвостовых насосов отделения измельчения и флотации где объединяются с отвальными хвостами флотации.
Хвостовое хозяйство обогатительной фабрики включает: Сорьинское хвостохранилище систему гидротранспорта и складирования хвостов систему оборотного водоснабжения.
Сорьинское хвостохранилище по способу заполнения – комбинированное предназначено для складирования хвостов обогащения а также для отстаивания и осветления сточных вод. Пыление пляжей хвостохранилища отсутствует так как пляжи поддерживаются во влажном состоянии. Дамбы обвалования сформированные из сухих отвальных хвостов с целью предотвращения пыления отсыпаны слоем гранулированного шлака.
Подача отходов обогащения осуществляется системой гидротранспорта включающей пульпонасосную станцию магистральные и распределительные пульповоды.
Система оборотного водоснабжения (максимальный расход 18864 м3час) предназначена для обеспечения оборотной водой обогатительной фабрики сернокислотного и металлургического цехов.
Забор воды из пруда-отстойника Сорьинского хвостохранилища для оборотного водоснабжения осуществляется двумя водозаборами сифонного типа с последующей подачей в приемный прудок насосной станции оборотного водоснабжения. Сточные воды нейтрализуются известковым молоком приготовленным из технической комовой негашеной извести в емкости-смесителе скреперной установки. Известковое молоко подается в струю сточных вод на входе в приемный прудок где происходит нейтрализация и осветление оборотной воды. Осветленная вода при помощи насосов Д630-90 по двум водоводам подается в основные производственные подразделения.
В соответствии с СанПиН 2.2.12.1.1.1200-03 «Санитарно-защитные зоны и санитарная классификация предприятий сооружений и иных объектов» предприятие относится к I классу опасности (производство по выплавке цветных металлов (меди) непосредственно из руд и концентратов) для которых устанавливается санитарно-защитная зона размером 1000 метров от границы территории промплощадки.
2 Технологические расчёты
Определить размер мельниц и рассчитать необходимое их число для измельчения в две стадии 1 млн. тонн руды в год исходной крупностью -20+0 мм до крупности 72% класса – 0074 мм.
Принятая за эталон руда перерабатывается на действующей фабрике оборудованной мельницами с разгрузкой через решётку МШЦ – 2100*3000. Каждая мельница потребляет мощность 165 кВт и имеет производительность 158 тч при питании рудой крупности -20 + 0 мм и содержании расчётного класса в конечном продукте 72%.
При выполнении расчётов принять следующие данные
R2=1.2 R3=0.50 k=0.8 M=1.6 kи=0.80 C=2 ρ=2.6 тм
В первой стадии измельчения предлагается использовать мельницы с центральной выгрузкой МШЦ.
Для каждой стадии рассмотреть несколько вариантов установки оборудования.
Qг=5 млн.тг dmax=10 мм. и =6 % к =72 %.
Действующая мельница:
dma и.д=6%; к.д. =68 %; Dд=2100; Qд=15.8 тч; Nд=165 кВт; Vд=8.8 м3
Расчёт схемы измельчения
Часовая производительность участка при kв=0.92 kн=1.1 :
Содержание расчётного класса в сливе первой стадии измельчения определим по формуле:
Степень разжижения слива классификатора и пульпы направляемого в автоклавное отделение определяется по формуле
где2 4 – содержимое класса -0040 мм в соответствующих продуктах
Масса песков предварительной классификации определяется по формуле:
Масса твёрдого в сливе предварительной классификации
Q4=Q2 – Q3 =137- 96.7= 40.3 тч
Масса расчётного класса (-0074 мм.):
- в разгрузке мельницы первой стадии измельчения
P2=Q2* 2=137*0.35=48 тч
- в сливе предварительной классификации по формуле
P4=Q4* 4=40.3*0.72=29.016 тч
- в песках предварительной классификации
P3=P2* P4=48-29.016=18.9 тч
Масса твёрдого в циркулирующей нагрузке
Q3=Q3* С=96.7*2=193.4 тч
Масса твёрдого в питании мельницы второй стадии по формуле
Q3=Q5=Q3 *(1+С)=96.7*(1+2)=290.1 тч
Масса твёрдого в сливе поверочной классификации
Содержание класса (-0.040 мм.) в разгрузке мельницы второй стадии измельчения
Содержание расчётного (-0.074 мм) в разгрузке мельницы находится по табл. 4
Параметры пульпы поступающей на предварительную классификацию
- Объём воды Ж2=R2*Q2=1.2*137=164.4 м3ч.
- Объём твёрдого Т2==52.7 м3ч
- Объём пульпы П2= Ж2+ Т2=164.4+52.7=217.1 м3ч
Содержание твёрдого в пульпе
Разжижение пульпы в сливе мельниц второй стадии
Ж5=R5*Q5=1.2*290.1=348.12 м3ч
П5= Ж5+ Т5=348.12+111.5=459.6 м3ч
Полученные численные результаты следует проставить на схеме измельчения
Выбор технологического оборудования
Выбор мельниц для первой стадии измельчения
Расчёт по удельной производительности
Удельная производительность по вновь образованному расчётному классу действующей мельницы
Значение коэффициента kk
гдеm1= 0.87 из табл.5 при крупности (-20 + 0)мм и содержании расчётного класса кд=68%
m2=0.85 при крупности (-20 + 0)мм и содержании расчётного класса 2=35%
Значение коэффициента kD определяется после выбора размера мельницы
КОНСТРУКТОРСКАЯ ЧАСТЬ
1 Описание конструкции мельницы
На рисунке 2.1изображён эскиз мельницы МШЦ 2100х3000.
– питатель правый; 2 – загрузочная часть; 3 – кольцо опорное; 4 – средняя часть; 5 – кольцо опорное с зубчатым венцом; 6 – загрузочная часть; 7 - бутара; 8 – привод барабана; 9 – ролики опорные
Рисунок 2.1 – эскиз мельницы МШЦ 2100х3000.
Техническая характеристика
Диаметр барабана мм 2100
Длина барабана мм 3000
Номинальный объём мельницы м3 85
Частота вращения барабана с-1 04
Производительность тч 10-29
Масса мельницы с электрооборудованием т 48
Максимальная масса мелющих тел т 165
Шаровая мельница МШЦ с центральной разгрузкой предназначены для измельчения медно-молибденовой руды и руд черных и цветных металлов и других рудных материалов на обогатительных фабриках.
Шаровая мельница МШР состоят из цилиндрического барабана закрытого с торцов конусными стенками к которым прикреплены полые цапфы - загрузочная и разгрузочная. Внутренние поверхности барабана имеют сменную облицовку состоящую из броней. Вращение барабана происходит от привода который состоит из электродвигателя приводной шестерни и соединяющей их упругой муфты с промвалом через зубчатый венец закрепленный на фланце разгрузочной цапфы.
Загрузка руды и шаров в барабан происходит через загрузочное устройство расположенное со стороны загрузочной цапфы. Разгрузка осуществляется через бутару прикрепленную к горловине. В бутаре кроме выгрузки происходит сортировка материала. Работа мельниц осуществляется при непрерывной подаче в полость вращающегося барабана руды и воды. Во время вращения барабана мельницы шары перекатываясь скользя и падая измельчают куски руды. Эти мельницы обладают повышенной производительностью и пониженным расходом электроэнергии.
В шаровых мельницах МШР продукт из зарешетного пространства выводится принудительно.
Шаровые мельницы МШР выдают продукт с максимальной крупностью частиц не более 35 меш (05 мм).
Стержневые и шаровые мельницы по своему устройству весьма близки друг к другу и отличаются лишь конструктивным исполнением отдельных узлов вытекающим из назначения машины. Всем им присущи:
высокая производительность и стабильность гранулометрического состава продукта;
надежность в работе и удобство обслуживания;
большая износостойкость футеровки;
низкие эксплуатационные расходы.
Шульгин Юрий Витальевич[UA]; Верич Евгений Дмитриевич[UA]; Федоров Георгий Дмитриевич[UA]
Патентообладатель(и):
Описаниеизобретения:
Изобретение относится к технике измельчения с одновременной сушкой и может быть использовано в промышленности строительных материалов химической энергетической и горно-обогатительной промышленности.
Известная барабанная мельница содержит выполненный с внутренними кольцевыми размольными дорожками цилиндрический корпус установленный с наклоном в сторону его разгрузочного торца размещенные в корпусе не менее двух пар катков каждая из которых установлена на оси параллельной оси корпуса и соединенной с устройствами для прижима катков к размольным дорожкам и привод. В корпусе над катками установлено сбрасывающее измельчаемый материал устройство. Предусмотрены система подачи горячих газов отвода и сепарации пылегазовой смеси определенный способ установки катков определенный криволинейный профиль вторых катков каждой пары по ходу перемещения измельчаемого материала.
3 Модернизация узлов машины
На данной мельнице стоял мощный электрический двигатель и более мощный
редуктор. Барабан представленной мельницы с двух сторон опирался на открытые передачи.
В данном курсовом проекте представлена мельница МШЦ 2100х3000. На данной мельнице производится замена опор барабана мельницы опор привода мельницы и соответственно производится замена самого привода. В представленной работе производится замены опор мельницы. Они заменены на опоры от горизонтального конвертора то есть установка опорных роликов и открытой зубчатой передачи через вал – шестерню на зубчатый венец различия только в том что конвертор поворачивается на определённый угол для слива продукта а мельница вращается постоянно.
Такая замена опор позволила по расчётам поставить более слабый электрический двигатель более маленький редуктор ну и конечно стало меньше шума и больше места.
1 Расчёт нагрузок и мощности привода мельницы
Расчет мощности привода механизма поворота
При повороте мельницы общий момент сопротивления равен сумме опрокидывающих моментов от масс пульпы и мелющих тел порожней мельницы и момента сил трения бандажа по роликам .
Опрокидывающий момент пульпы и мелющих тел определяется контуром футеровки при повороте мельницы.
Согласно методике расчета мощности привода механизма поворота мельницы опрокидывающий момент пульпы и мелющих тел определяется по формуле:
а – Плечо действия силы.
Для определения значения «a» необходимо определить координаты центра тяжести поперечного сечения при этом плечо силы «а» будет определяться значением координаты . Для расчета воспользуемся программой КОМПАС-3D V10 функция «расчет МЦХ плоских фигур».
Расчетная схема к определению представлена на рис.
На рисунке 3.1.1 изображена расчетная схема к определению .
Рисунок 3.1.1 - расчетная схема к определению .
Следующим этапом определим опрокидывающий момент от сил трения бандажа по роликам
Максимальный момент от сил трения определяется по формуле:
где - силы тяжести мельницы и пульпы соответственно Н.
- диаметры бандажа и ролика м.
- угол установки опор относительно вертикальной плоскости ().
- плечо качения которое определяется по формуле:
Е – Модуль упругости (для стали равен 1.75* Н).
b – толщина обода ролика.
=(0.365+0.225)*(+1)*0.74=4.26 МН*м.
Следующий этап расчета состоит в определении опрокидывающего момента от массы порожней мельницы. Для этого необходимо определить координаты центра тяжести печи.
Для начала определим координаты центров тяжести отдельных элементов печи.
Координаты центра тяжести бандажей
=0 м =0 м. Площадь бандажей определяется как площадь кольца и равна 2.63 .
Координаты центра тяжести бочки
=0 м =0 м. Площадь поперечного сечения бочки определяется как площадь кольца и равна 0.13.
Для определения координат центров тяжести и площадей поперечных сечений отдельных узлов и элементов корпуса мельницы воспользуемся компьютерной программой КОМПАС-3D V10 функция «Расчет МЦХ плоских фигур».
Расчетная схема к определению .
Определим координаты центра тяжести фигуры предварительно рассчитав значения параметров и .
Для этого воспользуемся формулами:
Координаты центра тяжести фигуры:
Для расчета воспользуемся формулой:
где - Общий вес мельницы. В данном случае =0.365 МН.
Определим общий опрокидывающий момент для чего воспользуемся формулой:
Из расчета видно что основной составляющей мощности привода является момент создаваемый силами трения бандажей по опорным роликам.
Эквивалентный момент двигателя вычислим по формуле:
где - Время установившегося движения;
- Время пуска и торможения соответственно;
Время работы мельницы при установившемся движении составляет 3600 сек.
Примем время пуска и торможения соответственно равными 10 и 6 секундам. Время всех пауз равным 6.5 мин или 390 сек.
При искусственной вентиляции двигателя числовые коэффициенты в приведенной выше формуле становятся равными 1. Имея в виду вышесказанное вычислим значение эквивалентного момента.
Определим необходимую мощность электродвигателя по формуле:
К.п.д механизма определим как произведение к.п.д редуктора и к.п.д открытой передачи.
N=0.067*0.4*(9550*0.93)=3.02 кВт.
По каталогу выбираем электродвигатель трехфазный асинхронный общего назначения АИР112МВ6 мощностью 4кВт. с числом оборотов в минуту 1000 КПД 82%.
2 Кинематические расчеты.
Этим расчетом определяются передаточные числа редуктора и открытой зубчатой передачи.
Примем n=24 обмин. Определим общее передаточное число механизма.
передаточное число открытой зубчатой передачи принято конструктивно и равняется
Определим необходимое передаточное число редуктора
Для выбора редуктора определим номинальный вращающий момент на валу электродвигателя
=9550*0.85*41000=32.47 Н*м.
По каталогу выбираем 2-х ступенчатый редуктор 2ЦТ2-100Н с передаточным числом =6.3 и номинальным передаваемым моментом 475 Н*м.
Определим фактическое передаточное число механизма а также фактическое число оборотов корпуса мельницы.
=100063=15.87 обмин.
Барабан мельницы рассчитывают как балку лежащую на двух опорах подвергаемую изгибу и кручению.
Крутящий момент на барабане Мкр = Т2 = 382 кН.
Внешней нагрузкой действующей на детали мельницы является масса вращающихся частей центробежная сила вращающихся мелющих тел и размалываемый материал.
Определим центробежную силу массы шаров и материала вращающихся вместе с мельницей по формуле:
Gц=025x(Gш+Gпульпы)=025х225=5625кН
Центробежная сила направлена под углом 25° к горизонтам. Определим горизонтальную и вертикальную составляющие от центробежной силы по формуле:
гдеGu - центробежная сила кН;
Gверт=5625х sin25=2377кН
Gгор=5625xcos 25=5097 кН.
Определим общее усилие в вертикальной плоскости по формуле:
Gверт+ Gобщ=2377+580=60377кН
ГдеGверт - вертикальная составляющая от центробежной силы кН;
Gобщ - общая нагрузка кН;
Определим равнодействующую горизонтальной и вертикальной составляющих по формуле:
гдеGгор - горизонтальная составляющая кН;
- общее усилие в вертикальной плоскости кН;
Шаровая мельница получает вращение от зубчатого венца поэтому на
корпус во время работы действует окружное усилие которое определяется
гдеМкр - крутящий момент кН
где m - модуль зубчатого венца мм;
- угол наклона зубьев;
Схема расположения радиальной и осевой сил представлена на рис.
На рисунке 3.2.1 изображена схема расположения радиальной и осевой сил Fr иF.
Рисунок 3.2.1 - схема расположения радиальной и осевой сил Fr.
Определим радиальную силу Fr на оси X и Y по формуле:
Определим равномерно распределенную нагрузку по длине барабана по формуле:
Определим реакции в опорах:
На рисунок 3.2.2 изображена расчетная схема мельницы МШЦ 2100х3000.
Рисунок 3.2.2 - расчетная схема мельницы МШЦ 2100х3000.
3 Прочностные расчёты основных узлов мельницы
Расчет бандажа производится по основному радиусу r который определяется по формуле:
гдеR – наружный радиус бандажа м.
r – внутренний радиус бандажа м.
Симметричная нагрузка создаваемая измельчаемым материалом и бандажом заменяется на сосредоточенное усилие G. В сечении В действуют параллельная сила перерезывающая сила Q и момент . Перерезывающая сила определяется по формуле:
В конечном итоге расчет сводится к нахождению максимальных эквивалентных напряжений возникающих в любом сечении бандажа и сравнении их с допустимыми.
гдеb h – ширина и толщина бандажа мм.
В нашем случае b=175 мм. h=345 мм. Наружный диаметр бандажа внутренний диаметр бандажа
Определим основной радиус бандажа:
Определим максимальные эквивалентные напряжения:
Допускаемые напряжения для Стали 35Л равны 185 МПа.
Запас прочности n=3 тогда
Условие прочности выполнено.
Расчет на прочность корпуса мельницы
Напряжения и деформации корпуса мельницы вызываются нагрузкой создаваемой массой корпуса футеровки измельчаемым материалом а также инерционными нагрузками.
При расчете корпуса мельницы на прочность воспользуемся рядом допущений:
Нагрузка от массы измельчаемого материала является или осесимметричной или сосредоточенной по вертикальной оси.
Нагрузка создаваемая силами тяжести мельницы распределена вдоль образующей мельницы.
При расчетах корпус мельницы проверяют по напряжениям изгиба тангенциальным и радиальным напряжениям.
Напряжения изгиба найдем по формуле:
гдеG - нагрузка приходящаяся на корпус мельницы. Складывается из собственного веса корпуса веса футеровки веса материала веса пульпы и веса мелющих тел Н;
- наружный диаметр бочки м;
- внутренний диаметр бочки м.
Вес корпуса с футеровкой(вращающаяся часть в сборе с пульпой и мелющими телами) 59 т (см. чертеж).
=59000*9.81=578790 Н.
Наружный диаметр бочки =2.140 м. внутренний диаметр бочки =2.10 м. длина бочки L=3.00 м.
Эксперименты показали что радиальные напряжения распределяются по бочке мельницы неравномерно и максимальные напряжения возникают в ее среднем сечении в нижней точке. Поэтому макс. радиальные и тангенциальные напряжения найдем по формулам которые выведены на основании этих экспериментов.
Определим результирующее напряжение:
По данным А.И.Басова при трехкратном запасе прочности допустимые напряжения корпусов изготовленных из стали 20ХГСА равны 115.0 МПа.
Условие прочности выполняется.
Расчет цилиндрической зубчатой передачи
Тип передачи Нереверсивная
Крутящий момент на шестерне в H*м 38.2
Частота вращения шестерни в обмин 158.7
Номинальное передаточное отношение 10
Срок службы передачи в годах 3
Коэффициент использования передачи в течении года 0.7
Коэффициент использования передачи в течении суток 0.7
Режим работы - Постоянный
Продолжительность включения в % 40
Материал заготовки шестерни - Сталь 40X
Термообработка - Улучшение твердость зуба - 269-302 HB
Материал заготовки колеса - Сталь 40X
Шероховатость поверхности зуба Ra 1.25
Взаимный перекос осей валов передачи в рад 0.0001
РЕЗУЛЬТАТЫ РАСЧЕТА ПЕРЕДАЧИ
ДОПУСКАЕМЫЕ НАПРЯЖЕНИЯ
Продолжительность работы передачи в ч 5151
Суммарное число циклов нагружения зуба шестерни Nc1 4.905E+07
Суммарное число циклов нагружения зуба колеса Nc2 1.226E+07
Коэффициенты эквивалентности для шестерни Khe1=1 Kfe1=1
Коэффициенты эквивалентности для колеса Khe2=1 Kfe2=1
Эквивалентное число циклов нагружения зуба шестерни Ne1 4.905E+07
Эквивалентное число циклов нагружения зуба колеса Ne2 1.226E+07
Базовое число циклов контактного нагружения шестерни Nно1 2.347E+07
Базовое число циклов контактного нагружения колеса Nно2 2.347E+07
Коэффициент учитывающий шероховатость поверхности зуба 1
Коэффициенты окружной скорости Zv1=0.959 Zv2=0.959
Коэффициенты долговечности для шестерни Khl1=1 Kfl1=1
Коэффициенты долговечности для колеса Khl2=1.114 Kfl2=1
Коэффициенты безопасности для шестерни Sh1=1.1 Sf1=1.89
Коэффициенты безопасности для колеса Sh2=1.1 Sf2=1.7
Базовый предел контактной выносливости для шестерни в МПа 641
Базовый предел контактной выносливости для колеса в МПа 641
Базовый предел изгибной выносливости для шестерни в МПа 499.6
Базовый предел изгибной выносливости для колеса в МПа 499.6
Допускаемые контактные напряжения для шестерни в МПа 859
Допускаемые контактные напряжения для колеса в МПа 822.9
Допускаемые контактные напряжения для передачи в МПа 759
Допускаемые напряжения изгиба для шестерни в МПа 564.5
Допускаемые напряжения изгиба для колеса в МПа 593.9
РАСЧЕТНЫЕ НАПРЯЖЕНИЯ
Удельная нормальная жесткость зубьев Н(мм*мкм) 14.918
Допуск на погрешность направления зуба мкм 40
Отклонение положения контактных линий в начальн.периодмкм 20
Коэффициент начального распредел.нагрузки по длине зуба 86.612
Коэффициент учитывающий приработку зубьев Khw 0.466
Коэффициенты распределения нагрузки между зубьями: Kha=1; Kfa=1
Коэффициенты распределения нагрузки по длине зуба: Khb=40.928; Kfb=26.446
Коэффициенты динамической нагрузки в зацеплении: Khv=2; Kfv=3.667
Коэффициенты перегрузки Kh=81.857; Kf=96.968
Коэффициент формы сопряженных поверхностей зубьев Zh 2.421
Коэффициентучитывающий суммарную длину контакт.линийZe 0.914
Коэффициентучитывающий перекрытие зубьев Ye 1
Коэффициенты формы зубьев: Yf1=3.401; Yf2=3.481
Расчетные контактные напряжения в МПа 285.5
Расчетные напряжения изгиба для шестерни в МПа 23.8
Расчетные напряжения изгиба для колеса в МПа 31.1
ГЕОМЕТРИЧЕСКИЕ ПАРАМЕТРЫ ПЕРЕДАЧИ
Межосевое расстояние в мм 1600
Число зубьев шестерни Z1 = 18 колеса Z2 = 180
Фактическое передаточное отношение 10
Угол зацепления 21гр.31'9''
Коэффициент смещения шестерни X1 = 0.5 колеса X2 = 0.537
Коэффициент воспринимаемого смещения 1
Коэффициент уравнительного смещения 0.037
Делительное межосевое расстояние 1584
Диаметр делительной окружности шестерни d1 в мм 288
Диаметр делительной окружности колеса d2 в мм 2880
Диаметр окружности вершин шестерни da1 в мм 334.821
Диаметр окружности вершин колеса da2 в мм 2928.005
Диаметр окружности впадин шестерни df1 в мм 264
Диаметр окружности впадин колеса df2 в мм 2857.184
Ширина венца шестерни в мм bw1= 230 колеса - bw2= 180
Коэффициент торцевого перекрытия 1.492
Окружная скорость в зацеплении в мс 2.39
УСИЛИЯ В ЗАЦЕПЛЕНИИ
Окружная сила в кН 0.265
Радиальная сила в кН 0.105
Расчет выполнен при помощи приложения «АРМКОН – расчеты» к программе «АВТОКАД-2000».
4 Расчёты унифицированных деталей и узлов машины
РАСЧЕТ НА ДОЛГОВЕЧНОСТЬ ПО ДИНАМИЧЕСКОЙ ГРУЗОПОДЬЕМНОСТИ
Роликоподшипник конический однорядный N 7622A
Внутренний диаметр подшипника в мм 110
Радиальная нагрузка в кН 681
Осевая нагрузка в кН 0
Частота вращения в обмин 8
Показатель степени кривой усталости 3.33
Коэффициент безопасности 1.3
Температурный коэффициент 1
Коэффициент вращения 1
Динамическая грузоподъемность в кН 660
Статическая грузоподъемность в кН 600
Эквивалентная динамическая нагрузка в кН 885.3
Коэффициент a1=1 коэффициент a23=1
Эквивалентная статическая нагрузка в кН 681
Долговечность подшипника в часах 783
Расчёт шпоночных соединений
Для соединения вала с деталями передающими вращение широкое применение находят призматические шпонки. Длину шпонки назначают из стандартного ряда принимая её на 5 10 мм меньше ступицы длины. Размеры шпонки в поперечном сечении а также размеры шпоночных пазов на валу и в ступице определяются диаметром вала. В указанных диапазонах длину шпонки следует выбирать из стандартного ряда.
Расчёт призматических шпонок выполняется как проверочный на смятие по формуле
гдеТ – крутящий момент на участке вала со шпоночным пазом Н*м;
t1 – глубина паза на валу;
- допускаемое напряжение смятия.
Для шпонок со скругленными торцами
где - длина шпонки - ширина шпонки.
Для стальных ступиц при реверсивном приводе .
Условие выполняется.
В данном курсовом проекте произведена модернизация опор мельницы МШЦ 2100х3000 : произведена замена электродвигателя более подходящего для данной машины. Все данные изменения производятся для снижения энергосбережения для увеличения работоспособности основных узлов и деталей машин. Были рассчитаны основные технологические и конструкторские показатели и величины: мощность привода мельницы расчет главного вала на прочность расчет шпонок на смятие и выбор подшипников качения.
По результатам проектирования был сделан вывод: электродвигатель СДМ 21526-32У4 мощностью данный электродвигатель имел высокую частоту оборотов и большой запас по мощности поэтому была произведена замена его на электродвигатель АИР112МВ6 мощностью имеющий меньшее число оборотов что привело к уменьшению энергозат
Библиографический список
Кохан Л.С. Сапко А.И. Жук А.Я. и др. Механическое оборудование заводов цветной металлургии. В 3-х частях. Ч.2. Учебник для вузов. М.: Металлургия 1988. 328 с.
Целиков А.И. Полухин П.И. Гребеник В.М. и др. Машины и агрегаты металлургических заводов. В 3-х томах. Т.2. Машины и агрегаты сталеплавильных цехов. Учебник для вузов. 2-е изд. перераб. и доп. – М.: Металлургия 1988. 432 с.
Басов А.И. Механическое оборудование обогатительных фабрик и заводов тяжёлых цветных металлов. – М.: Металлургия 1987. 578 с.
Бейзельман Р.Д. Цыпкин Б.В. Перель Л.Я. Подшипники качения. Справочник. Изд. 6-е перераб. и доп. М.: «Машиностроение» 1975. 572 с. С ил.
Рекомендуемые чертежи
Свободное скачивание на сегодня
- 29.08.2014
- 24.01.2023