Кран мостовой г/п 16 т



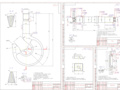
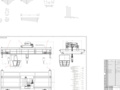
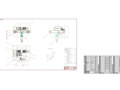
- Добавлен: 25.10.2022
- Размер: 1 MB
- Закачек: 0
Описание
Состав проекта
![]() |
![]() ![]() ![]() |
![]() ![]() ![]() ![]() |
![]() ![]() ![]() ![]() |
![]() ![]() ![]() ![]() |
Дополнительная информация
Записка2.doc
1.Расчет механизма подъема
Выбор крюковой подвески:
Грузоподъемность крюковой подвески не должна быть меньше заданной грузоподъемности:
где Q п - грузоподъемность крюковой подвески;
Q - заданная грузоподъемность.
Принимаем крюковую подвеску: 4-20-406 ОСТ 24.191.08-81
Параметры:Q п = 20т – грузоподъемность; 3М – режим работы;
Z бл. п. = 4 – число блоков; D бл.0. = 406мм – диаметр блока по дну канавок; В вн. = 76мм – расстояние между осями крайних внутренних блоков; Внар. = 260мм – расстояние между осями крайних наружных блоков; bс = 92мм – расстояние между осями крайнего наружного и соседнего с ним внутреннего блока; m = 318кг – масса подвески;
Схема системы полиспастов:
Рисунок 21. Схема палистпаста.
Вес номинального груза и крюковой подвески равен:
где G - вес номинального груза и крюковой подвески;
mгр - номинальная масса груза;
mп – масса крюковой подвески;
g – ускорение свободного падения.
G= (16·103 + 318)·98=160078 Н
По справочным данным находим п = 096; Zк.б = 2. Направляющие блоки в схеме отсутствуют поэтому н.бл = 1.
Максимальное статическое усилие:
G - Вес номинального груза и крюковой подвески;
zк.б .- число ветвей каната навиваемых на барабан;
п - кпд палистпаста;
н.бл - кпд обводных блоков.
Выбираем тип каната в виду того что навивка на барабан будет осуществляться в один слой. ЛК-Р6Х19 (ГОСТ 2688-80) имеющий линейное касание проволок и разные диаметры проволок в верхнем слое пряди.
k зап - коэффициент запаса.
По справочным данным находим:
по таблице ГОСТа выбираем типоразмер каната:
dk = 14 мм имеющий параметры
Назначение – грузовое;
Марка проволоки – высшая;
Маркировочная группа – 1666 Мпа;
Вид покрытия – оцинкованная для среднеагрессивных условий работы;
Вид свивки элементов – одностороннее;
Способ свивки каната – нераскручивающийся:
Направление свивки - правое.
По условию проверим перегиб каната на блоках подвески:
где D бл - диаметр блока измеряемый по средней линии навиваемого каната;
d k - диаметр каната;
e - коэффициент зависящий от типа машины и режима работы.
предварительно найдя по табл. значение е = 14.
d k ·e = 14·20 = 280 мм;
D бл. = D бл.о + d k = 280 + 15 = 295 мм;
D бл > d k·e следовательно условие проверки выполняется .
Основные размеры «Установки верхних блоков»:
По формулам определяем:
где Dбл - диаметр блока измеряемый по средней линии навиваемого каната;
предварительно найдя по табл. значение е = 20
D бл = 14·20 = 280 мм.
В первом приближении:
D бл.0 = D бл – d k ;
где D бл.0 - диаметр блока по дну канавки;
d k - диаметр каната.
D бл.0 = 280 – 14 = 266 мм;
Значение D бл.max. не должно быть меньше чем:
Dбл.о - диаметр блока по дну канавки;
h2 - глубина канавки.
По ОСТ 24.191 05-72 находим ближайшее значение:
Окончательно D бл.ma D бл.0 = D бл.ma D бл = D бл.о + d k = 276 + 14 = 290 мм.
Основные размеры «Установки барабана »
Примем диаметр барабана меньше чем диаметр блока на 15%. Вычислим:
5·d k·e = 085· 14·20 = 238 мм.
Примем Dб 0 = 400мм.
Dб = Dб 0 + d k = 400 + 14 = 414мм;
Рабочая длинна каната соответствующая одному нарезанному участку:
где L к.р. - рабочая длинна каната соответствующая одному нарезанному участку;
u п - кратность палистпаста.
Lк.р. = 10·4 = 40 м.
Число рабочих витков:
где z p - число рабочих витков;
Dб - диаметр барабана.
Длинна одного нарезанного участка:
z р - число рабочих витков для навивки половины полной рабочей длинны каната;
z непр - число неприкосновенных витков;
z кр - число витков для крепления конца каната.
Принимая z непр = l5 и z кр = 3 a также t=16 мм по формуле определяем длину одного нарезного участка:
lн = 16·(31 + 15+3) = 568 мм.
Значение hmin.б. = 3·Dб = 3·414 = 1242 мм.
Длину гладкого среднего участка определим по соотношению:
В нар l 0 В нар + 2h m
где В нар - расстояние между осями крайних наружных блоков крюковой подвески;
[g]-максимально принимаемое при предварительных расчетах значение угла отклонения каната от оси ручья блока.
0 мм l0 260 + 2·1242 (tg 6°) мм или
Длина гладкого концевого участка равна:
Длина барабана будет равна:
где L б - длина барабана;
l к - длинна одного гладкого концевого участка.
Lб=2·568 + 260 + 2·60 = 1516мм.
Максимальная статическая мощность двигателя:
G - вес номинального груза и крюковой подвески;
V-скорость подъема груза;
Предварительное значение КПД механизма примем равным пр= 085.
С учетом коэффициента использования мощности:
N дв = (07 08)·N ст.
где N дв - эквивалентная мощность двигателя;
N ст.max– максимальная статическая мощность.
Nдв = (07 08)· 188 = 1318 1504 кВт.
Выбираем двигатель типа МТF 312-6 имеющий параметры: N = 175 кВт; nд= 950 обмин; Jр.дв.= 0312 кг·м2; dв.дв. = 50 мм; mдв = 210 кг.
Частота вращения барабана равна:
где n б - частота вращения барабана;
v - скорость подъема груза;
u п - кратность палистпаста;
D б - диаметр барабана.
nб = 01·60·43142·0414 = 1846 обмин.
Требуемое передаточное число редуктора:
где u р.тр.- требуемое передаточное отношение;
n дв - частота вращения двигателя;
n б - частота вращения барабана.
Определим расчетный эквивалентный момент на тихоходном валу редуктора. Принимаем класс нагружения механизма В1. Ему при заданной группе режима работы 3М соответствует класс использования А4. По таблице находим значение коэффициента нагружения k = 025.
По табличным значениям находим tмаш = 6300 ч.
Частота вращения тихоходного вала редуктора должна быть равна:
nт = nб = 1846 обмин;
Число циклов нагружения на тихоходном валу редуктора:
Zт = 60·nт·tмаш = 60·1846·6300 = 6977880;
Суммарное число циклов контактных напряжений зуба шестерни тихоходной ступени редуктора:
где Zр – суммарное число циклов контактных напряжений зуба шестерни тихоходной ступени редуктора;
Z т - число циклов нагружения на тихоходном валу редуктора;
u т - передаточное число тихоходной ступени редуктора.
Передаточное число тихоходной ступени редуктора предполагаем близким к значению uт = 5.
Zр = 698·106·5 = 3489·106.
Коэффициент срока службы:
где k t – коэффициент срока службы;
Z р - суммарное число циклов контактных напряжений зуба шестерни тихоходной ступени редуктора;
Z 0 - базовое число циклов контактных напряжений.
Принимаем Z 0 = 125000000
Коэффициент долговечности:
где kд - коэффициент долговечности;
kq - коэффициент переменности нагрузки.
Значение коэффициента kq вычисляем по формуле:
Значения кпд опор барабана примем равными: б = 099.
Расчетный крутящий момент на тихоходном валу редуктора при подъеме номинального груза в период установившегося движения:
где Т р - расчетный крутящий момент на тихоходном валу редуктора при подъеме номинального груза в период установившегося движения;
z к.б.- число ветвей каната навиваемых на барабан;
rб - радиус барабана по средней линии каната;
б - кпд опор барабана.
Тр = 208437·2·0207099 = 87165 Н·м.
Эквивалентный момент на тихоходном валу редуктора:
где Тр.э.- эквивалентный момент на тихоходном валу редуктора;
kд - коэффициент долговечности;
Tр - расчетный крутящий момент на тихоходном валу редуктора при подъеме номинального груза в период установившегося движения.
Тр.э= 041· 87165 = 3574 H·м.
Для обеспечения выбранной кинематической схемы удобно использовать редуктор типа Ц2У имеющий шестерню на конце тихоходного вала.
Номинальный крутящий момент на тихоходном валу :
Тр.н. =8900 Н·м т.е. значительно больше расчетного эквивалентного момента. Следовательно редуктор Ц2У-315Н соответствует требованиям прочности и кинематике механизма. Редуктор имеет параметры: u=50; dв.быстр. = 50 мм; dв.тих. = 110 мм; mр = 510 кг.
Определим фактическую скорость подъема груза:
Передаточное число механизма равное:
где uмех - передаточное число механизма;
uр - передаточное число редуктора;
uп - кратность палистпаста.
Угловая скорость вала двигателя равна:
где дв - угловая скорость вала двигателя;
nдв - частота вращения двигателя.
дв = 3142·95030 = 9943 радс.
Фактическая скорость подъема равна:
где Vпод - фактическая скорость подъема;
uмех - передаточное число механизма.
Vпод = 9943·00207200 = 0103 мс.
Данная скорость отличается от заданной на 3 % что допустимо.
Выбор соединительной муфты:
Для соединения валов двигателя и редуктора выбираем тип муфты – зубчатая. Такая муфта хорошо компенсирует возможные неточности монтажа и может передавать большие крутящие моменты . Диаметры концов: dв.быстр = 50 мм dв.дв = 50 мм. По таблице выбираем типоразмер муфта 1-16000-50-1-50-2У2 ГОСТ 5006 – 83. Данная муфта имеет параметры: Тм.н = 1600 Н·м ; Jм = 006 кг·м2 ; dлев мах= dпр мах = 55 мм mм = 92 кг. Расточки в полумуфтах выполняют по заказу.
Статический крутящий момент при торможении:
где Tст.т - статический крутящий момент при торможении;
Tст.т = 160078·0207·092200 = 15243 Н·м.
Расчетный тормозной момент:
где Тт.р.- расчетный тормозной момент;
kт - коэффициент запаса торможения;
Tст.т - статический крутящий момент при торможении создаваемый весом номинального груза на валу на котором устанавливается тормоз.
По табличным значениям находим kт = 15.
Тт.р. = 15·15243 = 22863 Н·м .
Принимаем: Тт.р. = 230 Н·м.
Выбираем тормоз ТГК-200 с параметрами : Tт.м = 250 Н м ; mтор = 30 кг ; Dт.ш = 200 мм ; Вк = 90 мм.
Тормоз регулируется на расчетный тормозной момент 230 Н·м.
Выбор тормозного шкива:
Учитывая требуемый диаметр тормозного шкива ширину колодок и диаметр быстроходного вала редуктора выбираем муфту имеющую параметры:
Dт.ш = 200 мм ; Вт.ш = 95 мм ; dв. мах = 50 мм; m т.ш = 92кг; J м.т.ш.=0552 кг·м2.
Уточнение момента инерции муфы расположенной на быстроходном валу механизма:
Ранее была выбрана соединительная зубчатая муфта момент инерции которой равен: Jм = 006 кг·м2 .
Половину этой муфты расположенную ближе к редуктору мы заменили тормозным шкивом. Следовательно момент инерции муфты на быстроходном валу механизма изменится и будет равен:
J м.быстр = J м 2 + J м.т.ш ;
где J м.быстр – момент инерции муфт на быстроходном валу механизма;
J м - момент инерции соединительной муфты;
J м.т.ш - момент инерции тормозного шкива.
J м.быстр = 0062 + 0552 = 0582 кг·м2.
Проверка двигателя механизма главного подъема на нагрев
Зададимся усредненным графиком загрузки в зависимости от заданного режима работы.
Рисунок 22. График нагрузки механизма подъёма для режима 3М.
Проверку двигателя на нагрев проведём по эквивалентному крутящему моменту из условия:
где ТЭ – эквивалентный крутящий момент;
Тдв.н.- номинальный крутящий момент на валу электродвигателя.
Эквивалентный крутящий момент:
где Тст.под Тст.оп – статический момент при подъеме и опускании j-го груза;
tр.j. – время разгона при работе с j –м грузом;
tу.под. tу.оп. – время установившегося движения при подъеме и опускании.
Принимаем что за цикл работы производится 10 подъёмов-опусканий груза тогда:
G1 = G н = 160 кН – 4 раз;
G 2 = 0095G н = 152 кН – 3 раз;
G 3 = 005G н = 8 кН – 3 раз;
где G н - вес номинального груза и крюковой подвески.
Статический момент при подъеме j-го груза:
где T ст.п j- Статический момент при подъеме j-го груза;
rб – радиус барабана по средней линии каната;
Uм - передаточное отношение механизма подъёма;
м j – кпд механизма при j грузе;
Uм – передаточное отношение механизма подъёма.
Таблица 2. Результаты расчета.
Статический момент при опускании j-го груза:
где T ст.оп j- Статический момент при опускании j-го груза;
Uм– передаточное отношение механизма подъёма.
Момент инерции создаваемый грузом:
где Jгр. j - момент инерции создаваемый грузом;
m j – масса поступательно движущегося j груза;
Uмех - передаточное отношение механизма подъёма;
j – кпд механизма при j грузе.
Приведенный момент инерции:
где J мех.j - приведенный момент инерции;
g = 115 12 - коэффициент учитывающий момент инерции вращающихся частей;
Jгр.j – момент инерции создаваемый грузом;
Jдв - моменты инерции ротора двигателя;
Jм - моменты инерции муфты;
Jт.ш.- моменты инерции тормозного шкива.
Время разгона при подъёме и опускании:
где t р.п.j - время разгона при подъёме j-го груза;
t р.о.j - время разгона при опускании j-го груза;
wдв.п – угловая скорость двигателя при подъеме;
wдв.о. – угловая скорость двигателя при опускании;
ТП.СР.– пусковой момент двигателя;
T ст.п j- Статический момент при подъеме j-го груза;
T ст.оп j- Статический момент при опускании j-го груза;
w дв.о.= 2wс - w дв = 2×1047 – 994= 1099 с-1;
где n – частота вращения двигателя;
wс – синхронная угловая скорость электродвигателя;
Р = 3 – число полюсов электродвигателя.
Скорость подъема груза:
где wдв.п – угловая скорость двигателя при подъеме;
Uмех - передаточное отношение механизма подъёма.
Скорость опускания груза:
Время установившегося движения при подъёме и опускании:
где t уп - время установившегося движения при подъёме;
t оп - время установившегося движения при опускании;
НСР = 5 8 м – средняя высота подъема.
Окончательно рассчитываем эквивалентный момент:
Заданное условие выполняется следовательно двигатель перегреваться не будет.
Проверка времени торможения механизма подъема
Избыточный тормозной момент:
где Т п т.изб – избыточный тормозной момент;
ТT – тормозной момент;
Tстп - Статический момент при подъеме номинального груза;
Время торможения при подъеме:
где t тп – время торможения при подъеме;
J ппр - приведенный момент инерции;
п – угловая скорость двигателя при подъеме;
Т пт изб – избыточный тормозной момент.
где Т оп т.изб – избыточный тормозной момент;
Tстоп - статический момент при опускании номинального груза;
Время торможения при опускании:
где t тп – время торможения при опускании;
п – угловая скорость двигателя при опускании;
2. Механизм передвижения тележки
Выбираем кинематическую схему с центральным приводом. Ее достоинством является отсутствие перекоса колес при работе двигателя и тормоза во время пусков и торможения .
Рисунок 23. Схема механизма передвижения тележки..
Статические нагрузки на колеса:
Вес номинального груза равен : Gгр = 160078 кН.
Вес тележки определяем по соотношению:
где G - вес номинального груза и крюковой подвески.
Gт = (025 035)·160078=400195 560273 кН.
Принимаем: Gт = 56 кН.
С учетом коэффициента неравномерности распределения нагрузки на колеса максимальная статическая нагрузка на одно колесо будет равна:
Gгр – вес номинального груза и крюковой подвески;
Gт – вес грузовой тележки;
Z – число ходовых колес.
Pст.min= 56·09 4 = 126 кН.
Используя значение Pст.ma [Pk.max] = 100 кН.
Выбор колесных установок:
По диаметру колеса выбираем стандартные колесные установки: приводную колесную установку К2РП – 320 и не приводную колесную установку К2РН – 320 по ОСТ 24.090.09-75. Имеющие размеры:
D = 320 мм; d ц = 55мм; B =80 мм; m к.у.пр = 8502 кг; m к.у.непр = 7716 кг; z реб = 2.
Форма поверхности катания - цилиндрическая. Тип подшипника роликовой радиальный сферический двухрядный с симметричными роликами.
Выбор подтележечного рельса:
Выбираем рельс КР-60 ГОСТ 4121 – 76 с выпуклой головкой. Значение b = 60мм.
Проверим соотношение ширины дорожки катания колеса В и головки рельса b: В – b = 80 – 60 = 20 (соответствует норме 15 20 – для колес двухребордных тележечных).
Другие параметры рельса: R = 350 мм b осн = 105 мм y = 483 см F = 5099 см2 J m пог = 4003 кг материал: Сталь М62.
Сопротивление передвижению тележки:
Сопротивление создаваемое трением:
где Wтр - сопротивление создаваемое трением;
Gгр - вес номинального груза и крюковой подвески;
Gт - вес грузовой тележки;
- коэффициент трения качения колеса по рельсу.
f – приведенный коэффициент трения скольжения в подшипниках колес;
dц – диаметр цапфы колеса;
kдоп – коэффициент дополнительных сопротивлений.
По табличным значениям определяем : 040 f = 0015.
При гибком токопроводе тележки k доп = 20
Wтр = (160+56)·(2·04 + 0015·55 )·2 320 = 22 кН.
Сопротивление создаваемое уклоном:
где Wy - сопротивление создаваемое уклоном;
- уклон рельсового пути;
Gгр - вес номинального груза и крюковой подвески.
По табличным значениям определяем: = 0002 .
Wy = 0002·216 = 0432 кН.
Сопротивление создаваемое силами инерции:
где mпост – масса поступательно движущегося объекта;
mп – масса крюковой подвески.
mпост = 57 – 0318 = 539т
где Wин - сопротивление создаваемое силами инерции;
- коэффициент учитывающий инерцию вращающихся частей механизма;
mпост – масса поступательно движущегося объекта;
[а] – ускорение при разгоне.
По табличным значениям определяем: = 125 (т.к. скорость тележки меньше 1мс ) [a] = 005 мс2 (Рекомендуемое значение).
Wин = 125·539·005 = 0337 кН.
Сопротивление от раскачивания подвески:
W гиб =(Gгр + Gп)·[a] ;
где W гиб - сопротивление от раскачивания подвески;
G гр – вес номинального груза;
G п – вес крюковой подвески;
W гиб = ( 16 + 0.318 )·005 = 0816кН.
Учитывая что кран работает в помещении тогда полное сопротивление передвижению:
W = W тр + W y + W ин + W гиб ;
W = 22 + 0432 + 0337+ 0816 = 3785 кН.
Значение к.п.д. механизма примем = 09.
Из табличных значений = 155 – кратность средне пускового момента двигателя по отклонению к номинальному.
Требуемая мощность двигателя:
где N – требуемая мощность двигателя;
W - полное сопротивление передвижению;
v- скорость передвижения тележки;
- значение к.п.д. механизма;
- кратность среднепускового момента двигателя по отношению к номинальному;
N = 3785· 05 09· 155 = 136 кВт.
Выбираем двигатель: МТF – 011- 6 С параметрами: N дв = 17 кВт ПВ = 25 % n дв = 850 обмин J р.дв.= 0021 кг·м2; d в.дв. = 28 мм; m дв = 51 кг.
Частота вращения колес:
где nк - частота вращения колес;
nк = 30 31415·032 = 2986 обмин.
Требуемое передаточное число механизма равно:
где u - требуемое передаточное число механизма;
u = 850 2986 = 2846 .
Определим расчетный эквивалентный момент на тихоходном валу редуктора. Принимаем класс нагружения механизма В1. Ему при заданной группе режима работы 3М соответствует класс использования А4. По таблице находим значение коэффициента нагружения k=025.
Zт = 60·nк·tмаш = 60 · 2986 ·6300 = 11287080
где Zр - суммарное число циклов контактных напряжений зуба шестерни тихоходной ступени редуктора;
Zт-число циклов нагружения на тихоходном валу редуктора;
uт- передаточное число тихоходной ступени редуктора.
Передаточное число тихоходной ступени редуктора предполагаем близким к значению uт = 5
Zр = 1129·106·5 = 5643·106
Zо - базовое число циклов контактных напряжений.
Принимаем Zо = 125000000
Коэффициент долговечности:
k q - коэффициент переменности нагрузки
Значение коэффициента k q вычисляем по формуле:
Определяем расчетный крутящий момент Тр на тихоходном валу редуктора.
Ориентировочно ВКУ – 350 u p = 315.
КПД редуктора по данным завода изготовителя: р = 094.
Угловая скорость вала двигателя:
где дв – угловая скорость вала двигателя;
n дв - частота вращения двигателя.
дв = 314·85030 = 8894 радс.
Номинальный крутящий момент двигателя:
где Т дв.н. – номинальный крутящий момент двигателя;
дв – угловая скорость вала двигателя.
Тдв.н. = 17·1038894 = 191 Н·м.
Максимальный крутящий момент двигателя:
Т дв.макс. = Т дв.н.· п.макс.;
где Т дв.макс. – максимальный крутящий момент двигателя.
п.макс. – кратность максимального пускового момента;
Примем п.макс. = 2 – кратность максимального пускового момента.
Т дв.макс = 191·2 = 382 Н·м.
Крутящий момент на тихоходном валу редуктора:
Тр = Тдв макс· up·р ;
где Тр - крутящий момент на тихоходном валу редуктора:
Т дв.макс. – максимальный крутящий момент двигателя;
up – передаточное число редуктора;
Тр = 382·315·094 = 1132 Н·м.
Расчетный эквивалентный момент:
где Тр.э. - расчетный эквивалентный момент;
Т р - крутящий момент на тихоходном валу редуктора;
k д - коэффициент долговечности.
Тр э = 063·1132 = 713 Н·м.
Редуктор ВКУ – 350 имеет Тт = 725 Н·м следовательно нам подходит.
dв быстр = 30 мм; dв тих = 35 мм; mp = 120 кг.
Определение фактической скорости:
дв – угловая скорость вала двигателя;
rк – радиус ходового колеса;
uмех – передаточное число редуктора.
Отличие от заданной скорости 8 % - что допустимо.
Для быстроходного вала – зубчатая муфта 1-1000-28-2-30-2-2У2 ГОСТ 5006 – 83.
Для тихоходного вала – зубчатая муфта 1 - 1600 -35-1-55-1-2У2 ГОСТ 5006 –83.
Параметры муфты на быстроходном валу:
Тм н = 1000 Н·м ; Jм = 005 кг·м2 ; dлев =28 мм dправ = 30 мм ; mм = 67 кг.
Параметры муфты на тихоходном валу:
Тм н = 1600 Н·м ; Jм = 006 кг·м2 ; dлев =35 мм dправ = 50 мм ; mм = 92 кг.
Сопротивление передвижению тележки без груза:
где Wу 0 - сопротивление передвижению тележки без груза;
- уклон рельсогого пути;
Wу 0 = 0002·56 = 0112 кH.
Сопротивление передвижению создаваемое трением:
где Wтр 0 - сопротивление передвижению создаваемое трением;
Wтр 0 = 56·(2·04+0015·55)320 = 0143 кН.
Сопротивление передвижению создаваемое инерцией:
где Wин.0 - сопротивление передвижению создаваемое инерцией;
m т – масса грузовой тележки;
а – ускорение при разгоне.
Wин.0 = 125·57·005 = 0356 кН.
Крутящие моменты приведенные к первому валу механизма:
где Ту 0 – крутящий момент создаваемый уклоном приведенный к быстроходному валу редуктора;
Ттр 0 – крутящий момент создаваемый трением приведенный к быстроходному валу редуктора;
Тин.0 - крутящий момент создаваемый силами инерции приведенный к быстроходному валу редуктора;
rk – радиус ходового колеса;
к-т – кпд механизма на участке кинематической цепи «приводное колесо - тормоз»;
Расчетный тормозной момент механизма:
Т тр. мех. = Ту о + Тин.0 – Ттр о ;
Тин.0 - крутящий момент создаваемый силами инерции приведенный к быстроходному валу редуктора.
Т тр. мех. = 051 +154 - 155 = 05 Н·м
Ттр = Т тр. мех. т.к. тормоз в механизме один.
Выбираем тормоз типа ТКГ так как электрогидравлический толкатель являющийся приводом тормоза служит одновременно своеобразным демпфером снижая динамику замыкания тормоза. Это благоприятно скажется на сцеплении колес тележки с рельсами при торможении.
Выбираю типоразмер тормоза – тормоз ТКГ – 160 ОСТ 24.290.08-82.
Тт н = 98 Н·м ; Dт м = 160 мм ; mтор = 25 кг ; Вк = 70 мм ; Ршт = 157 Н ; Lуст = 200 мм ; hшт макс = 25 мм . Тип толкателя – ТЭГ-16М.
Dт.ш = 160 мм ; Вт.ш = 70 мм ; dв. мах = 40 мм; m т.ш = 69 кг; J м.т.ш.=03312 кг·м2.
Проверка двигателя механизма передвижения тележки на время разгона
Проверяем механизм передвижения на возможность проскальзывания колес при пуске.
Максимально допустимое ускорение при пуске:
где [а] - максимально допустимое ускорение при пуске;
z пр – число приводных колес;
z – общее число колес;
φ - коэффициент сцепления для кранов работающих в помещении;
k сц – коэффициент запаса сцепления;
d – диаметр цапфы вала колеса;
D хк – диаметр ходовых колес;
- коэффициент трения качения колеса по рельсу;
k р - коэффициент определяющий трение реборд о головку рельса.
По найденному значению максимально допустимого ускорения найдем минимальное время пуска:
где tп - минимальное время пуска;
v – скорость передвижения тележки;
[а] - максимально допустимое ускорение при пуске.
Определим момент инерции тормозного шкива.
Значение коэффициента учитывающего распределенность массы равно
Тогда момент инерции тормозного шкива будет равен:
где - момент инерции тормозного шкива;
- масса тормозного шкива;
- радиус тормозного шкива;
- коэффициент учитывающий распределенность массы.
Приведенный момент инерции при пуске:
где - приведенный момент инерции при пуске;
γ – коэффициент учитывающий дополнительные вращающиеся массы;
- момент инерции тормозного шкива;
- момент инерции ротора двигателя;
- момент инерции муфты;
m- масса поступательно движущихся частей;
- радиус ходового колеса;
- передаточное отношение редуктора;
Среднепусковой момент двигателя:
где - среднепусковой момент двигателя;
- кратность среднепускового момента двигателя;
- номинальный момент двигателя.
kдоп – коэффициент дополнительных сопротивлений;
По табличным значениям определяем : 04 f = 0015 k доп = 2
Wтр = 56·(2·04 + 0015·55 )·2 320 = 0832 кН .
Gт - вес грузовой тележки.
По табличным значениям определяем: = 0002.
Wy = 0002·56 = 0112 кН .
Учитывая что кран работает в помещении тогда статические сопротивления передвижению:
W = 0832 + 0112 = 094 кН.
Статический момент при разгоне:
где - статический момент при разгоне;
- сопротивления передвижению;
Фактическое время разгона:
где - фактическое время разгона;
- угловая скорость двигателя;
- приведенный момент инерции;
- среднепусковой момент двигателя;
- статический момент при разгоне.
Проверка времени торможения механизма передвижения тележки
Проверяем механизм передвижения на возможность проскальзывания колес при торможении.
Максимально допустимое ускорение при торможении:
где [а] - максимально допустимое замедление при торможении;
По найденному значению максимально допустимого замедления найдем минимальное время торможения:
где tп - минимальное время торможении;
[а] - максимально допустимое замедление при торможении.
Приведенный момент инерции при торможении:
где - приведенный момент инерции;
- масса поступательно движущихся частей;
По табличным значениям определяем : 04 f = 0015.
Wтр = 56·(2·04 + 0015·55 ) 320 = 0279 кН .
W = 0279 - 0112 = 0169 кН.
Статический момент при торможении:
где - статический момент при торможении;
Фактическое время торможении:
где - фактическое время торможении;
- статический момент при торможении.
Данное значение времени торможения слишком велико поэтому увеличим тормозной момент = 30Н·м тогда:
3. Механизм передвижения крана
Выбираем кинематическую схему с раздельным приводом.
Рисунок 24. Схема нагружения моста.
где Gт – вес тележки;
Pмах = максимальная нагрузка на одну сторону крана;
Pмин = максимальная нагрузка на одну сторону крана;
Вес номинального груза равен : Gгр = 160078 кН;
Вес тележки равен G т = 56 кН;
Вес кабины равен G каб =12 кН;
G м= G кр- G каб- G т;
G м= 213 - 12- 56 = 146 кН;
Z – число ходовых колес на одной стороне крана;
Используя значение Pст.ma [Pk.max] = 200 кН.
По диаметру колеса выбираем стандартные колесные установки: приводную колесную установку К2РП – 400 и не приводную колесную установку К2РН – 400. Имеющие размеры:
D = 400 мм; d ц =80 мм; B =100 мм; m к.у.пр = 17572 кг;
m к.у.непр = 16667 кг; z реб = 2.
Выбор подкранового рельса:
Сопротивление передвижению крана:
Gгр - вес номинального груза;
По табличным значениям определяем : 06 f = 0015 k доп = 11.
Wтр = (213+160)·(2·06 + 0015·80 )·11 400 = 2442 кН .
Wy = ·(G кр +G гр ) ;
Gгр - вес номинального груза.
По табличным значениям определяем: = 0001.
Wy = 0001·373 = 0373 кН .
По табличным значениям определяем: = 125 (т.к. скорость тележки меньше 1 мс ) [a] = 005 мс2 ( Рекомендуемое значение ).
Wин = 125·21.7·005 = 1.35 кН.
W гиб =(m гр+m п)·[a] ;
m п – масса крюковой подвески.
W гиб = ( 16 + 0318 )·005 = 08159 кН.
W = W тр + W y + W ин + W гиб;
W = 2442 + 0373 + 135 + 08159 = 498 кН.
Z - число приводов крана.
N = 498· 083 085· 155·2 = 15 кВт.
Выбираем двигатель: МТF – 012- 6 С параметрами: N дв = 27 кВт ПВ = 25 % n дв = 840 обмин J р.дв.= 0029 кг·м2; d в.дв. = 28 мм; m дв = 58 кг.
V- скорость передвижения тележки;
nк = 50 31415·04 = 398 обмин.
Выбираем тип редуктора Ц2У-160 с передаточным числом равным 22.
Zт = 60·nк·tмаш = 60·398·12500 = 7522200
Zр = 75222·106·5 = 37611·106.
где k д - коэффициент долговечности;
k q - коэффициент переменности нагрузки;
КПД редуктора по данным завода изготовителя: р = 097.
дв = 314·84030 = 8792 радс.
Тдв.н. = 27·1038792 = 307 Н·м
где Т дв.макс. – максимальный крутящий момент двигателя;
Т дв.макс = 307·2 = 614 Н·м.
Тр = 614·22·097 = 1310 Н·м
Тр э = 063·1310 = 825 Н·м.
Редуктор Ц2У-160 имеет Тт = 1000 Н·м следовательно нам подходит.
dв быстр = 25 мм; dв тих = 55 мм; u = 22; mp = 95 кг.
где V предв. кр. – скорость передвижения тележки;
V предв. кр. = 8792·0222 = 08 мс.
Отличие от заданной скорости 4 % - что допустимо.
Для быстроходного вала – зубчатая муфта 1-1000-28-2-25-2-2У2 ГОСТ 5006 – 83.
Для тихоходного вала – зубчатая муфта 1 - 10000 -80-1-55-1-2У2 ГОСТ 5006 –83.
Тм н = 1000 Н·м ; Jм = 005 кг·м2 ; dлев =28 мм dправ = 25 мм ; mм = 67 кг.
Тм н = 10000 Н·м ; Jм = 05 кг·м2 ; dлев =80 мм dправ = 55 мм ; mм = 369 кг.
Сопротивление передвижению крана без груза:
где Wу 0 - сопротивление передвижению крана без груза;
Wу 0 = 0001·213 = 0213 кH.
Wтр 0 = 213·(2·06+0015·80) 400 = 128 кН.
Wин.0 = 125·217·005 = 135 кН.
Т тр. мех. = Ту о + Тин.0 – Ттр о;
Т тр. мех. = 178 + 113 - 1265 = 043 Н·м.
Н·м т.к. тормозов в механизме два.
Проверка двигателя механизма передвижения крана на время разгона
Проверяем механизм передвижения на возможность проскальзывания колес при пуске
k – коэффициент учитывающий количество приводов в механизме.
- номинальный момент двигателя;
По табличным значениям определяем : 06 f = 0015. k доп = 2.
Wтр = 213·(2·06 + 0015·80 )·2 400 = 14 кН.
Wy = 0001·213 = 0213 кН.
W = 14 + 0213 = 1613 кН.
По табличным значениям определяем : 06 f = 0015.
Wтр = 213·(2·06 + 0015·80 ) 400 = 128 кН .
Wy = 0001·213 = 0213 кН .
W = 128 – 0213 = 1068 кН.
Данное значение времени торможения слишком велико поэтому увеличим тормозной момент каждого тормоза до =35 Н·м тогда:
1. Расчет элементов барабана
Толщина цилиндрической стенки
Принимая в качестве материала барабана сталь 35Л([сж] = 137 МПа определяем приближенное значение толщины стенки барабана:
t – расстояние между соседними витками каната;
[]сж – допустимое напряжение.
Уточним полученное значение для чего определим коэффициент влияния деформаций стенки барабана и каната:
где Eк – модуль упругости каната;
Fк – площадь сечения проволок каната;
Eб - модуль упругости стенки барабана.
то допускаемые напряжения смятия необходимо понизить на 5%.
Тогда []сж = 137 - 685= 13015 МПа.
С учетом уточнений толщина цилиндрической стенки барабана равна
Учитывая что стенка барабана в процессе эксплуатации изнашивается принимаем 8 = 10 мм.
Устойчивость цилиндрической стенки барабана
Для определения необходимости проверки устойчивости подсчитываем номинальное напряжение сжатия в стенке барабана
При этих параметрах следует что проверку устойчивости стенки необходимо производить если отношение LDб.0 > 4. Для проектируемого барабана LDб.0 = 1516400 = 379. Следовательно проверки устойчивости стенки не требуется.
Крепление каната к барабану
Применяя способ крепления прижимными планками с полукруглыми пазами прижимающими два соседних витка определяем суммарное усилие растяжения болтов.
где f – коэффициент трения между канатом и барабаном;
γ – угол наклона боковой грани трапециевидного выреза в планке к вертикале;
α – угол обхвата барабана неприкосновенными витками;
e – основание натурального логарифма.
Используя нормализованные планки ПО «Сибтяжмаш» для диаметров каната 14 17 мм задаемся диаметром болта М16 по диаметру отверстия в планке. Тогда необходимое число болтов (планок) выполненных из стали ВСтЗсп ([]сж = 230 МПа) будет равно
где k – коэффициент запаса надежности крепления каната к барабану;
l – расстояние от дна канавки на барабане до верхней плоскости прижимной планки.
Принимаем число крепежных болтов z= 6.
Ось барабана испытывает напряжения от веса барабана усилий в канатах сходящих с барабана.
Рисунок 25. Схема нагружения и эпюра изгибающего момента оси барабана.
где S1S2 – реакции на валу от барабана;
R1R2 – реакции в опорах.
Из уравнения моментов реакции опор равны:
Изгибающие моменты в сечениях под ступицами барабана:
Принимаем в качестве материала оси сталь 45 (в= 598 МПа 1 = 257 МПа). Допускаемые напряжения:
где [-1] – предел выносливости;
[n] – допускаемый коэффициент запаса прочности;
k0 – коэффициент учитывающий конструкцию детали.
Предварительно диаметр оси под правой ступицей (здесь действует наибольший момент) определяем по формуле
Принимаем d д = 84 мм. Исходя из этого диаметра конструируем ось барабана.
2. Расчет металлоконструкции моста
В дополнение к исходным данным на основании расчетов и проработки конструкции тележки и механизмов крана имеем: (GТ = 2746 кН - вес тележки; Вт = 43 м - база тележки; LT = 42 м - колея тележки; G Kp.п. = 360 кН - вес крюковой подвески механизма главного подъема; G пp = 90 кН - вес одного приводного узла механизма передвижения крана; jК = 01 мс2 - среднее ускорение крана при разгоне.
В соответствии с результатами компановки тележки статические давления на колеса составляют:
от номинального собственного веса: Дт = 1568 кН;
от веса номинального груза: ДQ = 6092 кН
суммарные статические: Дт = 766 кН.
Вес кабины управления принимаем равным GK = 15 кН.
Материал конструкции
В качестве материала для основных несущих элементов принимаем малоуглеродистую сталь ВСтЗсп5 по ГОСТ 380-71*.
Расчетные сопротивления основного металла R (МПа) равны:
при растяжении сжатии изгибе - R = 210; при срезе – Rсp = 130;
при смятии торцевой поверхности – R т.см. = 320.
Расчетные сопротивления сварных соединений (МПа) принимаем:
для заводских стыковых швов при работе на растяжение и сжатие - RCB= 210;
при работе на срез - RCBср = 130;
для угловых швов при работе на срез RCBу ср = 150.
Средняя часть пролетной балки
Необходимую высоту балки в среднем сечении определяем из условия :
Принимаем Н = 1100 мм.
Для обеспечения достаточной жесткости при кручении ширина балки по осям вертикальных листов выбирается из условий :
Принимаем В = 450 мм.
Рисунок 26. Сечение пролетной балки в средней части пролета.
Тогда геометрические характеристики сечения:
Вертикальной плоскости:
Реакции в опорах балки:
Изгибающие моменты в сечении балки:
Рисунок 27. Схема нагружения и эпюра изгибающего момента пролетной балки в вертикальной плоскости.
В горизонтальной плоскости:
При jК = 01 мс2 т.е. при jКg =00399 горизонтальные инерциальные нагрузки будут равны:
Рисунок 28. Схема нагружения и эпюра изгибающего момента пролетной балки в горизонтальной плоскости.
Проверку производим по условию:
Прочность средней части балки при общем изгибе в двух плоскостях обеспечена.
Опорная часть пролетной балки
Основные размеры определились при компановки опорного узла. Принятое поперечное сечение:
Рисунок 29. Сечение пролетной балки в опорной части пролета.
Геометрические характеристики сеченая:
Основные размеры торцевой балки определились при компановки опорного узла. Расчетная длина балки равно Lб.к = 35 м.
Рисунок 30. Сечение торцевой балки.
Геометрические характеристики сечения:
Проверку прочности балки в опасном сечении - узле сопряжения с пролетной балкой.
где P1P2 – реакции от действия пролетных балок.
Изгибающий момент в вертикальной плоскости:
Рисунок 31. Схема нагружения и эпюра изгибающего момента торцевой балки.
Прочность торцевой балки обеспечена.
Фактическая гибкость стенки пролетной балки в ее средней части:
75 200 т. е. стенка может укрепляться только поперечными основными ребрами жесткости. Диафрагмы будем выполнять из листового проката; в больших диафрагмах выполним вырезы в средней части.
Ширину выступающей части ребра определяем по условию:
толщина ребра должна быть не менее
Принимаем: b p = 009 м; p = 0008 м;
Момент инерции ребра относительно плоскости стенки:
Проверку прочности ребра по условиям работы его верхней кромки на сжатие:
м4 – момент инерции полки;
Jpc = 6546 см4 = 6546·10-6 м4 - момент инерции рельса;
где z – расчетная зона распределения давления колеса по ребру;
Jп - момент инерции полки;
где Д – давление колеса тележки;
S pc – длинна линии контакта рельса и пояса над ребром;
Следовательно прочность верхней кромки диафрагмы обеспечена.
Из условия прочности рельса:
Д – давление колеса тележки.
Учитывая что пояс балки достаточно тонкий для обеспечения его прочности при действии местных напряжений от давления колес тележки принимаем конструктивно шаг больших диафрагм в средней части балки a1= 3 м. В концевых частях балки ребра ставим в соответствии с необходимостью приварки фундаментов под привод механизма передвижения крана.
Технико-экономический расчет
Производительность крана наряду с грузоподъемностью является основным параметром грузоподъемных машин. Она зависит от грузоподъемности времени цикла опыта крановщика и других факторов.
Техническая производительность крана:
где Киг – коэффициент использования по грузоподъемности;
m – грузоподъемность;
tц – время цикла tц 40 с;
tс – время строповки и расстроповки груза tс 20 с;
Эксплуатационная производительность:
где КИВ = 04 07 – коэффициент использования машины по времени;
ПЭ =480 × 055 = 264 тч;
Стоимость машиносмены является основным показателем эффективности грузоподъемной машины.
где К ТР = 07 09 – коэффициент учитывающий транспортное время на перемещение между объектами;
С Р = 102 у. е.– расчетная стоимость перемещения одной тонны груза;
t СМ = 8 часов – продолжительность смены;
С МС = 08×099×264×102×8 = 170616 у.е.см;
Тележка.dwg

т. . . . . . . . . . . . . . . . . . . . . .16 2. Высота подъема груза
м. . . . . . . . . . . . . . . . . .10 3. Режим работы. . . . . . . . . . . . . . . . . . . . . . . . . . Л 4. Продолжительность включения. . . . . . . . . . ПВ=25% 5. Скорость
мс: подъема груза. . . . . . . . . . . . . . . . . . . . 0
передвижения тележки. . . . . . . . . . . . . . 0
6. Электродвигатель механизма: подъема груза: тип. . . . . . . . . . . . . . . . . . . МТF 312-6 мощность
кВт. . . . . . . . . . . . . . . . 17
обмин. . . . . . . .950 передвижения тележки: тип. . . . . . . . . . . . . . . . . . . .MTF 011-6 мощность
кВт. . . . . . . . . . . . . . . . .1
обмин. . . . . . . 850 7. Редуктор механизма: подъема груза: тип. . . . . . . . . . . . . . . . . . . .Ц2У-315Н передаточное число. . . . . . . . . . . . . 50 передвижения тележки: тип. . . . . . . . . . . . . . . . . . . . . . ВК-350 передаточное число. . . . . . . . . . . . . 31
8. Тормоз механизма подъема груза: тип. . . . . . . . . . . . . . . . . . . . . ТКГ-200 тормозной момент
Нм. . . . . . . . . . . 250 передвижения тележки: тип. . . . . . . . . . . . . . . . . . . . . ТКГ-160 тормозной момент
Нм. . . . . . . . . . . .98 10. Канат . . . . . . . . . . . . . 14-Г-Н-1666 ГОСТ 2688-80 11.тележки
кг. . . . . . . . . . . . . . . . . .5600±10%
Схема навивки каната механизма подъема
* Размеры для справок
-1000-30-1-40-1-2У2 ГОСТ 5006-83
Редуктор Ц2У-315Н-50-11-М-У3
электро-гидравлический ТКГ-160
электро-гидравлический ТКГ-200
Электродвигатель MTF 011-6
Элекктродвигатель MTF 312-6
Колесная установка 320
неприводная ОСТ 24.090.09-75
Колесная установка 320 приводная
Канат 14 Г-Н-1666 ГОСТ2688-80
Болт М16-40.58 ГОСТ 7798-70
Болт М16-50.58 ГОСТ 7798-70
Болт М24-60.58 ГОСТ 7798-70
Болт М24-70.58 ГОСТ 7798-70
Болт М27-65.58 ГОСТ 7798-70
Болт М20-60.58 ГОСТ 7798-70
Гайка М12.5 ГОСТ 5915-70
Гайка М16.5 ГОСТ 5915-70
Гайка М27.5 ГОСТ 5915-70
Гайка М20.5 ГОСТ 5915-70
Шайба 12 65Г ГОСТ 6402-70
Шайба 16 65Г ГОСТ 6402-70
Шайба 20 65Г ГОСТ 6402-70
Шайба 24 65Г ГОСТ 6402-70
Шайба 27 65Г ГОСТ 6402-70
Установка верхних блоков
Болт М12-50.58 ГОСТ 7798-70
деталировка.dwg

Неуказанные предельные отклонения размеров:
Радиусы скруглений 3мм.
Неуказанные радиусы 2 мм max.
Уклоны формовочные 3°.
Неуказанные радиусы 2мм.
кроме места указанного особо.
;остальных ±t2 по ГОСТ
Неуказанные предельные отклонения
откланения размеров по ГОСТ 7505-89.
штамповки неуказанные предельные
При изготовлении крюка методом горячей
* Размеры для справок
Сталь 20Г ГОСТ 1050-88
Сталь 20Х ГОСТ 4543-71
Сталь 45 ГОСТ 1050-88
общий вид.dwg

Техническая характеристика 1. Грузоподъемность
т. . . . . . . . . . . . . . . . . . . . .16 2. Высота подъема груза
м. . . . . . . . . . . . . . . . .10 3. Режим работы. . . . . . . . . . . . . . . . . . . . . .Легкий 4. Продолжительность включения. . . . . . . . . ПВ=25% 5. Скорость
мс: подъема груза. . . . . . . . . . . . . . . . . . . 0
передвижения тележки. . . . . . . . . . . . . .0
передвижения крана. . . . . . . . . . . . . . .0
6. Электродвигатель механизма: подъема груза: тип. . . . . . . . . . . . . . . . .. МТF 312-6 мощность
кВт. . . . . . . . . . . . . . .17
обмин. . . . . ..950 передвижения тележки: тип. . . . . . . . . . . . . . . . . .МТF 011-6 мощность
кВт. . . . . . . . . . . . . . .1
обмин. . . . . . 850 передвижения крана: тип. . . . . . . . . . . . . . . . . .МТF 012-6 мощность
кВт. . . . . . . . . . . . . . .2
обмин. . . . . ..840 7. Редуктор механизма: подъема груза: тип. . . . . . . . . . . . . . . . . . Ц2У-315Н передаточное число. . . . . . . . . . . .50 передвижения тележки: тип. . . . . . . . . . . . . . . . . . . . ВК-350 передаточное число. . . . . . . . . . .31
передвижения крана: тип. . . . . . . . . . . . . . . . . . . .Ц2У-160 передаточное число. . . . . . . . . . . .22 8. Тормоз механизма подъема груза: тип. . . . . . . . . . . . . . . . . . . ТКГ-200 тормозной момент
Нм. . . . . . . . . 250 передвижения тележки: тип. . . . . . . . . . . . . . . . . . . .ТКГ-160 тормозной момент
Нм. . . . . . . . . . 98 передвижения крана: тип. . . . . . . . . . . . . . . . . . . .ТКГ-160 тормозной момент
Нм. . . . . . . . . . 98
Механизм передвижения крана
Кабина с электроаппаратурой