Проектирование редуктора общего назначения для привода ленточного конвейера




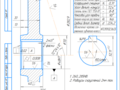
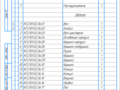
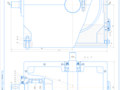
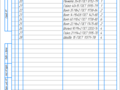
- Добавлен: 24.01.2023
- Размер: 899 KB
- Закачек: 0
Описание
Состав проекта
![]() |
![]() |
![]() |
![]() ![]() ![]() |
![]() ![]() ![]() ![]() |
![]() |
![]() |
![]() |
![]() ![]() ![]() ![]() |
![]() ![]() ![]() ![]() |
![]() ![]() ![]() ![]() |
![]() ![]() ![]() ![]() |
![]() ![]() ![]() ![]() |
![]() ![]() ![]() ![]() |
![]() ![]() ![]() ![]() |
![]() ![]() ![]() ![]() |
![]() ![]() ![]() ![]() |
![]() ![]() ![]() ![]() |
![]() ![]() ![]() ![]() |
![]() ![]() ![]() ![]() |
Дополнительная информация
.doc
Студента группы 31а Коробейникова Юрия.
Тема Проектирование редуктора общего назначения для привода ленточного конвейера.
Утверждено на заседании предметной комиссии
На курсовое проектирование по «деталям машин»
студенту Коробейникову Ю.В. гр. 31а.
Тема: Спроектировать редуктор общего назначения для привода ленточного конвейера
Данные: -тяговое усилие ленты - F»09 кН;
-скорость ленты - V»12 мс;
-диаметр ведущего барабана конвейера - Ds=320 мм;
-долговечность подшипников - Lh»20000 час;
Работа двухсменная; нагрузка нереверсивная близкая к постоянной.
РАСЧЕТНО-ПОЯСНИТЕЛЬНАЯ ЗАПИСКА содержит:
Ведомость курсового проекта.
задание на курсовое проектирование.
Выбор электродвигателя и кинематический расчет привода.
Кинематическая схема привода.
Расчет передач привода.
Определение конструктивных размеров зубчатой передачи.
Проектный расчет на прочность валов редуктора.
Эскизная компоновка редуктора.
Подбор подшипников для валов редуктора.
Проверочный расчет валов на выносливость.
Определение конструктивных размеров корпуса редуктора. Подбор арматуры.
Подбор шпонок и их проверочный расчет.
Подбор муфты и ее проверочный расчет.
Выбор посадок основных деталей редуктора.
Смазка зацепления и подшипников.
Краткая технология сборки редуктора.
Оценка спроектированного редуктора.
Список использованной литературы.
ГРАФИЧЕСКАЯ ЧАСТЬ ПРОЕКТА включает:
Сборочный чертеж редуктора.
Рабочие чертежи двух сопряженных деталей.
Спецификация к чертежам.
РЕКОМЕНДУЕМАЯ ЛИТЕРАТУРА:
Курсовое проектирование деталей машин. М.«Машиностроение»1979авт.Чернавский С.А
Курсовое проектирование одноступенчатых редукторов. М. «Высшая школа»1975авт. Чернилевский Д.В.Паныч Б.Б.
Конструирование узлов и деталей машин. М. «Высшая школа»1978авт. Дунаев П.Ф.
Редуктором называют механизм состоящий из зубчатых
или червячных передач выполненный в виде отдельного агрегата и служащий для передачи вращения от вала двигателя к валу рабочей машины.
Назначение редуктора понижение угловой скорости и соответственно повышение вращающего момента ведомого вала по сравнению с ведущим.
Конические прямозубые редукторы применяют для передачи движения между валами оси которых пересекаются обычно под углом 90°.Передачи с другими встречаются редко.
Расчет одного из таких редукторов смотрите далее
КИНЕМАТИЧЕСКАЯ СХЕМА ПРИВОДА
Выбор электродвигателя. Кинематический расчет привода.
1 Определение мощности и частоты вращения двигателя.
1.1Определение требуемой мощности рабочей машины.
Pб=FхV=0.9х1.2=1.08 кВт.
1.2Определение общего коэффициента полезного действия (КПД) привода:
hоб= hзуб х hрем х hподш 2х hмуфты=096х095х0992х098=0876
1.3Определение требуемой мощности двигателя Pтр.дв кВт:
Pтр.дв=Pрмhоб=1080876=123 кВт.
2Определение передаточного числа привода и его ступеней.
2.1Определение частоты вращения барабана.
wб=2хVD=12х2032=75с-1
nб=30хwб=30х0.753.14=71обмин.
2.2Нахождение общего передаточного числа.
Uзуб=3Uрем=3Uоб= Uзуб хUрем=9(табл.1.2) [1]
2.3Определение частоты вращения вала двигателя.
nдв= nбхUоб=71х9=639обмин.
2.4По полученным данным nдв=639обмин. и Pтр.дв=123 кВт. выбираем двигатель 100L8700для которого P=1.5 кВт и n=750 обмин.
2.5Уточнение передаточных чисел.
Uзуб=315 ; Uоб= nдвnб=75071=1056 ; Uрем= Uоб Uзуб=1056315=335
3Определение силовых и кинематических параметров привода.
Угловая скорость на ведущем и ведомом валах
= двUрем=785335=234 с-1.
дв= nдвх 30=750х31430=785 с-1.
Частота вращения ведущего и ведомого валов
n1=nдвUрем=7503.35=228.8 обмин.
Мощность передаваемая на ведущий и ведомый вал
p1=Pдвхhрем= 1.23х0.95=1.17кВт
p2= p1хhподш2хhзуб= 1.17х0992х096=11 кВт.
Вращающий момент на ведущем и ведомом валах
T1= p11=1.1723.4=0.05 Нхм
T2= p22=1.17.5=0.14 Нхм.
Вращающий момент на двигателе и барабане
Tдв= Pдв дв=1.578.5=0.019 Нхм.
Tб=Pбwб=1.087.5=0.14 Нхм.
Параметры передачи. Таблица 1.1.
Выбор материала зубчатых передач. Определение допускаемых напряжений.
1 Выбор материала зубчатой передачи.
Определяем марку стали:
для шестерни -45 Dпред=125 мм Sпред=80 мм твердость поверхности HB=235 262 HBср=248 т=540 МПа термообработка-улучшение.
для колеса -45 Dпред=125 мм Sпред=80 мм твердость поверхности HB=269 302HBср=2855 т=650 МПа термообработка-улучшение.
2 Определение допускаемых контактных напряжений для зубьев шестерни []h1 и колеса []h2.
[]h=Kh []f= Kflх[]f0. - допускаемые контактные напряжения и напряжения изгиба с учетом времени работы передачи.
Kh Kfl=6√Nf0N - коэффициент долговечности для шестерни
Nh01=100х106 млн.циклов (табл.3.3) [2]
Nh01=20х106 млн.циклов (табл.3.3) [2]
Nf0=4х106 млн.циклов (стр.52) [2]
N2=573х2хLh=573х7.5х2х104=8595х104 циклов.
N1=N2хUоб=8595х104х1056=90763х104 циклов. - соотв. для шестерни.
Khl1=6√100х10690763х104=069
Khl2=6√20х1068595х104=078 - коэффициент долговечности для колеса.
Kfl1=6√4х10690763х104=04
Kfl2=6√4х1068595х104=06
[]h1=069х(18х248+67)=354 МПа.
[]h2=078х(18х2855+67)=453 МПа.
[]f1=04х103х248=102 МПа.
[]f2=06х103х2855=1764 МПа.
[]h=045([]h1+[]h2)=045(354+453)=363 МПа.
Механические характеристики материалов зубчатой передачи. Таблица3.1.
Расчет закрытой конической зубчатой передачи.
1Внешний делительный диаметр окружности колеса.
de2≥165х104х 3√KhхUхT2 hх[]²h
где h=085-для прямозубых колес(стр.67) [2]
d=0166х√U²+1=0166х√315²+1=055.
Kh=128 (табл. 2.3) [1]
de2≥165х104х 3√128х315х140085х354х106)²=280 мм.
2Углы делительных конусов шестерни и колеса
3Внешнее конусное расстояние Reмм
Re=de2(2хsin2)=280(2хsin72)=146 мм
4Ширина зубчатого венца шестерни и колеса
где R=0285-коэффициент ширины венца.
b=0.285х146=41.6 округляем b=41 мм.(табл. 13.15 ) [2]
5Внешний окружной модуль передачи me(mte)
me(mte)=(14хT2х10³)(fхde2хbх[]f)Kf
me(mte)=(14х1.64х140)(0.85х0.28х0.041х102х106)=3.2м
где f=085-для прямозубых колес (стр.67) [1]
Kf=1.64 – коэффициент учитывающий распределение нагрузки по ширине венца.(табл. 2.5) [1]
6Число зубьев колеса Z1 и шестерни Z2
Округляя принимаем Z2=88
Округляя принимаем Z1=28
7Фактическое передаточное число Uф и его отклонение ΔU от заданного U
ΔU=(Uф-Uх100)U=(31428-315х100)3.15=022%≤4%
8Действительные углы делительных конусов шестерни и колеса
=arctgUф; 2=arctg31428=72387
=90- 2; 1=90-72387=17613
9Выбор коэффициента смещения инструмента Xe1 и Xe2
Xe1=031 (табл. 2.7) [1]
10Определение внешних диаметров шестерни и колеса мм
de1=meхZ1=32х28=896 мм- делительный диаметр шестерни. (стр. 68)[2]
de2= meхZ2=32х88=2816 мм - делительный диаметр колеса. (стр. 68)[2]
dae1= de1+2х(1+Xe1)хmeх dae1=896+2х(1+031)х32х0953=975 мм
dae2=de2+2х(1+Xe2)хmeх dae2=2816+2х(1-031)х32х0302=2829 мм
dfe1=de1-2х(12-Xe1)хmeх dfe1=896-2х(12-031)х32х095=841 мм
dfe2=de2-2х(12-Xe2)хmeх dfe2=2616-2х(12+031)х32х03=2606 мм
11Определение среднего делительного диаметра шестерни и колеса
d1=0857хde1=0857х896=768 мм
d2=0857хde2=0857х2816=2413 мм
12Проверка пригодности заготовок колес
Dзаг=de1+2хme+6; Dзаг=896+2х32+6=102 мм– диаметр заготовки шестерни.
Sзаг=8хme=8х32=256 мм– размер заготовки колеса.
Dзаг=102≤Dпред=125 мм
Sзаг=256≤Sпред=80 мм
Пригодность заготовки подтверждается.
13Проверка контактных напряжений h
h=470х√(Ftх√(Uф²+1))( hхde2хbх)KhαхKhхKh≤[]h
где Ft=(2хT2х10³) Ft=(2х140)0241=11618 Н
Khα=1 –коэффициент учитывающий распределение нагрузки между зубьями прямозубых колес
=2хd2(2х10³); =75х241(2х10³)=09 мс
Kh=101 – коэффициент динамической нагрузки.(табл. 4.3) [1]
h=470х√(11618х√(992+1))(085х2816х0041)х1х1х101=2969 МПа
Контактные напряжения удовлетворяют условию.
14Проверка напряжения изгиба зубьев шестерни и колеса
f2=(Yf2хYхFtхKfαхKfхKf)(fхbхme)≤[]
Kfα=1 –коэффициент учитывающий распределение нагрузки между зубьями прямозубых колес
Kf=14 -коэффициент динамической нагрузки
Yf1=335; Yf2=3 5 – коэффициенты формы зуба шестерни и колеса (табл.2.9) [1]
f2=(164х14х368х11618)(0041х00032х085)=88 МПа
f1=(88х335)368=80 МПа
Расчетные напряжения изгиба меньше допускаемых значит расчет произведен верно и контактная прочность передачи не нарушается.
Параметры зубчатой конической передачи мм. Таблица 4.1.
Внешнее конусное расстояние Re
Внешний окружной модуль me
Ширина зубчатого венца b
Число зубьев: шестерни Z1
Угол делительного конуса:
Внешний делительный диаметр: шестерни de1
Внешний диаметр окружности вершин: шестерни dae1
Внешний диаметр окружности впадин: шестерни dfe1
Средний делительный диаметр: шестерни d1
Контактные напряжения hНмм2
Напряжения изгиба fНмм2
Рис 4.1.Геометрические параметры конической зубчатой передачи.5 Расчет открытой передачи.
1Определение диаметра ведущего шкива d1
d1≥70х; =28 мм (табл. 5.1) [2]
Принимаем d1=224 (табл. К40) [2]
2Определение диаметра ведомого шкива d2
где =001 –коэффициент скольжения
d2=335х200х(1-001)=6633 мм
Принимаем d2=750 мм (табл. К40) [2]
3Определение фактического передаточного числа Uф
Uф=d1d2х(1- ); Uф=750224х(1-001)=338
ΔU=(Uф-UU)х100%=09%≤3%
4Определение ориентировочного межосевого расстояния a
a≥15х(d1+d2); a≥15х(224+750)=1461 мм
5Определение расчетной длины ремня l
l=2х1461+(3142)х(750+224)+(750+224)24х1461=4498 мм
Принимаем l=4500 (с.78) [2]
6Уточнение межосевого расстояния
a=18х2х4500-314х(750+224)+√[2х4500-314х(750+224)]2-8х(750-224)2=1461 мм
7Определение угла обхвата ремнем ведущего шкива α1
α1=180-57х(750-224)14613=1597≥150
8Определение скорости движения ремня
=314х224х2238(60х103)=26 мс
9Определение частоты пробегов ремня Uс-1
[U]=15 с-1 –допускаемая частота пробегов
10Определение окружной силы Ft Н передаваемую ремнем
Ft=Pномх10326=5769 Н
11Удельная окружная сила [kп] Нмм2
[kп]=[kо]хCхCαхCхCpхCdхCf ;
[kо]=232; C=08; Cα=091; C=103; Cp=09; Cd=12; Cf=085(табл. 52) [2]
b=Ftх[kп]; b=576928х158=1304 мм
Округляя принимаем b=100 а B=112 мм с.80 [2]
13Площадь поперечного сечения ремня Aмм
A=хb; A=28х100=280 мм2
14Сила предварительного натяжения ремня Fo
Fo=Aхo; Fo=280х2=560 Н
15Силы натяжения ведущей и ведомой ветвей ремня
F1=F0+Ft2=560+57692=8485 Н
F2=F0-Ft2=560-57692=2715 Н
16Сила давления ремня на вал Fоп Н
Fоп=2хF0хsinх(α12)=1098 Н
Fм=125х√T2=125х√140=1479 Н
Fr1=Fa2=036хFt1хcos1=036х11618х095=3973 Н
Fr2=Fa1=036хFt2хcos2=036х11618х03=1254 Н
17Проверочный расчет
=F0A+Ft2хA; 1=560280+5769560=30
н =90х28200=126 Нмм2
=ρх2х10-6; ρ=1000 1200 кгм3-для плоскоременных передач
=1100х262х10-6=00074 Нмм2
max=3+126+00074=42674≤[]p=8 Нмм2 значит ремень выдержит необходимую нагрузку
Параметры плоскоременной передачи Таблица 5.1.
Межосевое расстояние а мм
Угол обхвата ведущ. шкива α1
Число пробегов ремня
Диаметр ведущего шкива d1
Диаметр ведомого шкива d2
Максимальное напряжение max
Начальное натяжение ремня F0
Сила давления ремня на вал Fоп
Рис 5.1.Эскиз ведомого шкива.
Нагрузки валов редуктора
Рис.6.1.Схема сил в зацеплении.
Рис.6.2. Эскиз зацепления.7 Проектный расчет валов. Эскизная компоновка редуктора.
1Проектный расчет быстроходного вала.
1.1Выбор материала вала.
Выбираем сталь 45 термически обработанную улучшением среднеуглеродистую для которой Dпред=125 мм Sпред=80 мм твердость 235 262 HB.
1.2Выбор допускаемых напряжений на кручение.
[]к=10 20 Нмм2 причем для быстроходного вала принимается меньшее значение а для тихоходного наоборот.
1.3Определение геометрических параметров ступеней вала.
d1=3√(Mkх103)(02х10) - диаметр первой ступени вала.
где Mk=T1 []к=10 Нмм2– допускаемое напряжение на кручение.
d1=3√(50х103)(02х10)=292 мм округляя принимаем d1=30 мм (табл. 13.15 ) [2]
l 1=(12 15)хd1- длина первой ступени вала.
l 1=135х30=405 мм – под шкив округляя принимаем l1=40 мм (табл. 13.15 ) [2]
d2=d1+2хt - диаметр второй ступени вала.
где t=22 - высота буртика.(табл. 7.1 примечание) [2]
d2=30+22х2=344 мм – округляя принимаем d2=35 мм (табл. К27 ) [2]
l2=06хd4 - длина второй ступени вала.
где d4=d5+(2 4) мм - диаметр четвертой ступени вала.
d5=39 мм – диаметр пятой ступени вала.(табл. 10.11 ) [2]
d4=39+3=42 мм – округляя принимаем d4=45 (табл. К27 ) [2]
l2=06х45=252 мм округляя принимаем l2=26 мм (табл. 13.15 ) [2]
d3=d4+32хr - диаметр третьей ступени вала.
где r=2 - фаска подшипника.(табл. 7.1 примечание) [2]
d3=45+32х2=484 мм – округляя принимаем d3=48 мм (табл. 13.15 ) [2]
l3 l4 – определяется графически.
l5=04хd4 - длина пятой ступени вала.
1.4Предварительный подбор подшипников качения.
Выбираю подшипники роликовые конические типа 7209 при n11500 обмин. Легкая серия α=11 16 схема установки – в растяжку.
Рис.7.1.Эскиз конструкции вала быстроходного.
2Проектный расчет тихоходного вала.
2.1Определение геометрических параметров ступеней вала.
где Mk=T2 []к=20 Нмм2- допускаемое напряжение на кручение.
d1=3√(140х103)(02х10)=327 мм – округляя принимаем d1=34 мм (табл.13.15) [2]
l1=(10 15)хd1- длина первой ступени вала.
l1=135х30=425 мм – под полумуфту округляя принимаем l1=42 мм (табл. 13.15 ) [2]
где t=25 - высота буртика.(табл. 7.1 примечание) [2]
d2=30+25х2=39 мм – округляя принимаем d2=40 мм (табл. К27 ) [2]
l2=125хd2 - длина второй ступени вала.
где f=12 (табл. 7.1 примечание) [2]
d5=48+3х12=516 мм - округляя принимаем d1=50 мм (табл. 13.15) [2]
где r=25 - фаска подшипника.(табл. 7.1 примечание) [2]
l3 l4– определяется графически.
2.2Предварительный подбор подшипников качения.
Выбираю подшипники роликовые конические типа 7208. Легкая серия α=11 16 схема установки – в распор.
Рис.7.2.Эскиз конструкции вала тихоходного.8 Определение реакций опор построение эпюр.
1 Определение реакций подшипников ведомого вала. Построение эпюр.
Дано: Ft2=11618 Н; Fr2=1254 Н; Fa2=3973 Н; d1=238 мм;
1.1 Вертикальная плоскость.
Определение опорных реакций Н:
Rcy=(1254х133+3973х119)(57+133)=3366 Н;
Rdy=(3973х119-1254х57)(57+133)=2112 Н;
y=0; Rcy-Fr2+Rdy=3366-1254+2112=0;
Построение эпюр изгибающих моментов относительно оси x в характерных сечениях 1 3 Нхм
1.2 Горизонтальная плоскость.
My1=0; -Fa2хd12+Ft2хl1-Rd
Построение эпюр изгибающих моментов относительно оси y в характерных сечениях 1 4 Нхм
My1=0; My2=Rc My3=-Fмх My4=0;
1.3 Построение эпюр крутящих моментов Нхм:
Mk=Mz=-Ft2хd12=-11618х119=-151615 Нхм;
1.4 Определение суммарных радиальных реакций Н:
1.5 Определение суммарных изгибающих моментов в наиболее нагруженных сечениях:
M2=√M2 M3=My3=-59160 Нхм;
Рис.8.1. Расчетная схема ведомого вала с эскизами опасных сечений.
2 Определение реакций подшипников ведущего вала. Построение эпюр.
Дано: Ft1=11618 Н; Fa1=1254 Н; Fr1=3973 Н; Fоп=1098 Н; d1=78 мм;
2.1 Вертикальная плоскость.
Rby=(3973х(36+64)-1254х39-1098х80)64=-8281 Н;
Ray=(3973х36-1254х39-1098х(64+80))64=-23234 Н.
y=0; -Fr1+Rby-Ray-Fоп=0.
Построение эпюр изгибающих моментов относительно оси x в характерных сечениях 1 4 Нм
2.2 Горизонтальная плоскость.
My3=0; Fa1хd12+Ft1х(l1+l2)-Rb
My2=0; Fa1хd12+Ft1хl1-Ra
2.3 Построение эпюр крутящих моментов Нм:
My1=0; My2=Ft1х My3=0.
2.4 Определение суммарных радиальных реакций Н:
2.4 Определение суммарных изгибающих моментов в наиболее нагруженных сечениях:
Рис.8.2. Расчетная схема ведущего вала.9 Проверочный расчет подшипников.
1Определение эквивалентной динамической нагрузки подшипников 7209 на быстроходном валу схема установки – врастяжку. (рис.8.2).
1.1.Определение осевых составляющих радиальных нагрузок.
где e=041 (табл. К29 ) [2]
Rs1=083х041х2435=8286 Н;
Rs2=083х041х2064=7024 Н;
1.2Определение осевой нагрузки.
Ra2=Rs1+ Ra2=8286+125=9536 Н;
1.3.Определение коэффициентов.
Ra1VхRr1=8286(1х2435)=034.
Ra2VхRr2=9536(1х2064)=046.
X=04; Y=145; Kб=13 – коэффициент безопасности. (табл. 9.4) [2];
Кт=1 - температурный коэффициент (табл. 9.5 ) [2];
cor=334 - статическая грузоподъемность (табл. К29 ) [2]
1.4.Определение эквивалентной нагрузки.
Re1=VхRr1хKбхKт=2435х13х1=3165 Н;
Re2=(XхVхRr2+YхRa2)хKбхKт=(04х1х2064+145х9536)х13х1=2623 Н
1.5.Определение динамической грузоподъемности и долговечности подшипников.
Crp=Re1хm573хwх(Lh106);
Crp=31655х333573х785х(2х104106)=24408Cr=42700.
L10h=(106573хw)х(CrRe);
L10h=(106573х785)х(427х10331655)=128773>Lh.
Долговечность достаточная следовательно подшипник выслужит срок.
2.Определение эквивалентной динамической нагрузки подшипников 7208 на тихоходном валу схема установки – в распор. (рис. 8.1)
2.1.Определение осевых составляющих радиальных нагрузок.
Rs1=083х038х822=2595 Н;
Rs2=083х038х19017=600 Н;
2.2Определение осевой нагрузки.
Ra2=Rs1+ Ra2=2596+397=6596 Н;
2.3.Определение коэффициентов.
Ra1VхRr1=2596(1х8227)=03.
Ra2VхRr2=6566(1х19017)=034.
X=04; Y=156; Kб=13 – коэффициент безопасности. (табл. 9.4) [2];
Кт=1 - температурный коэффициент. (табл. 9.5) [2];
cor=327- статическая грузоподъемность.(табл. К29) [2]
2.4.Определение эквивалентной нагрузки.
Re1=VхRr1хKбхKт=2596х13х1=3373 Н;
Re2=VхRr2хKбхKт=19017х13х1=24713 Н
Crp=2471х333573х75х(2х104106)=94129Cr=42400.
L10h=(106573х75)х(424х10324713)=1615583>Lh.
Основные размеры и эксплуатационные характеристики подшипников. Таблица 9.1.
Динамическая грузоподъемность Н
Долговечность часов.
Расчет на выносливость ведомого вала.
Расчет шпоночных соединений. Посадки.
Выбираю шпонку под колесо по d=48 мм для которой: b=14 мм; h=9 мм; фаска 04 06 мм; t1=55 мм; t2=38 мм; l=26 мм (ГОСТ 23360-78)(табл. К42) [2]
Выбираю шпонку для выходного конца быстроходного вала по d=30 мм для которой: b=8 мм; h=7 мм; фаска 04 06 мм; t1=4 мм; t2=33мм; l=18 90 мм
(ГОСТ 23360-78) (табл. К42) [2]
Для шпонки на посадочных поверхностях вала и отверстия колеса создаем натяг d9 и h6 под открытую передачу и колесо соответственно.
Рис.10.1.Эскиз шпоночного соединения.
2.Проверка шпонки на смятие.
см=FtAсм≤[]см (стр.251)[2]
Aсм=(094хh-t1)хlp - площадь смятия. (стр.251)[2]
lp= l-b=28-14=14 мм - рабочая длина шпонки со скруглёнными торцами.
Aсм=(094х9-55)х14=4144 мм2
Условие прочности см≤[]см выполняется следовательно шпонка выдержит напряжение смятия.
3.Определение осевого и полярного момента сопротивлений.
для сечения А-А. (рис.8.1)
Wнетто=01хd3-(bхt1х(d-t1)2)2хd=01х483-(14х55х(48-55)2)2х48=9600 мм3.
Wр нетто=02хd3-(bхt1х(d-t1)2)2хd=20700 мм3.
для сечения B-B. (рис.8.1)
Wнетто=01хd3=01х403=6400 мм2
Wр нетто=02хd3=12800 мм2
4.Определение коэффициентов снижающих предел выносливости.
4.1.Определение расчетного напряжения изгиба.
где M – суммарный изгибающий момент MA-A=47 Нхм MB-B=59 Нхм
а=(47х103)9600=49 Нмм2.
b=(47х103)6400=92 Нмм2.
4.2.Определение расчетного напряжения кручения.
a=k2=(Mkх103)2хWр нетто
где k – расчетное напряжение кручения
Mk – крутящий момент Mk=151 Нхм.
a=(151х103)2х20700=36 Нмм3.
a=(151х103)2х12800=59 Нмм3.
4.3.Определение коэффициента концентрации нормальных и касательных напряжений.
(K)D=(KKd+KF-1)х1 (K)D=(KKd+KF-1)х1
где KKd=395 (табл. 11.2) [2]
KKd=28 (табл. 11.2) [2]
KF=1 - коэффициент влияния шероховатости.(табл. 11.4) [2]
Ky=16 - коэффициент влияния поверхностного прочнения.(табл. 11.5) [2]
(K)D=(395+1-1)х116=2469 – коэффициент концентрации нормальных напр.
(K)D=(28+1-1)х116=175 - коэффициент концентрации косательных напр.
4.4.Определение пределов выносливости.
[-1]D=-1(K)D; [-1]D=-1(K)D;
где -1=335 Нмм2; -1=058х-1=1943 Нмм2.
[-1]D=33525=134; [-1]D=194175=1108
4.5.Определение коэффициентов запаса прочности по нормальным и касательным напряжениям.
для сечения А-А. (рис. 8.1)
S=[-1]Da1=1344.9=273
для сечения B-B. (рис. 8.1)
4.6.Определение общего коэффициента запаса прочности в опасных сечениях.
S=(273х308)(√2732+3082)=204
S=(145х188)(√1452+1882)=115
Проверочные расчеты на прочность в обоих сечениях дают удовлетворительные результаты значит запас прочности достаточный.
Подбор и расчет муфт. Компоновка редуктора.
1.Смазывание зубчатого зацепления.
Подбираем сорт смазывающего масла для передачи ИГА-68. При мощности 11 кВт объем масляной ванны примерно 055 л. (табл. 10.29) [2]
Уровень масла m≤hm≤025хd2.
Выбираю круглый маслоуказатель и сливное отверстие в дне с пробкой с цилиндрической резьбой М 16х15; D=25мм; D1=219 мм; L=24 мм; b=3 мм; S=19 мм; t=19 мм; d2=16; D2=28 мм; b2=3 (табл. 10.30 ) [2]
Рис.11.1. Круглый маслоуказатель.
Рис.11.2. Пробка с цилиндрической резьбой.
2.Проверочный расчет стяжных винтов подшипниковых узлов. Винты изготовляют из стали 30 класс прочности 5 6(ГОСТ 11738-84)
Подшипник на тихоходном валу на ступени 4 и 2.
где Fp=[K3х(1-x)+x]хFв - расчетная сила затяжки винтов обеспечивающая нераскрытие стыка под нагрузкой
Fв=05хRy– сила воспринимаемая одним стяжным винтом.
Ry=59 Нхм– большая из реакций в вертикальной плоскости в опорах подшипников вала.
K3=175; – коэффициент затяжки при постоянной нагрузке. (стр.252)[2]
x=025. – коэффициент основной нагрузки для металлических деталей с резиновыми прокладками. (стр.252)[2]
A=хdp24 – площадь опасного сечения винта.
где dpd2-094хp– расчетный диаметр винта.
d2=М10– наружный диаметр винта. (табл. 10.17 ) [2]
p=15– шаг резьбы.(табл. К5) [2]
dp=10-094х15=859 мм.
A=314х85924=579 мм2.
Fp=[175х(1-025)+025]х295=46 Н.
экв.=13х46579=103≤[]=60 Нмм2.
Условие прочности выполняется следовательно винт выдержит затяжку и будет
крепко держать подшипники.
3.Подбор и расчет муфт.
3.1.Определение расчетного момента и выбор муфты.
где Kp=1375 – коэффициент режима нагрузки. (табл. 10.26 ) [2]
T1=140 Нхм. – момент на быстроходном валу.
Tp=1375х140=1925 Нхм.
Выбираем муфту с Т=250 Нхм и габаритными размерами: dd1=32353638404245
D=140 мм; L=121 мм;d0=28 мм;
Рис.11.3. Муфта упругая втулочно- пальцевая.
dп=14 мм; d0=М10; Z=6; dв=27 мм; lв=29 мм.
Радиальная сила вызванная радиальным смещением.
где Δr=03 – радиальное смещение(табл. К21) [2]
CΔr=3920 Нмм – радиальная жесткость муфты.(табл. 10.27) [2]
Пальцы изготовляют из стали 45 полумуфты из 30Л.
3.2.Проверочный расчет втулки на смятие.
где D0=Dх15хd0=140-15х28=98 мм
см=2х140х103(6х98х14х29)=117≤[см]=2 Нмм2.
Условие прочности втулки при смятии выполняется следовательно втулка выдержит напряжение смятия.
3.3.Проверочный расчет втулки на изгиб.
н=2хTх(05хlв+C)(ZхD0х01хdп3)
Где С=4 – зазор между полумуфтами.
н=2х140х103х(05х29+4)(6х98х01х143)=32 Нмм2.
[н]=(04 05)хт [н]=045х320=144 Нмм2. н≤[н].
Условие прочности втулки при изгибе выполняется следовательно втулка выдержит напряжение изгиба.
Конструирование основных элементов редуктора.
1. Конструирование зубчатого колеса.
Для получения заготовки используют литьё т.к. dae>180 мм. (табл. 10.3)[2]
Рис.12.1. Конструкция зубчатого колеса.
Определение основных параметров элементов колеса.
Толщина обода S=2.5х (табл. 10.3) [2]
Ширина обода bo=0.5хb; (табл. 10.3) [2]
Внутренний диаметр ступицы d=d3=48 мм
Наружный диаметр ступицы dст =155хd;(табл. 10.3)[2]
Толщина ступицы ст03хd;(табл. 10.3)[2]
Длина ступицы (табл. 10.3)[2]
Толщина диска C=0.5х(S+ст)≥0.25b; (табл. 10.3)[2]
C=0.5х(8+14.4)=11.2 мм
Радиусы закруглений R=12 мм (табл. 10.3) [2]
Отверстия принимаем d0=25 мм количеством n0=4 (табл. 10.4) [2]
На торцах зубьев выполняют фаски размером f=0.5хme (прим. к табл. 10.3) [2]
f=0.5х3.2=1.6 мм. Фаски снимают параллельно оси отверстия колеса.
2. Крепление и уплотнение подшипников тихоходного вала.
На тихоходном валу подшипники установлены без стаканов. Подшипники на глухом и сквозном конце вала крепятся буртиком пятой и третьей ступеней соответственно и уплотняются с другой стороны кольцом между внешней частью
подшипника и крышкой с полем допуска k6 и m6 соответственно что обеспечивает плотную установку. Поле допуска отверстия наружного кольца
подшипника на глухом и сквозном концах F8 и H7h6 соответственно.
Крепление и уплотнение подшипников быстроходного вала.
На быстроходном валу подшипники установлены также без стаканов. Они крепятся буртиком третьей ступени вала и гайкой круглой шлицевой класса точности А М39х15 (рис.12.2)(ГОСТ 11871-88) с параметрами: D=60 мм
D1=48 ммH=10 мм b=6 мм h=3 мм с≤1 мм (табл.К8) [2]
Кроме того подшипники уплотняются втулкой подобранной конструктивно с полем допуска Js7 отверстия и g6 на втулке (табл.10.15) [2]
Рис.12.2. Гайка круглая шлицевая.
3. Подбор крышек подшипниковых узлов.
Крышки выполнены из чугуна СЧ15.
На глухом конце тихоходного вала крышка глухая с параметрами:
D=72 мм D0=77 мм D3=62 мм h=16 мм h1=5 мм l=10 мм (табл.К18) [2]
На сквозном конце тихоходного вала крышка под манжетное уплотнение с параметрами: D=72 мм D0=77 мм D3=62 мм h=16 мм h1=5 мм l=10 мм l1=2 мм
Допускаемое отклонение диаметра крышки по h8.
Рис.12.3. Глухая крышка. Рис.12.4. Сквозная крышка под манжетное уплотнение.
На выходном конце быстроходного вала установлена крышка торцевая с отверстием под манжетное уплотнение (ГОСТ 18512-73) с параметрами:
D=90 мм D1=110 мм D2=130 мм D3=80 мм D4=92 мм d=4 мм d1=15 мм
d2=20 мм n=4 H=28 мм h=6 мм h1=12 мм B=15 мм b=4 мм S=6 мм B1=15 мм
b1=11 мм l=3 мм h2=3 мм отклонения отверстия в крышке H12(табл.К16)[2]
Рис.12.5. Крышка торцевая с отверстием.
4. Подбор уплотнительных устройств.
На сквозном конце тихоходного вала в крышку встроена армированная резиновая манжета (ГОСТ 8252-79) типа 1 с параметрами:
d=35 мм D1=58 мм h1=10 мм(табл.К20)[2]
Рис.12.6. Манжета армированная резиновая.
На сквозном конце быстроходного вала в крышку встроена такая же манжета как и на тихоходном валу по типоразмеру.
5. Корпус редуктора.
Толщина стенок корпуса =1124√Т2≥6 мм.
=1124√80=8 мм по рекомендациям выполняется толщина 15 мм(гл.10.5.)[2]
Крышка корпуса крепится винтами количеством 10 М10-6gx60.68.029
(ГОСТ 11738-84)(табл.К6) [2]
6. Конструирование смотровой крышки.
Выбираем крышку с ручкой с параметрами:
h5=3 мм к=5 мм которая крепится четырьмя винтами М6-6gх22.68.029
Рис.12.7. Смотровая крышка.
7. Конструирование шкива.
Ширина шкива передач:
Выбирается в зависимости от ширины ремня b=100 B=112 мм
чуг=003x(D+2xB)(табл.10.23) [2]
чуг1=003x(224+2x112)=1344 мм – для ведущего шкива
чуг1=003x(750+2x112)=292 мм – для ведомого шкива
С=(12 13)x(табл.10.23) [2]
С1=125x1344=168 мм – для ведущего шкива
С2=125x292=365 мм – для ведомого шкива
d=d1=30 мм (табл.10.23) [2]
где d1 – диаметр первой ступени ведущего вала конической передачи
dст=1.6xd – для чугунных шкивов. (табл.10.23) [2]
lcт=(12 15)xd(табл.10.23) [2]
Расчет массы и технический уровень редуктора.
1. Расчет массы редуктора.
φ0.43 (рис.12.2) [2]
ρ=7300 кгм3 - плотность чугуна
V=458х220х387=38994120 мм2
m=7300х0.43х38994120=1224 кг
2.Определение критерия технического уровня редуктора.
Низкая качествен-ная оценка техни-
Список использованной литературы:
Дунаев П.Ф.Леликов О.П.«Детали машин. Курсовое проектирование» М.1984.
Шейнблит А.Е.«Курсовое проектирование деталей машин» М.1991.
Куклин Н.Г. Куклина Г.С.«Детали Машин» учебник для техникумов М.1987.
.cdw

.cdw

.cdw

Неуказанные предельные отклонения размеров
точности по СТ СЭВ 302-76
Сталь 45 ГОСТ 1050-88
sechenia.cdw

(.1).spw

.cdw

.cdw

Передаточное число редуктора u=3
Вращающий момент на тихоходном
Частота вращения быстроходного
Технические требования:
Размеры для справок.
Редуктор залить маслом:
И-Г-А-68 ГОСТ 17479.4-87.
Привод допускается эксплуатировать
с отклонением от горизонтального
положения на угол до 5
быть обеспечен уровень масла
длясмазки зацепления.
Сталь 45 ГОСТ 1050-88
Характеристика зацепления
.cdw

(.2).spw

Подшипник 7209 ГОСТ 8338-75
Шайба 15 ГОСТ 11371-78
.cdw

.cdw

.cdw

Осев. ф-ма зуба ГОСТ 19325-73
Направление линии зуба
Коэффициент смещения
Степень точн. ГОСТ 1758-81
Межосевой угол передачи
Внешнее конусное расстояние
Средний делит. диаметр
Обозначение чертежа соп-
ряженного зубчатого колеса
Радиусы скруглений 2мм max.
Сталь 45 ГОСТ 1050-88
..cdw

Рекомендуемые чертежи
- 06.04.2022
- 24.01.2023
- 09.05.2024
- 19.01.2021