Расчет и выбор посадок для стандартных соединений




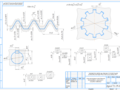


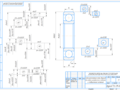
- Добавлен: 24.01.2023
- Размер: 477 KB
- Закачек: 0
Описание
Состав проекта
![]() |
![]() |
![]() |
![]() ![]() ![]() ![]() |
![]() |
![]() ![]() ![]() |
![]() |
![]() ![]() ![]() ![]() |
![]() ![]() ![]() ![]() |
![]() |
![]() ![]() ![]() ![]() |
![]() ![]() ![]() ![]() |
![]() |
![]() |
![]() |
Дополнительная информация
Спецификация.spw

Болт М6 х 16 ГОСТ 7798-70
Болт М5 х 16 ГОСТ 7805-70
Болт М8 х 8 ГОСТ 7808-70
Болт М6 х 28 ГОСТ 15591-70
Винт М6 х 6 ГОСТ P 50383-92
Винт М4х10 ГОСТ 17475-80
Гайка М6 ГОСТ 5916-70
Гайка М5 ГОСТ 5929-70
Гайка М24 ГОСТ 5929-70
Гайка стопорная М24 ГОСТ 28119-89
Подшипник 8206 ГОСТ 7872-89
Подшипник 211 ГОСТ 8338-75
Подшипник 7210 А ГОСТ 27365-87
Шайба 6 Н ГОСТ 6402-70
Шайба 7 Н ГОСТ 6402-70
Шайба 8 Н ГОСТ 6402-70
Шайба 27 ГОСТ 22355-77
Шпилька М5 х 28 ГОСТ 22036-76
Шпонка 10 х 8 х 22 ГОСТ 23360-78
Кольцо 044-058-2-2 ГОСТ 9833-73
Кольцо 053-061-2-2 ГОСТ 9833-73
Кольцо 047-065-2-2 ГОСТ 9833-73
Пояснительная записка.docx
Государственное образовательное учреждение высшего профессионального образования
«Курский государственный технический университет»
Кафедра «Управление качеством метрология и сертификация»
по дисциплине «Взаимозаменяемость»
на тему «Расчет и выбор посадок для стандартных соединений»
Специальность 200503 «Стандартизация и сертификация»
(инициалы фамилия) (подпись дата)
(подпись дата) (инициалы фамилия)
Данная курсовая работа посвящена выбору и расчету посадок для стандартных изделий.
В ходе выполнения работы был произведен выбор и расчет посадок для гладких соединений а именно: аналитический расчет посадки с натягом выбор и расчет посадки с зазором переходной посадки посадки с натягом а также выбор и расчет посадки для шпоночного шлицевого резьбового соединений и для соединения с подшипником качения. Также в работе выполнен расчёт размерной цепи методом максимум-минимум и вероятностным методам определен комплекс показателей точности для зубчатого колеса по требованиям к точности изготовления.
Курсовая работа выполнена на 36 листах содержит 2 таблицы (перечень графического материала и условные обозначения) приведён список использованных источников из 5 наименований книг. Графическая часть состоит из:
)Сборочный чертеж механизма (1 лист формата АЗ);
)Схемы расположения полей допусков для гладких цилиндрических соединений и соединений с подшипником качения (1 лист формата АЗ);
)Схемы расположения полей допусков для резьбового шпоночного и шлицевого соединений (1 лист формата АЗ);
)Чертеж зубчатого колеса (1 лист формата АЗ).
Расчет и выбор посадок для стандартных соединений
Расчет посадок гладких цилиндрических соединений 7
1Аналитический расчет посадки с натягом .. .7
2Выбор и расчет посадки с зазором . 11
3Выбор и расчет переходной посадки .. 12
4Выбор и расчет посадки с натягом . 13
Выбор и расчет посадки резьбового соединения 14
Выбор посадок и расчет шпоночного соединения . 16
Выбор посадок шлицевого соединения 17
Выбор и расчет посадок для соединений с подшипником качения ..19
Расчет размерной цепи А методом максимума - минимума .. 22
Расчет размерной цепи А вероятностным методом . 26
Определение комплекса контрольных параметров для зубчатого колеса
по требованиям к точности изготовления 30
Список использованных источников .. 35
Приложение А Перечень графического материала .36
Обозначения и сокращения
В данной курсовой работе используются условные обозначения которые приведены в таблице 1.
Таблица 1 - Условные обозначения
Номинальный размер отверстия
Номинальный размер вала
Наибольший предельный размер отверстия
Наименьший предельный размер отверстия
Наибольший предельный размер вала
Наименьший предельный размер вала
Верхнее отклонение отверстия
Нижнее отклонение отверстия
Верхнее отклонение вала
Нижнее отклонение вала
Допуск для отверстия
Координата середины поля допуска отверстия
Координата середины поля допуска вала
Наибольший (максимальный) натяг
Наименьший (минимальный) натяг
Допуск зазора посадки с зазором
Допуск натяга посадки с натягом
Номинальный размер увеличивающего звена
Номинальный размер уменьшающего звена
Допуск замыкающего звена
Номинальный размер замыкающего звена
Предел текучести охватываемой детали
Предел текучести охватывающей детали
Взаимозаменяемость оказывает огромное влияние на экономику страны. Она является одной из важнейших предпосылок организации серийного и массового производства способствует повышению эффективности труда и качества выпускаемой продукции. Достижение желаемого результата связано с выбором необходимой точности изготовления изделий расчетом размерных цепей выбором шероховатости поверхностей а также выбором отклонения от геометрической формы и расположения поверхностей. Взаимозаменяемость позволяет не только улучшить качество изделий но и сократить сроки их ремонта в процессе эксплуатации не осуществляя дополнительных измерений.
Взаимозаменяемость обеспечивает высокое качество изделий и снижает их стоимость способствуя при этом развитию прогрессивной технологии и измерительной техники. Без взаимозаменяемости невозможно современное производство. Взаимозаменяемость базируется на стандартизации – нахождении решений для повторяющихся задач в сфере науки техники и экономики направленной на достижение оптимальной степени упорядочения в определенной области.
Расчет посадок гладких цилиндрических соединений
1Аналитический расчет и выбор посадки с натягом
1.1 Исходные данные:
-для вала используется сталь 45:=36·107Hм2; - для зубчатого колеса используется сталь 45:=36·107 Hм2.
Высота неровности поверхности:
- отверстия =25 мкм
1.2 Определяем минимальное удельное давление на контактных поверхностях соединения:
где – минимальное удельное давление поверхности Нм2;
Мкр – крутящий момент Н·м;
d – номинальный диаметр соединения м;
– длина контакта сопрягаемых поверхностей м;
f – коэффициент трения
1.3 Определяем значение наименьшего расчётного натяга предварительно
определив коэффициенты Ляме с1 и с2:
где с1 и с2 – коэффициенты Ляме;
d1- диаметр отверстия в вале (охватываемой детали);
d2 - наружный диаметр втулки (охватывающей детали);
и 2 - коэффициенты Пуассона
где Е1 и Е2 – модули упругости Нм2;
с1 и с2 – коэффициенты Ляме
1.4 Определяем минимальный допустимый натяг с учётом поправок:
где – минимальный допустимый натяг мкм;
γш – поправка учитывающая смятие неровностей контактных
поверхностей деталей при образовании соединения
γt – поправка учитывающая различие рабочей температуры деталей и
температуры сборки различие коэффициентов линейного
расширения материалов соединяемых деталей;
γц – поправка учитывающая ослабление натяга под действием
γп – добавка компенсирующая уменьшение натяга при повторных запрессовках.
1.5 Определяем наибольшее допустимое удельное давление на поверхности вала и втулки соответствующие отсутствию пластической деформации на контактных поверхностях:
В качестве [берется наименьшее из двух значений.
1.6 Определяем наибольший расчётный натяг:
1.7 Определяем максимальный допустимый натяг с учётом поправок:
где γуд – коэффициент увеличения удельного давления у торцов
1.8 Выбираем стандартную посадку соблюдая условия:
1.9 Определяем необходимое максимальное усилие запрессовки предварительно определив удельное давление при максимальном натяге и коэффициент трения при запрессовке fп:
2Выбор и расчет посадки с зазором
2.1 Исходные данные:
2.2 Данная посадка имеет номинальный размер 50мм поле допуска отверстия D9 и поле допуска вала m6.
2.3 Определяем предельные отклонения по таблице 1.29 стр.79 [1]:
2.4 Определяем предельные размеры:
Dmax=D + ES= 50+0142=50142 (мм)
Dmin=D + EI= 50+0080=50080 (мм)
dmax=d + es=50+0025=50025 (мм)
dmin=d + ei=50+0009=50009 (мм)
2.5 Определяем допуски для отверстия и для вала:
TD=Dmax – Dmin = 50142 – 50080 =0062 (мм)
Td=dmax – dmin = 50025 – 50009 =0016 (мм)
2.6 Определяем предельные зазоры:
Smax=Dmax – dmin =50142 – 50009 =0133(мм)
Smin=Dmin – dmax =50080 –50025 =0055 (мм)
2.7 Определяем средний зазор:
2.8 Определяем допуск посадки:
TS=Smax – Smin=0133– 0055 =0078 (мм).
3Выбор и расчет переходной посадки
3.1 Исходные данные:
3.2 Посадка 55H7m6 имеет номинальный размер 55 мм поле допуска отверстия H7 и поле допуска вала m6. Данная посадка представлена в системе отверстия.
3.3 Определяем предельные отклонения по таблице 1.29 стр.79 [1]:
3.4 Определяем предельные размеры:
Dmax=D + ES= 55+0030 =55030 (мм)
Dmin=D + EI= 55+0=55 (мм)
dmax=d + es=55+0030=55030 (мм)
dmin=d + ei=55+0011=55011 (мм)
3.5 Определяем допуски для отверстия и для вала:
TD=Dmax – Dmin = 55030– 55=0030 (мм)
Td=dmax – dmin = 55030 – 55011 =0019 (мм)
3.6 Определяем наибольшие натяг и зазор:
Nmax=es – EI =003 – 0=003 (мм)
Smax= ES – ei =003 – 0011=0019 (мм)
3.7 Определяем средний натяг:
3.8 Определяем допуск посадки:
Smax + Nmax =0019 + =0049 (мм)
4Выбор и расчет посадки с натягом
4.1 Исходные данные:
4.2 Посадка 70H7u7 имеет номинальный размер 70мм с полем допуска отверстия H7 и полем допуска вала u7. Данная посадка представлена в системе отверстия и является посадкой с натягом.
4.3 Определяем предельные отклонения по таблице 1.29 стр.79 [1]:
4.4 Определяем предельные размеры:
Dmax=D + ES= 70+003=7003 (мм)
Dmin=D + EI= 70+0=70 (мм)
dmax=d + es=70+0132=70132 (мм)
dmin=d + ei=70+0102=70102 (мм)
4.5 Определяем допуски для отверстия и вала:
TD=Dmax – Dmin = 7003 – 70=003 (мм)
Td=dmax – dmin = 70132 – 70102 =003 (мм)
4.6 Определяем предельные натяги:
Nmax=dmax – Dmin =70132 –70 =0132 (мм)
Nmin=dmin – Dmax =70102 – 7003 =0072 (мм)
4.7 Определяем средний натяг:
4.8 Определяем допуск посадки:
=Nmax – Nmin=0132– 0072=006 (мм)
Выбор и расчет посадки для резьбового соединения
1 Исходные данные: М42-7G8g
2 Производим расшифровку условного обозначения:
М – резьба метрическая;
– наружный диаметр резьбы D=d=42 мм;
Шаг крупный - определяется по таблице;
G – поле допуска на средний диаметр гайки (D2);
G – поле допуска на внутренний диаметр гайки (D1);
g – поле допуска на средний диаметр болта (d2);
g – поле допуска на наружный диаметр болта (d);
Длина свинчивания относится к нормальной N группе длин свинчивания.
3Определяем шаг резьбы по таблице 4.10 стр.674 [2]:
4Определяем внутренний и средний диаметры резьбового соединения по формулам из таблицы 4.12 стр.677учитывая что шаг резьбы Р=45:
- внутренний диаметр
D1=d1=d-5+0129=42-5+0129=37129 (мм)
D2=d2=d-3+0077=42-3+0077=39077 (мм)
5Определяем по таблице 4.17 стр.686 [2] предельные отклонения для диаметров:
d2 (8g): es2=-0063 мм
d1 (8g): es1=-0063 мм
D2 (7G): ES2=0463 мм
D1 (7G): ES1=0913 мм
D (7G): ES-не нормируется
6Определяем предельные размеры диаметров:
d2max=d2+es2=39077 +(-0063)=39014 (мм)
d2min=d2 +ei2=39077 +(-0438)=38639 (мм)
d1max=d1+es1=37129 +(-0063)=37066 (мм)
d1min - не нормируется
dmax=d+es=42+(-0063)=41937(мм)
dmin=d+ei=42+(-0863)=41137(мм)
D2max=D2+ES2=39077 +0463=39540 (мм)
D2min=D2+EI2=39077 +0063=39140 (мм)
D1max=D1+ES1=37129 +0913=38042 (мм)
D1min=D1+EI1=37129 +0063=37192 (мм)
Dmax - не нормируется
Dmin=D+EI=42+0063=42063 (мм)
Выбор и расчет посадки для шпоночного соединения
1 Определяем номинальные размеры шпонки для исполнения А по
таблице 4.52 стр.773 [2]. Если диаметр вала равен d = 55 мм то ширина шпонки b =16мм и высота h =10 мм. Длину шпонки выбираем из ряда указанного в примечании таблицы 4.52 стр.773 [2] в интервале длин от 45 до 180мм: мм.
Условное обозначение шпонки: Шпонка 16×10×50 СТ СЭВ 189–75.
2 Предельные размеры фаски:
3 Определяем по таблице 4.52 стр.773[2] глубину шпоночного паза на валу t1 и во втулке t2:
t1 =6 мм; t2 =43 мм
4 Определяем размеры с учетом диаметра вала:
d – t1 = 55 – 6 = 49 (мм)
d + t2 = 55 + 43 = 593 (мм)
5 Радиусы закругления пазов:
6 Принимаем нормальное соединение а по таблице 4.53 стр. 775 [2]
выбираем поля допусков в зависимости от назначения посадки:
Поле допуска на ширину шпонки –
Поле допуска на ширину шпоночного паза на валу –
Поле допуска на ширину шпоночного паза во втулке –
Поле допуска на высоту шпонки –
Поле допуска на длину шпонки – h14.
7 Определяем предельные отклонения на размеры t1 и t2 по таблице 4.54 стр.776 [2]:
Выбор и расчет посадки для шлицевого соединения
1 Исходные данные: 8×36×40
2 Принимаем что шлицевое соединение является прямобочным. Определяем размеры прямобочного шлицевого соединения по таблице 4.58 стр.781[2]:
внутренний диаметр: d=36 мм
наружный диаметр: D=40 мм
ширина шлица: b=7 мм
радиус закругления: r=03 мм
3 Определяем подвижность соединения и способ центрирования вала и втулки:
Данное шлицевое соединение относится к легкой серии. Выбираем способ центрирования по внутреннему диаметру (d). Данный вид центрирования применяется в случаях повышенных требований к совпадению геометрических осей если твёрдость втулки не позволяет обрабатывать деталь протяжкой или когда может возникнуть коробление валов после термообработки. Соединение является подвижным.
4 Определяем посадку на центрирующий диаметр d по таблице 4.60
5 Определяем посадку на нецентрирующий диаметр D по таблице 4.62
6 Определяем посадку на ширину шлица по таблице 4.60 стр.785[2]:
7 Записываем обозначение шлицевого соединения с учётом найденных посадок:
8 Определяем предельные отклонения и предельные зазоры для внутреннего диаметра:
9 Определяем предельные отклонения и предельные зазоры для наружного диаметра:
a11 es=-300мкм=-03мм
11 Определяем предельные отклонения и предельные зазоры для шлица (зуба):
Расчет и выбор посадок для соединения с подшипником качения
2 Определяем интенсивность нагрузки по формуле:
R - радиальная реакция опоры на подшипник кН;
b - рабочая ширина посадочного места м;
Kп – динамический коэффициент посадки зависящий от характера нагрузки;
F – коэффициент учитывающий степень ослабления посадочного натяга при полом или тонкостенном корпусе;
FA – коэффициент неравномерности распределения радиальной нагрузки R между рядами роликов в двухрядных конических роликоподшипниках или между сдвоенными шарикоподшипниками при наличии осевой нагрузки на опору.
Для радиальных и радиально-упорных подшипников с одним наружным или внутренним кольцом FA=1 при сплошном вале F=1. Принимаем Kп=18 т.к. возможны сильные удары и вибрации перегрузка достигает 300%.
3 По таблице 4.82 стр. 818 [2] для заданных условий определяем поле допуска на вал который сопрягается с внутренним кольцом подшипника – m6.
Внутреннее кольцо воспринимает радиальную нагрузку последовательно всей окружностью дорожки качения и передает ее последовательно всей посадочной поверхности вала. Следовательно внутреннее кольцо испытывает циркуляционный вид нагружения.
4 Выбираем поле допуска для отверстия в корпусе поверхность которого сопрягается с наружным кольцом подшипника:
Корпус неподвижен поэтому наружное кольцо воспринимает радиальную нагрузку постоянную по направлению лишь ограниченным участком окружности дорожки качения и передает ее соответствующему ограниченному участку посадочной поверхности корпуса. Следовательно наружное кольцо имеет местное нагружение. По таблице 4.84 стр. 821 принимаем поле допуска для установки подшипника качения в корпус (под наружное кольцо) – Н7.
5Определяем предельные отклонения на наружный и внутренний диаметры:
6 Для подшипника принимаем 0 класс точности из ряда 06542.
7 Поле допуска на посадочный диаметр внутреннего кольца
Поле допуска на наружный диаметр подшипника l0.
8 Определяем предельное отклонение на наружный и внутренний диаметры подшипника:
9 Проверим правильность назначения поля допуска m6 на вал:
- определяем средний натяг для выбранной посадки
- определяем наименьший расчетный натяг
где – наименьший расчетный натяг мм;
R – наибольшая радиальная нагрузка на подшипник кН;
- коэффициент принимаемый приближенно для подшипников
- рабочая ширина кольца подшипники (за вычетом фасок) м.
- проверяем выполнимость условия
Условие выполнено следовательно поле допуска m6 для вала выбрано верно.
Расчет размерной цепи методом максимума-минимума
2Выполняем схему размерной цепи и определяем увеличивающие и уменьшающие звенья:
Рисунок 1 – Схема размерной цепи
Размеры А1 А2 являются увеличивающими т.к. при их увеличении исходное звено А увеличивается; размер А4 – уменьшающим т.к. при его увеличении исходное звено А уменьшается.
3 Определяем предельные отклонения исходного звена. Принимаем номинальный размер А=0 мм:
EI А= Аmin – А =04 (мм).
4 Определяем допуск исходного звена:
ТА=Аmax – Аmin=09 – 04=05(мм)=500(мкм).
Таким образом исходное звено можно представить в виде:
5 Определяем координату середины поля допуска исходного звена:
6 Определяем номинальное размер звена А4:
где m – число увеличивающих звеньев;
n – число уменьшающих звеньев.
А = (А1+А2+А3) – А4;
А4=(А1+А2+А3)- А=(22+7+55)-0=84 (мкм).
7 Находим число единиц допуска содержащихся в допуске исходного звена:
где - число единиц допуска;
- известный допуск j-го составляющего звена;
- единица неизвестного допуска j-го составляющего звена.
Принимаем 10 квалитет т.к. арасч = 8113 находится между 64 и 100 что соответствует 10 и11 квалитетам.
8 Назначаем поля допусков на составляющие звенья:
А1= 22 -012 ТА1=120мкм EсА1 = -60мкм
А2 = 7Js 10(±0029) ТА2=58мкм EсА2 = 0мкм
А3 = 55 В10() ТА3=120мкм EсА3 = 250мкм
Принимаем размет А4 за А4.
9 Определяем допуск составляющего звена А4:
ТА = ТА1+ТА2+ТА3+ ТА4
Т А4 = ТА-ТА1-ТА2-ТА3 = 500-120-58-120 = 202(мкм)
10 Определяем координату середины поля допуска размера А4:
ЕсА = (ЕсА1 + ЕсА2 + ЕсА3) – Ес А4
Ес А4 = (ЕсА1+ЕсА2 +ЕсА3)- ЕсА = -60+0+250-650=-460(мкм)
11Определяем верхнее и нижнее предельные отклонения размера А4:
ЕSА4 = ЕсА4 + ТА42 = -460+2022= - 359( мкм)
ЕIА4 = ЕсА4 - ТА42 = - 460 - 2022=-561( мкм)
12 Выбираем ближайшее стандартное поле допуска на размер А4 по таблице 1.9 стр.48:
13 Выполняем проверочный расчет размерной цепи методом максимум – минимум (обратная задача)
13.1 Определяем номинальный размер замыкающего звена:
А = (А1+А2+А3) – А4=(22+7+55) - 84= 0(мм)
13.2 Определяем допуск замыкающего звена:
ТА = ТА1+ТА2+ТА3+ТА4=120+58+120+140=438(мкм).
13.3Определяем координату середины поля допуска замыкающего звена:
ЕсА = (ЕсА1 + ЕсА2 + ЕсА3) – Ес А4=-60-0+250+450=640(мкм)
13.4Определяем верхнее и нижнее предельные отклонения замыкающего звена:
ЕSА = ЕсА + ТА 2 = 640+4382=859 (мкм)
ЕIА = ЕсА - ТА 2 = 640-4382=421 ( мкм)
13.5 Определяем наибольший и наименьший предельные размеры замыкающего звена:
Аmax = А+ ESА = 0+0859=0859 (мм)
Аmin = А+ EIА = 0+0421=0421 (мм)
13.6Проверяем выполнение условий:
59 мм 09 мм 0421 мм 04 мм
Условие выполнено поэтому поля допусков на составляющие звенья назначены правильно.
Расчет размерной цепи вероятностным методом
2 Выполняем схему размерной цепи и определяем увеличивающие и уменьшающие звенья:
Рисунок 2 – Схема размерной цепи
6Определяем номинальное размер звена А4:
где t – коэффициент принимаемый в зависимости от допускаемого процента риска t=3;
- коэффициент относительного рассеяния каждого из составляющих размеров λj =13;
- единица допуска j-го составляющего звена.
Принимаем 11 квалитет т.к. арасч = 153 находится между 100 и 160 что соответствует 11 и 12 квалитетам.
8Назначаем поля допусков на составляющие звенья:
А2 = 7h 11(-009) ТА2=90мкм EсА2 = -45мкм
А3 = 55 С11() ТА3=190мкм EсА3 = 235мкм
9Определяем допуск составляющего звена А4:
10Определяем координату середины поля допуска размера А4:
Ес А4 = (ЕсА1+ЕсА2 +ЕсА3)- ЕсА = -60+(-45)+235-650=-520(мкм)
ЕSА4 = ЕсА4 + ТА42 = -520+4372= - 302( мкм)
ЕIА4 = ЕсА4 - ТА42 = - 520 - 4372=-739( мкм)
12 Выбираем ближайшее стандартное поле допуска на размер А4 по табл. 1.9 1.8(стр. 44 – 48):
13 Выполняем проверочный расчет размерной цепи вероятностным методом (обратная задача)
13.1Определяем номинальный размер замыкающего звена:
13.2Определяем допуск замыкающего звена:
ЕсА = (ЕсА1 + ЕсА2 + ЕсА3) – Ес А4=-60+(-45)+235-(-450)=580(мкм)
ЕSА = ЕсА + ТА 2 = 580+3272=744 ( мкм)
ЕIА = ЕсА - ТА 2 = 580-3272=417 ( мкм)
13.5Определяем наибольший и наименьший предельные размеры замыкающего звена:
Аmax = А+ ESА = 0+0744=0744 (мм)
Аmin = А+ EIА = 0+0417=0417 (мм)
44 мм 09 мм 0417 мм 04 мм
Определение комплекса контрольных параметров для зубчатого колеса по требованиям к точности изготовления
посадочный диаметр отверстия зубчатого колеса: d=70мм
2 Принимаем диаметр делительной окружности:
где m – модуль зубчатого колеса;
Принимаем модуль m зубчатого колеса по таблице 5.3 стр. 836 [2]:
3 Определяем высоту ножки зуба:
hf =125 m = 125·2=25 (мм)
4 Определим высоту головки зуба:
5 Определяем окружность вершин:
da=d+2ha=140+2·2=144(мм)
6 Определяем окружность впадин:
d1f =d– 2hf =140 – 2·25=135(мм)
7 Пользуясь рекомендациями степеней точности и методов обработки для зубчатых колёс при m >1мм таблицы 5.12 стр.856[2] выбираем степень по нормам кинематической точности - 8(средняя точности) — зубчатые колёса общего машиностроения не требующие особой точности.
Так как m > 1 то нормы плавности работы зубчатого колеса могут быть не более чем на две степени точнее или на одну степень грубее норм кинематической точности поэтому выбираем 7-ую степень.
Нормы контакта зубьев могут назначаться по любым степеням более точным чем нормы плавности работы зубчатых колёс поэтому выбираем 7-ую степень.
Вид сопряжения – В — нормальный боковой зазор. Вид допуска бокового зазора - b.
Устанавливаем класс отклонений межосевого расстояния - V.
Записываем обозначение зубчатого колеса:
8 Определяем показатели кинематической точности зубчатого колеса по таблице 5.4 стр.842[2]. Принимаем комплекс III согласно которому для зубчатого колеса выбираем следующие показатели:
Fvwr—колебания длины общей нормали;
Frr—радиальное биение зубчатого венца.
Допуски на вышеуказанные показатели точности по таблице 5 стр. 431-432 [3]:
9 Выбираем показатели характеризующие плавность работы зубчатого конического колеса по таблице 7 стр. 435 [3]. Принимаем VII комплекс которому соответствуют такие показатели:
fPbr —отклонение шага зацепления
fPtr—отклонение шага
Допуски указанных показателей определяем по таблице 10 стр.439-440[3]:
10 Показатели характеризующие полноту контакта зубьев выбираем по таблицам 12 и 13 стр.444-445[3]. Определяем относительные размеры суммарного пятна контакта по высоте зубьев не менее 45% по длине зубьев не менее 60%.
11 Определяем величину гарантированного зазора по таблице 17 стр.451 [3]:
12 Определяем предельные отклонения межосевого расстояния:
13 Определяем наименьшее дополнительное смещение исходного контура по таблице 19 стр.454[3]:
14 Допуск на смещение исходного контура:
15 Наименьшее отклонение длины общей нормали а также средней длины общей нормали определяем по таблице 23 стр.457 [3] и по таблице 27 стр.461 [3]:
ЕW — наименьшее отклонение длины общей нормали
ЕWm—наименьшее отклонение средней длины общей нормали.
EWm=EWmI + EWmII = -(120+18) = -138 (мкм)
16 Определяем допуск на длину общей нормали по таблице 25 стр.459[3]:
17 Допуск на среднюю длину общей нормали по таблице 29 стр.462[3]:
18 Наименьшее отклонение толщины зуба по таблице 29 стр.463[3]:
19 Допуск на толщину зуба таблица 30 стр.464[3]:
20 Определяем длину общей нормали по формуле:
где W1 – значение длины общей нормали (определяем по таблице 5.30 стр.884[1]);
W=2312134246243(мм) W=4624
21 Определяем радиальное биение наружного цилиндра заготовки по таблице 5.26 стр.878[2]:
Fd a=06·Fr=06·63=378 (мкм)
22 Биение базового торца определяем по таблице 5.27 стр.879[2]: для 7- степени точности по нормам контакта ширине зубчатого колеса b=55мм отклонение наружного цилиндра Edа принимаем по полю допуска h 14.
В ходе выполнения данной курсовой работы приобретены навыки в выборе и расчете посадок для стандартных соединений в зависимости от их назначения и оказываемых на них нагрузок.
Кроме того в ходе выполнения работы были затронуты вопросы нормирования точности элементов деталей в машиностроении приобретены навыки работы с нормативно-технической и справочной документацией. Изучены условные обозначения предельных отклонений и допусков параметров шероховатости резьбового и шлицевого соединений.
Список использованных источников
Допуски и посадки. Справочник. В 2-х ч. Ч.1Под ред. В. Д. Мягкова. Л: Машиностроение. Ленингр. отд-ние 1979-с.1-544 ил.
Допуски и посадки. Справочник. В 2-х ч. Ч.2Под ред. В. Д. Мягкова. Л: Машиностроение. Ленингр. отд-ние 1979-с.544-1032 ил.
И.М.Белкин. Допуски и посадки (основные нормы взаимозаменяемости). М.: Машиностроение 1992-528 с. ил.
Курсовое проектирование деталей машин. С.А. Чернавский.-М.: Машиностроение 1988.- 416 с.:ил.
Курсовое проектирование деталей машин. В. Н. Кудрявцев
Ю. А. Державец. Л.: Машиностроение. Ленингр. отд-ние 1984. 400 с. ил.
Перечень графического материала
0503 ОПД.Ф.09.81.04.001
0503 ОПД.Ф.09.81.04.002
Схемы полей допусков для гладких цилиндрических соединений и соединений с подшипником качения
0503 ОПД.Ф.09.81.04.003
Схемы полей допусков для резьбового шпоночного и шлицевого соединений
0503 ОПД.Ф.09.81.04.004
Таблица А.1 – Перечень графического материала
Чертеж2.cdw

Чертеж3.cdw

Схема расположения полей допусков
для гладких цилиндрических соединений
и подшипника качения
Чертеж 41.cdw

Степень точности по ГОСТ 1643-81
Коэффициент смещения
Сталь 40X ГОСТ 4543-81
0503.ОПД.Ф.09.81.22.004.КР
Неуказанные предельные отклонения размеров: отверстий-по
Чертеж.cdw

шлицевого соединений
0503.ОПД.Ф.09.81.22.002.КР.