Редуктор двухступенчатый




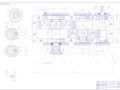
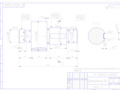
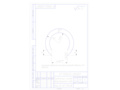
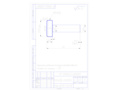
- Добавлен: 25.10.2022
- Размер: 670 KB
- Закачек: 1
Описание
Состав проекта
![]() |
![]() ![]() ![]() ![]() |
![]() ![]() |
![]() ![]() |
![]() ![]() ![]() |
![]() ![]() |
![]() ![]() ![]() ![]() |
![]() ![]() |
![]() ![]() ![]() |
![]() ![]() ![]() ![]() |
![]() ![]() |
![]() ![]() ![]() ![]() |
Дополнительная информация
sryerrr1.dwg

Сталь 45x ГОСТ 1050-88
КР 131000.62-0000001
sres3rrs8srrryere.doc
На промежуточном валу
Радиальное биение мкм
Коэф. запаса точности
Функциональный натяг мкм
Зубчатые колеса и передачи
Основы стандартизации
Число зубьев зубчатых колес
Замыкающий размер размерной цепи мм
Цель курсовой работы – получить навыки пользования нормативно-технической документацией и усвоить полученные знания по выбору сопряжений и расчёту их параметров при решении конкретных инженерных задач.
Курсовая работа состоит из графической части и расчётно-пояснительной записки.
Объем графической части и содержание расчетно-пояснительной записки 47страниц.
Графическая часть включает в себя следующие документы:
) сборочный чертёж узла (формат А1);
) рабочий чертёж детали узла (форматА3);
) рабочие чертежи калибра-пробки калибра – скобы (А4).
Оформление записки по СТП 3.1. «Общие требования к оформлению текстовых и графических студенческих работ. Текстовые материалы и иллюстрации».
Основы стандартизации8
Анализ номинальных размеров18
Выбор посадок гладких цилиндрических соединений20
1. Выбор переходной посадки20
2 Выбор посадки с натягом24
3 Расчет и выбор посадок подшипника качения26
4. Выбор посадок распорной втулки на вал и крышки подшипника в корпус30
Выбор посадок типовых соединений32
1. Выбор посадок шпоночного соединения32
2 Выбор посадок шлицевого соединения33
3 Расчёт параметров резьбового соединения35
Расчёт размерной цепи37
Обоснование требований к отклонениям формы и расположения и шероховатости поверхностей41
Средства измерений и контроля44
1 Выбор универсальных измерительных средств44
2. Проектирование калибров для контроля гладких цилиндрических деталей47
Список использованных источников50
Стандартизация - деятельность по установлению норм правил и характеристик (далее - требования) в целях обеспечения: безопасности продукции работ и услуг для окружающей среды жизни здоровья и имущества; технической и информационной совместимости а также взаимозаменяемости продукции; качества продукции работ и услуг в соответствии с уровнем развития науки техники и технологии; единства измерений; экономии всех видов ресурсов; безопасности хозяйственных объектов с учетом риска возникновения природных и техногенных катастроф и других чрезвычайных ситуаций; обороноспособности и мобилизационной готовности страны.
Стандартизация осуществляется в целях:
- повышения уровня безопасности жизни и здоровья граждан имущества физических и юридических лиц государственного или муниципального имущества экологической безопасности безопасности жизни и здоровья животных и растений и содействия соблюдению требований технических регламентов;
- повышения уровня безопасности объектов с учетом риска возникновения чрезвычайных ситуаций природного и техногенного характера;
- обеспечения научно-технического прогресса;
- повышения конкурентоспособности продукции работ услуг;
- рационального использования ресурсов;
- технической и информационной совместимости;
- сопоставимости результатов исследований (испытаний) и измерений технических и экономико-статистических данных;
- взаимозаменяемости продукции.
Стандартизация направлена на достижение оптимальной степени упорядочения в определенной области посредством установления положений для всеобщего и многократного применения в отношении реально существующих или потенциальных задач.
В развитом обществе стандартизация является одним из инструментов управления народным хозяйством. Она непосредственно влияет на повышение эффективности общественного производства представляя собой научный метод оптимального упорядочения в масштабах государства номенклатурой и качеством выпускаемой продукции. Стандарт и качество неотделимы. Государственный стандарт предназначен концентрировать передовой промышленный опыт и новейшие достижения науки и техники связывая их с перспективами развития народного хозяйства. Тем самым стандарт превращается в норму общественно необходимых требований к качеству продукции.
Стандартизацию следует рассматривать как практическую деятельность как систему управления и как науку [43].
Стандартизация как практическая деятельность заключается в установлении нормативных документов по стандартизации и применению правил норм и требований обеспечивающих оптимальное решение повторяющихся задач в сферах общественного производства и социальной жизни. Эта деятельность направлена на:
комплексное нормативно-техническое обеспечение всестороннего совершенствования управления народным хозяйством;
интенсификацию общественного производства и повышение его эффективности;
ускорение научно-технического прогресса и улучшение качества продукции;
рациональное и экономное использование ресурсов.
Стандартизация как система управления практической деятельностью осуществляется в Российской Федерации на основе Государственной системы стандартизации (ГСС) являющейся системой планового управления практической деятельностью по стандартизации. Она опирается на комплекс нормативно-технических документов устанавливающих взаимоувязанные требования по организации и методике выполнения практических работ по стандартизации.
Стандартизация как наука о методах и средствах стандартизации выявляет обобщает и формулирует закономерности деятельности по стандартизации в целом и по ее отдельным направлениям. Развитие стандартизации как науки помогает улучшать систему организации этой деятельности и способствует совершенствованию практических работ в этой области.
Объектом стандартизации (по ГОСТу Р 1.0) являются продукция работа (процесс) услуга подлежащие или подвергшиеся стандартизации которые в равной степени относятся к любому материалу компоненту оборудованию системе их совместимости правилу процедуре функции методу или деятельности. При этом услуга как объект стандартизации охватывает как услуги для населения так и производственные услуги для предприятий и организаций.
Продукция производственно-технического назначения и товары народного потребления являются наиболее традиционными объектами стандартизации на которые разработано наибольшее количество стандартов. Объектами стандартизации являются также типовые технологические процессы формы и методы организации труда и производства правила выполнения производственных и контрольных операций правила транспортирования и хранения продукции и т. п.
В социальной жизни общества объектами стандартизации являются охрана труда и здоровья населения охрана и улучшение природной среды обитания человека рациональное использование природных ресурсов средства информации и взаимопонимания людей и т. п.
ГОСТ 7798-70 Болты с шестигранной головкой класса точности В. Конструкция и размеры.
Стандарты основополагающие разрабатывают с целью содействия взаимопонимания и технического единства в различных областях науки и техники то есть они устанавливают организационные принципы и положения в целом они обеспечивают взаимодействие при разработке содержании эксплуатации продукта и услуг.
Основополагающие стандарты имеют общую целевую направленность и устанавливают согласованные требования к взаимосвязанным объектам. Чаще это объединение взаимосвязанных нормативных документов которые не противоречат закону и друг другу. Примером таких стандартов являются стандарты ЕСКД - единая система конструкторской документации стандарты по организации национальной системы Российской Федерации.
Основная цель нормативного документа ГОСТР 1.5 - обеспечение организационного единства и создания условий для своевременной подготовки к применению стандартов.
Настоящий стандарт устанавливает общие требования к построению изложению оформлению содержанию и обозначению межгосударственных стандартов правил и рекомендаций по межгосударственной стандартизации и изменений к ним.
Требования настоящего стандарта применяют при разработке подготовке к принятию и изданию межгосударственных стандартов правил и рекомендаций по межгосударственной стандартизации (далее - стандарты за исключением случаев когда необходимо специально указать на статус документа) и изменений к ним.
Примечание. Дополнительные требования к стандартам на оборонную продукцию установлены в специальном стандарте.
Требования настоящего стандарта не распространяются на действующие стандарты которые были приняты до введения его в действие. Их приведение в соответствие с требованиями настоящего стандарта осуществляют при очередном пересмотре указанных стандартов а в обоснованных случаях - при разработке очередных изменений к ним.
Стандарт — нормативный документ по стандартизации разработанный как правило на основе согласия характеризующегося отсутствием возражений по существенным вопросам у большинства заинтересованных сторон принятый (утвержденный) признанным органом (предприятием).
Стандарты направлены на достижение оптимальной пользы для общества и базируются на обобщенных результатах науки техники и практического опыта.
Элементы стандарта. Стандарт состоит из отдельных элементов. В стандарт в общем случае включают следующие элементы:
термины и определения;
обозначения и сокращения;
основные нормативные положения;
библиографические данные.
Элементы: «Содержание» «Введение» «Нормативные ссылки»
«Термины и определения» «Обозначения и сокращения» «Приложения» «Библиография» приводят в стандарте при необходимости то есть необязательные.
Титульный лист содержит эмблему федерального органа исполнительной власти наименование и обозначение стандарта его статус наименование стандарта и слова наименование стандарта официальные выходные данные.
Предисловие размещают на следующей странице после титульного листа (на его обороте) и начинают с соответствующего заголовка который помещают в верхней части страницы посередине записывают с прописной буквы и выделяют полужирным шрифтом.
Содержание. Если объем стандарта превышает 24 страницы рекомендуется включать в него элемент «Содержание». В элементе «Содержание» номера подразделов приводят после абзацного отступа равного двум знакам относительно номеров разделов. Элемент «Содержание» размещают после предисловия стандарта начиная с новой полосы страницы. При этом слово «Содержание» записывают в верхней части этой страницы посередине с прописной буквы и выделяют полужирным шрифтом.
Наименование стандарта должно быть кратким точно характеризовать объект стандартизации. Наименование стандарта как правило должно состоять из заголовка и подзаголовка а также перевод на английский язык под полужирной чертой пишется дата введения стандарта.
Область применения. В элементе «Область применения» указывают назначение стандарта и область его распространения (объект стандартизации) а при необходимости конкретизируют область применения стандарта. При указании назначения и области распространения стандарта применяют следующие формулировки: «Настоящий стандарт устанавливает » или «Настоящий стандарт распространяется на и устанав-
Настоящий стандарт устанавливает правила построения изложения оформления и обозначения национальных стандартов Российской Федерации общие требования к их содержанию а также правила оформления и изложения изменений к национальным стандартам Российской Федерации.
Настоящий стандарт не распространяется на действующие национальные стандарты Российской Федерации.
Термины и определения. В стандарте элемент «Термины и определения» приводят при необходимости терминологического обеспечения взаимопонимания между различными пользователями данного стандарта путем определения терминов
Элемент «Термины и определения» оформляют в виде одноименного раздела и начинают со слов:
«В настоящем стандарте применены следующие термины с соответствующими определениями».
Обозначения и сокращения. Если в стандарте необходимо использовать значительное количество (более пяти) обозначений иили сокращений то устанавливают данный элемент.
Нормативные ссылки. Присутствуют в стандарте если есть ссылки на государственный межгосударственный и международные стандарты и классификаторы.
Приложения. Материал дополняющий основную часть стандарта выполняется в виде приложения. Приложение пишется по центру. Приложение обозначается прописными буквами русского алфавита с буквы А (исключая буквы Ё О 3 И Ч Ь Ъ Ы).
Библиография. Если в стандарте есть ссылки на правила рекомендации нормы и санпины положение руководства то необходимо создать элемент библиография.
Библиографические данные. Располагаются на последней странице стандарта. Указывают: 1) индекс универсальной десятичной классификации (УДК) 2) код группы или подгруппы межгосударственного классификатора стандартов 3) ключевые слова.
Мы провели анализ ГОСТ 7798-70 Болты с шестигранной головкой класса точности В. Конструкция и размеры.
Данный документ содержит следующие элементы титульный лист; предисловие; область применения; основной текст; информационные данные.
Согласно ГОСТ Р 1.5 Пункт 6. Требования к оформлению стандарта.
1. Требования к оформлению текста проекта стандарта
1.1. Проект стандарта оформляют машинным способом. При этом используют гарнитуру шрифта Arial и Symbol.
1.2. Расстояние между заголовком раздела (подраздела) и предыдущим или последующим текстом а также между заголовками раздела и подраздела должно быть равно не менее чем четырем высотам шрифта которым набран основной текст стандарта.
Расстояние между строками заголовков подразделов и пунктов принимают таким же как в тексте.
1.3. Абзацный отступ должен быть одинаковым по всему тексту проекта стандарта и равен пяти знакам.
При оформлении проекта стандарта поле с левой стороны текста должно быть шириной не менее 20 мм.
1.4. При подготовке текста проекта стандарта буквы греческого и иных алфавитов формулы отдельные условные знаки допускается вписывать черной пастой или тушью. При этом плотность вписанного текста должна быть приближена к плотности остального текста. Если чертежи схемы диаграммы рисунки иили другой графический материал невозможно выполнить машинным способом то используют черную тушь или пасту.
1.5. При подготовке проекта стандарта должна быть обеспечена возможность изготовления его копии надлежащего качества способами репрографии.
2. Требования к оформлению страниц стандарта и его проекта
2.1. Первую страницу межгосударственного стандарта и его проекта оформляют в соответствии с Приложением Ж а первую страницу правил (рекомендаций) по межгосударственной стандартизации и их проекта - в соответствии с Приложением И.
Если при принятии межгосударственного стандарта установлена единая для всех государств дата его введения в действие *> то эту дату приводят на первой странице данного стандарта. В этом случае дату размещают под чертой ограничивающей снизу наименование стандарта и приводят аналогично записи в соответствии с Приложением И а также сопровождают сноской следующего содержания: "Единая для всех указанных в предисловии государств".
2.2. Оформление и нумерация страниц стандарта и его проекта (за исключением титульного листа и первой страницы) - в соответствии с Приложением К. При этом нумерацию всех страниц за исключением указанных в 6.2.4 проставляют арабскими цифрами.
Последнюю страницу проекта стандарта оформляют в соответствии с правилами приведенными в Приложении В.
2.3. При оформлении проекта стандарта на всех его страницах под индексом "ГОСТ" ("ПМГ" или "РМГ") приводят в скобках слово "проект" код альфа-2 (двухбуквенный код на основе латинского алфавита) страны-разработчика по МК (ИСО 3166) 004 и указывают его редакцию выделяя эту информацию курсивом. При этом предлагаемое обозначение стандарта (без цифр обозначающих год принятия стандарта) приводят только в следующих случаях:
если разработка проекта стандарта направлена на пересмотр действующего стандарта;
если это обозначение формируют в соответствии с 8.4 или 9.1.14;
если проект стандарта разработан в развитие уже действующего комплекса стандартов обозначение которого сформировано согласно 8.3.
В остальных случаях приводят только индекс: "ГОСТ" "ПМГ" или "РМГ" (без регистрационного номера документа и цифр обозначающих год его принятия).
На титульном листе проекта документа вместо слов: "Издание официальное" приводят слова: "Настоящий проект стандарта (правил рекомендаций) не подлежит применению до его принятия".
На первой странице проекта стандарта вместо слов: "Издание официальное" приводят слово "Проект" и после запятой указывают его редакцию выделяя эти слова курсивом.
2.4. Страницы стандарта на которых размещают элементы: "Предисловие" "Содержание" и "Введение" нумеруют римскими цифрами начиная с номера "II".
2.5. При подготовке к изданию стандарта на странице на которой приводят элемент "Предисловие" в нижней части страницы указывают данные об издательстве осуществляющем издание стандарта.
Если стандарт издается централизованно для всех государств то под данными об издательстве приводят следующую информацию: "Исключительное право официального опубликования настоящего стандарта на территории указанных выше государств принадлежит национальным органам по стандартизации (по управлению строительством) этих государств".
В остальных случаях под данными об издательстве приводят более конкретные сведения в соответствии с 3.15.1.
2.6. При оформлении стандарта содержащего сведения ограниченного распространения и его проекта соблюдают соответствующее законодательство действующее в государстве - разработчике стандарта и требования установленных на его основе соответствующих положений наставлений инструкций и правил по режиму.
Согласно ГОСТР 1.5 пункт 6 стандарт ГОСТ 7798-70 соответствует требованиям к оформлению стандарта .
В соответствии с Гост Р 1.0-2004 исследуемый нами ГОСТ 7798-70 Болты с шестигранной головкой класса точности в. Конструкция и размеры. В зависимости от объекта и аспекта стандартизации а также содержания устанавливаемых требований данный стандарт относится к виду - стандарты на продукцию.
ГОСТ Р 1.0-2004 Стандартизация в российской федерации. Основные положения.
Цели и принципы стандартизации в российской федерации установлены федеральным законом от 27 декабря 2002 г. N 184-фз "о техническом регулировании".
Настоящий стандарт устанавливает общие правила формирования ведения и применения положений системы стандартизации в российской федерации.
Положения основополагающих стандартов системы стандартизации в Российской Федерации разработаны для применения федеральными органами исполнительной власти субъектами хозяйственной деятельности техническими комитетами по стандартизации общественными объединениями и заинтересованными лицами.
При использовании настоящего стандарта применительно к оборонной продукции (работам услугам) поставляемой для федеральных государственных нужд по государственному оборонному заказу продукции (работам услугам) используемой в целях защиты сведений составляющих
государственную тайну или относимой к охраняемой в соответствии с законодательством Российской Федерации информации ограниченного доступа продукции (работам услугам) сведения о которой составляют государственную тайну учитывают также дополнительные требования изложенные в специальных стандартах устанавливающих правила разработки указанных документов.
ГОСТ 7798-70 распространяется на болты с шестигранной головкой класса точности В с диаметром резьбы от 6 до 48 мм.
Рисунок 1.1 - Болты с шестигранной головкой
Несмотря на то что в последнее время появилось много крепежных устройств различных конструкций болты по-прежнему находят самое широкое применение в крепеже. Болты и гайки используются как крепеж и в машиностроении и в строительстве и в мебельных конструкциях и просто в быту. Особенно незаменимы болты в тех случаях когда крепежный элемент по диаметру должен быть более 10мм. Болты и гайки относятся к элементам резьбовых соединений.
В России для резьбовых соединений принята метрическая цилиндрическая резьба.
В качестве материала для изготовления болтов и гаек чаще всего выбирают сталь марки Ст- 35. Это обеспечивает достаточную прочность болтов на разрыв и срез а также стойкость резьбы против смятия и срезания при больших усилиях затяжек.
Необходимо заметить что инструменты предназначенные для затягивания болтов и гаек изготавливаются такими чтобы с их помощью не могло случиться разрушение крепежных деталей как то: сварачивание резьбыили разрыв болтов. Для этого ручка ключа изготавливается длиной равной 15- 20диаметров затягиваемого болта. Ключ с более длинной ручкой при затягивании может разрушить болт.
В случае изготовления болтов и гаек из более мягких сталей чем сталь Ст- 35 легко будут срезатьсяили сминаться не только витки резьбы но и грани головки болта при многократном заворачивании его ключом.
Более твердый материал для болтов чем сталь Ст- 35 делает крепеж хрупким что также плохо для этих изделий.
Болты изготавливаются различной длины и диаметра. Небольшие длиной до 50мм болты увеличивают следующий размер на 5мм длиной более 50мм каждый следующий размер увеличивают на 10мм.
Стандартные диаметры болтов наиболее ходовых размеров представлены в таблице 1. Конструкция болтов бывает также разной.
С полной нарезкой резьбы стержня и с неполной со стандартной шестигранной головкой под ключ и с увеличенной. Изготавливаются болты и с полукруглой гладкой головкой при этом снизу головки выполняется четырёхгранная блокирующая от проворачивания часть болта. Болты небольшого диаметра изготавливают с головкой со шлицами под крестовую отвёрткуили плоскую.
На практике важно бывает знать какое усилие способен выдержать болт на разрыв в зависимости от его диаметра.
Моменты затяжки измеряют с помощью динамометрического ключа.
Гайки для болтов также изготавливаются предпочтительно из стали Ст- 35с соответствующей резьбой по диаметру болтов.
Высота гаек такова чтобы выдержать усилие затяжки. Увеличение числа витков резьбы в гайке приводит к увеличению её высоты но замет-
ного увеличения надёжности гайки при этом не происходит.
Анализ номинальных размеров
Курсовую работу начали с выполнения сборочного чертежа. Размеры деталей и сопряжений приведенных на чертеже послужили основой для расчетов и выбора посадок.
Таблица 2.1 - Анализ номинальных размеров
Анализируемый размер
Диаметр первичного вала под внутреннее кольцо подшипника 207
Размеры подшипников качения нормируются ГОСТ 8338-75
Диаметр отверстия под наружное кольцо подшипника 207
Диаметр внутреннего кольца подшипника 209
Диаметр наружного кольца подшипника 209
Диаметр внутреннего кольца подшипника 310
Диаметр наружного кольца подшипника 206
Номинальный размер для посадки с натягом
Размеры шпонки для вала d=60мм
Диаметр посадочной поверхности вала под зубчато колесо для переходной посадки
Диаметр распорной втулки
Наружный диаметр шлица
Параметры шлицевого соединения по ГОСТ 1139-80
Внутренний диаметр шлица
Диаметр резьбы болта
Базовыми размерами при выполнении чертежа являются:
)Размеры зубчатых колес которые позволяют определить d=m*z мм.
d4=m*z4=4*73=292 мм.
)Размеры шпонок принимаем по ГОСТ 23360-78 исходя из диаметров валов. По диаметру вала d=20мм ширина шпонки b = 6 мм; высота шпонки h =6мм; глубина паза вала t1 =35мм; глубина паза втулки t2 = 28 мм.
По диаметру вала d=56мм ширина шпонки b = 16 мм;
высота шпонки h =10мм; глубина паза вала t1 =6 мм; глубина паза втулки t2 = 4.3 мм.
)Размер шлицевого соединения выбираем исходя из условий задания и пользуясь ГОСТ 1139-80 По наружному диаметру и заданной серии выбираем номинальные параметры шлицевого сопряжения: наружный диаметр D =40мм; внутренний диаметр d = 36 мм; число шлицев z = 8; ширина шлица b =7 мм.
Остальные размеры принимаем конструктивно. При этом соблюдая все правила Единой системы конструкторской документации (ЕСКД).
На сборочном чертеже выполнены все виды и разрезы приведенные на схеме и проставлены позиции деталей. Спецификация оформлена на стандартном бланке и приложена в расчетно-пояснительную записку.
Посадки и размерная цепь нанесены на сборочный чертеж по мере их расчета. При конструировании нового механизма узла или детали нормальные размеры (диаметры длины расстояния между осями уступы и т.д.) находят расчётом их на прочность и жёсткость а так же конструктивно (произвольно) исходя из совершенства геометрических форм и обеспечения технологичности конструкций изделий.
Выбор посадок гладких цилиндрических соединений
1. Выбор переходной посадки
Для переходной посадки указанной на схеме определим номинальный диаметр замерив его на сборочном чертеже и округлив до ближайшего значения из ряда [2]. Радиальное биение и коэффициент запаса точности выберем из задания по своему варианту.
номинальный размер 56;
радиальное биение Fr = 48 мкм;
коэффициент запаса точности KT = 15
Для обеспечения заданного радиального биения максимальный зазор Smax находим по формуле 4.3 [2 с. 8]
Прежде чем выбрать посадку определимся с системой образования посадки. В рассматриваемом примере примем систему отверстия так как точные отверстия обрабатываются дорогостоящим мерным инструментом (зенкерами развертками протяжками и т. п.). Каждый такой инструмент применяют для обработки только одного размера с определенным полем допуска. Валы же независимо от их размера обрабатывают одним и тем же резцом или шлифовальным кругом.
При широком применении системы вала необходимость в мерном инструменте многократно возрастет поэтому предпочтение отдается системе отверстия.
Примем поле допуска основного вала 56 js6 и по таблицам стандартов [2] определим цифровые значения предельных отклонений:
верхнее es=+9мкм; нижнее e ЕI=0мкм. Для выбранной переходной посадки построим схему расположения полей допусков и определим:
наибольший предельный размер отверстия Dнб = 56019 мм;
наименьший предельный размер отверстия Dнм = 56000 мм;
наибольший предельный размер вала dнб = 56009 мм;
наименьший предельный размер вала dнм = 55991мм;
допуск отверстия TD =19 мкм;
допуск вала Td = 19 мкм;
наибольший зазор Sma
наибольший натяг Nma
средний зазор Sср =9.5мкм который соответствует средним размерам деталей и определяется по формуле 4.4 [2 с. 9] :
где =192=9.5мкм серединное отклонение отверстия; [2 с. 9];
=0мм - серединное отклонение вала. [2 с. 9];
Схему полей допусков покажем на рисунке 3.1.
Рисунок 3.1 - Схема расположения полей допусков переходной посадки
Определим вероятность получения в данной посадке зазоров и натягов считая что рассеяние размеров подчиняется нормальному закону который описывается кривой Гаусса. На расстоянии х =Sср =95мкм от оси у находится ордината соответствующая нулевому зазору (натягу). Заштрихованная площадь характеризует вероятность получения соединений с зазором незаштрихованная – с натягом. Вся площадь под кривой соответствует общему числу сопряжений данной посадки т. е. вероятность равна 1 или 100%.
Строим кривую Гаусса для закона нормального распределения (рисунок 3.2).
Рисунок 3.2- Кривая Гаусса для закона нормального распределения
По формуле 4.5 [2 с. 10] найдем среднее квадратическое отклонение
где:TD - допуск отверстия;
а относительное отклонение Z равно [2 с. 10] :
Определим диапазон рассеяния зазоров и натягов R допуск посадки Т по формулам 4.6 и 4.7 [2 с. 10]
Т = TD + Td = 19+19=38 мкм..(3.6)
Вероятное количество сопряжений с зазором находим по формуле 1.8[2 с. 10]
где 05 (50%) – половина площади под кривой Гаусса;
Ф(z) – функция от z соответствующая площади ограниченной
участком кривой между центром группирования и ординатой с нулевым зазором (натягом).
Определим значение функции Ф(z) [6]:
Вероятное количество сопряжений с зазором
Таким образом вероятное количество сопряжений с натягом (заштрихованная площадь кривой)
2 Выбор посадки с натягом
Посадки с натягом необходимы для получения неподвижных неразъёмных соединений без дополнительного крепления деталей. Эти посадки должны передавать определённые осевые силы и (или) крутящие моменты. Поэтому на схеме поля допусков валов всегда будут расположены выше полей допусков отверстий что указывает на гарантированный натяг в соединении.
Номинальный размер посадки с натягом равен 60 (исходя из размера подшипника 310 у которого d=50мм) максимальный и минимальный функциональные натяги равны: Nmax функц. = 150 мкм и Nmin функц. =30 мкм. Необходимо подобрать посадку с натягом.
Сначала выбираем систему образования посадки. В рассматриваемом примере примем систему отверстия. По ГОСТ 25346 [2] выберем посадку у которой значения натягов близки к заданным. Ближайшей посадкой является 60 H7t6 для которой Nmax табл. = 85 мкм и Nmin табл. =36 мкм.
Построим схему расположения полей допусков .
наибольший предельный размер отверстия Dнб =60030 мм;
наименьший предельный размер отверстия Dнм =60.000 мм;
наибольший предельный размер вала dнб =60.066 мм;
наименьший предельный размер вала dнм =60.085 мм;
допуск отверстия TD = 30 мкм;
допуск вала Td = 19 мкм.
Схема расположения полей допусков посадки с натягом представлена ниже.
На схеме горизонтальной штриховкой обозначим запас прочности деталей Nз.пр. =150-85=65мкм вертикальной штриховкой - запас на эксплуатацию Nз.эк. =66-60=6 мкм.
Схема расположения полей допусков посадки с натягом представлена на рисунке 3.3.
Рисунок 3.3 - Схема расположения полей допусков посадки с натягом
3 Расчет и выбор посадок подшипника качения
Для подшипника 207 при умеренной нагрузке и радиальной реакцией на опору R = 15кН выбрать посадки по наружному и внутреннему кольцам.
На первом этапе по номеру подшипника определяем его номинальные размеры:
мм – наружный диаметр наружного кольца;
мм – внутренний диаметр внутреннего кольца;
мм – ширина колец подшипника;
0мм– ширина фаски кольца подшипника.
Эти данные приводятся в ГОСТ 3478 в специальной литературе по подшипникам качения в справочниках конструктора-машиностроителя [4 и др.].
При местном нагружении наружного кольца подшипника поле допуска отверстия в корпусе выберем согласно рекомендациям приведенным в [3]. Для радиального подшипника нулевого класса точности установленного в разъемном корпусе рекомендуемое поле допуска 72Js7 а посадка наружного кольца подшипника в отверстие корпуса - 72Js7l0 где l0 - обозначение поля допуска наружного кольца подшипника с классом точности 0.
При циркуляционно нагруженного внутреннего кольца поле допуска вала определим по интенсивности нагрузки PR по формуле [1]:
где R – радиальная реакция опоры на подшипник (радиальная нагрузка) кН;
b – рабочая ширина посадочного места м (b = B-2r B – ширина подшипника r - ширина фаски кольца подшипника);
Kп – динамический коэффициент посадки зависящий от характера нагрузки (при перегрузке до 150% умеренных толчках и вибрации Kп = 1; при перегрузке до 300% сильных ударах и вибрации Kп = 18);
FA – коэффициент неравномерности распределения нагрузки на тела качения (для радиальных и радиально-упорных подшипников FA = 1);
F – коэффициент учитывающий степень ослабления посадочного натяга при полом вале (при сплошном вале F = 1).
Данной интенсивности нагрузки и 0 классу точности подшипника соответствует поле допуска вала 35n6 [3] а посадка имеет вид 35L0n6 где L0 - обозначение поля допуска внутреннего кольца подшипника с 0 классом точности.
Определим числовые значения предельных отклонений наружного кольца 72l0(-0013) внутреннего кольца 35L0(-0012) [3] отверстия в корпусе 72Js7(±0.015) вала 35n6() [3] и построим схему расположения полей допусков .
Проверим наличие радиального посадочного зазора в подшипнике при наибольшем натяге в посадке внутреннего кольца на вал. Величина посадочного радиального зазора S определяется по формуле [2 c.15] :
S = Sср – Δdнб (3.12)
где Sср - средний начальный радиальный зазор в подшипнике мкм;
Δdнб - наибольшая диаметральная деформация беговой дорожки кольца подшипника после соединения с валом мкм.
Sср = = 37.75мкм(3.13)
где Sнб и Sнм - наибольший и наименьший допустимые радиальные зазоры в подшипнике качения.
Наибольшую диаметральную деформацию беговой дорожки определим из выражения
dвн. и dнар. - диаметры внутреннего и наружного колец подшипника качения мм.
Расчет показывает что после соединения внутреннего кольца подшипника качения с валом посадочный радиальный зазор в подшипнике качения:
S =37.75-20.2=17.5мкм
Зазор обеспечивает свободное вращение подшипника.
Рисунок 3.4 – Схемы полей допусков посадок подшипника качения
4. Выбор посадок распорной втулки на вал и крышки подшипника в корпус
Для таких соединений применяются посадки низкой точности которые предназначены для подвижных соединений не требующих точности перемещения и работающих в условиях пыли и грязи.
Выбранные посадки и их данные сводим в таблицу 3.1
Примем для распорной втулки на вал посадку обеспечивающую зазор 45 D9к6 несистемная посадка а для крышки подшипника посадку 85Н7d9 посадка в системе отверстия с зазором.
Таблица 3.1 - Посадки распорной втулки на вал и крышки подшипника в корпус
Параметры сопряжений
верхнее отклонение отверстия
нижнее отклонение отверстия
верхнее отклонение вала
нижнее отклонение вала
Предельные размеры отверстий
Предельные размеры валов
Рисунок 3.5 - Схема полей допусков посадки распорной втулки на вал
Рисунок 3.6 - Схема полей допусков посадки крышки подшипника в корпус
Выбор посадок типовых соединений
1. Выбор посадок шпоночного соединения
По диаметру вала d=60мм. Определить номинальные размеры элементов шпоночного соединения по ГОСТ 23360-78;
ширина шпонки b=18мм; высота шпонки h=1мм; глубина паза вала t1=7 мм;
глубина паза втулки t2 = 4.4 мм.
Вид шпоночного соединения – свободное.
По таблицам выбираем посадки а по ГОСТ 25347-82 определяем допуски на размеры шпонки паза вала и паза втулки:
ширина шпонки - 18h9 = 18 –0052 мм;
ширина паза вала – 18H9 = 18+0.052 мм;
ширина паза втулки– 18D10 = 18 мм;
Определить допуски несопрягаемых размеров ГОСТ 25347-82
высота шпонки h=11h11=11-011 мм
глубина паза вала t1=7+02мм;
глубина паза втулки t2 = 44+02 мм;
длина паза вала ln = 50H15 = 50+084мм.
Строим схему полей допусков (рисунок 4.1).
Рисунок 4.1- Схема полей допусков шпоночного соединения
2 Выбор посадок шлицевого соединения
Дано шлицевое соединение с прямобочным профилем зуба средней серии воспринимающее ударные нагрузки и обеспечивающее нормальную точность центрирования.
По наружному диаметру и заданной серии выбираем номинальные параметры шлицевого сопряжения [3]: наружный диаметр D =40мм; внутренний диаметр d = 36 мм; число шлицев z = 8; ширина шлица b =7 мм.
выбираем центрирование по наружному диаметру D так как шлицевое сопряжение неподвижное имеет высокую точность центрирования и воспринимает спокойную нагрузку.
Посадочными поверхностями в данном случае является наружный диаметр D и ширина шлицев b.
Согласно рекомендациям [3] предпочтительными посадками обеспечивающими подвижность соединения являются: для D- для b –
Цифровые значения предельных отклонений приведены в тех же таблицах что и для гладких сопряжений [2]:
Схемы расположения полей допусков прямобочного шлицевого сопряжения приведены.
Приведем условные обозначения на чертежах:
шлицевого сопряжения ;
Рисунок 4.2 - Схемы полей допусков шлицевого соединения
3 Расчёт параметров резьбового соединения
По ГОСТ 9150-81 основные размеры параметров резьбы М 6*1-6Н6g
ГОСТ 16093-81находим предельные отклонения диаметров резьбы (в мкм):
Верхнее отклонение для dd1d2 .. -26мкм
Нижнее отклонение для d . –206мкм
Нижнее отклонение для d 2 - 138мкм
Нижнее отклонение для DD1D2 . 0мкм
Верхнее отклонение для D2 +150мкм
Верхнее отклонение для D1 +236мкм
Подсчитываем предельные размеры болта и гайки:
dmax =60 – 0026 = 6974мм
dmin =60 – 0206 = 6 794мм
d2max =535 - 0026 = 5324мм
d2min = 535-0206=5144мм
d1max = 4918- 0026 = 4892мм
d1min – впадина не должна выходить за линию плоского среза
Dmax – не нормируется
D2max = 535+0150 = 55мм
D1max = 4918+0236 =5154мм
Строим схемы полей допусков (рисунок 4.4).
Рисунок 4.4 - Схемы полей допусков резьбового соединения
Расчёт размерной цепи
Построим схему размерной цепи и покажем на рисунке 5.1
Рисунок 5.1 – Схема размерной цепи
Дан замыкающий размер БΔ =0+09мм (номинальный размер с предельными отклонениями) – это зазор обеспечивающий условия работы подшипникового узла при температурных деформациях. Требуется определить номинальные размеры и предельные отклонения составляющих звеньев.
Построим размерную цепь определим увеличивающие и уменьшающие звенья. Нанесем их на сборочный чертеж.
Номинальные размеры составляющих звеньев определим по сборочному чертежу. При этом один из размеров может быть «увязочным» для того чтобы соблюдалось условие (5.1). В нашем примере Б1 = 17 мм Б3 = 17 мм Б4 = 100 мм (что соответствует ряду R5). выражения (6.1) [2 с.23]
= 100 – (19 + Б2 + 19);
Определим допуски составляющих звеньев. Наиболее простым является метод равных допусков но его применяют в том случае если все составляющие звенья близки по своим номинальным размерам т. е. находятся в одном размерном интервале. В нашем случае этот метод не применим поэтому для обеспечения полной взаимозаменяемости воспользуемся методом равноточных допусков т. е. допуски всех составляющих размеров должны соответствовать одному квалитету.
Согласно принципу построения системы допусков и посадок для типовых соединений деталей машин одному квалитету соответствует постоянное количество единиц допусков – а = const [4] которое определяет точность размера. Величину допуска рассчитывают по формуле
где i является мерой точности и для размеров от 1 до 500 мм определяется зависимостью
i = 045 + 0001Б.(5.3)
допуск посадки определяется по формуле (6.2) [2 с.23]
Для составляющих звеньев от 1 до 500 мм значение i можно выбрать из таблицы приведенной в [5]:
iБ1 = iБ3 = 108 мкм iБ4 = 217 мкм iБ2 = 186 мкм. Тогда
Ближайшие стандартное значение a соответствуют 11-му квалитету JT11(a = 100).
Допуски этих размеров найдём из таблицы допусков [4]:
ТБ1 = ТБ3 = 110 мкм ТБ4 = 220 мкм.
Допуск «увязочного» звена определим из уравнения (6.2) [2 с.23]:
0 = 220 + (110 + ТБ2 + 110) ТБ = 460 мкм
что точнее 11-го квалитета но технологически легко достигается обычным точением.
Предельные отклонения составляющих звеньев кроме «увязочного» рекомендуется назначать для охватывающих размеров как для основных отверстий: EJ = 0 ES = +TБ; для охватываемых как для основных валов:
es = 0 e для прочих размеров расположение поля допуска симметричное т. е. ±ТБ2.
Так для Б1 и Б3 es = 0 e для Б4 ES = +220 мкм EJ = 0.
Нижнее предельное отклонение «увязочного» звена ei Б2 определим из уравнения (5.3):
+900 = +220 – (-110 + ei Б2 – 110)
Верхнее предельное отклонение «увязочного» звена es Б2 определим из уравнения (5.4):
= 0 – (0 + es Б2 – 0)
Правильность решения подтверждает проверка:
0 = 0- (-460) = 460 мкм.
Окончательные значения размеров запишем в таблицу 5.1.
Таблица 5.1- Параметры звеньев размерной цепи
Обозначения размеров
Обоснование требований к отклонениям формы и расположения и шероховатости поверхностей
Выбор параметров шероховатости поверхности производится в соответствии с ее функциональным назначением.
Основным во всех случаях является нормирование высотных параметров. Предпочтительно в том числе и для самых грубых поверхностей нормировать параметр Ra который лучше отражает отклонения профиля поскольку определяется по значительно большему числу точек чем Rz.
Параметр Rz нормируется в тех случаях когда прямой контроль Ra с помощью профилометров невозможен (режущие кромки инструментов и т. п.).
Следует применять в первую очередь предпочтительные значения.
В настоящее время существует несколько способов назначения шероховатости поверхности.
а) Рекомендации по выбору числовых значений для наиболее характерных видов сопряжений часть которых приведена в таблице 6.1.
Таблица 6.1 – Рекомендуемые значения параметра Rа
Характеристика поверхности
Значение параметра Ra мкм
Посадочные поверхности подшипников скольжения
Поверхности деталей в посадках с натягом
Поверхности валов под уплотнения
б) Шероховатость устанавливается стандартами на детали и изделия а также на поверхности с которыми они сопрягаются например требования к шероховатости поверхностей под подшипники качения (таблица 6.2).
в) Когда отсутствуют рекомендации по назначению шероховатости поверхности ограничения шероховатости могут быть связаны с допуском размера (IТ) формы (TF) или расположения (ТР). Большинство геометрических отклонений детали должно находиться в пределах поля допуска размера (рисунок 6.1).
Рисунок 6.1 - Назначение шероховатости
Поэтому величину параметра Rz рекомендуется назначать не более 033 от величины поля допуска на размер либо 05 04 от допуска расположения или формы. Если элемент детали имеет все три допуска то следует брать допуск с наименьшей величиной.
Таблица 6.2 - Шероховатость поверхностей под подшипники качения
Посадочная поверхность
Номинальный размер мм
Значение параметра Ra мкм не более
Класс точности подшипника
Опорных торцов заплечиков
Отклонения формы расположения шероховатость поверхности так же
как и отклонение собственно самого размера входят в общую классификацию отклонений геометрических параметров [7] где они представлены членами ряда Фурье.
Термины и определения основных видов отклонений форм и расположения представлены ГОСТ 24642. В основу нормирования и количественной оценки отклонений формы и расположения поверхностей положен принцип прилегающих прямых поверхностей и профилей.
Согласно ГОСТ 24643 для каждого вида допуска формы и расположения установлено 16 степеней точности [4].
В зависимости от соотношения между допуском размера и допусками формы или расположения установлены уровни относительной геометрической точности: А - нормальная (допуски формы или расположения составляют примерно 60% допуска размера); В – повышенная (допуски формы или расположения составляют примерно 40% допуска размера); С – высокая относительная геометрическая точность (допуски формы или расположения составляют примерно 25% допуска размера). Допуски формы цилиндрических поверхностей соответствующие А В С составляют примерно 30 20 и 12% допуска размера так как допуск формы ограничивает отклонение радиуса а допуск размера – отклонение диаметра поверхности.
Уровни относительной геометрической точности устанавливают в тех случаях когда по функциональным или технологическим причинам отклонения формы и расположения должны быть меньше допусков размеров например допуски формы и расположения посадочных мест вала и корпуса в сопряжениях с подшипниками качения или со ступицей зубчатого колеса. В общем случае допуски формы и расположения ограничивают допуском на размер.
При выполнении рабочего чертежа вала в курсовой работе мы пользовались рекомендациями приведенными в табл. 6.1 [8].
Средства измерений и контроля
Выбор измерительных средств предопределён организационно-технической формой производства (единичное серийное массовое). При единичном производстве как правило применяют универсальные приборы и инструменты. При серийном и массовом производствах используют специальные измерительные устройства (механические полуавтоматические и автоматические) среди которых наиболее распространёнными являются калибры.
1 Выбор универсальных измерительных средств
Одним из главных критериев выбора измерительных средств является предельная (наибольшая возможная) погрешность которая может возникнуть при измерении размера этим средством. ГОСТ 8.051 устанавливает допускаемые погрешности измерения изм при приемочном контроле деталей; она составляет от 20 до 35% от допуска на измеряемый диаметр. Для точных квалитетов этот процент выше для грубых – ниже.
Полагая что суммарная погрешность измерения сум близка к погрешности средств измерения с.и. подобрать средства измерения для контроля размеров вала и отверстия сопрягаемых по посадке с натягом из условия с.и.≤ изм.
Измерению подлежит размер отверстия ø60H7+0.030 мм
Допуск отверстия равен Т=30 мкм. По табл. 8.1 найдем допускаемую погрешность измерения изм = 9 мкм и рассчитаем значение А мет()
Погрешность измерения оказывает влияние на результаты измерения которые оцениваются следующими параметрами:
m – количество деталей в процентах от общего количества измеренных имеющих размеры выходящие за предельные табличные размеры и неправильно принятых в числе годных;
n – количество деталей в процентах от общего количества измеренных имеющих размеры не превышающие предельные размеры и неправильно забракованных;
с – вероятная предельная величина выхода размера у неправильно принятых деталей.
Параметры m n и с зависят от точности измерении характеризуемой соотношением А мет() между средним квадратичным отклонением погрешности измерения (изм) и допуском Т контролируемого размера а также от точности изготовления характеризуемой параметрами вероятностного распределения действительных размеров относительно поля допуска. Наибольшие значения параметров m n и с при самых неблагоприятных характеристиках распределения погрешностей изготовления.
По табл. 8.3 найдем: m = 5%; n = 8%; с = 025·30 = 75 мкм.
Вероятностные значения верхнего ESв и нижнего EIв предельных отклонений размеров неправильно принятых деталей (375% из общего числа измеренных) составят:
ESв = 0030+00075 = 00375 мм;
EIв = 0 - 00075 = -00075 мм
а наибольший Dmaxв и наименьший Dminв – предельные размеры этих деталей:
Dminв=60000 0 -00075 =599925 мм.
Измерению подлежит размер вала ø60t6
Допуск вала равен Т=19 мкм. По табл. 8.1 найдем допускаемую погрешность измерения изм = 5 мкм и рассчитаем значение А мет()
По табл. 8.3 найдем:
с = 017·39 = 66 мкм.
ESв = 0085+00066 =0.0916мм;
EIв =0066+00066 =0.0726мм
а наибольший dmaxв и наименьший dminв – предельные размеры этих деталей:
dminв=60000 0 -0.0726=59.9404мм.
Подберем средства измерения для контроля размеров вала и отверстия из условия с.и.≤ изм. Все результаты сведем в таблицу 7.1.
Таблица 7.1 - Средства измерения для контроля размеров вала и отверстия
Допускаемая погрешность измерения [Δ] мкм
Предельные погрешности инструмента (выбираем по таблицам справочника)
Допускаемая погрешность
Нутромер с микрометрической
Оптиметр вертикальный
2. Проектирование калибров для контроля гладких цилиндрических деталей
Расчет исполнительных размеров рабочих калибров и контркалибров к ним для контроля деталей сопряжения 56
По ГОСТ 25347-82 определить предельные отклонения отверстия и вала и вычислить их предельные размеры:
) для отверстия 56Н6;
Dmax =D + ES =56+0019= 56019мм
Dmin = D + EI =56+0=56 мм
dmax = d + es=56+0.009 = 56009 мм
dmin = d + ei =56-0.009=55991мм
По ГОСТ 24853-81 (прил.6) [1] определить данные для расчета исполнительных размеров калибров:
) для отверстия 56Н6
Н =3 мкм; Z=2.5мкм; Y= 2 мкм;α= 0;
Н1 = 5 мкм; Z1 =4мкм; Y1= 3мкм ; α1=0; Hp =2мкм
Пользуясь формулами вычислить исполнительные размеры калибров и контркалибров:
) калибры (пробки) для отверстия 56Н6;
ПРmax = Dmin + Z+ H2 =560+00025+00032=56004мм
ПРmin = Dmin + Z – H2 =560+00025-00032=56001 мм
ПРизн = Dmin – Y =55998 мм
Исполнительный размер калибра ПР 56004-0003 мм
НЕmax = Dmax +H2 =56019+0.0032=5602мм
НЕ min=Dmax – H2 =56019-0.0032=56017 мм
Исполнительный размер калибра НЕ 5602-0003 мм
)калибры (скобы) для вала 56
ПРmin = dmax – Z1 – H12 =56009-0.004-0.0025=56003мм
ПРmax = dmax –Z1 +H12 =56009-0004+00025=56008мм
ПРизн = dmax + Y =56006мм
Исполнительный размер калибра ПР56003+0005 мм
НЕmin = dmin – H12 =55991-0.0025=55989мм
НЕmax= dmin+ H12 =55991+0.0025=55993мм
Исполнительный размер калибра: НЕ55989 +0005 мм
) контркалибры к скобам для вала 56 js6:
К – ПРmax = dmax- Z1+ Hp2=56009-0.004+0.001 = 56006 мм
К – ПPmin = dmax – Z1 – Hp2 =56009-0.004-0.001 =56004 мм
Исполнительный размер калибра К – ПР 56006-0002мм
К – НEmax = d min + Hp2 =54991+0.001 =55992мм
К – НEmin = dmin - Hp2 =55991-0.001=5599мм
Исполнительный размер калибра: К- НЕ 55992-0002мм
К – Иmax = dmax +Y1+ Hp2 =56009+0003+0001 = 56013мм
К - И min = dmax +Y1 – Hp2 =56009+0003-0001=56011м
Исполнительный размер калибра: К – И 56011 -0002мм
Рисунок 7.1 – Схемы полей допусков калибров и контркалибров
Список использованных источников
Анухин В. И. Допуски и посадки: учеб. пособие для вузов В. И. Анухин. - 3-е изд. - СПб. : Питер 2005. - 206 с.
Метрология стандартизация и сертификация: Методические указания к практическим занятиям и к курсовой работе. Сост. В.С. Секацкий Н.В. Мерзликина — Красноярск: СФУ 2007. 46 с.
Димов Ю. В. Метрология стандартизация и сертификация: учебник для вузов Ю.В. Димов. - 2-е изд. - М. : Питер 2004. - 432 с. : ил.
Допуски и посадки: Справочник. В 2 ч. Ч. 1 В.Д. Мягков М.А. Палей А.Б. Романов В.А. Брагинский. – Л.: Машиностроение 1982. – 534с.
Допуски и посадки: Справочник. В 2 ч. Ч.2 В.Д. Мягков М.А. Палей. А.Б. Романов В.А. Брагинский. – Л.: Машиностроение 1983. – 448с.
Никифоров А. Д. Взаимозаменяемость стандартизация и технические измерения: учеб. пособие А. Д. Никифоров. - 2-е изд. стереотип. - М.: Высш. шк. 2002. - 510 с.
Романов А. Б. Таблицы и альбом по допускам и посадкам: справ. пособие А. Б. Романов В. Н. Федоров А. И. Кузнецов. - СПб. : Политехника 2005. - 88 с.
Якушев А.И. Воронцов Л.Н. Федотов Н.М. Взаимозаменяемость стандартизация и технические измерения: Учебник для вузов. — 6-е изд. перераб. и дополн. — М.: Машиностроение 1986. — 352 с.
ГОСТ 6636-69 Основные нормы взаимозаменяемости. Нормальные линейные размеры.
ГОСТ 8.051. Государственная система обеспечения единства измерений. Погрешности допускаемые при измерении линейных размеров до 500 мм.
ГОСТ 25347-82 Единая система допусков и посадок. Поля допусков и рекомендуемые посадки.
ГОСТ 24853-81 Калибры гладкие для размеров до 500 мм. Допуски.
ryisrrryer1.dwg

КР 131000.62-0000001
Неуказанные предельные отклонения размеров отверстий
rressrsrrerye.docx
образовательное учреждение
высшего профессионального образования
«СИБИРСКИЙ ФЕДЕРАЛЬНЫЙ УНИВЕРСИТЕТ»
Кафедра «Машины и оборудования нефтегазовой отрасли»
подпись дата инициалы фамилия
номер группы номер зачетной книжки подпись дата инициалы фамилия
sr1.dwg

rrr-3sres1.dwg

КР 131000.62-0000001