Модернизация мельницы МШР 2,6х13




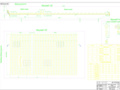
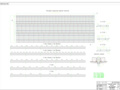
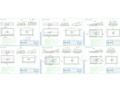
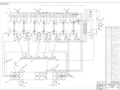
- Добавлен: 25.10.2022
- Размер: 4 MB
- Закачек: 2
Описание
Состав проекта
![]() |
![]() |
![]() ![]() |
![]() ![]() ![]() ![]() |
![]() ![]() ![]() ![]() |
![]() ![]() ![]() ![]() |
![]() ![]() ![]() ![]() |
![]() ![]() ![]() ![]() |
![]() ![]() |
![]() ![]() |
![]() ![]() ![]() ![]() |
![]() ![]() ![]() ![]() |
![]() ![]() ![]() ![]() |
![]() ![]() |
![]() ![]() |
![]() ![]() ![]() ![]() |
![]() ![]() ![]() ![]() |
![]() ![]() ![]() ![]() |
![]() |
![]() ![]() ![]() |
Дополнительная информация
электричество.dwg

тех.схема.dwg

все брони.dwg

Спец для мельницы.dwg

Спецификация.dwg

новфут.dwg

7_Таблица_ТЭП.dwg

форма в сборе.dwg

Схема трубной мельницы.dwg

футеровка старая.dwg

модель.dwg
