Поперечно-строгальный станок СПС-01




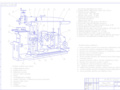
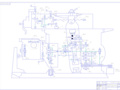
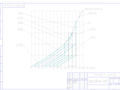
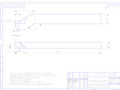
- Добавлен: 25.10.2022
- Размер: 2 MB
- Закачек: 0
Описание
Состав проекта
![]() |
![]() |
![]() ![]() |
![]() ![]() |
![]() ![]() ![]() |
![]() ![]() |
![]() ![]() |
![]() ![]() ![]() |
![]() ![]() ![]() ![]() |
![]() ![]() ![]() ![]() |
![]() ![]() ![]() ![]() |
![]() ![]() |
![]() |
![]() ![]() ![]() |
![]() ![]() ![]() |
![]() ![]() ![]() |
![]() ![]() ![]() |
Дополнительная информация
кинематическая схема.dwg

структурная сетка.dwg

резец строгальный.dwg

общий вид.dwg

график частот двойных ходов.dwg
