Двухконсольный козловой кран г/п 10 т




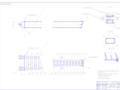
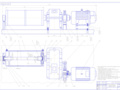
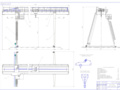
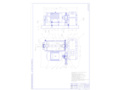
- Добавлен: 25.10.2022
- Размер: 2 MB
- Закачек: 0
Описание
Состав проекта
![]() |
![]() |
![]() ![]() ![]() ![]() |
![]() |
![]() ![]() ![]() ![]() |
![]() ![]() ![]() ![]() |
![]() ![]() ![]() ![]() |
![]() ![]() ![]() ![]() |
![]() |
![]() ![]() ![]() |
![]() ![]() ![]() |
![]() ![]() ![]() |
![]() ![]() ![]() |
![]() ![]() ![]() ![]() |
![]() ![]() ![]() ![]() |
![]() ![]() ![]() ![]() |
![]() |
![]() ![]() ![]() |
![]() ![]() ![]() |
![]() ![]() ![]() |
![]() ![]() ![]() |
![]() ![]() ![]() |
![]() ![]() ![]() |
Дополнительная информация
МЕХАНИЗМ ПЕРЕДВИЖЕНИЯ ТЕЛЕЖКИ.cdw

Тормоз отрегулировать на момент 107 Н*м
Угловая несооснасть оси выходного вала редуктора и
электродвигателя не более 0
Радиальная несоосность оси выходного вала редуктора и
Механизм обкатать без нагрузки в течении 1 часа .
Стук и резкий шум недопускается.
После обкатки масло из редуктора слить и залить
масло индустриальное И-40А ГОСТ20799-75 в количестве 4 литров.
Остальные технические требования по СТБ1022-96
* Размеры для справок
Механизм передвижения
МЕХАНИЗМ ПЕРЕДВИЖЕНИЯ ТЕЛЕЖКИ.cdw

Тормоз отрегулировать на момент 107 Н*м
Угловая несооснасть оси выходного вала редуктора и
электродвигателя не более 0
Радиальная несоосность оси выходного вала редуктора и
Механизм обкатать без нагрузки в течении 1 часа .
Стук и резкий шум недопускается.
После обкатки масло из редуктора слить и залить
масло индустриальное И-40А ГОСТ20799-75 в количестве 4 литров.
Остальные технические требования по СТБ1022-96
* Размеры для справок
Механизм передвижения
КОЗЛОВОЙ ОБЩИЙ ВИД.cdw

механизма подъема груза
Схема запасовки каната механизма
передвижения тележки
Техническая характеристика
Скорость подъема груза
Скорость передвижения крана
Скорость передвижения тележки
Максимальная высота подъема
Длина консоли левой (правой)
Группа режима работы механизма подьема груза М6
Группа режима работы механизма передвижения крана М4
Группа режима работы механизма передвижения тележки М3
МЕТАЛЛОК.cdw

Сварку выполнять по ГОСТ 5264-80.
Сварные швы зачистить.
H14 ; h14 ; ±0.5IT14.
* Размеры для справок.
Металлоконструкция опоры
МЕХАНИЗМ ПОДЬЕМА ГРУЗА.cdw

Тормоз отрегулировать на момент 233 Н*м
Угловая несооснасть оси выходного вала редуктора и
электродвигателя не более 0
Радиальная несоосность оси выходного вала редуктора и
Механизм обкатать без нагрузки в течении 1 часа .
Стук и резкий шум недопускается.
После обкатки масло из редуктора слить и залить
масло индустриальное И-40А ГОСТ20799-75 в количестве 4 литров.
Остальные технические требования по СТБ1022-96
* Размеры для справок
Механизм подьема груза
МЕХАНИЗМ ПОДЬЕМА ГРУЗА.dwg
Тормоз отрегулировать на момент 233 Н*м
Угловая несооснасть оси выходного вала редуктора и
электродвигателя не более 0
Радиальная несоосность оси выходного вала редуктора и
Механизм обкатать без нагрузки в течении 1 часа .
Стук и резкий шум недопускается.
После обкатки масло из редуктора слить и залить
масло индустриальное И-40А ГОСТ20799-75 в количестве 4 литров.
Остальные технические требования по СТБ1022-96
* Размеры для справок
Механизм подьема груза
МЕТАЛЛОК.dwg
Сварку выполнять по ГОСТ 5264-80.
Сварные швы зачистить.
H14 ; h14 ; ±0.5IT14.
* Размеры для справок.
Металлоконструкция опоры
МЕХАНИЗМ ПЕРЕДВИЖЕНИЯ ТЕЛЕЖКИ.dwg
Тормоз отрегулировать на момент 107 Н*м
Угловая несооснасть оси выходного вала редуктора и
электродвигателя не более 0
Радиальная несоосность оси выходного вала редуктора и
Механизм обкатать без нагрузки в течении 1 часа .
Стук и резкий шум недопускается.
После обкатки масло из редуктора слить и залить
масло индустриальное И-40А ГОСТ20799-75 в количестве 4 литров.
Остальные технические требования по СТБ1022-96
* Размеры для справок
Механизм передвижения
КОЗЛОВОЙ ОБЩИЙ ВИД.dwg
механизма подъема груза
Схема запасовки каната механизма
передвижения тележки
Техническая характеристика
Скорость подъема груза
Скорость передвижения крана
Скорость передвижения тележки
Максимальная высота подъема
Длина консоли левой (правой)
Группа режима работы механизма подьема груза М6
Группа режима работы механизма передвижения крана М4
Группа режима работы механизма передвижения тележки М3
КОЗЛОВОЙ ОБЩИЙ ВИД.cdw

механизма подъема груза
Схема запасовки каната механизма
передвижения тележки
Техническая характеристика
Скорость подъема груза
Скорость передвижения крана
Скорость передвижения тележки
Максимальная высота подъема
Длина консоли левой (правой)
Группа режима работы механизма подьема груза М6
Группа режима работы механизма передвижения крана М4
Группа режима работы механизма передвижения тележки М3
МЕТАЛЛОК.cdw

Сварку выполнять по ГОСТ 5264-80.
Сварные швы зачистить.
H14 ; h14 ; ±0.5IT14.
* Размеры для справок.
Металлоконструкция опоры
МЕХАНИЗМ ПОДЬЕМА ГРУЗА.cdw

Тормоз отрегулировать на момент 233 Н*м
Угловая несооснасть оси выходного вала редуктора и
электродвигателя не более 0
Радиальная несоосность оси выходного вала редуктора и
Механизм обкатать без нагрузки в течении 1 часа .
Стук и резкий шум недопускается.
После обкатки масло из редуктора слить и залить
масло индустриальное И-40А ГОСТ20799-75 в количестве 4 литров.
Остальные технические требования по СТБ1022-96
* Размеры для справок
Механизм подьема груза
Спецификация мет.docx
Гайка М30-6Н.5 (S46)
Металлоконструкция опоры козлового крана
крукович содержание.doc
Расчет механизма подъема .. .
Расчет механизма передвижения грузовой тележки .
Расчет металлоконструкции стойка-опоры .. ..
Охрана труда при эксплуатации козлового крана . ..
Список используемых источников
Приложение А Спецификация: общий вид механизм подъема механизм
передвижения грузовой тележки .. ..
Спецификация механизм подъем.docx
Болт М10-6g40.58 (S16)
Болт М10-6g55.58 (S16)
Болт М12-6g35.58 (S18)
Болт М20-6g100.58 (S30)
Болт М30-6g80.58 (S46)
Гайка М10-6Н.5 (S17)
Гайка М20-6Н.5 (S30)
Гайка М30-6Н.5 (S46)
Штифт 516 ГОСТ 3128-70
Редуктор Ц2-500 U=3242
Электродвигатель MTF411-6
P=15 кВт n=955 обмин
Спецификация механизм передвижения.docx
Механизм передвижения грузовой тележки
Болт М10-6g40.58 (S16)
Болт М10-6g55.58 (S16)
Болт М12-6g35.58 (S18)
Болт М20-6g100.58 (S30)
Болт М30-6g80.58 (S46)
Гайка М10-6Н.5 (S17)
Гайка М20-6Н.5 (S30)
Гайка М30-6Н.5 (S46)
Штифт 516 ГОСТ 3128-70
Редуктор Ц2-300 U=4134
Электродвигатель MTF211-6
P=105 кВт n=895 обмин
крукович записка.doc
КАНАТ МЕХАНИЗМ ПОДЪМА МЕХАНИЗ ПЕРЕДВИЖЕНИЯ СИЛА НАПРЯЖЕНИЕ БАЛКА.
В данном курсовом проекте представлена конструкция основных элементов крана козлового грузоподъемностью 10 т произведен расчёт его основных параметров.
В процессе работы произведен анализ существующих конструкций на мировом рынке проведен анализ существующих машин.
Разработаны мероприятия по охране труда.
Козловые краны применяют для обслуживания открытых складов и погрузочных площадок монтажа сборных строительных сооружений и оборудования промышленных предприятии обслуживания гидротехнических сооружений перегрузки крупнотоннажных контейнеров и длинномерных грузов. Козловые краны выполняют преимущественно крюковыми или со специальными захватами.
В зависимости от типа моста краны делятся на одно- и двухбалочные. Грузовые тележки бывают самоходными или с канатным приводом. Грузовые тележки двухбалочных кранов могут иметь поворотную стрелу.
Опоры крана устанавливаются на ходовые тележки движущиеся по рельсам. Опоры козловых кранов выполняют двухстоечными равной жёсткости или одну -жёсткой другую -гибкой(шарнирной).
Для механизмов передвижения козловых кранов предусматривают раздельные приводы. Приводными выполняют не менее половины всех ходовых колёс.
Обозначение по ГОСТ : Кран козловой ГОСТ 7352-75
Описание устройства и работы козлового двухконсольного крана
Козловые краны относятся к категории подъемных устройств мостового типа. Несущие элементы их конструкции опираются на подкрановый путь с помощью двух опорных стоек. Средний срок службы козловых кранов примерно 20 лет без учета режима работы и условий эксплуатации. Наработка на отказ – примерно 3000 циклов.
В статье мы расскажем о козловых кранах с полным электрическим приводом. По назначению их можно разделить на три группы. Первая группа – краны общего назначения со сравнительно небольшой высотой подъема (в среднем до 12 м). Применяют их для обслуживания открытых складских и перегрузочных площадок. Вторая группа – строительно-монтажные козловые краны для монтажа сборных строительных сооружений и оборудования промышленных предприятий. В третью группу входят конструкции специального назначения (обычно ККС) для обслуживания гидротехнических сооружений перегрузки крупнотоннажных контейнеров и длинномерных грузов.
В козловых кранах используются самые разные грузозахватные органы: однорогие и двурогие крюки грейферы (ковшовые захваты для навалочных грузов) грузоподъемные электромагниты серий М и ПМ специальные грузозахватные приспособления – клещевые захваты траверсы грузовые рамы спредеры.
В зависимости от конструкции моста козловые краны подразделяются на однобалочные и двухбалочные. Механизм подъема установлен на грузовой тележке которая перемещается по мосту. В зависимости от назначения кран оборудован одним или двумя механизмами подъема (основным и вспомогательным). Мощность привода и грузоподъемность вспомогательного механизма подъема как правило меньше мощности основного (главного) . Скорость таких механизмов подъема также различная – у вспомогательного обычно меньше. Есть однако конструкции козловых кранов в которых оба привода имеют одинаковые характеристики и работают синхронно. Тележки кранов такой конструкции выполняют подвесными монорельсовыми (грузоподъемность до 5 т реже – до 10 т) подвесными двухрельсовыми консольными и консольно-подвесными. Если мост крана однобалочный в качестве крановой тележки применяют электрические тали и в таком случае ее путь – это монорельсовая направляющая (двутавровая балка).
Сечение моста козлового крана может быть трубчатым коробчатым или решетчатым. Краны с двухбалочным мостом более металлоемкие но у них есть свои преимущества главное из которых – возможность установить тележки от мостовых кранов типовых конструкций выполненных по отработанной технологии. Грузовые тележки кранов с двухбалочным мостом иногда снабжают поворотной стрелой.
Обычно козловые краны изготовляют двухконсольными. Консоль – это часть моста выходящая за пределы подкранового пути (опоры). Наличие консолей расширяет рабочую зону кранов например дает возможность обслуживать с одного места несколько подъездных железнодорожных автомобильных путей и складских площадок.
Опоры козловых кранов выполняют двухстоечными равной жесткости или одну опору жесткой другую – «гибкой». В таких конструкциях шарнирное крепление устанавливается в узле остова крана. Это техническое решение позволяет компенсировать нагрузки перекоса в надопорных узлах остова крана. Изготовляют краны и с одностоечными опорами. Конструкции с однобалочными мостами и одностоечными опорами используют при совместной работе двух кранов.
Управление козловым краном осуществляется с пола или из кабины которая крепится к раме тележки или к мосту крана у опоры. Скорость его обычно не превышает 1 мс. Грузоподъемность козловых кранов общего назначения 32 32 т длина пролетов 10 32 м высота подъема груза 7 10 м (реже – до 12 м). Грузоподъемность строительно-монтажных кранов больше – до 400 т длина пролетов – до 80 м высота подъема – до 30 м.
Параметры козловых кранов специального назначения лучше – грузоподъемность до 900 т длина пролетов более 130 м высота подъема до 80 м. Например для обслуживания гидроэлектростанций используются краны грузоподъемностью 20 500 т с пролетом длиной 5 20 м. Такие подъемные механизмы иногда оснащают дополнительными грузоподъемными средствами – монтажной стрелой консольно-поворотным краном и т. п.
Контейнерные краны используются в основном для обслуживания крупных перегрузочных пунктов – морских портов контейнерных терминалов железнодорожных станций. Для работы в морском порту их оснащают подъемной консолью. Грузозахватным органом контейнерных кранов являются специальные грузовые рамы (спредеры) с автоматическими зацепами под фитинги и рым-узлы контейнеров. Особенность такой комплектации – то что кран оборудован специальной грузовой тележкой. Параметры козловых контейнерных кранов грузоподъемностью 20 и 32 т регламентирует ГОСТ 24390–99. Высота подъема этих кранов назначается в зависимости от условий штабелирования контейнеров т. е. ярусности складирования. Этот класс крановой техники заслуживает отдельной публикации.
Грейферные и магнитные краны распространены меньше чем краны общего назначения так как задачи по перегрузке навалочных грузов и грузов перемещаемых электрическими магнитами решаются в основном за счет применения съемных приводных грейферов и магнитов с независимым питанием и управлением. Однако необходимо помнить что краны этих типов должны быть оснащены специальными грузовыми тележками – грейферными или магнитными а захватные органы (грейфер или магнит) производитель должен поставлять как часть крана. Магнитный кран обязательно оснащают кабелеукладчиком и кабельным барабаном емкость которого соответствует высоте подъема магнита.
Управляемые с пола козловые краны грузоподъемностью до 10 т со скоростью передвижения до 1 мс не подлежат регистрации в органах
госгортехнадзора краны большей грузоподъемности допускаются к эксплуатации только после регистрации. Вместе с документами на регистрацию должна представляться справка о соответствии наземного пути нагрузкам устанавливаемого крана. Для выработавшего ресурс крана в составе документов на регистрацию должно быть представлено заключение специализированной организации о возможности его дальнейшей эксплуатации. Разрешение на пуск в работу козлового крана (после установки на новом месте после реконструкции ремонта или замены расчетных узлов металлоконструкций с применением сварки) должно быть получено в органе Госгортехнадзора зарегистрировавшем машину.
Козловые краны обязательно оснащают ограничителями рабочих движений для автоматического останова механизма подъема механизма передвижения крана независимо от скорости передвижения и механизма передвижения грузовой тележки. В комплект также должны входить автоматические ограничители перекоса противоугонные устройства (рельсовые захваты и т. п.) упругие буферные устройства. Краны группы режима не менее А6 и грузоподъемностью более 10 т по ИСО 43011 оборудуют регистраторами работы – так называемыми «черными ящиками».
Введена марочная система определяющая порядок допуска на кран специалистов чтобы свести к минимуму несчастные случаи при работе козлового крана в результате несогласованных действий машиниста и стропальщиков а также работников занятых на ремонте или обслуживании. Вводное устройство (защитная панель) крана оборудуется индивидуальным контактным замком с ключом. Ключ-марка предназначен для замыкания цепи управления и относится к приборам безопасности на нем выбит регистрационный номер крана.
Рисунок 1- устройство козлового крана
– пролет; 2 – кабина; 3 – крюковая подвеска; 4 – механизм передвижения крана; 5 – гибкая опора; 6-жесткая опора.
Расчет механизма подъема
Расчет механизма подъема козлового крана заключается в выборе схемы запасовки и расчета грузового каната двигателя редуктора муфт тормоза расчете барабана и крепления концов каната.
Исходные данные: грузоподъемность крана Q =10 т скорость подъема груза uг = 02 мc высота подъема H = 8 м группа режима работы механизма подъема груза – М6.
Механизм подъема груза установлен на грузовой тележке.
Согласно рекомендация по выбору полиспаста для грузоподъемности крана 10 тон кратность полиспаста должна быть 2 – 3 а сам полиспаст – сдвоенный. Принимаем механизм подъема со сдвоенным трехкратным полиспастом.
Рисунок 2 – схема запасовки грузового каната механизма подъема
Находим усилие в набегающей на барабан ветви каната по формуле
где: Q-номинальная грузоподъемность крана кг (Q=10000);
5- коэффициент учитывающий массу крюковой подвески;
z - число полиспастов в системе;
u – кратность полиспаста;
h0 – общий КПД полиспаста и обводных блоков;
где п – КПД полиспаста;
где бл – КПД блока (бл=0.98);
Подставляем значения в формулу
Расчетное разрывное усилие в канате при максимальной нагрузке на канат [1 стр. 53]
где zp – коэффициент использования каната[5.приложение 3] (для режима работы – М6; zp =56).
Выбираем канат двойной свивки типа ЛК – Р конструкции 6×19 (1+6+66)+1о.с по ГОСТ 2688-80. Диаметр каната d = 14 мм разрывное усилие в целом =108000 Н.
Фактический коэффициент использования каната:
zф=FкSб=10800017518=6.16
Требуемый диаметр барабана по средней линии навитого стального каната мм [1 стр. 59]
где: d – диаметр канатамм;
h1 – коэффициент зависящий от типа машины привода механизма и режима работы машины механизма.[5. приложение 6]
Принимаем диаметр барабана Dб=400 мм.
Dб – диаметр барабана;
t – шаг нарезки барабана;
h – глубина канавки;
Рисунок 3 – Параметры профиля канавок на барабане;
Требуемый диаметр блока мм
h2 – коэффициент зависящий от типа машины привода механизма и режима работы машины механизма. [5. приложение 6]
Требуемый диаметр уравнительного блока мм
h3 – коэффициент зависящий от типа машины привода механизма и режима работы машины механизма. [5. приложение 6]
По таблице III. 2.5[1] в зависимости от грузоподьемности и режима работы выбираем крюковую подвеску со следующими параметрами: тип d=15 мм; D=450 мм; b=270 мм; H=922 мм;
Длина каната навиваемого на барабан [1 стр. 60]
где: Н – высота подъема груза;
Uп – кратность полиспаста;
Dб – диаметр барабана по средней линии навитого каната;
Рабочая длина барабана м [1 стр. 60]
где: Lк – длина каната навиваемого на барабан;
t – шаг витка t = 0.017 [1.с.60 табл.2.8]
m – число слоев навивки;
dк – диаметр каната;
Dk – диаметр барабана;
j - коэффициент неплотности навивки;
Следовательно соотношение длины барабана и диаметра выбрано верно.
Толщина стенки литого чугунного барабана должна быть м [1 стр. 61]
где Dб.д – диаметр барабана по дну канавки;
Приняв в качестве материала барабана чугун марки СЧ 15 (dв=650 Мпа
[dсж]=130 МПа)[4 стр.32]. Найдем напряжения сжатия стенки барабана
где Sб – усилие в канате Н;
t – шаг витков каната на барабане м;
[dсж] – допускаемое напряжение сжатия для материала барабана;
Крепление конца каната к барабану.
Рисунок 4 – Крепление конца каната к барабану.
Натяжение каната в месте крепления на барабане [1 стр. 63]:
где f – коэффициент трения между канатом и барабаном;
a – угол обхвата барабана запасными витками каната;
При креплении конца каната на барабане накладкой
Сила растягивающая 1 болт [1 стр. 63]:
где f1- приведенный коэффициент трения между канатом и накладкой
– угол наклона боковой грани канавки
a – угол обхвата барабана витком крепления каната (а=2)
z – число болтов в накладке
Сила изгибающая болт [1 стр. 63]:
Суммарное напряжение в каждом болте [1 стр. 63]:
где k- коэффициент запаса надежности крепления каната(k> 15);
d1- внутренний диаметр резьбы болта м ; (d1 = 002м)
Статическая мощность двигателя кВт [1 стр. 35]
где: Q – номинальная грузоподъемность кг;
vг – скорость подъема груза мс;
h - КПД механизма(h = 085).
Рисунок 5 – кинематическая схема механизма подъема груза
-двигатель; 2-муфта; 3-редуктор цилиндрический двухступенчатый; 4-барабан;
Номинальная мощность двигателя принимается равной или несколько меньше статической мощности. Выбираем крановый электродвигатель с фазным ротором MTF – 411 – 6 У1 имеющим ПВ=40% номинальную мощность Рном= 15 кВт и частоту вращения nдв=955 обмин. момент инерции ротора Ip=0312 кгм2 .[1.с.315.табл.III.3.7]
Частота вращения барабана (обмин)
где: Uп – кратность полиспаста;
Dрасч – расчетный диаметр барабана м.
Общее передаточное число привода механизма
Выбираем редуктор цилиндрический двухступенчатый горизонталь-ный крановый типоразмера Ц2 – 500 с передаточным числом Uр =32.42 и мощностью на быстроходном валу при режиме работы механизма подъема груза – М6. Рр = 26.3 кВт [1.с.318табл.III.4.2].
Момент статического сопротивления на валу двигателя в период пуска Нм [1 стр. 22]
где z – число полиспастов в системе(z=2);
Dб – диаметр барабана м;
Uред – передаточное число редуктора;
б и пр – КПД барабана и привода (ориентировочно б=0.94 пр=0.9) [1.с.23табл.1.18 с.127 табл.5.1]
Номинальный момент передаваемый муфтой принимается равным моменту статических сопротивлений Тмном=Тс=400.71 Нм.
Номинальный момент на валу двигателя Нм [1 стр. 41]
где Рдв – мощность двигателя кВт;
nдв – частота вращения двигателя обмин;
Расчетный момент для выбора соединительной муфты Нм [1 стр. 41]
где к1 – коэффициент учитывающий степень ответственности механизма (к1=1.3) [1.стр.42табл.1.35].
к2 – коэффициент учитывающий режим работы механизма (к2=1.5) [1.стр.42табл.1.35].
Выбираем ближайшую по требуемому крутящему моменту упругую втулочно–пальцевую муфту с тормозным шкивом диаметром Dт=200 мм и наибольшим передаваемым крутящим моментом 500 Нм. момент инерции муфты Iм=0125 кгм2. [1.с.338табл.3.5.9].
Момент инерции ротора и муфты Нм
I=Iр+Iм=0.312+0.125=0.437 кгм2
Средний пусковой момент двигателя [1 стр. 35]
где ymax=MмахMном=480150 =3.2
ymin- минимальная кратность пускового момента электродвигателя:
Mмах- максимальный пусковой момент двигателя Нм
Mном- номинальный момент двигателя Нм
Время пуска при подъеме груза [1 стр. 35]
где d- коэффициент учитывающий влияние вращающихся масс привода
механизма (11 12) [1 стр.25]
Фактическая частота вращения барабана по формуле
Фактическая скорость подъема груза
где: uп – кратность полиспаста
Dрасч- расчетный диаметр барабана м
Проверяем фактическую скорость на точность условие удовлетворяется
Натяжение каната при опускании груза [1 стр. 53]
Момент статического сопротивления на валу двигателя для механизма подъема при опускании груза
Время пуска при опускании груза
Рисунок 6 - Усредненный график загрузки механизма подъема
Из графика усредненной загрузки механизма определим моменты развиваемые двигателем и время его пуска при подъеме и опускании груза в различные периоды работы механизма.Согласно графику за время цикла (подъем и опускание груза) механизм будет работать с номинальным грузом
Q=10000 кг – 2 разa.
7 Q=7000 кг – 4 разa.
17Q=1700 кг – 1 раз.
05Q=500 кг – 3 раза.
Таблица № 2. – Результаты расчета механизма подъема груза на перегрев
Наименование показателя
Результаты расчета при массе
поднимаемого груза кг
Натяжение каната у барабана при подъеме груза
Момент при подъеме груза
Время пуска при подъеме
Натяжение каната у барабана при опускании груза
Момент при опускании груза
Время пуска при опускании
Время установившегося движения
Н -номинальная высота подъема груза (Н=8 м)
Сумма времени пуска при подъеме и опускании груза за цикл работы механизма
Общее время включений двигателя за цикл
Среднеквадратичный момент [1 стр. 36]
где: tп – общее время пуска механизма в разные периоды работы с различной нагрузкой с;
M2сty – сумма произведений квадрата моментов статических сопротивлений движению при данной нагрузке на время установившегося движения при этой нагрузке.
t – общее время включения электродвигателя за цикл с.
Среднеквадратическая мощность двигателя кВт; [1 стр. 36]
где: Mср – среднеквадратичный момент преодолеваемый электродвигателем.
Во избежание перегрева электродвигателя необходимо чтобыразвиваемая двигателем среднеквадратичная мощность удовлетворяла условию
Рср Рном – условие соблюдается.
Момент статического сопротивления на валу двигателя при торможении механизма [1 стр. 22]
где: hт – КПД привода от вала барабана до тормозного вала;
U – общее передаточное число между тормозным валом и валом барабана.
Необходимый по нормам тормозной момент развиваемый тормозом выбираем из условия.
где кт – коэффициент запаса торможения (для тяжелого режима кт=2.0)
Выбираем тормоз ТКГ – 300 со следующими параметрами: тормозной момент 800 Н·м диаметром тормозного шкива Dт=300 мм. Регулировкой можно получить требуемый тормозной момент Мт=233.054 Н·м.[1.с.342]
У механизма подъема груза фактическое время торможения при опускании [1 стр. 23]
Зная фактическую скорость и требуемое ускорение замедления (=02 мс) при торможении мы можем провести регулировку тормоз и найти требуемый тормозной момент:
Для режима работы - М6 находим путь торможения механизма подъема груза
Находим время торможения в предположении что скорости подъема и опускания груза одинаковы:
Расчет механизма передвижения грузовой
Расчет механизма передвижения тележки заключается в подборе и расчете ходовых колес определении сопротивлений передвижению выбора двигателя редуктора муфты и тормоза.
Рисунок 7 – схема запассовки каната механизма передвижения тележки с канатным приводом.
Выбираем тележку с канатным приводом.
Рекомендуемый диаметр ходовых колес для грузоподъемности 5 10т равен 250 360 мм. Принимаем Dк=300 мм[1 таблица 1.29].
Коэффициент трения качения ходовых колес по рельсам с плоской головкой m=0.0006 м. Коэффициент трения в подшипниках качения ходовых колес f=0.02 [1 таблица 128].
Диаметр вала цапфы ходового колеса dк=(0.2 0.25)Dк мм ; dк=60 75 мм
Принимаем dк=70мм [1 стр. 33].
Общее сопротивление передвижению тележки Н[1 стр. 76]
где Wтр – сопротивление от трения;
Wукл – сопротивление от уклона рельсового пути;
Wв – сопротивление от ветровой нагрузки;
Wпров - сопротивление от провисания каната;
Сопротивление от трения [1 стр. 76]:
где кр – коэффициент учитывающий трение реборд о рельсы; кр=2.5 [1.с.68];
Gт – масса грузовой тележки кг;
Q – грузоподъемность крана кг;
m – коэффициент трения качения ходовых колес м;
f – коэффициент трения в подшипниках качения ходовых колес;
Сопротивление от уклона рельсового пути [1 стр. 76]
Сопротивление от ветровой нагрузки [1 стр. 76]
где р – распределенная ветровая нагрузка;
А – наветреваемая площадь груза; А10м2
где q – динамическое давление ветра. Если район установки крана неизвестен
принимают q = 450Па [1.с.21];
к – коэффициент учитывающий изменение динамического давления по высоте к = 1 т.к Н = 8м [1.с.21];
с – коэффициент аэродинамической силы с = 1.8 [1.с.21];
n – коэффициент перегрузки n = 1.1 [1.с.21];
Сопротивление от провисания каната [1 стр. 76]
где - масса свободного конца каната;
L – длина свободного конца каната;
h – высота провисания каната;
Усилие в канате набегающего на барабан [1 стр. 53]
об – КПД обводных блоков;
z – число обводных блоков; [1.с.54.табл.2.1]
Расчетное разрывное усилие в канате
где zp – коэффициент использования каната[5.приложение 3] (для режима работы – М3 zp =335).
Принимаем канат по ГОСТ 2688 – 80 двойной свивки типа ЛК-Р конструкции 6х19 (1+6+66)+1 О.С диаметром dk=13 мм имеющий при маркировочной группе проволок 1960 МПа разрывное усилие F=97000 Н.
Фактический коэффициент использования каната
zф=FкSб=970002685173=361>k=335
Требуемый диаметр барабана по средней линии навитого стального каната мм [1 стр. 59]
где: d – диаметр каната мм;
h1 – коэффициент зависящий от типа машины привода механизма и
режима работы машины механизма. [5. приложение 6]
Принимаем диаметр барабана Dб=260 мм.
Требуемый диаметр блока мм
h2 – коэффициент зависящий от типа машины привода механизма и режима работы механизма. [5. приложение 6]
где: Н – длина пролета крана с консолями;
z1 – число запасных ( неиспользуемых ) витков на барабане до места
крепления (z1=15 2);
z2 – число витков каната находящихся под зажимным устройством на
Толщина стенки литого чугунного барабана должна быть м [1 стр. 63]
где Dбд – диаметр барабана по дну канавки;
[dсж]=130 МПа) )[4 стр.32]. Найдем напряжения сжатия стенки барабана
t – шаг витков каната на барабане t = 0.017 [1.с.60 табл.2.8] м;
Рисунок 8 – Крепление конца каната к барабану.
Статическая мощность привода при h = 085 кВт: [1 стр. 35]
где W – общее сопротивление передвижению тележки Н;
vпер – скорость передвижения грузовой тележки мс;
Рисунок 9 –кинематическая схема механизма передвижения грузовой тележки
Выбираем крановый электродвигатель с фазным ротором MTF – 211 – 6У1 имеющим ПВ=15% номинальную мощность Рном= 105 кВт и частоту вращения nдв=895 обмин. момент инерции ротора Ip=0115 кгм2 .[2.с.14]
Общее передаточное число привода механизма
Выбираем редуктор цилиндрический двухступенчатый горизонтальный крановый типоразмера Ц2 – 300 с передаточным числом Uр =41.34 и мощностью на быстроходном валу при режиме работы – М3. Рр = 11.5 кВт [1.с.318табл.III.4.2].
Момент статического сопротивления на валу двигателя в период пуска
де z – число полиспастов в системе;
Номинальный момент передаваемый муфтой принимается равным моменту статических сопротивлений Ммном=М с=9981Нм.
Номинальный момент на валу двигателя Нм[1 стр. 41]
где к1 – коэффициент учитывающий степень ответственности механизма (к1=1.2) [1.с.42табл.1.35].
к2 – коэффициент учитывающий режим работы механизма (к2=1.1) [1.с.42табл.1.35].
Момент инерции ротора и муфты
где Iр – момент инерции ротора двигателя кгм2 (Iр=0.387);
Iм – момент инерции муфты кгм2 (Iм=0.125);
I= 0115+0.125=0.24 кгм2
ymin- минимальная кратность пускового момента электродвигателя (ymin=11 14)
Фактическое время пуска при передвижении тележки [1 стр.35]
механизма (11 12) [1 стр.25]
Проверяем фактическую скорость на точность
условие удовлетворяется
Момент статического сопротивления на валу двигателя при торможении механизма [1 стр. 22]
где кт – коэффициент запаса торможения (для режима работы – М3 кт=1.5).
Выбираем тормоз ТКГ – 300 со следующими параметрами: тормозной момент 500 Н·м диаметром тормозного шкива Dт=300 мм. Регулировкой можно получить требуемый тормозной момент Мт=10765Н·м.[1.с.342]
У механизма передвижения фактическое время торможения при опускании
Для режима работы - М3 находим путь торможения механизма передвижения тележки
Находим время торможения в предположении что скорости подъема и опускания груза одинаковы:
Замедление при торможении
Расчёт металлоконструкции крана
Рисунок 10 – опора козлового крана
-стойка-опора; 2-мост козлового крана; 3-стяжка; 4-грузовая тележка;
Рисунок 11 – расчетная схема стойки опоры
Определим силу действующую на опору:
F1- сила создаваемая массой тележки (с грузом) на 1 опору
где mг- максимальная грузоподъемность крана (mг=10 т);
mтел- масса грузовой тележки (mтел=035 т) [1 стр. 13];
F2- сила создаваемая массой крана на 1 опору;
где mкран – масса крана (mкран =35 т)[1 стр. 13];
Сила действующая на опору будет равна:
F=10153+175=27653 кН;
Определяем реакции в точке опоры стойки опоры. Для этого найдем суммарный момент относительно точки А:
Из расчетной схемы следует что Yb=
Для последующего определения сечения стойки опоры необходимо определить сжимающую силу N1. Для этого воспользуемся методом вырезания узлов и спроецируем все силы на ось Y :
Определим угол наклона стойки опоры:
Далее расчет ведем на устойчивость стойки опоры с выбором сечения
Стойка опоры состоит из двух швеллеров свариваемых между собой фасонками.
Рисунок 12 – сечение стойка опоры
Сечения стержней подбираются в зависимости от расчетных усилий. Сечение подбирается по формуле центрального сжатия из условия прочности и устойчивости
где - расчетное сопротивление.
- коэффициент продольного изгиба принимаемый по таблице 3 в зависимости от гибкости (задаемся =02);
- коэффициент условий работы ( );
Так как опора состоит из 2-ух швеллеров соединенных фасонками сечение 1-го швеллера будет равно:
Определяем площадь сечения 1-го швеллера:
Выбираем по сортаменту швеллер с прямыми полками [6 стр.46 таблица 4]:
Таблица 3 - Коэффициенты продольного изгиба центрально сжатых стержней в соответствии с кодексом установившейся практики
При гибкостях проверка устойчивости ведется по формуле Эйлера
Швеллер №16а с площадью поперечного сечения Атаб=195 см2. Радиус инерции .
Уточняем путем интерполяции коэффициент продольного изгиба
Сжимающие напряжения
Недонапряжение стержня составляет
Принимаем: коэффициент продольного изгиба и повторяем все расчеты.
- коэффициент продольного изгиба принимаемый по таблице 3 в зависимости от гибкости ;
Выбираем по сортаменту швеллер с прямыми полками из таблицы 4[6 стр.46]:
Швеллер №20 с площадью поперечного сечения Атаб=234 см2. Радиус инерции .
Швеллер №18а с площадью поперечного сечения Атаб=222см2. Радиус инерции .
Что допустимо следовательно расчет произведен верно.
Охрана труда при эксплуатации козловых кранов
Машинист грузоподъемных кранов обязан: знать требования знать инструкцию для машинистов грузоподъемных кранов а также инструкцию завода-изготовителя по монтажу и эксплуатации крана; знать безопасные способы строповки зацепки грузов и складирования; контролировать работу стропальщика и отвечать за действия прикрепленного к нему для прохождения стажировки ученика а также за нарушения требований должностной инструкции и инструкции завода-изготовителя по монтажу и эксплуатации крана; проверять наличие приборов и устройств безопасности на кране (концевых выключателей указателя грузоподъемности в зависимости от вылета стрелы сигнального прибора аварийного рубильника ограничителя грузоподъемности анемометра нулевой блокировки); проверять исправность съемных грузозахватных приспособлений и тары; сообщать о замеченных неисправностях железнодорожного пути ответственному за безопасное производство работ кранами; производить работы с использованием крана только по сигналу стропальщика[5].
Если стропальщик дает сигнал действуя вопреки инструкции то машинист по такому сигналу не должен производить требуемый маневр крана. За повреждения причиненные действиями крана вследствие выполнения неправильно поданного сигнала несут ответственность как машинист так и стропальщик подавший неправильный сигнал. Обмен сигналами между стропальщиком и машинистом должен производиться по установленному в организации порядку. Сигнал "Стоп" крановщик обязан выполнять независимо от того кто его подает;
определять по указателю грузоподъемности грузоподъемность крана для каждого вылета стрелы.
Перемещение груза можно производить только при отсутствии людей в зоне работы крана.
Указанные требования машинист должен выполнять также при подъеме и перемещении грейфера или грузоподъемного магнита; при погрузке и разгрузке вагонеток автомашин и прицепов к ним железнодорожных полувагонов и платформ убедиться в отсутствии людей на транспортных средствах; устанавливать крюк подъемного механизма над грузом так чтобы при подъеме груза исключалось косое натяжение грузового каната; при подъеме груза массой близкой к разрешенной грузоподъемности для данного вылета стрелы поднять его на высоту не более 200—300 мм чтобы убедиться в устойчивости крана и исправности действия тормозов после чего производить его подъем на нужную высоту;
при подъеме стрелы следует следить чтобы она не поднималась выше положения соответствующего наименьшему рабочему вылету; при подъеме и опускании груза находящегося вблизи стены колонны штабеля железнодорожного вагона автомашины станка или другого оборудования предварительно убедиться в отсутствии людей между поднимаемым грузом и указанными частями здания транспортными средствами или оборудованием а также в невозможности задевания стрелой или поднимаемым грузом стен колонн вагона и других препятствий.
Машинист грузоподъемного крана несет ответственность за нарушения требований Правил устройства и безопасной эксплуатации кранов; ему запрещается:
устанавливать кран под действующей линией электропередачи любого напряжения. Устанавливать кран или производить перемещение груза на расстоянии ближе 30 м от крайнего провода линии электропередачи машинист может только при наличии наряда-допуска подписанного главным инженером или главным энергетиком организации являющейся владельцем крана.
Работа крана в этом случае должна производиться под непосредственным руководством ответственного лица назначенного приказом по организации с указанием его фамилии; при наличии у крана двух механизмов подъема одновременная их работа. Крюк неработающего механизма должен быть всегда поднят в наивысшее положение; отключать приборы безопасности; производить подъем или опускание груза когда в зоне работы крана находятся люди;
допускать к обвязке или зацепке грузов лиц не имеющих удостоверения стропальщика а также применять грузозахватные приспособления без бирок или клейм.
Машинист в этих случаях должен прекратить работу краном и поставить в известность лицо ответственное за безопасное производство работ кранами;
поднимать или кантовать груз масса которого превышает грузоподъемность крана для данного вылета стрелы. Если машинист не знает массы груза то он должен получить в письменном виде сведения о массе груза у лица ответственного за безопасное производство работ кранами; опускать стрелу с грузом до вылета при котором грузоподъемность крана будет меньше массы поднимаемого груза;
производить резкое торможение при повороте стрелы с грузом; подтаскивать груз по земле рельсам и лагам крана при косом натяжении канатов а также передвигать железнодорожные вагоны платформы вагонетки или тележки при помощи крюка; поднимать крюком или грейфером груз засыпанный землей или примерзший к земле заложенный другими грузами укрепленный болтами или залитый бетоном; освобождать краном защемленные грузом съемные грузозахватные приспособления; поднимать железобетонные изделия с поврежденными петлями неправильно обвязанный груз находящийся в неустойчивом положении подвешенный за рог двурогого крюка а также в таре заполненной выше бортов;
укладывать груз на электрические кабели и трубопроводы а также на краю откоса или траншеи; поднимать груз с находящимися на нем людьми а также груз выравниваемый массой людей или поддерживаемый руками;
передавать управление краном лицам не имеющим прав на управление краном а также допускать к самостоятельному управлению учеников и стажеров без своего наблюдения за ними.
В данном курсовом проекте изложены:
) общие расчеты механизмов крана козлового двухкансольного грузоподъ- емностью 10 т скорость подъема груза 02 мc высота подъема груза 8 м пролет 16 м;
) методика выбора и проверки электродвигателей редукторов муфт и тормозов механизмов подъема груза и передвижения тележки;
) методика расчета металлоконструкции стойки опоры.
Список использованных источников
А.В. Кузьмин Ф.Л. Марон. Справочник по расчетам механизмов подъемно – транспортных машин. – 2-е изд. Перерад и доп.- Мн.: Выш. Шк. 1983 – 350с.
Справочник по кранам. Александров М.П. Гохберг М.М. том 12. -Л: Машиностроение1988.
Подъёмно-транспортные машины. Атлас конструкций. под ред. Александрова М.П. и Решетникова Д.Н.-М.:1987.
Конструирование узлов и деталей машин П.Ф. Дунаев. Высшая школа 1985
Правила устройства и безопасной эксплуатации грузоподъемных кранов – Мн.: ЦОТЖ 2006. – 219 с.
Технический кодекс установившейся практики ТКП 45-1.03-103-2009
(02250) «КРАНЫ ГРУЗОПОДЪЕМНЫЕ. КАПИТАЛЬНЫЙ
ПОЛНОКОМПЛЕКТНЫЙ И КАПИТАЛЬНОВОССТАНОВИТЕЛЬНЫЙ
РЕМОНТЫ». Правила выполнения. Министерство архитектуры и
строительства Республики Беларусь. Минск 2009.
Сопротивление материалов: Расчет.-проектировоч. работы: Учеб.
пособие для вузов Е.Ф. Винокуров А.Г. Петрович Л.И. Шевчук.-
Мн.:Выш. шк.1987.-227 с.:ил.