Проект завода для капитального ремонта тракторов Т - 130 и их агрегатов




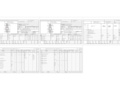
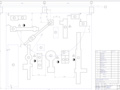
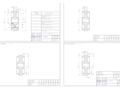
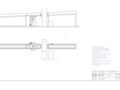
- Добавлен: 25.10.2022
- Размер: 730 KB
- Закачек: 1
Описание
Состав проекта
![]() |
![]() |
![]() ![]() |
![]() ![]() |
![]() ![]() ![]() ![]() |
![]() ![]() ![]() ![]() |
![]() ![]() ![]() ![]() |
![]() ![]() |
![]() ![]() |
![]() ![]() ![]() ![]() |
![]() |
![]() ![]() ![]() |
![]() ![]() ![]() |
![]() ![]() ![]() |
![]() ![]() ![]() |
![]() ![]() ![]() |
Дополнительная информация
лист 3.dwg

Суммарная площадь оборудования производственного
инвентаря и площадок в плане
поддерживающих колесс
Стенд для сборки опорных
Вертикально-сверлильный
Площадки для складирования
РМЗ - 01 - 01 - 00 ПТ
Площадь производственного участка
лист 4.dwg

Износ буртов направляющих
Износ беговых дорожек
Трещины в любом месте
Износ перемычек по высоте
маршрут карты.dwg

Наименование и марка
Наплавочная головка АДС-1000-2
Сварочный выпрямитель ВС-600
Очистить поверхность
Операционная карта механической обработки дет.
Наплавить беговую дорожку
выдерживая размеры 1
Наплавить торцевую поверхность
направляющего выступа
выдерживая размеры 4
Шлаковую корку удалять
Точить торцевую поверхность
(первый заглавный лист)
Наименование и содержание
продефектовать деталь
согласно карты контроля -
сортировки (таблица 5.1)
Наименование операции
Оборудование (Наименование
Инструмент (код и наименование)
Токарно-винторезный 1А64
Трехкулачковый патрон
Переустановить деталь
Маркировать дефекты краской
лист 1.dwg

Гидравлическую систему заправить
маслом И-20А ГОСТ 20799-75 уровень
масла на должен выходить за показания
Гидравлические шланги подвести таким
что бы они не мешали
перемещению раюочих на линии
Течь масла в местах разъемов на
Покрытие ЭМНЦ-25 светло-зеленый ГОСТ
Остальные технические требования по
записка.docx
За последние годы произошло значительное обновление парка строительных и дорожных машин (СДМ) отечественного производства. Сейчас это высокопроизводительные машины с гидравлическим и электрическим приводами унифицированными и долговечными узлами оснащенные автоматическими устройствами и приборами облегчающими контроль за их работой управлением техническим обслуживанием и ремонтом.
Важнейшими условиями повышения эффективности использования СДМ увеличения срока их службы и надежности является правильная эксплуатация и высококачественный ремонт. Этому способствует действующая в строительной отрасли система планово-предупредительного технического обслуживания и ремонта СДМ (ППР). Она представляет собой комплекс организационно-технических мероприятий предупредительного характера проводимых в плановом порядке в течении всего срока службы машин при соблюдении заданных условий и режимом их эксплуатации. В соответствии с этой системой предусмотрено проведение технических обслуживании и ремонтов: текущего и капитального.
На современных ремонтных предприятиях используют индустриальные методы ремонта и том числе агрегатно-узловой [1] базирующейся на замене вышедших из строя сборочных единиц и деталей отремонтированных в заводских условиях Оборудование этих предприятий аналогично оборудованию применяемому в машиностроении.
Несмотря на это в настоящее время ремонтное производство по своей эффективности организационному и техническому уровню все еще отстает как от машиностроения (сфера изготовления) так и от строительства (сфера потребления машин). Вследствие ряда причин ремонт СДМ все еще носит полукустарный характер что приводит к длительным простоям техники высокой стоимости и низкому качеству ремонта. В нашей стране на ремонт затрачиваются значительные трудовые материальные и финансовые ресурсы. Так стоимость ремонта строительной машины за весь срок службы в 2-3 раза превышает стоимость новой а на выполнение ремонтных работ в стране занято до 15% рабочих и 13 парка металлорежущих станков [1]. Все это отражаемся на себестоимости строительно-монтажных работ.
Эти данные свидетельствуют о том что совершенствование ремонтного производства СДМ является крупным резервом повышения эффективности отрасли капитального строительства.
В этой связи данная работа посвящена проектированию специализированного ремонтно-механического завода для капитального ремонта СДМ.
Анализ состояния ремонтного производства СДМ
1 Система планово-предупредительного ремонта
На работоспособность машин во многом влияет своевременное и качественное проведение ТО и ремонта. В нашей стране внедрена система планово-предупредительного ТО и ремонта (ППР) которая регламентирует сроки и объем работ предупреждающих возникновение неисправностей машин и механизмов повышает их производительность и улучшает качество строительства.
Система ППР представляет собой комплекс организационно-технических мероприятий предупредительного характера проводимых в плановом порядке для обеспечения работоспособности и исправности машин в течение всего их срока службы при соблюдении заданных условий и режимов эксплуатации.
Основана система ППР на обязательном планировании подготовке и проведении ТО и ремонтов каждой машины находящейся в эксплуатации с заданной последовательностью и периодичностью. ТО должно обеспечить поддержание работоспособности машины в процессе эксплуатации путем проведения комплекса работ по предупреждению повышенного изнашивания деталей отказов и повреждений машины. Указания и нормы по обеспечению работоспособности строительных машин регламентированы «Рекомендациями по организации технического обслуживания и ремонта строительных машин» разработанными ЦНИИОМТП Госстроя СССР и ВНИИстройдормашем Минстроидормаша СССР.
В процессе использования машин проводятся: а) ежесменное ТО (ЕО) выполняемое перед началом в течение или после рабочей смены; б) плановое ТО выполняемое в плановом порядке через определенное установленное заводом-изтотовителем время наработки; в) сезонное ТО (СО) выполняемое два раза в год при подготовке машины к использованию в период летнего или зимнего сезона.
Для сохранения работоспособности машины при транспортировании и хранении проводятся специальные ТО в соответствии с требованиями эксплуатационной документации.
ЕО проводится машинистами (членами экипажа) за которыми закреплена машина. Если на машинистов возложена функция только по управлению машиной то ЕО проводится централизованно во внесменное время персоналом специализированных участков планово-предупредительного ТО и ремонта машин. Выполнение работ предусмотренных ЕО обязательно и поэтому не планируется.
ТО для конкретных машин отличается друг от друга периодичностью и составом работ. Каждому виду ТО в зависимости от последовательности проведения присваивается порядковый номер (ТО-1 TO-2 ТО-3). В состав работ ТО имеющего более высокий порядковый номер входят работы каждого из предшествующих видов ТО включая ежесменное.
При ТО строительно-дорожных машин в основном выполняют очистку осмотр техническое диагностирование регулирование смазывание заправку и опробование.
Виды плановых ТО периодичность их проведения состав и порядок выполнении работ завод-изготовитель указывает в эксплуатационной документации по каждой модели машин. Периодичность ТО и ремонтов машин устанавливают в часах наработки.
После проведения ТО машину принимают машинист и механик эксплуатационного участка за которым она закреплена. При приемке машину осматривают и опробуют ни холостом и рабочем ходу. После этого в журнале учета ТО и ремонтов а также в журнале учета неисправностей делают соответствующие записи об объеме выполненных работ и ставят подписи ответственных лиц сдающих и принимающих работу.
Ремонт машин - это комплекс работ обеспечивающих устранение повреждений и отказов для восстановления работоспособности и исправности машин. Плановые ремонты машин установлены двух видов: текущий (Т) и капитальный (К).
Текущий ремонт должен обеспечивать гарантированную работоспособность машины до очередного планового ремонта путем восстановления и замены отдельных оборочных единиц и деталей в объема определяемом техническим состоянием машины. При текущем ремонте производится частичная разработка машин устраняются неисправности возникающие в процессе эксплуатации детали заменяются заранее отремонтированными.
Текущий ремонт машин на базе тракторов и машин с двигателями тракторного типа совпадает по периодичности с третьим ТО (ТО-3) поэтому они проводятся одновременно.
Капитальный ремонт должен обеспечивать исправность и полный или близкий к полному ресурс машины путем восстановления и замены сборочных единиц и деталей включая базовые.
Периодичность проведения ТО и ремонтов определяется межремонтным циклом и их структурой.
Межремонтный цикл-наработка машины в часах от начала ее эксплуатации до первого капитального ремонта или между двумя очередными капитальными ремонтами.
Структура межремонтного цикла – число периодичность и последовательность выполнения всех видов ремонта и ТО за межремонтный цикл. Структура межремонтного цикла для разных типов машин различна и устанавливается соответствующей технической документацией [23].
Таблица 1.1 -Периодичность ТО и ремонтов бульдозеров на базе трактора Т-130
Периодичность выполнения ТО маш.-ч
Число ТО и ремонтов в одном межремонтном цикле
Система планово-предупредительного ремонте машин реализуется: а) путем разработки планов ТО и ремонта; б) путем разработки и осуществления организационно-технических мероприятий обеспечивающих своевременное и качественное выполнение работ по ТО и ремонту в плановые сроки при минимальных материальных и трудовых затратах; в) путем организации систематического учета наработки машин и контроля за реализацией планов ТО и ремонта.
2 Технико-экономическое значение ремонта машин
Для капитального ремонта основные в строительстве машины -
экскаваторы бульдозеры краны автогрейдеры и т.п. обычно направляют на ремонтные заводы или ремонтируют их в условиях эксплуатации на основе сборочных единиц отремонтированных на этих заводах. Капитальный ремонт машин - сложная категория - и должен быть рассмотрен как с технических так и с экономических позиций.
С технической стороны капитальный ремонт восстанавливает ресурс машины выработанный в результате ее эксплуатации т. е. ликвидирует последствия физического износа. Для этого машины на ремонтных заводах подвергают воздействию определённых технологических процессов. Анализ технологий ремонта и изготовления одной и той же модели машины позволяет сделать заключение о тождественности этих технологий (рисунок 1.1). В сущности различие заключается только в подготовительных процессах. Поэтому заводской ремонт машин по выражению проф. К. Т. Кошкина является «вторичным машиностроением» т.е. вторичным производством на основе деталей бывших в употреблении.
Ремонт техники с экономических позиций является воспроизводством основных фондов. Иными словами и с этой стороны определение «вторичное машиностроение» вполне обосновано.
И хотя в настоящее время ресурс отремонтированных машин значительно ниже ресурса новых это не опровергает сделанного определения так как является не коренным пороком природы ремонта как техническо-экономической категории а лишь результатом исторически сложившихся и укоренившихся недостатков в организации ремонтного производства.
Рисунок 1.1 – Схема сопоставимости технологических процессов изготовления и ремонта строительных машин
При этом определение «вторичное машиностроение» «вторичное производство» учитывает и невозможность получения отремонтированной машины в точности равной новой поскольку не устраняет определенного остаточного физического износа (например усталости материала). Таким образом задача ремонта - обеспечение нормального функционирования техники т.е. поддержание и восстановление исправности или работоспособности машины утрачиваемые ею в процессе эксплуатации.
В практике ремонт строительных машин обходится достаточно дорого. Так стоимость ремонта машин за весь срок в 2-3 раза превышает стоимость новой [1].
Анализ затрат показывает что фактические затраты на ТО и ремонт машин возрастает в последующих межремонтных циклах по сравнению с первым циклом.
Значение ТО и ремонта машин в строительстве видно из доли затрат ни эти процессы в себестоимости эксплуатации. По данным [1] в составе плановой себестоимости 1 маш.-ч эксплуатации строительных машин затраты на ТО и ремонт составляют до 50%.
Значимость проблемы ремонта машин для всего народного хозяйства можно оценить исходя из следующего.
Срок службы машин в среднем 10-12 лет первый межремонтный цикл составляет примерно 3-4 года. Значит только 13 времени работает машина выпущенная машиностроительным заводом. Отсюда можно ориентировочно принять что в народном хозяйстве (в том числе и в строительстве) 23 работающего парка машин прошли капитальный ремонт. На выполнении ремонтных работ в стране занято до 15 % рабочих 13 парка металлорежущих станков.
С учетом выше изложенного капитальный ремонт как технико-экономическую категорию можно характеризовать разновидностью ремонта возникшую как способ воспроизводства для ликвидации дефиците в технике представляющую собой историческую категорию которая в зависимости от условий может развиваться или исчезнуть совсем если становиться не эффективной
3 Причины неудовлетворительного состояния ремонтного
Система ППР в строительстве позволила построить ТО и ремонт строительных и дорожных машин на единой нормативной основе. К сожалению эти нормативы имеют существенные недостатки. Главный из них заключается в том что нормативы являясь усредненными не отражают конкретных условий эксплуатации машин. Для каждой группы машин установлены единые нормативы независимо от отрасли строительства организации ремонтного производства грунтовых условий и т. п. Следовательно действующие нормативы пригодны лишь для условного укрупненного планирования и не стимулируют интенсификации производства.
До настоящего времени развитие ремонтного производства в нашей стране в том числе и ремонта строительной техники носило экстенсивный характер. С ростом механизации строительства оно происходило главным образом за счет увеличения числа ремонтных заводов. Что касается качественных показателей то они не улучшались.
Специфика строительства накладывает определенный отпечаток на постановку ремонтного производства. В свою очередь различные отрасли строительного производства также обладают спецификой что отражается на эксплуатации машин и должно быть учтено в организации их ремонта.
В зависимости от степени концентрации строительно-монтажных работ характера строящихся объектов и их территориального размещения капитальное строительство может быть классифицировано не сосредоточенное рассредоточенное и линейное.
Для сосредоточенного строительства (строительство электростанций заводов шахт и т. п.) характерна концентрация на сравнительно небольших площадях значительных объемов строительно-монтажных работ выполнение которых рассчитано на длительный период (5-8 лет). В этом случае производственно-техническая база для строительных организаций в том числе ремонтно-эксплутационная база для строительных машин носит стационарный характер и максимально приближена к объектам строительства. Сосредоточенному строительству свойственна большая специализация строительно-монтажных работ что позволяет в свою очередь специализировать парки машин управление ими ТО и ремонт.
Эти особенности сосредоточенного строительства создают условия для индустриализации ремонтных работ т.е. переноса основных их объемов на ремонтные предприятия освободив от этих обязанностей службы эксплуатации строительных организаций.
Для рассредоточенного строительства (например сельского строительства) характерны небольшие по объему объекты размещенных на определенной территории (несколько районов область) с непродолжительными сроками строительства. Строительно-монтажные работы выполняются передвижными механизированными колоннами (ПМК) оснащенными необходимым (обычно разнообразным по назначению а следовательно по конструкции и типоразмером) парком машин оборудования. После окончания строительства определенных объектов ПМК перебазируется на другие в пределах обслуживаемого ею территориального района. Обычно несколько ПМК объединяются в строительно-монтажном тресте. Наиболее целесообразной организационной формой управления парком машин такого треста является концентрация их в управлении механизации (УМ) треста. Такое УМ может иметь стационарную ремонтно-эксплуатационную базу обслуживающую все свои ПМК.
В этих условиях как правило невозможно проводить специализацию ремонта в рамках одного треста.
Линейное строительство (строительство железных шоссейных дорог газо- и нефтепроводов линий связи и электропередач и т.п.) характеризуется: большой протяженностью фронта строительно-монтажных работ; наличием большого числа мелких строительных объектов требующих для своего сооружения незначительного числа разнообразных машин; частой передислокации низовых строительно-монтажных организаций различного назначения (механизированные колонны земляных работ путеукладочные поезда дорожно-строительные отряды и т.п.); рассредоточением указанных организаций по трассе строительства; значительным расстоянием строительных объектов от ремонтно-эксплуатационных баз и ремонтных предприятий.
В условиях линейного строительства значительную долю в общих затратах времени на ремонт занимает время транспортирования машин с объектов строительства на ремонтные предприятия и обратно.
Здесь также невозможна специализация ремонтного производства в пределах одного строительства (например в пределах строительства какой-либо железнодорожной линии).
На состояние ремонтного производства в строительстве существенное влияние оказывает структура управления строительством и сложившееся традиционное мнение о месте работ по ремонту техники.
В настоящее время капитальное строительство ведется несколькими крупными территориальными строительными ведомствами. Каждое из них министерств и ведомств имеет определенный машинный парк и свою ремонтно-эксплутационную базу обслуживающие эти машины.
Все это самых серьезным образом отражается на результатах ремонта техники а следовательно на эффективности ее использования. Создалось положение при котором строительные машины выпушенные промышленностью на современном техническом уровне проработав 2-4 года (время одного ремонтного цикла) для восстановления своего ресурса попадают на полукустарные универсальные ремонтные заводы мелкосерийного и единичного производства где уже в силу хотя бы только их универсальности невозможно обеспечить ресурс и качество того уровня который был заложен при их изготовлении. Все это наносит серьезный ущерб народному хозяйству.
Из сказанного следует что на малую эффективность ремонта машин влияют следующие основные факторы:
) разобщенность ремонтных заводов по отдельным строительным организациям разных уровней (министерства главки тресты управления);
) отнесение ж ремонтных й заводов к вспомогательному производству;
) загрузка ремонтных заводов не свойственной им продукцией;
) отсутствие единого технического руководства в том числе методического центра;
) низкий уровень специализации и концентрации и как следствие слабая механизация работ высокая трудоемкость и стоимость ремонта;
) недостаточное обеспечение запасными частями со стороны промышленности;
) слабая организация восстановления деталей.
4 Технико-экономический анализ методов ремонта
и организации производства
В настоящее различают ремонт машин необезличенный и обезличенный [2].
При необезличенном ремонте восстановительные операции производятся с учетом принадлежности восстанавливаемых деталей и умов к определенному экземпляру данной модели машин. Это означает что узлы и основные детали после их ремонта устанавливают на ту же машину с которой они были сняты.
Основные недостатки: а) длительность так как время ремонта машины включает также время ремонта деталей; б) необходимость больших производственных площадей на ремонтных предприятиях так как разобранная машина все время затрачиваемое на ремонт снятых с нее деталей находится в цехе.
Необезличенный ремонт характерен для единичного или мелкосерийного производства. Он может быть применен лишь в тех случаях когда парк машин хозяйства обслуживаемого ремонтным предприятием состоит из небольшого числа машин различных видов и моделей.
Метод организации производства при необезличенном ремонте — бригадный (универсальные или специализированные бригады). При работе универсальными бригадами (тупиковый метод) каждая бригада рабочих разбирает машину. Детали направляют для ремонта в соответствующие цехи отделения или участки. Затем их возвращают в ту же бригаду и она производит сборку. Такая организация ремонта требует высокой квалификации рабочих так как каждый член бригады должен уметь отремонтировать любой узел. При этом каждая бригада должна иметь необходимые приспособления инструмент запасные части и техническую документацию для ремонта всех узлов машины.
Несколько лучшие результаты дает ремонт специализированными бригадами. В этом случае разборочно-сборочные работы выполняет одна бригада а ремонт узлов - другие бригады специализированные на ремонте определенного узла или группы узлов близких по технологическим признакам; ремонт осуществляют на определенных рабочих постах устанавливают на машину с которой они были сняты. Для таких методов организации ремонта характерны низкая производительность труда и высокая стоимость ремонта.
Обезличенный ремонт характеризуется тем что в процессе разработки и дефектации детали всех машин одной марки обезличивают а из отремонтированных годных после дефектации и новых деталей (взамен выброкованных) собирают обезличенные узлы которые устанавливают на любую машину данной модели.
Этот метод основанный на взаимозаменяемости деталей и узлов заложенный при изготовлении машин является в настоящее время основным методом ремонта. Обезличенный ремонт дает возможность укрупнить партии ремонтируемых деталей и узлов использовать преимущества серийного производства: провести внутризаводскую специализацию применять высокопроизводительное оборудование и оснащение механизировать и автоматизировать технологические процессы специализировать рабочих на определенных операциях.
Обезличенный ремонт позволяет применять профессиональные методы организации производства - агрегатно-узловой я поточный.
Агрегатно-узловой метод организации ремонта предусматривает при капитальном ремонте полную а при текущем ремонте - частичную замену узлов исправными поступающими из оборотного фонда.
Под оборотным фондом понимается определенный запас исправных сборочных единиц обеспечивающих обезличенный ремонт обслуживаемого парка машин . Первоначально этот запас образуется путем приобретения новых узлов и восстановления отдельных узлов списанных машин. Текущее пополнение оборотного фонда производят за счет ремонта узлов.
Потребное число сборочных единиц и агрегатов в оборотном фонде можно определить как [2]
Оф = 12АМВобТср(365Та) (1.1)
где 12 - коэффициент учитывающий возможности отклонения во (времени оборачиваемости элементов;
А- число одинаковых элементов и узлов на одной машине;
М - число однотипных машин в хозяйстве;
Воб - время оборачиваемости элемента (продолжительность нахождения в ремонте с момента сдачи до получения из ремонта включая время на [транспортировку) дни;
Тор - планируемое время работы машины в году ч;
Та - срок службы элемента до очередного ремонта ч.
Важнейшим условием организации ремонта агрегатно-узловым методом является сохранение неснижаемого расчетного количества узлов оборотного фонда так как иначе нарушится ритмичность производства.
Этот метод может применяться как на ремонтных предприятиях (в этом случае его именуют «узловым») так и в условиях эксплуатации т.е. на объектах строительства.
В первом случае машину разбирают на узлы которые направляют в ремонтные цехи. Сборку машин производят из узлов оборотного фонда. Отремонтированные узлы поступают в оборотный фонд.
При ремонте в условиях эксплуатации ремонтное предприятие производит только ремонт узлов а снятие (демонтаж) неисправных и сборку (монтаж) отремонтированных - производят на месте работы машины.
Агрегатно-узловой метод нашел широкое применение в различных отраслях народного хозяйства например при ремонте автомобилей тракторов экскаваторов станков и др.
Специфические условия строительства вызвали к жизни различные организационные формы агрегатно-узлового метода. Так в сосредоточенном строительстве (например при строительстве электростанций) применяется разновидность этого метода получившая наименование апериодическая замена ремонтных комплектов» (ПЗРК). Отличительная особенность ПЗРК заключается в том что сборочные единицы с близкими сроками службы группируются в комплекты заменяемые в сроки кратные наименьшему.
Например трактор Т-100М расчленен на три комплекта: в первый (К-1) входят опорные катки и натяжные колёса; во второй (К-2) - двигатель радиаторы муфты поворота муфта сцепления ходовые тележки в сборе; в третий (К-3) - корпус заднего моста с муфтой поворота муфтой сцепления и коробкой передач бортовой редуктор механизмы управления рессоры и кабина.
Ресурсы ремонтных комплектов устанавливают кратными ресурсу К-1 - наименее стойкому комплекту. Ресурсы комплекта К-1 – 1500ч К-2 - 3000 ч К-3 - 6000 ч. Установлены четыре плановых ремонта: Р-1 Р-2 Р-3 и Р-4. В объем плановых ремонтов входят замена ремонтных комплектов регулирование и испытание машины в целом. Ремонт Р-1 производится через 1500 ч работы машины и заключается в замене комплекта К-1. Ремонт Р-2 выполняют через 3000 ч работы. При этом заменяются комплекты К-1 и К-2. Ремонт Р-3 при котором заменяют комплект К-1 производят через 4500 ч работы машины а ремонт Р-4 -через 6000 ч работы. При ремонте Р-4 заменяют все три комплекта (К-1 К-2 и К-3).
При замене комплектов а не отдельных агрегатов сокращается число ремонтов машин и уменьшаются простои в ремонтах. Для проведения ремонта методом ПЗРК в эксплуатационных организациях должен создаваться оборотный фонд ремонтных комплектов.
Другой разновидностью является последовательно-узловой метод организации ремонта отличающийся тем что при очередном ремонте заменяют только узлы исчерпавшие свой ресурс т.e. весь потребный объем ремонта машины выполняется не одновременно. Замена определенных узлов или групп узлов (блоков) может выполняться при очередных ТО. Преимущества этого метода - сокращение сроков ремонта. Однако существенные трудности возникают при планировании ремонта и учете ресурса узлов.
Поточный метод может применяться на заводах ремонтирующих большое число одноименных машин. Он получил распространение на заводах по ремонту автомобилей тракторов экскаваторов.
Сущность поточного метода организации ремонта заключается в том что технологический процесс расчленен на отдельные операции выполняемые на определенных рабочих местах расположенных по ходу процесса. Этим методом может быть организованна сборка и разборка машин и агрегатов а также восстановление деталей. Расчленение технологического процесса на операции должно быть согласованно с тактом (ритмом) поточной линии.
Сборку на потоке выполняют на соответствующих сборочных постах которые могут быть подвижными что имеет место при ремонте больших серий сравнительно нетяжелых машин (например тракторов) и не подвижными - при ремонте небольших серий а также тяжелых машин (например экскаваторов с ковшом объемом более 05 м3).
Подвижные посты располагают обычно на тележках передвигаемых по рельсовому пути уложенному вдоль цеха от одного рабочего места к другому. Сборочные работы выполняют во время остановки тележек у рабочих мест.
При неподвижных постах на базовом узле собирают постепенно остальные при этом каждый узел или группа узлов собирается определенными бригадами 'Закончив сборку узла (группы узлов) на одном посту рабочие переходят к сборке такого же узла на следующем.
Поточная организация ремонта требует четкого планирования всего производственного процесса. Все цехи — разборочные ремонтные сборки узлов должны снабжать сборочную поточную линию в соответствии с установленным ритмом.
Благодаря расчленению процессов и узкой специализации рабочих мест при поточной организации ремонта создаются условия для механизации и автоматизации работ что позволяет значительно сократить время ремонта снизить трудоемкость и стоимость а также повысить качество.
Рассмотренные методы организации ремонтного производства применяются в определенных условиях В позволяют реализовать преимущество обезличенного ремонта и снизить трудоемкость стоимость и продолжительность ремонта.
Проведенный анализ методов ремонта позволяет составить классификационную схему (рисунок 1.2) в котором основным классификационным признаком служит: а) для методов ремонта -принадлежность восстанавливаемых деталей и сборочных единиц к тому экземпляру машины на которой они устанавливаются; б) для методов организации производства - степень расчлененности технического процесса.
Рисунок 1.2 – Классификация методов ремонта и организации производства
В таблице 1.1 приведены технико-экономические показатели ремонтных предприятий выполняющих необезличенный или обезличенный ремонт различными методами организации производства.
Таблица 1.1 - Технико-экономические показатели ремонтных предприятий при различных методах организации производства
Себестоимость одного ремонта
- на одного производственного рабочего
- на 1м2 производст-
Таким образом технико-экономический анализ методов и организации ремонтного производства СДМ показывает неоспоримые преимущества обезличенного метода ремонта.
Вместе с тем современное состояние ремонтного производства СДМ (низкая культура производства) а также его особенности (использование при ремонте деталей и узлов различного состояния: отремонтированных годных к эксплуатации и новых) не позволяет в полной мере пользоваться самой его прогрессивной формой организации поточного метода. Поэтому наиболее целесообразной формой организации производства на современных ремонтных предприятиях следует считать агрегатно-узловой метод ремонта.
При этом элементы поточного метода могут быть использованы на линиях сборки и разборки полнокомплектных машин и агрегатов а также на участках по восстановлению деталей.
5 Ремонтные предприятия в строительстве
Ремонтно-механические предприятия осуществляющие ремонт строительных машин и оборудования классифицируются по назначению объему производству и степени подвижности.
Для капитального ремонта сложных машин предназначены ремонтно-механические заводы (РМЗ).
ТО текущий в капитальный ремонт несложных машин выполняют базы технической эксплуатации строительных машин и их ремонтно-механические мастерские (РММ).
Базы технической эксплуатации строительных машин могут быть универсальными или специализированными. В первом случае они обеспечивают смешанные парки машин во втором - отдельные виды машин или группу машин предназначенных назначенных для выполнения определенных строительно-монтажных работ например землеройных подъемно-транспортных в т.д.
Специализация ремонтных предприятий позволяет механизировать трудоемкие и тяжелые операции применять специальные приспособления стенды оснастку и измерительные средства внедрять новые способы восстановления деталей (а это в свою очередь создает условия для улучшения качества ремонта повышения производительности труда ремонтных рабочих снижения себестоимости и продолжительности ремонта.)
По степени подвижности различают стационарные и передвижные ремонтные мастерские.
Передвижные ремонтные мастерские используют в тек случаях; когда машины постепенно перемешаются например в дорожном строительстве при сооружении газопроводов или на строительстве территориально разобщенных объектов.
В первом случае они выполняют все функции мастерских при специализированных подвижных строительных организациях - передвижных механизированных колонн (ПМК); во втором - обсаживают на месте те строительные машины которые по характеру своей работы или по конструктивным особенностям не могут возвращаться на базу для ТО или ремонта.
На строительных участках с длительным периодом работы на одном месте и большим числам строительных машин в механизмов для ТО и ремонта используют щитовые сборно-разборные мастерские и профилактории.
Передвижные мастерские обычно монтируют на шасси автомобилей. В закрытом утепленном кузове и в наружных нишах размещают комплект оборудования инструмента приспособлений запасных частей и материалов. Кузов имеет заднюю дверь и наружные ниши обогреваемые отопителем используемым летом для вентиляции.
Мастерская укомплектована необходимым числом специальных приспособлений и набором измерительных слесарных монтажных и металлорежущих инструментов. На одноосном прицепе размещен сварочный агрегат с автономным приводом. В мастерской можно выполнять мелкие ремонтные и электросварочные работы замену сборочных единиц агрегатов мойку машин их смазку проводить контрольно-регулировочные и крепежные работы. Обслуживает такую мастерскую бригада в составе трех человек: слесарь по ремонту топливной аппаратуры сварщик (он же слесарь-ремонтник) и шофер.
К средствам ТО строительных машин на месте их эксплуатации также относятся самоходные ремонтно-профилактические мастерские (СРПМ) предназначенные для комплексной механизации трудоемких работ по ТО и ремонту строительных работ; машины ТО; предназначенные для ТО и доставки к месту эксплуатации воды и горючесмазочных материалов; передвижные маслозаправочные станции диагностики гидросистем строительных машин.
В строительно-монтажных организациях строительные машины и механизмы сосредотачивают в основном ив базах механизации. Такие базы создаются при строительно-монтажных трестах управлениях механизации и крупных строительных управлениях. В своем состоянии они имеют ремонтную мастерскую профилакторий открытые и закрытые стоянки машин склады материалов запасных частей нефтепродуктов и другие помещения.
На базах механизации выполняется текущий ремонт ысех машин приписанных к ним капитальный ремонт несложных машин а также капитальный ремонт 25% сложных строительных машин агрегатным методом. Кроме того на этих базах проводят ТО всех машин в том числе 35 40% самоходных машин в профилактории снабжают машины запасными частями горючесмазочными и другими эксплуатационными материалами монтируют демонтируют комплектуют и хранят их.
На базах механизации производят ремонт и изготовление простйшего строительного инструмента приспособлений и инвентаря.
Ремонтные мастерские баз механизации имею и своем составе следующие производственные участки: механический агрегатный сварочный кузнечный электротехнический топливной аппаратуры аккумуляторный медницко-жестяницкий и несколько вспомогательных участков. Состав участков и их компоновка зависят от типа базы механизации от ее годовой производственной программы по ремонту и ТО.
Оборудование эксплуатационных баз позволяет выполнят ремонт и обслуживание современными высокопроизводительными универсальными металлорежущими станками: токарно-винторезными горизонтально- и вертикально-фрезерными поперечно-сверлильными долбежными круглошлифованными заточными обдирочными радиально- и вертикально-сверлильными; кузнечнопрессовым оборудованием: пневматическим молотом кузнечной нагревательной печью камерной и шахтной электропечами прессножницами механической ножовочной пилой; различным подъемно-транспортным оборудованием.
Для разборки сборки и испытания элементов предусмотрены стенды: для ремонта и испытания радиаторов для ремонта и испытания гидравлических и пневматических систем для испытания коробок передач гидравлический стенд для перепрессовки гусениц тракторов для демонтажа покрышек колесных машин для испытания и регулировки топливной аппаратуры для разборки и сборки обкатки и контрольного осмотра двигателей а также станки для притирки и шлифования клапанов и контроль-испытательный стенд для проверки электрооборудования.
При ремонте предусмотрено широкое применения малой механизации: поворотных электрических подъемников лебедок тяговых цепей домкратов переносных съемников гидравлических прессов электро- и пневмоинструмента.
В связи с большой номенклатурой машин и небольшим объемом работ по каждой из них ремонт производят тупиковым способом. т.е. разбирают машины ремонтируют базовые детали и собирают машины на одних и тех же постах. Снятые с машин агрегаты и сборочные единицы ремонтируют собирают и испытывают на специализированных постах. Детали требующие ремонта на соответствующих участках для восстановления.
Ремонтно-механическне заводы предназначены для капитального ремонта сложных машин: экскаваторов кранов на гусеничном и пневмоколесном ходу автогрейдеров самоходных скреперов тракторов и строительных машин на их базе (бульдозеров погрузчиков трубоукладчиков и т. п.) а также их агрегатов. По степени специализации заводы подразделяют на универсальные и специализированные.
На универсальных заводах ремонтируют машины различных типов и марок и их агрегаты изготовляют запасные чисти к ним. Для лучшей организации ремонта эти заводы имеют а цехи по ремонту отдельных типов машин например цехи ремонтные трактороремонтные и др.
На специализированных заводах ремонтируют машины какого-либо одного типа тракторы в машины на их базе. Специализация ремонтных заводов дает существенные преимущества: ремонт на этих предприятиях носит серийный характер что позволяет применить передовую организацию и технологию производства оснастить предприятия поточными линиями и высокопроизводительным оборудованием. Это значительно повышает производительность труда снижает себестоимость и сокращает сроки ремонта резко повышает его качества.
6 Основные требования к ремонтно-механическим заводам
Анализ состояния ремонтного производства СДМ опыт передовых предприятий и зарубежный опыт позволяет сформулировать основные требования к современным РМЗ [1] которые реализуются путем:
- индустриализации ремонта (т.е. приближение ремонтного производства к машиностроению);
- механизации и автоматизации производственных процессов ремонта;
- повышения качества ремонта машин;
- управления ремонтным производством на вневедомственной основе;
Индустриализация ремонтного производства в первую очередь зависит от степени его концентрации и специализации.
Концентрацией ремонтного производства называется сосредоточение ремонта на крупных ремонтных предприятиях (или в крупных ремонтных цехах). Она составляет одну из важных черт современной организации промышленного производства. Высокая концентрация производства при целесообразных размерах предприятий позволяет наиболее полно использовать высокопроизводительное оборудование материальные ресурсы и кадры. Она сопровождается ростом механизации и автоматизации производственных процессов внедрением передовой технологии развитием прогрессивных форм организации труда и производства.
Наиболее эффективной формой концентрации производства для отраслей машиностроения и металлообработки к которой относится и ремонт машин является сосредоточение на одном предприятии выпуска однородной продукции т.е. концентрация специализированного производства. Применительно к ремонту строительной техники это означает создание крупных предприятий по ремонту конструктивно родственных машин.
Концентрация ремонтного производства выражается в централизованном ремонте машин на специализированных ремонтных предприятиях.
Экономическая целесообразность концентрации проявляется во многих направлениях. Так при крупных масштабах производства сокращаются удельные капитальные вложения т.е. удешевляется единица мощности оборудования. При этом увеличивается фондоотдача так как использование оборудования в том числе высокопроизводительного и специального значительно повышается. Например при ремонте тракторов с увеличением ремонтной программы со 100 тыс. до 350 тыс. чел.-ч коэффициент загрузки станков повысился на 12%. Создается возможность применения специальных сборочных и испытательных стендов специализированных наплавочных автоматов оборудования для гальванического наращивания и т.п.
На крупных ремонтных предприятиях создаются условия для внедрения высокоэффективных технологических процессов особенно по восстановлению деталей что позволяет снизить расход новых (запасных частей экономнее расходовать материалы топливо энергию).
В условиях крупного специализированного ремонтного производства представляется возможность использовать передовые методы организации производства в частности поточные линии на сборке узлов и машин при восстановлении деталей. Это в свою очередь создает условия для механизации и автоматизации снижает трудоемкость и стоимость ремонта повышает производительность труда. Так по данным НИИАТ при концентрации ремонта автомобилей в 10 раз трудоемкость и себестоимость ремонта снизилась примерно на 25%.
Крупные предприятия имеют больше возможностей для внедрения научных достижений и передового опыта. Они в состоянии иметь соответствующие лаборатории технологические бюро отделы механизации и автоматизации с необходимой экспериментальной базой. Чем крупнее ремонтное предприятие тем меньше удельные показатели затрат (трудоемкость площадь оборудование) на единицу ремонта. Характер зависимости этих затрат от годового объема работ (рисунок 1.3) показывает что снижение затрат вначале происходит очень быстро а затем постепенно замедляется. Поэтому концентрация целесообразна в определенных пределах. При этом необходимо также учесть фактор дальности транспортирования машин в ремонт так как при увеличении размеров ремонтных заводов затраты на транспортирование ремонтного фонда и отремонтированных машин возрастут. Поэтому должны быть установлены рациональные границы концентрации т.е. целесообразные размеры РМЗ.
a - удельное количество станков; б- удельная площадь; в – удельная трудоемкость.
Рисунок 1.3 - зависимость удельных показателей на единицу ремонта от
годового объема ремонтных работ
Специализация ремонтного производства представляет такую форму его организации при которой ремонт машин или сборочных единиц (агрегатов и узлов) а также выполнение определенных оконченных технологических процессов по восстановлению деталей происходит на специальных предприятиях в цехах или на участках.
В ремонтном производстве находят применения все известные виды специализации предметная подетальная (поузловая) технологическая.
Предметная специализация применительно к ремонту строительной техники означает выделение ремонтных заводов специализированных на ремонте определенных видов машин. Примером могут служить типовые специализированные заводы по ремонту одноковшовых экскаваторов и гусеничных тракторов и машин на их базе и т.п.
Улучшение внутрипроизводственной структуры таких ремонтных заводов может идти по пути дальнейшего углубления специализации создавая цехи и участки поузловой (например цехи по ремонту двигателей) и технологической (участки по наплавке деталей гальванические участки и т. п.) специализации.
Поузловая специализация имеет место при обособлении отдельных агрегатов например агрегатно-ремонтные заводы мотороремонтные заводы.
В ремонтно-сборочных цехах распространена специализация участков (бригад) по ремонту однотипных или близких по конструции узлов (например участки ремонта гусеничного хода трансмиссии рабочего оборудования и т.п.). Такая специализация может иметь место и в крупных цехах универсальных ремонтных заводов. Для повышения продолжительности труда качества продукции и других показателей на этих заводах при достаточных масштабах производства выделяются специализированные цехи по ремонту экскаваторов бульдозеров двигателей и т.п.
Таким образом отличительной чертой специализации ремонтного производства является конструктивная однородность машин и однородность технологии. Признаком однородности является их технологическая близость определяемая общностью основных элементов производства.
Технико-экономические показатели ремонтных заводов передметной специализации выше чем у универсальных.
Узловая и технологическая специализация в связи с возможностью создания технологической однородности предпосылки к организации массово-поточного применению высокопроизводительного оборудования. Показатели этом будут выше чем предметной специализации.
Большой экономический эффект дает создание специализированных производств (заводов цехов участков) по специализированному восстановлению деталей машин.
Специализация ремонтных предприятий позволяет вести ремонт на индустриальной основе с применением прогрессивной техгологии передовых методов труда более полного использования специализированного высокопроизводительного оборудования. Это положительно влияет на рост производительности труда и повышения качества продукции.
Специализация ведет к уменьшению номенклатуры ремонтируемых машин что способствует улучшению производственной структуры предприятий в результате упрощается управление производством. сокращаются общезаводские накладные расходы.
Индустриализация ремонтного производства немыслима без механизации и автоматизации производственного процесса ремонта машин. В современных условиях решающее значение приобретают комплексная механизация и автоматизация так как они охватывают все этапы производственного процесса. Именно в этом случае достигается наибольший эффект в повышении производительности труда и улучшении всех технико-экономических показателей производства.
Развитие механизации и автоматизации на ремонтных заводах происходило главным образом для процессов механической обработки восстановления деталей.
Разборочно-сборочные работы при ремонте строительных машин составляющие 55-65% общей трудоемкости ремонта механизированы очень слабо: уровень механизации составляет в среднем 4-5% в то время как в машиностроении при серийном производстве уровень механизации сборочных машин составляет 15-20%. Особенно низка механизация слесарных работ 60-90% которых выполняется вручную.
Недостаточное оснащение разборочных и сборочных работ выполнение этих работ вручную влечет за собой дополнительные повреждения деталей при разборке а при сборке - несоблюдение технических условий и снижение качества ремонта.
Вместе с тем механизация ремонтных работ весьма эффективна. Каждый вложенный рубль дает эффект в 3-4 раза больший чем в машиностроении. Капиталовложения в механизацию слесарных работ окупаются меньше чем за один год [1]. Применение разборочно-сборочных стендов снижает трудозатраты на 15-20% а применение ручных машин - на 35-50%.
Непосредственное влияние на характер механизации и автоматизации технологических процессов оказывают объем производства размер и повторяемость партий (серийность) повторяемость процессов характеристика используемого оборудования и оснастки. Эти условия существенно влияют нв выбор средств механизации и автоматизации.
Применение высокопроизводительного оборудования и специальной ремонтной оснастки обеспечивает снижение трудозатрат повышение производительности труда и уменьшение стоимости ремонта. Однако такая эффективность может иметь место только при значительных объемах ремонта однотипных строительных машин. Поэтому основной внедрения средств механизации включая поточные Линии ремонта машин является концентрация и специализация ремонтного производства.
В настоящее время важнейшим требованием к ремонтному производству СДМ со стороны потребителя является проблема качества ремонта. Это приобретает особую актуальность в связи с тем многие машиностроительные заводы нашей отрасли перешли на выпуск новых более дорогих видов продукции.
Поэтому важно чтобы параметры (в том числе ресурс) отремонтированной машины приближались к параметрам новой. С экономических позиций потребителя вполне удовлетворит соотношение
где СрСн - соответственно стоимости капитально отремонтированной и новой машины;
Rp Rh - ресурсы отремонтированной и новой машины.
С организационно-технической точки зрения проблему качества ремонта СДМ можно решить путем:
-укрепления технологической дисциплины и службы технического контроля;
-создание и внедрения ремонтной документации обеспечивающей высокой качество ремонта;
-повышения материально-технического уровня ремонтных предприятий;
-укрепления технической базы контрольных служб.
Вопросы управления и руководство ремонтным производством напрямую влияют на качества и повышение его эффективности.
Отечественный и зарубежный опыт [1] показывает что управление ремонтным производством должно вестись на вневедомственной основе путем создания сети специализированных РМЗ рассредоточенных по территориальному признаку. Это создает возможности для проведения одной технической политики и повышения уровня технического руководства ремонтным производством. При этом будут сокращаться транспортные расходы по доставке техники на РМЗ. Из зарубежного опыта известно что сокращение транспортных расходов является значительным резервом снижения себестоимости ремонта техники. Так например американская тракторостроительная фирма «Катерпиллер трактор» имеет сеть ремонтных предприятий рассредоточенных таким образом что транспортные расходы не превышают 10% себестоимости ремонта. Это обеспечивает более полный охват техники заводским ремонтом на индустриальной основе.
Анализ состояния ремонтного производства СДМ позволяет сделать следующие выводы.
В настоящее время ремонтное производство по своей эффективности организационному и техническому уровню все еще отстает как от машиностроения (сфера изготовления) так и от строительства (сфера потребления СДМ).
К причинам неудовлетворительного состояния ремонтного производства СДМ можно отнести то что:
- существующие нормативы системы ППР не отражают конкретных условий эксплуатации и пригодны лишь для укрупненного планирования производства но не его стимулирования;
- специфика строительного производства (сосредоточенное рассредоточенное линейное) не позволяет в полной мере использовать преимущества индустриализации ремонта (концентрации и специализации);
- большинство СДМ ремонтируется на ремонтных предприятиях строительных организаций разного уровня для которых характерны низкий уровень специализации и концентрации и как следствие слабая механизация работ высокая трудоемкость и стоимость ремонта недостаточное обеспечение запасными частями со стороны промышленности слабая организация восстановления деталей;
- большинство машиностроительных заводов отрасли перешли на выпуск новых более дорогих видов продукции а к этому еще не готовы как эксплуатационные так и ремонтные предприятия.
Высококачественный ремонт СДМ возможен только на специализированных ремонтно-механических заводах рассредоточенных по территориальному принципу отвечающих требованиям концентрации и специализации ремонтного производства в целесообразных пределах: при этом управление этими предприятиями должно быть вневедомственными.
Наиболее целесообразной формой организации производства на современных РМЗ следует считать агрегатно-узловой метод ремонта который позволяет реализовать обезличенный ремонт. При этом линии сборки и разборки полнокомплектных машин а также участки по восстановлению деталей могут использовать поточную форму организации производства.
Расчет ремонтно-механического завода по укрупненным показателям
Расчет проектируемого РМЗ производится в соответствии со следующей учебно-методической литературой [4567]. При этом режим работы предприятия принимается двухсменный с пятидневной рабочей неделей и двумя выходными днями.
1 Определение производственной программы и трудоемкости работ
Производственной программой ремонтного предприятия принято называть затраты времени в человеко-часах для выполнения определенного вида работ за год.
Производственная программа определяется номенклатурой и количеством единиц ремонтируемой продукции. В соответствии с заданием на проектирование РМЗ ремонтирует разнородную продукцию. Поэтом для удобства расчета определяем значения годовых трудоемкостей по однородным видам продукции которыми для проектируемого предприятия являются:
- трактор на гусеничном ходу Т-130 — 300 шт.;
- бульдозер (навесное оборудование) - 300 шт.;
- рыхлитель (навесное оборудование) - 100 шт.;
- дизельный двигатель Д-160 - 100 шт.;
- ходовые тележки в сборе - 400 шт.
Для укрупненных расчетов используют нормативы трудоемкости на выполнение капитальных ремонтов машин и агрегатов приведенные в рекомендациях [45]
Произведем корректировку технической нормы времени:
Т’I - техническая норма времени на капитальный ремонт
КМ - коэффициент учитывающий снижение нормы с увеличением объема производства если ремонтируется до 100 машин то КМ =1 при большем объеме КМ =085; КВ - коэффициент учитывающий перевыполнение нормы выработки;
Бульдозер-рыхлитель (навесное оборудование):
Дизельный двигатель Д-160:
Ходовые тележки в сборе:
Определим годовую производственную программу РМЗ по каждому виду ремонтируемой продукции по формуле:
где Ni - число ремонтируемых единиц i-oгo вида продукции шт.
Тг1 = 511 · 300=153300 ч-ч;
Бульдозер-рыхлитель:
Тг2 = 42 · 400=16800 ч-ч;
Дизельный двигатель:
Тг3 = 131 · 100=13100 ч-ч;
Тг4 = 276 · 400=11040 ч-ч;
Произведем распределение годовой трудоемкости по каждому виду продукции по отделениям и участкам РМЗ [4]. Результаты расчета сведем и таблицу 2.I
2 Расчет количества работающих на заводе
В состав работающих на предприятии входят основные и вспомогательные производственные рабочие инженерно-технические работники (ИТР) счетно-конторский персонал (СКП) и младший обслуживающий персонал (МОП).
Численность основных производственных рабочих по отделениям выполняющих технологические операции по ремонту рассчитывают по формулам:
где - вочное и списочное число рабочих;
Тнpi Tдpi - номинальный и действительный фонды времени рабочего i-ого отделения ч.
Результаты расчета сводим в таблицу 2.2.
Таблица 2.2 - Сводные данные по определению численности основных производственных рабочих по отделениям
Трудоемкость работ Тoi ч-ч
Число работающих чел
Контроля и сортировки
Сборки машин и узлов
Медницко-радиаторное
Ремонта гидроаппаратуры
Ремонта и сборки ДВС
Топливной аппаратуры
Продолжение таблицы 2.2
Слесарно-механическая
Число вспомогательных рабочих ИТР МОП и СКП определяем исходя из процентного соотношения их к числу производственных рабочих [4]. Для этих категорий работающих подсчитываем только списочный состав.
Таблица 2.3 – Списочный состав других категорий работающих
Категории работающих
Процент от числа основных производственных рабочих
численность работающих чел
Инструментальное отделение
3 Определение площадей помещений ремонтного завода
Площади ремонтных предприятий делятся на производственные вспомогательные и площади для административно-бытовых помещений. К группе производственных площадей откосятся те которые заняты технологическим оборудованием основного и вспомогательного производств рабочими постами транспортным оборудованием а также рабочие зоны проходы и проезды между оборудованием.
Производственные площади цехов и отделений при укрупненном расчете подсчитываются по удельной площади на одного работающего в большей смене.
fP - удельная площадь на одного производственного рабочего м2;
- списочное количество работающих в отделении в большей (первой) смене.
Результаты расчета сводим в таблицу 2.4.
Таблица 2.4 – Результаты расчета площадей отделений завода
Количество работающих в большей смене
Площадь отделения м2
Обезжиривания и мойки
Сварочно-наплавочное
Суммарная площадь складских помещений при укрупненном расчете принимается равной 25% производственной площади.
Результаты расчета складских помещений сводим в таблицу 2.5.
Таблица 2.5 – Распределение площади складских помещений
Процент от общей площади складов
Деталей ожидающих ремонта
Агрегатов ожидающих ремонта
Отремонтированных агрегатов
С учетом складских помещений площадь производственного корпуса составит:
В административно-бытовые помещения включаются площади для управленческого персонала тех кабинет столовая гардеробы душевые умывальные туалеты. Все эти плошали кроме туалетов и умывальных должны располагаться в отдельном здании бытового корпуса.
При укрупненных расчетах плошали административно-бытовых помещений принимаем равным 17 % от суммарной производственной плошали [4] т.е.
Fc =1543 0.17 = 262 м2
Подсчитанную площадь производственною корпуса со складскими помещениями увеличиваем на 25 % для межцеховых проходов и проезда внутризаводского транспорта.
Тогда общая расчетная площадь производственного корпуса РМЗ составит
Fp = 1543 1.25 = 1930 м2
4 Компоновка производственного корпуса
Компоновка помещений ремонтного предприятия - это план рационального размещения производственных участков (отделений) складских и других помещении обеспечивающих технологическую связь между производственными участками наиболее короткие грузопотоки и соблюдение норм строительного противопожарного и санитарно-технического проектирования [67].
Здания ремонтных предприятий выполняются одноэтажными каркасного типа из сборного железобетона. Они состоят из нескольких однотипных параллельных пролетов одинаковой высоты образуемых рядами колонн.
Габаритные размеры производственного корпуса РМЗ выбирают исходя из его площади длины поточных линий унифицированных схем зданий (сетки колонн) высоты здания схемы технологического процесса а также применяемого технологического оборудования.
Сетка колонн здания характеризуется шириной пролета (расстояние между осями колонн в поперечном направлении) и шагом колонн (расстояние между осями колонн в продольном направлении) [46].
Для проектируемого РМЗ принимаем двух пролетное одноэтажное ода не каркасного типа с сеткой колонн: 18х12 и отсюда следует что ширина зданиия составляет 36м.
Длину панна определяем из выражения:
где FP - расчетная площадь ремонтного предприятия м2;
B3 - принятая ширина здания м2.
Полученное значение длины здания принимаем кратной 6 м (длины стеновой панели) те. Lз = 60 м.
Отсюда площадь проектируемого производственного корпуса РМЗ составит:
F3 = 36 60 = 2160 м2
Высоту пролетов производственного корпуса определим исходя из размеров ремонтируемого изделия (трактор Т-130) принятого вида грузоподъемного оборудования (мостовой кран грузоподъемностью 20 т.) и санитарно-гигиенических требований (на каждого работающего должно приходиться не менее 15 м объема и не менее 45 м площади помещений) [4].
На рисунке 2.1 представлена схема к определению высоты пролета здания производственного корпуса с мостовыми кранами. В соответствии с которой высота от пола до низа несущей конструкции определится по формуле:
где Н1 - расстояние от пола до головки подкранового рельса м;
h -расстояние от головки рельса до низа перекрытия м.
Н1 = K + Z + e + f + c (2.8)
где К - высота ремонтируемого изделия K=Зм;
Z - расстояние между транспортируемым изделием поднятым в крайнее верхнее положение и верхней точкой машины Z=1m;
е — высота наибольшего по размеру агрегата (кабина) ремонтируемого изделия в транспортном положении e=17 м;
f - расстояние от верхней кромки изделия до центра крюка в верхнем его положении f=15 м;
с - расстояние от предельного верхнего положения крюка до горизонтали проходящей через вершину подкранового рельса с=06 м [4].
Н1 = 3 + 1 + 1.7 + 1.5 + 0.6 = 78 м
Высота h зависит от габаритных размеров мостового крана:
да = 01 для крана грузоподъемностью 20 т [4].
Рисунок 2.1 – Схема к определению высоты пролета здания производственного корпуса с мостовыми кранами
По действующим нормативно-техническим документам [8] принимаем Н=10.8 м при этом Н1 = 815м.
С архитектурно-строительной точки зрения компоновочный план проектируемого РМЗ (рисунок 2.2) представляет собой двух пролетное одноэтажное здание из сборного железобетона. Пролет здания имеет сетку колонн 18х12. При этом с целью укрепления жесткости каркаса по периметру здания колонны размещены с шагом кратным 6 м. Привязка колонн каркаса и стен к разбивочным осям здания выполнена в соответствии с нормами строительного проектирования [8] которые предусматривают:
- совпадение осей сечения подкрановой части средних колонн с продольными и поперечными осями здания;
- нулевую привязку крайних рядов колонн и стен к продольным разбивочным осям здания;
- совпадение осей крайних торцевых колонн с привязочными осями здания с условием смещения их на 500 мм относительно внутренней поверхности торцовых стен.
Конфигурация здания производственного корпуса проектируемого РМЗ представляется рациональной (прямоугольник) что обеспечивает удешевление стоимости строительства за счет уменьшения путей перемещения грузоподъемных средств (башенных кранов) транспортировки строительных материалов и грузов [8].
В основу компоновочного плана проектируемого РМЗ положена прямоточная схема технологического процесса ремонта при которой разборочно-сборочные участки расположены в среднем пролете здания производственного корпуса (рисунок 2.2). При этом базовый узел машины рама трактора перемещается прямолинейно и передается на общую сборку без затруднений при помощи мостового крана грузоподъемностью 20 т. Участки (отделения) ремонта агрегатов восстановления и изготовления деталей располагаются по обе стороны разборочно-сборочной линии в двух пролетах которые отделены магистральным проездам.
Согласно противопожарным в санитарно-гигиеническим требованиям огнеопасные и вредные (по условиям работы) участки; кузнечный сварочно-наплавочный термический гальванический медницко-радиаторный металлизационный. полимерных покрытий ремонта рам и испытательный ДВС расположены отдельными группами у наружных стен производственного корпуса в крайних пролетах и отделены от них капитальными стенами.
С целью уменьшения количества пересекающихся и встречных грузопотоков инструментальный участок со складом расположен рядом со слесарно-механическим и ОГМ комплектовочный со складом - с участком сборки машин и узлов складом запчастей и отремонтированных агрегатов.
Таким образом разработанный компоновочный план РМЗ в наибольшей степени соответствует совпадению направления главного грузопотока с ходом технологического процесса ремонта машины (трактора Т-130) что в свою очередь обеспечивает кратчайшие пути движения объектов
ремонта материалов и запасных частей а также наличие минимума встречных и пересекающихся грузопотоков. В конечном итоге такая компоновка производственного корпуса позволит снизить стоимость капитального ремонта машины и повысить его эффективность.
Детальный расчет производственного участка
Произведем детальный расчет участка сборки ходовых тележк проектируемого РМЗ.
1 Расчет и выбор оборудования
В качестве основного технологического оборудования данного участка применяются стенды для сборочных работ а также испытательный стенд для обкатки опорных катков трактора Т-130.
Определим число сборочных стендов [11];
XC = TXT NXT (Tбо m) (3.1)
где TXT – техническая норма времени на сборку ходовой тележки трактора Т-130 TXT = 15 ч-ч;
NXT – годовая программа работ на участке сборки ходовых тележек
Tбо – действительный годовой фонд времени работы оборудования
m – число рабочих одновременно работающих на одном рабочем месте m = 1.
XC = 15 1000 (4015 1) =37
Принимаем числом сборочных стендов XC = 4 шт.
Определим число испытательных стендов для обкатки опорных катков
XU = (t1 + t2) NXT nok (Tдо nu nв) (3.2)
где t1 – продолжительность испытания агрегата t1 = 05 ч;
t2 – время установки и снятия агрегата со стенда t2 = 03 ч;
nok – число опорных катков в комплекте ходовой тележки на тракторе Т-130 nok = 5;
nu – число опорных катков одновременно испытываемых на стенде
nв – коэффициент использования оборудования по времени nв = 092.
XU = (05 + 03) 1000 5 (3975 5 092) = 02
Принимаем число испытательных стендов XU = 1.
В качестве вспомогательного оборудования для выполнения прочих слесарно-механических работ (например притирки колеи резинометаллических уплотнений катков и натяжного колеса) на участке используем вертикально-сверлильный станок.
Определим число рабочих постов па участке
Xpn = Txm Nxm (Tpn y m) (3.3)
где Tpn - годовой фонд времени рабочего поста ч;
у - сменность работы участка у=2.
Tpn = [365 – 104 + 9] tсм (3.4)
где tсм - продолжительность смены при пятидневной рабочей неделе
Tpn = [365 – 104 + 9] 82 = 2066 ч.
Xpn = 15 1000 (2066 2 1) = 36
На участке сборки ходовых тележек проектируемого РМЗ принимаем четыре рабочих поста что соответствует количеству сборочных стендов.
При этом по мере необходимости работы на испытательном стенде и вертикально-сверлильном станке могут выполняться персоналом (слесарями-сборщиками) наименее загруженных постов участка (например постов сборки натяжных колес или поддерживающих катков).
С учетом специфики сборочных работ а также результатов расчета в таблице 3.1 приведен перечень основного и вспомогательного оборудования используемого на участке сборки ходовых тележек трактора Т-130.
Произведем уточненный расчет площади участка [11]
Fy = (Fo + Fпл) Ко (35)
где Fo – суммарная площадь занимаемая оборудованием Fo = 169м2;
Fпл – суммарная площадь занимаемая площадками различного назначения Fпл = 75 м2;
Ко – коэффициент плотности расстановки оборудования Ко = 45 [11].
Fy = (169 + 75) 45 = 110 м2
Таблица 3.1 – Основное и вспомогательное оборудование участка
Наименование оборудования
Стенд для сборки ходовых тележек
Стенд для сборки натяжных колес
Продолжение таблицы 3.1
Стенд для сборки опорных катков
Стенд для сборки поддерживающих катков
Стенд для обкатки опорных катков
Вертикально сверлильный станок 2Н118
Консольный кран Q=05Т
2 Технологическая планировка производственного участка
Технологическая планировка производственного участка выполняется с учетом следующих требований [6 7 9 10 11]:
- план расстановки оборудования на участке выполняется на основе плана производственного корпуса проектируемого РМЗ;
- основным принципом планировки является прямоточность движения агрегатов или деталей при ремонте и установление минимальных расстояний между оборудованием и элементами зданий согласно нормам технологического проектирования;
- особенностью расстановки оборудования на сборочных участках является выделение постов под сборку агрегатов направление которых должно быть перпендикулярным к линии их общей сборки;
- при расстановке оборудования в пределах под сбором пых постов целесообразно выдерживать следующую планировочную схему: стеллажи для накопления деталей стенды для сборки верстаки оборудование для испытания узлов площадки с контейнерами для накопления собранных узлов;
- на все виды оборудования участка наносится сквозная цифровая нумерация сверху вниз и слева направо при этом подъемно-транспортное оборудование нумеруется после технологического;
- после расстановки оборудования показывают рабочие Посты и места подвода инженерных коммуникаций (сжатого воздуха воды пара электроэнергии и т. д.).
В соответствии с вышеизложенным на рисунке 3.1 представлена схема технологической планировки участка сборки ходовых тележек трактора Т-130 для проектируемого РМЗ.
-стенд для сборки ходовых тележек; 2 - стенд для сборки натяжных колес; 3 - стенд для сборки поддерживающих колес; 4 - стенд для сборки опорных катков; 5 - вертикально-сверлильных станков; б - стенд для обкатки опорных катков; 7 - консольный кран; 8 9 - площадки для межоперационного складирования узлов; 10 - площадка для складирования рам ходовых тележек Рисунок 3.1 - Технологическая планировка участка сборки ходовых тележек
Характерной особенностью планировочного решения является транспортная схема которая предусматривает поступление деталей и комплектующих изделий к сборочным постам при помощи внутризаводского транспорта (электрокаров электропогрузчиков) и разгрузки их мостовым краном (Q = 20 т) работающим в данном пролете производственного корпуса.
Транспортировка собранных узлов на площадки межоперационного складирования и далее на стенд сборки ходовых тележек осуществляется консольным поворотным краном грузоподъемностью Q = 05 т. Собранная ходовая тележка при помощи мостового крана транспортируется в малярное отделение и склад оборотного фонда РМЗ.
3 Расчет естественного и искусственного освещения участка
Расчет сводится к определению суммарной площади световых проемов комбинированного типа освещения т. к. участок сборки ходовых тележек находится в центральном пролете здания производственного корпуса РМЗ (рисунок 2.2) [11]
Sб = Fy lmin nok (100 c r1 K1) (3.6)
где Fy - площадь пола производственного участка Fy = 110 м2;
nok - световая характеристика окна nok = 26;
c - общий коэффициент светоиспускания c = 05;
r1 - коэффициент учитывающий влияние отраженного света при боковом освещении r1 = 145;
K1 - коэффициент учитывающий затенение окон противостоящими зданиями K1 = 1.
Sб = 110 15 26 (100 05 24 1) = 36м2
Расчет искусственного освещения сводится к определению необходимого светового потока освещения участка и потребной мощности ламп.
Определим необходимый световой поток:
Fc = Fy E Kзан nc(3.7)
где Е - норма искусственной освещенности Е =200 лк;
Кзан - коэффициент запаса освещенности Кзан = 13;
nc - коэффициент использования потока nc =045.
Fc = 110 200 13 045 = 63556 лм
Определим количество ламп:
где Fл - световой поток одной лампы для ламп мощностью 300 Вт
Zл = 63556 4100 = 16 шт
4 Расчет вентиляции участка
Расчет вентиляции участка сборки ходовых тележек сводится к определению площади фрамуг (форточек) т. к. кратность воздухообмена не более трех [11].
5 Расчет теплоснабжения
Расчет теплоснабжения сводится к определению годового расхода тепла на отопление вентиляцию горячее водоснабжение и технологические нужды для всего ремонтного предприятия т. к. многие участки не изолированы капитальными стенами.
Определим годовой расход тепла на отопление:
Qo = qo V3 Kl noc 24 (3.10)
где V3 - объем здания РМЗ V3 = 23328 м3;
qo - удельный часовой расход тепла на отопление qo = 80 (кДж*ч)м3;
noc - продолжительность отопительного сезона noc = 205 дн.
Kl = (16 – tн)41 (3.11)
где tн - расчетная наружность температура самой холодной недели tн=-25°С.
Kl = (16 + 25)41 = 1
Qo = 80 23328 1 205 24 10-3 = 9181901 мДж
Определим годовой расход тепла на вентиляцию:
Qb = qb V3 Kt y tсм noc (3.12)
где qb – удельный часовой расход тепла на вентиляцию qb = 270кДжчм3;
у – сменность работы РМЗ у = 2;
tсм – продолжительность смены tсм =82ч.
Qb = 270 23328 1 2 82 205 10-3 = 21175759мДж
Определим расход тепла на технологические нужды:
QТН = qT V3 TDO (3.13)
где qT – удельный часовой расход тепла на технологические нужды
QТН = 150 23328 4015 10-3 = 14049288мДж
Определим годовой расход тепла на горячее водоснабжение:
Qгв = qгв V3 y a b (3.14)
где qгв – удельный часовой расход тепла на горячее водоснабжение
а – продолжительность работы душей в смене а = 1ч;
b – число рабочих дней в году b = 252дн.
Qгв = 210 23328 2 1 252 10-3 = 246903мДж
6 Расчет потребного количества электроэнергии
Определим потребное годовое количество электроэнергии на участке сборки ходовых тележек:
Wг =Рэ Кв Тэ + Роэ Тоэ (3.15)
где Рэ - номинальная мощность электроприемников на участке Рэ = 25.3кВт (таблица 3.1);
Тэ - годовое использование электрических силовых нагрузок
Кв - коэффициент использования электрических силовых нагрузок по мощности Кв = 017;
Роэ - суммарная установленная мощность осветительных электроприемников кВт;
Тоэ - годовое использование освещения Тоэ = 2250 ч.
Роэ = Nл Zл 10-3 (3.16)
где Nл – мощность лампы освещения Nл = 300Вт.
Роэ = 300 16 10-3 = 48кВт
Wг =253 017 3200 + 48 2250 = 24563
7 Распет потребного количества воды
Определим годовой расход потребного количества воды на двойственные и водохозяйственные нужды РМЗ укрупненным методом [11]:
Qвп = qвп Тг Та (3.17)
Qвх = qвх Тг Та (3.18)
где qвп qвх – соответственно удельные расходы воды на производственные и водохозяйственные нужды при капитальном ремонте трактора «т-130»
qвп = 97м3 qвх = 7м3;
Тг - годовой объем работ на РМЗ Тг = 194240 ч-ч;
Та – трудоемкость ремонта трактора Т-130 Та = 500 ч-ч.
Qвп = 97 194240 500 = 3768м3
Qвх = 7 194240 500 = 2719м3
Стенд для сборки натяжных колес трактора Т-130
1 Описание конструкции
Стенд для сборки натяжных колес состоит из гидравлического горизонтального пресса 1 кантователя 2 скатов-накопителей 3 4 и гидростанции 5 (рисунки 4.14.2).
Скаты-накопители 3 4 выполнены в виде наклонных лотков с направляющими которые снабжены стопорными устройствами. Каждый скат-накопитель вмещает два натяжных колеса.
Гидростанция 5 размещена вблизи стенда на отдельной раме (рисунки 4.1 4.2). Она состоит из гидронасоса электродвигателя гидрораспределителя фильтра и бака ДЛЯ гидравлической жидкости. Все элементы гидростанции между собой соединены рукавами высокого давления.
Ниже приведена техническая характеристика стенда для сборки натяжных колес трактора Т-130.
Техническая характеристика
Усилие гидроцилиндра пресса кН 200
Номинальное давление в гидросистеме МПа 16
Количество обслуживающего персонала чел 1
Работа на стенде производится в следующей последовательности. Комплекты деталей для сборки натяжного колеса доставляются в контейнерах их комплектовочного отделения РМЗ электрокарами на рабочий пост сборки натяжных колес (рисунок 3.1) Слесарь-сборщик заполняет ими стеллаж при этом натяжное колесо с помощью мостового крана перегружается в скат-накопитель 3 (рисунок 4.1 4.2) и катится до упора в выступающую часть фиксирующего устройства. В скат-накопитель 3 устанавливается два натяжных колеса. После этого отводится упор фиксатора ската-накопителя 3 и колесо перекатывается вручную на призматические опоры гидравлического пресса.
Обеспечение соосности осей натяжного колеса и гидроцилиндра 2 пресса достигается включением гидроцилиндра подъема. Для этого производится включение гидроцилиндра оправка которого должна войти в отверстие ступицы колеса. Затем производится отвод оправки осей ступицы колеса и установка в ее отверстие наружного кольца подшипника с его запрессовкой. После этого колесо перекатывается на кантователь где фиксируется стопором кантуется на 180 путем нажатия на педаль фиксатора и возвращается на призматические опоры гидравлического пресса. В этой позиции слесарь-сборщик устанавливает в ступицу колеса дистанционную втулку и запрессовывает второе наружное кольцо подшипника.
В дальнейшем натяжное колесо перекатывается обратно на кантователь где производится его последующая сборка в соответствии с технологической схемой сборки. При этом запрессовка обойм подшипников на ось а также штифтов и стопоров в опоры и производится на вертикальном гидравлическом прессе поста сборки поддерживающих катков (рисунок 3.1).
Собранное натяжное колесо вкатывают в скат-накопитель 4 (рисунок 4.14.2) до упора в выступающую часть фиксирующего устройства.
Рабочий пост сборки натяжных колес трактора Т-130 кроме специальной оснастки (оправок и т.д.) оснащается пневматическим гайковертом ИП-3106 [14].
Применение стенда для сборки натяжных колес обеспечивает повышение производительности труда сокращает оперативное и вспомогательное время на сборку облегчает физический труд слесаря-сборщика улучшает условия его работы и повышает производственную культуру при капительном ремонте СДМ.
2 Расчет гидропривода пресса
Гидростанция линии сборки натяжных колес трактора Т-130 состоит из гидроцилиндра горизонтального пресса и гидроцилиндра подъема насоса распределителя фильтра и бака которые соединены между собой рукавами высокого давления. Гидросистема стенда выполнена по открытой схеме номинальное давление рн = 16 МПа. Усилие развиваемое гидроцилиндром пресса Р = 200кН скорость движения его штока Уц =0025 мс.
Определим диаметр поршня гидроцилиндра пресса [15]
где Δpц -эффективный перепад давления на гидроцилиндре МПа;
- гидромеханический КПД гидроцилиндра = 09;
Для открытой схемы эффективный перепад давления определим согласно выражению
где г - гидравлический КПД гидросистемы г =08 [ 15];
Δрц = 16 08 =128 МПа
Принимаем диаметр поршня гидроцилиндра пресса D = 016 м диаметр штока d = 008 м.
Определим расход рабочей жидкости из условия заданной скорости гидроцилиндра
где оц – объемный КПД гидроцилиндра оц = 1 [15].
Определим рабочий объем гидронасоса (примем Qн = Qц)
где nн – частота вращения вала насоса nн = 3000 обмин;
он – объемный КПД гидронасоса он = 093.
qн = = 0011 10-3 м3об
Принимаем насос НШ-14-3 [15] qн = 001375 10-3 м3об.
Определим мощность электродвигателя привода насоса
где н – общий КПД гидронасоса н = 085;
э – КПД электродвигателя э = 085.
Принимаем трехфазный асинхронный электродвигатель с короткозамкнутым ротором марки 4А132М2У3: N=11 кВт n=3000 обмин.
Скорости рабочей жидкости для напорного трубопровода рекомендуется выбирать в зависимости от номинального давления в гидросистеме. При давлении рн = 16 МПа выбираем скорость Уж = 5 мс.
Из условия неразрывности потока жидкости определим диаметр трубопровода:
Принимаем диаметр напорного трубопровода из стандартного ряда в соответствии с ГОСТ 165-80 dтп = 0014 м [15].
Рекомендуемая скорость рабочей жидкости для сливного трубопровода: Vж = 20 мс.
Принимаем диаметр сливного трубопровода из стандартного ряда в соответствии с ГОСТ 16516-80 dтс = 0018 м [15].
Рекомендуемая скорость рабочей жидкости для всасывающего трубопровода: Vж = 10 мс.
Принимаем диаметр всасывающего трубопровода из стандартного ряда в соответствии с ГОСТ 16516-80 dтв = 0025 м [15].
В качестве гидрораспределителя принимаем моноблочный гидрораспределитель типа Р80-2: do = 16 м; pн =16 МПа; Qн = 80 10-3 м3мин [15].
На сливном трубопроводе применяем фильтр типа 1.1.25-25: dо = 0025 м; Qн = 63 10-3 м3мин [15].
Определим объём гидробака согласно зависимости
Qб = 2 003 103 = 60л
Из стандартного ряда по ГОСТ 12448-80 принимаем Qб = 60 л [15].
В качестве рабочей жидкости в гидросистеме стенда используем
масло марок МГ-30 или ИС-20 [15].
Технология восстановления натяжного колеса
Источником пополнения фонда запасных частей является рациональное восстановление изношенных деталей. Замена изношенных деталей заранее восстановленными снижает расход металла на изготовление запасных частей частично высвобождает производственные мощности машиностроения снижает стоимость ремонта машин так как восстановление деталей как правило дешевле их изготовления. Так стоимость восстановленных деталей в зависимости от организации производства составляет в среднем от 30 до 50% стоимости новых [1617].
Опыт ремонта СДМ показывает что из современных способов восстановления позволяющих отремонтировать практически любую деталь наиболее широкое распространение получила наплавка этот способ экономичен относительно прост организационно дает возможность изменять химический состав наплавляемого металла не требует применения дорогостоящего оборудования. Как показывает практика каждая тонна наплавленного металла обеспечивает восстановление рабочих свойств 35 тонн деталей СДМ [16]. Этот способ даст возможность сравнительно быстро получить слой наплавленного металла значительной толщины что особенно важно при восстановлении сильно изношенных деталей» Поэтому в настоящее время наплавку применяют для восстановления самых ответственных деталей.
1 Дефекты натяжного колеса
Натяжное колесо трактора Т-130 изготовлено литым из стали 45Л-1 и подвержено термообработке. В соответствии с техническими условиями твердость его поверхностного слоя должна быть HRС≥45[13]. Колесо бракуется при толщине стенки беговой дорожки 9 мм. Основные дефекты и допустимые без ремонта размеры натяжного колеса трактора Т-130 представлены в таблице 5.1.
Из опыта работы ремонтных предприятий известно что наиболее часто встречающимися дефектами натяжного колеса трактора Т-130 являются: износ беговых дорожек и торцовых поверхностей направляющих реборд (буртов) колеса. Поэтому в данном курсовой работе разрабатывается технологический процесс восстановления натяжного колеса трактора Т-130 по маршрутной технологии с сочетанием вышеуказанных дефектов а именно: 2 3 позиции на ремонтном чертеже (рисунок 5.1) и в карте контроля-сортировки (таблица 5.1).
2 Выбор типа производства
Технологический процесс восстановления натяжного колеса состоит из двух операций: наплавочной под слоем флюса и токарно-винторезной. С учетом годовой программы ремонта проектируемого РМЗ задаемся годовым объемом восстанавливаемых деталей (натяжных колес трактора Т-130) N=500 штгод.
Таблица 5.1 – Карта контроля – сортировки на натяжное колесо трактора Т-130
Способ установления дефекта и измерительный инструмент
Способ восстановления детали
Допустимые без ремонта в сопряжении с деталями: работавшей новой
Износ поверхности отверстия по подшипник
Наплавить и обработать. Железнить и обработать
Износ беговых дорожек
Наплавить и обработать. При толщине стенки менее 9мм колесо подлежит замене
Наплавить и обработать
Трещины в любом месте
Визуальный контроль. Остукивание молотком. Лупа ЛШ-7х
Трещину разделать фаской 4х450 и заварить
Износ перемычек по высоте
При глубине износа более 10 мм наплавить
Определение штучного времени на выполнение основных операций технологического процесса проводим по приближенным формулам [161718].
Для наплавочной операции которая включает в себя наплавку беговых дорожек и буртов натяжного колеса штучное время определим как
где D - диаметр наплавляемой детали мм;
b - длина наплавляемой детали мм;
Vн - скорость наплавки Vн =34 мч [1617];
S - шаг наплавки S = 5 ммоб;
- КПД наплавки = 09;
Кв - коэффициент перехода от основного времени к штучному Кв =2.
Подставив значение параметров получим
Для токарно-винторезной операции которая включает в себя точение беговых дорожек и буртов натяжного колеса штучное время определим по формуле [18]
Тшт2 = (0037 () + 2 017 dд b) 10-3 (5.2)
где Dб - диаметр бурта колеса Dб = 796 мм;
dб - диаметр обрабатываемой поверхности беговой дорожки dб = 750 мм;
Тшт2 = (0037 (7962 - 7502) + 2 017 750 110) 10-3 = 166 мин
Определим количество станков необходимых для выполнения каждой технологической операции [18]
где Fн - номинальный годовой фонд времени работы оборудования при двусменной работе Fн = 4140 ч;
- коэффициент учитывающий простои оборудования в ремонте
зн - нормативный коэффициент загрузки оборудования зн = 08;
Для операций данного технологического процесса будем иметь:
Округлив mрi до ближайшего целого значения получим количество рабочих мест для выполнения каждой технологической опереции.
Определим фактические коэффициенты загрузки оборудования
эф1 = 035; эф2 = 004.
Определим количество операций закрепленных за каждым рабочим местом
Принимаем: О1 = 2; О2 =2 0.
Определим коэффициент закрепления операций [18]
Полученный коэффициент закрепления операций больше 10 следовательно тип производства - среднесерийное.
В условиях среднесерийного производстве изделия (детали агрегаты машины) выпускаются отдельными партиями - сериями состоящими из одноименных однообразных но конструкции и размерам изделий. При этом технологические операции выполняются на основной части рабочих мест (станках сборочных и других местах) последовательно над отдельными партиями изделий.
Характерными особенностями такого производства является: наличие в основном универсального оборудования; широкое применение универсально-наладочных приспособлений; относительно высокая квалификация рабочих; некоторая периодичность в работе по причине переналадки станков; расположение станков по групповому признаку (группы токарных фрезерных и других станков); наличие межоперационного складирования заготовок.
Определим количество деталей в партии для одновременного запуска в производство [18]
nд = 476 08 m Tшк.ср (5.7)
где m – сменность работы предприятия m = 2;
Tшк.ср - средняя величина штучно-калькуляционного времени для операций технологического процесса мин;
Tшк.ср = (Tшк1 + Tшк2) φ 2 (5.8)
где φ – коэффициент перехода от штучного к штучно-калькуляционному времени для среднесерийного производства φ = 16 [17]
Tшк.ср = (139 + 166) 16 2 = 1245
nд = 476 08 2 1245 = 6 шт
Определим периодичность запуска партии деталей
а = 254 6 500 = 3 дня
3 Маршрут восстановления натяжного колеса
Восстановление натяжного колесе трактора Т-130 производится в следующей технологической последовательности [131б17]:
Мойка натяжного колеса и зачистка его опорной поверхности предназначенной для наплавки стальной щеткой до металлического блеска.
Маркировка дефектов колеса наносится краской подлежащих устранению согласно технических условий на дефектовку (таблица 5.1).
Наплавка беговых дорожек колеса до размера 755+6 мм.
Наплавка поверхности буртов колеса до размеров: мм1162 мм
Токарная обработка беговых дорожек и буртов колеса до размеров: 750+6 мм 552 мм мм 1062 мм и 96 мм.
С учетом вышеизложенного в приложении к курсовой работе разработана технологическая документация на восстановление натяжного колеса трактора Т-130
4 Расчет режимов наплавки и норм времени
Наплавку беговых дорожек и буртов натяжного колеса производим проволокой Св 08Г2С диаметром 4 мм с использованием флюса АН-348А.
В качестве оборудования используется наплавочная головка АДС-1000-2 оорудованная шпинделем и сварочным выпрямителем ВС-600. Ток – постоянный обратной полярности [131617] J=600А напряжение U=34В. Деталь устанавливается на оправку закрепленную в шпинделе установки.
Определим скорость подачи электродной проволоки [16]
где αн – коэффициент наплавки αн = 15г(А-ч);
dэ – диаметр электродной проволоки dэ = 4 мм;
γ – плотность материала проволоки γ = 785 103 кгм3.
С учетом кинематических характеристик наплавочной головки АДС-1000-2 принимаем Vn = 90 мч [17].
Определим скорость наплавки
где - толщина слоя наплавки = 5 мм;
S – шаг наплавки S = 5 ммоб.
Определим частоту вращения детали [17]
где D – диаметр наплавляемой детали D = 735мм.
Определяем вылет электродной проволоки
L = (10 + 12) dэ (5.13)
Определим величину смещения электрода с зенита
= (005 + 007) D (5.14)
Наплавку беговых дорожек натяжного колеса производим в два слоя толщиной по 5 мм каждый. При этом первый и последний валики каждого слоя наплавляют при выключенном суппорте станка.
Определим технологическое время наплавки
где – КПД наплавки = 09;
b – длина наплавляемой поверхности b = 55мм.
Технологическое время для первого слоя наплавки
Технологическое время для второго слоя наплавки
То = 375 + 387 = 76 мин
Определим штучно-калькуляционное время
где Кц - коэффициент учитывающий затраты вспомогательного и подготовительно-заключительного времени Кц = 12 [19]
Наплавку торцовой поверхности бурта натяжного колеса производим при тех же режимах в четыре слоя толщиной по 5 мм каждый с выключенным суппортом станка. Для обеспечения этого необходимо
Определим технологческое время наплавки
где i – число слоев i = 4
Определим штучно-уалькуляционное время
Тш-к = 133 12 = 16 мин
5 Расчет режимов резания и норм времени
Произведем расчет режимов резания и норм времени для технологического перехода связанного с точением беговых дорожек натяжного колеса до размера 750+6 на длину 55 мм. Оборудование и оснастка: токарно-винторезный станок 1А64 резец — проходной упорный с твердосплавной пластиной Т15К6 деталь закреплена в трехкулачковом патроне.
Определим скорость резания
где Сv – коэффициент характеризующий условия обработки Сv = 340;
kv – поправочный коэффициент;
Т – стойкость резца Т = 60 мин;
t – глубина резания t = 25 мм;
S – подача инструмента S = 08 обмин;
kv = kv1 kv2 kv3 kv4 (5.19)
где kv1 - коэффициент учитывающий механические свойства обрабатываемого материала kv1 = 1;
kv2 - коэффициент учитывающий материал режущей части резца
kv3 - коэффициент учитывающий геометрию режущей части резца
kv4 - коэффициент характеризующий состояние обрабатываемой поверхности kv4 = 085.
kv = 1 1 08 085 = 07
Определим частоту вращения шпинделя станка
где d - диаметр обрабатываемой детали мм;
Для токарно-винторезного станка 1А64 принимаем nст=40 обмин [18].
Определим фактическую скорость резания
Определим тангенциальную составляющую силы резания
Pz = 10 Cp txp Syp Vn kp (5.21)
kp = kp1 kp2 kp3 kp4 (5.22)
Pz = 10 300 25 0807 942-015 09 = 2920Н
Определим мощность станка
N = Pz Vд 1020 60 (5.23)
где – КПД станка = 085.
N = 2920 942 1020 60 085 = 53 кВт
Мощность станка модели 1А64 равна 22 кВт [18].
Определим штучное время [19]
Тшт = То + Тв + Тдоп (5.24)
где То – основное время мин;
Тв – вспомогательное время мин;
Тдоп – дополнительное время мин.
где L - расчетная длина обрабатываемой поверхности мм;
L = l + l1 + l2 (5.26)
l1 l2 - соответственно величина врезания и перебега (l1 + l2) = 4 мм [19].
То = 591 4008 = 18 мин
Тв = Тв1 + Тв2 (5.27)
где Тв1 - вспомогательное время связанное с переходом Тв1=12 мин;
Тв2 - вспомогательное время зависящее от способа установки заготовки Тв1 = 22 мин.
Тв= 12 + 22 = 34 мин
Тдоп = 008-(То + Тв) (5.28)
Тдоп = 008(18 + 34) = 04 мин
Тшт = 18 + 34 + 04 = 56 мин
Тш-к = Тшт + Тnз n (5.29)
где Тnз – подготовительно-заключительное время Тnз = 10 мин [19];
n – количество деталей в партии n = 6.
Тш-к = 56 + 10 6 = 73
Опытно-конструкторские разработки проведенные в курсовой работе позволяют сделать следующие выводы:
В настоящее время ремонтное производство по своей эффективности организационному и техническому уровню все еще отстает от машиностроения (сфера изготовления) так и от строительства (сфера применения СДМ).
Высококачественный капитальный ремонт СДМ возможен только на
специализированных ремонтно-механических заводах обезличенным методом.
З В курсовой работе разработан специализированный ремонтно-механичесикий завод для капитального ремонта тракторов Т-130 и ИХ агрегатов. При этом структура завода соответствует агретатно-узловому методу ремонта в сочетании с поточной формой организации производства (линии сборки и разборки полнокомплектных машин)
Произведена детальная разработка специализированного участка по сборке ходовых тележек трактора Т-130. При этом все сборочные операции выполняются на специализированных рабочих постах с использованием высокопроизводительного оборудования.
Спроектирована и разработана конструкция стенда для сборки натяжного колеса.
Разработан маршрутный технологический процесс сборки натяжного колеса с использованием специализированного оборудования.
Список использованных источников
Ровках С.Е. Повышение эффективности ремонта машин в строительстве. – М.: Стройиздат 1976. – 204с.
Корчанов И.Я. Технология и оптимизация ремонта строительных машин т оборудования. –М.: Стройиздат 1990. – 351с.
Новиков И.В. Акильев С.А. Справочник по ремонту дорожных машин. – М.: Транспорт 1971. – 240с.
Расчет ремонтно-механического завода по укрупненным показателям : Метод. указания Сост. Е.В. Курилов. – Ярославль: ЯПИ 1990. – 34с.
Рекомендации по организации технического обслуживания и ремонта строительных машин. – М.: Стройиздат 1978. -92 с.
Курсовое и дипломное проектирование по эксплуатации и ремонту мелиоративных и строительных машинВ.М. Саньков Е.С. Кержиманов В.А. Слободкин. – М.: Агропромиздат 1989.-199с.
Зеленков Г.И. Дехтеринский Л.В. Крившин А.П. Технология ремонта дорожных машин и основы проектирования ремонтных предприятий. – М.: Высшая школа 1971. – 218с.
Шерешевский А.И. Конструирование промышленных зданий и сооружений. – М.: Транспорт 1984. – 192с.
Дехтеринский Л.В. др. Проектирование авторемонтных предприятий. – М.: Транспорт 1981. – 218с.
Курсовое и дипломное проектирование по ремонту машин А.П. Смелов и др. – М.: Колос 1984. – 192с.
спецификация.doc
Стенд для сборки натяжного колеса
РЕФЕРАТ, содержание.docx
КАПИТАЛЬНЫЙ РЕМОНТ МАШИН ТЕХНОЛОГИЯ. ИЗГОТОВЛЕНИЕ ВОССТАНОВЛЕНИЕ ОБЕЗЛИЧЕННЫЙ РЕМОНТ ЗАВОД КАРТА СБОРКИ РАБОЧИЙ ПОСТ ОБОРУДОВАНИЕ ДЕТАЛЬ АГРЕГАТ
Объектом исследования является проект специализированного ремонтно-механического завода для капитального ремонта полнокомплектных СДМ.
Цель работы - разработка проекта завода для капитального ремонта тракторов Т - 130 и их агрегатов.
В результате исследования разработаны:
- проект специализированного ремонтного предприятия для капитального
ремонта тракторов Т 130 агрегатно - узловым методом;
- технологическая планировка участка по сборке ходовых тележек трактора;
- технологический процесс сборки натяжного колеса трактора;
- специализированный стенд для сборки натяжного колеса трактора;
- технологический процесс восстановления натяжного колеса;
- схема технологического процесса капитального ремонта машин агрегатно-узловым методом.
Анализ состояния ремонтного производства СДМ
1 Система планово - предупредительного ремонта
2 Технико-экономическое значение ремонта машин
3 Причины неудовлетворительного состояния ремонтного производства СДМ1.4 Технико-экономический анализ методов ремонта и организации производства
5 Ремонтные предприятия в строительстве
6 Основные требования к ремонтно-механическим заводам
Расчет ремонтно-механического завода по укрупненным показателям
1 Определение производственной программы я трудоемкости работ
2 Расчет количества работающих на заводе
3 Определение площадей помещении ремонтного завода
4 Компоновка производственного корпуса
Детальный расчет производственного участка
1 Расчет и выбор оборудования
2 Технологическая планировка производственного участка
3 Расчет естественного и искусственного освещения участка
5 Расчет теплоснабжения
6 Расчет погребного количества электроэнергии
7 Расчет потребного количества воды
Стенд для сборки натяжного колеса трактора Т-130..
1 Описание конструкции
2 Расчет гидропривода пресса
Технология восстановления натяжного колеса
1 Дефекты натяжного колоса
2 Выбор типа производств
3 Маршрут восстановления натяжного колеса
4 Расчет режимов наплавки и норм времени
5 Расчет режимов резания и норм времени
Список использованной литературы
титульник.docx
Государственное образовательное учреждение
высшего профессионального образования
Ярославский государственный технический университет
Кафедра «Строительные и дорожные машины»
завода для капитального ремонта
Годовая производственная программа
Расчетно-пояснительная записка к курсовому проекту по дисциплине:
«Производство и ремонт дорожных машин»
Таблица 2.docx
Распределение трудоемкости по видам работ и номенклатура продукции
Годовая трудоемкость
Контроля и сортировки
Сборки машин и узлов
Медницко-радиаторное
Ремонта гидроаппаратуры
Ремонта и сборки ДВС
Топливной аппаратуры
Слесарно-механическая
-наружная мойка 2-разборочное3-выворки и мойки 4-контроля и сортировки5-комплектоновочнос со складом 6-ремонт рам 7-сборка машин и узлов 8-кабино-жестяночное 9-медницко-радиаторное 10-обойное и деревообделочное 11 -малярное 12-электроремонтное 13-ремонта гидроаппаратуры 14-ремонта и сборки ДВС 15-топливной аппаратуры 16-испытательнаяя ДВС 17-слесарно-механическое 18-кузнечное 19-термическое 20-наплавочное 21 –гальваническое 22-металлизации и полимерных покрытий 23-ОГМ 24-инструментальное 25-склад деталей и агрегатов ожидающих ремонта 26-склад отремонтированных деталей 27-склад материалов и запчастей 28-ЦИС
Рисунок 2.2 - Компоновочный план ремонтно-механического завода
– горизонтальный пресс; 2 – кантователь; 34 – скат накопитель; 5 – гидростанция
Рисунок 4.1 – Стенд ля сборки натяжных колес трактора Т-130(вид сбоку)
Рисунок 4.2 – Стенд ля сборки натяжных колес трактора Т-130(вид сбоку)
Рекомендуемые чертежи
- 25.10.2022
- 25.01.2023
- 04.11.2022
Свободное скачивание на сегодня
Другие проекты
- 25.01.2023