Модернизация комбинированного редуктора вертикальной клети стана 500




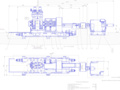
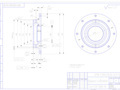
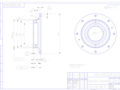
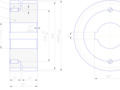
- Добавлен: 25.10.2022
- Размер: 6 MB
- Закачек: 1
Описание
Состав проекта
![]() |
![]() |
![]() ![]() |
![]() ![]() |
![]() ![]() ![]() ![]() |
![]() ![]() |
![]() ![]() |
![]() ![]() ![]() ![]() |
![]() ![]() ![]() ![]() |
![]() ![]() ![]() ![]() |
![]() ![]() |
![]() ![]() ![]() ![]() |
![]() ![]() |
![]() ![]() |
![]() ![]() ![]() ![]() |
![]() |
![]() ![]() |
![]() ![]() ![]() ![]() |
![]() ![]() ![]() ![]() |
![]() ![]() |
![]() ![]() ![]() ![]() |
![]() ![]() ![]() |
![]() ![]() |
![]() ![]() |
![]() ![]() |
![]() ![]() ![]() |
![]() ![]() |
![]() ![]() |
![]() ![]() ![]() ![]() |
![]() ![]() |
![]() ![]() ![]() ![]() |
![]() ![]() ![]() ![]() |
![]() ![]() ![]() ![]() |
![]() ![]() |
![]() ![]() ![]() ![]() |
![]() ![]() ![]() ![]() |
![]() ![]() ![]() ![]() |
![]() ![]() |
![]() ![]() |
![]() ![]() |
![]() ![]() ![]() ![]() |
![]() ![]() ![]() ![]() |
![]() ![]() |
![]() ![]() |
![]() ![]() |
![]() ![]() |
![]() ![]() ![]() ![]() |
![]() ![]() |
![]() ![]() ![]() ![]() |
![]() ![]() |
![]() ![]() |
![]() ![]() |
![]() ![]() |
![]() ![]() |
![]() ![]() ![]() ![]() |
![]() ![]() ![]() ![]() |
![]() ![]() |
![]() |
![]() ![]() ![]() |
![]() ![]() ![]() |
![]() ![]() ![]() |
![]() ![]() ![]() |
![]() |
![]() ![]() ![]() |
![]() ![]() |
![]() ![]() ![]() |
![]() ![]() ![]() |
![]() ![]() |
![]() ![]() ![]() |
![]() ![]() ![]() |
![]() |
![]() ![]() ![]() |
![]() ![]() ![]() |
Дополнительная информация
Шестерня нижняя в сборе.dwg

Шестерня дополнительная верхняя.dwg

Крышка сквозная.dwg

Валок шестеренный нижний.dwg

Клеть шестеренная после модернизации.dwg

Валок шестеренный верхний.dwg

Ведомость диплома лист1.dwg

Ведомость диплома лист2.dwg

вертикальная клеть в сборе.dwg

Вал верт (1). лист 1cdw.dwg

Чертеж.dwg

комб р-р 1.dwg

вал быстроходный.dwg

Комб р-р 2.dwg

Вал верт (1) лист 2.dwg

Общий вид клети.dwg

Чертеж зацепления.dwg

Вал верхний.dwg

Вал нижний.dwg

Крышка глухая.dwg

Шестерня осн. верхняя.dwg

Шестерня верхняя в сборе.dwg

Шестерня дополнительная нижн..dwg

Шестерня осн. нижн..dwg

Рекомендуемые чертежи
- 19.12.2016
Свободное скачивание на сегодня
- 22.08.2014
- 29.08.2014