Модернизация комбайна ДОН – 2600 с разработкой аксиально-роторного МСУ




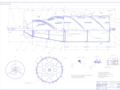
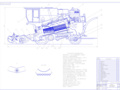
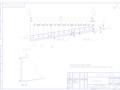
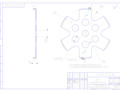
- Добавлен: 25.10.2022
- Размер: 1 MB
- Закачек: 1
Описание
Состав проекта
![]() |
![]() |
![]() ![]() ![]() |
![]() ![]() ![]() ![]() |
![]() ![]() ![]() ![]() |
![]() |
![]() ![]() ![]() |
![]() ![]() ![]() ![]() |
![]() ![]() ![]() ![]() |
![]() ![]() ![]() |
![]() ![]() ![]() |
![]() |
![]() ![]() ![]() |
![]() ![]() ![]() |
Дополнительная информация
5 начало сборки ротора А1.cdw

3 Вид общий А1.cdw

Диск крепления.cdw

Планка.cdw

Рекомендуемые чертежи
- 26.04.2015
- 29.07.2014
- 25.10.2022