Мостовой электрический кран 20 т.




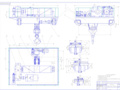
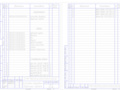
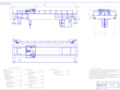
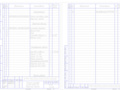
- Добавлен: 25.10.2022
- Размер: 2 MB
- Закачек: 0
Описание
Состав проекта
![]() |
![]() ![]() |
![]() |
![]() ![]() ![]() ![]() |
![]() ![]() ![]() ![]() |
![]() ![]() ![]() ![]() |
![]() ![]() ![]() ![]() |
![]() ![]() ![]() ![]() |
![]() ![]() ![]() ![]() |
![]() ![]() ![]() ![]() |
![]() ![]() ![]() ![]() |
![]() ![]() ![]() ![]() |
![]() ![]() ![]() ![]() |
![]() ![]() ![]() ![]() |
![]() ![]() ![]() ![]() |
![]() ![]() |
![]() ![]() |
![]() ![]() |
![]() ![]() |
![]() ![]() |
![]() |
![]() ![]() |
![]() ![]() |
![]() ![]() ![]() |
![]() ![]() |
![]() ![]() |
![]() |
![]() ![]() |
![]() ![]() |
![]() ![]() |
![]() |
![]() |
![]() ![]() |
Дополнительная информация
вал2.dwg

Размер обеспечивается инстр.
Неуказанные предельные отклонения размеров поверхностей
Крышка муфты.dwg

Неуказанные радиусы 2мм max
Неуказанные предельные отклонения размеров поверхностей
Установки барабана.dwg

Кран.dwg

Группа режима работы М5
передвижения моста 1
передвижения тележки 1
Электродвигатель механизма:
передвижения тележки:
Изготовление монтаж и эксплуатация крана должны соответствовать правилам
устроиства и безопасной эксплуатаций грузоподьемных кранов ПБ-382-00.
Электрооборудование крана
заземление должны соответс-
твовать Правилам устроиства электроустановок.
Кран оборудовать ограничителями рабочих движений для автоматической остановки
механизма подьема и механизма передвижения тележки
ограничителя высоты подьема
блокировкой напряжения при выходе на площадку.
Сварочные работы при монтаже крана должны производиться организациями
имеющими лицензию органов гостехнадзора
передаточное число 25
передаточное число 20
передаточное число 16
Техническая характеристика:
Техническая требования:
Деталировка крышка.dwg

Неуказанные радиусы 2мм max
Неуказанные предельные отклонения размеров поверхностей
Спецификация тележки.dwg

Д.ММ.190205.6120.КП.09.01.00.00.СБ
Тележка мостового крана
Д.ММ.190205.6-120.КП.09.01.02.00.СБ
ЭлектродвигательАМУ132МА6
Электродвигатель4МТМ225М8
СП телега10.dwg

Болт М20 х 38 ГОСТ 7798-70
Шайба 10 Н ГОСТ 6402-70
Шайба 12 Н ГОСТ 6402-70
Шайба 22 Н ГОСТ 6402-70
Шайба 32 Н ГОСТ 6402-70
Шайба 16 Н ГОСТ 6402-70
Шайба 20 Н ГОСТ 6402-70
Шайба 10 ГОСТ 11371-78
Шайба 12 ГОСТ 11371-78
Шайба 22 ГОСТ 11371-78
Шайба 32 ГОСТ 11371-78
Шайба 16 ГОСТ 11371-78
Шайба 20 ГОСТ 11371-78
Гайка М10 ГОСТ 5915-70
Гайка М12 ГОСТ 5915-70
Гайка М22 ГОСТ 5915-70
Гайка М32 ГОСТ 5915-70
Гайка М16 ГОСТ 5915-70
Гайка М20 ГОСТ 5915-70
Спецификация(Барабан).dwg

0205.КП.09.00.00.00.СБ
Болт М24 х 120 ГОСТ 7798-70
Подшипник1516 ГОСТ 28428-90
Болт М8 х 28 ГОСТ 7798-70
Болт М12 х 60 ГОСТ 7798-70
Гайка М12 ГОСТ 5915-70
Шайба 8 БрКМц3-1ГОСТ 6402-70
Шайба 12 БрКМц-3 ГОСТ 6402-70
Шайба 24 БрКМц3-1 ГОСТ 6402-70
Шайба 14 БрКМц-3ГОСТ 6402-70
Зубчатая муфта.dwg

Сталь40Х ГОСТ4543-71
Радиусы скруглений 1
Неуказанные предельные отклонения размеров: валов -t
Нормальный исходный
Коэфитциент смещения
тележка.dwg

Технические требования
Электроды типа Э-4 ГОСТ 9467-75.
Сварные швы по ГОСТ 1486-80.
* Размеры для справок.
Радиальное смещение осей опор валов барабанов не более 0
относительно друг друга.
вал.dwg

Размер обеспечивается инстр.
Неуказанные предельные отклонения размеров поверхностей
крышка сквозная.dwg

Неуказанные радиусы 2мм max
Неуказанные предельные отклонения размеров поверхностей
курсовой ГПМ Ахм.doc
1 Выбор кинематической схемы
Так как скорость подъема небольшая передаточное число механизма будет большим. Поэтому принимая за основу кинематическую схему изображенную на рис. 1.1
Рисунок 1.1- Кинематическая схема механизма подъема груза
Режим работы легкий М5
Высота подъема груза Н=12 м
Подъема груза – 02мс
Передвижения моста–16 мс
Передвижения тележки –1.0 мс
КП.ГПМ.6120.04.00.00.00ПЗ
2 Выбор крюковой подвески
В мостовых кранах для обеспечения строго вертикального подъёма груза применяются сдвоенные полиспасты у которых на барабан наматываются две ветви (рис. 1.2). Число ветвей каната на которых висит груз зависит от грузоподъёмности крана. Чем больше число ветвей тем меньше усилие в канате на барабане следовательно меньше и диаметр каната и барабана меньше диаметр вала и размеры подшипников вала и т.д. Однако с увеличением числа ветвей увеличивается число блоков а это усложняет и утяжеляет подвеску.
Рисунок 1.2 - Схема запасовки канатов (сдвоенный полиспаст)
Выбираем крюковую подвеску (ОСТ 24.191.08-81)типоразмер по стандарту 4-20-406 имеющая следушие параметры Qп=20т; режим работы легкий; zбл.полисп.=4; Dбл.о.=406 мм;Ввн=76 мм; Внар=260 мм; bc=92 мм; mп=318 кг.
Число блоков выбранной крюковой подвески соответствует числу блоков на кинематической схеме поэтому схема запасовки канатов в полиспасте сохраняется..Его передаточное число; (кратность) равно 4.
Вес номинального груза и крюковой подвески равен Q = (mгр + mп )g = (20*103 + 318)9.8=199116 Н. По таблице 2.2 находимп=096; Zк.б.= 2Направляющие блоки в схеме отсутствуют поэтому н.бл = 1. Определим максимальное статическое усилие:
Smax=G( Zк.б*uп*п* н.бл)=199116(2*4*1*098)=25397 Н
Выбираем тип каната ЛК-Р6 х х 19(1 + 6 + 6 + 66)+ 1 о.с. ГОСТ 2688-80 имеющий линейное касание проволок и разные диаметры проволок в верхнем слое пряди.
По условию –произведение максимального статического усилия в канате на коэфитциент запаса прочности не должно превышать разрывного усилия каната в целом указанного в госте:
Smax*Кзап=25397*5=126985
Из таблицы ГОСТа выбираем типоразмер каната. Канат 165-Г-В-С-О-Н-1470 ГОСТ 2688-80 имеет параметры: Fk=130000 Н; dк =16.5 мм; Fк = 104.61 мм2; назначение каната-грузовое; марка проволоки-высшая; маркировочная группа -1470 MПа; вид покрытия проволоки—оцинкованная;
Сочетание направлений свивки элементов –одностороннее; способ свивки каната- нераскручивающиися
По условию (23) должно выполняться соотношение между диаметром выбранного каната и диаметром блока крюковои подвески :
Dбл= Dбло+ dk=406+165=4225 мм
Следовательно условие проверки выполняется.
4 Основные размеры «Установки верхних блоков».
Конструкцию узла верхних блоков принимаем по типу конструкций разработаннои ПО
Рис 1.3 Компоновка верхних блоков
Dбл=dk*e=165*20=330 мм
Dбло.= Dбл.-dk=330-165=3135 мм
Dбл.max=Dбло +4dk=313.5+4*16.5=379.5 мм
Наидем ближаишее значение Dбл.max=380 мм
Определим остальные размеры показанные на рисунке:
Lв.бл=115* Dбло=115*324=3726 мм; Примем Lв.бл=380 мм
Вв.бл.=13* Dбло=13*324=4212 мм; Примем Вв.бл.=421 мм
Нв.бл=125* Dбло=125*324=405 мм Примем Нв.бл=405 мм
hв.бл.=06* Dбло=06*324=1944 мм Примем hв.бл.=195 мм
Расстояние между осями краиних блоков определим по формуле
Lo=(06-07) Lв.бл=(06-07)380=228 .266 мм Примем Lo=250 мм
5 Основные размеры уравнительного балансира.
Значение hmin ур.бал.=3*Dбло=3*324=972 мм
Размер Аур.бал. может быть определен из условия одинакового отклонения каната на внутренних блоках крюковои подвески и из условия максимально допускаемого отклонения при набегании на блок:
Используем орентировочные соотношения:
Lур.бал=(12-13) Аур.бал=(12-13)*250=300 325 мм Принимаем Lур.бал=310 мм
Вур.бал=(06-07) Аур.бал=(06-07)*250=150 175 мм Прнимаем Вур.бал=160 мм
Нур.бал. =(045-055) Аур.бал=(045-055)250=1125 137.5 мм
Принимаем Нур.бал. =120 мм
Lоп.ур.бал.=(065-075) Аур.бал=(065-075)250=1625 1875 мм
Принимаем Lоп.ур.бал.=170 мм
6 Основные размеры установки барабана.
Примем диаметр барабана меньше чем диаметр блока на 15%.
Вычислим 085* dк*е=085*165*20=2805 мм; Примем диаметр барабана Dб=450 мм
Наидем рабочую длину каната соответствующий одному нарезному участку:
Число рабочих витков:
zp= Lкр(п* Dб)=48314*045)=339=34
Примем Zнепр=15 и Zкр=3 где Zнепр -Число неприкосновенных витков требуемых правилами ГГНТ. Zкр-Число витков для крепления конца каната.
t=(11-123)dk=(11-123)165=1815 203 Примем t=19
Определим длину одного нарезного участка
lH=t(zp+ Zнепр+ Zкр)=19(34+1.5+3)=731 мм
Опредлим минимальное допускаемое расстояние между осью блоков крюковои
подвески: hмин.б.=3 Dб=3*450=1350 мм
Длина среднего гладкого участка может быть определена по формуле:
Внар≤l0≤ Внар+2 hмин.б*tg(γ)
0≤ l0 ≤260+2*1350* tg6
0 ≤ l0 ≤543 Принимаем l0=350 мм
Длина гладкого концевого участка:
к=(4-5)dk=(4-5)16.5=66 825 мм Примем 1к= 70 мм
Ширину зубчатого венца примем Вз.в.=120 мм
Длина барабана будет равна:
б.=2lH+ l0+21к.=2*731+350+2*70=1952мм
Длина барабана превышает диаметр в 46 раз что вполне приемлемо.
Определим другие размеры «установки барабана»:
Dmax=(1.1-1.3) Dб=(1.1-1.3)450=495 585 мм Примем Dmax=570 мм
=15 мм; =30 мм; Воп=100мм; Восн оп.=100 мм; Lосн оп. =370 мм
Lут.бар.=2372 мм;=2260 h=(02-03) Dб=100 150мм Принимаем h=110 мм
С1=(02-03) Восн оп.=20 30 мм; принимаем С1=50мм
С2=(05-08) Lосн оп. =185 296 мм; принимаем С2=280 мм
Предварительное значение к.п.д. механизма примем равным пр=085. Максимальная статическая мощность Nст мах (кВт) которую должен иметь механизм в период установившегося движения при подъеме номинального груза равна:
Nст мах=Gv пр=(200000Н+3180)*016085=382 кВт
С учетом коэфитциента использования
Nдв=к*Nст мах=(07-08)382=27 306 кВт
Выбираем двигатель крановый 4МТМ225М8 ; Nдв=30кВт; ПВ=40%; nдв=750 обмин;
mдв=390 кг; dвала=70 мм; I=095 кг*м2
Частота вращения барабана равна:
Требуемое передаточное число редуктора:
uред.треб.=nдвnбар=7502717=276
Определим расчетныи эквивалентныи момент на тихоходном валу редуктора. Принимаем класс нагружения механизма В2.Класс использования А3.Находим значение коэфитциента нагружения к=025.Значение kQ=
Машинное время работы механизма tмаш=6300 ч.
Число циклов нагружения на тихоходном валу редуктора
ZT=60nT tмаш=60*27.17*6300=10.2*106
Передаточное число тихоходнои ступени редуктора предпологаем близким к значению
uT=8.Определим zp- суммарной число циклов контактных напряжений зуба шестерни тихоходной ступени редуктора. zp=zT*uT=10.2*8=816*106.
z0 - базовое число циклов контактных напряжений для типажных редукторов
Определим коэфитциет долговечности кД:
Значение к.п.д. опор барабана и открытой передачи примем равными: = 099;
Расчетный крутящий момент на тихоходном валу редуктора при подъеме
номинального груза в период установившегося движения :
Эквивалентныи момент равен:
Тр.э.= kД*Тр=054*11544=6276 Н*м
Выбираем двигатель 1Ц2У-355. Передаточное число u=25.
Разница между uред.треб и uр равно:
Проверим выполнение условия Тр.э.≤Тр.н.
Номинальныи крутящий момент на тихоходном валу редуктора Тр.н.=14000 Н*м
76≤14000 Условие выполняеться. Следовательно редуктор 1Ц2У-355 соответствует требованиям прочности и кинематики механизма. Редуктор имеет параметры кроме выше найденных: awc=580 мм; dв.быст=55мм; dв.тих.=125 мм; u=25; m=700 кг.
Определим фактическую скорость подьема груза и фактический к.п.д. Передаточное число механизма равно: uмех=up*uп=25*4=100
Угловая скорость вала двигателя равна:
wдв=п*nдв30=314*75030=785 радс
Скорость подьема определиться:
vпод= wдв*rб uмех=785*0225100=0177 мс
Данная скорость отличаеться от заданнои на 10% что допустимо.
К.п.д. муфты на быстроходном валу примем равным м.б.=099
К.п.д. всего механизма мех=п*брм.б.=096*099*094*099=088
9 Выбор соединительной муфты.
Для соединения валов двигателя и редуктора выбираем тип муфты – зубчатую. Такая муфта хорошо компенсирует возможные неточности монтажа и может передавать большие крутяшие моменты. Диаметры концов валов
dв.дв=50 мм; dв.быстр.=70
Выбираем типоразмер: муфта 2-6300-70-2-55 ГОСТ5006-83.
Данная муфта имеет парамеры Т=6300 Н*м; Iм=025кг*м2; dлев.мах=dправ.мах=80мм;
Наидем kт=175.Определим максимальное значение к.п.д. механизма 1 на участке кинематическои цепи от крюка до тормоза. В качестве р1 возьмем максимально возможное значение к.п.д. р1=097
=р*б*1р=096*099*097=092
Определим статический крутящий момент при торможений создаваемый весом номиального груза на валу на кот. устанавливается тормоз.
Расчетный тормозной момент находим по формуле:
По условию Тт.н.≥Тт.р. выбираем тормоз ТТ-320 имеющий параметры:
Тт.н=800 Н*м; m=89кг; D=320 мм; В=135 мм.
11 Выбор муфты с тормозным шкивом.
Учитывая требуемыи диаметр тормозного шкива ширину колодок и и диаметр быстроходного вала выбираем муфту имеющие параметры: Dт.ш.=320 мм; В=145 мм; dмах=595 мм; m=26.2 кг.
Механизм передвижения тележки
Выбираем кинематическую схему изображенную на рис.2.1
Рис. 2.1 Механизм передвижения.
Её достоинством является отсутствие перекоса колес при работе двигателя и тормоза
Во время пусков и торможений.
2 Статические нагрузки на колеса
Вес номинального груза равен:
С учетом коэф. нераномерности колес мах. Статическая нагрузка на 1 колесо будет равно:
Минимальная статическая нагрузка на 1 колесо:
По табл. используя выбираем колесо диаметром D=400мм; F=100 кН.
4 Выбор колесных установок
По диаметру колеса выбираем стандартные коленные установки; приводную колесную установку К2РП-400 исполнения 1.и неприводную К2РН-400 имеющие параметры: D=400мм; d=80 мм; dц=95 мм; В=100 мм; mк.упр.=1752 кг; mк.неупр.=16667 кг
zреб=2. Форма поверхности катания цилиндрическая. Тип подшипника роликовый радиальныи сферический двухрядный с симметричными роликами.
5 Выбор подтележечного рельса
По таблице выбираем рельс КР70 ГОСТ 4121-76 с выпуклой головкой. b=70 мм.
Проверим соотношение ширины дорожки катания колеса В и головки рельса b:
В-b=100-70=30 что не меньше нормы.
Другие параметры рельса r=400 мм; bосн=120 мм ; у=593; F=67.3 см2; Iк=108169 см4;
6 Сопротивление передвижению тележки
По табл. определим коэф. трения качения =06. Определим приведенный коэф. трения . Скольжения в подшипниках колес f=0.015. При гибком токопроводе тележки kдоп=2. Определим сопротивление сил трения
Сопротивление создаваемое уклоном:
Сопротивление создаваемое при разгоне силами инерций:
При скорости движения менее 1 мс =125-коэф. учитывающий инерцию вращающихся
поступательно движ. обьекта:
Ускорение при разгоне:
а=а(05 10)(а)=(05 1)*01=005..01. Примем а=007
Сопротивление создаваемое раскачиванием груза:
Учитывая что кран работает в помещений:
Предварительное значение к.п.д. механизма примем равным =09. п.ср=16
Выбираем двигатель АМУ132МА6 ГОСТ15150 имеющий параметры:
N=4кВт; nдв=1000 обмин; dв.дв.=38 мм; m=55 кг;
Частота вращения колеса равна: nк=vп*D=1*60(3.14*0.4)=47.78 обмин.
Требуемое передаточное число механизма u=nдв nк=10004778=209. Выберем тип редуктора ВКУ-М.
Аналогично механизму подьема примем режим 3М. к=025; kQ=0.63; tмаш=6300 ч;
Частота вращения тихоходного вала редуктора равна частоте вращения колеса:
Число циклов нагружения на тихоходном валу редуктора:
Zt=30nt*tмаш=30*4778*6300=903*104
Передаточное число тихоходной передачи предположим равнои 5. Суммарное число
циклов контактных напряжений зуба шестерни тихоходной ступени:
Zp= Zt*ut=903*104*5=45.15*106
Базовое число циклов контактных напряжений Zо=125*106
Коэфитциент срока службы равен:
Коэфитциент долговечности: kД=kQ*kt=0.63*0.712=0.45
Значение kД необходимо принять не менее чем 0712. Поэтому kД=0712
Определим расчетный крутящий момент Тр на тихоходном валу редуктора. Будем ориентироваться на редуктор ВКУ-500М.Передаточное число равно u=20. что расходиться со значением 45 % на допустимую величину. К.п.д. равно =094
Определим угловую скорость двигателя: wдв=пnдв30=314*100030=1047 радс.
Тдв.ном.=Nдвwдв=40001047=382Н*м
Примем кратность мах. момента фц.мах=2 . То Тп.мах= Тдв.ном* фц.мах=382*2=764Н*м
Определим расчетный крутящий момент на тихоходном валу редуктора:
Определим расчетный эквивалентный момент:
Редуктор ВКУ-500М имеет номинальный крутящий момент на тихоходном валу:
ТР.Н.=76 186 кВт. Следовательно условие ТР.Э.≤ТР.Н. выполняется. Кроме указанных
редуктор имеет следующие параметры: аwc=500 мм; dр.быстр=40 мм; dт.в=65 мм; m=330 кг.
Схема сборки редуктора 13 или 23. Полное условное обозначение типоразмера редуктора
ВКУ-500М-40-23-У2 ТУ 24.01.3673-79.
9 Определение фактической скорости и к.п.д. механизма
Фактическая скорость передвижения тележки равна:
v=wдв*rk uмех=1047*0220=1047 мс
Это значение отличается от заданного на 47% что допустимо:
Поставим одну муфту между двигателем и редуктором и между редуктором и колесом. Поэтому: мех=м*р*м=099*094*099=092
Данное значение к.п.д. мало отличается от принятого предварительно поэтому перерасчет мощности не делаем.
По диаметрам концов соединяемых валов выбираем муфты: для быстроходного вала
зубчатую муфту 1-1000-38-2-40-2-2У2 ГОСТ 5006-83. Параметры Тм.н=1000 Н*м
IM=0.05 кг*м2. dлев.мах=dпр.мах=40 мм; m=67 кг. Для тихоходного вала зубчатую муфту
-6300-65-1-80-2-2У2 ГОСТ 5006-83. Параметры Тм.н=6300 Н*м; IM=0.25 кг*м2. dлев.мах=dпр.мах=80 мм; m=226 кг.
Определим сопртивление передвижению тележки без груза создаваемое уконом:
Определим сопртивление передвижению тележки без груза создаваемое инерцией:
Определим сопртивление передвижению тележки без груза создаваемое трением:
Определим момент создаваемый уклоном:
Определим момент создаваемый инерцией:
Определим момент создаваемый силами трения:
Определим расчетный тормозной момент механизма:
Расчетный тормозной момент тормоза равен Тт.р.=Тт.р.мех=08 Н*м.
Выбираем тормоз типа ТГК. Выбираем типоразмер тормоза ТГК-160-У2-50-380-40
ОСТ 24.290.08-82. Имеюший следующие параметры: Тт.н.=98 Н*м; Dт.ш.=160 мм;
Вк=70 мм; Ршт=157 Н; Lуст=200 мм; mтор=25 кг.
12 Выбор тормозного шкива
По диаметру конца вала двигателя и требуемому диаметру шкива выбираем стандартный тормозной шкив 1-го исполнения. Шкив имеет следующие параметры
Dт.ш.=160 мм; Воп=70 мм; d=355 мм; m=49 кг; условное обозначение типоразмера шкива
Ш1-160355 ОСТ 24290.06-75.
Механизм передвижения крана
Выбираем раздельный привод
Вес моста крана равен:
Где Gкр=2156кН конструктивный вес крана по ГОСТ25711-83.
Gкаб=12 кН вес кабины; Gт=618 кН.
Определим значения длин:
Представим кран в виде двухопорной балки и составим уравнения моментов сил относительно опор определим выражения Рмах и Рmin.
Нагрузка на 1 колесо будет равно: Рмах2=31252=15625 кН
По табл. используя выбираем колесо диаметром D=500мм; F=200 кН.
3 Выбор колесных установок
По диаметру колеса выбираем стандартные коленные установки; приводную колесную установку К2РП-500 исполнения 1.и неприводную К2РН-500 имеющие параметры: D=500мм; d=100 мм; dц=110 мм; В=100 мм; mк.упр.=31073 кг; mк.неупр.=29589 кг ; zреб=2. Форма поверхности катания цилиндрическая. Тип подшипника роликовый радиальныи сферический двухрядный с симметричными роликами.
4 Выбор подтележечного рельса
5 Сопротивление передвижению крана
По табл. определим коэф. трения качения =06. Определим приведенный коэф. трения . Скольжения в подшипниках колес f=0.015. При гибком токопроводе тележки kдоп=15. Определим сопротивление сил трения
При скорости движения более 1 мс =115-коэф. учитывающий инерцию вращающихся
а=а(05 10)(а)=(05 1)*01=005..01. Примем а=006
Т.к. двигателя 2 то 7412=37кВт
Выбираем трехфазный асинхронный крановый двигатель АИР112МВ6 имеющий параметры:
N=4кВт; nдв=1000 обмин; dв.дв.=42 мм;
Частота вращения колеса равна: nк=vп*D=16*60(3.14*0.5)=6115 обмин.
Требуемое передаточное число механизма u=nдв nк=10006115=1635. Выберем тип редуктора Ц2У.
Zt=30nt*tмаш=30*6115*6300=116*105
Zp= Zt*ut=116*105*5=58*106
Коэфитциент долговечности: kД=kQ*kt=0.63*0.774=0.49
Значение kД необходимо принять не менее чем 0774. Поэтому kД=0774
Определим расчетный крутящий момент Тр на тихоходном валу редуктора. Будем ориентироваться на редуктор Ц2У-200.Передаточное число равно u=16. что расходиться со значением 22 % на допустимую величину. К.п.д. равно =097
Тдв.ном.=Nдвwдв=75001047=716Н*м
Примем кратность мах. момента фц.мах=2 . То Тп.мах= Тдв.ном* фц.мах=716*2=1432Н*м
Редуктор Ц2У-200 имеет номинальный крутящий момент на тихоходном валу:
ТР.Н.=2500 Н*м. Следовательно условие ТР.Э.≤ТР.Н. выполняется. Кроме указанных
редуктор имеет следующие параметры: аwc=325 мм; dв.быстр=30 мм; dт.в=70 мм; m=170 кг.
8 Определение фактической скорости и к.п.д. механизма
v=wдв*rk uмех=1047*02516=164 мс
Это значение отличается от заданного на 24% что допустимо:
Поставим одну муфту между двигателем и редуктором и между редуктором и колесом. Поэтому: мех=м*р*м=099*097*099=095
зубчатую муфту 1-1600-42-2-30-2-2У2 ГОСТ 5006-83. Параметры Тм.н=1600 Н*м
IM=0.06 кг*м2. dлев.мах=dпр.мах=55 мм; m=92 кг. Для тихоходного вала зубчатую муфту
-10000-70-1-100-2-2У2 ГОСТ 5006-83. Параметры Тм.н=10000 Н*м; IM=0.5 кг*м2. dлев.мах=dпр.мах=100 мм; m=369 кг.
Определим сопртивление передвижению крана без груза создаваемое уконом:
Определим сопртивление передвижению крана без груза создаваемое инерцией:
Определим сопртивление передвижению крана без груза создаваемое трением:
Расчетный тормозной момент тормоза равен Тт.р.=Тт.р.мех=5 Н*м.
11 Выбор тормозного шкива
Расположим центр барабана в начало координатных осей хх и уу на виде сверху устанавливаем корпуса подшипников оси барабана через платики на верхний лист рамы тележки . Далее устанавливаем.
Намечаем пунктиром положения хребтовых балок тележки из условия опирания на них опор барабана стремясь к минимальному смещению центра барабана относительно продольной оси тележки.
Попытаемся расположить верхние блоки и уравнительный балансир со стороны зубчатого зацепления (это значительно уменьшает базу тележки) намечая сход канатов с барабана с противоположной стороны.
Намечаем пунктиром вертикальные поперечные листы рамы таким образом чтобы они воспринимали вертикальную нагрузку от верхних блоков и уравнительного балансира. Намечаем положение вертикальных листов рамы тележки на которые будут.опираться двигатели опора барабана
Для обеспечения лучших условий сцепления приводных колес с рельсами в порожнем состоянии привод механизма передвижения располагаем со стороны барабана главного подъема так как на этой стороне тележки расположено более тяжелое оборудование.
Ориентировочно намечаем положение неприводных ходовых колес и контур рамы тележки. Геометрический центр рамы принимаем за центр тяжести - точка Ор на рис. 12.2. Вес рамы определится разностью между ранее принятым весом тележки и весом оборудования установленного на ней.(табл. 1):
На виде сверху отмечаем центры тяжести всего оборудования и координаты относительно осей хх и уу заносим в табл. Определяем координаты центра тяжести порожней тележки (точка От) по формулам
Теперь уточняем положение неприводных ходовых колес т.е. базу тележки из условия одинаковой нагрузки на приводные и неприводные колеса по формуле :
Окончательно принимаем Вт =2100 мм и поскольку база изменилась (относительно принятой) менее чем на 5% уточнений в положении центров тяжести тележки и груза не производим.
Определяем нагрузки на ходовые колеса тележки в порожнем состояний по формулам:
Нагрузки на ходовые колеса от веса номинального груза главного подъема определяем используя формулы :
Суммарные статические нагрузки на ходовые колеса:
Р1 =193+ 495 = 688 кН;
Р11 =162+ 495 = 657кН
Р2 =146+ 582 =728 кН;
Р12 =1158+ 582 = 6978 кН;
Максимальная разница в нагрузках на колеса
Что является приемлемым. Наносим установочные размеры и габариты после чего можно переходить к конструктивной проработке механизмов.
Редуктор с тормозным шкивом
Передвижения тележки
Проверочные расчеты механизмов
1 Проверка двигателя механизма подъёма на время разгона
Для механизма подъёма груза наибольшее время разгона получается при разгоне на подъём. Его можно определять по приближенной формуле:
где wдв – угловая скорость двигателя радс;
дв=nдв =314750=785радс
Jмех. р – приведённый к валу двигателя момент инерции при разгоне всех движущихся частей механизма включая поступательно движущиеся массы кг·м2;
Тп. ср – средне пусковой момент двигателя Н·м;
Тст. р – момент статических сопротивлений при разгоне приведённый к валу двигателя Н·м.
Значение Тп. ср – определяют по формуле:
где yп. ср – кратность средне пускового момента двигателя
Значение Jмех. р равно:
Здесь Jвр – момент инерции при разгоне всех вращающихся частей механизма приведённый к валу двигателя:
где g=11 12 – коэффициент учёта инерции вращающихся масс расположенных на втором третьем и последующих валах механизма;
J1 – момент инерции вращающихся масс;
Jпост. р – момент инерции при разгоне поступательно движущихся частей механизма плюс груза приведённый к валу двигателя.
Момент инерций тормозного шкива:
Iт.ш=mт.ш*rт.ш.2*Е=237*0162*06=036
В механизме подъёма груза значение Jпост. р определяют следующим образом:
где rб=0225м – радиус барабана по оси навиваемого каната;
uмех – полное передаточное число механизма;
mпост – сумма массы подвески и массы груза;
hмех =088– КПД механизма.
rб =0225– радиус барабана;
uмех – передаточное число механизма;
hмех – КПД механизма
Время разгона механизма подъема груза находится в диапозоне рекомендуемых значений.
Среднее ускорение груза
Это значение не превышает рекомендуемое значение для кранов работающих в механосборочных цехах
2 Проверка двигателя механизма подъёма на нагрев.
где Тэ – эквивалентный момент на валу двигателя при работе с которым его нагрев будет таким же как и при работе с реальными моментами возникающими при подъёме и опускании грузов различного веса Н·м;
Тдв. н – номинальный момент двигателя Н·м.
Значение Тэ определяют по формуле:
где Тст. под j Тст. оп j – соответственно статические моменты на валу двигателя возникающие при подъёме и опускании груза j-го веса Н·м;
tpj – время разгона механизма при работе с грузом j-го веса с;
tу. под tу. оп – соответственно время установившегося движения при подъёме и опускании с;
b - коэффициент учитывающий ухудшение условий охлаждения двигателя в период пуска.
где Gj – вес j-го груза включая вес крюковой подвески Н;
hмех j – КПД механизма при работе с грузом j-го веса.
Значение и количество подъёмов и опусканий за один рабочий цикл принимают по графику нагружения механизма. Можно воспользоваться типовым усреднённым графиком.
Типовой график для группы режима работы 3М показан на рисунке.
Рисунок 1.18- График нагрузок механизмов крана (режим 6М)
Можно принять что за рабочий цикл производится всего 10 подъёмов (опусканий) грузов.
При общем количестве подъёмов (опусканий) за цикл равном десяти получается что в моём случае груз весом G поднимается и опускается 4 раз 0095G – 3 раз 005G- 3 раза.
Допускаем что остановка механизма осуществляется механическим тормозом без участия двигателя.
КПД механизма при работе с грузом j-го веса необходимо определять используя найденное значение КПД hмех при работе с номинальным грузом и график.
Определим моменты при подъёме и опускании:
Момент инерции массы j-го груза включая крюковую подвеску приведённый к первому валу:
mгр j – масса j-го груза.
Приведённый к валу двигателя момент инерции при разгоне всех движущихся частей механизма включая поступательно движущиеся массы:
Допуская что угловая скорость двигателя при работе в установившемся режиме зависит лишь от направления движения груза и не зависит от массы груза получаю:
где wдв – номинальная угловая скорость двигателя;
wс – синхронная угловая скорость двигателя (угловая скорость идеального холостого хода).
где f=50 Гц – частота промышленного трёхфазного тока;
p – число пар полюсов двигателя (значение р легко определить по условному обозначению типа двигателя (последняя цифра в условном обозначении есть число полюсов).
Время разгона при подъёме и опускании можно определить:
Время установившегося движения определяют по формулам:
где Нср – средняя высота подъёма груза.
Для кранов транспортирующих готовую продукцию Нср рекомендуется принимать – 6 м.
Фактические скорости движения груза при подъёме и опускании определяют по формулам:
Полученные результаты заносим в таблицу
Значение параметра при
Условие выполняется т. е. ТэТдв. н (296382).
3 Проверка двигателя механизма передвижения тележки на время разгона.
Определим момент инерции тормозного шкива. Значение коэффициента учитывающего распределенность массы равно = 06. Тогда Jт ш будет равен :
Момент инерции всех вращающихся частей на быстроходном валу механизма будет равен
Сумма поступательно движущихся масс равна тпост = тт+ тгр = 63 + 20 = 263 т = 263*104 кг. mпост – сумма массы подвески и массы груза По формулам находим другие параметры необходимые для расчета:
В механизме передвижения тележки значение Jпост. р определяют следующим образом:
где rк=02м – радиус колеса;
hмех =092– КПД механизма.
Данное значение не превышает рекомендуемого . Следовательно выбранный двигатель обеспечит необходимую интенсивность разгона.
4 Проверка времени торможения механизма передвижения тележки.
Определяем параметры:
Данное значение времени очень велико. Желательно чтобы время торможения тележки не превышало времени разгона. Если принять tт = 5с то необходимо увеличить тормозной момент тормоза. Он должен быть равен 402 Н*м. Тормоз ТКГ-160 необходимо отрегулировать на данный тормозной момент. Характеристика тормоза позволяет это так как Тт.н = 98 Н*м.
5 Проверка запаса сцепления колес тележки с рельсами при разгоне.
При компоновании тележки были получены фактические статические нагрузки на приводные колеса когда тележка не нагружена. Сумма нагрузок на приводные колеса равна Рпр.0 =355 кН. По формулам находим:сила сцепления приводного колеса
где fсц =02- коэфитциент сцепления колес с рельсами.
Момент на оси приводных колес создаваемый уклоном равен :
Момент на оси приводных колес создаваемый силами трения равен :
Здесь гц- радиус цапфы.
Определяем моменты инерции для порожнего состояния тележки:
Сила статического сопротивления движению равна:
Определим коэффициент жесткости тихоходного участка трансмиссии. Максимальный статический момент на тихоходном трансмиссионном валу действующий при передвижении тележки с номинальным грузом на крюке механизма главного подъема равен
В качестве материала трансмиссионного вала принимаем сталь 45. По табл. 2.19 в = 598 МПа. Тогда [] = 003 в = 003 598 = 1794 МПа. По формуле находим диаметр трансмиссионного вала:
Принимаем диаметр конца вала равным 50 мм. Такой диаметр должна также иметь расточка во втулке полумуфты. Тогда диаметр трансмиссионного "вала на наиболее длинном его участке можно принять равным 55 мм. При компоновании тележки было получено значение для ее колеи равное 115 м. Длину одного участка трансмиссионного вала принимаем равной половине колеи т.е. 0575 м. Полярный момент инерции поперечного сечения трансмиссионного вала
Определим коэфитциент жесткости одного участка трансмиссионного вала между зубчатым и ходовым колесами:
Суммарный угловой момент:
Динамический момент которым трансмиссионный вал нагружается при разгоне определим по формуле
Определим коэфитциент запаса сцепления колеса с рельсом:
Так как запас сцепления недостаточен необходимо ввести в схему управления двигателем предпусковую ступень. При этом зазор в передаче нужно выбрать до приложения полного момента двигателя. Динамический момент будет меньше.
Проверим запас сцепления колес с рельсами при разгоне тележки с номинальным грузом на крюке механизма главного подъема. При компоновании тележки была получена нагрузка на приводные колеса в груженом состоянии равная Рпр = 1345 кН. Определим соотвествующие параметры:
Необходимый запас сцепления при разгоне груженой тележки обеспечивается.
6 Проверка двигателя механизма передвижения крана на время разгона.
Сумма поступательно движущихся масс равна тпост = ткр+ тгр = 22 +20т = 42*104 кг. mпост – сумма массы подвески и массы груза По формулам находим другие параметры необходимые для расчета:
где rк=025м – радиус колеса;
hмех =095– КПД механизма.
7 Проверка времени торможения механизма передвижения крана.
Данное значение времени очень велико.Желательно чтобы время торможения тележки не превышало времени разгона. Если принять tт = 5с то необходимо увеличить тормозной момент тормоза. Он должен быть равен 404 Н*м. Тормоз ТКГ-160 необходимо отрегулировать на данный тормозной момент. Характеристика тормоза позволяет это так как Тт.н = 98 Н*м.
Расчеты сборочных единиц.
1 Барабан главного подъема. Толщина цилиндрической стенки.
Принимая в качестве материала барабана сталь 35Л([сж] = 137 МПа определяем приближенное значение толщины стенки барабана:
Уточним полученное значение для чего по формуле (5.2) определим коэффициент влияния деформаций стенки барабана и каната
то допускаемые напряжения смятия необходимо понизить на С=0165*1002=825%
Окончательная толщина цилиндрической стенки :
Из условия технологии изготовления литых барабанов толщина стенки должна быть не менее :
Учитывая что стенка барабана в процессе эксплуатации изнашивается принимаем = 15 мм.
2 Устойчивость цилиндрической стенки барабана
Для определения необходимости проверки устойчивости подсчитываем номинальное напряжение сжатия в стенке барабана:
При этих параметрах из табл. следует что проверку устойчивости стенки необходимо производить если отношение LD6.0 >6.5. Для проектируемого барабана
LD6.0 =1952441.75=4.4 Следовательно проверки устойчивости стенки не требуется.
Расчета стенки на совместное действие изгиба и кручения.
Где Ми – максимальный изгибающий момент.
Тк – крутящий момент; а=075 – коэф. учитывающий различие опасных напряжений изгиба и кручений; Wэ – эквотериальный момент сопротивления сечения барабана.
3 Крепление каната к барабану.
Применяя способ крепления прижимными планками с полукруглыми пазами прижимающими два соседних витка по формуле (5.6) определяем суммарное усилие растяжения болтов
Используя нормализованные планки ПО «Сибтяжмаш» задаемся диаметром болта. М24. Тогда необходимое число болтов (планок) выполненных из стали ВСтЗсп (тек = 230 МПа) будет равно
Принимаем число крепежных болтов z=4
4 Расчёт вала барабана
Соединение вала барабана с входным валом редуктора может производиться при помощи зубчатых муфт допускающих значительную несоосность соединяемых валов. Эти муфты характеризуются высокой надёжностью но имеют большие габариты.
Для предварительного расчёта длину оси барабана можно принять равной:
Нагрузки действующие на ступицы оси:
Принимаем значения длин:
Определение опорных реакций в точках A и B:
Подставляя все значения в формулу получаем:
RA=27.198+23.595-23.8=2699 (кН)
Расчёт оси барабана сводится к определению диаметров цапф dц и ступицы dст из условия работы оси на изгиб в симметричном цикле:
где М – изгибающий момент в расчётном сечении Н·см; W – момент сопротивления расчётного сечения см3; [s]-1 – допускаемое напряжение при симметричном цикле МПа.
Наибольший изгибающий момент под ступицей:
MСТ=M2=RBl2=2380002=4760(Нм)
Момент сопротивления сечения ступицы:
Материалом для оси барабана обычно служит сталь 45 с пределом выносливости s-1=257 МПа. Допускаемое напряжение при симметричном цикле можно определить по упрощённой формуле:
где значение коэффициентов k0=(2.0 28) для валов k0=2 и [n] =14.
Принимаем диаметр ступицы dст=90 (мм).
lст=15dст=15100=150 (мм)
Наибольший изгибающий момент для правой цапфы:
Wц=01dц—момент сопротивления сечения цапфы.
Определяем диаметр сечения цапфы:
Принимаем dц=80 (мм).
Допускаемое напряжение при симметричном цикле работы
Рисунок 1.11- Схема к расчету оси барабана
5 Расчет болтов соединяющих зубчатый венец с барабаном
Соединение обечайки барабана с венцом-ступицей осуществляется болтами (ГОСТ 7817-80) которые испытывают рабочие напряжения среза а также напряжения растяжения и кручения возникающие при сборке узла. Биение посадочной поверхности фланца по отношению к геометрической оси барабана допускается не
более 01 мм на каждые 500 мм диаметра барабана. Размеры венца-ступицы барабана определяются размерами зубчатого венца тихоходного вала выбранного редуктора. Предварительно диаметр окружности установки болтов может быть принят в пределах D = (13 14) D3=(1.3 1.4)280=364 392мм.Берем D=380мм где D3- наружный диаметр зубчатого венца вала редуктора. материал болтов-сталь 45 (т = = 353 МПа)
Окружное срезающее усилие действующее на все болты:
Допускаемое напряжение среза болта:
Задаваясь числом болтов тб = 6 по формуле (5.11) определяем их диаметр:
Принимаем диаметр болта d=11 мм. Напряжение смятия
где bСМ = 28 мм расчетная длина болта. Прочность болтов на смятие обеспечена так как допускаемые напряжения смятия болтов выполненных из стали 45 [см] = 280 МПа.
6 Ходовые колеса тележки.
Колеса предварительно выбранных колесных установок К2РП и К2РН проверяем на напряжения в контакте обода и рельса. Принимая материал .колес сталь марки 70 Л (с закалкой до твердости 300 350 НВ) и условия работы крана - на металлических опорах определяем коэффициенты входящие в формулу
Кд=1+аv=1+015*1047=1157
Напряжения в контакте обода:
Так как значение допускаемого напряжения при числе циклов нагружения N 104 для
выбранного материала колес в табл. 5.6 отсутствует то допускаемые напряжения определяем по формуле:
Для литых колес полученное значение следует уменьшить на 40%:
Усредненная скорость движения тележки vc= р Vт = 087 1.047 =0.91 мс.
Полное число оборотов колеса за срок службы при машинном времени Т= 3200 ч
Nc=36*104*0.91(3.14*20)*3200=16.69*106
Значение коэффициента определяем по таблице в зависимости от отношения минимальной: нагрузки на колесо к максимальной при 11.5872.8 = 016; =015. Приведенное число оборотов колеса за срок службы N=0.15*16.69*106=2.5*106
Допускаемое контактное напряжение определяем по формуле:
Поскольку = 351.4 МПа [N] = 420.2 МПа условия прочности удовлетворяются.
7 Установка конечного выключателя механизма передвижения тележки.
В качестве конечного выключателя применяем рычажный выключатель с самовозвратом тип КУ 701 который включаем в цепь управления двигателя. Поскольку положение выключателя зависит от тормозного пути определяем приведенный момент сопротивления передвижению тележки в порожнем состоянии и время торможения:
Тогда тормозной путь с учетом времени отключения тормоза t3 = 1 ; SТ = 1047 (2.92 + 1) =2.56 м.
Ввиду того что тележка обладает большой кинетической энергией применение двусторонних буферов затруднено из-за их больших размеров. Поэтому устанавливаем четыре односторонних буфера на мосту крана а на тележке - упоры в местах крепления букс ходовых колес к раме тележки. Тогда расстояние между упорами на тележке :
б=Вт- 2*lку= 21 – 2*018=174
Длина линейки из условия удержания рычага выключателя в повернутом положении на пути выбега тележки
Принимаем 1л = 13 м.
Положение конечного выключателя относительно буферов установленных на мосту крана
8 Буферные устройства тележки.
Так как скорость тележки Vт = 1047 мс 117 мс (см. § 5.4) применяем пружинные буферы одностороннего действия.
Максимальное замедление тележки в процессе наезда на буферы принимаем ат = 14 мс2. Скорость тележки в момент наезда на буферы при отключении двигателя в середине тормозного пути
vб = 0707 Vт = = 0707*1.047 = 074 мс.
Коэффициент сопротивления передвижению тележки
Теперь задавшись значением предварительного поджатия пружины буфера SП = 10 мм определяем силу пружины при максимальной ее деформации :
Рабочий ход пружины :
По этим исходным данным рассчитываем пружину буфера. Принимая для пружины пруток круглого сечения из стали марки 60С2А с углом подъема средней винтовой линии витков а = 12° определяем допускаемое напряжение:
где ['] = 735 МПа- допустимое касательное напряжение при действии статической нагрузки кнаг = 06-коэффициент учитывающий характер приложения нагрузки. Подбираем пружину:
Для силы Рк490 = 46906 Н подходит пружина из прутка d = 25 мм с индексом С =Dcd = 4. Средний диаметр пружины Dc = 100 мм.
Проверяем пружину на прочность. Напряжение кручения в материале пружины:
Здесь кс = 10+ 15С=10 ++ 154 = 1375-коэффициент кривизны пружины.
Необходимое число витков
где G = 78400 МПа-моду ль сдвига для принятой марки стали
Общее число витков пружины z0 = zВ + 15 = 34 + 15 = 35.5.
Длина разгруженной пружины Н0 =zв t +d=34*38.4 + 25 = 1330 мм.
Шаг витков пружины:
Уточненные расчеты механизмов
1 Расчет времени разгона механизма главного подъема
при автоматизированном линейно-ступенчатом запуске приводного электродвигателя.
Кратности перегрузок пер и тах подбираем исходя из выполнения соотношения
Из ранее выполненных расчетов момент от сил статических сопротивлений Тст = 509 Н м.
Проверим по условию
что соответствует требованию условия. Номинальное скольжение естественной характеристики выбранного электродвигателя равно 005.
При числе переключений с одной искусственной характеристики электропривода на другую z = 4 по формуле имеем
Скорость на естественной характеристике соответствующая моменту Tпер по формуле :
Из ранее выполненных расчетов суммарный приведенный момент инерции вращающихся частей механизма и груза J = 1.84 кг-м2.
Время разгона (до скорости на естественной характеристике соответствующей моменту Тпер :
2 Определение вероятности неразрушения каната
механизма подъема по несущей способности.
Выбранный канат имеет диаметр dк=16.5 мм маркировочная группа-1470 МПа. Расчетная площадь сечения всех проволок SК = 104.61 мм2. Разрывное усилие каната в целом F = 130000 Н. При определении вероятности неразрушения каната за максимальную расчетную нагрузку примем нагрузку стопорного нагружения порожнего механизма при крайнем верхнем положении крюковой подвески:
Коэффициент жесткости канатов при модуле упругости Ек = 1177*106 Нсм2 (1177 1010 Па) и расстоянии от оси блоков крюковой подвески до осей неподвижных блоков и барабана в крайнем верхнем положении крюковой подвески Н = 082 м -коэф. жесткости каната
Момент инерции вращающихся частей механизма J = 1.84 кг-м2 приведенная масса вращающихся частей:
т1 =4Iu2Dб2=4*1.84*1002* 0.880.452= 319842кг
Среднепусковой момент:
Среднепусковая сила электродвигателя приведенная к грузу
На колебания нагрузки двигателя влияет большое число равнозначных факторов поэтому распределение этой нагрузки близко к нормальному и значение среднепусковой силы принимаем за математическое ожидание нагрузки электродвигателя P>=242*103 Н
Максимальные нагрузки двигателя Ттлх = 652 Н-м Рмах = 304* 103 Н.
Минимальные нагрузки двигателя Тт1п =ТН пер = 5159 Н*м; Рт1п =1788*103 Н.
Предельные значения стопорной нагрузки канатов найдем по формуле:
Поскольку зависимость стопорной нагрузки от усилия электродвигателя слабонелинейная можно считать распределение стопорной нагрузки канатов нормальным. Статистические характеристики нагрузки:
Разбег предела прочности канатной проволоки типа В маркировочной группы 1470 МПа равен 1470 1755 МПа .
Таким же будет и разбег разрывного усилия:
Статистические характеристики разрывного усилия канатной подвески:
математическое ожидание
среднеквадратическое отклонение
Математическое ожидание нормально распределенного резерва прочности
Среднеквадратическое отклонение резерва прочности
Вероятность безотказной работы (или прочностная надежность)
Применяем замену переменной чтобы привести интеграл к табличному виду:
Нижнее значение предела интегрирования для новой переменной:
Поэтому нужный нам дляфасчета интеграл будет равен:
В соответствии с РТМ 24.090.25-76 для кранов общего назначения должно выполняться условие Р> [Р] = 099 что и соблюдается в данном случае.
3 Расчет совместного нагружения канатов механизма главного подъема и моста при стопорении порожнего крюка.
-коэф. жесткости каната
т1 =4Iu2Dб2=4*1.84*1002* 0.880.452= 319842кг- приведенная к грузу масса вращ. частей механизма
- приведенная к середине пролета масса моста
GM=141.8 кН- приведенный вес моста
- коэф. жесткости моста
v = 0177 мс. – скорость подьема
Частоты собственных колебаний найдем по формулам
Частные решения найдем по формулам:
Амплитуды гармонических составляющих найдем по формулам:
Наибольшие нагрузки в канатах и мосту найдем по формулам:
Эти же нагрузки при W= 0 без учета податливости моста найдем по формуле:
Пренебрежение податливостью моста дает в данном случае существенное завышение нагрузок:
т. е. на 05% для канатов и на 09% для моста.
Таким образом учет податливости моста в данном случае не существен.
4 Определение вероятности неразрушения каната
Коэффициент жесткости канатов при модуле упругости Ек = 1177*106 Нсм2 (1177 1010 Па) и расстоянии от оси блоков крюковой подвески до осей неподвижных блоков и барабана в крайнем верхнем положении крюковой подвески Н = 082 м с = 16932
Поэтому нужный нам для расчета интеграл будет равен:
ВБР канатной подвески при стопорении груза 099948 =ё 0995. В соответствии с РТМ 24.090.25-76 для кранов общего назначения должно выполняться условие Р ^ «* [Р] = 099 что и соблюдается в данном случае.'
БИБЛИОГРАФИЧЕСКИЙ СПИСОК
Курсовое проектирование грузоподъемных машин С.А.Казак В.Е.Дусье Е.С.Кузнецов и др.; Под ред. С.А.Казака. – М.: Высш. шк. 1989.- 319 с.: ил.
Подъемно-транспортные машины: Атлас конструкций М.П.Александров Д.Н.Решетов и др. - М. Машиностроение 1987. –122 с.
Руденко Н.Ф. Грузоподъемные машины: Атлас конструкций. – М. Машиностроение 1970 116 с.
Механизм подьема груза
1 Выбор кинематической схемы ..1
2 Выбор крюковой подвески 2
4 Основные размеры «Установки верхних блоков» 3
5 Основные размеры уравнительного балансира .4
6 Основные размеры «Установки барабана» ..5
7 Выбор двигателя .6
9 Выбор соединительной муфты .8
10 Выбор тормоза ..8
11 Выбор муфты с тормозным шкивом ..8
Механизм передвижения тележки
1 Выбор киематической схемы 9
2 Статические нагрузки на колеса 9
4 Выбор колесных установок 9
5 Выбор подтележечного рельса .10
6 Сопротивление передвижению тележки .10
7 Выбор двигателя 10
9 Определение фактической скорости 12
11 Выбор тормоза .12
12 Выбор тормозного шкива 13
Механизм передвижения крана
1 Выбор кинематической схемы .14
3 Выбор колесных установок ..14
4 Выбор подтележечного рельса .14
5 Сопротивление передвижению тележки .14
6 Выбор двигателя 15
8 Определение фактической скорости 16
10 Выбор тормоза ..16
11 Выбор тормозного шкива 17
Компоновка тележки .18
Проверочные расчеты механизмов
1 Проверка двигателя механизма подьема на время разгона 21
2 Проверка двигателя механизма подьема на нагрев .23
3 Проверка двигателя механизма передвижения тележки на время разгона ..27
4 Проверка времени торможения механизма передвижения тележки .28
5 Проверка запаса сцепления колес тележки с рельсом 29
6 Проверка двигателя механизма передвижения крана на время разгона ..32
7 Проверка времени торможения механизма передвижения крана .33
Расчеты сборочных единиц.
1 Барабан главного подьема .35
2 Устойчивость цилиндрической стенки барабана 35
3 Крепление каната к барабану 36
4 Расчет вала барабана ..37
5 Расчет болтов соединяющих зубчатый венец с барабаном 39
6. Проверка ходовых колес тележки ..40
7 Установка конечного выключателя механизма передвижения тележки ..41
8 Буферные устройства тележки ..42
Уточненные расчеты механизмов.
1 Расчет времени разгона механизма главного подъема .44
при автоматизированном линейно-ступенчатом запуске приводного электродвигателя
механизма подъема по несущей способности .44
3 Расчет совместного нагружения канатов механизма главного подъема и моста
при стопорений порожнего крюка ..47
механизма подъема по несущей способности 48