Путеремонтная летучка ПРЛ-4



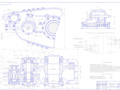
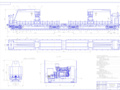
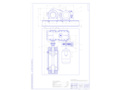
- Добавлен: 25.10.2022
- Размер: 4 MB
- Закачек: 0
Узнать, как скачать этот материал
Подписаться на ежедневные обновления каталога:
Описание
Путеремонтная летучка ПРЛ-4
Состав проекта
![]() |
![]() ![]() ![]() |
![]() |
![]() |
![]() ![]() ![]() ![]() |
![]() |
![]() ![]() |
![]() ![]() |
![]() ![]() |
![]() ![]() |
![]() ![]() |
![]() ![]() ![]() ![]() |
![]() ![]() ![]() ![]() |
Дополнительная информация
Контент чертежей
Общий вид.dwg

МПГ.dwg

СБ.dwg

Рекомендуемые чертежи
Свободное скачивание на сегодня
Обновление через: 3 часа 27 минут