Шаровая мельница МШЦ 4500х6000




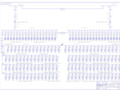
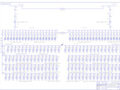
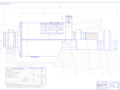
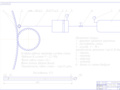
- Добавлен: 25.10.2022
- Размер: 9 MB
- Закачек: 3
Описание
Состав проекта
![]() |
![]() ![]() |
![]() |
![]() ![]() |
![]() ![]() ![]() ![]() |
![]() |
![]() ![]() |
![]() ![]() ![]() ![]() |
![]() ![]() ![]() ![]() |
![]() |
![]() |
![]() ![]() |
![]() ![]() |
![]() ![]() ![]() ![]() |
![]() ![]() |
![]() ![]() ![]() ![]() |
![]() |
![]() ![]() ![]() ![]() |
![]() ![]() ![]() ![]() |
![]() ![]() ![]() ![]() |
![]() |
![]() ![]() ![]() ![]() |
![]() ![]() ![]() ![]() |
![]() ![]() ![]() ![]() |
![]() |
![]() |
![]() ![]() ![]() ![]() |
![]() ![]() ![]() ![]() |
![]() ![]() ![]() ![]() |
![]() ![]() ![]() ![]() |
![]() ![]() ![]() ![]() |
![]() ![]() ![]() ![]() |
![]() ![]() ![]() ![]() |
![]() ![]() ![]() ![]() |
![]() ![]() ![]() ![]() |
![]() ![]() ![]() ![]() |
![]() ![]() |
![]() |
![]() ![]() ![]() |
![]() ![]() |
![]() ![]() |
![]() ![]() |
![]() ![]() |
![]() ![]() |
![]() |
![]() |
![]() ![]() |
![]() ![]() |
![]() ![]() |
![]() ![]() |
![]() ![]() |
![]() ![]() |
![]() ![]() |
![]() ![]() |
![]() ![]() |
Дополнительная информация
4_Параметры_движения_шара.dwg

мельницеи его скорости в момент
Наиболее эффективен удар по нормали к поверхности
футеровки для чего необходимы:
параболическая траектория движения шаров
скорость вращения барабана
крит - скорость при которой шары
переходят с параболической траектории к круговой.
Для мельницы МШЦ 4500х6000
Обозначения на схеме:
Рис. 1 Схема предлагаемого упрочняющего футеровку
режима работы шаровой мельниц
3_Параметры_воздействия_шара.dwg

характеризующие материал пластины.
Для динамических условий
Для стали Гадфильда с твердостью 200
МПа - для статических условий;
МПа - для динамических условий;
Оценка характеристик ударного воздействия
шаров на футеровку в случае работы мельницы
) сферической вмятины
- плотность материала;
- скорость в момент удара; Н
- динамическая твердость материала
пластины(коэффициент пропорциональности между усилием Р
по пластине наносится удар
Д получаемого отпечатка)
6_Графики_для_определения_твердости_и_износостойкости.dwg

от ее твердости при истирании отливок
Увеличение твердости стали
ее стойкость к истиранию в 1
Расчет рациональных параметров упрочняющей
1 Количество ударов по футеровке
с - время между ударами одного и
кр - длина круговой траектории движения шаров).
необходимое для нанесения
двадцатикратного удара
по всей площади футеровки
Повышение износостойкости стали 110Г13Л
5_Определение_твердости.dwg

4 Оценка влияния многократного удара
глубина наклепанного слоя с учетом малой
кривизны мелющих шаров
Расчет величины относительной деформации
увеличения твердости
в результате наклепа
Рис. 2 Зависимость твердости стали 110Г13Л
от величины относительной деформации
7_Время_эксплуатации_между_упрочняющими_обработками.dwg

упрочняющими обработками
Скорость истирания стали Гадфильда
С учетом упрочняющей обработки
повышающей износостойкость в 1
Допустимая толщина наклепанного слоя
подвергаемая истиранию
в течении которого футеровка
мельницы износится на величину
Влияние предлагаемых режимов
работы мельницы на работоспособность
ее основных конструкционных элементов
Рис. 4 Расчетная схема сил
действующих в горизонтальной
и вертикальной плоскости при работе
шаровой мельницы МШЦ 4500х6000
удельные нагрузки на
подшипник в т. А и В (2
МПа) при предлагаемых
режимах упрочняющей обработки не превышают
Профиль сегмента футеровки
после эксплуатации в шаровой мельнице
6_Схема_электроснабжения.dwg

Стержневые мельницы (СД1-6)
Шаровые мельницы (СД7-18)
Гидроциклоны ГЦ-500 (АД103-105)
Дешламаторы (АД7-15)
Ленточные конвейеры (длинные) (АД31-42)
Ленточные конвейеры (короткие) (АД43-45)
Магнитные сепараторы (АД61-72)
Гидроциклоны ГЦ-500 (АД106-108)
Гидроциклоны ГЦ-710 (АД109-120)
Стержневые мельницы (СД31-36)
Шаровые мельницы (СД19-30)
Дешламаторы (АД16-30)
Ленточные конвейеры (длинные) (АД49-60)
Ленточные конвейеры (короткие) (АД46-48)
Ленточные конвейеры (короткие) (АД73-75)
Ленточные конвейеры (короткие) (АД76-78)
Магнитные сепараторы (АД79-90)
Магнитные сепараторы (АД91-102)
Гидроциклоны ГЦ-500 (АД1-6)
4_Параметры_движения_шара.dwg

мельницеи его скорости в момент
Наиболее эффективен удар по нормали к поверхности
футеровки для чего необходимы:
параболическая траектория движения шаров
скорость вращения барабана
крит - скорость при которой шары
переходят с параболической траектории к круговой.
Для мельницы МШЦ 4500х6000
Обозначения на схеме:
Рис. 1 Схема предлагаемого упрочняющего футеровку
режима работы шаровой мельниц
8_Система_подачи_смазки.dwg

- фрагмент зубчатого зацепления;
- рассеиватель смазки;
периодичность заполнения 1 раз в 30 дней
- баллон со сжатым воздухом.
Основные рабочие параметры системы смазки:
время подачи смазки 3
(время полного оборота венца);
периодичность подачи смазки - 1 раз в сутки.
смазки к вал-шестерне
9_Ремонтный_чертеж.dwg

Степень точности по ГОСТ
Толщина зуба по хорде
Измерительная высотадо хорды
Допуск на накопленную
погрешность окружного шага
Допуск на разность окружных
Предельное отклонениеокружного
Допуск на направление зуба
Угол наклона зубьев нацилиндре
Очистить поверхность 1 от смазки промывкой в керосине или
другом растворителе;
Произвести ручную электродуговую наплавку боковой
поверхности зуба 1 электродом диаметром 4 мм;
Закрепить вал-шестерню в трехкулачковом патроне и
произвести фрезерование поверхности до толщины зуба по хорде
Произвести контрольное измерение толщины зуба по хорде
3_Параметры_воздействия_шара.dwg

характеризующие материал пластины.
Для динамических условий
Для стали Гадфильда с твердостью 200
МПа - для статических условий;
МПа - для динамических условий;
Оценка характеристик ударного воздействия
шаров на футеровку в случае работы мельницы
) сферической вмятины
- плотность материала;
- скорость в момент удара; Н
- динамическая твердость материала
пластины(коэффициент пропорциональности между усилием Р
по пластине наносится удар
Д получаемого отпечатка)
6_Графики_для_определения_твердости_и_износостойкости.dwg

от ее твердости при истирании отливок
Увеличение твердости стали
ее стойкость к истиранию в 1
Расчет рациональных параметров упрочняющей
1 Количество ударов по футеровке
с - время между ударами одного и
кр - длина круговой траектории движения шаров).
необходимое для нанесения
двадцатикратного удара
по всей площади футеровки
Повышение износостойкости стали 110Г13Л
1_Сводный_план_карьера.dwg

Шаровая мельница МШЦ 4500
Сводный план карьера
Костомукшского месторождения
Технология обогащения
технологии обогащения
10_Схема_электроснабжения.dwg

Стержневые мельницы (СД1-6)
Шаровые мельницы (СД7-18)
Гидроциклоны ГЦ-500 (АД103-105)
Дешламаторы (АД7-15)
Ленточные конвейеры (длинные) (АД31-42)
Ленточные конвейеры (короткие) (АД43-45)
Магнитные сепараторы (АД61-72)
Гидроциклоны ГЦ-500 (АД106-108)
Гидроциклоны ГЦ-710 (АД109-120)
Стержневые мельницы (СД31-36)
Шаровые мельницы (СД19-30)
Дешламаторы (АД16-30)
Ленточные конвейеры (длинные) (АД49-60)
Ленточные конвейеры (короткие) (АД46-48)
Ленточные конвейеры (короткие) (АД73-75)
Ленточные конвейеры (короткие) (АД76-78)
Магнитные сепараторы (АД79-90)
Магнитные сепараторы (АД91-102)
Гидроциклоны ГЦ-500 (АД1-6)
2_Общий_вид_мельницы.dwg

Внутренний диаметр барабана (без футеровки)
Номинальный рабочий объем барабана
Частота вращения барабана
Электродвигатель привода тип
мельницы (без шаровой загрузкой)
Примечание. Производительность мельницы зависит от физико-механических свойств
крупности исходного материала
принятой схемы измельчения и определяется расчетом.
Техническая характеристика
принятой схемы измельчения и определяется расчетом."
7_Таблица_ТЭП.dwg

Для шаровой мельницы
без упрочняющей обработки
с упрочняющей обработкой
Затраты на приобретение и замену футеровки
одной шаровой мельницы
- стоимость футеровки
- оплата труда персонала осуществляющего
монтаж и демонтаж футеровки
Амортизационные отчисления
(на одну шаровую мельницу)
Затраты электроэнергии на упрочняющие
технико-экономических
ТАБЛИЦА ТЕХНИКО-ЭКОНОМИЧЕСКИХ ПОКАЗАТЕЛЕЙ (на 10 лет)
5_Ремонтный_чертеж.dwg

Степень точности по ГОСТ
Толщина зуба по хорде
Измерительная высотадо хорды
Допуск на накопленную
погрешность окружного шага
Допуск на разность окружных
Предельное отклонениеокружного
Допуск на направление зуба
Угол наклона зубьев нацилиндре
Очистить поверхность 1 от смазки промывкой в керосине или
другом растворителе;
Произвести ручную электродуговую наплавку боковой
поверхности зуба 1 электродом диаметром 4 мм;
Закрепить вал-шестерню в трехкулачковом патроне и
произвести фрезерование поверхности до толщины зуба по хорде
Произвести контрольное измерение толщины зуба по хорде
11_Таблица_ТЭП.dwg

Для шаровой мельницы
без упрочняющей обработки
с упрочняющей обработкой
Затраты на приобретение и замену футеровки
одной шаровой мельницы
- стоимость футеровки
- оплата труда персонала осуществляющего
монтаж и демонтаж футеровки
Амортизационные отчисления
(на одну шаровую мельницу)
Затраты электроэнергии на упрочняющие
технико-экономических
ТАБЛИЦА ТЕХНИКО-ЭКОНОМИЧЕСКИХ ПОКАЗАТЕЛЕЙ (на 10 лет)
4_Система_подачи_смазки.dwg

- фрагмент зубчатого зацепления;
- рассеиватель смазки;
периодичность заполнения 1 раз в 30 дней
- баллон со сжатым воздухом.
Основные рабочие параметры системы смазки:
время подачи смазки 3
(время полного оборота венца);
периодичность подачи смазки - 1 раз в сутки.
смазки к вал-шестерне
3_Увеличение_срока_службы_футеровки.dwg

характеризующие материал пластины.
Для динамических условий
Для стали Гадфильда с твердостью 200
МПа - для статических условий;
МПа - для динамических условий;
2 Определение высоты подъема шара
мельницеи его скорости в момент
Наиболее эффективен удар по нормали к поверхности
футеровки для чего необходимы:
параболическая траектория движения шаров
скорость вращения барабана
крит - скорость при которой шары
переходят с параболической траектории к круговой.
Для мельницы МШЦ 4500х6000
Обозначения на схеме:
Рис. 1 Схема предлагаемого упрочняющего футеровку
режима работы шаровой мельниц
По формулам 1 и 2 определяем
4 Оценка влияния многократного удара
глубина наклепанного слоя с учетом малой
кривизны мелющих шаров
Расчет величины относительной деформации
увеличения твердости
в результате наклепа
Рис. 2 Зависимость твердости стали 110Г13Л
от величины относительной деформации
Рис. 3 Зависимость потери веса стали 110Г13Л
от ее твердости при истирании отливок
Увеличение твердости стали
ее стойкость к истиранию в 1
Расчет рациональных параметров упрочняющей
1 Количество ударов по футеровке
с - время между ударами одного и
кр - длина круговой траектории движения шаров).
необходимое для нанесения
двадцатикратного удара
по всей площади футеровки
Время эксплуатации мельницы между
упрочняющими обработками
Скорость истирания стали Гадфильда
С учетом упрочняющей обработки
повышающей износостойкость в 1
Допустимая толщина наклепанного слоя
подвергаемая истиранию
в течении которого футеровка
мельницы износится на величину
Влияние предлагаемых режимов
работы мельницы на работоспособность
ее основных конструкционных элементов
Рис. 5 Расчетная схема сил
действующих в горизонтальной
и вертикальной плоскости при работе
шаровой мельницы МШЦ 4500х6000
удельные нагрузки на
подшипник в т. А и В (2
МПа) при предлагаемых
режимах упрочняющей обработки не превышают
Оценка характеристик ударного воздействия
шаров на футеровку в случае работы мельницы
) сферической вмятины
- плотность материала;
- скорость в момент удара; Н
- динамическая твердость материала
пластины(коэффициент пропорциональности между усилием Р
по пластине наносится удар
Д получаемого отпечатка)
Повышение износостойкости стали 110Г13Л
Рис.4 Профиль сегмента футеровки
после эксплуатации в шаровой мельнице
5_Определение_твердости.dwg

4 Оценка влияния многократного удара
глубина наклепанного слоя с учетом малой
кривизны мелющих шаров
Расчет величины относительной деформации
увеличения твердости
в результате наклепа
Рис. 2 Зависимость твердости стали 110Г13Л
от величины относительной деформации
7_Время_эксплуатации_между_упрочняющими_обработками.dwg

упрочняющими обработками
Скорость истирания стали Гадфильда
С учетом упрочняющей обработки
повышающей износостойкость в 1
Допустимая толщина наклепанного слоя
подвергаемая истиранию
в течении которого футеровка
мельницы износится на величину
Влияние предлагаемых режимов
работы мельницы на работоспособность
ее основных конструкционных элементов
Рис. 4 Расчетная схема сил
действующих в горизонтальной
и вертикальной плоскости при работе
шаровой мельницы МШЦ 4500х6000
удельные нагрузки на
подшипник в т. А и В (2
МПа) при предлагаемых
режимах упрочняющей обработки не превышают
Профиль сегмента футеровки
после эксплуатации в шаровой мельнице
Диплом_Повышение_износостойкости.doc
Федеральное бюджетное образовательное учреждение высшего профессионального образования
Санкт-Петербургский государственный горный университет
Кафедра конструирования горных машин и технологии машиностроения
Допускается к защите в ГАК
Зав. кафедрой КГМ и ТМ
ПОЯСНИТЕЛЬНАЯ ЗАПИСКА
(должность звание) (подпись) (Ф.И.О.)
Зав. кафедрой КГМ и ТМ
«__» февраля 2011 г.
ЗАДАНИЕ НА ПРОЕКТИРОВАНИЕ
Студенту Бочкову В.С. уч. группы ГМэ-06
рассчитать систему смазки для увеличения срока службы вал-шестерни.
Тема специальной части: увеличение срока службы футеровки и вал-шестерни шаровой мельницы.
Требования к графической части проекта и пояснительной записке содержится в методических указаниях по проектированию.
В представленном дипломном проекте разработан способ увеличения срока службы футеровки шаровой мельницы МШЦ 4500×6000 путем ее эффективного наклепа в процессе работы мельницы в предлагаемом режиме. Рассчитаны основные параметры упрочняющего режима: скорость вращения барабана коэффициент загрузки шаровой мельницы скорость шара в момент удара о футеровку. Оценено влияние упрочняющего режима на износостойкость футеровки.
Рассмотрена возможность увеличения срока службы зубчатого зацепления (вал-шестерня – венец) используемого в приводе шаровой мельницы рассчитана система подачи смазки на зубчатое зацепление (вал-шестерня – венец). Рассчитаны основные рабочие параметры системы смазки: объем смазочного материала наносимого на зубчатое зацепление за один впрыск расход смазки и давление в системе.
Дипломный проект состоит из пояснительной записки и комплекта чертежей поясняющих материал рассмотренный в записке.
Пояснительная записка состоит из следующих разделов: горная часть специальная часть технологическая часть электрическая часть охрана труда охрана окружающей среды и экономическая часть.
Пояснительная записка состоит из 111 страниц 22 таблицы и 18 рисунков.
In the present capstone project developed a method for increasing the life of the lining of ball mill MSC 4500×6000 through efficient hardening in the process of working mills in the proposed regime. Calculate the main parameters of the hardening regime: the drum rotation speed load factor ball mill the speed of the ball at impact on the lining. The effect of hardening the regime to wear lining.
To extend the life of the gear (shaft-gear - the crown) used in the drive drum ball mill a system designed lubrication on gearing (pinion shaft - the crown). Calculate the main operating parameters of the lubrication system: amount of lubricant deposited on the gearing in one injection flow lubrication and system pressure.
Thesis project consists of explanatory notes and a set of drawings illustrating the material discussed in the note.
The explanatory note contains the following sections: the mountainous area the special part the technological part electrical part the economic part.
Explanatory memorandum consists of 111 pages 22 tables and 18 figures.
ГЛАВА 1 ГОРНАЯ ЧАСТЬ8
1 Геологическая характеристика месторождения8
2 Современное состояние горных работ в карьере9
3 Границы карьера I очереди10
4 Производительность и режим работы карьера.11
5 Механизация производственных процессов.12
5.1 Буровые работы12
5.2 Автоматизация буровых работ13
5.3 Взрывные работы14
5.4 Погрузочные работы15
6 Технологический транспорт15
6.1 Современное состояние15
6.2 Транспортная система и этапы ее развития15
6.3 Технологические грузопотоки16
6.4 Автомобильный транспорт18
6.5 Характеристика автомобильных дорог в карьере18
6.6 Железнодорожный транспорт19
7 Отвальное хозяйство20
7.1 Общая характеристика отвалов20
7.2 Автомобильные отвалы21
7.3 Железнодорожный отвал22
9 Технологическое оборудование и организация работ на участке измельчения25
9.1 Организация работ на участке26
9.2 Основное и вспомогательное технологическое оборудование участка28
ГЛАВА 2 СПЕЦИАЛЬНАЯ ЧАСТЬ29
1 Увеличение срока службы футеровки29
1.1 Аналитический обзор29
1.1.1 Сталь Гадфильда и ее стойкость к износу29
1.1.2 Теоретические основы упрочнения стали наклепом29
1.1.3 Основные виды изнашивания материалов30
1.1.4 Установление вида износа футеровки шаровых мельниц35
1.1.5 Шаровые барабанные мельницы35
1.1.6. Обзор возможных способов упрочнения футеровок шаровых мельниц43
2.2 Разработка способа упрочнения футеровок шаровой мельницы в процессе ее работы45
2.2.1 Определение параметров ударного воздействия шара на футеровочную плиту45
2.2.2 Определение твердости и износостойкости стали после упрочняющей обработки47
2.2.3 Расчет времени предлагаемой упрочняющей обработки48
2.2.4 Определение допустимого времени эксплуатации шаровой мельницы между упрочняющими наклепами49
2.2.5 Увеличение срока эксплуатации футеровочных плит в результате упрочняющей обработки49
2.2.6 Увеличение срока эксплуатации футеровочных плит в результате упрочняющей обработки49
2.2.7 Влияние предлагаемых режимов работы мельницы на работоспособность ее основных конструктивных элементов50
2 Увеличение срока службы вал-шестерни57
2.1 Постановка задачи57
2.2 Определение необходимого расхода смазки58
2.3 Определения давления на смазку на выходе из отверстий рассеивателя59
ГЛАВА 3 ТЕХНОЛОГИЯ РЕМОНТА ВАЛ-ШЕСТЕРНИ60
1 Химический состав и механический свойства материала изготовления вал-шестерни60
2 Определение критического износа зубьев вал-шестерни61
3 Порядок восстановления зубьев вал-шестерни61
4 Подготовка вал-шестерни к технологическим операциям61
5 Параметры ручной электродуговой наплавки63
5.1 Выбор диаметра dэ электрода63
5.2 Расчет массы наплавленного металла и количество необходимых для наплавки электродов63
5.3 Установление силы наплавочного тока основного времени наплавки эффективной мощности дуги64
5.4 Выбор сварочного аппарата65
5.5 Выбор подходящей марки электрода66
6 Параметры фрезерования66
ГЛАВА 4. ЭЛЕКТРИЧЕСКАЯ ЧАСТЬ69
1 Определение типа и мощности трансформатора для гпп69
2 Выбор типа и сечения высоковольтного кабеля70
3 Выбор типа и сечения фидерного кабеля71
4 Выбор типа и сечения кабеля подводимого к шаровым и стержневым мельницам72
4.1 Выбор сечения кабеля для стержневой мельницы мсц 3600×550072
4.2 Выбор сечения кабеля для шаровой мельницы мШц 4500×600072
5 Определение типа и мощности трансформатора для низковольтной линии73
6 Выбор типа и сечения шины74
7 Выбор типа и сечения кабеля подводимого к низковольтным электроприемникам75
7.1 Выбор сечения гибкого кабеля для конвейера ленточного (длинного)75
7.2 Выбор сечения гибкого кабеля для конвейера ленточного (короткого)75
7.3 Выбор сечения гибкого кабеля для магнитного сепаратора ПБМ-ПП-90-25076
7.4 Выбор сечения гибкого кабеля для гидроциклона гц-50076
7.5 Выбор сечения гибкого кабеля для гидроциклона гц-71076
7.6 Выбор сечения гибкого кабеля магнитного дешламатора мд-977
8 Проверка сети по потере напряжения77
8.1 Потеря напряжения в высоковольтном кабеле78
8.2 Потеря напряжения в фидерном кабеле78
8.3 Потеря напряжения в трансформаторе трдцн-80000110-у178
8.4 Потеря напряжения в трансформаторе ТМ 630035-678
8.5 Потеря напряжения в кабеле наиболее мощного электроприемника высоковольтной линии79
8.6 Потеря напряжения на шине низковольтной линии79
8.7 Потеря напряжения в гибком кабеле наиболее мощного электроприемника низковольтной линии79
8.8 Суммарные потери напряжения79
Проверка сети в режиме пуска79
Расчет величины токов короткого замыкания80
Выбор коммутационных аппаратов81
ГЛАВА 5 ОХРАНА ТРУДА82
1 Вредные и опасные факторы на обогатительной фабрике82
2 Анализ травматизма и профессиональной заболеваемости83
3 Мероприятия по соблюдению безопасности работ84
3.1 Рабочие площадки и проходы84
3.2 Лестницы наклонные проходы и полы производственных помещений85
3.3 Пусковые устройства85
3.4 Электробезопасность86
4 Мероприятия по снижению пылевыделений87
5 Производственная санитария88
5.1 Мероприятия по снижению производственного шума и вибрации88
5.2 Освещенность производственных помещений88
5.3 Вентиляция и отопление производственных помещений90
5.4 Средства индивидуальной защиты90
6 Пожарная безопасность90
7 Мероприятия по предотвращению чрезвычайных ситуаций и ликвидации последствий91
ГЛАВА 6 ОХРАНА ОКРУЖАЮЩЕЙ СРЕДЫ94
1 Экологическая характеристика региона94
1.2 Поверхностные и подземные воды94
1.3 Рельеф и почвы95
1.4 Растительность и животный мир95
2.1 Охрана атмосферного воздуха96
2.3 Контроль загрязнения воздушного бассейна в зоне техногенного воздействия комбината и в санитарно-защитной зоне города Костомукши97
2.4 Охрана поверхностных водоёмов97
2.5 Складирование и утилизация отходов производства98
3 Планирование и отчётность98
3.1 Планирование в области охраны окружающей среды98
ГЛАВА 7 ЭКОНОМИЧЕСКАЯ ЧАСТЬ102
1 Капитальные затраты102
1.1 Определение затрат на заработную плату персоналу осуществляющему монтаж и демонтаж футеровки шаровой мельницы102
2 Расчет себестоимости по амортизации104
СПИСОК ИСПОЛЬЗОВАННОЙ ЛИТЕРАТУРЫ107
Шаровые мельницы широко применяются на горно-обогатительных предприятиях для измельчения полезных ископаемых. Процесс измельчения один из наиболее энергоемких и металлоемких процессов на обогатительных предприятиях поэтому совершенствование технологии работы шаровых мельниц имеет важное научное и практическое значение.
Во время эксплуатации шаровых мельниц футеровка контактирующая с породой подвергается значительному износу вследствие чего она быстро выходит из строя. Поскольку футеровочные плины достигают массы 250 кг замена футеровки представляет собой длительный энергоемкий процесс. По этой причине продление срока работы футеровки является важной практической задачей.
В специальной части настоящего дипломного проекта анализируется влияние наклепа на износостойкость стали Гадфильда при различных видах износа (абразивном ударно-абразивном и при контактной усталости). Рассматривается возможность эффективного наклепа футеровки из стали 110Г13Л в случае работы шаровой мельницы без породы и бомбардировки мелющими телами непосредственно футеровочной плиты. Устанавливаются рациональные параметры работы мельницы для осуществления эффективного наклепа. Проводится проверка работоспособности основных конструктивных элементов шаровой мельницы при её работе в предлагаемом режиме.
Рассмотрена возможность увеличения срока службы зубчатого зацепления используемого в приводе шаровой мельницы за счет применения системы подачи смазки. Для этого были установлены основные параметры системы подачи смазки: объем смазочного материала наносимого на зубчатое зацепление за один впрыск расход смазки давление в системе.
ГЛАВА 1 ГОРНАЯ ЧАСТЬ
1 Геологическая характеристика месторождения
Костомукшское месторождение (ДП.060955.001) на базе которого осуществлено строительство Костомукшского горно-обогатительного комбината крупнейшее по запасам железистых кварцитов на Северо-Западе России. Месторождение относится к нижнепротерозойскому комплексу представленному рудными кварцитами кристаллическими сланцами различного состава и плагиопорфирами (геллифлинтами). В плане месторождение имеет форму дуги протяженностью 145км обращенной выпуклой стороной на юго-запад. Месторождение разведано до глубины 600 метров. Запасы магнетитовых руд составляют около 115 млрд.т. По простиранию месторождение делится условно на 4 участка: Северный-1 Северный-2 Центральный и Южный.
По горнотехническим условиям наиболее благоприятным является Центральный участок где сосредоточено примерно 70% всех запасов месторождения а мощность рудного тела в среднем достигает 280м (на других участках она изменяется от 40 до 80м). На Центральном участке незначительная мощность рыхлых отложений - в среднем 8м сравнительно низка заболоченность. Среднее содержание основных и вредных компонентов в руде: магнетитового железа - 2645% общего железа - 3221% серы - 020% фосфора - 007%. Качество руды изменчиво как в пределах рудных тел так и участков залежей горизонтов месторождения. Содержание магнетитового железа варьируется от 17 (бортовое) до 38-40%. В основном руды легко измельчаются легкообогатимы. Постоянной и характерной примесью в рудах является пирротин. Повышенное содержание серы в концентратах определяется наличием пирротина в кварцитах. Забалансовые руды с содержанием магнетитового железа 17-10%.
Физико-механические свойства горных пород Костомукшского месторождения представлены в табл. 1.1.
Физико-механические свойства железных руд и пород
Вмещающие скальные породы:
Центральный карьер Костомукшского рудника достиг отметки -65 метр. При этом возросла крепость породы до 17 по проф. М.М.Протодьяконову. Как следствие увеличились аварийные простои экскаваторов ЭКГ-10 из-за неисправностей поворотной платформы т.к. условия эксплуатации крайне усложнились. Крупность породы в забоях возросла вместе с нагрузкой на экскаватор.
2 Современное состояние горных работ в карьере
В настоящее время в качестве отправной точки для проектирования принято фактическое состояние горных работ на карьере на 01.01.1998г.
В 1997 году производительность карьера по руде составила 1693 млн.т. по вскрыше 897 млн.м3. Содержание в сырой руде Fe общ. - 3047% Fe магн. - 2569%. Обеспеченность карьера готовыми к выемке запасами руды составила 28 месяца. Недовыполнение предусмотренных годовой программой объемов добычных и вскрышных работ на 30% и 40% соответственно объясняется нестабильностью финансового положения и неплатежеспособностью потребителей товарной продукции в частности Череповецкого металлургического комбината.
В настоящее время горные работы ведутся на изолированных друг от друга Центральном и Южном участках с отметками дна +40м и +115м соответственно. Погрузка горной массы в забоях осуществляется исключительно в автосамосвалы. Вскрыша с Южного участка и большая часть вскрыши с Центрального участка автосамосвалами г.п 110т доставляется до отвалов. Руда и небольшая часть вскрыши перегружается в жд транспорт на экскаваторных складах расположенных на отметках 205 175 145м в 1997году подготовлены места для сооружения двух перегрузочных складов на отметке 151м восточного борта.
3 Границы карьера I очереди
В настоящее время границы открытых горных работ на Костомукшском месторождении в целом не пересматриваются. Однако с целью стабилизации текущего коэффициента вскрыши в ближайшие 20-25 лет на возможно более низком уровне выделен карьер I очереди. В границы этого карьера вошла большая часть запасов Центрального и Южного участков месторождения.
Из первоначальной разработки исключена северная часть Центрального участка карьера с наибольшим коэффициентом вскрыши с последующей отработкой ее в период затухания вскрышных работ а так же запасы малых рудных тел за исключением участков №№ 12345 последние характеризуются легкообогатимыми разновидностями руды и намечаются к разработке в два этапа - в границы I очереди включены запасы при отработке которых коэффициент вскрыши не превышает такового для запасов основной залежи в соответствующие периоды работы.
В соответствии с новыми данными по углам устойчивости бортов и уступов и принятой схемой вскрытия откорректированы границы карьера по основной залежи Центрального (в пределах I очереди ) и Южного участков. При этом очертания конечных бортов со стороны висячего бока основной залежи носят несколько условный характер поскольку верхние горизонты этих бортов начнут разноситься по мере сокращения рудных площадей I очереди карьера для вовлечения в разработку запасов малых рудных тел в целях под держания мощности комбината.
При оконтуривании Центрального участка с целью сокращения коэффициента вскрыши для отработки нижнего по глубине яруса высотой 90м предусмотрена предложенная ИГД технология отработки горизонтов карьера округлой формы с постепенной засыпкой отработанной части вскрышными породами при продвижении фронта горных работ по простиранию залежи. В зоне действия этой технологии борт укручается на 2-7° относительно вышерасположенных участков борта что достигается укручением самого нижнего 45-метрового уступа настолько сколько требуется для достижения максимально допустимого значения устойчивого угла погашения нижней 90-метровой части борта ( но не круче 75°) что возможно в связи с относительно малой продолжительностью его состояния без засыпки (до 1-15 лет).
На Южном участке с целью укручения конечных бортов карьера предусмотрено использование участков выработанного пространства для размещения транспортных коммуникаций на насыпном грунте взамен размещения их в конечных бортах. Предусмотрена засыпка участка №1 вскрышными породами от дна (отм.+10м) до гор.+70м где устраиваются экскаваторные перегрузочные пункты. После отработки карьера на участке №3 вскрытого в основном со стороны карьера основного рудного тела Южного участка ( дно на отметке +70м) в его выработанном пространстве на насыпном грунте укладывается система автосъездов с отметки +40м после чего опять формируется до отметки -35м на насыпном грунте в ранее выработанном пространстве западного торца Южного участка.
Аналогично предыдущему проекту в эксплуатационные запасы включены 50% балансовых запасов категории С2.
Показатели характеризующие геометрию выработанного пространства эксплуатационные запасы полезного ископаемого ( учетом потерь и засорения ) и объемы вскрыши в границах карьера I очереди приведены в табл. 1.2.
Показатели по карьеру I очереди.
Эксплуатационные запасы
Запасы забалансовой руды
4 Производительность и режим работы карьера.
Расчетная производительность Костомукшского карьера по сырой руде составляет 240 млн. тгод.
В границах карьера I очереди эта производительность обеспечивается одновременной разработкой Центрального (150млн. т) и Южного (90млн.т.) участков месторождения. Установленная в процессе календарного планирования расчетная производительность карьера по вскрыше составляет 220млн.м3 в том числе 130млн.м3 на Центральном и 90млн.м3 на Южном участках.
Годовая добыча 840млн.т. выдерживается до 2010года включительно затем уменьшается по мере доработки запасов Южного участка. К этому времени для поддержания расчетного уровня добычи предполагается подготовка и вовлечение в разработку рудных площадей за пределами I очереди карьера - северной части Центрального участка и малых рудных тел обоих участков.
Годовой объем вскрышных работ в границах карьера I очереди и размере 220млн.м3 выдерживается до 2009года с последующим уменьшением в связи с резким затуханием вскрышных работ на Южном участке при доработке глубинных горизонтов. Однако с учетом необходимости своевременного вовлечения в разработку запасов руды за пределами границ карьера I очереди характеризующихся повышенным коэффициентом вскрыши следует ожидать за пределами 2009года увеличения годовых объемов вскрышных работ.
5 Механизация производственных процессов.
Руды и вмещающие скальные породы Костомукшского месторождения подлежат буровому рыхлению. Проектом предусматривается применение на основном бурении шарошечных станков типа СБШ-250МНА-32 уже освоенных Костомукшским карьером. Режим буровых работ двухсменный по непрерывной рабочей неделе. Ниже приводится расчет годового объема буровых работ (табл. 1.3). Продолжительность смены -12 часов.
Расчет буровых работ
Наименование показателей
Рекомендация комбината
Производительность бурового станка
Списочный парк станков
Из имеющегося на сегодня парка станков СБШ-250-МНА-32 в количестве 20к концу 1998 года на замену изношенных потребуется приобрести 15и до 2003 года еще раз заменить все 20 станков. Кроме того для увеличения парка станков до расчетного необходимо приобрести еще 11 станков.
Для выполнения работ по вспомогательному бурению принимается 3 станка типа СБУ-100ГА-50.
Кроме того для проходки отрезной щели при заоткоске конечных и полустационарных бортов карьера предусматривается буровой станок типа КГА-1100 фирмы Тамрок.
5.2 Автоматизация буровых работ
Существующий парк буровых станков применяемых на Костомукшском карьере недостаточно оснащен средствами измерения и контроля процесса бурения. Для улучшения показателей бурения и обеспечения оперативной корректировки параметров режима в сложных условиях проходки скважины рекомендуется система автоматизированного регулирования процесса бурения "Режим - 2 НМ
Система обеспечивает регулирование осевого усилия и частоты вращения бурового инструмента а так же работу в ограниченных режимах при возникновении недопустимых перегрузок двигателя механизма вращения вибрации бурового става и при зашламовывании буровой скважины.
Схема функционирует следующим образом: электронный сигнал снимаемый с датчика скорости бурения ДС поступает на нелинейный преобразователь НП и масштабный блок МБ1. Преобразованный сигнал с преобразователя НП подается на вход усилителя У1 регулятора осевой нагрузки а с масштабного блока МБ1 - на вход регулятора частоты вращения. При уменьшении скорости бурения соответственно уменьшаются выходные сигналы НП и МБ1. Это приводит к увеличению выходного сигнала усилителя У1 и к уменьшению выходного сигнала промежуточного масштабного усилителя ПМУ. При этом осевое усиление на забой увеличивается а частота вращения бурового инструмента уменьшается.
Кроме регулирования параметров режима бурения система осуществляет их ограничение при недопустимых перегрузке двигателя вращателя и вибрациях станка а также при зашламовывании скважины.
В случае увеличения вибрации бурового става сверх допустимых срабатывает датчик вибрации ДВЦ сигнал которого поступает на ПМУ. В результате частота вращения бурового става снижается и вибрация уменьшается.
Эффект этой системы состоит в том что она обеспечивает повышение скорости проходки на 20 - 40% при снижении удельной энергоемкости на 20-50% и соответствующее снижение себестоимости бурения на 10-15%.
В качестве взрывчатых веществ для взрывания скважин проектом рекомендуются граммонит 7921В для сухих скважин (35%) ГЛВВ и гранулотол для обводненных скважин (65%) для вспомогательных работ - аммонит - 6ЖВ.
Применяется многорядное короткозамедленное взрывание. Удельный и годовой расход взрывчатых материалов приводится в табл. 1.4.
Расход взрывчатых материалов
Объем взрываемой горной массы
по рекомендации комбината
Подготовку и осуществление массовых взрывов предусматривается производить один раз в неделю со средней мощностью 620т взрывчатых веществ (ВВ).
Парк забоечных и зарядных машин по сравнению с предыдущим проектом остается без изменений - 5 забоечных машин типа ЗС-1М и 4 зарядные машины типа МЗ-4А 2 пгг - Акватол IV.
Общая емкость существующего базисного склада расположенного в 15км к юго-западу от карьера составляет 2340т что обеспечивает хранение запаса ВВ на один месяц. На территории непосредственно примыкающей к базисному складу имеется расходный склад взрывчатых материалов (ВМ) и пункт загрузки зарядных машин. Расход ВМ представлен в таблице 4. Для механизации погрузочно-разгрузочных работ на складах ВМ проектом 1994года предусмотрено применение 5 аккумуляторных погрузчиков типа ЭПВ-125.
5.4 Погрузочные работы
В 2010 году годовой объем разрабатываемой горной массы представленной рудой и скальными вскрышными породами составляет 293млн.м3. Из них 70млн.м3 подлежат экскаваторной перегрузке с автомобильного на железнодорожный транспорт.
6 Технологический транспорт
6.1 Современное состояние
В настоящее время Костомукшский карьер отрабатывается с использованием автомобильного и железнодорожного транспорта.
На доставке руды на обогатительную фабрику применяется комбинированная схема транспорта: руда автосамосвалами транспортируется на перегрузочные склады в карьере на отметках 175м и 145м. откуда железнодорожным транспортом подается на фабрику. Порода из карьера вывозится в отвалы автосамосвалами БелАЗ 7519 и Катерпиллар. грузоподъемностью 110т и 130т. так и по комбинированной схеме с перегрузкой на железнодорожный транспорт.
Технологическим автомобильным транспортом в 2010году было перевезено 424млн.т. горной массы в том числе руды 169млн.т породы 243млн.т при средневзвешенном расстоянии транспортирования 27км.
Объем перевозок железнодорожным транспортом составил 231млн.т в том числе тяговыми агрегатами перевезено 55млн.т тепловозами 176млн.т. Средневзвешенное расстояние транспортирования составило 59км.
По состоянию на конец октября 2010года на комбинате имелся следующий
парк основного технологического оборудования:
автосамосвалы БелАЗ-7519
тяговые агрегаты ОПЭ-1А
бульдозеры ДЗ-94С (Т-330)
бульдозеры ДЗ-118 (ДЭТ-250)
бульдозеры на тракторе Т-500
6.2 Транспортная система и этапы ее развития
Планируется сформировать независимую систему вскрывающих выработок с перешейка по борту Южного участка карьера с постепенным увеличением объемов горной массы перевозимых по жд путям выходящим на поверхность и уложенным в этих выработках. Транспортная система на поверхности формируется с учетом изменений внутрикарьерной транспортной системы и объемов перевозок. В первую очередь необходимо выполнить: в реконструкцию ст. Карьерная;
■завершить строительство двухпутного перегона ст. Карьерная - ст.Отвальная;
■построить ст. Отвальная;
■построить отвальные тупики на Восточном ж.д. отвале;
■построить ж.д. путь до железнодорожного склада геллифлинтов;
■построить приемный тупик на складе геллифлинтов в соответствии с рабочей документацией;
■построить двухпутный перегон по борту Южного участка;
■построить двухпутный перегон от траншеи Южного участка до ст.Отвальная;
■построить участок пути от ст. Отвальная и отвальный тупик на складе забалансовых руд;
■построить ж.д. путь от траншеи Южного участка до ст. Рудная в т.ч. путепровод на пересечении этого пути с путями ст. Карьерная - ст.Отвальная;
■построить автомобильную дорогу на автомобильный отвал Западный II.
6.3 Технологические грузопотоки
В рассматриваемые периоды отработка карьера будет производиться с применением на доставке горной массы к конечным пунктам: автомобильного железнодорожного автомобильно-железнодорожного видов транспорта.
Предпочтение будет отдаваться комбинированным схемам транспорта как наиболее экономичным в условиях Костомукшского карьера. Так как геометрия карьера не позволяет без значительных дополнительных затрат обеспечить глубокий ввод железнодорожного транспорта до забоев.
В 2010году в эксплуатации будут находиться 4 перегрузочных склада (один двусторонний) с автомобильного на железнодорожный транспорт и два перегрузочных склада (без аккумулирующих емкостей); один - с автомобильного на конвейерный транспорт; второй - с конвейерного на железнодорожный транспорт. С этих складов горная масса железнодорожным транспортом будет доставляться до конечных пунктов (отвалы склад фабрика). Кроме того часть породы (в том числе геллифлинты и забалансовая руда) будет перевозиться автомобильным и железнодорожным транспортом минуя перегрузочные склады. Последним видом транспорта будет перевозиться из забоев до фабрики и часть руды. Горная масса будет приниматься на следующих конечных пунктах транспортировки: фабрика (руда); Восточный автомобильный отвал (пустая порода геллифлинты забалансовая руда); Восточный железнодорожный отвал (пустая порода забалансовая руда); ДШУ с временным автомобильным складом (геллифлинты) временный железнодорожный склад геллифлинтов.
На Центральном участке руда в объеме 10 млн.т. с нижних горизонтов подается автотранспортом до концентрационного горизонта с отм. 0м где перегружается в конвейерный транспорт с последующей перегрузкой ее в железнодорожные составы на гор. 100м откуда они следуют со ст. "100м" через ст. "130м" траншею Центрального участка ст. Карьерная ст. Рудная фабрика. Часть руды с нижних горизонтов (29 млн.т.) доставляется автотранспортом на склад с отм.гор. 100м где перегружается в железнодорожный транспорт и далее через ст. "100м" маршрут следования аналогичен маршруту для руды направляемой с конвейерного подъемника. Кроме того 13 млн.т. руды с гор.85100м через вытяжной тупик ст. "100м" и 04 млн.т. руды с гор. 115130м через вытяжные тупики ст. "130м" непосредственно из забоев направляется на фабрику со ст. "130м" в общем рудном потоке с Центрального участка. Забалансовая руда (11 млн.т.) из забоев автотранспортом из забоев доставляется на перегрузочный склад гор. 100м где перегружается в ж.д. транспорт и далее направляется по маршруту ст. Карьерная - ст. Отвальная - Восточный ж.д. отвал. По этому же маршруту направляется от ст. "100м" 02 млн.т. забалансовой руды доставляемой на эту станцию непосредственно из забоев ж.д. транспортом. Пустые породы из забоев с гор. 145 + 175м в объеме 4 млн.т. доставляются автосамосвалами в Восточный автомобильный отвал. Часть пустых пород 156 млн.т. и геллифлинтов 25 млн.т. непосредственно из забоев с гор.65+130м через вытяжные тупики ст. "100м" и "130м" направляются через траншею Центрального участка со ст. Карьерная откуда по двухпутному перегону пустые породы через ст. Отвальная направляются на Восточный железнодорожный отвал а геллифлинты через путь отмыкающий от двухпутного перегона направляются на временный железнодорожный склад геллифлинтов.
В 2010 году вся руда Южного участка (9млн.т.) доставляется автосамосвалами на 2 перегрузочных склада расположенных на этом участке на гор. 130м где перегружается в железнодорожный транспорт и далее через траншею Южного участка однопутный рудный перегон примыкающий непосредственно к ст. Рудная и через эту станцию транспортируется тяговыми агрегатами на фабрику. Пустые породы 192 млн.т. и геллифтинты 43 млн.т. доставляются автосамосвалами в Восточный автомобильный отвал где складируются в отдельные штабеля. Один млн.т. геллифлинтов доставляется на ДШУ.
Кроме того технологические грузопотоки формируются при разработке перешейка между Центральным и Южными участками. Часть пустых пород с гор. 160 145м в объеме 43 млн.т. вывозится автосамосвалами в Восточный автомобильный отвал. С гор. 160 145м пустая порода 32 млн.т. и руда с горЛЗОм в объеме 045 млн.т. доставляются автосамосвалами на перегрузочные железнодорожные склады расположенные на горЛЗОм перешейка где они перегружаются в подвижной состав. Далее составы следуют по траншее Южного участка с разделением на выходе из траншеи по направлениям: с породой - по двухпутному перегону через ст. Отвальная на Восточный железнодорожный отвал; с рудой - по однопутному перегону через ст. Рудная на фабрику.
В 2009 году в связи с завершением строительства ст.П-130м значительно изменяется направление технологических грузопотоков. Уменьшатся объемы горной массы проходящие через траншею Центрального участка и ст.Карьерная так как с Центрального участка 20 млн.т. горной массы с конвейерных подъемников и порядка 5 млн.т. породы с перегрузочного склада будут грузиться в железнодорожный транспорт на путях примыкающих к стП-130м с выходом путей от станции через траншею Южного участка. Через эту же станцию будет направляться весь рудный поток с Южного участка карьера. В связи с чем к 2010 году необходимо завершить строительство 2-го пути от траншеи Южного участка до ст.Рудная.
6.4 Автомобильный транспорт
В настоящий момент автомобильный транспорт используется как в качестве сборочного на доставке горной массы к автомобильно-железнодорожным перегрузочным складам и бункерам крутонаклонного конвейерного подъемника так и непосредственной доставки породы из забоев в отвалы (практически вся порода с южного и частично с верхних горизонтов центрального участков).
Тип автосамосвалов занятых на перевозке горной массы определяется в зависимости от объема и расстояния перевозок условий работы (самостоятельно или в комбинированных системах) типа погрузочного оборудования в карьере фактической структурой существующего парка и других факторов.
6.5 Характеристика автомобильных дорог в карьере
К технологическим автодорогам на поверхности относятся дороги соединяющие карьер с подъездной автодорогой перегрузочным складом руды и отвалами. Перевозки внутри карьера осуществляются по системе постоянных и временных автодорог и съездов.
Все технологические автодороги относятся к категории Ш-к. Величина руководящего уклона принята равной 80 000 минимальный радиус кривых в плане – 26м что соответствует двум конструктивным радиусам разворота по переднему наружному колесу принятой модели самосвала. На автодорогах во всех случаях предусмотренных СНиПом устраивается ориентирующий грунтовый вал высотой 13м не менее чем в 1м от бровки откоса уступа со стороны выработанного пространства. При этом внутренняя бровка вала располагается вне призмы обрушения.
Основные параметры технологических автодорог и конструкция дорожной одежды приведены в табл. 1.4.
Параметры автодорог карьера
Ширина проезжей части м
Конструкция дорожной одежды
Постоянные на поверхности (для грузового движения)
черный щебень-30 см (10+20) подстилающий слой щебня -30 см (15+15) выравнивающий слой шебня - 40 см (20+20)
Постоянные автодороги в карьере
черный щебень-10 см (10+20); выравнивающий слой щебня - 20см
Постоянные автодороги на отвале
черный щебень-30 см (10+20) подстилающий слой щебня - 20 см выпавниваюший слой шебня - 20 см
Временные автодороги в карьере на отвале
выравнивающий слой щебня -15 см на рыхлом основании: выпавникятттгий слой тпебня - 30 см
Объездная автодорога вокруг карьерного поля
выравнивающий слой щебня -15 см на рыхлом основании: выравнивающий слой щебня - 30 см
6.6 Железнодорожный транспорт
На предприятии используются железнодорожные тяговые агрегаты работающие на переменном токе под напряжением 10кВ.
В настоящее время на комбинат поставляются тяговые агрегаты ОПЭ-1М с внешними характеристиками аналогичными вышеуказанным сформированные из электровоза управления и 2 моторных думпкаров.
В качестве прицепных вагонов используются сейчас и будут поставляться в дальнейшем шестиосные думпкары 2ВС-105 номинальной грузоподъемностью 105т. Переход на более современные восьмиосные вагоны может быть осуществлен по мере организации их серийного производства на отечественных заводах.
Для возможности работы на уклонах свыше 40%о весь подвижной состав должен быть укомплектован ВР-498 производства МТЗ.
С целью повышения весовой нормы при увеличенном руководящем уклоне железнодорожных путей (54%) возможно использовать новый принцип формирования поездов - с расположением двух локомотивных групп каждая из которых состоит из серийного электровоза управления и одного моторного думпкара в голове и хвосте состава и размещением прицепных думпкаров между ними. Предлагаемое формирование по схеме "тяни-толкай" повышает уровень безопасности движения так как локомотив находится всегда в голове поезда позволяет легко осуществлять переход с центральной на боковую контактную сеть и обратно а так же продвигать вагоны на приемных бункерах рудоподготовительных фабрик лишенных контактной сети.
7 Отвальное хозяйство
7.1 Общая характеристика отвалов
В настоящее время порода вывозится из карьера в три действующих отвала: в Западный автомобильный Восточный автомобильный и в Восточный железнодорожный построенный не по проекту и занимаемый площади предназначенные для автомобильного отвала.
К настоящему времени объемы породы подаваемые на этот отвал железнодорожным транспортом сокращаются ликвидированы два отвальных тупика остался один тупик который так же должен быть разобран. Высвободившиеся экскаваторы задействованы на приеме пустых пород обеспечивающих строительство Восточного железнодорожного отвала в проектных границах по которому ведется отсыпка насыпи под станцию "Отвальная". Кроме того часть геллифлинтов направляется автотранспортом на временный склад или непосредственно на переработку для получения щебня.
Проектом предусматривается что породы будут направляться в три отвала с учетом раздельного складирования трех разновидностей пород: Западный автомобильный (второй участок) Восточный автомобильный (действующий) и Восточный железнодорожный (строящийся). В Западный автомобильный отвал будут направляться только пустые породы в Восточный автомобильный - пустые породы забалансовая руда и геллифлинты. Восточный железнодорожный - по 2008 год - пустые породы и забалансовая руда а после 2008 года начнут поступать и геллифлинты. Кроме того предусматривается прием геллифлинтов на временный железнодорожный склад расположенный между промплощадкой и карьером (вместимость склада 15млн.м3 породы).
Общий объем складирования с распределением по отвалам и отвальным участкам приведен в табл. 1.5
Распределение вскрыши по отвалам
Участок складирования
Объем складируемой породы в плотном теле млн.м3
до конца отработки I оч.
В том числе до 2010 года
Всего складируется пород
Автомобильный отвал Западный 11 всего
Восточный автомобильный отвал всего
Восточный железнодорожный отвал всего:
Временный железнодорожный склад геллифлинтов
* - в том числе 22млн.м на ДЩУ;
** - в том числе 150млн.м на ДЩУ.
7.2 Автомобильные отвалы
В связи с отказом от заведения железнодорожного транспорта через Северо-западную выездную траншею появилась необходимость в создании нового автомобильного отвала так как вместимость существующего Западного автомобильного отвала практически исчерпана. Новый автомобильный отвал (Западный П) предлагается сформировать в непосредственной близости от существующего Западного отвала и границ карьера Центрального участка. На новый отвал пустые породы будут доставляться автомобильным транспортом с верхних горизонтов торцевой части лежачего и частично висячего бока залежи Центрального участка карьера.
Максимальная высота отвала будет достигать 70м. Отсыпка отвала будет осуществляться двумя ярусами. Высота нижнего яруса - 20-3 Ом верхнего -20м ширина берм на конечных границах отвала - 50м в рабочей зоне -50-350м угол откоса яруса - 38°.
Восточный автомобильный отвал является действующим на который порода доставляется с обоих участков верхних горизонтов карьера. В отличии от Западного П на этом отвале планируется складировать раздельно три вида пород: пустая порода геллифлинты и в значительном количестве забалансовые руды расположение последних двух предлагается в разных штабелях с расположением их на кровле первого яруса отсыпанного пустыми породами. Максимальная высота отвала будет достигать 80м. Высота нижнего яруса обусловлена сформировавшимся к настоящему времени отвалом и будут составлять 20-50м двум вышерасположенным по 20м ширина берм на конец отсыпки - 50м в рабочей зоне - 50-350м.
Схема развития автомобильных отвалов предполагает параллельное развития ярусов исходя из критерия максимально приведенной дальности транспортирования Шаг по длине в направлении основного развития отвала по которому определяют момент вовлечения в эксплуатацию вышележащего яруса равен 250-350м и в последующем это расстояние сохраняется между смежными ярусами.
На обоих автомобильных отвалах отвалообразование предусматривается осуществлять бульдозерами ДЗ-118 на тракторе ДЭТ-250.
7.3 Железнодорожный отвал
Как уже отмечалось в настоящий момент осуществляется отсыпка насыпи под железнодорожную станцию "Отвальная" играющей основную роль в распределении грузопотоков направляемых на восточный железнодорожный отвал. С нее же будет осуществляться обмен составов между станцией и отвальными тупиками до 2005-2010 год без строительства обменных постов на отвале.
На Восточный железнодорожный отвал будут поступать все объемы пустых пород и забалансовая руда с гор. 130м и ниже а частично с вышеуказанных горизонтов Центрального участка. С этого же участка после 2004 года будут направляться и геллифлинты.
Границы железнодорожного отвала со стороны карьера определялись границами Восточного автомобильного отвала. Последние находились из условий оптимального использования автомобильного транспорта по доставке пустых пород в отвал.
Максимальная высота отвала на конец отработки принята 80м отсыпка которого производится в 4 яруса. Высота первого яруса 10-40м трех вышележащих по 20м минимальная ширина берм - 50м угол откоса ярусов - 37-38°.
В период до 2010 года включительно отсыпка железнодорожного отвала осуществляется двумя ярусами с отметками соответственно 230 и 250м.
Отсыпка ярусов ведется таким образом чтобы в минимальные сроки создать необходимое количество отвальных тупиков для приема в 2004 году 99 млн.мЗ породы и создать площади на кровле первого яруса отвала для приема после 2004 года геллифлинтов. В связи с чем принята минимальная высота второго яруса. В последующем в период 2005-2010 годов по мере развития отвала высоты ярусов могут быть увеличены до 30м.
Кроме того следует отметить что дополнительные сложности в развитии отвала создают существующие - автомобильная дорога на деревню Вокнаволок и водоотводный канал которые отсекают площади с наиболее низкими отметками рельефа и сужают выход со станции "Отвальная" на тело отвала.
С карьера железнодорожным транспортом железная руда доставляется на дробильно-обогатительную фабрику (ДОФ) (ДП.060955.02СХ). Конечным продуктом дробильно-обогатительной фабрики является железорудный концентрат. Руда поступает в главный корпус обогащения где измельчается в три стадии с классификацией в гидроциклоне затем обогащается в три стадии сепарации и дешламации. Готовый продукт перекачивается в цех производства окатышей.
Первая стадия измельчения
Исходная руда крупностью кл.+15 мм до 10% системой конвейеров подается на первую стадию измельчения где установлены стержневые мельницы МСЦ 3600x5500 с полезным объемом 49 м3 в количестве одной единицы на каждую секцию.
Стержневая мельница работает в открытом цикле измельчения и должна обеспечивать крупность материала в разгрузке мельницы 2-0 мм (кл. +2 мм до 10 %)
Вторая стадия измельчения.
Питанием мельниц II стадии измельчения является промпродукт I стадии ММС. Мельница МШЦ 4500x6000 работает в замкнутом цикле с гидроциклонами ГЦ-710. Измельченный продукт самотеком из мельницы направляется в 1 технологический зумпф куда подается дополнительная вода для поддержания необходимой плотности питания гидроциклонов и определенного уровня пульпы. Из зумпфа пульпа насосом 12Гр-8 подается на гидроциклоны ГЦ-710 слив которых поступает на дешламацию 1 приема а пески возвращаются в мельницу на доизмельчение.
Третья стадия измельчения.
Питанием мельниц III стадии измельчения являются пески основной и контрольной классификации. Третья стадия измельчения работает в замкнутом цикле с гидроциклонами ГЦ - 500. Измельченный продукт из мельницы поступает во П-ой технологический зумпф откуда насосом 12 Гр-8 подается на гидроциклоны ГЦ-500. Для поддержания оптимальной плотности гидроциклонов и постоянного уровня в зумпф подается дополнительная вода. Слив гидроциклонов поступает на П-ой прием дешламации а пески возвращаются в мельницу МШЦ 4500x6000 на доизмельчение.
Классификация в гидроциклонах ГЦ-710 и ГЦ-500.
Классификация после второй стадии измельчения осуществляется в батареях по 3 гидроциклоиа d=710 мм из которых одна является резервной. Классификация после Ш-ей стадии измельчения осуществляется на 2-х батареях по 6 гидроциклонов d=500 мм одна из которых - резервная.
Первая стадия магнитной сепарации.
Слив стержневой мельницы поступает на I стадию сепарации на которой установлены два сепаратора ПБМ-П-120х300 с противоточной ванной. Промпродукт I стадии ММС направляется во II стадию измельчения а хвосты в хвостовой лоток. Первая стадия ММС позволяет удалить в голове схемы до 35-40 % от общего количества хвостов.
Вторая стадия магнитной сепарации.
1.Питанием II стадии ММС являются пески дешламаторов 1 приема которые насосом 8 Гр-8 или ГрА-70040 подаются в пульподелитель откуда на двухбарабанные сепараторы ПБМ-ПП-90х250 в количестве 5на каждой секции.
2. Промпродукт первого барабана поступает на перечистку на второй барабан откуда самотеком направляется в зумпф II приема для классификации в ГЦ- 500. Хвосты первого и второго барабанов направляются в хвостовой лоток.
Третья стадия магнитной сепарации.
1.Питанием III стадии ММС являются пески дешламации второго приема. Насосами 8Гр-8 (ГрА-70040) питание через пульподелитель распределяется на шесть двухбарабанных сепараторов ПБМ-ПП-90х250. В зависимости от типов перерабатываемой руды количество сепараторов в операции может быть сокращено.
2.Промпродукт первого барабана поступает на перечистку на второй барабан откуда самотеком поступает в зумпф для подачи его на предварительную классификацию. Хвосты первого и второго барабанов направляются в хвостовой лоток.
Операции дешламации первого и второго приемов.
Питанием дешламации 1 приема является слив гидроциклонов ГЦ-710 а дешламации II приема - слив гидроциклонов ГЦ-500. Дешламация осуществляется в дешламаторах МД-9 в количестве одного на каждый прием.
Операция дешламации третьего приема.
1. Питанием дешламации III приема являются три продукта: слив гидроциклонов контрольной класссификации слив гидроциклонов предварительной классификации и подрешетный продукт тонкого грохочения.
2. Дешламация осуществляется в дешламаторах МД-9 в количестве одного на каждую секцию.
Предварительная и контрольная классификация в гидроциклонах ГЦ-500
Питанием предварительной классификаций является промпродукт MMC-III а контрольной классификации - надрешетный продукт тонкого грохочения. Пульпа в гидроциклоны подается из зумпфов насосами 8 Гр-8 или ГрА-35040 с заданным уровнем плотности которая достигается расходом дополнительной воды в эти зумпфы. Каждая батарея состоит из 2 гидроциклонов d=500 мм
1.Питанием операции тонкого грохочения являются пески предварительной классификации поступающие самотеком через пульподелитель на поверхность щелевидных сит грохотов.
2.Тонкое грохочение осуществляется в один прием. Для регулирования качества концентрата в работе используется от 2 до 5 дек грохотов.
Конечным продуктом (готовый концентрат) являются пески дешламации третьего приема которые насосами 5Гр-5 (ГрА-17040) перекачиваются в корпус сгущения для дополнительной отмывки и сгущения в модернизированных сгустителях диаметром 30 метров с периферийным приводом.
На (ДП.060955.001) представлена технологическая схема обогащения.
9 Технологическое оборудование и организация работ на участке измельчения
Измельчение - процесс уменьшения крупности твердых частиц в результате различных физических воздействий. Для измельчения железной руды применяют барабанные мельницы. На участке измельчения находится 11 технологических секций каждая секция включает в себя три мельницы( одна стержневая и две шаровых). Для измельчения применяется трех стадиальная схема.
9.1 Организация работ на участке
Переработка (измельчение) руды в соответствии с утвержденным планом производства действующими стандартами и техническими условиями.
-технологическая служба;
-механическая служба:
-бригада по ремонту мельниц и конвейров
-бригада по ремонту гидроциклонов
-бригада по ремонту и обслуживанию систем централизованной смазки
-бригада по капитальному ремонту мельниц
-бригада по ремонту грузоподъемных машин (ГПМ);
-бригада по обслуживанию ГПМ;
-электрическая служба.
Подчиненность между работниками определяется в соответствии с организационной структурой подразделения. Распределение обязанностей между подчиненными работниками осуществляется руководителем подразделения на основании соответствующих положений должностных инструкций.
1.Для реализации поставленных задач участок измельчения выполняет следующие функции:
1.1.Выполнение суточного месячного годового плана задания по переработке (измельчению) руды по количественным и качественным показателям. Принятие необходимых оперативных мер по ликвидации возникших отклонений.
1.2.Осуществление контроля за качеством выпускаемой продукции.
1.3.Составление стратегии и планов развития подразделения.
1.4.Эффективная эксплуатация оборудования зданий и сооружений.
1.6. Обеспечение производственного контроля состояния промышленной безопасности.
2.основные функции внутренних подразделений:
2.1.Технологическая служба производит переработку (измельчение) руды в соответствии с техническими условиями.
2.2.Механическая служба обеспечивает работоспособность и техническую исправность механического оборудования участка.
2.3.Бригада по ремонту ГПМ обеспечивает работоспособность и техническую исправность мостовых кранов.
2.4 Бригада по обслуживанию ГПМ обеспечивает обслуживание кранов.
2.5. Электрическая служба обеспечивает работоспособность и техническую
исправность электрооборудования.
Взаимоотношения с другими структурами подразделениями предприятия по вопросам:
-обеспечения запасными частями и сменным оборудованием;
-ремонта вспомогательного оборудования.
Права и ответственность
1.Права по достижению выполнения поставленных перед участком задач и функций определены должностной инструкцией начальника участка.
2.Всю полноту ответственности за качество своевременность выполнения возложенных производственных задач и функций которые определяются должностной инструкцией несет начальник участка.
3.Степень ответственности других работников устанавливается должностными инструкциями
9.2 Основное и вспомогательное технологическое оборудование участка
К основному технологическому оборудованию участка измельчения относится: МСЦ-3600×5500 (мельница стержневая с центральной разгрузкой диаметром барабана 3600 мм и длиной 5500мм) в количестве 11МШЦ- 4500х6000 (мельница шаровая с центральной разгрузкой диаметром барабана 4500мм. и длиной 6000мм) в количестве 22ГЦ 710 (гидроциклон диаметром 710 мм) в количестве 66ГЦ 500 (гидроциклон диаметром 500 мм) в количестве 220К вспомогательному оборудованию участка относятся ленточные конвейера в количестве 3на каждой технологической секции. Технические характеристики оборудования. МСЦ 3600×5500
)Внутренний диаметр (без футеровки) - 3600 мм;
)Длина барабана (без футеровки) - 5500 мм;
)Номинальный объем барабана 49 м;
)Номинальная частота вращения барабана 13.7 обмин;
)Степеньзаполнения мелющими телами ( стержни D = 100 мм L = 5000 мм.) - 40%-42%;
)Мощность электрического двигателя 1000 кВт;
)Частота вращения ротора 166.6 обмин;
)Режим работы непрерывный МШЦ 4500×6000;
)Внутренний диаметр ( без футеровки ) - 4600 мм;
)Длина барабана ( без футеровки) - 6000 мм;
)Номинальный объем барабана 82 м;
)Номинальная частота вращения барабана 16.7 обмин;
)Степень заполнения мелющими телами ( шары D = 40 мм) - 42%;
)Мощность электрического двигателя главного привода - 2500 кВт;
)Частота вращения ротора 150 обмин;
)Режим работы - непрерывный ГЦ-710;
)Диаметр песковой насадки 75 мм;
)Диаметр сливной насадки 150 мм;
)Режим работы - непрерывный ГЦ-500;
)Диаметр песковой насадки 65 мм;
)Диаметр сливной насадки 120 мм;
)Режим работы непрерывный.
ГЛАВА 2 СПЕЦИАЛЬНАЯ ЧАСТЬ
1 Увеличение срока службы футеровки
1.1 Аналитический обзор
1.1.1 Сталь Гадфильда и ее стойкость к износу
В настоящее время подавляющее большинство футеровочных плит отечественных шаровых мельниц изготавливают из высокомарганцовистой аустенитной стали 110Г13Л более известной по имени автора как сталь Гадфильда. Эта сталь широко используется в качестве конструкционного материала деталей горного и обогатительного оборудования работающего в условиях интенсивного абразивного и ударно-абразивного износа (футеровка шаровых мельниц «щеки» дробилок «зубья» ковшей экскаваторов). Вместе с тем известно что эта сталь обладает высокой эрозионной стойкостью только при интенсивном наклепе имеющем место при работе детали в условиях значительных напряжений и динамических нагрузок. Так футеровки центробежных дробилок изготовленные из стали Гадфильда способны выдержать размол до 2000–4000т твердого гранита вследствии наклепа возникающего в результате удара гранита о поверхность футеровки. Щеки щековых дробилок при работе по таким же твердым породам наклепываются до твердости 500НВ (предельная твердость достигаемая сталью 110Г13Л ~ 600 НВ [23]) повышение твердости в свою очередь уменьшает интенсивность износа щек. При отсутствии значительных напряжений и динамических нагрузок каким-либо заметным преимуществом в эрозионной стойкости (по сравнению с обычной среднеуглеродистой сталью) сталь Гадфильда не обладает [12]. Например била для размола извести и скрепки установки для помола песка из этой стали очень недолговечны [22]. Не происходит заметного наклепа футеровочных плит из стали 110Г13Л и при работе шаровых мельниц когда мелющие тела воздействуют на футеровку только через слой породы [13].
1.1.2 Теоретические основы упрочнения стали наклепом
Пластическое деформирование выполняемое без использования внешней теплоты для обеспечения нужного комплекса свойств поверхностного слоя называют наклепом а слой металла в котором проявляются эти свойства соответственно – наклепанным. В результате наклепа повышаются все характеристики сопротивления металла деформации понижается его пластичность и увеличивается твердость. Упрочнение незакаленной стали происходит в результате изменения структурных несовершенств (плотности качества и взаимодействия дислокаций количества вакансий и др.) дроблением блоков и созданием микронапряжений. При упрочнении закаленных сталей помимо этого происходит частичное превращение остаточного аустенита в мартенсит и выделение дисперсных карбидных частиц. Поверхностная деформация приводит к образованию сдвигов и упругому искажению кристаллической решетки изменению формы и размеров зерен [12].
С ростом степени предварительной деформации ( = (F0- Fk) F0 100 где F0 и Fk — площадь сечения до и после деформации) механические свойства (В Т HB) характеризующие сопротивление деформации повышаются происходит деформационное упрочнение а способность к пластической деформации ( ) падает (рис.2.1). Предел текучести Т растет более интенсивно чем предел прочности В и по мере увеличения степени пластической деформации значения обеих характеристик сближаются [6].
Рис. 2.1 Влияние степени пластической деформации на механические свойства ( В Т) низкоуглеродистой стали
1.1.3 Основные виды изнашивания материалов
Абразивный износ. Термин «абразивное изнашивание» применяется для обозначения изнашивания деталей машин вызываемого действием неметаллических твердых тел обычно твердых минеральных частиц движущихся относительно поверхности детали. При службе деталей машин встречаются самые разнообразные условия определяющие воздействие таких твердых тел на металл.
Трение металлической детали может происходить о твердое тело однородное по составу (например руда) или представляющее собой массу твердых частиц сцементированных в монолитное тело (песчаник) или неоднородное тело в которое включены твердые минеральные вкрапления (твердая порода в угле). Изнашивающие металл твердые частицы не будут в этих случаях перемещаться относительно друг друга вдавливаться в основу или перекатываться; они будут оставлять на металле след в виде выдавленной или вырезанной царапины. Такие случаи абразивного изнашивания постоянно встречаются при трении металла о твердые горные породы или руду о содержащий породу уголь при резании весьма прочного или мерзлого грунта; в частности они встречаются при работе зубьев ковшей экскаваторов и драг рештаков скребковых конвейеров и других транспортных механизмов в которых перемещаемые куски твердых пород скользят по металлу инструментов обрабатывающих горные породы и т. п. Во всех этих случаях изнашивающее действие производят минералы более твердые чем металл и потому могущие его царапать или отдельные твердые частицы минералов закрепленные в менее твердой но достаточно прочной основе [26].
Как можно заключить из сказанного выше при работе шаровой мельницы абразивный износ может иметь место в случае контакта футеровки с абразивной породой более твердой чем металл футеровки (стали Гадфильда).
Для выяснения влияния наклепа на абразивную износостойкость стали Гадфильда в лаборатории кафедры конструирования горных машин и технологии машиностроения были проведены испытания на абразивный износ. Испытания проводились на цилиндрических образцах стали 110Г13Л диаметром D=8мм высотой H=50 мм с отверстием (d=4мм) на установке представляющей собой модифицированный вертикально-сверлильный станок. В качестве абразивной среды использовали электрокорунд как материал обладающий повышенной твердостью (~ 2230HB). Нагрузка при всех испытаниях составляла 200 Н. Схема испытаний представлена на рис.2.2.
Рис. 2.2 Схема испытания где 1 – вращающийся металлический образец; 2 – неподвижное основание (электрокорунд); P – нагрузка на образец (100÷300Н); n – частота вращения образца вокруг оси симметрии обмин
Испытания проводились в 2 этапа. Сначала изнашивали исходный образец с твердостью порядка 250HB а затем наклепанный. Для этого исходный образец подвергали пластическому деформированию сжатием с относительной деформацией 33% что приводило к повышению твердости материала до 336HB. Для исходного и наклепанного образца проводили по 7 циклов испытаний в течение t=10минут каждый. После каждого цикла определяли величину Δm - потери массы металла отнесенной к единице площади контакта с абразивом. Строили график Δm=f(t) для линейного участка кривых которого рассчитывали коэффициент износа K [].
Результаты испытаний представлены рис.2.3.
Рис.2.3 Зависимость потери относительной массы образца стали Гадфильда от времени : 1 – исходный материал; 2 – после наклепа
Как следует из вида кривых графика после начального периода зависимость Δm=f(t) для обеих сталей становится линейной. При этом тангенс угла наклона прямых (коэффициент износа K сталей) для исходного и наклепанного образца практически одинаков и составляет и соответственно. Из чего можно сделать вывод что увеличение твердости стали Гадфильда пластическим деформированием (наклепом) не влечет за собой увеличения её абразивной износостойкости.
Результаты данного эксперимента подтверждаются литературными данными [25 26] об отсутствии повышения абразивной износостойкости сталей после их наклепа.
Ударно-абразивный износ. Ударно-абразивное изнашивание происходит при ударе по твердым частицам способным поражать поверхность контактирования путем образования в ней лунок – следов прямого динамического внедрения этих частиц. Качественным признаком ударно-абразивного изнашивания является специфическая поверхность представляющая собой сочетание лунок разделенных перемычками. На поверхности подверженной ударно-абразивному изнашиванию нет направлений шероховатости в виде рисок и следовательно нет относительного перемещения твердых частиц вдоль этой поверхности (рис.2.4).
Рис. 2.4 Макрорельеф поверхности при ударно-абразивном изнашивании
Условия проявления ударно-абразивного изнашивания весьма разнообразны. Этот вид изнашивания развивается на плоских и сферических поверхностях контакта совершающих удар по абразивным или иным твердым частицам. Кроме того прямое динамическое внедрение твердых частиц в поверхность контакта возможно при качении цилиндра и шара по плоской цилиндрической и сферической поверхностям. Твердые частицы вызывающие при ударе по ним ударно-абразивное изнашивание могут быть различного происхождения. Обычно это минеральные абразивные частицы более твердые чем поверхность детали свободно расположенные в зоне контакта или находящиеся в связке монолита. Ударно-абразивное изнашивание могут вызвать твердые металлические частицы попадающие в зону контакта или образующиеся в ней при динамическом взаимодействии металлических пар; имеется в виду выкрашивание карбидов с армированных поверхностей образование твердых частиц в результате охрупчивания при наклепе и выкрашивании в процессе ударно-штамповых операций [9].
В литературе не обнаружено прямых сведений о влиянии наклепа на износостойкость материалов при ударно-абразивном изнашивании. Но есть сведения о влиянии на износостойкость предела прочности материала (рис. 2.5).
Поскольку предел прочности материалов с увеличением интенсивности наклепа всегда возрастает можно было ожидать что и износостойкость наклепанных материалов при ударно-абразивном изнашивании так же будет повышаться.
Рис.2.5 Влияние предела прочности B аустенитной стали 110Г13Л на её износостойкость при энергии удара Дж: 1 2 – 10; 3 4 - 5
Контактная усталость. Усталостное изнашивание (контактная усталость) происходит в результате накопления повреждений и разрушений поверхности под влиянием циклических контактных нагрузок вызывающих появление «ямок» (питтингов) выкрашивания. Усталостное изнашивание проявляется при трении качения или реже качении с проскальзыванием когда контакт деталей является сосредоточенным. Данный вид изнашивания может так же иметь место и при других условиях взаимодействия трущихся пар например при скольжении многократном соударении двух тел [20 26].
Контактное усталостное изнашивание характеризуется ограниченным пределом усталостного выкрашивания к т.е. максимальным нормальным напряжением цикла max при котором не наблюдается разрушение поверхностных слоев испытуемого металла при данной базе испытания.
Особенностью явлений контактной усталости является начальное и прогрессирующее выкрашивание. В отличие от прогрессирующего выкрашивания которое не прекращается с момента возникновения начальное выкрашивание наблюдается только в первый период работы а образовавшиеся питтинги в процессе работы заплывают металлом. Самозалечивание питтингов происходит вследствие повышения предела усталостного выкрашивания в результате наклепа и снижения величины контактного давления вследствие увеличения площади контакта по мере выглаживания трущихся поверхностей [26].
Поверхностное пластическое деформирование (наклеп) повышает плотность дислокации в упрочненном слое измельчает субструктуру (величину блоков) а при обработке закаленных поверхностей уменьшает количество остаточного аустенита. В результате поверхностное пластическое деформирование повышает сопротивление контактной усталости [20].
В шаровой мельнице в процессе ее работы контактная усталость как можно предположить может возникнуть вследствие воздействия на футеровку знакопеременных напряжений возникающих в результате падения шаров на футеровку. Под воздействием напряжений поверхностные слои футеровки подвергаются упругой деформации а после того как шаровая загрузка «уходит» на параболическую траекторию деформация исчезает. При многократном воздействии знакопеременных нагрузок на поверхность футеровки начинают зарождаться трещины развитие которых в дальнейшем может привести к выкрашиванию металла то есть износу футеровки. Развитие трещин в глубину металла может привести к растрескиванию и разрушению всего сегмента футеровки.
1.1.4 Установление вида износа футеровки шаровых мельниц
Вид поверхности футеровки из стали Гадфильда шаровой мельницы после эксплуатации представлен на рис.2.6. Как можно заключить из сравнения рис.2.4 и 2.6 вид представленных поверхностей идентичен. Это обстоятельство позволяет заключить что при работе шаровой мельницы по магнетиту ударно-абразивный износ является доминирующим.
Рис. 2.6 Поверхность футеровки из стали Гадфильда после эксплуатации в шаровой мельнице
Он возникает в месте контакта шар - измельчаемая порода – футеровка т.е. шар передает энергию удара от своего падения на породу которая за счет переданной ей энергии внедряется внешним абразивным слоем в поверхность футеровки. Для осуществления такого процесса необходимо чтобы абразивные частицы породы были более твердые чем поверхность футеровки [9]. В случае магнетита это условие соблюдается (570НV по сравнению с 240 НV для стали Гадфильда).
В работе [9] отмечается что износостойкость материалов повышается с увеличением их твердости (интенсивности наклепа) только до определенного уровня энергии удара.
1.1.5 Шаровые барабанные мельницы
Принцип действия. Наибольшее распространение для измельчения полезных ископаемых получили барабанные (шаровые и стержневые) мельницы. В последние десятилетия на фабриках большой производительности применяют барабанные мельницы самоизмельчения (бесшарового измельчения) или полусамоизмельчения (с небольшой добавкой шаров).
Барабанная мельница (рис.2.7) представляет собой пустотелый барабан 3 закрытый торцовыми крышками 2 и 4 в центре которых имеются полые цапфы 1 и 5. Цапфы опираются на подшипники и барабан вращается вокруг горизонтальной оси. Барабан заполняется примерно на половину объема дробящей средой (дробящими телами 6). При вращении барабана дробящие тела благодаря трению увлекаются его внутренней поверхностью поднимаются на некоторую высоту и свободно или перекатываясь падают вниз. Через одну полую цапфу внутрь барабана непрерывно подается измельчаемый материал который проходит вдоль него и подвергаясь воздействию дробящих тел измельчается ударом истиранием и раздавливанием. Измельченный продукт непрерывно разгружается через другую полую цапфу. При вращении барабана материал движется вдоль его оси вследствие перепада уровней загрузки и разгрузки и напора непрерывно подаваемого материала. При мокром измельчении материал увлекается сливным потоком воды при сухом - воздушным потоком возникающим при отсасывании воздуха из барабана.
Рис. 2.7 Схема и принцип действия барабанной (шаровой) мельницы а – общий вид; б – схема движения материала
По режиму работы мельницы делят на машины периодического и непрерывного действия; с вращающимся барабаном вибрационные центробежные и башенные.
В зависимости от формы барабана различают мельницы цилиндроконические и цилиндрические. Последние в свою очередь бывают трех типов - короткие длинные и трубные. У коротких мельниц длина меньше диаметра или близка к нему; у длинных - она достигает трех диаметров а у трубных - длина барабана больше диаметра не менее чем в 3 раза. Трубные мельницы применяют в цементной промышленности.
В зависимости от вида дробящей среды различают мельницы шаровые стержневые галечные рудно-галечные и самоизмельчения. У шаровых мельниц дробящая среда представлена стальными или чугунными шарами; у стержневых - стальными стержнями у галечных - окатанной кремневой галькой или рудой; у мельниц самоизмельчения - крупными кусками измельчаемой руды.
В зависимости от способа разгрузки измельченного продукта различают мельницы с центральной разгрузкой и разгрузкой через решетку. У мельниц с центральной разгрузкой измельченный продукт удаляется свободным сливом через пустотелую разгрузочную цапфу. Для этого необходимо чтобы уровень пульты в барабане был выше уровня нижней образующей разгрузочной цапфы. Поэтому мельницы с центральной разгрузкой называют иногда мельницами сливного типа или мельницами с высоким уровнем пульпы. У мельниц с разгрузкой через решетку имеется подъемное устройство принудительно разгружающее измельченный продукт. Поэтому в мельницах такого типа уровень пульпы может быть ниже уровня разгрузочной цапфы. Мельницы с разгрузкой через решетку иногда называют мельницами с принудительной разгрузкой или мельницами с низким уровнем пульпы.
Мельницы характеризуются внутренним диаметром барабана (при снятой футеровке) и его рабочей длиной.
Цилиндрические шаровые и стержневые мельницы широко применяются на обогатительных фабриках для измельчения руд. Стержневые мельницы могут быть использованы как аппараты мелкого дробления перед шаровыми мельницами и для измельчения мелковкрапленных руд перед гравитационным или электромагнитным обогащением. Галечные мельницы применяют в тех случаях когда нельзя допустить даже ничтожных примесей железа в измельчаемом материале. Мельницы самоизмельчения в последние десятилетия внедряются в практику измельчения руд. Самоизмельчение успешно конкурирует с измельчением стальной средой и в некоторых случаях не только удешевляет процесс рудоподготовки но и улучшает технологические показатели переработки руд [1].
Конструкции шаровых мельниц. Шаровая мельница с центральной разгрузкой МШЦ 4500×6000 (ДП.060955.002ВО спецификация к чертежу представлена в приложении 1) состоит из цилиндрического барабана 1 с торцовыми крышками 2 имеющими пустотелые цапфы 4 и 5 посредством которых барабан опирается на коренные подшипники 6 и 7. Барабан и крышки футеруют изнутри стальными плитами (футеровками) 8. В барабан загружают стальные или чугунные шары разного диаметра (от 40 до 120 мм). Вращение барабану передается от электродвигателя 17 вал которого вращается в подшипниках 16 далее вращение передаётся через промежуточный вал 15 на вал-шестерню 14 которая в свою очередь передаёт вращение зубчатому венцу 9 который передает вращение барабану 1 шаровой мельницы.
Исходный материал загружается в мельницу через левую загрузочную цапфу 10. Измельченный материал поступает в правую разгрузочную цапфу 11 и разгружается через бутару 18.
Барабан изготовляется сварным или клепаным из толстой листовой стали. На оба конца барабана приклепывают или приваривают стальные обработанные фланцы для прикрепления торцовых крышек. Иногда барабан изготовляют литым из стали и чугуна или стали с фланцами на концах.
В мельницах малых размеров где диаметр разгрузочной цапфы недостаточен для введения футеровки внутрь мельницы на барабане устраивается один или два диаметрально расположенных люка 12 и 13. Торцовые крышки с пустотелыми цапфами отливают из чугуна или стали в зависимости от размеров мельницы. Торцовые крышки к фланцам барабана мельницы крепят болтами. Для уплотнения соединения болтами и уменьшения нагрузки на них предусмотрен кольцевой выступ. Разгрузочная цапфа устраивается несколько большего диаметра чем загрузочная для создания уклона пульпы в мельнице. Снаружи на ней устраивается кольцевой выступ для предотвращения попадания пульпы в подшипник. Коренные подшипники делаются с большой опорной поверхностью. Часто применяют самоустанавливающиеся подшипники с баббитовыми вкладышами имеющими шаровую опору в корпусе подшипника.
Для предохранения обечайки мельницы от износа используют футеровочные плиты которые также предназначены для уменьшения скольжения между обечайкой и измельчающей средой. По мере износа футеровка подлежит замене для чего мельницу останавливают на ремонт. Футеровки различаются в зависимости от материала профиля и метода монтажа.
Футеровочные плиты барабана должны легко устанавливаться и заменяться. Обычно плиты изготовляют из чугуна или марганцовистой и хромистой стали а также резины и (редко) керамики. Литую марганцовистую сталь применяют при значительных нагрузках шаров большого диаметра. Толщина футеровочных плит колеблется от 50 мм для малых мельниц до 130-150 мм для больших.
Профили футеровочных плит показаны на рис.2.8. Для грубого измельчения применяют ребристые футеровки 5 6 8 10 12-15 а для тонкого - гладкие 11 или волнистые 1-4 7 9. Резиновую футеровку 16 применяют в шаровых мельницах в основном для тонкого измельчения (мельницы второй и третьей стадий). Ставят их иногда на мельницы с решеткой. Для первичных мельниц самоизмельчения толщина футеровки принимается равной 140-160 мм.
Рис. 2.8 Типы футеровок цилиндрической части барабана мельниц
-15 – стальные футеровки; 16 – резиновая футеровка с лифтером; 17-18 – футеровка мельниц самоизмельчения; 4 и 15 – с безболтовым креплением; остальные – с болтовым креплением к барабану
Заметное влияние на работу мельницы оказывает форма футеровки ее барабана.
Футеровка барабанов шаровых мельниц работающих на крупном исходном материале имеет ребра. Для мельниц работающих на мелком материале применяют футеровку с мелкими ребрами или совсем гладкую. Высота взаимное расположение и форма ребер определяют силу сцепления дробящей среды с барабаном а значит и результаты работы мельницы. Поэтому важно чтобы при изнашивании футеровки характер ее поверхности резко не изменялся [1].
Скоростные режимы работы мельницы. Режим работы шаровой мельницы в зависимости от скорости вращения её барабана может быть каскадным или водопадным.
При низкой скорости вращения мельницы вся шаровая нагрузка делает поворот в сторону вращения на некоторый угол и при постоянной скорости вращения остаётся в таком положении (рис.2.9). Шары непрерывно циркулируют поднимаясь по концентрическим круговым траекториям и скатываясь параллельными слоями каскадом вниз. Такой режим работы мельницы называется каскадным. Измельчение материала при каскадном режиме происходит главным образом его раздавливанием и истиранием перекатывающимися шарами [2].
Рис. 2.9 Каскадный режим работы шаровой мельницы
Каскадный режим работы мельницы характеризуется тонким измельчением с увеличением выходов шламов и повышенным износом футеровки [1].
По мере повышения скорости вращения мельницы угол поворота шаровой нагрузки увеличивается шары по круговым траекториям поднимаются всё выше но режим работы может оставаться еще каскадным. Когда наконец шары поднимутся до известной ещё большей высоты определяемой скоростью вращения мельницы они сходят с круговых траекторий и как тела брошенные под углом к горизонту по параболическим траекториям падают водопадом обратно на круговые траектории. Такой режим работы мельницы называется водопадным (рис.2.10). Измельчение материала при водопадном режиме происходит главным образом ударом падающих шаров и отчасти истиранием.
Рис. 2.10 Водопадный режим работы шаровой мельницы
При водопадном режиме вся траектория движения шара в каком-либо слое делится на два участка (рис.2.11). При подъёме шара от точки падения А1 до точки отрыва А5; шар движется по круговой траектории A1A5 и от точки отрыва A5 до точки падения А1— падает по параболической кривой А5А1.
Рис. 2.11 Траектория движения шара при водопадном режиме работы мельницы и силы действующие на шар
Положение шара на круговой траектории определяется углом отрыва а образуемым радиусом барабана мельницы проходящим через центр шара с вертикальным диаметром барабана.
В любой точке круговой траектории радиуса R шар находится под действием силы тяжести G и центробежной силы где v - линейная скорость шара на круговой траектории. Силу тяжести G можно разложить на составляющие: радиальную N=G·cosα и тангенциальную Т=G·sinα [1].
При постоянной угловой скорости вращения барабана центробежная сила С сохраняет постоянную величину на всех участках круговой траектории и постоянное направление от оси мельницы к периферии. Величина же и направление радиальной силы N меняются и зависят от положения шара на круговой траектории.
Шаровая нагрузка увлекается в движение по круговым траекториям силами трения возникающими между футеровкой барабана и прилегающим к ней внешним слоем шаров и вследствие трения между смежными слоями шаров стремится вращаться как сплошное тело вместе с барабаном. Величина сил трения зависит от коэффициента трения и нормального давления на внутреннюю поверхность барабана оказываемого радиальными составляющими силы тяжести N и центробежными силами С. Тангенциальные составляющие силы тяжести Т стремятся повернуть шаровую нагрузку против направления вращения. Для того чтобы нагрузка не скользила по футеровке момент сил трения относительно оси мельницы должен уравновешивать момент тангенциальных составляющих сил тяжести относительно той же оси.
Наибольшее давление на поверхность барабана шары оказывают в нижних квадрантах где радиальные силы N и С действуют в одну сторону. Здесь и возникает наибольшее трение создающее «подпор» обеспечивающий вращение шаровой нагрузки. В верхнем квадранте радиальная сила N действуя в противоположную сторону уменьшает давление оказываемое центробежной силой C уменьшая тем самым и силу трения.
Шар какого-либо слоя движется по круговой траектории и переходит из нижнего квадранта в верхний не как единичный изолированный шар в силу индивидуально вызываемого им трения а за счёт трения всей шаровой нагрузки как её составная часть увлекаемый в движение всей вращающейся массой шаров и «подпираемый» последующим рядом шаров того же слоя. Условия перехода шаров из нижнего квадранта в верхний нельзя основывать на уравнении равновесия единичного шара на круговой траектории не приходя при этом к противоречивым выводам. В мельнице с гладкой футеровкой барабана но при наличии трения единичный шар остается всё время в нижней точке барабана совершая небольшие колебания около среднего положения.
Коэффициент трения зависит от свойств измельчаемого материала характера поверхности барабана (футеровки) и консистенции пульпы (отношения Ж:Т). При низком коэффициенте трения при небольших шаровых нагрузках (менее 30% объёма мельницы) и при малой скорости вращения давление шаров может оказаться недостаточным и наблюдается скольжение внешнего слоя шаров по поверхности барабана и одного слоя шаров по другому при этом происходит вращение шаров вокруг их геометрической оси. При заполнении объёма мельницы шаровой нагрузкой на 40—50% скольжение шаров практически отсутствует.
Резкого перехода от чисто каскадного режима к чисто водопадному не наблюдается. Переход происходит постепенно и при промежуточных скоростях вращения мельница работает при смешанном каскадно-водопадном режиме. При таком режиме внешние слои шаров будут падать по параболическим траекториям но не на свои круговые а на внутренние слои скатывающиеся по склону вниз согласно каскадному режиму (рис.2.12).
Рис. 2.12 Траектория движения шаров при смешанном каскадно-водопадном режиме
Можно также выделить ещё один режим работы шаровой мельницы - полное центрифугирование шаров. Он возникает при достижении сверхкритической скорости вращения мельницы определяемой по формуле [2]
где DМ – внутренний диаметр барабана шаровой мельницы.
1.1.6. Обзор возможных способов упрочнения футеровок шаровых мельниц
Из возможных способов повышения износостойкости футеровки наиболее предпочтительными являются наклеп футеровочных плит взрывом и изменение геометрической формы поверхности футеровки.
Наклеп футеровочных плит взрывом. Энергия взрыва повышает износостойкость поверхностей изделий их твердость пределы прочности и текучести статическую прочность (сварных соединений в результате сквозного наклепа сварного шва и зоны термического влияния) циклическую прочность (из-за повышения пределов прочности и текучести материала). Упрочнение при импульсных нагрузках взрывом существенно отличается от упрочнения в обычных условиях. При ударе с большой скоростью свойственной взрыву эффект упрочнения возрастает по мере увеличения скорости удара. В металле могут возникнуть высокие локальные температуры вызывающие фазовые превращения в локальных участках. Одновременно действуют процессы присущие упрочнению при обычных скоростях деформирования такие как двойниковые сдвиги и фрагментация [14]. Принципиальная схема проведения наклепа взрывом представлена на рис.2.13.
Рис. 2.13 Наклеп футеровки взрывом где 1 – детонатор; 2 – взрывчатое вещество; 3 – футеровка шаровой мельницы
Преимущества упрочнения взрывом:
подходит для деталей большого сечения;
позволяет получить большую относительную деформацию металла а соответственно и поверхностную твердость за счет воздействия ударных волн от взрыва;
относительная дешевизна процесса.
операция является опасной так как связана с взрывчатыми веществами соответственно для ее проведения требуется квалифицированные специалисты и специализированные места хранения;
после истирания упрочненного слоя полученного в результате воздействия взрывной волны наблюдается повышенный износ футеровки.
Изменение геометрической формы футеровки шаровой мельницы. Для шаровых мельниц первой стадии измельчения работающих на относительно крупной руде и шарах больших размеров в настоящее время в качестве футеровки цилиндрической части барабана применяют броневые плиты с разнообразными профилями поперечного сечения: волновой Крюкова каскадный балочный ребристый норильский ступенчатый и другие. Это ведет к увеличению номенклатуры выпускаемых литейными цехами деталей и затруднению унификации ремонтных комплектов. Большое количество типов футеровочных плит испытанных на обогатительных предприятиях можно разделить на три группы по геометрическим признакам поперечного сечения (рис.2.14): первая группа — броневые плиты с углом подъема λ. рабочих поверхностей больше 45°; вторая группа — броневые плиты с углом подъема λ рабочих поверхностей меньше 45°; третья группа — самофутерующиеся броневые плиты. Углом подъема рабочих поверхностей λ будем называть угол между касательной к рабочей поверхности футеровки и касательной к окружности радиусом R.
Рис. 2.14 Футеровки различной геометрической формы:а) с углом λ больше 450; б) с углом λ меньше 450; в) самофутерующаяся броневая плита
Анализ справочного материала показывает что износостойкость футеровочных плит с профилями отнесенными к первой группе при прочих равных условиях оказалась выше износостойкости футеровочных плит второй группы. Это объясняется тем что плиты отнесенные к первой группе способны остановить загрузку сразу же после контакта и не допустить проскальзывания по футеровке. По футеровочным плитам второй группы имеет место проскальзывание загрузки о чем говорит образование на их поверхности радиальных канавок — выработок в процессе эксплуатации.
При небольших углах атаки приведенных к гладкой футеровке истинные углы атаки и шаровой загрузки по футеровочным плитам отнесенным к первой группе близки к 90°. При этом осуществляется надежный захват шаров без проскальзывания что обеспечивает повышение производительности мельницы.
Зависимость между углами атаки приведенными к гладкой футеровке и истинными углами атаки выражается уравнением.
Для футеровочных плит с повышенным расходом материала футеровки на тонну измельчаемого сырья характерным является понижение производительности мельницы и увеличение удельного расхода электроэнергии.
Футеровочные плиты отнесенные к третьей группе профилей имеют повышенную износостойкость за счет эффекта заклинивания шаров в пазах. В данном случае после заклинивания изнашивается не футеровка а заклиненные шары. Кроме того повышенной износостойкости этого типа футеровок способствует лучшая прокаливаемость в процессе термической обработки отсутствие рыхлости и микропор в металле [21]. К недостаткам футеровок третьей группы можно отнести повышенный расход шаров а также необходимость в изменении технологической оснастки при производстве футеровочных плит (замена литейных форм или штампов).
Проанализировав представленные выше способы было сделано заключение о целесообразности разработки нового способа повышения износостойкости футеровки лишенного указанных недостатков. Таким способом может служить упрочнение футеровки наклепом от падающих шаров получаемом в процессе работы шаровой мельницы в разработанных режимах без породы.
2.2 Разработка способа упрочнения футеровок шаровой мельницы в процессе ее работы
2.2.1 Определение параметров ударного воздействия шара на футеровочную плиту
Известны [24 27] формулы (2.3 2.4) связывающие диаметр (d) и глубину (h) сферической вмятины образующейся на пластине в результате ударного воздействия шарообразного предмета с параметрами шара (диаметром - D плотностью материала – ρ скоростью в момент удара - V) и пластины (Нд):
– динамическая твердость материала пластины (коэффициент пропорциональности между усилием Р с которым по пластине наносится удар и диаметром d получаемого отпечатка) не зависящая от величины энергии удара и диаметра шара.
В литературе не удалось обнаружить экспериментальных данных по динамической твердости стали Гадфильда. Поэтому значение Нд устанавливали расчетным путем исходя из твердости этого материала при статическом вдавливании шарика.
В соответствии с законом Майера справедливого при вдавливании как для статических так и для динамических испытаний [24 27]
где а0 n – постоянные характеризующие материал пластины.
Поскольку для динамических условий n = 2 [27] с учетом (2.5 2.6)
Исходя из условий проведения замеров твердости материалов по методу Бринелля (Р=30кН Dш=10мм) определяли (2.6) значения постоянной а0 для стали Гадфильда с твердостью 200НВ соответствующей диаметру отпечатка d=426мм [27] для статических условий принимая n=22 [24] которая оказалась равной 1960МПа.
Для перехода от статических к динамическим условиям воспользовались табличными данными [27] о соотношении а0дин и а0 для сталей в соответствии с которыми значение а0дин стали Гадфильда было оценено в 2800МПа а величина Нд рассчитанная по уравнению (2.7) оказалась равной 3567МПа.
Далее устанавливали траекторию движения шара при которой его удар о футеровку будет наноситься нормально к поверхности т. е. будет наиболее эффективным. В соответствии с [2] такая траектория имеет место при водопадном режиме движения шаров в мельнице при скорости вращения барабана Vб=075·Vбкрит=35мс (Vбкрит – скорость вращения соответствующая переходу параболической траектории движения шаров к круговой); при этом угол α отрыва шаров от корпуса барабана равен 55044’. Скорость V шара в момент удара о футеровку рассчитывали из уравнения свободного падения шара брошенного под углом к горизонту от наиболее высокой точки Н траектории до места его соприкосновения с сегментом футеровки (ДП.060955.005СХ)
После подстановки установленных значений Нд и V в уравнения (2.3 2.4) рассчитанные диаметр и глубина сферической вмятины на сегменте из стали Гадфильда полученной от единичного удара мелющего шара оказались равными d=58мм h=02мм.
Поскольку при последующих ударах диаметр лунки увеличивается (как показывают опыты [19] до 15 – 20 ударов) влияние многократного удара учитывалось по формуле (2.10) из [19]
Соответственно глубина наклепанного слоя hн.с с учетом малой кривизны мелющих шаров ( где [19]) оказалась равной ~7мм.
Таким образом при 20 кратном ударе мелющих шаров по стальной футеровке мельниц на футеровке способен образовываться наклепанный слой глубиной 7мм с диаметром кратеров на поверхности ~78мм.
2.2.2 Определение твердости и износостойкости стали после упрочняющей обработки
Исходя из величины относительной деформации () полученной материалом в результате ударного сжимающего воздействия твердость приобретенная наклепанным слоем в соответствии с [19] (ДП.060955.06) была оценена в 325НВ.
На чертеже ДП.060955.006 [22] изображены потери массы образцов из сталей различной твердости при их истирании в барабанах для очистки отливок (продолжительность галтовки 330часов). В этих условиях марганцовистая сталь с начальной твердость 200HB подвергается наклепу до предельной величины твердости ~460HB в результате чего эта сталь приобретает износостойкость мало уступающую белому чугуну. Поскольку условия проведения этих испытаний близки к условиям работы футеровки шаровых мельниц когда материал футеровки подвергается ударно-абразивному износу график на чертеже ДП.060955.06 был использован для определения сравнительной износостойкости футеровки из стали Гадфильда после ее ударной обработки шарами.
Как можно заключить из графика (см. ДП.060955.06) увеличение твердости стали с 200 до 325HB должно повысить её стойкость к истиранию (m200HBm325HB) примерно в 2 раза.
2.2.3 Расчет времени предлагаемой упрочняющей обработки
При расчете времени необходимого для 20 кратной бомбардировки всей поверхности футеровки барабана предполагали что эффективные удары наносят лишь шары внешнего слоя поскольку шары внутренних слоев соударяются с уже лежащими шарами. Количество шаров N во внешнем слое в поперечном сечении барабана мельницы рассчитывали по формуле
где L – длина дуги окружности барабана на которой находятся шары внешнего слоя в статическом положении.
Значение L рассчитанное для степени заполнения барабана φ=30% оказалась равным 55м а количество шаров N=138штук.
Тогда количество ударов по футеровке Nуд в поперечном сечении барабана в единицу времени равно
где ti - время между ударами по футеровке одного и того же шара.
При этом значение ti рассчитывали как сумму времен движения шара по круговой и параболической траекториям по формуле
В соответствии с расчетом значения ti и N оказались равными 27с и 3067ударовмин соответственно.
В предположении что места ударов шаров распределены по длине окружности барабана равномерно и по каждой точке окружности для эффективного наклепа необходимо нанести 20 ударов необходимое время бомбардировки tΣ составляет
2.2.4 Определение допустимого времени эксплуатации шаровой мельницы между упрочняющими наклепами
Расчет допустимого времени эксплуатации мельницы между упрочняющими наклепами проводили с использованием экспериментальных данных [18] о скорости износа футеровки из стали Гадфильда с твердостью 200HB в условиях работы шаровых мельниц: Vизн200HB=00054ммч (данная экспериментальная скорость износа оказалась сопоставима с эксплуатационной скоростью износа шаровой мельницы МШЦ-4500×6000 работающей по магнетиту) что с учетом упрочняющей обработки составляет Vизн325HB=Vизн200HB19=00028ммч.
Исходя из того что максимальная твердость наклепанного слоя распространяется примерно на четверть его глубины [25] в качестве допустимой толщины наклепанного слоя который может быть подвергнут истиранию была принята величина
hдоп=025h н.с=18мм. (2.15)
Отсюда заключаем что время в течение которого футеровка мельницы может изнашиваться на допустимую величину hдоп совпадающее с периодом между проведениями упрочняющего наклепа составляет
tм.у.н.=hдопV изн325HB =643ч27суток. (2.16)
Таким образом для повышения срока службы футеровочных плит из стали Гадфильда (в 19 раза) требуется проведение периодических (в течении ~ 12минут) упрочняющих обработок футеровки шарами с периодом между упрочняющими обработками 27суток.
2.2.5 Увеличение срока эксплуатации футеровочных плит в результате упрочняющей обработки
Исходя из того что футеровку мельницы МШЦ-4500×6000 меняют при полном износе гребня «волны» (т.е. когда поверхность футеровки становится абсолютно гладкой) до толщины в 81-87мм срок службы плиты составит порядка 700суток а количество упрочняющих обработок Nупр~28.
Необходимо отметить что предлагаемая работа мельницы без загрузки породы не противоречит нормативным документам по эксплуатации шаровых мельниц: при пуске мельниц после капитального или текущего ремонта ее проверяют на работоспособность без породы при загрузке шарами полной загрузочной массы в течение 20минут [9 13].
2.2.6 Увеличение срока эксплуатации футеровочных плит в результате упрочняющей обработки
2.2.7 Влияние предлагаемых режимов работы мельницы на работоспособность ее основных конструктивных элементов
Поскольку при работе мельницы без породы динамические нагрузки на ее конструктивные элементы существенно возрастают представлялось необходимым рассчитать эти нагрузки и проверить их соответствие допустимым. Расчет проводился для радиального подшипника – как наиболее чувствительного элемента мельниц к динамическим нагрузкам.
Расчет производился исходя из удельной нагрузки р в подшипнике [3].
Удельная нагрузка в подшипнике МПа
где d и [р] – допустимая удельная нагрузка (4 МПа); P – сила действующая на подшипник Н.
Расчет Р проводился исходя из массы отдельных частей мельницы и шаровой загрузки с учетом возникающей центробежной силы а также сил в зацеплении зубчатой передачи.
Вес отдельных частей мельницы МШЦ4500×6000 устанавливали из параметров однотипной (эталонной) мельницы (массы отдельных конструктивных элементов которой известны и приведены в литературе) в предположении об их геометрическом подобии. В качестве эталонной была использована мельница МШЦ2700×3600 со следующими параметрами: масса питателя 2т; масса барабана 165т; масса загрузочной части 83т; масса разгрузочной части 12т; масса зубчатого венца 84т. Определив коэффициент геометрического подобия:
где К = D DЭ были найдены следующие параметры мельницы:
вес загрузочной части
вес разгрузочной части
Вес шаровой загрузки при заданной величине коэффициента φ=30% определяется по формуле
где ρш – плотность шаров в насыпке (в массе); принимается равной 46тм3; V – объем барабана шаровой мельницы МШЦ4500×6000 (82м3).
Величина центробежной силы развиваемая массой вращающихся с мельницей шаров зависит прежде всего от режима работы мельницы.
При каскадном режиме вся масса шаров – GШ g – вращается с обечайкой. При смешанном и водопадном режимах с обечайкой вращается лишь часть шаровой загрузки. Данные о количестве шаров на круговой и параболической траекториях при различных относительных скоростях приведены в табл. 2.1.
При работе мельницы в предлагаемом режиме она будет иметь следующие параметры: α – угол отрыва шаров от корпуса барабана α=560=098рад.; – действительная рабочая скорость вращения мельницы (в процентах от критической) =75%; NК – относительное количество шаров данного слоя находящихся на круговой траектории NК=565%; NП–относительное количество шаров данного слоя находящихся на параболической траектории NП=436%.
Количество шаров на круговых и параболических траекториях
Относительное количество шаров данного слоя (с углом отрыва α) находящихся на круговой (NК) и параболической (NП) траекториях можно найти из следующих зависимостей:
Чтобы учесть действие всей массы загрузки перемещающейся с барабаном в рассмотрение вводится редуцированный слой находящийся от оси вращения барабана на расстоянии где R – радиус барабана в свету. Этот слой динамически заменяет всю массу вращающейся части шаровой загрузки. Таким образом центробежная сила найдется из выражения (рис. 2.13)
Рис.2.13 Расчетная схема для определения центробежной силы
Направление действия этой силы принимается под углом γ = 25 к горизонту. Составляющие этой силы: горизонтальная – PЦГ=РЦ·соsγ и вертикальная – РЦВ=РЦ·sinγ соответственно равны 249кН и 116кН.
В шаровой мельнице МШЦ 4500×6000 применяется открытая косозубая передача соответственно в месте контакта зубьев шестерни и зубчатого венца действуют три составляющие силы – окружная радиальная и осевая информация о которых необходима для расчета опорных реакций на подшипник.
Определение делительных диаметров:
Определение вращающих моментов на валах зубчатой передачи без учёта потерь на трение:
электродвигатель СД: Pдв=2500кВт; n=150мин-1.
Расчетная схема сил действующих в горизонтальной и вертикальной плоскости при работе шаровой мельницы МШЦ4500×6000 имеет вид (рис.2.14)
Рис. 2.14 Расчетная схема сил действующих в горизонтальной и вертикальной плоскости при работе шаровой мельницы МШЦ4500×6000
Результаты расчета опорных реакций шаровой мельницы выполненные по разработанной схеме (рис.2.14) а также их проверки представлены ниже:
Уравнение моментов сил относительно т. A:
где qв – распределенная нагрузка (от веса барабана Gб и вертикальной составляющей центробежной силы Pцв)
Уравнение моментов сил относительно т. B:
Реакции в т. A и т. B в результате расчетов соответственно составили:
где qг – распределенная нагрузка возникающая от горизонтальной составляющей центробежной силы Pцг.
Суммарная реакция в опоре A и B:
Реакции возникающие в процессе работы мельницы в предлагаемом режиме можно определить по следующей формуле:
где kдин – коэффициент характеризующий влияние динамики на реакции в подшипниках kдин2÷3.
Динамические реакции в опорах A и B:
На подшипник находящийся в т.A действует сила RAдин=PA=2946000Н на подшипник находящийся в т.B действует сила RBдин=PB=4704000Н.
Таким образом удельная нагрузка на подшипник в т.A:
и удельная нагрузка на подшипник в т.В:
при предлагаемых режимах эксплуатации мельницы оказались меньше допустимых (рдоп=4МПа).
Результаты расчетов по увеличению срока службы футеровки шаровой мельницы приведены на плакате ДП.060955.003.
2 Увеличение срока службы вал-шестерни
2.1 Постановка задачи
В настоящее время для снижения износа зубьев применяется «ручной» метод смазки когда смазка наносится парциально лопаткой на каждый зуб вал-шестерни во время проведения планово-предупредительного ремонта (ППР) который проводится раз в месяц. Поскольку при такой системе слой смазки не обновляется большой период времени и в ней накапливается абразив. В результате смешивания смазки с абразивом наблюдается повышенный износ зубьев вал-шестерни.
Для увеличения износостойкости зубьев в настоящем проекте разрабатывается система подачи смазки при которой отработавший слой смазки загрязненный абразивом будет непрерывно заменяться новым слоем смазки без абразива.
Осуществлять обновление смазки предлагается за счет ее периодической принудительной подачи в зону зацепления. Данный процесс можно осуществить системой подачи смазки технологическая схема которой представлена на чертеже (ДП.060955.06).
Система подачи (ДП.060955.007СХ) включает следующие элементы:
- рассеиватель (1) с помощью которого наносится смазка на поверхность зубьев представляющий собой горизонтальный цилиндр длиной равной ширине зуба с равномерно расположенными отверстиями (рис. 2.15) по своей длине;
- шланги (2) подводящие смазку к зубчатому зацеплению и рассеивателю;
- цилиндр (3) наполненный консистентной смазкой (солидолом);
- поршень (4) который вытесняет смазку из полости цилиндра при подаче на его внешнюю поверхность сжатого воздуха;
- подводящие шланги (5);
- баллон со сжатым воздухом (6).
Рис. 2.15 Рассеиватель смазки
Чтобы рассчитать данную систему подачи смазки необходимо знать расход смазки время и давление с которым необходимо воздействовать на поршень.
2.2 Определение необходимого расхода смазки
При установлении необходимого расхода смазки исходили из того что ее количество на эвольвентной поверхности вал-шестерни должно быть достаточным для обеспечения жидкостного трения. При таком виде трения сопряженные детали машин работают при непрерывной масляной пленке что способствует уменьшению износа.
Жидкостное трение т.е. полное разделение трущихся поверхностей слоем масла достигают непрерывной и принудительной подачей масла в зазор между трущимися поверхностями. Толщина масляного слоя измеряется при этом сотыми а иногда десятыми долями миллиметра [28].
Исходя из указанного выше условия примем толщину масляного слоя равную S=100мкм=1·10-4м.
Рассчитаем необходимый объем смазки наносимый на один зуб для этого сначала определим площадь боковой поверхности зуба
где Kб.п.з – коэффициент учитывающий эвольвентный профиль боковой поверхности зуба (принимается равным 13); H – ширина зубчатого венца вал-шестерни H=820мм; h – высота зуба h=449745мм.
Объем наносимого масляного слоя на одну боковую сторону зуба необходимый для создания в зубчатом зацеплении жидкостного трения
При жидкостном трении объем масла для нанесения на две боковые стороны составит
Количество смазочного материала необходимого для нанесения на все зубья (35 зубьев) вал-шестерни и все зубья зубчатого венца (316 зубьев)
где t – время одного оборота зубчатого венца t=36с.
2.3 Определения давления на смазку на выходе из отверстий рассеивателя
Скорость истечения потока масла через отверстия в рассеивателе
где - общая площадь отверстий рассеивателя N – количество отверстий в рассеивателе N=81 d – диаметр отверстия рассеивателя d=00008 м.
Давление масла на выходе из отверстий рассеивателя
где γ – коэффициент характеризующий гидравлические сопротивления γ=145 ρ – плотность масла ρ=09.
Необходимый объем емкости со смазочным материалом можно рассчитать из следующих условий:
смазка подается через каждые 24000 оборота зубчатого венца что соответствует одному разу в сутки;
время подачи смазки соответствует времени одного полного оборота венца (t=36с);
объем масла в емкости на межремонтный период (планово-предупредительный ремонт шаровой мельницы проводят один раз в месяц).
Исходя из указанных выше условий объем емкости равен
где N – количество смазок зубчатой передачи.
Схема предлагаемой системы смазки представлена на чертеже ДП.060955.004СХ.
ГЛАВА 3 ТЕХНОЛОГИЯ РЕМОНТА ВАЛ-ШЕСТЕРНИ
Износ вал-шестерни происходит главным образом в месте её зацепления с венцом шаровой мельницы т. е. в месте контакта зубьев. Так направление вращения шестерни неизменно происходит односторонний износ боковой поверхности зуба.
Основные причины износа зубьев вал-шестерни:
попадание в места контакта зубьев вал-шестерни и венца абразивной пульпы из мельницы которая попадает туда вследствие плохой герметизации болтового соединения корпуса шаровой мельницы с внутренней футеровкой;
несоосность вал-шестерни и венца;
неточность изготовления вал-шестерни;
несвоевременная смазка;
ненадлежащие ТО и Р.
Устранение описанных выше причин износа приведет к его уменьшению а соответственно и увеличению срока службы вал-шестерни.
В данном курсом проекте будет рассмотрен вариант восстановления профиля зуба вал-шестерни.
Зубчатые колеса подлежат замене при износе зубьев по толщине на делительном диаметре более 30 % для любых передач с чугунными колесами и открытых передач со стальными колесами [7].
1 Химический состав и механический свойства материала изготовления вал-шестерни
Материалом изготовления вал-шестерни является легированная сталь 34ХН3М химический состав которой представлен в табл. 3.1 а механические свойства данной стали представлены в табл. 3.2.
Химический состав стали
Механические свойства стали
2 Определение критического износа зубьев вал-шестерни
Зубчатые колеса подлежат замене при износе зубьев по толщине на делительном диаметре более 30 % для открытых передач со стальными колесами [7]. Поэтому исходя из этого условия толщину критически изношенного зуба Sкрит можно рассчитать по следующей формуле:
где Sx = 29мм – толщина зуба по хорде (при высоте до хорды hx = 19мм).
3 Порядок восстановления зубьев вал-шестерни
ручная электродуговая наплавка;
отделочная зубообработка на фрезерном станке 5А342.
4 Подготовка вал-шестерни к технологическим операциям
Для выполнения ремонта необходимо выявление дефектов и пороков детали. Выявление дефектов предусматривает выполнение следующих работ:
- промывка от следов смазки и ржавчины;
- тщательный осмотр и проверка повреждений а также мелких дефектов.
Качество очистки деталей влияет на их восстановление и дефектацию. Выбор способа очистки зависит от конфигурации и размеров детали вида ее загрязнения. Несмотря на различную природу все загрязнения (масла и смазки нагар лаковые отложения продукты коррозии и т.д.) обладают высокой адгезией (прилипаемость).
Для удаления следов смазки деталь промывается керосине или в обезжиривающих растворах. Деталь со следами ржавчины погружаем в керосин на 6-8 часов (либо в емкость с керосином подается под давлением перегретый водяной пар тогда время очистки детали от смазки значительно сокращается) после чего деталь протирается обтирочными материалами (ветошью) насухо.
После промывки проводится дефектация по её результатам детали разделяют на три группы:
Годные детали размеры которых лежат в пределах допустимых величин. Их отправляют на сборку или склад готовой продукции.
Детали подлежащие ремонту износ и повреждения которых могут быть исправлены. Их отправляют на ремонт или склад деталей ожидающих ремонта.
Детали забракованные. Восстановить их невозможно или экономически нецелесообразно. Их отправляют на склад утиля как лом.
В результате осмотра выявляем степень износа зубьев шестерни и определяем целесообразность ремонта.
Зубчатые колеса не подлежат восстановлению если имеются поломанные зубья трещины питинг на большом числе зубьев отслоения на рабочей стороне зубьев цементированного слоя.
Поверхности детали которые необходимо сохранить от брызг и налетов окислов закрывают сухим или мокрым асбестом [7].
По результатам осмотра зубьев вал-шестерни составляют дефектовочную карту (табл.3.3)
Номер позиции на эскизе
Наиме-нование дефекта
Способ установления дефекта
Номинальные размеры мм
Допус-тимые размеры без ремонта мм
Размеры допус-тимые для ремонта мм
Отделочная зубообработка на фрезерном станке
5 Параметры ручной электродуговой наплавки
5.1 Выбор диаметра dэ электрода
Наплавка вал-шестерни осуществляется от сварочного генератора или выпрямителя при постоянном токе при обратной полярности подключения т. к. обратная полярность рекомендуется для большинства марок качественных электродов [8].
При наплавке (особенно электродами ОЗН) перегрев наплавленного слоя не допускается. Для этого слой наплавляют отдельными валиками с полным последовательным охлаждением каждого валика. Положение электрода при наплавке должно соответствовать изображенному на рис. 3.
Рис. 3.1 Положение электрода при наплавке отдельными валиками
Для ручной дуговой наплавки применяют как специальные наплавочные электроды так и обычные сварочные предназначенные для сварки легированных сталей (ГОСТ 1005-75).
При наплавке регламентируют только два параметра режима – диаметр электрода и наплавочный ток. Длина дуги составляет обычно 05 11 от диаметра электрода и выдерживается сварщиком вручную. Лучшее качество наплавки обеспечивает короткая дуга [8].
Диаметр электрода dэ выбирают исходя из толщины наплавляемого слоя S. В случае работы шаровой мельницы вал-шестерня вращается только в одну сторону соответственно изнашиваться будет только одна сторона зуба вал-шестерни. Исходя из этого толщина наплавляемого слоя на изношенную сторону будет составлять S=87мм с учетом запаса на последующую механическую обработку общая толщина наплавляемого слоя составит Sобщ=10мм диаметр электрода dэ=4мм.
5.2 Расчет массы наплавленного металла и количество необходимых для наплавки электродов
Площадь боковой поверхности зуба:
Объем наплавляемого металла:
где S – толщина наплавляемого слоя металла Sобщ=10мм.
Масса наплавленного металла:
где ρ – плотность наплавляемого материала (для стали 78·103 кгм3).
Необходимая масса электродного материала:
Масса рабочей части электрода (Lэл=420мм) диаметром 4мм стандартной длины:
где Fэл – площадь электрода.
Количество электродов необходимое для наплавки одного зуба:
С учетом того что вал-шестерня имеет 35 зубьев количество электродов составит:
5.3 Установление силы наплавочного тока основного времени наплавки эффективной мощности дуги
Наплавочный ток ориентировочно рассчитывается по следующей упрощенной формуле
При зажигании дуги напряжение Uд между электродом и свариваемой деталью составляет примерно 60 В. При замыкании сварочной цепи оно падает до нуля а после возбуждения дуги поддерживается в пределах 16 30В в зависимости от длины дуги и марки электрода. Так для стальных электродов напряжение дуги может быть вычислено по формуле
где a=15В; b=3В; l=07·dэ=07·4=28мм.
При установившемся процессе наплавки плавление электрода под действием дуги происходит равномерно:
где gн.м - масса расплавленного электродного металла gэ.м=1625г; αр- коэффициент расплавления αр=10г(А ч); I – сила тока I=120А; t - время горения дуги ч.
Преобразовав (11) получается что время горения дуги и соответственно время наплавки одного зуба составляет
Общее время горения дуги на наплавку 35 зубьев
Эффективная мощность дуги (мощность расходуемая на нагрев металла)
где А - эффективный КПД процесса нагрева металла (07 085); Q0 - полная мощность выделяющаяся в столбе дуги Q0=IUд=120·234=2808Вт [2].
5.4 Выбор сварочного аппарата
Для наплавки выбирается сварочный аппарат РусичС300 со следующими техническими характеристиками (табл.3.4).
Технические характеристики сварочного аппарата РусичС300
Диапазон питающей сети
Напряжение холостого хода
переменный постоянный
АС 20-300 А DC 20-230 А
Продолжительность нагрузки в режиме сварки при максимальном сварочном токе
Выходная мощность в режиме сварки
Пределы регулирования
5.5 Выбор подходящей марки электрода
Металлические электроды для сварки представляют собой пруток из сварочной проволоки называемый стержнем электрода1 (рис. 3.2) на который нанесен слой покрытия2.
Рис. 3.2 Металлический толстопокрытый электрод: 1 — стержень 2 — покрытие
Электроды с диаметром стержня dэ=4мм имеют стандартную длину lэ=450мм. Один конец электрода на длине 30 40мм оставляют свободным от покрытия (рис. 1) для закрепления электрода в держателе и подведения сварочного тока [2].
Для наплавки боковой поверхности зубьев вал-шестерни выбирается наплавочная проволока того же состава или близкая по механическим свойствам к основному материалу изготовления это связано с необходимостью поддержания разных твердостей зубьев у вал-шестерни и венца шаровой мельницы.
Наплавка осуществляется электродной проволокой 4 Н-34ХН3М условное обозначение электрода:
Стальная наплавочная проволока диаметром 4 мм содержащая в своем составе ~ 034%С 1%Cr 3%N Т - 590— марка электрода; 40 — диаметр электрода мм; Н — для наплавки легированных сталей; Д - с толстым покрытием второй группы качества; 30 — предел прочности материала сварного шва (300МПа); 1 — относительное удлинение 18 %; 5 — ударная вязкость не менее 343 Джсм2; Б — с основным покрытием; 4 - для наплавки в нижнем положении; 0 - на постоянном токе обратной полярности.
6 Параметры фрезерования
Для фрезерования может быть использован станок 5А342 (рис. 3.3) который предназначен для фрезерования зубьев цилиндрических зубчатых колес методом обкатки червячной фрезой и методом единичного деления дисковой или пальцевой фрезами. основные технические характеристики которого представлены в табл.3.5.
Рис. 3.3 Общий вид зубофрезерного станка 5А342
Технические характеристики станка 5А342
Наибольший диаметр обрабатываемых цилиндрических зубчатых колес мм
Наибольшая длина вертикального перемещения фрезерного суппорта мм
Наибольший модуль обрабатываемого колеса (не менее) мм:
Наибольший угол наклона линии зуба обрабатываемых зубчатых колес град
Наибольшая масса устанавливаемой заготовки (с учетом массы закрепляющих элементов) кг
Наибольший диаметр устанавливаемых червячных фрез мм
Наибольшая длина устанавливаемых червячных фрез мм
Пределы чисел нарезаемых зубьев
Пределы частоты вращения шпинделя обмин
Пределы осевых подач мммин:
Пределы радиальных подач мммин
Наибольший крутящий момент на шпинделе (не менее) кН.м
Продолжение таблицы 3.5
Род тока питающей сети
Переменный трехфазный
Номинальная частота Гц
Номинальное напряжение В
Мощность привода главного движения (не менее) кВт
Габаритные размеры станка мм:
- высота над уровнем пола
Технологическая карта по фрезерованию восстановленной поверхности шестерни представлены в приложении2.
На ремонтном чертеже (ДП.060955.009) представлена последовательность технологических операций для восстановления изношенных зубьев вал-шестерни.
ГЛАВА 4. ЭЛЕКТРИЧЕСКАЯ ЧАСТЬ
В данной части дипломного проекта была рассчитана схема электроснабжения участка измельчения дробильно-обогатительной фабрики (ДОФ). Паспортные данные электроприемников которые находятся на участке измельчения представлены в табл. 4.1.
Паспортные данные электроприемников
Стержневая мельница с центральной разгрузкой МСЦ3600×5500
Шаровая мельница с центральной разгрузкой МШЦ4500×6000
Конвейер ленточный (длинный)
Конвейер ленточный (короткий)
Магнитный сепаратор ПБМ-ПП-90-250
Магнитный дешламатор МД-9
Примечание. KП - кратность пускового тока
IПУСК - пусковой ток; IНОМ - номинальный ток.
1 Определение типа и мощности трансформатора для гпп
Принимаем к установке трансформатор типа ТРДЦН. Мощность трансформатора (Sтр) определяем методом коэффициента спроса [29].
Для однотрансформаторной подстанции Sтр > Sр
где Sp - полная расчётная мощность электроприемников:
Рр – активная расчётная мощность электроприемников; cosφср.взвеш – средневзвешенный cosφ.
Средневзвешенный cosφ определяется из выражения
В соответствии с методом коэффициента спроса расчётная активная мощность определяется
Коэффициент спроса Kс определяется по эмпирической формуле
где РН.max – максимальный по мощности из установленных электроприемников участка измельчения
По формуле (2.1) определяем
По рассчитанной мощности всех электроприемников Sp выбирается трансформатор ТРДЦН-63000110-У1 технические характеристики которого представлены в табл. 4.2.
Серия трансформатора
Номинальное напряжение (ВН первичное) кВ
Номинальное напряжение (НН вторичное) кВ
Номинальная мощность кВА
Активное сопротивление трансформатора Ом
Индуктивное сопротивление трансформатора Ом
2 Выбор типа и сечения высоковольтного кабеля
Принимаем к установке высоковольтный сталеалюминиевый провод АС. Сечение токоведущих жил кабеля выбирается по допустимой токовой нагрузке т.е. нужно выбрать такое сечение которому соответствует допустимый ток ближайший больший расчетного тока.
Учтём возможный рост нагрузки участка до полной мощности трансформатора ТРДЦН-80000110-У1. В этом случае расчётный ток высоковольтного кабеля определяется по номинальной мощности трансформатора.
Из табл.79 [11 с. 120] выбираем сечение сталеалюминиевого провода АС-150 на 110 кВ S=227мм2 у которого величина допустимого тока IД = 445А.
Окончательно принимаем к установке кабель АС-150 1×227.
Погонные сопротивления выбранного кабеля из табл. 79 [11 с. 120] и табл. 83 [1 с.123]:
Сопротивление высоковольтных кабелей приведённое к напряжению высоковольтных электроприемников участка измельчения
где Uб - базисное напряжение (в данном примере Uб = Uн); Uср - номинальное напряжение увеличенное на 5%.
3 Выбор типа и сечения фидерного кабеля
Принимаем к установке высоковольтный кабель марки ААШВ. Сечение токоведущих жил кабеля выбирается по допусртимому нагреву изоляции т.е. нужно выбрать такое сечение которому соответствует допустимый ток ближайший больший расчетного тока.
Из табл.86 [11 с. 125] выбираем сечение кабеля ААШВ на 6 кВ S= 300 мм2 у которого величина допустимого тока IД=1000А.
Поскольку выбираем 8 кабелей S=300мм2 включенных параллельно. В этом случае суммарный допустимый ток составит IД=8·1000=8000А.
Окончательно принимаем к установке кабель ААШВ 8×300.
Погонные сопротивления выбранных кабелей из табл. 93 [11 с. 130]:
4 Выбор типа и сечения кабеля подводимого к шаровым и стержневым мельницам
Принимаем к установке высоковольтный кабель марки ААШВ.
Сечение токоведущих жил кабеля выбирается по нагреву изоляции т.е. нужно выбрать такое сечение которому соответствует допустимый ток ближайший больший номинального тока соответствующего приёмника:
4.1 Выбор сечения кабеля для стержневой мельницы мсц 3600×5500
Величина номинального тока стержневой мельницы
Из табл. 86 [11 с. 125] выбираем сечение кабеля ААШВ на 6 кВ S=50мм2 у которого величина допустимого тока IД = 145 А.
Окончательно принимаем к установке кабель ААШВ 1×50.
Погонные сопротивления выбранного кабеля из табл. 94 [1 с. 130]
Сопротивление кабеля для стержневой мельницы
4.2 Выбор сечения кабеля для шаровой мельницы мШц 4500×6000
Величина номинального тока шаровой мельницы
Из табл. 86 [11 с. 125] выбираем сечение кабеля ААШВ на 6 кВ S=150мм2 у которого величина допустимого тока IД = 290 А.
Окончательно принимаем к установке кабель ААШВ 1×150.
5 Определение типа и мощности трансформатора для низковольтной линии
Принимаем к установке трансформатор типа ТМ. Мощность трансформатора (Sтр) определяем методом коэффициента спроса.
где Sp – полная расчётная мощность электроприемников:
Рр - активная расчётная мощность электроприемников; cosφср.взвеш – средневзвешенный cosφ.
По формуле (2.23) определяем
Нагрузка на низковольтной линии равномерно распределяется между двумя трансформаторами ТМ 630035-6 технические характеристики которого представлены в табл. 4.3.
6 Выбор типа и сечения шины
Принимаем к установке шину из алюминиевого сплава марки АД31-Т1.
Сечение шины выбирается по нагреву изоляции т.е. нужно выбрать такое сечение которому соответствует допустимый ток ближайший больший расчетного тока.
Величина расчетного тока
Из табл.102 [11 с. 141] выбираем шинопровод труба№30210190 (шина из алюминиевого сплава марки АД31-Т1) S = 6200 мм2 у которого величина допустимого тока IД=7580А.
Окончательно принимаем к установке шину АД31-Т1.
Погонные сопротивления выбранной шины из табл. 102 [1 с. 141]:
Сопротивление шины приведенное к напряжению низковольтной линии участка измельчения
7 Выбор типа и сечения кабеля подводимого к низковольтным электроприемникам
Принимаем к установке низковольтный кабель марки ПВ.
Сечение токоведущих жил кабеля выбирается по нагреву изоляции т.е. нужно выбрать такое сечение которому соответствует допустимый ток ближайший больший номинального тока соответствующего электроприёмника:
7.1 Выбор сечения гибкого кабеля для конвейера ленточного (длинного)
Величина номинального тока ленточного конвейера (длинного)
Из табл. 86 [11 с. 125] выбираем сечение кабеля ПВ на 038 кВ S=35мм2 у которого величина допустимого тока IД = 200 А.
Поскольку выбираем три кабелей S = 35 мм2 включенных параллельно. В этом случае суммарный допустимый ток составит IД = 3·200 = 600А.
Окончательно принимаем к установке кабель ПВ 3×35.
Погонные сопротивления выбранного кабеля из табл. 93 [11 с. 130]
Сопротивление кабеля для конвейера (длинного)
7.2 Выбор сечения гибкого кабеля для конвейера ленточного (короткого)
Величина номинального тока ленточного конвейера (короткого)
Из табл. 86 [11 с. 125] выбираем сечение кабеля ПВ на 038 кВ S=70мм2 у которого величина допустимого тока IД = 305 А.
Окончательно принимаем к установке кабель ПВ 1×70.
Погонные сопротивления выбранного кабеля из табл. 93 [1 с. 130]
Сопротивление кабеля для конвейера (короткого)
7.3 Выбор сечения гибкого кабеля для магнитного сепаратора ПБМ-ПП-90-250
Величина номинального тока сепаратора
Из табл. 86 [11 с. 125] выбираем сечение двухжильного кабеля ПВ на 038 кВ S=25мм2 у которого величина допустимого тока IД = 30 А.
Окончательно принимаем к установке кабель ПВ 1×25.
Сопротивление кабеля для сепаратора
7.4 Выбор сечения гибкого кабеля для гидроциклона гц-500
Величина номинального тока гидроциклона
Из табл. 86 [11 с. 125] выбираем сечение кабеля ПВ на 038 кВ S=6мм2 у которого величина допустимого тока IД = 75 А.
Окончательно принимаем к установке кабель ПВ 1×6.
Сопротивление кабеля для гидроциклона
7.5 Выбор сечения гибкого кабеля для гидроциклона гц-710
Из табл. 86 [11 с. 125] выбираем сечение кабеля ПВ на 038 кВ S=10мм2 у которого величина допустимого тока IД = 95 А.
Окончательно принимаем к установке кабель ПВ 1×10.
7.6 Выбор сечения гибкого кабеля магнитного дешламатора мд-9
Величина номинального тока дешламатора
Из табл. 86 [11 с. 125] выбираем сечение кабеля ПВ на 038 кВ S=25мм2 у которого величина допустимого тока IД = 160 А.
8 Проверка сети по потере напряжения
В соответствии с ГОСТ 13109-97 напряжение на зажимах электроприёмников в нормальном установившемся режиме должно быть не менее 95% от Uном.
Для проверки этого требования необходимо определить потери напряжений на всех участках сети от источника до наиболее мощного и удалённого электроприемника.
Потеря напряжения складывается из потерь напряжений на отдельных участках
где ΔUВК - потеря напряжения в высоковольтном кабеле; ΔUТР1 и ΔUТР2 - потеря напряжения в трансформаторах соответственно в ТРДЦН-80000110-У1 и в ТМ 630035-6; ΔUШ - потеря напряжения в шине; ΔUГК1 и ΔUГК2 - потеря напряжения в гибких кабелях.
При определении ΔU следует учитывать 5% добавку напряжения от трансформатора
Если условие не выполняется необходимо усилить кабель на каком-либо участке.
8.1 Потеря напряжения в высоковольтном кабеле
Упрощённое выражение для определения ΔUВК:
8.2 Потеря напряжения в фидерном кабеле
8.3 Потеря напряжения в трансформаторе трдцн-80000110-у1
8.4 Потеря напряжения в трансформаторе ТМ 630035-6
8.5 Потеря напряжения в кабеле наиболее мощного электроприемника высоковольтной линии
В данном случае это шаровая мельница МШЦ 4500×6000
8.6 Потеря напряжения на шине низковольтной линии
8.7 Потеря напряжения в гибком кабеле наиболее мощного электроприемника низковольтной линии
В данном случае таким приемником является ленточный конвейер (длинный).
8.8 Суммарные потери напряжения
С учетом 5% добавки напряжения от трансформатора требования ГОСТа выполняются.
Проверка сети в режиме пуска
Проверяется режим пуска наиболее мощного электродвигателя (в данном случае шаровой мельницы МШЦ 4500×6000).
Напряжение на зажимах электродвигателя в режиме пуска не должно опускаться ниже допустимых значений .
Для упрощения принимаем величину .
Для мельницы величина пускового тока .
Вывод: Условие пуска выполняется.
Расчет величины токов короткого замыкания
Для выбора автоматического фидерного выключателя необходимо знать величину возможного тока трёхфазного короткого замыкания непосредственно за выключателем. Поэтому в расчётную схему войдут сопротивления высоковольтного кабеля трансформатора и фидерного кабеля.
В результате расчета величина возможного тока трёхфазного короткого замыкания непосредственно за фидерным выключателем IКЗ1 оказался равным 22414 А.
Для выбора пускателей и уставок срабатывания максимальной токовой защиты на высоковольтной линии необходимо знать величины трехфазных коротких замыканий на зажимах электродвигателей. Поэтому в расчётную схему войдут сопротивления высоковольтного кабеля трансформатора фидерного кабеля и гибкого кабеля до соответствующего электродвигателя (стержневой IКЗСМ и шаровой IКЗШМ мельницы).
По результатам расчет IКЗСМ и IКЗШМ оказались соответственно равны 12460 и 16833А.
Для выбора автоматического выключателя на шине низковольтной линии необходимо знать величину возможного тока трёхфазного короткого замыкания непосредственно за выключателем. Поэтому в расчётную схему войдут сопротивления возникающие на высоковольтной линии (высоковольтный кабель высоковольтный трансформатор и фидерный кабель) и сопротивления на низковольтной линии (низковольтный трансформатор и шина).
В результате расчета величина возможного тока трёхфазного короткого замыкания на низковольтной линии непосредственно за выключателем на шине IКЗ2 оказался равным 1117А.
Для выбора пускателей и уставок срабатывания максимальной токовой защиты на низковольтной линии необходимо знать величины трехфазных коротких замыканий на зажимах электродвигателей. Поэтому в расчётную схему войдут сопротивления высоковольтной и низковольтной линии и гибкого кабеля до соответствующего электродвигателя (ленточного конвейера (длинного) IКЗКД ленточного конвейера (короткого) IКЗКК магнитного сепаратора IКЗС гидроциклонов ГЦ-500 IКЗГ5 и ГЦ-710 IКЗГ7 магнитного дешламатора IКЗД).
Результаты расчета токов короткого замыкания электроприемников на низковольтной линии представлены в табл. 4.4.
Рассчитанная схема электроснабжения участка измельчения ДОФ представлена на чертеже ДП.060955.006СХ.
Выбор коммутационных аппаратов
Выбранные коммутационные аппараты представлены в приложении 3.
ГЛАВА 5 ОХРАНА ТРУДА
1 Вредные и опасные факторы на обогатительной фабрике
При работе технологического электрического и подъемно-транспортного оборудования обогатительной фабрики существует ряд объективных причин вызывающих несчастные случаи на производстве и профессиональные заболевания [30].
К вредным факторам относятся:
Промышленная пыль - это совокупность твердых частиц образующихся при дроблении грохочении перегрузке руды и находящихся во взвешенном состоянии.
Вибрация - возникает при работе грохотов дробилок мельниц насосов вредно действует на обслуживающий эти механизмы персонал. Вибрация общая и локальная передается через металлоконструкции при непосредственном контакте.
Производственный шум - возникает при работе дробилок мельниц насосов и другого оборудования. Оказывает вредное влияние на органы слуха и центральную нервную систему снижает производительность труда рабочих.
К опасным факторам относится:
механические привода дробилок грохотов мельниц питателей ленточных конвейеров и т.п. движущиеся части машин и механизмов;
возможные обрывы тросов подъемно-транспортного оборудования и падение грузов при их перемещении;
электрический ток наличие установок с напряжением свыше 1000 В
вылет кусков из дробилок.
Процессы безопасности всех тяжелых и трудоемких работ на обогатительной фабрике решаются механизацией и автоматизацией.
2 Анализ травматизма и профессиональной заболеваемости
Численность пострадавших при несчастных случаях на ДОФ за2010 г.
Аналогичный период прошлого года
Среднесписочная численность
Количество несчастных случаев
Групповыхиз них пострадавших
Кч - коэффициент частоты
Кт- коэффициент тяжести
Ущерб от травм (выплаты по больничному листу)
Выполнено мероприятий по устранению причин несчастного случая
Сведения о профессиональной заболеваемости и степени утраты профессиональной пригодности представлены соответственно в табл. 5.2 и табл. 5.3.
Сведения о профессиональной заболеваемости на 2010г. по ДОФ
Зарегистрировано добавилось
Вибрационная болезнь
Заболевание опорнодвигательного аппарата
Токсическая энцефалопатия
Аллергическая болезнь
Сведения о степени утраты профессиональной пригодности работниками по ДОФ
Степень утраты профессиональной пригодности
Продолжение таблицы 5.3
За минувший 2010 год у трёх работников ДОФ выявлено проф. заболевание с утратой проф. пригодности у одного из них на 10%.
На начало 2011г. на ДОФ работает 21 человек с профессиональным заболеванием у семи из них отмечена утрата профессиональной пригодности на 10%.
3 Мероприятия по соблюдению безопасности работ
Все вновь прибывшие на работу проходят медицинское освидетельствование и вводный инструктаж по ТБ. Повторный инструктаж проводится не реже одного раза в год.
Все движущиеся острые и представляющие опасность для человека части механизмов должны иметь ограждения: у дробилок ограждаются привода передачи приемные части и разгрузочные отверстия; у мельниц ограждаются вращающийся барабан венцовые шестерни разгрузочные горловины соединительные муфты двигатели; у конвейеров ограждаются головные и хвостовые барабаны привод с передачей.
3.1 Рабочие площадки и проходы
У каждой машины должны быть устроены безопасные и удобные для работы проходы и площадки (у бункерных питателей вдоль конвейеров у цапф мельниц у редукторов электродвигателей у сепараторов у дешламаторов и т.д.) У дробилок устраиваются площадки на уровне загрузочного окна для подхода к нему во время остановки пропуска отдельных кусков и разгрузки забившегося впускного окна. Для наблюдения за загрузкой предусматривается отдельная площадка над дробилкой. Предусматривается также площадка на уровне приводаи дробилок для доступа к подшипникам и электродвигателю к смазочному устройству.
Площадки у грохотов предусмотрены на уровне нижней кромки их короба чтобы с них было удобно заменить сита. Площадки у грохотов на уровне загрузки используются для регулировки питателей. Площадки ограждены перилами.
В отделении измельчения рабочие площадки устраиваются у подбункерных питателей вдоль сборных и наклонных конвейеров у загрузочных и разгрузочных цапф мельниц у редукторов и электродвигателей.
Все обслуживающие площадки переходные мостики и лестницы имеют достаточную прочность устойчивы и снабжены перилами высотой не менее одного метра с перекладиной и сплошной обшивкой по низу перил на высоту 014 м.
Рабочие площадки на высоте более 03 м ограждены перилами и снабжены лестницами.
3.2 Лестницы наклонные проходы и полы производственных помещений
Лестницы к рабочим площадкам и механизмам имеют угол наклона:
а)постоянно эксплуатируемые - не более 45°;
б)посещаемые 1-2 раза в неделю - не более 60°;
в)в зумпфах колодцах - до 75°.
Во всех случаях ширина лестниц не менее 06 м высота ступеней не более 03 м ширина ступеней не менее 025 м. Металлические ступеньки лестниц и площадки выполняются из рифленого металла.
В наклонных галереях и проходах имеющих угол наклона более 7° предусмотрены на полу набивные рейки.
Главные магистральные проходы служат для сообщения между отдельными производственными участками и имеют ширину 15-2 м. Ширину проходов у крупного оборудования (дробилок мельниц) принимают не менее 12-15м В главном корпусе предусмотрены главные магистральные проходы:
а)вдоль фронта мельниц по всей длине машинного пролета;
б)параллельно сборным конвейерам;
в)вдоль магнитных сепараторов.
Главный корпус фабрики - мокрый цех поэтому полы должны быть асфальтированные и иметь наклон в сторону дренажного желоба. Уклон полов принимают не более 2-4° дренажные желоба перекрыты металлической решеткой.
3.3 Пусковые устройства
Эти устройства предусмотрены в таком месте чтобы в поле зренияпускающего были видны все площадки около пускаемой машины.
У каждого аппарата и машины (дробилок мельниц магнитных сепараторов конвейеров) вывешиваются инструкции по пуску и обслуживанию.
Перед пуском оборудования обязательно подается предупредительный звуковой сигнал.
Перед запуском в работу оборудования находящегося вне зоны видимости должен быть подан звуковой сигнал продолжительностью не менее 10 секунд. После первого сигнала предусматривается выдержка времени не менее 30 секунд после чего перед пуском оборудования должен подаваться второй сигнал продолжительностью 30 секунд. В местах с повышенным уровнем шума должна также предусматриваться дублирующая световая сигнализация.
При пуске машин обеспечивается полная безопасность обслуживающего персонала. Остановка и пуск в работу оборудования после монтажа или ремонта производится с соблюдением положений бирочной системы.
Пуск оборудования после монтажа или ремонта производится только после проверки отсутствия в опасной зоне людей а также посторонних предметов. Пуск производится только под наблюдением мастера производившего монтажно- ремонтные работы при обязательном участии механика цеха или лиц их заменяющих.
Пусковые устройства местного управления (пуск мельниц конвейеров) находятся в зоне обслуживания агрегата и в зоне видимости обслуживающего персонала.
Каждая машина имеет аварийную кнопку «стоп». Для аварийного отключения электродвигателя конвейера из любой точки по его длине предусмотрен трос протянутый вдоль конвейера.
3.4 Электробезопасность
Помещения обогатительной фабрики в отношении опасности поражения людей электричеством относятся к помещениям с повышенной опасностью. Они характеризуются наличием сырости (главный корпус) токопроводящего пола. Для предупреждения поражения человека электрическим током на фабрике предусмотрены следующие мероприятия : установка электрооборудования в отделении дробления и грохочения в закрытом исполнении так как они работают в пыльных условиях. Для мельниц устанавливаются двигатели в защитном исполнении. Для привода насосов применяются двигатели в закрытом исполнении с влагостойкой изоляцией; установка аппаратов защиты предназначенных для отключения электродвигателей при ненормальных режимах (перегрузках двигателей снижении или повышении напряжения появлении значительных токов вызванных коротким замыканием); распределительные системы внутреннего электроснабжения проложены кабельными шинами (укладка кабеля производится по специальным кабельным конструкциям; при переходе через стены и перекрытия при подводе питания к машинам и аппаратам кабели прокладываются в трубах); на фабрике все электроконструкции корпуса электродвигателей аппаратов и т.п. нормально не находящиеся под напряжением но могущие оказаться под таковым вследствие повреждения изоляции заземляются. Присоединение к заземляющему устройству корпусов электроприемников и аппаратов производится при помощи стальных труб служащих для прокладки кабелей стальных полос четвертой жилы кабеля. Сопротивление заземления равно 4 Ома. Все токоведущие части должны иметь ограждения. При ремонтных работах электрическая энергия отключается. На пусковых устройствах вывешивается: "Не включать! Ведутся работы!
4 Мероприятия по снижению пылевыделений
Для снижения запыленности воздуха до санитарных норм в проекте предусматриваются следующие инженерно-технические мероприятия:
герметизация пылящего оборудования (дробильное отделение отделение измельчения места перегрузок);
для снижения запыленности до установленных норм содержание S
запроектирована приточно-вытяжная вентиляция (в дробильном корпусе для сепарации применяются дымососы для очистки загрязненного воздуха перед выбросом в атмосферу устанавливают мокрые пылеуловители КМЦП; воздух удаленный из корпуса аспирационной установкой компенсируется воздухом подаваемым приточной системой состоящей из центробежного вентилятора рулонного фильтра и трубчатого калорифера);
установка местной вентиляции обеспечивающей удаление загрязненного воздуха и подачу свежего воздуха на определенные рабочие места (некоторое количество пыли остается в воздухе производственных помещений она постепенно оседает на оборудование пол стены и при определенных условиях может вновь перейти во взвешенное состояние и создать концентрации пыли в воздухе превышающие допустимые).
Чтобы обеспечить уборку пыли стены потолки фабрики сделаны гладкими; углы и плинтусы закруглены; подоконники и другие аналогичные устройства имеют откос не более 60° для того чтобы предотвратить скопление на них пыли. Раз в смену предусматривается мокрая уборка. В местах где невозможно снизить запыленность воздуха рабочим выдаются респираторы.
Работа в корпусах сушки разрешается только в респираторах типа «лепесток». В местах перегрузок руды и сухого концентрата устанавливаются аппараты для гидрообеспыливания и увлажнения руды. На каждом рабочем месте три раза в месяц определяют запыленность воздуха.
5 Производственная санитария
5.1 Мероприятия по снижению производственного шума и вибрации
Источником шума является соударение металлических частей машин падение материала при перегрузке и т.д. Для уменьшения уровня шума применяют шумопоглащающие материалы кроме того применяют индивидуальные средства защиты - наушники.
В корпусе дробления оборудование является источником интенсивного шума который превышает допустимые нормы особенно много шума вызывает работа длинных желобов несмотря на шумоподавление путем подкладывания под футеровку желобов старых конвейерных лент. Для уменьшения шума на грохотах установливаются резиновые амортизаторы между поддерживающими опорами и несущими конструкциями. В отделении измельчения заметно снижают шум резиновые листы проложенные между корпусом мельницы и футеровочными плитами. Основными источниками шума грохотов служат поверхности течек борта направляющие планки сит.
Для снижения шума используют защитные элементы из транспортерной ленты установленные на боковые или лобовые поверхности течек; применяют звукоизолирующие ограждения из листовой стали внутренняя поверхность которых покрыта звукопоглощающими материалами. Установка машин осуществляется на упругие амортизаторы; операторские пульты звукоизолированы; производится систематическая смазка частей машин; своевременный ремонт.
Для снижения вибрации до предельно допустимых уровней выполняются следующие мероприятия: тщательная сборка движущихся частей; систематическая смазка поверхностей трения машин; крупное оборудование (дробилки мельницы и т.д.) установлено на самостоятельном фундаменте; своевременный ремонт; применение виброизоляций (резина войлок).
5.2 Освещенность производственных помещений
Организация рационального освещения является одним из основных факторов создания высокопроизводительной и безопасной работы трудящихся. Недостаточное освещение не вызывает само по себе несчастных случаев но может обусловить их возникновение так как оно притупляет внимание и вызывает преждевременное утомление работающих. Кроме того источники света могут быть причиной возникновения пожара
Освещение на проектируемой фабрике предусматривается искусственное и естественное.
Для искусственного освещения производственных помещений предусматривают люминесцентные лампы. Освещенность в основных цехах не менее 100 люкс во вспомогательных - не менее 30 люкс. Естественное освещение осуществляется через окна в наружных стенах и через световые фонари. Предусмотрено аварийное освещение которое обеспечивает освещенность составляющую 10% рабочего освещения и имеет независимый источник питания. Для ремонтных работ применяется стационарная сеть напряжением 12В.
Пример расчета освещенности в производственно - техническом отделе ДОФ:
Определение площади помещения: ;
Определение индекса помещения:
Определение требуемого количества светильников:
где Е - требуемая освещенность горизонтальной плоскости лк; S - площадь помещения м2; KЗ - коэффициент запаса (KЗ=08); U - коэффициент использования осветительной установки; ФЛ - световой поток одной лампы лм; n - число ламп в одном светильнике.
Помещение а = 9м b = 6м h = 32м
Светильник ARSR4xl8W
Лампы люминесцентные 18Вт а в одном светильнике 4 лампы ФЛ=11150лм(данные из таблицы "Начальный световой поток люминесцентных ламп) Нормы освещённости Е=300лк на уровне 08м от пола
Коэффициент запаса KЗ=08
Коэффициент отражения потолка - 50 стен - 30 пола - 10(данные из таблицы коэффициентов отражения) Расчет:
Определяем площадь помещения: ;
Определяем индекс помещения:
Определим коэффициент использования исходя из значений коэффициентов отражения и индекса помещения: U=51.
Определим требуемое количество светильников: .
Освещенность выбрана согласно санитарным правилам по объектам различения – 300 лк. (2.2.12.1.1. 1278-03).
5.3 Вентиляция и отопление производственных помещений
С помощью вентиляции отопления и кондиционирования воздуха решается важнейшая задача обеспечения в производственных помещениях обогатительной фабрики предельно допустимой концентрации вредных веществ. Предусматривается вытяжная вентиляция в зонах пылеобразования (дробление грохочение измельчение). Для создания благоприятных микроклиматических условий предусматривается местная приточная вентиляция в виде воздушных завес воздушных душей. В стенах и фонарях помещений сделаны специальные проемы в которых устроены створные переплеты. В производственных помещениях где по условиям технологического процесса воздух должен иметь заданные параметры используют кондиционеры. Для обеспечения необходимых микроклиматических условий в рабочей зоне производственных помещений применяют системы центрального водяного и парового отопления. В зимнее время фабрика отапливается от центральной ТЭЦ. Для создания нормальных санитарно-гигиенических условий труда на фабриках предусмотрена: установка вентиляционных и аспирациоиных устройств организация службы контроля состава воздуха эксплуатации и ремонта всех вентиляционных и аспирационных устройств; меры снижающие пылегазообразование и пылегазовыделения на всех участках.
5.4 Средства индивидуальной защиты
Каждый рабочий получает спецодежду и защитные приспособления предусмотренные его обязанностями (очки рукавицы резиновая обувь каски наушники респираторы и т.д.).
6 Пожарная безопасность
Дробильно-обогатительная фабрика по степени пожарной опасности относится к категории "Д". Здания и сооружения относятся ко II степени огнестойкости (предел огнестойкости 25 часа). Внутри корпусов запроектировано достаточное количество лестниц соединяющих между собой все этажи и рабочие площадки обеспечивающие свободную эвакуацию рабочих в случае пожара. Также предусмотрены запасные эвакуационные выходы. Каждое здание выше 10 м снабжено наружными лестницами имеющими выход на кровлю. К каждому зданию с двух длинных сторон примыкают бетонированные проезды шириной не менее 6 м. Разрывы между зданиями не менее 10 м. В производственных помещениях по проекту предусмотрены локальные средства пожаротушения (ящики с песком огнетушители) и противопожарный водопровод объединенный с производственным. Пожарные гидранты наружного противопожарного водопровода заглублены в траншее ниже глубины промерзания располагаются вдоль дорог и переездов на расстоянии не более 150 м друг от друга не ближе 5 м от стен здания и вблизи перекрестков не далее 2 м от края проезжей части. Внутри производственных помещений фабрики предусматривается внутренний пожарный водопровод подключенный к наружному водопроводу. Внутренние пожарные краны с рукавами не менее 10 м со стволом устанавливаются на лестничных клетках у входов в коридорах в производственных помещениях и других местах. Размещаются пожарные краны так чтобы можно было с двух пожарных кранов одновременно попасть в одну и туже точку возгорания. Для ликвидации небольшого загорания на предприятии используют первичные средства пожаротушения: пожарные стволы (водяные и воздушно-пенные) действующие от внутреннего пожарного водопровода (внутренних пожарных кранов) огнетушители сухой песок асбестовые одеяла и другой пожарный инвентарь. Для успешного тушения пожара решающее значение имеет быстрое обнаружение пожара и своевременный вызов пожарных подразделений к месту пожара. Фабрика должна быть обеспечена надежными средствами оповещения или сигнализацией о пожаре. Проектом предусмотрены автоматические сигнализаторы для пожарной команды.
Фабрика обслуживается городской пожарной командой. А так же на фабрике создана постоянно-действующая пожарно-техническая комиссия и пожарная охрана.
7 Мероприятия по предотвращению чрезвычайных ситуаций и ликвидации последствий
Компания имеет все необходимые Лицензии связанные с вопросами промышленной безопасности.
Разработаны необходимые декларации безопасности для хвостохранилища базисного склада взрывчатых материалов склада ГСМ.
Склад горюче-смазочных материалов;
Центральная котельная;
Склад взрывчатых материалов (ВМ);
Объекты электроснабжения;
Склад радиоизотопов.
В соответствии с российским законодательством на предприятии разработан План действий в чрезвычайных ситуациях. Основные виды потенциальных аварийных ситуаций включают:
Авария на взрывоопасных производствах (склад ВМ);
Аварии на энергосетях и энергообъектах (аварии на главных понизительных подстанциях возгорание трансформаторов и масляных выключателей);
Аварии на тепловых сетях (взрывы и пожары);
Аварии на объектах хвостового хозяйства (прорыв трубопроводов оборотного водоснабжения и отвода пульпы затопление насосных станций прорывы дамб хвостохранилища и т. д.);
Аварии с хлором на городских водоочистных сооружениях (ВОС) при погрузочно-разгрузочных работах и транспортировке;
Аварии с оборудованием ВОС (прекращение питьевого водоснабжения);
Аварии с радиоизотопами;
План действия в ЧС содержит также мероприятия по предотвращению аварийных ситуаций локальную схему оповещения о ЧС.
Для всех объектов разработаны всеобъемлющие Планы ликвидации аварий (ПЛА).
На предприятии создано формирование гражданской обороны насчитывающее 396 человек функционирует эвакуационная комиссия. В каждом цехе создан штаб ГО и ЧС.
Проводятся учения по ликвидации аварий и лекции по ГО и ЧС. Работники предприятия сдают экзамены по вопросам ГО и ЧС.
Регулярно проводится обучение личного состава гражданской обороны предприятия в области ГО и ЧС. В 2004 году в «Учебно-методический центр ГО и ЧС Республики Карелия» (г. Петрозаводск) было направлено на обучение 6 человек в 2005 г. планируется обучить 10 человек.
Налажена связь с городским отделением милиции пожарная часть находится непосредственно на промплощадке комбината.
распределяются обязанности и ответственность за проведение противопаводковых мероприятий;
содержится перечень организационно-технических мероприятий по подготовке к работе в паводковый период.
Принимаются дополнительные меры по предупреждению выявлению и своевременному пресечению террористических проявлений.
ГЛАВА 6 ОХРАНА ОКРУЖАЮЩЕЙ СРЕДЫ
1 Экологическая характеристика региона
Район Костомукшского месторождения расположен в секторе умеренного климатического пояса характеризующемся умеренно теплым летом холодной зимой и большим количеством осадков.
Средняя температура воздуха самого жаркого месяца - июля составляет +15°С самого холодного месяца - января -11°С. Летом температура воздуха может повышаться до +30°С минимальная температура зимой -30°С.
Среднегодовая скорость ветра составляет 3-35 мсек. Среднегодовое количество осадков около 500 мм с максимумом в летние и осенние месяцы.
Снежный покров формируется в конце октября - начале ноября сходит в мае. Мощность снежного покрова составляет 70-80 см среднее число дней со снежным покровом - 175.
1.2 Поверхностные и подземные воды
Железорудное Костомукшское месторождение находится в пределах озерно-речной системы р. Кенти. Площадь водосбора р. Кенти - 949 км . Площадь озер составляет 11% заболоченность 7%. Длина реки - 75 км расход воды - 821 м3с. Ближайшими русловыми озерами системы являются: Костомукшское преобразованное в 1979 году в хвостохраиилище Окуневое Куроярви Поппалиярви Юриккаярви Койвас Кенто и др.
Реки в рассматриваемом регионе имеют смешанное питание преобладающим является снеговое. Средний годовой слой стока - 300 мм.
Большинство водоемов Карелии имеют высокое рыбохозяйственное значение поскольку являются местами нереста и нагула ценных промысловых видов рыб (лосось форель кумжа сиг ряпушка карповые рыбы и др.).
Гидрогеологические условия Костомукшского месторождения характеризуются тем что при эксплуатации карьера водопритоки формируются за счет трещинных вод скальной толщи и атмосферных осадков. Суммарный водоприток в карьер в среднем составляет от 990 до 1500 м3час.
Территория месторождения находится на северном склоне Западно-Карельской возвышенности.
Рельеф района месторождения характеризуется чередованием грядовых возвышенностей со слабовсхолмленной моренной равниной. Удлиненные гряды чередуются с узкими понижениями озерами болотами. Максимальная высота гряд составляет 2579 м.
Территория сложена породами архейского возраста - кристаллическими сланцами кварцитами железистыми кварцитами гнейсами плагиопорфитами п л агиосл анцами.
Почвообразующими породами являются ледниковые отложения с высоким содержанием обломков кристаллических пород что определяет малую мощность и неравномерность почвенного покрова.
Преобладают следующие виды почв: подзолистые (наиболее распространены) подзолисто-глеевые торфяно-болотные. Промерзание почвы на открытых участках в среднем начинается в октябре-ноябре и достигает максимума в апреле. Средняя глубина промерзания колеблется в пределах 30-60 см достигая в отдельные зимы 85см. Оттаивание почвы обычно завершается к середине мая.
Почвы Костомукшского района характеризуются пониженными значениями рН (кислые почвы) высокой засоренностью валунами и гравием и малой мощностью и малопригодны для дальнейшего использования после снятия почвенно- растительного покрова в процессе строительных работ.
1.4 Растительность и животный мир
Растительность района Костомукшского месторождения относится к типу
северной и средней тайги. Характерной особенностью является доминирование в растительном покрове хвойных деревьев - сосна ель. Наиболее распространенными из лиственных пород являются береза осина черная ольха. Особую ценность представляет карельская береза древесина которой идет на изготовление мебели и художественных бытовых предметов.
Фауна представлена северо-таежными видами млекопитающих (ондатра выдра бобр и т. д.). Распространен северный олень. Белая куропатка глухарь рябчик - наиболее типичны из птиц. Также встречаются хищные птицы: совы ястребы канюки и другие. В лесной подстилке живут землеройки лесные мыши. В первом этаже леса встречаются заяц-беляк лось. Из хищников широко представлены: лисица бурый медведь волк рысь росомаха куница горностай ласка. Из водоплавающих птиц наиболее характерны утки на болотах - кулики. В озерах и реках - щука окунь налим и лососевые - сиги хариус "каменноозерская" популяция лосося.
К югу от г. Костомукша расположен Костомукшский заповедник площадью 476тыс. га созданный в 1983 году. В заповеднике разбита сеть наблюдательных площадей для мониторинга окружающей среды в том числе и ее загрязнения а в 1992 г. организована станция интегрированного мониторинга окружающей среды. Согласно результатам оценки воздействия на биоту проведенной представителями Общественного Движения г. Костомукши «Экополис» в районе Костомукшского заповедника нарушений в стабильности развития ни у одной из групп исследованных организмов не выявлено.
2.1 Охрана атмосферного воздуха
За минувший год было обследовано 69 газопылеулавливающих установок.
При этом было сделано 483 замера концентраций неорганической пыли 24 замера на содержание газообразных загрязняющих веществ и 552 замера скоростных полей газопылеулавливающих установок. Средняя эффективность этого оборудования при очистке от неорганической пыли согласно инструментальным замерам составила 942 процента.
Согласно типовой форме 2-ТП (воздух) от стационарных источников в 2004 году составили 44400543 тонны в том числе основного загрязняющего компонента - сернистого ангидрида - 35371028.
Взвешенных веществ (неорганическая и другие виды пыли) было выброшено 6292342 тонны окислов азота в пересчете на двуокись азота - 1378686 окиси углерода - 1112763 тонны.
В 2004 году комбинатом было получено разрешение на выброс загрязняющих вредных веществ в атмосферный воздух от стационарных источников загрязнения. В нем были указаны предельно допустимые величины выбросов. Срок действия этого документа - по 31 декабря 2004 года. Благодаря выполненным на ГОКе природоохранным мероприятиям выбросы сернистого ангидрида не превысили пределов предусмотренных разрешением.
На комбинате эксплуатируется 1189 вентиляционных систем в том числе 435 приточных 674 вытяжных и 80 тепловых завес и тепловых агрегатов.
2.3 Контроль загрязнения воздушного бассейна в зоне техногенного воздействия комбината и в санитарно-защитной зоне города Костомукши
Согласно графику контроля за чистотой атмосферного воздуха утвержденному управлением природных ресурсов и охраны окружающей среды МПР России по Республике Карелия за отчетный период проведено 22 замера содержания загрязняющих вредных веществ (сернистого ангидрида и двуокиси азота) в атмосферном воздухе.
Анализ полученных данных показывает что экологическая ситуация в зоне техногенного воздействия комбината и в санитарно- защитной зоне города в большинстве точек для сернистого ангидрида и двуокиси азота не превышает ПДК.
2.4 Охрана поверхностных водоёмов
В 2010 году про изведен сброс воды хвостохраннлища в озерно-речную систему Кенти - Кенто в объеме 19372 миллиона кубических метров. Сброс производился согласно лицензии серии ПГЗNQOOO 14 на водопользование (сброс сточных вод хвостохраннлища в озера Окуневое Попполиярви). Контроль за качеством сбрасываемой воды осуществлялся центральной лабораторией охраны окружающей среды по двум контрольным створам согласованным с Государственным комитетом природных ресурсов по Республике Карелия.Совместно с Карельским научным центром Российской академии наук продолжались работы по изучению влияния сброса воды хвостохранилища на экологическое состояние озерно-речной системы Кенти-Куйто.
Химический анализ техногенных вод (рудничной хвостохранилиша фильтрационной) показал что все они загрязнены минеральными веществами в первую очередь - калием и сульфатами. Среднегодовая концентрация загрязняющих веществ в сбрасываемой воде составила: аммонийного азота - 004 мгл; нитратного азота - 691 мгл; нитритного азота - 0014 мгл; взвешенных веществ 052 мгл; железа общего - 0371 мгл; калия - 1429 мтл; кальция - 350 мтл; магния - 147 мгл; марганца - 0013 мгл; натрия - 147 мгл; сульфатов 1893 мгл; хлоридов - 53 мгл.
Существенным фактором является снижение концентрации нитритного и нитратного азота по сравнению с 2003 годом. Это связано с переходом на использование эмульсионных взрывчатых веществ типа «Сибирит».
2.5 Складирование и утилизация отходов производства
Складирование вскрышных пород в объеме 5288131 тысячи тонн и отходов обогащения в объеме 12463331 тысячи тонн производил ось согласно проекту. При этом не были превышены лимиты установленные Государственным комитетом природных ресурсов по Республике Карелия. Отходы производства в количестве 512 тонн были вывезены на проектную свалку.
Токсичные отходы первого класса опасности (ртутьсодержащие лампы) в количестве 69754 штук отравлены на специализированное предприятие для демеркуризации.
Токсичные отходы второго класса опасности (отработанные масла) в количестве 29689 тонны утилизированы путем сжигания вместе с мазутом на котельной комбината.
3 Планирование и отчётность
3.1 Планирование в области охраны окружающей среды
На предприятии имеются следующие планы в области охраны окружающей среды:
Ежегодная комплексная программа по уменьшению воздействия отходов производства на экологическую ситуацию региона г. Костомукша;
Комплексная программа по уменьшению воздействия отходов производства на экологическую ситуацию региона г. Костомукша на 2005 г.;
Раздел «Охрана окружающей среды» ежегодной Программы капитальных вложений.
Также составляются отчеты о фактически затраченных за год средствах на природоохранные мероприятия (табл. 6.1).
Отправка отработанных ртутных ламп на демеркуризацию
Строительство биотермической ямы
Замена системы горения на обжиговых машинах
Установка роликовых грохотов
Установка магнитных сепараторов на 1-ю стадию сепарации ДОФ
Пригруз низового откоса дамбы хвостохранилища
Переход на производство взрывных работ эмульсионными взрывчатыми веществами
Внедрение полномасштабного грохота в технологическую линию окомкования
Экспериментальные работы по закреплению пылящих поверхностей хвостохранилища
Научно-исследовательская работа «Оценка состава вод озерно-речной системы Кенти-Кенто»
Всего капиталовложений природоохранного назначения:
Следует отметить что все эти планы:
Практически не отличаются друг от друга;
Содержат масштабные мероприятия относящиеся к внедрению новых технологий и требующие больших капитальных вложений на протяжении нескольких лет (что обуславливает повторение мероприятий из года в год);
Не содержат ни одного организационного мероприятия;
Не содержат мероприятий в области сероочистки
В этой связи необходимо переработать стратегический план природоохранных мероприятий включить в него организационные мероприятия такие как экологическое обучение персонала разработку экологической политики компании и системы мониторинга окружающей среды и т. д. Также начиная с 2003 года следует
составляется документ «План природоохранных мероприятий» включающий все мероприятия в области охраны окружающей среды в том числе и организационные с указанием сроков реализации мероприятий ответственных за их исполнение источников и объемов финансирования и пометками о выполнении мероприятий.
-тп (токсичные отходы);
Согласно форме государственной статистической отчетности по форме 4-ос за 2010г. платежи за загрязнение окружающей среды плата за природные ресурсы и затраты на охрану окружающей среды составили (табл. 6.2):
Затраты на охрану окружающей среды платежи за загрязнение окружающей среды и плата за природные ресурсы в 2010 году
Затраты по охране и рациональному использованию водных ресурсов
в т. ч. выплачено другим предприятиям за прием и очистку сточных вод
Затраты по охране атмосферного воздуха
Затраты по охране окружающей среды от отходов производства и потребления
в т. ч. выплачено другим предприятиям за прием хранение и уничтожение отходов
Затраты на капитальный ремонт основных производственных фондов по охране окружающей среды
Плата за выбросы загрязняющих веществ в атмосферный воздух
Плата за размещение отходов
Продолжение таблицы 6.2
Плата за сбросы загрязняющих веществ в водные объекты
в т. ч. за сверхнормативные сбросы загрязняющих веществ в водные объекты
Плата за природные ресурсы: (всего)
Задолженности по экологическим платежам комбинат не имеет.
ГЛАВА 7 ЭКОНОМИЧЕСКАЯ ЧАСТЬ
1 Капитальные затраты
Капитальные затраты на оборудования в частности шаровой мельницы складываются из нескольких расчет которых представлен ниже.
Стоимость запасных частей:
Стоимость тары в упаковке:
Заготовительно-складские расходы:
Транспортные расходы на поставку и монтаж:
Балансовая стоимость:
1.1 Определение затрат на заработную плату персоналу осуществляющему монтаж и демонтаж футеровки шаровой мельницы
При расчете заработной платы следует учитывать различные виды доплат: премиальные отпускные северные поясной коэффициент ночные сверхурочные бригадирские вознаграждения за выслугу лет и т.д.
Затраты на заработную плату производственных рабочих занятых ремонтом машины [4]:
где - основная заработная плата
где - дополнительная заработная плата руб.; - прямая заработная плата; - доплаты к прямой заработной плате.
Предлагаемый способ поверхностного упрочнения футеровок шаровых мельниц позволяет увеличить их срок службы и соответственно уменьшить количество ремонтов связанных с заменой комплектов футеровок.
Для сравнения затрат на заработную плату персонала по монтажу футеровки без применения способа упрочнения футеровки шаровой мельницы МШЦ 4500×6000 применяемой на II стадии измельчения и с применением. Расчетный период составляет 10 лет.
Заработная плата (в час) персонала осуществляющего монтаж и демонтаж футеровки представлена в табл. 7.1.
Расчетное значение руб
Прямая зарплата (в час)
Доплаты к прямой зарплате
прочие доплаты (10% от )
Доплаты по районному коэффициенту (40% от )
процентная надбавка уплачиваемая к заработной плате в районах Крайнего Севера (80% от )
Итого основная заработная плата
Дополнительная заработная плата
Итого заработная плата
В табл. 7.2 представлена заработная работников при выполнении ими работ по замене футеровки.
Время выполнения ремонтной операции ч
Кол-во рабочих занятых на выполнении соответствующей ремонтной операции
Заработная плата за выполненную ремонтную операцию руб.
Демонтаж изношенной футеровки
Монтаж комплекта новой футеровки
Проверка крепления футеровки (путем холостого пуска шаровой мельницы с одновременной подачей воды)
Подтяжка ослабленных болтов
Из таблицы 7.2 видно стоимость ремонтных операций по замене футеровки составляет CРО=49454 руб.
Без проведения упрочняющей операции футеровка служит S=548дней и за L=10лет=3650дней затраты на заработную плату составят
При проведении предлагаемых периодических упрочняющих обработок футеровка служит S=1041день и за L=10лет=3650дней затраты на заработную плату составят
Соответственно экономический эффект ЭЗП от сокращения затрат на заработную плату за 10 лет составит
2 Расчет себестоимости по амортизации
Амортизационные отчисления (за 10 лет) при текущем режиме эксплуатации футеровки с учетом наличия 7 комплектов футеровки и сроке эксплуатации каждого комплекта 548 дней:
где - норма амортизации на полное восстановление n – срок полезного использования мельницы выраженный в годах n=10лет; К – капитальные затраты на приобретение комплекта из 7 футеровок К1=6448750руб.
Амортизационные отчисления (за 10 лет) при применении режима периодических упрочнений футеровки в процессе эксплуатации с учетом наличия 4 комплектов и срока службы каждого комплекта 1057 дней
где n=10лет; К – капитальные затраты на приобретения 4 комплектов футеровки К2=3685000руб KИ – коэффициент учитывающий инфляцию за 10 лет KИ = 111; L – амортизационный период L = 10 лет.
Соответственно экономия амортизационных средств (за 10 лет) составит
С учетом сокращения затрат на заработную плату общая экономия составит
где Kм – затраты на мероприятие Cэ – стоимость электроэнергии необходимой для осуществления режима упрочняющей обработки Cэ=243000руб. Cч – затраты на приобретение и монтаж частотных преобразователей необходимых для изменения частоты вращения шаровой мельницы что в свою очередь позволит создать упрочняющий футеровку режим работы шаровой мельницы Cч=1800000руб.
где НП – налог на прибыль НП=08.
Таблица технико-экономических показателей представлена на плакате ДП.060955.007.
В результате выполнения представленного дипломного проекта получены следующие результаты:
На примере мельницы шаровой МШЦ 4500×6000 показано что при работе мельницы без породы бомбардировка мелющими телами непосредственно футеровки из стали Гадфильда способна за счет наклепа повысить ее твердость с 200 до 325НВ что приведет к увеличению стойкости к истиранию футеровки примерно в 2 раза.
Для обеспечения эффективного наклепа шары должны циркулировать в водопадном режиме с направлением удара нормально к поверхности футеровке что обеспечивается при скорости вращения барабана мельницы VБ=075Vбкрит=35мс.
Для использованной степени заполнения шарами (φ=30%) время необходимое для осуществления эффективной бомбардировки составляет ~12минут период между упрочняющими наклепами ~27суток количество упрочняющих обработок в течение срока службы футеровки ~28.
На примере расчета удельных нагрузок действующих на подшипники скольжения показано что работа мельницы в предлагаемых режимах без породы не скажется на работоспособности ее основных конструкционных элементов.
На разработанный способ упрочнения футеровки подана заявка на изобретение [16] по результатам исследования опубликована статья [5].
Рассмотрена возможность увеличения срока службы зубчатого зацепления (вал-шестерня - венец) используемого в приводе шаровой мельницы за счет применения системы подачи смазки. В результате расчета системы смазки
Получены численные значения основных рабочих характеристик системы подачи смазки: объем смазочного материала наносимого за один впрыск составил 26·10-3м3 расход смазки 72·10-4м3с давление в системе оказалось равным 02 МПа объем емкости 0078м3 (рассчитано из условия пополнения емкости раз в месяц).
Разработана технология восстановления зубьев вал-шестерни.
Рассчитаны технико-экономические показатели от внедрения режима упрочняющей футеровку обработки.
СПИСОК ИСПОЛЬЗОВАННОЙ ЛИТЕРАТУРЫ
АндреевЕ.Е. Дробление измельчение и подготовка сырья к обогащению: Учебник Е.Е.Андреев О.Н.Тихонов. СПГГИ (ТУ). СПб 2007. 439с.
АндреевС.Е. Дробление измельчение и грохочение полезных ископаемых C.Е.Андреев В.В.Зверевич В.А.Перов. М.: Недра 1966. 396с.
АнурьевВ.И. Справочник конструктора-машиностроителя: в 3-х т.: Т.2. – 8-е изд. перераб. и доп. Под ред. И.Н.Жестковой. М.: Машиностроение 2001. 912с.
БолобовВ.И. Увеличение срока эксплуатации брони шаровых мельниц осуществлением ее эффективного наклепа В.И.Болобов А.П.Баталов Ю.П.Бойцов В.С.Бочков «Проблемы создания экологически рациональных и ресурсосберегающих технологий добычи полезных ископаемы и переработки отходов горного производства» 3-я Международная конференция по проблемам рационального природопользования ТулГУ Тула 2010. С48-51.
Болобов В.И. Материаловедение. Строение свойства и диаграммы состояния углеродистых сталей и чугунов: Учеб. пособие В.И.Болобов С.Ю.Кувшинкин Э.А.Кремчеев С.Л.Иванов. СПГГИ (ТУ). СПб 2009. 108с.
БойцовЮ.П. Технология конструкционных материалов. Изготовление соединений методами сварки и пайки: Методич. указ. к лаб. Работам Ю.П.Бойцов В.И.Болобов С.Л.Иванов Э.А.Кремчеев С.Ю.Кувшинкин. СПГГИ (ТУ). СПб 2006. 33с.
ВиноградовВ.Н. Изнашивание при ударе В.Н.Виноградов Г.М.Сорокин А.Ю.Албагачиев. – М.: Машиностроение 1982. – 192с.
ГорбачевскийВ.В. Эксплуатация и ремонт шаровых барабанных мельниц.- Киев 1967. 40c.
Гольстрем В.А. Справочник энергетика промышленных предприятий В.А.Гольстрем А.С.Иваненко. Изд. 4-е перераб. и доп. Киев «Техника» 1977. 464с.
ГуляевА.П. Металловедение. М.: Металлургия 1986. 544с.
ДавыдовН.Г. Высокомарганцевая сталь. М.: «Металлургия» 1979. 176с.
Евдокимов В.Д. Технология упрочнения машиностроительных материалов: Учебное пособие-справочник В.Д.Евдокимов Л.П.Клименко А.Н.Евдокимова. Одесса Николаев: Изд-во НГГУ им. Петра Могилы 2005. 352с.
ЕгерманУ.Ф. Инструкция по ремонту углеразмольных шаровых барабанных мельниц. М. «Госэнергоиздат» 1963. 32с.
Заявка на получение патента РФ «Способ поверхностного упрочнения футеровок шаровых мельниц» №2010133477 от 09.08.2010 авторы БочковВ.С. БолобовВ.И. БаталовА.П. БойцовЮ.П.
Крагельский Н.В. Трение и износ. М. Машиздат 1962.
КрюковД.К. Футеровки шаровых мельниц. М.: Машиностроение 1965. 184с.
ЛахтинЮ.М. Материаловедение Ю.М.Лахтин В.П.Леонтьева. М.: Машиностроение 1990.
Марганцовистая сталь. Пер. с англ. Б.А.Белоуса под ред. М.Е.Блантера. М.: Металлургиздат 1959. 94с.
Марочник сталей и сплавов Под общ. ред. А.С. Зубченко. – М.: Машиностроение 2003. 784 с.
СаверинМ.М. Дробеструйный наклеп. М.: Машгиз 1955. 312с.
ТкачевВ.Н. Методы повышения долговечности деталей машин. В.Н.Ткачев Б.М.Фиштейн В.Д.Власенко В.А.Уланов. М.: Машиностроение 1971. 272с.
ХрущовМ.М. Исследования изнашивания металлов. М.М.Хрущов М.А.Бабичев. М. Изд-во АН СССР 1960. 352с.
ШапошниковН.А. Механические испытания металлов. М.-Л.: Машгиз 1954. 443с.
Шилов П.М. Технология производства и ремонт горных машин. Изд-во «Недра» 1971. 384 с.
Электроснабжение горных предприятий: Программа методические указания и контрольное задание СПГГИ (ТУ). Сост. П.М.Каменев. СПб 2010. 23с.
Квагинидзе В.С. Безопасность труда на обогатительных фабриках Севера В.С. Квагинидзе Н.А. Корецкая. М.: Горная книга 2005. 328 с.
Рекомендуемые чертежи
Свободное скачивание на сегодня
- 23.08.2014