Экскаватор Caterpillar 330DL




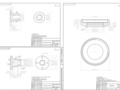
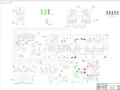
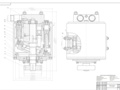
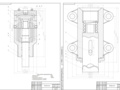
- Добавлен: 25.10.2022
- Размер: 3 MB
- Закачек: 2
Описание
Состав проекта
![]() |
![]() |
![]() |
![]() ![]() ![]() ![]() |
![]() |
![]() ![]() ![]() ![]() |
![]() |
![]() ![]() ![]() ![]() |
![]() |
![]() ![]() ![]() ![]() |
![]() |
![]() ![]() ![]() ![]() |
![]() |
![]() ![]() ![]() ![]() |
![]() ![]() ![]() ![]() |
![]() ![]() ![]() ![]() |
![]() ![]() ![]() ![]() |
![]() ![]() ![]() ![]() |
![]() ![]() ![]() ![]() |
![]() ![]() ![]() ![]() |
![]() ![]() ![]() ![]() |
![]() |
![]() ![]() ![]() ![]() |
![]() |
![]() ![]() ![]() ![]() |
![]() |
![]() ![]() ![]() ![]() |
![]() |
![]() ![]() ![]() ![]() |
![]() |
![]() ![]() ![]() |
Дополнительная информация
ТЕХмаш.dwg

НВ 269 302 2. Радиусы скругления 1
3. Неуказанные предельные отклонения размеров:отверстий + t
остальных+ t2 среднего класса точности
Первичное применение
Сталь 30 ГОСТ 1050-88
ЮРГТУ (НПИ) Кафедра СДКМ ФЭМТМ V-8
Преспособление для зубофрезерования
0603.Д11.105.03.17.00
Ковш.dwg

Первичное применение
Вид А (силовая плита)
Технические требования : 1. Внутренние не обработанные и наружние поверхности окрасить
атмосферостойкой краской ХВ 124 желтого цвета. 2. В собранном рабочем оборудовании проверить боковые зазоры
которые дожны соответствовать степени точности по ГОСТ3675-81. 3. Неравномрный шум и чрезмерное нагревание при работе рабочего оборудования не допускается. 4. Течь смазки по плоскости разьема и по контору крышек не допускается.
Деталировка.dwg

235 262 НВ 2. Формофочные уклоны 2 3. Н14;+ T142 4. Размер обеспечен инструментом 5. Неуказанные радиусы скругления R=2мм max
Первичное применение
0603.Д11.105.01.04.03.07.CБ
235 262 НВ кроме мест указанных особо. 2. Н14;+ T142 3. Размер обеспечен инструментом 4. Радиусы скругления R=1
мм max 5. Формофочные уклоны 1
0603.Д11.105.03.18.00.CБ
0603.Д11.105.01.04.04.02.CБ
235 262 НВ 2. Н14;+ T142 3. Размер обеспечен инструментом 4. Радиусы скругления R=1
ЮРГТУ (НПИ) Кафедра СДКМ ФЭМТМ V-8
Вибратор и виброзуб.dwg

ЮРГТУ (НПИ) Кафедра СДКМ ФЭМТМ V-8
Технические характеристики 1.Диаметр боика 50мм 2.Ход поршня 150мм 3.Номинальное давление 320МПа 4. Обьемныек потери Q= 3 cм3мин. 5. Потери давления Рпк = 0
Гидросхема.dwg

Первичное применение
Предохранительный механизм Рукояти
Клапанный блок 270-5947
Мотор гидравлический 242-6776
Распределитель изменения потока 242-6880
Блок дистанционного управления механизмом хода правый 167-3466
Блок дистанционного управления механизмом хода левый 167-3466
Клапанный блок 190-7745
Мотор GPS Sning 200-3373
Клапаный блок GPS Sning 158-9085
Пилот клапанна рукояти 270-5951
Пилот клапанна ковша 270-5952
Челнок клапана 184-0462
Переключатель давления 167-3466
Фильтр случая утечки 126-2075
Клапан давления 232-4102
Насос гидравлический 259-0815
Клапан челнока 259-7732
Датчик контроля правого насоса 221-8859
Главный силовой насос 283-6116
Предохранительный механизм стрелы
Главный Клапанный блок управления 285-1536
Правый ходовой механизм2204-2819
Левый ходовой мотор GP271-6376
Левый ходовой механизм2204-2819
Механизм привода вентилятора 234-4624
Правый ходовой мотор GP271-6376
Пилот клапана коллектора 215-5037
ЮРГТУ (НПИ) Кафедра СДКМ ФЭМТМ V-8
Спецификация Виброзуб.dwg

ЮРГТУ (НПИ) Кафедра СДКМ ФЭМТМ V-8
0603.Д11.105.01.04.03.05
0603.Д11.105.01.04.03 СБ
Кольцо уплотнительное
спецификация спецификация преспособлениеклист1.dwg

0603.Д11.105.05.00.00 CБ
Преспособление для зубофрезерование
Спецификация Ковш.dwg

0603.Д11.105.01.04.03.00
0603.Д11.105.01.04.00 СБ
0603.Д11.105.01.04.04.00
Спецификация гидромотор лист 2.dwg

Спецификация вибратор.dwg

ЮРГТУ (НПИ) Кафедра СДКМ ФЭМТМ V-8
0100.Д11.105.01.04.04 СБ
0603.Д11.105.01.04.04.02
спецификация гидромотор.dwg

Диск распределительный
0603.Д11.105.04.00.00 СБ
Кольцо дистанционное
Гидронасос регулируемый
Кольцо уплотнительное
Спецификация Общий вид.dwg

Поворотная платформа
0603.Д11.105.01.00.00 ВО
0603.Д11.105.01.04.00 CБ
Ved1.dwg

Пояснительная записка
Гидросхема экскаватора
Графические документы
Экскаватор САТ330 DL
0603.Д11.105.02.00.00 СХ
0603.Д11.105.01.04.04 СБ
0603.Д11.105.03.00.00 СБ
0603.Д11.105.01.04.04 02
0603.Д11.105.01.00.00.ВО
0603.Д11.105.01.04.03.07
0603.Д10.125.08.00.00 СБ
0603.Д11.105.03.05.00
0603.Д11.105.03.06.00
0603.Д11.105.03.13.00.
0603.Д11.105.06.00.00.ОЭ
0603.Д11.105.03.17.00
0603.Д11.105.04.00.00
0603.Д11.105.05.00.00.CБ
0603.Д11.105 00.00.00. ПЗ
0603.Д11.105.01.04.03 СБ
Общий вид САТ330 DL.dwg

макс.кмч; 9 Наибольшая высота выгрузки; 5200 Двигатель дизельный четырехтактный
шестицелиндровыцй с водяным охлаждением Марка двигателя САТ 420СG52 Эксплутационная мощность кВт; 380 Частота вращения коленчатого вала при эксплутационной мощности об.мин; 2200 Номинальное давление в гидросистеме мПа; 32 Система пуска Электростартер
Экскаватор CAT 330 DL
ЮРГТУ (НПИ) Кафедра СДКМ ФЭМТМ V-8
Первичное применение
0603.Д11.105.01.00.00.ВО
Гидронасос.dwg

ЮРГТУ (НПИ) Кафедра СДКМ ФЭМТМ V-8
Технические характеристики Рабочий объем qн= 54
см3об; Номинальная подача Qн.ном= 1
1 10-3 м3с; Номинальное давление Pн.ном = 20 МПа; Номинальная частота вращения Nн.ном.= 25 обс (1500 обмин); Объемный КПД о.н.= 0
; Механический КПД мех.н.= 0
тех маш 1.dwg

Операция-05 Установка А
Токарно- револьверный 1П365
Наименование оборудования
Нормальный исходный контур
ЮРГТУ (НПИ) Кафедра СДКМ ФЭМТМ V-8
Деталироовка 1.dwg

262 302 НВ 2. Н14;+ T142 3. Размер обеспечен инструментом 4. Радиусы скругления R=1
мм max 5. Формофочные уклоны 1
235 262 НВ кроме мест указанных особо. 2. Н14;+ T142 3. Размер обеспечен инструментом 4. Радиусы скругления R=1
Первичное применение
Сталь 30 ГОСТ 1050-88
Распределительный диск
ЮРГТУ (НПИ) Кафедра СДКМ ФЭМТМ V-8
пояснительная записка.docx
ГОСУДАРСТВЕННОЕ ОБРАЗОВАТЕЛЬНОЕ УЧРЕЖДЕНИЕ ВЫСШЕГО
ПРОФЕССИОНАЛЬНОГО ОБРАЗОВАНИЯ
ЮЖНО-РОССИЙСКИЙ ГОСУДАРСТВЕННЫЙ
ТЕХНИЧЕСКИЙ УНИВЕРСИТЕТ
СПЕЦИАЛЬНОСТЬ 190603
Заведующий кафедрой
д.т.н. профессор Исаков В.С.
ПОЯСНИТЕЛЬНАЯ ЗАПИСКА
к дипломному проекту
Новочеркасск 2011 г.
СПЕЦИАЛЬНОСТЬ 19020565
(Фамилия имя отчество полностью )
Тема утверждена приказом по университету № 412ЛС от «25» февраля 2010 г.
Консультанты дипломного проекта
Наименование раздела должность ученая степень Ф.И.О
Общий раздел доцент к.т.н.
Специальный раздел доцент к.т.н.
Технологический раздел доцент к.т.н.
Экономический раздел доцент к.э.н.
Безопасность жизнедеятельности доцент к.т.н.
Исходные данные к проекту: Емкость ковша (по SAE) 165 м3 Двигатель: Модель CAT-540CT Мощность двигателя 540 л.с. Частота вращения вала двигателя 2200 обмин.. Давление в гидросистеме 32 MПа.. Напряжение в электросети 12 В. Радиус копания 106 м. Радиус копания на уровне стоянки 945 м. Глубина копания 78 м. Высота выгрузки 7 м. Угол поворота ковша 177(град.). Габаритные размеры: Длина 9400 мм. Ширина 2500 мм. Высота 3300 мм. 32 т. Момент на валу гидромотора: Мм ном = 369 Н м; Частота вращения вала гидромотора: -nмном = 1300 обмин. = 216 обс.; Время работы - = 5 сек. Время простоя = 4 сек. Рабочая жидкость – ВМГЗ; Температура рабочей жидкости t=40 0С
Содержание расчетно-пояснительной записки (перечень вопросов подлежащих разработке): Общие сведения о гидравлических одноковшовых экскаваторах. Назначение и классификация. Рабочее оборудование. Рабочий процесс. Анализ состояния вопроса разработки прочных и мерзлых грунтов одноковшовыми экскаваторам. Расчета гидропривода питания механизма гидроударников. Расчёт себестоимости и цены модернизации рабочего. Анализ опасностей которые могут возникнуть при эксплуатации и ремонте экскаватор
Перечень графического материала:
Общий вид экскаватора CAT330 DL. 1 лист
Гидросхема экскаватора CAT330 0DL. 1 лист
Вибратор и виброзуб. 1 лист
Деталировка. 2 листа
Операционные эскизы. 1 лист
В выпускной работе приведены общие сведения классификации и обзор существующих моделей одноковшовых экскаваторов анализ состояния вопроса разработки прочных и мерзлых грунтов одноковшовыми экскаваторами описана конструкция экскаватора САТ 330 DL. На основе анализа приведенных материалов предложена смешанное рабочее оборудование с ковшом активного действия который включает в себя ковш с пятью гидроударными блоками. Выполнены необходимые расчеты доказывающие работоспособность и эффективность предлагаемой конструкции.
В специальной части представлены расчеты гидропривода питания механизма гидроударников и элементов привода с отражением в графической части проекта выбраны управляющие устройства определены статистические характеристики гидропривода с машинным регулированием.
Разработка техпроцесса изготовления детали шестерни (сателлита) отражает вопросы выбора заготовки по двум вариантам определены тип производства припуски и режимы резания а также расчёт контрольного инструмента и приспособления (делительной головки).
В проекте содержатся расчёты технико-экономическая оценки качества спроектированного изделия полной себестоимости и отпускной цены модернизации рабочего оборудования экскаватора СAT-330DL
с учётом всех затрат на материалы полуфабрикаты и готовые изделия заработную плату всех категорий работающих составлен сетевой график разработки и изготовления системы.
Раздел обеспечения безопасной жизнедеятельности содержит необходимые мероприятия и расчёты обеспечивающие безопасную и безвредную работу персонала.
Ведомость дипломного проекта 8
Общие сведения о гидравлических одноковшовых экскаваторах 12
1 Назначение и классификация 12
2 Рабочее оборудование 15
3 Рабочий процесс 18
4 Анализ состояния вопроса разработки прочных и мерзлых
грунтов одноковшовыми экскаваторами 20
4.1 Классификация грунтов по трудности разработки 20
4.2 Методы разработки прочных и мерзлых грунтов 22
4.3 Разработка прочных и мерзлых грунтов машинами
для земляных работ 24
4.4 Анализ конструктивных схем ковшей активного действия 27
5 Модернизация и расчет экскаватора САТ 330 DL 32
5.1 Назначение и техническая характеристика экскаватора
5.2 Определение усилий резания 34
6 Разработка ковша экскаватора активного действия для
разработки прочных грунтов 37
7 Расчет основных параметров гидроударного
Расчета гидропривода питания механизма гидроударников 43
1 Выбор управляющего устройства давления и составление
2 Выбор объемных гидромашин 43
2.1 Расчет и выбор гидронасоса 43
3. Выбор гидроаппаратов и кондиционеров рабочей жидкости 44
4. Расчет и выбор трубопроводов 45
5. Расчет потерь давления в трубопровод 48
6. Определение потерь мощности в гидроприводе 51
7. Расчет статистических характеристик гидропривода с
машинным регулированием 52
Разработка технологического процесса изготовления детали
1. Назначение шестерни 55
2. Технические требования на изготовление шестерни 55
3. Разработка маршрута механической обработки шестерни 55
4. Расчёт припусков 56
5. Расчёт режимов резания 61
6. Расчет нормы штучного времени 85
7. Расчет калибр-пробки 91
8. Назначение и конструкция станочного приспособления 93
9. Расчёт сил зажима при обработке деталей фрезерованием 93
Расчёт себестоимости и цены модернизации рабочего
оборудования экскаватора СAT-330DL 95
1 Технико-экономическая оценка качества
спроектированного изделия 95
2 Расчёт себестоимости и цены 97
2.1. Покупные изделия и полуфабрикаты 97
2.2 Основная заработная плата производственных рабочих 98
2.3 Дополнительная заработная плата производственных
2.4 Отчисления на социальное страхование. 100
2.5 Расходы на содержание и эксплуатацию оборудования 100
2.6 Цеховые расходы 100
2.7 Расходы на подготовку производства 101
2.8 Цеховая себестоимость 101
2.9 Общепроизводственные расходы 101
2.10 Производственная себестоимость 101
2.11 Внепроизводственные расходы 101
2.12 Полная себестоимость 102
2.13. Прибыль нормативная 102
2.14 Оптовая цена предприятия 102
2.15 Налог на добавленную стоимость и спец налог 102
2.16 Отпускная цена 102
3 Построение сетевого графика проектирования нового изделия 104
Безопасность жизнедеятельности 109
1 Анализ опасностей которые могут возникнуть при
эксплуатации и ремонте экскаватора 109
2 Техника безопасности 110
2.1 Общие положения 110
3 Условия безопасного изготовления детали 111
4 Пожарная безопасность 113
5 Эргономический анализ кабины управления экскаватором 115
5.1 Общие требования безопасности и эргономики к рабочему
5.2 Управляемость 118
3.4. Запыленность 120
5.5 Температура относительная 120
5.6 Методы контроля эргономических требований 121
6 Освещения строительных площадок 123
6.1 Общие положения 123
6.2 Нормы освещенности 124
6.3 Освещенность кабины и зоны работ 125
7.1 Общие положения 126
7.2 Методы измерения вибрации на рабочих местах самоходных
строительно-дорожных машин 127
7.3 Анализ результатов испытаний 130
9 Инструкция по безопасной эксплуатации CAT 330 DL 132
9.1 Техника безопасности при эксплуатации экскаватора 132
9.2 Техника безопасности при передвижении экскаватора 135
9.3 Меры безопасности при техническом обслуживании и
текущем ремонте экскаватора 135
9.4 Действия в экстремальных ситуациях 139
9.5 Техника безопасности при монтаже и демонтаже экскаватора 140
10 Выводы по разделу 140
Список используемой литературы. 142
В настоящее время в парке строительных одноковшовых экскаваторов в нашей стране и за рубежом преобладают гидравлические машины с жесткой подвеской рабочего оборудования. Исключение составляют экскаваторы с рабочим оборудованием драглайна в которых сохранена гибкая (канатная) подвеска. Широкое распространение гидравлических экскаваторов обусловлено неоспоримыми преимуществами гидрообъёмного привода перед приводом с механической трансмиссией и гибкой подвеской рабочего оборудования в первую очередь простотой кинематических связей между источниками и потребителями энергии способностью простыми средствами преобразовать вращательное движение первичного двигателя в поступательное движение конечного звена исполнительного механизма способностью реализовать большие усилия на рабочих органах при минимальных размерах передаточных устройств возможностью силового воздействия на рабочие органы как в прямом так и в возвратном направлении и др. эти преимущества обеспечили гидравлическим экскаваторам высокую эффективность в частности более низкую чем у канатных экскаваторов материалоемкость.
Гидравлические экскаваторы появились в начале ХХ в. Один из первых гидравлических экскаваторов французской фирмы Поклейн представлял собой прототип широко распространенных полуповоротных тракторных экскаваторов.
Установка на экскаваторе с гидравлическим приводом оборудования обратной лопаты позволила получить на зубьях ковша усилия в 3..4 раза превышающие усилия развиваемые подобным оборудованием канатных машин такой же мощности и массы. Это резко расширило область их применения. В нашей стране освоен серийный выпуск строительных экскаваторов с ковшами вместимостью 025 32 м3.
Конструктивно-кинематическая схема рабочего оборудования гидравлической обратной лопаты обеспечивает жесткую передачу усилий при любом движении ковша что создало особые условия для работы ковша – точность и возможность изменения скорости и направления движения недостижимых при канатных системах. Главной особенностью явилась возможность непосредственного воздействия привода на исполнительные органы экскаватора без применения сложных механических трансмиссий снабженных муфтами тормозами редукторами коробками передач требующих сложного управления с применением для этого значительных усилий и сервомоторов трансформирующих крутящие моменты в конечные обычно поступательные и возвратные перемещения исполнительных органов. Все эти элементы заменяются в гидравлических экскаваторах трубопроводом подающим от насосов жидкость в исполнительные рабочие цилиндры штоки которых воздействуют через простые рычажные системы на рабочие органы. Ввиду того что рабочие цилиндры должны перемещаться вместе с рабочими органами подводка трубопроводом к цилиндрам в основном осуществляется гибкими шлангами. Сложное силовое управление механическими передачами при этом заменилось легким управлением золотниками изменяющими направление движения жидкости подаваемой насосом высокого давления в рабочие цилиндры. Однако в тех механизмах которые должны выполнять работу приводя в движение исполнительные и рабочие органы - ведущие колеса ходового оборудования гусеницы поворотные платформы сверла буры - частично сохранились зубчатые передачи но максимально сократилось их количество за счет применения мотор-колес высокомоментных гидродвигателей и др. Механические передачи насчитывающие в экскаваторах тысячи деталей заменяются несколькими десятками элементов. Таким образом главной особенностью гидравлического экскаватора является малое количество элементов трансмиссии.
Общие сведения о гидравлических одноковшовых экскаваторах
1 Назначение и классификация
Cтроительные гидравлические одноковшовые экскаваторы предназначены для разработки грунтов до 4 категории включительно без их предварительного разрыхления при отрывке котлованов траншей каналов дорожных кюветов и других выемок разработке резервов для отсыпки насыпей а также разработке карьеров строительных материалов. Они могут также разрабатывать более прочные грунты включая мерзлые и скальные после их разрыхления другими средствами. Эти машины широко используют в промышленном гражданском дорожном аэродромном трубопроводном гидротехническом и других видах строительства а также в промышленности строительных материалов.
Строительные неполноповоротные машины (малые модели) и полноповоротные гидравлические экскаваторы являются самоходными машинными с пневмоколесным (рис. 1.1) или гусеничным (рис.1.2) ходовым устройством. Пневмоколёсные экскаваторы используют на рассредоточенных строительных объектах с небольшими объёмами работ. Благодаря высокой скорости передвижения (на порядок выше скорости гусеничных машин) эти экскаваторы способны преодолевать большие расстояния при смене строительных объектов. Гусеничные экскаваторы обладая повышенной проходимостью передвигаются со скоростью не превышающей 3 кмч – для отечественных и 55 кмч – для зарубежных машин. Этими показателями предопределена область использования гусеничных экскаваторов – объекты с большими объёмами земляных работ без специальной подготовки рабочих площадок включая карьеры. Ходовые устройства этих экскаваторов используются лишь как опорные для передачи внешних нагрузок на грунтовое или иное основание в процессе экскавации грунта а так же для передвижения экскаваторов на небольшие расстояния в том числе с преодолением брода глубиной до 08 метров и их перемещения на новую стоянку (позицию) после отработки элемента забоя в пределах досягаемости рабочего оборудования или части рабочей зоны экскаватора ограниченной требованиями безопасной работы. Для перевозки этих машин на большие расстояния используют специальные транспортные средства (тяжеловозы железодорожный транспорт и т.п.). погружается экскаватор на транспортное средство собственным ходом. Главным направлением технического прогресса гидравлических экскаваторов является повышение рабочего давления насосов и двигателей (до 40 50 МПа) что уменьшает габариты и массу гидравлического оборудования. Однако увеличение давления вызывает повышение требований к конструкции надежности уплотнений и точности изготовления деталей гидрооборудования.
Дальнейшее совершенствование конструкций гидравлических экскаваторов связано с оптимизацией их основных параметров первым этапом которой является овладение методами расчета их основных параметров. К настоящему времени эти методы ещё не сформировались в единую теорию прежде всего из-за разнообразия подходов при конструировании экскаваторов различными заводами НИИ и зарубежными фирмами в связи с чем для учебных целей в качестве основного метода принято математическое моделирование процессов функционирования гидравлических обратных лопат как основного вида рабочего оборудования этих машин.
В соответствии с действующей в нашей стране индексацией гидравлические одноковшовые экскаваторы обозначают индексами состоящими из двух букв ЭО и через дефис четырех цифр первая из которых обозначает размерную группу экскаватора вторая – тип ходового устройства (1 – гусеничного2 – гусеничного с увеличенной опорной поверностью гусениц 3 – пневмоколесного) третья – исполнение рабочего оборудования (для гидравлических экскаваторов – 2) четвертая – порядковый номер модели (1 2 5 и т.д.). индексы модернизированных экскаваторов дополняются в конце буквой русского алфавита. А Б В и т.д. в порядке очередной модернизации). Индексы экскаваторов специального климатического исполнения дополняются в конце буквами ( ХЛ – северное исполнение Т – тропическое исполнение и т.п.) например гусеничный гидравлический экскаватор четвертой размерной группы четвертой модели прошедший первую модернизацию обозначают: ЭО 4241
Рис. 1.1 Одноковшовые гидравлические полноповоротные экскаваторы с жесткой подвеской рабочего оборудования: 1 – опорно-поворотное устройств о; 2 – пневмоколесное ходовое устройство; 3 – выносная опора; 4 – поворотная платформа; 5 – силовая установка; 689 – гидроцилиндры стрелы; 7 – стрела; 10 – рукоять; 11 – ковш обратной лопаты; 12 – бульдозерный отвал; 13 – кабина машиниста; 14 – гусеничное ходовое устройство; 15 – ковш прямой лопаты; 16 – телескопическая стрела.
Рис. 1.2. Одноковшовый полноповоротный гусеничный экскаватор пятой размерной группы: 1 – гусеничное ходовое устройство; 2 – противовес; 3 – кабина; 4 – стрела; 5 6 9 – гидроцилиндры рукояти ковша и стрелы; 7 – рукоять; 8 – ковш обратной лопаты; 10 – поворотная платформа.
Каждая модель экскаватора характеризуется рабочими размерами – максимальный глубиной копания радиусом копания на уровне стоянки и высотой выгрузки грунта. Требуемые параметры гидравлических экскаваторов рассчитывают по основному рабочему оборудованию с основными ковшами по этим параметрам выбирают комплектующие изделия (двигатели насосы гидроцилиндры гидромоторы и т.п.) назначают размеры несущих конструкций удовлетворяющие условиям прочности выносливости и другим категориям жизнеспособности машины определяют её выходные характеристики (рабочие размеры – максимальную глубину и радиус копания высоту выгрузки грунта и т.п. теоретическую производительность). Выходные характеристики экскаватора с другими типами ковшей или иными видами рабочего оборудования определяют исходя из его технологических возможностей обусловленных силовым оборудованием передаточными механизмами опорно–поворотным ходовым и другими устройствами соответствующими расчетным параметрам по основному виду рабочего оборудования.
Стандарт ограничивает средние удельные давления на опорную поверхность гусеничных экскаваторов массой до 18 т – не более 50 кПа до 25 т – не более 65 кПа до 32 т – не более 90 кПа до 50 – не более 120 кПа свыше 50 т – не более 220 кПа.
2 Рабочее оборудование
согласно ГОСТ – 30067-93 конструкция экскаватора должна обеспечивать возможность использования не менее 3 видов рабочего оборудования с различными сменными рабочими органами устойчивость при работе в том числе с наклоном в любом направлении на угол 5 градусов к горизонту с основным рабочим оборудованием; устойчивость при передвижении по твердой сухой поверхности вдоль косогора; стопорение поворотной части относительно неповоротной в транспортном положении.
В качестве основных рабочих органов на гидравлических экскаваторах используют ковши прямой и обратной лопат погрузчика грейфера. Сменными рабочими органами расширяющими номенклатуру выполняемых этими машинами работ могут быть бульдозерные отвалы для грубой планировки земляных поверхностей однозубые и многозубые рыхлителидля рыхления прочных грунтов пород и прослоек взламывания асфальтовых покрытий при ремонте автомобильных дорог а так же работ крановые подвески различные модификации грейферов и захватов для работы экскаватора в режиме крана шнековые буры для рытья колодцев небольших диаметров и др. экскаваторы способные работать с различными сменными рабочими органами называют универсальными а экскаваторы работающие только с одним видом рабочего оборудования – специальными.
В качестве основного для экскаваторов СНГ до 5-ой размерной группы включительно принято рабочее оборудование обратная лопата а для 6-ой размерной группы – прямая лопата. Диапазон использования рабочего оборудования обратная лопата в конструкциях зарубежных гидравлических экскаваторов существенно расширен. Так фирма Catarpillar комплектует этим видом рабочего оборудования экскаваторы соответствующие 7-ой размерной группе отечественных машин. Как на отечественных так и на зарубежных экскаваторах устанавливают ковши различной вместимости: основные (типа 02 по отечественной индексации) узкие (01) – меньшей вместимости для слабых грунтов и широкие (03) – большей вместимости для слабых грунтов. Ковши всех типов имеют одинаковые размеры профильной проекции и отличаются шириной и числом устанавливаемых на их передней стенке зубьев.
Рабочее оборудование обратная лопата включает последовательно соединенные между собой шарнирами стрелу рукоять и ковш. Стрела кроме того шарнирно соединена с поворотной платформой. Вместе с последней элементы рабочего оборудования образуют шарнирно-рычажный четырехзвенный механизм позволяющий занимать ковшу и режущим кромкам его зубьев различные положения в пределах рабочей зоны экскаватора на всех операциях его рабочего цикла.
Стрела может быть составной и моноблочной. Первая состоит из двух секций: корневой шарнирно соединённой с поворотной платформой и удлиняющей соединяемой с корневой секцией болтами. Чаще составными стрелами комплектуют универсальные экскаваторы. При замене рабочего оборудования обратной лопаты на прямую сохраняют только корневую секцию а удлиняют секцию либо используют в качестве рукояти прямой лопаты соответственно перемонтировав её либо заменяют новой. Моноблочная стрела коробчатого поперечного сечения обычно с разнесенными шарнирами для соединения с поворотной платформой и вилкой на противоположном конце в её головной части для соединения с рукоятью изогнутой конфигурации в профильной проекции обусловленной необходимостью работы в её нижнем положении без задевания за ходовую тележку (особенно при таком взаимном положении поворотной платформы и нижней рамы когда вертикальная плоскость симметрии рабочего оборудования совмещена с диагональной плоскостью опорного контура – «на угол ходовой тележки») и созданием подстрелового пространства при движениях ковша без задевания за стрелу. Стрела поднимается и опускается одним или двумя гидроцилиндрами шарнирно соединенными с ней и с передней поперечной балкой поворотной платформы. При одном гидроцилиндре шарнир его соединения со стрелой располагается либо в теле стрелы либо в проушинах под стрелой. В первом случае шток гидроцилиндра перемещается в прореви нижнего листа стрелы. Для компенсации прочностных свойств стрелы её боковые листы в этой зоне усиливают накладками или устраивают дополнительные внутренние продольные перегородки. При двух гидроцилиндрах их шарниры располагаются по обе стороны стрелы на приваренных к ней цапфах.
Рукоять так же коробчатого поперечного сечения с хвостовой частью (кривошипом) ориентированным относительно основной её части от приводящего её гидроцилиндра шарнирно соединенного с кривошипом и со стрелой.
Ковш в форме емкости открытой с одной стороны с зубьями установленными в карманы на передней стенке или без них (для разработки слабых грунтов) соединен с рукоятью шарнирно в её головной части и приводится шарнирно установленным одним концом на рукояти гидроцилиндром через шарнирно-рычажный механизм состоящий из коромысла и тяги и выполняющий функцию мультипликатора. В качестве основных в конструкциях гидравлических экскаваторов применяют ковши оснащенные зубьями.
Рабочий цикл гидравлического одноковшового экскаватора состоит из следующих последовательно выполняемых операций: отделения грунта от массива и заполнения им ковша (копания) перемещения грунта в ковше к месту выгрузки собственно разгрузки грунта и возвращения рабочего оборудования на исходную позицию следующего рабочего цикла. Только первые три операции являются рабочими последняя же четвертая операция вспомогательна необходимая для подготовки экскаватора к следующему рабочему циклу. Рабочий процесс экскаватора также называют экскавацией.
Копают грунт либо поворотом рукояти при фиксированном на ней ковше либо поворотом ковша при фиксированных стреле и рукояти либо совместным поворотом рукояти и ковша. Чаще всего используют первый способ. При этом гидроцилиндр стрелы отключают от насоса переведя его в плавающий режим работы. Поворотом рукояти к стреле ковш перемещается снизу вверх отделяя грунт от массива и заполняясь им стрела при этом в каждый момент времени занимает положение соответствующее минимуму затрат энергии на перемещение рабочего оборудования и на преодоление сил сопротивления грунта копанию. Этому же условию подчиняется траектория движения режущих кромок ковша. В общем случае эта траектория может отличаться от требуемой например по условиям получения однородных по форме срезов на всех рабочих циклах. Её корректируют кратковременным включением стрелового гидроцилиндра на подъем или опускание стрелы. Такая схема копания характерна при работе экскаватора открытой проходкой – удлинением или уширением уже имеющейся выемки. При разработке же выемки закрытой проходкой (от поверхности земли) включая разработку пионерной выемки грунт копают любым из перечисленных выше способов.
В конце операции копания для предотвращения от просыпания грунта из ковша на следующей транспортной операции ковш подворачивают к рукояти после чего рабочее оборудование поднимают стреловым гидроцилиндром. Поворотное движение платформы начинают после того как рабочее оборудование будет выведено из выемки. Одновременно с подъемом стрелы маневровыми движениями рукояти и ковша добиваются установки последнего в конце поворота платформы в положение выгрузки.
Разгружают грунт отворотом ковша от рукояти. Различают разгрузку в отвал и в транспортное стредства. В первом случае эта операция не требует полной остановки платформы – разгрузку начинают в конце поворотного движения в прямом направлении и заканчивают в начале возвратного вращения. Во втором же случае во избежание просыпания грунта при его разгрузке требуется четкая координация ковша относительно кузова транспортного средства. Для этого платформу останавливают и включают на возвратное вращение только после полной выгрузки ковша. Разгрузка в транспортное средство требует большего времени чем разгрузка в отвал а следовательно она менее производительна по сравнению с последней. Заметим что эта оценка справедлива только в части производительности экскаватора но не всего механизированного комплекса занятого на отрывке выемки. Если например отвал рассматривать как промежуточное хранилище грунта который впоследствии будет вывезен за пределы строительной площадки то на этом последнем этапе дополнительно будут задействованы те же экскаваторы или погрузочные машины что безусловно снизит производительность комплекса по сравнению с работой экскаватора вместе с транспортными средствами без промежуточного отвала.
По составу рабочих движений последняя операция – возврат рабочего оборудования на исходную позицию следующего рабочего цикла – аналогична операции транспортирования грунта на разгрузку но выполняется в обратной последовательности указанных движений.
После отработки элемента забоя в пределах допустимой СНиП части рабочей зоны экскаватора последний перемещают на новую стоянку (позицию) предварительно сориентировав рабочее оборудование вдоль гусениц. При межпозиционных передвижках пневмоколёсных экскаваторов кроме того требуется поднять выносные опоры и бульдозерный отвал если таким оборудован экскаватор а на новой позиции установить эти устройства в рабочее положение. Совокупность всех рабочих циклов выполненных с одной позиции экскаватора вместе с его передвижкой на новую позицию образует большой цикл.
4 Анализ состояния вопроса разработки прочных и мерзлых грунтов одноковшовыми экскаваторами
4.1 Классификация грунтов по трудности разработки
Классификация грунтов по трудности разработки землеройными машинами представляет определенную сложность ввиду значительного многообразия и изменчивость прочностных характеристик.
С накоплением фактических данных о свойствах грунтов оказалось возможным классифицировать их по одному характерному показателю прочности хорошо коррелирующемуся с сопротивляемостью грунта разрушению рабочими органами землеройных машин.
Одной из наиболее общих явилась классификация горных пород (грунтов) М.М. Протодъяконовым на десять категорий (I – X) коэффициенту крепости (прочности) – обобщенному показателю их сопротивляемости разрушению (табл 2.1) Коэффициент крепости является интергальной численной характеристикой прочностных свойств горных пород. За единицу крепости скальных грунтов (I – VI категории) принята прочность кубина породы имеющего сопротивление одноосному сжатию 10 МПа. Для нескальных грунтов ( VIа – X категории) принята прочность определен в виде где угол внутреннего трения
Нескальные грунты имеющие коэффициент крепости f2 относятся к довольно мягким породам. Их разработку осуществляют землеройными машинами: экскаваторами бульдозерами скреперами грейдер-элеваторами без предварительного рыхления.
Скальные и мерзлые грунты с f=25 являются породами средней крепости. Разрабатывают их землеройными машинами после предварительного рыхления механическими средствами.
Скальные грунты с f5 предварительно разрыхляют взрывом и затем перемещают землеройными машинами. В ряде случаев при относительно тонких прослойках (до 20 см) такие грунты можно разрабатывать механическим способом.
Таблица 1.1 – Классификация грунтов по коэффициенту крепости
Коэффициент крепости (прочности)
Наиболее крепкие кварциты и базальты
Гранитные породы кварцевый порфир очень крепкий кремнистый сланец менее крепкие кварциты крепкие песчаные известняки
Плотный гранит менее крепкие песчаники и известняки кварцевые рудные жилы крепкий конгломерат очень крепкие железные руды
Некрепкий гранит крепкий мрамор доломит колчеданы
Обыкновенный песчаник железные руды
Песчаные сланцы сланцевые песчаники
Продолжение таблицы 1.1
Крепкий глинистый сланец некрепкий песчаник и известняк мягкий конгломерат
Разнообразные сланцы плотный мергель
Мягкий сланец известняк мел гипс мерзлый грунт антрацит обыкновенный мергель разрушенный песчаник
Щебенистый грунт разрушенный сланец слежавшаяся галька и щебень отвердевшая глина
Плотная глина мягкий каменный уголь глинистый грунт
Легкая песчанистая глина лесс гравий
Растительная земля торф легкий суглинок сырой песок
Песок осыпи мелкий гравий насыпанная земля
Плывуны болотистый грунт разжиженные грунты
В строительстве при нормировании землеройных работ и определении расценок наибольшее распространение получила классификация Госстроя распределяющая немерзлые и мерзлые грунты в состоянии природной влажности и плотности по группам в зависимости от трудности разработки перемещения и укладки разными машинами. Принятая классификация позволяет оценить трудность разработки не только однородных грунтов но и с большим количеством включений валунов строительного мусора с примесями щебня гравия и т.п.
4.2 Методы разработки прочных и мерзлых грунтов
в настоящее время исследования в СНГ и за рубежом показывают что общее количество способов разработки мерзлых грунтов непрерывно растет.
Появляются новые технологии основанные на последних достижениях механики физики химии электротехники и др. В связи с этим возникает задача оценки этих технологий и определения областей из применения.
Земляные работы при разработке прочных и мерзлых грунтов осуществляется следующими методами:
- методом предварительной подготовки грунтов с последующей их разработкой обычными способами;
- методом предварительной нарезки мерзлых грунтов на блоки;
- методом разработки грунтов без предварительной подготовки.
Предварительная подготовка грунта для разработки зимой заключается в предохранении его от промерзания оттаивания мерзлого грунта и предварительном рыхлении мерзлого грунта. Наиболее простой способ защиты поверхности грунта от промерзания состоит в утеплении его термоизоляционными материалами; для этого используются торфяная мелочь стружки и опилки шлак соломенные маты и т.п. которые укладываются слоем 20-40 см непосредственно по грунту. Поверхностное утепление применяют в основном для небольших по площади выемок.
Для утепления значительных по площади участков применяется механическое рыхление про котором грунт вспахивается тракторными плугами или рыхлителями на глубину 20-35 см. с последующим боронованием на глубину 15-20см.
Механическое рыхление мерзлого грунта при глубине промерзания до 025 м производится тяжелыми рыхлителями. При промерзании до 06 – 07 м при отрывке небольших котлованов и траншей применяют так называемое рыхление раскалыванием. Ударные мерзлоторыхлители хорошо работают при низких температурах грунта когда для него характерны хрупкие деформации способствующие его раскалыванию под действием удара. Для рыхления грунта при большой глубине промерзания (до 13 м) используется дизель-молот с клином. Разработка мерзлого грунта резанием заключается в нарезке взаимно перпендикулярных борозд глубиной составляющей 08 глубины промерзания. Размер блока должен быть на 10-15 % меньше размера ковша экскаватора.
Оттаивание мерзлого грунта осуществляется при помощи горячей воды пара электрического тока или огневым способом. Оттаивание является наиболее сложным трудоемким и дорогим способом поэтому к нему прибегают в исключительных случаях например при проведении аварийных работ.
Наиболее эффективным способом разработки мерзлых грунтов является ударный с использованием навесных устройств. Эффективность применения той или иной технологии разработки грунтов будет зависеть от научно обоснованного выбора конструктивных и технических параметров ударных устройств схем средств навески и перемещения их в технологическом пространстве относительно разрушаемого объекта.
4.3 Разработка прочных и мерзлых грунтов машинами для земляных работ
Машины для земляных работ в основном рассчитаны на работу в грунтах и породах с удельным сопротивлением копанию до 4 кгсм2. Работа в более тяжелых группах приводит к резкому снижению их производительности перегрузке проводных двигателей и узлов пробуксовке муфт повышению энергоемкости процесса. В связи с этим в последнее время большое внимание уделяется созданию машин динамического разрушения горных пород и мерзлых грунтов с последующим удалением разрыхлённого грунта из забоя серийной машиной для земляных работ.
В зависимости от назначения и конструктивных особенностей машины для земляных работ при разработке прочных и мерзлых грунтов можно разделить на две группы.
К первой группе относятся землеройные и землеройно – транспортные машины предназначенные в основном для выполнения земляных работ в летнее время но имеющие прочность рабочего оборудования и мощность двигателей достаточные для рыхления мерзлых грунтов залегающих слоями ограниченной толщины (в большинстве случаев менее 20-40 см). К таким машинам относятся экскаваторы (прямая лопата) с геометрической вместимостью ковша более 05 – 10 м3 и бульдозеры преимущественно гусеничные с мощностью двигателей от 90 кВт и более.
Экскаватором с прямой лопатой вместимостью 065 м3 в средних условиях можно разрабатывать грунт промерзший с поверхности на глубину до 25 см а с лопатой вместимостью более 1 м3 – 40 см.
Возможности использования экскаваторов для разработки мерзлого грунта значительно повышаются при применении так называемых ковшей активного действия. Особенность их заключается в том что они имеют подвижные ударные зубья установленные в полой передней станке ковша. Эти зубья действуют подобно электромолоткам или пневматическим молоткам. Они включаются в работу при определенном (повышенном) сопротивлении погружению ковша в грунт. Экскаваторами с такими ковшами вместимостью 07 м3 можно разрабатывать мерзлые слои толщиной 05-08 м.
Бульдозеры используют для разрушения способом подламывания снизу мерзлых слоев толщиной до 20-25 см.
В отдельных случаях для разработки тонких слоев слабомерзшихся песчаных грунтов используют также большегрузные скреперы. Воздушно-сухие песчаные грунты смерзаются слабо не образуя прочных монолитов. В начале зимы при глубине промерзания менее 15-20 см их можно разрабатывать непосредственно скреперами. При большой толщине и прочности мерзлого слоя его необходимо предварительно рыхлить бульдозерами или рыхлителями.
Ко второй группе относят машины имеющие оборудование специально предназначенное для рыхления мерзлых грунтов. Таким оборудованием являются тяжелые металлические отливки шаровой или клинообразной формы мощные прицепные или навесные рыхлители баровые машины. С их помощью можно разрыхлять слои мерзлого грунта толщиной 08 – 14 м а иногда и более.
Наиболее простой вид оборудования для рыхления мерзлых грунтов ударной нагрузкой – чугунные или стальные шары-молоты массой 15 – 4 т которые подвешивают на канате к стреле крана или экскаватора и затем сбрасывают на разрыхляемый грунт с высоты 3 – 5 м и более.
Более совершенным подвесным оборудованием к экскаваторам являются различные клин – молоты представляющие собой массивные металлические отливки имеющие в нижней части острый угол. Из сбрасывают так чтобы они при падении откалывали куски мерзлого грунта. Наибольшую производительность в мерзлых связных грунтах клин-молоты имеют при угле заострения 25-30 градусов. При разработке несвязных мерзлых грунтов угол может быть увеличен до 35 градусов. При меньших углах заострения клин легче погружается в мерзлый грунт но не всегда откалывает мерзлые глыбы так как расклинивающее усилие может оказаться недостаточным. При большом угле заострения возрастает расход энергии на смятие мерзлого грунта и уменьшается глубина погружения клина. Клин-молотом массой 3-4 т сбрасываемым с высоты 8-10 м можно дробить слои мерзлого грунта толщиной 08-14 м.
Недостатками применения свободного падающих отливок любой формы закрепленных на тросе являются низкая производительность износ троса и самого экскаватора.
В гражданском строительстве особенно при рытье траншей для различных трубопроводов с успехом используют машины разрабатывающие мерзлые грунты по способу нарезания в них узких щелей и затем скола ослабленного грунта между щелями. В дорожном строительстве подобные машины применяют редко.
Значительно чаще при разработке резервов и карьеров в зимних условиях применяют различного рода прицепные и навесные рыхлители производящие послойное рыхление мерзлых грунтов. Одностоечные рыхлители на тягачах мощностью 200 кВт и более за несколько проходов рыхлят слои мерзлого грунта толщиной до 10 м. Эффективность применения их повышается при объединении в одной конструкции рыхлящего зуба и пневмомолота в работе зуба в виброударном режиме.
Недостаток работы мощных одностоечных рыхлителей – разделение грунта на крупные глыбы зачастую требующее дополнительного дробления.
Во всех случаях разработки мерзлых грунтов необходимо учитывать дальнейшее использование его после рыхления. Для разрыхленного мерзлого грунта величина глыб ограничивается только размерами ковша используемого экскаватора. При укладке грунта в насыпь размеры получаемых при отколе кусков не должны превосходить размеров допускаемых техническими указаниями из условий уплотнения отсыпаемых слоев (15-30 см).
Выбор машин и оборудования для рыхления мерзлых грунтов определяется в основном глубиной промерзания прочностью мерзлого слоя и стоимостью производства работ. В начале зимнего периода может быть использовано большинство из перечисленных выше машин и оборудования. При малой толщине мерзлых слоев чаще всего используют экскаваторы и бульдозеры. Этими машинами производят как рыхление мерзлых поверхностных слоев так и разработку расположенных ниже талых грунтов.
Из известных способов механического разрушения мерзлых грунтов лучшими показателями обладают динамический скол грунта с отрывом. Эти обстоятельства обусловили разработку ковшей активного действия к гидравлическим экскаватором с использованием данных способов разрушения. Оснащение парка экскаваторов сменными ковшами активного действия позволит выполнить весь комплекс по рыхлению и ударению мерзлого грунта и использование экскаваторного парка увеличить производительность экскаваторов не только в мерзлых но и тяжелых талых и скальных грунтах при одновременном снижении трудовых затрат и стоимости работ.
В настоящее время разработаны различные конструктивные схемы активных ковшей использующие принцип ударного воздействия на забой.
4.4 Анализ конструктивных схем ковшей активного действия
Используя принцип ударного воздействия на забой были разработаны различные конструктивные схемы активных ковшей с электрическим пневматическим и гидравлическими приводами.
С электрическим проводом можно выделить работы НИИ по строительству (г. Екатеринбург Россия) которым были созданы различные модели ковшей с виброударными зубьями а также МИСИ и ВНИИСтройдормаш (Россия) проводивших теоретические и экспериментальные исследования активных ковшей с принудительными колебаниями передней стенки. Однако они не нашли применения в практике вследствие отсутствия обратной связи между исполнительными механизмами и забоем низкой удельной энергии на рабочих инструментах значительных динамических нагрузках на электродвигателях трудности регулирования энергии и частоты колебания при суммарном воздействии напорного режущего усилия и веса грунта в ковше.
С 1969 по 1971 г.г. в СССР осуществлялся выпуск ковшей активного действия отдельными небольшими сериями использующих в качестве привода сжатый воздух. Эксплуатация их на различных строительных объектах подтвердила перспективность непосредственной экскавации прочных и мерзлых грунтов рабочими органами оснащенными источниками импульсной энергии. К недостаткам ковшей с пневматическими ударными устройствами следует отнести применение дорогостоящих и громоздких компрессорных установок имеющих малый коэффициент использования мощности и снижающих маневренность базовой машины.
Широкое применение гидравлических экскаваторов создают предпосылки к создания ковшей активного действия с гидравлическими импульсными системами. Гидравлический привод импульсных систем активных ковшей по конструктивным особенностям дополнительных механизмов подразделяется на: виброударный вибрационный кулачковый с гидросвязью и гидроударный. Гидропривод импульсных систем активных ковшей можно выделить в три структурные схемы: общий индивидуальный насосно-аккумуляторный. Одним из направлений использования гидропривода в ковшах активного действия является импульсная система с гидропневмоаккумуляторным приводом достоинство которой – высокая энергия единичного удара малые габаритные размеры низкая металлоемкость высокий КПД возможность плавного в широком диапазоне изменения энергии и частоты ударов.
Для обобщения и систематизации импульсных систем ковшей активного действия составлена их классификация учитывающая вид энергии принцип действия исполнительных механизмов наличие обратной связи между забоем и исполнительным механизмом и вид импульсов возникающих на режущей кромке ковша.
Импульсные системы активных ковшей
По виду подводимой энергии
Шатунно-эксцентриковые
По виду обратных связей между забоем и исполнительным механизмом
Рассмотрим реализацию различных конструктивных схем ковшей активного действия. Ковш с виброударными зубьями ВК-2 (рис 1.3) был выполнен как сменное навесное оборудование к экскаватору Э-505. Параметры виброударных механизмов обеспечивали получение на режущей кромке ковша удельной энергии 005 Нм.
Рис 1.3: Активный ковш 1 – зуб; 2 – вибромолот; 3 – дебаланс; 4 – спинка ковша; 5 – шток зуба
Ударной частью вибромолота является вибратор состоящий из электродвигателя АО-42-4 на выходных валах которого насажены дебалансы и плита с наковальней. При работе электродвигателя с дебалансами последние сообщают ударные нагрузки плите с наковальней которая в свою очередь через зубьям. На оптимальный режим вибромолоты настраиваются путем изменения степени поджатия пружин регулировкой стяжных болтов. Для гашения холостых ударов при отсутствии контакта с грунтом предусмотрены амортизационные пружины.
В заграничной практике импульсные системы с электрическим приводом имеют малое распространение. Попыткой создания активного ковша с электрическим приводом является конструкция показанная на рис 2.3. рыхлители грунта 2 опирающиеся в раме 1 на пружины 6 подвергаются вибрациям при помощи двигателя 4 который вращает два эксцентрика 3 с параллельными осями. Двигатель с эксцентриком установлен на раме 5 соединенный со стержнями 7 и направляется так чтобы они скользили вертикально и передавали вибрации рыхлителям.
Сменное рабочее оборудование с ковшом активного действия приведенное на рис 2.4 включает в себя ковш с тремя пневмоударными блоками воздухопровод с флюгерным устройством и передвижной компрессор.
Ударный блок состоит из трех основных узлов компактно объединенных в один рабочий орган: узла крепления инструмента ударного механизма с воздухораспределительным устройством узла автоматического запуска пневмомолота в работу. Узел крепления инструмента состоит из собственного инструмента корпуса и мпонки.
Рис 1.4: : Активный ковш 1 – рама; 2 – рыхлитель грунта; 3 – эксцентрик; 4 – двигатель; 5 – рама; 6 – пружина; 7 - стержень
Ковш модели «Hymas Dynamin» (Щвеция) емкостью 011 м3 (рис 2.5) имеет шесть сменных рабочих органов различного типа и используется на гусеничных и пневмоколесных гидравлических экскаваторах различных моделей для рыхления мерзлых грунтов и скальных пород уплотнения грунтов погружения шпунта и ударного бурения. Ударный механизм позволяет развивать энергию единичного удара 400 Дж с частотой 83 100 Гц.
Рис 1.5: Ковш активного действия фирмы«Hymas Dynamin»
5 Модернизация и расчет экскаватора САТ 330 DL
Гидравлический экскаватор САТ 330 DL (рис 1.9) на гусеничном ходу пятой размерной группы наиболее эффективно может быть использован на крупных объектах в условиях городского сельского промышленного и транспортного строительства для разработки грунтов I-IV категорий погрузки сыпучих материалов разрыхленных скальных пород и мерзлых грунтов с величиной кусков не более 400 мм а также для планировочных земляных работ в районах с умеренным климатом при температуре воздуха от -40 до +40 градусов Цельсия.
Рис 1.9: общий вид экскаватора САТ 330 DL 1 – поворотная платформа; 2 – гусеничная тележка; 3 – стрела; 4 – активный ковш.
Поворотная платформа экскаватора САТ 330 DL является основной металлоконструкцией экскаватора на которой установлены рабочее оборудование гидропривод кабина с системой управления механизм поворота. Основной целью размещения оборудования на поворотной платформе является получение наибольшего статического момента удерживающего экскаватор от опрокидывания. Для этой цели на поворотной платформе устанавливают противовес. Поворотная платформа опорно-поворотным кругом соединяется с ходовым устройством через которое нагрузки действующие на рабочее оборудование при работе а также сила тяжести поворотной части машины передаются на ходовое устройство.
Опорно – поворотный круг состоит из наружной обоймы прикрепляемой к поворотной платформе и зубчатого венца жестко соединенного с рамой ходового устройства. На профильной дорожке обоймы размещен ряд роликов в постоянном зацеплении с зубчатым венцом находится обегающая шестерня. Механизм поворота с помощью гидроприводов обеспечивает поворот рабочего оборудования к месту выгрузки и обратно в забой. Удержание поворотной платформы при копании траншей и при расположении машины на уклонах обеспечивается автоматическим колодочным тормозом срабатывающим при выключении гидродвигателя. К поворотной платформе крепится подвижная часть центрального масляного коллектора через который рабочая жидкость подается к гидромоторам ходового устройства.
Ходовое устройство предназначено для восприятия и передачи на опорную площадку силы тяжести экскаватора и сил взаимодействия рабочего органа с грунтом стопорения машины в забое маневрирования в забое и перемещения его между объектами работ. Ходовое устройство включает в себя раму гусеничный движитель механизм их привода и стопорения.
Техническая характеристика экскаватора САТ 330 DL приведена в таблице 3.1
Наименование показателей
Мощность двигателя л.с.
гидрораспределителями
Рычажное с сервоуправлением
Вспомогательными механизмами
Скорости передвижения кмч
Частота вращения поворотной платформы. Обмин
Преодлеваемый экскаватором уклон пути;град
В гидросистеме сервоуправления
Угол поворота рабочего оборудования град
Масса экскаватора с оборудованием обратной лопаты кг
Вместимость ковша м3:
При работе прямой лопатой
При работе обратной лопатой с удлиненной рукоятью
При работе обратной лопаты с удлиненной рукоятью
5.2 Определение усилий резания
D01 = D01D+D01I+D01d
Где D01D - составляющая от резания грунта;
D01I - Составляющая от наполнения ковша;
D01 - Составляющая от резания ковша о грунт.
Нормальная составляющая реакция грунта от копания:
Где 125 кгсм2 максимальный предел прочности грунта при смятии;
y= 3 см проекция контура износа режущей кромки на касательную траектории резания;
n=5 – число зубьев ковша
bр=15 cм ширина зуба ковша
g=98 мс2 – ускорение свободного падение
Составляющая от резания грунта:
D01d=[hc(Bk+ hc)(055+0015α)+nbр+уnbр)]g
=125кгсм2 максимальный предел прочности грунта при срезе;
hc= толщина срезаемой стружки;
α = 490 передний угол резания
z= 08 см проекция износа режущей кромки на нормаль к траектории;
=05 коэффициент трения стали о грунт;
Толщина срезаемой стружки определяем исходя из условия наполнения ковша на135% при коэффициенте разрыхления Кр=135 наполнение ковша происходит при полном его повороте на 1520
Объём грунта в ковше
=2 м3- вместимость ковша;
– коэффициент наполнения ковша;
R hc – смотри рисунок 32.
Решив уравнение (3.4) получим hC = 015м = 15 см.
P01P = [125·15·(120+15)·(055 + 0015·49) + 125·(06·5·8+05·3·5·8)]·981 = 42201 Н.
Составляющая от наполнения ковша
Где НН = 06 м высота наполнения ковша;
ρ = 20 тм3 плотность грунта в плотном теле;
= 10 коэффициент трения грунта о грунт;
После подстановки расчетных величин получим:
Примем φi = 90°. Тогда cos φi = 0 и Р01Н = 0.
Составляющую Р01Т не учитываем ввиду ее малого значения. Тогда касательная составляющая реакции грунта копанию:
Р01 = Р01Р = 42209 Н.
Нормальная составляющая реакции грунта копанию по формуле (3.2):
Р02 = 125·3·5·8·981 = 14715 Н.
6 Разработка ковша экскаватора активного действия для разработки прочных грунтов
Для разработки мерзлых и прочных грунтов активно используются гидроударные рабочие органы. Использование гидроударных органов улучшает выход фракционного состава продуктов экскавации расширяет возможность базовой машины и резкое сокращение объема буровзрывных работ. Широкое распространение гидроударных рабочих органов обусловлено безопасностью их работы во влажных запыленных и взрывоопасных помещениях а так же при работе на открытом воздухе так как их привод нечувствителен к внешним условиям. Кроме того эти машины обладают высокой надежностью и долговечностью безотказностью в работе нечувствительностью к перегрузкам возможностью продолжительного режима безостановочной работы.
В настоящей работе предлагается сменное рабочее оборудование с ковшом активного действия который включает в себя ковш с пятью гидроударными блоками.
Ковш активного действия (рисунок 1.3) представляет собой сварную конструкцию отличающуюся от обычных ковшей тем что с вместе жестко закрепленными зубьями имеет пять гидроударных устройства. Подвод рабочей жидкости к ударным устройствам осуществляется по гидромагистралям высокого давления расположенным в рукояти и стенках корпуса.
Работа гидроударного устройства происходит следующим образом (рисунок 1.3). В начале такта поршень-боек 6 и золотник 7 находятся в нижнем положении под действием сил тяжести. Рабочая жидкость поступает по каналу в кольцевые выточки А и Б золотниковой коробки и будет создавать давление на золотник снизу. Одновременно рабочая жидкость проходя по каналу 2 будет давить на верхний обрез золотника сверху. Но поскольку вся надпоршневая полость через канал 3 соединена с маслобаком давление на золотник сверху будет несколько меньше чем снизу он займет верхнее положение. Тогда рабочая жидкость поступит по выточкам А и Б и далее по каналу 4 под поршень-боек и будет перемещать его вверх т.е. начинается холостой ход.
Рис. 1.7 Активный ковш с гидроударниками: 1 – сварная конструкция ковша; 2 – гидроударное устройство; 3 – зуб
Рис. 1.11 Активный ковш с гидроударниками: 1 – сварная конструкция ковша; 2 – гидроударное устройство; 3 – зуб
Жидкость из верхней полости во избежание противодавления будет отводиться в маслобак по каналам 3 и 5. Когда поршень-боек перемещаясь вверх перекроет эти каналы то в верхней полости создается давление действующее на золотник сверху и он будет находиться в состоянии равновесия. При дальнейшем движении поршня-бойка вверх открывается канал 3 жидкость начнет уходить в маслобак по каналам 3 и 4 давление на золотник снизу упадет и он перейдет в нижнее положение. Тогда рабочая жидкость поступит по каналу 2 и под его давлением поршень-боек переместится вниз. жидкость из надпоршневого пространства будет отводиться в маслобак по каналу 3. При движении вниз поршень-боек открывает канал 5 в который поступает рабочая жидкость создавая давление на золотник снизу. Золотник будет находиться в состоянии равновесия ( под действием давления сверху и снизу) до тех пор пока поршень-боек в крайнем нижнем положении не откроет канал 3. Тогда рабочая жидкость из надпоршневого пространства будет выходить в маслобак давление на золотник сверху уменьшится и он переместится в верхнее положение заставляя поршень-боек подниматься вверх.
7 Расчет основных параметров гидроударного устройства
К основным параметрам гидроударного устройства относятся: работа единичного удара А1 (Н·м) число ударов поршня-бойка в минуту n (мин -1) мощность привода N (кВт) и расход рабочей жидкости Q (л3мин). Для упрощения расчета делаем следующие допущения: рабочий ход поршня-бойка происходит при постоянном давлении рабочей жидкости на его поверхность; противодавление на поршень-боек во время рабочего и холостого ходов неизменно; движение поршня-бойка при постоянном давлении – равноускоренное.
При этом кинематическая энергия накопленная поршнем-бойком за рабочий ход составит:
где d – диаметр поршня-бойка d = 005 м;
s – ход поршня-бойка s = 015;
pi – среднее индикаторное давление в цилиндре во время рабочего хода.
Используя практические данные принимаем потери давления в пусковых и распределительных устройствах машин равными 20 30% от номинального а противодавление на поршень-боек примерно на 15% выше атмосферного. Тогда
где p0 – номинальное (на входе в инструмент) давление (p0 = 24·106 Па).
pi = 0730·106 – 005106 = 21106.
Работа А2 совершаемая рабочим наконечником будет меньше А1 на величину потерь при соударении поршня-бойка с наконечником т.е.
Где уд – коэффициент полезного действия удара который зависит от масс соударяющихся тел и их упругих свойств обычно уд = 085 098.
А2 = 6·09 = 5564 Дж.
Число ударов поршня-бойка в минуту
где Т – продолжительность времени между двумя ударами.
где tp – время рабочего хода поршня-бойка;
tx-x – время холостого хода поршня-бойка.
С учетом принятых допущений
где m1 – масса поршня-бойка m1 = 0.35 кг.
Время холостого хода поршня-бойка tx-x = 12 tp = 12 ·0031 = 0038 с.
Т = 0038+0058 = 0096 с.
Мощность развиваемая одним гидроударным устройством
N = 6182·10.4·09·10 -3 = 52 кВт.
Расход жидкости (лмин) затрачиваемый на работу гидроударного устройства зависит от рабочего пространства цилиндра устройства числа ударов поршня-бойка в минуту и среднего индикаторного давления в цилиндре т.е
где kn – коэффициент учитывающий потери рабочей жидкости в гиромагистралях устройствах (kn = 12 135) принимаем kn = 04
Расчетная производительность гидромотора (лмин) для питания всех гидроударных устройств
Где K1 – коэффициент одновременности работы устройств при одновременной работе пяти устройств K1 = 09
Q = 5·12·09 = 54 лмин.
На основании выполненного расчета получены следующие характеристики гидроударного устройства:
Давление рабочей жидкости 21
Энергия единичного удара Дж 6
Частота ударов Гц 104
Расход рабочей жидкости одного устройства лмин 12
Производительность насоса лмин 82
Расчет гидропривода питания механизма гидроударников.
1 Выбор управляющего устройства давления и составление гидросхемы
Выходная мощность рассчитывается для гидропривода:
Nвых.max= (2314216169) =2592 кВт
Так как максимальная величина выходной мощности больше 5 кВт выбирают машинное регулирование.
Для реализации исходных данных подходит гидросхема представлена на рисунке. Ее описание приведено ниже.
2 Выбор объемных гидромашин
2.1 Расчет и выбор гидронасоса
На экскаваторе ЕК – 18 для привода гидромотора поворота платформы используется аксиально-поршневой регулируемый насос типа 310.20.55
- рабочий объем qн= 548 см3об;
- номинальная подача Qн.ном= 1301 10-3 м3с; (822 лмин)
- номинальное давление Pн.ном = 20 МПа;
- номинальная частота вращения Nн.ном.= 25 обс (1500 обмин);
- объемный КПД о.н.= 095;
- механический КПД мех.н.= 0958;
- полный КПД н = 091.
Определим ориентировочное давление гидронасоса:
где Рг –максимальное давление для гидромотора Р = 32 МПа;
ΣΔР – суммарные потери давления в гидроцилиндре
ΣΔР = 005 Рг = 16 МПа.
Подставляя числовые значения получим
Определим ориентировочную подачу насоса
где Qг1 = 3м3с расход гидромотора при номинальных оборотах
ΣΔQ – суммарные объемные потери в гидроприводе
ΣΔQ = 01 Qг1 = 01 127310-3 =м3с таким образом
Qн = 127310-3 + 1.27 10-4 = 1393 10-3 м3с .
3 Выбор гидроаппаратов и кондиционеров рабочей жидкости
Согласно гидросхеме выбираем гидроаппараты: распределитель жидкости предохранительный клапанфильтр только по Qн так как он установлен в сливном трубопроводе.
Выбираем 3 секционный распределитель жидкости типа ГР-520 с механическим управлением и условным проходом 30 мм выписываем его паспортные данные:
- номинальное давление Pр.ном= 30 МПа;
- номинальный расход Qр.ном= 266 10-3 м3с (160лмин);
- объемные потери ΔQр. = 75см3мин;
- потери давления ΔPр.= 07 МПа
Выбираем первичный предохранительный клапан непрямого действия патронного исполнения 510.20.01А и выписываем его паспортные данные:
- номинальное давление Pп.к.ном= 20 МПа;
- номинальный расход Qп.к..ном= 266 10-3 м3с (160лмин);
- потери давления ΔPп.к..= 06 МПа.
Выбираем блок вторичных предохранительных клапанов непрямого действия типа КЗ.10.01 и выписываем его паспортные данные:
- максимальный расход Qп.к..мак. = 2 10-3 м3с (120лмин);
- диапазон регулирования давления 5 – 42 МПа
Для аксиально-поршневых насосов тонкость фильтрации рабочей жидкости должна быть 16 -25 мкм. Так как установку фильтра предусматриваем в сливном трубопроводе то выбираем фильтр типа 1.1.32-25 из прил. 51 выписываем его паспортные данные:
- номинальное давление Pф.ном= 063 МПа;
- номинальный расход Qф..ном= 166 10-3 м3с (100лмин);
- потери давления ΔPф..= 005 МПа
- тонкость фильтрации25 мкм;
- материал фильтрующей шторы Бумага БФМ.
4 Расчет и выбор трубопроводов
Расчет выполняем отдельно для всасывающего напорного и сливного трубопроводов используя одни и те же формулы. Внутренний диаметр трубопровода определяем по трем условиям обеспечения:
допустимой скорости рабочей жидкости в трубопроводе;
ламинарного режима движения рабочей жидкости;
допустимых потерь давления в трубопроводе.
Принимаем допустимую скорость движения рабочей жидкости в трубопроводах: всасывающем Vтр.в= 1 мс; напорном Vтр.н= 45 мс; сливном Vтр.с= 15 мс.
Определим внутренний диаметр всасывающего трубопровода по условиям:
здесь – кинематическая вязкость масла МГ-30 при температуре 50°С
где – кинематическая вязкость масла МГ-30 при температуре 20°С
= 15010-6 м2с;Lтр.в.- длина всасывающего трубопровода Lтр.в= 1м; - допускаемые потери давления в трубопроводе = 02 МПа.
Из трех значений dтр.в1 dтр.в2 dтр.в3 принимаем большее значение dтр.в=00407м.
Определяем внутренний диаметр напорного трубопровода по условиям:
второму как и для всасывающего трубопровода
Здесь длину напорного трубопровода принимаем Lтр.н= 3м.
Из трех значений dтр.н1 dтр.н2 dтр.н3 выбираем большее dтр.н=0026м.
Определяем внутренний диаметр сливного трубопровода по условиям:
Здесь длину сливного трубопровода принимаем Lтр.с= 25м.
Из трех значений dтр.с1 dтр.с2 dтр.с3 выбираем большее dтр.с=00332м.
Определяем толщину стенки трубопровода:
где Р – давление в трубопроводе принимаем для всасывающего и сливного Р = 02 МПа а для напорного трубопровода Р = Рн = 336 1595 МПа; бВР – предел прочности на растяжение материала трубопровода принимаем трубопровод из стали Ст. 3 тогда бВР = 400 МПа; Кб – коэффициент безопасности принимаем для всасывающего и сливного трубопроводов Кб = 2 т.к. давление в них близко к нулю а для напорного трубопровода принимаем Кб = 3 т.к. считаем что у гидропривода будет ненапряженный режим работы.
Далее определяем толщину стенки трубопроводов
По внутреннему диаметру dтр.в dтр.н и dтр.с а также по толщине S трубопровода выбираем из прил. 55 сортамент труб для трубопроводов:
внутренний диаметр dтр.н = 26 мм
толщина стенки трубопровода Sв = 35 мм
внутренний диаметр dтр.в = 41 мм
толщина стенки трубопровода Sн = 2мм
внутренний диаметр dтр.с = 33 мм
толщина стенки трубопровода Sс = 15 мм
Толщина стенок всасывающего и сливного трубопроводов увеличена из условий жесткости и соответствует стандартному ряду.
Уточняем скорость движения мс рабочей жидкости в трубопроводе по формуле:
Всасывающий трубопровод
Напорный трубопровод
5 Расчет потерь давления в трубопроводе
Определяем число Рейнольдса:
Тогда коэффициент сопротивления трубопровода
Потери давления на трение по длине всасывающего трубопровода
ΔPL.B=05ρλB LTP.B(VTP.B)2dTP.B = 058900055610986241 10-3 = 5872 Па.
Потери давления в местных сопротивлениях всасывающего трубопровода
Принимаем во всасывающем трубопроводе два плавных поворота и сужение потока за счет крана на всасывающей стороне перед маслобаком. По прил. 56 принимаем: коэффициент сопротивления плавного поворота 1 = 015 коэффициент сопротивления трубопровода за счет сужения 2 = 1.
Находим сумму коэффициентов местных сопротивлений:
Σв = 1 2+2 = 015 2 + 1 = 13.
Суммарные потери давления во всасывающем трубопроводе определяем по формуле
ΔРтр.в =ΔРL.в + ΔРм.в =5872 + 5624 = 11496 Па.
Определяем число Рейнольдса
Потери давления на трение по длине трубопровода
ΔPL.н = 05ρλн Lтр.н(Vтр.н)2dтр.н = 05890003533245226 10-3 = 10879 Па.
Потери давления в местных сопротивлениях напорного трубопровода
Принимаем в напорном трубопроводе шесть плавных поворотов с коэффициентом сопротивления 1= 015 четыре поворота под прямым углом с коэффициентом сопротивления 2= 15 три тройника с коэффициентом сопротивления 3= 1 пять штуцеров с коэффициентом 4= 01.
Определяем сумму коэффициентов местных сопротивлений
Σн = 1 6 + 2 4 + 3 3 +4 5 = 0156 + 15 4+ 1 3 + 01 5 = 104.
Суммарные потери давления в напорном трубопроводе определяем по формуле
ΔРтр.н =ΔРL.н + ΔРм.н =10879 + 277796 = 386586 Па.
Потери давления на трение по длине сливного трубопровода
ΔPL.с = 05ρλс Lтр.с(Vтр.с)2dтр.с = 058900044825152233 10-3 = 34894 Па.
Потери давления в местных сопротивлениях сливного трубопровода
Принимаем в сливном трубопроводе семь плавных поворотов с коэффициентом сопротивления 1= 015 пять поворотов под прямым углом с коэффициентом сопротивления 2= 15 два тройника с коэффициентом сопротивления 3= 1 четыре штуцера с коэффициентом 4= 01.
Находим сумму коэффициентов местных сопротивлений
Σн = 1 7 + 2 5 + 3 2 +4 4 = 0157 + 15 5+ 1 2 + 01 4 = 1095.
Вычисляем суммарные потери давления в сливном трубопроводе
ΔРтр.с =ΔРL.с + ΔРм.с =34894 + 11258 = 147474 Па.
ΣΔР = ΣΔРтр + ΣΔРг.а
где ΣΔРтр- суммарные потери давления во всасывающем напорном и сливном трубопроводах: ΣΔРг.а – суммарные потери давления в гидроаппаратах (ΔРдр= 015 МПа ΔРр= 07 МПа ΔРф= 005 МПа).
ΣΔР= 11496 + 386586 + 147474 + 150000 + 700000 + 50000 =
=9545556 Па = 0955 МПа.
6 Определение потерь мощности в гидроприводе
Средние потери мощности переходящие в тепло определяем по формуле
где ΔN1 ΔN2 – потери мощности в гидроприводе когда вал вращается влево вправо; ΔN3 – и когда вал неподвижен; t1 t2 t3- время работы гидропривода когда вал вращается влево в право и неподвижен.
Определяем потери мощности
ΔN = Nпотр.н. (1 – общ.гп.)
Потребляемую насосом мощности находим по формуле
Nпотр.н.i = Qн.i Pнн
где Qн.ном = 1301 10-3 м3с; (822 лмин) – подача насоса м3с для регулируемого - расчетная подача необходимая для обеспечения заданных значений Vп.
н =. полный КПД насоса по паспортным данным.
ΣΔР= 0955 МПа суммарные потери в трубопроводе.
Мощность Вт потребляемая насосом находится по формуле
где Qн. – подача насоса м3с для регулируемого - расчетная подача необходимая для обеспечения заданных значений Vп. и nм.; Pн. - уточненное давление развиваемое насосом Па; н – полный КПД насоса по паспортным данным.
Уточненное давление насоса определяется для каждого режима c учетом потерь давления в трубопроводе ΣΔP= 0955 МПа суммарные потери в трубопроводе
Где Pr.i – давление в полости гидромотора которое определяем по формулам:
Pr. =2 Ммqм мех.м=2314169560968=1958 МПа
Pн =1958+0955=2053 МПа
Nпотр.н =1301 10-3 2053091 = 2936кВт = 29356Вт
Общий КПД рассчитываем следующим образом
общ.гп = Nпол.Nпотр.н
где Nпол.Nпотр.н – полезная мощность гидромторора
Nпол= Мм nм 2 = 169 216 2314=22925 Вт кВт
общ.гп =229252936=078;
Потери мощности в гидроприводе:
Для случая когда поворотная платформа на подвижна а рабочая жидкость от насоса проходит на слив в маслобак потери мощности определяем по формуле:
ΔN1= Qн.ном ΣΔP=130110-30955=124 кВт
Средние потери мощности составят
ΔNср=6465+12449=414 кВт
7 Расчет статистических характеристик гидропривода с машинным регулированием
Согласно принятой нами гидросхеме регулирование режима работы гидропривода будет выполняться регулируемым гидронасосом. Для этого случая уравнение статистической характеристики обс будет иметь вид
Исходными данными для расчета характеристик гидропривода с машинным регулированием являются: момент сопротивления на валу гидромотора МмН М; частота вращения гидромотора nмобс.; объемный КПД гидромотора м его рабочий объем qмсм3с; номинальное давление Pм.ном Па; подачу насоса Qн м3с; частота вращения вала nн обс;обьемный КПД он; номинальное давление развиваемое Pм.ном
В ходе расчета определяем следующие параметры:
коэффициент гидромотора
теоретическую подачу гидронасоса
объемные потери гидронасоса
ΔQн = Qн.т (1 – о.н) = 1369 10-3(1 – 095) = 6847 10-5 м3с;
расход гидромотора при номинальной частоте вращения
Qм = qм nм.ном ом = (5610-6 216)095 = 1273210-4 м3с;
объемные потери в гидромоторе
ΔQм = Qм(1 - ом) = 12732 10-4(1- 095) = 633610-5м3с;
коэффициент объемных потерь насоса ан и гидромотора ам
общий коэффициент объемных потерь
а = ан + ам = (3423 + 3183)10-12 =660610-12м5(сН).
Подставляя все полученные параметры имеем следующее уравнение статистической характеристики:
nм = 2444Uн – 000685Мм обс.
Подставляя в последнее уравнение момент на валу гидромотора Мм от 0 до 80 Нм при различных значениях параметра регулирования насоса Uн от 1 до 04 полученные значения частоты вращения nм вала гидромотора сведем в табл.4.3.
Расчетные данные частоты вращения вала гидромотора nмобс
при различных параметрах регулирования гидронасоса
Момент гидромотора Нм
По результатам расчета строим графики (рис.2.1) статистических характеристик гидропривода с регулируемым гидронасосом.
На этих же графиках определяем две рабочие точки 1 и 2 при параметрах регулирования гидронасоса Uн1 = 049 и Uн2 = 071.
Разработка технологического процесса изготовления детали (шестерни)
1 Назначение шестерни
Изготавливаемая (шестерня) предназначена для передачи крутящего момента от двигателя внутреннего сгорания к гидромотору за счет эвольвентного зацепления в приводном редукторе экскаватора САТ-330DL
2. Технические требования на изготовление шестерни
Материал заготовки – легированная сталь 40 Х ГОСТ 4543 с последующим термическим улучшением (твёрдость НВ 269-302).
Твёрдость плоскостей проверять не менее чем в двух местах на каждой из плоскостей на расстоянии не менее 20 мм от края штамповки.
Наиболее ответственные поверхности обрабатываются по 8 квалитету точности и 5-6 классу чистоты поверхности.
Для шестерни при изготовлении из проката характерна не только повышенная трудоёмкость обработки но и низкий коэффициент использования материала. Поэтому для них заготовки целесообразно получать горячей штамповкой
3 Разработка маршрута механической обработки шестерни
Операция05.Токарная.
Производится обработка на токарно-револьверном станке 1П365 за два установа.
Обрабатывается посадочное отверстие 1 за два перехода с двух позиций револьверной головки подрезаются торцы 24 и в зоне зубьев 3 снимаются фаски.
Производится чистовая обработка посадочного отверстия 1 на токарно- револьверном станке 1П365.
Операция15.Зуборезная
Производится нарезание зубьев поверхности 5. Выполняется на вертикально - зубофрезерном станке 5К324А.Заготовка устанавливается на центрирующую оправу и опирается диском на подставки. Подставки смонтированы на делительном столе обеспечивающем поворот заготовки на шаг при переходе к другому зубу.
Операция20. Шлифовальная
Производится шлифование зубьев поверхности 5. Шлифование производится на зубошлифовальном станке 586.
После изготовления проводится проверка изготовленной шестерни на соответствие её заданным расчётным размерам и допускам.
Заготовка представляет штамповку 5 класса точности. Технологический маршрут обработки отверстия 60Н7 состоит из двух операций: чернового и чистового растачивания выполняемых при двойной установке обрабатываемой детали. Базами для заготовки наружная поверхность.
Технологический маршрут обработки записываем в расчетную таблицу 3.1. Там же записываем соответствующие заготовке и каждому технологическому переходу значения элементов припуска.
Так как обработка ведется в специальном приспособлении погрешность установки в радиальном направлении (е) равна нулю. В этом случае эту величину можно не учитывать и соответствующую графу из таблицы 3.1 можно исключить. Суммарное отклонение Rz и Т характеризующие качество поверхности заготовки находим по табл. (27 стр.65.66[25]) и заносим в таблицу3.1.
Таблица3.1 Технологический маршрут обработки
ческие переходы обработки поверхнос
Расчётный припуск 2z
Расчётный размер dмм
Предельный размер мм
Предельные значения припусков мкм
Растачивание черновое
Растачивание чистовое
Минимальный припуск на черновое растачивание
где - пространственное смещение заготовки мкм
ρсм – вектор смещения мкм
ρкор – вектор коробления мкм
Величина коробления учитывается как в диаметральном так и в основном сечении заготовки:
где удельная кривизна заготовки Δ=07 мкм на 1 мм длины.
D=60мм-диаметр обрабатываемого отверстия
l=225мм-длина отверстия
Смещение отверстия в штамповке определяется по формуле:
Суммарное значение пространственных отклонений для заготовки данного типа:
Погрешность установки при черновом растачивании мкм
Где б – погрешность базирования по длине мкм;
б – погрешность закрепления заготовки мкм тогда
Таким образом минимальный припуск на черновое растачивание:
Остаточное пространственное отклонение
где Ку - коэффициент уточнения формы. После чернового растачивания (Ку = 0.06) После чистового растачивания (Ку = 0.04)
Остаточная погрешность установки при чистовом растачивании:
Минимальный припуск на чистовое растачивание:
Графу «расчетный размер dр» заполняем начиная с конечного (чертежного) размера путем последовательного вычитания расчетного минимального припуска каждого технологического перехода:
Назначаем допуски каждому переходу в соответствии с выбранным квалитетом [13]
Заготовка з=1000 мкм
Чистовое растачивание 2=40 мкм;
Черновое растачивание 1=160 мкм
Наименьшие предельные размеры вычисляем вычитанием допуска из округленного наибольшего предельного размера:
Максимальные предельные значения припусков Zпр.max определяем как разность наименьших предельных размеров:
Минимальные предельные значения припусков Zпр.min определяем как разность наибольших предельных размеров:
Проверка правильности расчетов
На остальные обрабатываемые поверхности припуски и допуски выбираем по таблицам (ГОСТ 1855-55).
Рисунок 3.1 шестерня.
Схема графического расположения припусков и допусков на обработку отверстия диаметром 60 мм
5 Расчёт режимов резания
Станок – токарно–револьверный модель 1П365.
Техническая характеристика станка:
Диаметр обрабатываемой заготовки (максимальный)- 500 мм;
Частота вращения шпинделя n=135 185 275 385 530 775 1080 обмин
Количество ступеней частоты вращения шпинделя - 12
Подачи револьверного суппорта ммоб – 009; 012; 017; 025; 035; 05; 07; 1; 135 27
Инструмент – резец подрезной с пластинами из твёрдого сплава Т15К6 по МН 592-64 [13].
Глубина резания t = 2 мм
Длина рабочего хода:
L1 + L2 =(t+2)+0=2+2=4
где L1= t+2 мм - длина подвода мм
L2=0 – отвод точение в упор мм
Подача Sо= 06 ммоб принимаем подачу принятую по паспорту станка:
Tм= 50 мин - Стойкость инструмента наладки (стр.545)[16].
инструмента в наладке. = Lрез Lр.х. = 2226=085> 07; Принимаем =1
vт=90ммин - скорость по табличным данным
k5=1 — коэффициент зависящий от обрабатываемого материала;
k6 = 15 – коэффициент зависящий от периода стойкости;
K7 = 1 – коэффициент зависящий от вида обработки
Число оборотов шпинделя:
Уточняем число оборотов
по таблице 13 6 находим ближайшее значение х m-1=12- 1=11=1264 что соответствует =112
По паспорту станка принимаем ближайшее значение n=385
Должно выполняться условие:
Nт – номинальная табличная мощность кВт;
Основное время на операцию:
Черновое растачивание отверстия диаметром =56мм
Инструмент –резец проходной отогнутый φ=90 с пластинами из твёрдого сплава Т15к6 ГОСТ 10863-73
Глубина резания t = 125 мм
Число проходов i=22=1
где L1+L2=0+2 мм – длина врезания и перебега.
Коэффициент времени резания каждого инструмента наладки
= LрезLр.х. = 225245=0918 > 07; Принимаем = 1.
K7 = 085 – коэффициент зависящий от вида обработки
По паспорту станка принимаем ближайшее значение n=530 обмин
Припуск на обработку [16] – 2а=06мм
По паспорту принимаем ближайшее стандартное значение
Определяем стойкость инструмента стр.552 [16]
Tм = 50 мин – 3 инструмента в наладке.
Скорость резания – стр. 553 [16] табл. 8.
по таблице 13 6 находим ближайшее значение х m-1=12-1=11=1264 что соответствует =112
По паспорту станка принимаем ближайшее значение n=530обмин
Снятие фаски 25×45 в зоне зубьев
По паспорту станка принимаем ближайшее значение n=385обмин.
инструмента в наладке. = Lрез Lр.х. = 4549=09> 07; Принимаем =1
k5 = 1 — коэффициент зависящий от обрабатываемого материала;
по таблице 13 6 находим ближайшее значение х m-1=12 - 1=11=1264 что соответствует =112
Чистовое растачивание отверстия диаметром =60мм
Глубина резания t = 075 мм
где L1+L2=4 мм – длина врезания и перебега.
= LрезLр.х. = 225265=084 > 07; Принимаем = 1.
По паспорту станка принимаем ближайшее значение n=530обмин.
Фрезерование зубьев.
Станок - вертикально-зубофрезерный модель 5К324А
Инструмент – фреза модуль 4 мм ГОСТ 15127-69.
Делительный диаметр d=92 мм
Принимаем подачу на зуб:
Принимаем подачу на зуб Sz=012ммзуб
Стойкость инструмента Тм=130мин.
V=35мммин.-табличная скорость
Принимаем ближайшее паспортное значение из ряда:
E=025величина приведённая в таблице
Основное время операции:
Шлифование поверхности зубьев.
Станок зубошлифовальный 586 с фасонным кругом.
Наибольшая ширина заготовки 200 мм.
Количество зубьев 10-300.
Мощность двигателя N=7 кВт.
Инструмент – круг шлифовальный для зубошлифовальных станков по ГОСТ 2424-67 D=250мм
Глубина резания t=03мм.
Vш – скорость шлифовального круга V=28мс.
V – скорость движения детали V=6ммин.
Радиальная подача Sрад=001мм
Частота вращения круга
Принимаем ближайшее паспортное значение n=1500мин-1.
Время на перемещение детали д=005 мин.
Основное время на операцию
6. Расчет нормы штучного времени
В серийном и мелкосерийном производстве нормы штучного времени определяются по формуле[26] стр. 101:
Тшт = Т0 + Тв + Тоб + Тот;
Где Т0 – основное время мин.
Тв – вспомогательное время мин.
Тв = Ту.с. + Тз.о. + Туп + Тиз;
Ту.с. – время на установку и снятие детали мин.;
Тз.о. – время на закрепление и открепление детали мин.;
Туп – время на приемы управления мин.;
Тиз – время на измерение детали мин.
Тоб – время на обслуживание рабочего места мин. Тоб = Ттех + Торг;
Здесь Ттех – время на техническое обслуживание.
- для токарных фрезерных и сверлильных операций:
- tсм – время на смену инструмента и наладку станка;
- tп – время на одну правку шлифовального круга;
- Птех – затраты на техническое обслуживание рабочего места в процентах от основного;
- Т – период стойкости при работе одним инструментом или период стойкости лимитирующего инструмента при многоинструментальной обработке мин.
Торг – время на организационное обслуживание рабочего места. Определяется в процентах от оперативного времени.
Торг = (Т0п*Порг)100;
Тот – время перерывов на отдых и личные надобности.
Процент времени на отдых (Тот) находится по приложению 5 в зависимости от процента основного времени Т0 от оперативного Топ
То=018 мин Т=50 мин
По приложению 5.1. [26] находим Ту.с. + Тз.о.
Для закрепления детали в само центрирующем патроне
Ту.с. + Тз.о.=023 мин
Время включения и выключения станка кнопкой 001 мин. Время на перемещение кареток суппорта в продольном направлении на длину 100 мм равно 004 мин тогда
Ту.п.=001+004=005 мин.
Время на измерение детали
Тв=023+005+12=148 мин.
Топ.=То+Тв=03+148=178 мин.
Техническая норма времени:
где tсм=2 - количество смен
Т – стойкость инструмента.
Время на организационное обслуживание находится в процентах от Топ. где проценты приведены в приложении 5 [26]
Время перерывов на отдых так же находится в % от Топ
Тшт =03+002+016+0012=049 мин.
То=0106 мин Т=50 мин
Топ.=То+Тв=0106+136=147 мин.
Тшт =0106+0004+0019+013=0259 мин.
То=002 мин Т=50 мин
Топ.=То+Тв=002+136=138 мин.
Тшт =002+00008+0018+012=0159 мин.
То=0045 мин Т=50 мин
Топ.=То+Тв=0045+136=1405 мин.
Тшт =0045+00018+0019+013=0196 мин
Топ.=То+Тв=0275+136=1635 мин.
Тшт =0275+0011+0021+015=0457 мин.
То=27 мин Т=130 мин.
Ту.с. + Тз.о.=026+0024=0284 мин
Где 026 - время установки на главной оправке с креплением гайкой. 0024 мин. – крепление рукояткой.
Ту.п.=002+004+006+002+002=016 мин.
Тв=0284+0024+016+012=0588 мин.
Топ.=То+Тв=261+0588=3198 мин.
Тшт =3198+004+0045+019=347 мин.
То=238 мин Т=150 мин.
Топ.=То+Тв=112+0564=1684 мин.
Где 11 – время на правку одного шлифовального круга.
Тшт =238+0012+034+029=325 мин.
7. Расчет калибр-пробки
Предельные размеры и допуски для пробки находим по ГОСТ 21401-75 “Исполнительные размеры рабочих калибров”.
Рис 3.2 Колибр пробка
Найти отклонения для отверстия номинальным диаметром Dном=60мм
Верхнее отклонение - верхнее = 40 мкм
Нижнее отклонение - нижнее = 0 мкм По СТ СЭВ 145-75 табл.1
Допуск Т=верхнее - нижнее =40-0=40 мкм
Dmax = Dном + верхнее=60+004=6004мм
Dmin = Dном + нижнее =60+0000=60000мм
Допуски и отклонения калибров принимаем по ГОСТ 24853-81 табл.1.
ДЛЯ 7 КВАЛИТЕТА НАХОДИМ:
Z= 5 мкм Y= 4 мкм HS= 6 мкм H= 6 мкм.
Р-ПРmax = Dном+ нижнее +Z +H2 =60+0+0005+00062=60008 мм
Р-ПРmin = Dном+ нижнее +Z - H2 =60+0+0005-00062=60002 мм
Проходная изношенная-
Р-ПРmin = Dmin- Y =60-0004=59996 мм
Непроходная сторона-
Р-НЕmax = Dном+верхнее +HS2 =60+004+00062=60043 мм
Р-НЕmin = Dном+верхнее - HS2 =60+004-00062=60037 мм
Расположение полей допусков калибров для контроля отверстий.
8 Назначение и конструкция станочного приспособления
Разработанное приспособление предназначено для нарезания зубьев звёздочки.
Приспособление (см. лист 190602 Д06077 ТС 10 00 СБ) состоит из основания 5 муфты 4 центрирующего пальца 3 оправки 2 центрирующего кольца 1.
К основанию 5 приспособления крепится муфта 4 восемью крепёжными болтами 68. на центрирующий палец 3 проходящий через основание 5 и муфту 4 одевается оправка 2 и центрирующее кольцо 1 вместе с звёздочкой. Крепится звёздочка прижимной планкой 7 и гайкой 9 к центрирующему пальцу 3.
9 Расчёт сил зажима при обработке деталей фрезерованием
Надёжный зажим заготовки обеспечивается при условии:
k=125-коэффициент запаса;
-момент силы трения;
-момент силы резания;
f=02 - коэффициент трения;
N=211 кВт-мощность резания;
Из условия надёжности получим выражение
Сила зажима определяется по формуле:
Диаметр крепёжного болта определим из условия:
Минимальный диаметр болта определяется по формуле:
Из конструктивных соображений принимаем d=16мм.
Расчёт себестоимости и цены модернизации рабочего оборудования экскаватора СAT-330DL
1 Технико-экономическая оценка качества спроектированного изделия
В дипломном проекте проводятся расчёты модернизации рабочего оборудования экскаватора СAT-330DL путём установки ковша с вибрирующими зубьями. Предлагаемая модернизация состоит в установке на ковш экскаватора гидравлических виброзубьев. Данная конструкция позволит разрабатывать грунты с наибольшим коэффициентом прочности.
Единичные показатели технологичности конструкций
В том числе стандартных(ГОСТ; ОСТ; СТП):
Заимствованных из других конструкций:
* – без учета деталей входящих в состав сборочных единиц и стандартных крепежных деталей.
Обобщающие показатели технологичности рассчитывают по формулам:
коэффициент сборности конструкции изделия
коэффициент стандартизации изделия
коэффициент унификации изделия
Обобщающие показатели технологичности
Структура материалоемкости изделий
Виды материалов полуфабрикатов и готовых изделий
Покупные полуфабрикаты и готовые изделия
Структура трудоемкости изделий
Расчёты приведённые в таблице 4.1 – 4.4 показывают что показатель сборности конструкции у проектного изобретения выше чем у базового показатели стандартизации унификации одинаковы материалоемкости изделий у проектного выше чем у базового трудоемкости изделий у проектного выше чем у базового.
2 Расчёт себестоимости и цены модернизации рабочего оборудования экскаватора СAT-330DL.
2.1 Покупные изделия и полуфабрикаты
Затраты по этой статье определяются по формуле:
- коэффициент учитывающий транспортно-заготовительные расходы (Кт=105-11);
n - количество групп покупных изделий и полуфабрикатов шт;
- количество покупных изделий данной группы шт;
- цена единицы покупного изделия или полуфабриката руб.
Расчет затрат сведен в таблицу 4.5.
Затраты на покупку изделий и полуфабрикатов.
Клапан предохранительный
Крепежные направляющие
Трубопровод высокого давления
Трубопровод низкого давления
2.2 Основная заработная плата производственных рабочих
Основная заработная плата производственных рабочих определяется трудоемкостью квалификацией рабочих и часовой тарифной ставкой.
п – общее количество операций по изготовлению изделия;
Зпi – часовая тарифная ставка на работы выполняемые на данной операции рубч.
Кпр - коэффициент премирования по отношению к тарифной заработной плате (14).
Расчет затрат на основную заработную плату производственных рабочих приведен в таблице 4.6.
Затраты на основную заработную плату производственных рабочих.
Среднечасовая тарифная ставка рубч
Нормативная трудоемкость ч
2.3 Дополнительная заработная плата производственных рабочих
Выплачивается за отпуск и прочее нерабочее время оплата которого предусматривается трудовым законодательством. Сумма дополнительной заработной платы приходящейся на единицу продукции LД руб. рассчитывается по формуле:
а1 = 20% - дополнительная заработная плата и премиальные выплаты.
2.4 Отчисления на социальное страхование
Отчисления на социальное страхование в себестоимости изделий рассчитывается по отношению к основной и дополнительной заработным платам производственных рабочих по установленным ставкам.
аr = 34% – отчисления во внебюджетные фонды.
2.5 Расходы на содержание и эксплуатацию оборудования
Основная цель данных затрат – поддержание в рабочем состоянии основных производственных фондов. Расходы на содержание и эксплуатацию оборудования РЭО вычисляются пропорционально основной заработной плате основных рабочих.
К цеховым расходам РЦ относятся расходы на выполнение общецеховых работ а также заработная плата цехового персонала и служащих.
Этот вид затрат относится на себестоимость пропорционально заработной плате производственных рабочих.
2.7 Расходы на подготовку производства
Расходы на подготовку производства составляют 10-20% от основной заработной платы производственных рабочих
2.8 Цеховая себестоимость
2.9 Общепроизводственные расходы
Общепроизводственные расходы представляют собой комплекс затрат связанных с управлением предприятием общехозяйственными и некоторыми другими расходами.
2.10 Производственная себестоимость
2.11 Внепроизводственные расходы.
При исчислении полной себестоимости изготовления изделия в нее включают издержки по сбыту передвижению продукции и прочие накладные расходы. Это затраты на тару упаковку транспортировку и рекламу изделия. На себестоимости изделия они относятся пропорционально производственной себестоимости.
2.12 Полная себестоимость
2.13 Прибыль нормативная
2.14 Оптовая цена предприятия
2.15 Налог на добавленную стоимость
В таблице 4.7 приведена сводная калькуляция себестоимости и оптовой цены изделия
Расчет проектной себестоимости модернизации рабочего оборудования экскаватора СAT-330DL.
Наименование статей расхода
Основная заработная плата производственных рабочих
Дополнительная заработная плата
Отчисления во внебюджетные фонды
Расходы на содержание и эксплуатацию оборудования
Расходы на подготовку производства
Цеховая себестоимость
Общепроизводственные расходы
Производственная себестоимость
Внепроизводственные расходы
Полная себестоимость
Оптовая цена предприятия
Налог на добавленную стоимость и спец налог
Расчёты приведённые в таблице 4.7. показывают что полная себестоимость изготовления рабочего оборудования равна 35603 руб. а отпускная цена равна 53161
3 Построение сетевого графика
Сетевой график представляет собой графическое изображение проекта в котором отдельные операции т. е. работы по выполнению проекта изображаются стрелками. Начало и конец стрелки обозначают соответственно начало и конец операции.
Содержание работ по проектированию стрелы экскаватора и ожидаемые сроки их выполнения приведены в таблице 4.8.
Перечень событий и работ
Оценка ожидаемости дней
Количество исполнителей Кр чел.
Эскизное проектирование
Анализ состояния вопроса
Подбор и изучение научно-технической литературы
Проведение патентных исследований
Составление и согласование с заказчиком технического задания на проектирование конструкции
Поиск существующих конструкций
Выявление возможных вариантов разработки и оценки их эффективности.
Составление принципиальной схемы
Уточнение основных исходных данных на основе выбранного варианта разработки
Составление и согласование с заказчиком технического задания
Проведение основных расчетов
Разработка систематических чертежей общего вида конструкции.
Продолжение таблицы 4.8.
Теоретическая разработка
Оптимизация параметров принципиальной схемы
Уточнение принципиальной схемы
Техническое проектирование
Утверждение эскизного проекта
Разработка и согласование технического проекта
Уточнение схемы и расчетов
Изготовление опытного образца
Технологическая и материальная подготовка производства
Запрос формуляров и разрешений на постановку материалов и полуфабрикатов
Сборка узлов механизмов и агрегатов
Проведение отладочных испытаний
Корректировка технической документации
Заводские испытания опытного образца
Проведение стендовых эксплуатационных испытаний
Предъявление образца на государственные испытания.
Обобщения выводы и предложения по теме
Определения возможности внедрения в производство результатов проведенной работы
Техническая отчетность
Составление технического отчета о выполненной работе
Корректировка сдача технической документации
Таблица 4.9. Расчет временных параметров сетевого графика
Продолжение таблицы 4.9.
На основании данных таблицы 4.8. строится сетевой график.
По построенной сетевой модели рассчитываются основные параметры графика.
Построение сетевого графика ведется на основании перечня работ подлежащих выполнению сведений о планируемой продолжительности каждой из них и численности занятых работников. На графике обозначены все рабочие внесенные в перечень с указанием номеров событий длительностей работ численности занятых работников.
Расчет графика проводится на основании построенной сетевой модели он заключается в определении ранних и поздних сроков начала и окончания работ:
полных и свободных резервов времени выполнения работ ;
резервов времени свершения события .
При этом величины определяются как время наибольшего из путей от начального события до события i а величины как разность между длительностью критического пути и времени наибольшего из путей от конечного события до события j. Критическим является наибольший из путей между начальным и конечным событием его длительность равна времени свершения конечного события (для которого ).
Для определения следует прибавить к планируемую длительность работы i - j для определения - вычесть из планируемую длительность работы i - j.
Величины резервов времени определяются по зависимостям:
Критический путь по сетевому графику (рисунок 4.1) равен 59 дней следовательно комплекс работ по проектированию и модернизации рабочего оборудования экскаватора СAT-330DL будет выполнен за 59 дней. Наибольшее количество исполнителей за период работы - 6 человек.
Безопасность жизнедеятельности
1 Анализ опасных факторов при работе на гидравлическом экскаватора CAT 330DL
Опасным производственным фактором называется такой фактор воздействие которого на работающего в определенных условиях приводит к травме или другому внезапному резкому ухудшению здоровья и трудоспособности.
Вредным производственным фактором является производственный фактор воздействие которого на работающего приводит к снижению работоспособности.
В процессе эксплуатации и обслуживания экскаватора CAT 330DL применяемый для разработки горных пород существует ряд опасных и вредных факторов анализ которых приведен в таблице 5.1.
Таблица 5.1. Анализ опасных и вредных факторов возникающих при эксплуатации и обслуживании экскаватора CAT 330DL
Наименование фактора
Носитель опасного фактора
Круг лиц на которых возможно воздействие фактора
Возможные последствия действия фактора
Средства локализации и профилактики опасных и вредных факторов
Работающие механизмы неисправное оборудование
Оперативный ремонтный обслуживающий персонал
Утомляемость расстройство слухового аппарата
Шумоизоляция периодическая проверка оборудования
Электрооборудование кабина крана
Поражение огнем и продуктами горения
Установка системы пожаротушения в рабочей зоне узлы и механизмы в искробезопасном исполнении
Продолженме таблицы 5.1
Поражение электрическим током
Поражение электрическим током электроожоги
Четкое выполнение требований ПТБ И ПТЭ и контроль исправности оборудования
Перемещающиеся вращающиеся элементы механизмов
Механизмы узлы оборудования
Весь персонал находящийся в зоне работы механизмов
Возможность наезда защемления частей тела и т.д.
Установка кожухов ограждений подача звуковых сигналов
Выпадение груза из грейфера при перегрузке
Персонал находящийся в зоне работы
Травмы и повреждения людей
Запрещение нахождения водителя в кабине автомобиля при перегрузке
Трансформаторное масло пары растворителей эмалей
Персонал работающий в зоне действия фактора
Отравление головная боль тошнота
Применение средств индивидуальной защиты вентиляция
Недостаточная освещенность рабочих мест
Осветительные приборы
Персонал работающий на площадке
Снижение трудоспособности ухудшение зрения
Принятие мер п обеспечению достаточной освещенности
2 Техника безопасности
Для безопасного ведения всех видов работ обслуживающий персонал должен строго соблюдать правила техники безопасности при эксплуатации работе техническом обслуживании и ремонте экскаватора. Несоблюдение этих правил может привести к несчастным случаям связанным с получением различных травм и потерей трудоспособности.
Обслуживающий персонал должен пройти инструктаж по технике безопасности и работать в специальной одежде соответствующей климатическим условиям.
На экскаваторе должны быть аптечка для оказания первой медицинской помощи и исправный огнетушитель.
3 Условия безопасного изготовления детали
При изготовлении деталииспользуют – различное станочное оборудование (токарные фрезерные шлифовальные сверлильные и другие станки) к которым предъявляются требования обеспечивающие их безопасную эксплуатацию.
К работе на них допускаются лица не моложе 18 лет прошедшие специальную подготовку инструктажи и имеющие классификационное удостоверение.
Запрещается работа на неисправном станочном оборудовании и стендах. Все вращающиеся механизмы и передачи имеют ограждения и кожухи а электроприводы – заземлены на общий заземляющий контур как и распределительные щиты. Около стендов и станков устанавливают деревянные решётки. Все операции по техническому обслуживанию и ремонту станочного оборудования и стендов выполняют при их полной остановке и отключении от электросети.
Во время работы на токарных станках особое внимание уделяют мерам защиты от стружки.
Для защиты от стружки на токарных станках устанавливают защитные щиты. Самое простое защитное устройство состоит из трёх узлов: стоек неподвижно укреплённых винтами на поперечном суппорте горизонтальных рычагов и рамки со смотровым стеклом из оргстекла. Рамка шарнирно соединена с рычагами. При установке или снятии детали запретный экран опускается до упора посредством рукоятки. Чтобы предупредить рассеивание стружки сзади устанавливается экран из металлической сетки. Более совершенное защитное устройство показано на рисунке 5.1. Оно состоит из кожуха 4
Рисунок 5.1 – защитный кожух к токарному станку
– щиток со стеклом; 2 – верхний щит; 3 – сетка; 4 – защитный кожух;
– спиральная пружина с осью.
шарнирно укреплённого винтами на поперечном суппорте с помощью спиральной пружины с осью 5 верхнего щита 2 и щитка 1 со стеклом. На задней части кожуха 4 укреплена металлическая сетка препятствующая разлетанию стружки. Стружка убирается специальными лопаточками или крючками а не руками. Для ограждения сверла вертикально-сверлильного станка применяют сетчатое ограждение механического действия. Для этого к суппорту шпинделя станка при помощи двух подвижных штанг свободно крепится сетчатый стакан. На заточных станках с местным освещением устанавливаются защитные экраны для предохранения глаз работающего от абразивных частиц и стружки. Значительную опасность для работающих при несоблюдении мер безопасности представляет эксплуатация абразивных кругов на шлифовальных и заточных станках. Перед установкой круги проверяются на отсутствие трещин. Крепление круга на шпинделе должно быть надёжным и не создавать в нём внутренних напряжений. Круг закрывается металлическим кожухом. Помимо кожухов на заточных станках установлены прозрачные козырьки обеспечивающие хорошую видимость места обработки и устройства для отсоса пыли (принудительная вентиляция).
В ремонтных мастерских используются стенды для удобства разборки и сборки отдельных узлов и механизмов а также их обкатки после ремонта. Все стенды прочно укрепляются на полу или устойчивых тележках а устройства для крепления агрегата или узла на стенде должно быть исправными. Для стендов имеющих устройство для поворота узла на угол в кинематике имеются червячные редукторы которые обеспечивают самоторможение и не позволяют самопроизвольно поворачиваться разбираемому или собираемому узлу. Все вращающие элементы стендов (зубчатые передачи соединительные муфты и др.) имеют защитные ограждения или кожухи а электроприводы – соединены с заземляющим контуром.
4 Пожарная безопасность
Пожарная безопасность объекта должна обеспечиваться:
системой предотвращения пожара;
системой противопожарной защиты;
организационно-техническими мероприятиями.
Системы предотвращения пожара и противопожарной защиты в совокупности должны исключать воздействие на людей опасных факторов пожара имеющих значение превышающие допустимые.
Предотвращение пожара должно достигаться:
предотвращением образования горючей среды;
предотвращением образования в горючей среде источников зажигания.
Предотвращением образования горючей среды должно обеспечиваться:
максимально возможным применением негорючих и трудногорючих веществ и материалов;
применением устройств защиты оборудования с горючими веществами от повреждений и аварий установкой отключающих устройств;
применением для горючих веществ герметичного оборудования и тары.
Предотвращение образования в горючей среде источников зажигания должно достигаться:
применением электрооборудования соответствующего взрывоопасным и пожароопасным зонам в соответствии с требованиями “Правил устройства электроустановок”;
устройством молниезащитных зданий сооружений и оборудования;
исключением возможности появления искрового разряда в горючей среде.
Требования к системе противопожарной защиты:
применение средств пожаротушения и пожарной техники;
применение автоматических установок пожарной сигнализации и пожаротушения;
устройством обеспечивающим ограничения распространения пожара;
организация своевременной эвакуации людей;
применение средств защиты людей.
Кабина управления должна быть снабжена огнетушителем. Пол кабины должен быть покрыт малотеплопроводящим материалом. Для обогрева кабин иногда используют теплоэлектрообогреватели (N=1000 Вт). Они должны быть закрыты перфорированным кожухом.
Объекты должны иметь системы пожарной безопасности направленных на предотвращение воздействия на людей опасных факторов пожара.
Вероятность возникновения пожара от электричества или другого оборудования технического изделия при их разработке и изготовлении не должна превышать значение 10-6 в год.
Необходимо при возгорании кабелей проводов и аппаратов на панелях щитов управления снять напряжение с панелей на которых возник пожар и приступить к тушению пожара не допуская перехода гоня на соседнюю панель. В этом случае применять нужно и огнетушители и распыленную воду. Хорошие результаты дает химическая пена образуясь в результате взаимодействия пеногенераторных порошков с водой.12
Ручной пенный огнетушитель типа ОП – 5 предназначен для тушения различных материалов на небольшой площади горения. При смешивании составных частей огнетушителя в результате химической реакции образуется углекислый газ который создает в баллоне давление под действием которого пена выбрасывается струей через специальное отверстие – спрыск.
Пожарная сигнализация обычно срабатывает от кнопок или приборов действующих автоматически от повышенной температуры.
5 Эргономический анализ кабины управления экскаватором.
5.1 Общие требования безопасности и эргономики к рабочему месту машиниста
Большое внимание должно уделяться нормам эргономики т.е. взаимоотношением человека с механизмом определенным с учетом физических и психологических факторов человека. Основными нормами эргономики являются параметры окружающей среды - климат уровень шума запыленность освещенность и параметры обслуживания - видимость механические колебания конструкция и форма средств обслуживания и другие факторы относящиеся к рабочему месту экскаваторщика.
Оператору следует обеспечить соответствующую трудовой деятельности физиологически рациональную рабочую позу по отношению к средствам контроля и отображения информации. При этом допустим поворот головы в горизонтальной плоскости не более 45 а в вертикальной – не более 30 градусов.
Понятие "климат" для условий работы определяются в основном степенью излучений температурой влажностью и скоростью движения воздуха. Для нормальной жизнедеятельности человека важно чтобы температура его тела была около 37 С а тепловой баланс тела выравнивался за определенный промежуток времени т.е. восприятие тепла должно быть таким как и отдача тепла в окружающую среду. В большой степени на теплообмен влияет климат который является благоприятным тогда когда для обеспечения теплового баланса не требуется применение специальных регулирующих систем и неблагоприятными если без применения систем не может наступить равновесие между восприятием и отдачей тепла.
Шум состоит из звуков с большим количеством составляющих частот и представляет собой периодические колебания среды. Оценивается по уровню звука и громкости. Уровень шума измеряется в децибелах и является мерой фактических колебаний воздушного давления. Для промышленных территорий он не должен превышать 50-70 дБ.
Освещение рабочей зоны должно характеризоваться освещенностью не менее 100лк при степени равномерности освещения не менее 13. Понятие "видимость" характеризует расстояние на которое можно четко видеть человеку с нормальным зрением. Видимость из кабины экскаватора определяется расположением сидения экскаваторщика конструкцией окон кабины и ее расположением на экскаваторе.
Конструкция кабины и ее расположение устройство кресла оператора и органов управления должны обеспечивать оператору возможность свободного обзора за рабочим органом экскаватора при любом его расположении.
Сиденье кресла оператора устанавливается на высоте 400-500 мм над уровнем пола кабины. Высота стенки кресла 240-260 мм кресло имеет мягкое сиденье стенку и подлокотники и снабжается устройством для регулирования положения сиденья от среднего положения (±50 мм) в вертикальной и горизонтальной плоскостях. Спинка кресла должна иметь регулируемый угол наклона.
Размещение оборудования внутри кабины управления проводится с учетом требований ГОСТ 12.2.032 - 78.
Рис 5.2 Обзорность кабины.
Высота кабины от пола до любой выступающей точки на потолке должна быть не менее 1800 мм ширина пола 1100 мм длина пола 1400 мм.
Распределение функций между человеком и машиной следует определять степенью автоматизации исполнительных операций при управлении и контроле состояния механизмов.
Схемы автоматизированного управления экскаватором должны предусматривать полную или частичную автоматическую коррекцию технологических операций процессов копания (черпания) перемещения стрелы и ковша. Должны быть предусмотрены системы регулирования нагрузок в механизмах ограничения координат перемещения ковша блокировочных устройств устройств защиты дистанционного контроля (по требованию заказчика) диагностирования состояния оборудования и счетчик количества загруженных транспортных средств.
Обзор и видимость объектов преимущественного и периодического наблюдений должны быть обеспечены из области расположения точки зрения (ОРТЗ) с учетом возможных изменений рабочей позы машиниста. Оценку обзорности с рабочего места машиниста проводят по коэффициенту обзорности (КО) который должен быть не менее 0605.
На участке лобового остекления не должно быть визуальных помех в направлении нормальной линии взгляда машиниста сидящего в рабочей позе.
Средства отображения информации (СОИ) должны обеспечивать получение и анализ данных о состоянии оборудования механизмов и некоторых технологических параметров с применением по возможности микропроцессорной техники.
Лицевые поверхности СОИ следует располагать в плоскостях перпендикулярных к линии взгляда машиниста сидящего в кресле. Допускается отклонение плоскостей до 45°.
В кабине должно быть предусмотрено место для средств связи с участниками совместной работы в пределах досягаемости с рабочего места машиниста.
Основные и аварийные органы управления (ОУ) должны быть расположены в зоне комфорта вспомогательные — в пределах зон досягаемости.
ПУ для работы машиниста в положении сидя должны иметь пространство для ног со следующими размерами по ГОСТ 23000: по высоте не менее 600 мм по глубине — не менее 400 мм на уровне колен и не менее 600 мм на уровне пола по ширине — не менее 500 мм. При отсутствии ножных командных аппаратов следует предусмотреть подставку для ног шириной не менее 420 мм глубиной —не менее 345 мм и углом наклона 10° — 15°.
Кресло должно создавать условия для поддержания корпуса человека в физиологически рациональном положении в том числе за счет профилирования спинки и сиденья а также обеспечивать условия для отдыха.
Факторы трудового процесса при управлении экскаватором:
При организации рабочего места машиниста следует учитывать: внешняя механическая работа рабочая поза число объектов преимущественного наблюдения длительность сосредоточенного наблюдения от времени смены число информационных сигналов монотонность и темп работы.
Кабина должна быть оборудована средствами или устройствами:
) для предотвращения запотевания и обмерзания стекла;
) для защиты глаз машиниста от прямых солнечных лучей (солнцезащитные козырьки тонированные стекла и др.);
) для очистки наружной поверхности лобового стекла от загрязнения и атмосферных осадков обеспечивающими рациональные зоны очистки;
) для установления регулирования и поддержания комфортных микроклиматических условий;
) для аварийного покидания кабины.
Для подъема на рабочее место машиниста на экскаваторе должна быть установлена безопасная лестница с высотой перил от поверхности ступени 850—950 мм.
Дверной проем должен иметь высоту не менее 1900 мм ширину не менее 650 мм (для исполнения ХЛ — не менее 750 мм) с учетом уплотнения. Запорное устройство и уплотнение должны обеспечивать герметичность и безотказное открывание и закрывание двери.
Содержание аэрозолей фиброгенного действия в воздухе на постоянном рабочем месте машиниста не должно превышать предельно допустимых концентраций (ГОСТ 12.1.005-ВВ ССБТ).
5.5 Температура относительная
Температура относительная. влажность и скорость движения воздуха в кабине управления должны соответствовать для категорий работ средней тяжести Па и соответствовать значениям указанным в табл. 5.
Температура воздуха "С
Относительная влажность воздуха %
Скорость движения воздуха мс
Холодный и переходный периоды
Примечание. Вертикальный и горизонтальный перепад температур не должен превышать 4°С.
В районах с повышенной относительной влажностью наружного воздуха допускается для теплого периода года относительная влажность в кабине на 10 % выше установленной в табл. 5.
Температура металлических поверхностей стен внутри кабины на высоте не более 05 мм не должна превышать 35 °С.
Санитарно-бытовые требования
В кабине должны быть предусмотрены места для хранения инструмента документации спецодежды аптечки и термоса а также емкость для питьевой воды и кружка.
5.6 Методы контроля эргономических требований
Внешнюю механическую работу машиниста (А) кДж по управлению экскаватором с помощью ручных и ножных ОУ рассчитывают по формуле
где Ft — среднее усилие по перемещению -го ОУ Н;
— среднее количество переключений -го ОУ за 8-часовую смену;
— среднее перемещение -го ОУ за одно переключение м;
п — количество основных ОУ.
Удобство рабочей позы оценивают по величине и длительности отклонения корпуса и конечностей от нормированного положения.
Длительность сосредоточенного наблюдения определяют как отношение суммарного времени затрачиваемого на копание и выгрузку к продолжительности смены.
Число информационных сигналов определяют путем суммирования поступающих к машинисту единичных сигналов. Информационным сигналом считают любую информацию получаемую машинистом посредством органов чувств требующую выполнения ответных действий.
Монотонность работы машиниста оценивают по числу приемов за один цикл работы экскаватора и по длительности циклов. За прием принимают единичные элементы цикла например черпание поворот выгрузка и др. Длительность цикла определяют секундомером.
Темп работы определяют числом переключений ОУ за 1 ч. За единичное переключение принимают действие выполненное в течение не менее 025 с т. е. за время ответной реакции человека на управляющее действие. Количество переключений командных аппаратов определяют путем осциллографирования значений задающих напряжений или визуально. Количество переключений остальных ОУ определяют визуально. За число переключений ОУ принимают суммарное количество переключений всех ОУ.
Измерение температуры и относительной влажности воздуха в кабине машиниста проводят на высоте 15 м (на уровне головы и около стенки кабины) и 015 м от пола при работе экскаватора в течение трех рабочих дней (в период с 12 до 15 ч).
Измерение скорости движения воздуха в кабине проводят на уровне головы машиниста.
Измерения температуры скорости движения относительной влажности воздуха следует проводить в соответствии с ГОСТ 12.2.106.
Оценку содержания аэрозолей фиброгенного действия (пыли) в кабине машиниста проводят при закрытых окнах и дверях при работающих системах отопления или кондиционирования.
Содержание пыли определяют в зоне дыхания машиниста.
Отбор проб воздуха проводят при цикличной работе экскаватора и во время технологических перерывов продолжительностью не более 10 мин.
Воздухоприемное отверстие прибора или аллонжа с фильтром располагают так чтобы плоскость всасывания имела угол наклона 70°—90° к направлению движения потока запыленного воздуха.
6 Освещения строительных площадок
Для электрического освещения строительных площадок и участков следует применять типовые стационарные и передвижные инвентарные осветительные установки.
Передвижные инвентарные осветительные установки должны размещаться на строительной площадке в местах производства работ в зоне транспортных путей и др.
Строительные машины должны быть оборудованы осветительными установками наружного освещения.
В тех случаях когда строительные машины не поставляются комплектно с осветительным оборудованием для наружного освещения при проектировании электрического освещения должны быть предусмотрены установки наружного освещения монтируемые на корпусах машин.
Электрическое освещение строительных площадок и участков подразделяется на рабочее аварийное эвакуационное и охранное.
Рабочее освещение должно быть предусмотрено для всех строительных площадок и участков где работы выполняются в ночное время и сумеречное время суток и осуществляется установками общего освещения (равномерного или локализованного) и комбинированного (к общему добавляется местное).
Общее равномерное освещение следует применять если нормируемая величина освещенности не превышает 2 лк. В остальных случаях в дополнение к общему равномерному должно предусматриваться общее локализованное освещение или местное освещение.
Для общего равномерного освещения строительных площадок должны применяться световые приборы:
светильники с ЛН при ширине строительной площадки до 20 м;
светильники с лампами типа ДРЛ и типа НЛВД — при ширине площадки от 20 до 150 м;
прожекторы с ЛН и лампами ДРИ — при ширине площадок от 150 до 300 м;
светильники и прожекторы с лампами ДКсТ имеющие коэффициент усиления силы света не менее 10 — при ширине площадки свыше 300 м.
Для освещения мест производства строительных и монтажных работ внутри здания должны применяться светильники с лампами накаливания общего назначения.
Для общего локализованного освещения при расположении светильников на расстоянии 15 м и менее от мест производства работ должны применяться светильники с лампами типов ДРЛ и НЛВД а также прожекторы с лампами типов ЛН и ДРЛ.
Светильники общего локализованного освещения устанавливаются на зданиях конструкциях и мачтах общего равномерного освещения. Установка осветительных устройств на сгораемых кровлях (покрытиях) зданий запрещается.
6.2 Нормы освещенности.
Для строительных площадок и участков работ необходимо предусматривать общее равномерное освещение. При этом освещенность должна быть не менее 2 лк независимо от применяемых источников света за исключением авто и жд дорог освещенность которых должна быть не менее указанной в табл. 5.1.
Для участков работ где нормируемые уровни освещенности должны быть более 2 лк в дополнение к общему равномерному освещению следует предусматривать общее локализованное освещение.
Для тех участков на которых возможно только временное пребывание людей уровни освещенности должны быть снижены до 05 лк.
Участки строительных площадок и работ
Наименьшая освещенность лк
Уровень поверхности на которой нормируется освещенность
Автомобильные дороги на строительной площадке
На уровне проезжей части
Железнодорожные пути на строительных площадках
На поверхности головки рельсов
6.3 Освещенность кабины и зоны работ
Освещенность пульта управления измеряют при работе экскаватора при включенном освещении кабины. Светочувствительный элемент устанавливают на рабочую поверхность пульта управления и на поверхность стола.
Освещенность зоны объекта различения измеряют на высоте 08 м от уровня забоя в плоскости перпендикулярной к линии взгляда машиниста.
Средняя освещенность зоны объекта различения определяется как среднеарифметическое значений освешенностей точек расположенных вдоль проекции оси стрелы на высоте 08 м от уровня забоя в плоскости перпендикулярной к линии взгляда машиниста. Измерения проводят при шаге 1—5 м в зависимости от типа экскаватора количество точек измерения должно быть не менее пяти.
Освещенность зоны под стрелой в крайней точке черпания определяют как среднеарифметическое значений освещенностей в точках пересечения наибольшего радиуса черпания с продолжением линии правого левого башмака (гусеницы) и проекции оси стрелы соответственно на высоте 08 м от уровня забоя в плоскости перпендикулярной к линии взгляда.
Измерения освещенности проводят в темное время суток при отношении значений естественной и искусственной освещенностей не более 01.
Освещенность на постоянном рабочем месте и поверхности забоя при всех включенных осветительных приборах должна соответствовать следующим значениям:
пульт управления при работе экскаватора . . 20
зона объекта различения 75
зона под стрелой в крайней точке черпания 10
Одним из важнейших показателей эргономичности рабочего места (сиденье) водителя (оператора) на самоходных гусеничных строительно-дорожные и землеройно-транспортные машинах является уровень вибрации.
Вибрационными характеристиками на постоянном рабочем месте машиниста экскаватора являются:
корректированные значения виброускорения в диапазоне частот 14—90 Гц (интегральный метод) или среднеквадратические значения виброскорости или виброускорения (или их логарифмические уровни) в октавных или 13 – октавных полосах частот (спектральный метод) на сиденье машиниста;
корректированные значения виброускорения в диапазоне частот 56—1410 Гц или среднеквадратические значения виброскорости или виброускорения в октавных полосах частот на рукоятках управления.
Допустимые корректированные значения виброускорения не должны превышать значений приведенных в табл. 5.2 (ГОСТ 12.1.012-90ССБТ).
Допустимые корректированные значения виброускорения мс2
на сиденье машиниста в направлении х у z*
на рукоятках управления в направлении движения руки
* Технически достижимая вибрационная характеристика должна быть не более 054 мс2.
7.2 Методы измерения вибрации на рабочих местах самоходных гусеничных строительно-дорожных машин
Измерение вибрации на рабочем месте оператора обусловлено неровностью микропрофиля поверхности по которой осуществляется движение воздействиями на рабочий орган во время выполнения технологических операций и возмущениями от силовой установки и трансмиссии.
Параметры вибрации следует измерять виброизмерительной аппаратурой обеспечивающей непосредственное получение средних квадратических значений параметров вибрации в полосах частот или дозы вибрации.
Участок для выполнения транспортных операций должен иметь бетонное или асфальтовое покрытие без видимых дефектов и уклонов чтобы обеспечить движение машины в прямолинейном направлении с постоянной скоростью на расстоянии не менее 300 м.
К испытаниям допускаются машины соответствующие стандартам и (или) техническим условиям прошедшие обкатку и техническое обслуживание в соответствии с инструкцией предприятия-изготовителя.
Баки для топлива должны быть наполнены не менее чем на 50 %.
Виброизмерительную аппаратуру следует установить непосредственно на обследуемой машине. Расположение и установка аппаратуры не должны создавать неудобств водителю изменять зоны досягаемости к рычагам управления и препятствовать их перемещению.
Установка виброизмерительной аппаратуры не должна вносить каких-либо ограничений в режим работы машины (скорость движения характер выполнения операций и т. п.).
Виброизмерительные преобразователи жестко укрепляют на металлическом диске диаметром (250+50) мм и толщиной 4 мм. При измерении вибрации диск устанавливают между водителем и подушкой сиденья. Соприкасание диска с жесткими элементами конструкции сиденья не допускается. Резонансная частота которую обеспечивают элементы крепления виброизмерительных преобразователей должна быть не менее 200 Гц.
При регулируемых сиденьях сиденье должно быть отрегулировано в соответствии с ростом и массой водителя (рекомендуемая масса водителя при испытаниях (80+5) кг).
Измерения общей вибрации проводят при выполнении конкретных технологических операций соответствующих реальным условиям эксплуатации машины.
Вибрацию измеряют в трех взаимно перпендикулярных направлениях: вертикальном (ось Z— перпендикулярная к опорной поверхности) продольном (ось х —совпадает с осью движения машины) поперечном (ось у — перпендикулярная к плоскости образованной вертикальной и продольной осями).
Скорость выполнения конкретных технологических операций при измерении вибрации должна соответствовать скорости обеспечивающей максимальную производительность машины для данного режима.
Время измерения вибрации не должно быть менее 30 с.
Время интегрирования не менее 10 с.
Число измерений п устанавливают в зависимости от разброса измеренных значений вибрационного параметра. Исходное число измерений на рабочем месте в каждом направлении должно быть не менее трех.
Общее число необходимых измерений п (п > 3) устанавливают из условия
где W(п) — безразмерная функция (зависимость W(п) приведена в таблице); и — безразмерные параметры вибрации нормированные на значение вибрационного параметра полученное из первого измерения;
В случае спектрального анализа и — значения вибрационного параметра полученные в результате -го и первого измерений и взятые в той полосе частот в которой по первым трем измерениям получается максимальный разброс вибрационного параметра.
В случае интегральной оценки - корректированное значение контролируемого параметра в результате -го измерения.
Пределы погрешности измерения среднего значения вибрационного параметра за рабочую смену не должны быть более ±3 дБ с вероятностью 095.
7.3 Анализ результатов испытаний
При спектральном анализе в качестве результатов измерения принимают средние квадратические значения параметра вибрации в октавных или третьоктавных полосах частот определяемые по п измерениям спектров.
где— значение вибрационного параметра в -й октавной полосе при -м измерении.
При интегральной оценке вибрации в качестве результата измерения принимают значение Сэкв по данным п измерений.
Загрязнение атмосферы при работе экскаваторов происходит отработавшими газами машин летучими соединениями вяжущих материалов растворителей а также пылью тонкодисперсных грунтов каменных материалов.
Основную массу загрязняющих воздух веществ составляют отработавшие газы. В настоящее время в отработавших газах двигателей внутреннего сгорания обнаружено около 1200 компонентов из которых расшифровано не более 200. Токсичность отработавших газов дизельных двигателей а именно они используются на погрузчиках обуславливается главным образом содержанием в них окислов азота и сажи.
Объем отработавших газов и содержание в них вредных веществ в основном зависят от количества потребляемого топлива и технического состояния двигателя главным образом системы питания. Количество воздуха потребляемое двигателем и соответственно объем отработавших газов составляет в среднем 24 кг на 1 кг топлива. Полностью исправные экскаваторы расходуют меньше на 40% по сравнению со среднестатистическими данными топлива а значит и меньше загрязняют воздух.
Дымность отработавших газов дизельных двигателей экскаваторов определяется в соответствии с требованиями ГОСТ 23.1-441 – 76 и не должны превышать 40% в режиме свободного ускорения.
При работе с частой сменой нагрузочных режимов работы двигателя тоскичность дизелей увеличивается причем как при снижении рабочей нагрузки так и при её повышении. Установлено что минимальную удельную токсичность отработавших газов имеют дизельные двигатели при 60-70% рабочей нагрузке. Исходя из этого можно определять оптимальный режим работы машины при выполнении земляных работ.
При сгорании топлива атмосфера загрязняется не только токсичными компонентами выхлопных газов. Происходит существенной изменение воздушной среды за счет потребления большого количества кислорода и поглощает часть выделяющегося с земной поверхности тепла и возвращает его по принципу стеклянной крышки назад вызывая потепление климата.
При работе экскаваторов образование пыли обуславливают недостаточная влажность перегружаемых грунтов наличие в них дисперсных пылеватых и глинистых частиц а также ветровые воздействия. Для исключения загрязнения воздуха пылью превышающего предельно допустимые нормы необходимо проводить мероприятия по пылеподавлению и снижению пылимости.
При эксплуатации экскаваторов для снижения загрязнения атмосферы необходимы проведения следующих мероприятий:
- совершенствование (модернизация систем питания увеличение полноты сгорания топлива; ужесточение технологических допусков при изготовлении деталей формирующих камеру сгорания систему подачи топлива улучшение конструкции поршневых колец использование микропроцессорного управления;
- повышение качества моторных топлив. Отказ от использования тетраэтилсвинца в бензинах снижение содержания серы в дизельном топливе ароматических углеводородов;
- рециркуляция отработавших газов;
- нейтрализация отработавших газов фильтрация твердых частиц;
- поддержание технического состояния (теплового режима регулировок) в пределах допусков заводов-изготовителей;
- использование новых рабочих процессов и видов энергоресурсов (природный газ синтез-газ водород спирты электропривод).
9 Инструкция по безопасной эксплуатации CAT 330 DL
9.1 Техника безопасности при эксплуатации экскаватора
Перед началом земляных работ должны быть получены сведения об отсутствии подземных коммуникаций и сооружений. При обнаружении в земле кабеля трубопроводов и других подземных коммуникаций и сооружений работа должна быть немедленно приостановлена. Продолжение работ в зоне подземных коммуникаций и сооружений необходимо проводить в присутствии представителя соответствующей организации.
В вечернее и ночное время экскаватор забой место разгрузки грунта и подъездные пути должны быть хорошо освещены. Необходимые для работы инвентарь и инструмент должны находиться в инструментальном ящике. В населенных пунктах забой или участок где работает экскаватор должны быть огорожены щитами с предупредительными надписями.
Перед началом работы обслуживающий персонал должен получить точные указания о порядке выполнения задания и соблюдении необходимых мер безопасности. Работать следует только на исправном экскаваторе заправленном топливом смазочной рабочей и охлаждающей жидкостями. После заправки необходимо удалить случайно разлитую жидкость. Перед пуском дизеля рычаги управления должны быть установлены в нейтральное положение. Перед началом работы машинист должен дать предупреждение звуковым сигналом.
Работающий экскаватор должен стоять на ровном месте. При работе следует стремиться к плавному выполнению всех операций. Во время работы пребывание посторонних лиц на экскаваторе и в радиусе 15м от него не разрешается.
Категорически запрещается:
осматривать смазывать регулировать или ремонтировать механизмы экскаватора при работающем дизеле;
установка сменных видов рабочего оборудования и рабочих органов не предусмотренных заводом-изготовителем для данной модели экскаватора.
перевозка пассажиров.
обслуживать гидросистему экскаватора при рабочем оборудовании не опущенном на землю и гидросистему находящуюся под давлением;
хранить на экскаваторе легковоспламеняющиеся вещества (бензин керосин и др.);
оставлять без присмотра экскаватор с работающим двигателем;
обслуживающему персоналу находиться у подошвы забоя во избежание несчастных случаев которые могут быть вызваны обрушением грунта;
устанавливать экскаватор и транспортные средства на призме обрушения;
подавать на экскаватор и снимать с него какие-либо материалы или инструмент во время работы;
оставлять ковш на весу во время осмотра механизмов;
работать на склонах более 5°;
выполнять работы не соответствующие техническим характеристикам экскаватора;
работать на режимах превышающих допускаемые.
при разработке высокого забоя следует удалять с его верхней части крупные куски грунта так как его обрушение может повредить экскаватор и вызвать несчастный случай. Запрещается работать в забое имеющем «козырек» (нависающий в верхней части забоя грунт).
при копании ниже уровня стоянки во избежание обрушения экскаватора необходимо определять возможное приближение зоны забоя к опорному контуру машины учитывая состояние грунта (угол естественного откоса вязкость и др.).
При погрузке грунта в автомобильный транспорт категорически запрещается перемещать ковш экскаватора над его кабиной. При загрузке транспорта не имеющего над кабиной предохранительного козырька водитель должен находиться на безопасном расстоянии от экскаватора.
9.2 Техника безопасности при передвижении экскаватора
При передвижении экскаватора стрела должна быть установлена вдоль оси движения а ковш находиться на высоте не более 1 м от земли. Передвижение экскаватора с наполненным ковшом запрещается. При передвижении экскаватора ведущие колеса пневмоколесного хода должны находиться сзади. Категорически запрещается во время передвижения экскаватора входить на него или сходить с него.
При остановке экскаватора на уклоне необходимо принять меры исключающие его самопроизвольное передвижение (опустить ковш на землю при необходимости подложить под колеса упоры и др.).
В зимнее время при передвижении по скользкой дороге должна быть установлена зимняя резина.
Передвижение экскаватора через железнодорожные переезды и по искусственным сооружениям (мостам дамбам) допускается только после получения специального разрешения. Передвижение экскаватора под линиями действующих высоковольтных электропередач допускается тогда когда расстояние по вертикали между верхней точкой экскаватора и ближайшим к ней проводом электропередачи составляет: при напряжении линии электропередачи до 1 кВ — 1 м; при 1 — 20 кВ — 2 м; при 21—100 кВ — 3 м; при 101—220 кВ — 4 м; при 221—330 кВ — 5 м; при 331-500 кВ — б м.
9.3 Меры безопасности при техническом обслуживании и текущем ремонте экскаватора
Обслуживание и ремонт экскаватора должны проводиться на ровной
специально оборудованной площадке исключающей возможность загрязнения окружающей среды свободной от ненужных предметов или в специальном помещении.
На экскаваторе не должны находиться посторонние лица не участвующие в проведении работ и не обученные должным образом.
Перед обслуживанием экскаватора убедитесь что двигатель выключен ковш опущен рычаги управления находятся в нейтральном положении включен стояночный тормоз отключено электрооборудование. Заблокируйте колеса чтобы предупредить непроизвольное движение машины.
Запускать двигатель можно лишь в случаях специально оговоренных в руководствах по обслуживанию и ремонту экскаватора и двигателя строго выполняя изложенные в них указания. Проверку и регулировку механизмов при работающем двигателе следует проводить вдвоем при этом в кабине должен находиться обученный работник задачей которого является обеспечение безопасности механика выполняющего проверку или регулировку.
На пульте управления укрепляют табличку с надписью: «Двигатель не пускать — работают люди».
Обслуживание аккумуляторных батарей должно обязательно производиться в перчатках и в соответствующей спецодежде. Для нейтрализации кислоты попавшей на одежду следует применять нашатырный спирт а на кожу рук — воду с добавлением небольшого количества соды. Необходимо помнить что во избежание несчастного случая при смешивании кислоты с водой нужно наливать кислоту в воду а не наоборот.
Не допускается перемыкание металлическим предметом разнополярных выводов аккумулятора так как это может вызвать короткое замыкание.
Перед ремонтом трубопроводов с применением сварки их необходимо предварительно очистить и промыть. Место сварки следует обжечь горелкой. Исправление сваркой одного и того же места допускают не более 2 раз. При дальнейшем появлении дефектов трубопровод заменяют.
При ремонте и обслуживании экскаватора используйте только рекомендуемые заводом-изготовителем детали и материалы запасные части заводского производства либо изготовленные самостоятельно с разрешения завода-изготовителя. Нарушение этих правил связано с риском для безопасности персонала технического состояния экскаватора и его надежности.
Неправильное пользование домкратом может быть опасным. Домкраты должны быть грузоподъемностью не менее 5 т. и абсолютно исправны. Под экскаватором устанавливайте домкраты только в специально предназначенных местах. Перед началом подъема экскаватора убедитесь в том что домкрат стоит устойчиво заблокируйте колеса которые не будут подниматься. При поддомкрачивании экскаватора двигатель не должен работать.
Нельзя проводить никаких работ и даже кратковременных инспекций под экскаватором поднятом на домкратах или с помощью рабочего оборудования. В этих случаях экскаватор должен быть установлен на надежные опоры.
При необходимости проведения электросварки непосредственно на экскаваторе подключите заземляющий кабель возможно ближе к месту сварки таким образом чтобы сварочный ток не проходил через подшипники или через монтажные опоры узлов (при прохождении тока эти детали будут повреждены). Двигатель экскаватора должен быть остановлен. Сварку элементов гидросистемы (трубопроводы гидробак и т.п.) производите только после их тщательной очистки от масла.
Перед началом обслуживания гидросистемы опустите рабочее оборудование на землю таким образом чтобы не могло произойти непроизвольное движение экскаватора и рабочего органа снимите давление в системе путем многократного включения при неработающем двигателе всех рычагов управления. Соблюдайте осторожность при разборке соединений гидросистемы так как если давление в системе снято не полностью может брызнуть фонтан масла. Примите меры для предотвращения утечек рабочей жидкости ослабьте соединения затем убедившись в безопасности полностью разъедините детали. Для сбора масла сливающегося из отсоединенных деталей используйте специальный поддон.
Не находитесь вблизи трубопроводов высокого давления при испытаниях и пробном пуске гидропривода после ремонта.
Не ищите течи в гидросистеме на ощупь. Из находящейся под давлением гидравлической системы масло может вытекать через мелкие отверстия почти невидимыми струйками обладающими достаточной силой чтобы пробить кожу.
Соблюдайте осторожность при разборке соединений пневмосистемы.
Предварительно убедитесь что в системе отсутствует давление.
Спускные штуцера пневмосистемы нельзя отворачивать более чем на два оборота так как давление воздуха может вырвать штуцер и нанести травму.
Соблюдайте особую осторожность при обслуживании аккумуляторных батарей. Не курите и не пользуйтесь открытым огнем не допускайте образования искр вблизи батареи - это может привести к пожару или взрыву т.к. аккумуляторы выделяют легковоспламеняющиеся газы.
Чтобы избежать возникновения искр вблизи батареи провод ведущий к "массе" всегда подсоединяйте последним а отсоединяйте первым. Не допускайте чтобы какой-нибудь металлический предмет или соединительный провод одновременно прикасался бы к положительному полюсу батареи и к другой металлической детали экскаватора. При таком касании искра может вызвать взрыв. Чтобы определить степень разряженности аккумуляторов пользуйтесь вольтметром (нагрузочной вилкой) или ареометром. Перед подключением или отключением аккумуляторов убедитесь в том что включатель "массы" отключен.
Постояннно следите за состоянием изоляции и надежностью крепления
электрических проводов. Искрение в местах повреждения изоляции и ослабление крепления может привести к пожару.
В случае возгорания электропроводки немедленно отключите "массу" аккумулятора!
Немедленно устраняйте все обнаруженные течи топлива и масла. Насухо протрите все загрязненные места на экскаваторе.
Никогда не открывайте горловину топливного бака и не заливайте топливо в бак при работающем двигателе. Не курите обслуживая топливную систему. В холодное время года не пользуйтесь открытым огнем для прогрева топливо проводов и поддона дизеля. Пары топлива опасны искры или открытое пламя могут привести к их взрыву или пожару.
Следите чтобы во время работы дизеля вблизи выпускного коллектора и глушителя не было легковоспламеняющихся материалов.
Используйте только рекомендованные сорта топлива. Никогда не смешивайте дизельное топливо с бензином спиртом и т.д. - это может привести к пожару или взрыву.
Перед обслуживанием тормозов заблокируйте колеса чтобы предотвратить непроизвольное передвижение экскаватора.
Запрещается эксплуатировать экскаватор с неисправным стояночным тормозом. До устранения этой неисправности поставьте экскаватор на стоянку на ровной площадке и заблокируйте колеса чтобы предотвратить непроизвольное движение машины.
9.4 Действия в экстремальных ситуациях
При возникновении пожара опустите рабочее оборудование на землю остановите двигатель выключением подачи топлива отключите "массу" аккумулятора и немедленно покиньте экскаватор.
При пожаре горящее топливо и масла нельзя тушить водой. Следует применять огнетушитель забрасывать пламя землей или песком. Нельзя подходить к открытому огню в промасленной одежде.
При опрокидывании экскаватора немедленно покиньте его через лобовое стекло или через боковые или задний проемы выдавив стекло.
9.5 Техника безопасности при монтаже и демонтаже экскаватора
Площадка для разборки и сборки экскаватора должна быть освобождена от посторонних предметов и выровнена. Подъемные средства и приспособления применяемые при разборке и сборке экскаватора следует предварительно осмотреть и испытать. Тали и домкраты нужно прочно установить и закрепить. При осмотре цепей и строп грузоподъемных приспособлений следует тщательно проверять места сварки цепей и места сращивания и крепления канатов. Если обнаружено превышающее нормы количество оборванных проволочек каната его необходимо заменить.
В процессе опускания на площадку грузоподъемными средствами узлов и деталей экскаватора запрещается устанавливать под них подкладки.
10 Выводы по разделу
В данном разделе рассмотрена техника безопасности при транспортировании эксплуатации и ремонте экскаватора. Произведён анализ эргономичности кабины управления и уделено внимание вопросам освещения вибрации пожарной безопасности и акустики.
Цель данного раздела - обеспечить безопасность строительных работ рабочий процесс которых выполняется при помощи САТ 330 DL а также свести к минимуму вероятность любых возможных опасностей для жизни и здоровья обслуживающего персонала.
В данном дипломном проекте была произведена модернизация рабочего оборудования экскаватора САТ 330 DL.
В общей части дипломного проекта на основе анализа приведенных материалов предложена смешанное рабочее оборудование с ковшом активного действия. Выполнены необходимые расчеты доказывающие работоспособность и эффективность предлагаемой конструкции.
Расчеты гидропривода представленные в специальной части подтвердили правильность выбора управляющих устройств. Проведен расчет элементов а также статистических характеристик гидропривода с машинным регулированием.
Разработка техпроцесса изготовления детали шестерни отразила все вопросы связанные с выбором заготовки определения типа производства в раздел проведены расчёты контрольного инструмента и приспособления.
В экономической части проекта были проведены расчёты технико-экономической оценки качества спроектированного изделия полной себестоимости и отпускной цены энергосберегающей системы. Расчёты показывают что полная себестоимость модернизации рабочего оборудования экскаватора СAT-330DL равна 302327 руб. а отпускная цена равна 42808.64руб.
Список используемой литературы.
Строительные машины и средства малой механизации” Автор: Д. П. Волков Москва. 2002г. 240 с.
Технология и механизация”: Автор: Б.Ф Белецкий Ростов – на – дону Феникс” 2003г. 360с.
Ремонт дорожных машин” Ткаченко В.Ф.– М.: Транспорт 1981. – 237с
. Ерейский А.В. Суражева В.С. Исследование энергонакопительного торможения механизма поворота промышленного робота Интеллектуальный резерв университета - решению проблем Сев.-Кавк. региона : материалы 48-й науч.-техн. конф. студ. и асп. ЮРГТУ Юж.-Рос. гос. техн. ун-т (НПИ). – Новочеркасск: ЮРГТУ 2000. - С. 36-37
Джента Дж. Накопление кинетической энергии Пер. с англ. Под ред. Г.Г.Портнова. М.: Мир 1988. – 430 с. ил.
Болотин Л.М. Корендясев А.И. Саламандра Б.Л. Тывес Л.И. Цикловые роботы с аккумуляторами механической энергии. Основы построения привода. Станки и инструмент. 1984. №4 с. 7-10
Накопители энергии: Учеб. Пособие для вузовД.А.Бут Б.Л.Алиевский С.Р.Мизюрин П.В.Васюкевич; Под ред. Д.А.Бута.-М.: Энергоатомиздат 1991.-400 с.: ил.
Расчёт объёмного гидропривода” Методическое пособие к курсовому проектированию Авторы: Бутов А.И. Кондрашев В.Л. Чернов О.В.. – Новочеркасск.: НГТУ 1996. – 111 с.
Справочник конструктора” Автор: Анурьев В.И.– машиностроителя. Т.1. – М.: Машиностроение 1978. – 728 с
Детали машин” Автор: Кудрявцев В.Н.. – Л.: Машиностроение 1980. – 464с
Краткий справочник конструктора” Автор: Гжиров Р.И.. – Л.: Машиностроение Ленинградское отделение 1984. – 464с
Справочник технолога машиностроителя” Под ред. А.Г. Касиловой. – М.: Машиностроение 1985. – 656 с
Справочник по ремонту дорожных машин” Авторы: Новиков И.В. Акильев С.А. – М.: Транспорт 1971. – 240с
Методические указания по выполнению организационно-экономической части дипломного проекта студентами специальности 190603(1709)” «Подъемно-транспортные строительно-дорожные машины и оборудование Наконечный А.Г. Резанова В.Н.» Новочеркасск.: ЮРГТУ(НПИ) 2008. – 48с
Охрана труда” в дипломных проектах. Авторы: Бойко В.А. Фрундин В.Е. методические указания по разработке раздела. – Днепропетровск.: ДГИ 1980. – 50с.
ГОСТ 12.1.005-88. Воздух рабочей среды. Общие санитарно-технические требования. – М.: Стандартиздат 1989 – 76 с.
Рекомендуемые чертежи
- 25.10.2022
- 09.08.2014
Свободное скачивание на сегодня
- 29.08.2014
- 24.01.2023