Двухступенчатый редуктор привода скребкового конвейера




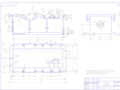
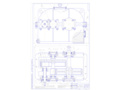
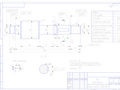
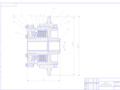
- Добавлен: 25.10.2022
- Размер: 2 MB
- Закачек: 0
Описание
Состав проекта
![]() |
![]() |
![]() ![]() |
![]() ![]() |
![]() ![]() ![]() ![]() |
![]() ![]() ![]() ![]() |
![]() ![]() ![]() ![]() |
![]() ![]() |
![]() ![]() |
![]() ![]() ![]() ![]() |
![]() ![]() |
![]() ![]() |
![]() ![]() |
![]() ![]() ![]() ![]() |
![]() ![]() |
![]() ![]() ![]() ![]() |
![]() ![]() |
![]() ![]() |
![]() ![]() ![]() ![]() |
![]() ![]() |
![]() ![]() |
![]() ![]() |
![]() ![]() |
![]() ![]() ![]() ![]() |
![]() ![]() |
![]() ![]() ![]() ![]() |
![]() ![]() |
![]() ![]() |
![]() ![]() |
![]() ![]() ![]() ![]() |
![]() ![]() |
![]() |
![]() ![]() ![]() |
Дополнительная информация
Привод скребкового конвейера.dwg

Муфта предохранительная
фрикционно -дисковая
Болт М10х50.58 ГОСТ 7798-70
Болт М16х75.58 ГОСТ 7798-70
Гайка М20.05 ГОСТ 5915-70
Гайка М10.05 ГОСТ 5915-70
Гайка М16.05 ГОСТ 5915-70
Шайба 20 ГОСТ 11371-78
Шайба 10 ГОСТ 11371-78
Шайба 16 ГОСТ 11371-78
Электродвигатель 4А112МА8 ГОСТ 19523-81
муфта.dwg

Спецификация муфта.dwg

фрикционная дисковая
Болт М8х30.58 ГОСТ 7798-70
Шайба 8 ГОСТ 6402-70
Винт М30х20.58 ГОСТ 11738-84
Шпонка 20х12х42 ГОСТ 23360-72
Гайка М30 ГОСТ 11871-73
Компановка.dwg

Вал шестерня.dwg

Высота до постоянной хорды
Коэффициент смещения
Делительный диаметр
Неуказанные предельные отклонения
размеров валов по h14
Сталь 40ГОСТ 1050-88
Редуктор двухступенчатый 12V.dwg

Пробка маслоспускная
Кольцо маслоотражательное
Болт М10х45.58 ГОСТ 7798-70
Болт М12х95.58 ГОСТ 7798-70
Болт М8х30.58 ГОСТ 7798-70
Болт М6х25.58 ГОСТ 7798-70
Болт М6х16.58 ГОСТ 7798-70
Гайка М10.05 ГОСТ 5915-70
Гайка М12.05 ГОСТ 5915-70
Колесо зубчатое.dwg

Высота до постоянной хорды
Коэффициент смещения
Делительный диаметр
Неуказанные предельные отклонения
размеров валов по h14
Радиусы скруглений R=3мм.
Сталь 50 ГОСТ 1050-88
корпус редуктора1.dwg

Неуказанные формовочные уклоны по ГОСТ 3212-92.
Неуказанные литейные радиусы R=5мм.
редуктор.dwg

В редуктор залить 1 л масла ИП-160.
Перед окончательной сборкой стыки фланцев корпуса покрыить пастой "Герметик".
Номинальный момент на ведомом валу Т
Частота вращения веомого вала n
Передаточное число u=5.
Модуль зацепления m = 2
Технические требования
Техническая характеристика
привод 2.dwg

Мощность электродвигателя n = 2
Частота вращения конвейера 24
Вращающий момент на валу скребкового конвейера Т =235Нм.
скребкового конвейера
Техническая характеристика
Прямозуб,внутр2013,10.doc
Выбор электродвигателя. Кинематический расчет привода. 5-7
Силовой расчет привода. 8
Расчет зубчатой цилиндрической зубчатой передачи. 9-14
Расчет цилиндрической зубчатой передачи внутреннего зацепления.15-20
Расчет цепной передачи. 21-22
Определение нагрузок валов редуктора.23
Предварительный расчет валов редуктора подбор подшипников. 24-27
Разработка чертежей общего вида редуктора эскизная компановка. 28
Проверочный расчет подшипников. 29-38
Проверочные расчеты. 39-48
Разработка общего вида привода. 49-54
Выбор смазки и уплотнений55
Расчет и выбор муфт.56
Библиографический список.58
Натяжение ветвей двух цепей конвейера:
Скорость цепи конвейера VЦ =040мс;
Шаг тяговой цепи p =02м = 200мм;
Число зубьев звездочки z = 5;
L= 8000час.– ресурс работы редуктора;
% -допускаемое отклонение скорости грузовой цепи.
Цель курсового проектирования – систематизировать закрепить расширить теоретические знания а также развить расчетно-графические навыки студентов. Основные требования предъявляемые к создаваемой машине: высокая производительность надежность технологичность минимальные габариты и масса удобство в эксплуатации и экономичность. В проектируемых редукторах используются различные передачи. Передачи классифицируются:
По принципу действия:
а) с использованием сил трения (фрикционные ременные)
б) работающие в результате возникновения давления между зубьями и кулачками
Редуктором называется механизм состоящий из зубчатых и червячных передач выполненный в виде отдельного агрегата и служащий для передачи мощности от двигателя к рабочей машине;
Назначение редуктора - понижение угловой скорости и повышение вращающего момента ведомого вала по сравнению сведущим валом;
Механизм для повышения угловой скорости выполненный в виде отдельного агрегата называется ускорителем или мультипликатором.
Редуктор состоит из корпуса (литого чугунного или сварного стального) в который помещают элементы передачи - зубчатые колеса валы подшипники и т.д.
Редуктор классифицируется по следующим основным признакам:
тип передачи (зубчатые червячные зубчато-червячные);
число ступеней (одноступенчатые двухступенчатые и т.д.);
тип зубчатых колес (цилиндрические конические и т.д.);
относительное расположение валов в пространстве (горизонтальное
особенность кинематической схемы (развернутая с раздвоенной
Детали машин должны быть надежными т.е. сохранять работоспособность в течение заданного срока службы.
Важнейшие критерии: прочность жесткость износостойкость теплостойкость и вибростойкость.
Нагрузки на детали машин и напряжения в них могут быть постоянными и переменными во времени.
Выбор электродвигателя. Кинематический расчет привода.
1. Определяем окружную силу на звездочках конвейера:
2. Определяем номинальную мощность двигателя:
где Ft – окружная сила на звездочках конвейера Н;
v - скорость движения цепи конвейера мс.
3. Определяем общий КПД привода:
где = 096 – КПД прямозубой закрытой передачи рекомендуемые значения- 096-098;
ВН = 096- КПД прямозубой передачи с внутренним зацеплением рекомендуемые значения -096-098;
цеп = 09- КПД цепной передачи рекомендуемые значения -09;
м = 098- КПД муфты рекомендуемые значения 098;
пк = 099 - КПД подшипников качения рекомендуемые значения - 099
(одной пары подшипников качения)(КПД определяются по табл.1 прил.1).
пс = 099 - КПД опор приводного вала рекомендуемые значения - 099
КПД определяются по табл.1 прил.
4.Определяем требуемая мощность электродвигателя: Рэ.тр кВт
Рэ.тр. = Рвобщ =1607965 = 201кВт.
5.Подбираем по таблице марки электродвигателя :
Таблица 2.1 . Типы двигателей.
Частота вращения обмин
Номинальная мощность
6. Определяем частоту вращения барабана nРМ. обмин.
- скорость конвейера мс
z – число зубьев ведущей звездочки тягового органа
р – шаг тяговой цепи мм
7. Определяем передаточное число привода для всех приемлимых вариантов типа двигателей при заданной номинальной мощности РНОМ
8. Производим разбивку передаточного числа привода:
Проанализировав полученные результаты выбираем nном =700обмин
Тип электродвигателя 4А112MA8
и получаем u =uЦЕП х uЦИЛ хuВН=18х 5х315=2835.
9. Определяем максимальное допускаемое отклонение вращения приводного вала рабочей машины :
где - допускаемое отклонение скорости приводного вала рабочей машины.
10. Определяем кинематические параметры привода:
10.1.Число оборотов вала электродвигателя и и вала с шестерней внутренного зацепления редуктора:
10.2.Число оборотов промежуточного вала с колесом внутреннего зацепления и шестерней цилиндрического зацепления:
10.3.Число оборотов тихоходного вала с колесом внешнего зацепления и малой звездочной цепной передачи:
10.4.Число оборотов большой звездочки цепной передачи и звездочек конвейера:
10.5.Угловая скорость вала электродвигателя и и вала с шестерней внутреннего зацепления редуктора:
10.6. Угловая скорость промежуточного вала с колесом внутреннего зацепления и шестерней цилиндрического зацепления:
10.7. Число оборотов тихоходного вала с колесом внешнего зацепления и малой звездочкой цепной передачи:
10.8. Число оборотов большой звездочки цепной передачи и звездочек конвейера:
Силовой расчет привода.
1. Вращающий момент на валу звездочки скребкового конвейера и большой звездочке цепной передачи:
ТЗК =Т4= Ft х Dзв.б2 = 4000 Х 0117562 = 235Hм;
где Dзв.б = Рзв. sin (200sin(=11756мм.
2. Вращающий момент на валу малой звездочке цепной передачи и цилиндрического зубчатого колеса:
Т3 =Т4(цеп.х uцеп х )= 235(096Х18 х099)= 1374Нм.
3. Вращающий момент на валу цилиндрической шестерни и колесе внутреннего зацепления цилиндрической зубчатой передачи:
Т2 =Т3(цил.х uцил х)= 1374 (096 Х 5 х099)= 289 Нм.
4. Вращающий момент на валу шестерни передачи внутреннего зацепления:
Т1=Т2(ВН.х uВН х)= 289 (096 Х 315 х099)= 965 Нм.
5. Вращающий момент на валу электродвигателя:
ТЭ=Т1( )= 965 (098)= 985 Нм.
Расчет цилиндрической зубчатой передачи
1. Выбор материала зубчатой передачи определение допускаемых напряжений.
1.1.Выбор твердости термообработки и материала колес.
Выбираем для изготовления и шестерни сталь 50 (термообработка- улучшение).
НВ1 = 228 255 для колеса сталь 40 –(термообработка улучшение) НВ2 =192 228. При этом обеспечивается приработка зубьев обеих ступеней .
Рекомендуется назначать больше твердости колеса не менее чем на 20 50 единиц).
Средняя твердость для шестерни НВ3СР =.
Средняя твердость для колеса НВ3СР =
Проверим необходимую разность средних твердостей зубьев шестерни и колеса:
НВ3СР – НВ3СР =2415-228=135 выполняется.
При заданной твердости механические характеристики сталей для шестерни и колеса в закрытой передачи будут равны:
Приданной твердости значения размеров заготовки для шестерни (Dпред –диаметр и колеса
(Sпред- толщина обода или диска)в закрытой передачи будут равны Dпред =100мм; Sпред=60мм.
1.2. Определяем допускаемые контактные напряжения [ нмм2.
а) Определяем коэффициент долговечности для зубьев шестерни ZN3 для колеса ZN4:
где число циклов перемены напряжений соответствующие пределу выносливости
NHE–число циклов перемены напряжений за весь срок службы ( наработка)
T=T2 =289Нм – максимальный момент передаваемый рассчитываемой шестерней в течении времени Н×м
T21=07Т= – момент действующий в течении часов
T22=05Т= – момент действующий в течении часов
С – число колес находящихся в зацеплении с рассчитываемым С=10;
=- частота вращения шестерни обмин
-=8000ч-число часов работы передачи за расчетный срок службы час
T=T3 =1374Нм – максимальный момент передаваемый рассчитываемым колесом в течении времени Н×м
T31=07Т= – момент действующий в течении часов
T32=05Т= – момент действующий в течении часов
=обмин- частота вращения колеса обмин
1.3. Определяем допускаемые контактные напряжения и соответствующие пределу контактной выносливости при числе цикле и и принимая коэффициент запаса прочности S=1.1:
. НО3= 2НВ1СР + 70 =2х2415 + 70 =553 МПа;
НО4= 2НВ2СР + 70 =2х218 + 70 = 506МПа;
Определяем допускаемые контактные напряжения для зубьев шестерни и колеса
1.4. Определяем расчетное допускаемое контактное напряжение:
принимаем в качестве расчетного допускаемого контактного напряжения шестерни Нмм2 .
2. Определяем допускаемые напряжения изгиба () и ()Нмм2:
принимаем коэффициент запаса прочности S=1.7.
2.1.Определяем коэффициент долговечности при расчете на изгибную выносливость:
где -базовое число напряжений при изгибе.
Согласно условию (5.17)принимаем YN1= YN2. По рекомендациям содержащимся в параграфе 5.2. находим коэффициент YА учитывающий двухстороннее нагружение в нашем случае YА1= YА2=1.
2.2.Определяем допускаемое напряжение изгиба
FO3 и FO4 соответствующее пределу изгибной выносливости при числе циклов перемены напряжений по таблице
FO3= 175HBСР =175 Х 2415 = 4226 МПа.
FO4= 175HBСР =175 Х 218 = 3815 МПа.
2.3.Определяем допустимые напряжения изгиба :
3.Опрелеление межосевого расстояния передачи
3.1. Согласно параграфу 5.3. принимаем:
- коэффициент относительной ширины колес :
-расчетный коэффициент для прямозубых передач ;
-коэффициент учитывающий неравномерность нагрузки .
3.2. Определяем модуль:
3.3.Определяем числа зубьев шестерни и колеса:
3.4. Определяем геометрические параметры передачи:
-делительные диаметры :
Проверяем межосевое расстояние:
мм принимаем b4=55мм.
Определяем диаметры вершин колес:
Определяем диаметры впадин колес колес:
4.Проверочный расчет на выносливость по контактным напряжениям без учета дополнительных нагрузок:
-коэффициент учитывающий механические свойства материалов сопряженных зубчатых колес для стали ;
- коэффициент учитывающий форму сопряженных поверхностей зубьев в полюсе зацепления:
Где - коэффициент торцевого перекрытия
4.1. Проверочный расчет на выносливость по контактным напряжениям с учетом дополнительных нагрузок:
Коэффициент нагрузки равен
Входящие в это выражение коэффициенты равны:
(Рис.5.7. при и при 3 схеме.
-для прямозубых передач
Контактные напряжения с учетом дополнительных нагрузок:
что меньше допустимого напряжения .
5. Проверочный расчет на выносливость по напряжениям изгиба:
По таблице 5.7. назначаем 9 степень точности.
Коэффициент формы зуба шестерни
определяем напряжения изгиба для наиболее слабого элемента по соотношению: :
Наиболее слабый элемент шестерня поэтому напряжения изгиба рассчитываем для шестерни:
Полученные значения меньше допустимых.
Коэффициент нагрузки
Здесь КА=1;(Рис.5.8) ;(табл.5.11.
Расчет цилиндрической зубчатой передачи внутреннего зацепления
Средняя твердость для шестерни НВ1СР =.
Средняя твердость для колеса НВ2СР =
НВ1СР – НВ2СР =2415-228=135 выполняется.
а) Определяем коэффициент долговечности для зубьев шестерни ZN1 для колеса ZN2:
T=Т1 =965Нм – максимальный момент передаваемый рассчитываемой шестерней в течении времени Н×м
T11=07Т= – момент действующий в течении часов
T12=05Т= – момент действующий в течении часов
T=T2 =289Нм – максимальный момент передаваемый рассчитываемым колесом в течении времени Н×м
. НО1= 2НВ1СР + 70 =2х2415 + 70 =553 МПа;
НО2= 2НВ2СР + 70 =2х218 + 70 = 506МПа;
FO1 и FO2 соответствующее пределу изгибной выносливости при числе циклов перемены напряжений по таблице
FO1= 175HBСР =175 Х 2415 = 4226 МПа.
FO2= 175HBСР =175 Х 218 = 3815 МПа.
3.Расчет геометрических параметров цилиндрической передачи внутреннего зацепления:
3.1.Принимаем z1=31 тогда принимаем z2=98.
Принимаем модуль m=2.5мм
Наиболее слабый элемент колесо поэтому напряжения изгиба рассчитываем для колеса:
Расчет цепной передачи
Число оборотов ведущей звездочки обмин.
Вращающий момент на валу ведущей звездочки:Нм;
на валу ведомой звездочки: Нм;
Передаточное число цепной передачи u=18.
1. Определяем число зубьев цепной передачи:
1.1.Число зубьев ведущей звездочки:
1.2.Число зубьев ведомой звездочки:
z4= z3х uцеп=25х18=45.
1.3.Выбираем однорядную цепь и вычисляем шаг цепи:
Расчетный коэффициент нагрузки: Кэ=kд х kа х kн х kсм х kРЕГ х kРЕЖ
где kд=12 – динамический коэффициент при спокойной нагрузке (передаче к цепному конвейеру);
kа=1 – учитывает влияние межосевого расстояния (при ац(30-50)t t – шаг цепи;
kн=1 – учитывает влиятие угла наклона цепи (при углах не более 60°);
kРЕГ=11– при периодическом регулировании натяжения цепи;
kСМ=15 – при капельной смазке;
kРЕЖ=1 – при односменной работе.
Кэ=12 х 1 х 1 х 15 х 1 х 11=18
Принимаем по табл. 82 среднее значение допускаемого давления в шарнирах цепи при частоте вращения вала малой звездочки 4444 обмин: [p]=35 Мпа.
Определяем шаг однорядной цепи:
мм принимаем t=1905мм по ГОСТ13568 (табл.81).
1.3.Принимаем значение межосевого расстояния выраженное в шагах а =40t.
1.4. Определяем число звеньев цепи:
1.5.Уточняем межосевое расстояние:
1.6. Определяем длину цепи :
1.7. Определяем диаметры делительных окружностей звездочек:
1.8. Определяем диаметры окружностей выступов звездочек:
1.9. Определяем диаметры окружностей впадин звездочек:
1.10. Средняя скорость цепи:
1.11 Полезная нагрузка (окружная сила) передаваемая цепью:
Принимаем ближайший стандартный шаг t=19.05 мм (табл. 21) (Q=31800Н q=1.9 кгм F=105.мм2 d3=11.91мм b1=12.7мм).
1.12.Проверочный расчет цепи на износостойкость:
Давление в шарнире цепи.
МПаМПа=.Расчетное давление в цепи меньше допустимого следовательно износостойкость цепи при заданных нагрузках обеспечена.
1.13. Проверяем прочность цепи :
Коэффициент запаса прочности :.s=FРАЗР.Fmax=318001826=174[s]=(5-6).
Определение нагрузка валов редуктора
1.Определение сил в зацеплении внутренней цилиндрической передачи:
1.2. Радиальная сила:
2. Определение сил в цилиндрической прямозубой передачи внешнего зацепления:
1.3.Сила давления на вал от муфты:
2.1. Окружная сила передаваемая цепью:
Предварительный расчет валов редуктора подбор подшипников
1. Выбор материала валов.
Для быстроходного и тихоходного валов выбираем легированную сталь 45 термообработка нормализация
Механические характеристики выбираем из таблицы :
2. Выбор допускаемых напряжений на кручение.
Принимаем для быстроходного и тихоходного вала : [
Для промежуточного вала : [
3. Определение геометрических параметров валов.
3.1. Определяем геометрические параметры каждой ступени быстроходного вала- шестерни : их диаметры d и длину L:
a) Первая ступень вала под полумуфту:
d1– диаметр шейки вала под полумуфты мм;
[]k =20 – допускаемое напряжение на кручение Нмм2;
Мк =95– крутящий момент равный вращающему моменту на валу кНм
L1– длина шейки вала под полумуфту
L1 = (10..15)× 18 = (18-27)мм с учётом Lцил полумуфты принимаем L1 = 40 мм;
б) Вторая ступень под уплотнение крышки с отверстием и подшипники:
d2 = d1+3-7=18+(3-7)=(21+25)=25мм
L2 = 127мм-определяем графически по эскизной компановке
в) Третья ступень между подшипником и шестерней :
d3 = d2+3-7=25+(3-7)=(28+32)=32мм;
Принимаем d3 = 32 мм;
L3 =21мм– определяется графически по эскизной компановке;
Шестерню выполняем заодно с валом.
4. Определяем геометрические параметры каждой ступени промежуточного вала : их диаметры d и длину L:
4.1. Первая ступень вала под подшипник:
мм принимаем d1П = 25 мм;
L1 – длина шейки вала под подшипник мм.
4.2. Вторая ступень диаметр вала между подшипником и шестерней :
d2П = 25+(3-7) = (28-32) мм; принимаем d2П=30мм
4.3. Третья ступень диаметр вала между цилиндрической шестерней и колесом внутреннего зацепления
L3=46мм – определяется графически.
4.4. Четвёртая ступень диаметр вала упорного бурта перед колесом внутреннего зацеплени :
d4П = 30+(3-7) = (33-37) мм; принимаем d4П=35мм
4.5. Пятая ступень диаметр вала под колесом внутреннего зацепления
L5 =45мм– равен длине ступицы колеса.
4.6. Шестая ступень диаметр вала между колесом и подшипником и под подшипником
L5 =33мм– под подшипником и между подшипником и колесом.
5. Определяем геометрические параметры каждой ступени тихоходного вала : их диаметры d и длину L
5.1. Первая ступень вала под звездочку:
мм принимаем d1П = 35 мм;
L1 – длина шейки вала под звездочкой мм
L1 = 40 мм; принимаем мм.
5.2. Вторая ступень диаметр вала под уплотнение крышки с отверстием и подшипник:
d2Т = 35+(3-7) = (38-42) мм; принимаем d2Т=40мм.
5.3. Третья ступень диаметр вала буртика перед подшипником:
d3Т = 40+(3-7) = (43-47) мм; принимаем 45мм
L3 =10мм– определяется графически.
5.4. Четвёртая ступень диаметр вала между упорных буртиков подшипника и колеса :
d3Т = 35мм принимаем по выходному диаметру d1 для обеспечения зазора между валом и колесом внутреннего зацепления.
L4 =94мм– определяется графически.
5.5. Пятая ступень диаметр вала буртика перед зубчатым колесом:
5.6. Шестая ступень под зубчатое колесо:
L5 =64мм– определяем по ширине ступицы зубчатого колеса.
5.7 .Седьмая ступень диаметр вала под подшипник:
L6 =39мм– определяем графически.
6. Предварительный выбор подшипников качения
6.1. По таблице П5. определяем для быстроходного вала:
тип подшипника – радиальные однорядные;
Выбираем подшипники ГОСТ 8338-75 №304 d = 25мм; D = 52мм; В = 15мм; с грузоподъёмность: Cr = 14 кН; C0r = 69 кН.
6.2. По таблице П5. определяем для промежуточного вала:
Выбираем подшипники ГОСТ 8338-75 №305 d = 25мм; D = 62мм; В = 17мм; с грузоподъёмность: Cr = 225 кН; C0r = 114 кН.
6.3. По таблице П5 определяем для тихоходного вала:
тип подшипника – конические однорядные;
схема установки – в распор;
Выбираем для тихоходного вала подшипники ГОСТ 8338-75 - №308 d = 40мм;
D =900мм; В = 23мм; грузоподъёмность: Cr = 41 кН;
Разработка чертежа общего вида редуктора (эскизная компановка).
1. Намечаем расположение проекций чертежа в соответствии с кинематической схемой привода и наибольшими размерами колес.
2. Проводим оси проекций и осевые линии валов цилиндрической передачи внешнего зацепления на расстоянии аW = 160мм параллельно друг другу.
3. Вычерчиваем редукторную пару в соответствии с геометрическими параметрами полученными в результате проектного расчета.
В конструкции зубчатого колеса предусматриваем ступицу :
dст=(155 .16)d3=(1.55 16)принимаем72мм; принимаем 65мм.
4. Вычерчиваем промежуточный вал и на нем зубчатое колесо внутреннего зацепления предусматривая в нем ступицу:
dст=(155 .16)d3=(1.55 16)принимаем48мм; принимаем 45мм.
Вычерчиваем шестерню и вал передачи внутреннего зацепления.
4. Толщина стенки корпуса редуктора:
5.Зазор между стенкой корпуса редуктора:
- по диаметру: Х=принимаем 10мм
- по торцам: Х1=принимаем 8мм.
6. Прочерчиваем контур внутренней поверхности стенок корпуса редуктора с зазорами Х и Х1 от вращающихся поверхностей колеса и торцов для предотвращения задевания:
Расстояние y между дном корпуса и поверхностью колеса принимаем
Действительный контур и размер корпуса разрабатываем на чертеже общего вида привода.
7. Вычерчиваем ступени валов на соответствующих осях по размерам d и l полученным в проектном расчете валов.
8.Вычерчиваем контуры подшипников в соответствии с схемой их установки по размерам dD T.
9. Определение точек приложения консольных сил.
По схеме эскизной компановки определяем расстояния приложения сил.
-для быстроходного вала: ;;
;-место приложения реакции муфты в конце вала
-для промежуточного вала:;
-для тихоходного вала:;;
;-место приложения окружной силы цепи в середине выходного конца вала.
10.Проставляемразмеры на проекциях эскизной компановкивыполняем таблицу и основную надпись.
Проверочный расчет подшипников
1.Определение реакций в подшипниках быстроходного вала:
1.2.Вертикальная плоскость:
а определяем опорные реакции Н:
Следовательно реакции определены правильно
б) строим эпюру изгибающих моментов относительно оси X в характерных сечениях 1 4 Нм:
1.3. Горизонтальная плоскость
а) определяем опорные реакции Н:
Проверка: Σх = 0; -;
б) строим эпюру изгибающих моментов относительно оси Y в характерных сечениях 1 4 Нм:
в) строим эпюру крутящих моментов Нм:
1.4.Определяем суммарные радиальные реакции Н:
1.5.Определяем суммарные изгибающие моменты в наиболее нагруженном сечении 2 Нм:
2. Определение реакций в подшипниках тихоходного вала:
2.1.Вертикальная плоскость
б) строим эпюру изгибающих моментов относительно оси Х в характерных сечениях 1 4 Нм:
2.2.Горизонтальная плоскость
Следовательно реакции определены правильно.
2.3.Строим эпюру крутящих моментов Нм:
2.4.Определяем суммарные радиальные реакции Н:
2.5.Определяем суммарные изгибающие моменты в наиболее нагруженных сечениях 23 Нм:
3.Определение реакций в подшипниках промежуточного вала:
3.1.Вертикальная плоскость:
3.2.Горизонтальная плоскость:
3.4.Определяем суммарные радиальные реакции Н:
3.5.Определяем суммарные изгибающие моменты в наиболее нагруженных сечении 3 Нм:
4.Проверяем пригодность для быстроходной вал-шестерни шариковых радиальных однорядных подшипников:
По таблице П5. определяем для быстроходного вала:
тип подшипника – радиальные однорядные;серия – легкая;
Реакции в подшипниках RА = 2726Н; RВ = 1696 Н;
Требуемая долговечность подшипников Lh = 8000 ч
Подшипники установлены по схеме враспор
Определяем отношение т.к. Ra = 0 отношение ≤ e
Определяем эквивалентную динамическую нагрузку наиболее нагруженного подшипника при ≤ e выбираем формулу
Определяем динамическую грузоподъёмность
Определяем долговечность подшипника:
5.Для тихоходного вала:
По таблице П5 определяем для тихоходного вала:
тип подшипника – конические однорядные;серия – средняя;
Выбираем для тихоходного вала подшипники ГОСТ 8338-75 - №308
d = 40мм; D =900мм; В = 23мм; грузоподъёмность: Cr = 41 кН;
Угловая скорость вала = 4.65 с-1;
Реакции в подшипниках RЕ = 2263; RF = 1090 Н;
Требуемая долговечность подшипников Lh = 8000 ч;
Определяем отношение т.к. Ra = 0 отношение ≤ e.
.Определяем долговечность подшипника:
6. Для промежуточного вала:
По таблице П5. определяем для промежуточного вала:
тип подшипника – радиальные однорядные;серия – средняя;
Выбираем подшипники ГОСТ 8338-75 №305 d = 25мм; D = 62мм;
В = 17мм; с грузоподъёмность: Cr = 225 кН; C0r = 114 кН.
Угловая скорость вала = 23.26 с-1;
Реакции в подшипниках RС = 141.6; RD = 703 Н;
Подшипники установлены по схеме враспор.
Определяем динамическую грузоподъёмность:
1.Проверочный расчет шпонок.
1.1. Рассчитаем шпоночное соединение для входного быстроходного вала с полумуфтой. Шпонку выбираем призматическую по ГОСТ 23360-70. Размеры шпонки выбираем по диаметру вала: d=18 мм
- сечение b x h = 6х6мм
- глубина паза вала t1=35мм
- глубина паза ступицы t2=28мм
Шпонка призматическая со скругленными торцами. Материал шпонки – сталь 45 нормализованная. Напряжение смятия и условия прочности определяем по формуле:
Передаваемый момент 965 Н.
При стальной полумуфте
1.2 Рассчитаем шпоночное соединение для выходного тихоходного вала со зубчатым колесом.
Соединение вал- зубчатое колесо. d=45мм.
Шпонку выбираем призматическую по ГОСТ 23360-70.Размеры шпонки выбираем по валу:
- глубина паза вала t1=55 мм;
- глубина паза ступицы t2=38 мм;
Шпонка призматическая со скругленными торцами. Материал шпонки – сталь 45 нормализованная. Напряжения смятия и условия прочности определяем по формуле:
При стальной ступице колеса колеса :
Передаваемый момент Т3 =1374Нм
1.3. Соединение вала со звездочкой:d=35мм
Шпонку выбираем призматическую по ГОСТ 23360-70.Размеры шпонки выбираем по диаметру вала:
- сечение b x h=10х8мм
- глубина паза вала t1=50мм
- глубина паза ступицы t2=33мм
Передаваемый момент 289Нм.
При стальной ступице
следовательно муфту из стали 45.
1.4. Рассчитаем шпоночное соединение для промежуточного вала со зубчатым колесом.
- глубина паза вала t1=5 мм;
При стальной ступице колеса колеса : .
Передаваемый момент Т2 =289Нм.
2. Проверочный расчет стяжных болтов.
2.1. Определяем эквивалентные напряжения.
а)FP – расчетная сила затяжки винтов обеспечивающая не раскрытие стыка под нагрузкой Н:
FP =[K3 (1-x)+x]FB =[1.25(1-0.2)+0.2]11255=1351Н.
К3=125 - коэффициент затяжки при постоянной нагрузке;
б) А- площадь опасного сечения винта мм2
3.Проверочный расчет валов:
Проверочный расчет валов на прочность выполняем на совместное действие изгиба и кручения.
Цель расчета –определить коэффициенты запаса прочности в опасных сечениях валов и сравниваем их с допускаемыми s
Пределы выносливости материала:
3.1. Тихоходный вал:
Проверка прочности вала в сечении 2 (Концентрация напряжений посадка с натягом ).
Суммарный изгибающий момент в сечении 2 – М2 =114Н м.
Крутящий момент МК3 =Т3=1374Н м.
3.2 Моменты сопротивления сечения вала под подшипником :d=40мм
3.3. Напряжения изгиба:
3.4. Напряжения кручения:
3.5.Определяем коэффициент концентрации нормальных и касательных напряжений для сечения тихоходного вала 2.
где : ;- эффективные коэффициенты концентрации напряжений .Они зависят от механических характеристик материала и размеров сечения. Выбираем по таблице 10.11.
К- коэффициент влияния шероховатости табл. 11.13.
К- коэффициент влияния поверхностного упрочнения табл.10.14.
3.6. определяем пределы выносливости в расчетном сечении вала(2):
3.7. Коэффициент запаса только по нормальным напряжениям изгиба:
3.8. Коэффициент запаса только по касательным напряжениям кручения:
3.9.Определяем общий коэффициент запаса прочности в опасном сечении (2):
3.9. Тихоходный вал:
Крутящий момент МК1 =Т1=965Н м.
3.10 Моменты сопротивления сечения вала под подшипником :d=40мм
3.11. Напряжения изгиба:
3.12. Напряжения кручения:
3.13.Определяем коэффициент концентрации нормальных и касательных напряжений для сечения тихоходного вала 2.
К- коэффициент влияния шероховатости табл. 10.13.
3.14. определяем пределы выносливости в расчетном сечении вала(2):
3.15. Коэффициент запаса только по нормальным напряжениям изгиба:
3.16. Коэффициент запаса только по касательным напряжениям кручения:
3.17.Определяем общий коэффициент запаса прочности в опасном сечении (2):
Проверка прочности вала в сечении (2) (Концентрация напряжений посадка снатягом ).
Суммарный изгибающий момент в сечении 2 – М1 =183Н м.
4.1 Моменты сопротивления сечения вала под подшипником :d=25мм
4.2. Напряжения изгиба:
4.3. Напряжения кручения:
4.4.Определяем коэффициент концентрации нормальных и касательных напряжений для сечения тихоходного вала 2.
где : - эффективные коэффициенты концентрации напряжений .Они зависят от механических характеристик материала и размеров сечения. Выбираем по таблице 10.11.
К- коэффициент влияния шероховатости табл. 1013.
К- коэффициент влияния поверхностного упрочнения табл.1014.
4.5. определяем пределы выносливости в расчетном сечении вала(3)
4.6. Коэффициент запаса только по нормальным напряжениям изгиба:
4.7. Коэффициент запаса только по касательным напряжениям кручения:
4.8.Определяем общий коэффициент запаса прочности в опасном сечении (2):
5.Промежуточный вал.
Проверка прочности вала в сечении (3) (Концентрация напряжений посадка впадины шестерни ).
Суммарный изгибающий момент в сечении 3 – М1 =401Н м.
Крутящий момент МК2 =Т2=289Н м.
5.1 Моменты сопротивления сечения вала во впадинах шестерни :d=7125мм
5.2. Напряжения изгиба:
5.3. Напряжения кручения:
5.4.Определяем коэффициент концентрации нормальных и касательных напряжений для сечения тихоходного вала 2.
5.5. определяем пределы выносливости в расчетном сечении вала(3)
5.6. Коэффициент запаса только по нормальным напряжениям изгиба:
5.7. Коэффициент запаса только по касательным напряжениям кручения:
5.8.Определяем общий коэффициент запаса прочности в опасном сечении (2):
Разработка общего вида привода.
1.Конструирование зубчатого колеса шестерни внешнего зацепления:
1.1. Основные размеры:
- диаметры вершин колес:
- диаметры впадин колес колес:
-ширина колеса b4=55мм
-ширина шестерни мм.
- диаметр ступицы колеса мм
-длина ступицы колеса LCT=мм принимаем 65мм.
- с=(02-03)b3=(0.2-0.3)=(11-16.5)мм –толщина диска колеса
- принимаем 8мм- толщина обода
шестерню выполняем заодно с валом
-радиусы закруглений R=6.
2.Конструирование зубчатого колеса шестерни внутреннего зацепления:
2.1. Основные размеры:
-ширина колеса b2=40мм
-длина ступицы колеса LCT=мм принимаем 55мм.
- с=(02-03)b3=(0.2-0.3)=(8-135)мм принимаем 15мм–толщина диска колеса
- принимаем 7мм- толщина обода
3. Конструирование валов:
3.1.Быстроходный вал шестерня:
- диаметр вала под муфту d1 = 18мм;
-длина вала под муфту
- на конце вала фаска 16х45(табл.10.8.)
-на переходном конце вала галтель r=20мм(табл.10.8.);
-шпоночный паз выполняем размерами b
- посадка муфты с допуском 18(H7s7);
-диаметр вала в сквозной крышке ф25h9 длиной 36 мм;
-диаметр вала под подшипники 25k6 длиной 90мм;
-на переходном участке вала под подшипником с участком вала от подшипника к шестерне выполняем канавку шириной 3мм глубиной 025мм (табл.10.7.);
-переходной участок вала от подшипника до шестерни выполняем ф32мм длиной 21мм;
-шестерню выполняем ф825мм шириной 45мм согласно ранее рассчитанным размерам;
- диаметр вала под звездочку d1 = 35(H7s7)мм;
-длина вала под звездочку
-диаметр вала в сквозной крышке ф40h9 длиной 31мм;
-диаметр вала под подшипник 40k6 длиной 24мм;
-диаметр упорного буртика ф45мм длина10мм;
-диаметр вала между упорными буртиками ф35мм длиной 935мм;
-диаметр упорного буртика ф50мм длина10мм;
- диаметр вала под колесом выполняем ф=45( H7s7)длиной 65мм;
на переходном участке вала под колесом с буртиком выполняем канавку шириной 5мм глубиной 05мм (табл.10.7.)
-диаметр вала под подшипник выполняем 40k6 длиной 39мм
- на переходном участке вала под подшипником с участком вала от подшипника к колесу выполняем канавку шириной 5 мм глубиной 05мм (табл.10.7.);
- на конце вала фаска 16х45(табл.10.8.).
3.3.Промежуточный вал:
- диаметр вала под подшипник d1 = 25(H7k6)мм;
-длина вала под подшипник
-диаметр вала под колесом ф30s7H7 длиной 33
-шпоночный паз выполняем размерами b x t x l=10 х 80 х 35 мм
-на расстоянии 5 мм от торца переходной ступени;
-диаметр упорного буртика ф35мм длина10мм;
-на переходном участке вала под колесом с буртиком выполняем канавку ------шириной 5мм глубиной 05мм (табл.10.7.)
-диаметр вала между упорными буртиками ф30мм длиной 46мм;
-шестерня ф825мм длиной 60мм
- диаметр вала под подшипник d1 = 25(H7k6)мм длиной 18мм
3.4.Соединения валов с деталями выбраны в предыдущем пункте.
4.Конструирование подшипниковых узлов:
4.1. Схема установки подшипников :
Осевое фиксирование тихоходного вала в двух опорах :
Обе опоры конструируем одинаково при этом каждый подшипник ограничивает осевое перемещении вала в одном направлении. Внутренние кольца подшипников закрепляют на валу упором в буртики либо в торец зубчатого колеса( через маслоотражательные кольца). Наружные кольца подшипников закрепляем от осевого смещения упором в торцы крышек.
4.2.Быстроходный вал. Осевое фиксирование быстроходного вала в двух опорах :
ный вал. Осевое фиксирование быстроходного вала в двух опорах :
4.4. Посадки подшипников:
-для внутренних колец подшипников : ф40(H7k6) ф25(H7k6)ф25(Н7k6)поле допуска для наружного кольца Н7.
4.5. Крышки подшипниковых узлов.
Для герметизации подшипниковых узлов редуктора осевой фиксации подшипников и воспринятия осевых нагрузок применяем крышки. В нашем случае изготавливаем из Cт.3 првертные. На каждом вале с одной стороны устанавливаем глухие крышки
Размеры крышек определяем в зависимости от диаметра наружного кольца подшипника
4.6.Регулировочные устройства .
Регулировка подшипников осуществляем при помощи регулировочных прокладок .
5. Конструирование корпуса редуктора.
5.1.Корпус редуктора разъемный.
Форму корпуса принимаем прямоугольной формы
5.2. Толщина стенок корпуса и ребер жесткости:
5.3. Фланцевые соединения.
-диаметр фундаментных болтов принимаем согласно таблице 10.17. в зависимости от межцентрового расстояния редуктора равного 160мм – d1 =М16;
- диаметр стяжных болтов у подшипников d2 = М12
- диаметр стяжных болтов у подшипников d3 = М10
-ширина фланца фундаментных болтов К1 =40мм;
-ширина фланца стяжных болтов К2 =32мм;
-ширина фланца стяжных болтов К23=28мм;
-расстояние до центра фундаментных болтов С1 =18мм ;
-расстояние до центра стяжных болтов С2 =15мм;
-расстояние до центра стяжных болтов С3 =13мм;
-диаметр под головку фундаментного болта d0 =30мм;
- глубина отверстия под головку фундаментного болта b01 = 1.0мм;
-количество стяжных болтов на одну сторону 4шт. и 5шт.
- опорная поверхность фундаментного фланца основания корпуса редуктора выполняем в виде двух полос шириной 48мм(К1 +.
5.4.Детали и элементы корпуса редуктора.
- Смотровой люк служит для контроля сборки и осмотра редуктора при эксплуатации. Для удобства располагаем его в верхней крышке корпуса что позволяет использовать его для заливки масла. Люк выполняем прямоугольной формы . Люк закрываем крышкой толщиной .Для того чтобы внутрь корпуса извне не засасывалась пыль под крышку ставим уплотняющую прокладку из картона толщиной 1..15мм.На крышку устанавливаем пробку – отдушину которую привариваем к крышке. В пробке пробиты два отверстия ф4мм.Крышку крепим к корпусу винтами четырьмя болтами М8.
Расточку отверстий под подшипники в крышке и основании корпуса производим в сборе.
Перед расточкой устанавливаем два фиксирующих штифта на возможно большем расстоянии друг от друга. Диаметр штифта равен d=(0.8d3) = 0.8
Уплотняющие покрытия плоскости разъема склеивает крышку и основание корпуса. Для подъема и транспортировки крышки корпуса и собранного редуктора применяем проушины отливая их заодно с крышкой. Диаметром d=толщина металла до края а=15мм
Отверстия под фонарный маслоуказатель (М5и ф4мм) и пробку (К12) выполняем на противоположных торцевых сторонах основания корпуса в доступном месте. Нижняя сливная кромка сливного отверстия ниже уровня днища .Дно с уклоном в сторону отверстия 1-2. У самого отверстия выполняем местное углубление для стока масла и отстоявшейся грязи. Отверстие под маслоуказатель выполняем на высоте достаточной для точного замера верхнего и нижнего уровня масла. Наружные стороны отверстий оформляем платиками. При установке маслоуказателя и сливной пробки применяем уплотнительные прокладки.
Выбор смазки и уплотнений редуктора.
1.Система смазки (см. пример в 5)
Окружная скорость в зацеплении u мс:
v = 2×d2(2×103) = 2326×2452000 = 2.84 мс
Контактное напряжение H= 1326 Нмм2;
По таблице выбираем масло И-Г-А-68;
Глубину колеса принимаем:
hм = 05d2 при этом hmin = 22m
hmin = 22×3 = 6.6 мм.
2. Для смазки шарикоподшипников валов принимаем пластичную смазку ЦИАТИМ-201 которую закладываем в подшипники при сборке.
Уплотнение на выходе быстроходного вала и вала колеса примем манжетные ГОСТ 8752-79 [1;табл.19.16;стр.373]
для быстроходного вала:
d= 25 мм. D=42 мм. h1= 10 мм.ГОСТ 8752-79.
для тихоходного вала:
d= 40мм. D= 60 мм. h1= 10 мм. ГОСТ 8752-79.
Расчет и выбор муфт
1.Основной характеристикой для выбора муфты является номинальный вращающий момент Т Нм установленный стандартом. Муфту выбираем по большему диаметру концов соединяемых валов и расчётному моменту Т Нм который должен быть в пределах номинального:
коэффициент режима нагрузки
1. Рассчитываем для соединения редуктора с электродвигателем
Выбираем упругую муфту втулочно-пальцевую МУВП 315 ГОСТ 21424-93.
Габаритные размеры: D = 90 мм; Lцил = 84 мм;
Отверстие: d = 18 мм; Lцил = 40 мм;
Смещение осей валов не более: Δr = 1 мм; Δγ = 1º; Δα = 1 мм.
2. Рассчитываем для соединения редуктора со звездочками скребкового конвейера:
Выбираем предохранительную фрикционную дисковую муфту ГОСТ 15622-96.
Габаритные размеры: D = 145 мм; Lцил = 180 мм;
Отверстие: d = 40 мм; Lцил = 58 мм;
1. Перед сборкой внутреннюю полость корпуса и крышки редуктора очищают
и покрывают маслостойкой краской
2. Сборку производят согласно чертежам. Начинают сборку с валов
3 На ведущий промежуточный и ведомый вал насаживают шестерню колесо подшипники предварительно нагретые до 80 - 100 С.
4. Собранные узлы укладываются в основание корпуса ставятся прокладки
крышки штифты закрепляются крышки и т.д.
5. Ставятся шпонки полумуфты маслосливная пробка и т.д.
6. Заливают масло и подвергают стендовым испытаниям.
Библиографический список
1. М.Р. Ерохина. Детали машин и основы конструирования. Москва. «Колос С».2005г.
2. А.Е.Шейнблит. Курсовое проектирование деталей машин. Калининград. Янтарный сказ.1999г.
3. П.Ф. ДунаевО.П.Леликов. Детали машин. Курсовое проектирование. Учеб. Пособие для машиностроительных вузов и техникумов. М. «Высшая школа» 1990г.
4. Д.В. Чернилевский. Детали машин. Проектирование приводов технологического оборудования. Москва.«Машиностроение»560с;2003г.
5. Иванов М.Н. Детали машин. Курсовое проектирование. Учеб. Пособие для машиностроительных вузов. Москва. «Высшая школа».
Рекомендуемые чертежи
- 03.12.2021