Проектирование привода пластинчатого конвейера




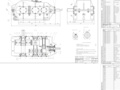
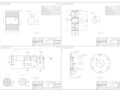

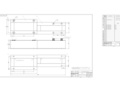
- Добавлен: 25.10.2022
- Размер: 2 MB
- Закачек: 0
Описание
Состав проекта
![]() |
![]() ![]() ![]() ![]() |
![]() ![]() ![]() |
![]() ![]() ![]() ![]() |
![]() ![]() ![]() ![]() |
![]() |
![]() |
![]() |
![]() |
![]() |
![]() |
![]() |
![]() ![]() ![]() ![]() |
![]() ![]() ![]() |
![]() |
Дополнительная информация
Редуктор Сборочный чертеж.dwg

Передаточное число 12
Крутящий момент на выходном валу
подводимая к редуктору
Плоскость разъема покрыть герметиком при окончательной
После окончательной сборки быстроходный вал должен свободно
от руки проворачиваться
Редуктор красить изнутри маслостойкой краской
Шпонки ГОСТ 23360-78
Манжеты ГОСТ 8752-79
записка 16-6.doc
Детали машин являются первым из расчетно-конструкторских курсов в котором изучают основы проектирования машин и механизмов. Именно по этой дисциплине выполняют первый курсовой проект требующий от студента знания не отдельной дисциплины а ряда дисциплин в комплексе. Выполняя этот проект студент использует материал изученный в таких дисциплинах как сопромат материаловедение теоретическая механика и т.д. Курсовой по деталям машин является первой по своей сути творческой работой студента.
Основная цель курсового проекта по деталям машин – приобретение студентом навыков проектирования. Работая над проектом студент выполняет расчёты учится рациональному выбору материалов и форм деталей стремится обеспечить их высокую экономичность надёжность и долговечность. Приобретённый студентом опыт является основой для выполнения им курсовых проектов по специальным дисциплинам и для дипломного проектирования а так же всей дальнейшей конструкторской работы.
Основной задачей данного курсового проекта является создание и проектирование по заранее заданным техническим характеристикам и кинематической схеме привода скребкового конвейера общего назначения. Изучение методов расчета и выбора элементов привода получение навыков проектирования позволяющих обеспечить необходимый технический уровень надежность и долговечность механизма. В состав проекта входят подбор электродвигателя разработка общего вида привода кинематический и прочностной расчет редуктора в частности тихоходной ступени вала со звездочкой и подшипниками рамы и рабочих чертежей деталей.
F = 1800 H – на одной звездочке;
Срок службы – С = 6 лет.
Кинематическая схема:
Кинематический и силовой расчет привода. Выбор двигателя.
Определим делительный диаметр приводной звездочки:
Определим угловую скорость вращения барабана.
Определим по формуле 5.3 (1 стр. 74) требуемую мощность двигателя.
Где - общий КПД привода.
– КПД одной пары подшипников ;
- КПД конической передачи .
- КПД цилиндрической передачи .
По ГОСТ 19523-81 примем электродвигатель 4А132М4У3 мощностью 11кВт. Синхронная частота вращения вала двигателя .
Угловая скорость вала двигателя:
Требуемое передаточное число привода.
Примем передаточное число конической передачи первой цилиндрической передаточное число второй цилиндрической передачи:
Определим угловые скорости валов:
Мощности на валах привода:
Крутящие моменты на валах привода:
Расчет конической передачи.
1 Выбор материалов и расчет допускаемых напряжений.
Примем материал шестерни сталь 40Х с твердостью НВ1 = 250 а колеса – сталь 40Х с твердостью НВ2 = 220.
По таблице 9.8 (1. стр. 174) определим пределы контактной и изгибной выносливости.
По формуле 9.10 (1. стр. 151) определим допускаемые контактные напряжения:
Для косозубых колес
- коэффициент запаса.
По формуле 9.14 (1. стр. 152) определим допускаемые напряжения изгиба:
По формуле 9.40 (1. стр. 162) определим внешний делительный диаметр колеса.
- для колес с круговыми зубьями (1 стр. 162)
- коэффициент распределения нагрузки между зубьями.
- коэффициент отношения длины зуба к внешнему конусному расстоянию.
Примем (по ГОСТ 12289-76).
Примем внешний окружной модуль
Определим числа зубьев колес.
Внешний делительный диаметр шестерни
Углы делительных конусов.
Внешнее конусное расстояние
Среднее конусное расстояние
Средний окружной модуль
Средние делительные диаметры
3 Проверочный расчет
Данный расчет выполним по формуле 9.42(1 стр.163) определим действительные контактные напряжения и сравним их с допускаемыми.
Окружная скорость колес:
Принимаем 7 – ю степень точности зацепления.
- для прямозубых колес.
По формуле 9.45 (1 стр. 164) выполним проверочный расчет на изгиб.
Где - коэффициент формы зуба зависящий от приведенного числа зубьев
По таблице 9.10 (1 стр. 175)
Рассмотрим отношения:
У колеса отношение меньше по нему и ведем дальнейший расчет.
Для косозубых колес .
Расчет цилиндрической зубчатой передачи.
Материалы колес примем те же что и при расчете первой ступени.
По формуле 9.39 (1 стр. 162) определим межосевое расстояние.
- для косозубых колес и 495 – для прямозубых.
- принятое отношение ширины зубчатого венца колеса к межосевому расстоянию.
Ширину шестерни примем .
Примем предварительно модуль зацепления .
Угол наклона зуба =10º.
Определим число зубьев шестерни:
Число зубьев колеса:
Определим делительное межосевое расстояние:
Приняв межосевое расстояние а=140мм определим действительный угол наклона зуба:
Делительные диаметры:
Межосевое расстояние:
2 Проверочный расчет.
Данный расчет ведем по формуле 9.42 (1 стр. 163)
Принимаем 8-ю степень точности зацепления.
По формуле 9.44 (1 стр. 164) проверим прочность зубьев колес на изгиб.
Расчет цилиндрической зубчатой передачи (третьей ступени).
Проектный расчет валов.
Данный расчет ведем по формуле 14.7 (1 стр. 294)
- допускаемое напряжение кручения (1 стр. 294).
1 Быстроходный вал.
Примем диаметр конца вала 32мм под подшипники 35мм.
Примем диаметр вала под подшипники 35мм под колесом 40мм.
Примем диаметр под подшипники 45мм под колесом 50мм.
4 Выходной и приводной валы.
Примем диаметр конца вала 48мм под подшипники 50мм под колесом и звездочками 55мм.
Расчет конструктивных размеров корпуса и крышки редуктора.
Данный расчет выполняем согласно таблице 10.2 (2 стр. 241).
Толщина стенки корпуса и крышки.
Толщина фланцев разъема.
Толщина нижнего пояса корпуса.
Диаметр фундаментных болтов.
Диаметр стяжных болтов фланцев примем .
Ширина нижнего пояса корпуса . Расстояние от стенки корпуса до оси болта .
Для фланцев разъема: ; .
Расчет шпоночных соединений.
Данный расчет ведем по формуле 4.1 (1 стр. 48)
Где - допускаемое напряжение смятия (1 стр. 48).
- диаметр вала в месте установки шпонки
- рабочая длина шпонки без учета закруглений
- размеры сечения шпонки и глубина шпоночного паза вала по ГОСТ 23360-78.
- величина крутящего момента.
Длина ступицы колеса 40мм.
4 Конец выходного вала.
5 Выходной вал в месте установки колеса.
Расчет усилий действующих в цилиндрической прямозубой передаче.
Примем величину консольной нагрузки от муфты.
Подбор подшипников выходного вала.
Примем расстояние между опорами вала L =276мм. Расстояние от середины колеса до опоры примем 76мм. Расстояние от середины конца вала до опоры примем 82мм. Составляем расчетную схему для определения. Опорных реакций в вертикальной и горизонтальной плоскостях.
Определим опорные реакции в вертикальной плоскости.
Строим эпюру изгибающих моментов.
Определим опорные реакции в горизонтальной плоскости.
Строим эпюру изгибающих моментов
Строим эпюру суммарных моментов.
По большей реакции ведем подбор подшипников.
Устанавливаем на вал шарикоподшипник 210 с динамической грузоподъемностью .
По формуле 16.1 (1 стр. 331) определим расчетную нагрузку действующую на подшипник
Где - коэффициент безопасности.
- коэффициент учета температуры.
Рассмотрим отношение:
По таблице 16.12 (1 стр. 358)
По формуле 16.9 (1 стр. 332) определим требуемую долговечность принятого подшипника при работе в две смены.
Определим требуемую динамическую грузоподъемность подшипника.
Проверочный расчет выходного вала.
По формуле 14.8 (1 стр. 294) определим коэффициент запаса прочности материала вала.
- наименее допускаемый коэффициент запаса материала вала
- запасы прочности по изгибу и кручению
и - пределы выносливости материала вала при изгибе и кручении. Примем материал вала сталь 45 с пределом прочности .
- амплитуды и средние напряжения циклов нормальных и касательных напряжений.
По таблице 14.2 (1 стр. 299)
По таблице 14.3 (1 стр. 300)
По таблице 14.4 (1 стр. 300)
Муфты выбираем по расчетному моменту определяемому по формуле 17.1 (1 стр. 364)
- коэффициент условий работы
1 Муфта между двигателем и редуктором.
По ГОСТ 21424-75 принимаем упругую муфту передающую наибольший крутящий момент 250Нм.
2 Муфта между редуктором и барабаном.
По ГОСТ 5006-83 принимаем зубчатую муфту передающую наибольший крутящий момент 1400 Нм.
Смазка узлов привода
Зубчатые передачи смазываем картерным способом путем окунания зубчатых колес в масляную ванну. Тип масла примем И-100А по ГОСТ 20799-75. В подшипниковые опоры закладываем солидол жировой по ГОСТ 1033-79.
Для контроля за уровнем масла устанавливаем маслоуказатель для слива масла – маслосливную пробку.
При выполнении курсового проекта по «Деталям машин» были закреплены знания пройденных предметов: теоретическая механика сопротивление материалов материаловедения и других предметов. Также получены навыки по проектированию закрытых конических и цилиндрических зубчатых передач.
Кроме того произведен подбор подшипников валов рассчитаны шпоночные соединения выполнен проверочный расчет выходного вала выбран двигатель.
Список использованных источников
Кузьмин А.В. Расчеты деталей машин А.В. Кузьмин и др. – Мн.: 1986.
Чернавский С.А. Курсовое проектирование деталей машин С.А. Чернавский и др. – М.:1987г.
Привод Сборочный чертеж.dwg

Электродвигатель 4A225М2
Передаточное число 12.06
Привод обкатать без нагрузки в течение не менее 1 часа. Стук и
резкий шум не допускаются.
После обкатки масло из редуктора слить и залить масло
индустриальное И-100А ГОСТ 20799-75 в количестве одного литра
Электродвигатель 4A132М4У3
Передаточное число 12
Схема крепления привода к раме (1:5)
Схема крепления рамы к фундаменту (1:5)
Муфта упругая втулочно-
Рама Сборочный чертеж.dwg

контуру прилегания деталей.
После сборки раму отжечь для снятия внутренних напряжений.
деталировка.dwg

Степень точности по ГОСТ 16202-81
Сталь 45 ГОСТ 1050-88
Сталь 40Х ГОСТ 4543-71
Сталь 20 ГОСТ 1050-88
содержание.doc
Расчет конической передачи . .. .. . 7
1 Выбор материалов и расчет допускаемых напряжений. 7
2 Проектный расчет по контактным напряжениям .. 7
3 Проверочный расчет по контактным напряжениям .. 9
Расчет цилиндрической зубчатой передачи .11
1 Проектный расчет .11
2 Проверочный расчет 12
Расчет третьей ступени 14
1 Проектный расчет .14
2 Проверочный расчет .15
Проектный расчет валов . 17
Расчет конструктивных размеров корпуса и крышки редуктора.. 18
Расчет шпоночных соединений 19
Расчет усилий действующих в цилиндрической прямозубой передаче .21
Подбор подшипников выходного вала ..22
Проверочный расчет выходного вала ..25
Смазка узлов привода .. ..28
Список использованных источников ..30
Рекомендуемые чертежи
Свободное скачивание на сегодня
- 24.01.2023