Курсовой проект по ТММ. Вариант 7



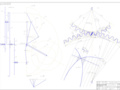
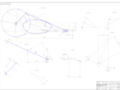
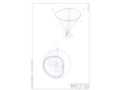
- Добавлен: 25.10.2022
- Размер: 635 KB
- Закачек: 0
Описание
Состав проекта
![]() |
![]() ![]() |
![]() ![]() |
![]() ![]() |
![]() ![]() |
![]() ![]() |
![]() ![]() ![]() ![]() |
![]() ![]() ![]() ![]() |
![]() ![]() |
![]() ![]() ![]() |
![]() ![]() ![]() ![]() |
Дополнительная информация
Чертеж 3.dwg

Чертеж 1.dwg

Пояснительная.doc
ДОНЕЦКИЙ НАЦИОНАЛЬНЫЙ ТЕХНИЧЕСКИЙ УНИВЕРСИТЕТ
Каф. «Основы проектирования машин»
ПОЯСНИТЕЛЬНАЯ ЗАПИСКА
к курсовому проекту по дисциплине: «Теория механизмов и машин»
на тему: Спроектировать и исследовать механизмы компрессора
Руководительк.т.н. доцент
Задание на курсовой проект
Раздел 1. Исследование зубчатого механизма
1. Построение картины эвольвентного зацепления
1.1. Расчет геометрических параметров зацепления
1.2. Расчет контрольных размеров зацепления
2. Проверка качества зубьев и зубчатого зацепления
3. Построение диаграмм удельных скольжений
4. Кинематический анализ
4.1. Аналитический метод
4.2. Графический метод
4.3. Проверка условий существования планетарной передачи
5. Анализ результатов исследования (заключение)
Раздел 2. Исследование рычажного механизма
1. Построение планов механизма
2. Кинематический анализ механизма графическим методом
3. Кинетостатический анализ механизма графическими методами
3.1. Метод планов сил
3.2. Метод рычага Жуковского
4. Анализ результатов исследования (заключение)
Раздел 3. Исследование кулачкового механизма
1. Расчет законов движения толкателя
2. Построение профилей кулачка
3. Анализ результатов исследования (заключение)
Список учебно-методической и используемой литературы
Построение картины эвольвентного прямозубого цилиндрического зацепления колес 5 и 6 выполнено с помощью программного комплекса «КОМПАС-3D». Последовательность построения приведена в методических указаниях [2 стр. 13]. Используемая литература [3 4 5].
Построение картины зацепление осуществлено в масштабе:
Значение коэффициент смещения зубчатых колес принято в соответствии с рекомендациями описанными в методических указаниях
[2 стр. 9]: x5=0.593 xΣ=1.111 тогда x6= xΣ - x5=1.111- 0.593=0.518.
Шаг по делительной окружности колес 5 6:
Радиусы делительных окружностей колес 5 и 6 :
Радиусы основных окружностей колес 5 и 6:
Шаг по основной окружности:
где - эвольвентная функция угла профиля исходного контура α=20° значение функции выбирается в соответствии с рекомендациями методических указаний [2 стр. 11].
По полученному значению эвольвентной функции выбираем в соответствии с указаниями приведенными выше угол зацепления колес 5 и 6 – αw=2301°.
Радиусы начальных окружностей колес 5 и 6:
Межосевое расстояние зубчатого зацепления:
Радиусы окружностей впадин:
Где h*a=1 – коэффициент высоты головки зуба; с*=025 – коэффициент радиального зазора.
Радиусы окружностей вершин колес 5 и 6:
Толщина зуба по делительной окружности:
Толщина зуба по основной окружности:
Толщина зуба по начальной окружности:
Шаг по начальной окружности:
Расхождение равенства:
Вывод: расхождение 002ммчто допустимо.
Толщина зуба по окружности вершин колеса 5:
Где - эвольвентная функция угла профиля на окружности вершин колеса 5 значение функции выбирается в соответствии с рекомендациями методических указаний [2 стр.11].
Где - эвольвентная функция угла профиля на окружности вершин колеса 6 значение функции выбирается в соответствии с рекомендациями методических указаний [2 стр.11].
Длина линии зацепления:
Радиусы кривизны эвольвенты в точке контакта колес 5 и 6 в момент входа зубьев в зацепление:
Радиусы кривизны эвольвенты в точке контакта колес 5 и 6 в момент выхода зубьев из зацепления:
Коэффициент перекрытия:
Результаты сравнения значений геометрических параметров зацепления полученных аналитическим и графическим методами приведены в таблице 1 за основу приняты результаты полученные аналитически. Полученные значения относительных ошибок находятся в допустимых пределах.
Таблица 1 – Результаты определения геометрических параметров зацепления
Геометрические параметры мм
Размер по постоянной хорде колес 5 и 6:
Расстояние от окружности вершин до постоянной хорды:
Длина общей нормали колес 5 и 6:
Где и - число впадин охватываемых измерительной скобой принимается соответственно и .
Результаты сравнения значений контрольных размеров зацепления полученных аналитическим и графическим методами приведены в
таблице 2 за основу приняты результаты полученные аналитически. Полученные значения относительных ошибок находятся в допустимых пределах.
Таблица 2 – Результаты определения контрольных размеров зацепления
Контрольные размеры мм
Проверка на незаострение зубьев колеса 5:
Вывод: условие выполняется следовательно зубья пятого колеса по толщине по окружности вершин незаострены.
Проверка на незаострение зубьев колеса 6:
Вывод: условие выполняется следовательно зубья пятого колеса по толщине по окружности вершин незаострены.
Проверка на условие подрезания зубьев колеса 5:
Вывод: условие выполняется следовательно подрезание зубьев колес 5 отсутствует.
Проверка на условие подрезания зубьев колеса 6:
Вывод: условие выполняется следовательно подрезание зубьев колес 6 отсутствует.
Проверка на отсутствие интерференции между зубьями колеса 6 и выкружками зубьев колеса 5:
Вывод: условие выполняется значит зубья колеса 6 и колеса 5 контактируют только эвольвентными частями профилей т. е. интерференция отсутствует.
Проверка на отсутствие интерференции между зубьями колеса 5 и выкружками зубьев колеса 6:
Проверка по коэффициенту перекрытия:
Вывод: условие выполняется следовательно плавность зацепления колес 5 и 6 обеспечена.
Диаграммы удельных скольжений колес 5 и 6 строятся как функции положения точки контакта колес на линии зацепления по значениям приведенным в таблице 3.
Построение диаграмм выполняется с учетом масштабного коэффициента:
Таблица 3 – Значения коэффициентов удельных скольжений
Положение точки на линии зацепления
Граничные значения коэффициентов удельных скольжений:
- на ножке зуба колеса 5:
- на головке зуба колеса 6:
- на ножке зуба колеса 6:
- на головке зуба колеса 5:
Результаты сравнения граничных значений коэффициентов удельных скольжений полученных аналитическим и графическим метода приведены в таблице 4 за основу приняты результаты полученные аналитически. Полученные значения относительных ошибок находятся в допустимых пределах.
Таблица 4 – Результаты определения коэффициентов удельных скольжений
Коэффициенты удельных скольжений
4. Кинематический анализ зубчатого механизма
Передаточное отношение двухрядной планетарной передачи определяется по методу Виллиса:
Решая данную систему уравнений получаем:
Передаточное отношение цилиндрической зубчатой передачи внешнего зацепления:
Общее передаточное отношение зубчатого механизма:
Угловая скорость колеса 1:
Угловая скорость колеса 6:
Угловая скорость водила Н и колеса 5:
Угловая скорость сателлитов 2 и 3 определяется по методу Виллиса:
Решая эту систему уравнений получаем:
Для кинематического анализа зубчатого механизма графическим методом строится кинематическая схема механизма диаграммы линейных и угловых скоростей. Порядок построения диаграмм приведен в методических указаниях [6 стр. 14].
При построении кинематической схемы зубчатого механизма необходимо учитывать что зубчатые колеса планетарной передачи (1 2 3 и 4) изготовлены без смещения (нулевые) соответственно без скольжения осуществляется качение делительных окружностей колес 1 2 3 и 4. Колеса цилиндрической зубчатой передачи внешнего зацепления (5 и 6) изготовлены со смещением поэтому без скольжения осуществляется качение начальных окружностей колес 5 и 6.
Радиусы делительных окружностей колес планетарной передачи зубчатого механизма:
Построение кинематической схемы механизма выполняется с учетом масштабного коэффициента:
Скорость точки А колеса 1:
Масштабный коэффициент диаграммы линейных скоростей:
где (aa`) – вектор изображающий скорость точки А на диаграмме линейных скоростей.
Масштабный коэффициент диаграммы угловых скоростей:
где ОР=50 мм – расстояние от горизонтальной оси до полюса Р.
Результаты сравнения значений угловых скоростей звеньев зубчатого механизма полученных аналитическим и графическим методами приведены в таблице 5 за основу приняты результаты полученные аналитически. Полученные значения относительных ошибок находятся в допустимых пределах.
Таблица 5 – Результаты расчета угловых скоростей звеньев механизма
Угловая скорость радс
Проверка условия сборки планетарной передачи:
где Е – любое целое число.
Вывод: условие не выполняется т.е. зубья сателлитов не совпадают с впадинами центральных колес.
Проверка условия соосности планетарной передачи:
Вывод: условие выполняется следовательно геометрические оси центральных колес совпадают с геометрической осью вращения водила.
Проверка условия соседства сателлитов планетарной передачи:
Вывод: условие выполняется следовательно колеса соседних сателлитов не соприкасаются
Исследования зубчатого механизма компрессора проведено аналитическим и графическим методами. Полученные значения относительных ошибок результатов исследования различными методами находятся в допустимых пределах.
Зубчатый механизм представляет собой двухступенчатый редуктор состоящий из двухрядной планетарной передачи (передаточное отношение U1-H=8 ) и цилиндрической передачи внешнего зацепления ( передаточное отношение U5-6=-1968 ). Общее передаточное отношение зубчатого механизма равно - U1-6=-15744.
Планетарная передача отвечает условиям существования. Цилиндрическая передача удовлетворяет требованиям качества зубьев и зацепления. В ходе исследования механизма выполнено кинематический анализ и построение картины цилиндрического внешнего зацепления колес 5 и 6.
На основе результатов кинематического исследования зубчатого механизма выполняется его проектирование.
Раздел 2. Исследование рычажного механизма
Построение планов механизма выполняется с помощью программного комплекса «КОМПАС-3D» [1]. Используемая литература [345].
Построение 9 планов механизма (8 соответствующих восьми равностоящих положениям кривошипа через 45° и план в конечном положении механизма) выполняется методом засечек с учетом масштабного коэффициента:
Начало отсчета угла поворота кривошипа 1 принимается от начального положения механизма против часовой стрелки.
На планах механизма строятся траектории движения точек А В S2 путем соединения одноименных точек во всех положениях механизма пунктирной утолщенной линией.
Построение планов скоростей и ускорений кривошипа ползунного механизма выполняется с помощью программного комплекса «КОМПАС-3D» [1]. Используемая литература [345].
Построение плана скоростей для заданного положения механизма (φ*=45°) выполняется с учетом масштабного коэффициента:
Угловая скорость кривошипа 1 принимается равной угловой скорости колеса 6 зубчатого механизма определенной по результатам его кинематического анализа аналитическим методом (см. раздел 1.4.1):
вектор – направлен по касательной к траектории движения точки А в сторону вращения кривошипа 1 т.е. в сторону .
Где - относительная скорость точки В вектор – направлен по касательной к траектории относительного движения точки В вокруг точки А т.е. ; - скорость точки В вектор – направлен вдоль траектории движения точки В т.е. горизонтально.
После построения плана скоростей определяется относительная и абсолютная скорости точки В:
Скорость точки S2 по теореме подобия:
Угловая скорость шатуна 2:
Направление – против часовой стрелки в соответствии с вектором
Построение плана ускорений для заданного положения механизма (φ*=45°) выполняется с учетом масштабного коэффициента:
где (мс2) – нормальное ускорение точки А вектор – направлен к центру вращения кривошипа 1 – к точке О т.е. ; (мс2) – касательное ускорение точки А равно нулю т.к. .
Где (мс2) – относительное нормальное ускорение точки В вектор – направлен к центру относительного вращения шатуна 2 – к точке А т.е. ; - относительное тангенциальное ускорение точки В вектор – направлен по касательной к траектории относительного движения точки В вокруг точки А т.е. ;
- ускорение точки В вектор – направлен вдоль траектории движения точки В т.е. горизонтально.
После построения плана ускорений определяется относительное тангенциальное и абсолютное ускорения точки В:
Ускорение точки S2 по теореме подобия:
Угловое ускорение шатуна 2:
Направление – по часовой стрелке в соответствии с вектором .
Построение планов сил групп звеньев кривошипно-ползунного механизма выполняется с помощью программного комплекса «КОМПАС-3D» [1]. Используемая литература [345].
Кинетостатический анализ выполняется в предположении что трение в кинематических парах отсутствует и все силы действующие на звенья механизма расположены в одной плоскости.
Сила тяжести шатуна 2 и ползуна 3:
Где мс2 – ускорение свободного падения.
Векторы сил тяжести шатуна 2 и ползуна 3 приложены к центрам тяжести звеньев соответственно в точках S2 и В и направлены вертикально вниз.
Центральный момент инерции шатуна 2:
Силы инерции шатуна 2 и ползуна 3:
Векторы – направлены в противоположную сторону ускорению центра тяжести соответственно шатуна 2 и ползуна 3.
Момент сил инерции шатуна 2:
Направление – противоположное направлению углового ускорения шатуна 2.
Момент сил инерции шатуна 2 заменяем парой сил:
Искомые реакции и неизвестны по величине и направлению поэтому показываются условно. Реакция в шарнире А раскладывается на составляющие:
Из уравнения равновесия группы звеньев 2-3:
определяется тангенциальная составляющая реакции в шарнире А
Из уравнения геометрического равновесия группы звеньев 2-3 определяются сила реакции в шарнире А и сила реакции между ползуном3 и направляющей стойки 4:
Построение плана сил группы звеньев 2-3 выполняется с учетом масштабного коэффициента:
После построения плана сил определяются искомые силы реакций:
Сила реакции в шарнире В определяется из уравнения геометрического равновесия звена 2:
Из уравнения равновесия кривошипа
определяется значение уравновешивающей силы:
Реакция в шарнире А определяется из уравнения геометрического равновесия кривошипа 1:
Построение плана сил кривошипа 1 выполняется с учетом масштабного коэффициента:
После построения плана сил определяется искомая сила реакции:
3.2 Метод рычага Жуковського
Построение рычага Жуковского кривошипно-ползунного механизма выполняется с помощью программного комплекса «КОМПАС-3D» [1]. Используемая литература [345].
Построение рычага Жуковского выполняется с учетом масштабного коэффициента:
Из уравнения равновесия рычага Жуковского:
Определяется уравновешивающая сила приложенная к кривошипу 1:
Относительная ошибка значения уравновешивающей силы Fур полученного по результатам анализа аналитическим и методом рычага Жуковского (соответственно Н и Н) находится в допустимых пределах (Δ=% за основу принят результат полученный аналитически).
В ходе выполнения курсового проекта проведено исследование рычажного механизма компрессора графическим методом. Полученные значения относительных ошибок результатов исследования различными способами находятся в допустимых пределах.
Рычажный механизм представляет собой кривошипно-ползунный механизм. Для заданного положения механизма (φ*=45°) установлено значение уравновешивающей силы (Fур=Н) которую необходимо приложить к кривошипу для того чтобы механизм находился в равновесии в данном положении.
На основе результатов кинетостатического анализа выполняется расчет звеньев механизма на прочность жесткость и продольную устойчивость а так же расчет кинематических пар 1-4 1-2 2-3 и 3-4 на износ долговечность и невыдавливаемость смазочного материала.
Расчет законов движения толкателя кулачкового механизма выполняется при помощи компьютерной программы “Синтез кулачкового механизма”. Протокол результатов расчета приведен на странице 25 пояснительной записки. Построение графиков законов движения толкателя выполняется с помощью программы “Microsoft Excel”. На рисунках 1 и 2 приведены графики законов движения толкателя на этапе удаления и на этапе возвращения.
Угловая скорость кулачка принимается равной угловой скорости колеса 6 зубчатого механизма определенной по результатам его кинематического анализа аналитическим методом (см. раздел 1.4.1):
Фазовые углы поворота кулачка соответствующие этапу удаления и этапу возвращения разбиваются на 10 равных интервалов каждый соответственно от 0 до 10 и от 11 до 21. Расчет законов движения толкателя ведется для каждого интервала.
Максимальные значения скорости толкателя на этапе и на этапе возвращения:
Где и - максимальное значение аналога скорости толкателя на этапе удаления и на этапе возвращения соответственно (см. протокол на стр. 25)
Фазовые углы поворота кулачка:
- удаление толкателя fy (град) 115
- дальнего выстоя толкателя fд (град) 65
- возвращения толкателя fв (град) 100
Максимальное перемещение толкателя h (мм) 120
Результаты расчета движения толкателя
Рисунок 1 – Графики законов движения толкателя на этапе удаления.
Рисунок 2 – Графики законов движения толкателя на этапе возвращения
Максимальные значения ускорения толкателя на этапе удаления и на этапе возвращения:
Где и - максимальное значение аналога ускорения толкателя на этапе удаления и на этапе возвращения соответственно (см. протокол на стр.25).
Построение профилей кулачка кулачкового механизма выполняется с помощью программного комплекса «КОМПАС-3D»[1]. Порядок определения минимального радиуса теоретического профиля кулачка приведен в методических указаниях [7 стр.28]. последовательность построения теоретического и действительного профилей кулачка приведены в методических указаниях [7 стр. 33]. Используемая литература [3 4 5].
Характер замыкания кинематической пары кулачок-ролик толкателя принимается геометрическим – за счет использования пазового кулачка. Минимальный радиус теоретического профиля кулачка выбирается из условия ограничения величины угла передачи движения γ характеризующего косвенным образом трение в кинематических парах механизма.
Графические построения для определения минимального радиуса теоретического профиля кулачка выполняются с учетом масштабного коэффициента:
Минимальный радиус – принимается равным r0=140 мм.
Графическое построение теоретического и действительного профилей кулачка выполняется с учетом масштабного коэффициента:
Внешний радиус кулачка принимается равным R=240 мм.
В таблице 6 приведены значения угла передачи движения на этапе удаления и этапе возвращения. На рисунке 3 приведен график изменения угла передачи движения.
Таблица 6 – Значения угла передачи движения на этапе удаления и этапе возвращения
Интервалы этапа удаления
Продолжение таблицы 6
Интервалы этапа возвращения
Рисунок 3 – График изменения угла передачи движения как функция угла поворота кулачка γ=f(φ).
3 Анализ результатов исследования (заключение)
В ходе выполнения курсового проекта проведено исследование кулачкового механизма компрессора графическим методом.
По заданному закону движения толкателя синтезирован профиль кулачка соответствующей формы. Профиль кулачка определяется из условий не заклинивания (γ ≤γmin) и минимальных габаритов (r0) кулачкового механизма.
На основе полученных результатов выполняется силовой расчет звеньев механизма а также расчет кинематических пар кулачок- ролик кулачок-стойка и толкатель-стойка на износ и долговечность.
Кудрявцев В.М. КОМПАС-3D V7. Наиболее полное руководство. – М.: ДМК Пресс 2005. – 664 с.
Проектування евольвентного зубчатого зачеплення з використанням графічної системи КОМПАС-3D. Методичні вказівки до виконання розділу курсового проекту з теорії механізмів і машин Е.Л. Гордієнко В.Г. Пархоменко. – Донецьк: ДонНТУ 2007. – 24с.*
Кіницький Я.Т. Теорія механізмів і машин. Підручник. – К.: Наукова думка 2002. – 660с.
Кіницький Я.Т. Практикум із теорії механізмів і машин. Навчальний посібник. – Львів: Афіша 2004. – 451 с.
Кіницький Я.Т. Короткий курс теорії механізмів і машин. Підручник для інж.-техн. Спец. Вищих навч. закладів України. – 2-е вид. перероб. і. скор. – Львів: Афіша 2004. – 272 с.
Синтез і аналіз планетарних механізмів. Методичний посібник до виконання розділу курсового проекту з теорії механізмів і машин «Проектування зубчастого редуктора»(для студентів механічних спеціальностей) Укл.: Е.Л. Гордієнко В.В. Мазуренко О.Л. Сотніков. – Донецьк: ДонНТУ 2003. – 16 с.*
Методическое указание по применению вычислительной техники в курсовом проектировании по ТММ для студентов механических специальностей Кондрахин П.М. Кучер В.С. Пархоменко В.Г. Гордиенко Э.Л. – Донецк: ДПИ 1982. – 44с.
Чертеж 2.dwg
