Ремонт ходовой тележки башенного крана



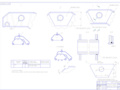
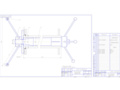
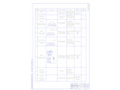
- Добавлен: 25.10.2022
- Размер: 1 MB
- Закачек: 0
Описание
Состав проекта
![]() |
![]() ![]() ![]() |
![]() ![]() |
![]() ![]() |
![]() ![]() ![]() |
![]() ![]() ![]() ![]() |
![]() ![]() ![]() |
![]() ![]() ![]() |
![]() |
![]() |
![]() ![]() ![]() |
![]() ![]() ![]() ![]() |
![]() ![]() |
![]() |
![]() ![]() ![]() ![]() |
Дополнительная информация
Содержание.docx
Анализ патентной и научно-технической литературы по ме-
тодам ремонта крановых металлоконструкций
Выбор способов устранения дефекта и оборудования
Проектирование технологического процесса
Расчет технологических режимов и норм времени
Конструкторская разработка прижимного приспособления
Технические расчёты прижимного приспособления
Устройство и принцип работы прижимного приспособления
Список использованных источников
Приложение А – спецификация
Приложение Б – комплект документов технологического
процесса восстановления тележки ходовой рамы башен-
Операционная карта.docx
Код наименование операции
Обозначение документа
Код наименование оборудования
Наименование детали сб. единицы или материала
Пл I U Vнапл SM ЧП d3 h3
Полуавтомат сварочный ПДГ-600
Закрепить накладку струбциной
Приварить накладку по контуру прилегания
200 А 28 В 01 ммин 35 1 18 15
Сварка в углекислом газе
Лист №1. Ремонтный чертеж тележки.dwg

наложитб накладку и приварить
Неуказанные размеры определить по месту
Ресурс тележки не меньше 90% от ресурса новой
Технологический маршрут:
ПОЯСНИТЕЛЬНАЯ ЗАПИСКА.docx
Целью курсовой работы является проектирование технологического процесса восстановления ходовой тележки башенного крана.
Основная задача курсовой работы по дисциплине "Технология производства и ремонта машин" является закрепление углубление и обобщение теоретических знаний полученных из лекционного курса а также приобретение навыков проектирования технологических процессов восстановления деталей машин и пользования ГОСТами нормативной и другой справочной литературой.
На сегодняшний день вследсви высокой стоимости башенных кранов их ремонт является актуальным. После проведения необходимой сертификации произведённых ремонтных работ а также прохождения контроля органами госпроматомнадзора восстановленные и отремонтированные краны способны далее выполнять строительные работы.
Анализ условий работы и дефектов ходовой тележки башенного крана
Башенные краны выпускают в виде передвижных приставных или самоподъемных кранов.
Башенные передвижные краны представляют собой рельсовый свободнострящий поворотный кран с закрепленной в верхней части башни стрелой. Они имеют многомоторный электрический привод с питанием через кабель и токоприемник.
Основными технологическими преимуществами башенных кранов на рельсовом ходу являются их устойчивость в работе и большой вылет крюка позволяющий монтировать здания при односторонней установке.
У большинства башенных кранов механизмы и противовес расположены на поворотной платформе что повышает их устойчивость. Краны перевозят в собранном виде на буксире монтируют и демонтируют их методом самомонтажа и самодемонтажа всего за несколько часов. Башенные краны имеют самоподъемную стрелу которая поднимает и перемещает груз по горизонтали или горизонтальную стрелу с грузовой кареткой.
Для массового строительства отечественная промышленность выпускает башенные краны грузоподъемностью 3 10 т на основе универсального параметрического ряда и модификации основных моделей кранов.
Кран КБ-401 (КБ-160.2) имеет подъемную стрелу. При изменении вылета груз движется по траектории близкой к горизонтальной что обеспечивается кинематической связью грузовой и стреловой лебедок. Предназначен для строительства многоэтажных жилых и гражданских зданий высотой до 16 этажей. В обычном исполнении может работать в зимнее время при температуре до —25°С. При использовании в гидротолкателях тормозов жидкости типа АМГ-10 и ПГ-271 кран может работать при температуре до —40°С. Высота башни меняется способом подращивания по мере возведения сооружаемого объекта. Грузовая характеристика зависит от числа секций в башне и района установки крана [1].
Краны в процессе эксплуатации помимо полнокомплектных ремонтов проводимых по результатам обследования должны подвергаться и капитально-восстановительному ремонту. При этом ремонте в процессе разборки должна проводиться дефектация всех элементов с ремонтом тех из них которые имеют дефекты превышающие допустимые.
Периодичность обследования и сроки проведения капитально-восстановительного ремонта следует принимать согласно Руководящего нормативного документа [6].
Обследование состояния ходовой тележки проводится в рамках обследования металлоконструкции крана в целом.
По результатам проверки и контроля оформляется журнал осмотра с указанием соответствующих дефектов и повреждений далее направляется вместе с краном на ремонтное предприятие в том случае если осмотр и диагностика проводилась вне ремонтного предприятия.
В процессе работы крана ходовая тележка испытывает изгибающие нагрузки в горизонтальной плоскости в районе втулки шкворня вследствие сил инерции возникающих от веса металлоконструкции крана и груза при разгоне крана и при его торможении.
В нашем случае после обследования выявлены следующие дефект:
Трещина в сварном шве втулки шкворня.
Тележка башенного крана выполнена сварным из листовой и прокатной стали марки Сталь сп3 ГОСТ 380.
Тележка бракуется при усталостном разрушении основного металла.
Рисунок 1- Башенный кран КБ-160.2:
— стреловая расчалка; 2 — стрела; 3 — датчик усилий ограничителя грузоподъемности; 4 — крюковая обойма; 5 — башия; 6 — грузовая лебедка; 7 — механизм поворота; 8 — поворотная платформа; 9 — тележка; 10 — стреловая лебедка; 11 — стреловой канат; 12 — грузовой канат
Таблица 1 – Техническая характеристика крана КБ-401 (КБ-160.2)
Максимальный грузовой момент кНм
Частота вращения с-1
Время полного изменения вылета мин
Установленная мощность электродвигателей кВт
Примечание. Нижний предел грузоподъемности и высоты подъема соответствует наибольшему вылету верхний — наименьшему.
Анализ патентной и научно-технической литературы по методам ремонта крановых металлоконструкций
Металлоконструкция кранов восстанавливается при помощи сварки. Проведем анализ основных способов сварки и свойств сварных швов.
Сваркой называется процесс получения неразъемного соединения деталей путем применения местного нагрева.
Сварным соединением называется соединение двух деталей полученное при помощи сварки. Сварной шов — это часть сварного соединения которая образуется из расплавленного в процессе сварки и затем затвердевшего металла *(Это определение справедливо лишь для тех видов сварки у которых место соединения деталей доводится до расплавления.
Металлургический процесс при сварке и наплавке по сравнению с металлургическим процессом получения сплавов более сложен так как обладает рядом особенностей: кратковременностью процесса значительной скоростью охлаждения высокой температурой (до 2300° С) нагрева металла и др. Все это приводит к тому что химические реакции в зоне наплавки протекают мгновенно не успевают полностью завершиться до кристаллизации в результате создаются неравномерные структуры. Высокая температура провоцирует переход газов находящихся в воздухе (кислород азот водород) в атомарное состояние. Газы активно поглощаются металлом взаимодействуют с ним и легирующими элементами резко снижая механические характеристики наплавленного металла.
Газы попадают в сварочную ванну из воздуха флюсов обмазок электродов защитных газов адсорбированной на поверхности изделия влаги с остатками смазок ржавчиной и др.
При контакте кислорода с расплавленным металлом происходит растворение кислорода и образование окислов часть которых остается в сплаве после его кристаллизации. Азот растворяясь в металле со многими элементами образует нитриды. Поэтому во время сварки сталей при недостаточной защите наплавляемого металла совместное действие кислорода и азота вызывает резкое усиление хрупкости слоя наносимого на поверхность детали. Азот сильно снижает относительное удлинение способствует повышению пористости усиливает склонность металла к старению.
Водород подобно кислороду в процессе сварки поглощается жидким металлом. Но при остывании последнего (особенно в момент кристаллизации) растворимость водорода резко снижается. Выделение водорода не прекращается не только по окончании кристаллизации но даже при комнатной температуре. Диффундируя в объеме застывшего металла водород накапливается в микрополостях и создает такие значительные удельные давления что происходит разрушение наплавленного слоя [2].
Существенное влияние на растворимость газов оказывают погонная энергия (зависящая от способа и режимов сварки) размеры детали структура и состав металла восстанавливаемого изделия предварительный и сопутствующий нагревы и т.д.
При ремонте металлоконструкций сварке и наплавке подвергаются детали изготовленные в основном из конструкционных низкоуглеродистых средне- и низколегированных прокатных и литых сталей. Углерод и легирующие элементы входящие в состав стали оказывают существенное влияние на свариваемость и делят последнюю на четыре группы: хорошую удовлетворительную ограниченную и плохую свариваемость. Поэтому при разработке технологического процесса прежде всего нужно оценить свариваемость металла восстанавливаемого изделия и назначить (при необходимости) определенные операции уменьшающие или исключающие отрицательное воздействие тех или иных компонентов на качество восстановленного слоя.
Свариваемостью называется сочетание технологических свойств металлов и сплавов дающих возможность образовывать в процессе сварки или наплавки соединения и слои которые по своим свойствам не уступают свойствам материала восстанавливаемого изделия.
Более всего на свариваемость оказывают влияние химический состав сплава фазовая структура и ее изменения в процессе нагрева и охлаждения физико-химические и механические свойства активность реакций элементов и др.
В связи с тем что параметров характеризующих основной и присадочный (электродный) материалы очень много то свариваемость представляет комплексную характеристику включающую чувствительность металла к окислению и порообразованию соответствие свойств сварного соединения заданным эксплуатационным реакцию на термические циклы сопротивляемость образованию холодных и горячих трещин и т.д.
Из перечисленных параметров наиболее существенным при сварке и наплавке углеродистых и низколегированных сталей является сопротивляемость образованию трещин. Горячие трещины чаще всего возникают при ослаблении деформационной способности металла из-за появления в структуре легкоплавких хрупких эвтектик дефектов кристаллического строения внутренних и внешних напряжений. Вероятность появления при сварке или наплавке горячих трещин можно определить по показателю Уилкинсона (H.C.S):
Условием появления горячих трещин является Н.С.S. > 2. Так например при обычной сварке низколегированной стали трещины начинают возникать при Н.С.S. = 4. Холодные трещины чаще всего возникают из-за закаливаемости стали при быстром охлаждении и насыщении металла шва и зоны термического влияния водородом. Они как правило зарождаются по истечении некоторого времени после сварки и наплавки и развиваются в течение нескольких часов или даже суток.
Для оценки склонности металла к появлению холодных трещин чаще всего используется углеродный эквивалент которым можно пользоваться как показателем характеризующим свариваемость при предварительной оценке последней. Для этой цели имеется ряд уравнений [2].
Температура сопутствующего сварке или наплавке подогрева зависит от материала изделия и колеблется в среднем от 250 до 400 ° С.
Уменьшение содержания водорода в наплавленном металле достигается улучшением защиты сварочной ванны от внешней среды тщательной подготовкой поверхности перед наплавкой прокаливанием присадочного материала и др.
При анализе свариваемости не следует упускать из виду тот факт что от воздействия значительных температур происходит разупрочнение термически упрочненных сталей. Таким образом перед разработкой технологии сварки или наплавки следует определить свариваемость основного присадочного металла и металла шва; вероятность появления трещин; разупрочнение сплава и назначить необходимые мероприятия для уменьшения или исключения нежелательных явлений.
Основным металлом называют металл из которого изготовлены свариваемые детали. При газовой сварке в месте расположения шва расплавляется основной металл но в большинстве случаев его бывает недостаточно для заполнения всего зазора между деталями. Поэтому в сварочное пламя вводят присадочную проволоку которая расплавляясь дает дополнительный жидкий металл образующий шов.
Рисунок 2- Схема сварного соединения:
- усиления шва; 2 - сварной шов; 3 - сварочная пайка; 4 - основной металл; 5 - металл шва
Сечение шва делают большим по толщине чем толщина основного металла. Это утолщение называют усилением шва (рисунок 2).
В месте нагрева деталей сварочным пламенем образуется углубление в расплавленном металле которое называют сварочной ванной.
В настоящее время существует много различных способов сварки которые классифицируются по различным признакам. В зависимости от степени нагрева свариваемый металл может быть или в пластическом (тестообразном) или в расплавленном (жидком) состоянии. В первом случае для осуществления процесса сварки необходимо приложить к свариваемому изделию усилие (сварка давлением). Во втором случае расплавленный металл свариваемых изделий и присадочного прутка образует общую ванну после остывания которой сварка оказывается осуществленной без применения механического воздействия (сварка плавлением) [2].
Следует отметить что имеются такие способы сварки при которых металл либо совсем не нагревается (холодная сварка глубокой деформацией) либо нагревается до температур при которых металл не доводится даже до пластического состояния (ультразвуковая сварка).
Классификация основных видов сварки представлена на рисунке 3 [2].
Рисунок 3 - Классификация основных видов сварки
Контактная сварка. Детали включаются в электрическую цепь сварочной машины и через них пропускается электрический ток большой силы и низкого напряжения. При этом в месте стыка (контакта) деталей выделяется тепло которое нагревает их до расплавления или до пластического состояния. Контактная сварка в зависимости от способа выполнения подразделяется на стыковую точечную и шовную.
Стыковая сварка (рисунок 4 а) применяется для соединения стержней рельсов труб и т. п. Детали 1 закрепляются в электродах 2. Затем через них пропускается ток от вторичного витка 4 сварочного трансформатора. В месте соприкосновения стержни нагреваются до высокой температуры после чего ток выключают стержни сжимаются и детали свариваются.
Точечная сварка применяется для сварки листовых конструкций у которых сварные соединения должны быть прочными но не плотными. При точечной сварке (рисунок 4 б) свариваемые листы 1 укладывают кромками друг на друга и зажимают между медными электродами 2. Через электроды пропускается электрический ток от сварочного трансформатора. Металл под электродами сильно нагревается и при сжатии электродов сваривается в одной точке.
Роликовая сварка применяется для сварки листовых конструкций требующих плотно-прочных швов например различных резервуаров баков тары и других изделий массового производства.
Рисунок 4 - Схема стыковой (а) точечной (б) и роликовой (в) сварки: 1 — свариваемая деталь; 2 — электроды; 3 — гибкие шины; 4 — вторичный виток трансформатора; 5 — первичная обмотка трансформатора; 6 — хобот
При роликовой сварке (рисунок 4 в) свариваемые листы 1 укладывают так же как при точечной сварке между электродами 2 имеющими форму роликов. К роликам подводится электрический ток При прохождении листов между вращающимися роликами образуется сплошной плотный шов состоящий из ряда сварных точек перекрывающих друг друга [2].
Сварка трением осуществляется на станках подобных токарным. После закрепления двух цилиндрических деталей в зажимах станка детали сводятся вплотную и с большой силой прижимаются друг к другу. При быстром вращении одной из деталей в месте стыка их в результате трения выделяется большое количество тепла достаточное для нагрева концов деталей до пластического состояния (1200°С).
После нагрева до такой температуры вращение прекращается детали дополнительно сжимаются и свариваются.
Этот способ сварки впервые предложен в 1956 г. рабочим-новатором А. И. Чудиковым (Россия).
Термитной сваркой называется процесс получения неразъемного соединения деталей при котором для нагрева металла применяется термит.
Термит представляет собой механическую смесь состоящую из 78% (по весу) порошка железной окалины (окись железа) и 22% порошка чистого алюминия. При сгорании термита развивается температура около 3000° С. В результате сгорания термита получается расплазленное железо и жидкий шлак (окись алюминия) которыми заливают свариваемые концы. Сжигание термита производится в огнеупорном тигле.
Рисунок 5- Термитная сварка давлением (а) и плавлением (б):
— форма; 2 —тигель; 3 — термитный металл; 4 — свариваемые детали
Различают термитную сварку давлением (рисунок 5 а) и термитную сварку плавлением (рисунок 5б). В первом случае жидкий металл и шлак выливаются из тигля в форму в которой установлены концы свариваемых деталей. Нагретые до пластического состояния стержни сжимаются специальным прессом и свариваются.
Во втором случае свариваемые части заформовываются с зазором величина которого зависит от размера сечения свариваемых концов. Этот зазор заполняется жидким металлом из тигля; давление при этом не прикладывается.
Термитная сварка нашла применение при сварке трамвайных рельсов при ремонте и изготовлении некоторых судовых деталей и т. д.
Электрическая дуговая сварка. При дуговой электрической сварке тепло необходимое для расплавления металла в месте сварки выделяется электрической дугой возникающей между электродом и основным металлом при пропускании через них электрического тока. Электрод (угольный или металлический) закрепляется в специальном электрододержателе (рисунок 6). В дуге развивается температура порядка 6000° С которая обеспечивает быстрый нагрев и расплавление свариваемых кромок. При дуговой сварке угольным электродом (способ Бенардоса) заполнение шва производится расплавленным металлом присадочной проволоки которая вводится в зону дуги (рисунок 6 б) [3].
Рисунок 6 - Схема электрической дуговой сварки металлическим (а) и угольным (б) электродом:
— свариваемая деталь; 2 — металлический электрод; 3 — угольный электрод; 4 — присадочная проволока
При дуговой сварке металлическим электродом (способ Славянова) соединение кромок осуществляется расплавленным металлом электрода (рисунок 7 а). Процесс сварки может вестись как на постоянном так и на переменном токе. Для защиты расплавленного металла от насыщения азотом и кислородом воздуха для обогащения металла шва необходимыми примесями и повышения устойчивости горения дуги при сварке применяются металлические электроды покрытые слоем специальной обмазки. Для питания дуги электрическим током применяются сварочные генераторы постоянного тока и трансформаторы переменного тока. Простота процесса значительная скорость сварки и высокое качество соединения обеспечили повсеместное внедрение электродуговой сварки [3].
Рисунок 7 - Схема автоматической сварки под слоем флюса:
— свариваемая деталь; 2 — подача флюса; 3— сварочная головка; 4— подача электродной проволоки; 5 — бухта проволоки; 6 — сварочный шов; 7 — шлаковая корка; 8 — флюс
Более прогрессивным методом является автоматическая электросварка при которой дуга горит под слоем сыпучего флюса (рисунок 7) выполняющего ту же роль что и обмазка при ручной электродуговой сварке. Непрерывная подача проволоки в зону сварки и автоматическое поддержание горения дуги осуществляются посредством сварочной головки 3 которая в процессе сварки либо перемещается по изделию 1 либо устанавливается неподвижно и тогда свариваемые детали перемещаются относительно головки.
Электрошлаковая сварка (рисунок 8).
Рисунок 8 - Схема электрошлаковой сварки
Свариваемые кромки деталей располагают вертикально с некоторым зазором. В зоне сварки к кромкам прижаты медные башмаки 4 которые удерживают флюс 3 и расплавленный металл 5 сварочной ванны. Башмаки движутся снизу вверх одновременно с механизмом сварочной головки непрерывно подающим сварочную проволоку 2 в зону сварки. Дуга вначале горит между проволокой и металлом ванны. Когда флюс расплавится дуга гаснет и ток проходит только через расплавленный флюс. При установившемся процессе сварки флюс проволока и кромки свариваемого металла расплавляются теплом выделяющимся при прохождении твка через расплавленный флюс. По мере заполнения зазора металлом формирующие башмаки поднимаются вверх. Жидкий металл затвердевает снизу вверх и образует шов 6. При электрошлаковой сварке достигается очень высокая производительность труда.
Рисунок 9 - Схема атомноводородной сварки
Атомноводородная сварка (рисунок 9). При этом способе деталь расплавляется так называемой дугой косвенного действия горящей между двумя вольфрамовыми электродами. Электроды вставлены в мундштуки по которым к дуге подается водород. Сварочный шов получается путем расплавления присадочной проволоки. Таким образом дуга и жидкий металл сварочной ванны защищены водородом от вредного воздействия кислорода и азота воздуха. Водород под действием тепла дуги расщепляется на атомы а последние соприкасаясь с более холодным металлом вновь соединяются в молекулы. При этом выделяется большое количество тепла идущее на дополнительный нагрев металла сварочной ванны. Этот способ сварки применяют для сварки металлов небольшой толщины и для сварки цветных металлов [2].
Газовая сварка. Этот способ сварки состоит в том что для нагревания и плавления свариваемых кромок используется пламя полученное при сжигании горючего газа в смеси с кислородом. Для получения газокислородной смеси ее сжигания и выполнения сварки применяют специальные сварочные горелки.
Газовая сварка относится к сварке плавлением. Заполнение зазора между кромками свариваемых деталей производится в основном расплавленным металлом присадочной проволоки. Схема газовой сварки представлена на рисунке 10.
Рисунок 10 - Газовая сварка:
— сварочная горелка; 2 — пламя; 3 — присадочная проволока
Газовая сварка широко применяется в различных отраслях народного хозяйства особенно при сварке стали малой толщины цветных металлов чугуна и при ремонте различных деталей.
Пламя газовой горелки используется для правки покоробленных деталей для очистки металла от ржавчины окалины краски для поверхностной закалки различных деталей а также может быть использовано для местной термической обработки сварных швов. С помощью газового пламени часто наносят различные покрытия (металлические и неметаллические) на поверхности деталей.
Особое и совершенно самостоятельное место в промышленности занимает кислородная (газовая) резка металлов [3].
Выбор рационального способа и технологических приемов сварки и наплавки определяется необходимостью получения детали с требуемыми размерами и наплавленного слоя с требуемыми свойствами. При этом должна быть обеспечена максимальная производительность и экономичность процесса.
Ремонт металлоконструкций ГПК должен производиться по утвержденным технологическим процессам разработанным в соответствии с требованиями Правил устройства и безопасной эксплуатации грузоподъемных кранов.
При ремонте ответственных сварных конструкций допускается применение только электродуговой сварки. Применяемые методы и режимы сварки должны обеспечить провар всего сечения свариваемых элементов и особенно корня шва [6].
При ремонте металлоконструкций имеющих трещины необходимо руководствоваться следующими условиями:
трещина длинной более 100 мм расположенная параллельно основному шву не должна находиться от него на расстоянии менее 100 мм;
трещина длинной менее 100 мм расположенная параллельно основному шву не должна находиться от него на расстоянии менее чем толщина сваренного металла (но не менее 20 мм);
не допускается крестообразное с основным швом расположение трещин [6].
При невозможности соблюдения указанных требований ремонт следует производить методом вставок.
В металлоконструкциях решетчатых стрел сквозные и несквозные трещины на несущих продольных уголках расположенных не ближе 130 мм от плоскости разъема секции или от места приварки вертикальных и горизонтальных листов стрелы разрешается ремонтировать способом наложения усиливающих накладок с приваркой их к уголкам только продольными швами. При этом накладка должна перекрывать трещины не менее чем на 120 мм с каждой стороны.
До наложения накладки трещины в уголках должны быть заварены с внутренней (противоположной от накладки) стороны.
При расположении трещин на несущих уголках ближе 130 мм от плоскости разъема секции или от места приварки вертикальных и горизонтальных листов весь уголок подлежит замене.
Замене также подлежат и другие элементы (раскосы связи листы) при невозможности исправления их деформации или иного дефекта.
Марки сталей применяемых для ремонта сварных металлоконструкций должны соответствовать маркам указанным в чертежах или равноценными им по механическим свойствам маркам стали [7].
Типы и марки электродов сварочной проволоки и защитных газов применяемых при ремонте должны соответствовать техническим условиям заводов – изготовителей и выбираться применительно к маркам свариваемой стали так чтобы механические свойства шва и сварочного соединения (предел прочности предел текучести относительное удлинение угол загиба и ударная вязкость) были не менее нижнего предела указанных свойств основного металла конструкции установленных стандартами или техническими условиями.
Рекомендуемые марки электродов для ручной дуговой сварки крановых металлоконструкций приведены в таблице 2 а режимы электродуговой ручной сварки с учетом диаметра электрода его марки и положения сварки в таблице 3 [7].
Таблица 2 – Марки электродов для ручной дуговой сварки крановых металлоконструкций с температурой эксплуатации от плюс 40 до минус 40
Электроды по ГОСТ 9467-75
Для сварки несущих конструкций из углеродистых горячекатаных сталей
УОНИ – 1345 СМ – 11 ОЗС – 2 АНО –3 ОЗС – 6 ОЗС – 4 УП 245 УП 145 АНО – 4 МР - 3
Для сварки несущих конструкций из низколегированных сталей в горячекатаном и термообработанном состоянии поставки
СМ – 11 УОНИ 1355 УП 155 УП255 УОНИ – 1365 К – 5А
Для сварки вспомогательных конструкций из углеродистых сталей
АНО – 1 АНО – 3 АНО – 4 АНО – 5 АНО – 6
Таблица 3 – Режимы электродуговой ручной сварки
Сила сварочного тока А
Переменный постоянный обратная или прямая
Примечание: Напряжение сварочного тока зависит от применяемого источника сварочного тока и устанавливается автоматически.
Для сварки крановых металлоконструкций механизированной электродуговой сваркой в среде углекислого газа в соответствии с требованиями следует применять проволоку марок Cв-08Г2С и Cв-09Г2СЦ диаметром до 16 мм (ГОСТ 2246-70). Режимы сварки в углекислом газе в зависимости от диаметра электродной проволоки приведены в таблице 4 [7].
Таблица 4 – Режим сварки в углекислом газе
Диаметр электродной проволоки мм
Вылет электродной проволоки мм
Расход углекислого газа лмин
Скорость подачи электродной проволоки мч
Примечание: Скорость подачи электродной проволоки назначается в зависимости от марки сварочного полуавтомата.
Рекомендуемые режимы сварки в углекислом газе в зависимости от толщины свариваемого металла и типа соединения приведены в таблице 5 [7].
Таблица 5 – Режимы сварки в углекислом газе в зависимости от толщины свариваемого металла
Толщина свариваемого ме-талла мм
Расход углекис-лого газа лмин
Выбор способов устранения дефекта и оборудования
После проведенного анализа для восстановления ходовой тележки используем полуавтоматическую сварку в среде углекислого газа.
Порядок восстановления следующий:
Разделываем дефектный шов (рисунок 11 а) завариваем его и зачищаем заподлицо (рисунок 11 б). На дефектное место устанавливаем накладку и привариваем ее по контуру (рисунок 11 в).
Рисунок 11 – Порядок ремонта тележки
Для очистки подкоса от грязи и старой смазки используется моечный аппарат высокого давления «Portotechnika 600».
Производительность лч ..500
Потребляемая мощность кВт ..22
Размеры (д х ш х в) мм ..375х360х935
Макс. температура воды на входе град. С..60
Для сварки будем использовать сварочный полуавтомат ПДГ-600 с газовой аппаратурой - баллон СО2 с углекислотным редуктором.
Сварочный полуавтомат ПДГ-600 предназначен для полуавтоматической сварки сплошной и порошковой проволокой на постоянном токе в среде защитных газов в комплекте с источниками для МИГМАГ сварки. Предназначен для длительной работы в жестких промышленных условиях на повышенных режимах сварки.
Плавная регулировка выходного напряжения сварочного источника и скорости подачи электродной проволоки с подающего механизма.
Обеспечивает стабилизацию скорости подачи сварочной проволоки и обратную связь по напряжению на двигателе подачи сварочной проволоки что позволяет производить качественную сварку на расстоянии до 50 метров от сварочного источника. Стабильная скорость подачи сварочной проволоки при длине шлейфа горелки 3 5 м и изгибах шлейфа. Автоматическое управление газовым трактом сварочным источником и подающим механизмом кнопки на горелке.
Три режима сварки: «Длинные швы» (4-х такт режим) «короткие швы» (2-х такт режим) и Inter Lock.
Таблица 7 -Техническая характеристика сварочного полуавтомата ПДГ-600
Напряжение питающей сети В (f=50Гц)
Номинальный сварочный токА
Количество роликов шт.
Диаметр электродной проволоки мм :
Тип разъема сварочной горелки
Вместимость сварочной кассеты кг
Масса (без кассеты с проволокой) кг
Габариты мм не более (длина х ширина х высота)
Обеспечивает установку кассеты (диаметром 300мм) с проволокой весом 15 кг.
Подача сварочной проволоки может производиться непосредственно с кассеты или с бухты уложенной на разматывающее устройство. Подключается к любому типу сварочных источников для МИГМАГ сварки производства «Фирмы ЭЛМА». Подключается к любому типу сварочных источников других производителей через блок питания БП-02.
Разделку трещин и обработку сварных швов производим угловой шлифовальной машиной Bosch 1000.
Потребляемая мощность - 1000 Вт скорость без нагрузки - 2800-11000 обмин максимальный диаметр диска - 125 мм резьба шпинделя - М14 вес - 1.8 кг.
Для контроля будем использовать дефектоскоп (рисунок 12 табл.8)
Рисунок 12 – Ультразвуковой дефектоскоп УД2-70
Предназначен для контроля продукции на наличие дефектов типа нарушения сплошности и однородности материалов готовых изделий полуфабрикатов и сварных (паяных) соединений измерения глубины и координат залегания дефектов измерения отношений амплитуд сигналов отражённых от дефектов.
Особенности дефектоскопа:
два независимых измерительных строба
система автоматической сигнализации дефектов
возможность запоминания: 100 программ настроек 100 изображений экрана 2000 результатов измерения параметров сигналов
режим "электронная лупа
протоколирование процедуры контроля с использованием программного обеспечения "Ultra UD2-70
Таблица 8 - Основные технические характеристики УД2-70:
5; 18; 25; 50; 100МГц
Диапазон контроля (по стали)
Диапазон диапазон усиления приёмного тракта
Динамический диапазон временной регулировки чувствительности(ВРЧ)
Абсолютная погрешность при измерении глубины залегания дефекта
Абсолютная погрешность при измерении отношения амплитуд сигналов
Время непрерывной работы от аккумуляторной батареи
Габаритные размеры (без ручки)
Диапазон рабочих температур
После восстановления и контроля производим покраску грунтовкой Крэс-3 в один слой и эмалью Крэс-5 . Для покраски используем компрессор масляный КМ-500 с максимальный расходом воздуха 500 лмин и давлением 12 атм. Для покраски настраиваем компрессор на расход 240-260 лмин и давление 4 5 атм.
Проектирование технологического процесса
При составлении технологического маршрута необходимо учитывать следующие требования:
одноимённые операции по всем дефектам маршрута должны быть объединены;
каждая последующая операция должна обеспечить сохранность качества работы поверхностей детали достигнутую при предыдущих операциях;
в начале должны идти подготовительные операции затем восстановительные слесарно-механические шлифовальные и доводочные.
План рациональной последовательности технологического процесса восстановления телескопического подкоса принимаем следующий:
5 Моечная (очистка подкоса от грязи и старой краски).
0 Дефектация (дефектовать подкос).
5 Слесарно- механическая (разделать трещину под заварку).
0 Сварочная (заварить трещину сплошным швом).
0 Слесарно- механическая (зачистить сварной шов заподлицо).
5 Сварочная (приварить накладку).
0 Контрольная (контролировать сварные швы).
0 Малярная (окрасить тележку).
Технологический маршрут восстановления с указание оборудования и режимов представлен в приложении А курсовой работы.
Расчет технологических режимов и норм времени
Расчет режимов сварки.
Сварочная дуга является мощным дуговым разрядом в ионизированной среде газов и паров металла. Характеристиками дуги являются ее ток Iд и напряжение Uд.
Статическая вольтамперная характеристика дуги (рис. 12) показывает зависимость Uд = f(Iд) при Iд = const. Она имеет три характерных участка: падающий I жесткий II и возрастающий III.
Рисунок 12 - Статические вольт-амперные характеристики дуги
Крутопадающая характеристика дуги (участок I) бывает при плотности тока не более 10–12 Амм2. При увеличении Iд увеличиваются поперечное сечение столба дуги и электропроводность причем увеличение последних идет с некоторым опережением роста тока дуги. Поэтому на участке I напряжение дуги при увеличении тока падает.
При дальнейшем увеличении Iд (участок II) пропорционально ему растут площадь поперечного сечения и плотность тока. В связи с этим напряжение дуги остается практически неизменным. Такое состояние характерно для дуг с плотностью тока 12 80 Амм2 т.е. практически во всем диапазоне режимов сварки штучными электродами неплавящимися электродами и под флюсом.
При сварке плавящимся электродом в защитных газах на форсированных режимах под флюсом (когда плотность тока более 80 Амм2) при увеличении Iд резервы роста сечения столба дуги исчерпаны поэтому он сжимается и вызывает увеличение напряжения Uд. На таких режимах статическая характеристика дуги (участок III) становится возрастающей.
В процессе сварки дуга и источник ее питания образуют взаимосвязанную систему. Устойчивость горения дуги и стабильность режима сварки зависят как от условий существования дугового разряда так и от свойств и параметров источников питания и в первую очередь от внешней характеристики источника.
Внешней характеристикой источника питания сварочной дуги называется зависимость между напряжением на его зажимах Uип и током Icв протекающим в сварочной цепи при нагрузке т.е. Uип = f (Icв).
Существуют следующие внешние характеристики источников питания: падающие пологопадающие жесткие возрастающие (рисунок 13).
Рисунок 13 - Внешние характеристики источников питания: 1 – падающие;
– пологопадающие; 3 – жесткие; 4 – возрастающие
Установившийся режим работы системы определяется точкой пересечения (рисунок 13) внешней характеристики источника 1 и вольт-амперной характеристики 2 дуги т. е. для нормального протекания процесса сварки необходимо равенство напряжений на дуге и клеммах источника питания (Uд = Uип). Однако устойчивое ее горение будет при токе соответствующем точке В. Ток соответствующий точке А(IA) является током зажигания дуги. После появления последней он автоматически повысится до рабочей величины Iв.
Рисунок 14 - Внешняя характеристика источника питания и вольт-амперная характеристика дуги: IA – ток зажигания дуги; IB – ток устойчивого горения дуги
Выбор источника питания сварочной дуги по типу внешней характеристики
производится в зависимости от способа сварки.
Если форма характеристики дуги падающая то внешняя характеристика источника
питания (рисунок 15) должна быть более крутопадающей.
Рисунок 15 - Характеристики системы “дуга – источник питания”: 1 – вольтамперная характеристика дуги; 2345 – внешние характеристики источников питания
При жесткой характеристике дуги характеристика источника должна быть
пологопадающей или жесткой но в меньшей степени чем характеристика дуги. И при возрастающей вольт-амперной характеристике дуги принимается источник питания с жесткой или слегка возрастающей характеристикой.
При ручной сварке как правило наблюдаются значительные колебания длины дуги а соответственно и напряжения на дуге но режим сварки при этом должен быть
Значит в этом случае чем круче характеристика источника питания тем более
устойчива дуга т.е. тем меньше изменение тока при изменении длины дуги.
При автоматической сварке плавящимся электродом происходит саморегулирование при котором длина дуги после ее изменения восстанавливается автоматически за счет изменения тока и соответственно скорости плавления проволоки. Явление
саморегулирования наиболее сильно проявляется при повышении плотности тока в
электроде и уменьшении крутизны внешней характеристики источника питания.
Следовательно источники питания сварочной дуги с крутопадающей внешней характеристикой используются как правило при ручной сварке при сварке неплавящимся электродом в среде защитных газов и сварке под флюсом при сравнительно небольших плотностях тока [2].
Для сварки выбираем проволоку Св-08Г2С диаметром 18 мм.
Величина тока зависит от диаметра электродной проволоки скорости ее подачи и от толщины свариваемых деталей. Сварочная дуга устойчиво горит при плотности сварочного тока не менее 25 Амм.
Плотность тока равна:
- площадь сечения электродной проволоки мм:
где - диаметр электродной проволоки.
Скорость автоматической сварки определяется по формуле:
где - глубина зачищенного слоя;
- коэффициент плавления проволоки;
- скорость подачи электродной проволоки ммин:
Тогда скорость сварки равна:
Конструкторская разработка прижимного приспособления
Целью конструкторской разработки является разработка приспособления для установки и приварки накладки на дефектное место. Габариты тележки не дают возможность использовать стандартные станочные приспособления.
Использование различных приспособлений для установки закрепления элементов свариваемой конструкции или изделия при их сборке прихватке и сварке значительно уменьшает трудоемкость сборочно-сварочных работ повышает точность сборки и качество сварки снижает деформации и коробления при сварке сокращает длительность производственного цикла и снижает себестоимость изделия. Поэтому при современном уровне организации сварочных работ использование приспособлений является обязательным. Сборка и сварка без приспособлений допускается только в отдельных случаях когда это диктуется необходимостью и местными условиями (ограниченными сроками работ простотой формы конструкции и др.)
Приспособления бывают сборочные и сборочно-сварочные. В приспособлениях первой группы производится только сборка изделий а в приспособлениях второй группы —сборка и сварка. Чаще применяются сборочно-сварочные приспособления так как они не требуют снятия изделия после сборки. Какие приспособления являются наиболее целесообразными в том или ином случае—следует определять с учетом типа сварной конструкции и организации производственного процесса.
При сборке и сварке в качестве приспособлений используют прихватки стяжки плиты распорки. Находят широкое применение и более сложные приспособления — кондукторы поворотные столы (манипуляторы) кантователи роликовые стенды и др. Более сложные приспособления выгодны при массовом и крупносерийном производстве однотипных сварных изделий. Приспособления для сборки и сварки можно разбить на следующие типы.
Опорные. К ним относятся плиты стеллажи сборочно-сварочные стенды. Плиты для сборки выполняются из чугуна литыми с пазами для закладки головок болтов закрепляющих изделия. Кроме того они имеют дополнительные отверстия для установки различных упоров.
Постоянные сварочно-сборочные стенды изготовляют из двутавровых балок швеллеров или рельсов с продольными пазами для крепящих болтов. Изготовление чугунных плит обходится дороже но они имеют то преимущество что к их поверхности не привариваются капли металла.
Для сборки решетчатых конструкций применяют стеллажи располагаемые на козлах или столбах вдоль которых сверху укладывают балки или рельсы [5].
Для приварки накладки используем приспособление позволяющее прижать привариваемую накладку на место дефекта и приварить ее по контуру что позволяет исключить помощь слесаря. Приспособление показано на рисунке 16. Приспособление состоит из прижима 1 пластины 2 двух разрезных втулок 3 и оси 4. Ось 4 устанавливается в отверстие втулки тележки после по краям устанавливаются две втулки до упора. Устанавливаем накладку и на нее устанавливаем платину приспособления 2 и прижимаем с двух сторон прижимами 1 втулки запирают ось неподвижно во втулке посредством разрезных втулок подобно работы анкерных болтов.
Приспособление является универсальным при помощи данного приспособления можно приваривать соосно втулки или работать как струбциной при ремонте или изготовлении различных металлоконструкций.
Рисунок 16 – Приспособление для приварки накладки
Технические расчёты прижимного приспособления
Произведём расчёт резьбы прижимной гайки приспособления по напряжениям среза приняв случай установки тележки в вертикальном положении:
Отсюда минимальный диаметр резьбы гайки:
где - осевая сила Н;
- глубина завинчивания мм;
- коэффициент полноты резьбы (=087);
- коэффициент неравномерности нагрузки по виткам резьбы (=06).
- допускаемые напряжения среза МПА (=40МПа для стали 10).
Определим необходимое усилие затяжки гайки из условия отсутствия сдвига деталей:
где - коэффициент запаса (=18);
- внешняя нагрузка Н;
- число плоскостей стыка детали (=1);
- коэффициент трения в стыке (=015).
Внешнюю нагрузку определим как силу которую необходимо приложить для сдвига накладки:
- ориентировочная масса накладки (=5 кг);
- коэффициент трения накладки о тележку накладки (=09);
Тогда окружная составляющая сил резания:
Усилие затяжки гайки:
Диаметр резьбы болта:
Из конструктивных соображений из-за большого диаметра отверстия в накладке принимаем резьбу М62.
Устройство и принцип работы прижимного приспособления
Приспособление состоит из прижима пластины двух разрезных втулок и оси. Ось устанавливается в отверстие втулки тележки после по краям устанавливаются две втулки до упора. Устанавливаем накладку и на нее устанавливаем платину приспособления и прижимаем с двух сторон прижимами втулки запирают ось неподвижно во втулке посредством разрезных втулок подобно работы анкерных болтов.
Результатом данного курсового проекта является разработка технологического процесса ремонта тележки ходовой рамы башенного крана КБ-160.2 (КБ-401) соответствующий необходимым ГОСТам и руководящим документам.
Также в итоге было разработано универсальное прижимное приспособление обеспечивающее приварку соосных втулок или работу в качестве струбцины при ремонте или изготовлении различных металлоконструкций.
Список использованных источников
«Правила устройства и безопасной эксплуатации грузоподъемных кранов» (Постановление МЧС РБ от 03.12.2004г. №45 рег.НРПА №811889).
Алексеев Е.К. Мельник В.И. Сварочное дело. Госстройиздат 1959г.
Глизманенко Д.Л. Сварка и резка металлов. Издание пятое переработанное. Москва 1970.
Гарост М.М. Масловская Е. М. Учебно - методическое пособие к курсовой работе по дисциплине «Технология производства и ремонта машин» – Минск: БНТУ 2008.
Болотин Х.Л. Костромин Ф.П. Станочные приспособления. Изд.5-е переработанное и дополненное.М. «Машиностроение» 1973. -344с.
«Методические указания по обследованию машин с истекшим сроком службы. Часть 3. Башенные стреловые несамоходные и мачтовые краны краны-лесопогрузчики» РД 10.4.30-90.
"Указания по выбору материалов для изготовления стальных конструкций грузоподъемных кранов" РД 22-19-97.
Комплект документов технологического процесса восстановления
тележки ходовой рамы башенного крана
Техпроцесс.DOC
Министерство образования Республики Беларусь
Белорусский национальный технический университет
Руководитель М.М. Гарост
ТЕХНОЛОГИЧЕСКОГО ПРОЦЕССА ВОССТАНОВЛЕНИЯТЕЛЕЖКИ ХОДОВОЙ РАМЫ БАШЕННОГО КРАНА
ГОСТ 3.118-82 форма 1
ТЕЛЕЖКА ХОДОВОЙ РАМЫ
Код наименование операции
Обозначение документации
Код наименование оборудования
Моечный аппарат высокого давления « Portotechnika 600 » щетка металлическая перчатки. 1-2
РМ 010 Дефектовочная
Стол дефектовщика дефектоскоп УД2-70 щетка металлическая перчатки штангельциркуль ШЦ -1-125-01 ГОСТ 166-89.
РМ015 Слесарно- механическая
Угловая шлифовальная машина BOSCH 1000 круг шлифовальный 180-25-5 «Bulflex» очки защитные наушники перчатки щетка металлическая
Полуавтомат сварочный ПДГ-600 газовая аппаратура щетка металлическая проволока СВ-08Г2С
РМ 025 Слесарно- механическая
Наименование детали сборочной единицы или материала
Полуавтомат сварочный ПДГ-600 газовая аппаратура приспособление щетка металлическая
Дефектоскоп УД2-70 щетка металлическая перчатки штангенциркуль ШЦ -1-125-01 ГОСТ 166-89 шаблон сварщика.
Компрессор КМ-500 краскопульт 005мм щетка металлическая.
Министерство образования Республики Беларусь.docx
БЕЛОРУССКИЙ НАЦИОНАЛЬНЫЙ ТЕХНИЧЕСКИЙ УНИВЕРСИТЕТ
Факультет транспортных коммуникаций
Кафедра: «Строительные и дорожные машины»
По дисциплине «Технология производства и ремонта машин»
Тема: «Технологический процесс ремонта тележки ходовой рамы башенного крана»
Руководитель: Гарост М.М.
ЛИСТ №2 - Маршрутный процесс восстановления.dwg

Основное оборудование
Мойка высокого давления
-разделать дефектный
Машинка углошлифоваль-
Полуавтомат сварочный
Слесарно-механическая:
- приварить накладку
по контуру прилегания
кран консольный Q=1.0т
Маршрутный технологический
процесс восстановления тележки
ЛИСТ №3-Приспособление.dwg
