Разделение смеси муравьиная кислота - уксусная кислота ректификацией


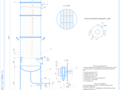
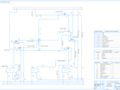
- Добавлен: 25.01.2023
- Размер: 657 KB
- Закачек: 0
Узнать, как скачать этот материал
Подписаться на ежедневные обновления каталога:
Описание
Разделение смеси муравьиная кислота - уксусная кислота ректификацией
Состав проекта
![]() |
![]() ![]() ![]() ![]() |
![]() |
![]() ![]() ![]() |
![]() ![]() ![]() ![]() |
Дополнительная информация
Контент чертежей
колонна 3000.cdw

Техническая характеристика
Аппарат предназначен для разделения смеси муравьинная кислота
- уксусная кислота с концентрацией низкокипящего компонента
Емкость номинальная 183 м
Производительность 11 тч
Давление в колонне 0
Температура в кубе 110
Среда в аппарате токсичная
Тип тарелок - колпачковые.
Технические требования.
испытании и поставке аппарата должны
выполняться требования:
3 - 76 " Оборудование производственное. Общие
требования безопасности ".
б) ОСТ 26 - 291 - 79 "Сосуды и аппараты стальные сварные.
Технические требования".
Материал тарелок и частей колонны соприкасающиеся с
разделяемыми жидкостями или их парами из стали 12Х18Н10Т ГОСТ
остальные элементы колонны - из стали СТ 3. ГОСТ
Аппарат испытать на прочность гидравлически:
а) в горизонтальном положении - давлением 0
б) в вертикальном положении - наливом.
Сборные соединения должны соответствовать требованиям ОН
-01-71-68 "Сварка в химическом машиностроении". Сварку
производить электродами марки АНО-5-4
Сборочные швы в объеме 100% контролировать
рентгенопросвечиванием.
Действительное расположение штуцеров и цапф смотри на
Размеры для справок
Вход парожидкостной смеси
Выход жидкости из куба
Для выхода кубового остатка
Схема расположения штуцеров и цапф
пояснительная ректификация МК-УК.docx
Государственное образовательное учреждение высшего
профессионального образования
Казанский национальный исследовательский технологический университет
Кафедра процессов и аппаратов химической технологии
РЕКТИФИКАЦИОННАЯ КОЛОННА
Пояснительная записка к курсовому проекту
Описание функциональной схемы
Технологический расчет
Конструктивный расчет .
Гидравлический расчет ..
Механический расчет .
Техника безопасности
В химической технологии широко распространены и имеют важное значение процессы массопередачи характеризуемые переходом одного или нескольких веществ из одной фазы в другую. Путем переноса одного или более компонентов из фазы в фазу можно разделять как гетерогенные так и гомогенные системы (газовые смеси жидкие растворы и др.) причем наиболее часто процессы массопередачи используют для разделения гомогенных систем.
Одним из наиболее распространенных методов разделения жидких однородных смесей состоящих из двух или большего числа компонентов является перегонка (дистилляция и ректификация).
Простая перегонка представляет собой процесс однократного частичного испарения жидкой смеси и конденсации образующихся паров. Простая перегонка применима только для разделения смесей летучести компонентов которой существенно различны.
Значительно более полное разделение жидких смесей на компоненты достигается путем ректификации.
Ректификация представляет собой процесс многократного частичного испарения жидкости и конденсации паров. Процесс осуществляется путем контакта потоков пара и жидкости имеющих различную температуру и проводится обычно в колонных аппаратах.
Ректификация известна с начала 19 века как один из важнейших технологических процессов главным образом спиртовой и нефтяной промышленности. В настоящее время ректификацию всё шире применяют в самых различных областях химической технологии где выделение компонентов в чистом виде имеет весьма важное значение (в производствах органического синтеза изотопов полимеров и др.)
Процессы перегонки осуществляется периодически или непрерывно.
Процесс ректификации протекает на поверхности раздела фаз поэтому аппараты должны обеспечивать развитую поверхность соприкосновения между жидкостью и газом.
По способу образования этой поверхности ректификационные аппараты можно разделить на следующие группы: 1) поверхностные и плёночные; 2) насадочные; 3) барботажные (тарельчатые); 4) распыливающие.
Тарельчатые ректификационные колонны нашли широкое распространение в промышленности. В настоящее время применяются разнообразные конструкции тарелок. По способу слива жидкости с тарелки их можно подразделить:
) тарелки со сливными устройствами;
) тарелки без сливных устройств.
К тарелкам со сливными устройствами относятся: ситчатые колпачковые клапанные и балластные пластинчатые.
В тарелке без сливных устройств газ и жидкость проходят через одни и те же отверстия или щели. На тарелке одновременно с взаимодействием жидкости и газа путем барботажа происходит сток части жидкости на нижерасположенную тарелку – «проваливание» жидкости. Поэтому тарелки такого типа обычно называют провальными. К ним относятся дырчатые решётчатые трубчатые и волнистые тарелки.
Выбор конкретного вида тарелки зависит от многих факторов например гидравлическое сопротивление тарелки диапазон устойчивой работы эффективность производительность по жидкости и газу и т.д.
Ситчатые тарелки обладают невысоким сопротивлением большой эффективностью и
интенсивностью требуют малого расхода металла и легкости монтажа.
Колпачковые тарелки обладают достаточно большой областью работы большой эффективностью и обеспечивают легкость пуска и остановки аппарата.
Клапанные тарелки обладают большой областью устойчивой работы малым брызгоуносом требуют малого расстояния между тарелками имеют высокую интенсивность и эффективность.
Описание функциональной схемы
Исходная смесь поступает в накопительную ёмкость Е1 необходимую для равномерного питания ректификационной колонны РК. Насосом Н1 смесь подаётся на питающую тарелку в РК проходя через теплообменник – подогреватель П. В подогревателе исходной смеси смесь подогревается до температуры кипения за счет подачи в межтрубное пространство греющего пара. Поступающая в РК при температуре кипения исходная смесь стекает по тарелкам в нижнюю часть колонны. На каждой ступени (тарелке) происходит взаимодействие жидкости стекающей вниз и паров поднимающихся вверх по колонне при этом из паров конденсируется высококипящий компонент (ВК) а из жидкости испаряется низкокипящий компонент (НК). В результате такого взаимодействия на каждой ступени в конечном счёте с верхней части колонны выходит практически чистый НК а из кубовой части колонны удаляется ВК. Пары в кубе получают путём испарения кубовой жидкости в теплообменнике – кипятильнике К. Пары отводимые с верхней части колонны направляются в теплообменник – конденсатор Д. За счет подачи охлаждающей воды в трубное пространство пары конденсируются и отводятся из аппарата при температуре конденсации. Далее поток конденсата разделяется на две части: флегму и дистиллят. Под флегмой понимают часть конденсата возвращающегося в верхнюю часть колонны для её орошения. Дистиллят – готовый продукт (целевой) который с начало охлаждают в теплообменнике – холодильнике Х2 а потом подают в накопительную ёмкость Е3. Насосом Н4 дистиллят перекачивается к потребителю. Кубовый остаток (ВК) отводится с куба и направляется в теплообменник – холодильник Х1 после чего накапливается в ёмкости Е2 откуда насосом Н3 перекачивается к потребителю.
Ректификационная установка является сложным управляемым объектом поэтому включает в себя большое количество приборов КИП и автоматики систему предупреждающей и аварийной сигнализации а также блокировки.
Технологический расчет
Задание: Рассчитать и спроектировать ректификационную колонну непрерывного действия с колпачковыми тарелками для разделения смеси уксусная кислота - муравьиная кислота состоящей из XF = 36 (масс. %) низкокипящего компонента. Производительность по исходной смеси G = 11 тч. Начальная температура исходной смеси 18о С. Концентрация низкокипящего компонента (НК) в дистиляте XD = 95 (масс. %) в кубовом остатке XW = 15 %. Давление греющего пара P = 50 кгс см2. tDконд. = tWконд.= 20о.
1. Материальный баланс колонны и рабочее флегмовое число
Производительность колонны по дистилляту Р и кубовому остатку W определим из уравнений материального баланса колонны:
Переводим массовые концентрации в мольные доли:
масса муравьиной кислоты;
масса уксусной кислоты.
Относительный мольный расход питания:
По данным [3 или 2 c.526] строим равновесную кривую на рис. 1
Минимальное флегмовое число:
Для определения оптимального флегмового числа производим следующее:
Пусть = 105 – коэффициент избытка флегмы тогда рабочее флегмовое число
R = Rmin = 105 5717 = 6002
Уравнение рабочей прямой верхней части колонны:
N = 685; N(R+1) = 685 (6002+1) = 47967
Пусть = 15 тогда R = Rmin = 15 5171 = 8575
N = 37; N(R+1) = 37 (8575+1) = 35427
Пусть = 18 тогда R = Rmin = 2 5171 =11433
N = 17 N(R+1) = 18 (2054+1) = 565
Пусть = 25 тогда R = Rmin = 25 5171 = 14292
N = 275; N(R+1) = 275 (14292+1) = 42052
Пусть = 3 тогда R = Rmin = 3 5171 = 1715
N = 256; N(R+1) = 256 (1715+1) = 46464
Полученные результаты сводим в таблицу:
По данным таблицы строим график рис. 7 и определяем оптимальное рабочее флегмовое число принимаем Rопт = 9 тогда уравнения рабочих прямых:
строим их на рис. 6.
Средние массовые расходы по жидкости для верхней и нижней частей колонны определяют из соотношений:
- мольная масса дистиллята.
- мольная масса исходной смеси;
- средние мольные массы жидкости для верхней и нижней частей колонны:
здесь средние концентрации:
= 02213 46 + (1 – 02213) 60 = 569 тогда
Средние массовые потоки пара в верхней и нижней частях колонны:
здесь - средние мольные массы паров в верхней и нижней частях колонны:
здесь средние концентрации паров определяем из уравнений рабочих прямых:
2 Скорость пара и диаметр колонны
Определяем средние температуры паров и жидкости по данным равновесия литературы [2 c.526]:
Плотность пара для верхней части колонны:
Плотность смеси жидкости в верхней части колонны:
здесь концентрации в объемных долях при 1043 °С плотности компонентов: - муравьиная кислота - уксусная кислота [2 c.495].
тогда плотность смеси:
Плотности компонентов при 1112°С по [2 c.495]: - муравьиная кислота - уксусная кислота.
Объемная концентрация:
Тогда плотность смеси:
Максимальная скорость пара и диаметр верхней части колонны
Принимаем расстояние между тарелками Н=400 мм. Последующим расчетом проверим правильность принятого значения.
Объемный расход пара
k1=1 (для колпачковых тарелок) [2 с. 118]
с1=520 [4 с. 119 рис. III-3]
(для колпачковых тарелок) [4 с. 118]
3.4. Максимально допустимая скорость пара
Диаметр верхней части колонны
Максимальная скорость пара и диаметр нижней части колонны
Максимально допустимая скорость пара
Диаметр нижней части колонны
Выбор диаметра колонны
Из двух найденных диаметров и выбираем максимальный () и в соответствии с этим выбираем из принятого в химической промышленности нормального ряда диаметров колонн [4 с. 122]. При этом диаметре колонны расстояние между тарелками выбрано правильно [4 с. 115].
Выберем тарелку типа ТСК-Р по ОСТ 26-808–73 для колонны диаметром
Основные характеристики тарелки:
Свободное сечение колонны м2 – 707
Рабочее сечение колонны м2 – 239
Длина линии барботажа м – 804
Периметр слива м – 239 (Lсл)
Сечение перелива м2 – 0902
Свободное сечение тарелки м2 – 0849
Относительная площадь для прохода паров FC % – 121
Средняя скорость паров в колонне при этом:
Здесь - средний расход пара;
Скорость пара в рабочем сечении тарелки:
3 Высота светлого слоя жидкости на тарелке и паросодержание
Для колпачковых тарелок высоту слоя жидкости h0 находим по формуле для верхней части колонны:
Для нижней части колонны:
= 003м – высота сливной перегородки;
- удельный расход жидкости на 1 метр ширины сливной перегородки в верхней части колонны;
- удельный расход жидкости на 1 метр ширины сливной перегородки в нижней части колонны;
Паросодержание барботажного слоя находят по формуле:
Тогда для верхней части колонны:
для нижней части колонны:
4.Коэффициенты диффузии и вязкости паров
Коэффициенты диффузии в жидкости для верхней части колонны:
здесь вязкости муравьиной и уксусной кислот взяты при 20°С [2 c.500].
здесь плотности муравьиной и уксусной кислот взяты при 20°С [2 c.495].
А = 127 В = 1 [2 c.278].
v1 = 462 – мольный объем муравьиной кислоты;
v2 = 684 – мольный объем уксусной кислоты [2 c.278].
Коэффициент диффузии в жидкости для нижней части колонны:
здесь вязкости метилового спирта и воды взяты при 20°С [2 c.500].
Коэффициент диффузии паров в верхней части колонны:
Коэффициент диффузии паров в нижней части колонны:
Коэффициент вязкости паров в верхней части колонны:
Здесь взяты вязкости паров муравьиной и уксусной кислот при 1033°С [4].
Коэффициенты вязкости паров нижней части колонны:
5 Коэффициенты массопередачи и высота колонны
Коэффициент массопередачи в жидкости для верхней части колонны:
Коэффициент массопередачи в жидкости для нижней части колонны:
Коэффициент массопередачи в паровой фазе для верхней части колонны:
Коэффициент массопередачи в паровой фазе для нижней части колонны:
Переводим полученные коэффициенты массопередачи в нужную размерность на :
Расчет КПД методом Мерфи.
Пусть х = 06. Коэффициент распределения компонента по фазам (тангенс угла наклона равновесной линии в этой точке) m = 08745
Коэффициент массопередачи:
Общее число единиц переноса на тарелку:
Локальная эффективность:
Фактор массопередачи:
Доля байпасирующей жидкости:
При факторе скорости ; [5 c.202]
Число ячеек полного перемешивания:
здесь L = 035м – длина пути жидкости соответствующей одной ячейке перемешивания.
Коэффициент m который влияет на унос жидкости с тарелки:
а) верхняя часть колонны:
б) нижняя часть колонны:
Комплекс по которому определяем унос жидкости с тарелки при Н = 04м – расстояние между тарелками:
Аналогичные расчеты проводим и для других точек результаты сводим в таблицу.
Нижняя часть колонны
Верхняя часть колонны
По данным таблицы строим кинетическую линию на рис. 6. По рисунку определим что число действительных тарелок 26.
Nв = 36шт. – в верхней части колонны;
Nн = 22– в нижней части колонны.
Высота тарельчатой части колонны определяется по формуле:
Н = h · (n – 1) + Zв + Zн = 04 · (58 – 1) + 1 + 2 = 258 м здесь
Zв=1м – высота сепарационного пространства;
Zн=2м – высота кубовой части [1 c.235].
Конструктивный расчет
Диаметр штуцера для ввода исходной смеси:
Здесь - скорость потока жидкости при подачи насосом [1 c.16]
- плотность исходной смеси при [2 c.495]:
Диаметр штуцера для вывода паров из колонны:
Здесь - плотность паров на вверху колонны;
- скорость потока насыщенных паров [1 c.16].
Диаметр штуцера для ввода флегмы:
Здесь - расход флегмы;
- скорость при перекачивании насосом [1 c.16];
- плотность при [2 c.495]:
Диаметр штуцера для ввода паров из кипятильника:
Здесь - скорость насыщенных паров [1 c.16];
Диаметр штуцеров для слива кубового остатка и жидкости из куба для подачи в кипятильник:
Здесь - скорость потока при движении самотеком [1 c.16];
- плотность кубового остатка при 80°С [2 c.495]:
Гидравлический расчет
Гидравлическое сопротивление тарелок колонны определяет по формуле:
где и гидравлическое сопротивление тарелки соответственно верхней и нижней частей колонны Па.
Полное гидравлическое сопротивление тарелки складывается из трех слагаемых:
) Гидравлическое сопротивление сухой колпачковой тарелки [1 c.244]:
Здесь - коэффициент сопротивления сухой ситчатой тарелки [1 c.210]
) Гидравлическое сопротивление газожидкостного слоя на тарелках различно для верхней и нижней частей колонны:
) Гидравлическое сопротивление обусловленное силами поверхностного натяжения:
Тогда полное гидравлическое сопротивление одной тарелки верхней и нижней частей колонны равно:
Полное гидравлическое сопротивление ректификационной колонны:
Корпуса аппаратов чаще всего работают в условиях статистических нагрузок под внутренним избыточным давлением вакуумом или наружным избыточным давлением.
1 Цилиндрические обечайки
Толщина стенки обечайки:
D = 3000 мм – диаметр обечайки;
р = 01 МПа – давление в аппарате;
φ = 10 – коэффициент сварного шва [1 с. 395];
с = П · Та = 01 · 10 = 1 мм – прибавка на коррозию где
П = 01 ммгод – скорость коррозии;
Та = 10 лет – срок службы аппарата;
[] = · - допускаемое напряжение;
= 10 – коэффициент [1 с. 394];
= 152 МПа – допускаемое нормативное напряжение для стали 08Х1713М2Т [4 с. 11] тогда
S ≥ по [1 с. 211] принимаем S = 10 мм.
2 Расчет днищ и крышек
Эллиптическая крышка рассчитываются по формуле.
P = 01 МПа – давление в аппарате;
с = П · Та = 01 · 10 = 1мм – прибавка на коррозию где
по [1 с. 211] принимаем S = 10 мм.
Расчет ведем по [3 с. 691]:
При используют цилиндрические опоры тип II [3 с. 672]
Определим вес аппарата при гидроиспытании:
Gмах = g · (Mоб + Мж) определяем ориентировочно.
Mоб = · D · S · H · ρст = 314 · 3 · 0010 · 258 · 7850 19000 кг – масса обечайки.
Мж = 0785 · · H · ρж = 0785 · 3² · 258 · 10³ 183000 кг – масса жидкости;
Gмах = 981 · (19000 + 183000) = 198 МН принимаем с запасом 2 МН так как не учитывали вес насадки площадок и лестниц а также штуцеров и т.д.
Принимаем толщину стенки цилиндрической опоры S = 20мм. Напряжение сжатия в этой стенке с учетом наличия в ней отверстия для лаза d = 05м при максимальной нагрузке от силы тяжести аппарата:
Rc = 0052 рис. 15.8 [3]
Допускаемое напряжение на сжатие в обечайке опоры:
Условие с сд выполняется.
Максимальное напряжение на сжатие в сварном шве соединяющем цилиндрическую опору с корпусом аппарата при коэффициенте сварного шва φш = 07:
F = 0785 · (D²1 - D²2) = 0785 · (324² - 294²) = 15 м²
D1 = D + 2 · S + 02 = 3 + 2 · 002 + 02 = 324 м – наружный диаметр опорного кольца;
D2 = D – 006 = 3 – 006 = 294 м – внутренний диаметр опорного кольца;
Максимальное напряжение на сжатие опорной поверхности кольца:
Номинальная расчетная толщина опорного кольца при L = 02м
Sк = 173 L · с учетом прибавок Sк = 24 мм.
Расчетная нагрузка на один болт:
где Z = 8 – число фундаментных болтов принимаем.
Расчетный внутренний диаметр резьбы болтов:
принимаем с запасом М40.
Техника безопасности
Обслуживание сосудов должно поручаться лицам достигшим 18-летнего возраста прошедшим медицинское освидетельствование производственное обучение проверку знаний квалификационной комиссии инструктаж по безопасному обслуживанию сосудов и имеющим удостоверение на право обслуживания сосудов. Периодическая проверка знаний персонала по обслуживанию сосудов должна производиться не реже чем через каждые 12 месяцев. Допуск персонала к самостоятельному обслуживанию сосудов оформляется приказом по организации или распоряжением по цеху. Все сосуды на которые распространяются правила ПБ 03-576-03 должны быть до пуска в работу зарегистрированы в органах Госгортехнадзора России и в технадзоре общества. Инструкция должна находиться на рабочих местах и выдаваться под расписку обслуживающему персоналу. На рабочих местах должны быть вывешены схемы включения сосудов.
Обслуживающий персонал должен знать:
- месторасположение сосудов их регистрационные номера технологические номера рабочие параметры среду и их назначение;
- обязанности персонала по наблюдению и контролю за работой сосуда в течение смены;
- порядок проверки исправности обслуживаемых сосудов и относящегося к ним оборудования в рабочем состоянии;
- порядок сроки и способы проверки арматуры предохранительных устройств (ППК мембраны) приборов автоматики защиты и сигнализации;
- порядок пуска в работу и останова сосуда в т.ч. в зимний период времени;
- меры безопасности при эксплуатации сосуда и выводе его в ремонт дополнительные меры безопасности для сосудов с пожароопасной взрывоопасной или ядовитой средой;
- случаи требующие аварийной остановки сосуда предусмотренные ст. 7.3.1 правил ПБ 03-576-03;
- действие персонала при ликвидации аварийных ситуаций;
- порядок ведения сменного журнала (оформление приема и сдачи смены записи о проверках производимые персоналом на смене проверка записей лицом ответственным за безопасную эксплуатацию сосуда).
На каждом сосуде до пуска в эксплуатацию должна быть на видном месте красной краской сделана надпись или вывешена специальная табличка размером 200х150 мм. где указывается:
а) регистрационный номер;
б) технологический номер;
в) разрешенное давление;
г) число месяц и год следующих внутреннего осмотра и гидравлического испытания.
После каждого периодического освидетельствования надпись меняется в соответствии с записью в паспорте сосуда в течение 10 дней. На каждый сосуд должен быть оформлен паспорт установленной формы согласно "Правил". К каждому паспорту сосуда работающего под давлением должны быть приложены:
- удостоверение о качестве монтажа составленное монтажной организацией и подписанное руководителем этой организации а также руководителем организации являющейся владельцем сосуда и скрепленное печатями;
- схема включения сосуда с указанием источника давления параметров рабочей среды
арматуры контрольно-измерительных приборов средств автоматического управления предохранительных и блокирующих устройств; схема должна быть утверждена техническим директором общества;
- паспорт предохранительного клапана с расчетом его пропускной способности.
Каждый сосуд согласно "Системы технического обслуживания и ремонта оборудования" должен быть включен в график ППР и согласно правил ежегодно должен составляться график технического освидетельствования по форме N 5 ОГМ. Все ремонты и технические освидетельствования сосуда должны записываться в паспорт сосуда и в ремонтный журнал.
На первой странице паспорта запрещено делать какие - нибудь записи и изменения. Все необходимые изменения рабочих параметров записываются в раздел паспорта "Записи результатов освидетельствования" за подписью лица ответственного за безопасную эксплуатацию сосуда. Для всех сосудов попадающих под действие правил любые изменения в конструкции технологической схеме рабочих параметрах должны быть согласованны со специализированной проектной организацией имеющей лицензию и Госгортехнадзором России. Включать сосуд в эксплуатацию разрешается только по письменному распоряжению лица ответственного за исправное состояние и безопасное действие сосуда.
Обо всех обнаруженных неполадках в работе и целостности сосуда лицо ответственное за исправное состояние должно сообщать в бюро технадзора общества и УПО Госгортехнадзора России.
Работа сосуда должна быть запрещена если истек срок очередного технического освидетельствования истек ресурс эксплуатации сосуда установленный заводом-изготовителем или истек срок ресурса работы определенный экспертной организацией или специализированной научно-исследовательской организацией или выявлены дефекты угрожающие безопасной работе сосуда. Для управления работой и обеспечения безопасных условий работы сосуды в зависимости от назначения должны быть оснащены:
- запорной или запорно-регулирующей арматурой
- приборами для измерения температуры
- предохранительными устройствами
- указателями уровня жидкости.
Установка запорной и запорно-регулирующей арматуры манометров предохранительных устройств и др. приборов должна производиться в соответствии с требованиями раздела 5 правил ПБ 03-576-03 и пунктами 2.10-2.26 РУА-93. Поверка манометров с их опломбированием или клеймением должна производиться не реже чем один раз в год кроме того не реже одного раза в 6 месяцев владельцем контрольным манометром с записью результатов в журнале манометров. Манометры применять не разрешается в случаях когда:
а) отсутствует пломба или клеймо;
б) просрочен срок поверки манометра;
в) стрелка манометра при его выключении не возвращается к нулевому показанию шкалы.
г) разбито стекло или имеются другие повреждения.
Манометр должен выбираться с такой шкалой чтобы при рабочем давлении его стрелка находилась во второй трети шкалы. На циферблат манометра должна быть нанесена красная черта на деление шкалы соответствующей разрешенному рабочему давлению. Взамен красной черты на манометре допускается устанавливать снаружи металлическую пластину окрашенную в красный цвет плотно прилегающую к стеклу манометра и жестко закрепленную на корпусе. В тех случаях когда по роду производства или вследствие действия содержимого в сосуде предохранительный клапан не может надежно работать вместо него необходимо сосуд снабдить предохранительной мембраной. На патрубке между предохранительным клапаном и стоящей перед ним мембраной должен быть установлен штуцер с краником для контроля исправного состояния мембраны. Эксплуатация ревизия ремонт и периодичность проверки предохранительных устройств должны осуществляться в соответствии с РУПК-78 и инструкцией завода-изготовителя.
Согласно заданию был произведен расчет и проектирование тарельчатой ректификационной колонны для разделения смеси муравьиная кислота – уксусная кислота с производительностью 11000 кгч. Тарелка - колпачковая.. Диаметр колонны 3000мм число тарелок - 58 высота цилиндрической части колонны проектная 258 м.
Пособие по проектированию "Основные ПАХТ" под ред. Ю.И.Дытнерского 2-е издание переработанное и дополненное;
М.: Химия1983. - 272 с.
К.Ф.Павлов П.Г.Романков А.А.Носков "Примеры и задачи по курсу ПАХТ" Учебное пособие для ВУЗов Под ред. чл. – корр. АН СССР П.Г. Романкова. – 9-е издание перераб. и доп. – Л.: Химия 1981. – 560 с.
А.А.Лащинский А.Р.Толчинский "Основы расчета и конструирования химической аппаратуры" М.: Физматгиз1970 .- 725с.
М.Ф.Михалев "Расчет и конструирование машин и аппаратов химических производств" Л.: Машиностроение 1984 . - 301 с.
А.С.Тимонин "Основы конструирования и расчета технологического и природоохранного оборудования" Том 1 2002 .
Чернобыльский И.И. “Машины и аппараты химических производств” Изд. 3-е перераб. и доп.М. Машиностроение 1975.-454с.
Рамм В.М. “Абсорбция газов”. Изд. 2-у перераб. и доп. М. Химия 1976-655 с.
Н.Б. Варгафтик "Справочник по теплофизическим свойствам газов и жидкостей". М.:Физматгиз 1963 . - 708 с.
М.: Химия1991. - 496 с.
Схема.cdw

Наименование среды в трубопроводе
Паро - жидкостная эмульсия
Точка замера и контроля
Контролируемый параметр
Колонна ректификационная
Вентиль регулирующий
РК 1. 05. 00. 00. 000. ТС
Технологическая схема
Рекомендуемые чертежи
- 16.02.2015
- 25.01.2023
- 19.01.2024
Свободное скачивание на сегодня
Обновление через: 7 часов 5 минут
- 23.08.2014