Разработка технологического процесса обработки вала



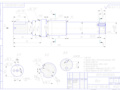
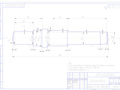
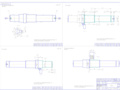
- Добавлен: 25.10.2022
- Размер: 1 MB
- Закачек: 1
Описание
Состав проекта
![]() |
![]() |
![]() |
![]() ![]() ![]() ![]() |
![]() ![]() ![]() ![]() |
![]() ![]() ![]() ![]() |
![]() ![]() ![]() ![]() |
![]() ![]() ![]() |
![]() ![]() ![]() |
![]() ![]() ![]() |
![]() ![]() ![]() ![]() |
![]() ![]() ![]() ![]() |
![]() |
![]() ![]() ![]() |
![]() ![]() ![]() |
![]() ![]() ![]() |
![]() ![]() ![]() |
![]() ![]() ![]() |
![]() ![]() ![]() |
![]() ![]() ![]() |
![]() ![]() ![]() |
![]() ![]() ![]() |
Дополнительная информация
Вал_v13.cdw

Общие допуски по ГОСТ 30893.1-m
Оперрации_v13.cdw

одновременно выдерживая размеры 1 6.
*Размеры обеспечиваются инструментом.
выдерживая размеры 1 5 и
технические условия 6.
технические условия 6
0 Круглошлифовальная
Шлифовать поверхность
выдерживая размеры 1
и технические требования 3.
Наименование и модель станка
Фрезерно-центров. 6Т12
Токарноый с ЧПУ 16К20Ф3
Круглошлифовальный 3М151
Заготовка_v13.cdw

Неуказанные радиусы 1 3
Сталь 45 ГОСТ 1050-88
Оперрации.cdw

одновременно выдерживая размеры 1 6.
*Размеры обеспечиваются инструментом.
выдерживая размеры 1 5 и
технические условия 6.
технические условия 6
0 Круглошлифовальная
Шлифовать поверхность
выдерживая размеры 1
и технические требования 3.
Наименование и модель станка
Фрезерно-центров. 6Т12
Токарноый с ЧПУ 16К20Ф3
Круглошлифовальный 3М151
Заготовка.dwg
Неуказанные радиусы 1 3
Сталь 45 ГОСТ 1050-88
Вал.dwg
Общие допуски по ГОСТ 30893.1-m
Оперрации.dwg
одновременно выдерживая размеры 1 6.
*Размеры обеспечиваются инструментом.
выдерживая размеры 1 5 и
технические условия 6.
технические условия 6
0 Круглошлифовальная
Шлифовать поверхность
выдерживая размеры 1
и технические требования 3.
Наименование и модель станка
Фрезерно-центров. 6Т12
Токарноый с ЧПУ 16К20Ф3
Круглошлифовальный 3М151
Вал.cdw

Общие допуски по ГОСТ 30893.1-m
Заготовка.cdw

Неуказанные радиусы 1 3
Сталь 45 ГОСТ 1050-88
Технический контроль.docx
Кафедра Горные машины
Наименование операции
Наименование марка материала
Наименование оборудования
Контролируемые параметры
Наименование средств в ТО
Отсутствие забоин заусенцев и других дефектов осмотр
Шероховатость обработанных поверхностей
61312109 образцы шероховатости ГОСТ 9378
910121315 8133-0910 скоба
356781114171819 штангенциркуль ШЦ-I-125-01 ГОСТ 166
Технический контроль
ГОСТ 3.1105-84 Форма 7а
Операционная карта.docx
Кафедра «Горные машины»
Наименование операции
Фрезерно-центровальная
Оборудование устройства ЧПУ
Обозначение программы
Приспособление при станке П-1
Установить деталь закрепить. 30 15 1 006 486 128
Фрезеровать торцы выдержав размеры 1.
Тиски само-центрирующие специальные. Оправка для фрезы 6222-0097 ГОСТ 265441-85. Фреза 2214-0386Т15К6 ГОСТ 26595-85.
Центровать торцы выдержав размеры 2 и 3.63 75 315 1 006 486 128
Втулка переходная специальная. Втулка разжимная специальная. Сверло 2317-0013Р6М6 ГОСТ 14952-75.
ОПЕРАЦИОННАЯ КАРТА МЕХАНИЧЕСКОЙ ОБРАБОТКИ
Установить деталь закрепить.
Шлифовать поверхности выдерживая размеры 1 3. 43 0002 1 0002 311
Хомутик 7107-0061 ГОСТ 1648-70 Центр упорный ГОСТ 18259-72 Круг шлифовальный ПЛ 600x90x305 24А25СТ25К5
Содержание ТМ.docx
Технологический контроль чертежа и анализ технологичности детали .. .7
Определение типа производства и организации формы работы .. .. 10
Выбор метода получения заготовки и разработка её чертежа 14
Разработка варианта технологического маршрута 16
Выбор металлорежущих станков . .18
Разработка операций технологического процесса ..19
Расчет и назначение припусков на механическую обработку 21
Расчет и назначение режимов резания . 28
Определение норм времени для операций .. ..31
Технико-экономические показатели работы ..33
Заключение . .. .. .39
Список использованной литературы . ..40
Маршрутная карта.docx
Сталь 45 ГОСТ 1050-88
Код наименование операции
Обозначение документа
Код наименование оборудования
5 4269 Фрезерно-центровальная ИОТ № 148
МP-71М 19479 3 101Р 1 1 1 - 1 06 223
0 4110 Токарная ИОТ № 145
К20 19149 3 101Р 1 1 1 - 1 06 182
Установить деталь закрепить.
Точить поверхности выдерживая размеры .
Хомутик поводковый 7107-0031 ГОСТ 2578-70. Центр А1-5-Н ГОСТ 8742-75. Центр плавающий специальный. Резец 2102-0171Т15К6 ГОСТ 21151-75.
5 4110 Токарная ИОТ № 145
К20 19149 3 101Р 1 1 1 - 1 06 105
М А Р Ш Р У Т Н А Я К А Р Т А
ГОСТ 3.1118-82 Форма 2
0 4110 Шлицефрезерная ИОТ № 148
50 19479 4 101Р 1 1 1 - 1 06 48
Фрезеровать шлицы 6 х 48 х 50 выдержав размер
Оправка для фрезы специальная. Фреза червячная Р6М5 специальная. Хомутик 7107-0031 ГОСТ 2578-70. Центр упорный ГОСТ 18259-72.
5 4110 Фрезерная (паз) 19479 ИОТ № 153
Р82Ш 4 101Р 1 1 1 - 1 06 301
Обработать паз концевой фрезой d8.
Конус шпинделя по ГОСТ 30064-93.Фреза с цилиндрическим хвостовиком ГОСТ 17025–71.
ГОСТ 3.1118-82 Форма 3
0 4105 Кругошлифовальная ИОТ № 113
М161 19630 3 101Р 1 1 1 - 1 06 214
Шлифовать поверхность выдержав размер .
Хомутик 7107-0061 ГОСТ 1648-70 Центр упорный ГОСТ 18259-72 Круг шлифовальный ПЛ 600x90x305 24А25СТ25К5
Хомутик 7107-0061 ГОСТ 1648-70 Центр упорный ГОСТ 18259-72 Круг шлифовальный ПЛ 600x90x305 24А25СТ25К5
ГОСТ 3.1118-82 Форма 4
5 4165 Сверлильная ИОТ № 192
CCГ35 18335 3 101Р 1 1 1 - 1 06 183
Сверлить 2 отверстия выдерживая размеры
Патрон быстросменный 6251-0182 ГОСТ 14077-83 Сверло 64 2300-1011Р6М5 ГОСТ 886-77 Штангенциркуль ШЦ-II-250-005 ГОСТ 166-80.
Нарезать 2 резьбы выдерживая размер М8.
0 4165 Сверлильная ИОТ № 192
CCГ35 18335 3 101Р 1 1 1 - 1 06 178
KD.docx
МИНИСТЕРСТВО ОБРАЗОВАНИЯ РЕСПУБЛИКИ БЕЛАРУСЬ
БЕЛОРУССКИЙ НАЦИОНАЛЬНЫЙ ТЕХНИЧЕСКИЙ УНИВЕРСИТЕТ
Руководитель: Сокоров И.О.
Консультант: Сокоров И.О.
НА ТЕХНОЛОГИЧЕСКИЙ ПРОЦЕСС МЕХПНИЧЕСКОЙ ОБРАБОТКИ
Заключение.docx
- произведен анализ технологичности конструкции детали – вал при заданной годовой программе выпуска 7000 штук;
- определен тип производства – мелкосерийное;
- выбран метод получения заготовки – штамповка в закрытых штампах;
- рассчитаны припуски и режимы резания для обработки поверхности.
- разработан маршрут и технологический процесс изготовления рассматриваемой детали;
- оформлена технологическая документация.
Список используемой литературы
Горбацевич А.Ф. Шкред В.А. Курсовое проектирование по технологии машиностроения -Мн.: Выш. шк. 1983 - 256с.
Режимы резания металлов. Справочник. Под ред. Ю.В. Барановского. - М. Машиностроение 1972. - 406с.
Проектирование технологических процессов механической обработки в машиностроении. Под.ред. В.В. Бабука. - Мн.: Выш. шк. 1987 - 255с.
Анурьев В. И. Справочник конструктора- машиностроителя. – М. Машиностроение 2001.
Записка.docx
Деталь – вал предназначена для передачи крутящего момента от электродвигателя к раздаточному валу при помощи зубчатого зацепления. Заготовка получена на ГКМ повышенной точности штамповкой поэтому конфигурация наружного контура не вызывает значительных трудностей. На валу имеются посадочные поверхности под подшипники диаметром 40 мм и 50 мм.вала 4 кг длина 290 мм. Вал имеет резьбовые отверстия и поджимается болтами М 8. Сопряжение разных диаметров детали имеет высокую геометрию для снятия напряжения и выхода шлифовального круга предусмотрены плавные переходы от поверхностей разных диаметров. Наличие фасок на поверхности вала облегчает её сборку.
Наиболее точными поверхностями являются посадка под подшипник диаметром 50мм класс точности к7 и шероховатость Rа=063.
Материал заготовки – сталь 45
Данные свойства стали сведены в таблице 1.1 и 1.2
Таблица 1.1 - Химический состав стали 45 по ГОСТ 1050-88
Таблица 1.2 - Механические свойства стали 45 по ГОСТ 1050-88
Технологический контроль чертежа и анализ технологичности детали
Целью технологического контроля чертежа и анализа технологичности является выявление недостатков в конструкции детали.
Отработка конструкции на технологичность – комплекс мероприятий по обеспечению необходимого уровня технологичности конструкции по установленным показателям. Она направлена на повышение производительности труда снижение затрат и сокращение времени на изготовление изделия при обеспечении необходимого его качества. Виды и показатели технологичности конструкции приведены в ГОСТ 14.203-89 а правили отработки конструкции изделия и перечень обязательных показателей технологичности – ГОСТ 14.201-83.
Метод получения заготовки имеет много преимуществ так как штамповка сводит к минимуму отходы материала в виде стружки по сравнению с прокатом.
На представленном чертеже детали дано полное представление о детали и ее конструкции. На чертеже указаны необходимые размеры а также требования к точности шероховатости и взаимному расположению поверхностей детали в соответствии с их конструктивным назначением.
Оценка технологичности конструкции может быть двух видов: качественной конструкции обобщенно на основании опыта исполнителя и допускается на всех стадиях проектирования как предварительная. Количественная оценка технологичности изделия выражается числовыми показателями и оправдана в том случае если они существенно влияют на технологичность рассматриваемой конструкции.
В качестве количественных показателей технологичности рассматриваем: массу детали коэффициент точности обработки коэффициент шероховатости поверхностей уровень технологичности конструкции по технологической себестоимости.
Ведем анализ по качественным и количественным показателям оценки технологичности в соответствии с ГОСТ 1402-73.
К основным показателям относятся:
)Трудоемкость изготовления детали;
)Технологическая себестоимость.
К дополнительным показателям относятся:
Коэффициент унификации конструктивных элементов:
где Qу.э – число унифицированных конструктивных элементов детали;
Qэ – общее число элементов детали.
Деталь содержит 11 конструктивных элементов: канавки цилиндрические поверхности резьбы фаски шлицы. Из них унифицированные – 11.
Коэффициент применяемости стандартизованных обрабатываемых поверхностей
где Dо.с = 14 – число поверхностей детали обрабатываемых стандартным инструментом;
Dн.о = 15 – число поверхностей детали подвергаемых механической обработке.
Коэффициент обрабатываемости поверхностей
Коэффициент использования материала
где q = 4 кг – масса детали;
Q = 55 кг масса заготовки.
Минимальное значение параметра Ra = 125 мкм.
Максимальный квалитет точности 7.
Учитывая размеры и форму поверхностей делаем вывод что заготовку лучше всего получать штамповкой. Главной особенностью рассматриваемой детали является обработка. Анализируя технологичность конструкции по применяемую материалу следует отметить что сталь 45 имеет среднюю обрабатываемость не высокую стоимость и достаточную легкость при изготовлении и приобретении. При анализе конструкции детали можно обратить внимание на простоту формы – тело вращения небольшое количество обрабатываемых поверхностей имеющих простую форму. Это позволяет применить высокопроизводительное оборудование и унифицированные наладки. С точки зрения технологических размеров и допусков сталь не требует жестких ограничений что является положительным фактором Самой точной является поверхность под подшипники качения требующая шлифования. В качестве заготовки целесообразно принять штамповку длинной 2973 мм ГОСТ 15830-84 . В целом следует считать рассматриваемую деталь технологичной.
Определение типа производства
Составим план механической обработки рассматриваемой детали.
Операция 005 – фрезерно-центровальная:
- фрезеровать и центровать торцы.
Операция 010 – токарная с ЧПУ:
-токарная обработка детали.
Операция 015 – токарная с ЧПУ:
Операция 020 шлицефрезерная:
-нарезаем шлиц D6 .
Операция 025 концевое фрезерование:
Операция 030 – круглошлифовальная:
Операция 035 – сверлильная:
- сверлить отверстие зенковать фаски нарезать две резьбы М8
Операция 040 – сверлильная:
Рассчитаем основное время для каждой обрабатываемой поверхности и назначим штучно-калькуляционное время для всех операций механической обработки детали по рекомендациям [1 стр. 146 147].
Операция 005 – фрезерно-центровальная:
Операция 020 – шлицефрезерная:
Операция 025 - концевое фрезерование
Операция 030 – круглошлифовальная
Сверлить по 2 отверстия одного торца вала
Сверлить по 2 отверстия другого торца вала
Т02=(00004dl)2=(00004818)2=0115 мин
Определим коэффициент серийности
Pi – явочное число рабочих участка
Тшт.к.ср. – среднее штучно-калькуляционное время.
где Nм – месячная программа выпуска
Тшт.к.ср. – среднее штучно-калькуляционное время
н – планируемый нормативный коэффициент загрузки станка (08)
Общее число операций выполняемых на участке в течение месяца:
4+85+42+28+201+89+602+786=2467
Число рабочих обслуживающих каждый станок в отдельности:
Явочное число рабочих на участке (в одну смену):
Pi = 077*n = 0.77*8=616
где n – число операций
Согласно ГОСТ 3.1119-83 при Кзо=381 принимаем производство мелкосерийное. [5 стр.9]
Определение размера партии.
Кзо=39; Nм=580; no=9 шт; nсб=20;
Предельно допустимые параметры портии:
Принимаем nmin=180 (кратно nсб=20) .
Расчетная периодичность повторения партий деталей:
Принимаем ближайшее большее In=11 дней.
Размер партии согласно условию:
Проверяем выполнение условия: 180290449.
Таким образом два раза в месяц требуется запускать партию деталей.
Выбор метода получения заготовки и разработка чертежа заготовки
Для получения заготовки будем использовать штамповку в закрытых штампах. Этот метод является наиболее оптимальным не требует больших затрат времени обладает невысокой трудоемкостью.
Данный вид штамповки позволяет получить заготовки массой до 50 кг. Припуски и допуски по ГОСТ 7505-74. Припуски на сторону поковок изготавливаемых на молотах массой до 40 кг с размерами до 800 мм – от 06 -12 до 30 - 64 мм. Поле допусков соответственно от 07 - 34 до 16 - 11 мм. Для штампованных заготовок изготавливаемых на кривошипных прессах припуски на 01-06 мм меньше. При холодной калибровке допуски от ±(01..025) мм – калибровка обычной точности до (005..015) мм – калибровка повышенной точности.
Вес заготовки 55 кг.
- относительно высокая точность поковок.
- более высокая производительность — на 30-50% выше чем на молотах.
- более высокая надежность в эксплуатации.
Основными недостатками этого метода являются следующие особенности:
- пониженная стойкость штампов;
- ограниченное колебание объема заготовок;
- образование технологических остатков;
- нет условий для выполнения операции подкатки и протяжки заготовки;
- более сложная конструкция штампов;
- необходимость очистки заготовок от окалины;
- высокая стоимость;
- малая универсальность.
Исходные данные по детали.
1. Материал – Сталь 45 (по ГОСТ 1050-88):
Исходные данные для расчета:
1.поковки – 7.15 кг (расчетная): расчетный коэффициент К р =
(см. приложение 3 [4]); 69 * 13 = 88 кг.
2. Класс точности – Т4 (см. приложение 1[4]).
3. Группа стали – М2 (см. табл.1 [4]).
4. Степень сложности – C1 (см. приложение 2 [4]).
Размеры описывающей поковку фигуры (цилиндр) мм:
диаметр 59 (59 * 105);
длина 290 +(38 +38)=2976.
5. Конфигурация поверхности разъема штампа П (плоская) – (см. табл.[4]).
6. Исходной индекс – 12 (см. табл. 2 [4]).
Размеры штамповки и их допустимые отклонения
1. Размеры штамповки мм
диаметр 59 при Н=62мм - 59+ мм;
диаметр 40 при Н=54мм - 60+ мм;
диаметр 50 при Н=43мм - 50+ мм;
диаметр 41 при Н=38мм - 41+ мм;
2. Радиус закругления наружных углов – 20 50 мм принимается 20 мм
3. Неуказанные предельные отклонения размеров применяется равным 1.5
допуска соответствующего размера поковки с равными допускаемыми
отклонениями – по п. 5.5 [4].
4. Допускаемое отклонение от плоскостности 1 мм (см. табл. 13[4]).
Разработка варианта технологического маршрута
Разрабатываемый технологический процесс должен быть прогрессивным обеспечивать повышение производительности труда и качества деталей сокращение трудовых и материальных затрат на его реализацию уменьшение вредных воздействий на окружающую среду.
Базовой исходной информацией для проектирования технологического процесса служат: рабочие чертежи деталей технические требования регламентирующие точность параметр шероховатости поверхности и другие требования качества; объем годового выпуска изделий определяющий возможность организации поточного производства.
Операция 000 – Заготовительная. Заготовку получаем на горячештамповочном прессе в закрытом штампе.
Операция 005 – Фрезерно-центровальная. На данной операции за два перехода обрабатывается торец и сверлится центровое отверстие при этом деталь закрепляется в трехкулачковом патроне.
Для первого перехода используется токарный проходной отогнутый правый резец. Марка материала режущей кромки – твердый сплав Т15К6 т.к. данная марка материала наиболее подходит для подрезания торцов.
Для второго перехода (сверление отверстия) используется комбинированные центровочное сверло. Марка режущей кромки – твердый сплав Т5К10. Комбинированные сверла являются весьма производительным инструментом т.к. они одновременно сверлят отверстие с обработкой фаски. Центровые отверстия позволяют обеспечить принцип постоянства баз для следующих операций.
Операция 010 - Токарная с ЧПУ на станке 16К20 ФЗ. На данной операции деталь зажимается в трехкулачковом и обрабатываются диаметры мм503 мм403 мм.
Операция 015 – Токарная с ЧПУ на станке 16К20 ФЗ. На данной операции деталь зажимается в трехкулачковом и обрабатываются диаметры 503 мм413 мм403 мм.
Операция 020 – Шлицефрезерная. Деталь зажимается в центрах на поверхности диаметром 503 мм фрезеруют шлицы.
Для данной обработки используется червячная шлицевая фреза без усиков диаметром 100 мм. Марка режущей кромки Р6М5.
Операция 025 – Концевое фрезерование. Обработка ведется фрезой d8 с вертикальной осью вращения.
Операция 030 – Шлифовальная. Установка детали осуществляется на рифленые центра. В качестве инструмента используется абразивный круг.
Операция 035 – Сверлильная. На данной операции сверлятся 2 отверстия глубиной 25 мм и нарезают резьбу М8 в одном торце вала.
Операция 040 – Сверлильная. На данной операции сверлятся 2 отверстия глубиной 20 мм и нарезают резьбу М8 в одном торце вала.
Выбор металлорежущих станков
Подробное описание маршрутного техпроцесса с содержанием операций и перечнем оборудования приспособлений и инструмента приведено в технологических картах на механическую обработку детали в приложении.
Принцип выбора оборудования основывается на концентрации и дифференциации операций.
По возможности необходимо стремиться к обработке с одной установки максимально возможного количества поверхностей.
Установив при проектировании технологического процесса план и метод обработки детали указываем на каком станке будет выполняться данная операция:
Операция 005 – Фрезерно-центровальная
Данная операция выполняется на фрезерно-центровальныйполуавтомате
Операция 010 - Токарная с ЧПУ (одна сторона)
Данная операция выполняется на станке с 16К20 ФЗ.
Операция 015 - Токарная с ЧПУ (вторая сторона)
Операция 020 – Шлицефрезерная
Данная операция выполняется на шлицефрезерном станке модели 5350А.
Операция 025 - Концевое фрезерование.
Данная операция выполняется на универсальном фрезерном станке модели 6Р82Ш.
Операция 030 - Круглошлифовальная
Данная операция выполняется на круглошлифовальном станке 3М151.
Операция 035 – Сверлильная
Данная операция выполняется на горизонтально-сверлильном станке ССГ35.
Операция 040 – Сверлильная
Данная операция выполняется горизонтально-сверлильном станке ССГ35.
Разработка операций технологического процесса
В соответствии с разработанным планом механической обработки детали для каждой операций составляем технологически процесс:
Установить и закрепить заготовку.
Подрезать 2 торца выдерживая размер 290 мм.
Центровать 2 отверстия 6.
Операция 010 – Токарная с ЧПУ
Обрабатывать по программе выдерживая размер 59х8 мм.
Обрабатывать по программе выдерживая размер 50х30 мм.
Обрабатывать по программе выдерживая размер 40х60 мм
Точить фаски по программе выдерживая размер 1*45о мм.
Переустановить деталь.
Операция 015 – Токарная с ЧПУ (2 сторона)
Обрабатывать по программе выдерживая размер 50х67 мм.
Обрабатывать по программе выдерживая размер 41х105 мм.
Обрабатывать по программе выдерживая размер 40х20 мм
Точить фаску по программе выдерживая размер 2*45о мм.
Точить фаску по программе выдерживая размер 05*45о мм
Операция 020 – Шлицефрезерная.
Установить и закрепить деталь.
Фрезеровать поверхности 6 х 48 х 50 мм.
Операция 025 – Концевая фреза
Фрезеровать канавку глубиной 45 мм длинной 40 мм с диаметром фрезы d8.
Операция 030 – Шлифовальная
Шлифовать поверхность 59 х 8.
Шлифовать поверхность 50 х 30.
Шлифовать поверхность 40 х 60
Шлифовать поверхность 50 х 67
Шлифовать поверхность 41 х 105
Шлифовать поверхность 40 х 20
Операция 035 – Сверлильная.
Сверлить два отверстия 65х 25.
Операция 040 – Сверлильная.
Сверлить два отверстия 65 х 20.
Операция 020 – Контрольная.
Измерить линейные размеры.
Измерить шероховатость.
Дать заключение о годности детали.
Расчет и назначение припуска на механическую обработку
Рассчитаем припуски на обработку и промежуточные предельные размеры для поверхности мм. Технологический маршрут обработки поверхности состоит из операций точения предварительного и чистового а также шлифования однократного. Заготовкой является пруток круглого сечения.
Расчет ведем посредством заполнения таблицы 1.
Расчет припусков и предельных размеров по техническим переходам
на обработку поверхности вала мм.
Технологические переходы обработки поверхности
Элементы припуска мкм
Расчетный размер dр мм
Предельный размер мм
Предельное значе-ние припуска мм
Расчетная формула для определения припуска i-го перехода
где Rz – высота неровностей профиля;
h – глубина дефектного слоя;
ρ – суммарное значение пространственных отклонений;
– погрешность установки.
Значения Rz и T выбираем по таблицам 4.3 и 4.6 [1 стр. 63 65].
Суммарное пространственное отклонение для заготовки данного типа определяем по формуле [1 табл. 4.7].
Допуск на поверхности используемые в качестве базовых на фрезерно-центровальной операции определяем по ГОСТ 7505-74 для заготовок полученных штамповкой в закрытых штампах
Остаточные пространственные отклонения
где – исходное отклонение заготовки;
– коэффициент уточнения формы [1 стр. 73].
Минимальное значение межоперационного припуска:
для предварительного точения
для чистового точения
Расчетный размер определяется начиная с конечного (чертежного) размера последовательным добавлеием расчетного минимального припуска каждого технологического перехода
Значения допусков каждого перехода принимаются по таблицам в соответствии с квалитетом того или иного вида обработки.
Наименьшие значение предельного размера dmin получается по расчетным размерам округленным до точности допуска соответствующего перехода. Наибольшие предельные размеры dmax определяются из наименьших предельных размеров прибавлением к ним допусков соответствующих переходов.
Минимальные предельные значения припусков 2·Zmin равны разности наименьших предельных размеров выполняемого и предшествующего переходов а максимальные значения 2·Zmax – соответственно разности наибольших предельных размеров.
Произведем проверку правильности произведенных расчетов
Условия выполняются. Расчеты выполнены правильно.
В завершении расчета строим схему расположения припусков на обработку поверхности мм.
Рисунок 1 - Схема расположения припусков и допусков
на обработку поверхности мм.
Рассчитаем припуски на обработку и промежуточные предельные размеры для поверхности мм. Технологический маршрут обработки поверхности состоит из операций точения предварительного и чистового а также шлифования однократного. Заготовкой является поковка.
Расчет ведем посредством заполнения таблицы 3.
Допуск на поверхности используемые в качестве базовых
Остаточные пространственные отклонения
После точения чистового
После шлифования предварительного
Расчетный размер определяется начиная с конечного (чертежного) размера последовательным добавлением расчетного минимального припуска каждого технологического перехода: мм;
Рисунок 2 - Схема расположения припусков и допусков
на обработку поверхности мм
Расчет и назначение режимов резания
Назначим режимы резания для предварительного точения поверхности мм. Обработка ведется на токарно-винторезном станке 16К20 резцом с материалом режущей части Т15К6. Глубина резания t = 20 мм.
Расчет длины рабочего хода
где – длина резания =192мм;
у – длина подвода врезания и перебега инструмента у = 4 мм [2 стр. 300];
– дополнительная длина хода = 0.
Назначение подачи на оборот шпинделя станка S = 04 ммоб. [2 стр. 24] по паспорту станка принимаем S0 = 04ммоб.
Определение стойкости инструмента
Расчет скорости резания и числа оборотов шпинделя
где – скорость резания по таблице =42 ммин. [2 стр. 29];
– коэффициент зависящий от обрабатываемого материала = 10 [2 стр. 32];
– коэффициент зависящий от стойкости инструмента =155 [2 стр. 33];
– коэффициент зависящий от обработки = 10 [2 стр. 34].
По паспорту станка принимаем nпр = 400 мин-1 тогда скорость резания
Расчет основного машинного времени обработки
Назначим режимы резания чистового точения поверхности мм. Обработка ведется на токарно-винторезном станке резцом с материалом режущей части ВК8. Глубина резания t = 04мм.
где – длина резания =192 мм;
Назначение подачи на оборот шпинделя станка S = 025 ммоб. [2 стр. 24] по паспорту станка принимаем S0 = 025ммоб.
– коэффициент зависящий от стойкости инструмента =115 [2 стр. 33];
– коэффициент зависящий от обработки = 1 [2 стр. 34].
По паспорту станка принимаем nпр = 3000 мин-1 тогда скорость резания
Назначим режимы шлифования поверхности мм. Обработка ведется на круглошлифовальном станке шлифовальным кругом марки ПП. Глубина шлифования t = 015мм.
Обработку ведем на круглошлифовальном станке 3М151.
Выбираем характеристики шлифовального круга- Э9А 25 – 40С2 – СТ1 5 К [2стр172].
Определяем размеры шлифовального круга –D=100 мм; B=80 мм; [2стр173].
Рассчитываем скорость шлифовального круга в мс
Скорость вращения детали V=25 ммин [2стр193].
Число оборотов детали
По паспорту станка принимаем n=150 обмин тогда скорость вращения
Определяем поперечную подачу круга
.Время выхаживания мин [2стр175].
Слой металла снимаемый при выхаживании мм [2стр176].
Машинное время при автоматическом цикле шлифования
Назначим режимы резания фрезерования шлиц . Обработку ведем червячной шлицевой фрезой 80 мм из быстрорежущей стали Р6М5.
где – длина резания = 48 мм;
у – длина подвода врезания и перебега инструмента у = 18 мм;
Назначение подачи на оборот детали S = 22 ммоб. по паспорту станка принимаем S0 = 20 ммоб.
где – скорость резания по таблице =25 ммин. ;
– коэффициент зависящий от стойкости инструмента = 1 ;
По паспорту станка принимаем nпр = 150 мин-1 тогда скорость резания
Определение технологических норм времени
Технические нормы времени в условиях массового и серийного производств устанавливаются расчетно-аналитическим методом.
В серийном производстве норма штучно-калькуляционного времени определяется по формуле:
где Тшт – норма штучного времени:
где - основное (технологическое) время мин.
– вспомогательное время мин.
Вспомогательное время состоит из затрат времени на отдельные приемы:
где - время на установку и снятие детали мин;
– время на закрепление и открепление детали мин;
– время на приемы управления мин;
– время на измерение детали мин;
– время на обслуживание рабочего места мин. Складывается из времени на организационное и времени на техническое обслуживание рабочего места;
– время перерывов на отдых и личные надовности.
Рассчитаем норму норму штучно-калькуляционного времени для Токарной операции 010.
Нормативы времени принимаются по [1 прил. 5].
Определяем состав подготовительно-заключительного времени: наладка станка инструмента и приспособления – 6 мин; на дополнительные приемы – 7 мин;
Время на установку и снятие детали закрепление ее и открепление:
Время затраченное на приемы управления: включить и выключить станок кнопкой – 001 мин; подвести резец к детали в горизонтальном направлении – 004 мин; установить и снять инструмент – 018 мин. Тогда
Время затраченное на измерение детали равно 004 мин.
Время на обслуживание рабочего места и отдых составляет 6% оперативного времени:
Штучно-калькуляционное время:
Результаты расчетов технической нормы времени сведены в табл.
Технико-экономические показатели работы
Рассчитаем стоимость получения заготовок. Исходные данные для расчета сводим в таблицу 11.1.
Данные для расчетов стоимости заготовки.
Штамповка в закрытых штампах
Класс размерной точности
Масса заготовки Q кг
Стоимость одной тонны заготовок принятых за базу Ci руб.
Стоимость одной тонны стружки Cотх руб.
Стоимость заготовки:
Кт Кс Кв Км Кп – коэффициенты зависящие от класса точности группы сложности массы марки материала объема производства заготовок.
Кс =084 [3таб.4.17];
Кв = 087 [3таб.4.17];
Q – масса заготовки кг;
q – масса готовой детали кг;
Sотх – стоимость отходов руб.
Определим себестоимость механической обработки рассматриваемой детали.
Часовые приведенные затраты:
где – основная и дополнительная зарплата с начислениями;
– затраты часовые на эксплуатацию рабочего места;
– нормативный коэффициент экономической эффективности капитальных вложений = 015 [3 стр. 81];
– удельные часовые капитальные вложения в здание;
– удельные часовые капитальные вложения в станок.
Основная и дополнительная зарплата с начислениями и учетом многостаночного обслуживания:
где – коэффициент к часовой тарифной ставке = 266 [3 стр. 81];
– часовая тарифная ставка станочника-сдельщика соответствующего разряда;
– коэффициент учитывающий зарплату наладчика;
– коэффициент штучного времени учитывающий оплату труда рабочего при многостаночном обслуживании;
Часовые затраты на эксплуатацию рабочего места
где – практические часовые затраты на базовом рабочем месте = 3800 руб.ч [3 стр. 81];
– коэффициент показывающий во сколько раз затраты связанные с работой данного станка больше чем аналогичные расходы связанные с работой базового станка.
Удельные часовые капитальные вложения в станок
где – балансовая стоимость станка;
– эффективный годовой фонд времени работы станка;
– коэффициент загрузки станка.
Удельные часовые капитальные вложения в здание
где – стоимость 1 м2 производственной площади = 1300000 руб. [3 стр. 83];
А – производственная площадь занимаемая станком с учетом проходов
где – площадь станка;
– коэффициент учитывающий дополнительную производственную площадь проходов проездов и т. д.
Технологическая себестоимость операции механической обработки:
где – коэффициент перевыполнения = 13 [3 стр. 83]
– штучно-калькуляционное время обработки детали на данном станке.
Операция 005 - обработка на фрезерно-центровальном станке МР – 71М.
Операция 010 - обработка на токарно-винторезном станке 16К20.
Операция 015 - обработка на токарно-винторезном станке 16К20.
Операция 020 – обработка на шлице фрезерном автомате 5350А
Операция 025 - обработка на универсально-фрезерном станке X6328B.
Операция 030 – обработка на круглошлифовальном станке 3М151.
Операция 035 – обработка на горизонтально-сверлильном станке ССГ35.
Операция 040 – обработка на горизонтально-сверлильном станке ССГ35.
В ходе выполнения курсовой работы нами были решены следующие задачи:
- произведен анализ технологичности конструкции детали – вал при заданной годовой программе выпуска 2000 штук;
- определен тип производства – среднесерийное;
- выбран метод получения заготовки – штамповка в закрытых штампах;
- рассчитаны припуски и режимы резания для обработки поверхности.
- разработан маршрут и технологический процесс изготовления рассматриваемой детали;
- оформлена технологическая документация.
Список используемой литературы
Горбацевич А.Ф. Шкред В.А. Курсовое проектирование по технологии машиностроения -Мн.: Выш. шк. 1983 - 256с.
Режимы резания металлов. Справочник. Под ред. Ю.В. Барановского. - М. Машиностроение 1972. - 406с.
Проектирование технологических процессов механической обработки в машиностроении. Под. ред. В.В. Бабука. - Мн.: Выш. шк. 1987 - 255с.
Анурьев В. И. Справочник конструктора- машиностроителя. – М. Машиностроение 2001.
titulnik.docx
Белорусский национальный технический университет
Факультет горного дела и инженерной экологии
Кафедра “Горные машины”
по дисциплине “Технология машиностроения и ремонта горных машин”
Тема: Разработка технологического процесса обработки вала
Исполнитель: студент факультета ФГДЭ 4 курса группы 102830
Руководитель проекта:
ПОЯСНИТЕЛЬНАЯ ЗАПИСКА
Исполнитель: студент группы 102830
Руководитель: Сокоров И.О
Карта эскизов.docx
К А Р Т А Э С К И З О В
ГОСТ 3.1105-84 Форма 7
Рекомендуемые чертежи
- 24.01.2023
- 24.05.2017
- 24.01.2023
- 10.06.2015
- 01.07.2014