Организация технологического процесса восстановления вторичного вала КПП автомобиля КамАЗ-5320




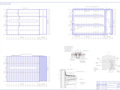
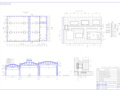
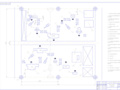
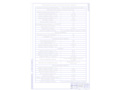
- Добавлен: 25.10.2022
- Размер: 2 MB
- Закачек: 1
Описание
Состав проекта
![]() |
![]() ![]() ![]() |
![]() ![]() ![]() |
![]() ![]() ![]() |
![]() ![]() ![]() |
![]() |
![]() ![]() |
![]() ![]() |
![]() ![]() |
![]() ![]() |
![]() ![]() |
![]() ![]() |
![]() ![]() |
![]() ![]() |
![]() ![]() ![]() |
![]() ![]() ![]() |
![]() ![]() ![]() |
![]() ![]() ![]() |
![]() |
![]() ![]() ![]() ![]() |
![]() ![]() ![]() ![]() |
![]() ![]() ![]() ![]() |
![]() ![]() ![]() ![]() |
![]() ![]() ![]() ![]() |
![]() ![]() ![]() ![]() |
![]() ![]() ![]() ![]() |
![]() ![]() ![]() ![]() |
![]() ![]() ![]() |
![]() ![]() ![]() |
![]() ![]() ![]() |
![]() ![]() ![]() |
Дополнительная информация
7 Экономика.doc
Определение экономической эффективности использования предложенной конструкторской разработки предполагает:
)определение стоимости основных производственных фондов на участке;
)разработку сметы затрат по участку;
)расчет объема дополнительных капитальных вложений;
)определение экономии эксплуатационных затрат участка;
)расчет срока окупаемости капитальных вложений.
1 Расчет стоимости основных фондов
1.1 Расчет стоимости зданий
Стоимость помещения СУЧ руб определяется по формуле
где С1 - стоимость 1 м3 здания руб. С1 = 22000 руб;
VУЧ - объем помещения занимаемого участком м3.
Объем помещения определяется по формуле
где SВН - площадь участка по внутреннему периметру м2;
h - высота здания м;
- коэффициент учитывающий площадь участка по наружному периметру.
Стоимость производственных помещений составит
Стоимость служебных и бытовых помещений (ССЛ) принимаем в размере 10-15% от стоимости производственных зданий:
1.2 Расчет стоимости машин и оборудования
Приобретение нового оборудования проектом не предусматривается. Используется только оборудование уже имеющееся на участке. Стоимость оборудования на момент проектирования сводим в таблицу 7.1.
Таблица 7.1 - Балансовая стоимость машин и оборудования
Наименование оборудования
Стоимость нового оборудования руб.
Балансовая стоимость руб.
Универсальный токарно-винторезный станок 16К20
Пресс гидравлический CP150 для правки валов
Зубофрезерный станок модели ЕЗ – 208
Верстак слесарный металлический 2-тумбовый
Станок вертикально-сверлильный 2Т140
Универсальный токарно-винторезный станок 16К20 модернизированный
2 Расчет стоимости малоценного и быстроизнашивающегося оборудования инструмента инвентаря
Приобретение нового малоценного и быстроизнашивающегося оборудования инструмента инвентаря проектом не предусматривается. Приобретается только оборудование и инструмент необходимый для внедрения предлагаемого проектом технологического процесса.
Расчет балансовой стоимости малоценного быстроизнашивающегося оборудования инструмента инвентаря производится по той же формуле что и балансовая стоимость машин и оборудования. Результаты расчетов сводим в таблицу 7.2.
Таблица 7.2 - Балансовая стоимость малоценного и быстроизнашивающегося оборудования инструмента инвентаря
Установленная мощность кВт
Цена за единицу руб.
Приспособление для упрочняющего накатывания
Фреза червячная ГОСТ 8027-86
3 Труд и заработная плата
3.1 Расчет численности рабочих
Расчет численности рабочих произведен во втором разделе (таблица 2.4).
3.2 Распределение рабочих по разрядам
Таблица 7.3 - Распределение рабочих по разрядам
Оператор станка упрочняющего накатывания
3.3 Расчет численности подсобно-вспомогательных рабочих
Численность подсобно-вспомогательных рабочих принимается от 15 до 35% от численности ремонтных рабочих. Расчет подсобно-вспомогательных рабочих был произведен во втором разделе формула (2.24). Принимается 2 дежурных слесаря 4 разряда.
3.4 Расчет численности руководителей
Расчет численности руководителей ведется исходя из 10-15% на суммарную численность ремонтных и подсобно-вспомогательных рабочих. Расчет руководителей был произведен во втором разделе формула (2.25). Принимается начальник участка и два мастера.
3.5 Расчет численности служащих
Расчет численности служащих ведется исходя из 2-5% на суммарную численность ремонтных и подсобно-вспомогательных рабочих. Расчет служащих был произведен во втором разделе формула (2.27). Принимается один служащий 4 разряда.
4 Расчет фонда заработной платы
4.1 Расчет фонда заработной платы ремонтных рабочих
Фонд заработной платы ремонтных рабочих определяется по формуле
где - основной фонд заработной платы руб.;
- дополнительный фонд заработной платы руб.;
- районный коэффициент к заработной плате = 115.
Основной фонд заработной платы определяется по формуле
где - сумма доплат и выплат стимулирующего и компенсационного характера руб.;
- тарифный фонд заработной платы руб.;
Тарифный фонд заработной платы при повременно-премиальной системе оплаты труда определяется по формуле
где - годовой фонд рабочего времени час;
- среднечасовая тарифная ставка руб.;
- численность производственных рабочих чел.
Среднечасовая тарифная ставка определяется по формуле
где - часовая тарифная ставка меньшего разряда из двух смежных руб.;
- часовая тарифная ставка большего разряда из двух смежных руб.;
- средний разряд рабочих;
- меньший разряд из двух смежных.
Доплаты и выплаты стимулирующего и компенсационного характера могут быть рассчитаны по формуле
где - доплаты за профессиональное мастерство руб.;
- доплаты за отклонение от нормальных условий труда руб.;
- доплаты за руководство бригадой неосвобожденным бригадирам руб.;
- доплаты за часы ночной работы руб.;
- другие принятые доплаты руб.
Доплаты за профессиональное мастерство определяются по формуле
где - процент доплат за профессиональное мастерство;
- часовая тарифная ставка -го разряда час;
- количество рабочих -го разряда чел;
n- число разрядов ед.
Доплаты за отклонения от нормальных условий труда определяются по формуле
где – процент доплат за отклонения от нормальных условий труда. ( - 4-12%).
Доплаты за совмещение профессий
где – процент доплат за совмещение профессий
Общая сумма доплат составит
Сумма премии определяется по формуле
где – процент премии.
Основной фонд заработной платы ремонтных рабочих составит
Дополнительный фонд заработной платы определяется по формуле:
где – процент дополнительной заработной платы %:
где – календарное число дней в году;
– количество выходных дней в году;
– количество праздничных дней в году Дп – 11 дней;
– количество дней отпуска Д ОО – 24 дня;
– количество дней дополнительного отпуска за вредные и тяжелые условия труда;
– количество дней выполнения государственных и общественных обязанностей;
– количество дней дополнительного отпуска за выслугу лет;
Общий фонд заработной платы участка составит:
4.2 Расчет фонда заработной платы подсобно-вспомогательных рабочих
Фонд заработной платы вспомогательных рабочих определяется по формуле
где – годовой фонд рабочего времени вспомогательного рабочего час;
- среднечасовая тарифная ставка вспомогательного рабочего руб.;
– коэффициент учитывающий доплаты и выплаты компенсационного и стимулирующего характера;
– коэффициент учитывающий премии;
– коэффициент учитывающий дополнительный фонд заработной платы.
4.3 Расчет фонда заработной платы руководителей специалистов и служащих
Фонд заработной платы руководителей специалистов и служащих определяется по формуле
где – месячный оклад -ой должности руб.;
– численность работников по -ой должности чел.;
– коэффициент учитывающий премии.
Определим фонд заработной платы начальника:
Определим фонд заработной платы мастера
4.4 Расчет среднемесячной заработной платы по категориям работающих
Среднемесячная заработная плата i-ой категории работающих определяется по формуле
где – общий фонд заработной платы -ой категории работающих руб.;
– численность -ой категории работающих чел.
Среднемесячная заработная плата ремонтных рабочих составит:
Результаты расчетов численности работающих фонда заработной платы и среднемесячной заработной платы сводятся в таблицу 7.4.
Таблица 7.4 – Заработная плата
Наименование категорий работающих
Профессия квалификация
Общий фонд заработной платы руб.
Среднемесячная заработная плата руб.
Производственные рабочие
Подсобно-вспомогательные
5 Расчет сметы затрат участка
5.1 Основная и дополнительная заработная плата производственных рабочих
Расчет произведен в разделе 7.4.1 таблица 7.4
ФЗП общ = 21181101 руб.
5.2 Отчисления на социальные нужды
Отчисления на социальные нужды рассчитываются по формуле
где 265 % – размер отчислений на социальные нужды включающий единый социальный налог (26%) и отчисления на обязательное страхование от несчастных случаев и профзаболеваний для предприятий данного класса профессионального риска ( 05 %).
5.3 Затраты на содержание и эксплуатацию оборудования
5.3.1 Затраты на содержание оборудования и рабочих мест
5.3.1.1 Основная и дополнительная заработная плата вспомогательных рабочих
Основная и дополнительная заработная плата вспомогательных рабочих.
Расчет произведен в табл. 7.4 ФЗП всп = 14544925 руб.
5.3.1.2 Отчисления на социальные нужды вспомогательных рабочих
5.3.1.3 Затраты на вспомогательные материалы
Затраты на вспомогательные материалы определяются по формуле
где – норматив затрат на вспомогательные материалы на единицу – го вида оборудования руб.;
– количество единиц – го вида оборудования ед.
Норматив затрат на вспомогательные материалы () принимается укрупнено в размере 850 руб. в год на единицу сложного оборудования (металлорежущие станки прессы сложные стенды моющие машины и т.п.) и 250 руб. в год на единицу несложного оборудования приборов инвентаря.
5.3.1.4 Затраты на силовую энергию для производственных нужд
Затраты на силовую электроэнергию определяется по формуле
где - общая установленная мощность токоприёмников кВт;
– годовой фонд времени работы оборудования час; ( принимается по данным технологического расчета);
– коэффициент загрузки оборудования по времени ( – 06-075);
– коэффициентn спроса учитывающий неодновременность работы потребителей ;
– тариф 1кВт ч электроэнергии руб.;
– коэффициент учитывающий потери электроэнергии (- 090);
5.3.2 Затраты на текущий ремонт оборудования инструментов инвентаря
Расходы по этой статье Зрем принимаем в размере 5% от балансовой стоимости оборудования
где Н рем – норматив затрат на ремонт оборудования %.
5.3.3 Амортизация оборудования инструмента инвентаря Аоб определяется по формуле
где Наi – норма амортизационных отчислений по i – му виду оборудования инструмента инвентаря %.
Результаты расчета амортизации оборудования сводим в таблицу 7.5.
Таблица 7.5 - Амортизация оборудования
Сумма амортизации руб.
Универсальный токарно-винторезный станок
Пресс гидравлический для правки валов
Зубофрезерный станок модели
Станок вертикально-сверлильный
Универсальный токарно-винторезный станок модернизированный
Результаты расчетов по статье 7.5.3 сводим в таблицу 7.6.
Таблица 7.6 - Расходы на содержание и эксплуатацию оборудования инструмента инвентаря
Затраты на содержание оборудования и рабочих мест
Затраты на текущий ремонт оборудования
Амортизация оборудования
5.4 Общецеховые расходы
5.4.1 Основная и дополнительная заработная плата ИТР
Расчет произведен в разделе 7.4.1 таблица 7.4
ФЗП итр = 531990 руб.
5.4.2 Отчисления на социальные нужды ИТР
5.4.3 Амортизация зданий и сооружений
Амортизация зданий и сооружений А зд принимается в размере 25% от балансовой стоимости зданий и сооружений:
5.4.4 Текущий ремонт зданий и сооружений
Затраты по этой статье принимаются в размере 35% от балансовой стоимости зданий и сооружений:
5.4.5 Содержание зданий и сооружений
Затраты по данной статье принимаем укрупнено в размере 5% от балансовой стоимости зданий и сооружений
5.4.6 Испытания опыты и рационализация
Затраты по этой статье принимаем в размере 1200 руб на 1 рабочего на участке
5.4.7 Затраты на охрану труда и технику безопасности
Расходы по данной статье принимаем в размере 1300 руб на 1 рабочего:
5.4.8 Затраты на спецодежду
Расходы на спецодежду принимаем в размере 1500 рублей на одного рабочего в год:
5.4.9 Прочие общецеховые расходы
Затраты по данной статье принимаем в размере 5% от суммы затрат по статьям 7.5.4.1 - 7.5.4.8.
Результаты расчета общецеховых расходов сводим в таблицу 7.7.
Таблица 7.7 - Общецеховые расходы
Содержание общецехового персонала
Отчисления на социальные нужды
Амортизация зданий и сооружений
Ремонт зданий и сооружений
Содержание зданий и сооружений
Охрана труда и техника безопасности
Затраты на спецодежду
На основании произведенных выше расчетов составляем смету затрат участка в таблице 7.8.
Таблица 7.8 - Смета затрат участка
Основная и дополнительная заработная плата производственных рабочих
Отчисления на социальные нужды производственных рабочих
Расходы на содержание и эксплуатацию оборудования
Таким образом эксплуатационные затраты по участку составили
З об = 64364735 руб.
6 Расчет себестоимости продукции
Себестоимость продукции Эобщ руб. определяется по формуле
7 Расчет годового валового дохода
Расчет годового валового дохода ВД год производится по формуле
где П - процент прибыли;
N – годовая программа шт.
Срок окупаемости Ток руб. определяется по формуле
9 Технико-экономические показатели проекта
Основные технико-экономические показатели проекта приведены в таблице 7.9.
Таблица 7.9 - Технико-экономические показатели
Наименование показателей
Годовая производственная программа шт.
Количество единиц технологического оборудования шт.
Численность рабочих чел.
Балансовая стоимость машин и оборудования руб.
Балансовая стоимость малоценного и быстроизнашивающегося оборудования инструмента инвентаря руб.
Амортизация оборудования руб.
Расходы на содержание и эксплуатацию оборудования инструмента инвентаря руб.
Общецеховые расходы руб.
Эксплуатационные затраты по участку руб.
Себестоимость продукции руб.
Годовой валовой доход руб.
Срок окупаемости лет
6 Экология 9с гот..doc
Высокая загрязненность окружающей среды истощение запасов природных ресурсов ухудшение качества нашей среды обитания – это мыслышим чутьли некаждый день иуже успели привыкнуть кподобным сообщениям.
Однако все чаще мыслышим идругое: система управления окружающей средой экологическая безопасность продукции ресурсосберегающие технологии экологический имидж компании ит.п. Эти понятия еще мало знакомы населению зато вызывают все больший интерес упроизводителей. Экологические проблемы вышли науровень взаимоотношения «производитель– потребитель» «предприятие– государство» «товар— рынок».
Причина перехода проблемы изсферы ведения отдельных структур всферу взаимодействия различных секторов рынка состоит вследующем: загрязнение окружающей среды– проблема давно уже нерегиональная икеерешению должны подключиться вкаждой стране ивсе участники процесса влияния наокружающую среду. Среди основных участников этого процесса– производственные предприятия.
Мировое и впервую очередь Европейское сообщество уже выдвинуло ряд требований корганизациям торгующим состранами ЕС. Это нормы обязательного ирекомендательного характера касающиеся построения напредприятии систем менеджмента вобласти экологической безопасности социальной ответственности качества продукции. Правила– международные стандарты— являются основанием для добровольной сертификации готовой продукции или систем менеджментауправления напредприятии очем ипойдет речь внастоящей брошюре.
В России эти стандарты известны далеко невсем неговоря уже обихшироком применении натерритории РФ. Однако при попытке выйти намеждународный рынок заключить договор сбанком внешнеторговой организацией выбыстро ощутите «рекомендательный» характер таких стандартов. Вглазах вашего потенциального партнера наличие подобных сертификатов является подтверждением высокого уровня вашей ответственности запроцесс производства залюдей работающих вкомпании изакачество окружающей среды. Другими словами отэтого зависит ваш имидж аследовательно иконкурентоспособность.
Насколькобы спорны нибыли причины тех или иных изменений вокружающей нас среде уже существует комплекс стандартов принятый мировой общественностью ипредъявляющий определенные требования кучастникам рынка. И чтобы соответствовать современным тенденциям достижения делового ифинансового успеха необходимо учитывать эти условия.
2 Анализ выбросов участка
Все выбросы делятся на две основные группы – парогазовые и аэрозольные.
Парогазовые выбросы – это смесь газов (паров) не несущая в себе твердых или жидких взвешенных частичек. Эту группу целесообразно разделить на подгруппы.
а. Выбросы не подлежащие очистке либо по причине их безвредности либо по соображениям экономической целесообразности рассеивания через недорогие (невысокие) трубы либо из-за полного отсутствия технических возможностей очистки в данный период времени. Последнее может быть допущено только временно; необходимо срочно организовать НИР и ОКР с целью разработки проектных решений приемлемых в промышленном масштабе.
б. Выбросы подлежащие обязательной очистке (обезвреживанию). Сюда относятся выбросы содержащие вредные компоненты отрицательное влияние которых не может быть устранено только путем рассеивания (либо для этого требуются очень высокие и дорогостоящие трубы). Подразумевается что технические средства для очистки (обезвреживания) имеются.
Аэрозольные выбросы – это смесь газов (паров) несущая твердые или жидкие взвешенные частички.
В этой группе можно выделить следующие подгруппы.
а. Аэрозоли в которых дисперсная фаза подлежит улавливанию а парогазовая (дисперсионная среда) относится к подгруппе 1а и при этом не оказывает влияния на работу газоочистительных сооружений т. е. является нейтральной в процессе очистки.
б. Аэрозоли у которых дисперсная фаза подлежит улавливанию а парогазовая относясь к подгруппе 1а в то же время оказывает определенное влияние на ход очистки.
в. Аэрозоли у которых дисперсная фаза подлежит улавливанию а парогазовая относится к подгруппе 1б. В этом случае требуется либо комбинированная очистка в одном аппарате либо комбинация последовательно расположенных аппаратов для селективного улавливания дисперсной фазы и вредных примесей дисперсионной среды.
г. Аэрозоли у которых дисперсионная среда относится к подгруппе 1б а дисперсная фаза улавливанию не подлежит (например из-за очень низкой ее концентрации) и в то же время не оказывает влияния на процесс очистки.
д. Аэрозоли у которых дисперсионная среда относится к подгруппе 1б а дисперсная фаза улавливанию не подлежит однако может оказывать влияние на процесс очистки (например постепенно загрязнять жидкий или твердый поглотитель – сорбент).
е. Аэрозоли у которых дисперсионная среда относится к подгруппе 1а а дисперсная фаза – к 2г или 2д. Такой аэрозоль не нуждается в очистке.
Предложенная классификация достаточно проста и соответствует задачам настоящей книги. Более подробная оценка выбросов должна производиться при конкретном проектировании.
В массе летучих промышленных выбросов аэрозоли составляют несравненно более значительную часть нежели парогазовые выбросы. Дисперсионной средой в аэрозольных выбросах являются как правило многокомпонентные парогазовые смеси. Как отмечено выше характеристики аэрозоля универсальны поскольку они включают в себя данные обо всех его компонентах в том числе и о парогазовых.
Свойства парогазовых компонентов в составе аэрозолей в общем сохраняются однако наличие дисперсной фазы в ряде случаев способно повлиять на интенсивность их проявления. При потенциально пожаро- и взрывоопасной дисперсионной среде негорючая дисперсная фаза играет роль флегматизатора т. е. служит дополнительным фактором безопасности. В зависимости от природы аэрозольных частиц и дисперсионной среды отдельные парогазовые ком-поненты могут поглощаться частицами. Такие избирательные контакты между фазами аэрозоля представляют значительный практический интерес. В мировой практике они используются для очистки газов от некоторых газообразных примесей.
Например для очистки выбросов от фтороводорода в поток газа содержащего HF вводится дозированное количество тонко диспергированного твердого сорбента – глинозема Аl2О3. Последний поглощает HF после чего химически видоизмененный аэрозоль пропускается через тканевые или электрические фильтры. Глинозем насыщенный HF улавливается и возвращается в производство.
В жидких аэрозолях помимо поглощения частицами дисперсной фазы компонентов дисперсионной среды в определенных условиях наблюдается обратная картина – испарение капелек тумана с появлением в составе дисперсионной среды новых компонентов.
В отличие от парогазового выброса аэрозольный выброс является системой с ярко выраженной внутренней динамикой которая особенно сложна в смешанных аэрозолях. Усилению динамики способствует то что промышленные аэрозоли во всех без исключения случаях полидисперсны а частицы твердых аэрозолей обладают очень разнообразной морфологией.
3 Меры по снижению вредного воздействия на экологию
Для снижения вредного воздействия авторемонтного завода на окружающую среду при его проектировании строительстве и эксплуатации должны выполняться природоохранительные мероприятия.
Вокруг предприятия должна быть санитарно-защитная зона шириной не менее 50 м. Эту зону озеленяют и благоустраивают. Зеленые насаждения обогащают воздух кислородом поглощают углекислый газ шум очищают воздух от пыли и регулируют микроклимат.
Производства с вредными выделениями (окрасочный кузнечно-рессорный деревообрабатывающий и другие участки) по возможности сосредоточивают в филиалах на окраине города.
Предельно допустимый выброс вредных веществ в атмосферу определяют в соответствии с требованиями ГОСТ 17.2.3.02-78. При этом исходят из условия что концентрация вредных веществ в приземном слое атмосферы не должна превышать ПДК.
С целью поддержания чистоты атмосферного воздуха в пределах норм на авторемонтном заводе предусматривают предварительную очистку вентиляционных и технологических выбросов с их последующим рассеиванием в атмосфере.
Воздух удаляемый из окрасочного отделения с применением пульверизационной окраски перед выбросом в атмосферу очищают в гидрофильтрах.
Для очистки воздуха удаляемого из сушильных камер применяют дожигание или каталитическое дожигание. В первом случае пары растворителей содержащиеся в воздухе сгорают в струе горящего природного газа во втором случае загрязненный воздух нагревается до температуры 400 °C и подается на катализатор где и происходит дожигание вредных газообразных примесей.
Для очистки воздуха от сварочного аэрозоля выделяемого при сварке используют мокрые пылеуловители например барботеры где загрязненный воздух в виде пузырьков проходит через слой жидкости и очищается. Могут быть использованы и пластинчатые электрофильтры в которых частицы пыли получают электрический заряд и оседают на электроде при этом эффективность очистки составляет 095.
Снижения выброса вредных веществ котельными установками можно добиться за счет перевода с факельного сжигания жидкого топлива на процесс сжигания с избытком воздуха (с наддувом). Кроме того в течение всего отопительного сезона необходимо счищать дымоходы не реже одного раза в 2 мес. Важно также своевременно их ремонтировать.
В тех случаях когда очистные сооружения установить невозможно или они отсутствуют концентрацию вредных веществ в воздухе приземного слоя можно уменьшить путем рационального рассеивания пылегазовых выбросов в атмосфере. Это достигается при помощи высоких труб выхлопных шахт увеличенной высоты или повышением скорости выброса (факельный выброс).
Благоприятное воздействие на атмосферу в приземном слое оказывают искусственные водоемы которые поглощают пыль увлажняют охлаждают и ионизируют воздух.
Аннотация.doc
Во введении определена актуальность авторемонтного производства в условиях рыночных отношений. Обозначена цель проекта и задачи направленные на ее достижение.
В рамках технико-экономического обоснования освещены вопросы отражающие работу технических служб производственной базы предприятия произведен анализ организации и управления ремонтом.
В разделе технологический расчет дан выбор рационального способа восстановления детали. Произведен расчет рабочих числа оборудования производственных площадей.
В организационном разделе обосновываются организация технического контроля на предприятии.
В разделе безопасность труда и охрана окружающей среды произведен анализ опасных и вредных воздействий на рабочих и окружающую среду. Произведен расчет естественного освещения на участке. Смоделирована чрезвычайная ситуация.
В разделе экономическая часть рассчитан экономический эффект от внедрения технологического процесса рассчитан срок окупаемости дополнительных капитальных вложений.
Захватов Анатолий Алексеевич главный механик МАУ ДОР
3_Раздел.doc
1 Организация технического контроля на предприятии
Качество отремонтированной продукции оценивают по ее соответствию требованиям технических условий стандартов и других документов. Для контроля качества продукции на предприятии создается служба технического контроля. Основная задача службы заключается в предотвращении выпуска недоброкачественной продукции.
В задачи службы технического контроля на этапе производства также входят (рисунок 3.1):
- входной контроль качества поступающих на предприятие сырья материалов полуфабрикатов и комплектующих изделий;
- операционный контроль во время выполнения или после завершения определенных технологических операций;
- приемочный контроль с целью принятия решения о пригодности продукции к поставкам и использованию (ГОСТ 16504 -81);
- эксплуатационный контроль с целью проверки правильности проведения периода обкатки агрегатов и автомобиля в условиях эксплуатации соблюдения периодичности и объема технического обслуживания сбора и анализа информации о надежности продукции ремонтного предприятия.
По охвату контролируемой продукции различают:
- сплошной контроль всех единиц продукции в партии;
- выборочный контроль который характеризуется проверкой одной или нескольких единиц из определенной партии или потока продукции.
По месту проверки различают:
- стационарный контроль – выполняется на специально оборудованном в цехе (участке) контрольном посту;
- скользящий контроль – выполняется на рабочем месте куда доставляют необходимые средства контроля и прибывает контролер.
Рисунок 3.1 – Классификация видов технического контроля
Посты OTK планируют размещают и оснащают с учетом их назначения характера выполняемых контрольных операций. Посты контроля специализируются по предметному признаку (пост контроля коленчатых валов пост контроля корпусных деталей и т. п.).
Планирование контроля в АРЗ включает: определение объемов и составление планов контроля оценку качества продукции по результатам контроля.
Приемо-сдаточным испытаниям и приемочному контролю подвергается 100 % отремонтированных автомобилей. Приемосдаточные испытания целесообразно проводить на обкаточно-тормозных стендах. Представитель OTK завода в паспорте обкатанного и принятого автомобиля делает отметку о его пригодности к эксплуатации.
Важным этапом в организации OTK является подбор кадров при котором должен действовать принцип: превосходство знания контролирующего над знаниями контролируемого. Работник OTK должен хорошо знать технологический процесс уметь не только обнаружить дефекты продукции но и установить причину их появления а также участвовать в разработках мероприятий по повышению качества выпуска изделий.
2 Разработка генерального плана авторемонтного завода
Генеральный план (генплан) АРЗ отражает расположение на участке застройки (территории предприятия) зданий и сооружений складских площадок транспортных путей зеленых насаждений ограждений и других объектов. Перечень размещаемых объектов и их размеры должны быть установлены перед разработкой генплана. Наиболее важным является определение количества производственных корпусов и расположения вспомогательных (административно-бытовых) помещений.
Рекомендуется по возможности блокировать цеха и помещения в одном здании что позволяет снизить затраты на строительство зданий и прокладку инженерных коммуникаций.
У входа на территорию предприятия предусматривают площадку для стоянки легковых автомобилей из расчета десяти машино-мест на 88 работающих в одну смену при площади одного машино-места 25 м2.
Генеральные планы ремонтных предприятий выполняют как правило в масштабе 1:500.
3 Компоновочный план участка ремонта КПП
Здания АРЗ проектируют как правило с железобетонными колоннами. Оси колонн определяющие в плане расположение их рядов называют разбивочными осями. Расстояние между разбивочными осями в поперечном направлении называют пролетом в продольном – шагом колонн. Пролет L и шаг колонн t в метрах образуют сетку колонн обозначаемую Lt. На чертежах компоновочных планов разбивочные оси маркируют по длинной стороне здания цифрами слева направо и по короткой – заглавными буквами русского алфавита снизу вверх.
Компоновочный план разрабатывают для каждого отдельно стоящего здания а при использовании многоэтажных зданий – для каждого этажа. На нем указывают расположение производственных участков складских и административно-бытовых помещений вентиляционных камер трансформаторных подстанций тепловых пунктов продольных и поперечных проездов. Обозначают габаритные размеры здания сетку колонн с маркировкой разбивочных осей наружные и внутренние стены и перегородки подвалы и антресоли. На компоновочном плане показывают подъемно-транспортное оборудование связанное с конструктивными элементами зданий (опорные и подвесные краны лифты). Расстановку технологического оборудования на компоновочном плане не показывают. Исключением является обозначение расположения основных поточных линий если это необходимо для обоснования принимаемого объемно-планировочного решения. На свободном поле чертежа показывают вертикальный разрез здания с указанием высоты пролетов от пола до низа несущих конструкций здания а в пролетах с мостовыми кранами дополнительно указывают расстояние от пола до головки рельсов подкрановых путей. Компоновочные планы выполняют в масштабах 1:400 или 1:200.
В зависимости от направления перемещения в процессе ремонта рамы (для предприятий по ремонту полнокомплектных автомобилей) или базовой детали (для предприятий по ремонту агрегатов) различают три компоновочные схемы: прямоточную Г-образную и П-образную.
Преимуществами прямоточной схемы являются прямолинейность и соответственно удобство перемещения базовой детали и других крупногабаритных и тяжелых деталей минимальное пересечение транспортных потоков. Недостатки — наличие ограничений на длину разборочных и сборочных поточных линий относительное увеличение дальности транспортирования деталей от мест разборки к местам сборки затрудненность изоляции разборочно-моечного участка от других участков.
Применение Г-образной и П-образной схем позволяет более эффективно изолировать разборочно-моечный участок от других участков несколько сократить дальность транспортирования деталей значительно ослабляет ограничения на длину разборочных и сборочных поточных линий (особенно при П-образной схеме) однако непрямолинейность перемещения базовой детали и других крупногабаритных и тяжелых деталей вызывает повышенное пересечение транспортных потоков и трудности в их организации.
Разработку компоновочного плана начинают с выбора сетки колонн и определения габаритных размеров здания. Для одноэтажных зданий наиболее часто применяется сетка колонн 126 м с которой и рекомендуется начать определение габаритных размеров здания. Исходя из принятой компоновочной схемы задают число пролетов регламентируя тем самым ширину здания. Длину здания определяют путем деления его площади на ширину. Рекомендуемые соотношения ширины и длины здания – от 1:13 до 1:2. Добиться рекомендуемых соотношений можно изменяя число пролетов а при необходимости — и сетку колонн выбирая ее из ряда 186 м 1812 м 2412 м. Размеры пролетов и шагов колонн могут быть и большими но обязательно кратными 6 м что диктуется требованиями унификации изделий строительной индустрии.
Размещение в производственном корпусе производственных складских и вспомогательных помещений удобно начать с определения расположения продольных магистральных проездов.
Расположение в производственном корпусе производственных складских и вспомогательных помещений должно удовлетворять следующим требованиям:
- расположение производственных участков основного производства должно соответствовать технологической последовательности выполнения работ при минимальном грузообороте;
- производственные участки вспомогательного производства следует располагать вблизи от обслуживаемых ими участков основного производства;
- склады следует располагать вблизи от обслуживаемых ими производственных подразделений;
- изолировать производственные участки и склады от других помещений стенами следует только при необходимости которая диктуется противопожарными и санитарными требованиями а также требованиями сохранности материальных ценностей.
2_Раздел.doc
Исходными данными для разработки технологического процесса являются:
рабочий чертёж детали № 14.1701105 с технологическими требованиями на её изготовление;
производственная программа Nг = 5000 штгод;
маршрутный коэффициент Mк = 023;
карта технических требований на дефектацию детали № 14.1701105;
типовой технологический процесс восстановления деталей класса “круглые стержни”;
каталоги и справочники по используемому оборудованию и технологической оснастке.
Рисунок 1 – Дефекты вала вторичного коробки передач
Таблица 1 – Карта дефектации вала вторичного коробки передач
Износ шейки под подшипники
Износ шеек под ролики подшипников
Износ поверхности под подшипник
Наибольший износ вторичного вала детали 14.1701105 происходит по шлицевому элементу под синхронизатор 4 и 5 передачи так называемому замку (или утонению). Этот дефект имеет 72 процента ремфонда.
Для валов с односторонним износом шлицевого элемента применяется односторонняя наплавка проволокой 51ХФА 12 мм на полуавтомате А547-У в среде углекислого газа. Далее детали обрабатывают по следующей технологии:
) зачистка центров 2) шлифование наружного диаметра в зоне наплавки заподлицо с основным металлом 3) фрезерование наплавленного шлицевого элемента в номинальный размер 4) зачистка наплывов.
Утонение с восстанавливаемой стороны шлица не фрезеруют используя в качестве замка утонение оставшееся с неизношенной стороны шлицев.
Все валы проверяют на сопрягаемость кареткой синхронизатора 4 и 5 передачи детали 14.1701156.
У валов с полным износом утонения после наплавки утонение фрезеруют с 2-х сторон. Операция фрезерования производится специальной фрезерной головкой оснащенной твердосплавной напайкой ВК6 ВК8. Твердость восстановленного шлицевого элемента HRC 52-53. При фрезеровании утонения применяют концевые фрезы с такой же напайкой.
При срыве или износе резьбы не более 1 нитки следует калибровать резьбу плашкой. При износе резьбы более 1 нитки наплавить резьбу сварочной проволокой Св-08Г2С 12 мм затем точить под резьбу и нарезать новую резьбу. В мелкосерийном производстве можно обработать поверхность П под резьбу .
Среди посадочных мест наибольший износ имеют шейки под роликоподшипники . Характер износа: следы проворота роликоподшипника наклеп на шейке следы сплавления роликоподшипника с шейкой.
Для восстановления шеек применимы газопламенное напыление с оплавлением электроконтактная наплавка порошком с последующим шлифованием в номинальный размер кругами 91А40СМ1. Шейки можно шлифовать "как чисто" затем хромировать или осталивать с припуском на последующую механическую обработку.
2 Разработка ремонтного чертежа
Ремонтный чертеж разрабатывается в соответствии с требованиями ГОСТ ГОСТ 2.604-2000.
На ремонтном чертеже: места подлежащие восстановлению выполняются сплошной основной линией остальные изображения сплошной тонкой линией. Допуски на свободные размеры (14;15;16 квалитетов) округляются до десятых долей миллиметра.
На ремонтных чертежах изображаются только те виды сечения и размеры которые необходимы для восстановления детали.
Ремонтные и пригоночные размеры а также размеры детали ремонтируемой снятием необходимого минимального слоя металла обозначают буквами а их числовые значения и другие данные указывают на выносных линиях или в таблице помещаемой в правой верхней части чертежа. На ремонтном чертеже помещают также технологические требования и указания. Обозначение ремонтного размера выполняется с добавлением индекса "Р" к номеру детали.
3 Обоснование размера партии
В условиях ремонтного производства размер производственной партии принимается равной месячной декадной или дневной потребности в ремонтируемых или изготавливаемых деталях.
В начальной стадии проектирования технологического процесса величина производственной партии определяется ориентировочно по формуле
где годовая производственная программа полнокомплектных ремонтов автомобилей;
маршрутный коэффициент ремонта деталеи;
коэффициент потери деталей в процессе ремонта от неисправимого брака обнаруженных дефектов и т.д. для ремонтного производства;
коэффициент учитывающий размер детали :
– 3 дня для крупных деталей (вес более 50 кг.);
дней – для средних деталей;
дней – для мелких деталей;
количество одинаковых деталей в автомобиле (агрегате)шт. ;
количество рабочих дней в году дн.
4 Определение последовательности выполнения операций подбор оборудования приспособлений режущего и вспомогательного инструмента
4.1 Определение последовательности выполнения операций
Восстановление изношенной детали – это комплекс работ по устранению дефектов появившихся в период эксплуатации или хранения машины обеспечивающей восстановления работоспособности и надёжности до уровня равного или превышающего уровень установленный для новой детали. Выбор рационального способа восстановления детали по критерию применимости выполняем по этапам.
этап - Отбираем все существующие способы восстановления обеспечивающие требуемую толщину твёрдость сцепляемость и шероховатость восстановленной поверхности. При восстановлении шлицов принимаем следующие способы: дуговая наплавка под слоем флюса; вибродуговая наплавка; наплавка в среде углекислого газа; электроконтактная наплавка лентой; термическая обработка (нормализация); токарная обработка; фрезерная обработка; термическая обработка; хромирование; осталивание; упрочняющее накатывание.
этап - Рассматриваем способы с точки зрения их воздействия на невосстанавливаемые поверхности деталь в целом а так же оцениваем влияние восстановленной поверхности на показатели надёжности сопряжённой детали. Из-за большого температурного воздействия на деталь и возможности её коробления отбрасываем термическая обработка в качестве упрочняющих работ после фрезерования. Оставляем следующие способы: дуговая наплавка под слоем флюса; вибродуговая наплавка; наплавка в среде углекислого газа; электроконтактная наплавка лентой; термическая обработка (нормализация); токарная обработка; фрезерная обработка; хромирование; осталивание; упрочняющее накатывание.
этап - Оставшиеся способы рассматриваем с точки зрения технологической возможности их использовании при создании поточно-механизированной линии для восстановления деталей. Оставляем следующие способы: дуговая наплавка под слоем флюса; термическая обработка (нормализация); токарная обработка; фрезерная обработка; хромирование; осталивание; упрочняющее накатывание.
этап - Анализируем дефицитность ремонтных материалов и технологического оборудования. Отказываемся от хромирования из-за дефицитности оборудования. Оставляем следующие способы: дуговая наплавка под слоем флюса; термическая обработка (нормализация); токарная обработка; фрезерная обработка; осталивание; упрочняющее накатывание.
этап - Учитываем влияние способов восстановления на рабочих и окружающую среду отказываемся от осталивания. По этому критерию применимости принимаем следующие способы: дуговая наплавка под слоем флюса; термическая обработка (нормализация); токарная обработка; фрезерная обработка; упрочняющее накатывание.
Окончательный выбор рационального способа восстановления детали производим при помощи технико-экономического критерия.
Используем операции связанные только с восстановлением шлицов. Это связанно с тем что на проектируемый участок поступают только первичные валы с дефектными шлицами. С другими неисправностями первичные валы не принимаются.
Очистить вал и промыть его в растворе моющего средства МС-8 концентрации 20 гл и температурой 75-80 0 С.
Наличие смолистых отложений загрязнения и смазки на поверхности вала не допускаются.
Машина для очистки ОМ-5288.
Разряд работы-2. Трудоемкость-45 мин .
Провести тщательный визуальный осмотр. Определить геометрические параметры вала – измерить инструментом.
Разряд работ-5. Трудоемкость-85 мин.
) Дуговая наплавка под слоем флюса.
Производится заваривание шлицов.
Оборудование: наплавочный станок У651.
Приспособления и инструмент: аппарат для автоматической наплавки А1408.
Число проходов определяется по формуле
где D – диаметр до которого наплавляют деталь мм;
d – диаметр наплавляемой поверхности мм;
t – толщина наплавляемого слоя за один проход мм.
Силу тока Iсв принимаем равную 140 А при диаметре электрода dпр = 2 мм.
Напряжение U В определяется по формуле
Показатель характеризующий удельное значение скорости наплавки коэффициент наплавки КН гА·ч определяется по формуле
Скорость перемещения дуги и скорость наплавки VH мч обуславливается шириной валиков и глубиной проплавления
где F – площадь поперечного сечения наплавляемого валика F = 02 см2;
γ – плотность металла шва гсм3.
Частота вращения детали
Скорость подачи электродной проволоки Vпр мч определяется возможностью её полного расправления
Принимаем Vпр =50 мч. Отсюда следует что плотность метала шва γ гмс3 определяется по формуле
Вылет электрода равен
Смещение электрода равно
Основное время наплавки То мин определяется по формуле
Разряд работ – 5. То = 10072 мин. Тв = 08 мин. Тдоп = 113 мин. Тпз = 16 мин.
) Термическая обработка (нормализация).
Оборудование: печь для отпуска Pyro 1611G.
Разряд работы – 5. Трудоёмкость – 60 мин.
Оборудование: универсальный токарно-винторезный станок 16К20.
Расчёт глубины резанья t мм
где d – диаметр поверхности детали до обработки мм;
d1 – диаметр поверхнолсти детали после обработки мм.
Срез необходимого слоя проводится в 3 прохода резца: 2 прохода черновой обработки с оставлением припуска 001 мм на чистовую обработку.
Расчёт основного времени Тo мин
где Sф – табличное значение подачи станка ммоб;
nф – табличное значение частоты вращения шпинделя обмин;
L – длина обрабатываемой поверхности мм;
Расчёт основного времени на чистовую обработку
Расчёт основного времени на черновую обработку
Разряд работ – 6. То= 308 мин. Тв= 1 мин. Тдоп = 017 мин. Тпз= 16 мин.
Оборудование: зубофрезерный станок модели ЕЗ – 208.
Приспособления и инструмент: фреза червячная для шлицевых валов с прямым профилем 10х72х78 ГОСТ 8027 – 86.
Расчёт подачи на один зуб фрезы Sz ммзуб
где So – табличное значение подачи ммоб;
Z – число зубьев фрезы.
Расчёт подачи на один зуб фрезы при чистовом фрезеровании:
Расчёт подачи на один зуб фрезы при черновом фрезеровании
Расчёт минутной подачи SM мммин
где nф – фактическое частота вращение фрезы взятая из параметров станка мин-1.
Расчёт минутной подачи при чистовом фрезеровании
Расчёт минутной подачи при черновом фрезеровании
где L – длина пути проходимого инструментом мм;
i – число проходов фрезы .
Расчёт основного времени при чистовом фрезеровании
Расчёт основного времени при черновом фрезеровании
Разряд работ – 6. То= 428 мин. Тв= 1 мин. Тдоп = 022 мин. Тпз= 16 мин.
) Упрочняющее накатывание.
Оборудование: универсальный токарно-винторезный станок 16К20 модернизированный.
Приспособления и инструмент: делительная головка ST 130 приспособление для упрочняющего накатывания гидростанция серии 108.
Определение скорости продольного перемещения установки Vпр мммин
где Sпр – продольная подача взятая из характеристик станка ммоб;
n – частота оборотов шпинделя взятая из характеристик станка обмин.
Определение скорости поперечного перемещения установки Vпоп мммин
где Sпоп – поперечная подача взятая из характеристик станка ммоб.
Накат шарика осуществляется через каждые 025 мм. исходя из этого определяем число продольных проходов
где h – высота зуба мм.
Расчёт основного времени упрочняющего накатывания То мин
Разряд работ – 6. То= 221 мин. Тв= 1 мин. Тдоп = 347 мин. Тпз= 19 мин.
Провести контроль согласно техническим требованиям на выдачу вторичного вала из восстановления.
Разряд работ – 5. Трудоемкость – 8 мин.
4.2 Выбор оборудования
Номенклатура и количество оборудования по рабочим местам рассчитываются в соответствии с технологическим процессом трудоёмкостью выполняемых работ и фондом времени.
Перечень применяемого оборудования приведен в таблице 2.2
Таблица 2.2 – Оборудование для восстановления детали № 14.1701105 на слесарно-механическом участке
Универсальный токарно-винторезный станок 16К20
Пресс гидравлический CP150 для правки валов
Зубофрезерный станок модели ЕЗ – 208
Верстак слесарный металлический 2-тумбовый
Станок вертикально-сверлильный 2Т140
Универсальный токарно-винторезный станок 16К20 модернизированный
4.3 Выбор приспособлений
Вид подъемно-транспортного средства выбираем по таблицам в зависимости от номенклатуры восстанавливаемого объекта типа производства частоты и дальности перевозок объектов.
Принимаем тележку ручную для длинных грузов ДЛ.
Также для ремонтных работ выбираем делительную головку ST 130 гидростанция серии 108 и приспособление для упрочняющего накатывания.
4.4 Выбор режущего и вспомогательного инструмента
Для фрезерования используется фреза червячная для шлицевых валов с прямым профилем 10х72х78 ГОСТ 8027 – 86 резец 2103-0695 ВК8 ГОСТ 20872-80 тип 3.
5 Расчет годового объема работ участка
Годовой объем работы (годовая трудоемкость) авторемонтного завода определяется по формуле
где t – трудоемкость ремонтных работ чел.-ч;
– годовая производственная программа шт.
Для вторичного вала двигателя КамАЗ-740 годовая t = 424 чел.-ч.
Годовая производственная программа в соответствии с выданным заданием Nг = 5000 штгод.
Исходя из приведенных данных определяем величину годового объема работ всего авторемонтного завода
Годовой объем работы (годовая трудоемкость) участка восстановления основных и базовых деталей определяется в процентном отношении от годового объема работ авторемонтного завода.
По данным трудоемкость участка восстановления основных и базовых деталей при капитальном ремонте полнокомплектного грузового автомобиля составляет 11 %.
Для учета работ по самообслуживанию производства необходимо увеличить этот полученное значение на 10 %
Таким образом годовой объем работ проектируемого участка составляет:
Годовой объем механических работ распределяется по видам обработки с учетом их процентного соотношения принятого в практике проектирования АРП. Сводная годового объема работ по видам обработки приведена в таблице 2.3.
Таблица 2.3 – Годовая трудоемкость по видам работ участка по ремонту КПП
Годовой объем работ в процентах от общего объема
Годовой объем работ чел.-ч
Работы по первичному валу:
Накатное полирование и упрочняющее накатывание
6 Расчет состава рабочих на участке
Технологически необходимое число рабочих т.е. число фактически являющихся на работу определяется по формуле
где - годовой объем работ чел.-ч;
- номинальный годовой фонд времени рабочих ч;
- коэффициент повышения производительности труда; принимается равным 120.
Штатное число рабочих т.е. число фактически являющихся на работу и отсутствующих по уважительным причинам определяется по формуле
где - действительный годовой фонд времени рабочих ч.
Принимая во внимание значения и определим общее число производственных работников.
Количество токарей по ремонту вторичных валов
Принимаем четыре токаря по ремонту вторичных валов.
Количество фрезеровщиков по ремонту вторичных валов
Принимаем два фрезеровщика по ремонту вторичных валов.
Количество операторов по электромагнитной наплавке вторичных валов
Принимаем четыре оператора по электромагнитной наплавке вторичных валов.
Количество слесарей по ремонту вторичных валов принимаем из учёта слесарных и сверлильных работ
Принимаем два слесаря по ремонту вторичных валов.
Количество операторов прессовых станков по ремонту вторичных валов
Принимаем одного оператора прессовых станков по ремонту вторичных валов.
Итого производственных рабочих 13 чел.
Число вспомогательных рабочих определяется в процентах от списочного числа производственных рабочих по формуле
Принимаем двух вспомогательных рабочих.
Число инженерно-технических работников определяется в процентах от списочного числа производственных и вспомогательных рабочих по формуле
Принимаем трёх инженерно-технических работников.
Число младшего обслуживающего персонала определяется в процентах от списочного числа производственных и вспомогательных рабочих по формуле
Принимаем одного человека.
Число служащих определяется в процентах от списочного числа производственных и вспомогательных рабочих по формуле
Принимаем одного служащего.
Результаты расчета состава работающих приведены в таблице 2.4.
Таблица 2.4 – Штатное расписание участка по ремонту КПП
Наименование профессии
Фрезеровщиков по ремонту вторичных валов
Оператора по электромагнитной наплавке
Операторов прессовых станков
Токарей по ремонту вторичных валов
Вспомогательный рабочий
Младший обслуживающий персонал
7 Расчет количества станков
Число станков по каждому виду работ определяем по формуле
где – действительный годовой фонд времени оборудования ч;
у – количество смен.
Принимаем два токарных станка.
Принимаем два фрезерных станка.
Станков по электромагнитной наплавке
Принимаем два станка.
Принимаем один пресс.
Количество сверлильных станков
Принимаем один сверлильный станок.
Количество верстаков определяем исходя из слесарных работ
Принимаем один верстак.
8 Расчет производственных площадей
Площадь производственного участка предварительно рассчитывается по суммарной площади занимаемой технологическим оборудованием производственным инвентарем и коэффициенту плотности расстановки оборудования учитывающему рабочие места перед оборудованием проходы проезды нормы расстояний между оборудованием и элементами зданий.
Суммарная площадь занимаемую технологическим оборудованием и производственным инвентарем определяется по формуле
где- площадь i-го оборудования м2
m- общее количество оборудования шт;
n- количество i-го оборудования шт.
Площадь производственного участка определяется по формуле
Для участка по ремонту КПП .
5 Безоп труда гот.doc
1 Анализ условий труда и вредных производственных факторов
1.1 Параметры микроклимата
Параметры микроклимата оказывают непосредственное влияние на тепловое самочувствие человека и его работоспособность. Например понижение температуры и повышение скорости воздуха способствуют усилению конвективного теплообмена и процесса теплоотдачи при испарении пота что может привести к переохлаждению организма. При повышении температуры воздуха возникают обратные явления.
Исследованиями установлено что при температуре воздуха более 30°С работоспособность человека начинает падать. Для человека определены максимальные температуры и зависимости от длительности их воздействия и используемых средств защиты Предельная температура вдыхаемого воздуха при которой человек в состоянии дышать в течение нескольких минут без специальных средств защиты около 116°С.
Переносимость человеком температуры как и его теплоощущение в значительной мере зависит от влажности и скорости окружающего воздуха. Чем больше относительная влажность тем меньше испаряется пота в единицу времени и тем быстрее наступает перегрев тела. Особенно неблагоприятное воздействие на тепловое самочувствие человека оказывает высокая влажность при t 30°С так как при этом почти вся выделяемая теплота отдается в окружающую среду при испарении пота. При повышении влажности пот не испаряется а утекает каплями с поверхности кожного покрова. Возникает так называемое «проливное» течение пота изнуряющее организм и не обеспечивающее необходимую теплоотдачу.
Недостаточная влажность воздуха также может оказаться неблагоприятной для человека вследствие интенсивного испарения влаги со слизистых оболочек их пересыхания и растрескивания а затем и загрязнения болезнетворными микроорганизмами.
Длительное воздействие высокой температуры особенно в сочетании с повышенной влажностью может привести к значительному накоплению теплоты в организме и развитию перегревания организма выше допустимого уровня — гипертермии - состоянию при котором температура тела поднимается до 38 39°С. При гипертермии и как следствие тепловом ударе наблюдаются головная боль головокружение общая слабость искажение цветового восприятия сухость во рту тошнота рвота обильное потовыделение. Пульс и дыхание учащены в крови увеличивается содержание азота и молочной кислоты. При этом наблюдается бледность синюшность зрачки расширены временами возникают судороги потеря сознания.
Производственные процессы выполняемые при пониженной температуре большой подвижности и влажности воздуха могут быть причиной охлаждения и даже переохлаждения организма — гипотермии. В начальный период воздействия умеренного холода наблюдается уменьшение частоты дыхания увеличение объема вдоха. При продолжительном действии холода дыхание становится неритмичным частота и объем вдоха увеличиваются изменяется углеводный обмен. Увеличение обменных процессов при понижении температуры на 1°С составляет около 10 % а при интенсивном охлаждении может возрасти в 3 раза по сравнению с уровнем основного обмена. Появление мышечной дрожи при которой внешняя работа не совершается а вся энергия превращается в теплоту может в течение некоторого времени задерживать снижение температуры внутренних органов. Результатом действия низких температур являются холодовые травмы.
Атмосферное давление оказывает существенное влияние на процесс дыхания и самочувствие человека.
Избыточное давление воздуха приводит к повышению парциального давления кислорода в альвеолярном воздухе к уменьшению объёма легких и увеличению силы дыхательной мускулатуры необходимой для производства вдоха-выдоха. В связи с этим работа на глубине требует поддержания повышенного давления с помощью специального снаряжения или оборудования в частности кессонов или водолазного снаряжения.
При работе в условиях избыточного давления снижаются показатели вентиляции легких за счет некоторого урежения частоты дыхания и пульса. Длительное пребывание при избыточном давлении (порядка 700 кПа) приводит к токсическому действию некоторых газов входящих в состав вдыхаемого воздуха. Оно проявляется в нарушении координации движений возбуждении или угнетении галлюцинациях ослаблении памяти расстройстве зрения и слуха.
1.2 Вредные вещества
В настоящее время известно около 7 млн. химических веществ и соединений из которых 60 тыс. находят применение в деятельности человека. На международном рынке ежегодно появляется 500 1000 новых химических соединений и смесей.
Вредным называется вещество которое при контакте с организмом человека может вызывать травмы заболевания или отклонения в состоянии здоровья обнаруживаемые современными методами как в процессе контакта с ним так и в отдаленные сроки жизни настоящего и последующих поколений.
Химические вещества (органические неорганические элементорганические) в зависимости от их практического использования классифицируются на:
- промышленные яды используемые в производстве: например органические растворители (дихлорэтан) топливо (пропан бутан) красители (анилин);
- ядохимикаты используемые в сельском хозяйстве: пестициды (гексахлоран) инсектициды (карбофос) и др.;
- лекарственные средства;
- бытовые химикаты используемые в виде пищевых добавок (уксусная кислота) средства санитарии личной гигиены косметики и т. д.;
- биологические растительные и животные яды которые содержатся в растениях и грибах (аконит цикута) у животных и насекомых (змей пчел скорпионов);
- отравляющие вещества (ОВ): зарин иприт фосген и др.
Ядовитые свойства могут проявить все вещества даже такие как поваренная соль в больших дозах или кислород при повышенном давлении. Однако к ядам принято относить лишь те которые свое вредное действие проявляют в обычных условиях и в относительно небольших количествах.
К промышленным ядам относится большая группа химических веществ и соединений которые в виде сырья промежуточных или готовых продуктов встречаются в производстве.
В организм промышленные химические вещества могут проникать через органы дыхания желудочно-кишечный тракт и неповрежденную кожу. Однако основным путем поступления являются легкие. Помимо острых и хронических профессиональных интоксикаций промышленные яды могут быть причиной понижения устойчивости организма и повышенной общей заболеваемости. Бытовые отравления чаще всего возникают при попадании яда в желудочно-кишечный тракт (ядохимикатов бытовых химикатов лекарственных веществ).
1.3 Электробезопасность
Повышение электробезопасности в установках достигается nрименением систем защитного заземления зануления защитного отключения и других средств и методов защиты в том числе знаков безопасности и предупредительных плакатов и надписей. В системах местного освещения в ручном электрофицированном инструменте и в некоторых других случаях применяют пониженное напряжение.
Помещения без повышенной опасности - это сухие беспыльные помещения с нормальной температурой воздуxa и с изолирующими (например деревянными) полами т. е. в которых отсутствуют условия свойственные помещениям с повышенной опасностью и особо опасным.
Помещения с повышенной опасностью характеризуются наличием одного из следующих пяти условий создающих повышенную опасность:
- сырости когда относительная влажность воздуха длительно превышает 75 %; такие помещения называют сырыми;
- высокой температуры когда температура воздуха длительно (свыше суток) превышает + 35°С; такие помещения называются жаркими;
- токопроводящей пыли когда по условиям производства в помещениях выделяется токопроводящая технологическая пыль (например угольная металлическая и т. п.) в таком количестве что она оседает на проводах проникает внутрь машин аппаратов и т. п.; такие помещения называются пыльными с токопроводящей пылью;
- токопроводящих полов – металлических земляных железобетонных кирпичных и т. п.;
- возможности одновременного прикосновения человека к имеющим соединение с землей металлоконструкциям зданий технологическим аппаратам механизмам и т. п. с одной стороны и к металлическим корпусам электрооборудования – с другой.
Помещения особо опасные характеризуются наличием одного из следующих трех условий создающих особую опасность:
- особой сырости когда относительная влажность воздуха близка к 100 % (стены пол и предметы находящиеся в помещении покрыты влагой) такие помещения называются особо сырыми;
- химически активной или органической среды т. е. помещения в которых постоянно или в течение длительного времени содержатся агрессивные пары газы жидкости образующие отложения или плесень действующие разрушающе на изоляцию и токоведущие части электрооборудования; такие помещения называют помещениями с химически активной или органической средой;
- одновременного наличия двух и более условий свойственны помещениям с повышенной опасностью.
Особо опасными помещениями является большая часть производственных помещений в том числе все цехи машиностроительных заводов испытательные станции гальванические цехи мастерские и т. п. К таким же помещениям относятся и участки работ на земле под открытым небом или под навесом.
Во взрывоопасных зонах электроустановки заземляются при любых напряжениях питания независимо от рода тока.
Защитному заземлению или занулению подлежат металлические части электроустановок доступные для прикосновения человека которые могут оказаться под напряжением в результате повреждения изоляции.
Защитное отключение электроустановок обеспечивается путем введения устройства автоматически отключающего оборудование — потребитель тока при возникновении опасности поражения током.
Повышение электробезопасности достигается также путем применения изолирующих ограждающих предохранительных и сигнализирующих средств защиты.
2 Нормирование условий труда и вредных производственных факторов
2.1 Температура влажность и подвижность воздуха рабочей зоны
Оптимальные и допустимые величины устанавливаются для рабочей зоны помещений с учётом избытка тепла выполняемой работы и сезонов года. При кондиционировании производственных помещений должны соблюдаться оптимальные параметры микроклиматических условий.
Таблица 5.1 - Оптимальные нормы температуры относительной влажности и скорости движения воздуха в рабочей зоне производственных помещений
Скорость движения воздуха
Холодный и переходный периоды года
Средней тяжести -IIа Средней тяжести-IIб
Средней тяжести –IIа
Средней тяжести-IIб Тяжелая — III
2.2 Предельно допустимое содержание вредных веществ
Таблица 5.2 - Предельно допустимые уровни загрязнения кожи рук работающих с вредными веществами с соответствии с ГН 2.2.5.563—96 .
Наименование вещества
Металлическая сурьма
Метиловый спирт (метанол)
Содержание вредных веществ в воздухе рабочей зоны не должно превышать установленных ГОСТ 12.1.005 - 88 ПДК. В качестве примера в таблице 5.3 приведены ПДК некоторых веществ.
Таблица 5.3 - Предельно допустимые концентрации вредных веществ в воздухе рабочей зоны по ГОСТ 12.1.005—88 (извлечение)
Агрегатное состояние в условиях производства
Особенности действия на организм
Алюминий и его сплавы
Свинец и его соединения
Условные обозначения: П — пары и (или) газы; а — аэрозоль; П + а — смесь паров и аэрозоля; О — вещество с остронаправленным механизмом действия требующее автоматического контроля за его содержанием в воздухе; А — вещества способные вызывать аллергические заболевания; К — канцерогены; Ф — аэрозоли преимущественно фиброгенного действия.
2.3 Общие требования электробезопасности
При устройстве электрических сетей на строительной площадке необходимо предусматривать возможность отключения всех электроустановок в пределах отдельных объектов и участков работ.
Работы связанные с присоединением (отсоединением) проводов ремонтом наладкой профилактикой и испытанием электроустановок должны выполняться электротехническим персоналом имеющим соответствующую квалификационную группу по технике безопасности.
Присоединение к электрической сети передвижных электроустановок ручных электрических машин и переносных электрических светильников при помощи штепсельных соединений удовлетворяющих требованиям электробезопасности разрешается выполнять персоналу допущенному к работе с ними.
Установка предохранителей а также электрических ламп должна выполняться электромонтером применяющим средства индивидуальной защиты.
Монтажные и ремонтные работы на электрических сетях и электроустановках должны производиться после полного снятия с них напряжения и при осуществлении мероприятий по обеспечению безопасного выполнения работ.
При хранении проверке выдаче для работы и эксплуатации ручных электрических машин понижающих трансформаторов преобразователей частоты и переносных электрических светильников должны соблюдаться Правила техники безопасности при эксплуатации электроустановок потребителей.
При ведении работ вне помещений во всех случаях а в помещениях - в условиях повышенной опасности поражения работающих электрическим током необходимо применять ручные электрические машины II и III классов по ГОСТ 12.2.007.0-75. При работе с электрическими машинами II класса необходимо применять средства индивидуальной защиты.
При наличии особо опасных условий поражения работающих электрическим током следует пользоваться только электрическими машинами класса III по ГОСТ 12.2.007.0-75 с применением диэлектрических перчаток галош и ковриков.
В электроустановках напряжением до 1000 В с глухозаземленной нейтралью или глухозаземленным выводом источника однофазного тока заземление корпусов приемников электрической энергии (электротехнических изделий) без их зануления не допускается.
Токоведущие части электроустановок должны быть изолированы ограждены или размещены в местах не доступных для прикосновения к ним.
Наружные электропроводки временного электроснабжения должны быть выполнены изолированным проводом размещены на опорах на высоте над уровнем земли пола настила не менее 25 м. - над рабочими местами; 35 м. - над проходами; 60 м. - над проездами.
Монтаж и эксплуатация электропроводок и электротехнических изделий должны исключать возможность тепловых проявлений электрического тока которые могут привести к загоранию изоляции или рядом находящихся горючих материалов.
Светильники общего освещения присоединенные к источнику питания (электросети) напряжением 127 и 220 В должны устанавливаться на высоте не менее 25 м от уровня земли пола настила. При высоте подвеса менее 25 м светильники должны подсоединяться к сети напряжением не выше 42 В.
При работах в особо опасных условиях должны применяться переносные светильники напряжением не выше 12 В.
В качестве источника питания напряжением до 42 В следует применять понижающие трансформаторы машинные преобразователи генераторы аккумуляторные батареи. Не допускается применять для указанных целей автотрансформаторы.
Электросварочные устройства должны удовлетворять требованиям ГОСТ 12.2.003—74 и ГОСТ 12.2.007.8—75.Электросварочные работы должны проводиться в соответствии с требованиями ГОСТ 12.3.003—75.
3 Определение параметров микроклимата в рабочей зоне помещения
Параметры микроклимата определялись на одном из участков Оренбургского локомотиворемонтного завода.
Температура измеряется ртутным термометром и составляет 25 ºС.
Влажность определяется по психрометрическим таблицам в соответствии с показателями сухого и влажного термометра психрометра Ассмана.
где - абсолютная влажность мм.рт.ст.
мм.рт.ст. - максимальная влажность;
где =163 мм.рт.ст. - парциальное давление водяных паров при температуре влажного термометра;
=25 ºС - показание сухого термометра;
=19 ºС - показание влажного термометра;
=740 мм.рт.ст. - барометрическое давление;
Для расчёта скорости движения воздуха и определения воздухообмена примем производительность вентиляторов м3ч.
Воздухообмен в помещении
где = 11 - число работающих на одном участке;
= 40 м3ч - расход воздуха на одного работающего;
Кратность воздухообмена - показывает во сколько раз в течении часа полностью меняется воздух в помещении
где =8864 м.3 –объём помещения;
Так как > значит воздухообмен на участке соответствует требованиям.
Таким образом в рабочей зоне помещения параметры микроклимата оптимальны.
4 Пожарная безопасность
Система обеспечения пожарной безопасности – совокупность сил и средств а так же мер правового организационного экономического социального и научно- технического характера направленных на борьбу с пожарами.
Организационные мероприятия по обеспечении пожарной безопасности:
а) во всех производственных административных складских и вспомогательных помещениях на видных местах должны быть вывешены таблички с указанием номера телефона вызова пожарной охраны;
б) правила применения на территории предприятий открытого огня проезда транспорта допустимость курения и проведения временных пожароопасных работ устанавливаются общеобъектовыми инструкциями о мерах пожарной безопасности;
в) на каждом предприятии приказом должен быть установлен соответствующий их пожарной опасности противопожарный режим в том числе:
) определены и оборудованы места для курения;
) определены места и допустимое количество единовременно находящихся в помещениях сырья полуфабрикатов и готовой продукции;
) установлен порядок уборки горючих отходов и пыли хранение промаслённой одежды;
) определен порядок обесточивания электрооборудования в случае пожара и по окончании рабочего дня;
) регламентированы: порядок проведения временных огневых и других пожароопасных работ; порядок осмотра и закрытия помещений после окончания работы; действия работников при обнаружении пожара;
) определен порядок и сроки прохождения противопожарного инструктажа и занятий по пожарно-техническому минимуму а также назначены ответственные за их проведение;
г) в зданиях и сооружениях при единовременном нахождении на этаже более10 человек должны быть разработаны и на видных местах вывешены планы эвакуации людей в случае пожара а также предусмотрена система оповещения людей о пожаре.
Руководитель объекта с массовым пребыванием людей (более 50 человек) в дополнение к схематическому плану эвакуации людей при пожаре обязан разработать инструкцию определяющую действия персонала по обеспечению безопасной и быстрой эвакуации людей по которой не реже одного раза в полугодие должны проводиться практические тренировки всех задействованных для эксплуатации работников;
д) работники предприятия а также граждане обязаны:
) соблюдать на производстве и в быту требования пожарной безопасности стандартов норм и правил утвержденных в установленном порядке а также соблюдать и поддерживать противопожарный режим;
) выполнять меры предосторожности при пользовании газовыми приборами предметами бытовой химии проведении работ с легковоспламеняющимися и горючими жидкостями другими опасными в пожарном отношении веществами материалами и оборудованием;
) граждане обязаны предоставлять в порядке установленном законодательством РФ возможность государственным инспекторам по пожарному надзору проводить обследования и проверки принадлежащих им производственных хозяйственных жилых и иных помещений и строений в целях контроля за соблюдением пожарной безопасности.
е) лица которым поручено проведение мероприятий с массовым участием людей обязаны перед их началом тщательно осмотреть помещения и убедиться в полной готовности их проведения первоочередных аварийно-спасательных работ на этих предприятиях.
ж) руководители предприятий на которых применяются перерабатываются и хранятся опасные сильнодействующие ядовитые вещества обязаны сообщать подразделениям пожарной охраны о них данные необходимые для обеспечения безопасности личного состава привлекаемого для тушения пожара и проведения первоочередных аварийно-спасательных работ на этих предприятиях.
Для помещений хранения транспорта в количестве более 25 единиц должен быть разработан план расстановки транспортных средств с описанием очередности и порядка их эвакуации в случае пожара.
Помещения для стоянки и площадки открытого хранения транспортных средств (кроме индивидуального) должны быть оснащены буксирными тросами и штангами из расчета один трос (штанга) на 10 единиц техники.
В помещениях под навесами и на открытых площадках хранения транспорта запрещается:
- устанавливать транспортные средства в количестве превышающем
норму нарушать план их расстановки уменьшать расстояние между автомобилями;
- загромождать выездные ворота и проезды
- производить кузнечные термические сварочные малярные и деревообделочные работы а также промывку деталей с использованием
- держать транспортные средства с открытыми горловинами топливных баков а также при наличии течи горючего и масла;
- заправлять транспортные средства горючим и сливать из них топливо;
хранить тару из-под горючего а также горючее и масла (кроме гаражей
индивидуального транспорта);
- подзаряжать аккумуляторы непосредственно на транспортных средствах;
- подогревать двигатели открытым огнем (костры факелы паяльные лампы) пользоваться открытыми источниками огня для освещения;
- устанавливать на общих стоянках транспортные средства для перевозки ЛВЖ и ГЖ а также ГГ.
В гаражах индивидуального пользования не разрешается хранить мебель предметы домашнего обихода из горючих материалов и т.п.
5 Возможные чрезвычайные ситуации
Чрезвычайная ситуация – это обстановка на определённой территории сложившаяся в результате аварии опасного природного явления катастрофы стихийного или иного бедствия которые могут повлечь или повлекли за собой человеческие жертвы ущерб здоровью людей или окружающей природной среде значительные материальные потери и нарушения условий жизнедеятельности людей.
На участке возможно возникновение следующих чрезвычайных ситуаций: пожар поражение электрическим током и др.
Наиболее опасной и вероятной чрезвычайной ситуацией является пожар. На случай возникновения пожара должна быть обеспечена возможность безопасной эвакуации в первую очередь людей; во вторую очередь материальных ценностей. Необходимое время эвакуации рабочих определённое нормативом составляет 015 минут.
Для одновременного обнаружения пожара помещение оборудовано автоматической пожарной сигнализацией. Также на моечном участке имеются средства первичной защиты такие как: огнетушители песок в ёмкости лопаты багры топор.
При начале значительного пожара необходимо вызвать пожарную службу по телефону 01 затем сообщить директору и до приезда пожарных приступить к эвакуации ценного имущества и тушению пожара собственными силами.
Заключение.doc
Проведенный технологический расчет на основе данных предприятия определил объективно необходимые показатели деятельности предприятия: трудоемкость выполнения работ численность производственных рабочих необходимое количество оборудования для ремонта а также площади производственных помещений зон и участков.
Проектом были предложены мероприятия направленные на сокращение непроизводительного потребления энергозатрат в частности предложено введение нового технологического прцесса реконструкция моторного цеха с разделением на дополнительные участки.
Проведенный экономический расчет определил зфективность предложенной технологии объем дополнительных капитальных вложений эксплуатационные затраты по разрабатываемому проекту был проведен расчет общего экономического эффекта от проводимых мероприятий по технологическому перевооружению и срок окупаемости дополнительных капитальных вложений.
Был проведен анализ вредных факторов и намечены мероприятия по охране труда и окружающей среды.
Список использованных источников
Напольский Г.М. Технологическое проектирование автотранспортных предприятий и станций технического обслуживания. - М.: Транспорт 1985.-231 с.
Безуглов Ю. И. Ныров Г. К. Методическое пособие по дипломному проектированию. - Оренбург.: ОГУ 1995. - 87 с.
Табель технологического оборудования и специализированного инструмента для АТП АТО и БЦТО. - М.: Транспорт 1983. - 98 с.
Суханов Б. Н. Борзых И. О. Бедорев Ю. Ф. Техническое обслуживание и ремонт автомобилей: Пособие по курсовому и дипломному проектированию. - М.: Транспорт 1985. - 224 с.
Типовые проекты рабочих мест на автотранспортном предприятии. - М.: Транспорт 1977. - 197 с.
Бабушкин А. К. Дипломное проектирование по технической эксплуатации автомобилей: Учебное пособие. - Оренбург.: 1983. - 156 с.
Решетов Д. Н. Детали машин. - М.: Машиностроение 1989. - 496 с.
Левицкий В. С. Машиностроительное черчение. - М.: Высшая школа 1988. - 351 с.
Салов А. И. Охрана труда на предприятиях автомобильного транспорта. - М.: Транспорт 1985. - 351 с.
Кнорринг Г. М. Проектирование осветительных установок. - М.: Высшая школа 1958. - 283 с
Анурьев. В. И. Справочник конструктора-машиностроителя. В 3-х т. - М.: Машиностроение 1980. - 728 с
Наскова Л. В. Методические указания по составлению раздела « Охрана окружающей среды» в дипломных проектах студентов автотранспортного факультета. - Оренбург: ОрПтИ1986. - 22 с.
Василенко В. А. Охрана труда: Методические указания по выполнению раздела в дипломных проектах для студентов всех специальностей дневного и вечернего отделений. - Оренбург.: ОрПтИ 1986. - 49 с.
Бабин М. Б Котов В. Ф. Методические указания к курсовой работе по организации и планированию производства. - Оренбург.: ОГУ 1987. - 49 с.
Стрельникова Л. М. Методические указания к технико-экономическому обоснованию конструкторской разработки. - Оренбург.: ОрПтИ 1992. - 10 с.
Буцко В. А. Цыцура А. А. Греков И. И. Зинюхин Г. Б. Основы экологических знаний: Учебное пособие. – Оренбург.: ОГУ 1998. – 99 с.
Павлова Е.И. Буравлев Ю.В. Экология транспорта. - М.: Транспорт 1998. - 230 с.
Чекмарёва О.В. Оценка и управление пылегазовыми выбросами от автомобильного транспорта в атмосферу промышленного города. Дисс канд. техн. наук. – Оренбург 2002. – 155 с.
Козлов Ю.С. Меньшова В.П. Святкин И.А. Экологическая безопасность автомобильного транспорта. - М.: Изд-во «Агар» 2000. - 173 с.
Сарбаев В.И. Селиванов С.С. Коноплев В.Н. Демин Ю.Н. Техническое обслуживание и ремонт автомобилей: механизация и экологическая безопасность производственных процессов Серия «Учебники учебные пособия». – Ростов нД: «Феникс» 2004. – 448 с.
Чекмарёва О.В. Бондаренко Е.В. Оценка роли автодорожного комплекса в формировании атмосферного воздуха: Методические указания к практическим занятиям. – Оренбург: ГОУ ОГУ 2004. – 43 с.
4_Раздел.doc
1. Структура авторемонтного предприятия и характеристика его подразделений
Основное и вспомогательное производства могут быть построены по бесцеховой или цеховой структуре. При бесцеховой структуре отдельные участки возглавляет мастер подчиненный непосредственно заводоуправлению. Бесцеховая структура рекомендуется для предприятий с числом рабочих до 500 чел. При цеховой структуре отдельные производственные участки объединяются в цеха возглавляемые начальниками цехов. Число рабочих в цехе обычно составляет 100 125 чел. Производственное деление предприятия на цехи и участки зависит от мощности предприятия характера и степени специализации производства.
Организационная структура предприятия включает руководство (директор главный инженер заместители директора) подразделения управления производством (производственно диспетчерский отдел) службы и подразделения главного инженера (главного конструктора главного технолога главного механика и энергетика отдел механизации и автоматизации производственных процессов заводская лаборатория) подразделения обеспечения производства (бухгалтерия планово-экономический отдел ОТК отдел труда и зарплаты отдел кадров подразделения снабжения и сбыта транспортный отдел и др.)производственные подразделения (основные производственные цехи или участки службы вспомогательного производства и склады).
К основным производственным подразделениям АРЗ относятся следующие цехи и участки.
Разборочный цех включает: разборочно-моечный участок на котором производятся подразборка и разборка предварительная и окончательная мойка и очистка деталей; контрольно-сортировочный участок где дефектуют и сортируют детали на группы годных подлежащих восстановлению и негодных а также назначают маршруты их восстановления; склад деталей ожидающих ремонта для учета и хранения подлежащих восстановлению деталей и для комплектования партий деталей по маршрутам их восстановления.
Сборочный цех состоит из участков: комплектовочного и слесарно-подгоночного на которых осуществляются номенклатурный подбор деталей для сборочных групп комплектование пар деталей для групповой сборки и слесарно-подгоночные работы; агрегатно-сборочного на котором собирают испытывают и окрашивают все агрегаты за исключением двигателя; отделения двигателей предназначенного для сборки испытания и окраски двигателей; рамного где разбирают переклепывают и окрашивают рамы; сборки автомобилей где собирают автомобили и агрегаты; регулировочного на котором автомобили испытывают на стенде или пробегом и устраняют обнаруженные неисправности; медницко-радиаторного где восстанавливают радиаторы топливные баки и различного рода трубопроводы; шиномонтажного и шиноремонтного для ремонта колес покрышек и камер балансировки и окраски колес; по ремонту электрооборудования где проводятся работы по ремонту электроагрегатов приборов и электропроводки; приборов питания на котором ремонтируют топливные насосы карбюраторы форсунки; аккумуляторного – для ремонта и зарядки аккумуляторных батарей.
Кузовной цех влючает участки: деревообделочный где сушится и обрабатывается древесина для деревянных платформ; по ремонту деревянных кузовов; по ремонту металлических платформ и кузова; жестяницко-арматурный где восстанавливают крылья двери и арматуру кабины брызговики с применением сварочных работ и полимеров производится подготовка к окраске; малярный где окрашивают кабины детали кузова и узлы; обойный служащий для ремонта подушек и спинок сидений и обивки кабины автомобиля.
Цех восстановления и изготовления деталей включает участки: кузнечно-рессорный где ремонтируют упругие элементы подвесок с устранением остаточных деформаций восстанавливают детали других узлов методом пластического деформирования; сварочных на котором применяют различные виды сварки; гальванический предназначенный для размерного износостойкого и декоративного покрытия деталей; для восстановления деталей напылением расплавленного металла; для восстановления деталей синтетическим материалом; термический для термической и химико-термической обработки; слесарно-механический служащий для восстановления деталей механической и слесарной обработкой.
Участки вспомогательного производства: инструментальный на котором изготавливают и ремонтируют средства технологической оснастки и инструмента затачивают режущий инструмент хранят и выдают приспособления и инструмент; ремонтно-механический отдел главного механика предназначенный для обслуживания и ремонта технологического оборудования и санитарно-технических установок а также для изготовления нестандартного оборудования; электроремонтный на котором обеспечивают ремонт электродвигателей и электрических установок ремонт и обслуживание компрессорных систем уход за осветительной сетью; ремонтно-строительный где выполняют работы по обслуживанию изданий сооружений и подъездных путей. Общезаводские склады служат для приемки переработки хранения и выдачи различных материалов и полуфабрикатов. К общезаводским складам относят склады материалов и химикатов металла запасных частей лесоматериалов ремонтного фонда готовой продукции топлива смазки и утиля.
2 Основы организации производственного процесса
Производственный процесс капитального ремонта автомобилей и их составных частей организуется на основе следующих научных принципов: прямоточности пропорциональности ритмичности параллельности непрерывности и кратности. По пропорциональности непрерывности и кратности оценивается уровень организации средств и предметов труда а по прямоточности ритмичности и параллельности — движение предметов труда в производстве.
Принцип прямоточности производственного процесса определяет кратчайший путь движения предметов труда от поступления ремонтного фонда до выпуска готовой продукции. Соблюдение принципа прямоточности в сочетании со специализацией и друга-ми принципами создает благоприятные условия для комплексной механизации и автоматизации производственных процессов.
Принцип пропорциональности заключается в том что число рабочих на каждом участке (рабочем месте) должно быть пропорционально трудоемкости выполняемых на нем операций. Повышение степени пропорциональности процесса является условием увеличения производственной мощности предприятия улучшения использования производственных фондов повышения рентабельности за счет снижения себестоимости и фондоёмкости продукции.
Ритмичность выпуска продукции или выполнения технологических процессов является одним из важнейших принципов организации ремонтного производства. Опыт показывает что основными причинами нарушения ритмичности являются неодинаковая пропускная способность различных участков производства внеплановые простои оборудования несвоевременное материально-техническое обеспечение и т. д.
Принцип параллельности означает параллельное осуществление отдельных частей производственного процесса. Параллельность выполнения основных вспомогательных и обслуживающих операций сокращает длительность производственного цикла а следовательно и время нахождения автомобиля в ремонте.
Непрерывность процесса ремонта характеризуется выполнением последовательных технологических операций без разрыва во времени. Степень непрерывности выполнения отдельных операций зависит от уровня специализации рабочих мест. С уменьшением числа выполняемых операций на одном рабочем месте перерывы в работе связанные с переналадкой оборудования сокращаются – степень непрерывности снижается. Причинами прерывности процесса могут быть непропорциональность производственного процесса (периодическое скопление предметов труда в одних местах и недостаток в других); случайные потери рабочего времени на отдельных рабочих местах и др.
Кратность и равновеликость распределения трудоемкости работ по постам является одной из предпосылок организации поточного производства.
Каждый тип предприятия каждая марка автомобиля имеют свою детальную конкретную схему технологического процесса КР но обязательно учитывающую основные принципы его организации. Отступление от этих принципов снижает эффективность производственного процесса.
Организация рабочего места оказывает весьма существенное влияние на экономику производства. Правильная организация рабочего места предполагает четкое определение объема и характера выполняемых на нем работ необходимое оснащение рациональную планировку благоприятные и безопасные условия труда. На каждое рабочее место составляют паспорт в котором указывают содержание выполняемой работы годовое задание в человеко-часах режим и условия работы планировку оснащение и порядок обслуживания данного рабочего места.
Рабочее место оснащают по утвержденной технической документации. Оно включает организационную и технологическую оснастку. К организационной оснастке относятся устройства для хранения и размещения при работе инструмента приспособлений чертежно-технической документации и предметов по уходу за рабочим местом (верстаки инструментальные шкафы штативы); устройства для временного размещения на рабочем месте заготовок деталей узлов и агрегатов (стеллажи подставки специальная тара); устройства для обеспечения необходимой удобной рабочей позы и безопасных условий труда (подъемно-поворотные стулья решетки под ноги упоры для ног защитные экраны и очки местные вентиляционные устройства); устройства для транспортирования деталей и заготовок и др.
Количество и номенклатура оргоснастки должны обеспечить непрерывность работы ее высокую производительность и удобство. Качество и номенклатура технологической оснастки на рабочем месте определяются принятым технологическим процессом. Технологическое оснащение включает оборудование и оснастку измерительный режущий монтажный и вспомогательный инструмент а также техническую документацию. С целью совершенствования организации рабочих мест на основе анализа условий
3 Организация технического контроля на предприятии
Качество отремонтированной продукции оценивают по ее соответствию требованиям технических условий стандартов и других документов. Для контроля качества продукции на предприятиях создают службы технического контроля. Основная задача службы заключается в предотвращении выпуска недоброкачественной продукции.
В задачи службы технического контроля на этапе производства также входят:
- входной контроль качества поступающих на предприятие сырья материалов полуфабрикатов и комплектующих изделий;
- операционный контроль во время выполнения или после завершения определенных технологических операций; приемочный контроль с целью принятия решения о пригодности продукции к поставкам и использованию (ГОСТ 16504-81);
- эксплуатационный контроль с целью проверки правильности проведения периода обкатки агрегатов и автомобиля в условиях эксплуатации соблюдения периодичности и объема технического обслуживания сбора и анализа информации о надежности продукции ремонтного предприятия.
По охвату контролируемой продукции различают:
- сплошной контроль всех единиц продукции в партии;
- выборочный контроль который характеризуется проверкой одной или нескольких единиц из определенной партии или потока продукции. - По месту проверки различают:
- стационарный контроль – выполняется на специально оборудованном в цехе (участке) контрольном посту;
- скользящий контроль – выполняется на рабочем месте куда доставляют необходимые средства контроля и прибывает контролер.
Посты ОТК планируют размещают и оснащают с учетом их назначения характера выполняемых контрольных операций. Посты контроля специализируются по предметному признаку (пост контроля коленчатых валов пост контроля корпусных деталей и т. п.).
Планирование контроля в АРП включает: определение объемов и составление планов контроля оценку качества продукции по результатам контроля.
Приемо-сдаточным испытаниям и приемочному контролю подвергается 100 % отремонтированных автомобилей. Приемо-сдаточные испытания целесообразно проводить на обкаточно-тормозных стендах. Представитель ОТК завода в паспорте обкатанного и принятого автомобиля делает отметку о его пригодности к эксплуатации.
Важным этапом в организации ОТК является подбор кадров при котором должен действовать принцип: превосходство знания контролирующего над знаниями контролируемого. Работник ОТК должен хорошо знать технологический процесс уметь не только обнаружить дефекты продукции но и установить причину их появления а также участвовать в разработках мероприятий по повышению качества выпуска изделий.
4 Анализ способов электромагнитной наплавки и устройства реализующие их
В последние годы все более широкие исследования проводятся по изысканию и внедрению новых физических и электрофизических способов воздействия на жидкий металл непосредственно в процессе наплавки которые направлены на исключение из технологических процессов многочисленных конструкционных недостатков. Одним из методов электрофизического воздействия является электромагнитная наплавка обеспечивающая нанесение термообработку упрочнение формируемого покрытия в электромагнитном поле. При этом формируются необходимые размеры обрабатываемой детали физико-механические и эксплуатационные свойства поверхности изделий. Процесс ЭМН обеспечивает формирование тонких слоев защитных покрытий толщиной 01 06 мм на сторону а также высокую прочность соединения наплавленного покрытия с основой при минимальном тепловыделении и расплавлении материала основы. С учетом выше рассмотренных достоинств ЭМН очевидно что метод находит наибольшее применение при восстановлении посадочных мест валов осей и других тел вращения (диаметром от 20 мм и более) под подшипники качения и скольжения зубчатые колеса шкивы шестерни звездочки и другие детали сельскохозяйственного и автодорожного производства.
Следует отметить что в настоящее время широко известно большое количество устройств и схем реализующих процесс ЭМН при восстановлении и упрочнении деталей машин. Ниже рассматриваются способы устройства и схемы реализующие процесс ЭМН.
На рисунке 4.2 приведены принципиальные схемы ЭМН отражающие сущность технологии упрочнения и восстановления наружных поверхностей деталей в комбинированном физическом поле. Обрабатываемая деталь 1 устанавливается на определенном расстоянии (зазор D=20 30 мм) от полюсного наконечника 4 электромагнита 5. В зазор между полюсным наконечником и обрабатываемой поверхностью детали подают ферромагнитный порошок из бункера-дозатора 3 в потоке рабочей жидкости. На полюсный наконечник и обрабатываемую деталь подается разность потенциалов от источника электрического тока. Зерна ферромагнитного порошка выстраиваются вдоль магнитных силовых линий в цепочку 2 и замыкают электрическую цепь между заготовкой и наконечником. При этом в рабочей зоне “обрабатываемая поверхность детали – полюсный наконечник” в результате возникновения электрического разряда происходит расплавление зерен ферромагнитного порошка импульсами разрядов полярный перенос и распределение по подплавленной поверхности заготовки в постоянном магнитом поле.
Конструкции устройств реализующих процесс ЭМН очень просты и могут быть выполнены по однополюсной и двухполюсной схемам (рисунок 4.1 б и в) 7. При двухполюсной схеме обеспечивается более высокая производительность ЭМН а при однополюсной – сплошность наносимого покрытия 7. Стабильность процесса ЭМН и прочность покрытия повышается если подачу порошка осуществлять в потоке рабочей жидкости 8. При этом рабочая жидкость должна удовлетворять требованиям: низкой коррозионной активности к материалам порошков и обрабатываемой заготовки; высокой температуре вспышки; хорошей фильтруемости; отсутствию запаха и низкой токсичности. В качестве СОЖ широко используются водные растворы эмульсолов Э-2 “Аквол” различной концентрации 9. Повышение стабильности и равномерности процесса получено в результате использования в рабочей жидкости солей калия кальция натрия 7. В процессе эксплуатации рабочая жидкость засоряется ферромагнитным порошком и продуктами разрушения. Очистку СОЖ осуществляют с помощью фильтров и постоянных магнитов.
Значительное повышение стабильности протекания процесса наплавки обеспечивается применением устройства для ЭМН в пульсирующем магнитном поле с вибрацией полюсного наконечника 4 (рисунок 4.1 в). При этом обеспечивается синхронизация изменения магнитного потока в рабочем зазоре с вибрацией полюсного наконечника. Использование этой принципиальной схемы исключает возможность возникновения короткого замыкания в цепи разрядного тока.
а–однополюсная с вибрацией полюсного наконечника; б – однополюсная; в – двухполюсная
– заготовка 2 – ферромагнитный порошок; 3 – бункер-дозатор; 4 – полюсный наконечник; 5 – сердечник электромагнита; 6 – электромагнитная катушка; 7 – источник питания электромагнитной катушки; 8 – источник разрядного тока; 9 – пластинчатая пружина; 10 – скользящий контакт
Рисунок 4.1 - Принципиальные схемы электромагнитной наплавки наружных поверхностей тел вращения
Для увеличения геометрических параметров и повышения физико-механических свойств упрочненных и восстановленных поверхностей деталей машин перспективно применять комбинированный метод ЭМН с поверхностным пластическим деформированием (ППД). Совмещение наплавки и поверхностного пластического деформирования обеспечивает получение сжимающих остаточных напряжений повышающих усталостную прочность восстановленных изделий. Комбинированный метод ЭМН с ППД осуществляется по различным схемам с использованием одного двух или трех исходных устройств 7 9 (рисунок 4.2 а).
Авторами работы 4 5 рекомендуется для формирования упрочненного слоя обрабатываемой поверхности детали комбинированный метод ЭМН с дополнительным термическим воздействием угольным электродом 14 (Рисунок 4.2 в) установленным между наконечником электромагнита и калибрующим роликом 10. Для получения необходимых параметров толщины наплавляемого слоя сплошности и шероховатости покрытия авторами 5 6 предложено совмещать ЭМН одновременно со шлифованием нанесенного покрытия абразивным кругом 11 (рисунок 4.2 б).
а – с поверхностным пластическим деформированием накатным устройством 10; б – с обработкой абразивным кругом 10; в – с термическим воздействием угольным электродом и механическим воздействием калибрующим роликом 10
– заготовка; 2 – ферромагнитный порошок; 3 – бункер-дозатор; 4 – полюсный наконечник; 5 – сердечник электромагнита; 6 – электромагнитная катушка; 7 – источник питания электромагнитной катушки; 8 – источник разрядного тока; 9 – скользящий контакт; 11 – угольный электрод
Рисунок 4.2 - Принципиальные схемы комбинированных методов электромагнитной наплавки
5 Особенности магнитных систем устройств электромагнитной наплавки
Известно 11 что энергия магнитного поля необходима для удержания ферропорошка и формирования цепочек-электродов в рабочем зазоре. В качестве источника магнитного поля в рабочей зоне при ЭМН применяется электрический магнит состоящий из ферромагнитного сердечника (прямоугольного или круглого сечения) сменного полюсного наконечника и намагничивающей катушки. Электромагнитные катушки дают возможность получать различные по величине параметры магнитной индукции путем изменения тока питающего намагничивающие катушки 7 9. При этом напряжение питающего тока в обмотках катушки электромагнита изменялось в пределах 34 40 В.
В установке для ЭМН 14 16 вибрацию полюсного наконечника и переменное магнитное поле создают электромагнитной катушкой питаемой выпрямленным током по однополупериодной схеме. В устройстве электромагнит выполнен в виде диска с зубцами снабженным обмотками 16. Такая конструкция электромагнита позволяет удерживать магнитным полем возле зубцов ферропорошок и при попадании его в рабочий зазор наплавлять на внутреннюю поверхность изделия. Известно устройство магнитной системы 7 в которой сердечник электромагнита имеет выступы а магнитопровод состоит из двух П-образных частей. Намагничивающая катушка подключается к источнику импульсного электрического тока. Под воздействием магнитных сил полюсный наконечник с сердечником совершают поступательное движение к детали и возврат их в исходное положение в момент паузы тока в катушке электромагнита.
Рабочий орган установки для наплавки в электромагнитном поле 18 содержащий цилиндрический сердечник кинематически связан со съемным полюсным наконечником и размещен в электромагнитной катушке. Имеет возможность осциллирования (возвратно-поступательное движение) посредством связи с приводом перемещения через рычаг. В работе 19 в качестве источника магнитного поля применяют комбинированную электромагнитную систему в которой электромагниты имеют полюсные наконечники выполненные из постоянных магнитов.
В качестве источника постоянного магнитного поля в рабочей зоне при магнитно-абразивной обработке (МАО) применяют магнитные системы съемных индукторов состоящие из двух одинаковых блоков постоянных магнитов (рисунок 4.3) расположенных друг над другом 13. Эти блоки имеют возможность относительного смещения что позволяет управлять величиной магнитной индукцией в рабочей зоне.
а – с механизмом осцилляции
– корпус; 2 – механизм осцилляции; 3 – осциллирующая головка; 4 – механизм выключения индуктора; 5 – изделие; 6 – постоянные магниты; 7 – подвижный и неподвижный блоки магнитов;
б – без механизма осцилляции
– верхний подвижный блок магнитов; 2 – механизм поворота верхнего блока включения индуктора; 3 – постоянные магниты; 4 – нижний блок магнитов
Рисунок 4.3 – Конструкции съемных магнитных индукторов магнитно-абразивной обработки
Таким образом проведенный анализ схем и устройств магнитных систем показал что электрические магниты надежны в работе имеют высокие эксплуатационные и технические характеристики дают возможность получать различные по величине параметры магнитной индукции. Но вместе с тем у них увеличенные размеры по сравнению с индукторами на постоянных магнитах а также существует необходимость в электропитании. При этом максимальная электрическая мощность расходуемая для создания управляющих магнитных полей находится в пределах 5 10% мощности затрачиваемой в наплавочной (сварочной) цепи.
Сравнительные характеристики электрических магнитов и индукторов на постоянных магнитах даны в таблице 4.1.
Таблица 4.1 – Сравнительные характеристики магнитных систем
Магнитная система с использованием электромагнитной катушки
Магнитная система с использованием постоянных магнитов
Питание электрическим током
Питание электрическим током Требуются электро-контактные устройства источник питания пульт управления и электроизмерительная аппаратура Не требуется
Достижимые значения магнитной индукции в рабочем зазоре Тл
Возможность управления магнитной индукцией в рабочем зазоре
Бесступенчатое регулирование при помощи изменения электрического тока в намагничивающих катушках
Бесступенчатое регулирование при помощи частичного шунтирования или нейтрализации магнитного потока
Возможность выключения магнитного поля в рабочей зоне
Осуществляется выключением питания намагничивающих катушек
Осуществляется методами шунтирования или нейтрализации магнитного потока
Производя анализ метода ЭМН с целью использования альтернативного следует в первую очередь отказаться от схемы с электромагнитами. Несмотря на их эффективность на первый план выступают ограничивающие факторы и в данном случае ими являются сложность конструкции и габариты электромагнитов поэтому следует учитывать что конкретный способ упрочнения и восстановления поверхности детали характеризуется специфическими особенностями и требованиями которые предъявляются к оборудованию. К ним относят: высокие качество и производительность технологического процесса; надежность работы и эргономические показатели оборудования; рациональное расходование материалов и электроэнергии; минимальные затраты на изготовление и техническое обслуживание оснастки и оборудования.
Так определенная номенклатура заготовок и деталей подвергнутых упрочнению и восстановлению с использованием электромагнитной наплавки а также различие их геометрических размеров массы и физико-механических свойств материалов существенно влияют на выбор технологических процессов ЭМН конструкцию установок их производительность. В свою очередь качество формируемых покрытий и производительность процесса зависят от технических характеристик используемого оборудования источников энергии и конструкции рабочих органов установок ЭМН и необходимой вспомогательной оснастки.
Опыт использования магнитных систем показывает что используемые в установках ЭМН электрические магниты не в полной мере удовлетворяют требованиям по обеспечению необходимого качества покрытий (сплошность пористость равномерность нанесенного покрытия по толщине и др.) стабильности и устойчивости процесса 20. Это обусловлено прежде всего тем что используются электромагнитные катушки на выпрямленном или переменном токе которые позволяют получать периодически изменяющуюся во времени величину магнитной индукции
где – мгновенная и максимальная величина магнитной индукции в рабочем зазоре Тл;
– круговая частота Гц;
Одновременно в рабочей зоне присутствует градиент магнитной индукции который определяется неравномерностью распределения магнитного потока а суммарная сила действующая на зерна порошка со стороны более удаленных зерен определяется зависимостью
где n – число зерен в цепочке;
– расстояние от границы
– размеры большой и малой осей эллипсоида м;
– магнитная проницаемость порошкового материала Гнм;
– магнитная восприимчивость материала ферропорошка Гнм;
– напряженность магнитного поля у верхней границы зерна Ам;
– величина рабочего зазора м.
Анализ динамики изменения параметров зависимости (4.2) при их взаимодействии показывает что величина магнитной индукции оказывает влияние на интенсивность образования цепочек из зерен ферропорошка и электрическую проводимость. Переменный характер магнитной индукции на границах участков с различным сопротивлением способствует хаотичному распределению ферропорошка в рабочем зазоре. В результате – градиент магнитной индукции на отдельных участках рабочего зазора меняется с частотой образования разрядных цепочек из зерен ферропорошка. При таких условиях магнитная сила удерживающая цепочки-микроэлектроды в рабочей зоне не будет одинаковой для всех зерен. Таким образом изменение величины магнитной индукции во времени способствует формированию недостаточно качественного покрытия – неравномерного по толщине и с высокой шероховатостью поверхности 21.
6 Пути совершенствования систем ЭМН
Одним из приоритетных направлений устранения указанных выше недостатков и повышения эффективности процесса упрочнения и восстановления поверхностей деталей в электромагнитном поле является применение постоянных магнитов. Использование постоянного магнитного поля в рабочем зазоре позволяет отказаться от дополнительного источника питания упростить конструкцию установки ЭМН уменьшить габаритные размеры и массу снизить трудоемкость его изготовления и обслуживания.
Известно 11 что в процессе работы магнитная система установки испытывает воздействие целого ряда возмущающих факторов: тепловое излучение дуги магнитное поле сварочного тока воздействие высоких температур изменение магнитного сопротивления цепи арматуры устройства и др. Причем для обеспечения устойчивой и стабильной наплавки необходимо однородное и постоянное во времени магнитное поле в рабочей зоне с индукцией в пределах 06 09 Тл. Поэтому к используемым материалам для постоянных магнитов предъявляются требования:
- стабильность магнитных свойств в широкой области температур;
- большая величина остаточной индукции;
- высокая механическая прочность;
- коррозионная стойкость;
- низкая цена по сравнению с другими магнитотвердыми материалами.
Вследствие того что ферриты и гибкие магниты не обладают требуемой остаточной индукцией (Вr) и максимальной удельной магнитной энергией а редкоземельные магниты на основе сплавов Nd-Fe-B и Sm-Co не приемлемы из-за большой стоимости то наиболее полно отвечают этим требованиям магнитные материалы на основе сплава Al-Ni-Co-Fe (ЮНДК). Эти магниты обладают высокой стабильностью параметров магнитного поля достаточной магнитной индукцией до 12 Тл коэрцитивной силой Hc до 140 кАм удельной магнитной энергией до 165 кДжм3 и обеспечивают формирование плотной и эластичной щетки из ферропорошка в рабочем зазоре. При этом магниты из сплава ЮНДК в 3–10 раз дешевле редкоземельных материалов 22. Сравнительные характеристики материалов для постоянных магнитов представлены в таблице4.2
Таблица 4.2 - Сравнительные характеристики материалов для магнитов
Цена за 1 кг материала
Гибкие магнитные материалы (магнитопласты)
При проектировании оптимальной конструкции магнитной системы установки ЭМН ставились две основные задачи:
- получить требуемую величину магнитной индукции в рабочем зазоре;
- определить размеры магнитной системы при использовании постоянных магнитов.
При расчете магнитных систем со стационарным полем учитывалось влияние магнитной арматуры выполненной из магнитомягкого материала и постоянных магнитов. Магнитотвердые материалы выступают в качестве первичных элементов формирующих магнитный поток а магнитная арматура – вторичных. Конструктивно магнитные системы могут быть выполнены с замкнутым и разомкнутым магнитопроводом. Из теории электромагнетизма известно 23 24 что наименьшие магнитные потери обеспечиваются замкнутой магнитной системой прототипом которой является тороидальный соленоид. Однако для таких систем требуется питание электрическим током который должен быть стабилизирован. Поэтому конструктивно а также в эксплуатации эти системы сложны так как требуют использования стабилизатора тока и охлаждения обмоток 19. В настоящее время применяемые при ЭМН электромагнитные системы содержат прямоугольный магнитопровод с квадратным сечением профиля и намагничивающие катушки которые располагаются на звеньях магнитопровода.
Результаты проведенных исследований по влиянию геометрической формы магнитопровода на эффективность электромагнитных систем 20 показывают что наиболее эффективными являются замкнутые системы содержащие одну или две симметричные ветви замыкающего звена магнитопровода. Однако на практике для процесса ЭМН существует широкая номенклатура заготовок и деталей (плоские внутренние поверхности тел вращения и др.) которые по своим размерам и форме не позволяют использовать замкнутый магнитопровод. Тогда электромагнитные системы выполняются разомкнутыми (по однополюсной или двухполюсной схемам) т. е. без замыкающего звена что сопровождается снижением их эффективности использования. При разомкнутом магнитопроводе можно получать регулируемую величину индукции меняя величину электрического тока в намагничивающих катушках а также варьируя местом расположения и массой добавочных ферромагнитных элементов 26.
Следует отметить что использование постоянных магнитов частично ограничивает управление величиной индукции в рабочем зазоре. Это возможно только при помощи шунтирования или нейтрализации магнитного потока 27. Поэтому важное значение при проектировании системы имеет форма самого магнита и относительное расположение звеньев магнитопровода которые обеспечивают необходимую и постоянную во времени величину индукции в рабочем зазоре.
Экспериментально установлено что широкий ассортимент часто используемых магнитных систем сводится к некоторому сравнительно небольшому числу типовых магнитных систем (прямоугольные параллелепипеды Е-образные С-образные дугообразные и др.). При этом последние выбираются исходя из конструктивных соображений к числу которых относятся: наибольшие диаметр и длина обрабатываемой заготовки высота центров установочных приспособлений ширина и длина полюсных наконечников схема подачи смазочно-охлаждающей жидкости и ферропорошка в рабочий зазор размеры устройства к которому крепится магнитная система и др.
Принимая во внимание результаты исследований опыт проектирования и изготовления магнитных систем 7 26 – 28 в качестве источника постоянного магнитного поля были выбраны магниты Е-образной формы так как они обеспечивают однородное и симметричное магнитное поле относительно продольной оси рабочего воздушного зазора. Использование магнитов стандартной формы (прямоугольных параллелепипедов) оказалось невозможным из-за того что магнитную систему необходимо изготавливать из отдельных блоков магнитотвердых материалов и арматуры тем самым увеличивая массу системы что экономически нецелесообразно. Магниты дугообразной и С-образной формы как концентраторы однородного поля в рабочем зазоре по конструктивным соображениям не могут быть использованы в устройствах ЭМН.
Проектирование оптимальной конструкции магнитной системы устройства ЭМН состоит в определении параметров характеризующих геометрию системы и свойства постоянного магнита обеспечивающих выполнение необходимых требований:
- рабочая зона (ширина полюсного наконечника) до 80 мм;
- величина рабочего зазора 2 мм;
- величина магнитного поля в центре рабочего зазора Вр=08 Тл;
- длина однородного участка магнитного поля в рабочей зоне до 50 мм;
- минимальная масса устройства при использовании магнитотвердого материала из сплава ЮНДК.
В связи с этим анализ позволил наметить пути реализации – создание компактной магнитной системы и использование в качестве источника магнитного поля постоянных магнитов.
7 Ориентировочный расчет магнитной системы
Известно 28 при проектировании магнитной системы необходимо обеспечить величину магнитного поля в центре рабочего зазора Вр =08 Тл. Так как магнитный сплав дорогостоящий материал то необходимо произвести оптимизацию размеров и формы магнита.
При аналитическом расчете электромагнитной составляющей рабочей зоны требуется определить величину сопротивлений отдельных участков системы на пути прохождения магнитного потока в том числе и в самой зоне где поток проходит по воздуху
где Rст–магнитное сопротивление участков стального магнитопровода 1Гн;
Rв–сопротивление воздушного зазора 1Гн.
В этом случае магнитное сопротивление участков стального магнитопровода и воздушного зазора можем записать соответственно:
CТ–относительная магнитная проницаемость стали;
о–магнитная постоянная о >> 125×10 -7 Гнм;
S–площадь поперечного сечения магнитопровода м2;
D–длина воздушного участка м.
Магнитная индукция в рабочей зоне электромагнитной системы может определяться по эмпирической зависимости 9:
где I–сила тока в электромагнитной катушке А;
–количество витков проволоки в катушке;
Kp –поправочный коэффициент учитывающий насыщение магнитопровода.
Для упрощения расчета конструкции магнитной системы изготавливаемой на основе магнитотвердых материалов следует принять допущения что магнитное сопротивление стального магнитопровода отсутствует магнитное поле плоскопараллельно а поверхности между которыми определяются проводимости эквипотенциальные.
Принимаем что рабочая зона не заполнена ферромагнитным порошком а магнитный поток проходит по воздуху в зазоре 23 28 30. Тогда величины индукции и напряженности магнитного поля в рабочем зазоре определяются
Bз=kз и Hз=Bзо (4.6)
где kз – коэффициент учитывающий соотношение величин индукций в середине и центре полюсных наконечников магнита kз=105 11.
Длина Lм и площадь нейтрального сечения Sм постоянного магнита представляют основные искомые величины
где f – коэффициент учитывающий изменение намагничивающей силы в магнитопроводе стыках и зазорах f=11 14;
Sз – площадь поперечного сечения рабочего зазора м2;
Вd и Нd – индукция и напряженность поля соответствующие точке (ВН) максимальной кривой размагничивания постоянного магнита;
s1–коэффициент рассеяния магнитного потока.
Согласно 28 ориентировочно величину s1 принимаем 10 20 для системы армированной полюсным наконечником. По вычисленным величинам Lм Sм магнитной системы и на основании результатов экспериментальных исследований потокораспределения в системе магнитная цепь условно разбивается на ряд участков и рассчитывается проводимость каждого звена магнитной системы (рисунок 4.3 а и б). Проводимости рабочего Gв и технологических воздушных зазоров Gт находятся соответственно
где Sт – площадь поперечного сечения технологического зазора м2;
dз dт – длины технологического и рабочего зазоров соответственно м.
Тогда полная проводимость всех воздушных путей магнитного потока рабочей зоны будет
где Gd–проводимости технологического и рабочего зазоров м;
Ga –проводимости отдельных участков арматуры м;
Gм –полная проводимость воздушных путей магнита м.
Определение величин Вм Нм (индукция напряженность постоянного магнита) и В3 производится графически с помощью кривой размагничивания Вм=f (Н·м). Строились характеристики полной проводимости магнитной системы k1 и рассеяния магнита и деталей арматуры с учетом углового коэффициента k2 соответственно
Устанавливалась величина индукции Вм постоянного магнита на графической зависимости возврата и определялась величина В3 в рабочем зазоре:
Для ориентировочного расчета исследуемых конструкций магнитных систем была разработана программа написанная на языке программирования “V размеры форма и материал постоянных магнитов арматуры и полюсных наконечников; количество полюсов; скорость подачи охлаждающей жидкости ферропорошка в рабочий зазор 31.
Расчёт магнитных систем с применением программы проводили по методике 23 использующей эмпирические соотношения и коэффициенты (2.1 2.7) полученные ранее и проверенные многолетним опытом 28. Предварительно вычисляли Lм Sм (2.5) магнитной системы и строили картину рассеяния магнитного потока на основании экспериментальных данных потокораспределения в исследуемой конструкции. Затем рассчитывали проводимости каждого звена магнитной системы: постоянного магнита Gм арматуры магнитопровода Ga рабочего и технологических зазоров Gd (2.7). Определение действительной рабочей точки графической зависимости размагничивания магнита (Вм Нм) с учетом марки материала магнита и магнитопровода потоков утечки Ф сопротивления в зазорах и стыках проводили графическим методом используя зависимость Вм=f (Н·м). После этого определяли напряжённость Нз и индукцию Вз магнитного поля в рабочем зазоре а также величину коэффициента рассеяния магнитного поля для оптимизируемой конструкции магнитной системы (2.82.9). В случае не совпадения полученного значения Вз с заданным размеры магнитной системы или отдельных ее деталей корректируются и вся цепь рассчитывается повторно в том же порядке.
Рисунок 4.4 Фрагменты интерфейса программы ориентировочного расчета конструкций магнитной системы установки ЭМН
Рисунок 4.4 Схема конструкции Е-образной магнитной системы с разомкнутым магнитопроводом
Расчет магнитных систем проводили при следующих постоянных значениях факторов: рабочий зазор (Dп) –20 мм; материал магнитопровода–отожженная сталь Ст3 (ГОСТ 380–88); диаметр обрабатываемой заготовки 40 мм; материал заготовки–сталь45 (ГОСТ 1050-88); величина индукции в рабочем зазоре Вз=07 Тл. Анализ полученных данных ориентировочных расчетов систем показал что наиболее оптимальной является разомкнутая конструкция магнитной системы с Е-образным магнитом из сплава ЮНДК24Т (ГОСТ 17809–72) имеющая длину постоянного магнита Lм=120 мм и площадь нейтрального сечения последнего Sм=275x102 мм2.
Исследуемая система состоит из постоянного магнита Е-образной формы 1 (Рисунок 4.4) к торцевым поверхностям которого примыкают два плоских наконечника 4 установленные с зазором Dп относительно заготовки 5. Сердечник 2 системы со сменным полюсным наконечником 3 установлены в центральной части магнита с возможностью регулирования величины магнитной индукции Вз в рабочем зазоре посредством изменения расстояния dп между магнитотвердыми материалами (боковыми полюсными наконечниками) и обрабатываемой поверхностью изделия. При этом величина рабочего зазора Dп остается постоянной а магнитный поток Ф который проходит по магниту полюсным наконечникам рабочим и технологическим воздушным зазорам и заготовке образует замкнутую Ф-образную магнитную цепь.
8 Установка электромагнитной наплавки деталей типа тел вращения
В результате принятых технологических решений изготовлена установка для нанесения износостойких покрытий (рисунок 4.5) у которого источником поля в рабочем зазоре является постоянный магнит из сплава ЮНДК 24Т.
Установка работает следующим образом. Обрабатываемая деталь крепится в центрах и приводится во вращательное движение от привода станка. На полюсный наконечник и заготовку подают напряжение от источника технологического тока наплавки а в зазор между полюсным наконечником и деталью–ферромагнитный порошок из бункера-дозатора в потоке рабочей жидкости. Частицы ферромагнитного порошка выстраиваются вдоль магнитных силовых линий циркулирующих в двух замкнутых кольцевых потоках “постоянный магнит–деталь” образующихся благодаря Е-образной форме постоянного магнита с расположенным в центре сердечником. При возникновении дугового разряда в рабочей зоне происходит расплавление зерен ферромагнитного порошка импульсами электрических разрядов полярный перенос и распределение по поверхности детали в постоянном магнитном поле.
Тепловая энергия передаваемая полюсному наконечнику отводится охлаждающей жидкостью проходящей через него. Этим обеспечивается стабильный температурный режим необходимый для продолжительной и нормальной работы постоянного магнита. Для надежной защиты от механического воздействия магнит помещен в экранирующий корпус выполненный из неферромагнитного материала.
–смеситель; 2–постоянный магнит; 3–полюсный наконечник; 4–сердечник магнита; 5–защитный экран магнита; 6–токарно-винторезный станок мод. 1Е61М; 7–заготовка; 8–трубопровод; 9–корпус устройства; 10–пульт управления; 11–бункер-дозатор
Рисунок 4.5 Установка электромагнитной наплавки
9 Сравнение систем электромагнитной наплавки на постоянных и электрических магнитах
Проведенные исследования стабильности характеристики магнитотвердых материалов показали что магниты Е-образной формы обеспечивают требуемые технические и эксплуатационные характеристики предъявляемые к электромагнитным системам установки для ЭМН. При этом применение постоянных магнитов вместо электрических обусловлено следующими преимуществами:
уменьшаются габаритные размеры и масса системы;
не требуется материалы для изготовления электромагнитных катушек;
не требуется электроэнергия для питания катушек;
обеспечивается надежность в работе простота обслуживания и управления.
Таблица 4.3 Сравнительные характеристики магнитных систем установок ЭМН
Магнитная система с электрическими магнитами
Магнитная система с постоянными магнитами
Величина индукции Тл
Величина напряжения В
Величина рабочего зазора мм
Расход порошка г(с мм2) 10-3
Расход СОЖ дм3(с мм2) 10-3
Коэффициент использования порошка
Производительность мг
Сплошность покрытия %
Пористость покрытия %
Потребляемая мощность кВт
Габаритные размеры мм
Рисунок 4.6 Блок-схема типового технологического процесса восстановления и упрочнения посадочных мест под подшипники валов
Таблица 4.4 Рациональные режимы технологического процесса восстановления и упрочнения посадочных поверхностей цилиндрических деталей
Технологические факторы методов обработки
Режимы операций технологического процесса
Электромагнитная наплавка с постоянными магнитами
Плотность технологического тока i Амм2
Величина магнитной индукции В Тл
Скорость продольной подачи S ммоб
Окружная скорость заготовки V мс
Расход ферромагнитного порошка q г(с·мм2)·10-3
Расход СОЖq дм3(с·мм2)·10-3
Ферромагнитный порошок
Смазочно-охлаждающая жидкость
%-ный раствор товарного эмульсола Э2 в воде
Термическая обработка
Трехкратный отпуск при температуре Т °С
Электромеханическая обработка
Сила технологического тока I А
Усилие деформирования Р кН
Окружная скорость круга Vк мс
Окружная скорость заготовки Vд мс
Продольная минутная подача Sпр мммин
Поперечная подача Sпоп ммдв. ход
Характеристика шлифовального круга
А10ПС27К5 35мс А 1 кл.
Магнитно-абразивная обработка
Скорость продольной подачи Sпр ммоб
Продолжение таблицы 4.4
Степень заполнения порошком рабочей зоны К
Ферро-абразивный порошок
7.dwg

процесса восстановления и
упрочнения посадочных
поверхностей цилиндрических деталей
ГОУ ОГУ 190601.14.09.04.00.00
Технологические факторы методов обработки
Режимы операций технологического процесса
Электромагнитная наплавка с постоянными магнитами
Плотность технологического тока i
Величина магнитной индукции В
Скорость продольной подачи S
Окружная скорость заготовки V
Величина рабочего зазора
Расход ферромагнитного порошка q
Ферромагнитный порошок
Смазочно-охлаждающая жидкость
Термическая обработка
Трехкратный отпуск при температуре Т
Электромеханическая обработка
Сила технологического тока I
Усилие деформирования Р
Окружная скорость круга V
Продольная минутная подача S
Характеристика шлифовального круга
Магнитно-абразивная обработка
Степень заполнения порошком рабочей зоны К
Ферро-абразивный порошок
%-ный раствор товарного эмульсола Э2 в воде
%-ный раствор товарного эмульсола
А10ПС27К5 35 мс А 1 кл.
Рациональные режимы технологического процесса
лист 2.dwg

КФ ОГУ 190601.14.09.04 000
основной ковер бикроста 2 слоя
защитный ковер из бикроста
плитный пенополистирол
слой рубероида на мастике
стальной проф. настил
установочные болты М6х14
дополнительных слоя толя
необозначенные плиты профнастила поз. 6
Схема расположения плит покрытия М 1:400
Схема расположения элементов фундамента М 1:400
8.dwg

Технико-экономические
Наименование показателей
Годовая производственная программа
Количество единиц технологического оборудования
Балансовая стоимость машин и оборудования
Балансовая стоимость малоценного и
быстроизнашивающегося
Общий фонд заработной платы
Среднемесячная заработная плата
Амортизация оборудования
Расходы на содержание и эксплуатацию
Эксплуатационные затраты по участку
Себестоимость продукции
Годовой валовой доход
КФ ОГУ 190601. 1 4 09. 17. 00. 00
5.dwg

Принципиальные схемы
электромагнитной наплавки
- ферромагнитный порошок; 3 - бункер-дозатор; 4 - полюсный наконечник; 5 - сердечник электромагнита;
- электромагнитная катушка; 7 - источник питания электромагнитной катушки; 8 - источник разрядного тока;
- пластинчатая пружина; 10 - скользящий контакт
Принципиальные схемы электромагнитной наплавки
Однополюсная наплавка с вибрацией наконечника
3.dwg

- Склад для хранения заготовок.
- Место для обрабатываемых
- Фрезерно-центровальный
- Шкафчик для инструмента.
- Токарный станок с ЧПУ
- Шлицефрезерный станок 5350.
- Ручной манипулятор.
- Инструментальная кладовая.
- Вертикально-фрезерный
- Торцекруглошлифовалный
- Шлицешлифовальный станок
- Резьбошлифовальный станок
- Контрольно-обкатный станок
- Слесарный верстак.
- Место для хранения стружки.
- Место для хранения готовых
- Кран-балка с тельфером.
- Горизонтально- фрезерный
4.dwg

Технологически маршрут:
шлифование наружного диаметра в зоне наплавки заподлицо с основным металлом
фрезерование наплавленного шлицевого элемента в номинальный размер
Овальность и конусообразность шейки под
подшипники (Е) не более 0
Овальность и конусообразность шейки под
подшипников (Ж) не более 0
Радиальное биение отверстия под роликовый
подшипник относительно шеек (Е) и (П) не более
Шероховатость шеек (Е) и (П) не более Ra=1
Шероховатость поверхности под ролики
подшипников не более
Допускаемые способы
Износ шейки под подшипники
Износ шеек под ролики подшипников
Износ поверхности под подшипник
Базирование вала при восстановлении
6.dwg

технологического процесса
восстановления и упрочнения посадочных
под подшипники валов
обработка поверхности
Термическая обработка
Контроль размеров изделий
Очистка и мойка изделий от загрязнений
Дефектация и сортировка изделий
Электромагнитная наплавка
Механическая обработка покрытий
Магнитно-абразивная обработка покрытий
лист 1.dwg

План на отметке 0.000
доборный угловой блок
Экспликация зданий и сооружений
Производственный корпус
Административное здание
Склад готовой продукции
Склад расходных материалов
Стоянка для автомобилей
Генеральный план М 1:1000
Литература.doc
Керашев М. А. Экономика промышленного производства [Текст]: Учебник. Краснодар: Изд-во “Печатный двор Кубани” 1998. – 173 с.
Намаконов Б. В. Автомобиль не может быть “Одноразовым” [Текст]: журнал “Грузовое и пассажирское автохозяйство” НП Издательский дом “Панорама”. – 2007 №2. – С. 78 – 79.
Фасхиев С. Х. Оценка качества автомобилей запасных частей и комплектующих [Текст]: журнал “Грузовое и пассажирское автохозяйство” НП Издательский дом “Панорама”. – 2007 №2. – С. 61 – 66.
Технологические основы обработки изделий в магнитном поле П. И. Ящерицын Л. М. Кожуро А. П. Ракомсин и др. – Мн.: ФТИ НАНБ 1997. – 416 с.
Дюмин И.Е. Ремонт автомобилей под ред. И. Е. Дюмина. – М.: Транспорт 1999. – 280 с.
Кожуро Л. М. Обработка деталей машин в магнитном поле [Текст]. – Мн.: Наука и техника 1995. – 232 с.
Скворчевский Н. Я. Эффективность магнитно-абразивной обработки [Текст]. - Мн.: Навука i тэхнiка 1991. - 215 с.
Мрочек Ж. А. Прогрессивные технологии восстановления и упрочнения деталей машин [Текст]. – Мн.: УП «Технопринт» 2000. – 268 с.
Ракомсин А. П. Упрочнение и восстановление изделий в электромагнитном поле [Текст] Под ред. П. А. Витязя. - Мн.: Парадокс 2000. - 201 с.
Хейфец М. Л. Процессы самоорганизации при формировании поверхностей [Текст]. – Гомель: ИММС НАНБ 1999. – 276 с.
Справочник по электрохимическим и электрофизическим методам обработки Г. Л. Амитан И. А. Байсупов Ю. М. Барон и др.; Под общ. ред. В. А. Волосатова. - Л.: Машиностроение 1988. - 719 с.
А.с. 349769 СССР. Устройство для нанесения ферромагнитных покрытий Б. П. Чемисов Г. С. Шулев. – Опубл. в БИ № 26. 1972.
А.с. 1747538 СССР. Устройство для нанесения ферромагнитных покрытий Ж. А. Мрочек Л. М. Акулович Л. М. Кожуро и др. – Опубл. в БИ №26. 1992.
А.с. 503369 СССР. Устройство для упрочнения и наращивания плоских поверхностей токопроводящих заготовок В. И. Абрамов Б. П. Чемисов. – Опубл. в БИ. №19.1976.
А.с. 1301601 СССР. Устройство для упрочнения поверхностей деталей ферромагнитными порошками в магнитном поле Г. С. Шулев В. А. Люцко О. И. Палий. – Опубл. в БИ №13. 1987.
Описание полезной модели к патенту РБ 322. Рабочий орган установки магнитоэлектрического упрочнения М. П. Кульгейко И. В. Гринкевич В. М. Кисленок. – Опубл. в БИ №30. 2001.
Патент РФ 2016718. Способ магнитоэлектрического легирования металлических поверхностей Г. С. Шулев В. А. Хенсон Т. А. Иванова. – Опубл. в БИ №14. 1994.
Совершенствование конструкции магнитной системы установки электромагнитной наплавки А. П. Ракомсин М. И. Сидоренко Л. М. Кожуро А. В. Миранович Теория и практика машиностроения. – 2004. – № 4. – С. 23 – 26.
Установка для электромагнитной наплавки поверхностей деталей машин А. В. Миранович Ж. А. Мрочек Л. М. Кожуро Вестник БНТУ. – 2005. – № 2. – С. 30 – 34.
Иродов И. Е. Основные законы электромагнетизма [Текст]: Учеб. пособие для студентов вузов. - М.: Высшая школа 1991. – 288 с.
Сильные и сверхсильные магнитные поля и их применения: Пер. с англ.Под ред. Ф. Херлаха. - М.: Мир 1988. – 456 с.
Константинов О. Я. Расчет и конструирование магнитных и электромагнитных приспособлений. – М.: Машиностроение 1967.– 312 с.
Постоянные магниты: Справочник А. Б. Альтман Э. Е. Верниковский А. Н. Герберг и др.; Под ред. Ю. М. Пятина. – М.: Энергия 1983. – 486 с.
Келин Н. А. Методы и устройства для контроля магнитных свойств постоянных магнитов [Текст]. - М.: Энергоиздат 1984. –79 с.
Миткевич А. В. Стабильность постоянных магнитов [Текст]. – Л.: Энергия 1991. –128 с.
Василевский И. Н. Повышение эксплуатационных свойств деталей машин наплавкой паст в электромагнитном поле Агропанорама. – Мн. 2003. – № 4. – С. 11 – 12.
Корольков П. М. Причины возникновения магнитного дутья при сварке и способы его устранения Сварочное производство. – М. 2004. – № 3. – С. 38 – 40.
Рыжов Р. Н. Применение шестиполюсной электромагнитной системы для управления параметрами формирования швов при сварке неплавящимся электродом Автоматическая сварка. – К. 2004. – № 2. – С. 45 – 49.
Пат. №1378. МКИ С23С2600. Устройство для нанесения металлических покрытий П. А. Витязь А. Ф. Ильющенко Л. М. Кожуро А. В. Миранович. – Заявл. 22.09.03; Опубл. 30.06.04. Бюл. №30. – 2 с.
1_Раздел.doc
Становление рыночной экономики предъявляет новые и повышенные требования к анализу и организации роста эффективности производства. Актуальна проблема эффективности и в авторемонтном производстве который функционируя в качестве вспомогательного в то же время по существу относится к производству средств производства. Авторемонтное производство продолжая процесс воспроизводства является подотраслью машиностроения хотя организационно часто включается в состав автотранспортного комплекса.
Правительством РБ постановлением №348 от 30.11.2007 года 3 принята программа о развитии сельского хозяйства на 2008-2012 годы где предусмотрены мероприятия по внедрению интенсивных ресурсосберегающих технологий проведение капитально-восстановительного ремонта и модернизации сельскохозяйственной техники и укрепление материально-технической базы республиканских машинно-технологических станций за счет взноса Республики Башкортостан в их уставные капиталы.
На сегодняшний день в Республике Башкортостан насчитывается порядка 12 предприятий по ремонту подвижного состава автомобильного транспорта:
- Давлекановский авторемонтный завод (452120 г. Давлеканово ул. Комсомольская д. 48);
- РЕМАГРО (452756 г. Туймазы ул. Столярова д. 3);
- 487 Центральный автомобильный ремонтный завод (452155 Чишминский р-н дер. Алкино Заводская 1);
- Мелеузовский авторемонтный завод филиал ГУП "Башавтотранс" РБ (453310 г. Мелеуз Смоленская 182).
Из приведенных данных очевидно что предприятия сосредоточены в основном на севере и востоке Республики. Южный регион ранее обслуживался Мелеузовским авторемонтным заводом но в 2006 году его деятельность была перенаправлена на 4:
установку газобаллонного оборудования производства итальянской фирмы «ЛОВАТО»;
сборку основания автобуса (каркаса) из новых материалов;
производство «школьного» автобуса для сельских районов республики;
установку новых силовых агрегатов на автобусы ПАЗ.
Таким образом (из приведенных данных) предприятия Куюргазинского Кугарчинского Зиянчуринского Федоровского и Мелеузовского районов (общая площадь порядка 31250 км2) не имеют возможности производить капитальный ремонт подвижного состава автомобильного транспорта в непосредственной близости. Между тем развитие и совершенствование авторемонтного производства требует правильной организации ремонта автомобилей и их агрегатов и узлов которая зависит в свою очередь от целого ряда факторов наиболее важными из которых являются:
рациональное размещение ремонтных предприятий;
производственная мощность.
В то же время в Куюргазинском районе имеется предприятие производственные мощности которого недоиспользуются на сегодняшний день. Неравномерная загруженность предприятия по времени обусловленная узкой номенклатурой выполняемых работ отрицательно сказывается на стабильности кадрового состава что несомненно сказывается на качестве выполняемых работ ведет его к банкротству. Адекватная реакция на сложившуюся ситуацию позволит сохранить предприятие и обеспечит регион надежной авторемонтной базой.
Эффективность ремонтно-восстановительного производства складывается из повторного использования деталей меньших затрат на восстановление по сравнению с производством новых. Автомобиль – сложное в конструктивном отношении средство труда составные части которого только в сборе и придают ему новое качество - потребительную ценность как средства труда. Автомобиль в состоянии нормально эксплуатироваться только при условии что все эти элементы находятся в нормальном состоянии. Выход из строя хотя бы одного существенного элемента в результате достижения предельного технического износа нарушает их единство и автомобиль становится неспособным выполнять свои функции. Потребительная ценность его как средства труда в этот момент утрачивается. Полная утрата потребительной ценности автомобиля не означает полного технического разрушения всех остальных его конструктивных элементов. Как правило большая их часть обладает достаточно высокой технической годностью. На время ремонта автомобиль становится своеобразным “полуфабрикатом” на основе которого возможно восстановление первоначального технического единства конструктивных элементов обеспечивающего его потребительскую ценность. Ремонт создает новую потребительную ценность автомобиля. Причем величина ее будет определяться временем до выхода из строя очередного наиболее устойчивого элемента.
На конкурентоспособность авторемонтного производства влияет стоимость нового автомобиля или импортного автомобиля стоимость капитального ремонта автомобиля пробег нового или импортного автомобиля до постановки его в капитальный ремонт пробег капитально отремонтированного автомобиля до списания или следующего ремонта расходы на поддержание в исправном состоянии нового импортного или капитально отремонтированного автомобиля до списания или следующего ремонта; расходы на перевозку автомобиля до автотранспортного предприятия ликвидационная стоимость ремонтируемого автомобиля. Чем большим будет количество затрат на километр пробега тем менее конкурентно данное направление пополнения подвижного состава. При всем понятным преимуществам нового и импортного автомобиля в сравнении с капитально отремонтированным относительно его большего пробега (в среднем в 2 - 3 раза) стоимость нового и импортного автомобиля (новые тарифные ограничения на импортные автомобили касаются и грузовые автомобили и автобусы) в десятки раз дороже капитального ремонта автомобиля или агрегата (стоимость базовой детали например нового коленчатого вала равна стоимости ремонта всего двигателя – 26-30 тыс. руб.). Относительно дорогой является и доставка новых и импортных автомобилей в сравнении с небольшими расходами по доставке с авторемонтных заводов приближенных к потребителю.
В производственном корпусе производится общая разборка тракторов К-700А разборка агрегатов и узлов ремонт двигателей коробок передач ремонт электорооборудования восстановления деталей автомобилей КАМАЗ ЗИЛ МАЗ сборка испытания и окраска агрегатов и узлов обкатка двигателей и коробок передач а также общая сборка.
Однако в настоящее время динамика выпуска продукции такова что на начало 90-х годов предприятие производит лишь порядка 200 капитальных ремонтов полнокомплектных К-700А и около 1200 ремонтов агрегатов в год. К началу 2000-х эти цифры еще более уменьшились в связи со старением оборудования необходимостью реконструкции.
Предприятие имеет штат из 46 человек годовой оборот составляет 2896785 рублей.
На предприятия имеются следующие участки: разборочно-моечный участок участок дефектации участок ремонта топливной аппаратуры сварочно-наплавочный участок участок ремонта узлов гидросистемы участок ремонта КПП участок восстановления дисков КПП участок ремонта электрооборудования слесарно-механический участок участок сборки двигателей участок обкатки узлов участок общей сборки.
Общая площадь производственного корпуса составляет 2304 м2.
Здание одноэтажное огнестойкость II степени отопление центральное вентиляция приточно-вытяжная водопровод и канализация с присоединением к местным сетям электроснабжение от местных сетей.
Фундамент железобетонный сборный; стены кирпичные; покрытия сборные железобетонные; перегородки кирпичные сетчатые металлические и др. Полы бетонные и из керамических плиток. Кровля рулонная отделка простая.
2 Характеристика участка ремонта КПП
Участок предназначен для ремонта деталей коробок передач. Участок расположен в производственном корпусе ремонтного предприятия и занимает порядка 32 м2 производственной площади. Участок рассчитан на ремонт 1000 коробок передач К-700А в год. Непосредственно на участке осуществляется восстановление грузового вала коробок передач К-700А и К-701 и сборка КПП. Имеется централизированный подвод электроэнергии и воды к технологическому оборудованию.
К недостаткам участка следует отнести устаревшее оборудование низкую квалификацию рабочих плохую организацию труда несоблюдение технических требований на ремонт и восстановление деталей.
3 Выбор варианта технологического маршрута и его технико-экономическое обоснование
Принципиальным решением проблемы поддержки уровня конкурентоспособности является непрерывное обновление ряда предлагаемой предприятием продукции и освоение новых изделий. Именно это является посылкой для завоевания стратегического преимущества.
Однако не каждое предприятие может позволить себе успешно “вписать” в план производство новое изделие и вот несколько причин:
– перегруженность мощностей предприятия;
– недостаточные финансовые ресурсы;
– жесткие временные рамки освоения продукции.
Известно что каждое изделие проектируемое на предприятии может иметь несколько вариантов маршрутных технологий (технологий изготовления) отличающихся по стоимости длительности процесса изготовления длительности процесса подготовки производства. Вопрос выбора наилучшей технологии – это вопрос успешного функционирования предприятия.
Известно что изношенные поверхности деталей могут быть восстановлены как правило несколькими способами. Для обеспечения наилучших экономических показателей в каждом конкретном случае необходимо выбрать наиболее рациональный способ восстановления.
Выбор рационального способа восстановления зависит от конструктивно- технологических особенностей деталей (формы и размера материала и термообработки поверхностной твердости и шероховатости) от условий ее работы (характер нагрузки род и вид трения) и величины износа а также стоимости восстановления.
Для учета всех этих факторов рекомендуется последовательно пользоваться тремя критериями:
- технологическим критерием или критерием применимости;
- критерием долговечности;
- технико-экономическим критерием (отношением себестоимости восстановления к коэффициенту долговечности).
Технологический критерий (критерий применимости) учитывает с одной стороны особенности подлежащих восстановлению поверхностей деталей а с другой - технологические возможности соответствующих способов восстановления.
Среди посадочных мест на вторичном вале коробки передач КАМАЗ-5320 наибольший износ имеют шейки под роликоподшипники . Характер износа: следы проворота роликоподшипника наклеп на шейке следы сплавления роликоподшипника с шейкой.
Для их восстановления могут быть использованы следующие способы:
– наплавка в углекислом газе вибродуговая наплавка;
– диффузионный метод хромирование электролитическое;
– гальванический метод вибродуговая наплавка.
Так как восстанавливаемая поверхность в процессе работы не испытывает значительных динамических и знакопеременных нагрузок численное значение коэффициента долговечности определяется только численным значением коэффициента износостойкости.
Выбор оптимального способа восстановления проводиться по технико-экономическому показателю численно равному отношению себестоимости восстановления к коэффициенту долговечности для этих способов.
Окончательному выбору подлежит тот способ который обеспечивает минимальное значение этого отношения
где – коэффициент долговечности восстановленной поверхности;
– себестоимость восстановления соответствующей поверхности руб.
При обосновании способов восстановления поверхностей значение себестоимости восстановления определяется из выражения
где – удельная себестоимость восстановления ;
S – площадь восстанавливаемой поверхности .
Наиболее оптимальным при этом является наплавка. В последние годы все более широкие исследования проводятся по изысканию и внедрению новых физических и электрофизических способов воздействия на жидкий металл непосредственно в процессе наплавки которые направлены на исключение из технологических процессов многочисленных конструкционных недостатков. Одним из методов электрофизического воздействия является электромагнитная наплавка обеспечивающая нанесение термообработку упрочнение формируемого покрытия в электромагнитном поле. При этом формируются необходимые размеры обрабатываемой детали физико-механические и эксплуатационные свойства поверхности изделий. Процесс ЭМН обеспечивает формирование тонких слоев защитных покрытий толщиной 01 06 мм на сторону а также высокую прочность соединения наплавленного покрытия с основой при минимальном тепловыделении и расплавлении материала основы. С учетом выше рассмотренных достоинств ЭМН очевидно что метод находит наибольшее применение при восстановлении посадочных мест валов осей и других тел вращения (диаметром от 20 мм и более) под подшипники качения и скольжения зубчатые колеса шкивы шестерни звездочки и другие детали.
Введение.doc
В то же время необходимо помнить что все материальные ресурсы после завершения жизненного цикла любого изделия подлежат вторичному использованию. Однако утилизации обязательно должны предшествовать экономически обоснованное число ремонтов и реноваций дающих максимальный экологический технический функциональный и финансовый эффект. Для снижения экологической напряженности и сохранения нашей цивилизации любой характер воссоздания ничем не ограничивается а путь на свалку – крайняя мера для особых случаев.
К концу первого межремонтного пробега автомобиля в металлолом выбраковывается не более 20% деталей до 20% деталей пригодны к дальнейшей работе без ремонтных воздействий а свыше 60% имеют остаточный запас долговечности до 90% и остаточную стоимость до 85 % от новых изготовленных из первичных ресурсов. Переработка этих групп деталей как металлолома обусловливает потери до 70% и только на 60% снижает вредные выбросы 2.
При весовом износе в 04% от общего веса автомобиль становится непригоден к эффективной дальнейшей эксплуатации. По деталям прецизионной группы критический износ составляет 001 002% от веса детали 2.
Отсюда следует вывод: затраты материалов и энергии на реновацию деталей (т.е. на восстановление) составляют менее 10% от их веса что примерно в 100 раз меньше чем на изготовление первичных.
Следовательно в 100 раз меньше расходуется энергоресурсов и в 100 раз меньше образуется различных загрязнений приходящихся на материал.
Объём восстановительных работ в 4 5 раз меньше по сравнению с первичным производством следовательно количество выбросов и расход энергии от реализации технологических процессов восстановления деталей во столько же раз меньше. Имеются данные свидетельствующие о том что выбросы вредных веществ при капитальном ремонте автомобильного двигателя в среднем в 250 раз меньше чем при изготовлении 2. Отмечается что основным источником загрязнения являются металлургические и энергогенерирующие предприятия.
Используемые в настоящее время способы реновации изношенных деталей машин позволяют восстанавливать их до номинальных параметров долговечности с себестоимостью не более 40% от их первичной стоимости. Эти задачи успешно решены и теоретически и практически 2. Например для получения заготовок зубчатых колес из изношенных деталей разработаны и используются прокатные станы с тактом выпуска 05 10 мин. а поршневые пальцы восстанавливают методом пластического деформирования с тактом 03 мин. В США восстанавливают в промышленных масштабах коленчатые валы. Их стоимость в 5 раз ниже а износостойкость значительно выше чем у новых. Подобные технологии успешно используются во всем мире.
Даже с учетом выбраковки изношенных деталей (до 25%) и получаемых загрязнений от реализации технологических процессов восстановления экологичность реновации агрегатов и автомобиля в целом на порядок.
При разработке данного проекта основной целью является организация такого технологического процесса восстановления вторичного вала КПП автомобиля КамАЗ-5320 при котором минимизируются материальный издержки и обеспечивается максимально возможный ресурс восстановленного изделия.
Для достижения поставленной цели необходимо решить следующие задачи:
провести анализ существующих технологических процессов восстановления;
выявить недостатки в организации производственного процесса;
разработать мероприятия обеспечивающие оптимальные условия реализации процесса восстановления;
провести анализ опасных и вредных факторов при проведении реновационных работ и выработать направления снижения их влияния на работающих;
провести оценку влияния производственной деятельности авторемонтного предприятия на окружающую среду и разработать мероприятия по повышению экологической безопасности производства;
определить технико-экономические показатели проекта.
Рекомендуемые чертежи
- 29.04.2021
- 24.01.2020