Разработка надштабельного ленточного конвейера




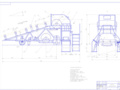
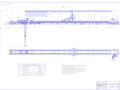
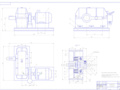
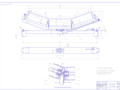
- Добавлен: 25.10.2022
- Размер: 12 MB
- Закачек: 1
Описание
Состав проекта
![]() |
![]() ![]() |
![]() |
![]() ![]() ![]() ![]() |
![]() ![]() |
![]() |
![]() ![]() ![]() |
![]() ![]() ![]() ![]() |
![]() ![]() |
![]() |
![]() ![]() ![]() ![]() |
![]() ![]() |
![]() ![]() |
![]() ![]() ![]() ![]() |
![]() ![]() ![]() ![]() |
Дополнительная информация
3-r-rrreryerrryirsr-rrrrrsrsrs.dwg

) Тип роликоопоры - желобчатая
) Угол наклона роликов - 30
) Диаметр ролика - 89 мм.
ТНД-511.03.00.00.00.
rrryiresryer-28.05-rsryerr.doc
1.Определение и классификация ..6
2.Основные характеристики машин 9
3.Характеристика транспортируемых материалов 9
4.Режимы работы конвейеров ..15
Анализ различных вариантов конструктивного исполнения
и проведения основных кинематических и прочностных расчетов 16
1.Цепные конвейеры 16
2.Ковшовые конвейеры ..19
3.Винтовые конвейеры 20
4.Роликовые конвейеры ..21
Описание конструкции и предварительная разработка общего вида
1.Описание ленточного конвейера ..23
2.Описание разрабатываемого ленточного конвейера ..30
Расчет (уточненный) ленточного горизонтального конвейера 31
1.Выбор скорости конвейера 31
2.Выбор ширины ленты 31
3.Масса груза приходящаяся на 1м. длинны ленты (кгм) 31
4.Расчетная схема трассы конвейера ..32
5.Расчет сопротивлений движению ленты на участках трассы
7.Расчет и выбор основного оборудования
ленточного конвейера 40
8.Очистные устройства 52
9.Средства автоматизации и безопасности
ленточных конвейеров .. .53
10 Устройства для промежуточной разгрузки конвейеров 55
Организация работ 56
1.Описание технологического процесса 56
2.Механизированное железнодорожное приемное устройство .. .58
3.Автомобильное приемное устройство 58
4.Технологическая схема .59
5.Предназначение и описание работ и операций производимых
надштабельным ленточным конвейером 60
Технологическая часть .62
1.Анализ технологических требований к конструкции детали 62
2.Оценка жёсткости технологической детали и выбор способов
установки на операциях по формированию контура .63
3.Выбор вида и размеров заготовки для детали .. ..64
4.Составление укрупнённого маршрута изготовления детали . 65
5.Разработка операций по формированию контура детали .. 66
Расчёт экономической эффективности ..77
Безопасности жизнедеятельности 88
1.Общие положения ..88
2.Естественное и искусственное освещение ..90
3.Выбор системы освещения 92
4.Условия выбора светильника 95
5.Размещение осветительных приборов .97
Список литературы 101
При проектировании погрузочно-разгрузочных участков складов выборе вариантов технологии и механизации погрузки и выгрузки транспортных средств ставятся следующие основные задачи: обеспечение погрузки и
выгрузки транспортных средств в нормативные сроки сохранность грузов и
транспортных средств при погрузочно-разгрузочных работах сокращение
трудозатрат исключение тяжелого ручного труда на погрузочно-разгрузочных работах; обеспечение эффективной технологии дальнейшей переработки грузов (после разгрузки) взаимосвязь с общей технологией и организацией
переработки грузов на складе; минимальная себестоимость
погрузочно-разгрузочных работ; возможность дальнейшего совершенствования технологии и технической оснащенности погрузочно-разгрузочных участков складов в том числе внедрение в последующем автоматизации
погрузочно-разгрузочных работ.
Механизация и автоматизация погрузочно-разгрузочных транспортных и складских работ позволяет высвободить значительное количество рабочей
силы занятой на вспомогательных работах и приносит существенный
технико-экономический эффект.
Поднимать и перемещать вручную тяжелые грузы а также в больших
количествах легкие грузы неэкономично. Такие работы протекали бы чрезвычайно медленно а иногда представляли бы опасность для занятых на них людей. Поэтому в основном грузы перемещают при помощи специальных машин и механизмов выбор которых зачастую зависит от особенностей физического состояния а также химического состава различных грузов.
Значение разного рода устройств для механизированного транспортирования и перемещение грузов особенно возросло с начала текущего столетия когда в промышленности начал внедряться метод поточного производства.
Здесь погрузочно-разгрузочные и транспортные операции являются
связующими звеньями между отдельными технологическими операциями обеспечивающими непрерывность процесса производства. Более того подъемно-транспортное оборудование перерастает рамки подсобного оборудования и приобретает функции регулятора производственного процесса в целом.
На современном заводе или предприятии подъемно-транспортное оборудование влияет на размещение технологического оборудования последовательность и соответствующую группировку процессов производства и определяет ритм работы предприятия на всех этапах производства – от складских и заготовительных до отгрузки продукции и отходов производства. В итоге мы видим что с каждым годом всё более и более растёт роль такого рода машин и механизмов на производстве. Как следствие этого возникла необходимость в разработке новых конструкторских решений (способных максимально снизить трудозатраты повысить производительность и условия труда а также автоматизировать
грузопереработку) с последующей их реализацией и внедрением на
Все отдельные грузоподъемные и транспортные средства на предприятии должны образовывать в общем производственном цикле стройную (единую) систему внутризаводского транспорта тщательно приспособленного к
производственному процессу и местным условиям.
На железнодорожном транспорте при переработке грузов которая является одним из основных производственных этапов определяющих качество и уровень работы железной дороги внедрение механизации наряду с повышением производительности труда – важное средство сокращения времени простоя подвижного состава улучшение сохранности грузов и вагонов. При этом
основной задачей является конечно быстрое и надежное точное и безопасное перемещение транспортируемых грузов с наименьшими денежными расходами и наименьшей затратой ручного труда.
силы занятой на вспомогательных работах и приносит существенный технико-экономический эффект.
Обзор существующих конструкций и выбор рациональной схемы машины.
1. Определение и классификация.
Транспортирующие машины применяют преимущественно в карьерах и на производственных предприятиях для перемещения сыпучих и
однродных штучных грузов непрерывным потоком на небольшие
расстояния в пределах одной или нескольких связанных между собой
производственных площадок.
По принципу действия транспортирующие машины (рис. 2.1) применяемые в строительстве классифицируют на конвейеры (ленточные пластинчатые ковшовые скребковые и др.) в которых перемещаемому
материалу движение сообщается механическим путем и
пневмотранспортные установки в которых перемещение материала
осуществляется в потоке движущего воздуха или с аэрацией материала
Ленточные конвейеры (рис. 2.1 а) предназначены для транспортирования сыпучих порошкообразных мелко- и среднекусковых
материалов а также однотипных штучных грузов в горизонтальном и слабо наклонном направлении. Рабочим органом на котором
размещается транспортируемый материал является резинотканевая лента состоящая из тканевых прокладок со связывающими их
резиновыми прокладками и обкладками. Применяют также ленты с
завулканизированными стальными канатами (тросами) малых диаметров так называемые резинотросовые ленты. Очень редко для транспортирования горячих материалов используют стальные ленты.
Пластинчатые конвейеры (рис. 2.1 б) применяют для транспортирования крупнокусковых абразивных и нагретых материалов а также крупных штучных грузов в горизонтальном и слабо наклонном направлениях.
Рабочим органом является тяговая цепь с плоскими или фасонными пластинами на которых размещается материал или отдельные штучные
грузы. Для транспортирования материалов в вертикальном и сильно
наклонном направлении применяют ковшовые конвейеры — элеваторы
Скребковые конвейеры перемещают малоабразивный материал волоком по желобу. Рабочим органом их является пластинчатая тяговая цепь; к ее звеньям прикрепляются скребки между которыми и размещается материал.
Винтовые конвейеры (рис. 2.1 г) транспортируют сыпучие и вязкие материалы в горизонтальном и слабо наклонном направлениях а иногда и в вертикальном направлении. Рабочим органом является винт
вращающийся в желобе с полукруглым днищем.
Роликовые конвейеры (рис. 2.1 д) используют для перемещения
однородных с развитой поверхностью штучных грузов. Рабочим
органом их являются неприводные или приводные вращающиеся
ролики на которых размещается транспортируемый груз.
Тяговым элементом ленточных пластинчатых и ковшовых конвейеров служит лента или цепь замкнутая в бесконечный контур. На концах
конвейера они огибают приводные и натяжные барабаны (при лентах) или звездочки (при цепях) а на трассе опираются на ролики (при лентах)
или колесами на направляющие (при цепях). Опорой является
несущая рама конвейера (рис. 2.2).
Винтовые или роликовые конвейеры не имеют тягового элемента
материал перемещается рабочим элементом машины.
В пневмотранспортных установках (рис. 2.1 е) материал преимущественно порошкообразный и пылевидный перемещается по трубопроводу
под действием воздушного потока. В месте загрузки материал смешивается с воздухом в определенной концентрации а в месте выгрузки отделяется от воздуха. Разновидностью пневмотранспортных установок являются пневмомеханические в которых аэрированный материал приобретает свойство текучести и перемещается механическим путем.
2. Основные характеристики машин
К основным характеристикам транспортирующей машины относятся ее производительность выраженная в объемных или массовых единицах (м3ч или тч) и трасса транспортирования а именно длина ее горизонтальной проекции Lr и высота подъема материала Н связанные между собой зависимостью
LГ = L cos и H = L sin где L — общая длина
трассы; — средний угол подъема трассы.
При сопоставлении машин разных типов которые можно применять для выполнения однотипных транспортных операций нужно исходить из общего экономического показателя определяемого стоимостью перемещения единицы материала зависящей от стоимости машины и срока ее службы эксплуатационных расходов а также численности обслуживающего персонала и его квалификации.
3. Характеристика транспортируемых материалов
Для правильного выбора типа машины необходимо учитывать существенные для процесса транспортирования физико-механические свойства материала: гранулометрический состав (состав по крупности) плотность подвижность и др.
Гранулометрический состав определяют ситовым анализом при котором регламентированный объем материала (пробы) просеивают последовательно через набор сит с калиброванными отверстиями различных размеров (номеров) (рис. 2.3).
По гранулометрическому составу различают материалы пылевидные (размер частиц до 005 мм) порошкообразные (005 050) мелкозернистые
(05 2) крупнозернистые (2 10) мелко-кусковые (11 60)
среднекусковые (61 160) крупнокусковые (161 320) особо крупные
Кусок размером более 500 мм считается «негабаритом» и перед транспортированием должен дробиться.
Если кусок в трех измерениях имеет размеры а1 а2 а3 то усредненный расчетный размер
Куски размером от аmax до 08amax образуют группу наибольших кусков. Отношение массы т0 группы наибольших кусков к массе т всей пробы
(с = т0т) характеризует расчетную крупность материала. Куском с
максимальным расчетным размером считают кусок размером а при
с > 01 и размером а' = 08ашах при с 01.
В зависимости от соотношения отдельных фракций различают рядовой и сортированный материал. Если аmax и аmin — размеры наибольшего и наименьшего кусков то для рядового материала
аmахamin > 25 для сортированного amaxamin 25.
Для сортированного материала типичным куском считается кусок размером а=05(аmах + amim). Плотностью материала называется отношение его массы к занимаемому объему. Для грузов представляющих собой куски различной крупности используют понятие насыпной плотности
Рис. 2.3. Схема ситового анализатора.
представляющей отношение массы груза в насыпном состоянии к его объему. Насыпная плотность зависит от плотности кусков (частиц) материала и его гранулометрического состава от пористости и степени заполнения пор водой что определяется влажностью материала. Для влажного кускового и
зернистого материала насыпная плотность
где — плотность сухого материала; — влажность определяемая экспериментальным путем; = (т1 — m2)m2 здесь т1 и m2 — массы проб до и после высушивания.
Подвижность является характерной особенностью сыпучих материалов. Степень подвижности зависит от внутренних сил трения и сцепления между частицами определяемых в общем случае сопротивлением Т сыпучего тела сдвигу:
где N — сила давления материала; — коэффициент
внутреннего трения сыпучего материала равный тангенсу угла внутреннего трения; с — сила сцепления приходящаяся на единицу площади F по которой происходит сдвиг.
После деления всех членов этого уравнения на F получим;
где и — касательное и нормальное напряжения.
Различают хорошо сыпучие материалы у которых сцепление отсутствует и плохо сыпучие (связные) обладающие сцеплением. Сила сцепления хорошо сыпучих материалов при их кратковременном слеживании (с = 04 1 кПа) значительно ниже силы сцепления таких грунтов как супесь (с = 10 20 кПа) суглинок и глина (с = 40 100 кПа).
Если поры сыпучего материала заполнены цементирующим веществом (особенно при продолжительном слеживании) или капиллярной водой (создающей поверхностное натяжение) силы сцепления значительно возрастают. Возрастают они и в том случае когда частицы сыпучего материала имеют
неровности которыми они сцепляются между собой.
Численные значения сил сцепления определены только для некоторых сыпучих материалов и для большинства из них (кроме грунтов) отсутствуют.
Отсутствуют также экспериментальные данные о влиянии крупности и формы на сцепление кусковых материалов.
Подвижность сыпучих материалов определяется углом их естественного откоса в покое т. е. углом наклона к горизонтальной плоскости образующей конуса свободно насыпанного (без падения с высоты) материала (рис. 2.4). Для хорошо сыпучих материалов угол ф1 естественного откоса равен углу внутреннего трения: .
Если материал насыпается при падении с некоторой высоты угол ф2
естественного откоса окажется уже углом естественного откоса в движении; он меньше угла ф1 так как потенциальная энергия падающего материала трансформируется в кинетическую энергию дополнительного движения материала. Угол ф2 определяют при высоте падения около 1 м. На основании экспериментальных исследований принимают что при этом условии .
Для связных насыпных материалов образующая поверхности откоса не прямолинейна; средний угол естественного откоса больше угла внутреннего трения и зависит от способа формирования откоса — насыпанием или обрушением.
Коэффициент внешнего трения f материала о стенки хранилищ и грузонесущие элементы транспортирующих машин зависит от того находится ли материал в покое или в движении и определяется экспериментально.
Коэффициенты внутреннего и внешнего трения зависят один от другого. Ориентировочно можно принимать что коэффициент трения материала о сталь fc = 075tg о резину fp = 085tg о бетон .
Численные значения и и для наиболее распространенных строительных материалов приведены в табл. 2.1.
Материалы с насыпной плотностью до 06 тм3 считаются легкими от 06 до 16 — средними от 16 до 2 — тяжелыми выше 2 — весьма тяжелыми.
Кроме перечисленных в табл. 2.1 основных физико-механических свойств сыпучих материалов при выборе типа транспортирующей
машины необходимо учитывать особые свойства материалов: абразивность острокромочность липкость хрупкость
слеживаемость смерзаемость и др. Численные значения показателей этих свойств подлежат экспериментальному определению.
Абразивностью т. е. свойством истирать при относительном движении соприкасающиеся поверхности обладают все основные строительные материалы поэтому их не следует перемещать машинами в которых материал скользит по грузонесущему элементу.
Острокромочность свойственна для большинства средне и крупнокусковых строительных материалов особенно добываемых взрывным способом. Такие материалы не следует перемещать на грузонесущих элементах машины с недостаточно прочной поверхностью например на обрезиненных лентах.
Липкостью (адгезией) т. е. свойством прилипать к соприкасающимся поверхностям обладают в основном влажные и мокрые грузы — бетоны растворы и др. При транспортировании необходимо обеспечивать их принудительную разгрузку.
Хрупкостью т. е. способностью разрушаться при толчках и падении в процессе перегрузок отличаются различного рода керамические изделия. Их следует транспортировать особо осторожно не допуская падения с высоты.
Слеживаемостыо т. е. способностью терять подвижность частиц при длительном хранении обладают многие строительные материалы — цемент
известь глина и др. Слеживаемость увеличивается при давлении влажности и тряске. Длительное хранение слеживающихся материалов нецелесообразно.
Смерзаемостью обладают преимущественно влажные материалы и материалы хранящиеся во влажной среде. Транспортировать их при отрицательных температурах следует по утепленным трассам.
4. Режимы работы конвейеров.
В зависимости от классов использования конвейера по времени и производительности различают пять режимов работы: ВЛ — весьма легкий Л — легкий С — средний Т — тяжелый ВТ — весьма тяжелый (табл. 2.2).
Анализ различных вариантов конструктивного исполнения и проведения основных кинематических и прочностных расчетов.
1. Цепные конвейеры.
Цепными конвейерами являются конвейеры в которых тяговым элементом является длиннозвенная обычно пластинчатая цепь. В зависимости от типа несущего органа цепные конвейеры классифицируют на пластинчатые скребковые ковшовые люлечные тележечные подвесные тяговые толкающие и др. В промышленности строительных материалов применяют преимущественно пластинчатые конвейеры используемые для перемещения крупнокусковых и горячих материалов.
В тех случаях когда необходимо транспортировать горячие и острокромочные материалы а также кусковые или штучные большой массой которые ленточным конвейером перемещать невозможно применяют цепные пластинчатые конвейеры горизонтальные или слабо наклонные. В промышленности строительных материалов широкое распространение получили короткие пластинчатые конвейеры (ГОСТ 22281-76) для перемещения крупнокускового камня в дробилки шириной настила 04 16 м при скорости транспортирования 001 1 мс.
При сходстве общих схем пластинчатый и ленточный конвейеры конструктивно значительно отличаются друг от друга.
Пластинчатый конвейер состоит из двух бесконечных пластинчатых длиннозвенных цепей (рис. 3.1.) которые огибают установленные по концам конвейера приводные и натяжные звездочки 8 и 4; в пролете между ними цепи опираются роликами 6 на направляющие 7 закрепленные на раме 2. Ведущие (приводные) звездочки установлены в головной части конвейера. Привод 9 конвейера не отличается от привода ленточных конвейеров и выполняется обычно редукторным иногда - при малых скоростях конвейера - с дополнительной зубчатой передачей к валу ведущих звездочек. Цепи натягиваются винтовым натяжным устройством 3.
В отличие от ленточных конвейеров в которых работа натяжного устройства заключается в обеспечении передачи тягового усилия трением в пластинчатых конвейерах тяговое усилие передается зацеплением и работа натяжного устройства заключается только в выборе слабины тягового элемента. Поэтому предварительное натяжение должно быть минимальным (1 2 кН) но не меньше динамического усилия.
К цепям прикрепляется настил 5 состоящий из металлических пластин (гладких или фигурных штампованных или литых). Для перемещения сыпучих материалов отдельные пластины на шарнирах цепи перекрывают друг друга что предотвращает просыпание материала. Конвейер загружается через загрузочную воронку разгружается — через звездочки. При гладком настиле возможна разгрузка плужковым сбрасывателем. Скорость перемещения рабочих элементов v = 005 063 мс обычно v= 02 05 мс.
Основные параметры стационарных пластинчатых конвейеров общего назначения стандартизованы (ГОСТ 22281—76*).
Известны конструкции пластинчатых конвейеров для транспортирования материалов по криволинейному пути в плане и под углом до 30° к горизонту. Настил таких конвейеров состоит из элементов шарнирно связанных между собой а тяговый цепной элемент может изгибаться в двух плоскостях. В строительстве такие конвейеры применения не получили.
Разновидностью наклонных пластинчатых конвейеров являются эскалаторы тоннельные для метрополитенов и поэтажные для крупных общественных зданий магазинов и др.
В эскалаторе (рис. 3.2.а) в качестве тягового элемента применяю две
параллельных пластинчатых тяговых цепи малого
шага обычно t = 200 мм а в качестве настила используют ступени глубиной А = 400 мм и шириной В = 1000 мм (рис. 3.2. в) опирающиеся при помощи колес на две системы направляющих что позволяет ступенькам складываться на верхней и нижней площадках в плоский настил. В поэтажных эскалаторах иногда применяют настил шириной В=600 мм. В качестве поручней в эскалаторах используют ленточные конвейеры с резинотканевой лентой специального профиля
2. Ковшовые конвейеры.
В ковшовых конвейерах материал перемещается в отдельных сосудах ковшах укрепленных на тяговом элементе конвейерной резинотканевой ленте или цепях.
Ковшовые конвейеры разделяют на ковшовые элеваторы перемещающие материал в вертикальном или круто наклонном направлении и конвейеры перемещающие материал по пространственной кольцевой трассе. В строительстве применяют только ковшовые элеваторы являющиеся по существу подъемниками перемещающими материал в ковшах непрерывным потоком.
Ковшовый элеватор имеет бесконечный замкнутый тяговый элемент 2
(рис. 3.3. а) на котором с равными интервалами укреплены ковши 1. Тяговым элементом являются ленты (рис. 3.3. а) или одна или две цепи (рис. 3.3. б в). Лента огибает приводной 3 и натяжной 4 барабаны укрепленные в верхней и нижней частях элеватора. Цепь огибает укрепленные в этих же местах звездочки. В пролете между крайними точками тяговый элемент в вертикальных элеваторах небольшой высоты опор не имеет В наклонных и высоких вертикальных элеваторах лента опирается на направляющие ролики. Цепи катятся роликами по направляющим (рис. 3.3. г) или опираются так же как и лента на направляющие ролики (рис. 3.3. д). Элеватор закрыт металлическим кожухом с окнами для осмотра и состоит из отдельных секций. Наклонные элеваторы иногда бывают открытыми без кожуха (рис. 3.3. д).
3. Винтовые конвейеры
Винтовой конвейер имеет желоб 4 (рис. 3.4. а) полукруглой формы внутри которого расположен винт 5 вращающийся в подшипниках 3 при помощи привода 8. Материал загружается через загрузочное отверстие 2 а выгружается через выходное отверстие 6 с задвижкой 7. Желоб обычно закрыт крышкой 1 но иногда имеет песочный затвор. Винтовые конвейеры используют для транспортирования на небольшие расстояния
(30 40 м) сыпучих и мелкокусковых (цемента гравия песка шлака и т. п.) а также вязких и тестообразных (мокрой глины бетона и т. п.) материалов.
4. Роликовые конвейеры.
Роликовые конвейеры применяют для перемещения штучных грузов преимущественно удлиненной формы (металлических листов листов сухой штукатурки и др.) выполняют в виде ряда последовательно
установленных на прямолинейной или криволинейной раме роликов на которые опирается перемещаемый груз. Расстояние между роликами задается таким чтобы груз в любом положении опирался не менее чем на три ролика.
Применяют приводные и не приводные роликовые конвейеры. В приводных (ГОСТ 20708—75) конвейерах отдельные ролики приводятся цепной или ременной передачей.
Ролики выполняют из стальных труб и устанавливают на подшипниках качения на неподвижных осях.
При необходимости работать с крупноразмерными металлическими листами (например в цехах металлоконструкций) применяют специальные столы с шариками. Применяются также роликовые столы с эксцентрично-поворотными роликами. Шариковые и роликовые столы выполняют горизонтальными.
1. Описание технологического процесса
Технологический процесс предусматривает 2-е схемы работы комплекса.
-ая - Прием инертных грузов с железнодорожного или автомобильного приемного устройства и подача материалов на хранение в склад.
-ая схема - Выдача инертных материалов со склада в производство
1.1.Описание схемы № 1.
В зависимости от прибытия грузов железнодорожным или автомобильным транспортом груз соответственно принимается железнодорожным или автомобильным приемным устройством.
Возможна схема одновременной работы 2-х приемных устройств при этом оператор должен определить какой из 2-х конвейеров (ЛК-2. ЛК-3) должен работать на прием инертных грузов с железнодорожного приемного устройства и соответственно с автомобильного приемного устройства.
На железнодорожном приемном устройстве инертные грузы
(щебень песок) из полувагонов разгружаются в бункеры под которыми установлен горизонтальный ленточный конвейер.
Горизонтальный конвейер передает материал на наклонно-горизонтальный конвейергкоторый в свою очередь передает или на конвейер ЛК-2 или на ЛК-3 в зависимости от принятой (оператором) схемы передачи материала.
С наклонно-горизонтального конвейера материал сбрасывается на ЛК-3 плужковым сбрасывателем на конвейер ЛК-2 - с приводного барабана.
На автомобильном приемном устройстве инертные грузы разгружаются с автосамосвалов в приемные бункеры. Под бункерами соответственно установлены питатели и ленточный конвейер ЛК-1 с плужковым сбрасывателем.
Далее материал с конвейеров ЛК-2 и ЛК-3 подается на конвейеры ЛК-4 и ЛК-5 соответственно.
На конвейерах ЛК-4 и ЛК-5 установлены разгрузочные реверсивные тележки которые загружают отсеки склада материалом поступающим от приемных устройств (автомобильным и железнодорожным). При полном заполнении любого из отсека склада срабатывает один из датчиков уровня материала установленного в верхней части отсеков склада при этом отключается конвейерный тракт подачи материала от приемных устройств в обратной последовательности его включения т.е. сначала отключаются конвейеры установленные под бункерами приемных устройств (АПУ и ЖДПУ) затем последующие конвейеры тракта.
Для заполнения следующего отсека склада оператор включает привод передвижения разгрузочной тележки конвейеров ЛК-4 и ЛК-5. Отключение передвижения разгрузочных тележек осуществляется автоматически от конечных выключателей установленных над каждым отсеком склада с определенным шагом.
При одновременной разгрузке заполнителей с двух приемных устройств (автомобильного и железнодорожного) оператор выбирает последовательность включения конвейеров ЛК-2; ЛК-3; ЛК-4; ЛК-5 в зависимости от выбранной схемы подачи материала от приемных устройств на ту или иную линию конвейеров.
1.2. Описание схемы № 2.
Выдача инертных материалов со склада в БСУ осуществляется в следующем порядке:
Из отсеков склада песок или щебень через вибропитатели поступают на подштабельные ленточные конвейеры - ЛК-6 или ЛК-7. Далее подача материала с конвейеров ЛК-6 и ЛК-7 осуществляется в следующей последовательности ЛК-8 ЛК-9ЛК-10. Конвейер ЛК-10 подает материал на существующий конвейер-питатель №26 расположенный в здании БСУ на отметке +20.80 м который в свою очередь подает материал в на копительные бункеры БСУ.
Последовательность включения конвейерного тракта выдачи материала со склада следующая:
Конвейер-питатель № 26 ЛК-10ЛК-9ЛК-8ЛК-6 или ЛК-7 вибролотки.
Отключение конвейерного тракта осуществляется в обратной последовательности его включения при этом материал находящийся на конвейерах должен полностью отработан (пересыпан) в накопительные бункеры БСУ.
2. Механизированное железнодорожное приемное устройство.
В качестве аналога по электротехнической части проекта необходимо использовать имеющиеся в архиве материалы проекта №6232 где принципиальные схеы управления бурорыхлильного комплекса приемного устройства аналогичны разрабатываемому проекту за исключением замены устаревшего электрооборудования которое показано на технологических чертежах данного задания.
3.Автомобильное приемное устройство
В автомобильном приемном устройстве установить местный пульт управления (пуско-наладочный) для управления конвейером ЛК-1 ЛК-12 и подбункерными вибролотковыми питателями и вибраторами установленными на бункерах приемного устройства.
4. Технологическая схема.
5. Предназначение и описание работ и операций производимых
надштабельным ленточным конвейером.
Конвейер предназначен для приема заполнителей бетона с конвейеров подающих материал от приемных устройств (железнодорожного и автомобильного) с последующей подачей материала в складские емкости.
Конвейер размещается в верхней части склада на отметке 13.70.
Перед началом работ надштабельного конвейера включается предпусковая сигнализация (световая и пусковая) затем включается привод конвейера который включается приводит в движение конвейерную ленту. После чего материал поступающий конвейерными системами от приемных устройств подается на ленту надштабельного конвейера.
Надштабельный конвейер с помощью разгрузочной тележки отсыпает материал в отсеки складской емкости.
В зависимости от поступающего груза (песок или щебень) разгрузочная тележка устанавливается над соответствующим отсеком склада.
При этом оператор определяет с помощью датчиков установленных каждом отсеке степень заполнения складских емкостей.
После окончания подачи материала от приемных устройств (железнодорожного или автомобильного) конвейер выключается. Отключение конвейера осуществляется после полного схода материала с конвейерной ленты.
Для работы разгрузочной тележки к раме прикрепляется вертикальная
штанга для питающего кабеля привода тележки. Питающий кабель подвешивается на каретки перемещающиеся по монорельсовому пути обеспечивая при этом ход тележки вдоль склада на расстоянии порядка 100 м.
Для натяжения конвейерной ленты приводного барабана предусмотрена грузовая натяжка вертикального расположения. Конвейерная лента с
помощью грузов подвешенных к раме натяжного барабана находится в постоянном натяжении обеспечивая при этом нормальное сцепление ленты с приводным барабаном. В нижней части натяжного устройства установлен конечный выключатель который реагирует на предельную вытяжку конвейерной ленты. При срабатывании данного конечника отключается привод конвейера сигнализирующий о необходимости перетяжки
Расчет эксплуатационной производительности:
Техническая производительность
Коэффициент по времени (4.1)
Коэффициент рабочих дней за год (4.2)
Коэффициент учитывающий простои на техосмотр и ремонт
Описание конструкции и предварительная разработка общего вида машины.
1. Описание ленточного конвейера.
Основными частями ленточного конвейера (рис. 5.1.) Являются: гибкая лента служащая одновременно грузонесущим и тяговым органом; привод состоящий из одного или двух барабанов одного или большего числа двигателей и редукторов; станина и установленные на ней стационарные роликоопоры поддерживающие ленту по длине конвейера и натяжное устройство для ленты. В отдельных случаях при перемещении нетяжелых штучных грузов рабочая ветвь ленты вместо роликоопор движется по настилу. Кроме того в состав конвейера могут входить погрузочное и разгрузочное устройство устройства для очистки ленты для взвешивания груза на ленте контрольная
Рис. 5.1. Схема ленточного конвейера.
-лента; 2 – роликоопоры; 3- приводной барабан; 4-натяжной барабан; 5- погрузочная станция.
и автоматическая аппаратура. В некоторых случаях на конвейере устанавливают два или большее число приводов а также два натяжных устройства или
Ленточные конвейеры являющиеся наиболее распространенным средством непрерывного транспорта в промышленности на строительстве в сельском хозяйстве и производстве служат для перемещения как разнородных насыпных
так и штучных грузов. Транспортируемые насыпные грузы могут быть порошкообразные зернистые и мелкокусковые среднекусковые и крупнокусковые а также рядовые. Размеры и вес штучных грузов
ограничиваются условиями перемещения их на ленте. Ленточные конвейеры для насыпных грузов характеризуются чрезвычайно широким диапазоном производительности — от нескольких тонн до нескольких тысяч тонн в час (на наиболее мощных установках достигнута производительность до
Длина ленточных конвейеров колеблется в широких пределах — от нескольких метров до нескольких сотен и даже тысяч метров ( наибольшая длина ленточного конвейера достигает 4500 м а конвейерных линий 10—12 км и более).
В зависимости от типа роликоопор лента может иметь плоскую или желобчатую форму. Первую применяют преимущественно при транспортировании штучных грузов вторую — при транспортировании насыпных так как желобчатая форма обеспечивает большую производительность при той же ширине и скорости ленты.
Ленточные конвейеры могут быть горизонтальные или наклонные с движением груза вверх или вниз. Наибольший допустимый угол наклона конвейера ограничивается возникновением скольжения или ссыпания груза вдоль ленты под действием силы тяжести. Провес ленты между роликоопорами и перегибы на роликоопорах способствуют возникновению скольжения груза по ленте поэтому допускаемый угол наклона конвейера принимают несколько меньше угла трения груза по ленте. Для увеличения угла наклона сверх этого предела применяют специальные типы лент и ленточных конвейеров.
Ленточные конвейеры могут быть как прямолинейными так и изогнутыми в вертикальной плоскости с выпуклостью вверх или вниз. При выпуклости вверх лента в месте изгиба огибает отклоняющий барабан или батарею расположенных по кривой роликоопор. При выпуклости вниз лента лежит на расположенных по кривой роликоопорах причем радиус кривизны должен быть достаточно велик чтобы лента под натяжением не приподнималась с роликоопор. Геометрические схемы ленточных конвейеров показаны на (рис.5.2. а-ж .)
Рис.5.2. геометрические схемы ленточных конвейеров
Основной тип ленты - прорезиненная лента с тканевой или тросовой основой. Кроме того применяют ленты из тонкой стальной цельнокатаной полосы а также ленты проволочного плетения. К специальным типам конвейеров с грузонесущей лентой относятся ленточно-канатные и ленточно-цепные конвейеры. На них лента служит только грузонесущим элементом а функции тягового элемента выполняют канаты или цепи.
В зависимости от назначения ленточные конвейеры разделяют по конструкции на стационарные передвижные и переносные.
Конвейерная лента служащая тяговым и грузонесущим элементом конвейера состоит из придающего ей прочности каркаса и защитных резиновых обкладок.
Наибольшее распространение имеют ленты с каркасом из тканевых прокладок соединяемых между собой тонкими (толщиной 02-03мм ) резиновыми прослойками сквиджами (рис.5.3. а). На мощных конвейерах на которых лента испытывает значительные тяговые усилия получает применение
каркас из тросов свитых из тонких проволок (рис. 5.4. б).
Рис .5.3. Сечение конвейерных лент : а - с прокладками ; б – с тросами.
К конвейерной ленте предъявляются требования высокой продольной прочности эластичности (гибкости) при изгибе в продольном (на барабанах) и поперечном (на лотковых роликоопорах) направлении невысокий собственный вес малое упругое и остаточное удлинение под действием продольных сил малая гигроскопичность хорошая сопротивляемость расслоению от действия многократных перегибов на барабанах и роликоопорах а также сопротивляемость
истиранию и повреждению падающими на ленту в месте погрузки кусками груза особенно - абразивного и крупнокускового.
Тканевые прокладки изготовляют из прочных воспринимающих тяговую нагрузку нитей основы и более слабых и редких нитей утка. Прокладки лент повышенной прочности изготовляют также из толстых шнуров основы соединенных между собой тонкими нитями утка (уточная шнуровая ткань). Для повышения сопротивления ленты пробою падающими тяжелыми кусками тканевый каркас иногда покрывают сверху и с боков защитной разреженной брекерной тканью
Количество прокладок в ленте определяемое по требующейся продольной прочности зависит также от ее ширины. В лентах типа ОПБ и суточной шнуровой тканью предусматривается следующее число прокладок.
Ширина ленты в мм 650 800 1000 1200 1400 1600 1800 2000 Число прокладок 3—5 3—6 4—8 5—9 6—10 7—10 8—12 10—12
Все большее применение получают ленты с прокладками из синтетических тканей обладающих значительно большей механической и усталостной прочностью и устойчивостью против гниения.
Поддерживающие ленту по всей длине роликоопоры разделяют на однороликовые (рис. 54 а) — для плоской ленты на грузовой ветви и для обратной ветви двухроликовые (рис. 54 б) трехроликовые (рис. 54 в) — для лотковой ленты и четырех и пятироликовые — для весьма широких
лент. Трехроликовые опоры нормальных типов имеют все три ролика одинаковой длины и боковые ролики расположенные обычно под углом 20 или 30° а для весьма широких лент 35°. Ленты с синтетической и тросовой основой имеющие повышенную поперечную гибкость допускают увели-чение угла наклона боковых роликов до 30 и 35° без ущерба для долговечности ленты. Достоинством таких роликоопор является возможность повышения
производительности при той же ширине ленты примерно на 15% и лучшее центрирование хода ленты.
Ролики обратной ветви нередко делают с надетыми на них металлическими или резиновыми дисками. Такие ролики меньше подвержены загрязнению и способствуют очищению ленты.
По конструкции ролики отличаются чрезвычайным разнообразием однако на основании большого опыта эксплуатации ленточных конвейеров и усовершенствования технологии изготовления роликов намечается все большее применение роликов на сквозной не вращающейся оси с лабиринтным
уплотнением шарикоподшипников и долговременной смазкой.
Устройства для очистки ленты.
Полная очистка ленты от приставших к ней частиц груза имеет существенное значение для повышения срока службы ленты и обеспечения нормальной эксплуатации конвейера. Неотделенные от ленты частицы груза вжимаются в ее
обкладку при огибании ею барабанов рабочей стороной а также при движении
по роликоопорам обратной ветви налипают на поверхность барабанов вызывая перекосы а на приводных барабанах — уменьшение силы сцепления с ленты.
К средствам очистки ленты предъявляются требования не только полноты очистки но и сохранности обкладки ленты длительных срокоц работы без большого износа и загрязнения простоты и надежности конструкции. Однако существующие средства очистки далеко не полностью удовлетворяют этим требованиям.
Механическая очистка ленты производится с помощью устанавливаемых под головным барабаном или вблизи него скребков или приводимых в действие двигателями щеток. Скребки делают цельными по всей ширине ленты (рис. Рис.5.5.) или состоящими из отдельных небольших скребков-лопаток устанавливаемых в два ряда и прижимаемых к ленте пружиной. Вращающиеся щетки изготовляют из резиновых полос капроновых или других эластичных нитей из синтетического материала. Щетки быстро вращаются навстречу движению ленты и отбрасывают снимаемые с ленты
частицы. Помимо механических способов очистки применяют гидравлический и пневматический способы производя смыв или сдувание частиц струями воды или воздуха выходящими под большим давлением через узкие отверстия расположенные на близком расстоянии от ленты. Гидравлическая очистка хотя и может быть довольно полной имеет тот недостаток что попадающая на приводной барабан вода влечет уменьшение коэффициента трения ленты по барабану.
2. Описание разрабатываемого ленточного конвейера.
В соответствии с требованиями завода я спроектировал ленточный
Длинна складской емкости составляет 9816м. которая разбита на 7 секций для приема и хранения заполнителей бетона.
Конвейер надштабельный состоит из основных узлов и агрегатов позволяющие осуществлять процесс загрузки склада согласно технологической схеме работы складского комплекса.
В состав конвейера входят:
- натяжное устройство конвейера
- роликоопоры верхние желобчатые
- роликоопоры нижние
- Барабан приводной концевой и отклоняющий
- Конвейерная лента резинотканевая
- Тележка разгрузочная с вертикальной штангой (для перемещения питающего кабеля.)
- Ограждающие конструкции приводной станции концевого барабана средней части конвейера и других узлов.
- Устройства от схода ленты.
- Устройство для аварийного отключения конвейера.
Управление конвейером осуществляется дистанционно с пульта управления оператором.
Расчет (уточненный) ленточного горизонтального конвейера ЛК – 4
1. Выбор скорости конвейера.
Выбираем согласно с ГОСТ 22644-77 для конвейера длиной – 10936 м. скорость конвейера v=16 мсек (табл. 1 стр. 9 каталога).
2. Выбор ширины ленты.
Где Q=400 тчас – расчетная весовая доля конвейера;
- насыпная плотность груза (задана ТУ черт.
№ 03-0630-00. ТХ).В соответствии с ГОСТ 22644-77 выбираем
ближайшее большое стандартное значение В=800 мм.
3.груза приходящаяся на 1м длинны ленты (кгм).
численно равна линейной нагрузке от массы груза (Нм)
определяемой по формуле:
и - линейные нагрузки (Нм) от массы вращающихся частей роликоопор соответственно верхней и нижней ветвей ленты численно равные массам вращающихся частей соответствующих роликоопор в кгм:
где и - массы вращающихся частей одной роликовой опоры соответственно верхней и нижней ветвей ленты (табл. 7 стр.14 каталога);
и - расстояние между роликоопорами соответственно верхней и нижней ветвей ленты (шаг роликоопор стр. 13 каталога).
Средняя линейная нагрузка ленты зависит от массы резинотканевой ленты (табл. 6 стр. 13 каталога).
4. Расчетная схема трассы конвейера.
5. Расчет сопротивлений движению ленты на участках трассы
5.1. Для режима 1 – пускового с грузом.
5.1.1. Отклоняющий барабан:
5.1.2. Горизонтальный участок нижней ветви:
5.1.3. Оборотный барабан:
5.1.5. Натяжной барабан:
5.1.6. Подъем ленты:
5.1.7. Оборотный барабан:
5.1.8. Горизонтальный участок нижней ветви:
5.1.9. Отклоняющий барабан:
5.1.10. Хвостовой барабан:
5.1.11. Горизонтальный участок верхней ветви:
5.1.12. Наклонный участок верхней ветви:
5.1.13. Разгрузочная тележка:
5.1.14. Горизонтальный участок верхней ветви:
5.1.15. Загрузочное устройство.
для (табл. 49 стр. 94 каталога).
(прибавляется к сопротивлению движению ленты на наклонном участке верхней ветви ).
5.2. Для режима 2-установившегося с грузом.
5.2.1. Отклоняющий барабан.
5.2.2. Горизонтальный участок нижней ветви:
5.2.3. Оборотный барабан:
5.2.5. Натяжной барабан:
5.2.6. Подъем ленты:
5.2.7. Оборотный барабан:
5.2.8. Горизонтальный участок нижней ветви:
5.2.9. Отклоняющий барабан:
5.2.10. Хвостовой барабан:
5.2.11. Горизонтальный участок верхней ветви:
5.2.12. Наклонный участок верхней ветви:
5.2.13. Разгрузочная тележка:
5.2.14. Горизонтальный участок верхней ветви:
5.2.15. Загрузочное устройство.
6.1. Для режима 1 – пускового с грузом.
Тяговый фактор приводного барабана однобарабанного привода определяется соотношением между натяжениями ветвей ленты набегающей на приводной барабан и сбегающий с приводного барабана:
Решаем одновременно два уравнения и определяем
Значение берем в табл. 16 стр. 34 каталога - в табл. 17 стр. 35 каталога : (для поверхности приводного барабана футерованной резиной загрязнении нелипкими грузами – песком углем и влажной атмосферой).
(при и угле обхвата приводного барабана или 367 – в радианах).
Полученное значение подставляем последовательно и определяем натяжение ленты во всех рассматриваемых точках трассы ленточного конвейера.
6.2. Для режима 2 – установившегося с грузом.
7. Расчет и выбор основного оборудования ленточного конвейера.
Мощность привода типоразмеры конвейера барабанов и грузового устройства должны определятся по результатам уточненного тягового расчета режима 1 (пусковой с грузом) типоразмер ленты – режима 2 (установившийся с грузом).
7.1. Приводной барабан.
Окружное усилие на приводном барабане (Н) определяется по формуле (режим 1):
где - к.п.д. приводного барабана который определяется по формуле:
где - коэффициент сопро сопротивления вращению приводного барабана (с учетом сопротивлений очистительных устройств и изгиба ленты). Для установившегося режима для пускового . Значение выбираем в табл. 17 стр. 35 каталога (при и угле обхвата барабана ).
Нагрузка на барабан (6.7.3)
По окружному усилию и нагрузке на барабан из табл. 8 стр.
каталога выбираем типоразмер приводного барабана:
Расчетный крутящий момент на валу приводного барабана:
7.2. Неприводные барабаны.
В уточненном методе расчета неприводной барабан выбираем или проверяем по фактической нагрузке от натяжения ленты действующей на неприводной барабан при режиме 1 ( пуск загруженного конвейера ). Нагрузку определяем по формуле :
7.2.1. Отклоняющий барабан .
где - натяжение ленты на барабане т.е.
Расчетная нагрузка должна быть не более допустимой нагрузки т.е.
Выбираем по табл.20 стр. 45 каталога типоразмер отклоняющего барабана: « 80315 - 50 »
Проверяем - в таблице больше расчетного .
7.2.2. Оборотный барабан .
Выбираем по табл.20 стр. 45 каталога типоразмер оборотного барабана:
Проверяем - в таблице больше расчетного .
7.2.3. Натяжной барабан .
Выбираем по табл.20 стр. 45 каталога типоразмер натяжного барабана:
7.2.4. Оборотный барабан .
7.2.5. Отклоняющий барабан .
7.2.6. Хвостовой барабан .
Выбираем по табл.20 стр. 45 каталога типоразмер хвостового барабана:
7.3. Приводной механизм.
Расчетная мощность двигателя Nр ( кВт ) определяется по формуле :
где К - коэффициент неучтенных потерь для приводов мощностью до
кВт и слабонаклонном конвейере К = 115 ( стр. 23 каталога );
- к.п.д. редуктора режимов 1 и 2 .
Расчетная частота вращения приводного барабана ( обмин ) определяется по формуле :
Расчетное передаточное число редуктора (6.7.19)
где - синхронная частота вращения двигателя.
На основании принятой скорости ленты расчетной мощности
двигателя N = 2756 кВт расчетного передаточного числа редуктора
и подбираем приводной механизм:
двигатель серии 4А напряжением 380В50гц с номинальной мощностью N= 30 кВт синхронной частотой вращения и
редуктор « Ц2У - 315Н » с передаточным числом сборки 12;
тормоз « ТГК -300 »;
муфта тихоходная кулачково - дисковая « КДН 320 - 11ОЦ2У90Н2»;
муфта быстроходная «710-40-.1-55-.1»
Фактическая скорость ленты конвейера ( мсек ) определяется по формуле : (6.7.20)
Расчетное число прокладок резинотканевой ленты определяется по формуле :
где - запас прочности ленты на разрыв;
В - ширина ленты см;
Кр - номинальная прочность тканевых прокладок даНсм ширины
Выбираем по табл. 18 стр.38 каталога конвейерную ленту по ГОСТ 20-85 : лента конвейерная типа 2 подтипа 2.2 общего назначения шириной 800мм с 3-мя прокладками из ткани ТК-100 с рабочей обкладкой 5мм и нерабочей 2мм обкладки из резины класса ИБ :
лента 2.2-800-3-ТК-100-5-2-ИБ ГОСТ 20-85.
По табл. 18 стр. 38 каталога берем значение коэффициента Кр =1000 Нсм и вариант 4 для определения
По табл. 18 стр.40 каталога при варианте 4 и угле наклона конвейера до 10 град. (у нас 0 град.) принимаем
При В = 80 см расчетное число прокладок
Принимаем количество прокладок равным 3 согласно минимально допустимому количеству указанному в табл. 18 стр.38 каталога для данного вида ленты.
7.5. Проверка диаметра приводного барабана по соотношению:
где - коэффициент учитывающий тип тканевой прокладки ленты. Для ткани ТК-100 по табл. 10 стр. 22 каталога выбираем
и угле обхвата барабана лентой . по табл.11 стр.22 каталога коэффициент где - допустимое усилие в ленте а 8]5 = 5б - усилие в ленте в месте установки барабана.
7.6. Проверка диаметра неприводных барабанов по соотношению (6.7.24)
где - коэффициент учитывающий тип тканевой прокладки ленты. Для ткани ТК-100 по табл. 10 стр. 22 каталога определяем ;
При и угле обхвата барабана лентой по табл.11 стр.22 каталога выбираем коэффициент где - допустимое усилие в ленте а - усилие в ленте в месте установки
7.6.1. Отклоняющий барабан
При по табл.11 стр.22 каталога выбираем коэффициент К2 = 32. (6.7.25)
7.6.2. Оборотный барабан
При по табл.11 стр.22 каталога выбираем коэффициент К2 = 40. (6.7.26)
7.6.3. Натяжной барабан
При по табл.11 стр.22 каталога выбираем коэффициент К2 = 50. (6.7.27)
7.6.4. Оборотный барабан
При по табл.11 стр.22 каталога выбираем коэффициент К2 =40. (6.7.28)
7.6.5. Отклоняющий барабан
При по табл.11 стр.22 каталога выбираем коэффициент К2 = 32. (6.7.29)
7.6.6. Хвостовой барабан
При по табл.11 стр.22 каталога выбираем коэффициент К2 = 50. (6.7.30)
7.7. Натяжное устройство.
7.7.1. Выбор типоразмера натяжной рамы.
В данном методе расчета в отличие от приближенного метода типоразмер натяжного устройства выбираем или проверяем по фактическому усилию действующему на натяжной барабан при установившемся режиме работы
Конвейера S' т. е. необходимому усилию натяжного устройства. Это усилие равно сумме натяжений ленты в точке набегания ленты на натяжной барабан и в точке сбегания ленты с барабана т. е. применительно к схеме конвейера
S' = S5 + S6 = 66553 + 69216 = 139759 Н. (6.7.31)
Усилие S' не должно быть больше допустимой нагрузки на натяжной барабан т.е. поэтому выбираем типоразмер натяжной
рамы : « 8040Р —60 » для которого
(табл. 39 стр. 77 каталога).
Выбор типоразмера натяжной рамы определяется по необходимому
расчетному усилию (Н) грузового устройства которое с учетом пускового режима и с достаточной точностью для конвейера с вертикальным натяжным устройством рассчитывается по следующей формуле :
где - натяжение ветви ленты сбегающей с натяжного барабана;
- нагрузка (Н) от массы натяжного барабана с ходовым устройством
(натяжной тележкой натяжной рамой) которая численно равна
массе (кг) натяжного барабана с ходовым устройством. Значение принимаем по натяжной раме ( тележке ) типоразмер которой (диаметр барабана) меньше диаметра приводного барабана.
7.7.2. Расчет и выбор грузового устройства.
Грузовые устройства характеризуются наибольшим усилием создаваемым устройством т.е. усилием от максимально допустимого числа грузов. Необходимая масса груза Сгр (кг) грузового устройства без полиспаста численно равна усилию т.е. (6.7.33)
Для вертикального грузового устройства без полиспаста . (6.7.34)
Тогда число грузов без полиспаста для натяжного устройства определяем по формуле:
где 90 - масса одного груза кг.
Принимаем Zгр = 18 шт.
Тип грузового устройства с общим количеством грузов 18и с общей длиной каната 20 м - « 80 - 18 - 20 ».
7.7.3. Выбор каната.
Выбираем канат при ширине ленты В=800 мм и количестве грузов
÷30- « 175 - I - Н - 180 » ГОСТ 3070 - 88
(табл. 40 стр. 82 каталога).
7.8. Роликоопоры и ролики.
Типы и основные размеры роликоопор определены ГОСТ 22645 - 77. Роликоопоры подразделяются на роликоопоры верхней ветви ленты и роликоопоры нижней ветви ленты. Верхние могут быть желобчатые с () или прямыми (). Роликоопоры также разделяются на рядовые т. е. те которые составляют основное число несущих роликоопор и на специальные: амортизирующие центрирующие др.
Для предотвращения схода ленты кроме центрирующих роликоопор применяются дефлекторные ролики верхней и нижней ветвей ленты. Типоразмеры роликоопор для одной и той же ширины ленты отличаются друг от друга диаметром ролика в зависимости от которого различаются допустимые на них нагрузки. Выбор диаметра роликов роликоопор определяется путем сравнения нагрузки действующей на роликоопоры при заданных исходных данных ( Р'Р Р" Р) с допустимой нагрузкой ( Р' Р") предварительно принятого типоразмера роликоопоры.
Нагрузки действующие на роликоопоры (Н) от:
- верхней желобчатой ветви ленты
- нижней прямой ветви ленты
где - шаг роликоопор соответственно верхней и нижней ветвей ленты м.
Унифицированные значения равны 10 м. и 24 м. соответственно для верхней и нижней ветвей ленты.
Нагрузки Р'Р Р" Р не должны превышать допустимые нагрузки Р' Р" скорректированные по условиям долговечности и условиям эксплуатации т.е. :
- для верхней ветви ленты (6.7.40)
- для нижней ветви ленты (6.7.41)
где и - допустимые наибольшие нагрузки на роликоопоры в зависимости от ширины ленты В = 800 мм назначения
роликоопоры и ее типоразмера : д'р= 127 мм и д"р = 127 мм ( табл.21
Кv = 087 - коэффициент зависящий от скорости ленты v = 16 мсек (табл. 22 стр. 48 каталога)
КП = 12 - коэффициент зависящий от долговечности подшипников равной среднему значению - 10 тыс. час. и роликоопоры ( табл. 23
стр. 49 каталога) Ку= 05 - коэффициент зависящий от разряда условий работы роликоопоры - тяжелого ( Т) и диаметра ее роликов: д'р = 127 мм и д"р = 127 мм ( табл. 24 стр.49 каталога ) разряд условий работы определяется табл. 25 стр. 49 каталога в зависимости от суммы баллов равной 28 и которые в свою очередь определяются по табл. 26 стр. 49 каталога.
Кк = 10 - коэффициент зависящий от наибольшего размера кусков груза -для 60 мм и для ролика диаметром 127 мм ( табл. 27 стр. 49 каталога). Тогда или 551 10962 Н
Выбираем для конвейера роликоопору верхнюю гладкую желобчатую с шириной ленты В = 800 мм роликом диаметром Д = 127 мм и углом наклона бокового ролика 30 град.: роликоопору « ЖГ 80 - 127 - 30 »
ГОСТ 22645-77 ( табл. 21 стр. 48 каталога ) роликоопору
« ЖА 80-127-30 » ГОСТ 22645-77 ( табл.31. стр. 56 каталога ) для установки в местах загрузки ленты. Подбираем применяемые подшипники - № 304 для роликов роликоопор с диаметром 127 мм по табл. 29 стр.
Смазка роликов закладная и осуществляется через пресс- масленку. Выбираем для конвейера роликоопору нижнюю прямую с шириной ленты В = 800 мм с гладким роликом диаметром Д = 127 мм : роликоопору « НГ 80
- 127 ГОСТ 22645 - 77 ( табл. 21 стр. 48 каталога ).
Роликоопора предназначена для поддержания нижней нерабочей ветви ленты. Крепится роликоопора снизу к секции средней части конвейера.
8. Очистные устройства.
Транспортируемый ленточным конвейером груз из-за целого ряда причин (схода ленты вибрации ленты и др.) просыпается на настил секций металлоконструкций средней части конвейера нижнюю ветвь ленты и пол. То же самое происходит после разгрузки конвейера когда частицы груза прилипают к рабочей поверхности нижней ветви ленты и по мере ее движения по роликам отделяются от ленты. На барабанах и роликах роликоопор конвейера образуется налипание груза которое тем больше чем более влажный и липкий груз. Налипание груза уменьшается при футеровке ( покрытии ) барабанов и роликов резиной. Груз налипший на ленту барабаны и ролики роликоопор резко снижает срок службы ленты ухудшает устойчивость хода ленты увеличивает динамические нагрузки от нарушения балансировки роликов роликоопор увеличивает запыленность помещений и др. Очистка ленты и оборудования от налипшего груза а также уборка просыпи требуют установки очистных устройств (очистителей) технических средств и приспособлений для уборки просыпи и пыли. Очистные устройства крепятся к опорным металлоконструкциям.
8.1. Устройства для очистки ленты.
Очистители ( скребки ) для очистки рабочей стороны ленты после разгрузки конвейера могут быть одинарными и двойными. С учетом заводской комплектации выбираем одинарный скребок для очистки конвейерной ленты В = 800 мм : скребок для очистки ленты «В - 800 ».
Усилие прижатия скребка к ленте не должно превышать 2 Нсм
длины контактной кромки.
Плужковое очистное устройство устанавливаем перед натяжным барабаном на нерабочей стороне нижней ветви ленты для очистки ее от попадаемых частиц транспортируемого груза. Для конвейера с шириной ленты В = 800 мм выбираем: устройство очистное плужковое «В - 800».
8.2. Устройства для очистки барабанов.
Для очистки приводных и неприводных барабанов применяют очистители. Выбираем при ширине ленты В = 800 мм для приводного барабана : очиститель приводного барабана « 8063 - 100 »
9 Расчёт вала приводного барабана на прочность
Расчёт вала приводного барабана на прочность выполним с помощью программы APM WinMachine.
Исходные данные необходимые для расчёта сведены в таблице 8.
Конструкционная (прокат)
Параметры материала:
Коэффициент Пуассона
Предел прочности по растяжению
Предел текучести сдвига
Усталостная прочность по нормальным напряжениям
Усталостная прочность по касательным напряжениям
Продальная сила от приводного барабана:
Крутящий момент от редуктора:
Полученные результаты приведены на рисунках
Автоматизация управления ленточного конвейера.
1. Задачи электрооборудования и систем управления
1.1. Основные термины и определения
Определение электрического привода как технического устройства дано в ГОСТ 16593-79 «Электроприводы. Термины и определения».
Электрическим приводом называется электромеханическое устройство предназначенное для приведения в движение рабочих органов машин и управления их технологическими процессами состоящее из передаточного устройства электродвигательного устройства преобразовательного устройства и управляющего устройства.
Передаточное устройство содержит механические передачи и соединительные муфты необходимые для передачи вырабатываемой двигателем механической энергии исполнительному механизму.
Преобразовательное устройство предназначается для управления потоком электрической энергии поступающим из сети с целью регулирования режимов работы двигателя и механизма. Оно представляет собой энергетическую исполнительную часть системы управления электроприводом.
Управляющее устройство – информационная слаботочная часть системы управления предназначенная для фиксации и обработки поступающей информации о задающих воздействиях и состоянии системы и выработки на ее основе сигналов управления преобразовательным электродвигательным и передаточным устройствами.
Современный электропривод является индивидуальным автоматизированным электроприводом. Это означает что он всегда содержит в своем составе систему автоматического управления (САУ) которая в простейших случаях осуществляет пуск отключение двигателя и его защиту а в более сложных случаях управляет технологическим процессом приводимого в движение механизма. Указанные особенности автоматизированного электропривода определяют характерную тенденцию в развитии современного машиностроения – упрощение кинематических цепей машин при усложнении и совершенствовании управления их электроприводами.
2. Назначение электрооборудования и систем управления
Внедрение подъемно-транспортных строительных и дорожных машин и оборудования в технологические процессы производства вызывает необходимость повышения их производительности и надежности работы. ПТМ СДМ часто определяют режим работы основных машин поэтому без автоматизации управления ими и повышения рабочих скоростей при сохранении точности остановки механизмов и плавности переходных процессов нельзя добиться повышения производительности.
Вне зависимости от назначения и степени автоматизации ПТМ СДМ электрооборудование (ЭО) и системы управления (СУ) должны обеспечить:
необходимую плавность разгона привода;
перемещение рабочих органов (грузов) со скоростью достаточной для заданной производительности;
постоянные скорости отдельных приводов механизмов;
предотвращение и выравнивание перекосов металлоконструкций и перегрузки канатов;
точную остановку механизмов в пределах заданной погрешности;
защиту ПТМ СДМ в рабочей зоне от перегрузки и опрокидывания;
контроль и диагностирование оборудования по основным параметрам с блокировкой рабочих органов при достижении критических значений параметров.
Автоматическое управление ПТМ СДМ и системы реализующие это управление должны решать следующие задачи:
создание оптимальных силовых воздействий при неустановившихся режимах: пуске торможении регулировании скорости с заданными ограничениями перегрузок ускорений колебаний груза с сохранением заданной производительности;
выполнение технологических операций в заданной последовательности с оптимальной взаимосвязью;
создание оптимальной тахограммы перемещения механизмов для грузовых и холостых операций и обеспечения точной остановки;
корректирование и поддержание устойчивости процессов управления и регулирования систем электропривода с помощью внутренних и внешних обратных связей;
автоматическое перераспределение нагрузок;
автоматическое выполнение функций защиты привода механизмов и всего сооружения ( ограничение перекосов перегрузки двигателей и механизмов блокировки механизмов исключение возможности длительной работы в режимах перегрузки опрокидывания и т.п.);
адресование грузов тележки кранов в пункты заданные программой или единичной командой;
контроль и дигностирование агрегатов ПТМ СДМ.
3. Состав электрооборудования и систем управления
Оборудование ПТМ СДМ электрическим приводом предполагает оснащение каждого рабочего механизма (РМ) ПТМ СДМ некоторым определенным набором электромеханических устройств совокупность которых называется электрооборудование и системой управления ПТМ СДМ.
Электрооборудование отдельных РМ в ПТМ СДМ выполняется всегда по одной и той же схеме индивидуального автоматизированного электропривода (ЭП) предназначенного для перемещения груза в пространстве в заданном направлении. Другими словами в основе электрооборудования и СУ ПТМ СДМ лежит система ЭП ПТМ СДМ в которой выполняется главная функция ЭП – преобразование электрической энергии в механическую.
Для математического описания процесса преобразования используются параметры функционирования этой системы и учитываются показатели требуемых режимов ее работы. В электрической части системы такими параметрами являются напряжение U и ток I а в механической – момент инерции J крутящий момент М угловая скорость вращения угловое ускорение s и передаточное отношение редуктора i. Основной показатель качества работы системы – коэффициент полезного действия (КПД) – должен иметь достаточно высокие значения при заданном диапазоне регулирования скорости D и требуемой продолжительности включения ПВ %.
Для электродвигателя (ЭД) переменного тока в преобразовательных устройствах (ПрУ) осуществляют при необходимости изменение величины питающего напряжения U или частоты питающего тока I для ЭД постоянного тока – выпрямление переменного тока в постоянный.
Главная функция ЭП реализуется в электродвигательном устройстве ЭД в качестве которого используют электродвигатели постоянного или переменного тока. ЭД преобразуют электрическую мощность в механическую и передает ее на входной вал передаточного устройства (ПУ).
Управление процессом преобразования энергии в ЭП ПТМ СДМ имеет своей целью реализацию заданной диаграммы скорости движения РМ и осуществляется в управляющем устройстве (УУ).
В зависимости от сложности заданной диаграммы скорости и требуемого режима работы в УУ используется система управления ЭП которая реализует тот или иной способ управления так чтобы при воздействии на параметры управления были достигнуты необходимые показатели качества управления.
Основным параметром системы управления является ток ЭД и пропорциональный ему вращающий момент М. В зависимости от соотношения вращающего момента М поступающего с выходного вала ПУ на РМ и статического момента Мс который создает груз на устройстве РМ формируется нагрузочная диаграмма ЭП. На этапе проектирования ЭП анализ Д (нагрузочной диаграммы позволяет осуществить правильный выбор ЭД и системы управления. Такой анализ проводят на основании сравнения характеристик различных ЭД и характеристик РМ в статических и динамических режимах работы. Характеристики ЭД РМ в статических режимах называются механическими.
Источником механической энергии Д ( силовой установкой ) на большинстве ПТМ СДМ служат тепловые ( дизельные ) или электрические двигатели как наиболее экономичные. Они преобразуют энергию тепловую или электрическую в энергию механическую передаваемую рабочему механизму РМ. Такие двигатели принято называть первичными. В зависимости от типа применяемого основного двигателя различают ПТМ СДМ как дизельного так и электрического двигателя. Для работы в районах не имеющих электроэнергии применяют комбинированную силовую установку: дизель-электрический агрегат. Дизель вращает генератор переменного тока от которого получает электроэнергию двигатель преобразовательного агрегата. Такая дизель-генераторная установка обеспечивает автономное энергопитание ПТМ СДМ.
Передаточное устройство (ПУ) предназначено для передачи энергии (движения) от двигателя Д к рабочим механизмам которые осуществляют движение элементов рабочего оборудования и другие функции.
Одним из видов передаточного устройства является устройство где движение передается от основного двигателя к рабочим механизмам с помощью валов муфт зубчатых шестерен цепных канатных и шестеренчато-реечных передач. При этом они не только передают движение и усилие но и преобразовывают один вид движения в другой а также при необходимости изменяют направление и частоту вращения механизма и останавливают с помощью тормоза. Такая передача где транспортирование энергии осуществляется за счет взаимодействия твердых тел называется механической силовой передачей или механической трансмиссией. По типу такой в целом ПТМ СДМ называется механическим.
Комплекс элементов состоящий из электродвигателя передаточного механизма (ПУ) и электроаппаратуры устройства управления (УУ) назвают обобщенно электроприводом.
Другой вид передачи наиболее распространен из-за простоты транспортирования энергии. При этом генератором механическая энергия вращения электродвигателя преобразуется в электрическую передаваемую по проводам к исполнительному двигателю а затем исполнительным двигателем из электрической снова преобразуется в механическую энергию и поступает на рабочий механизм. Такая передача энергии называется электрической.
Если первичный двигатель – дизель (Д) работает с синхронным генератором переменного тока (СГ) то силовая установка называется комбинированной дизель-генераторной ( или дизель-электрической ). Силовую установку из дизель-генераторной группы называют силовым преобразовательным агрегатом поскольку в нем производится преобразование электроэнергии переменного тока в постоянный ток генератора. В последние годы вместо такого электромашинного преобразователя тока в образцах ПТМ СДМ применяют статические преобразователи-тиристоры в сочетании с магнитными усилителями.
В электроприводе с системой «генератор-дизель» управляющее воздействие оказывают на генератор а основной двигатель служит только для вращения генератора.
Управляющее устройство ( или система управления ) – это комплекс устройств управляющих поступлением энергии рабочим механизмам - ее распределением между ними и регулированием их скорости движения а также предохраняющих конструкции ПТМСДМ от недопустимых перегрузок. В простейшем электроприводе управляющими устройствами являются автоматические выключатели контакторы пускатели для подключения и отключения двигателя от питающей сети. В сложных электроприводах управляющие устройства содержат магнитные усилители полупроводниковую и прочую аппаратуру и представляют собой как правило замкнутую систему автоматического регулирования (САР).
На механических (дизельных) ПТМ СДМ применяют электрическую силовую систему для пуска дизельных двигателей и системы освещения отопления вентиляции и сигнализации. Схема электропроводки обычно однопроводная в ней минусовым проводом служит металлический корпус
( металлические части) самой машины. На электрических ПТМ СДМ перемещение рабочих органов осуществляется с помощью электроприводов обычно питаемых трехфазным напряжением промышленной частоты от внешнего источника или дизель-генератора. Как на дизельных так и на электрических машины сегодня применяют электронные системы управления.
4. Электрооборудование конвейеров
Конвейеры транспортеры – это машины непрерывного действия для перемещения сыпучих кусковых или штучных грузов.
Конвейеры являются составной неотъемлемой частью современного технологического процесса. Они устанавливают и регулируют темп производства обеспечивают его ритмичность способствуют повышению производительности труда и увеличению выпуска продукции. Тесная связь транспортирующих машин с общим технологическим процессом производства обусловливает высокую ответственность их работы и назначения. Поэтому конвейеры должны быть надежными прочными удобными в эксплуатации и способными работать в автоматических режимах.
Конвейеры в зависимости от их назначения и области применения могут эксплуатироваться в самых разнообразных условиях в том числе крайне неблагоприятных. Это определяет необходимость использования для данной группы механизмов электрооборудования по типу и исполнению отвечающего условиям эксплуатации и выдвигает жесткие требования к безопасности и простоте его обслуживания и надежности работы. Это в первую очередь относится к приводным двигателям которые как правило должны иметь закрытое исполнение и обладать повышенным пусковым моментом.
Привод устанавливается в конце рабочего участка. Это позволяет разгрузить последующую холостую ветвь конвейера от больших натяжений рабочего участка. Привод конвейера может иметь один два или три отдельных электродвигателя. Два двигателя устанавливают на один приводной вал при использовании редукторов меньшей мощности ( вместо одного большого ) и для более компактной планировки привода. Три двигателя применяют в двухбарабанном приводе ленточного конвейера.
5. Средства автоматизации и безопасности ленточных конвейеров.
Продолжительная и надежная работа ленточных конвейеров а также безопасное их обслуживание в значительной мере зависит от уровня автоматизации и наличия средств техники безопасности. Основными причинами выхода из строя конвейеров и связанного с ним оборудования является попадание в них металлических предметов которые вызывают порывы и порезы ленты сход ленты а следовательно увеличения просыпи забивку загрузочных и разгрузочных устройств и др.
Различают выключающие устройства автоматические и ручные
(к саморегулирующим устройствам для поддержания ленты в рабочем состоянии относятся центрирующие роликоопоры и дефлекторные ролики). Автоматические выключающие устройства в свою очередь различаются на рычажные и датчики скорости.
5.1. Устройства выключающие рычажные.
Выключающие рычажные устройства устанавливаются на металлоконструкцию средней части конвейера для отключения привода при аварийном сходе ленты. При длине конвейера до 50 м устанавливают два устройства в головной части. В нашем случае при длине конвейера 1094 м. и ширине ленты В=800 мм. выбираем: устройство выключающее рычажное «В - 800 » - 6 шт.
5.2.Устройства выключающие канатные.
Выключающие канатные устройства применяются для ручной остановки
конвейера по всей его длине со стороны прохода для обслуживания. В тех
случаях когда вдоль конвейера имеются проходы с двух сторон эти устройства устанавливают с обеих сторон.
Длина каната одного устройства 70 м устройство следует устанавливать при длине конвейера более 10 м. Выключающее канатное устройство может использоваться для блокировки привода с укрытиями и ограждениями барабанов и натяжных устройств что сокращает число устанавливаемых выключателей . Для рассчитываемого конвейера выбираем: устройство выключающее
канатное « ВК - 55x2 П(Л) » - 2 шт.
5.3. Устройства от продольного пореза ленты.
С целью предотвращения продольного пореза ленты посторонними
предметами попадающими на нее при загрузке конвейера устанавливается выключающее устройство от продольного пореза ленты. Устройство поставляется комплектно на раме вместе с роликоопорами.
Для конвейера с шириной ленты В=800 мм и роликоопорой
ЖА 80-127-30 выбираем: устройство от продольного пореза ленты
« ЖА 80 - 1 27 - 30 ».
5.4 Устройства для промежуточной разгрузки конвейеров.
К устройствам обеспечивающим промежуточную разгрузку конвейера относятся барабанные разгрузочные тележки и сбрасывающие плужки.
Разгрузочные тележки позволяют осуществить разгрузку горизонтального
участка конвейера в любом его месте.
Разгрузочная воронка тележки может иметь конструкцию которая позволяет сбрасывать груз с ленты на две стороны и вперед (в любом сочетании).
Разгрузочная тележка передвигается по рельсам устанавливаемым на специальной конструкции - треке который одновременно является и средней частью конвейера с закрепленными на ней роликами.
Согласно наибольшему натяжению ленты Smах=179572 Н и ширине лен-
ты конвейера В=800 мм. по табл. 55 на стр. 116 каталога выбираем тип разгрузочной тележки - «Б-8050-П-II-127» с разгрузкой на две стороны
исполнением воронки - II и правым расположением привода.
5.5.Контроль мест перегрузки
В местах передачи грузов с одного конвейера на другой часто возникают завалы которые ведут к сбрасыванию грузов с конвейераи повреждению последних. Применяется ряд конструкций сигнализаторов завалов перегрузочных пунктов. При переполнении перегрузочного желоба материал отклоняет подвижный элемент датчика который отключает двигатель подающего конвейра.
На чертеже 10 показано механическое устройство контроля мест перегрузки с подвижным бортом. Груз с конвейера 1 поступает на конвейер 3 через погрузочный лоток 2. Левый борт 4 лотка установлен
Шарнирно и удерживается в рабочем положении пружиной 7. При переполнении лотка шарнир борт отклоняется влево и толкателем 6 размывает контактную группу SМП конечного выключателя 5 который через реле времени КПМ исключающие ложные срабатывание устройства случайном отклонении борта падающим грузом отключает пускатель подающего конвейера или всю линию. В современных схемах широкое применение находят электронные и изотопные датчики.
5.6 Контроль схода ленты
Для контроля схода лент и отключения конвейеров при отклонении ленты используется аппарат (чертеж 10) состоящий из двух конечных выключателей 1 (SЛ1 и SЛ2) рычагов 2 и контролирующих роликов 3. Ролик в нормальном состоянии перекатывается по не рабочей стороне ленты 4. При отсутствии ленты над роликом рычаг под действием груза 5 поворачивается и переключает контакты выключателей SЛ. При этом размыкается цепь катушки КЛ который отключает пускатель конвейера или всю линию. Аппарат контролирует сход ленты обе стороны
Технологическая часть
1. Изготовление вала приводного барабана
1.1. Анализ технологических требований к конструкции детали
Рисунок 8.2. Компоновочная схема узла.
– 1-ая ступень вала; 2 – 2-ая ступень вала; 3 – 3-я ступень вала;
– 4-ая ступень вала; 5 – 5-ая ступень вала; 6 – 6-я ступень вала;
– 7-я ступень вала; 8 – 8-я ступень вала;
– МУВП (на рисунке указана полумуфта);
12 15 – манжетное уплотнение; 11 16 – подшипники;
14 – приводной барабан.
Первая и седьмая ступени диаметром 85 мм и длиной 40 мм обрабатываются с допуском k6 предназначены для посадки подшипника шероховатость Rа = 063 мкм.
Вторая и шестая ступени диаметром 90 мм и длиной 330 мм имеют фаску 25 х 45° являются посадочной поверхностью под уплотнение манжетное резиновое армированное. Поверхности обрабатываются с допуском d11 и шероховатостью Ra = 032 мкм.
Третья и пятая ступени диаметром 100 мм и длиной 200 мм обрабатываются с допуском f6 имеют шпоночные пазы 25х9х170 для посадки ребер жесткости барабана и отверстия под винт.
Четвертая ступень диаметром 95 мм и длиной 400 мм специально не обрабатывается
Восьмая ступень диаметром 80 мм и длиной 170 мм имеет шпоночный паз 25х9х105 для установки полумуфты МУВП также имеет фаску 25 х 45°. Обрабатывается с допуском f6 и шероховатостью Rа = 1.25 мкм. Фаски не являются рабочими поэтому точность и шероховатость обеспечивается инструментом.
В качестве конструкционных баз выбираем поверхности 3 и 6 так как эти поверхности детали соприкасаются с подшипником и определяют своё положение в сборочной единице.
Для шпоночных пазов назначаем шероховатость для боковых поверхностей Ra = 32.
Необходимо при изготовлении детали выдерживать допуски формы и расположения.
Допуск цилиндричности (см. табл. 24.2 [7])
- для поверхностей 1 и 4 (100 f6)
Тo=05 .22=11 мкм. Принимаем Тo=001 мм. (8.1)
- для поверхностей 3 и 6 (80 k6)
Тo=05 .22=11 мкм. Принимаем Тo=001 мм (8.2)
- для поверхности 3 и 6 (80 k6)
Т=01 .В1 .ТТабл (см. табл. 22.5 [9]) (8.3)
Т=01 .25 .6=15 мкм. Принимаем Т=002 мм.
Допуск перпендикулярности упорного буртика под подшипник
- для шарикового – степень точности допуска 8 (см. табл. 22.4 [7]). Т=003 мм (см. табл. 22.8 [7]). (8.4)
Допуски параллельности и симметричности шпоночного паза для посадки ребра жесткости
Т=05 .tшп=05·52=26 мкм. Принимаем Т=003 мм; (8.5)
мкм. Принимаем мм. (8.6)
Допуски параллельности и симметричности шпоночных пазов определяем в соответствии с рекомендациями книги [1стр. 394 табл. 224]
Т = 05 tшп Т = 2 tшп (8.7)
где: tшп – допуск ширины шпоночного паза.
Т = 05 tшп Т = 2 tшп (8.8)
где tшп – допуск ширины шпоночного паза.
Для шпоночного паза 25Р9 – tшп=0043 мм согласно [1стр. 452 табл. 242]: (8.9)
Принимаем Т = 003 и Т = 01 соответственно.
1.2. Обоснование способов изготовления конструктивных элементов детали
Главным при выборе заготовки является: вид изделия объём выпуска и тип производства. Вид изделия определяет главные конструктивные и технологические признаки; объём выпуска и тип производства определяют степень технологического оснащения механизации и автоматизации технологических процессов и специализации.
Деталь изготовляется в условиях единичного производства из стали 45 ГОСТ 1050-88 твёрдостью 280 НВ. В качестве заготовки согласно ГОСТ 2590-88 выбираем круглый сортовой прокат.
Способы изготовления конструктивных элементов зависят от толщины срезаемого слоя металла величины допуска и шероховатости.
Для обрезки заготовки в размер L=1710 мм и для формирования профиля вала применим токарный станок 16К20.
Поверхности 3 и 5 (100f6) – посадочное место под приводной барабан. Из требований к шероховатости согласно [1стр. 386 табл. 222] и получения точности размера по квалитету 6 применяется окончательное шлифование. Снимаем фаску 25х45º резцом Т15к6 с углом в плане 45º. Фрезеруем концевой фрезой шпоночный паз длиной 170 мм. Радиус закругления резца с углом в плане 90º при получистовом обтачивании обеспечивает галтель радиусом 2мм.
Поверхности 2 и 6 (90d11) – посадочное место под уплотнение. Из требований к шероховатости согласно [1] и получения точности размера по квалитету 11 применяется окончательное шлифование после чего производится полировка. Радиус закругления резца с углом в плане 90º при получистовом обтачивании обеспечивает галтель радиусом 2мм.
Поверхность 4(95h14) с квалитетом h14 не будет использоваться в качестве технологической базы так как она не является рабочей. Rz= 80 метод обработки – токарная (черновое обтачивание). Радиус закругления резца с углом в плане 90º при получистовом обтачивании обеспечивает галтель радиусом 2мм..
Поверхности 1 и 7 (85k6) – посадочное место под подшипник. Из требований к шероховатости согласно [1стр. 386 табл. 222] и получения точности размера по квалитету 6 применяется окончательное шлифование. Снимаем фаску 25х45º резцом Т15к6 с углом в плане 45º.
Галтели и фаски получаем точением на токарном станке. Торцы вала подрезаются «начисто». Обработка нерабочих поверхностей вала – обтачивание черновое.
и 7 ступени: 85k6 финишная обработка – окончательное шлифование;
и 6 ступени: 90d11 финишная обработка – окончательное шлифование;
и 5 ступени: 100f6 финишная обработка – окончательное шлифование;
ступень:95h14 финишная обработка – черновое обтачивание;
ступень: 80f6 финишная обработка – окончательное шлифование и полирование;
1.3. Выбор способа установки детали на технологических операциях
Средний диаметр заготовки по формуле:
гдеn – число конструктивных элементов;
Определяем технологическую жёсткость по формуле:
Т.к. то применяем установку в центрах с люнетом. Для обработки детали в центрах необходимо выбрать вид и типоразмер центровых отверстий.
В соответствии с [2] принимаем центровые отверстия типа В ГОСТ 14034-74 – рисунок 2. Такие центровые отверстия являются базой для многократного использования и сохраняются в готовых изделиях.
Рис.1 Центровое отверстие.
Исходя из максимального диаметра вала 100 мм выбираем центровые отверстия с защитной фаской В 63 ГОСТ 14034-74 размерами L = 128 мм и d= 10 мм. С углами фасок 600 (для рабочей) и 120º (для защитной).
1.4. Выбор вида и размеров заготовки для детали
При максимальном диаметре детали 100 мм и отношении диаметр заготовки составляет 105 мм и длина 1705 мм (ГОСТ 2590-71). Из сортамента выпускаемого круглого проката выбираем в качестве заготовки сталь горячекатаную круглую обычной точности прокатки (В).
При диаметре заготовки 105 мм верхнее отклонение мм и нижнее отклонение мм допуск на заготовку составит мм что соответствует 16 квалитету (см. табл. 62 стр. 169 [8]).
– припуск на торцевую обработку детали.
1.5. Составление укрупнённого маршрута изготовления детали
Отрезать заготовку от проката круглого сечения обычной степени точности 105(+04-17)мм длиной 1715 мм.
0 Всю деталь подвергнуть термообработке - нормализации.
Изготавливаем центровые отверстия;
Изготавливаем канавку под люнет;
Черновая токарная обработка одной стороны заготовки;
Обрабатываем черновой токарной обработкой другую сторону;
Получистовая обработка этого конца детали;
Получистовая обработка другого конца вала;
Предварительно шлифовать заготовку с одной стороны заготовки;
Окончательно шлифовать заготовку с той же стороны;
Предварительно шлифовать заготовку с другой стороны заготовки;
Окончательно шлифовать заготовку с другой стороны заготовки;
Фрезерование шпоночных пазов.
0 Отделочная операция
Полировка поверхностей 2 и 6 вала с шероховатостью .
Проверить точность изготовления деталей по чертежам.
2. Разработка операций по формированию наружной поверхности детали
2.1. Расчёт числа переходов механической обработки числа стадий и достижений точности конструктивного элемента
Расчет каждой ступени вала выполним по следующим формулам:
Ужесточение точности:
Число стадий обработки:
- коэффициент ужесточения точности.
Все полученные в результате расчёта значения сведены в таблице 6
Расчёт количества переходов обработки резанием
Коэффициент ужесточения точности
Расчётное значение количества переходов
Принятое значение количества переходов
прокат круглый сталь 45 38 +05-1.1
2.2. Определение точности промежуточных размеров заготовки по стадиям механической обработки
Определим точность заготовки по каждой стадии механической обработки для каждой поверхности. При расчете используется принцип убывающей арифметической прогрессии. Расчеты выполнены в табличном виде (таблица 6.1.).
Определение квалитетов промежуточных размеров
Для поверхностей 3 и 5 (100f6) 1 и 7 (85k6) 8 (80f6)
Для поверхностей 2 и 6 (90d11)
Для поверхности 4 (95h14)
2.3. Расчет промежуточных размеров по стадиям механической обработки
При выборе припусков на обрабатываемые поверхности будем отталкиваться от принятых в практике примерных процентных отношений между общим припуском и припуском на черновую получистовую чистовую и окончательную обработки выбираемых из таблицы [3].
Исходя из этого условия и анализа требований к точности и шероховатости обрабатываемых поверхностей для удобства все данные сведём в таблицу. Так как тип производства единичный то припуски по стадиям обработки 2Ziтабл берутся согласно [3 с. 184 табл. 27].Расчёт производим по формуле:
где - размер на предшествующем переходе;
- размер на текущем переходе;
- табличное значение припуска на текущую обработку.
Результат расчёта сводим в таблицу 8.3. Значение шероховатости для каждого технологического перехода принимаем согласно [2 с. 359 табл. 41].
Промежуточные размеры заготовки
За исходный размер берем максимальный диаметр 99964 мм
Предельное отклонение
Шлифование окончательное
Шлифование предварительное
Получистовое точение
Продолжение табл. 8.2.
За исходный размер берем максимальный диаметр 8988 мм
За исходный размер берем максимальный диаметр 95 мм
За исходный размер берем максимальный диаметр 85025 мм
Выбираем из сортамента мм мм и получаем небольшой слой срезаемого лишнего металла что экономически выгодно при нашей технологии.
3 Составление плана токарной и шлифовальной обработок детали
Расчёт выполним исходя из характеристик станка 16К20:
Мощность электродвигателя главного движения вращения шпинделя:
Максимальный диаметр заготовки:. . . . . . . . . . . . . . . . . . . . . . . . 400 мм;
Максимальный диаметр закрепляемой детали в трёхкулачковом патроне:.190 мм;
Диаметр центрового отверстия в шпинделе станка для пропуска проката: 58 мм
Максимальная длина заготовки: . 1400мм.
Частота вращения шпинделя: 125; 16; 20; 25; 315; 40; 56; 63; 80; 100; 125; 160; 200; 250; 315; 400; 500; 630; 860; 1000; 1250; 1600 мин-1.
Продольная подача суппорта резца Sпродол: 005; 006; 0075; 009; 01; 0125; 015; 0175; 02; 025; 03; 035; 04; 05; 06; 07; 08; 1; 12; 14; 16; 22; 28 ммоб.
Поперечная подача: .Sпопер. = 05 Sпродол.
Глубину резания для технологического перехода рассчитываем по формуле:
и сравниваем полученное значение с предельно допустимым для данного диаметра:
-если то переход возможен
-если то переход невозможен.
Согласно [4] значение . (8.22)
Так как Кж=7678 то в дальнейших расчётах принимаем значение что находится в рекомендуемых пределах.
Выполним также анализ допустимой глубины резания исходя из ограничения по мощности резания.
В нормах [4 стр.266 табл. 11] приведены ориентировочные значения мощности резания в соответствии с глубиной резания и подачей .
5 токарно-винторезная.
Установ А (торцевание центрование заготовки)
Установить закрепить снять заготовку.
Подрезать торец «как чисто».
Сверлить центровое отверстие по условиям эскиза.
Установ Б (торцевание центрование заготовки)
Переустановить закрепить снять заготовку.
Подрезать торец справа с соблюдением размера длины детали – 2000 мм.
Проточить канавку под люнет.
Установ В (черновое обтачивание)
Следовательно переход возможен. Уточним по мощности резания
Исходя из ограничений по мощности выбираем глубину резания 21мм. Согласно [4 с. 266 табл. 11] выбираем подачу 05 ммоб согласно [7 с. 27 табл. 12] выбираем мощность 59 кВт.
Таким образом 1 технологический переход выполним до мм
Исходя из ограничений по мощности выбираем глубину резания 5 мм. Согласно [4 с. 266 табл. 11] выбираем подачу 05 ммоб согласно [7 с. 27 табл. 12] выбираем мощность 92 кВт.
Таким образом 2 технологический переход выполним до 9048 мм.
Найдём глубины резания.
Точение черновое t1=(D-d)2=(9048-85685+)2=24 мм (8.26)
Исходя из ограничений по мощности выбираем глубину резания 24 мм. Согласно [4 с. 266 табл. 11] выбираем подачу 05 ммоб согласно [7 с. 27 табл. 12] выбираем мощность 59кВт.
Таким образом 4 технологический переход выполним до 85685 мм.
Точение черновое t1=(D-d)2=(85685-80685+)2=25 мм (8.27)
Исходя из ограничений по мощности выбираем глубину резания 25 мм. Согласно [4 с. 266 табл. 11] выбираем подачу 05 ммоб согласно [7 с. 27 табл. 12] выбираем мощность 59кВт.
Таким образом 4 технологический переход выполним до 80685 мм.
План обработки на установ В(черновое обтачивание) имеет вид:
Установить закрепить и снять заготовку.
Точить заготовку начерно в размер 1 обеспечивая размер 6.
Точить заготовку начерно в размер 2 обеспечивая размер 7.
Точить заготовку начерно в размер 3 обеспечивая размер 8.
Точить заготовку начерно в размер 4 обеспечивая размер 9.
Точить заготовку начерно в размер 5 обеспечивая размер 10.
Установ Г (черновое обтачивание)
Точение черновое t1=(D-d)2=(85685-80685+)2=25 мм (8.31)
План обработки на установ Г(черновое обтачивание) имеет вид:
Переустановить заготовку.
Точить начерно в размер 1 обеспечивая размер 2.
Точить начерно в размер 3 обеспечивая размер 4.
Точить начерно в размер 5 обеспечивая размер 6.
Точить начерно в размер 7 обеспечивая размер 8.
Установ Г (получистовое обтачивание)
Точить фаски в размеры 7 8 9.
Установ Д (получистовое обтачивание)
Точить начерно в размер 1 обеспечивая размер 5.
Точить начерно в размер 2 обеспечивая размер 6.
Точить начерно в размер 3 обеспечивая размер 7.
Точить начерно в размер 4 обеспечивая размер 8.
Точить фаски в размеры 9 10 11.
0 круглошлифовальная.
Установ Д (шлифование предварительное окончательное)
Шлифовать предварительно поверхность в размер 1 и 3
и 5 6 и 8 9 и 11 12 и 13 14 и 16 .
Шлифовать окончательно поверхность в размер 2 и 3
и 8 10 и 11 15 и 16 .
Установ А (шлифование предварительное окончательное)
Шлифовать предварительно поверхность в размер 1 и 3.
Шлифовать окончательно поверхность в размер 2 и 3.
4 Выбор и расчёт режимов резани
5 токарно-винторезная
Расчёт режимов резания осуществляется для конкретных переходов в последовательности установленной планом токарной обработки.
Согласно [2 стр. 614 табл. 2] выбираем резец Т15К6 из твердого сплава.
Расчёт выполняем в следующей последовательности:
Определим скорость резания
где Cv - коэффициент скорости зависящий от значения величины подачи.
Согласно [4 табл.17 стр.269] для материала режущей части резца Т15К6 и подачи 03s07 принимаем Cv=350;
x y m - показатели степени.
Согласно [4 табл.17 стр.269] для материала режущей части резца Т15К6 и подачи 03s07 принимаем y=035; m=020;
Т – расчётная стойкость резца в минуту. Принимаем согласно [4 стр.268];
t – глубина резания;
-для чернового обтачивания принимаем значение глубины резания из пункта 8.7.
-для получистового обтачивания: . (8.33)
-для чернового обтачивания принимаем значение подачи из пункта 8.7.
-для получистового обтачивания: (8.34)
где Ks - коэффициент корректировки подачи. Согласно [4 стр.271] принимаем Ks = 08;
- табличное значение подачи. Согласно [4 табл.14 стр.268] принимаем .
ммоб. Принимаем s = 07 ммоб. (8.35)
Kv – поправочный коэффициент
где - коэффициент учитывающий материал заготовки.
Согласно [4 табл.1 стр.261] (8.37)
где КГ - коэффициент характеризующий группу стали по обрабатываемости.
Согласно [4 табл.2 стр.262] при =650мПа>550мПа принимаем Кг=10;
- временное сопротивление.
Согласно [4 табл.2 стр.262] принимаем =650мПа;
nv – показатель степени.
Согласно [4 табл.2 стр.262] при обработке резцами из твёрдого сплава принимаем nv=1.
– коэффициент учитывающий влияние состояния поверхности заготовки на скорость резания.
Согласно [4 табл.5 стр.263] при состоянии поверхности заготовки:
-прокат с коркой принимаем КПv=09;
-без корки принимаем КПv=1;
– коэффициент учитывающий качество материала инструмента.
Согласно [4 табл.6 стр.263] для марки инструментального материала Т15К6 принимаем КИv=1;
- коэффициент учитывающий главный угол в плане.
Согласно [4 табл.18 стр.271] при главном угле резца в плане φ=45 принимаем Кφv=1.
Определим частоту вращения:
Полученное значение принимаем согласно частоте вращения шпинделя.
Все полученные значения сведены в таблице 8.4.
Расчётные значения режимов резанья Таблице 8.4.
Диаметр поверхности мм
- Установ В (черновое обтачивание)
- Установ Г (черновое обтачивание)
- Установ Г (получистовое обтачивание)
- Установ Д (получистовое обтачивание)
Для обеспечения при предварительном и окончательном шлифовании параметров шероховатости Ra 08 125 термически обработанной стали выбираем шлифовальный круг прямого профиля размерами:
Следующего обозначения ПП-24А-40Н-М2-5-К8-А [5].
Где: ПП – прямого профиля;
А – белый электрокорунд;
– зернистость абразива;
Н – структура зернистости;
М2 – степень твердости;
К8 – керамическая связка (8-для электрокорунд);
А – степень точности.
Расчёт режимов шлифования выполним исходя из характеристик шлифовального станка 3Б151:
Наибольший диаметр и длина шлифуемой поверхности – мм;
Диаметр и толщина шлифовального круга – 600мм и 63мм;
Частота вращения детали – 63 400 (регулирование бесступенчатое);
Скорость продольного перемещения рабочего стола - 01 6 ммин (регулирование бесступенчатое);
Поперечная подача шлифовального круга – 00025 005 мм за 1 ход рабочего стола с шагом 00025 мм;
Дискретные значения подач шлифовального круга
Непрерывная подача шлифовального круга при врезном шлифовании – 01 2 мммин (00005 001 ммоб.); (8.39)
Мощность электродвигателя привода шлифовального круга – 7кВт.
Предварительное и окончательное шлифование.
Согласно [4 табл.55 стр.301] назначаем следующий режим шлифования:
Скорость вращения шлифовального круга Vшл.кр. = 30мс;
Скорость вращения заготовки:
- для предварительного шлифования Vзаг = 12ммин;
- для окончательного шлифования Vзаг = 15ммин
Подача шлифовального круга:
- для предварительного шлифования s = (03 07) Вшл.кр. = (03 07)·63=189 441 ммоб. (8.40)
Принимаем s = 20 ммоб;
- для окончательного шлифования s = (02 04) Вшл.кр. = (02 04)·63=126 255 ммоб. (8.41)
Принимаем s = 14 ммоб;
Глубина шлифования:
- для предварительного шлифования мм; (8.42)
- для окончательного шлифования мм. (8.43)
Так как за один проход согласно [4 табл.55 стр.301] снимается:
- для предварительного шлифования мм то необходимое число рабочих ходов шлифовального круга:
- для окончательного шлифования мм то необходимое число рабочих ходов шлифовального круга:
Частота вращения заготовки
Частота вращения шлифовального круга
Проверка шлифовального станка по мощности:
где - поправочный коэффициент и показатели степени.
Согласно [4 табл.56 стр.303] круглого наружного шлифования с поперечной подачей принимаем CN=26; n=05; y=055; q=0. С использованием шлифовального круга с зернистостью 40 – 50 и твердостью СМ1 – СМ2.
Если условие N[N]=7 кВт выполняется то проверка выполнена.
Все полученные значения сведены в таблице 8.6.
Расчётные значения режимов шлифования таблице 8.6.
Установ Д- предварительное шлифование
окончательное шлифование
Установ А- окончательное шлифование
- окончательное шлифование
В ходе дипломной работы был разработан технологический процесс механической обработки детали - ступенчатого вала барабанного привода ленточного конвейера щебнеочистительной машины.
Черновое и получистовое обтачивание заготовки осуществляется на токарном станке 16К20 с помощью резца Т15К6.
Предварительное и окончательное шлифование выполняется на шлифовальном станке 3Б151.
Оформлена технологическая документация на операции и переходы применяемые в ходе получения детали
Техно-экономические расчеты.
Расчёт экономической эффективности.
В экономической части рассматриваем два конвейера базовый вариант и новый вариант конвейера. Нужно разработать такой новый конвейер чтобы он был более эффективен чем базовый вариант. Я рассчитаю экономическую эффективность базового и нового варианта и докажу выгодность нового варианта конвейера.
Капитал предприятия формируется из двух источников: собственного и заёмного. Для привлечения капитала из этих источников предприятию необходимо платить. Это либо процент по кредитам (заёмный капитал) либо дивиденды (акционерный капитал). Чем более рисковый проект тем более высоких дивидендов будут ожидать акционеры а кредиторы будут предлагать кредиты под более высокие проценты. И акции предприятия и кредиты реализуются на финансовых рынках. И именно цены свободного рынка определяют степень риска инвестиций.
Поэтому можно сказать что стоимость капитала предприятия представляет собой рыночную оценку уровня риска по операциям предприятия. Предприятия принимают эту оценку в качестве среднего значения барьерного коэффициента HR т.к. у них нет более объективного показателя.
В общем случае стоимость капитала – это средневзвешенная цена (в процентах) которую предприятие уплатило за денежные средства используемые для формирования своего капитала. Эта величина определяется соотношением заёмного и собственного капиталов:
- стоимость долга %;
- доля собственного капитала;
- стоимость собственного капитала %;
Так как выплаты процентов уменьшают величину налогооблагаемой прибыли то соответственно уменьшается и величина налоговых выплат. Экономия на налогах частично компенсирует выплаты по долгам. Поэтому реальный процент выплат по долгам с учётом экономии составит:
где - ставка налога на прибыль;
- уровень реальной процентной ставки;
Доля долга и собственных средств в сумме равны единице. Поэтому определив одну из составляющих можно определить и другую:
Собственность собственного капитала при отсутствии развитого фондового рынка в России для Государственного предприятия берём на уровне альтернативного размещения средств (депозитные банковские ставки проценты по государственным облигациям и т.д.).
В условия высокой инфляции ставки ссудного процента и депозитные ставки рассчитываются с учётом внутригодовых реинвестиций и очищаются от инфляции по следующей методике.
Берём номинальные (т.е. с учётом инфляции) годовые ставки коммерческих банков. На их основе рассчитываем эффективные ставки (т.е. с учётом реинвестиций по периодам внутри года):
где - номинальная эффективная ставка (кредитная и депозитная соответственно);
- номинальная банковская ставка (кредитная = 015 и депозитная = 01 соответственно);
- число периодов начисления процентов внутри года;
Очищенные от инфляции эффективные ставки являются реальными ставками :
где - годовой уровень инфляции;
В данном расчёте сравниваем два варианта – до модернизации и после неё.
Наименование показателей
Количество рабочих смен в год
Продолжительность смены
Время приведения в рабочее пол.
Обслуживающий персонал
Срок службы до кап. ремонта
Рассчитаем годовой объём работ по базовому варианту исходя из производительности машины и времени её работы по формуле:
где ч – Продолжительность работы конвейера в день;
мин – время приведения машины в рабочее;
м3ч – производительность машины;
-Количество рабочих смен в год
Годовой объём работ по новому варианту составит:
Определим новую цену машины:
где руб – цена снятого оборудования;
БС= руб - цена нового оборудования образуется из следующих составляющих:
Управляющая Электроаппаратра
- затраты на установку нового оборудования;
где - количество человек для установки нового оборудования;
ч – количество времени затраченного на установку;
рубчас – тарифная ставка рабочих;
- затраты на изготовление нового оборудования;
где руб – тарифная ставка рабочего станочника;
ч – время на обработку вала;
ч – время на обработку зуба;
- количество зубьев;
-время на установку нового электрооборудования.
-тарифная ставка рабочего электромонтера
-время установки конвейера на ОПУ
-тарифная ставка слесаря механосборщика
- время установки конвейера на ОПУ
-тарифная ставка электросварщика
Рассчитаем годовые эксплуатационные издержки при использовании базового варианта по формуле:
где - зарплата работников;
где руб – часовая тарифная ставка рабочего 6го разряда;
руб – часовая тарифная ставка помощника рабочего 5го разряда;
- коэффициент отчисления на заработную плату;
- количество смен в году;
ч – продолжительность смены;
=160650 руб - стоимость энергии (4р=1кВт);
- стоимость текущего ремонта;
- коэффициент отчисления на текущий ремонт;
- стоимость капитального ремонта;
где - коэффициент отчисления на капительный ремонт;
Потери связанные не поступлением щебня и песка в производство составляют 556640 руб.
Рассчитаем годовые эксплуатационные издержки при использовании нового варианта:
Заработная плата работника - руб;
Удельная заработная плата машиниста по отношению к базовому варианту руб; (9.19)
Стоимость энергии - руб;
Удельная стоимость энергии по отношению к базовому варианту:
Отчисления на текущий ремонт - руб;
Удельные отчисления на текущий ремонт по отношению к базовому варианту: руб; (9.21)
Отчисления на капитальный ремонт - руб;
Удельные отчисления на капитальный ремонт по отношению к базовому варианту: руб; (9.22)
Удельная стоимость задержки пода заполнителей в производство
Рассчитаем чистые денежные потоки:
Изменение разходов руб.
-Содержание и эксплуатация оборудования
-Стоимость задержки поступление заполнителей в производство
-Уменьшение расходов
Корректировка денежных потоков
Определим эффективность инвестиций.
Основным показателем эффективности инвестиций является чистая текущая стоимость NPV.
где - чистый денежный поток руб;
- число лет функционирования объекта.
Вывод: таким образом применение системы модернизированного конвейера обеспечивает чистый денежный доход за 10 лет в сумме 1113057руб. Срок окупаемости проекта 2 года.
Определим график зависимости чистой текущей стоимости NPV от барьерной ставки HR.
График зависимости NPV=f(БС).
Обеспечение безопасности жизнедеятельности.
1 Безопасность персонала при обслуживании погрузочных-разгрузочных работ
1.1. Эксплуатационно-технические характеристики ленточного конвейера. Виды работ
Ленточные конвейеры предназначены для транспортирования сыпучих порошкообразных мелко- и среднекусковых материалов а также однотипных штучных грузов в горизонтальном и слабо наклонном направлении. Рабочим органом на котором размещается транспортируемый материал является резинотканевая лента состоящая из тканевых прокладок со связывающими их резиновыми прокладками и обкладками.
Технические характеристики ленточного конвейера
N=30кВт; n=1500обмин
Габариты лент. конвейера
Высота ( грузовое натяжное устройство) мм
Ширина конвейера ( с приводом) мм
1.2 Требования к персоналу режимы работы технология обслуживания квалификация персонала
Оператор погрузочно-разгрузочных работ могут обслуживать мужчины не моложе 18 лет прошедшие соответствующую подготовку имеющие профессиональные навыки удостоверение на техническую работу с конвейером перед допуском к самостоятельной работе должны пройти: обязательные предварительные и периодические медицинские осмотры для признания годными к выполнению работ в установленном порядке; обучение безопасным методам и приемам выполнения работ инструктаж по охране труда стажировку на рабочем месте и проверку знаний требований охраны труда. [28].
Для защиты от производственных загрязнений и механических воздействий машинисты обязаны пользоваться при выполнении работ средствами индивидуальной защиты которые выдаются в соответствии с Типовыми отраслевыми нормами бесплатной выдачи рабочим и служащим специальной одежды специальной обуви и других средств индивидуальной защиты [28].
Средства индивидуальной защиты
Комбинезон хлопчатобумажный для защиты от общих производственных загрязнений и механических воздействий
Ботинки кожаные (сапоги кирзовые)
Рукавицы комбинированные
Перчатки с полимерным покрытием
Жилеты сигнальные 2-го класса защиты
Наушники противошумные (с креплением на каску) или вкладыши противошумные
Зимой дополнительно:
продолжение табл. 10.3
Куртка хб на утепляющей прокладке
Брюки хб на утепляющей прокладке
Валенки с резиновым низом или ботинки кожаные утепленные с жестким подноском
Перчатки с защитным покрытием морозостойкие с шерстяными вкладышами
Операторов и сотрудников ремонт подразделения обязаны выполнять правила внутреннего распорядка. Допуск посторонних лиц а также работников в нетрезвом состоянии запрещается.
В процессе повседневной деятельности операторы должны: применять в процессе работы машины по назначению в соответствии с инструкциями заводов-изготовителей; выполнять только ту работу которая поручена руководителем работ; поддерживать машину в технически исправном состоянии
Виды и периодичность обслуживания ленточного конвейера.
Периодичность выполнения ТО и ТР маш.-ч.
Ежесменное техническое обслуживание (ЕО)
В течение рабочей смены
Первое техническое обслуживание (ТО-1)
Рабочий 7 разряда механик сервисный инженер
Второе техническое обслуживание (ТО-2)
Сезонное техническое обслуживание (СТО)
Период подготовки к зимней или летней эксплуатации
Высококвалифицированная бригада
Капитальный ремонт (КР)
Ежесменное обслуживание проводит обычно серверсный механик К ТО и текущему ремонту ленточного конвейра допускаются лица имеющие соответствующую квалификацию и знающие правила безопасного ведения работ. Они должны быть обеспечены комплектом исправных инструментов.
Рекомендуется выполнять ЕО до начала и после работы. При сосредоточении большого числа ленточных конвейеров на одном месте организуют специальные бригады по техническому обслуживанию которые должны выполнять ЕО и ТО с привлечением оператора.
1.3. Основные опасности и вредности при работе персонала
В соответствии со стандартом «ГОСТ 12.0.003-74 ССБТ. Опасные и вредные производственные факторы. Классификация» при конвейера возникают следующие физические опасные и вредные производственные факторы [3]:
движущиеся машины и механизмы незащищенные подвижные элементы машины;
повышенная запыленность и загазованность воздуха;
повышенный уровень шума на рабочем месте; повышенный уровень вибрации;
повышенная или пониженная влажность воздуха;
недостаточная видимость рабочей зоны;
отсутствие или недостаточность естественного освещения; недостаточная освещенность рабочей зоны;
1.4 Технические решения и организационные мероприятия по обеспечению безопасности персонала при работе на ленточном конвейере
Оператор сталкиваются с воздействием таких физически опасных и вредных производственных факторов как повышенный уровень шума отсутствие и недостаток естественного освещения недостаточная освещенность рабочей зоны.
Недостаточная освещенность рабочей зоны ленточного конвейра приводит к быстрой утомляемости дискомфорту опасности травматизма ухудшению зрения оператора погрузочно-разгрузочных работ.
При освещении открытых территорий применяется исключительно система общего освещения при равномерном размещении светильников. Общее равномерное освещение обеспечивается равномерным размещением светильников с неизменным расстоянием между ними в каждом ряду и между рядами. Такое расположение светильников используется в тех случаях когда необходимо обеспечить одинаковые условия освещения по всей площади помещения в целом.
Для освещения больших по площади территорий наряду со светильниками применяют прожекторное освещение. Прожекторная осветительная установка характеризуется значительно меньшими эксплуатационными расходами по сравнению с осветительной установкой выполненной светильниками. Кроме снижения необходимого числа опор прожекторное освещение выгодно отличается от освещения светильниками более благоприятным соотношением горизонтальной и вертикальной освещенностей.
Одновременно с перечисленными преимуществами прожекторному освещению присущи некоторые недостатки. Основными из них являются большое слепящее действие и трудность борьбы с затенениями. Если на пути прожекторного луча направление которого близко к горизонтальному находится преграда то возникает резкая тень. Устранение тени затруднено особенно при групповом размещении прожекторов когда на одной опоре располагается 10 и более прожекторов.
Перечисленные недостатки могут быть в большинстве случаев устранены за счет правильного размещения прожекторов.
Размещение осветительных приборов.
Прожекторы могут размещаться на освещаемой территории либо индивидуально (1—2 прожектора) либо группами по 10—15 штук.
Примеры расположения осветительных приборов (рис.9.1.).
Прожекторы могут размещаться на освещаемой территории либо индивидуально (1—2 прожектора) либо группами по 10—15 штук. Групповое размещение прожекторов обычно применяется при освещении больших территорий площадь которых превышает 10 000 м2 высоких уровнях нормированной освещенности а также в тех случаях когда по условиям освещаемого объекта число опор должно быть сведено к минимуму. При групповой системе расположения прожекторов расстояние между мачтами доходит до 400—500 м упрощается электрическая сеть за счет уменьшения точек питания. Одновременно с этим повышается неравномерность освещения и возрастает трудность борьбы с тенями.
Выбираем прожектор типа ПЗС – 35
В целях уменьшения затенения мест участок освещаем с двух сторон.
Расстояниеlмежду прожекторными мачтами по длине парка определяем из выражения:
где:l– расстояние между прожекторными мачтами м .
Количество мачт по длине парка определяется по формуле
где:Nдл– количество мачт по длине парка шт;
L– длина парка (3000 м).
Общее число прожекторных мачт определяем из выражения
Площадь освещаемой территории объекта определяется по формуле:
Общее число прожекторов определяется по формуле [6]:
где:n– общее число прожекторов;
Ен– нормированное значение освещенности (10 лк) [6];
S– площадь освещаемой территории м2;
К– коэффициент запаса учитывающий старение ламп и окружающую среду (принимаетсяК=15) [6];
V– коэффициент учитывающий рельеф местности (принимаетсяV=115) [6];
Z– коэффициент неравномерности освещения (принимаетсяZ=25) [6].
Световой поток прожектора принимается из выражения:
где:Fл– световой поток лампы (30750 лм).
Результаты расчета освещенности
Наименование параметра
Расстояние между прожекторными мачтами по длине парка
Количество мачт по длине
Площадь освещаемой территории объекта
Общее число прожекторов
Световой поток прожектора
Оптимальный угол наклона оптической оси прожектора
Выбираем прожектор типа ПЗС – 35 (табл. 10.1.)
Нормированная.свещенность
При размещении прожекторов их оптическая ось устанавливается под некоторым углом к горизонту. В зависимости от величины этого угла называемого углом наклона оптической оси прожектора изменяется размер светового пятна создаваемого лучом прожектора на освещаемой территории. Наивыгоднейшим углом наклона обеспечивающим минимальную установленную мощность будет такой угол при котором площадь светового пятна ограниченная заданным значением освещенности будет максимальна. Наивыгоднейший угол наклона оптической оси прожектора можно определить приближенно:
где - коэффициенты зависящие от углов рассеяния прожектора в горизонтальной и вертикальной плоскостях;
- расчетная освещенность лк;
- высота установки прожектора над условной горизонтальной плоскостью проходящей через расчетную точку освещенности на вертикальной плоскости.
Величина расчетной освещенности зависит от нормируемой освещенности коэффициента запаса и размещения светового пятна прожектора по освещаемой территории. Если территория освещается несколькими прожекторами расположенными так что вся освещаемая поверхность заполнена световыми пятнами без пропусков и излишних перекрытий то в точках перекрытия расчетная освещенность будет создаваться световыми потоками двух прожекторов и следовательно может быть принята равной . Если же территория освещается одним прожектором то расчетная освещенность определяется произведением ЕК. Величины наивыгоднейшего угла наклона прожекторов заливающего света в зависимости от значения произведения приведены в таблице 9.3.
Наивыгоднейший угол наклона прожектора заливного света принимаем равный 21 град. Тогда высоту установки прожекторов определяем из соотношения = 900
Наивыгоднейший угол наклона град
Величина произведения
ПЗС – 45 лампа 1000 Вт
ПЗС – 35 лампа 500 Вт
Приступая к размещению прожекторов следует вначале выбрать такое положение прожекторных мачт которое исключало бы или сводило к минимуму затенение освещаемой территории а также обеспечивало совпадение направления светового пучка с преобладающим направлением осей зрения работающих. Определив таким образом положение прожекторов и наивыгоднейшие углы наклона можно выбрать направление их оптических осей с таким расчетом чтобы на освещаемую поверхность не падали тени от оборудования или построек а также чтобы обеспечивалось благоприятное соотношение освещенностей вертикальной и горизонтальной плоскостей.
Принимаем размещение прожекторов по схеме (а) на рисунке 9.3.
2. Безопасность персонала в чрезвычайных ситуациях
2.1. Пожарная безопасность
Под пожаром понимается неконтролируемый процесс горения при котором возможны уничтожение материальных ценностей и опасность для жизни людей. Причинами возникновения пожаров на автогрейдере чаще всего являются [29]:
неосторожное обращение с огнем;
несоблюдение правил эксплуатации производственного оборудования; самовозгорание обтирочных горючих и легковоспламеняющихся материалов;
перегрузка электроустановок и замыкания в электрической сети;
грозовые разряды и др.
Обслуживающий персонал обязан соблюдать следующие противопожарные мероприятия :
четко знать и выполнять установленные правила пожарной безопасности не допускать действий которые могут привести к пожару;
строго выполнять требования инструкций по обеспечению пожарной безопасности технологических процессов в подвижном составе;
не допускать использования неисправных инструментов приборов оборудования соблюдать правила безопасности по их эксплуатации а также указания руководителей и лиц ответственных за пожарную безопасность при проведении пожароопасных работ;
убирать рабочие места и отключать бытовые электроприборы после окончания работы;
уметь применять имеющиеся в подразделении (подвижном составе) средства пожаротушения;
в случае возникновения пожара или обнаружения его признаков немедленно сообщить об этом в пожарную охрану а в подвижном составе в пути следования - начальнику (механику-бригадиру) поезда или машинисту локомотива и принять меры к ликвидации пожара и эвакуации пассажиров действуя в соответствии с требованиями п. 7 главы 1 Правил а также действующих инструкций по обеспечению пожарной безопасности в подвижном составе железнодорожного транспорта.
Если тушение пожара невозможно по каким-либо причинам то необходимо провести эвакуацию людей из опасной зоны пожара. Эвакуация людей при пожаре представляет собой процесс организованного движения людей из опасной зоны пожара.
При тушении загоревшегося электрооборудования используют углекислотные огнетушители.
Углекислотные огнетушители ОУ предназначены для тушения загораний веществ горение которых не может происходить без доступа воздуха загораний электроустановок находящихся под напряжением не более 1000 В жидких и газообразных веществ (класс В С). ОУ применяют особенно эффективно при объемном тушении и когда для тушения пожара необходимы «чистые» огнетушащие составы не повреждающие защищаемое оборудование или объекты. Огнетушащее вещество - двуокись углерода (СО2). Углекислота попадая на горящее вещество охлаждает его и производит тушение. Испаряясь она не оставляет следов [7].
Указание по эксплуатации и безопасности углекислотных огнетушителей.
Правила приведения огнетушителя в действие указаны на этикетке помещенной на корпусе огнетушителя.
При тушении электроустановок находящихся под напряжением не допускается подводить раструб ближе 1м до электроустановки и пламени.
Перезарядка и ремонт огнетушителей должны производится в специализированных организациях на зарядных станциях.
Эксплуатация углекислотных огнетушителей без чеки и пломбы завода - изготовителя или организации производившей перезарядку не допускается.
Огнетушители углекислотные должны размещается в легкодоступных и заметных местах. Не допускается хранение и эксплуатация огнетушителей в местах где температура может превышать 50°С и под прямыми лучами солнца.
Необходимо соблюдать осторожность при выпуске огнетушащего вещества из раструба т.к. температура на его поверхности понижается до минус 60-70С.
После применения углекислотного огнетушителя в закрытом помещении помещение необходимо проветрить.
Рекомендуется периодически проверять массу заряда - не реже одного раза в два года. Величина массы баллона с запорно-пусковым устройством без заряда выбита на корпусе запорного устройства (см. рисунок). Суммарная масса углекислотного огнетушителя определяется прибавлением к ней массы СО2 указанной на этикетке или в паспорте. Необходимо проводить перезарядку и переосвидетельствование баллона через 5 лет.
Транспортировка углекислотного огнетушителя допускается всеми видами транспорта;
Гарантийный срок хранения и эксплуатации - 2 года со дня изготовления но не более 1 года с момента ввода в эксплуатацию по НПБ 166-97.
Технические характеристики углекислотного огнетушителя ОУ-3.
Огнетушащее вещество ГОСТ 8050-85
Длина струи огнетушащего вещества м
Продолжительность подачи огнетушащего вещества сек
Огнетушащая способность (по классу В) не менее м2
Масса заряда огнетушащего вещества кг
Огнетушащая способность
Максимальное рабочее давление МПа
Диапазон рабочих температур °C
Габаритные размеры мм
Средний срок службы лет
Вспомогательное оборудование для перемещения грузов. Лысяков А.Г.
-е изд. перераб. и доп.-М.: Машиностроение 1989.-232 с.с
Справочник конструктора – машиностроителя. Анурьев В.И. т.2 5-е издание переработанное и дополненное. М.: «Машиностроение» 1979 – 559с. ил. с.
Подъемно-транспортные машины. Вайнсон А.А. 4-е издание переработанное и дополненное. М.: «Машиностроение» 1989.
Детали машин. Курсовое проектирование П.Ф. Дунаев О.П.
Леликов М.: «Высшая школа» 1984.
Курсовое проектирование деталей машин С.А. Чернавский К.Н.
Боков М.: «Машиностроение» 1987.
Транспортирующие машины. Спиваковский А.О. Дьячков В.К. Изд. 2-е
перераб. и доп. М. изд-во «Машиностроение» 1968 504 стр.
Справочник технолога – машиностроителя т.1. под ред. Косиловой А.Г.
Мещерякова Р.К. М.: «Машиностроение» 1986.
Нормирование точности геометрических параметров. Мет. Указания.
Гвоздев В.Д. М.: МИИТ 1989.
Допуски и посадки. Справочник. Под ред. В.Д. Мягков и др. часть 1. М.:
«Машиностроение» 1982.
Методические указания. В.А. Аверкин. Москва – 2005.
Безопасность жизнедеятельности. Учебник для вузовС.В. Белов А.В. Ильницкая А.Ф. Козьяков и др.;Под общ. Ред. С.В. Белова. 2-е изд. испр. И доп. – М.: Высш. Шк. 1999. – 448 с.: ил.
Охрана труда на железнодорожном транспорте. В.С. Крутяков А.Л. Левицкий Ю.Г. Сибаров и др.: Под. Ред. В.С. Крутякова. – М.: Транспорт 1987. – 312 с.
Гражданская оборона на железнодорожном транспорте.
Юрпольский И.И. Ильин Г.Т. Янченков Н.Н. – М.: Транспорт 1987.-с.272
Каталог Часть . Оборудование “Конвейеры ленточные стационарные”.
2-rrrrrryer-srrrssrrsrrs.dwg

Техническая характеристика
Механизм перемещения:
а) Количество - 1 шт.
б) Электродвигатель - 4А100S4.
в) Мощность - 3 кВт; n=1500 обмин.
а) Количество - 2 шт.
б) Электродвигатель - 4А71В4.
) Скорость перемещения тележки - 0
) Способ разррузки - двусторонний.
ТНД-511.02.00.00.00.
1-rrrsrsrsr-ryerrrrrrs.dwg

Электродвигатель привода
N=30кВт; n=1500обмин
Дефлекторные ролики верхние и нижние ставить через 10 12м;
Отверстия для дефлекторных роликов и дополнительных
роликоопор сверлить при монтаже;
В местах загрузки верхние роликоопоры ставить через 500мм;
У приводного и концевого барабанов на участках
переходит из плоского положения в желобчатое следует
осуществлять плавный переход ленты с помощью прямой
роликоопоры - как показано на чертеже;
* Размер для справок.
Надштабельный ленточный
ТНД-511.01.00.00.00.
4-rrrsrrrr-rrsrrrr.dwg

) Полости подшипников заполнить смазкой
ЦИАТИМ 201 ГОСТ 6267-74.
) Резьбу крепежных изделий покрыть
ТНД-511.04.00.00.00.
5-rsrerrrrrr-rrsrrrerr.dwg

) Полости подшипников заполнить смазкой
ЦИАТИМ 201 ГОСТ 62-67
) В редуктор залить масло И-20 ГОСТ 1707-51
ТНД-511.05.00.00.00.
Рекомендуемые чертежи
- 18.11.2018
- 14.09.2015
Свободное скачивание на сегодня
- 23.08.2014