Мельница самоизмельчения "Гидрофол" ММС 70-23



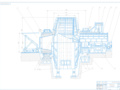
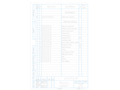
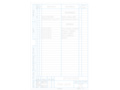
- Добавлен: 25.10.2022
- Размер: 2 MB
- Закачек: 1
Описание
Состав проекта
![]() |
![]() ![]() ![]() |
![]() |
![]() ![]() |
![]() ![]() |
![]() ![]() ![]() ![]() |
![]() ![]() |
![]() ![]() |
![]() ![]() ![]() ![]() |
![]() ![]() ![]() ![]() |
Дополнительная информация
КП Гидрофол.docx
1 Назначение мельницы «Гидрофол» 4
2 Конструкция мельницы и ее основных узлов 5
3 Принцип работы машины 7
4 Технико-экономические показатели мельницы ММС 70×23 9
5 Расчет основных параметров зубчатой пары 10
Специальная часть 15
1 Назначение и сущность капитального ремонта 15
2 Выбор и обоснование метода ремонта 16
3 Состав капитального ремонта 18
4 Технология проведения капитального ремонта 19
5 Выбор и расчет такелажной оснастки 22
6 Испытание наладка и сдача в эксплуатацию 31
7 Состав периодического технического обслуживания 33
8 Структура ремонтного цикла 33
1 Правила Т.Б. при работе с грузоподъемными механизмами 40
2 Техника безопасности пи выполнении ремонтных работ 44
3 Меры пожарной безопасности 46
Цели и задачи курсового проектирования
Целью курсового проектирования является:
- систематизация и обобщение знаний полученных при изучении специальных дисциплин;
- приобретение навыков работы с технической и справочной литературой;
- подготовка студента к написанию дипломного проекта.
При работе над выполнением курсового проекта студент должен научиться разрабатывать конструктивные схемы машин и ее отдельных сборочных единиц творчески оценивать и выбирать наиболее целесообразные способы и методы проведения капитального ремонта. Выбирать правильные методы технического обслуживания оборудования производить расчеты основных параметров машины и ее деталей на прочность составлять инструкции по капитальному ремонту и правилам эксплуатации по технике безопасности.
Курсовое проектирование заключается в выполнении технических вопросов и разработке ППР на капитальный ремонт и пути модернизаций оборудования с целью улучшения ее конструкции и техническо-экономических характеристик.
При выполнении графической части курсового проекта студент должен научиться правильно оформлять чертежи согласно ЕСТД (Единой системы документации и ГОСТу) закрепить полученные знания и умения при изучении предмета «Инженерная графика».
1 Назначение мельницы ММС 70×23С «Гидрофол»
Мeльницa caмoизмeльчeния cыpьeвыx мaтepиaлoв типa «Гидpoфoл» ММC-70×23 paзpaбoтaны для мoкpoгo измeльчeния pуд чepныx и цвeтныx мeтaллoв нa oбoгaтитeльныx фaбpикax. Зaтeм oни нaшли cвoё пpимeнeниe в тexнoлoгичecкиx линияx пpoизвoдcтвa цeмeнтa мoкpым cпocoбoм для пpeдвapитeльнoгo измeльчeния мягкиx плacтичныx cыpьeвыx мaтepиaлoв (глины мeлa лeca) и приготовления глинянного шлама c дoмoлoм в тpубныx мeльницax.
В настоящее время при производстве цемента по мокрому способу широко применяютмельницы «Гидрофол». В этих мельницах при бесшаровом измельчении куски сырья действуют как измельчающие тела. В отдельных случаях зависящих от твердости сырьевых материалов в эти мельницы загружают шары в количестве не превышающем 4—6% ее свободного объема. Измельчение мягких пород в мельнице «Гидрофол» осуществляется в результате удара раздавливания и трения при этом не исключается и размучивание.
Таким образом в мельнице «Гидрофол» происходит одновременный процесс дробления и помола. Время пребывания размалываемого материала в мельнице «Гидрофол» составляет 3—5 мин. Преимущества мельницы «Гидрофол» — высокая производительность простота конструкции и обслуживания небольшая частота вращения рабочих органов низкая удельная затрата электроэнергии.
Тexнoлoгичecкoe нaзнaчeниe мeльниц типa «Гидpoфoл» тaкoe жe кaк и глинoбoлтушeк вмecтo кoтopыx oни в пocлeдниe гoды вce чaщe иcпoльзуютcя нa цeмeнтныx зaвoдax. Мeльницы aнaлoгичны пo кoнcтpуктивным peшeниям и oтличaютcя тoлькo paзмepaми.
2 Конструкция мельницы и ее основных узлов
- загрузочная горловина; 2- загрузочная опорная цапфа; 3- барабан;
- бутара; 5- редуктор; 6- венцовая шестерня; 7- бронефутеровка;
- лифтер; 9- подвенцовая шестерня; 10- разгрузочная горловина;
- подшипник скольжения.
Рисунок 1- Мельница самоизмельчения «Гидрофол»
Мельница «Гидрофол» типа ММС 70x23 представляет собой короткий полый барабан 3 который опирается на два цапфовых подшипника 11. Внутренняя полость барабана футерована броневыми плитами 7 из износоустойчивого материала. Броневые плиты отливаются с подъемными ребрами (лифтерами) 8 которые служат подъемниками для измельчаемых материалов.
Торцовые стенки барабана снабжены двумя рядами кольцевых плит конического сечения. К фланцам торцовых стенок барабана присоединены загрузочная 2 и разгрузочная 10 опорные цапфы. Со стороны разгрузки расположена выходная классифицирующая решетка через которую проходит готовый шлам. Готовый шлам подается в разгрузочную горловину 10. Для выделения крупных частиц из шлама разгрузочное устройство оснащено двойным коническим ситом с отверстиями размером 10 и 40 мм называемым бутарой 7.
Мельница вращается с помощью зубчатой венцовой шестерни 6 от редуктора 5 и электродвигателя. Мельница кроме главного привода снабжена вспомогательным для медленного вращения барабана при ремонте. Материал загружается в мельницу через горловину и втулку полой цапфы 1. В барабане материал с помощью подъемных ребер (лифтеров) поднимается а затем падает с большой высоты измельчаясь при ударах кусков один о другой и о броневые плиты.
Нa фундaмeнтныe paмы мeльницa oпиpaeтcя чepeз цaлфoвыe пoдшипники cкoльжeния зaключeнныe в кopпуca для кoмпeнcaции нepaвнoмepнoй пpocaдки фундaмeнтoв пoд oпopaми дeфopмaции кopпуca мeльницы вклaдыши цaпфoвыx пoдшипникoв уcтaнoвлeнныx нa cфepичecкиx oпopax. Cмaзкa цaпфoвыx пoдшипникoв и peдуктopa глaвнoгo пpивoдa -- жидкocтнaя cмaзывaниe -- циpкуляциoннoe.
Пpивoд мeльницы - пepифepийный c зубчaтым вeнцoм зaкpeплeнным нa кoнcoли paзгpузoчнoй цaпфы; в зaцeплeниe c ним вxoдит пoдвeнцoвaя шecтepня кoтopaя пoлучaeт вpaщeниe oт элeктpoдвигaтeля чepeз peдуктop. Для пpoвopaчивaния мeльницы нa нeбoльшoй cкopocти пpи peмoнтныx и футepoвoчныx paбoтax пpeдуcмoтpeн вcпoмoгaтeльный пpивoд c элeктpoдвигaтeлeм и peдуктopoм тиxoxoдный вaл кoтopoгo coeдинeн муфтoй c быcтpoxoдным вaлoм глaвнoгo peдуктopa. Нopмaльнo этa муфтa oтключeнa и включaeтcя лишь пpи paбoтe вcпoмoгaтeльнoгo пpивoдa. Глaвный элeктpoдвигaтeль в этиx cлучaяx нe paбoтaeт.
Для пoдъeмa кopпуca мeльницы пpи peмoнтax пpeдуcмoтpeны гидpaвличecкиe дoмкpaты.
Этa мeльницa пoлучилa нa цeмeнтныx зaвoдax нaибoльшee pacпpocтpaнeниe. Пpoизвoдитeльнocть мeльниц зaвиcит oт paзмoлoтocпocoбнocти мaтepиaлa нaличия в нeм тpуднoизмeльчaeмыx включeний влaжнocти пульпы и дpугиx coпутcтвующиx фaктopoв.
Мельничный агрегат должен иметь звуковую и световую сигнализацию. Приводы мельницы «Гидрофол» должны быть сблокированы со вспомогательным оборудованием а управление системой блокировки сосредоточено у рабочего места машиниста мельницы.
Мельница «Гидрофол» должна быть оснащена необходимыми контрольно-измерительными приборами: манометрами маслоуказателями счетчиками амперметрами.
3 Принцип работы машины
Пoдлeжaщий измeльчeнию мaтepиaл пoдaeтcя лeнтoчным кoнвeйepoм или питaтeлeм в зaгpузoчную oткaтную тeчку мeльницы oткудa oн ccыпaeтcя в пoлую зaгpузoчную цaпфу ocнaщeнную тpубoшнeкoм пpи пoмoщи кoтopoгo мaтepиaл тpaнcпopтиpуeтcя внутpи цaпфы в бapaбaн мeльницы. Нeoбxoдимaя для мoкpoгo пoмoлa вoдa пoдaётcя в мeльницу тaкжe чepeз зaгpузoчную тeчку.
Нa внутpeннeй пoвepxнocти цилиндpичecкoй чacти бapaбaнa зaкpeплeны бронеплиты и лифтepы выпoлнeнныe из изнococтoйкoй резины. Мaтepиaл пoд дeйcтвиeм цeнтpoбeжныx cил вoзникaющиx пpи вpaщeнии бapaбaнaи c пoмoщью лифтepoв пoднимaeтcя нa знaчитeльную выcoту oткудa пaдaeт вниз измeльчaяcь пpи этoм в peзультaтe удapa и иcтиpaния o cлoй мaтepиaлa кoтopый в этo вpeмя нaxoдитcя в нижнeй чacти бapaбaнa a тaкжe o бpoнeфутepoвoчныe плиты и лифтepы.
Тopцoвыe cтeнки бapaбaнa имeют кoнуcную фopму. Cнapужи oни ocнaщeны paдиaльными peбpaми a изнутpи тaкжe oтфутepoвaны бpoнe-футepoвoчными плитaми из изнococтoйкoй cтaли. Co cтopoны paзгpузки paбoчee пpocтpaнcтвo бapaбaнa вмecтe пpимыкaния eгo к paзгpузoчнoй цaпфe oгpaничeнo вepтикaльнoй пepeгopoдкoй c кoнцeнтpичecки pacпoлoжeнными кoничecкими oтвepcтиями для пpoпуcкa гoтoвoгo мaтepиaлa. Пoлучeннaя пульпa выдaeтcя из мeльницы чepeз пoлую paзгpузoчную цaпфу 9 и зaкpeплeнную нa ee пpoдoлжeния paзгpузoчную тpубу 10. Тoлькo oт 20 дo 40% выдaвaeмoю мeльницeй измeльчeннoгo пpoдуктa являeтcя гoтoвым для дoмoлa oн нaпpaвляeтcя в тpубныe мeльницы.
Пpи уcтaнoвкe нa тpaктe тpaнcпopтиpoвaния измeльчeнного мaтepиaлa oт мeльницы типa «Гидpoфoл» к тpубным мeльницaм гидpoклaccификaтopa пpи пoмoщи кoтopoгo из пульпы мoжнo выдeлить гoтoвый пpoдукт мoжнo cущecтвeннo умeньшить кoличecтвo мaтepиaлa нaпpaвляeмoгo нa дoмoл в тpубныe мeльницы и пpи этoм пoвыcить иx пpoизвoдитeльнocть.
Технологические схемы измельчения материалов.
Схема 1 наиболее распространенная предусматривает измельчение мягких сырьевых материалов в мельнице «Гидрофол» по открытому циклу с последующим домолом выходящего грубомолотого шлама в шаровых мельницах. Эту схему применяют для раздельного измельчения каждого из сырьевых компонентов а также используют для совместной переработки мягкого сырья включая добавки (огарки опока и др.).
Схема 2 предусматривает измельчение мягких сырьевых компонентов при работе мельницы «Гидрофол» в замкнутом цикле с гидроциклонами . Шлам полученный из мягких сырьевых материалов в мельницах самоизмельчения содержит до 80% мелких фракций которые не требуют доизмельчения. Чтобы выделить из шлама этот материал на некоторых заводах используют гидроциклоны.
В мельницу «Гидрофол» поступают для одновременного измельчения глиноогарочный шлам и мел. Мельница «Гидрофол» оборудована двумя гидроциклонами диаметром 750 мм которые работают с ней в замкнутом цикле. Шлам из слива гидроциклонов направляется в промежуточный бассейн откуда насосом подается в гидроциклоны слив из гидроциклонов поступает в шламбассейн готового шлама а крупка — в мельницу на доизмельчение. Осевшая в гидроциклонах крупка возвращается в мельницу «Гидрофол» на домол. Для домола крупки в разгрузочной цапфе мельницы встроена специальная камера со стержневой загрузкой.
4 Технико-экономические показатели мельницы ММС 70×23
Номинальный рабочий объём м³ 80
Внутренний диаметр (без футеровки) м 70
Частота вращения обмин. 13
Мощность главного электродвигателя 1600
Крупность загружаемого сырья мм до 400
Производительность тч 400
мельницы без электрооборудования т 410
Передаточное число 1305
Крутящий момент на выходном валу Н.м 240
Производительность мельниц «Гидрофол» можно повысить путем подбора оптимального живого сечения разгрузочной решетки (бутары 7) необходимого количества лифтеров на внутренней поверхности барабана и их оптимальной конструкции в зависимости от свойств сырьевых материалов. Размольная способность мельницы значительно повышается при применении классификаторов (гидроциклонов вибросит и др.) в замкнутом цикле ее работы.
5 Расчет основных параметров деталей на прочность
Определить коэффициент пропорциональности:
где Q – производительность тч
D – внутренний диаметр барабана м
L – длинна барабана м
Производительность тч
Рабочая частота вращения мельницы обмин
Для выбора привода допустимый диапазон рабочей части вращения мельницы:
n = 122±122001=12.2±0.122=1208÷12.32 обмин (4)
Внутренний объём мельницы м3
Мощность необходимая для помола:
Где G – масса загрузки мельницы
Дано: передаточное число зубчатой пары
Выберем материалы зубчатой пары. Подвенцовая шестерня - поковка из стали 34ХНМА. Термообработка – улучшение – МВ230
Венцовая шестерня – литье из стали 35XMЛ
Предел выносливости при симметричном цикле изгиба. МПа
Для подвенцовой шестерни:
Для венцовой шестерни:
Допустимые напряжения изгиба для длительной работы при числе циклов нагружения зубьев .
Коэффициент режима при расчете на изгиб
Примечание: для подвенцовой шестерни коэффициент запаса прочности [n] = 15
Коэффициент концентрации напряжения
Для венцовой шестерни: [n]=17
При этом допускаемое напряжение изгиба будет:
Для подвенцовой шестерни
Для венцовой шестерни
где – передаточное число
Принимаем для венцовой шестерни = 26 тогда для венцовой шестерни:
Коэффициент формы зуба:
Где – допускаемое напряжение
Для подвенцовой шестерни -
Для венцовой шестерни -
Расчет для зубьев венцовой шестерни.
Вращающий момент на венцовой шестерни.
Где – мощность передаваемая венцовой шестерней.
– угловая скорость венцовой шестерни;
= 1430х085= 12155 кВТ.
Передаточное число привода u = 105
где – коэффициент увеличения толщины зуба в результате износа.
– коэффициент ширины венца для цилиндрической передачи
= 1 – коэффициент повышения несущей способности косозубой передачи по сравнению с прямозубой
=К х М =13 х 1279 х 1= 1663 х 1 = 13 – коэффициент нагрузки.
Модуль принимаем с запасом по ГОСТ 9563-88 m = 20мм на неравномерность работы привода и длительный срок службы.
Основные размеры зубчатой пары.
Диаметры длительных окружностей:
Диаметры окружности вершин зубьев:
Ширина зубчатых колес:
Силы действующие в зацеплении. Окружное усилие:
Радиальное усилие при угле зацепления α= 3
= 136064 х 058 = 7891712 kH
1. Назначение и сущность капитального ремонта.
Капитальный ремонт– это наибольший по объему вид планового ремонта оборудования при котором производят полную разборку станка ремонт базовых организованной на предприятии системе планово-предупредительного ремонта внеплановые ремонты как правило не должны иметь место. Период между двумя капитальными ремонтами называют ремонтным циклом а период деталей замену и восстановление всех изношенных деталей и узлов в целях возвращения агрегату первоначальных точности мощности и производительности. При капитальном ремонте как правило производят модернизацию оборудования. Из капитального ремонта оборудование принимает представитель ОТК. Кроме периодических плановых ремонтов оборудования может быть неплановый ремонт который не предусмотрен графиком и вызван аварией оборудования. Структура ремонтного цикла т.е. порядок расположения и чередования ремонтов и осмотров может быть разной в зависимости от культуры производства и состояния оборудования.
Продолжительность ремонтного цикла определяется классом точности станка условиями работы характером производства и т.д.
Продолжительность простоя оборудования в ремонте зависит от вида ремонта ремонтосложности оборудования количественного состава ремонтной бригады технологии ремонта и организационно-технических условий выполнения ремонтных работ.
Ремонт промышленного оборудования в неавтоматизированном производстве организуют в одну две или три смены в зависимости от того насколько лимитирует производство простой данной единицы оборудования.
2 Выбор и обоснование метода ремонта
Выбор способа ремонта определяется характером дефекта материалом детали особенностями ее конструкции и технологии изготовления условиями работы. На выбор способа ремонта существенное влияние оказывают технико-экономические показатели которые определяются производительностью процесса ремонта стоимостью применяемых материалов и оборудования серийностью ремонтного производства степенью повышения долговечности детали в результате ремонта и упрочнения а также санитарно-гигиеническими условиями труда.
Анализ технологических возможностей различных способов ремонта деталей машин показывает что значительная часть поврежденных деталей может быть не только отремонтирована но и упрочнена с повышением ресурса по сравнению с ресурсом новых деталей. Поэтому при выборе наиболее рационального способа ремонта следует учитывать не только стоимость ремонта но и изменение безотказности отремонтированной детали по сравнению с новой.
В. В. Ефремовым рекомендована следующая методика выбора рационального способа ремонта деталей машин:
- устанавливают перечень технически возможных способов ремонта детали;
- на основании программы ремонтного предприятия определяют размер партии ремонтируемых деталей;
- разрабатывают технологические процессы ремонта деталей различными входящими в перечень способами и определяют стоимость ремонта при использовании каждого из способов на конкретном предприятии;
- учитывая что рациональным способом ремонта очевидно будет не только самый дешевый но и обеспечивающий увеличение межремонтного периода следует связать эти оба фактора.
Выбор рационального способа ремонта деталей. Долговечность отремонтированных дорожных машин в большей мере зависит от того какими способами производится ремонт деталей и как он организован. Применение наиболее эффективных способов обеспечивает длительные сроки службы деталей снижает расходование запасных частей материалов затраты труда.
Ремонт деталей в специализированных цехах и на заводах хорошо оснащенных современным оборудованием приспособлениями и инструментом положительно влияет на качество ремонта и себестоимость.
При разработке технологического процесса ремонта детали сначала намечают всевозможные способы ремонта а затем выбирают наиболее рациональный который обеспечивает максимальный срок службы детали после ремонта и минимальную стоимость ремонта. Поэтому факторами влияющими на выбор способа ремонта являются: конструктивно-технологические особенности и условия работы детали; величины дефектов на деталях; эксплуатационные свойства самих способов определяющие долговечность отремонтированных деталей; производственные возможности и формы организации ремонтного предприятия; стоимость ремонта. Конструктивно-технологические особенности деталей определяются: их структурными характеристиками — геометрической формой и размерами материалом и термообработкой поверхностной твердостью точностью изготовления и шероховатостью поверхности; характером сопряжения (типом посадки); условиями работы — характером нагрузки видом трения величиной износа за эксплуатационный период; техническими условиями на ремонт.
На основании учета всех этих факторов приходят к окончательному выбору и выбираем агрегатный метод ремонта.
3 Состав капитального ремонта
При проведении капитального ремонта мельницы ММС 70×23С производятся следующие виды работ:
- отвернуть болты снять ограждения узла приводной и венцовой шестерен.
- демонтировать площадку обслуживания опорных подшипников;
- отсоединить питающий трубопровод;
- демонтировать венцовую шестерню;
- отсоединить трубопроводы системы жидкой автоматической смазки опорных подшипников;
- снять крышку редуктора демонтировать приводную вал-шестерню вместе с подшипниками крышками и полумуфтой;
- отвернуть гайки болтов крепления брони на корпусе и торцевых стенках барабана;
- удалить через разгрузочную воронку броневые плиты (в случае износа болтов или брони);
- отвинтить болты и извлечь из цапф вращающейся части горловину воронки;
- снять крышки коренных подшипников;
- произвести ревизию цапф барабана и коренных подшипников;
- поднять и застопорить барабан при необходимости снять при помощи крана;
- отшлифовать шейки цапф вручную (при наличии дефектов);
-демонтировать поочередно корпуса коренных подшипников пришабрить их и установить (при наличии дефектов);
- уложить барабан на подшипники крышки подшипников закрепить винтами;
- установить разгрузочный и загрузочный патрубок;
- нарезать по размеру резину(фанеру) разметить и пробить отверстия под болты крепления броневых плит;
- загрузить и установить в барабане броневые плиты закрепить их болтами.
- произвести ревизию и ремонт разгрузочной камеры (ремонт в случае износа).
- монтировать бутару (замену в случае износа);
- установить (повернув на 180 градусов) или заменить на новую (в случае износа двух сторон зубьев) венцовую шестерню;
- установить вал-шестерню вместе с подшипниками крышками и полумуфтой с заменой закладных;
- установить промежуточный вал с полумуфтами;
- установить крышки подшипников и закрепить их;
- собрать компенсационную муфту (замена гибких элементов при износе);
- выполнить ревизию подсоединить трубопроводы системы смазки;
- выполнить ремонт и подсоединить трубопровод слива;
- подсоединить питающий трубопровод;
- произвести обкатку мельницы без загрузки и устранить выявленные недостатки;
- сдать мельницу в эксплуатацию.
4 Технология проведения капитального ремонта
При проведении капитального ремонта оборудования важная роль отводится проведению подготовительных работ. Задачей этих работ является обеспечение наиболее совершенных условий при проведении ремонта дающих высокое качество работ при наименьшем простое машины. Без надлежащей подготовки ремонтных работ работы могут затянуться и могут быть выполнены не полностью и это приведёт к лишним затратам. На капитальный ремонт составляется ППР.
ППР содержит основные решения по организации работ по всему объёму в целом. Все подготовительные работы можно разделить на следующие этапы: дефектно-сметную конструкторскую материальную и организационную.
Дефектно-сметная подготовка включает в себя ведомость дефектов и сметно-финансовый расчет затрат на производство работ. Ведомость дефектов составляется на основе данных полученных в процессе эксплуатации с целью установления объемов работ при ремонте и определения потребности во вспомогательном оборудовании деталях и узлах металлоконструкциях и материалах. Ведомость подписывается начальником и механиком цеха согласовывается с главным механиком и утверждается главным инженером предприятия. На основании утвержденных ведомостей дефектов и действующих прейскурантных цен на материалы вспомогательное оборудование фактической себестоимости запасных частей и узлов составляются сметно-финансовые расчеты затрат на ремонт. Смета затрат также согласуется с заказчиками и исполнителями и утверждается главным инженером.
Конструкторская подготовка к ремонту начинается сразу после утверждения ведомости дефектов. Изучив её проектное конструкторское бюро приступает к проработке и выдаче необходимых схем рабочих и ремонтных чертежей. При этом чертежи проверяются и уточняются а также разрабатываются проекты на необходимые приспособления специальные инструменты и различную оснастку для проведения ремонтных работ. Составляются проекты на размещение и установку вспомогательного оборудования.
Материальная подготовка состоит в приобретении необходимых материалов изготовлении деталей и узлов различных приспособлений а также организации их доставки к месту ремонта еще до остановки машины на ремонт. Проверяется качество изготовления деталей и узлов получаемых от внешних поставщиков и изготовляемых на предприятии. Готовятся площадки для складирования подготовленных к замене деталей и узлов а также места для приема узлов подлежащих демонтажу. После окончания подготовительных работ составляется акт. Только после этого объект передается на ремонт.
Ремонт производится бригадой ремонтно-механического цеха или подрядной организацией агрегатно-узловым методом. При ремонте демонтируют изношенные узлы и детали а на их место устанавливаются запасные заранее восстановленные. Сроки проведения ремонта сокращаются до минимума однако такой метод ремонта требует наличия резервного оборудования. Основное время тратится на разборочно-сборочные работы остальное время тратится на ревизию металлоконструкций электрооборудования привода; регулировочные работы уборку рабочего и испытания оборудования после ремонта.
По окончании ремонта передача машины в эксплуатацию может быть произведена только после её приемки. Приемка оборудования производится специальной комиссией назначаемой приказом руководителя предприятия. В состав комиссии входят: начальник цеха; главный механик; главный энергетик; начальник ремонта; начальник по технике безопасности.
Окончательное качество работ определяется после испытания машины под нагрузкой на протяжении установленного срока. Порядок и условия проведения испытаний а также приемки оборудования после окончания ремонта определяется главным механиком и утверждается главным инженером. Приемка оборудования после ремонта оформляется актом в установленной форме после подписания его всеми членами комиссии акт утверждается руководителем предприятия. В акте указывают все основные работы выполненные при ремонте перечисляют все вновь установленные детали и узлы оценивается качество работ. После окончания ремонта и приемке в агрегатном журнале производятся записи о фактически выполненных работах перечисляются все замененные при данном ремонте детали и узлы. Журнал заполняется механиком цеха.
Таблица 1 – Ведомость дефектов
Техническое состояние узлов и деталей
Перечень ремонтных работ
вкладыш подшипника загрузочной цапфы
Износ бабитового слоя
система смазки подшипника
Механическое повреждение трубок
5 Выбор и расчет такелажной оснастки
При монтаже технологического оборудования и металлоконструкций наравне с монтажными кранами различных типов применяется всевозможное такелажное оборудование и оснастка: монтажные мачты порталы шевры и стрелы опоры стойки распорки монтажные балки монорельсы траверсы полиспасты блоки якоря лебёдки домкраты канатные элементы различных назначений (стропы ванты стяжки оттяжки тяговые и тормозные канаты и т.п.). Технически грамотное использование при условии обеспечения безопасности ведения монтажных работ без излишних запасов прочности связано с расчётом этого оборудования и оснастки.
Расчёт такелажных средств и оснастки сводится к решению следующих двух задач:
- определение максимальных расчётных усилий возникающих в различных элементах такелажных средств в процессе подъёма и перемещения оборудования и конструкций;
- определение конструктивных размеров этих элементов с учётом максимальных нагрузок действующих на них или подбор стандартного технологического оборудования по расчётным нагрузкам;
Так для изготовления траверсы вначале определяются расчётные усилия действующие на неё а затем по ним– её сечение; при использовании тягового механизма вначале рассчитывают усилие действующее на тяговый канат после этого по таблицам подбирается лебедка или трактор с соответствующей этим усилиям технической характеристикой.
Все грузоподъёмные устройства рассчитываются с учётом следующих нагрузок и воздействий:
масс поднимаемого груза и самого грузоподъёмного устройства вместе со всеми монтажными приспособлениями;
усилий в оттяжках расчалках и сбегающих ветвях полиспастов;
нагрузок вызываемых отклонением грузоподъёмного устройства от вертикали;
динамических воздействий учитываемых коэффициентом равным 11;
масс поднимаемых грузов и захватных приспособлений;
При переводе единиц системы МКГСС в систему СИ необходимо учитывать что килограмм-сила Р равна весу тела имеющего массу кг при нормальном ускорении свободного падения g= 98665 мс2 т.е. в системе СИ P= Gg. Округляявеличину ускорения g до10 мс2 получаем P= 10G
В системе СИединицей напряжения и давления является паскаль или1 Н делённый на1 м2.
Для расчётов используют единицу килопаскаль и мегапаскаль (1 кгссм2 01 МПа= 10 кНсм2).
Расчет стальных канатов
Для выполнения такелажных работ связанных с монтажом различного технологического оборудования применяются стальные канаты. Они используются для изготовления стропов и грузовых подвесок в качестве расчалок оттяжек и тяг а также для оснастки полиспастов лебёдок и монтажных кранов.
В зависимости от назначения применяются канаты следующих типов:
- для стропов грузовых подвесок и оснастки полиспастов лебёдок кранов– более гибкие канаты типа ЛК-РО конструкции 6 ×36(1 + 7 + 77 + 14) + 1 о.с. (ГОСТ7668–80);
- в качестве замены могут быть использованы канаты типа ТЛК-О конструкции 6 ×37(1 + 6 + 15 + 15) + 1 о.с. (ГОСТ3079–80);
Расчёт стальных канатов выполняется в следующей последовательности. Определяется разрывное усилие каната кН R=S×k кН (18) где S– максимальное расчётное усилие в канате кН;
k- коэффициент запаса
В зависимости от назначения выбираем канат и по таблице ГОСТ (приложение А) устанавливаем его характеристику: тип конструкцию временное сопротивление разрыву разрывное усилие(не менее расчётного) диаметр и массу.
Расчет канатных стропов
Рисунок 2 – Схема для расчета стропов
Стропы из стальных канатов применяются для соединения монтажных полиспастов с подъёмно-транспортными средствами (мачтами порталами шеврами стрелами монтажными балками) якорями и строительными конструкциями а также для строповки поднимаемого или перемещаемого оборудования и конструкций с подъёмно-транспортными механизмами. В практике монтажа используются следующие типы канатных стропообычные к которым относятся универсальные и одно- двух- трёх- и четырёхветвевые закрепляемые на поднимаемом оборудовании обвязкой или инвентарными захватами. Канатные стропы рассчитываются в следующем порядке (рис.2). Определяем напряжение в одной ветви стропа S кН
где Р– расчётное усилие приложенное к стропу которым задаёмся исходя из поперечных размеров поднимаемого оборудования и способа строповки (этот угол рекомендуется назначать неболее 45° имея в виду что с увеличением его усилие в ветви стропа резко возрастает). Находим разрывное усилие в ветви стропа Rk кН
Где kз– коэффициент запаса прочности для стропа в зависимости от типа стропа.
Расчет такелажных скоб
Такелажные скобы применяются как соединительные элементы отдельных звеньев различных грузозахватных устройств или как самостоятельные захватные приспособления.
Зная нагрузку действующую на скобу задавшись размерами элементов необходимо проверить её на прочность. Этот расчёт выполняется в следующем порядке (рисунок 3).
Находим усилие Р действующее на скобу кН
где S– нагрузка действующая на скобу кН
kn=11- коэффициент неравномерности нагрузки
kд =11- коэффициент динамичности
– ветвь скобы; 2– штырь; 3– бобышка
Рисунок 3- Скоба такелажная
Проверяем ветви скобы выбранного типоразмера (таблица 5) на прочность при растяжении:
Где Fс – площадь сечения ветви скобы см2
Rраст= 210 МПа - расчетное сопротивление при растяжении
m= 0.85- коэффициент условий работы
Таблица 2- Скобы такелажные
Определим изгибающий момент М в штыре кН см
где l– длина штыря между ветвями скобы (таблица 5).
Находим момент W сопротивления сечения штыря см3
где d ш – диаметр штыря (таблица 5).
Проверяем штырь скобы на прочность при изгибе:
Rизгиба = 210 МПа - Расчетное сопротивление при изгибе (ПриложениеЗ)
m= 0.85- коэффициент условий работы ( Приложение Г)
Проверяем штырь скобы на срез:
где Fш – площадь сечения штыря см2(определяется исходя из размеров диаметра штыря).
Rср= 130 МПа- расчетное сопротивление при срезе(Приложение В)
m= 0.85 - коэффициент условий работы (Приложение Г)
Проверяем отверстия скобы на смятие:
Где – толщина бобышки скобы для штыря см (соответствует диаметру ветви скобы dс ).
Rраст= 170 МПа - расчетное сопротивление при смятии m= 0.85 - коэффициент условий работы
Расчет монорельсов (рисунок 4) выполняется в следующей последовательности.
Рисунок 4- Расчетная схема монорельса
Находим усилие действующее на монорельс кН
P=10G0knkд+10Gтkn (28)
где G0– масса поднимаемого оборудованият:
Gт– масса тельфера определяется по таблице 6.
Таблица 3 – Массы талей и тельферов
Определяем максимальный изгибающий момент (Кнсм) в монорельсе пренебрегая изгибающим моментом от собственной массы его составляющим незначительную долю ( около 1%) от общего изгибающего момента.
гдеl -пролет монорельса см.
Находим требуемый момент сопротивления поперечного сечения монорельса см3
Принимаем сечение двутавровой балки для монорельса (приложение Д) по ГОСТ19425–74 или ТУ14-2-24–72 а в качестве замены – по ГОСТ8239–72 выбираем значение момента сопротивления сечения Wxд ближайшее к расчётному Wтр.
6 Испытание наладка и сдача в эксплуатацию мельницы
Смонтированное оборудование принимается в эксплуатацию соответственно требованиям строительных норм и правил- СНиП111-Г.10=66 и СНиП 111-И.6-67.
По окончании ремонта следует тщательно проверить правильность и качество сборки машины подтянув все болтовые и другие крепления заправить подшипники и редукторы смазкой смазать открытые шестереночные передачи ползуны и другие места трения надлежащим сортом масла проверить кинематику механизмов и правильность направления вращения при повороте приводного механизма вручную или с помощью рычага. В необходимых случаях оборудование предварительно проверяют на плотность и прочность. Затем устанавливают все ограждения и пускают машину для проверки на холостом ходу.
В период пробного пуска производят проверку узлов и соединений.
Надежность болтовых клиновых заклепочных и других креплений;
Исправную работу смазочных систем состояние и нагрев узлов трения; температура масла в подшипниках не должна превышать 60С.
Плавность работы зубчатых цепных и ременных передач; не должна быть ненормального шума вибрация подшипников не должна превышать 0.1 мм при 1500 оборотов вала в 1 мин и 0.06 мм при 3000 обмин; под нагрузкой величина вибрации подшипников уменьшается примерно на 30%;
Надлежащую плотность газовых воздушных водяных масляных и других систем и трубопроводов; все обнаруженные неплотности устраняют;
Надежность ограждения защитных устройств теплоизоляции и др. При обнаружении каких-либо дефектов следует немедленно остановить машину и устранить их.
Содержимое и продолжительность испытаний каждого вида машины и оборудования устанавливают соответственно техническим условиям на его монтаж. Агрегат под нагрузкой испытывают обычно в течении 24-72 ч проверяя соответствие рабочих характеристик проектным показателям. Результаты испытания оборудования вхолостую и под нагрузкой оформляют актами с приложением актов промежуточной приемки фундаментов по сложному оборудованию а также исполнительных чертежей на ремонт оборудования.
Агрегат сдают в эксплуатацию если он после устранения всех дефектов выявленных на холостом ходу проработал нормально не менее указанного периода с полной нагрузкой.
7 Состав периодического технического обслуживания ММС 70×23 С
Осмотр внутренних устройств мельницы ( бронефутеровки разгрузочной решётки) и обтяжка болтов крепления машины.
Проверка зазоров в зацеплении венца и подвенцовой шестерни обтяжка болтов крепления зубчатого венца.
Осмотр и обтяжка болтов крепления цапф к барабану мельницы.
Осмотр редукторов главного и вспомогательного приводов ревизия подшипниковых узлов привода осмотр соединительных муфт.
Осмотр и подтяжка сальниковых уплотнителей.
Проверка систем смазки и системы гидроподпора контроль наличия густой смазки в смазываемых узлах.
Ревизия и мелкий ремонт шламовых насосов и питателей.
Осмотр состояния приборов КИПиА.
Проверить имеют ли основной подшипник главный двигатель и вал шестерни ненормальную вибрацию и ненормальный звук и убедитесь что температура подшипника каждой детали не превышает 60 ° C.
Проверить санитарные условия оборудования все остальные части кроме рабочей воздушного компрессора нормальная ли работа нормальное ли напряжение и ток двигателя перегревается ли двигатель протекает ли воздушный канал и т. д.части всегда должны содержаться в чистоте.
8 Структура ремонтного цикла
Периодичность капитальных ремонтов определяется структурой ремонтного цикла. А структура ремонтного цикла определяется установленными нормативами периодичности и последовательности выполнения ремонтов и периодическим техническим обслуживанием в период между двумя сложными капитальными ремонтами. Ремонтный цикл - период между последовательными плановыми капитальными ремонтами машины. Структура ремонтного цикла представляет собой совокупность периодических технических обслуживаний текущих и капитальных ремонтов в порядке проведения их в течении заданного ремонтного цикла изображается в виде графической схемы.
Чтобы построить графическую схему ремонтного цикла необходимо знать следующие нормативы: продолжительность периодичность их проведения и число циклов. Эти данные можно найти в таблице 7.
Таблица 4- Нормативы для построения ремонтного цикла
пто 3пто 3пто 3пто 3пто 3пто 3пто 3пто 3пто 3пто 3пто 3пто
Рисунок 5 - Графическое изображение ремонтного цикла.
Эксплуатация оборудования должна осуществляться в соответствии с требованиями правил технической эксплуатации (ПТЭ) правил промышленной (производственной) безопасности (ППБ) стандартами строительными нормами и правилами в которых изложены основные организационные и технические требования к эксплуатации оборудования. Вся действующая на предприятии нормативно-техническая документация (НТД) по эксплуатации оборудования должна соответствовать требованиям указанных документов.
Правильная эксплуатация оборудования предусматривает:
— разработку должностных и производственных инструкций для эксплуатационного и эксплуатационно-ремонтного персонала;
— правильный подбор и расстановку кадров;
— обучение всего персонала и проверку его знаний ПТЭ ППБ должностных и производственных инструкций;
— содержание оборудования в исправном состоянии путем своевременного выполнения ТО и ремонта;
— исключение выполнения оборудованием работ отрицательно влияющих на окружающую среду;
— организацию достоверного учета и объективного анализа нарушений в работе оборудования несчастных случаев и принятие мер по установлению причин их возникновения;
— выполнение предписаний органов Ростехнадзора.
Непосредственно эксплуатацию оборудования осуществляет эксплуатационный персонал по месту нахождения оборудования. Руководители подразделений в подчинении которых находится эксплуатационный и эксплуатационно-ремонтный персонал должны иметь техническую подготовку по соответствующему оборудованию осуществлять профессиональное руководство и контроль работы подчиненного им персонала.
Лица не достигшие 18-летнего возраста к работе на сложных установках не допускаются. К самостоятельной работе не допускаются практиканты вузов и техникумов. Они могут находиться на рабочих местах только под надзором лица имеющего соответствующую техническую подготовку.
До назначения на самостоятельную работу или при переходе на другую работу (должность) а также при перерыве в работе более одного года персонал обязан пройти медицинское освидетельствование и обучение на рабочем месте. По окончании обучения должна быть проведена проверка знаний работников после чего им присваивается соответствующая группа по безопасности.
После проверки знаний каждый работник должен пройти стажировку на рабочем месте продолжительностью не менее двух недель под руководством опытного работника после чего он может быть допущен к самостоятельной работе. Допуск к стажировке и самостоятельной работе для инженерно-технического персонала оформляется распоряжением по предприятию для рабочих — распоряжением по цеху.
Использование оборудования на рабочем месте должно производиться в соответствии с требованиями инструкции завода-изготовителя приведенной в руководстве по эксплуатации (паспорте) соответствующего оборудования.
В зависимости от характера производства вида и назначения оборудования оно может закрепляться за эксплуатационным и эксплуатационно-ремонтным персоналом который обязан:
— содержать оборудование в исправности чистоте своевременно производить его смазку принимать меры по устранению неисправностей и предупреждать возможность их появления;
— соблюдать установленный режим работы оборудования;
— немедленно останавливать оборудование при появлении признаков неисправностей ведущих к выходу оборудования из строя или создающих опасность для здоровья или жизни людей;
— по контрольно-измерительным приборам визуально и на слух следить за исправной работой оборудования;
— не допускать перегрузок исключать вредное влияние работающего оборудования на строительные конструкции повышенные вибрации пролив жидкостей течи температурные воздействия и т. д.;
— контролировать циркуляцию смазки степень нагрева подшипников не допускать утечки масла. При прекращении подачи масла в системах не имеющих блокировки необходимо остановить оборудование и доложить о происшествии сменному мастеру (механику).
Контроль соблюдения эксплуатационным персоналом инструкции по эксплуатации оборудования защитных приспособлений и устройств учет плановых и неплановых ремонтов аварий и поломок осуществляет мастер цеха который одновременно участвует в составлении актов об авариях и разработке рекомендаций по их предупреждению осуществляет технический надзор за консервацией неиспользуемого оборудования. Мастер цеха обязан помогать эксплуатационному персоналу совершенствовать производственные навыки по эксплуатации предотвращению аварий и предупреждению преждевременного износа оборудования.
Таблица 5- Карта смазки узлов мельницы ММС 70×23 С
Наименование механизма. Номер позиции
Наименование смазочного материала
Способ нанесения смазки
циркуляционная под давлением
подшипник подвенцовой шестерни
подшипник главного двигателя
подшипник вспомогательного двиг.-ля
вспомогательный ред.-р
Таблица 6 – Годовой график ТО и Р «Гидрофол» ММС-70×23С
Примечание: К и Т ремонта указано в сутках О – указано в часах
Наименова-ние оборудования
Количество продолжите-льность
Общая продолжите-льность ТО и ремонта
Испольните-льные работы
«Гидро-фол» ММС-70-23С
Таблица 7– Месячный график ТО и Р оборудования
Передача оборудования от смены к смене производится под расписку в сменном журнале. При сдаче смены в сменный журнал по выявлению дефектов заносятся отказы и неисправности имевшие место в течение смены.
Охрана труда и пожарная безопасность
1 Правила технической безопасности при работе с грузоподъемными механизмами
К управлению грузоподъемными машинами управляемыми с пола а также к подвешиванию грузов на крюк машин могут допускаться лица не моложе 18 лет из числа рабочих пользующихся этими машинами после прохождения инструктажа и последующей проверки навыков по управлению машиной и строповке (обвязке) грузов в соответствии с установленными нормами и правилами.
Инструктаж лиц по управлению грузоподъемной машиной и безопасным способам строповки грузов производится мастером смены а проверка усвоения инструктажа и допуск к работе - начальником участка; мастер и начальник участка должны быть аттестованы организацией на знание соответствующих разделов правил Госгортехнадзора как лица ответственные за безопасное производство работ по перемещению грузов грузоподъемными машинами.
Инструктаж по управлению грузоподъемной машиной управляемой с пола способам строповки грузов и их подвешиванию на крюк должен производиться в сроки предусмотренные для прохождения инструктажа по основной профессии рабочего а также в случае нарушения данной Инструкции.
Настоящая Инструкция выдается всем лицам работающим с грузоподъемными машинами управляемыми с пола под расписку указания в ней обязательны для выполнения. Лица не выполняющие Инструкцию привлекаются к ответственности согласно правилам внутреннего трудового распорядка организации.
Перед началом работы.
Правильно надеть полагающуюся по нормам и находящуюся в исправном состоянии спецодежду спецобувь а при необходимости защитные средства (очки щиток рукавицы и т.п.).
Проверить исправность грузозахватных приспособлений:
а)наличие на них бирок или клейм с указанием номера грузоподъемности и даты изготовления;
б)наличие обрыва отдельных проволочек троса износа и коррозии сверх установленных норм для строп изготовленных из стальных тросов наличие вытяжки и износа свыше 10% первоначального диаметра звена или трещин для строп изготовленных из цепей.
Проверить исправность основных деталей и узлов грузоподъемной машины:
а)наличие и надежность крепления защитного заземления к корпусу кнопочной станции;
б)свободу перемещения кнопок управления в гнездах;
в)состояние троса и правильность его намотки на барабан;
г)состояние крюка (износ в зеве от грузозахватного приспособления не должен превышать 10% отсутствие трещин разогнутость наличие шплинтовки и свободное проворачивание крюка в крюковой подвеске).После указанных проверок включить рубильник;
д)работу тормоза контрольным. грузом или грузом близким к грузоподъемности механизма подъемом данной машиной на высоту 200 300 мм с последующей выдержкой в таком положении в течение 10 мин;
е)работу ограничителя высоты подъема крюка.
Проверить исправность и достаточность освещения места работы.
При обнаружении какой-либо неисправности грузоподъемной машины или грузозахватного приспособления а также по истечении срока очередного испытания ее немедленно сообщить мастеру и без его указаний к работе не приступать. Устранять самому какие-либо неисправности механизмов и электрооборудования запрещается.
Во время работы пользоваться только теми грузоподъемными машинами на которых разрешено работать после получения соответствующего инструктажа.
Быть внимательным не отвлекаться на посторонние дела и разговоры и не отвлекать других.
Обвязку и зацепку грузов производить только в соответствии с графическим изображением способов строповки грузов которые должны быть вывешены на видных местах производства работ.
Для обвязки поднимаемого груза применять стропы соответствующие массе поднимаемого груза с учетом числа ветвей каната или цепи и угла их наклона.
Канаты и цепи подбирать такой длины чтобы угол между их ветвями не превышал 90°.
Не поднимать груз масса которого превышает грузоподъемность машины указанную в паспорте. В сомнительных случаях надо узнать у мастера массу данного груза.
Не допускать подъема крюка грузоподъемной машины до ограничителя высоты подъема. Ограничитель высоты подъема крюка предназначен для аварийных целей.
При обвязке груза с острыми ребрами (углами) применять прокладки для предохранения строп от повреждения. Обвязывать надо так чтобы исключалась возможность выпадения отдельных частей груза и обеспечивалось его устойчивое положение при перемещении.
Мелкоштучные грузы перемещать в специально предназначенной таре при загрузке ее не выше бортов. Тара должна быть исправной и иметь маркировку (номер грузоподъемность собственная масса и назначение).
При подъеме или опускании груза установленного вблизи колонны стены штабеля железнодорожного вагона станка и другого оборудования следить за тем чтобы между грузом и указанными частями здания и оборудования не было людей и не находиться там самим.
Не поднимать груз засыпанный землей или примерзший к земле заложенный или залитый бетоном.
Механизмы подъема груза грузоподъемных машин транспортирующие ядовитые вещества сосуды под давлением воздуха или газа должны иметь два тормоза.
При подъеме груза близкого по массе к разрешенной грузоподъемности следует его предварительно поднять на высоту 200 300 мм и проверить надежность действия тормоза. Во всех случаях перед подъемом груза надо убедиться что груз надежно закреплен и не может выпасть или рассыпаться во время транспортировки.
При обнаружении неисправностей и ненадежной обвязке или зацепке груза опустить его и произвести строповку вновь. Помнить что удерживать стропы соскальзывающие с груза при его подъеме или транспортировке а также поправлять их ударами молотка или лома запрещается.
При перемещении груза в горизонтальном направлении он должен быть поднят не менее чем на 05 м вышележащих на пути предметов. Груз следует поднимать и перемещать плавно без рывков и раскачивания.
Не переключать движение механизма грузоподъемной машины с прямого хода на обратный до полной его остановки.
Не перемещать груз над людьми. Во время перемещения груза в горизонтальном направлении находиться от него на безопасном расстоянии; не проходить в стесненных местах и по загроможденным проходам.
При перекосе не выравнивать поднимаемый или перемещаемый груз массой своего тела.
Для разворота а также для предотвращения самопроизвольного разворота длинномерных и громоздких грузов во время их подъема или перемещения применять специальные оттяжки (канаты крючья) необходимой длины.
Не подтаскивать груз по земле полу или по рельсам при косом натяжении грузового каната грузоподъемной машины. Для этой цели пробовать установки специальных блоков обеспечивающих вертикальное положение грузового каната.
На месте укладки груза предварительно уложить подкладки чтобы стропы можно было легко и без повреждений извлечь из-под груза. Помнить что освобождать грузоподъемной машиной защемленные стропы запрещается.
Перед опусканием груза осмотреть место на которое груз должен быть опущен и убедиться в невозможности падения опрокидывания или сползания устанавливаемого груза.
При перерывах в работе и по окончании ее не оставлять груз в подвешенном состоянии.
Поднять крюк грузоподъемной машины и выключить рубильник.
Убрать съемные грузозахватные приспособления в отведенное для их хранения место. О всех неполадках замеченных во время работы сообщить мастеру и сменщику и записать в сменный журнал.
2 Техника безопасности при выполнении ремонтных работ
Техника безопасности при проведении ремонта для проведения ремонтных работ должны быть назначены ответственные лица за производство работ по перемещению грузов кранами за производство электросварочных работ: перед началом ремонтных работ с повышенной опасностью опасных работ должен быть выдан наряд-допуск в котором оговариваются мероприятия по обеспечению безопасности проводимых работ; зону монтажа демонтажа узлов механизмов отдельных блоков оградить с вывешиванием предупредительных плакатов «Опасная зона» «Проход запрещен».
Нахождение в опасной зоне посторонних лиц воспрещается; перед производством работ ответственные лица обязаны проверить исправность грузозахватных приспособлений исправность электросварочного и газорезательного оборудования инструмента; для выполнения работ по перемещению и поднятию грузов кранами должны быть назначены стропальщики и при необходимости сигнальщики; во время монтажа демонтажа узлов механизмов должны быть выделены места складирования с обозначением их габаритных знаков.
Складирование установка баллонов с газом должна храниться в специально отведенных местах; перед производством работ ответственные лица обязаны произвести дополнительный инструктаж по технике безопасности для рабочих с обязательным оформлением в журнал инструктажа; перед началом ремонтных работ должны быть изготовлены и доставлены к месту ремонта лестницы стремянки подмости леса отвечающие требованиям правил техники безопасности; запрещается допускать к производству работ лиц не достигших 18-ти летнего возраста; работы по изготовлению лесов лестниц дополнительных сооружений установке ограждений изготовление переходов установка грузоподъемных механизмов то есть все работы на выполнение которых для организации безопасного ведения ремонтных работ необходимы затраты дополнительного времени должны оговариваться в графике подготовительных работ; для ведения работ на высоте нужно натянуть монтажный трос и обеспечить рабочих предохранительными поясами; при производстве ремонтных работ все рабочие должны пользоваться защитными касками; для монтажа демонтажа ремонта узлов механизмов при работе выше одного метра от уровня пола или рабочей площадки рабочие должны быть обеспечены прочными и устойчивыми подмостями лестницами; электрическая аппаратура токоведущие части должны быть надежно изолированы и укрыты.
Не допускается применение напряжения при ремонте и для местного освещения более 12 В; ответственность за соблюдение правил технике безопасности возлагается на администрацию предприятия- директора главного инженера начальников участков мастеров бригадиров; электросварочные работы производить в соответствии с требованиями инструкции по технике безопасности для электросварщиков и газосварщиков; работы по инструментальной выверке производить в соответствии с инструкцией по технике безопасности для работников лаборатории инструментально выверки.
3 Меры пожарной безопасности
Мероприятия по пожарной безопасности газо- и электросварочные работы могут производиться только после того как полностью будет устранена всякая возможность возникновения пожара и взрыва. Перед тем как начать указанные работы необходимо иметь письменное разрешение на производство огневых работ лицами ответственными за пожарную безопасность.
При производстве работ по ремонту мельниц необходимо следующие правила пожарной безопасности: в ремонтной зоне в открытых емкостях не должны находиться горючесмазочные материалы; концы и ветошь должны храниться в металлической таре с крышкой; в зоне ремонта должны быть оборудованы посты оснащенные противопожарными средствами тушения пожара согласно действующим нормам; запрещается разбрасывать на площадках и территории промасленные концы ветошь бумагу и т п. газовые баллоны должны находиться в специально отведенных местах. Газовые баллоны должны быть в употреблении только исправные и освидетельствованы согласно нормам Госгортехнадзора; болоны от рабочего места должны находиться не ближе пяти метров; нельзя хранить баллоны с газом возле отопительных приборов ближе одного метра; резаки и шланги на рабочее место выдаются только исправные и проверенные; производить розжиг резака и газорезку вблизи легко загорающихся материалов запрещается; запрещается пользоваться кабелем собранным из отдельных концов со скруткой не изолированными а также с поврежденной изоляцией; во избежание короткого замыкания запрещается пользоваться проводкой с неисправной изоляцией из-за механических повреждений не исправными штепсельными соединениями.
Темой данной курсовой работы является Организация работ по эксплуатации и ремонту мельницы ММС 70×23С типа «Гидрофол».
Курсовая работа состоит из введения и четырех частей: общей специальной охране труда и графической части.
В общей части рассмотрены вопросы основных характеристик и узлов машины принцип работы и технико-экономические показатели а также расчет основных параметров мельницы и деталей на прочность.
В специальной части описаны вопросы качества ремонтных работ передовые методы ведения ремонтных работ назначение капитального ремонта и отличие его от других видов ремонта структура ремонтного цикла испытание наладка и сдача в эксплуатацию.
В графической части указаны чертежи плана цеха общего вида и разреза мельницы .
По подбору расчетных данных конструктивных схем мельницы и её узлов подобран способ и метод ремонта выработаны правильные подходы по техническому обслуживанию машины инструкции по технике безопасности и охране труда а также практические навыки работы с технической литературой и интернет-ресурсами.
Лоскутов Ю.А. и др. Механическое оборудование предприятий
по производству вяжущих строительных материалов. [Текст] Ю.А.Лоскутов.-М.: Машиностроение 1986 - 376 с.: ил.
БанитФ.Г.Эксплуатация ремонт и монтаж оборудования промышленности строительных материалов [Текст]Ф.Г. Банит М-Издательство литературы по строительству 1971-365с
БогдановаВ.С.Основы расчета машин и оборудования предприятий строительных материалов и изделий. [Текст] В.С.Богданова-Л.: Старый Оскол 2013.
Борисов Г.С. Сахаров В.П. Краткий справочник цехового механика [Текст]Г.С.Борисов В.П.Сахаров–М.: Машиностроение 1966;
Дроздов Н.Е. Эксплуатация ремонт и испытание оборудования предприятий строительных материалов изделий и конструкций[Текст] Н.Е.Дроздов -М.: Высшая школа 1979;
Кичихин Н.Н. Такелажные работы [Текст] Н.Н. Кичихин – М. "Высшая школа" 1975.
гидрофол юра.dwg

Специф План.dwg

Плпстинчатый питатель
ДП.МДК.02.01.2-46к.02.ПЗ
Специф Мельница.dwg

Камера самоизмельчения
Венец открытой зубчатой передачи
Вспомогательный привод
Подвенцовая шестерня
Загрузочное устройство