Изготовление вала


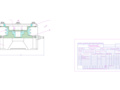
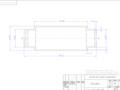
- Добавлен: 25.10.2022
- Размер: 963 KB
- Закачек: 0
- ВКонтакте
- РћРТвЂВВВВВВВВнокласснРСвЂВВВВВВВВРєРСвЂВВВВВВВВ
- Telegram
Описание
Состав проекта
![]() |
![]() ![]() ![]() |
![]() ![]() ![]() ![]() |
![]() |
![]() ![]() ![]() |
![]() ![]() ![]() |
![]() ![]() ![]() ![]() |
![]() |
![]() |
Дополнительная информация
курсовой 1.docx
ТИП ПРОИЗВОДСТВА КОЛИЧЕСТВО ДЕТАЛЕЙ В ПАРТИИ8
ВИД ЗАГОТОВКИ И ПРИПУСКИ НА ОБРАБОТКУ11
СТРУКТУРА ТЕХНОЛОГИЧЕСКОГО ПРОЦЕССА15
ВЫБОР ОБОРУДОВАНИЯ И ПРИСПОСОБЛЕНИЯ.17
ВЫБОР РЕЖУЩЕГО ИНСТРУМЕНТА21
РАСЧЁТ РЕЖИМА РЕЗАНИЯ25
1 Режимы резания при сверлении25
КОНСТРУИРОВАНИЕ ПРИСПОСОБЛЕНИЯ29
ОФОРМЛЕНИЕ ДОКУМЕНТАЦИИ.30
ТЕХНИКА БЕЗОПАСНОСТИ.31
Современное машиностроение представляет очень высокие требования к точности и состоянию поверхностей деталей машин которые можно обеспечить в основном только механической обработкой.
Обработка металлов резанием представляет собой совокупность действий направленных на изменение формы заготовки путем снятия припуска режущими инструментами на металлорежущих станках обеспечивая заданную точность и шероховатость обработанной поверхности.
В зависимости от формы деталей характера обрабатываемых поверхностей и требований предъявляемых к ним их обработку можно проводить различными способами: механическими - точением строганием фрезерованием протягиванием шлифованием и др.; электрическими - электроискровым электроимпульсным или анодно-механическим а также ультразвуковым электрохимическим лучевыми и другими способами обработки.
Процесс обработки металлов резанием играет ведущую роль в машиностроении так как точность форм и размеров и высокая частота поверхностей металлических деталей машин в большинстве случаев обеспечивается только такой обработкой.
Этот процесс успешно применяется во всех без исключения отраслей промышленности.
Обработка металлов резанием является весьма трудоемким и дорогостоящим процессом. Так например в среднем в машиностроении стоимость обработки заготовок резанием составляет от 50 до 60 стоимости готовых изделий.
Обработка металлов резанием как правило осуществляется на металлорежущих станках. Лишь отдельные виды обработки резанием относящиеся к слесарным работам выполняются вручную или с помощью механизированных инструментов.
В современных методах механической обработки металлов заметны следующие тенденции:
) обработка заготовок с малыми припусками что приводит к экономии металлов и увеличении доли отделочных операций;
) широкое применение методов упрочняющей обработки без снятия стружки путем накатывания роликами и шариками обдувки дробью дорнирования чеканки и т. п.;
) применение многоинструментальной обработки взамен одноинструментальной и многолезвийного режущего инструмента вместо однолезвийного;
) возрастания скоростей резания и подач;
) увеличение части работ выполняемых на автоматических и полуавтоматических станках роботизированных комплексов с применением систем программного управления;
) широкое проведение модернизации металлорежущего оборудования;
) использование быстродействующих и многоместных приспособлений для закрепления заготовок и механизмов при автоматизации универсальных металлорежущих станков;
) изготовление деталей из специальных и жаростойких сплавов обрабатываемость которых значительно хуже чем обычных металлов;
) участие технологов в разработке конструкции машин для обеспечения их высокой технологичности.
Более рационально получать сразу готовую деталь минуя стадию заготовки. Это достигается применением точных методов литья и обработки давлением порошковой металлургией. Эти процессы более прогрессивны и они будут все шире внедряться в технику.
Исходные данные по заданию
Наименование работы:
Разработать технологический процесс изготовления вала.
Исходные данные по заданию приведены в таблице 1.1.
Таблица 1.1 – Исходные данные по заданию
Производственная программа тыс.В год
Данная деталь изготавливается из стали 3кп ГОСТ 380-2005; химический состав механические и технологические свойства приведены в таблице 1.2-1.4.
Таблица 1.2 – Химический состав Ст3кп (ГОСТ 380-2005).
Содержание элементов %
Таблица 1.3 - Механические свойства Ст3кп (ГОСТ 535-2005).
sВ- Предел кратковременной прочности [МПа]
sт- Предел пропорциональности (предел текучести для остаточной деформации) [МПа]
- Относительное удлинение при разрыве [ % ]
%- Относительное сужение [ % ]
HB- Твердость по Бринеллю [МПа]
Таблица 1.4 - Технологические свойства материала Ст3кп (ГОСТ 535-2005).
Флокеночувствительность
Склонность к отпускной хрупкости
Для получения детали с твердостью 55 60 HRC необходимо произвести цементацию при Т=900 0С закалку при Т=880 0С с последующим низкотемпературным отпуском при Т=200 0С.
Тип производства количество деталей в партии
В зависимости от размера производственной программы сложности и трудоемкости изготовляемых деталей (изделий) различают три типа (вида) производства: единичное серийное массовое. Условно можно отнести к тому или иному типу производства обработку деталей заданного типоразмера на основании таблицы 2.1.
Таблица 2.1 – Типы производства
Количество обрабатываемых деталей в год штук
средних от 5 до 20 кг
1 Определим массу детали по формуле (1):
где m – масса детали кг;
– плотность стали кг м3;
V – объем детали м3;
Для стали принимаем =785 103 кг м3.
Рассчитываем объем вала по формуле (2): (2)
V1=314·252·278=545575 мм3;
V2=314·23652·22=38638 мм3;
V3=314·352·155=5962075 мм3;
V4=314·252·25=490625 мм3;
V5=314·452·50=31793 мм3;
V6=314·62·5+12·3·5=4752 мм3;
Vобщ = V1 - V2 + V3 + V4 –V5 -V6 = 545575 – 38638 +5962075+490625 – 31793 – 4752 = 6923092 мм3.
Определяем массу детали:
Мд = 7850·6923092·10-9 = 54 кг.
2 Определяем массу поковки:
V13=314·282·57=14032032 мм3;
V2=314·382·1615=73226684 мм3;
Vобщ = V13 + V2 = 14032032 + 73226684 = 87258716 мм3;
Mп = 7850·87258716·10-9 = 685 кг.
Определяем коэффициент использования материала:
По таблице 2.1 определили тип производства. Так как производственная программа составляет 5600 деталей то тип производства – массовое.
При массовом производстве на оборудовании непрерывно обрабатываются или изготавливаются детали заданного типоразмера в течении длительного времени.
Количество деталей в партии можно определить по формуле (3):
где: N – годовая программа выпуска деталей;
t – число дней на которое необходимо иметь запас готовых деталей для бесперебойной работы цеха;
Ф – число рабочих дней в году.
Принимаем N=5600 t=2 Ф=255
Вид заготовки и припуски на обработку
Заготовкой называется предмет производства из которого изменением формы размеров качества поверхностей и свойств материала изготовляют требуемую деталь. Выбор вида заготовки зависит от материала формы и размера ее назначения условий работы и испытываемой нагрузки от типа производства.
Для изготовления деталей могут применяться следующие виды заготовок:
отливки поковки прокат холодно- и горячекатаный.
В нашем случае заготовка — поковка.
Поковка - это металлическое изделие или промежуточная заготовка получаемая ковкой или горячей объемной штамповкой в кузнечно-штамповом производстве имеющее минимальные припуски на металлообработку.
Такая поковка отличается высокой прочностью и качеством изготовления а также позволяет снизить время металлообработки.
Поковка многофункциональна и может использоваться в промышленности для различных целей.
Поковка создается в процессе обработки металла особым образом: под давлением и при высокой температуре что позволяет металлу уплотнятся и сращиваться. В таком виде металл может принимать любые необходимые размеры и формы.
Паковка обладает пластичностью хорошей прочностью и высокой надежностью в связи с этим их часто применяют в металлургической атомной и автомобильной промышленности в которых немаловажным становится сопротивление изделий напряжению ударной нагрузке и усталости. Поэтому дальнейшее применение поковок это использование их в производстве различных деталей и заготовок (коленвалы редуктора шпиндели т.д.)
В зависимости от применяемой стали в качестве сырья и от назначения поковки бывают видов:
Поковки углеродистые. Изготовление осуществляется способом горячей штамповки и ковки из углеродистых специальных сталей характеризующихся особой прочностью.
Поковки прессовые. Изготавливаются с помощью метода штамповки. Требуемый объем металла располагают в специальной форме и с помощью пресса получают нужную заготовку. Эти поковки применяют в машиностроение и др. отраслях.
Молотовые поковки. Аналогично прессовым поковкам используются в машиностроении. Изготовление осуществляется путем воздействия кузнечно-прессового молота что придает заготовке пластичность. Этот способ позволяет изготавливать заготовки высокого качества но по скорости производительности значительно уступает штамповке.
Нержавеющие поковки. Изготавливают из нержавеющей стали. Применяются в качестве заготовок роторов в электрической промышленности газовых турбин баллеров в судостроении валов и пр.
Легированные поковки. Производятся из специальных легированных сталей из-за чего в зависимости от назначения изменяются физические механические химические и электрические свойства изделий.
Инструментальные поковки. Требуются для изготовления инструментов. Заготовки изготавливаются с особой прочностью и точностью. Используются специальные легированные и углеродистые стали.
Величина припуска на обработку т.е. толщина снимаемого слоя металла зависит от вида заготовки и способа ее изготовления от размеров и формы детали и от требуемых точности и шероховатости обработанных поверхностей.
Для снижения себестоимости обработки и расхода металла припуски должны быть такими чтобы их можно было снять за минимальное число проходов. В тоже время для нормальной работы режущего инструмента припуск должен превышать толщину твердой литейной корки для литых заготовок или слоя окалины для поковок.
Общий припуск на сторону должен включать кроме толщины поверхностного дефектного слоя сумму межоперационных припусков т. е. слоев снимаемых на каждой операции с учетом погрешности установки отклонений от правильной формы допусков на размеры заготовки.
Определяем припуски на механическую обработку:
1 Исходные данные по детали.
Материал – ст3кп C – 014 - 022% Si - до 005% Mn – 03-06% P - 004% S – 005% Cr - 03% Ni – 03% Cu – 03%.
Масса детали – 54 кг.
2 Исходные данные для расчета.
Масса поковки Мп = 685 кг.
Группа стали – М1 (таблица 3.2 [5]).
Класс точности – Т5 (таблица 3.4 [5]).
Степень сложности – С1 (таблица 3.3 [5]).
Размеры описывающей поковку фигуры (цилиндр) мм: диаметр 735 (70·105); длинна 231 (220·105) где 105 – коэффициент.
Масса описывающей фигуры (расчетная) 76 кг;
Конфигурация поверхности разъема штампа – плоская.
Исходный индекс – 14 (таблица 3.5 [5]).
3 Определяем основные припуски на размеры (таблица 4.1 [5]) мм:
– диаметр 50 и шероховатость поверхности 125;
– диаметр 70 и шероховатость поверхности 125;
– толщина 210 и шероховатость поверхности 10;
– толщина 155 и шероховатость поверхности 25.
Дополнительные припуски учитывающие:
смещение по поверхности разъема – 04 мм (таблица 4.2 [5]);
отклонение от плоскостности – 08 мм (таблица 4.3 [5]).
Штамповочные уклоны на наружных поверхностях 50 (таблица 6.1 [5]).
4 Определяем размеры поковки мм:
диаметр 50 + (22 + 08)·2 = 56 мм;
диаметр 70 + (22 + 08)·2 = 76 мм;
толщина 210 + (3 + 04 + 08)·2 = 2184 принимается 2185 мм;
толщина 155 + (23 + 08)·2 = 1612 принимается 1615 мм.
Радиус закругления наружных углов – 30 мм (таблица 4.5 [5]).
Допускаемые отклонения размеров мм (таблица 6.1 [5]):
Неуказанные допуски радиусов закругления – 20 мм (таблица 6.8 [5]).
Допускаемая величина остаточного облоя – 12 мм (таблица 6.3 [5]).
Допускаемое отклонение от плоскостности – 12 мм (таблица 6.6 [5]).
Допускаемое смещение по поверхности разъема штампа – 10 мм (таблица 6.2 [5]).
Допускаемая величина высоты заусенца – 40 мм (таблица 6.4 [5]).
Структура технологического процесса
Технологической операцией называется законченная часть технологического процесса выполняемая на одном рабочем месте в частности при обработке резанием – на одном станке. Если после обработки части поверхностей заготовка передается на другое рабочие место а затем возвращается на тот же станок то дальнейшая обработка на нем составит следующую операцию.
Установом называется часть операции выполняемая при неизменном закреплении обрабатываемой заготовки.
Позицией называется фиксированное положение занимаемое неизменно закрепленной обрабатываемой заготовки совместно с приспособлением относительно инструмента или неподвижной части операции.
Технологическим переходом называется законченная часть операции выполняемая одним и тем же инструментом при постоянных поверхности образуемой обработкой технологических режимах и установке.
Структура технологического процесса представлена на рисунке 4.1
Рисунок 4.1 – Структура технологического процесса
Выбор оборудования и приспособления
При выборе типа станка и степени его автоматизации необходимо учитывать следующие факторы:
Габаритные размеры и форму детали;
Форму обработанных поверхностей их расположение;
Технические требования точности размеров формы и к шероховатости обработанных поверхностей;
Размер производственной программы характеризующий тип производства данной детали.
В единичном мелкосерийном производстве используются универсальные станки в серийном наряду с универсальными станками широко применяются полуавтоматы и автоматы в крупносерийном и массовом производстве - специальные станки автоматы агрегатные станки и автоматические линии.
Всё более широкое применение в настоящее время находят в серийном производстве автоматические станки с числовым программным управлением позволяющие производить быструю переналадку с обработки одних деталей на другие путём замены программы зафиксированной например на бумажной перфоленте или на магнитной ленте.
Для обработки данной детали выбираем:
) Токарно-винторезный станок 1А616;
) Вертикально-сверлильный станок 2Н118;
) Вертикально-фрезерный консольный станок 6Р10;
) Круглошлифовальный станок 3М150.
Для токарной операции выбираем в качестве приспособления трехкулачковый патрон.
Для сверлильной операции выбираем в качестве приспособления тиски.
Для фрезеровальной операции выбираем в качестве приспособления призму со струбциной.
Для шлифовальной операции выбираем в качестве приспособления неподвижные и вращающиеся центра.
Технические характеристики станков приведены в таблицах
Таблица 5.1 Технические параметры токарно-винторезного станка 1А616
Наибольший диаметр обрабатываемой детали мм
Расстояние между центрами мм
Число ступеней частоты вращения шпинделя
Частота вращения шпинделя обмин
Число ступеней подач суппорта
Подачи суппорта ммоб:
Мощность главного электродвигателя кВт
Наибольшая сила подачи механизмов подачи кгс
Таблица 5.2 Технические параметры вертикально-сверлильного станка 2Н118
Наибольший диаметр сверления мм
Вертикальное перемещение сверлильной головки мм
Число ступеней подач
Подача шпинделя ммоб
Наибольший крутящий момент на шпинделе кгс*м
Наибольшее усилие подачи кгс
Мощность электродвигателя кВт
Таблица 5.3 Технические параметры вертикально-фрезерного консольного станка 6Р10
Размеры рабочей поверхности стола (ширина×длина)
Наибольшее перемещение стола мм
Наибольший угол поворота шпиндельной головки о
Число скоростей шпинделя
продольная и поперечная
Мощность электродвигателя привода главного движения кВт
Таблица 5.4 Технические параметры круглошлифовального станка 3М150
Наибольшие размеры устанавливаемой заготовки:
Высота центров над столом
Наибольшее продольное перемещение стола мм
Угол поворота стола о
против часовой стрелки
Скорость автоматического перемещения стола ммин
Частота вращения шпинделя заготовки с бесступенчатым регулированием обмин
Наибольшие размеры шлифовального круга мм
Перемещение шлифовальной бабки наибольшее мм
Частота вращения шпинделя шлифовального круга при наружном шлифовании обмин
Скорость врезной подачи шлифовальной бабки мммин
Для расчетов режимов резания при сверлении рассчитываем значение подач и частот вращения станка по следующим формулам:
где S1 и Sz – минимальное и максимальное значение подачи;
n1 и nz – минимальное и максимальное значение частоты вращения;
z – количество ступеней.
S2 = φ2-1·S1 = 141·01 = 0141;
S3 = φ3-1·S1 = 1412·01 = 0198;
S4 = φ4-1·S1 = 1413·01 = 028;
S5 = φ5-1·S1 = 1414·01 = 039;
S6 = φ6-1·S1 = 1415·01 = 056.
n2 = n1·φn = 180·141 = 253;
n3 = n1·φn2 = 180·1412 = 357;
n4 = n1·φn3 = 180·1413 = 504;
n5 = n1·φn4 = 180·1414 = 711;
n6 = n1·φn5 = 180·1415 = 1003;
n7 = n1·φn6 = 180·1416 = 1414;
n8 = n1·φn7 = 180·1417 = 1994;
n9 = n1·φn8 = 180·1418 = 2812.
При выборе режущего инструмента необходимо исходить из способа обработки и типа станка формы и расположения обрабатываемых поверхностей материала заготовки и его механических свойств.
Инструмент должен обеспечить получение заданной точности формы и размеров требуемой шероховатости обработанных поверхностей высокую производительность и стойкость должен быть достаточно прочным виброустойчивым и экономичным.
Для токарной операции выбираем:
а) Резец проходной упорный Т15К6 ГОСТ 18877 –73 изображенный на рисунке 6.1.
Рисунок 6.1 – Проходной упорный резец
б) Проходной отогнутый резец оснащенный пластинкой из твердого сплава Т15К6 ГОСТ 18868-73 изображенный на рисунке 6.2.
Рисунок 6.2 – проходной отогнутый резец
г) Отрезной резец из быстрорежущей стали по ГОСТ(18874-73) изображенный на рисунке 6.3.
Рисунок 6.3 – отрезной резец
Для сверления отверстия диаметром 9 мм выбираю стандартное спиральное сверло оснащенное пластинками из твердого сплава коническим хвостовиком (ГОСТ 2092-77) изображенное на рисунке 6.4.
Рисунок 6.4 – Спиральное сверло
Для проточки шпоночной канавки выбираем шпоночную фрезу ГОСТ 5841-83 изображенный на рисунке 6.5.
Рисунок 6.5 – Шпоночная фреза.
Для шлифования выбираю шлифовальный круг ГОСТ 2424-83 изображенный на рисунке 6.6.
Рисунок 6.6 – Шлифовальный круг
1 Выбор материала режущей части
Материал режущей части инструмента имеет важнейшее значение в достижении высокой производительности обработки. При выборе марки твердого сплава необходимо помнить что чем больше содержание в нем карбида титана и чем меньше кобальта тем больше его износо- и термостойкость но тем меньше его прочность на изгиб и вязкость т.е. сплав более хрупкий. Деталь рекомендуется обрабатывать инструментами оснащенными твердым сплавом марки Т15К6. Для сверл рекомендуется марка инструментального материала Р12.
Выбор периода стойкости режущего инструмента
Стойкостью называется период работы режущего инструмента до его затупления. Так как период стойкости инструмента оказывает наибольшее влияние на скорость резания правильный выбор этого фактора имеет большое значение.
Период стойкости колеблется в больших приделах. Так период стойкости мин принимают равным: для резцов с пластинками из твердого сплава – 90-120; для сверл из быстрорежущей стали диаметром до 20 мм – 25 – 40; стойкость шлифовального круга – 10 –20 мин. [4]. На величину стойкости инструмента существенное влияние оказывает смазочно-охлаждающая жидкость (СОЖ). Как правило применения СОЖ облегчает стружкообразование и снижает температуру в зоне резания что существенно повышает стойкость режущего инструмента.
Расчет режимов резания
Производительность и себестоимость обработки изделий на металлорежущих станках качество обработанной поверхности зависят прежде всего от принятых режимов резания. Поэтому важен выбор их оптимальных значений при проектировании технологического процесса механической обработки.
Оптимальные т.е. наивыгоднейшие режимы резания выбираются из условий наиболее полного использования режущей способности инструмента кинематических и силовых способностей станка. При этом должны обеспечиваться высокая производительность требуемые точности и шероховатость обработанной поверхности и минимальная себестоимость.
1 Режимы резания при сверлении
Глубина резания мм принимается равной половине диаметра сверла:
где D – диаметр поверхности после обработки мм;
Подача ммоб может быть принята по таблицам справочной литературы или подсчитана:
где Сs – коэффициент зависящий от механических свойств
обрабатываемого материала;
x – показатель степени равный 06 для сверления инструментом из
быстрорежущей стали;
Ks – поправочный коэффициент вводимый при длине сверления более трёх диаметров сверла.
По паспортным данным станка принимается фактическая подача Sф (ближайшая меньшая).
Расчётная скорость резания при точении р ммин вычисляется по формуле:
где T – расчётная стойкость сверла мин
K – поправочный коэффициент равен произведению ряда
где Kм – поправочный коэффициент зависящий от обрабатываемого
Kп – коэффициент зависящий от состояния поверхности;
Расчётная частота вращения:
Полученное значение частоты вращения шпинделя сравните с имеющимся на металлорежущем станке и примите ближайшее меньшее.
Подсчитаем фактическую скорость резания:
Крутящий момент потребный на резание и осевую силу подсчитаем по формулам:
где CM и Cp – коэффициенты крутящего момента и осевой силы;
D – диаметр сверла мм;
ZM и Zp – показатели степени влияния диметра сверла на величину
момента и осевой силы;
YM и Yp – показатели степени влияния подачи на величину M и
KM и Kp – поправочные коэффициенты на изменённые условия.
Эффективная мощность резания кВт
Коэффициент использования станка
Подсчитаем фактическую стойкость инструмента Tф мин
где T и р – расчетные значения стойкости инструмента и скорости резания.
Основное технологическое (машинное) время непосредственно затраченное на процесс сверления мин
где L – расчетная длина обработки;
nф – частота вращения шпинделя;
Расчетную длину обработки находим по формуле
За длину обработки l мм принимается путь пройденный вершиной инструмента в процессе резания и измеренный в направлении подачи. Величина l1 мм при точении вычисляется из соотношения
где φ – главный угол резца в плане.
Величина перебега l2 принимается равной 5 мм.
Конструирование приспособления
В задачу курсовой работы входит разработка конструкции одного приспособления входящего в технологическую оснастку проектируемого процесса механической обработки.
Станочные приспособления предназначены для установки и закрепления обрабатываемой детали и разделяются: по степени специализации – на универсальные переналаживаемые сборные из нормализованных деталей и узлов; по степени механизации – на ручные механизированные автоматические; по назначению – на приспособления для токарных сверлильных фрезерных шлифовальных и др. станков; по конструкции – на одно- и многоместные одно- и многопозиционные.
Выбор вида приспособления зависит от типа производства программы выпуска деталей от формы размеров обрабатываемой детали и от требуемой точности обработки.
При проектировании станочного приспособления решаются следующие основные задачи:
) упразднение трудоемкой операции – разметки деталей перед обработкой;
) сокращение вспомогательного времени на установку закрепление и переустановку детали относительно инструмента;
) повышения точности обработки;
) снижение машинного и вспомогательного времени за счет одновременной обработки нескольких деталей или совмещенной обработки несколькими инструментами;
) облегчение труда рабочего и снижения трудоемкости обработки;
) повышение технологических возможностей и специализация станка
В результате применения приспособления должны значительно возрасти производительность и снизится себестоимость обработки.
В качестве приспособления для сверления выбираем станочные тиски ГОСТ 1789-88.
Оформление технической документации
В качестве основного документа технической документации представлена маршрутная карта где указаны все операции и переходы а также оборудование приспособление режущий и измерительный инструмент количество рабочих. Указан профиль и размеры.
Вторым технологическим документом является операционная карта. В ней указаны переходы на одну операцию указан её номер и материал заготовки её масса и твердость детали. Для всех переходов указан режущий и измерительный инструмент. Кроме того подсчитаны расчетные размеры глубина резания число проходов обороты шпинделя и скорость режимов обработки. Подсчитано машинное и вспомогательное время.
Техника безопасности.
Техника безопасности охватывает комплекс технических устройств и правил обеспечивающих нормальную жизнедеятельность человека в процессе труда и исключающих производственный травматизм. При работе на металлорежущих станках рабочий должен быть предохранен от действия электрического тока от ударов движущимися частями станка а также обрабатываемыми деталями или режущим инструментом вследствие слабого их закрепления или поломки от отделяющейся стружки от воздействия пыли и СОЖ.
1 Общие правила техники безопасности при работе на металлорежущих станках:
К самостоятельной работе допускаются лица прошедшие медицинское освидетельствование прошедшие вводный инструктаж первичный инструктаж на рабочем месте имеющие удостоверение по охране труда.
Выполнять только работу входящую в круг обязанностей.
Работать только в исправной аккуратно заправленной спецодежде и спецобуви предусмотренными инструкциями по охране труда.
Пользоваться только исправными приспособлениями оснасткой инструментом применять их по назначению.
Не оставлять без присмотра включенные (работающие) машины и механизмы оборудование. При уходе даже на короткое время отключать его от электросети вводным выключателем.
Не стирать спецодежду в керосине бензине растворителях эмульсиях и не мыть в них руки.
Не прикасаться к токоведущим частям электрооборудования машин и механизмов обрабатываемым заготовкам и деталям при их вращении.
Не обдувать сжатым воздухом детали не пользоваться сжатым воздухом для удаления стружки.
Пользоваться при работе деревянным настилом и содержать его в исправном состоянии и чистоте.
Основные опасные и вредные производственные факторы:
возможность поражения электротоком;
возможность получения ожогов и механических повреждений стружкой;
повышенный уровень шума;
возможность падения устанавливаемых и обрабатываемых деталей заготовок.
При работе на станках применение перчаток или рукавиц не допустимо.
При обработке детали в центрах запрещается применять центра с изношенными конусами.
Запрещается работать на станке без защитных очков.
Запрещается прикасаться руками к вращающимся частям станка а также к обрабатываемой детали.
Требования безопасности по окончании работ.
Выключить станок обесточить электрооборудование.
Привести в порядок рабочее место.
Протереть и смазать трущиеся части станка.
Убрать разлитые масло и эмульсию посыпав загрязненные места песком.
Уборку стружки пыли производить щеткой-сметкой.
Использованные во время уборки и при работе тряпки ветошь вынести за пределы цеха в отведенные для этой цели места.
При сдаче смены сообщить мастеру и сменщику о замеченных недостатках и принятых мерах по их устранению.
Вымыть лицо и руки теплой водой с мылом или принять душ.
Казаченко В.П. Савенко А.Н. Терешко Ю.Д. Материаловедение и технология материалов III. Обработка металлов резанием. Пособие по курсовому проектированию – Гомель: БелГУТ 1997 – 47 с.
Дольский А.Н. и др. Технология конструкционных материалов. – М.: Машиностроение 1985 – 448 с.
Справочник технолого-машиностроителя. В 2 т. Т I под редакцией Косиловой А.Г. и Мещераковой Р.М. – М.: 1972 – 649 с. Т II под редакцией Малова А.Н. – М.: 1972 – 568 с.
Горбунов В.И. Обработка металлов резанием. Металлорежущие инструменты и станки. – М.: Машиностроение.
Железняков А.А. Конструирование поковок штампуемых на молотах прессах и горизонтально – ковочных машинах. Учебно – методическое пособие по курсовому проектированию. – Гомель: БелГУТ 2006.
Тараканов И.Л. Савенко А.Н. Методички расчета рациональных режимов резания. – Гомель: БелИИЖТ 1980.
Федин А.П. Материаловедение и технология материалов. – Гомель: БелИИЖТ 1982 – 83 с.
Терешко Ю.Д. Петров С.В. Егоров А.И. Материаловедение и технология материалов. Учебное пособие. 2е изд. доп. – Гомель: БелГУТ 2004. – 131 с.
поковка.dwg

Радиус закругления наружных углов - 3
мм 2. Неуказанные допуски радиусов закруглений - 2
мм 3. Штамповочные уклоны на наружных поверхностях 5
Маршрутная карта заполненная.dwg
Расточить поверхность
Расточить отверстие
Рассверлить отверстие 4 на проход
Вертикально-сверлильный
Кондуктор ГОСТ 16891-71
Переустановить заготовку
Сверло с цилиндрическим
хвостиком ГОСТ 4010-64
Токарно-винторезный
Шлифовать отверстие 7
Шлифовать поверхность 9
Наименование и содержание
Объем производствен.
Шлифовать поверхность 15
Вертикально-фрезерный
консольный станок 6Р10
Призма со струбциной
Сверло с коническим
хвостиком ГОСТ 2092-77
Фрезеровать поверхность 14
Сверлить отверстие 13 ø9
Точить поверхность 2
Точить поверхность 3
Точить поверхность 4
Точить поверхность 8
Точить поверхность 9
Точить поверхность 10
Шлифовать поверхность 16
Шлифовать поверхность 17
Шлифовать поверхность 18
Шлифовать поверхность 19
операционная карта.dwg

Наименование операции
Наименование и марка материала
Кол. одноврем. обраб.деталей
Оборудование ( наимеование
Приспособление ( код и наимен. )
Инструмент ( код и наименование )
Вертикально - сверлильный станок 2Н118
Установить заготовку
Сверлить отверстие диаметром 9 мм
Рекомендуемые чертежи
- 31.01.2023
- 24.01.2023