Разработка технологии капитального ремонта двигателя ЯМЗ 238 автомобиля КРАЗ 257




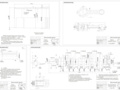
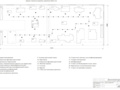
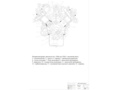
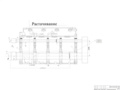
- Добавлен: 25.10.2022
- Размер: 1 MB
- Закачек: 2
Описание
Состав проекта
![]() |
![]() ![]() ![]() |
![]() ![]() ![]() |
![]() ![]() ![]() |
![]() ![]() ![]() |
![]() ![]() ![]() |
![]() ![]() ![]() |
![]() |
![]() |
![]() ![]() ![]() ![]() |
![]() |
![]() |
![]() ![]() ![]() ![]() |
![]() ![]() ![]() ![]() |
![]() |
![]() |
![]() ![]() ![]() ![]() |
![]() ![]() ![]() ![]() |
![]() |
![]() ![]() ![]() ![]() |
Дополнительная информация
план участка.dwg

Технологические наладки.dwg

двигатель.dwg

Технико-экономические проект.dwg

007.dwg

приспособление.dwg

Рекомендуемые чертежи
- 24.01.2023
- 25.10.2022