Взаимозаменяемость основных видов сопряжений




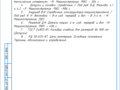
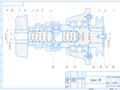
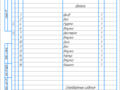
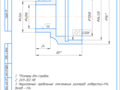
- Добавлен: 24.01.2023
- Размер: 615 KB
- Закачек: 0
Описание
Состав проекта
![]() |
![]() ![]() ![]() ![]() |
![]() ![]() ![]() ![]() |
![]() ![]() ![]() ![]() |
![]() ![]() ![]() ![]() |
![]() ![]() ![]() |
![]() ![]() ![]() ![]() |
![]() ![]() ![]() ![]() |
![]() ![]() ![]() ![]() |
![]() ![]() ![]() ![]() |
![]() ![]() ![]() |
![]() ![]() ![]() ![]() |
![]() ![]() ![]() ![]() |
![]() ![]() ![]() ![]() |
Дополнительная информация
Спецификация.spw

Зуб кол.cdw

Степень точности по
Колебание длины общей
Неуказанные предельные отклонения H14
Литература.cdw

Поле допуска резьбы М8.cdw

Содержание.doc
Расчет посадки для гладкого цилиндрического соединения
Расчет посадки подшипника качения
Расчет гладких калибров
Расчет полей допусков деталей резьбового соединения
Взаимозаменяемость и контроль зубчатых передач
Расчет размерной цепи методом полной взаимозаменяемости
Метод групповой взаимозаменяемости
Реферат на тему «Сущность сертификации и основные определения»
Сборочный чертеж узла
Чертеж зубчатого колеса
Чертеж калибра-скобы
Скоба.cdw

Пластинки припаять латунью
Покрыть нерабочие поверхности эмалью МЛ-165 ГОСТ12034-70
Твердость измерительных поверхностей калибров HRC 58 64
Муфта.cdw

Неуказанные предельные отклонения размеров отверстий-H14
Узел 18.cdw

2Схема полей допуска подшипника.cdw

пояснительная записка.doc
- внутренний диаметр втулки 6
- номинальный диаметр сопрягаемых поверхностей
- внутренний диаметр муфты 4
- коэффициент трения при продольном смещении детали
Материал муфты - Сталь20 материал шестерни- 40Х
- коэффициент Пуассона;
1 Наименьший расчетный натяг:
Соединение 4-7 нагружено крутящим моментом следовательно
Поправка к рачетному натягу:
исходя из условий сборки принимаем: t=0;
2 Наименьший функциональный натяг
3 По величине NminF подберем ближайшую посадку:
4 Проверка прочности соединяемых деталей при Nmax:
) давление на поверхности контакта муфты и шестерни
) допустимое давление на поверхности муфты
) допустимое давление на поверхности шестерни
Таким образом запас прочности муфты:
запас прочности шестерни:
Выбранная посадка обеспечивает необходимую прочность соединения.
Строим схему полей допусков выбранной посадки-ф45H7s6
Расчет посадки подшипника качения: 3
Посадки подшипников качения на вал и в корпус выбирают в зависимости от типа подшипника условий по эксплуатации величины и характера действующих на него нагрузок и вида нагружения колец по ГОСТ 3325-85.
В моем случае дан подшипник 6-310 по ГОСТ 8338-75:
1. Выбор посадок на вал и в корпус.
Подшипник 3 имеет местно нагруженное внешнее кольцо и циркуляционно нагруженное внутреннее.
Местно-нагруженные кольца должны иметь соединения с зазором или незначительный натяг между кольцом и сопрягаемой деталью.
Циркуляционно- нагруженные кольца должны иметь неподвижное соединение с сопрягаемой деталью.
При циркуляционном нагружении колец подшипников посадки на вал и в корпус выбирают по величине Рr - интенсивности радиальной нагрузки на посадочной поверхности которую определяют по формуле:
Нагрузка с умеренными толчками и вибрацией перегрузка до 150% осевой нагрузки на опору нет.
- динамический коэффициент посадки зависящий от характера нагрузки;
- коэффициент учитывающий степень ослабления посадочного натяга (вал сплошной);
- коэффициент неравномерности распределения радиальной нагрузки Fr равен 1 так как Fa=0;
Так как класс точности подшипника 6 то заданным условиям посадки в корпус соответствует поле допуска js6. Корпус разъемный поэтому для наружнего кольца выбираем посадку ф110H7.
2. Выбор предельных отклонений размеров посадочных диаметров подшипника по ГОСТ 520-71:
dm=50 ESk=0; EJk= -0.010
Dm=110 esk=0; eik=-0.013mm
3. Выбор предельных отклонений размеров посадочных поверхностей сопрягаемых с кольцами подшипников качения:
d=50js6: es=+0.008 e
D=110H7: EJ=0 ES=+0.035
Предельные зазоры в соединении наружнего кольца с отверстием корпуса:
Smax= ES-eik= 0.035-(-0.013)=0.048mm.
Предельный натяг в соединении внутреннего кольца с валом:
Nmax= es-EJk= 0.008-(-0.010)=0.018mm.
Nmin= ei-ESk= -0.008-0= -0.008mm.
5 Строим схему полей допусков
Расчёт гладких калибров для контроля детали 4 соединения 4-7
1.Предельные размеры вала ф45s6:
Наибольший - dmax= d+es= 45+0.059=45.059mm
Наименьший - dmin= d+ei= 45+0.043=45.043mm
2. Шестому квалитету точности соответсвуют значения допусков и отклонений калибров по ГОСТ 24853-81:
Z1 mkm Y1 mkm Hmkm Hp mkm
где y1 - допустимый выход размера изношенного проходного калибра для отверстия за границу поля допусков ;
z1 - отклонение поля допуска на изготовление проходного калибра для отверстия относительно наибольшего предельного размера;
H1 - допуск на изготовление калибров для отверстий;
Нр - допуск на изготовление контрольного калибра для отверстия;
3 Определение предельных и исполнительных размеров калибров-скоб для контроля валов ф45s6.
ПРисп. = ПРmin(+H1 ) = 45.049+0.007
Непроходная сторона:
HEисп. = HEmin(+H1) = 45.039+0.007
4 Основные параметры калибра скобы
Dномmm D1mm Hmm Bmm Smm lmm hmm
5 Схема полей допусков калибров
Расчет полей допусков деталей резьбового соединения.
1 Определение основных параметров резьбы.
Эксплуатационные требования к резьбам зависят от их назначения. Требования надежности долговечности и свинчиваемости без подгонки независимо изготовленных резьбовых соединений при сохранении эксплуатационных качеств соединения являются общими для всех резьб.
Основные параметры резьбы М8:
d=D d1=D1 d2=D2 P H H8 H6 H4
где d(D) - наружный диаметр резьбы мм;
d1(D1) - внутренний диаметр резьбы мм;
d2(D2) - средний диаметр резьбы мм;
- уголь профиля резьбы град;
Н - высота исходного треугольника профиля мм;
По назначению резьба М8 крепежная служит для фиксации шкифа 1 с помощью болта 18. Резьбовое соединение выполняется по среднему классу точности рекомендуемые поля допусков на диаметры резьбы:
гайки - 6Н; болта - 6g. (ГОСТ 16093-81)
Обозначение резьбы – М8-6Н6g где
М - метрическая резьба;
- наружний диаметр резьбы d=D мм;
Н - поле допуска на средний (D2) и внутреннийт(D1) диаметры резьбы гайки;
g - поле допуска на средний (d2) и наружний (d) диаметры болта.
Допуски на наружний диаметр резьбы гайки и внутренний диаметр резьбы болта не устанавливаются.
Длина свинчивания резьбы - длинная шаг резьбы - крупный Р=175мм.
2 Определение отклонений на диметры резьбовых деталей.
Отклонения определяются по ГОСТ 16093-81:
Диаметр Отклонение Наружная Внутренняя
Верхнее ES es -0034 -
Нижнee EJ ei -0299 0
Верхнее ES es -0.034 +0.2
Нижнее EJ ei -0.184 0
Верхнее ES es -0.034 +0.335
d2max= d2+esd2= 6.863+(-0.034)= 6.829мм.
Предельные размеры резьбы.
Диаметры Обозначения Численное значение мм
d2max(D2max) 6.829 6.863
d2min(D2min) 6.679 6.063
d1max(D1max) 6.072 6.441
d1min(D1min) - 6.106
3 Определение предельных размеров резьбы.
Dmax - не определяется.
D2max= D2+ESD2=6.863+0.2=7.063мм.
4 Схема расположения полей допусокв резьбы.
Рис. 4. Поля допусков резьбы строятся относительно номинального профиля. Вверх от профиля окладываются положительные отклонения а вниз - отрицательные.
5 Методы и средства контроля цилиндрических резьб
Точность резьбы можно контролировать дифференцированным ( контроль каждого параметра отдельно) и комплексным методами. Дифференцированный метод контроля резьбы очень трудоемок поэтому его применяют для точных резьб. Иногда по результатам контроля отдельных параметров судят о комплексном параметре. Комплексный контроль резьбы выполняют либо с помощью предельных калибров либо с помощью проекторов и шаблонов с предельными контурами. В систему калибров входят рабочие гладкие и резьбовые проходные и непроходные калибры и контркалибры для проверки и регулирования рабочих резьбовых скоб и колец.
Взаимозаменяемость и контроль зубчатых передач.
Параметры зубчатого колеса 7:
Диаметр делительной окружности: d= m*z= 1.75*45= 60мм;
1 Выбор степени точности.
Степень точности колес и передач устанавливают в зависимости от требований к кинематической точности плавности передаваемой мощности а также окружной скорости колес. Для данного колеса примем 6-8 степени точности. Рассматриваемое зубчатое колесо относится к колесам общего назначения (машиностроения). Назначим 8 степень точности по всем трем нормам.
Системой допусков на зубчатые передачи устанавливают гарантированный боковой зазор. Для удовлетворения требований различных отраслей промышленности предусмотрено шесть видов сопряжений определяющих боковой зазор A B C D E H. Выберем вид сопряжения зубчатого колеса - В (нормальный зазор) которому соответствуют 3-11 классы точности и соответствующий вид допуска - b.
Обозначение зубчатой передачи: 8- B ГОСТ1643-81.
2 Выбор контролируемых параметров их численные значения. Средства измерения.
Для зубчатых колес устанавливаются три нормы точности: кинематическая плавность работы и контакта зубьев.
Нормы кинематической точности важны для делительных и планетарных передач. Нормы плавности работы колеса имеют наибольшее значение при силовых высокоскоростных передачах. Нормы контакта зубьев важны для
тяжелонагруженных тихоходных передач.
ГОСТ 1643-81 предусматривает несколько вариантов показателей точности колес. Эти варианты равноправны.
Для 8 степени точности выберем контролируемые параметры:
) Нормы кинематической точности:
- допуск радиального биения (по ГОСТ 1643-81):
) Нормы плавности работы:
- погрешность шага зацепления:
fpt=(+-)26мкм - отклонение основного шага зуба;
=20 - угол профиля исходного контура;
fpb= (+-)0026 *cos20= (+-)00244мм;
) Нормы полноты контакта зубьев:
Полнота контакта определяется суммарным пятном контакта:
а) по высоте зуба - допуск по высоте не менее 40% при ширине зубчатого колеса до 40мм;
б) по длине зуба - допуск по длине не менее 50% при ширине зубчатого колеса до 40мм.
Средства измерения цилиндрических зубчатых колес.
Измеряемый Средства измерения
элемент специальные универсальные
Кинематическая и Приборы для контроля
циклическая кин-ой погрешности -
погрешности волномеры;
Накопленная Прибор для поэлем- го Теодолиты лимбы
погрешность шага контроля приборы для делительные
контроля накопленной диски - все с при
погрешности шага; мен. рыч.-чувств.
Измерительное Приборы для контроля Щтихмассы
межосевое рас изм- го межосевого
стояние расстояния;
Радиальное би Биениемеры Плита с центрами
ение зубчатого ролики и рыч.-
Основной шаг Шагомеры для основного Штангенциркуль
шага микрометрический
Профиль зубьев Эвольвентометры Пректоры боль-
Суммарное пятно Контрольно- обкатные Контрольные при
контакта станки способления в ра
бочем корпусеНаправление Ходомер Ролик и чувств.
зуба прибор на стойке
Толщина зубьев Зубомеры нормалемеры Два ролика и
длина общей микрометр
нормали штангенциркуль
Схемы приборов для контроля параметров зубчатых колес рис. 5.1 - 5.4
Рис.5.1 Прибор для контроля кинематической
погрешности зубчатого
Рис.5.2 Прибор для контроля межосевого расстояния
Рис.5.3 Прибор для контроля колебания
Рис.5.4 Прибор для контроля отклонения шага
Расчет размерной цепи методом полной взаимозаменяемости.
По условию задания рассматривается размерная цепь А-А.
Звенья размерной цепи:
А2А4 - увеличивающее;
Число увеличивающих звеньев m=3;
Число уменьшающих звеньев n= 1;
Известными являются номинальные размеры всех звеньев цепи и предельные отклонения исодного звена.
Применим способ допусков одного квалитета когда все составляющие цепь размеры могут быть выполнены с допуском одного квалитета и допуски составляющих размеров зависят от их номинального значения.
Определим номинальный размер замыкающего звена:
А0= (А2+А3+А4)-А1= (19+10+19)-47=1мм;
А0m А0max = 1.5мм следовательно предельные отклонения :
Тогда допуск для исходного звена:
TA0 = ES(А0) - EI(А0) = 0-500 = 500мкм;
Для способа одного квалитета точности количество единиц допуска определяется по формуле:
аср = TA0 (i1+i2+i3+i4)=
0(2*1.31+1.56+0.9+)=98.42=>100;
По значению аср выберем ближайший квалитет - 11.
Назначаем допуски и отклонения на составляющие звенья
по выбранному квалитету точности и номинальным размерам согласно ГОСТ25346-82:
ТА1=0160мм ТА2=0120мм ТА3=0100мм ТА4=0120мм;
ТА0=500мкм >= ТА1 +ТА2 +ТА3 +ТА4 = 500мкм;
А2=А4=19-0120 ; А3=10-0100;
Для звена А1 предельные отклонения определим по формуле:
ESA0= ESA1 - (EJA2+EJA3+EJA4);
0= ESA1- (-120-100-120); ESA1= 500-340=160мкм;
= EJA2 - 0; EJA2 = 0мкм;
Условие ТА0= ТАi= 160+120+100+120=500мкм - выполняется.
Результаты расчета - табл.6:
Групповая взаимозаменяемость.
Метод групповой взаимозаменяемости применяют когда средняя точность размеров цепи очень высокая и экономически неприемлимая. Сущность метода групповой взаимозаменяемости заключается в изготовлении деталей со сравнительно широкими технологически выполнимыми допусками выбираемыми из соответствующих стандартов сортировке деталей на равное число групп с более узкими групповыми допусками и сборке их по одноименным группам. Такую сборку называют селективной.
При селективной сборке наибольшие зазоры и натяги уменьшаются а наименьшие увеличиваются приближаясь с увеличением числа групп сортировки к среднему значению зазора или натяга для даннй посадки.
Соединение ф172 Н9е9
Точность эксплуатационного соединения TSэкс= 50мкм
Допуски и предельные отклонения размеров деталей соединения ( ГОСТ 25347-82):
отклонения отверстия: EJ = 0 ES = +100мкм;
Определим наибольшие и наименьшие предельные размеры вала и отверстия:
TD=TA= ES-EJ= 100мкм;
Определим наибольшие и наименьшие предельные зазоры:
Определим число групп отверстия и вала для обеспечения заданной точности соединения:
nгр= TSTSэкс= 20050= 4;
Групповой допуск деталей при селективной сборке:
ТАгр=ТВгр=1004= 25мкм;
Составим карту сортировщика (табл.7) и вычертим схему полей допусков разделив поля допусков отверстия и вала на требуемое число групп. Группы пронумеруем. Рис.7.
ОСНОВНЫЕ ПОНЯТИЯ В ОБЛАСТИ СЕРТИФИКАЦИИ
В условиях рыночной экономики когда продукцию и услуги представляют предприятия различных форм собственности наиболее эффективным способом гарантии качества продукции и услуг а точнее соответствия их установленным требованиям является сертификация.
Это следует из сущности самого понятия сертификации и той организационной системы которая создается для ее реализации. Понятие "сертификация соответствия" было сформулировано специальным Комитетом Совета Международной Организации по стандартизации (ИСО) по вопросам сертификации (СЕРТИКО) и включено в Руководство № 2 ИСО выпущенное в ноябре 1982 г. Пересмотренное Руководство ИСОМЭК 2 вышедшее как совместное издание ИСО и МЭК (Международная электротехническая комиссия) без существенных изменений воспроизводит определение этого понятия Международная организация по стандартизации (ИСО) — International Organization for Standartization - создана в 1947 году. Её целью является содействие стандартизации в мировом масштабе. В состав ИСО входят национальные органы по стандартизации. ИСО разрабатывает свои стандарты и другие документы на продукцию терминологию классификацию организационную деятельность.
Документ "Руководство 2 ИСОМЭК: 1996 Стандартизация и смежные виды деятельности — Общий словарь" (Русская версия —1999 г.) содержит следующие формулировки основных понятий относящихся к сертификации.
Оценка соответствия — любая деятельность связанная с прямым или косвенным определением того что соответствующие требования выполняются.
Третья сторона — лицо или орган признаваемые независимыми от участвующих сторон в рассматриваемом вопросе.
Аккредитация — процедура посредством которой признанный орган официально признает компетентность органа или лица выполнять конкретные работы
Испытание - техническая операция заключающаяся в определении одной или нескольких характеристик данной продукции процесса или услуги в соответствии с установленной процедурой.
Испытания типа — испытания на соответствие продукции на оснвое одного или нескольких представительных образцов данной продукции.
Сертификация - процедура посредством которой третья сторона документально удостоверяет что продукция процесс или услуга соответствуют заданным требованиям.
Лицензия (по сертификации) - документ выданный в соответствии с правилами системы сертификации посредством которого орган по сертификации наделяет лицо или орган правом использовать сертификаты или знаки соответствия для своей продукции процессов или услуг согласно правилам соответствующей системы сертификации.
Сертификат соответствия — документ выданный в соответствии с правилами системы сертификации и удостоверяющий то что должным образом идентифицированная продукция процесс или услуга соответствуют конкретному стандарту или другому нормативному документу.
Знак соответствия (по сертификации) — защищенный в установленном порядке знак применяемый или выданный в соответствии с правилами системы сертификации и указывающий что соответствующая продукция процесс или услуга соответствует конкретному стандарту или другому нормативному документу.
Во многих странах национальные системы сертификации создавались с целью повышения качества экспортной продукции. На начальном этапе своего развития сертификация в нашей стране пошла по этому пути.
3Поле допуска калибра-скобы.cdw

Групповая взаимозаменяемость.cdw

Схема соединения 4-7.cdw

Рекомендуемые чертежи
- 01.07.2014
- 20.08.2014