Ленточный конвейер для транспортировки угля


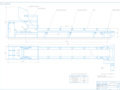
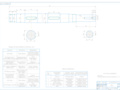
- Добавлен: 25.10.2022
- Размер: 535 KB
- Закачек: 2
Узнать, как скачать этот материал
Подписаться на ежедневные обновления каталога:
Описание
Ленточный конвейер для транспортировки угля
Состав проекта
![]() |
![]() |
![]() ![]() |
![]() ![]() |
![]() ![]() ![]() |
![]() ![]() ![]() ![]() |
![]() ![]() |
![]() ![]() ![]() ![]() |
![]() ![]() |
Дополнительная информация
Контент чертежей
Курсовая работа.docx
2 Техническая характеристика ленточного конвейера
3 Основные элементы конструкции принцип действия
ТЕХНОЛОГИЧЕСКАЯ ЧАСТЬ
1 Техническое обслуживание
2 Текущий ремонт ТР1 ТР2
3 Капитальный ремонт
3.5 Обкатка и опробование
4 Не исправности их способы устранения
ТЕХНОЛОГИЯ РЕМОНТА ДЕТАЛИ
1 Выбор способа и методы ремонта
2 Восттанавление детали
3 Техника безопастности при выполнение ремонтных работ
1 Расчет графика ППР
2 Расчет трудоемкости ремонтных работ
3 Расчет ремонтников необходиых для ремонта
4 Расчет воставнавление детали наплавкой
Для успешного функционирования производственных звеньев сформированы обслуживающие подразделения - транспортное и складское хозяйства различные службы по обеспечению охраны окружающей среды чистоты производственной эстетики территории предприятия.
Первичным звеном организации производственного процесса является рабочее место. Рабочее место – это часть производственной площади оснащённая оборудованием и различными приспособлениями на которой рабочий или группа рабочих (бригада) выполняют одну или несколько операций производственного процесса.
Несколько однородных технологических участков формируют более крупные подразделения предприятия – производственные цехи.
Цех – это административное обособленное подразделения предприятия в котором изготовляется продукция подлежащая дальнейшей переработке на предприятии (полуфабрикат) или готовая продукция поступающая в народно-хозяйственный оборот. Цехи территориально обособлены и работают на основах хозяйственного расчёта. Цех является основным структурным подразделением предприятия. По отношению к выпуску продукции различают основные вспомогательные и подсобные цехи.
Вспомогательные цехи содействуют основным цехам в выпуске основной продукции оказывая им различные услуги. На предприятии функционируют следующие вспомогательные цехи:
Ремонтно-механический цех (РМЦ) поддерживает оборудование на надлежащем техническом уровне;
Электрический цех - производит ремонт электрооборудования перемотку и установку электродвигателей в производственных цехах;
Ремонтно-строительный цех (РСЦ) – осуществляет ремонт зданий и сооружений;
Энергетический цех – включает понизительные преобразовательные подстанции теплоэлектроцентраль парокотельную станцию газогенераторную кислородную установку цех связи.
К подсобным цехам относятся цехи изготовляющие тару или упаковывающую продукцию цехи производящие продукцию из отходов основных и вспомогательных цехов.
Структура управления предприятиями определяется его производственной структурой и учитывает территориальное расположение производственных единиц их специализацию степень юридической самостоятельности и производственно-хозяйственные связи. Управленческие органы в целом осуществляют разработку и принятие основных производственно-хозяйственных и научно-технических решений определяют стратегические направления развития предприятия.
В последние годы на металлургических заводах для перевозки массовых грузов сырья и топлива все большее применение находит конвейерный транспорт. Этот вид транспорта применяют не только на вновь строящихся и проектируемых предприятиях но и на действующих – при реконструкции основных агрегатов. Конвейерами перевозят сырье от вагоноопрокидывателей сортировочных станций или от причала заводского порта на склад со склада на агломерационную фабрику в доменный и коксохимический цехи. Конвейерный транспорт применяют также для подачи твердого топлива на ТЭЦ; известняка руды и других материалов – в сталеплавильные цехи и т.д.
Конвейерный транспорт широко используют для внутрицеховых перевозок. Этому в значительной мере способствует повышение степени непрерывности технологических процессов первых переделов коксохимического агломерационного доменного сталеплавильного при которой другие виды транспорта не обеспечивают современного уровня производства этих переделов.
Развитию внутрицехового конвейерного транспорта способствовало расширение межцеховых перевозок и создание непрерывного технологического потока в масштабе всего завода от приема и складирования сырья до отгрузки готовой продукции. Внутрицеховой конвейерный транспорт применяют не только для выполнения ремонтных работ а также на установках по переработке металлургических шлаков.
Из конвейеров всех типов наибольшее распространение на металлургических заводах получили ленточные доля которых составляет 95 – 97%. Широкое применение конвейерного транспорта объясняется его преимуществами перед транспортом других видов при перемещении значительных объемов грузов на небольшие расстояния. К таким преимуществам относятся: простота конструкции надежность в работе высокая производительность и небольшие эксплуатационные расходы. Кроме того применение конвейерного транспорта позволяет повысить производительность труда и степень автоматизации производства сократить на 10 – 15% площадь завода уменьшить расстояние между цехами упростить транспортные коммуникации вынести общезаводскую железнодорожную станцию прибытия за пределы завода. Внедрение конвейерного транспорта дает возможность повысить степень безопасности на транспорте.
Возможность применения конвейерного транспорта на металлургических заводах в еще большей степени возрастает с разработкой и созданием теплостойких лент позволяющих транспортировать горячие материалы металлургического производства агломерата шлак кокс и др.
1 Общие сведения о ленточном конвейере
Ленточные конвейеры являются наиболее распространенным типом транспортирующих машин непрерывного действия во всех отраслях промышленности. Из более чем полумиллиона конвейерных установок эксплуатирующихся в нашей стране 90% составляют ленточные конвейеры.
Они используются в горнодобывающей промышленности — для транспортирования руд полезных ископаемых и угля при открытой разработке в металлургии – для подачи земли и топлива на предприятиях с поточным производством – для транспортирования заготовок между рабочими местами.
Обычно ленточные конвейеры имеют тяговый элемент в виде бесконечной ленты являющейся и несущим элементом конвейера привод приводящий в движение барабан натяжное устройство с барабаном груз роликовые опоры на рабочей ветви ленты и на холостой ветви ленты отклоняющий барабан загрузочное устройство и разгрузочные устройства и разгрузочный желоб и устройство для очистки ленты. Все элементы конвейера смонтированы на раме.
Ленточный конвейер – машина непрерывного действия предназначенная для транспортировки навалочных грузов по горизонтальным и комбинированным трассам.
Конвейер представляет собой бесконечную непрерывно движущуюся ленту транспортирующую различные навалочные грузы. Лента приводится в движение силой трения между ней и приводным барабаном; опирается по всей длине на стационарные роликоопоры. В шахтах и карьерах ленточные конвейеры служат для транспортирования полезных ископаемых и породы из проходческих вскрышных и добычных забоев по горизонтальным и наклонным выработкам внутри горных предприятий подъёма их на поверхность и последующего перемещения к обогатительной фабрике или погрузочному пункту внешнего транспорта а породы - в отвал. Ленточные конвейеры применяют также для доставки полезных ископаемых от горного предприятия непосредственно к потребителю (например угля на теплоэнергоцентраль или руды на металлургический завод). В шахтах специально приспособленные ленточные конвейеры используются иногда для перемещения людей по наклонным выработкам.
Часто конвейерная лента является одной из частей транспортирующего устройства. Например зернопогрузчик применяющийся на механизированном току для сбора зерновой массы с площадки имеет щёточные скребки далее зерно поднимается норией и попадает на ленточный конвейер который забрасывает зерно в кузов грузового автомобиля.
Ленточные конвейеры широко используются во многих отраслях промышленности – горнодобывающей и горнообрабатывающей промышленности металлургии производстве строительных материалов химической промышленности в переработке и утилизации отходовмусора.
2 Техническая характеристика ленточного конвейера
Техническая характеристика ленточного конвейера представлена в таблице 1.1.
Таблица 1.1 – Техническая характеристика ленточного конвейера
3 Основные элементы конструкции принцип действия
Основным элементом ленточного конвейера является прорезиненная вертикально замкнутая лента огибающая концевые барабаны один из которых является приводным другой – натяжным (рисунок 1.1).
Рисунок 1.1 - Конструкция конвейера
На верхней ветви ленты перемещается транспортируемый груз она является грузонесущей (рабочей) нижняя ветвь является холостой (нерабочей). На всем протяжении трассы лента поддерживаетсяроликоопорамиверхней и нижней ветвей. Лента на холостой ветви имеет плоскую форму на рабочей – желобчатую форму.
Поступательное движение конвейер получает от фрикционного привода необходимое первоначальное натяжение ленты обеспечивается натяжным устройством.В конвейере используется грузовое натяжное устройство которое обеспечивает автоматическое натяжение ленты.
Груз поступает на ленту через одно или несколько загрузочных устройств разгрузка производится с концевого барабана в приемный бункер (концевая).Очистка ленты от прилипших частиц груза осуществляется с помощью очистных устройств.
Технологическая часть
1 Техническое обслуживание
Техническое обслуживание конвейеров включает: осмотр всех элементов конвейера; проверку правильности их работы; регулировку механизмов; ремонт механизмов и деталей.
Техническое обслуживание конвейеров производят визуально при холостом ходе и остановках во время передачи смены машинистами и дежурными слесарями при осмотре проверяют: наличие повреждений ленты; прочность стыка; состояние обкладки бортов; качество очистки ленты; прилегание ленты к роликам; правильность хода ленты загрузки и разгрузки; отсутствие заштыбовки чрезмерного провисания между роликоопорами.
Посадочные места под подшипники качения на оси роликов рабочие поверхности барабанов и роликов подвергаются механическому и абразивно-механическому износу в результате чего происходит изменение их начальных размеров искажение геометрических форм появление рисок и задиров. Причиной дефектов является трение поверхностей деталей при значительных давлениях в присутствии абразивной пыли. Сопрягаемые поверхности роликоопор воспринимают динамические и знакопеременные нагрузки в них возникают различного рода напряжения в ряде случаев они подвергаются интенсивному старению и износу.
При осмотре конвейера проверяют наличие повреждений ленты качество ее очистки прилегание к роликам правильность хода разгрузки и загрузки отсутствие заштыбовки чрезмерного провисания между роликоопорами и опасности пробуксовки.
Плохая очистка ленты ускоряет ее износ поэтому очистные устройства должны быть тщательно отрегулированы. Мелкий ремонт ленты выполняют на месте а при крупных повреждениях на большой длине ленту или ее отдельные участки заменяют.
Сход ленты в сторону должен быть устранен так как он ведет к повреждению кромок ленты и просыпанию груза на холостую ветвь с переносом на натяжную станцию и заштыбовкой ленты. Эксплуатация при ослабленном натяжении ленты приводит к энергетическим потерям снижает срок службы ленты и является причиной пробуксовки на приводном барабане которая ведет к интенсивному износу ленты и футеровки барабана. При работе зимой необходимо следить за тем чтобы не было обледенения барабанов и ленты.
Техническое обслуживание роликоопор ленточных конвейеров предусматривает их периодический осмотр регулировку и замену.
При осмотре приводных станций необходимо следить за износом футеровки приводных барабанов наличием масла в редукторе состоянием муфт тормозов и остановов
ТО барабанов ленточных конвейеров предусматривает их осмотр регулировку и смазку. При осмотре проверяют состояние подшипников по внешним признакам (шум нагрев) и футеровки (износ обрыв). Поврежденную футеровку ремонтируют или заменяют на месте без демонтажа барабана. Для устранения нагрева проверяют и регулируют положение барабана проверяют состояние подшипников. Неисправности подшипниковых узлов происходят из-за отсутствия избытка или загрязнения смазки перекоса самого подшипника.
Натяжные устройства при техническом обслуживании осматривают и устраняют неисправности.
При ТО металлоконструкций проводится тщательный осмотр характерных зон возможных повреждений все расчетные сварные швы заклепочные и болтовые соединения и другие места вероятного появления трещин: резкие изменения сечений элементов; места примыкания ребер накладок косынок; концы сварных швов и места с изменением их толщины и формы.
При обнаружении трещин в ответственных местах металлоконструкций машину не допускают к работе; если дефекты не представляют опасность для нормальной работы машин и обслуживающего персонала их исправление можно приурочить к очередному ремонту.
2 Текущий ремонт ТР1 ТР2
При проведении текущегоремонта конвейераспециалистами сервисного центра могут проводиться следующие работы:
- ремонт или замена изношенной ленты транспортёра;
- очищение и рихтование поврежденных элементов с предварительным снятием облицовки;
- выполнение ремонтных работ моторного блока;
- промывка цепи и звездочек с последующей заменой изношенных элементов и их смазкой;
- регулировка тормозной системы;
- при необходимости производится ремонт или регулировка шлюзных затворов. Их работа должна выполняться в определенном ритме без отставания и задержек. При задевании ими ленты транспортера производится регулировка затворов и установка зазора не менее 5 мм.;
- смазывание и при необходимости замена деталей механизма выдвижной ленты и механизма угла наклона;
- проверка натяжения рабочей поверхности ленты при отвисании произвести сшивание или склеивание;
- проверка кабельных соединений и заземления электросетей устранение повреждение;
- покрытие краской внешней обшивки оборудования;
- финальная проверка работы конвейера на холостом ходу и при полной максимальной нагрузке.
3 Капитальный ремонт
Капитальный ремонт – это плановый ремонт выполняемый с целью восстановления исправности и гарантированного обеспечения работоспособности в течение установленного нормативами количества часов работы до следующего капитального ремонта при котором должны быть восстановлены первоначальные качественные характеристики оборудования; мощность производительность точность и др.
При капитальном ремонте обязательно составляется ведомость дефектов ремонтируемого агрегата. Эта ведомость составляется при разборке оборудования. Каждую деталь рекомендуется маркировать обозначая номер станка в числители порядковый номер детали по ведомости дефектов в знаменателе.
При капитальном ремонте производится очистка полная разборка оборудования промывка узлов замена или ремонт базовых деталей замена всех изношенных деталей и узлов сборка наладка оборудования.
При капитальном ремонте необходимо выполнить разборку оборудования.
Последовательность разборки:
– снять загрузочные устройства и боковые направляющие;
– демонтировать ленту;
– демонтаж натяжного устройства;
– разборка подшипниковых узлов приводного барабана;
– разборка приводного барабана;
– демонтаж натяжной тележки и разборка натяжного барабана;
– разборка роликоопор.
Процесс очистки – этопроцесс удаления загрязненийс поверхностей объектов очистки с помощью физико-химического химического теплового и механического воздействия до такой степени при которой оставшиеся загрязнения не препятствуют проведению ремонтных работ.
Выбор способа очистки и используемого оборудования зависит от массы и размеров детали.
В процессе ремонта распространение получили: физико-химический ультразвуковой и механическиеспособы мойки и очистки деталей.
Физико-химический способ мойки (струйный и в ваннах) заключается в том что загрязнения удаляют с поверхностей деталей водными растворами различных препаратов или специальными растворителями при определенных режимах. Основные режимы это высокая температура химического раствора 80-95°С поток или струя раствора под давлением и эффективные моющие средства.
Ультразвуковой способ основан на передаче энергии от излучателя ультразвука через жидкую среду к поверхности. Колебания составляют 20-30 Гц вызывают большие ускорения и приводят к появлению в жидкости мелких пузырьков при разрыве которых возникают гидравлические удары большой силы. Этотспособ применяется для очисткии конфигураций производится следующими растворами: каустической содой эмульгатор ОБ5-10.
В качестве моющих жидкостей применяются водные щелочные растворы при температуре 80-85°С. Недостаток этих растворов высокое коррозионное действие поэтому применяются для мойки черных металлов. Препараты МЛ-52 МС-8 используют для выварки в ваннах деталей от прочных углеродистых отложений температура этих растворов 70-80°С продолжительность 20 мин. Концентрация водного раствора 20-30 гр. на литр.
По окончании обработки деталей в щелочной ванне их промывают в воде. При температуре 60°С и нейтрализуют 10% водным раствором ортофосфорной кислоты.
Наиболее распространенный механический способ удаления загрязнений косточковой крошкой. Так же бывают пластмассовой крошкой стеклянными шариками гранулами сухого льда.
После промывки на поверхностях разобранных деталей хорошо видны царапины трещины выбоины и можно с необходимой точностью измерить детали при дефектовке.
Дефектовку промытых просушенных деталей производят после их комплектовки по сборочным единицам которую нужно выполнять аккуратно и внимательно. Каждую деталь сначала осматривают затем соответствующим поверочным и измерительным инструментом проверяют ее форму и размеры. В отдельных случаях проверяют взаимодействие данной детали с другими сопряжениями с ней чтобы установить возможен ли ремонт данной детали или целесообразнее её заменить новой.
Сведения о деталях подлежащих ремонту и замене заносят в ведомость дефектов на ремонт оборудования.
Правильно составленная и достаточно подробная ведомость дефектов является существенным фактором в подготовке к ремонту. Этот ответственный документ обычно составляет технолог по ремонту оборудования с участием бригадира ремонтной бригады мастера ремонтного цеха представителей ОТК.
При дефекации важно знать и уметь назначить величины предельных износов для различных деталей оборудования и допустимые предельные размеры.
Детали разбраковывают на три группы:
– Первая – годные для дальнейшей эксплуатации.
– Вторая – требующие ремонта или восстановления.
– Третья – негодные подлежащие замене.
Ремонту подвергают трудоёмкие в изготовлении детали восстановление которых обходится значительно дешевле вновь изготовляемых. Ремонтируемая деталь должна обладать значительным запасом прочности позволяющей восстанавливать или изменять размеры сопрягаемых поверхностей (по системе ремонтных размеров) не снижая (в ряде случаев повышая) их долговечность сохранив или улучшив эксплуатационные качества сборочной единицы агрегата.
Детали подлежат замене если уменьшение их размеров в результате износа нарушают нормальную работу механизма или вызывает дальнейший интенсивный износ который приводит к выходу механизма из строя.
При ремонте оборудования заменяют детали с предельным износом а также износом меньше допустимого если они по расчетам ни дослужат до очередного ремонта. Срок службы деталей рассчитывают с учетом предварительного износа и интенсивности их изнашивания в фактических условиях эксплуатации.
При дефектовке детали необходимо маркировать порядковым номером ведомости дефектов а также инвентарным номером оборудования или станка это облегчает выполнения дальнейших ремонтных операций.
Маркировку выполняют клеймами краской бирками электрографом или кислотой.
Детали которые при дефектовке решено заменить хранят до окончания ремонта механизма они могут понадобиться для составления чертежей или изготовления образцов новых деталей.
Основным техническим документом необходимым для производства плановых работ является дефектная ведомость (таблица 2.1).
Дефектную ведомость составляет бригадир ремонтной бригады или техник ремонтных мастерских. Предварительную дефектную ведомость на средний и капитальные ремонты составляют за 2-3 месяца до ремонта во время одного из плановых осмотров. Окончательную дефектную ведомость составляют при разборке машины перед ремонтом. В дефектной ведомости перечисляют все дефекты отдельных деталей и узлов и указывают методы их устранения. Окончательная ведомость дефектов является документом определяющим объём работ при ремонте.
Таблица 2.1 – Ведомость дефектов.
Метод восстановления
Износ посадочных поверхностей
Износ опорных поверхностей
Износ поверхностей качения
Разрушение сепаратора
Натяжной и приводной барабаны
Износ кромочной поверхности
После капитального ремонта необходимо выполнить сборку оборудования.
Последовательность сборки:
– сборка роликоопор.
– монтаж натяжной тележки и сборка натяжного барабана;
– сборка приводного барабана;
– сборка подшипниковых узлов приводного барабана;
– монтаж натяжного устройства;
– монтировать ленту;
– установить загрузочные устройства и боковые направляющие;
3.5 Обкатка и опробование
При приемо-сдаточных испытаниях следует проводить:
- внешний осмотр и проверку;
- испытания на холостом ходу;
- испытания под нагрузкой;
Внешний осмотр и проверку конвейера проводят перед первым пуском при этом контролируют:
- комплектность и правильность монтажа конвейера;
- комплектность защитных и предохранительных устройств правильность их монтажа;
- комплектность электрооборудования;
- прямолинейность оси конвейера;
- правильность размеров и монтажа роликоопор;
- правильность монтажа барабанов;
- правильность монтажа натяжного устройства;
- правильность монтажа двигателей редукторов и муфт приводов;
- правильность монтажа: очистительных устройств загрузочно-разгрузочных устройств специальных принадлежностей;
- конвейерную ленту правильность выбора ее рабочей стороны качество стыка прямолинейность и симметричность расположения ленты на роликах;
- смазочные вещества правильность наполнения и обозначения смазочных мест;
- действие централизованных и местных смазочных устройств до видимого выжима смазочного материала у объектов смазки;
- действие предупредительных и сигнальных устройств многоразовым их включением и выключением;
- качество окраски поверхностей.
Испытания на холостом ходу проводят после внешнего осмотра и проверки конвейера. Испытания должны охватывать контроль действия и безопасной эксплуатации ленточного конвейера его узлов и деталей при эксплуатации без груза.
Продолжительность испытания стационарного конвейера - до достижения стабильного прямолинейного движения ленты но не менее 2 ч.
При испытании на холостом ходу контролируют:
- фактическую скорость ленты в мс;
- действие тормозов (при четырехкратном пуске и торможении конвейера);
- действие натяжного устройства ленты;
- равномерное вращение барабанов роликов и приводов;
- действия устройств контролирующих ход ленты;
- ход и центрирование ленты на барабанах и роликах верхней и нижней ветви.
Допустимое отклонение ленты от продольной оси конвейера не должно превышать половины разности между длиной приводного (концевого оборотного) барабана и шириной ленты.
Контроль проводят по концевым барабанам при этом датчик положения ленты не должен выключать привод;
- температуру подшипников барабанов роликов и редукторов.
Контроль проводят при помощи датчиков температуры. После непрерывной работы конвейера не менее 2 ч температура подшипников с консистентной смазкой не должна превышать 40 °С жидкой смазкой 70 °С;
- расход энергии приводных двигателей при номинальной скорости ленты;
- действие устройств управления;
- действие предохранительных устройств включением поочередно каждого конечного выключателя ограничителей хода ленты и загрузки конвейера;
- действие электрической блокировки приводов конвейеров (для системы последовательно работающих конвейеров).
Испытания под нагрузкой должны проводиться после испытаний конвейера на холостом ходу. Испытания под нагрузкой должны охватывать контроль работы и безопасной эксплуатации конвейера его узлов и деталей во время эксплуатации конвейера с перемещаемым грузом. Перемещаемый груз должен соответствовать указанному в эксплуатационных документах.
При испытании первый пуск конвейера должен проводиться без груза. Конвейер следует загружать постепенно с помощью загрузочного устройства только после достижения номинальной скорости ленты.
Подача перемещаемого груза должна осуществляться так чтобы начальная производительность конвейера не превышала 25% номинальной производительности после чего подача должна равномерно повышаться до достижения номинальной производительности.
Испытания должны продолжаться до установления стабильности прямолинейного движения ленты но не менее 2 ч.
При испытании под нагрузкой контролируют:
- правильность загрузки конвейера в продольном направлении и центрирование перемещаемого груза на ленте (контроль проводят визуально);
- стабильность положения перемещаемого груза на ленте (контроль проводят визуально);
- действие тормозов (при четырехкратном пуске и торможении конвейера определяют путь и время торможения и отпуска тормозов);
- действие натяжного устройства конвейерной ленты путем двукратного натяжения и ослабления ленты при этом ленту каждый раз следует разгонять до номинальной скорости;
- ход и центрирование ленты на барабанах и роликах верхней и нижней ветви. Ход ленты проверяют при работе конвейера не менее 1 ч при этом сигнализатор хода ленты (указатель перекоса) не должен выключать привод конвейера;
- температуру подшипников барабанов редукторов приводных двигателей и натяжных устройств;
- расход энергии приводных двигателей при номинальной скорости ленты и номинальной производительности конвейера;
- разгон нагруженного конвейера;
- время разгона ленты нагруженного конвейера до номинальной скорости;
- действие устройств для очистки ленты и барабанов;
- действие электрической блокировки приводов конвейеров;
- действие ограничителя обратного хода наклонных конвейеров при загруженной на наклонных участках ленте и отключенном приводе;
- действие устройства для предотвращения превышения номинальной скорости ленты у загруженного конвейера во время перемещения груза под уклон;
- действие загрузочно-разгрузочных устройств;
- производительность конвейера;
- соблюдение специальных требований по вибрации шуму концентрации пыли в рабочей зоне конвейера.
4 Неисправности их способы устранения
Надёжная и бесперебойная работа ленточных конвейеров во многом зависит от того насколько качественные подбирались узлы и детали а также от качества сборки и монтажа. Сначала разбивают оси транспортёра затем монтируется приводная станция. Особое внимание уделяется надёжности закрепленияконвейерав выработке ведь неисправности ленточных конвейеров проявляются часто из-за неустойчивого крепления
Закрепление в зависимости от особенностей конструкции может осуществляться различным способами – распорками если снизу основание ненадёжное штырями если есть за что зацепиться или фундаментальной установкой на бетонное основание. Делее монтируется став затем хвостовая часть. Никаких изгибов оси не должно быть ни в коем случае в противном случае лента будет слетать нарушая работу всей системы.
Основные неисправности ленточного конвейера:
- бывает что рама транспортёра искривлена изначально или стыкование ленты неидеально (отклонение по оси);
- Незапараллелены оси барабанов (приводного – натяжного);
- Перекошены роликоопоры в обеих плоскостях (горизонталь и вертикаль);
- Отклонена от оси лента конвейера;
- Горизонтальная прямолинейность ленты нарушена;
- Натяжение ленты по всей ширине распределена несимметрично.
Проверять на предмет дефектов детали и узлы конвейера следует после тщательной зачистки и промывки их поверхностей. В этом случае все трещины и выбоины становятся заметны также их становится возможным измерять с необходимой точностью (важно для дефектовке). Проверку конвейера на предмет обнаружения дефектов осмотр всех узлов и роликов необходимо осуществлять каждый день перед началом пуска. Каждый месяц должны производиться профилактические работы плановая замена смазочных материалов рабочих жидкостей если необходимо и ремонт узлов.
Неисправности ленточных конвейеров их причины и способы устранения:
) Заклинило ролики барабаны катки и прочее в общем не вращается то что должно вращаться.
Причина: возможно неисправен (расколот) подшипник качения либо некоторые детали лабиринтного уплотнения.
Исправить это можно разобрав подшипник смазав или заменив вышедшие из строя детали.
) Сильно нагреваются некоторые подшипники в барабанах.
Возможно засорение лабиринтного уплотнения сломался сепаратор подшипника или высохла смазка.
Исправляется демонтажем и заменой подшипника или его промывкой и нанесением новой смазки.
) Постоянно сбивается лента в обе стороны.
Либо жёсткость ленты завышена либо загружена не по центру или же узлы собраны недостаточно жёстко.
Излишне жёсткую ленту заменить более подходящим вариантом либо таким же но с меньшим количеством прокладок. Можно также немного наклонить ролики внутрь либо добавить сблокированные направляющие. Крепление узлов проверить и отрегулировать по стандартам.
Если в редукторе привода обнаруживаются ненормальные шумы а также возникают порывы ленты неисправность тормозов видна утечка масла из узлов то при таких неисправностях производится обязательное отключение конвейера.
Технология ремонта детали
1 Выбор способа и методы ремонта
Ремонтная служба на предприятии возлагается на отдел главного механика. Основная задача этого отдела и его цехов – поддержание оборудования предприятия в работоспособном состоянии на основе планово – предупредительного ремонта.
Главный механик возглавляющий отдел несет ответственность перед дирекцией завода за состояние всего заводского оборудования.
Существует три вида организации выполнения ремонтных работ.
На промышленных предприятиях: централизованное децентрализованное и смешанная.
Централизованная организация предусматривает выполнение всех ремонтных работ на заводе силами и средствами отдела главного- механика цеха. Такая организация типично для предприятий с небольшим количеством оборудования.
Децентрализованная организация – выполнение ремонтных работ состоит в том что все виды ремонтных работ – межремонтное обслуживание периодические ремонты в том числе и капитальный ремонт - производят под руководствам механиков цехов так называемыми цеховыми ремонтными базами. В состав цеховых ремонтных баз входят ремонтные бригады. Ремонтно-механический цех подчиняется главному механику осуществляет только капитальный ремонт сложных агрегатов. Кроме того он изготовляет и восстанавливает для цеховых ремонтных баз детали и сборочные единицы оборудования изготовление которых требует применения оборудования отсутствующего на ремонтной базе.
Смешенная организация – выполнение ремонтных работ характерна тем что все виды ремонта кроме капитального выполняют цеховые ремонтные базы а капитальный ремонт – ремонтно-механический цех.
Ремонтно-механический цех также занимается модернизацией действующего парка оборудования в процессе выполнения капитального ремонта и изготовлением запасных деталей для оборудования завода.
В соответствии с работами поручаемыми ремонтно-механическому цеху в его состав входят станочное слесарное и электрогазосварочное отделения.
Цеховые ремонтные базы на крупных заводах входят обычно в состав основных производственных цехов а на небольших заводах часто подчиняются начальнику ремонтно-механического цеха. Их назначение – проводить техническое обслуживание оборудования и выполнять работы по ремонту оборудования. Объём и характер ремонтных работ выполняемых ремонтной базой зависит от того какой вид организации их принят на заводе.
Узловая организация – выполнения ремонтных работ. При более высоком уровне организации производства применяется узловой метод ремонта. При этом методе узлы агрегата требующие ремонта снимают и заменяют запасными заранее отремонтированными приобретенными или изготовленными.
Узловой метод ремонта сокращает время простоя оборудования применяется для оборудования состоящего из конструктивно обособленных узлов. Наиболее целесообразно его применять для следующих видов оборудования: одноименных моделей агрегатов имеющихся на предприятии в большом количестве агрегатов являющихся основными для данного производства кранового оборудования независимо от его количества.
Последовательно-поузловая организация ремонтных работ. Этот метод используют при капитальном ремонте узлов машин. Их ремонтируют не одновременно а последовательно используя кратковременные плановые остановки на малые ремонты а также выходные дни и не рабочие смены. Метод рекомендуется для ремонта уникальных установок и ряда конструктивно-обособленных узлов подъемно-транспортного крупного литейного оборудования агрегатных станков. Агрегат разделяют на узлы которые ремонтируют поочередно.
Изношенные детали восстанавливают следующими способами:
а) сварка дуговая ручная и автоматическая под флюсом и в углекислом газе; сваркой восстанавливают станины и корпусные детали;
б) наплавка - процесс увеличения размеров изношенных деталей электродуговым способом с последующей обработкой детали на заданные размеры; наплавку используют для восстановления валов червячных роторов втулок и т.п.;
в) металлизация - процесс нанесения расплавленного металла с помощью сжатого воздуха; такое напыление осуществляется послойно до 10 мм;
г) электрохимическое покрытие - это процессы хромирования никелирования цинкования до 3 мм;
д) пластические деформации - правка раздача обжатие и т.п.
В ремонтной практике применяются следующие основныеспособы восстановления изношенных деталей: механическая и слесарная обработка сварка наплавка металлизация хромирование никелирование осталивание склеивание упрочнение поверхности деталей и восстановление их формы под давлением. Как правило после восстановления детали одним из способов ее подвергают механической или слесарной обработке что необходимо для восстановления посадок сопряженных деталей устранения овальности или конусности их поверхностей обеспечения требуемой чистоты обработки.
Механической и слесарной обработкой восстанавливают детали с плоскими сопрягаемыми поверхностями (направляющие станин планки клинья). При износе направляющих до 02 мм их восстанавливают шабрением при износе до 05 мм – шлифованием а при износе более 05 мм – строганием с последующим шлифованием или шабрением.
При ремонте валов осей винтов и т. п. в первую очередь проверяют и восстанавливают их центровые отверстия. После этого поверхности имеющие незначительный износ (царапины риски овальность до 002 мм) шлифуют а при более значительных износах наращивают обтачивают и шлифуют до ремонтного размера.
При ремонте изношенных деталей нередко возникают трудности при выборе способа базирования детали для обработки в связи с изменением основной установочной базы изношенной детали. В таких случаях ориентируются не на основные установочные а на вспомогательные базы и от них ведут обработку рабочих поверхностей. Наряду с восстановлением деталей механической обработкой при ремонте негодную часть детали иногда заменяют новой.
Применение компенсаторов износа. Чтобы восстановить первоначальные посадки сопряженных деталей при их значительном износе применяют детали-компенсаторы. Одну из сопрягаемых деталей обрабатывают до ближайшего ремонтного размера и во вторую вставляют промежуточную деталь-компенсатор. Детали-компенсаторы могут быть сменными и подвижными. Сменные компенсаторы устанавливают в сопряжении в котором износ появился к моменту ремонта. Подвижные компенсаторы устанавливают тогда когда можно не производя ремонта соответствующим перемещением компенсатора относительно основных деталей устранить зазор образующийся вследствие износа деталей. Сменными компенсаторами для цилиндрических деталей служат втулки и кольца а для плоских— планки. Для наиболее распространенных узлов станков сменные детали-компенсаторы целесообразно заготавливать заранее в соответствии со шкалой ремонтных размеров.
Ремонт повреждений и заделка трещин. Дефекты возникающие в деталях в результате действия внутренних напряжений больших усилий или из-за механических повреждений (трещины пробоины значительные задиры царапины и выкрашивания) устраняют слесарно-механической обработкой. Трещины и пробоины запаивают заваривают заливают металлизируют ставят штифты и заплаты. Заплаты применяют для заделки пробоин и больших трещин соединяя заплату с основной деталью винтами или заклепками. Для чугунных и дюралюминиевых деталей используют винты а для стальных — еще и заклепки.
Восстановление деталей сваркой и наплавкой
При ремонте оборудования сварку применяют: для получения неразъемных соединений при восстановлении разрушенных и поврежденных деталей для восстановления размеров изношенных деталей и повышения их износостойкости путем наплавки более стойких металлов.
Автоматизированные процессы сварки и наплавки являются более совершенными и экономически эффективными по сравнению с ручными способами. Наибольшее распространение в ремонтной практике получила автоматическая и полуавтоматическая дуговая сварка и наплавка под слоем флюса. Ручные способы сварки и наплавки менее совершенны но являются незаменимыми при ремонте деталей машин в неспециализированных ремонтных предприятиях благодаря маневренности универсальности и простоте процесса.
Газовую сваркуприменяют для восстановления деталей из серого чугуна. Детали малого размера и веса сваривают без предварительного подогрева а крупные детали предварительно нагревают.
Электродуговая сваркаболее экономична и создает более надежное сварное соединение по сравнению с газовой сваркой.
Правильная подготовка детали к сварке обеспечивает высокое качество наплавленного слоя и прочное сцепление его с основным металлом. Перед сваркой детали очищают и разделывают их кромки. Поверхность деталей очищают стальной щеткой напильником наждачным полотном абразивным кругом пескоструйным аппаратом затем промывают бензином или керосином а также подвергают щелочному травлению. Кромки листов свариваемых встык разделывают (скашивают) под углом (60—70°) а края изломов и пробоин выравнивают.
Наплавкаявляется одним из основных методов восстановления деталей. Она широко применяется в тех случаях когда трущимся поверхностям необходимо придать большую износоустойчивость. Наплавляют два три и более слоев часто твердыми сплавами позволяющими увеличить срок службы деталей в несколько раз. Качество наплавки в значительной степени зависит от состояния восстанавливаемой поверхности. Чугунные и стальные детали из малоуглеродистой стали перед наплавкой обезжиривают с целью удаления масла из пор и трещин. Для этого поверхность детали обжигают газовой горелкой паяльной лампой или в нагревательных печах. Копоть налет окислов после обжига удаляют с поверхности детали наждачным полотном или ветошью смоченной керосином или бензином. Участок детали под наплавку обрабатывают стальными щетками или абразивными кругами.
Восстановление деталей металлизацией
Металлизацией называется нанесение расплавленного металла на поверхность детали. Расплавленный металл в специальном приборе — металлизаторе струей воздуха или газа распыляется на мельчайшие частицы и переносится на предварительно подготовленную поверхность детали. Нанесенный слой не является монолитным а представляет собой пористую массу состоящую из мельчайших окисленных частиц.
Способом металлизации восстанавливают размеры посадочных мест для подшипников качения зубчатых колес муфт шеек коленчатых валов и т. п. Чтобы металлизационный слой прочно соединился с поверхностью детали поверхность очищают от грязи и масла и подвергают пескоструйной обработке.
Твердость металлизационного покрытия определяется качеством наносимого материала.
Гальванические покрытия
Для повышения поверхностной твердости деталей и увеличения их сопротивления механическому износу а также для восстановления размеров деталей их покрывают слоем хрома (хромируют) толщиной 025 и 03 мм.
Твердые хромовые покрытия подразделяются на два вида: гладкое и пористое. При гладком хромировании смазка на поверхности детали не удерживается из-за плохой «смачиваемости». При работе деталей возникает сухое трение на трущихся поверхностях появляются задиры. Для устранения этого недостатка применяют пористое хромирование. В порах и каналах образующихся на наружной поверхности детали задерживается смазка снижающая износ и удлиняющая срок службы деталей. Твердое гладкое хромирование применяют для восстановления размеров деталей работающих с неподвижными посадками а пористое — для деталей работающих при значительных удельных давлениях повышенных температурах и с большими скоростями скольжения. Поры и каналы в хромовых покрытиях чаще всего образуются электрохимическим способом при помощи анодного травления.
Восстановление деталей путем гальванического наращивания слоя стали(осталивание или железнение) — один из эффективных методов современной технологии ремонта. Осталивание в отличие от хромирования позволяет наносить слой металла значительно большей толщины (2—3 мм и более). Этим способом целесообразно восстанавливать; детали с неподвижными посадками или детали с невысокой поверхностной твердостью; детали работающие на трение при величине износа более 05 мм; детали работающие одновременно на удары и истира ние.
Твердое никелирование. Повышенная твердость никелевых покрытий достигается за счет применения электролитов специального состава обеспечивающих получение осадков никеля с фосфором. Никелевые покрытия с содержанием фосфора обычно называют никельфосфорными покрытиями а процесс их получения — твердым никелированием. Твердое никелирование может осуществляться электрическим и химическим способами. Химическое никелирование является более простым и осуществляется путем выделения никеля из растворов его солей с помощью химических препаратов — восстановителей.
Восстановление изношенных деталей давлением
Поврежденные и изношенные детали можно восстанавливать давлением. Этот способ основан на использовании пластичности металлов т. е. их способности под действием внешних сил изменять свою геометрическую форму не разрушаясь. Детали восстанавливают до номинальных размеров при помощи специальных приспособлений путем перемещения части металла с нерабочих участков детали к ее изношенным поверхностям. При восстановлении деталей давлением изменяется не только их внешняя форма но также структура и механические свойства металла. Применяя обработку давлением можно восстанавливать детали материал которых обладает пластичностью в холодном или нагретом состоянии. Изменение формы детали и некоторых ее размеров в результате перераспределения металла не должно ухудшать их работоспособность и снижать срока службы. Механическая прочность восстановленной детали должна быть не ниже чем у новой детали.
К основным видам восстановления различных деталей давлением относятся:
- осадка при восстановлении втулок пальцев зубчатых колес;
- раздача при восстановлении пальцев поршней роликов автоматов;
- обжатие при восстановлении вкладышей подшипников и втулок;
- вдавливание при восстановлении зубчатых колес и шлицевых валиков;
- правка для выправления гладких и коленчатых валов и рычагов;
- накатка для увеличения диаметра шеек и цапф валов за счет поднятия гребешков металла при образовании канавок.
Метод пластического деформирования при ремонте деталей применяется не только для восстановления размеров изношенных деталей но и с целью повышения их прочности и долговечности. Поверхностное упрочнение деталей повышает износостойкость и прочность деталей. Пластическое деформирование деталей производят также обработкой стальной или чугунной дробью чеканкой обкаткой роликами или шариками.
2 Восстанавление детали
У валов наиболее часто дефекты появляются на посадочных поверхностях под подшипники и резьбовых поверхностях. Поверхности под подшипники восстанавливают при износе более 0017 - 0060 мм; поверхности неподвижных соединений (места под ступицы со шпоночными пазами и др.) за счет дополнительных деталей - при износе более 04 - 13 мм под уплотнения - более 015 -020 мм. Шпоночные пазы восстанавливают при износе более 0065 - 0095 мм; шлицевые поверхности - при износе более 02 - 05 мм.
Деталь представляет собой вал предназначенный для передачи крутящего момента от ступицы зубчатого колеса на внешнюю нагрузку и изготовлен из стали 40Х ГОСТ 4543-71.
Этот вал нуждается в ремонте одного дефекта: ремонт поверхности посадочных мест
Способы наплавки изношенных посадочных мест
Контактная наварка металлической ленты.
Сущность способа заключается в приварке и изношенной поверхности детали стальной ленты мощными импульсами тока. Режимы работы: частота вращения шпинделя 5 7 мин-1 подача каретки 30 36 ммоб сила тока 5 55 кА. Оборудование: установка 011-1-02М «Ремдеталь».
Механизированная наплавка в среде защитного газа.
В качестве защитной среды используется углекислый газ или водяной пар. Оборудование: выпрямитель ВСЭ-303 сварочный трансформатор ТДФ-500.
Режим работы: наплавку ведут на постоянном токе обратной полярности толщина наплавляемого слоя 08 10 мм сила тока 85 110 А напряжение 18 20 В шаг наплавки 28 32 мм.
Сущность способа состоит в привязке к изношенной поверхности металлической проволоки при пропускании через нее мощного импульса тока. Режим работы: ток 12.. .25 кА шаг 1.. .25 мм усилие прижатия 06 10 кН. Оборудование: установка УЭМО-2.
Плазменная сварка и наплавка.
Наиболее распространенным и простым способом наплавки является наплавка по заранее насыпанному на наплавляемую поверхность порошку. Условия работы: наплавочный материал ПГ-УС25 толщина наплавляемого слоя 1.5 мм напряжение 58 В ток 140 А скорость наплавки 017 ммм. Оборудование: установка для плазменной наплавки УПН-303.
Автоматическая вибродуговая наплавка.
Можно наплавлять детали диаметром от 10 до 400 мм. Рекомендуется применять режимы наплавки в следующих пределах:
Скорость подачи электродной проволоки 14—22 ммсек
Диаметр электродной проволоки 15—2 мм
Наплавка под слоем флюса.
Электрическая дуга горит под слоем гранулированного флюса в газовом пузыре. Сварочный ток 150-200 Амм2 на единицу площади проволоки. Коэффициент наплавки в 15-2 раза выше чем при ручной электродуговой наплавке.
Ручная дуговая наплавка.
Наплавка выполняется металлическими плавящимися одиночными электродами пучком электродов лежачими пластинчатыми электродами и т.д. Для наплавки используют электроды диаметром 3-6 мм. Для обеспечения минимального проплавления основного металла при достаточной устойчивости дуги плотность тока должна составлять 11-12 Амм2.
Для восстановления посадочных мест рационально выполнить автоматическую вибродуговую наплавку.
Таблица 1. Коэффициент долговечности восстанавливаемой детали.
Способ восстановления
Вибродуговая наплавка
Электродуговая наплавка
В среде углекислого газа
Маршрут для восстановления посадочных мест представлен в таблице 3.1.
Таблица 3.1 – Маршрут восстановления посадочных мест
Погружная моечная машина тупикового типа марки ОМ-5287
0 Дефектация и комплектование маршрутов
Промеряют размеры и определяют износы
Стол дефектовщика ОРГ-1468.
5Автоматическая вибродуговая наплавка поверхностей
Восстановление поверхности
Сварочный преобразователь ПС-500.
0 Токарная обработка поверхностей
Обтачивание поверхности
Станок токарно-винторезный 1К62.
Высокий отпуск при температуре 550 – 600°С
0 Шлифование цилиндрических поверхностей
Шлифовать цилиндрическую поверхности
Станок шлифовальный ЗМ153
Контроль восстановленной поверхности
Стол дефектовщика ОРГ-1468
Операции по восстановлению дефектов
Наплавочная: наплавлять поверхности 1. Станок - сварочный преобразователь типа ПС-500. Патрон трехкулачковый 7100-0009 ГОСТ 2675-80 центр вращающийся ГОСТ 8742-75 штангенциркуль ШЦ-П-160-002 ГОСТ 166-80 наплавочная проволока Св-08А.
Токарная: точить поверхности 1. Станок токарно-винторезный 1К62 патрон трехкулачковый 7100-0009 ГОСТ 2675-80 центр вращающийся ГОСТ 8742-75 штангенциркуль ШЦ-П-160-002 ГОСТ 166-80.
Шлифовальная: шлифовать поверхности 1. Станок шлифовальный ЗМ153 хомутик 7107-0031 ГОСТ 2578-70 центр упорный ГОСТ 13214-79 центр вращающийся А-1-5-И ГОСТ 8742-75 ГШ 200x13x32.
Контрольная: стол дефектовщика ОРГ-1468. Штангенциркуль ШЦ-П-160-002-1 ГОСТ 166-80.
3 Техника безопастности при выполнение ремонтных работ
Требования безопасности перед началом работы.
К работе в качестве ремонтного и дежурного слесаря допускаются лица прошедшие специальное обучение инструктаж по технике безопасности и усвоившие безопасные приемы в работе.
Слесари по ремонту оборудования связанные по условиям работы с подъемом транспортировкой и установкой груза при помощи грузоподъемных кранов должны пройти специальное обучение сдать экзамен и иметь при себе удостоверение на ШСУ – 2 – стропальщика на право этих работ.
Обвязку груза производить в соответствии с имеющими схемами строповки находящихся на каждом участке цеха.
Каждый слесарь должен знать и выполнять все требования инструкции при работе с ручным пневматическим и абразивным инструментами при работе на сверлильных и заточных станках при использовании в работе персональных лестниц спасательных поясов.
При совместной работе с электросварщиками или бензорезчиками пользоваться специальными защитными очками (щитками) и рукавицами.
При ремонте технологического оборудования дежурные и ремонтные слесари должны быть объединены в бригады которых мастер назначает старшим квалифицированного рабочего.
До начала производства ремонтных работ должны быть выполнены требования по отключению электроэнергии и принятию мер безопасности согласно «Положения бирочной системы и системы наряд допусков».
Внимательно осмотреть место предстоящих работ или верстак привести его в порядок убрать все загромождающиеся и мешающие работе посторонние предметы. Расположить материал и инструмент приспособления на рабочей площадке так чтобы производить минимум переходов движений поворотов при использовании того или иного элемента.
Проверить наличие и исправность инструмента приспособлений средств индивидуальной и противопожарной защиты. Работать только исправным инструментом и приспособлениями.
При переноске инструмента применять специальную сумку или ящик с несколькими отделениями переносить инструмент в карманах запрещается.
Ручной инструмент должен удовлетворять следующим требованиям:
Слесарные молотки кувалда должны иметь ровную слегка выпуклую поверхность быть насажены на рукоятки овального сечения изготовленные из дерева твердых и вязких пород (дуб береза вяз). Поверхность ручки должна быть гладкой без трещин заусенец и сучков.
Ударный инструмент – молотки зубила бородки обжимки кёрна не должны иметь трещин и заусенец. Длина зубила и крейцмейселя должна быть не менее 150 – 200мм оттянутая часть 60-70мм режущая кромка должна представлять прямую или слегка вытянутую линию.
Напильники отвертки ножовки и другие инструменты с заостренным нерабочим кольцом должны быть прочно закреплены в гладко зачищенной рукоятке снабжены кольцами предохраняющими их от раскалывания.
Гаечные ключи должны соответствовать размерам гаек головок болтов и не иметь трещин и забоин.
Ножовочные станки должны обеспечивать закрепление ножовочных полотен. Не работать полотном имеющим трещины или надломы.
Лезвия отверток должны быть оттянуты и расплющены до такой толщины чтобы они входили без зазора в прорези головок винтов.
Стол слесарного верстака устанавливается горизонтально поверхность стола должна быть гладкой без выбоин и заусенец.
Тиски должны быть прочно закреплены на верстаке и установлены так чтобы в процессе работы слесарь мог занять правильное положение. Слесарные тиски должны иметь хорошо насеченные губки и исправный винт с ограничителем.
Место ремонтных работ должно быть хорошо освещено и чтобы свет не слепил глаза. Если необходимо пользоваться переносной электрической лампочкой проверить есть ли на лампе защитная сетка исправны ли шнур и изоляционная резиновая оплетка. Напряжение допускается не выше 42 вольт а при работе в особо сырых местах или внутри металлоконструкций напряжение должно быть не выше 12 вольт.
К ремонту оборудования приступают:
После разборки эл. схемы согласно установленной в цехе системы допусков и наличия предупредительных плакатов на пусковых устройствах “Не включать – ремонт”.
После отключения питающих трубопроводов сжатого воздуха холодной воды и т.п. и наличия предупредительных плакатов “Не включать – ремонт”.
После снятия приводных ремней рассоединения муфт т.е. тогда когда ни одна часть механизма не могла прийти в движение от случайного включения пусковых приспособлений.
Требования безопасности во время работы.
При работе гаечным ключом запрещается пользоваться прокладками между губками ключа бить молотком по ключу применять ключ вместо молотка наращивать ключ другими ключами или трубой для увеличения усилия затяжек гаек.
Не работать замасленными ключами а в местах не доступных для плоского ключа пользоваться торцевым не пользоваться для свертывания гайки молотком и зубилом.
При работе отверткой не держать изделие в руках навесу а отвертку в другой руке. Отвертка может соскользнуть и поранить руку. Не наносить удар молотком по ручке отвертки.
При работе шабером второй конец закрывать специальным футляром – ручкой.
Для того чтобы при резке металла ручными ножницами не было заусенец между половинками должен быть отрегулирован необходимый зазор а сами ножницы должны быть хорошо заточены. При резке на ручных ножницах коротких полос металла придерживать их клещами или плоскогубцами.
Чистку напильников производить только металлической щеткой.
При работе ударным инструментом пользоваться очками с небьющимися стеклами из органического стекла. Работу ударным инструментом производить в местах огражденных предохранительными устройствами не допускающими облетания осколков в сторону находящихся по соседству рабочих и в направлении проходов. При невозможности установки предохранительных щитков люди из близлежащей зоны должны быть удалены.
При работах требующих разъединения или соединения деталей при помощи кувалды деталь держать клещами не находиться против работающего кувалдой а стоять от него сбоку.
Надевать рукавицы при съеме с ремонтируемого объекта деталей подъеме и переносе их чтобы предохранить руки от ранений а при работе на горячих участках – от ожогов.
Разборку узлов станков агрегатов производить последовательно открепляя деталь следить за тем чтоб не упали сопрягаемые детали на ноги.
Освобождение деталей открепления типа кронштейнов должно производиться после того как приняты меры для предупреждения их опрокидывания.
При разборке (сборке) крупногабаритного оборудования сообщить мастеру о начале работ и производить ее в его присутствии.
Снятые при разборке узлы и детали укладываются устойчиво на деревянные прокладки и в случае необходимости надежно закрепить не загромождать при этом проходов.
Снятие и запрессовку муфт подшипников производить только с помощью специальных приспособлений.
При перемещении детали с одного места на другое последнюю протереть от масла.
Во избежание загрязнения маслом концами и упаковочными материалами места работ следует производить разборку и чистку деталей в стороне от основных работ. Все материалы и отходы необходимо немедленно убирать.
Промывку деталей производить в специально отведенных местах в ваннах или поддонах.
При укладке деталей и узлов следует их так сгруппировать чтобы не пришлось извлекать из-под других деталей.
При ремонтных работах производимых одновременно на разных уровнях нужно принять меры для защиты рабочих от случайно падающих предметов инструмента и приспособлений. Если на высоте работают люди необходимо обходить места работы на безопасном расстоянии участок производства работ должен быть огражден.
Для установки совпадения отверстий в деталях пользоваться только конусными оправками а для отверстий в деталях со значительной толщиной применять сборочные пробки. Проверять совпадение отверстий пальцем запрещается.
Перед пуском отремонтированного узла станка пресса агрегата:
Тщательно осмотреть его и убедиться в том что на станке прессе агрегате и внутри его нет посторонних предметов деталей гаек болтов ключей.
Удалить людей от испытуемого оборудования на безопасное расстояние.
Проверить установлены ли все необходимые ограждения.
Проверить нет ли заедания ударов подозрительных шумов или стуков.
Проверить исправность защитного заземления.
Заполнить соответствующей смазкой масляные картеры.
Опробование станка пресса агрегата в холостую и под нагрузкой допускается только тогда когда оборудование полностью собрано проверено качество выполненных работ произведена регулировка с проверкой на легкость вращения от руки там где это возможно а также установлены ограждения движущихся и вращающихся частей.
Пуск и остановка оборудования после ремонта производится только по команде ответственного лица за ремонт.
Все открытые места и люки около станка пресса агрегата должны быть закрыты.
Если пробный пуск необходим при снятом ограждении предупредить об этом всех работающих рядом выставить предупредительные сигналы “ОСТОРОЖНО – ПРОКРУТКА” и убедиться в том что пуск никому не грозит опасностью.
Не разрешается выполнять работы по ремонту настройке оборудования или устранению всякого рода неполадок не по своей профессии.
Запрещается выполнять ремонтные работы осмотр и устранение дефектов оборудования при ямах под работающими механизмами а также которые могут самопроизвольно опускаться в низ без установки предохранительных прокладок.
Запрещается производить включение каких-либо механизмов если не имеешь на это право.
Требования безопасности по окончанию работы.
Собрать инструмент и приспособления привести в надлежащий порядок и убрать их в отведенное для этого место.
Навести порядок на рабочей площадке.
Убрать с верстака (если здесь работал) все детали уложить их устойчиво в установленное для этого место.
Не мыть руки в масле керосине или бензине и не вытирать их концами обтирочного материал загрязненными стружками.
1 Расчет графика ППР
К работе на ленточных конвейерах как и на других конвейерах допускаются лица прошедшие специальное обучение и имеющие соответствующее удостоверение на право работы на конвейере.
Текущий ремонт Т1 имеет периодичность ЦТ1= 730 часов и продолжительностью Т1=8 часов.
Текущий ремонт Т2 имеет периодичность ЦТ2 = 4380 часов и продолжительностью Т2=36 часа.
Межремонтный цикл ЦК = 19 года = 19 × 26280 = 49932 часов продолжительность капитального ремонта КР= 144 часов.
) Определяем количество текущих ремонтов Т2 в межремонтном цикле:
RТ2=(ЦК ЦТ2) – 1 (4.1)
где ЦК – периодичность межремонтного цикла ч;
ЦТ2 – периодичность ремонтов Т2 ч
RТ2= (49932 4380) –1 = 10411
) Определяем количество текущих ремонтов Т1 в межремонтном цикле:
RТ1=(ЦК ЦТ1) – (RТ2 + 1) (4.2)
где ЦТ1 – периодичность ремонтов Т1 ч
RТ1 = (49932 730) – (104 + 1) = 57
) Структура ремонтного цикла:
2 Расчет трудоемкости ремонтых работ
Из «Временного положения о техническом обслуживании ремонта (ТОиР) механического оборудования » выбираем нормативы затрат труда одну единицу ремонтной сложности для общеотраслевого оборудования:
ЧТ1 = 1 чел × ч – для текущего ремонта Т1
ЧТ2 = 3 чел × ч – для текущего ремонта Т2
ЧТ3 = 5 чел × ч – для капитального ремонта КР
) Определяем трудоемкость текущих ремонтов Т2:
где ЧТ2 – норматив затрат труда на одну единицу ремонтной сложности для ремонта Т2 чел × ч;
Крс – категория ремонтной сложности
ТТ2 = 3 20 = 60 чел ч
) Определяем трудоемкость текущих ремонтов Т1:
где ЧТ1 – нормативы затрат труда на одну единицу ремонтной сложности для ремонта Т1 чел × ч
ТТ1 = 1 20 = 20 чел ч
) Определяем трудоемкость капитального ремонта КР:
где ТКР – трудоемкость капитального ремонта КР
ЧКР – норматив затрат труда на одну единицу ремонтной сложности для
ТКР = 5 20 = 100 чел ч
) Определяем количество ремонтных рабочих на текущий ремонт Т2:
РТ2 = ТТ2 ТТ1 (4.6)
где ТТ2 – продолжительность ремонтов Т2 ч
РТ2 = 60 20 = 3 чел. Принимаем: 3 чел
) Определяем количество ремонтных рабочих на текущий ремонт Т1:
РТ1 = ТТ1 ТТ1 (4.7)
где ТТ1 – продолжительность ремонтов Т1 ч
РТ1 = 20 8 =25 чел. Принимаем: 3 чел
) Определяем количество ремонтных рабочих на капитальный ремонт КР:
РКР = ТКР ТКР (4.8)
где ТКР – продолжительность ремонтов КР ч
РКР = 100 36 =27 чел. Принимаем: 3 чел
4 Расчет воставнавление детали наплавкой
) Расчет наплавляемого слоя
где Acл – величина наплавляемого слоя;
K – припуск на обработки до нанесения материалов;
Z – припуск на механическую обработку после нанесения материалов.
) Размер до восстановления
где Дп – изношенный размер детали.
Pu=1562-2(10+15)=1512
) Размер после восстановления
) Диаметр наплавочной проволоки
Принять значение Дэ по ГОСТ’у
) Коэффициент наплавки
Басов А.И. Механическое оборудование обогатительных фабрик и заводов тяжелых цветных металлов. – М.: Металлургия 1984.
Басов А.И. Ельцев Ф.П. Справочник механика заводов цветной металлургии. – М.: Металлургия 1981.
Донченко А.С. Донченко В.А. Справочник механика рудообогатительной фабрики. – М.: Недра 1975.
Епифанцев Ю.А. Механическое оборудование для обогащения руд. – М.: Машиностроение 1978.
Марон Ф.П. Кузьмин А.В. Справочник по расчетам механизмов подъемно-транспортных машин. – Минск: Высшая школа 1977.
Положение о планово-предупредительных ремонтах оборудования и транспортных средств на предприятиях министерства цветной металлургии.
Свирин В.Г. Ремонтно-вспомогательное хозяйство обогатительных фабрик. – М.: Недра 1978.
ЧЕРТЕЖ.dwg

Верхняя роликовая опора
Загрузочное устройство
*Размеры для справок
Неуказанные предельные отклонения П 142
Наименование показателя
Траспортируемый груз
КП-1014000.З-17-11-ТМ.ВО
Техническая характеристика
Технические требования
ЧЕРТЕЖ2.dwg

комплектование маршрутов
Промеряют размеры и
наплавка поверхности
преобразователь ПС-500
0 Токарная обработка
Неуказаны предельные отклонения размеров H14
КП-1014000.З-17-11-ТМ.РЧ
Сталь 45 ГОСТ 1050-88
Маршрут для восстановления посадочных мест
Технические требования
Рекомендуемые чертежи
- 24.01.2023
Свободное скачивание на сегодня
Обновление через: 22 часа 58 минут
- 25.10.2022