Определение допусков основных видов соединений и решение размерных цепей





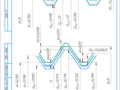
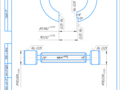
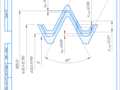
- Добавлен: 24.01.2023
- Размер: 364 KB
- Закачек: 0
Описание
Состав проекта
![]() |
![]() ![]() ![]() ![]() |
![]() ![]() ![]() ![]() |
![]() ![]() ![]() |
![]() ![]() ![]() |
![]() ![]() ![]() ![]() |
![]() ![]() ![]() ![]() |
![]() ![]() ![]() ![]() |
![]() ![]() ![]() ![]() |
![]() ![]() ![]() ![]() |
![]() ![]() ![]() ![]() |
![]() ![]() ![]() |
![]() ![]() ![]() ![]() |
![]() ![]() ![]() ![]() |
![]() ![]() ![]() ![]() |
Дополнительная информация
поля допусков калибров.cdw

допусков калибров для контроля
БГТУ им. В.Г. Шухова
подшипник.cdw

таблица2.docx
Характер действия на А0
Вторая (проектная задача)
Ec(Аj)= Ei(Аj)+ TАj2
Курсовая.doc
Кафедра технологии машиностроения
«Метрология стандартизация и сертификация»
Задание №1. Расчет предельных размеров элементов гладкого цилиндрического соединения и калибров . ..3
Задание №2. Определение допусков и предельных размеров шпоночного соединения 6
Задание №3. Определение допусков и предельных размеров шлицевого соединения .7
Задание №4. Выбор посадки подшипника качения на вал и в корпус .8
Задание №5. Определение предельных размеров деталей резьбового соединения 10
Задание №6. Расчет сборочных размерных цепей 12
Расчет предельных размеров элементов гладкого цилиндрического соединения и калибров
Усвоить основные понятия и термины а также научиться определять предельные размеры зазоры (натяги) и допуски.
Приобрести навыки пользования стандартами для определения предельных отклонений.
Научиться правильно оформлять чертежи с обозначением посадок допусков и предельных отклонений.
Освоить методику расчета предельных калибров для контроля гладких цилиндрических соединений.
Расчет гладкого цилиндрического соединения
- посадка с зазором в системе вала.
- переходная посадка в системе вала.
- посадка с натягом в системе вала.
Расчет для посадки с натягом 80 в системе вала
По ГОСТ 25347-82 определим предельные отклонения отверстия и вала:
Расчет для посадки с зазором 80 в системе вала
Расчет для переходной посадки 80 в системе вала
Вычислим предельные размеры отверстия и вала:
Dmax=D+ES=80+0027=80027 (мм)
dmin=D+ei=80-0035=79965 (мм).
Определим величину допуска отверстия и вала:
Td= dmax- dmin=80-79965=0035 (мм).
Найдем величину наибольшего предельного зазора натяга и допуска посадки:
T(SN)= Smax + Nmax =0062+0027=0089 (мм).
Так как посадка переходная то определим вероятность получения зазоров и натягов в соединении а также вероятные их величины.
Для заданной посадки 80 зазор может быть в пределах от 0 до 62 мкм натяг - от 0 до 27 мкм. Допуск посадки составляет 89 мкм.
Считаем что рассеивание размеров отверстия и вала а также зазоров (натягов) подчиняется закону нормального распределения и допуск деталей равен полю рассеивания т.е. T=6.
Учитывая принятые условия получим:
Среднее квадратическое отклонение для распределения зазоров и натягов в посадке:
При средних значениях размеров отверстия Dm и вала dm получаем
S= Dm- dm=80-79983=0017 (мм)=17 (мкм).
Вычислим вероятность того что значения зазора находятся в пределах от 0 до 17 мкм т.е. найдем площадь ограниченную линией симметрии кривой Гаусса и ординатой расположенной в 17 мкм от линии симметрии.
Вероятность получения зазора определим с помощью интегральной функции вероятности Ф(z) - функции Лапласа где z - предел интегрирования
Пользуясь таблицей значений интегралов Ф(z) находим Ф(z)= Ф(227)=04394.
Вероятность получения зазоров в соединении: 05+04394=0.9394 или 9394%.
Вероятность получения натягов: 1-09394=00606 или 606%.
Вероятный зазор равен: -17+3 =-17+3·11=16 мкм.
Вероятный натяг равен: -17-3=-17-3·11=-50 мкм.
Вычислим предельные и исполнительные размеры гладких рабочих калибров для контроля годности отверстия D=80 мм и допуском Js8 а также вала d=80 мм и допуском h7.
1.По ГОСТ 24853-81 определим числовые значения величин необходимых для расчета калибров:
a)для калибр-пробки H=6 мкм; Z=8 мкм; Y=8 мкм;
b)для калибр-скобы H1=6 мкм; Z1=5 мкм; Y1=4 мкм.
2.В соответствии с вышеприведенными формулами определяем предельные размеры калибров:
НЕmin=Dmax-H2=80027-0003=80024 (мм).
НЕmin=dmin-H12=79965-0003=79962 (мм).
3.Определим исполнительные размеры калибров:
ПРИСП =79984-0006 (мм);
НЕИСП =8003-0006 (мм).
ПРИСП =79992+0006 (мм);
НЕИСП =79962+0006 (мм).
Определение допусков и предельных размеров шпоночного соединения
В соответствии с заданным типом шпоночного соединения определить допуски и предельные размеры всех элементов соединения а также представить схему расположения полей допусков по ширине шпонки и сборочный чертеж шпоночного соединения.
Расчет шпоночного соединения
Шпонка призматическая исполнение В соединение свободное. Диаметр вала - 30 мм длина шпонки - 50 мм.
Определим номинальные размеры элементов шпоночного соединения по ГОСТ 23360-78: b=8 мм; h=7 мм; t1=40 мм; t2=33 мм; (d-t1)=26 мм; (d+t2)=333 мм.
Определим допуски непосадочных размеров по ГОСТ 23360-78:
высота шпонки h=7h11=7-0090 мм;
глубина паза вала t1=40+02 мм;
глубина паза втулки t2=33+02 мм;
длина паза вала под шпонку l1=50H15=50+12 мм.
Определим допуски на посадочные размеры элементов шпоночного соединения по ширине шпонки b по ГОСТ 23360-78:
ширина шпонки 8h9=8-0036 мм;
ширина паза вала 8H9=8+0036 мм;
ширина паза втулки 8D10=6 мм.
Определение допусков и предельных размеров шлицевого соединения
Для прямобочного шлицевого соединения с заданным числом зубьев номинальными размерами и характером соединения выбрать способ центрирования.
Определить допуски и предельные размеры всех элементов соединения. Построить схему расположения полей допусков посадок и представить чертеж шлицевого соединения.
Расчет прямобочного шлицевого соединения
Исходные данные: неподвижное шлицевое соединение с номинальными размерами 83642.
По ГОСТ 1139-80 находим размер b=7мм d1=335мм. В данном случае целесообразно выбрать центрирование по наружному диаметру D. Посадки выбираем по ГОСТ 1139-80:
для размера d (не центрирующий диаметр) - .
Обозначение шлицевого соединения:
По ГОСТ 25347-82 определим предельные отклонения диаметров:
отверстие 42H7=42+0025;
отверстие 36H11=36+0160;
ширина впадины втулки 7F8=7;
ширина зуба вала 7f8=7.
Выбор посадки подшипника качения на вал и в корпус
В соответствии с исходными данными выбрать посадки для соединения внутреннего кольца подшипника с валом и наружного кольца с корпусом. Представить схемы расположения полей допусков деталей соединения а также чертежи посадочных поверхностей вала корпуса и сборочного узла.
Выбор посадки подшипника качения
условное обозначение подшипника - 317;
радиальная нагрузка Fr=2000 Н.
Внутреннее кольцо испытывает местное нагружение наружное кольцо - циркуляционное. Режим работы - перегрузка до 150%.
По условному обозначению подшипника качения определим его основные размеры (ГОСТ 8338-75):
диаметр отверстия внутреннего кольца d=85 мм;
диаметр наружного кольца D=180 мм;
ширина подшипника B=41 мм;
радиус закругления фаски r=4 мм;
рабочая ширина посадочного места b=B-2·r=41-2·4=33 мм.
По ГОСТ 520-89 определим предельные отклонения на изготовление колец подшипника:
для d=85 (внутреннее кольцо) ES=0; EI=-15 мкм;
для D=180 (наружное кольцо) es=0; ei=-20 мкм.
Выбираем посадку циркуляционно нагруженного внутреннего кольца подшипника по интенсивности радиальной нагрузки PR на посадочную поверхность вала которую рассчитываем по формуле:
где k1 - при перегрузке до 150% k1=1;
k2 - вал сплошной k2=1;
k3 - подшипник однорядный без осевой нагрузки на опору k3=1.
Такой интенсивности радиальной нагрузки соответствует допуск вала jS6.
Для наружного кольца подшипника испытывающего циркуляционное нагружение по ГОСТ 3325-55 назначаем допуск посадочной поверхности отверстия в корпусе H6.
Определим предельные отклонения размеров вала и отверстия корпуса по ГОСТ 25347-82:
для вала 85 jS6 es=+0011 мм; e
для отверстия корпуса 180 H6 ES=+0025 мм; EI=0.
По ГОСТ 520-89 определим шероховатость поверхности посадочных мест вала и отверстия корпуса. Для посадочной поверхности вала и отверстия корпуса Ra - не более 125 мкм для торцов заплечиков валов и отверстий корпусов Ra - не более 25 мкм.
Вычислим допуски формы (овальность и конусообразность) посадочных мест вала и отверстия корпуса.
Для посадочной поверхности вала:
для посадочной поверхности отверстия корпуса:
TD=05·0025=00125 мм.
По ГОСТ 520-89 определим допускаемое торцовое биение заплечиков вала и отверстия корпуса.
для заплечиков вала Δ=0012 мм;
для заплечиков отверстия корпуса Δ=0030 мм.
Определение предельных размеров деталей резьбового соединения
Усвоить основные параметры метрической резьбы и их обозначения на чертеже.
Приобрести навыки пользования стандартами для определения предельных диаметров болта и гайки и правильно производить их расчет.
Научиться оформлять чертежи с обозначением полей допусков и посадок резьбового соединения.
Расчет предельных размеров деталей резьбового соединения
Задано резьбовое соединение M241 - 6H6h. По ГОСТ24705-81 определим номинальные размеры основных элементов резьбового соединения:
наружный диаметр болта и гайки d=D=24 мм;
средний диаметр болта и гайки d2=D2=2335 мм;
внутренний диаметр болта и гайки d1=D1=23918 мм;
угол профиля резьбы α=60°.
Определим предельные отклонения диаметров болта и гайки резьбы по ГОСТ16093-81.
Предельные отклонения болта при допуске 6h:
для d2 d d1 верхнее отклонение es=0;
для d2 нижнее отклонение e
для d нижнее отклонение e
для d1 нижнее отклонение не регламентируется.
Предельные отклонения гайки при допуске 6H:
для D2 D D1 нижнее отклонение EI=0;
для D2 верхнее отклонение ES=+170 мкм;
для D верхнее отклонение не регламентируется;
для D1 верхнее отклонение ES=+236 мкм.
Вычислим предельные размеры болта и гайки:
D1 min= D1 + EI = 23918+0=23918 мм.
Определим величины зазоров в соединении:
по наружному диаметру:
по среднему диаметру:
Smin= D2 min - d2 max= 2335-2335=0.
Расчет сборочных размерных цепей
Выполнить расчет заданной размерной цепи способом допусков одного квалитета двумя методами - максимума-минимума и теоретико-вероятностным.
Расчет сборочной размерной цепи
Вал редуктора установлен на подшипниках качения 6-217. Предельные отклонения на изготовление подшипников качения по ширине принимаем по ГОСТ 520-89 в зависимости от диаметра внутреннего кольца который в данном случае равен d=85 мм.
Имеем верхнее отклонение по ширине колец подшипника равное 0 и нижнее отклонение равное -200 мкм. Тогда при заданной ширине В=28 мм подшипника 6-217 звенья А4 и А8 имеют размер А4= А8= мм. Остальные составляющие звенья размерной цепи имеют следующие номинальные значения: А1=270 мм; А2=5 мм; А3=25 мм; А5=20 мм; А6=60 мм; А7=102 мм; А9=6 мм; А10=8мм.
Замыкающее звено А0 имеет предельные отклонения: верхнее ES(А0)=+680 мкм; нижнее EI(А0)=+060 мкм.
Предварительно рассчитаем следующие данные:
а)номинальный размер замыкающего звена:
где - сумма номинальных размеров увеличивающих звеньев;
- сумма номинальных размеров уменьшающих звеньев.
б)допуск замыкающего звена:
в)среднее отклонение поля допуска замыкающего звена:
г)допуск на ширину колец подшипников качения:
д)среднее отклонение поля допуска 4-го и 8-го звеньев:
Расчет размерной цепи методом максимума-минимума
Решение первой задачи:
Рассчитаем допуск составляющих звеньев размерной цепи по способу допусков одного квалитета. Определим единицу допуска составляющих звеньев с учетом их номинального размера.
Рассчитаем среднее число единиц допуска составляющих звеньев цепи с учетом известных допусков ТА4 и ТА8:
где m - общее число звеньев размерной цепи m=11;
q - число звеньев цепи с известными допусками по условию задачи (звенья 4 и 8) q=2;
ij - единица допуска составляющих звеньев.
По найденному значению аm выберем ближайший квалитет. Для всех звеньев цепи кроме А1 примем 7-й квалитет. Для А1 (наиболее сложное звено) примем 8-й квалитет. Так как аm не равно значению а по ГОСТ 25346-89 то одно из звеньев цепи необходимо выбрать в качестве корректирующего. В данном случае за корректирующее примем звенопростое в изготовлении.
Назначим допуск составляющих звеньев с учетом их номинального размера и принятого квалитета по ГОСТ 25346-89 и занесем в таблицу 1.
Определим допуск корректирующего звена из условия:
где ТА3 - допуск корректирующего звена.
Определим предельные отклонения составляющих звеньев цепи.
Принимаем предельные отклонения составляющих звеньев равными допуску на изготовление. Знак предельных отклонений назначаем для увеличивающих (охватывающих) размеров - как для основного отверстия (знак «+») а для уменьшающих (охватываемых) размеров - как для основного вала (знак «-»).
Рассчитаем координату середины поля допуска составляющих звеньев.
Для этого определим среднее отклонение полей допусков составляющих звеньев кроме корректирующего. Для любого составляющего звена цепи имеем:
Определим среднее отклонение поля допуска корректирующего звенаиз выражения:
В итоге получим (мкм).
По найденной величине ЕС(А3) и допуску ТА3 рассчитаем предельные отклонения корректирующего звена:
Сведения о расчете размерной цепи методом максимума-минимума
(способ допусков одного квалитета)
Первая задача (проектная)
Решение второй задачи:
Проверим замыкающее звено размерной цепи по следующим параметрам:
а)соответствие допуска замыкающего звена допускам составляющих звеньев:
б)соответствие среднему отклонению поля допуска замыкающего звена:
в)предельные отклонения замыкающего звена:
Проверочный расчет размерной цепи показывает что проектная задача решена верно.
Расчет размерной цепи теоретико-вероятностным методом
Считаем что рассеивание отклонений размеров подчиняется закону нормального распределения а границы их вероятного рассеивания совпадают с границами полей допусков.
Установим допуск составляющих звеньев. Для этого определим квадрат единицы допуска i2 составляющих звеньев с учетом их номинального размера а затем рассчитаем среднее число единиц допуска составляющих звеньев с учетом известных допусков ТА4 и ТА8:
Установим по найденному значению аm ближайший квалитет. В данном случае для всех звеньев цепи примем 9-й квалитет. Корректирующим будет 3-е звено размерной цепи.
Назначим по ГОСТ 25346-89 допуск составляющих звеньев размерной цепи с учетом их номинального размера и принятого квалитета.
Определим допуск корректирующего звена исходя из условия:
Отсюда ТА3=25 (мкм).
Определим предельные отклонения составляющих звеньев которые принимаем равными допуску для охватывающих размеров как для основного отверстия (со знаком «+») а для охватываемых размеров - как для основного вала (со знаком «-»).
Рассчитаем среднее отклонение полей допусков составляющих звеньев которое определим по формуле:
Среднее отклонение поля допуска корректирующего звена определим из условия:
Отсюда ЕС(А3)=-150 (мкм).
При известных ЕС(А6) и ТА6 рассчитаем предельные отклонения корректирующего звена:
Сведения о расчете размерной цепи теоретико-вероятностным методом
(способ допусков одного квалитета)
Проверим правильность расчета составляющих размеров по следующим параметрам замыкающего звена:
а)допуск замыкающего звена:
б)среднее отклонение поля допуска замыкающего звена:
Анурьев В.И. Справочник конструктора-машиностроителя. В 3-х т. - М.: Машиностроение 1978. Т. 1-3.
Мочалов В.Д. Взаимозаменяемость и технические измерения. Метрология стандартизация и сертификация: учебное пособие В.Д.Мочалов А.А. Погонин А.Г. Схиртладзе. - Белгород: Изд-во БГТУ 2006. - 204с.
Мягков В.Д. Допуски и посадки: справочник: в 2 чВ.Д. Мягков М.А. Палей. - Л.: Машиностроение 1982-1983.
посадка подшипника.cdw

элементов деталей подшипника
БГТУ им. В.Г. Шухова
резьба.cdw

допуски резьбового соединения.cdw

допусков соединения
БГТУ им. В.Г. Шухова
Шпонка.cdw

допусков элементов шпоночного
соединения по ширине шпонки
БГТУ им. В.Г. Шухова
калибр.cdw

для контроля годности деталей
БГТУ им. В.Г. Шухова
допуски гайка и болт.cdw

допусков болта M33-6g-R
БГТУ им. В.Г. Шухова
таблица1.docx
Характер действия на А0
Первая (проектная задача)
Ec(Аj)= Ei(Аj)+ TАj2
посадка.cdw

редуктор.cdw

шлицевое соединение.cdw

щлицевого соединения
БГТУ им. В.Г. Шухова
Рекомендуемые чертежи
- 20.12.2023
- 25.01.2023
Свободное скачивание на сегодня
Другие проекты
- 24.04.2014