Редуктор цилиндрический




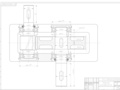
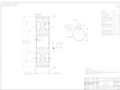
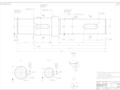
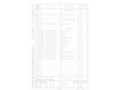
- Добавлен: 25.10.2022
- Размер: 2 MB
- Закачек: 3
Описание
Состав проекта
![]() |
![]() |
![]() |
![]() |
![]() |
![]() |
![]() |
![]() |
![]() |
![]() |
![]() |
![]() |
![]() |
![]() |
![]() |
![]() |
![]() |
![]() ![]() |
![]() ![]() |
![]() ![]() |
![]() ![]() |
![]() ![]() |
![]() ![]() |
![]() ![]() |
![]() |
![]() ![]() ![]() ![]() |
![]() ![]() ![]() ![]() |
![]() ![]() ![]() |
![]() ![]() ![]() ![]() |
![]() ![]() ![]() ![]() |
![]() ![]() ![]() ![]() |
![]() |
![]() ![]() ![]() |
![]() ![]() ![]() |
![]() ![]() ![]() |
![]() ![]() ![]() |
![]() ![]() ![]() |
Дополнительная информация
Спец..Кон.dwg

сборочка.dwg

Техническая характеристика
Вращающий момент на выходном валу
Частота вращения входного вала
Степень точности изготовления передачи
Коэффициент полезного действия
Технические требования
Необработанные поверхности литых деталей
красить маслостойкой красной эмалью
Наружные поверхности корпуса красить серой эмалью ПФ-115
Плоскость разьема покрыть тонким слоем герметика УТ-34
ГОСТ 24285-80 при окончательной сборке
В картер залить масло марки И-Г-А 68 ГОСТ 174794-89
Спец.. нач.dwg

ПГУ 2.190205.0210.000 СБ
ПГУ 2.190205.0210.002
ПГУ 2.190205.0210.005
ПГУ 2.190205.0210.001
ПГУ 2.190205.0210.007
ПГУ 2.190205.0210.009
ПГУ 2.190205.0210.010
ПГУ 2.190205.0210.011
ПГУ 2.190205.0210.012
ПГУ 2.190205.0210.013
ПГУ 2.190205.0210.003
ПГУ 2.190205.0210.004
ПГУ 2.190205.0210.006
ПГУ 2.190205.0210.008
ПГУ 2.190205.0210.011
РЕДУКТОР ЭСКИЗ .bak.dwg

вал.dwg

Сталь 45 ГОСТ 1050-88
НВ190 220 кроме места указанного особо.
*Размер обеспеч. инстр.
Острые кромки притупить.
Неуказанные предельные отклонения размеров
Колесо зубчатое.dwg

Сталь 35ХМ ГОСТ 4543-71
Радиусы скруглений 1
Неуказанные предельные отклонения размеров отверстий Н14
Направление линии зуба
Коэффициент смещения
ПГУ 2.190205.0210.011
Реферат!_.docx
В пояснительной записке приведен расчет редуктора к ленточному конвейеру выполненный на 45 листах в котором подробно расписана методика кинематического расчета привода и выбора электродвигателя проведен проектный расчет на прочность зубчатой передачи редуктора расчет тихоходного вала редуктора на прочность кроме этого расчет шпоночного соединения под колесом на тихоходном валу редуктора и выбора подшипников качения.
Графическая часть содержит:
формата А0 – сборочный чертеж редуктора;
формата А1 – чертеж тихоходного вала редуктора;
формата А2 – чертеж зубчатого колеса редуктора.
Титульный лист1 4.doc
Пензенский государственный университет
Кафедра: «Теоретическая и прикладная механика»
ПОЯСНИТЕЛЬНАЯ ЗАПИСКА
к курсовому проекту по дисциплине
«Детали машин и основы конструирования»
на тему: «Привод редуктора к цепному конвейеру»
Руководитель: Кочетков Д.В.
моя курсовая.docx
1.Выбор электродвигателя
Электродвигатель подбирается по каталогу по требуемой мощности в соответствии с режимом эксплуатации машины. При выборе электродвигателя различают три основных режима работы: длительный кратковременный и повторно-кратковременный.
Определяем потребляемую мощность двигателя по формуле[1 с.5 ф.1.2]:
Далее проводим оценку кинематических возможностей привода по формуле[1 стр.10 ф. 1.7]:
Затем определяем частоту вращения третьего вала:
Следовательно можем определить диапазон частот вращения двигателя:
После этого по таблице 1.3 [1 с.8] подбираем электродвигатель с мощностью и частотой вращения вала близкими к полученным и . При этом мощность двигателя должна быть равна или больше требуемой можно выбрать электродвигатель меньшей мощности. В этом случае он будет работать с перегрузкой величину которой определяют по формуле:
где допускаемая перегрузка двигателя =5 8% при постоянной нагрузке.
Выбираем из таблицы 1.3 [1 с.8] двигатель с синхронной частотой 1000 марки 4АМ132М6У3 мощностью кВт мм. - представлен в таблице 1.4 [1 с.9]
2. Кинематический расчёт привода
После окончательного выбора определяем общее передаточное число привода по формуле[1 с.10 ф.1.6]:
Полученное расчётом общее передаточное число распределяем между ступенями передач:
Окончательно распределив общее передаточное число привода по ступеням определяем его расчётное значение:
При этом отклонение его от требуемого не должно превышать 4% :
Определяем частоты вращения валов:
Определяем мощность на валах:
Определяем вращающие моменты на валах:
Рисунок 1 – Схема редуктора
Проектный расчёт на прочность зубчатых передач
Целью проектного расчёта является определение геометрических размеров передачи обеспечивающих её работоспособность и надёжность при заданных условиях эксплуатации и заданном ресурсе. Исходные данные для проектного расчёта принимаются по результатам кинематического расчёта привода. При
расчёте необходимо учитывать экономические факторы (обеспечение минимальных габаритов массы и стоимость передачи).
1. Выбор материала шестерни и колеса
Для редукторов шестерни и колеса следует изготовлять из одинаковых марок сталей 45; 40Х; 40ХН; 35ХМ; 45ХЦ и др. с термической обработкой (т. о.) по двум вариантам:
т.о. колеса – улучшение твёрдость HB 235 262
т.о. шестерни – улучшение твёрдость НВ 269 302
т.о. колеса – улучшение твёрдость HB 269 302
т.о. шестерни – улучшение и закалка ТВЧ твёрдость поверхности в зависимости от марки стали 45 50
Из таблицы 2.1 [1 с.29] выбираем материал для шестерни и колеса сталь 35ХМ. Улучшение зубьев колеса НВ 269 302. Улучшение и закалка ТВЧ зубьев шестерни 48 53
2 Определение допускаемых напряжений
Допускаемые напряжения при расчётах на контактную и изгибную выносливость необходимо определять с учётом режима нагружений зубьев и требуемого ресурса передачи (ч.)
Допускаемые напряжения определяются отдельно для зубьев шестерни и колеса.
Рисунок 2 – Режим нагружения зубьев
2.1.Допускаемые контактные напряжения
Допускаемые напряжения для зубьев шестерни и колеса определяют по общей зависимости:
- длительный предел контактной выносливости определяемый по табл. 2.2 [1 с.32] в зависимости от материала зубчатого колеса и вида термической обработки по среднему значению твёрдости поверхностей зубьев равной полусумме верхнего и нижнего значений их твёрдости взятых из табл. 2.1.[1 с.30]
коэффициент учитывающий шероховатость рабочих поверхностей зубьев
коэффициент учитывающий влияние скорости
коэффициент долговечности учитывающий режим нагружений и требуемый ресурс передачи принимается в пределах 1≤ ≤
коэффициент запаса контактной прочности принимается из таблицы 2.2
При твёрдости зубьев шестерни:
При твёрдости зубьев колеса:
При (притирка и обкатывание) ;
При твёрдости поверхностей зубьев менее 350 НВ
При твёрдости поверхностей зубьев более 350 НВ
Коэффициент долговечности учитывающий режим нагружений и требуемый ресурс передачи рассчитывается по формуле :
число циклов нагружений зуба соответствующее перелому кривой усталости.
условие не выполняется
требуемый ресурс рассчитываемого зубчатого колеса в циклах рассчитывается по формуле [1 с.32 ф.2.2]:
c – число вхождений в зацепление зуба рассчитываемого колеса за один оборот ;
n – число оборотов в минуту рассчитываемого колеса
требуемый ресурс передачи ч.
Для косозубых и шевронных передач с твёрдостью колеса и твёрдостью шестерни расчётное допускаемое напряжение определяют по формуле[1 с.33]:
Это напряжение не должно превышать . В противном случае принимают
2.2 Допускаемые напряжения изгиба зубьев
Допускаемые напряжения изгиба зубьев шестерни и колеса определяются по формуле:
длительный предел выносливости при «отнулевом» цикле нагружений выбирается по табл. 2.3 [1 с. 34] в зависимости от материала и твёрдости зубьев.
коэффициент запаса изгибной прочности выбирают по табл. 2.3 [1с.34]
коэффициент долговечности принимаемый в пределах 1≤ ≤
показатель степени кривой усталости; для нормализованных и улучшенных колёс; для поверхностно упрочнённых колёс.
требуемый ресурс рассчитываемого зубчатого колеса в циклах
3. Проектный расчёт на прочность закрытых цилиндрических
зубчатых передач редукторов
Предварительные геометрические размеры передачи определяют расчётом на контактную выносливость зубьев.
Исходные данные полученные при кинематическом расчёте:
- вращающий момент на шестерне
- вращающий момент на колесе
- частота вращения колеса
- передаточное число
- допускаемое контактное напряжение
- допускаемое контактное напряжение изгиба зубьев колеса
- допускаемое контактное напряжение изгиба зубьев шестерни
Рисунок 3 – Цилиндрическая зубчатая передача
Определяем предварительное значение межосевого расстояния
где знак «+» (здесь и далее) относится к внешнему зацеплению а знак «-» - к внутреннему
- вращающий момент колеса Нм
Коэффициент K в зависимости от поверхностной твёрдости зубьев шестерни и колеса имеет следующие значения
Коэффициент K : 10 8 6
Уточняем найденное значение межосевого расстояния по формуле
для косозубых и шевронных зубчатых колёс
для прямозубых зубчатых колёс
Коэффициент ширины венца зубчатого колеса для редукторных зубчатых колёс из улучшенных сталей при несимметричном расположении относительно опор 0315 04; для колёс из закалённых сталей 025 0315; при симметричном расположении 04 05; при консольном расположении – 02 025. Для шевронных передач . Для передач внутреннего зацепления . Стандартные значения для редукторов: 01; 0125; 016; 02; 025; 0315; 04; 05; 063; 08; 10; 125.
Коэффициент нагрузки рассчитывается по формуле [1 с.36 ф.2.8]:
Коэффициент учитывающий внутреннюю динамическую нагрузку зависит от окружной скорости и степени точности изготовления передачи. Окружная скорость определяется по формуле :
Степень точности выбираем по табл. 2.4 [1 с.37]. Значение коэффициента выбираем по табл. 2.5 [1 с.37].
Принимаем 8 степень точности (передачи пониженной точности).
Коэффициент учитывающий неравномерность распределения нагрузки по длине контактных линий определяется по номограмме [1 стр.38 рис. 2.4] в зависимости от коэффициентов ширины определяемый по формуле
[1 с. 39] схемы передачи и твёрдости зубьев:
Коэффициент учитывающий неравномерность распределения нагрузки между одновременно зацепляющимися парами зубьев в связи с погрешностями изготовления шестерни и колеса для косозубых передач определяется по формуле: [1 с.39 ф.2.10]
число обозначающее степень точности передачи
Определяем ширину венца колеса и округляем до ближайшего целого значения в миллиметрах [1 стр. 39]:
Определяем ширину венца шестерни и округляем до ближайшего целого значения в миллиметрах:
Определяем значение нормального модуля зубчатых колёс. Оно должно быть в пределах:
Минимальный модуль определяем из условий прочности зубьев на изгиб по известному межосевому расстоянию по следующей зависимости:
для косозубых и шевронных передач
коэффициент нагрузки принимаемый равным
Максимально допустимый модуль определяем из условия неподрезания зубьев у основания :
В диапазоне от до принимаем стандартное значение нормального модуля по ГОСТ 9563 – 60 мм.
Определяем минимальный угол наклона зубьев :
Определяем суммарное число зубьев:
Полученное значение округляем в меньшую сторону до целого числа.
Определяем число зубьев шестерни [1 с. 41 ф. 2.16]:
Округляем до целого числа принимаем данное условие выполняется.
– косозубые и шевронные колёса [1 с. 41]
Определяем число зубьев колеса :
Необходимо определить точное значение угла наклона зубьев с целью сохранения принятого межосевого расстояния :
Определяем фактическое значение передаточного числа :
Общее фактическое передаточное число не должно отличаться от заданного более чем на .
Выполняем проверочный расчёт на контактную выносливость
Если расчётные напряжения меньше допускаемых в пределах 15 20или превышают их в пределах 5 то ранее принятые параметры передачи принимают за окончательные. В противном случае необходимо изменить геометрические параметры колёс или повысить сопротивление усталости материала.
Наиболее просто изменить ширину зубчатого венца
скорректированная рабочая ширина зубчатого венца колеса
Выполняем проверочный расчёт на выносливость при изгибе для зубьев шестерни и колеса по общей зависимости:
рассчитывается по формуле :
коэффициент учитывающий внутреннюю динамическую нагрузку в передаче определяется по табл. 2.5 [1 с. 37]
коэффициент учитывающий неравномерность распределения нагрузки по длине контактных линий определяется по номограммам [1 с. 38 рис 2.4] аналогично определению коэффициента [1 с. 37]
коэффициент учитывающий форму зуба и концентрацию напряжений определяется по табл. 2.6 [1 стр. 43] в зависимости от приведённого числа зубьев и коэффициента смещения инструмента ( при отсутствии смещения :
Тогда при отсутствии смещения
коэффициент учитывающий наклон зуба рассчитывается по формуле
коэффициент осевого перекрытия определяется по формуле :
коэффициент учитывающий перекрытие зубьев определяется по формуле :
коэффициент торцевого перекрытия определяется по формуле :
Определяем геометрические размеры передачи:
d – делительный диаметр колёс определяется по формуле:
Проверка определения делительных диаметров колёс:
диаметр вершин зубьев определяется по формуле :
диаметр впадин зубьев определяется по формуле:
Определяем силы в зацеплении необходимые для расчёта валов и подшипников:
окружная сила определяется по формуле :
радиальная сила определяется по формуле :
осевая сила определяется по формуле :
Рисунок 4 – Схема сил действующих на вал от зубчатых колёс в
цилиндрической передаче
Определение компоновочных размеров
По конструктивным и технологическим соображениям в редукторах применяют ступенчатые валы имеющие различные диаметры отдельных ступеней. Предварительно диаметры консольных участков входного и выходного валов редуктора определяют по формулам:
Диаметры остальных участков этих валов для удобства посадки на вал подшипников качения зубчатых колёс и других деталей назначаются по конструктивным и технологическим соображениям с учётом необходимости фиксации деталей на валу в осевом направлении.
Полученные диаметры отдельных участков вала округляют до ближайшего значения по ряду 40 нормальных линейных размеров (ГОСТ 6636-69).
Принимаем диаметр под подшипник [2с.12]:
Предварительно выбираем подшипники лёгкой серии шарикоподшипники радиальные однорядные по ГОСТ 8338-75: 209; 210. [1с.139ТП1]
Определяем диаметр упорного буртика под подшипник [2 с.12]:
t – высота буртика величину которой принимаем в зависимости от диаметра вала [2с.12 т.2.1]:
Определяем диаметр упорного буртика под колесо [2 с.12]:
Определяем диаметр стяжного винта [2 с.14]:
Результаты сводим в таблицу 1.
Конструирование деталей зубчатой передачи
Определяем толщину диска колеса [2 с.34]:
Размеры остальных элементов зубчатых колёс принимаем [2 с.36]:
Определяем диаметр ступицы:
Определяем стандартный размер фасок [2 с.36 т.3.1]:
Определяем толщину стенки корпуса [2 с.71]:
Расчёт шпоночного соединения под колесом
на тихоходном валу редуктора
Чаще всего применяют призматические (1 с.149 т.П.6) и сегментные
(1 с.150 т. П.7) шпонки. Соединения с помощью призматических и сегментных шпонок относятся к ненапряженным соединениям.
ГОСТ 23360-78 предусматривает для каждого диаметра вала опреде-
ленные размеры поперечного сечения шпонки. Поэтому при проектных
расчетах размеры поперечного сечения шпонки b и h принимаем из табл. П.6 [1 с.149] и определяем рабочую длину шпонки . Длину шпонки со скругленными или плоскими торцами выбираем из стандартного ряда
При передаче вращающего момента на противоположных боковых
узких гранях шпонки возникают напряжения смятия а в продольном
сечении - напряжения среза (рис. 5). У стандартных шпонок размеры
b и h подобраны так что нагрузку соединения ограничивают не напряже-
ния среза а напряжения смятия. Поэтому рабочую длину шпонки опре-
Рисунок 5 – Схема напряжений в шпоночном соединении
Определяем рабочую длину шпонки из условий прочности на смятие:
При диаметре под колесом (на тихоходном валу) из таблицы П6 [1 с. 149] выбираем размеры для шпоночного соединения: соединения призматической шпонкой.
Рисунок 6 – Соединение призматической шпонкой
Следовательно выбираем шпонку ГОСТ 23360-78:
Расчёт тихоходного вала редуктора
На вал от зубчатого колеса подшипников и других деталей передаются окружные радиальные и осевые силы создающие в поперечных сечениях продольные и поперечные силы изгибающие и вращающие моменты. Таким образом вал испытывает сложную деформацию – изгиба (растяжения – сжатия) и кручения. Продольные силы создают в сечениях вала нормальные напряжения растяжения или сжатия небольшой величины поэтому они в расчётах не учитываются.
Действующие на вал силы распределены по длине ступицы ширине подшипника. При проектном расчёте считаем эти силы сосредоточенными и приложенными на середине ширины зубчатого венца или подшипника. Эти сечения принимаем за расчётные. По длине вала место приложения нагрузки зависит от расположения зубчатого колеса и опор. Муфта создаёт силу лежащую в плоскости перпендикулярной к оси вала. После приведения этих сил к оси вала последний оказывается нагруженным поперечными силами и вращающим моментом. Косозубая цилиндрическая передача кроме сил лежащих в плоскостях вызывает появление осевой силы приложенной на зубьях. Приведение этой силы к оси вала даёт осевую (сжимающую или растягивающую) силу и сосредоточенный изгибающий момент.
Силы действующие на вал от косозубой цилиндрической передачи ( определены при расчёте передачи):
окружная - - действует в вертикальной плоскости;
радиальная - и осевая - (действуют в горизонтальной плоскости);
Вращающий момент на валу – ;
Частота вращения вала – ;
Диаметр делительной окружности зубчатого колеса установленного на валу – ;
Режим нагружения – постоянный;
Требуемый ресурс – ;
Диаметр вала под подшипник – ;
Диаметр вала под колесо –
Расстояние между опорами вала координаты точек приложения сил определяем по эскизной компоновке редуктора:
Последовательность расчёта:
Определяем радиальную силу от муфты действующую на консольный участок вала по формуле [1 с.91 ф.4.2]:
Принимаем действие этой силы в вертикальной плоскости (как и силы ) направленной на увеличение деформации от силы .
Используя эскизную компоновку редуктора составляем расчётную схему вала (см.рисунок 7 а)
Опорные реакции в горизонтальной плоскости (см. рисунок 7 б):
Проверка правильности определения реакций:
Опорные реакции в вертикальной плоскости (см. рисунок 7 в):
Опорные реакции силы (см. рисунок 7 г):
Суммарные реакции в опорах (приведённые в одну плоскость) которые будут использованы в качестве радиальных нагрузок при выборе подшипников качения:
в горизонтальной плоскости (см. рисунок 7 б):
в вертикальной плоскости (см. рисунок 7 в):
изгибающие моменты от силы (см. рисунок 7 г):
изгибающий момент в сечении С (под колесом):
Суммарный изгибающий момент в сечении под колесом (сечение C – это сечение наиболее нагруженное):
Принимаем: материал вала – сталь 45 [1 с.83 т.4.1];
механическая обработка вала – тонкая обточка [1 c.98 т.4.6]; вал не подвергается поверхностному упрочнению [1 c.98 т.4.7].
Расчёт на сопротивление усталости.
Для опасного сечения вала (сечение C) расчетный коэффициент запаса прочности определяем по формуле [1 с.93 ф.4.8] а коэффициенты и по формулам [1 с.93 ф.4.10] и [1с.93 ф.4.11] соответственно:
Коэффициент долговечности:
где циклов; т.к. то
Суммарные коэффициенты и определяются по формулам [1 с.95 ф.4.20]. В этих формулах значения эффективных коэффициентов концентрации напряжений и зависят от вида концентраторов напряжений. В месте посадки колеса на вал имеется два типа концентраторов: ступенчатый переход с галтелью и шпоночная канавка. Для этих концентраторов по таблицам 4.3 и 4.4
[1 с.96-97] находим значение и :
для ступенчатого перехода с галтелью ( приняты по рекомендациям [1 с.96]):
для шпоночной канавки выполненной пальцевой фрезой:
Следовательно большее влияние на прочность вала оказывает ступенчатый переход с галтелью поэтому для расчёта принимаем
В этом сечении вал имеет сплошное круглое сечение.
По таблице 4.5 [1 с.98] находим по таблице 4.6 [1 с.98] –
; коэффициент т.к. вал не подвергается поверхностному упрочнению.
По формулам (4.14) [1 c.94] определяем амплитудные значения напряжений:
где моменты сопротивления определены по формулам [1 c.94 ф.4.15]:
Определяем коэффициент запаса прочности [1 c.93 ф.4.8]:
Следовательно вал удовлетворяет условию прочности по сопротивлению усталости.
Выбор подшипников качения
При частоте вращения n ≥ 1 мин-1 выбор подшипников производится по динамической радиальной грузоподъемности и статической радиальной грузоподъемности а при n 1 мин-1 – только при статической грузоподъемности.
d=45 мм – диаметр опорной части вала;
H и H – радиальные нагрузки действующие на подшипник;
– внешняя осевая сила ( направлена в сторону опоры 2 см.рис.7);
n = 1025 мин-1 – частота вращения внутреннего кольца подшипника;
Lh = 25000 ч – требуемый ресурс подшипника;
режим нагружения постоянный.
Последовательность расчета.
Выбираем предварительно [1 c.139 т.П1] шарикоподшипник легкой серии 210 у которого динамическая радиальная грузоподъемность
= а статическая радиальная грузоподъемность и .
Определяем эквивалентную динамическую нагрузку [1 c.108 ф.5.3]:
где номер опоры (=1;2);
коэффициент вращения ( при вращении внутреннего кольца подшипника при вращении наружного кольца);
радиальная сила действующая на подшипник H;
осевая нагрузка действующая на подшипник Н;
и коэффициенты учитывающие разное повреждающее действие радиальной и осевой нагрузок;
коэффициент безопасности учитывающий характер нагрузки
для коробок скоростей металлорежущих станков
коэффициент учитывающий температуру подшипникового узла
при температуре ≤ 100оС .
Рисунок 8 Схема установки двух шариковых подшипников
Осевую нагрузку воспринимает подшипник 2поэтому
Выбираем из таблицы 5.1[1 c.110] для соотношения
и находим коэффициент минимальной осевой нагрузки: e=029
Следовательно коэффициенты учитывающие повреждающие действия радиальной и осевой нагрузок принимаем
Дальнейший расчет ведем по более нагруженной опоре 2.
Определяем ресурс принятого подшипника[1 c.107 ф.5.1 ф.5.2]:
где n частота вращения кольца мин-1;L ресурс подшипника млн.оборотов.
где коэффициент долговечности при повышенных требованиях к надежности равной 90% (редукторы и коробки скоростей) ; коэффициент учитывающий качество металла деталей подшипника и условия эксплуатации принимаем ;
P показатель степени(для шариковых подшипников P=3);
динамическая радиальная грузоподъемность выбранного подшипникаН.
Так как ресурс выбранного подшипника на много меньше требуемого то принимаем подшипник средней серии 310 у которого динамическая грузоподъемность статическая грузоподъемность
Следовательно принимаем подшипник средней серии 310.
Во избежание появления опасных для работы остаточных деформаций на контактирующих поверхностях нагрузку подшипников ограничивают статической грузоподъемностью. Проверка на отсутствие остаточных деформаций в зоне контакта тел качения с кольцами проводится по условию
где эквивалентная статическая радиальная нагрузка Н;
статическая радиальная грузоподъемность Н.
При совместном действии на подшипник радиальной и осевой нагрузок эквивалентная статическая нагрузка определяется как наибольшее значение из двух:
где коэффициенты радиальной и осевой статических нагрузок соответственно [1 c.114 т.5.2]:
следовательно принимаем
Подшипник пригоден. При заданном ресурсе вероятность безотказной работы данного подшипника будет выше 90%.
Пантелеев В.Ф. Расчеты деталей машин: Учебное пособие. – 2е изд. доп. – Пенза: Изд-во ПГУ 2002г.
Пантелеев В.Ф. Конструирование деталей и узлов технологических и транспортных машин: - Пенза 2003 – 204с. 110ил.41 таб.
Дунаев П.Ф. Леликов О.П. Конструирование узлов и деталей маши: Учебное пособие .- 7е изд. - М.: Высшая школа 2001.
Реферат!.docx
В пояснительной записке приведен расчет редуктора к ленточному конвейеру выполненный на 45 листах в котором подробно расписана методика кинематического расчета привода и выбора электродвигателя проведен проектный расчет на прочность зубчатой передачи редуктора расчет тихоходного вала редуктора на прочность кроме этого расчет шпоночного соединения под колесом на тихоходном валу редуктора и выбора подшипников качения.
Графическая часть содержит:
формата А0 – сборочный чертеж редуктора;
формата А1 – чертеж тихоходного вала редуктора;
формата А2 – чертеж зубчатого колеса редуктора.
Содержание.doc
1.Выбор электродвигателя 5
2. Кинематический расчёт привода .6
Проектный расчёт на прочность зубчатой передачи редуктора .8
1. Выбор материала шестерни и колеса .. 8
2.Определение допускаемых напряжений ..8
2.1. Допускаемые контактные напряжения .9
2.2. Допускаемые напряжения изгибов зубьев .11
3. Проектный расчёт на прочность закрытой цилиндрической зубчатой передачи редуктора 12
Определение компоновочных размеров редуктора 22
Расчёт шпоночного соединения под колесом на тихоходном валу редуктора . ..25
Расчёт тихоходного вала редуктора ..27
Выбор подшипников качения 33