Расчет посадок соединений и размерных цепей узлов машин




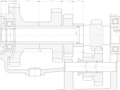
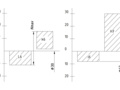
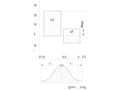
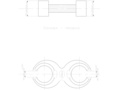
- Добавлен: 24.01.2023
- Размер: 1 MB
- Закачек: 0
Описание
Состав проекта
![]() |
![]() ![]() ![]() |
![]() ![]() |
![]() ![]() ![]() ![]() |
![]() ![]() ![]() |
![]() ![]() ![]() ![]() |
![]() ![]() |
![]() ![]() ![]() |
![]() ![]() ![]() |
![]() ![]() ![]() |
![]() ![]() ![]() |
![]() ![]() ![]() ![]() |
![]() |
![]() ![]() ![]() |
![]() ![]() ![]() |
![]() ![]() ![]() ![]() |
![]() ![]() ![]() |
Дополнительная информация
3. Переходная-готово.docx
Для номинального диаметра 45 мм назначаем переходную предпочтительную посадку: 45
- для отверстия 45 - для вала.
Для этой посадки: Smax= ES – ei = 25-(-8)=33мкм
Smin = EJ – es = -8мкм – натяг.
Средний зазор: Sср===12.5 мкм.
Определение среднеквадратичного отклонения посадки.
Определение предела интегрирования.
Zc= Sср = 12.5495 = 253.
Определение значения функции Ф(z) с учётом предела интегрирования [1табл.стр.193]: Ф(z) = 04943.
Определение вероятности натяга и зазора.
PN=05-Ф(zc) = 00057 PS=05+Ф(zc) = 09943.
Определение процента натягов и зазоров.
ПN=PN100 = 057 ПS=PS100 = 9943
5_калибры.dwg

2_Зазор_готов.docx
Диаметр сопряжения D2=25 мм
Длина соединения L2=50 мм
Осевое усилие на соединение R=015 кН
Частота вращения вала N=600 1мин
Температура масла T=390 C
Материал вала Ст 50 Е=206*1011 Па
Материал втулки БрАЖ-9-4 Е=11*1011 Па
Цель расчёта - определить такой hmin при котором бы выполнялось условие жидкостного трения и на основании этого назначить посадку.
Определение оптимального зазора.
d – номинальный размер соединения (D=D2=25 мм)
опт – оптимальный относительный зазор.
- динамическая вязкость масла зависит от марки масла и
температуры окружающей среды (масло Тур.22 tокр=39)
n – число оборотов вала(n=600 1мин)
р – среднее удельное давление на опору (р=Rdl где
R – радиальная нагрузка на подшипник R=015 кН
d – номинальный диаметр
l – длина шипа l=50мм)
К - коэффициент учитывающий угол охвата и отношение ld (по
[1 табл.III-1]: =180 К =132
р=015*1030025*0050=012 МПа
При учёте климата в котором работает соединение рассчитывается динамическая вязкость при данной температуре:
t=50(50t)n [1 табл.III-3] где
t- фактическая температура масла
n- показатель степени по [1 табл.III-3].:
n=26 t=0020*(5039)26 =0.04
опт=0293*132*=5.5*10-3
Sопт=5.5*10-3*0025=0138 мм
Определение max возможной толщины масляного слоя.
hmax=0252оптd=0252*5.5*10-3*0025=0035мм.
Определение среднего зазора.
St – температурный зазор в подшипнике.
St=(АВ)(tп - 20)d где
А и В - коэффициенты линейного расширения материала вала и
втулки: вал – Ст50 втулка – БрАЖ-9-4 Е [3 табл.III-4]
tп – температура подшипника.
St=(17.8 – 12)*10-6*(39 – 20)*0025=0003 мм
Sср=0138 – 0003=0135 мм.
Условием выбора посадки с зазором является коэффициент =SсрТs1 где
Для номинального размера d=25 мм в [2 табл.стр.148] определяем строку элементы которой представляют собой значения Smax и Smin . Для каждого элемента выбранной строки определяем Ts= Smax - Smin. По формуле определяем и если это выражение больше единицы то мы выбрали верную посадку причём из множества посадок выбираем одну для которой - минимально но больше 1.
(Smax=54 мкм Smin=0 мкм) Ts=54 мкм и =251
(Smax=66 мкм Smin=0 мкм) Ts=66 мкм и =20>1
(Smax=85 мкм Smin=0 мкм) Ts=85 мкм и =16>1
(Smax=169 мкм Smin=65 мкм) Ts=104 мкм и =13>1
(Smax=144 мкм Smin=40 мкм) Ts=104 мкм и =13>1
(Smax=124 мкм Smin=20 мкм) Ts=104 мкм и =13>1
(Smax=104 мкм Smin=0 мкм) Ts=104 мкм и =13>1
(Smax=136 мкм Smin=0 мкм) Ts=136 мкм и =0991
Назначаем рекомендуемую посадку : Smax=169 мкм Smin=65 мкм Ts=104 мкм min==131.
Выбранная посадка не учитывает точность изготовления элементов соединения. Поэтому надо ввести в расчёты показатели качества обработанных поверхностей.
Определение действительного зазора в соединении.
S= Smin + St + 2(RzA + RzB) = 65+3+2*(4+25) = 81 мкм
S= Smax + St + 2(RzA + RzB) = 169+3+2*(4+25) = 185 мкм где
RzA RzB – высота микронеровностей профиля по десяти точкам отверстия и вала: RzA=1 – 4мкм RzB=1 – 3мкм.
Определение max и min относительных зазоров в соединении.
Чтобы определить Е необходимо узнать коэффициент нагруженности подшипника СR:
CR min=94=94=049 где
CR max=94=94=257 где
Определив значения коэффициентов нагруженности и зная отношение ld используя [1 табл.III-5] находим значение Е для половинного подшипника (т.е. принимаем угол обхвата смазки подшипника развернутым): Еmin=03 Emax=07.
Проверка условия жидкостного трения.
КА КВ – конусность (К=0125*10-3)
Rв – радиальное биение (Rв=10мкм).
4 146 – условие выполняется.
4_ПК.dwg

6. Размерная цепь-готово.docx
Замыкающее звено ΔА=2 мм
Допуск замыкающего звена ТА=09 мм
Номинальные размеры составляющих звеньев: А2=16 мм.
Уравнение размерной цепи: А=где
m – число увеличивающих звеньев размерной цепи = +1
n – число уменьшающих звеньев размерной цепи = –1.
Определим неизвестный размер последнего звена:
А8= А1+ А2+ А3+ А4+ А5+ А6+ А7+ ΔА=18+16+6+52+43+22+22+2=181 мм.
Методом полной взаимозаменяемости.
Средняя степень точности: аср=73
i1=1.08 i3=0.73 i4=1.86 i5=156 i6=1.31 i7=1.31 i8=2.9.
Т – допуск стандартного звена
к – количество стандартных звеньев
i – количество единиц допуска.
Чтобы определить квалитет надо полученное аср формально умножить на i и выбрать квалитет по [1табл.VII–1]:
IT10 По [2табл.1.8 стр.43] определяем допуска для звеньев цепи проверяя выполнение условия: Т(1)
Принимаем аср= 64· i => IT10
А1=18 мм – ТА1=0070 мм
А3=6 мм – ТА3=0048 мм
А4=52 мм – ТА4=0120 мм
А5=43 мм – ТА5=0100 мм
А6=22 мм – ТА6=0084 мм
А7=22 мм – ТА7=0084 мм
А8=181 мм – ТА8=0185 мм
Условие выполняется.
Назначаем предельные отклонения на составляющие звенья размерной цепи при этом должно соблюдаться условие:
ЕС=0 – координата середины поля допуска замыкающего звена.
Назначим координаты середин полей допусков на уменьшающие звенья цепи. Уменьшающее звено – это вал поэтому расчёт ведём в системе вала:
ЕС1= –h2 = – 702 = – 35 мкм ЕС2= –h2 = – 1202 = – 60 мкм
ЕС3= –h2 = – 482 = –24 мкм ЕС4= –h2 = – 1202 = – 60 мкм
ЕС5= –h2 = – 1002 = – 50 мкм ЕС6= –h2 = – 842 = – 41 мкм
ЕС7= –h2 = – 842 = – 41 мкм
ЕС8= –35–60–24–60–50–41–41= – 311 мкм.
По известным значениям координат середин полей допусков и значениям допусков определяем значения верхних и нижних предельных отклонений для каждого звена размерной цепи:
А1=18 А2=16 А3=6 А4=52 А5=43 А6=22 А7=22 А8=181.
Вероятностно–статистический метод.
Средняя степень точности: аср= = 177 где
t – коэффициент зависящий от выбранного процента брака (t=3)
– коэффициент зависящий от закона распределения случайной величины (=13).
Принимаем аср= 160· i => IT12
Следовательно уменьшаем квалитет уменьшающих звеньев.
Получаем: А1=18 мм – ТА1=0180 мм
А3=6 мм – ТА3=0120 мм
А4=52 мм – ТА4=0300 мм
А5=43 мм – ТА5=0250 мм
А6=22 мм – ТА6=0210 мм
А7=22 мм – ТА7=0210 мм
А8=181 мм – ТА8=0460 мм
условие выполняется.
где ЕС=0 – координата середины поля допуска замыкающего звена.
Назначим координаты середин полей допусков на уменьшающие звенья цепи:
ЕС1= –h2 = – 1802 = – 90 мкм ЕС2= –h2 = – 1202 = – 60 мкм
ЕС3= –h2 = – 1202 = – 60 мкм ЕС4= –h2 = – 3002 = – 150 мкм
ЕС5= –h2 = – 2502 = – 125 мкм ЕС6= –h2 = – 2102 = – 105 мкм
ЕС7= –h2 = – 2102 = – 105 мкм
ЕС8 = –90–60–60–150–125–105–105= – 695 мкм
По известным значениям координат середин полей допусков и значениям допусков определяем значения верхних и нижних предельных отклонений для каждого звена размерной цепи:
А1=18 А2=16 А3=6 А4=52 А5=43 А6=22 А7=22 А8=209.
Вывод: полученные двумя способами значения предельных отклонений размеров делаем вывод: расчёт по вероятностно–статистическому методу даёт значения допусков больше чем при расчёте по методу полной взаимозаменяемости что облегчает изготовление но приводит к определённому проценту брака.
4_ПК_в_процессе.docx
Процент перегрузки 180%
Радиальная нагрузка R=45 кН
Подшипник №206: d=30 мм D=62 мм B=16 мм r=15.
Определение интенсивности нагружения:
КП =18 – динамический коэффициент посадки [1табл.III-14]
F=1(вал сплошной) – учитывает степень ослабления посадки
FА=1 – для однорядного подшипника.
По найденному значению интенсивности нагружения и значениям номинальных диаметров внутреннего и внешнего кольца подшипника по [1табл. III-11] и [1табл. III-13] и по тексту [1стр.74]. назначаем посадки: на вал 30 в корпус 62.
По [2табл.стр.92] и [2табл.стр.79] определяем предельные отклонения:
вал 30 отверстие в корпусе 62.
7. Литература-готов.docx
Допуски и посадки. Справочник. В 2-х ч. В.Д. Мягков и др.- Л.: Машиностроение 1987. т.1
Допуски и посадки. Справочник. В 2-х ч. В.Д. Мягков и др.- Л.: Машиностроение 1987. т.2
Стандарты СТ СЭВ 157-75
1.Натяг_готов.docx
Диаметр сопряжения номинальный d=(D1) = 50 мм;
Диаметр осевого отверстия d1 = (D2)= 25 мм;
Наружный диаметр втулки - d2= мм;
Длина соединения L1 = 50 мм;
Осевое усилие на соединение P = 40 кН;
Крутящий момент M = 94 Н*м;
Материал шестерни Ст 45 Е = 206*1011 Па;
Материал втулки БрАЖ-9-4 Е=11*1011 Па.
Рис. 1. расчетная схема.
Определение min натяга.
d=50 мм – номинальный диаметр соединения;
Рэ – эксплуатационное удельное давление:
n – коэффициент запаса прочности (n=15 – 2) принимаем 175;
f – коэффициент трения – зависит от материала и вида запрессовки (шестерня – Ст45 втулка – БрАЖ-9-4 по [1 табл.III-7] f=007 запрессовка нагревом шестерни или охлаждением втулки);
Мкр – крутящий момент передаваемый соединением (Мкр=94 Н*м);
р — осевое усилие на соединение (P=40 кН).
ЕА=206*1011 Па ЕВ=11*1011 Па – модули упругости материалов шестерни и втулки.
где А=03 В=025 – коэффициенты Пуассона выбираемые по [1табл.III—6].
Получаем: Nmin=1748 =0017 мм
Определяем характер деформирования вызванный удельным давлением.
=005 =05 из [1 граф.III—11].
Определяем точку С: находиться в I –ой зоне – зоне упругости.
Так как то наибольшее допустимое давление равно допускаемому которое определяется по теории касательных напряжений:
[Рдоп] = 058[1—]А = 058092353106 = 188 Мпа – для шестерни
[Рдоп] = 058[1—]В = 05809075392106 = 142 МПа – для втулки где
— коэффициент который зависит от соотношения диаметров и
ld=5050=1 и определяется из [1 граф.III—10] (для шестерни–092 для втулки–09).
Определение максимального натяга исходя из наибольшего допускаемого давления для материала шестерни:
Nmax=[Pнаиб.доп] (+)d = 188106()10—11005 = 024 мм.
а)Nmin расч. Nmin табл. Nmax расч Nmax табл.
Выписываем TN = 95-45=50 мкм
Исходя из этих условий выбираем стандартную предпочтительную посадку по СТ СЭВ 144—75 [2 стр.155]: 50
отверстие в шестерне 50 втулка 50 .
Для данной посадки: Nmin=31 мкм Nmax=109 мкм.
узел-готово.dwg

0_титульник_готов.docx
Российский государственный университет
Нефти и Газа им. И.М. Губкина
Факультет инженерной механики
Кафедра «Стандартизация сертификация и
управление качеством нефтегазового оборудования»
«Расчет посадок соединений
и размерных цепей узлов машин»
«Метрология стандартизация и сертификация»
Zadanye_MSS.doc
КАФЕДРА «СТАНДАРТИЗАЦИЯ СЕРТИФИКАЦИЯ И УПРАВЛЕНИЕ КАЧЕСТВОМ ПРОИЗВОДСТВА НЕФТЕГАЗОВОГО ОБОРУДОВАНИЯ»
НА КУРСОВУЮ РАБОТУ «РАСЧЕТ ПОСАДОК СОЕДИНЕНИЙ
И РАЗМЕРНЫХ ЦЕПЕЙ УЗЛОВ МАШИН»
ПО ДИСЦИПЛИНЕ «МЕТРОЛОГИЯ СТАНДАРТИЗАЦИЯ И
Расcчитать и выбрать посадки вычертить схемы расположения полей допусков для гладких цилиндрических соединений с натягом (d1) зазором (d2) и переходную (d3) для соединений вал втулка.
Назначить и расcчитать посадки подшипника качения (d D) и построить схемы полей допусков.
Расcчитать калибры для деталей вал и втулка гладкого цилиндрического соединения d1 и построить схемы полей допусков.
Выполнить рабочий чертеж калибров скобы и пробки.
Расcчитать размерную цепь А методом полной взаимозаменяемости и вероятностно-статистическим методом.
На формате А4 выполнить чертеж узла (начертить вручную или с помощью компьютера КОПИРОВАТЬ НЕЛЬЗЯ исправить ошибки) указать рассчитанные посадки и схему размерной цепи.
3_переход.dwg

5. Калибры-готово.docx
гладкого цилиндрического соединения D1.
Данное соединение вал–втулка осуществляется по посадке с натягом .
Калибры–пробки: 50Н8 или 50
Dmin=50мм Dmax=50039мм.
По [4 табл.2] допуски и предельные отклонения:
Z=6 мкм у=5мкм Н=4 мкм.
Проходной калибр–пробка:
ПРmax=Dmin+Z+H2 = 50+0006+00042 = 50008 мм
ПРmin=Dmin+Z – H2 = 50+0006–00042 = 50004 мм
ПРизн=Dmin – у = 50 – 0005 = 39995 мм
Непроходной калибр–пробка:
НЕmax=Dmax+H2 = 50039+00042 =50041 мм
НЕmin=Dmax– H2 = 50039–00042 = 50037 мм
Исполнительные размеры:
Калибры–скобы и контркалибры к ним:
u8 или 50 Dmin=50070 мм Dmax=50109 мм.
По табл.2 СТ СЭВ 157–75 допуски и предельные отклонения: Z1=6 мкм у1=5 мкм Н1=7 мкм Нр=25 мкм.
Проходной калибр–скоба:
ПРmax=Dmax – Z1+H12 = 50109 – 0006+00072 = 501065 мм
ПРmin=Dmax – Z1 – H12 = 50109 – 0005 – 00072 = 501005 мм
ПРизн=Dmax+ у1 = 50109+0005 = 50114 мм
Непроходной калибр–скоба:
НЕmax=Dmin+H12 = 50070 +00072= 500735 мм
НЕmin=Dmin – H12 = 50070 – 00072 = 500665 мм
ПР=501005 НЕ=500665.
Контркалибры к скобам:
К – ПРmax=Dmax – Z1+Hр2 = 50109 – 0006+000252 = 5010425мм
К – ПРmin= Dmax – Z1 – Hр2 = 50109 – 0006 – 000252 = 5010175 мм
К – Иmax= Dmax+у1+Нр2 = 50109+0005+000252 =5011525 мм
К – Иmin=Dmax+у1 – Нр2 = 50109+0005 – 000252 =5011275 мм
К – НЕmax=Dmin+Нр2 = 50070+000252 = 5007125 мм
К – НЕmin= Dmin – Нр2 = 50070 – 000252 = 5006875мм
К – ПР=5010425 К – И=5011525 К – НЕ=5007125.