Модернизация клапана холодного дутья




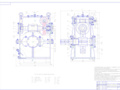
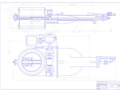
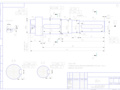
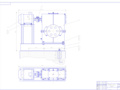
- Добавлен: 25.10.2022
- Размер: 2 MB
- Закачек: 0
Описание
Состав проекта
![]() |
![]() |
![]() ![]() ![]() ![]() |
![]() ![]() ![]() ![]() |
![]() ![]() |
![]() ![]() |
![]() ![]() |
![]() ![]() ![]() ![]() |
![]() ![]() |
![]() ![]() |
![]() ![]() ![]() ![]() |
![]() ![]() ![]() ![]() |
![]() ![]() |
![]() ![]() |
![]() ![]() ![]() ![]() |
![]() ![]() |
![]() ![]() ![]() ![]() |
![]() ![]() ![]() ![]() |
![]() ![]() |
![]() ![]() ![]() ![]() |
![]() |
![]() ![]() ![]() |
Дополнительная информация
Редуктор червячный двухступенчатый.dwg

Деталировка.dwg

СПЕЦИФИКАЦИЯ КЛАПАН ХОЛОДНОГО ДУТЬЯ.dwg

Муфта предельного момента.dwg

СПЕЦИФИКАЦИЯ НА РЕДУКТОР_ЛИСТ 2.dwg

Муфта.dwg

Общий вид.dwg

Общий вид привода.dwg

Спецификация общего вида привода_лист 1.dwg

Рекомендуемые чертежи
- 02.10.2013
- 19.12.2016
- 05.11.2021
Свободное скачивание на сегодня
- 28.08.2024