Проектирование редуктора привода конвейера курсовой чертежи в AutoCAD





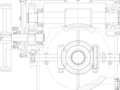
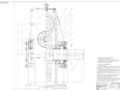
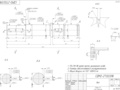
- Добавлен: 25.10.2022
- Размер: 9 MB
- Закачек: 0
Описание
Состав проекта
![]() |
![]() |
![]() ![]() |
![]() ![]() ![]() |
![]() ![]() |
![]() ![]() ![]() |
![]() ![]() ![]() |
![]() ![]() ![]() |
![]() ![]() ![]() |
![]() ![]() ![]() |
![]() ![]() |
![]() ![]() ![]() |
![]() ![]() ![]() |
![]() ![]() |
![]() ![]() ![]() |
![]() ![]() ![]() |
![]() ![]() ![]() |
![]() ![]() ![]() |
![]() ![]() |
![]() ![]() |
![]() ![]() ![]() |
![]() ![]() |
![]() ![]() ![]() |
![]() ![]() ![]() |
Дополнительная информация
во.dwg

сп во 1.dwg

сп во2.dwg

Компоновка 2 А1.dwg

сб 2 А1.dwg

компоновка 1 А1.dwg

сп сб 2.dwg

сп сб 3.dwg

Колесо А3.dwg

вал.dwg

крышка а4.dwg

сп сб 1.dwg

сб 1 А1.dwg

Рекомендуемые чертежи
- 24.01.2023
- 17.04.2018