Проектирование технологии изготовления отливки «Крышка муфты сцепления»




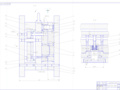
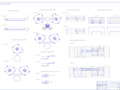
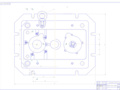
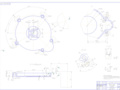
- Добавлен: 25.10.2022
- Размер: 953 KB
- Закачек: 1
Описание
Состав проекта
![]() |
![]() |
![]() ![]() ![]() |
![]() ![]() ![]() ![]() |
![]() |
![]() ![]() ![]() |
![]() ![]() ![]() |
![]() ![]() ![]() |
![]() ![]() ![]() |
![]() ![]() ![]() |
![]() ![]() ![]() |
![]() ![]() ![]() |
![]() ![]() ![]() ![]() |
![]() |
![]() ![]() ![]() ![]() |
![]() ![]() ![]() ![]() |
![]() ![]() ![]() ![]() |
![]() ![]() ![]() ![]() |
![]() |
![]() ![]() ![]() |
Дополнительная информация
Спецификация.CDW

Чертеж отливки.cdw

Отклонения размеров необрабатываемых поверх-
ностей по ГОСТ26645-85 кроме указанных особо.
МГТУ им. Н.Э.Баумана
Курсовой проект по ОТЛП
Спецификация2.dwg
Пружина тарельчатая 1-1-2-35x11x0.9x1.5
Штифт цилиндрический 12m6x50
Штифт цилиндрический 12m6x80
Спецификация.dwg
МГТУ им. Н.Э.Баумана
Плита крепления неподвижная
Стержень неподвижный
Плита крепления подвижная
Плита выталкивателей
Анализ вариантов.dwg
Выбор способа подвода металла
Выбор плоскости разъёма
Выбор конструкции стержней
Выбор способа выталкивания отливки
МГТУ им. Н.Э.Баумана
Выбор расположения отливок в форме.
Выбор крепления вкладышей в обойме.
Выбор конфигурации вентиляционных каналов.
Чертеж отливки.dwg
Отклонения размеров необрабатываемых поверх-
ностей по ГОСТ26645-85 кроме указанных особо.
МГТУ им. Н.Э.Баумана
Курсовой проект по ОТЛП
Спецификация2.cdw

Пружина тарельчатая 1-1-2-35x11x0.9x1.5
Штифт цилиндрический 12m6x50
Штифт цилиндрический 12m6x80
Анализ вариантов.cdw

Выбор способа подвода металла
Выбор плоскости разъёма
Выбор конструкции стержней
Выбор способа выталкивания отливки
МГТУ им. Н.Э.Баумана
Выбор расположения отливок в форме.
Выбор крепления вкладышей в обойме.
Выбор конфигурации вентиляционных каналов.
Чертеж пресс-формы 2.cdw

Чертеж пресс-формы 3.cdw

Чертеж пресс-формы 1.cdw

РПЗ.doc
ордена Ленина ордена Октябрьской Революции и ордена Трудового Красного Знамени Государственный Технический Университет имени Н. Э. Баумана
Расчётно-пояснительная записка
к курсовому проекту по ОТЛП.
студент: Гордеев А.Е.
Руководитель проекта:
Введение . . . . . . . . . . . . . . . . . . . . . . . . . . . . . . . . . . . . . . . . . . . . . . 3
Анализ вариантов . . . . . . . . . . . . . . . . . . . . . . . . . . . . . . . . . . . . . . 4
1 Выбор расположения плоскости разъёма . . . . . . . . . . . . . 4
2 Выбор расположения отливок в форме . . . . . . . . . . . . . . 4
3 Выбор варианта подвода металла . . . . . . . . . . . . . . . . . . . 4
4 Выбор конфигурации вентиляционных каналов . . . . . . 4
5 Выбор конструкции стержней . . . . . . . . . . . . . . . . . . . . . . 5
6 Крепление вкладышей в обойме . . . . . . . . . . . . . . . . . . . . 5
5 Выбор способа выталкивания отливки . . . . . . . . . . . . . . . 5
Определение количества отливок в форме . . . . . . . . . . . . . . . . . 5
Выбор машины . . . . . . . . . . . . . . . . . . . . . . . . . . . . . . . . . . . . . . . . 7
Расчет литниковой системы . . . . . . . . . . . . . . . . . . . . . . . . . . . . . .7
Определение диаметра камеры прессования . . . . . . . . . . . . . . . . 8
Конструирование вентиляционной системы . . . . . . . . . . . . . . . . 9
Определение тепловых факторов литья . . . . . . . . . . . . . . . . . . . 10
Проектирование пресс-формы . . . . . . . . . . . . . . . . . . . . . . . . . . . 11
Материалы пресс- формы . . . . . . . . . . . . . . . . . . . . . . . . . . . . . .12
Расчет подкладной плиты на прогиб . . . . . . . . . . . . . . . . . . . . .13
Смазка пресс – формы . . . . . . . . . . . . . . . . . . . . . . . . . . . . . . . . 14
Обслуживание ремонт и хранение пресс-форм . . . . . . . . . . . 15
Заключение . . . . . . . . . . . . . . . . . . . . . . . . . . . . . . . . . . . . . . . . . 16
Список литературы . . . . . . . . . . . . . . . . . . . . . . . . . . . . . . . . . . . . . 17
Целью данного курсового проекта является проектирование технологии изготовления отливки «Крышка муфты сцепления». Проектирование технологии включает разработку чертежа отливки проектирование оснастки для выбранного способа разработка технологии изготовления отливки. Отливка выполняется из сплава АК5М7.
Тип производства – массовое.
1 Выбор расположения плоскости разъёма.
При выборе плоскости разъёма желательно стремиться к такому положению плоскости разъема чтобы вся отливка располагалась в одной полуформе. Также необходимо чтобы при раскрытии пресс-формы отливка оставалась в подвижной полуформе. Рассмотрим два варианта расположения плоскости разъёма. С учетом вышесказанного вариант №1 более приемлем.
2 Выбор расположения отливок в форме.
Из двух вариантов расположения отливок более целесообразно выбрать расположение отливок согласно варианту №1. При расположении отливок согласно варианту №2 центр масс куста расположен ниже центра масс плиты машины поэтому нижние колоны машины будут работать с большей нагрузкой чем верхние а это нежелательно. В варианте №1 во избежание преждевременного попадания металла из камеры прессования в полость формы предусмотрен противопоршень который открывается только тогда когда весь воздух будет вытеснен из камеры прессования.
3 Выбор варианта подвода металла.
Для коробчатых отливок подвод металла желательно осуществлять параллельно стенке. Также подвод металла желательно осуществлять в обрабатываемую поверхность. Следовательно вариант №1 более приемлем.
4 Выбор конфигурации вентиляционных каналов.
Полнота удаления газов из пресс-формы зависит не только от площади fв но и от длины вентиляционного канала (для обычного щелевого канала коэффициент расхода mв=01 02 большой протяжённости и mв »05 если длина не превышает 2 3мм). Уменьшение длины вентиляционного канала на практике достигают использованием его ступенчатой конструкции.
Поэтому выбираем вариант №2 (вентиляционный канал ступенчатой конструкции).
5 Выбор конструкции стержней.
Рассмотрим два варианта конструкции стержней. При использовании конструкции представленной в варианте №1 отверстие в отливке оформляется одним стержнем закреплённым в неподвижной полуформе. Однако при использовании такой конструкции возникает опасность того что отливка не сойдёт со стержней и останется в неподвижной полуформе. Следовательно этот вариант не подходит. В варианте №2 представлена конструкция в которой отверстие в отливке оформляется двумя стержнями. Эта конструкция более целесообразна.
6 Крепление вкладышей в обойме.
Вкладыши крепят в обоймах пресс-форм различными способами. Врезные вкладыши крепят винтами (вариант №1). Недостатком этого способа является то что по мере износа резьбы вкладыш может разбалтываться в гнезде. Сквозные вкладыши закрепляют в обоймах с помощью опорного буртика высота которого (6—12 мм) зависит от усилия выталкивания отливки (вариант №2). Этот способ крепления более надежен и прост.
7 Выбор способа выталкивания отливки.
Рассмотрим два варианта выталкивания отливки. В варианте №1 выталкивание производится с помощью цилиндрического выталкивателя. Под толкатель предусмотрен специальный прилив. В варианте №2 выталкивание производится трубчатым толкателем.
Так как трубчатый толкатель сложен по конструкции а также используется довольно протяженный стержень малого диаметра. Такая конструкция нецелесообразна. Поэтому останавливаемся на варианте №1.
Определение количества отливок в форме.
Площадь проекции отливки:
Площадь проекции куста:
где площадь проекции промывников; площадь проекции литниковой системы.
Усилие раскрытия пресс формы:
где - давление прессования.
Усилие запирания машины должно быть больше усилия раскрытия примерно на 20%.
Наименьшее усилие запирание для промышленных машин с холодной горизонтальной камерой прессования что намного больше усилия раскрытия
Следовательно изготовление пресс-формы для одной отливки нецелесообразно.
Следовательно целесообразно изготавливать сразу две отливки на машине с усилием запирания .
С учетом сделанных расчетов (см. выше) выбираем машину 711А08 с усилием запирания
Расчет литниковой системы.
Основным элементом литниковой системы является питатель. Расчет ведем по методу А. К. Белопухова
Площадь поперечного сечения питателя для одного гнезда пресс-формы:
Скорость впуска расплава в форму:
K1 =075 20 и принимается тем больше чем меньше толщина отдельных элементов отливки (ребер микрорельефа надписей на ней и т.д.) и сложнее ее конфигурация; К2 =25 10 учитывает давление прессования (при давлении прессования свыше 100 МПа К2 =10);
Принимаем коэффициенты:
режим дисперсный т.к.
Продолжительность заполнения формы:
Кз=11 05 учитывает тип заливаемого сплава и уменьшается с повышением температуры плавления и снижением его жидкотекучести (Кз=10 для отливок из Zn-сплавов); K4=05 15 учитывает толщину стенки оливки (для толщин более 90 мм K4=15).
Площадь поперечного сечения питателя для одного гнезда пресс-формы :
-время заполнения пресс-формы
Обычно геометрические размеры питателей устанавливают с учетом конфигурации и толщины стенки отливки в месте подвода расплава и удобства отделения литниковой системы от отливки. Так при изменении толщины отливок к которым предъявляются высокие требования к качеству поверхности от 10 до 60 мм рекомендуется назначать толщину питателя для Al- 08 20 мм. Принимаем толщину питателя 12 мм.
Площадь поперечного сечения трапециевидного подводящего канала принимают
Глубину Нпк и ширину по средней линии Впк подводящего канала определяют по эмпирическим формулам
Кромки питателя и подводящего канала выходящие на плоскость разъема формы не должны иметь округлений радиусы нижних кромок должны быть не менее 10мм а их боковые поверхности выполняются с уклоном 5 150. Во избежание преждевременного отделения питателей от отливки при ее удалении из пресс-формы рекомендуется под питателями устанавливать толкатели.
Определение минимального диаметра камеры прессования.
Усилие запирания превышает обычно усилие раскрытия на 10-20%. Диаметр камеры прессования выбирают исходя из объема требуемой для получения отливки (с учетом литников промывников и пресс остатка) дозы металла и степени наполнения камеры прессования 60-75%. Минимально допустимый диаметр камеры прессования определяют исходя из условия надежного запирания пресс-формы
Принимаем диаметр камеры прессования .
Конструирование вентиляционной системы.
При заливке воздух находящийся в полости пресс-формы не успевает из нее удалиться образуя воздушные раковины и пористость для уменьшения этого фактора необходимо в пресс-форме выполнять вентиляционные каналы. Предпочтительнее их выполнять в конечной части полости.
Требуемая площадь сечения вентиляционных каналов определяется из уравнения:
допустимая глубина вентиляционных каналов равна 01-012 мм и ширина 20-40мм.
Также важным технологическим элементом являются промывники предназначенные для:
-удаления из отливки первых некачественных порций металла вместе со сплавом выносится и воздух попадающий в него по литниковым каналам из камеры прессования;
-равномерного прогрева пресс-формы;
-гашения гидравлического удара в момент окончания заполнения формы.
Глубина канала соединяющего промывники с отливкой должна быть 035-04 мм но меньше глубины питателя. Чем больше объем промывника тем меньше в отливке включений воздушных пузырей вследствие чего увеличивается плотность отливки. Важно чтобы промывник и полость отливки заполнялись в разное время.
Определение тепловых факторов литья.
К основным и весьма существенным тепловым факторам литья относятся температура заливаемого сплава температура формы. Температура сплава при поступлении в литник должна быть для данной отливки минимальной. По данным Б. Б. Гуляева перегрев сплава при работе на машинах с холодной камерой бесполезен так как он автоматически снимается уже в камере. Если забирают вязкий сплав из раздаточной печи то можно задержать работу так как он не будет отделяться полностью от ложки при заливке в камеру. Поэтому из печи забирают сплав с небольшим перегревом – на 10-208 выше температуры начала кристаллизации.
При работе на алюминиевых сплавах существует оптимальная температура формы при которой получаются отливки с наиболее высокими механическими свойствами. С достаточной для практики точностью эта температура в среднем должна быть равна 13 температуры заливаемого сплава.
Так для отливок с толщиной стенки 15мм из алюминиевых сплавов с температурой заливки 6008 средняя температура формы должна быть 2508.
Расчет времени рабочего цикла.
Если поступление тепла в форму при ее нагреве до необходимой температуры обозначить через тепло вносимое отливкой через тепло переданное отливкой форме через и тепло ушедшее с отливкой при её удалении из формы через то тепловой баланс формы за один цикл составит:
Количество тепла вносимого отливкой равно:
где температура заливки в 8С;
вес отливки +06 от веса литника в г;
удельная теплоёмкость жидкого сплава в ;
q – удельная теплоёмкость кристаллизации в ;
Количество тепла переданного отливкой форме составит
где коэффициент отдачи с поверхности отливки в несмазанной форме;
поверхность отливки в ;
время охлаждения в сек составляющее (по опытным данным) 03 – 04 от времени полного цикла.
Количество тепла теряемое при удалении отливки из формы равно:
где средняя температура удалённой из формы отливки в 8С.
Получим приближенное уравнение теплового баланса:
Время охлаждения равно:
Проектирование пресс-формы.
Пресс-форма для литья под давлением состоит из неподвижной и подвижной частей в которых смонтированы все остальные детали. Неподвижную часть пресс-формы с помощью неподвижной плиты крепления крепят к прессующему блоку машины с горизонтальной камерой прессования а подвижную часть с помощью подвижной плиты крепления — к постаменту установленному на подвижном запирающем блоке машины.
В плитах называемых неподвижной и подвижной обоймами смонтированы специальные вставки в которых оформляется внешний контур отливки.
Для последовательного заполнения формы предусмотрен противопоршень. Противопоршень с пакетом тарельчатых пружин устанавливают в подвижной части пресс-формы так что при закрытой форме противопоршень своим днищем упирается в литниковую втулку и полностью перекрывает подводящий канал. При заполнении формы жидким сплавом противопоршень преграждает ему путь и задерживает его в камере прессования. И только при запрессовке под давлением сплава противопоршень сжимая пружины углубляется в подвижную формообразующую вставку и позволяет металлу заполнить полость формы.
При раскрытии пресс-формы отливка остается в подвижной части. При перемещении подвижной полуформы плита съема соединенная с плитой выталкивателей наталкивается на неподвижные упоры и останавливается затем выталкиватели удаляют отливку. При закрытии пресс-формы контртолкатели упираются в неподвижную обойму и возвращают выталкиватели в исходное положение. Центрирование неподвижной и подвижной полуформ осуществляется направляющими втулками и колонками.
Большую часть стержней и выступов оформляющих внутренние и наружные контуры отливки располагают в подвижной полуформе таким образом чтобы отливка при раскрытии пресс-формы всегда оставалась в последней. Поэтому в подвижной полуформе делают устройство для выталкивания или сбрасывания отливки.
Основные детали пресс-формы в зависимости от их назначения подразделяют на три группы: формообразующие конструктивные и входящие в механизмы пресс-формы. Кроме основных деталей пресс-форма имеет ряд вспомогательных крепежных деталей конструкции и размеры которых определяются стандартами.
Материалы пресс- формы.
Все формообразующие детали пресс-форм при работе подвергаются сложному силовому тепловому и химическому воздействию расплава смазочных и охлаждающих материалов. Материалы формообразующих деталей не должны вступать в физико-химическое взаимодействие с расплавом должны обладать высоким сопротивлением термоциклическим нагрузкам высокой твердостью вязкостью и прочностью при нагреве малым коэффициентом термического расширения хорошо обрабатываться мало деформироваться при термической обработке.
Для придания необходимых служебных свойств формообразующие детали пресс-форм подвергают термической и химико-термической обработке — низкотемпературному цианированию на глубину 005 02 мм. После закалки и отпуска они должны иметь твердость на поверхности HRC 58 62.
Вкладыши вставки стержни выталкиватели противопоршень втулки литниковые-3Х2В8Ф 4Х5МФС (HRC 58-62)
Плиты-обоймы ползуны рейки втулки стержней- 4040Х (HRC 30-34)
Плиты подкладные - 3545 (HRC 30-34)
Втулки ползуна втулки стержней - 40Х45 (HRC 48-52)
Колонки направляющие контртолкатели - У10А (HRC 50-55)
Расчет подкладной плиты на прогиб.
При сквозных вкладышах необходимо принимать во внимание давление металла которое передается от вкладыша на подкладную плиту.
Подкладную плиту на прочность рассчитывают из условия что она жестко закреплена с двух сторон. Изгибающий момент М действующий на подкладную плиту
Прогиб подкладной плиты определяется уравнением:
-допускаемый прогиб подкладной плиты обычно принимаемый равным 002;
E-модуль упругости материала плиты;
J-момент инерции плиты;
расчетный прогиб подкладной плиты меньше допустимого.
Смазка пресс – формы.
В совершенствовании технологического процесса литья под давлением все большее значение приобретает операция смазывания пресс-формы которая осуществляется в целях уменьшения усилий необходимых для удаления отливок из пресс-формы и стержней из отливок предотвращения образования задиров на отливках и приваривания их к поверхности пресс-формы т. е. в целях обеспечения бесперебойной работы пресс-формы. Смазочный материал влияет на качество отливок. Обильное смазывание приводит к образованию неспаев узорчатости и пятен на поверхности отливок а также повышает их пористость снижает прочность и герметичность.
Смазочные материалы для пресс-формы
На основе нефтепродуктов или жиров с наполнителями например масло Вапор с 3—10% графита
Высокая смазывающая способность сильное выделение газов в атмосферу и отливку
Растворы остаточных масел в органическом растворителе с противозадирными добавками например состав ЛД на основе масла МС-20 растворяемый в керосине
На простые отливки автоматически с помощью форсунок на сложные вручную распылителем
Хорошая смазывающая способность среднее выделение газов в атмосферу и отливку
Эмульсии остаточных масел в воде с графитом и без него: Графитолы и Прессолы (Элитолы)
Удовлетворительная смазывающая способность выделение газов ниже среднего дополнительно охлаждает пресс-форму
На солевой основе (например 5% фтористого натрия и 95% воды)
Удовлетворительная смазывающая способность при повышенных температурах отсутствие газотворной способности затрудняет очистку и снижает стойкость пресс-форм
Комбинированный: на жировой основе (первый слой); фтористый натрий в воде (второй слой)
Первый слой вручную помазком второй —
Высокая смазывающая способность при пониженной газотворности снижает производительность процесса литья
Обслуживание ремонт и хранение пресс-форм.
Условием получения качественных отливок является хорошее состояние рабочих поверхностей оформляющих гнезд пресс-формы и ее оформляющей поверхности. Обслуживание пресс-форм можно разделить на два этапа: обслуживание при эксплуатации и обслуживание при ремонте и хранении. При эксплуатации пресс-формы выполняют следующие:
)чистку разъема и гнезд от облоя излишков смазки грязи и пыли; обдувку пресс-формы сжатым воздухом и очистку волосяной кистью или тряпкой.
)наружный осмотр пресс-формы.
)Проверяют в холостую последовательно все движения которые требуются от данной пресс-формы за литейный цикл.
)Проверяют правильность удаления и ввода подвижных стержней; в клиновых механизмах в момент смыкания полуформ клин-палец должен плавно входить в ползун.
)Проверяют работу выталкивающего механизма: правильность установки выталкивателей и контртолкателей в крайних положениях; отсутствие заеданий и перекосов.
Ремонт пресс-форм делят на текущий профилактический и капитальный. Текущий ремонт состоит в том что по ходу работы или небольших перерывах в работе заменяют изношенные детали осматривают и исправляют крепление полуформ на плитах машины. В текущий ремонт входят работы выполняемые после остановки машины по окончании смены: замена стержней выталкивателей и других подвижных частей механизмов выталкивания и стержневых механизмов замена вкладышей и т.д.
Профилактический ремонт производят при смене пресс-формы. В процессе ремонта пресс-форму разбирают очищают от грязи заменяют изношенные и поврежденные детали стержневых и выталкивающих механизмов. Профилактический ремонт включает зачистку полости и плоскости разъема от привара с последующим шлифованием и полированием.
Капитальный ремонт рентабелен только в том случае если стоимость ремонта не превышает 23 стоимости новой пресс-формы. При капитальном ремонте заменяют обоймы и плиты вышедшие из строя из-за трещин или коробления.
Смазанная тавотом или машинным маслом пресс-форма поступает на склад. Склад должен быть светлым просторным и обязательно сухим чтобы исключить резкие колебания температур. Пресс-формы хранят на складе в закрытом состоянии.
В результате проделанной работы была разработана технология производства отливки детали «Крышка муфты сцепления» а именно разработан чертеж отливки спроектирована пресс-форма для литья под давлением и выполнен ее сборочный чертеж. Графическая часть работы занимает 5 листов формата А1 расчетно-пояснительная записка листов формата А4.
Литье под давлением. Под ред. А. К. Белопухова. М. «Машиностроение» 1975.
Инженерная монография по литейному производству.
”Справочник конструктора машиностроителя” В.И.Анурьев изд-во “Машиностроение” Москва 1980г.
Рекомендуемые чертежи
- 31.05.2020
- 05.11.2023