Проходческий комбайн 4ПУ



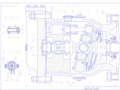
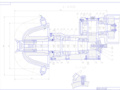
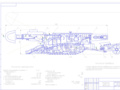
- Добавлен: 25.10.2022
- Размер: 1 MB
- Закачек: 0
Узнать, как скачать этот материал
Подписаться на ежедневные обновления каталога:
Описание
Проходческий комбайн 4ПУ
Состав проекта
![]() |
![]() ![]() |
![]() |
![]() ![]() ![]() ![]() |
![]() ![]() ![]() ![]() |
![]() ![]() ![]() ![]() |
![]() ![]() |
![]() ![]() ![]() |
![]() ![]() |
![]() ![]() |
![]() ![]() |
Дополнительная информация
Контент чертежей
1лист 1 А2.dwg

1лист 2 А2.dwg

1Чертеж лист2.dwg

Рекомендуемые чертежи
- 14.09.2014
Свободное скачивание на сегодня
Обновление через: 11 часов 41 минуту
- 22.08.2014
- 29.08.2014