Кран портальный « Альбатрос» 10/20 т




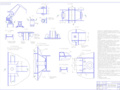
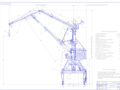
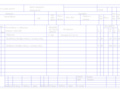
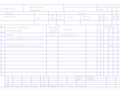
- Добавлен: 25.10.2022
- Размер: 5 MB
- Закачек: 7
Описание
Состав проекта
![]() |
![]() ![]() |
![]() ![]() ![]() |
![]() ![]() ![]() |
![]() ![]() ![]() |
![]() ![]() ![]() ![]() |
![]() ![]() ![]() ![]() |
![]() |
![]() |
![]() ![]() ![]() ![]() |
![]() ![]() ![]() ![]() |
![]() |
![]() ![]() ![]() ![]() |
![]() ![]() ![]() ![]() |
![]() ![]() ![]() ![]() |
![]() ![]() ![]() ![]() |
![]() ![]() ![]() ![]() |
![]() ![]() ![]() ![]() |
![]() ![]() ![]() ![]() |
![]() ![]() ![]() |
![]() ![]() ![]() ![]() |
![]() ![]() ![]() ![]() |
![]() |
![]() ![]() ![]() ![]() |
![]() ![]() |
![]() ![]() ![]() |
![]() ![]() ![]() |
![]() ![]() ![]() |
![]() ![]() |
![]() ![]() ![]() ![]() |
![]() ![]() |
![]() ![]() ![]() |
![]() |
![]() ![]() ![]() ![]() |
![]() ![]() ![]() ![]() |
![]() ![]() ![]() ![]() |
![]() ![]() ![]() ![]() |
![]() ![]() ![]() ![]() |
![]() ![]() ![]() ![]() |
![]() |
![]() ![]() ![]() ![]() |
![]() ![]() ![]() ![]() |
![]() ![]() ![]() ![]() |
![]() ![]() ![]() |
![]() |
![]() ![]() ![]() |
![]() |
![]() ![]() ![]() ![]() |
![]() ![]() ![]() |
![]() ![]() ![]() ![]() |
![]() |
![]() ![]() ![]() ![]() |
![]() ![]() ![]() ![]() |
![]() ![]() ![]() |
![]() |
![]() ![]() ![]() ![]() |
![]() ![]() ![]() |
![]() ![]() ![]() |
![]() ![]() ![]() |
![]() |
![]() ![]() |
![]() ![]() |
![]() ![]() |
![]() ![]() |
![]() ![]() |
![]() ![]() |
![]() ![]() |
![]() ![]() |
![]() ![]() ![]() |
![]() ![]() |
![]() |
![]() ![]() |
![]() ![]() |
![]() ![]() |
![]() ![]() |
![]() ![]() |
![]() ![]() |
![]() ![]() ![]() |
![]() ![]() ![]() |
![]() ![]() |
![]() |
![]() ![]() |
![]() ![]() |
![]() ![]() |
![]() ![]() |
![]() ![]() ![]() |
![]() ![]() ![]() |
![]() ![]() |
![]() ![]() |
![]() ![]() |
![]() ![]() ![]() |
![]() |
![]() ![]() |
![]() ![]() |
![]() ![]() |
![]() ![]() |
![]() |
![]() |
![]() ![]() ![]() |
![]() |
![]() ![]() |
![]() ![]() ![]() |
![]() ![]() |
![]() ![]() |
![]() ![]() |
![]() |
![]() ![]() |
![]() ![]() ![]() ![]() |
![]() ![]() ![]() |
![]() |
![]() ![]() |
![]() ![]() ![]() |
![]() ![]() |
![]() ![]() ![]() |
![]() ![]() ![]() |
![]() ![]() ![]() |
Дополнительная информация
Спец общий вид крана.dwg

Ведомость.dwg

Спец общий вид крана.dwg

Ведомость.dwg

Операц карта5.dwg

Стенд.dwg

Операц карта6.dwg

Операц карта2.dwg

Операционные эскизы.dwg

ПРИСПОСОБЛЕНИЕ.dwg

Операц карта4.dwg

Операц карта7.dwg

Операц карта3.dwg

Схема стрелы.dwg

Расчетные длины для сечений.dwg

схема нагрузок.dwg

Общий вид сечения стрелы.dwg

3 Хобот.dwg

1 Общий вид крана Альбатрос.dwg

6 Ведомость дефектов и проект.dwg

5 Портал.dwg

4 Оттяжка.dwg

2 Стрела.dwg

Сетевой график.dwg

Лист1.dwg

Сетевой график в записку.dwg

Лист1.dwg

Механические характеристики.dwg

Фрагмент.dwg

Тахограмма.dwg

Схема электр..dwg

Циклограмма.dwg

Рекомендуемые чертежи
Свободное скачивание на сегодня
- 22.08.2014
- 29.08.2014