Проектирования конструкции автогрейдера




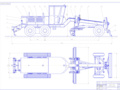
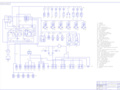
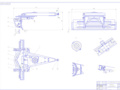
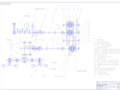
- Добавлен: 25.10.2022
- Размер: 6 MB
- Закачек: 1
Описание
Состав проекта
![]() |
![]() |
![]() ![]() ![]() |
![]() ![]() ![]() ![]() |
![]() |
![]() ![]() ![]() ![]() |
![]() ![]() ![]() ![]() |
![]() |
![]() |
![]() |
![]() ![]() ![]() |
![]() |
![]() ![]() ![]() |
![]() ![]() |
![]() ![]() |
![]() ![]() ![]() |
![]() ![]() ![]() |
![]() ![]() ![]() |
![]() ![]() ![]() |
![]() ![]() ![]() |
![]() ![]() |
![]() ![]() |
![]() ![]() ![]() |
![]() ![]() ![]() |
![]() ![]() ![]() |
![]() ![]() |
![]() ![]() ![]() |
![]() ![]() ![]() |
![]() ![]() ![]() ![]() |
![]() ![]() ![]() ![]() |
![]() ![]() ![]() ![]() |
![]() ![]() ![]() |
![]() ![]() ![]() ![]() |
![]() ![]() ![]() ![]() |
![]() ![]() ![]() |
![]() ![]() ![]() |
![]() ![]() ![]() ![]() |
![]() ![]() ![]() ![]() |
![]() ![]() ![]() |
![]() |
![]() ![]() ![]() |
Дополнительная информация
Спецификация - поворотный круг.cdw

ДП.0908.481412.14.03.000 СБ
ДП.0908.481412.14.03.001
ДП.0908.481412.14.03.002
ДП.0908.481412.14.03.003
ДП.0908.481412.14.03.004
ДП.0908.481412.14.03.005
ДП.0908.481412.14.03.006
ДП.0908.481412.14.03.007
ДП.0908.481412.14.03.008
3.Основная рама.cdw

Для сварных швов электрод по ГОСТ 9467-75
Неуказаные предельные отклонения размеров
направленного металла 19кг.
Клеймить сварные швы номером клейма сварщика ударным
ДП.0908.481412.02.00.000
7.APM.cdw

ДП.0908.481412.00.00.000И1
Расчет рамы автогрейдера
в САПР АПМ WinMachine
Карта перемещений (мм)
Расчет рамы автогрейдера в САПР APM WinMachine
9.Электросхема.cdw

аккумуляторные батареи;
фиксация рычага подвески;
установка угла резания отвала;
датчик уровня топлива;
датчик температуры воды;
индикатор загрязненности фильтра;
сигнализатор температуры;
указатель уровня топлива;
указатель температуры воды;
фонарь контрольной лампы красный;
фонарь контрольной лампы зеленый;
лампа подсветки приборов;
фара переднего рабочего освещения;
фара заднего рабочего освещения;
фара транспортного освещения;
фонарь контрольной лампы синий;
фонарь проблесковый (маяк);
прерыватель указателей поворотов;
ДП.0908.481412.00.00.000С3
Спецификация - рама основная.cdw

ДП.0908.481412.02.00.000СБ
ДП.0908.481412.02.01.000 СБ
ДП.0908.481412.02.02.000 СБ
ДП.0908.481412.02.03.000 СБ
ДП.0908.481412.02.04.000 СБ
ДП.0908.481412.02.05.000 СБ
ДП.0908.481412.02.06.000 СБ
ДП.0908.481412.02.07.000 СБ
ДП.0908.481412.02.08.000 СБ
ДП.0908.481412.02.09.000 СБ
Кронштейн крепления рыхлителя
Кронштейн крепления бульдозера
2.Кинематическая схема.dwg
- шестерни промежуточного вала;
- шестерни вторичного вала;
- шестерни первичного вала;
- промежуточный вал;
- шестерни ведомого вала;
- ведущая коническая шестерня;
- ведомая коническая шестерня;
- шестерни редуктора;
- шестерни балансира;
ДП.0908.481412.00.00.000К3
Кинематическая схема
Спецификация - тяговая рама.dwg
ДП.0908.481412.14.02.001
ДП.0908.481412.14.02.002
ДП.0908.481412.14.02.003
ДП.0908.481412.14.02.004
ДП.0908.481412.14.02.005
ДП.0908.481412.14.02.006
ДП.0908.481412.14.02.007
Спецификация - отвал.dwg
ДП.0908.481412.14.11.001
ДП.0908.481412.14.11.002
ДП.0908.481412.14.11.003
ДП.0908.481412.14.11.004
ДП.0908.481412.14.11.005
ДП.0908.481412.14.11.006
ДП.0908.481412.14.11.007
9.Электросхема.dwg
аккумуляторные батареи;
фиксация рычага подвески;
установка угла резания отвала;
датчик уровня топлива;
датчик температуры воды;
индикатор загрязненности фильтра;
сигнализатор температуры;
указатель уровня топлива;
указатель температуры воды;
фонарь контрольной лампы красный;
фонарь контрольной лампы зеленый;
лампа подсветки приборов;
фара переднего рабочего освещения;
фара заднего рабочего освещения;
фара транспортного освещения;
фонарь контрольной лампы синий;
фонарь проблесковый (маяк);
прерыватель указателей поворотов;
ДП.0908.481412.00.00.000С3
Спецификация - общий вид.dwg
ДП.0908.481412.00.00.000 ПЗ
ДП.0908.481412.01.00.000 СБ
ДП.0908.481412.02.00.000 СБ
ДП.0908.481412.03.00.000 СБ
ДП.0908.481412.04.00.000 СБ
ДП.0908.481412.05.00.000 СБ
ДП.0908.481412.06.00.000 СБ
ДП.0908.481412.07.00.000 СБ
ДП.0908.481412.08.00.000 СБ
ДП.0908.481412.09.00.000 СБ
ДП.0908.481412.10.00.000 СБ
ДП.0908.481412.11.00.000 СБ
ДП.0908.481412.12.00.000 СБ
ДП.0908.481412.13.00.000 СБ
ДП.0908.481412.14.00.000 СБ
ДП.0908.481412.15.00.000 СБ
ДП.0908.481412.16.00.000 СБ
ДП.0908.481412.17.00.000 СБ
Поснительная записка
Общий вид автогрейдера
Гидроцилиндр подъема
Рабочее оборудование
Бульдозерное оборудование
7.APM.dwg
ДП.0908.481412.00.00.000И1
Расчет рамы автогрейдера
в САПР АПМ WinMachine
Карта перемещений (мм)
Расчет рамы автогрейдера в САПР APM WinMachine
5.Тяговая рама.dwg
Неуказаные предельные отклонения размеров
направленного металла 19кг.
Клеймить сварные швы номером клейма сварщика ударным
Условное обозначение
ДП.0908.481412.14.02.000 СБ
Спецификация - поворотный круг.dwg
ДП.0908.481412.14.03.001
ДП.0908.481412.14.03.002
ДП.0908.481412.14.03.003
ДП.0908.481412.14.03.004
ДП.0908.481412.14.03.005
ДП.0908.481412.14.03.006
ДП.0908.481412.14.03.007
ДП.0908.481412.14.03.008
Спецификация - рама основная.dwg
ДП.0908.481412.02.00.000СБ
ДП.0908.481412.02.01.000 СБ
ДП.0908.481412.02.02.000 СБ
ДП.0908.481412.02.03.000 СБ
ДП.0908.481412.02.04.000 СБ
ДП.0908.481412.02.05.000 СБ
ДП.0908.481412.02.06.000 СБ
ДП.0908.481412.02.07.000 СБ
ДП.0908.481412.02.08.000 СБ
ДП.0908.481412.02.09.000 СБ
Кронштейн крепления рыхлителя
Кронштейн крепления бульдозера
Спецификация - рабочее оборудование.dwg
ДП.0908.481412.14.02.000 СБ
ДП.0908.481412.14.03.000 СБ
ДП.0908.481412.14.04.000 СБ
ДП.0908.481412.14.05.000 СБ
ДП.0908.481412.14.06.000 СБ
ДП.0908.481412.14.07.000 СБ
ДП.0908.481412.14.08.000 СБ
ДП.0908.481412.14.09.000 СБ
ДП.0908.481412.14.10.000 СБ
ДП.0908.481412.14.11.000 СБ
Рабочее оборудование
Гидравлический шарнир
Редуктор поворота отвала
Гидроцилиндр изменения
ДП.0908.481412.14.01.000 СБ
ДП.0908.481412.14.13.000 СБ
ДП.0908.481412.14.12.000 СБ
6.2.Поворотный круг.dwg
Неуказаные предельные отклонения размеров
Клеймить сварные швы номером клейма сварщика ударным
Условное обозначение
ДП.0908.481412.14.03.000 СБ
3.Основная рама.dwg
Для сварных швов электрод по ГОСТ 9467-75
Неуказаные предельные отклонения размеров
направленного металла 19кг.
Клеймить сварные швы номером клейма сварщика ударным
ДП.0908.481412.02.00.000 СБ
10.Экономика.cdw

6.2.Поворотный круг.cdw

Неуказаные предельные отклонения размеров
Клеймить сварные швы номером клейма сварщика ударным
Условное обозначение
ДП.0908.481412.14.03.000
5.Тяговая рама.cdw

Неуказаные предельные отклонения размеров
направленного металла 19кг.
Клеймить сварные швы номером клейма сварщика ударным
Условное обозначение
ДП.0908.481412.14.02.000
Спецификация - отвал.cdw

ДП.0908.481412.14.11.000 СБ
ДП.0908.481412.14.11.001
ДП.0908.481412.14.11.002
ДП.0908.481412.14.11.003
ДП.0908.481412.14.11.004
ДП.0908.481412.14.11.005
ДП.0908.481412.14.11.006
ДП.0908.481412.14.11.007
6.1.Отвал.cdw

1.Общий вид.cdw

Спецификация - тяговая рама.cdw

ДП.0908.481412.14.02.000 СБ
ДП.0908.481412.14.02.001
ДП.0908.481412.14.02.002
ДП.0908.481412.14.02.003
ДП.0908.481412.14.02.004
ДП.0908.481412.14.02.005
ДП.0908.481412.14.02.006
ДП.0908.481412.14.02.007
Спецификация - рабочее оборудование.cdw

ДП.0908.481412.14.00.000 СБ
ДП.0908.481412.14.02.000 СБ
ДП.0908.481412.14.03.000 СБ
ДП.0908.481412.14.04.000 СБ
ДП.0908.481412.14.05.000 СБ
ДП.0908.481412.14.06.000 СБ
ДП.0908.481412.14.07.000 СБ
ДП.0908.481412.14.08.000 СБ
ДП.0908.481412.14.09.000 СБ
ДП.0908.481412.14.10.000 СБ
ДП.0908.481412.14.11.000 СБ
Рабочее оборудование
Гидравлический шарнир
Редуктор поворота отвала
Гидроцилиндр изменения
ДП.0908.481412.14.01.000 СБ
ДП.0908.481412.14.13.000 СБ
ДП.0908.481412.14.12.000 СБ
4.Основное рабочее оборудование.cdw

2.Кинематическая схема.cdw

- шестерни промежуточного вала;
- шестерни вторичного вала;
- шестерни первичного вала;
- промежуточный вал;
- шестерни ведомого вала;
- ведущая коническая шестерня;
- ведомая коническая шестерня;
- шестерни редуктора;
- шестерни балансира;
ДП.0908.481412.00.00.000
Кинематическая схема
Спецификация - общий вид.cdw

ДП.0908.481412.00.00.000 ПЗ
ДП.0908.481412.00.00.000 ВО
ДП.0908.481412.01.00.000 СБ
ДП.0908.481412.02.00.000 СБ
ДП.0908.481412.03.00.000 СБ
ДП.0908.481412.04.00.000 СБ
ДП.0908.481412.05.00.000 СБ
ДП.0908.481412.06.00.000 СБ
ДП.0908.481412.07.00.000 СБ
ДП.0908.481412.08.00.000 СБ
ДП.0908.481412.09.00.000 СБ
ДП.0908.481412.10.00.000 СБ
ДП.0908.481412.11.00.000 СБ
ДП.0908.481412.12.00.000 СБ
ДП.0908.481412.13.00.000 СБ
ДП.0908.481412.14.00.000 СБ
ДП.0908.481412.15.00.000 СБ
ДП.0908.481412.16.00.000 СБ
ДП.0908.481412.17.00.000 СБ
Поснительная записка
Общий вид автогрейдера
Гидроцилиндр подъема
Рабочее оборудование
Бульдозерное оборудование
моя ПЗ.docx
Анализ вариантов проектирования конструкции автогрейдера и выбор окончательного варианта проектирования для дипломного проекта 9
Описание устройства выбранного варианта конструкции машины 11
Патентный поиск с целью проверки изделия на патентную чистоту 19
Расчет и проектирование автогрейдера 24
1 Мощность двигателя 24
3 Расчет производительности автогрейдера 33
4 Определение сил действующих на автогрейдер 34
5 Расчет механизмов управления 39
6 Расчет ходового оборудования 42
7 Определение нагрузок действующих на раму автогрейдера 45
7.1 Расчетный случай I 45
7.2 Расчетный случай II 50
8 Расчет основной рамы в САПР АПМ WinMachine 53
Гидравлическая система 69
Электрооборудование машины 73
Экономико-организационная часть 83
1 Оценка технической целесообразности конструкции изделия 83
2 Расчет трудоемкости ОКР 87
3 Расчет временных и стоимостных затрат на проектирование изделии 93
4 Прогнозирование себестоимости изделия 96
5 Определение прогнозируемой цены изделия 100
6 Расчет капитальных вложений в НИОКР и освоение производства 101
7 Оценка эффекта от производства и использования изделия 102
8 Сводные показатели оценки экономической целесообразности проекта 102
3 Общие санитарно- гигиенические требования к воздуху рабочей зоны 114
4 Светотехнические приборы машины и освещение территории 115
5 Пожарная безопасность 116
6 Охрана природы 117
7 Указание мер безопасности 118
Список литературы 123
Приложение: спецификации 125
Первые опыты строительства грунтовых дорог с использованием грейдера были проведены в России еще в 1910-х годах и впоследствии эти машины получили у нас широкое распространение. Из-за огромных масштабов дорожного строительства в нашей стране в послевоенное время возникла и развилась новая отрасль машиностроения. В настоящее время дорожно-строительное производство немыслимо без применения этих специализированных машин современной конструкции. Строительные организации РФ располагают значительным парком дорожно-строительных машин; из года в год расширяется их номенклатура растет выпуск улучшается качество машин.
Число производителей автогрейдеров в мире велико хотя эти машины менее многочисленны чем скажем бульдозеры или одноковшовые погрузчики. Несмотря на обилие марок лежащие в основе конструкций автогрейдеров технические идеи практически одинаковы. Именно они придают этим машинам столь оригинальный вид. Современный автогрейдер – это как правило длиннобазовые трехосные машины у которых две пары задних колес расположены очень близко друг к другу а между средней и передней осями размещается грейдерный отвал длина которого больше высоты в 5 7 раз.
Выпуск автогрейдеров в России в настоящее время осуществляют три завода строительно-дорожных машин – Брянский Орловский и Челябинский причем серийный выпуск тяжелых грейдеров освоил лишь Челябинский завод. Эти машины наиболее эффективны при выполнении землеройно-планировочных работ на строительстве при ремонте и содержании дорог. По необходимости применяют их и в других сферах деятельности. Российские машиностроители могут с уверенностью сказать что наши автогрейдеры по своим характеристикам мало уступают зарубежным аналогам и экспортируются более чем в 50 стран мира. Отечественным производителям автогрейдеров противостоит мощная конкуренция компаний передовых стран которая вынуждает российские фирмы следовать тенденциям мирового технического прогресса.
Тем не менее по данным Госстроя России парк автогрейдеров в стране в силу различных причин в последнее время становится меньше. Так в 1995 году их насчитывалось 14 тысяч в 2000 – уже не более 10 тысяч причем 20% выработали срок амортизации. Начиная с 1997 года производство автогрейдеров начало увеличиваться но в 2001-м произошел резкий его спад. Если в 1990 году было изготовлено 4732 автогрейдера то в 2002 – лишь 992.
Снижение динамики продаж дорожно-строительной техники отмечается и в Западной Европе. Так объем продаж грейдеров в 2003 году по отношению к 2002 году составил лишь 84%. Причины спада за рубежом очень похожи на российские – значительные производственные и финансовые ресурсы необходимые для выпуска подобной техники ее дороговизна и многое другое.Однако просторы нашей страны состояние дорог и универсальность автогрейдеров всегда обеспечат высокий спрос на эти машины.
Такое положение вещей обостряет конкуренцию и производители вынуждены постоянно улучшать свою продукцию используя самые современные технические решения. Основное внимание уделяется выпуску высокопроизводительных энергонасыщенных и автоматизированных машин обеспечивающих выполнение работ в дорожном строительстве прогрессивными методами и позволяющих решать задачи комплексной механизации трудоемких строительных процессов. Это предъявляет определенные требования к уровню эксплуатации строительных дорожных машин а так же квалификации обслуживающего персонала.
Словом сейчас многие сервисные и машиностроительные предприятия России оперативно реагируют на нужды рынка. В последнее время в развитии конструкций автогрейдеров определились такие тенденции: повышение мощности двигателей без значительного увеличения массы машины; улучшение способности работать при большом крене а также в условиях низких и высоких температур сильной запыленности воздуха; повышение транспортной и рабочей скоростей автоматизация управления профилированием по заданным параметрам; повышение эргономичности и комфортности кабины; соответствие возрастающим требованиям по экологии.
Цели и задачи проектирования
Целью проекта является разработка конструкции автогрейдера класса 140 с гидравлической системой управления рабочими органами. Для достижения этой цели необходимо решить следующие задачи:
на основании сравнительного анализа различных вариантов исполнения автогрейдера выбрать конструкцию автогрейдера для проектирования;
выполнить описание устройства и работы выбранной конструкции;
выполнить патентный поиск с целью проверки изделия на патентную чистоту;
определить основные параметры автогрейдера выполнить тяговый расчет расчет производительности;
выполнить расчет механизмов управления и ходового оборудования;
определить силы действующие на рамы автогрейдера и на его рабочее оборудование;
рассчитать раму автогрейдера в системе автоматического проектирования с применением программы АПМ W
в экономическом разделе дать экономическое обоснование принятым в проекте техническим решениям;
в разделе «охрана труда» разработать мероприятия по ликвидации возникающих вредных и опасных факторов влияющие на рабочего и окружающую среду;
по результатам проделанной работы сделать заключение.
Анализ вариантов проектирования конструкции автогрейдера и выбор окончательного варианта проектирования для дипломного проекта
Для сравнительного анализа необходимо рассмотреть предназначение достоинства и недостатки классифицируемых автогрейдеров.является одним из главных параметров автогрейдеров так как от нее зависят нагрузки на колеса а следовательно тяговое усилие на ведущие колеса являющиеся тем показателем по которому судят о рабочих возможностях автогрейдеров. Легкие автогрейдеры не обладают достаточными мощностями для выполнения всех необходимых видов работ. Поэтому их применение ограничивается лишь работами по содержанию и ремонту дорог.
Краткой но выразительной характеристикой ходовой части автогрейдеров является их «колесная формула». Это общепринятое сочетание трех символов составляемое по схеме «A х B х C». A - показывает количество осей с управляемыми колесами B – число ведущих осей и C – общее количество осей. Легкие и средние автогрейдеры имеют одинаковую колесную формулу 1 х 2 х 3. В тяжелых грунтовых условиях или ситуациях когда скорость работы важней всего предпочтительна формула 1 х 3 х 3. Как правило это тяжелые машины массой 19 тонн и более широкое использование которых сдерживалось их непропорционально большой ценой. Следует отметить что серийный выпуск тяжелых грейдеров освоил лишь Челябинский завод. Возможно когда бурное развитие гидрообъемных трансмиссий коснется и этой отрасли дорожного машиностроения стоимость полноприводных автогрейдеров не будет столь разительно отличать их от заднеприводных. У полноприводных автогрейдеров выше сила тяги и значительно лучше курсовая устойчивость (потеря курсовой устойчивости при больших сопротивлениях на отвале – слабое место всех автогрейдеров). Их целесообразно применять при сооружении строительстве и содержании дорог в сложных грунтовых условиях в северных регионах страны.
У строителей наиболее популярны машины с формулой 1 х 2 х 3. Так автогрейдеры среднего типа предназначены для работ при сооружении дорог средних грунтовых условиях при ремонте и восстановлении грунтовых дорог. Средние автогрейдеры по сравнению с тяжелыми имеют меньшие габаритные размеры что повышает их маневренность. На территории центрального Черноземья целесообразно использовать модели средних автогрейдеров так как они превосходят своих легких собратьев по большинству показателей.
Специфика машины такова что без специального переоборудования ее можно использовать только для планирования и профилирования доля которых в общем объеме работ относительно невелика. Отдельного упоминания заслуживают усилия машиностроителей направленные на сокращение простоев автогрейдеров. Их конструкция позволяет использовать почти все виды дополнительного рабочего оборудования навешиваемые на раму. Это повышает его производительность. Все модели автогрейдеров унифицированы. В российских условиях машины выходят из строя после 7 9 лет жесткой эксплуатации. Они не просто ломаются а изнашиваются. У этой проблемы есть решения – капитальный полнокомплектный ремонт при котором возможна замена до 90% изношенных деталей. Этот вариант решения обойдется значительно дешевле чем покупка новой машины это немаловажно.
Проанализировав сказанное ранее я выбираю автогрейдер класса 140 с колесной формулой 1 х 2 х 3. Этот автогрейдер наиболее подходит для нашего региона и обладает хорошими технико - экономическими показателями в том числе и наиболее разумной ценой. В случае необходимости можно будет провести полнокомплектный ремонт с установкой самых последних новшеств и рационализаторских предложений.
Описание выбранной конструкции
Автогрейдер класса 140 предназначен для землеройно-профилировочных работ строительства и содержания дорог и может использоваться на работах по перемещению и распределению грунта и дорожно-строительных материалов планировке откосов выемок насыпей устройству корыта и боковых канав очистке дорог от снега смещения грунтов с добавками и вяжущими материалами на полотне дороги а также для рыхления асфальтовых покрытий булыжных мостовых и тяжелых грунтов с помощью дополнительного рабочего органа-рыхлителя заднего расположения. Он может работать в грунтах I-III категорий при температуре от 313К (40о) до 233К (-40 о) в условиях умеренного климата.
Общий вид автогрейдера приведен ниже на рисунке 3.1. Главными составными частями являются: основная рама тяговая рама с поворотным кругом и отвалом бульдозер силовая установка трансмиссия ходовая часть механизмы управления кабина оператора рыхлитель - кирковщик.
На автогрейдере в качестве силовой установки используется дизельный двигатель. В силовую передачу входят: муфта сцепления коробка передач задний мост и карданные валы.
Муфта сцепления двухдисковая постоянно замкнутого типа установлено на дизеле. На автогрейдерах устанавливается механическая коробка передач с шестью передачами вперед и двумя назад. Задний мост представляет собой балансирную двухосную тележку со всеми ведущими колесами. Передний мост шарнирно соединен с основной рамой автогрейдера. Такое соединение обеспечивает поперечное качение моста в обе стороны. Основным рабочим органом автогрейдера является отвал который имеет универсальную установку в пространстве для производства работ специфичных для автогрейдера. Дополнительные рабочие органы – бульдозер и рыхлитель. Рулевое управление состоит из гидроруля и привода к нему. Передние колеса поворачиваются цилиндрами. Колеса заднего моста оборудованы колодочными тормозами. В системе управления тормозами имеется гидроусилитель. Стояночный тормоз колодочного типа установлен на входном валу заднего моста. Управление муфтой сцепления механическое с гидроусилителем. Гидравлическая система управления рабочими органами раздельно-агрегатная. Гидронасос установлен на двигателе. Гидрораспределители закреплены снаружи на передней стенке кабины. Кабина оборудована сиденьем рычагами и педалями управления щитком приборов. На автогрейдере имеются звуковой сигнал указатели поворотов габаритов и торможения рабочие и транспортные фары проблесковый маяк. Конструкция автогрейдеров предусматривает возможность агрегатирования с плужным снегоочистителем удлинителем отвала толкающей плитой щеткой погрузчиком а также другим навесным оборудованием.
Рисунок 3.1 - Общий вид автогрейдера.
- рыхлитель-кирковщик; 2-рама подмоторная; 316-корпус фары; 4-бак гидросистемы; 5-крыло; 7-ящик аккумуляторный; 8-мост задний; 9-бак топливный; 10-кабина; 11-гидроцилиндр выноса тяговой рамы; 12-механизм фиксации; 13-гидроцилиндр подъема отвала; 14-рама тяговая; 15-балка хребтовая; 17-бульдозер; 18-мост передний; 19-круг поворотный; 20-отвал; 21-гидроцилиндр изменения угла резания отвала; 22-подножка; 23-коробка передач; 24-вал карданный
Рама автогрейдера сварной конструкции. Она состоит из подмоторной рамы и хребтовой балки. На подмоторной раме установлены кабина коробка передач двигатель капот баки. В задней части подмоторной рамы крепится рыхлитель – кирковщик снизу присоединяется задний мост. К хребтовой балке к передней части присоединены передний мост бульдозер и тяговая рама рабочего органа. В средней части к раме крепиться механизм подвески гидроцилиндров подъема отвала и выноса тяговой рамы.
Рисунок 3.2 - Основная рама.
-кронштейн крепления рыхлителя; 2-подмоторная рама; 3-хомут; 4-опора кабины; 5-подножка; 6-хребтовая балка; 7-механизм подвески гидроцилиндров; 8-отливка головная; 9-рама крепления бульдозера; 10-поворотный хомут; 11-цапфа; 12-сектор; 13-фиксатор; 14-винт; 1517-штуцер; 16-гидроцилиндр
Механизм подвески гидроцилиндров имеет поворотный хомут 10 с тремя кронштейнами на которых установлены вилки гидроцилиндров подъема отвала и выноса тяговой рамы. Хомут может поварачиваться вокруг цапфы 11 приваренной к хребтовой балке. Замыкания поворотного хомута в определенном положении производиться фиксатором 13 который закреплен на штоке гидроцилиндра16. Сектор 12 приваренный к хребтовой балке имеет 5 пазов. Крайние пазы служат для фиксации механизма подвески при установке отвала под углом до 90 градусов средний паз служит для установки механизма в исходное положение промежуточные пазы – для промежуточных положений.
Управление гидроцилиндром фиксатора производится рычагом из кабины. При замыкании механизма фиксатор входит в паз сектора при размыкании – выходит из паза.
Грейдерный отвал – основной рабочий орган машины и его главное достоинство – способность занимать в пространстве практически любое положение. Он может вращаться в горизонтальной плоскости на 360° в любом направлении становиться вертикально справа или слева от автогрейдера выдвигаться вправо или влево более чем на треть своей длины поворачиваться вокруг собственной режущей кромки. А получил он такую замечательную возможность благодаря системе крепления отвала к раме машины.
Главная особенность системы крепления заключена в том что собственно отвал является частью узла основу которого составляет тяговая рама автогрейдера представляющая собой А- или Т-образную в плане металлоконструкцию сваренную из балок коробчатого сечения и шарнирно прикрепленную к передней части основной рамы (хребтовой балки) машины в одной точке над осью передних колес. Для крепления тяговой рамы используется универсальный шарнир позволяющий ей поворачиваться во все стороны и вращаться вокруг собственной продольной оси. Прочность шарнира вполне соответствует усилиям возникающим на отвале.
Широкая сторона тяговой рамы поддерживается двумя гидроцилиндрами подъемаопускания отвала (левым и правым). Вместе эти устройства образуют своеобразный рычажный механизм жесткость которому в поперечном направлении придает еще один гидроцилиндр служащий для выноса тяговой рамы в сторону и образующий диагональ «четырехугольника». Такая система обеспечивает раме большие возможности перемещения диапазон которых резко увеличивается если гидроцилиндры подъемаопускания отвала и гидроцилиндр выноса тяговой рамы крепятся к скобе вращающейся вокруг хребтовой балки машины.
К тяговой раме крепятся скользящие опоры (пять и более) поддерживающие большое зубчатое колесо с внешним или внутренним зацеплением – поворотный круг к которому прикреплен отвал вращающийся относительно тяговой рамы благодаря гидромотору или гидроцилиндрам. Особенности крепления отвала к поворотному кругу позволяют поворачивать его относительно режущей кромки и сдвигать относительно круга влево или вправо.
Рисунок 3.3 - Рабочее оборудование.
-тяговая рама; 2-поворотный круг; 3-гидроцилиндр выноса отвала; 4-гидравлический шарнир; 5-шарнир; 6-водило; 7-редуктор поворота отвала; 8-палец; 9-крышка; 10-шарнир; 11-отвал; 12-кронштейн; 13-гидроцилиндр изменения угла резания отвала; 14-кронштейн; 15-регулировочный болт; 16-накладка; 17-болт; 18-регулировачная прокладка; 19-зубчатый венец
Рабочее оборудование состоит из трех крупных узлов: тяговой рамы 1 поворотного круга 2 отвала 11 и закрепленных на них агрегатов.
Тяговая рама 1 сварной конструкции V- образной формы. В передней части рамы имеется шарнир с крышкой для соединения с головной отливкой основной рамы. Снизу к раме приварены плиты для крепления поворотного круга 2 на передней плите крепиться также редуктор поворота отвала 7. На поперечной балке имеется три шарнира для крепления штоков цилиндров подъема отвала и выноса тяговой рамы.
Поворотный круг состоит из кольца с приваренными лапами и зубчатого венца 19 прикрепленного к кольцу болтами. Это дает возможность изменять положение венца относительно поворотного круга при неравномерном износе зубьев. К тяговой раме поворотный круг крепится с накладками 16 с регулировочными прокладками 18.
Отвал 11 крепиться к поворотному кругу двумя кронштейнами 12 установленными на штанге поворотного круга. На отвале установлены основные и боковые ножи реверсивного типа. При износе режущей кромки основных ножей перестановка их производится переворачиванием. При износе режущей кромки боковых ножей перестановка их производится выдвижением ( смешением на одно отверстие вниз) или переворачиванием.
Изменение угла резания отвала производиться гидроцилиндрами 13. Вынос отвала относительно тяговой рамы в обе стороны производится гидроцилиндром 3. Съемный кронштейн для крепления головки штока гидроцилиндра на отвале может быть передвинуть.
Поворот отвала в плане осуществляется редуктором 7 цилиндрическая шестерня которого входит в зацепление с зубчатым венцом поворотного круга.
Гидравлический шарнир 4 закрепленный на поперечной балке тяговой рамы служит для подвода рабочей жидкости к гидроцилиндрам изменения угла резания отвала и выноса отвала.
Описание кинематической схемы
Первичный вал 18 коробки передач вращается на подшипниках посаженных в корпусе. На первичном валу на шлицах закреплена ведущая шестерня 17 которая находится в постоянном зацеплении с шестерней 14 вторичного вала 15. Кроме того на первичном валу на подшипниках посажены шестерня16 находящаяся в постоянном зацеплении с шестернями 13 и 19 и шестерня 7 которая находиться в постоянном зацеплении с шестерней 6 промежуточного вала. На первичном валу на шлицах закреплена шестерня 8 по которой скользит зубчатая муфта 9.
На вторичном валу на подшипниках посажены шестерни 10 и 13 и на шлицах шестерни 14 и 11. По шестерни 11 скользит зубчатая муфта 12. Зубчатые муфты 9 и 12 управляются рычагом из кабины водителя. На промежуточном валу 21 на шлицах неподвижно закреплены шестерни 561920. Шестерни 5 и 20 находятся в постоянном зацеплении соответственно с шестернями 27 и 22 ведомого вала посаженными на подшипниках. По шестерне 26 закрепленной неподвижно на шлицах на ведомом валу 23 скользит зубчатая муфта 24 управляемая рычагом из кабины водителя.
Коробка передач соединена с муфтой сцепления двигателя карданным валом 2 для остановки которого установлен тормозок 1.
Задний мост служит для увеличения крутящего момента подводимого к нему от коробки передач и передачи его на колеса. Задний мост состоит из редуктора моста и двух бортовых редукторов (балансира). Редуктор моста соединяется с коробкой передач карданным валом 4 и состоит из смонтированных в одном блоке главной передачи с дифференциалом и двух планетарных передач.
Главная передача – коническая одинарная. Ведущая коническая шестерня 27 вращается на двухрядном коническом роликовом подшипнике. Ведомая коническая шестерня 28 закреплена на ступице дифференциала представляющим собой двухстороннюю зубчатую муфту свободного хода бесшумного типа. Корпус дифференциала вращается на шариковом подшипнике и двухрядном коническом роликовом подшипнике. Передача крутящего момента от главной передачи на колеса осуществляется валами 29 планетарными передачами через шестерни 32 редуктора моста и шестерни 33 34 правого и левого балансиров на колесные валы 35 на которых закреплены ступицы с установленными на них колесами и колесными тормозами 36.
На редукторе заднего моста установлен стояночный тормоз 3 дискового типа диск которого закреплен на фланце входного вала этого редуктора. Стояночный тормоз через систему рычагов и тяг управляется из кабины водителя.
Патентный поиск с целью проверки изделия на патентную чистоту
1 Характеристика объекта разработки
Объектом разработки является самоходная машина- автогрейдер основным рабочим органом которой является отвал с ножом.
Ретро-спектив-ность (за какой период)
Источники информации
Страны (68) и классификационные индексы предмета поиска (МКИ) (79)
Рефе-ратив-ный журнал
О патентном поиске при исследовании автогрейдера
Наименование источника
Классификационные индексы предмета поиска
№ авторских свидетельств патенты или периодические издания
5 Библиографический перечень
Отобранной в процессе поиска информации (указываются изобретения непосредственно относящиеся к исследуемому объекту).
№ авторского свидетельства
Название изобретения
Рабочий орган автогрейдера
Трехосный автогрейдер
Система автоматического управления рабочим органом автогрейдера
Отобранная в процессе поиска информация.
№2134328 Изобретение относится к строительно-дорожным машинам а именно к гидроприводам автогрейдеров. С целью создания более надежной и с большим быстродействием системы защиты отвала автогрейдера в автогрейдере включающем основную и тяговую рамы соединенные между собой гидроцилиндром перемещения и двумя гидроцилиндрами подъема тяговой рамы поршневые полости гидроцилиндров подъема соединены с поршневой полостью гидроцилиндра перемещения тяговой рамы через два обратных клапана а штоковая полость этого гидроцилиндра соединена с напорным клапаном который в свою очередь соединен через два обратных клапана со штоковыми полостями гидроцилиндров подъема отвала при этом отношение площадей штоковых и поршневых полостей гидроцилиндров должны удовлетворять условию Sn1Sш1 Sn2Sш2 где Sn1 - площадь поршневой полости гидроцилиндра подъема тяговой рамы; Sш1 - площадь штоковой полости гидроцилиндра подъема тяговой рамы; Sn2 - площадь поршневой полости гидроцилиндра перемещения тяговой рамы Sш2 - площадь штоковой полости гидроцилиндра перемещения тяговой рамы.
№2184813 Изобретение относится к землеройно-транспортным машинам типа автогрейдеров. Рабочий орган автогрейдера состоит из центральной двух боковых секций и гидроцилиндров их выдвижения. Каждый гидроцилиндр связан с соответствующей боковой секцией с помощью шарнира представляющего корпус образованный стаканом и втулкой который своим стаканом закреплен на конце штока гидроцилиндра а втулкой охватывает верхний конец пальца который своим нижним концом шарнирно соединен с верхней частью наружного конца соответствующей боковой секции. Центральная секция снабжена с тыльной стороны винтовыми направляющими "шевронного" типа с подъемом в направлении от торцов к середине центральной секции в которых посредством ползунов установлены боковые секции. Каждая боковая секция имеет длину l=(L2)-025 м где L - длина центральной секции. Увеличивается производительность планировочных работ упрощается конструкция рабочего органа.
№2200799 Трехосный автогрейдер относится к землеройно-транспортным машинам и предназначен для планировки грунта при строительстве и ремонте дорог а также для скоростной очистки дорог площадей и аэродромов от снега. Трехосный автогрейдер содержит тягач имеющий две задние ведущие оси с установленными на них колесами и связанную с ним хребтовую балку с передней поддерживающей осью на которой установлены колеса. Колеса на задних ведущих осях выполнены управляемыми. Хребтовая балка балансирно соединена с тягачом а колеса на передней поддерживающей оси выполнены свободно поворачивающимися. Одна из задних ведущих осей тягача и передняя поддерживающая ось установлены на поперечно качающихся осях. Повышаются планирующая способность и производительность автогрейдера.
№2006123158 Система автоматического управления рабочим органом автогрейдера содержащая датчик действительной скорости движения машины датчик объема грунта задатчик опорных сигналов управляющий блок включающий в себя устройство ввода постоянное запоминающее устройство к выходам которых подключен однокристальный микроконтроллер присоединенный своим выходом к устройству вывода и исполнительный механизм состоящий из электрозолотников подключенных своим входом к устройству вывода и гидроцилиндров присоединенных входом к выходу электрозолотников и управляющих заглублением или выглублением рабочего органа отличающаяся тем что с целью достижения максимально возможной текущей производительности автогрейдера при высоком качестве получаемой поверхности в процессе планирования грунта управляющим воздействием служит изменение угла захвата косопоставленного отвала для чего она снабжена одним дополнительным гидроцилиндром обеспечивающим стабильную возможность непрерывного управления поворотом отвала во время разработки грунта причем в исполнительном механизме системы автоматического управления используются не гидроцилиндры применяемые для заглубления и выглубления рабочего органа а стандартное устройство поворота отвала и один дополнительный гидроцилиндр для поворота отвала относительно продольной оси машины присоединенный своим входом к выходу электрозолотников к другому выходу которых присоединено своим входом стандартное устройство поворота отвала которые в результате совместной работы увеличивают или уменьшают угол захвата рабочего органа что приводит к отсутствию управляющих воздействий в виде вертикальных перемещений отвала в процессе планирования грунта.
Указанные изобретения в разработанном проекте автогрейдера не применяются. Следовательно разработанный проект автогрейдера обладает патентной чистотой по отношению к зарегистрированным на территории России указанным выше патентам.
Расчет и проектирование автогрейдера
1 Мощность двигателя
Сила тяжести G – главный параметр автогрейдера
где коэффициент учитывающий неравномерность в сечении стружки
при отдельных проходах автогрейдера ;
- площадь поперечного сечения кювета глубина кювета (03 08 м)
удельное сопротивление грунта копанию; если учесть не только
резание но и перемещение грунта как перед отвалом так и вдоль
него то можно полагать что кН м;
коэффициент для колесной формулы ;
коэффициент сцепления для растительного покрова
число проходов обычно составляет .
Максимальная свободная сила тяги автогрейдера
где коэффициент для колесной формулы ;
G – сила тяжести автогрейдера.
Развивающая на ведущих колесах общая мощность
мощность расходуемая на вырезание грунта (полезная мощность);
мощность расходуемая на передвижение автогрейдера как тележки;
мощность расходуемая на буксование.
где коэффициент сцепления ;
сила тяжести автогрейдера кН;
фактическая рабочая скорость автогрейдера кмч;
Мощность расходуемая на передвижение автогрейдера как тележки
где коэффициент сопротивления движению автогрейдера
Мощность расходуемая на буксование
коэффициент сопротивления движению автогрейдера
коэффициент буксования =018 022;
фактическая рабочая скорость автогрейдера кмч
Мощность двигателя для транспортного режима
где коэффициент буксования =004 0045;
к.п.д. трансмиссии - для механической;
заданная максимальная скорость автогрейдера кмч; =35 50 кмч
Необходимая мощность двигателя
где развивающая на ведущих колесах общая мощность;
коэффициент снижения мощности двигателя ввиду неустановившейся нагрузки =09;
к.п.д. трансмиссии - для механической.
На автогрейдер устанавливается двигатель ЯМЗ 236 Г-2 мощностью 110 кВт.
При работе автогрейдера по вырезанию и одновременному перемещению грунта необходимая сила тяги находится по формуле:
где сопротивление перемещению автогрейдера как тележки;
сопротивление сил инерции при трогании с места;
сопротивление грунта резанию;
сопротивление перемещению призмы волочения;
сопротивление от перемещения грунта вверх по отвалу;
сопротивление от перемещения грунта вдоль отвала (в сторону).
где G- общая сила тяжести машины;
- коэффициент сопротивления движению автогрейдера f=007-010;
где скорость машины принимаем для расчета скорость первой передачи
коэффициент учитывающий инерцию вращающихся масс
трансмиссии и двигателя
масса машины М=13120 кг.
где удельное сопротивление грунта резанию кН м;
h – толщина стружки h=(008 012)Н=012*620=744м; где H – высота отвала.
где сила тяжести грунта в призме волочения;
коэффициент трения грунта о грунт ;
где объем призмы волочения;
объемная масса грунта кг м;
ускорение силы тяжести.
где длина призмы L=3680мм=368м;
высота призмы Н=550мм=055м;
поправочный коэффициент .
коэффициент трения грунта о сталь ;
Условие движения автогрейдера без пробуксовки. Необходимо чтобы сила тяги на ведущих колесах превышала общее сопротивление. Для реализации этого тягового усилия должно соблюдаться неравенство
Условие выполняется.
3Расчет производительности автогрейдера
Часовая производительность по объему (мч) вырезанного грунта может быть выражена зависимостью
где V- объем призмы грунта вырезанной и перемещенной отвалом за один
коэффициент использования времени;
t- время рабочего цикла ч.
Время рабочего цикла определяется по формуле
где время прохода по участку которое определяется по его длине и скорости движения машины C;
время подъема и опускания отвала мин; ;
продолжительность поворота автогрейдера в конце участка включая
время затрачиваемое на переключение скоростей .
4Определение сил действующих на автогрейдер
На рисунке 5.4.1 представлена схема сил действующих в процессе резания грунта. Автогрейдер устроен с применением самой распространенной колесной формулы: . Действующие на автогрейдер силы можно разделить на активные и реактивные.
Рисунок 5.4.1 – Силы действующие на автогрейдер
К активным силам относятся сила тяжести и окружная сила на ведущих колесах ; к реактивным - вертикальные реакции на колесах и силы сопротивления грунта перекатыванию колес и реакция грунта действующая на отвал которая может быть разложена на горизонтальную и вертикальную составляющие а также боковые реакции направленные вдоль осей автогрейдера и . Последние образуются за счет сил сцепления развивающихся на поверхностях контактов колес с грунтом.
Здесь допускается что реакция грунта направлена перпендикулярно отвалу а реакции и на правых и левых колесах равны и направлены по их вертикальным осям. Кроме того допускается что реакции на всех ведущих колесах одинаковы. Известными являются силы и а неизвестными - ; ; ; ; ; ; и . Определить эти неизвестные силы можно по уравнениям равновесия:
при этом должны быть учтены следующие соотношения между силами:
Выражаем из 4-го уравнения :
Выразим из 1-го уравнения :
Подставив найденные значения и в 3-е уравнение найдем :
Подставим и найдем и :
Сила будет находится из 5-го уравнения:
Сила будет находится из 2-го уравнения:
Сила стремиться повернуть машину вокруг центра тяжести. Такому повороту препятствуют силы сцепления и поэтому должна быть проверена устойчивость машины в горизонтальной плоскости во время работы. При таком расчете следует принять максимальное значение которое может быть определено из следующего уравнения:
Устойчивость машины определится неравенством
Здесь горизонтальные силы и должны быть определены по условиям сцепления:
5Расчет механизмов управления
Для того чтобы обеспечить бесперебойную работу машины необходимо иметь достаточные скорости управления различными рабочими органами автогрейдера. Так например при перегрузке двигателя когда есть опасность его остановки нужно быстро разгрузить отвал путем подъема его из грунта. Быстрое управление отвалом бывает также необходимым при планировочных работах когда требуется менять его установку в соответствии с рельефом местности.
Механизм подъема отвала рассчитывается исходя из таких предпосылок. Рабочий ход механизма подъема должен обеспечивать заданную глубину копания возможность полного выглубления отвала и удовлетворять условиям проходимости автогрейдера в транспортном положении. При расчете механизма подъема в соответствии с рисунком 5.5.1 определяют подъемное усилие необходимое для выполнения этой операции мощность.
Подъемное усилие рассчитывается при выглублении отвала опущенного в грунт одним концом. Предполагается что угол захвата равен и на отвал действуют силы и .
Рисунок 5.5.1 - Расчетная схема для определения усилия подъема рамы автогрейдера
Тогда согласно схеме этого рисунка
где сила тяжести тяговой рамы с отвалом; здесь можно принять
Считается что в этом случае автогрейдер реализует полное усилие тяги по сцеплению. Тогда
коэффициент для колесной формулы .
Мощность привода механизма находится по формуле:
- скорость подъема отвала принимается равной 009 018 мс;
Поворот отвала в горизонтальной плоскости осуществляется зубчатым редуктором или гидравлическим приводом. Последний может быть выполнен в виде гидродвигателя. В связи с тем что поворот отвала производится лишь при полном его выглублении из грунта затрачиваемая на это мощность незначительна поэтому может не рассчитываться.
6Расчет ходового оборудования
На ходовое устройство автогрейдера действуют усилия являющиеся следствием как силы тяжести машины так и сил действующих со стороны грунта на отвал.
Тележка заднего моста в обычных условиях находится под воздействием реакции и боковых сил . Кроме того оси находятся под воздействием крутящих моментов и . Ранее для упрощения было принято что реакция со стороны грунта для передних и задних колес тележки одинаковы. Однако в действительности ввиду действия подводимого от двигателя крутящего момента реакции неодинаковы.
В соответствии с рисунком 5.6.1 балансир представляет собой систему зубчатых передач где вращение ходовым колесом передается от центральной шестерни через промежуточные зубчатые колеса.
Рисунок 5.6.1 - Схема балансира
Реакции и находятся из уравнения равновесия системы относительно оси подвески балансира с учетом того что
где часть действующей на тележку силы тяжести машины.
где передаточное число от ведущего вала балансира к осям ведущих
к.п.д. балансирной передачи
Здесь расстояние от оси подвески балансира до горизонтальной оси колес.
7Определение нагрузок действующих на раму автогрейдера
7.1 Расчетный случай I.
На раму автогрейдера действует максимальные нагрузки возникающие в условиях нормальной эксплуатации в соответствии с рисунком 5.7.1. Такие условия имеют место в конце зарезания когда передний мост вывешен и упирается в край кювета; задние колеса буксуют на месте отвал установлен под углом 45о и режет одним краем а автогрейдер наклонен под некоторым углом к горизонту
Рисунок 5.7.1 - Схема сил действующих в I случае
Силы и реакции действующие на автогрейдер сосредоточены в следующих точках.
Точка О – конец режущей кромки ножа отвала. Действуют горизонтальное усилие RX боковое RY и вертикальное RZ.
Точки О1 О2 – проекции середин балансиров на опорную поверхность. Действующие реакции и силы: вертикальные реакции Z1 и Z2 силы тяги X1 и X2 боковые реакции Y1 и Y2.
Точка О3 – касание переднего колеса края кювета соответствующее нижнему концу вертикального диаметра передних колес. Действует боковая реакция Y3 .
Вес сосредоточен в центре тяжести автогрейдера определяемом координатами Н и l2 .
Высота расположения центра тяжести
где rc – статический радиус колес.
где В– база автогрейдера.
Силы инерции действуют на машину в процессе торможения. Равнодействующая этих сил Рj приложена в центр тяжести и состовляет
где – коэффициент динамичности ;
– коэффициент использования сцепного веса;
– вес автогрейдера приходящийся на задний мост
Силы и реакции находятся из соотношений:
Определяем усилия в переднем шаровом шарнире приложенные в точке О4:
Рисунок 5.7.2 - Схема сил действующих на передний шаровой шарнир
7.2 Расчетный случай II.
Этот случай соответствует действию нагрузок возникающих при встрече автогрейдера с труднопреодолимым препятствиями. На величину нагрузок основное влияние оказывает масса машины и препятствия и скорость в момент столкновения. Наибольшее значение динамические нагрузки достигают в режиме планировки или перемещения грунта в связи с высокой скоростью выполнения указанных работ составляющей 5 7 кмч при малом буксовании ведущих колес. Ось поворотного круга лежит в плоскости продольной симметрии автогрейдера отвал выдвинут в сторону. Этот случай соответствует рисунку 5.7.3.
Рисунок 5.7.3 - Схема сил действующих во II случая
В точке О (точка контакта с препятствием) действуют силы и . В центре тяжести машины действуют вес и дополнительное динамическое усилие .
Дополнительная динамическая нагрузка
где m – масса автогрейдера;
v – скорость автогрейдера в момент встречи с препятствием;
c – суммарная жесткость 6 20 кНсм.
Силы и реакции находятся из следующих соотношений:
Определяем усилия в переднем шаровом шарнире для II случая:
8 Расчет рамы автогрейдера в САПР АПМ WinMachine
Рама автогрейдера является основным несущим элементом автогрейдера на котором монтируют все силовые агрегаты рабочее и ходовое оборудование. Она изготавливают из профильного проката или отдельных листов свариваемых между собой.
Рама автогрейдера изготовляется из низколегированной стали 09Г2С. Эта сталь имеет по сравнению со сталью Ст3 более высокие механические свойства (временное сопротивление и предел текучести) повышенную стойкость против атмосферной коррозии и меньшую хладноломкость лучшую износостойкость. Применение низколегированных сталей приводит к уменьшению массы металлоконструкции примерно на 15%. Маркируется двумя цифрами показывающими содержание углерода в сотых долях процента. Также содержит 2 % марганца и 1 % кремния.
Название вида: Произвольный Вид
Количество стержней 24
Хрептовая балка (0)
Подмоторная балка (1)
Полка 50 * 200 мм (2)
) Загружение 0 Множитель собст. веса 0
Таблица: Нагрузки на узлы Загружение: Загружение 0
Коэф. температурного расширения [°C]
Коэф. теплопроводности [Вт(°C*мм)]
модели 1045.586843 [кг]
Центр тяжести модели ( 3704.258155 750.000000 148.794750 ) [мм]
Моменты инерции модели ( 21160002000.111843 922052289.126651 62073063.192016 ) [кг*мм*мм]
Список поперечных сечений
Поперечное сечение 0
Площадь 11122.18 кв.мм
Центр масс: X= -0.007 Y= 41.775мм
относит. оси X 169872894.89мм4
относит. оси Y 150520506.10мм4
полярный 320393400.99мм4
Угол наклона главных центральных осей 0.01градус
Поперечное сечение 1
Площадь 5381.25 кв.мм
Центр масс: X= -0.000 Y= 0.001мм
относит. оси X 38500291.81мм4
относит. оси Y 6559724.88мм4
полярный 45060016.69мм4
Поперечное сечение 2
Площадь 9999.85 кв.мм
Центр масс: X= -0.001 Y= 0.000мм
относит. оси X 2079774.01мм4
относит. оси Y 33328392.62мм4
полярный 35408166.63мм4
Угол наклона главных центральных осей 0.00градус
Таблица: Перемещения узлов (Загружение 0)
Линейное перемещение [мм]
Угловое перемещение [градус]
Усилия в узлах стержней (Загружение 0)
Индекс стержня 0 (Rod 10)
Индекс стержня 1 (Rod 11)
Индекс стержня 2 (Rod 12)
Индекс стержня 3 (Rod 13)
Индекс стержня 4 (Rod 14)
Индекс стержня 5 (Rod 15)
Индекс стержня 6 (Rod 16)
Индекс стержня 7 (Rod 17)
Индекс стержня 8 (Rod 19)
Индекс стержня 9 (Rod 20)
Индекс стержня 10 (Rod 21)
Индекс стержня 11 (Rod 22)
Индекс стержня 12 (Rod 23)
Индекс стержня 13 (Rod 25)
Индекс стержня 14 (Rod 26)
Индекс стержня 15 (Rod 27)
Индекс стержня 16 (Rod 28)
Индекс стержня 17 (Rod 29)
Индекс стержня 18 (Rod 30)
Индекс стержня 19 (Rod 36)
Индекс стержня 20 (Rod 37)
Индекс стержня 21 (Rod 38)
Индекс стержня 22 (Rod 39)
Индекс стержня 23 (Rod 40)
Общая масса конструкции 1045.59 кг
Напряжение в стержне (макс.) [Нм^2] (Загружение 0)
Карта результатов - Загружение 0
Гидравлическая система
Гидравлическая система автогрейдера состоит из бака двух гидронасосов распределителя гидроцилиндров гидромотора гидроруля гидроусилителей и трубопроводов.
Рисунок 6.1 - Схема гидравлическая
Н1Н2 - гидронасосы; МН1 МН3 - манометры; УС1УС2 - гидроусилители; КР1 КР5 - клапаны предохранительные; В1В2 - гидробаки; ЗМ1 ЗМ7 - гидрозамки; КЗ1 КЗ3 - клапаны замедлительные; М1 - гидромотор; Т - фильтр; Н3 - насос-дозатор (гидроруль); С1 С14 - гидроцилиндры; Р1 - гидрораспределитель; КРТ1 - клапан потока
Гидронасос расположенный с левой стороны дизеля служит для привода гидроруля. Правый гидронасос предназначен для привода всех остальных агрегатов.
Работа гидросистемы происходит следующим образом: рабочая жидкость из бака всасывается насосами и подается к распределителю и гидрорулю. При нейтральном положении рычагов распределителя полости всех гидроцилиндров и гидромотора заперты и рабочая жидкость от правого насоса пройдя через гидроусилители сцепления тормоза и распределитель сливается через фильтр в бак. Включая соответствующие рукоятки распределителя машинист направляет поток жидкости в соответствующую полость гидроцилиндра (другая полость соединяется при этом со сливом).
Рабочая жидкость от левого насоса проходит через гидроруль и сливается через тот же фильтр в бак. При повороте рулевого колеса жидкость через гидроруль подается в один из цилиндров поворота передних колес.
Бак гидросистемы состоит из двух баков соединенных между собой рукавом низкого давления. Они установлены в задней части подмоторной рамы и служат элементами капота.
К правому баку подсоединены всасывающие трубопроводы насоса НШ-50 дизеля.
К левому баку подключены всасывающий трубопровод насоса НШ-10 слив распределителей и дренаж. Для нормальной работы гидросистемы крышка левого бака должна быть плотно закрыта (для создания избыточного давления).
Маслоуказатели расположены на правом баке. Уровень масла следует проверять при неработающем дизеле. Уровень должен быть не ниже нижнего маслоуказателя и не выше.
Распределитель. Служит для управления потоком рабочей жидкости приводящим в движение исполнительные механизмы в гидроприводе. Под управлением потоком рабочей жидкости подразумевается изменение его направления регулирование его величины и запирание рабочей жидкости в полостях гидроцилиндров и гидромоторов. Применен гидроцилиндр секционного типа. Состоит из 10 секций собранных в один блок с помощью промежуточной плиты и шпилек. В первой секции имеется предохранительный клапан. Рычаги управления золотниками выведены в кабину. Рабочая жидкость подводится к распределительному устройству от насоса НШ-50.
При нейтральном положении золотников рабочая жидкость проходит через распределительное устройство на слив.
При включении золотника любой секции линия слива перекрывается и рабочая жидкость поступает по трубопроводу в полость гидроцилиндра другая полость гидроцилиндра в это время соединяется со сливом.
При повышении давления в напорной линии выше давления настройки открывается предохранительный клапан и рабочая жидкость проходит на слив.
Гидроцилиндры. С их помощью производится перемещение рабочего и другого оборудования автогрейдера. Гидроцилиндры автогрейдера однотипны по устройству. Гидроцилиндры подъема отвала наклдона колес выноса отвала выноса тяговой рамы и поворота колес имеют одинаковые диаметры гильзы поршня штока и уплотнения.
Гидроцилиндры поворота колес плунжерного типа одностороннего действия. Роль поршня в цилиндре выполняет шток.
Гидроцилиндры рыхлителя и бульдозера отличаются большим диаметром гильзы поршня штока и уплотнений.
На гидроцилиндрах наклона колес подъема отвала бульдозера и рыхлителя установлены гидрозамки. Они предназначены для запирания гидроцилиндров при неработающем двигателе или при повреждении трубопроводов от замка к распределителю.
Фильтры. Предназначены для очистки масла от механических примесей размером до 25 мкм. Они устанавливаются в сливных линиях и разделяются на магистральные и встроенные (в гидробаки) фильтры с бумажными фильтрующими элементами и сетчатыми фильтрующими дисками.
Гидробак. Емкость для рабочей жидкости служит для ее охлаждения и создания запаса на случай возможных утечек. Вместимость бака превышает вместимость всей системы в 15 раза и более. Его сваривают из штампованного листа и снабжают заливной горловиной с фильтром грубой очистки сапуном для связи полости бака с атмосферой сливным отверстием с пробкой и указателем уровня масла.
Трубопроводы. Разделяются на жесткие и эластичные. Жесткие трубопроводы изготавливаются из стальных труб (цельно-натянутые для проводов высокого давления и сварные – для низкого давления). Эластичные трубопроводы предназначены для подсоединения подвижных гидроагрегатов (гидроцилиндров). Их подсоединение осуществляется с помощью типовых быстроразъемных резьбовых соединений.
Электрооборудование машины
Рисунок 7.1 - Схема размещения электрооборудования на автогрейдере
34-блокфара; 56-аккумуляторная батарея; 78-стеклоочиститель; 9-фонарь; 10-плафон; 11-отопитель; 12 – стеклоомыватель электрический; 13 – преобразователь напряжения; 14 – датчик указателя уровня топлива; 15 – лампа подкапотная; 16 21 – сигнал звуковой; 17 - датчики; 18 – индикатор загрязненности фильтра; 19 – стартер; 20 – генератор; 22 – фара.
Система электрооборудования автогрейдера выполнена по однопроводной схеме с присоединением минуса на массу автогрейдера. Напряжение в сети 12 В.
Электрооборудование автогрейдера включает следующие основные группы:
- источники электроэнергии питающие электрическую схему;
- потребители электроэнергии обеспечивающих работу систем и механизмов автогрейдера;
- коммутационную аппаратуру и провода с помощью которой осуществляется включение потребителей электроэнергии защита электрической схемы ее монтаж;
- электрические провода.
Все электрооборудование размещается на машине согласно его функциональному назначению сообразуясь со схемой расположения механизмов удобством использования и управления электрооборудованием.
Источниками электроэнергии являются аккумуляторные батареи и генератор переменного тока.
На автогрейдере установлены две аккумуляторные батареи соединенные параллельно что обеспечивает получение общего напряжения 12 В. При пуске дизеля в цепи питания электростартера напряжение равно 24 В. Это обеспечивается переключателем соединяющим батареи последовательно. Питание остальных потребителей в этот момент осуществляется от одной батареи. Схема электрическая принципиальная приведена на чертеже.
Электрооборудование работоспособно только при наличии аккумуляторных батарей. При остановках автогрейдера в целях предупреждения разряда батарей необходимо отключить батарею выключателем «массы».
Основными потребителями электроэнергии на автогрейдерах являются стартер электродвигатели отопительной системы кабины вентилятора и стеклоочистителя контрольно-измерительные приборы фонари система освещения и сигнализации а так же автоматическая система управления отвалом в случае ее наличия.
Система освещения. Предназначена для освещения пути движения и зоны работы автогрейдера в темное время суток обозначения габаритов автогрейдера предупреждения о его поворотах остановках освещения рабочего места машиниста и пульта управления. К ней относятся дорожные (транспортные) фары рабочие фары лампы освещения щитков приборов фонари контрольных ламп указатели поворотов передние и задние фонари плафон. На автогрейдерах предусмотрена и переносная лампа со штепселем включаемая в электрическую цепь предназначенная для освещения мест подлежащих обслуживанию и ремонту.
Фара состоит из корпуса рефлектора с патроном стекла – рассеивателя лампы ободка с прокладкой и проводов. Корпус изготавливается из тонкого стального листа. Рефлектор служит для отражения световых лучей узким параллельным пучком на расстояние до 150 м. Его внутренняя поверхность серебрится хромируется и полируется.
Стекло – рассеиватель выполнен рифленым и служит для преломления световых лучей с целью получения нужного распределения освещенности на полотне дороги.
Лампы используемые в фарах подфарниках имеют крепление фланцевое и на шпильках. При фланцевом креплении ламп подпружиненные штифты патрона входят в прорези фланцев удерживая его на патроне. При креплении на шпильках радиально расположенные на цоколе ламп шпильки входят в Г-образные прорези патрона при нажатии подпружиненный контакт и повороте ламп в нем. Переключателем 13
Звуковая сигнализация. Применяется специальный электрический вибрационный звуковой сигнал питаемый от аккумуляторной батареи 6. Он состоит из корпуса 1 расположенной на его торце мембраны 7 с резонатором 5 электромагнита 3 с якорем 4 по оси которого проходит стержень 10 одной стороной связанный с мембраной и резонатором а другой действующий на контакты 1112 прерывателя цепи 9 электромагнита. Электропитание поступает на клеммы сигнала от аккумуляторной батареи 6 через массу и кнопку 2 сигнала находящуюся на щитке приборов в кабине. При нажатии этой кнопки возбуждается цепь; электромагнита якорь притягивается перемещая стержень 10 с мембраной и размыкая контакты 1112 прерывателя. Мембрана 7 возвращает якорь 4 и стержень 10 в исходное состояние и цикл повторяется. Для исключения искрения контактов в цепь сигнала введен конденсатор 13. Колебания мембраны и создают звук.
Рисунок 7.2 - Сигнал
-корпус; 2-кнопка; 3-электромагнит; 4-якорь; 5-резонатор; 6-аккумуляторная батарея; 7 – мембрана; 8 – перегородка; 9 - обмотка; 10–стержень; 11 12 – контакты прерывателя 13 – конденсатор
Аккумуляторные батареи. Устанавливают на автогрейдерах для питания электрическим током стартера при пусках двигателя а также другого электрооборудования при неработающем двигателе. На автогрейдерах применяют 12-вольтные свинцово-кислотные аккумуляторные батареи различной емкости (в ампер-часах). При необходимости увеличить емкость аккумуляторные батареи соединяют в группу параллельно. На тяжелых автогрейдерах используется электропитание напряжением 24 В. В этом случае две аккумуляторные батареи по 12 вольт соединяют последовательно. Для увеличения емкости к ним параллельно подсоединяется еще такая же групп аккумуляторов.
Рисунок 7.3 - Аккумуляторная батарея
– бак 2 – защитный щиток 3. 7 – отрицательный и положительный штыри 4 – пробка 5 – перемычка 6- крышка 8 – элемент
Каждая аккумуляторная батарея состоит из эбонитового или пластмассового бака 1 разделенного перегородками на шесть отсеков и вставленных в отсеки шести последовательно соединенных элементов 8. В отсеки бака запрессованы тонкостенные кислотостойкие вставки из пластмассы предохраняющие бак от разъедания кислотой. Каждый из шести элементов включает несколько положительно и отрицательно заряженных пластин специальной конструкции. Каждая пластина представляет собой отлитую из свинца с сурьмой (для прочности) решетку в которую впрессована так называемая активная масса т. е. смесь порошкообразного свинца или его окислов (свинцового сурика или свинцового глёта) с серной кислотой. После изготовления такие пластины подвергают многократным процессам зарядки и разрядки. Все пластины с одним зарядом соединяются в полублок общей свинцовой перемычкой с выводным штырем. Таким образом в каждом отсеке бака располагаются два полублока из положительных и отрицательных пластин с таким расчетом чтобы положительные пластины были закрыты с двух сторон отрицательными (поэтому отрицательных на одну больше). Это препятствует короблению положительных пластин при большом разрядном токе. В отсеки заливается электролит которым является раствор серной кислоты плотностью 124 131 гсм3. В эксплутационых условиях аккумуляторная батарея заливается в зависимости от климатического пояса различными по плотности растворами серной кислоты. Плотность электролита зависит от степени заряженности аккумуляторной батареи и с достаточной точностью для практических подсчетов можно принять что уменьшение плотности электролита на 001 гсм3 соответствует разряду батареи на 6 %.
От соприкосновения соседних пластин или замыкания их выпадающей активной массы предохраняют пористые прокладки (сепараторы) через которые легко проходит электролит. Их изготавливают из эбонита пластмассы и др. Элементы в сборе снизу в отсеках бака устанавливаются не на дно а на выступы дна что предохраняет их от замыкания при выпадании на дно активной массы. Сверху каждый элемент перекрыт пластмассовым
щитком 2 с многочисленными отверстиями дли пропуска электролита при
его заливе. Щиток предохраняет пластины от механических повреждений. Каждый отсек сверху закрыт крышкой 6 снабженной отверстием с пробкой 4. Для герметичности места соединения крышки с баком замазаны кислотоупорной мастикой. Через крышки зыведены штыри блока пластин. У соседних элементов штыря соединены междусобой перемычками 5. Крайние выступающие штыри 3 7 аккумуляторной батареи служат для подсоединения проводов от внешней электрической сети. Через отверстия в крышках производится заливка электролита и проверка его уровня а через отверстия в пробках выходят газы из отсеков батареи. Новые аккумуляторные батареи поставляются в сухом (без электролита) виде. Для приведения батареи в работоспособное состояние необходимо залить электролит и зарядить. Напряжение в одном заряженном элементе независимо от количества пластин всегда равно примерно 2 В (при полной разрядке допустимо напряжение 17 В). При последовательном соединении элементов пропорционально растет только напряжение батареи но не ее емкость. Все данные по аккумуляторной батарее заложены в ее маркировке. На автогрейдере установлены батареи марки 6СТ-182ЭМ обозначает последовательно: 6 – число элементов СТ – стартерного типа 182 – емкость в ампер-часах Э – эбонитовый бак М – мипластовый сепаратор.
Генератор. Предназначены для питания электрооборудования и зарядки аккумуляторной батареи во время работы двигателя. Хотя они могут быть переменного и постоянного тока чаще всего применяются генераторы переменного тока отличающиеся простотой и надежностью.
Рисунок 7.4 - Генератор
– обмотка возбуждения ротора 2 – ротор 3 – обмотка статора 4- статор 5 11 – крышки 6 8 – кремнивые вентили. 7 – корпус выпрямителя 9 – крыльчатка 10 – шкив
Такие генераторы состоят из статора 4 собранного из электротехнической стали с надетыми на выступы статора девятью катушками 3 трехфазной обмотки стального ротора 2 имеющего форму шестилучевой звезды с обмотками возбуждения 1 двух крышек 511 с опорными подшипниками качения для вала ротора полупроводникового выпрямителя на кремниевых диодах установленного на передней крышке генератора и предназначенного для преобразования переменного трехфазного тока и приводного шкива 10 служащего для привода генератора от двигателя автогрейдера с помощью клиноременной передачи. На шкиве закреплена крыльчатка 9 вентилятора для создания потока воздуха с целью охлаждения выпрямителя и генератора. Выпрямитель в свою очередь состоит из алюминиевого корпуса 7 с тремя запрессованными в него кремниевыми диодами 8 с отрицательным потенциалом и изолированного теплоотвода с запрессованными диодами 6 с положительным потенциалом.
Генераторы должны работать с реле-регуляторами обеспечивающими автоматическое поддержание напряжения в заданных пределах а также нормальных режимов зарядки аккумуляторной батареи. Для этого реле-регуляторы содержат: регулятор напряжения поддерживающий величину напряжения при изменении оборотов двигателя и генератора; ограничитель силы тока предупреждающий перегрузку генератора при одновременном питании аккумуляторной батареи и электрооборудования; реле обратного тока автоматически включающее аккумуляторную батарею когда ЭДС генератора выше ЭДС батареи и наоборот выключающего аккумуляторную батарею когда ЭДС батареи выше ЭДС генератора чтобы исключить прохождение через генератор разрядного тока и тем самым защитить генератор от повреждений а аккумуляторную батарею от бесполезной разрядки.
Стартеры. Предназначены для проворачивания коленчатого вала двигателя при его пуске. В зависимости от напряжения в электрической системе автогрейдера применяют стартеры с напряжением в цепи 12 и 24 В. Стартер представляет собой электродвигатель постоянного тока питаемый непосредственно от аккумуляторной батареи снабженной выключателем и механизмом включения ведущей шестерни.
Рисунок 7.5 - Схема стартера с механическим включением и дистанционным управлением
– пусковая кнопка 2 – добавочное реле 3 – контакты добавочного реле 4 5 – обмотки сцепного реле 6 – якорь 7 – рычаг 8 – обгонная муфта 9 – ведущая шестерня 10 –пластина 11 – зубчатый венец маховика 12 – стартер 13 – аккумуляторная батарея
Так как этот электродвигатель имеет последовательное или смешанное возбуждение он обладает способностью развивать возрастающий крутящий момент при увеличении сопротивления на якоре что и требуется для пуска холодного двигателя автогрейдера. Крутящий момент достигает наибольшей величины при полном торможении якоря и при питании от полностью заряженной аккумуляторной батареи когда сила тока в цепи стартера достигает максимальной величины (до 800 А). Наиболее употребительны стартеры с механическим включением шестерни и дистанционным управлением. Стартер оснащен сцепным реле имеющим две обмотки 45 с расположенным внутри якорем 6 воздействующим через двуплечий рычаг 7 на обгонную муфту 8 с ведущей шестерней 9 для ввода ее в зацепление с зубчатым венцом 11 маховика. При включении пусковой кнопки 1 срабатывает добавочное реле 2 которое замыкает контакты 3 в цепи сцепного реле и вводит его в действие. В его обе обмотки 45 попадает ток создавая магнитное поле втягивающее якорь 6 а с ним вместе рычаг 7 который перемещает обгонную муфту 8 и шестерню 9 в направлении маховика. При этом толкатель якоря своей торцовой пластиной 10 замкнет цепь стартера 12 приводя его в действие и отключит цепь одной из обмоток якоря (что позволит увеличить силу тока в электродвигателе и соответственно крутящий момент на его валу).После пуска двигателя автогрейдера ведущая шестерня 9 стартера становится ведомой и срабатывает обгонная роликовая муфта 8 предотвращая ее воздействие на вал. Из зацепления с зубчатым венцом 11 маховика шестерню выводит после остановки стартера возвратная пружина.
Экономико-организационный раздел
При подготовке производства новых изделий необходимо проанализировать спрос на разрабатываемые изделия размеры финансирования на разработку проекта и освоение производства с целью обоснования целесообразности принятых решений которые определят экономический успех предприятия в случае успешной реализации новой продукции.
В связи с ограничением финансовых ресурсов и конкуренции в условиях рыночных отношений крайне важно на ранних стадиях конструкторской проработки оценить техническую и экономическую целесообразность проектов и своевременно прекратить финансирование неперспективных вариантов.
Вывод о целесообразности проектирования и производства новых видов продукции возможен с помощью предлагаемых методических указаний.
1 Оценка технической целесообразности конструкции изделия
Сравнительный анализ проектируемого изделия на техническом уровне является первым этапом оценки и отбора лучшего варианта.
- оценка технической целесообразности спроектированной конструкции на основании сравнения с аналогом по основным группам функционально-технических показателей;
- обеспечение расчета лимитной цены изделия.
Оценка выполняется в следующей последовательности:
1.1 Выбор перечня показателей оценки технического уровня конструкций
Все показатели используемые для оценки технического уровня конструкции можно классифицировать на:
- показатели назначения и тактико-технические данные изделия;
- конструкторские (специальные) показатели влияющие на функционирование изделия;
- общие конструкторские (технические) показатели влияющие на условия производства.
Таблица 8.1 Перечень показателей технического уровня и качества изделий.
Проектируемое изделие
Транспортная скорость
Коэф-т исп-ия материала
1.2 Оценка весомости (значимости) показателей
Оценка весомости показателей изделия осуществляется на основе экспертных оценок. Наиболее простым методом индивидуальной экспертизы используемым для оценки весомости показателей является метод попарных сравнений.
Результаты экспертизы представляются в виде матрицы (таблица 6) в которой на пересечении строки и столбца фиксируются индексы тех показателей которые являются более важными в оценке качества изделия при их попарном сравнении.
Далее для каждого показателя определяется количество предпочтений полученных им по отношению ко всем остальным показателям (в первой строке подсчитывается количество 1 во второй – 2 в третьей – 3 и т.д.). Полученное значение увеличивается на единицу.
Количественное представление весомости (значимости) показателей может быть получено по формуле:
где Кi – количество предпочтений i – го показателя.
Таблица 8.2 Матрица попарного сравнения показателей.
1.3 Расчет комплексного показателя технического уровня и качества конструкции
Комплексный показатель позволяет дать обобщенную оценку совокупной технической ценности изделия. В основе оценки лежит сравнение значений выбранного набора показателей базового и проектного варианта с эталонными значениями. В качестве эталонных могут использоваться наилучшие (идеальные) технически достижимые значения рассматриваемых показателей.
Комплексный показатель рассчитывается по формуле:
где q - безразмерный показатель качества по
r Относительный показатель качества по i - му параметру может быть рассчитан с помощью формулы:
где Pjn pjэ - количественные значения i - го показателя соответственно сопоставляемых вариантов и эталонного значения.
Первая формула используется для показателей при увеличении абсолютных значений которых возрастает обобщенный показатель в противном случае вторая формула.
Сопоставление комплексных показателей качества по потенциально воз
можным вариантам конструкций позволяет сделать вывод о технической целесообразности новой разработки определить коэффициент изменения качества при сравнении изделия с аналогом:
Где Wn Wб - комплексные показатели качества проектного и базового вариантов. Данный коэффициент используется при определении лимитной цены проектируемого изделия.
Таблица 8.3 Оценка технической целесообразности конструкции по вариантам (П - проектный Б - базовый).
Наименование показателей по
Коэффициент значимости
значимости показателя
Оценка вклада показателя
Коэф-т исп-я материала
Коэффициент изменения качества
2 Расчет трудоемкости ОКР
Многообразие существующих методов нормирования ОКР можно свести к трем основным: экспертному опытно-статистическому и расчетно аналитическому. Первый метод базируется на экспертных оценках второй -на сравнении нормируемого объекта с аналогичным нормативы на который известны третий - на корреляционных зависимостях трудоемкости работ от основных технических параметров изделия.
В основу предложенной методики по определению трудоемкости ОКР положен бальный метод.
С помощью бальных оценок по отдельным факторам определяется суммарный показатель объема работ в единицах сложности (баллы) который затем с помощью удельного норматива переводится в трудоемкость. Оценка факторов выполняется дифференцированно по главным узлам и видам работ.
Выделено два вида работ: расчетно-аналитические и чертежно-графические для которых порядок расчета объемных показателей различен.
Расчет выполняют в следующей последовательности:
Осуществляется сбор исходной информации о проектируемом объекте:
-наличие аналога или прототипа оценка общей сложности схемы объекта;
- состав главных узлов объекта;
-характеристики узлов (степень новизны конструкции количество кинематических пар количество оригинальных деталей объем конструкции по внешним контурам количество сложных деталей в узлах).
На основании значений исходных показателей таблицы 8.4 – 8.8 выбираются по каждому узлу нормативы объемов работ в баллах для первой и второй групп QH QH а также корректирующие коэффициенты к0 к1 к2 к3 к4. Результаты сведем в табл.8.9.
Таблица 8.4 Показатель объема работ 1-й группы в единицах сложности (баллах).
Характеристика группы новизны
Имеется близкий аналог (отличия не более 20%).
Имеется аналог с небольшими отличиями (20 – 50%).
Имеется прототип похожий по принципу действия и конструкции отдельных узлов. Отличается по многим параметрам.
Известен прототип из информационных и патентных источников. Нет чертежей.
Прототипа нет или он неизвестен.
Нет прототипа в основе конструкции лежит новая идея.
Таблица 8.5 Показатель объема работ 2-й группы в единицах сложности (баллах).
Группа насыщенности узла деталями
Примерное число оригинальных деталей
Таблица 8.6 Коэффициент К1 К2.
Группа сложности по числу кинематических пар
Таблица 8.7 Коэффициент К3.
Группа объемности конструкции узла
Объем по внешним контурам дм3
Таблица 8.8 Коэффициент К4.
Группа насыщенности узла сложными деталями*
Примерное количество сложных деталей
К сложным относятся детали имеющие сложную форму требующие при конструировании специальных расчетов а также расчеты размерных цепей.
Таблица 8.9 Исходные данные для расчета трудоемкости ОКР.
Характеристика объектов
Сложность схемы изделия
Новизна конструкции
Сложность узла по количеству кинематических пар
Насыщенность оригинальными деталями
Объем конструкции по внешним контурам
Насыщенность сложными деталями
Таблица 8.10 Коэффициент К0 учитывающий сложность и степень автоматизации схемы объекта.
Группа сложности схемы
Простейшая схема с одним энергопотоком без управления процессом.
Простая схема с разветвлением энергопотока с частично автоматическим или ручным управлением
Схема средней сложности с ветвящимся энергопотоком наличием блокировочных регулирующих и других элементов.
Сложная схема с автоматизацией рабочего цикла имеются взаимодействия механических электрически гидравлических и других связей в конструкции
Схема повышенной сложности с полной автоматизацией наличием обратных связей управление от устройства автоматики по заданной программе.
Осуществляется расчет показателей.
Показатель объема работ первой группы по узлу i определяется по формуле:
где QH - нормативное значение объема работ (первой группы в баллах) выбираемое в зависимости от группы новизны узла;
K1 - корректирующий коэффициент учитывающий влияние сложности узла по числу кинематических пар.
Показатель объема работ второй группы по узлу i определяется по формуле:
где QH2 - нормативное значение объема работ второй группы в баллах выбираемое в зависимости от количества оригинальных деталей в узле;
К2 К3 К4 - корректирующие коэффициенты учитывающие влияние группы сложности по числу кинематических пар группы объемности насыщенности узла сложными деталями соответственно.
Суммарная трудоемкость ОКР определяется по формуле:
Где tн - норматив удельной трудоемкости чел.-дн.бал. Норматив устанавливается на основе статистических данных по результатам проектирования аналогичных изделий;
Ко - коэффициент учитывающий сложность и степень автоматизации управления объектов в целом. Расчет трудоемкости ОКР проведем в табл.
Объем работ по группам в баллах
Расчетно-аналитические
Чертежно-графические
Норматив удельной трудоемкости на 1 балл чел - дн
Коэффициент сложности схемы К0
Трудоемкость ОКР чел – дн
3 Расчет временных и стоимостных затрат на проектирование изделия
Важными показателями используемые при технико-экономическом анализе изделия являются стоимостные затраты на разработку и срок реализации проекта.
Укрупненный способ расчета основанный на данных о трудоемкости ОКР известной структуре распределения трудозатрат по стадиям проектирования (таблица 8.12) и норматив длительности стадии (таблица 8.13).
Расчет реализуется в табличной (таблица 8.14) форме в следующей последовательности:
) по типу производства выбирается соотношение трудоемкости
стадий проектирования %; tуд;
) рассчитывается трудоемкость отдельных стадий проектирования
)по суммарной трудоемкости ОКР выбирается нормативная длительность цикла технического и рабочего проектирования Ттпи и Трпи
)определяется длительность цикла технологической подготовки
производства по формуле:
) определяется потребная численность исполнителей по стадиям проектирования:
где Fpн - месячный фонд времени работника (176 часов);
Квн - коэффициент выполнения нормы Квн=11 12.
) Определяется фонд заработной платы на разработку проекта:
где 3jм - средняя месячная заработная плата исполнителей
Нсн - коэффициент отчисления на социальные нужды (Нсн=26%);
) определяются полные затраты на разработку проекта:
где Кзп - удельный вес заработной платы в общей структуре себестоимости выбирается по статистическим данным (КЗП = 035 – 04);
) осуществляется оценка срока реализации проекта:
где Кпар - коэффициент параллельности учитывающий величину совмещения стадий (Кпар=07).
Таблица 8.12 Соотношение трудоемкости стадий проектирования %.
Стадии и этапы работ
Разработка ТЗ и эскизное проектирование
Техническое проектирование (ТП)
Рабочее проектирование (РП)
Технологическая подготовка
Проектирование технологических процессов
Проектирование спецоснастки
Таблица 8.13 Нормативы длительности стадий конструкторской подготовки производства.
Общая трудоемкость проектирования н–ч.
Длительность цикла мес.
Таблица 8.14 Расчет временных и стоимостных затрат на проектирование изделия.
Соотношение трудоемкости стадий проектирования %
Трудоемкость нормо-час
Длительность производственного цикла мес.
Потребное количество исполнителей чел
Средняя заработная плата исполнителей руб.
Фонд заработной платы по стадиям руб.
Общий фонд заработной платы на проектирование руб.
Оценка затрат на разработку проекта руб.
Оценка срока реализации проекта мес.
4 Прогнозирование себестоимости изделия
На стадии конструкторской подготовки проекта когда отсутствуют необходимые технологические документы и нормативы для расчета себестоимости приходится применять различные методы прогнозирования: удельных весов и коэффициентов приведения известной структуры себестоимости аналогов.
Прямыми стадиями определяющими себестоимость конструкции являются:
- затраты на основные материалы;
- затраты на комплектующие основные изделия;
- заработная плата производственных рабочих.
4.1 Расчет затрат на основные материалы
Расчет затрат на основные материалы при небольшом количестве деталей и узлов можно выполнять в целом по изделию.
Стоимость основных материалов определяется на основе норм расхода каждого вида материала и цен за вычетом стоимости отходов.
Расчет затрат на основные материалы производим в табличной форме.
Затраты на основные материалы по базовому узлу можно рассчитать по формуле:
Цм - цена материала руб;
Ц° - цена отходов руб;
Котх - средний процент реализации отходов (табл.8.15 );
Ктз - коэффициент транспортно-заготовительных расходов (Ктз=103 -107).
Таблица 8.15 Нормы планируемых отходов %.
Таблица 8.16 Расчет затрат на основные материалы.
Итого по базовому узлу руб.
С учетом транспортно-заготовительных расходов
4.2 Затраты на комплектующие покупные изделия
Затраты на покупные комплектующие изделия осуществляются на основе спецификаций применяемости Рij и цен Цкi по формуле:
Расчет затрат на комплектующие покупные изделия см. табл.8.17
Расчет затрат на комплектующие покупные изделия и полуфабрикаты по базовому узлу.
Двигатель ЯМЗ 236 Г-2
Редуктор поворота отвала
С учетом транспортно-заготовительных расходов руб.
Таблица 8.18 Расчет затрат на основные материалы в целом по изделию.
Комплектующие изделия
4.3 Расчет затрат на заработную плату производственных рабочих
На стадии конструкторской подготовки производства расчет заработной платы базируется на показателе удельной трудоемкости на 1 кг массы конструкции изделия аналога. При отсутствии таких данных для приближенных расчетов можно использовать усредненные отраслевые значения. Расчет заработной платы (основной и дополнительной) производственных рабочих.
Трудоемкость изделия
tуд - удельная трудоемкость 1 кг массы конструкции; G - масса конструкции.
Трудоемкость годового выпуска
Nг-прогнозируемый объм выпуска
Потребное количество основных производственных рабочих
Fpr - годовой действительный фонд времени одного рабочего
Годовой фонд ЗП основной и дополнительный
Зср-средняя заработная плата ОПР
ЗП с учетом отчислений на соц. нужды.
Нсн - коэффициент расходов на социальные нужды Нсн=26%
4.4 Расчет полной себестоимости изделия
Расчет полной себестоимости изделия осуществляется по формуле:
Нвн - норматив внепроизводственных расходов %; (для данного типа производства 7%);
З0и - заработная плата производственных рабочих на единицу изделия.
5 Определение прогнозируемой цены изделия
Лимитная цена выражает предельно допустимый уровень цены проектируемого изделия с учетом улучшения потребительских свойств изделия при котором обеспечивается относительное удешевление его для потребителя.
При отсутствии аналогов для сопоставления и невозможности определить полезный эффект от принципиально нового изделия лимитная цена определяется на основе укрупнённых нормативов материальных и трудовых затрат и повышенной по сравнению с нормативным уровнем рентабельности до 15 раз
где - плановая себестоимость изделия;
- плановый уровень рентабельности к себестоимости изделия.
6 Расчет уровня капитальных вложений в НИОКР и освоение производства
В условиях ограничения финансовых ресурсов технический и коммерческий успех проекта во многом определяется величиной новых капитальных вложений при его разработке и реализации. Капитальные затраты на всех этапах жизненного цикла изделия являются важной оценкой экономической эффективности новых проектов.
Единовременные затраты в сфере производства включают предпроизводственные затраты Кппз и капитальные вложения в производственные фонды завода изготовителя Кпф
Укрупненный расчет капитальных вложений в производственные фонды завода может производиться по формуле.
где Коб - капитальные вложения в оборудование и оснастку руб.;
Кос - капитальные вложения в оборотные средства руб.
где Цп - прогнозируемая цена изделия руб.;
Nе- прогнозируемый объем выпуска шт.;
- отраслевой норматив удельных капитальных вложений в оборудование на один рубль объема реализации новых изделий
- коэффициенты учитывающие соответственно годовой объем
производства для данного типа производства соответственно 125 и 115.
Расчет прибыли на единицу изделия:
7 Оценка эффекта от производства и использования
Расчет экономической эффективности новых изделий основан на сопоставлении результатов и затрат в сфере производства и в сфере использования.
Формула расчета экономического эффекта:
где П – прибыль на одно изделие руб.; ЕН – нормативный коэффициент экономической эффективности ЕН=015; КУ – удельные капитальные вложения в производство рубшт; N – прогнозируемый годовой объем выпуска
Расчет экономической эффективности
8 Сводные показатели оценки экономической целесообразности
Заключительным этапом технико-экономического обоснования проектируемого изделия является составление таблицы показателей оценки экономической целесообразности конструкции (таблица 8.20).
Наименование показателя
Прогнозируемый объем выпуска
Единовременные капитальные вложения
Производственные затраты
Вложения в производство
Текущие издержки на производство
Полная себестоимость
Прибыль на единицу изделия
Прогнозируемая цена изделия
Экономический эффект
Срок реализации проекта
Вывод. Проведенные технико-экономическое обоснование производства автогрейдера выявило перспективность осуществления этого проекта. Проектируемое изделие по ряду технических показателей будет превосходить существующие аналоги. Проведенные экономические расчеты себестоимости и цены изделия позволяют определить планируемую прибыль и рентабельность а также годовой экономический эффект при производстве проектируемого изделия - автогрейдера.
Охрана труда и окружающей природы
Характеризуя условия использования машины устанавливают климатическую зону ее эксплуатации. Данный автогрейдер обычного исполнения предназначенный для районов с умеренным климатом (температура воздуха от -40 до 35 С относительная влажность 60 95%). Одновременно с разработкой узлов и систем машины на начальной стадии проектирования следует обеспечить безвредные и безопасные условия труда обслуживающего персонала.
Обзорность рабочей площадки из кабины оператора определяется конструкцией самой кабины местоположением относительно рабочих органов.
Рисунок 9.1 - Размещение органов управления машиной
- зона очень часто используемых и важных объектов;23- зоны часто и редко используемых объектов.
Хорошая обзорность не вызывает дополнительных движений обеспечивает удобство позы. Это повышает производительность и безопасность труда понижает утомляемость. Проектируя машину на специальном шасси местоположение кабины устанавливают из условия наилучшей обзорности. На основании рекомендаций инженерной психологии эргономике и результатов исследований расположение наиболее часто используемых органов управления назначают в соответствии с данными. Высота кабины автогрейдера должна позволять оператору работать стоя.
Выявляются уровни потенциальных вредностей и опасностей. Рассмотрим такие вредные факторы: шум вибрацию санитарно-гигиенические требования к воздуху рабочей зоны нормы выбросов вредных веществ и дымности отработавших газов.
Шум - это совокупность звуков неблагоприятно воздействующих на человека мешающих его работе и отдыху. ГОСТ 12.1.003-83
По характеру спектра шум следует подразделять: широкополосный с непрерывным спектром шириной более 1 октавы; тональный в спектре которого имеются выраженные дискретные тона. Тональный характер шума для практических целей устанавливают измерением в третьоктавных полосах частот по превышению уровня звукового давления в одной полосе над соседними не менее чем на 10 дБ.
Воздействие шума на человека может проявляться не только в виде специфического поражения органа слуха но и неблагоприятно воздействовать на многие другие органы и функции организма.
Кратковременное воздействие интенсивного шума приводит к временному понижению остроты слуха с быстрым восстановлением функций после прекращения действия фактора (адаптационная защитно-приспособительная реакция слухового органа). Длительное воздействие интенсивного шума может приводить к перераздражению клеток звукового анализатора и его утомлению а затем к стойкому снижению остроты слуха. Наиболее неблагоприятными с этой точки зрения являются высокочастотные (около 4000 Гц) импульсные шумы. Длительное воздействие шума свыше 75 дБ может привести к резкой потере слуха - профессиональной глухоте.
Помимо действия шума на органы слуха установлено его влияние и на центральную нервную систем которое проявляется в виде комплекса симптомов: раздражительность ослабление памяти апатия подавленность изменение кожаной чувствительности замедление скорости психических реакций расстройство сна и другое. При работе на фоне шума повышается расход энергии при одинаковой физической нагрузке значительно ослабляет внимание рабочего увеличивает число ошибок в работе в результате чего снижается производительность труда и ухудшается качество работы. Шум затрудняет своевременную реакцию рабочего что способствует возникнoвению несчастных случаев.
У лиц подвергающихся действию шума отмечаются изменения секреторной и моторной функций желудочно-кишечного тракта скорости дыхания и пульса возникновение сердечно-сосудистых заболеваний гипертонической болезни сдвиги в обменных процессах (нарушение основного витаминного углеводного белкового жирового солевого обменов). Шум с уровнем звукового давления 30 35 дБ является привычным для человека и не беспокоит его. Повышение уровня звукового давления до 40 70 дБ создает значительную нагрузку на нервную систему вызывая ухудшение самочувствия снижение производительности умственного труда а при длительном действии может явиться причиной невроза язвенной и гипертонической болезни.
Допустимые уровни звукового давления в октановых полосах частот уровни звука и эквивалентные уровни звука на рабочих местах следует принимать: для широкополосного постоянного и непостоянного (кроме импульсного) шума – по таблице 9.1.
Таблица 9.1 Допустимые уровни звукового давления в октановых полосах частот.
Вид трудовой деятельности рабочие места
Уровни звукового давления дБ в октановых полосах со среднегеометрическими частотами Гц
Уровни звука и эквивалентные уровни звука дБ А
Рабочие места водителей и обслуживающего персонала тракторов самоходных шасси прицепных и навесных сельскохозяйственных машин строительно-дорожных и др. аналогичных машин
Для тонального и импульсного шума – на 5 дБ меньше значений указанных в таблице.
Источники шума в автогрейдерах двигатели компрессоры коробки передач раздаточные коробки агрегаты гидропривода. Уровень интенсивности основного источника шума – двигателя равен 105 115 дБ для компрессоров и воздуходувок порядка 100 дБ для вибраторов – 105 110 дБ. В кабину шум проникает через воздушную среду через металлоконструкции при жестком креплении к ним источников шума и кабины. Эти конструкции могут усиливать действие первичных источников за счет резонирования отдельных элементов конструкций и стенок ограждений (капот стенки кабины приборные щитки) ненадежном креплении агрегатов к раме.
Для снижения шума могут быть применены следующие методы:
Уменьшение шума в источнике – наиболее рациональное средство борьбы с шумом. Шум механизмов возникает вследствие упругих колебаний машины в целом и ее отдельных частей. Причины этих колебаний – механические аэро- гидродинамические и электрические явления.
Снижение механического шума возникающего вследствие вибрации поверхностей машин и оборудования а также одиночных или периодических ударов сочленении деталей сборочных единиц или конструкций в целом достигается улучшением конструкции оборудования. Заменой по возможности зубчатых и цепных передач клиноременными и зубчато-ременными (снижение шума на 10—14 дБ); заменой подшипников качения на подшипники скольжения (снижение шума на 10—15 дБ); использованием металлов с большим внутренним трением; заменой где это возможно металлических деталей деталями из пластмасс. Эффективно (особенно для высоких тонов) применение демпфирования при котором колеблющаяся поверхность покрывается материалом с большим внутренним трением (резина пробка битум войлок и др.). Основными требованиями предъявляемыми к демпфирующим материалам должны быть высокая эффективность малая масса способность прочно удерживаться на металле и предохранять его от коррозии.
Причиной аэро- и гидродинамических шумов являются соответственно стационарные или нестационарные процессы в газах или жидкостях. Их снижение достигается прежде всего уменьшением скорости обтекания и улучшением аэро- и гидродинамики тел что приводит к уменьшению вихреоб-разования в струях а также путем звукоизоляции источника и установки глушителей.
Электромагнитные шумы возникают вследствие колебаний элементов электромеханических устройств под влиянием переменных магнитных сил — колебания статора и ротора электрических машин сердечника трансформатора и др. Снижение электромагнитного шума осуществляется путем конструктивных изменений в электрических машинах.
Уменьшение шума на пути его распространения путем установки звукоизолирующих преград в виде стен перегородок кожухов причем их эффективность возрастает с увеличением частоты шума.
Сущность звукоизоляции состоит в том что падающая на ограждение энергия отражается в гораздо большей степени чем проникает за ограждение.
Такие преграды имеют гладкую поверхность. При одной и той же толщине звукоизолирующей преграды эффект возрастает с увеличением числа слоев материала но при условии отсутствия жесткой связи между слоями.
Средствами индивидуальной защиты от шума являются вкладыши наушники и шлемофоны.
Вкладыши вставляют в наружный слуховой проход они бывают мягкие (эластичные и волокнистые) и твердые. Мягкие изготавливают из губки ваты марли ультратонкой стекловаты (иногда их пропитывают маслами воском смолами парафином); твердые – из пластмасс эбонита резины.
Вкладыши являются самыми дешевыми и компактными средствами защиты от шума однако недостаточно эффективными (снижение шума на 5-20 дБ) и в ряде случаев неудобными так как раздражают слуховой проход.
Наушники плотно облегают ушную раковину и удерживаются дугообразной пружиной (могут встраиваться в головной убор). Степень ослабления шума зависит от конструкции наушников и частоты шума причем наибольший эффект наблюдается на высоких частотах что необходимо учитывать при их использовании.
Шлемы применяют при воздействии шумов с уровнями более 120 дБ так как в этом случае шум действует непосредственно на мозг человека (через черепную коробку) и вкладыши и наушники не обеспечивают необходимой защиты.
Вибрация – это механические колебания воспринимаемые человеком как сотрясение. ГОСТ 12.1.012-2004. Колебания механических тел с частотой ниже 20 Гц воспринимаются организмом как вибрация а колебания с частотой выше 20 Гц — одновременно и как вибрация и как звук. В настоящее время на многих производствах вибрация является одним из наиболее распространенных вредных факторов воздействующих на работающих.
По способу передачи на человека вибрацию подразделяют:
- общая вибрация передающаяся через опорные поверхности на тело сидящего или стоящего человека;
- локальная вибрация передающаяся через руки человека на ноги сидящего человека и на предплечья контактирующие с вибрирующими поверхностями рабочих столов.
По источнику возникновения общая вибрация бывает:
категории — транспортная вибрация воздействующая на человека на рабочих местах самоходных и прицепных машин транспортных средств при движении по местности и дорогам (в том числе при их строительстве);
категории — транспортно-технологическая вибрация воздействующая на человека на рабочих местах машин перемещающихся по специально подготовленным поверхностям производственных помещений промышленных площадок;
категории — технологическая вибрация воздействующая на человека на рабочих местах стационарных машин или передающаяся на рабочие места не имеющие источников вибрации.
На оператора автогрейдера воздействует общая вибрация 1 категории. Общая вибрация с частотой менее 07 Гц (качка) хотя и неприятна но не приводит к вибрационной болезни. Следствием такой вибрации является морская болезнь которая наблюдается из-за нарушения нормальной деятельности органов равновесия (вестибулярного аппарата). При систематическом воздействии на человека общей вибрации с частотой более 1 Гц могут возникнуть стойкие нарушения опорно-двигательного аппарата центральной и периферической нервной системы системы пищеварения. Особенно опасны общие вибрации с частотами близкими к частотам собственного колебания человека так как в этом случае наблюдается явление резонанса (резкое усиление амплитуды собственных колебаний). Для стоящего наблюдается два пика на частотах 5-12Гц и 17-25 Гц; для сидящего – на частотах 4-6 Гц. Для головы такие частоты лежат в области 20-30 Гц. Начиная с частоты 40 Гц колебания тела под влиянием вибрации становятся во много раз меньше вибрирующей поверхности. Колебания рабочих мест с указанными частотами опасны так как могут вызвать механические повреждения и даже разрыв внутренних органов. Систематическое воздействие общих вибраций в резонансной и околорезонансной зоне может быть причиной вибрационной болезни – стойких нарушения физиологических функций организма обусловленных преимущественно воздействием вибраций на центральную нервную систему. Эти нарушения проявляются в виде головных болей головокружений плохого сна пониженной работоспособности плохого самочувствия нарушений сердечной деятельности.
При работе на автогрейдере появляются колебания незатухающего характера. Высокочастотные с частотой 20 Гц возникают из-за недостаточной уравновешенности двигателя карданных передач. Низкочастотные до 10 Гц появляются вследствие движения машины по неровностям опорной поверхности и в связи с непостоянством нагрузок на рабочем органе. Санитарными нормами ограничивается допустимый уровень вибрации 20 Гц на рабочих местах.
Ослабление вибрации в источнике - наиболее рациональное средство борьбы с вибрациями на момент проектирования. Выбор кинематических и технологических схем при которых динамические процессы вызванные ударами резкими ускорениями были бы исключены или предельно снижены (например замена: кривошипных механизмов равномерно вращающимися ковки и штамповки — прессованием). Уравновешивание балансировка вращающихся частей для обеспечения плавности работы машины. Устранение дефектов и разболтанности отдельных частей.
Чтобы уменьшить воздействие вибрации на машиниста и на остов машины необходима виброизоляция (введение в систему дополнительной упругой связи с целью ослабления передачи вибраций смежному элементу конструкции или рабочему месту) между рамой машины и такими элементами как двигатель коробка передач кабина приборы рычаги управления. Применяют виброизолирующие опоры типа упругих прокладок или пружин.
Пружинные виброизоляторы по сравнению с прокладками имеют ряд преимуществ. Они могут применяться для изоляции как низких так и высоких частот дольше сохраняют постоянство упругих свойств во времени хорошо противостоят действию масел и температуры относительно малогабаритны. Однако они могут пропускать высокочастотные колебания поэтому пружинные виброизоляторы рекомендуется в этом случае устанавливать на прокладки из упругих материалов типа резины (комбинированный виброизолятор) В кабине кресло оператора необходимо подрессоривать. Система должна обеспечивать только вертикальные перемещения кресла. На автогрейдерах следует устанавливать кресла с эластичной подвеской так как жесткое подрессоривание выполняют при частоте колебаний остова менее 2 Гц. Исходными данными для расчета виброизоляции рабочего места являются виброскорость = мс на частоте колебаний=5 Гц масса опорной поверхности =10 кг масса человека =80 кг. Расчет виброизоляции с использованием пружин:
По ГОСТ 12.1.012-90 ССБТ «Вибрационная безопасность. Общие требования» (табл. 1) для заданной частоты вынужденных колебаний =5 Гц допустимую виброскорость рабочего места =045 мс.
Необходимый для данной системы виброизоляции коэффициент передачи
Частоту собственных колебаний виброизолированного рабочего места Гц
Статическая деформация пружинных виброизоляторов м
где Гц – частота собственных колебаний рабочего места; мс2 – ускорение свободного падения.
Требуемая суммарная жесткость пружинных виброизоляторов Нм
Выбираем количество устанавливаемых пружин –
Жесткость одного виброизолятора Нм
Расчетная нагрузка на одну пружину Н
Диаметр проволоки для изготовления пружины м
где =12 – эмпирический коэффициент; =7 – отношение диаметра пружины к диаметру проволоки; – допускаемое напряжение материала пружины на кручение (для пружинной стали марки при Нм2).
Число рабочих витков пружины
где – модуль упругости на сдвиг (для стали Нм2).
Число нерабочих витков пружины
при (на оба торца пружины).
Полное число витков пружины
Также применяют вибродемпфирование уменьшение вибраций за счет увеличения силы трения демпфирующего устройства т. е. перевод энергии колебаний в теплоту и виброгашение (динамическое гашение колебаний) введение в колебательную систему дополнительных масс или увеличение жесткости системы.
В качестве средств индивидуальной защиты от вибрации применяют специальные рукавицы и специальную обувь изготавливаемые с использованием упругодемпфирующих материалов в соответствии с требованиями стандартов ГОСТ 12.4.002—97 «ССБТ. Средства защиты рук от вибрации» ГОСТ 12.4.010—75 «ССБТ. Средства индивидуальной защиты. Рукавицы специальные» ГОСТ 12.4.024—76 «ССБТ. Обувь специальная виброзащитная.»
3 Общие санитарно-гигиенические требования к воздуху рабочей зоны
Микроклимат – метеорологические условия внутренней среды кабины определяемые температурой воздуха относительной влажностью воздуха скоростью движения воздуха интенсивностью теплового излучения.
В кабинах пультах и постах управления технологическими процессами при выполнении работ связанных с нервно - эмоциональным напряжением должны соблюдаться оптимальные величины температуры 22-24 градуса относительной влажности 60-40% и скорости движения не более 01 мс.
Для обеспечения санитарных норм в холодное время года в кабину автогрейдера устанавливается отопительная система. В целях уменьшения теплопотерь стенки кабины выполняют двухслойными. Наружный слой представляет собой обшивку из стального листа толщиной 06 12 мм внутренний – картон или иной термоизоляционный материал (бумага войлок асбест кожа сталь стекло) толщиной до 4мм. При очень низких температурах атмосферного воздуха проектируют дополнительные термоизоляционные слои. Все соединения кабины герметизированы специальными резиновыми уплотнениями. Пол кабины покрыт войлочно-резиновым ковриком предназначенный как для теплоизоляции так и для уменьшения шума и вибрации на рабочем месте. Большое значение для нормализации воздушной среды в кабине имеет система вентиляция. В летний период теплота передаваемая от внешнего воздуха работающего двигателя и посредством солнечной радиации нагревает кабину. Чтобы снизить утомляемость оператора повысить производительность труда ее оснащают системой кондиционирования воздуха.
Содержание вредных веществ в воздухе рабочей зоны не должно превышать предельно допустимых концентраций (ПДК). Полный список вредных веществ и их ПДК приведен ГОСТ 12.1.005-88.
4 Светотехнические приборы машины и освещение территории
Для обеспечения безопасности движения и выполнения работ в темное время суток автогрейдер оборудуется осветительными приборами. Недостаточная освещенность строительных площадок утомляет операторов приводит к удлинению рабочего цикла машины снижению производительности труда а также резко повышает вероятность возникновения аварийной ситуации. Особую опасность представляют машины не оборудованные требуемыми осветительными приборами при движении ночью в потоке с другими транспортными средствами.
В соответствии с требованиями безопасности движения самоходные машины оборудуются: двухсветными фарами переднего света передними и задними габаритными огнями световыми указателями поворотов «стоп-сигналами» фонарями номерного знака. Цвет передних габаритных огней должен быть белый а задних – красный. При необходимости на автогрейдер устанавливаются дополнительные фары для освещения рабочих органов. Кабина оператора оборудуется осветительным плафоном в ней предусматривается подсветка приборного щитка.
Необходимо общее освещение рабочих площадок сигнальная разметка знаки. ГОСТ Р 12.4.026-2001 распространяется на сигнальные цвета знаки безопасности и сигнальную разметку для производственной общественной и иной хозяйственной деятельности людей строительных площадок и иных объектов где необходимо обеспечение безопасности предотвращения несчастных случаев устранение опасности для жизни вреда для здоровья людей.
5 Пожарная безопасность
Пожарная безопасность (ГОСТ 12.1.004-91) объекта должна обеспечиваться системами предотвращения пожара и противопожарной защиты в том числе организационно-техническими мероприятиями.
Противопожарная защита должно достигаться способами: применение средств пожаротушения применение конструкций и материалов в том числе используемых для облицовок конструкций с нормированными показателями пожарной опасности применение пропитки конструкций объектов антипиренами и нанесение на их поверхность огнезащитных красок и составов применение средств коллективной и индивидуальной защиты людей от опасных факторов пожара. Обязательна организация обучения работников правилам пожарной безопасности.
Необходимо соблюдать следующие правила. Запрещается курить и пользоваться огнеопасными предметами во время работы с горюче- смазочными материалами в холодное время года пользоваться факелами для разогрева масла в агрегатах автогрейдера во время заправки и при работающем дизеле производить монтажные и демонтажные работы. После заправки необходимо удалить подтеки горюче-смазочных материалов. Не допускается попадание горюче-смазочных материалов на агрегаты электрооборудования (генератор стартер и т.д.). Промасленный обтирочный материал хранить в закрытом металлическом ящике. Ремонтные работы связанные с искрообразованием и высокой температурой (сварочные паяльные и др.) производить не на автогрейдере за исключением деталей и узлов которые невозможно снять. Сварочные работы производить на расстоянии не менее 20 метров от машины. Соблюдать правила обращения с электролитом низкозамерзающими жидкостями и этилированным бензином. Для тушения воспламенившегося топлива применять огнетушители засыпать или покрыть его брезентом или войлоком.
Автогрейдер должен отвечать экологическим показателям: выбросы вредных веществ с отработавшими газами ГОСТ 17.2.2.05 – 97 дымность отработавших газов ГОСТ 17.2.2.02 – 98.
Значение удельных выбросов вновь изготовленных и капитально отремонтированных на ремонтных заводах дизелей тракторов и машин не должно быть более норм приведенных в таблице 9.2.
Таблица 9.2 Нормы удельных выбросов.
Наименование вредных веществ
Удельные выбросы г(кВт*ч) при воздухообмене
Нормы выбросов оксидов азота установлены по сумме оксидов азота приведенных к оксиду азота(IV)
Нормы выбросов углеводородов установлены по сумме углеводородов приведенных к условному составу С1Н185
Значение дымности на установившихся режимах вновь изготовленных и капитально отремонтированных на ремонтных заводах дизелей тракторов и машин не должно быть более норм приведенных в таблице:
Таблица 9.3 Нормы дымности.
Условный расход воздуха дм3с
Дымность м-1(%) не более при воздухообмене
7 Указания мер безопасности
- К работе на автогрейдере допускаются лица знающие устройство и правила эксплуатации и имеющие удостоверение на право управления автогрейдером.
- Работать на неисправной машине строго запрещается. К работе приступить убедившись в исправности всех механизмов и агрегатов обратив особое внимание на исправность рулевого управления колесных тормозов трансмиссии и дизеля.
- Во время работы пол кабины должен быть чистым и свободным от посторонних предметов посторонним лицам запрещается находиться в кабине и в зоне работы.
- Во время движения автогрейдера запрещается удалять из-под ножей посторонние предметы.
- Нельзя на ходу автогрейдера регулировать исправлять или смазывать его механизмы.
- Запрещается сидеть и стоять на раме рабочих органах и крыльях во время движения.
- При выполнении работ по ремонту или техническому обслуживанию следует надежно затормозить автогрейдер стояночным тормозом опустить рабочее оборудование на землю или подставки. Производить работы при работающем двигателе не допускается.
- Работы по техническому обслуживанию или ремонту должны производиться в специально отведенных местах где обеспечивается удобный доступ и хорошее освещение.
- Во время технического обслуживания и ремонта приборов электрооборудования выключить включатель «массы».
- Монтаж или демонтаж шин производить на стенде или чистом полу. При накачивании необходимо следить за показаниями манометра не допускается превышение давления воздуха выше нормы.
- При необходимости отлучиться от машины надо затормозить стояночным тормозом и заглушить двигатель. Нельзя оставлять автогрейдер на уклонах.
- Категорически запрещается при спусках с горы переключать передачи или выключать муфту сцепления. Спуск с горы производить на рабочих передачах.
- В случае невозможности транспортирования автогрейдера на специальное место для ремонта его необходимо оградить на месте вынужденной остановки или установить знаки аварийной остановки согласно «Правилам дорожного движения».
- После окончания смены машинист обязан предупредить сменщика о всех неисправностях автогрейдера.
- При пользовании домкратом необходимо придать ему устойчивое положение предупреждающее завал машины. Места установки домкратов под балкой переднего моста и под корпусами балансиров.
- Перед запуском дизеля поставить рычаг переключения передач в нейтральное положение и затормозить автогрейдер стояночным тормозом.
- Езда на автогрейдере при открытых незакрепленных дверях кабины запрещается. При движении на транспортных передачах двери должны быть закрыты.
- Рычаг распределителя управляющий положением кронштейна подвески гидроцилиндров подъема отвала тяговой рамы должен постоянно находиться в нейтральном положении. При установке отвала для срезания откосов запрещено находиться посторонним лицам в радиусе не менее 3-х метров.
- При транспортировании автогрейдера обращать особое внимание на выбор скоростей движения с учетом дорожных условий радиусов поворота видимости и обзорности.
- При транспортировании автогрейдера своим ходом на большие расстояния тяговую раму и бульдозерный отвал закрепить проволокой к основной раме. - Поворот (складывание) шарнирно-сочлененной рамы можно производить только на месте или в движении со скоростью не более 6 кмч (первая рабочая передача).
- Движение автогрейдера со сложенной рамой на транспортных передачах запрещается.
- При выносе отвала и поворота рамы следите за тем чтобы отвал не касался других частей машины.
В данном дипломном проекте был проведен сравнительный анализ различных вариантов исполнения автогрейдера выполнен патентный поиск с целью проверки изделия на патентную чистоту. Приведено описание устройства и работы выбранного варианта автогрейдера.
Определены основные параметры машины такие как масса и требуемая мощность двигателя. Был выбран двигатель соответствующий полученным значениям. Была определена часовая производительность по объему вырезанного грунта. На основе полученных параметров сделан тяговый расчет и в результате которого были найдены:
сопротивление перемещению автогрейдера как тележки;
Определены силы действующие на рабочее оборудование и раму: активные и реактивные. Был произведен расчет механизма управления для обеспечения бесперебойной работы машины. Рассчитано ходовое оборудование.
Определены силы возникающие во время работы и действующие на раму автогрейдера по данным которых проведен расчет основной рамы с использованием системы автоматизированного проектирования САПР АПМ WinMachine.
Приведены схемы гидравлической и электрической системы автогрейдера. Имеется описание работы и составных частей приведенных схем.
В экономическом разделе дипломного проекта проведено технико-экономическое обоснование производства автогрейдера. Проведенные экономические расчеты себестоимости и цены изделия позволяют определить прибыль годовой экономический эффект при производстве изделия.
В разделе охрана труда были выявлены вредные факторы влияющие на рабочего в результате эксплуатации автогрейдера. Предложены средства защиты от них.
Хархута Н. Я. Дорожные машины : теория конструкция и расчет Н. Я. Хархута М.И. Капустин В.П. Семенов И.М. Эвентов. - 2-е изд. перераб. и доп. – Л. : Машиностроение 1976. – 472 с.
Бородачев И. П. Справочник конструктора дорожных машин : cправочник Б. Ф. Бондаков С.А.Варганов М.Р. Гарбер и др.. - 2-е изд. перераб. И доп.– М. : Машиностроение 1973. – 504 с.
Холодов А. М. Проектирование машин для земляных работ : учеб. пособиеА.М. Холодов. – Х. : Вища. шк. Изд-во при Харьк. ун-те 1986. – 272 с.
Машины для землеройно-транспортных работ: отраслевой каталог ЦНИИТЭстроймаш. – М.:1989.-202 с.
Бандаков Б.Ф. Автогрейдеры: учеб. для подг. и повыш. квал-ции кадров и мастеров на пр-ве. Б. Ф. Бандаков. – М. : Транспорт 1988. – 301 с.
Абрамов Н. Н. Курсовое и дипломное проектирование. Учеб. пособие для студентов дорожно-строительных вузов. М. «Высш. школа» 1972. -120с.
Добронравов С. С. Строительные машины и оборудование: справочник С. С. Добронравов М.С. Добронравов. – 2-е изд. перераб. и доп.– М. : Высш. шк. 2006. – 445 с.
Плешков Д. И. Бульдозеры скреперы грейдеры. Учебник для средн. проф.-техн. учеб. заведений. Плешков Д. И. Хейфец М. И. Яркин А. А. Изд. 2е перераб. и доп. – М: Высш. шк. 1976. 320 с.
Папаев С. Т. Охрана труда. С.Т. Папаев - М.: ИПК Издательство стандартов 2003. - 400 с.
О дальнейшем стимулировании творческой активности молодых ученых : Пост. Совета Министров СССР от 26 янв. 1991 года № 231 Собр. законодательства РФ. - 1991. - № 6. – Ст. 117.
ГОСТ Р 51771 –2001. Аппаратура радиоэлектронная бытовая. Входные и выходные параметры и типы соединений. Технические требования. – Введ. 2002-01-01. – М. : Госстандарт России : Изд-во стандартов 2001. – IV 27 с. : ил.
ГОСТ 7.53-2001. Издания. Международная стандартная нумерация книг. - Взамен ГОСТ 7.53-86 ; введ. 2002-07-01. - Минск : Межгос. совет по стандартизации метрологии и сертификации ; М. : Изд-во стандартов сор. 2002. – 3 с. - (Система стандартов по информации библиотечному и издательскому делу).
А. с. 107970 СССР МКИ В25 J 1500. Устройство для захвата неориентированных деталей типа валов
В. С. Ваулин В. Г. Кемайкин (СССР). – № 336058525 -08 ;
заявл. 23.11.81 ; опубл. 30.03.83 Бюл. № 12. - 2 с. : ил.
Пат. 2187888 Российская Федерация МПК H 04 B 138 H 04 J 1300. Приемопередающее устройство Чуева В. И. ; заявитель и патентообладатель Воронеж. науч.-исслед. ин-т связи. - № 200013173609 ; заявл. 18.12.00 ; опубл. 20.08.02 Бюл. № 23 (II ч.). - 3 с. : ил.
Винтовой холодильный компрессор ВХ 1400-7-3 : каталог Центр. ин-т НТИ и техн.-экон. исслед. по хим. и нефт. машиностроению. – М. 1993. – 2 с.
Оптовые цены на инструменты с алмазной насечкой : прейскурант № 19-08 : утв. Госкомцен СССР 12.08.90 : ввод. в действие 01.01.91. – М. : Прейскурантиздат 1990. – 60 с.
Спиридонова В. И. Понятие свободы у М. Крозье и его критика В. И. Спиридонова МГУ им. М. В. Ломоносова. - М. 1984. – 24 с. – Библиогр.: с. 23-24. - Деп. в ИНИОН АН СССР 27.09.92 № 319097.
Белова С.В. Безопасность жизнедеятельности: Учебник для вузовС.В. Белов А.В. Ильницкая А.Ф. Козьяков и др. 4-е изд. испр. и доп. – М.: Высш. шк. 2004. – 606 с.
Гохберг М.М. Справочник по кранам: в 2 т. Т. 1. Характеристики материалов и нагрузок В.И. Брауде М.М. Гохберг И.Е. Звягин и др.-Л.:Машиностроение. Лен-ое отд-ие 1988.-536 с.
Техническое описание и инструкция по экспл-ции
автогрейдера ДЗ-180А ТО 1993. – 157 с.
Каталог деталей и сборочных единиц ДЗ-180А Каталог
Каталог на рус.англ.фр.и исп. яз. – Внешторгиздат
ГРМТИ 1993. – 127 с.
Крикун В.Я. Строительные машины: учебное Книга
пособие для вузовВ.Я. Крикун. –М.: АСВ2005.-232с. с 1 автором
Рекомендуемые чертежи
- 22.08.2014