Взаимозаменяемость Стандартизация и технические измерения




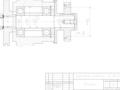
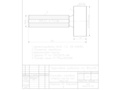
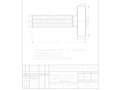
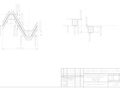
- Добавлен: 24.01.2023
- Размер: 537 KB
- Закачек: 0
Описание
Состав проекта
![]() |
![]() ![]() ![]() |
![]() ![]() ![]() |
![]() ![]() ![]() ![]() |
![]() ![]() ![]() |
![]() ![]() ![]() |
![]() ![]() ![]() |
![]() ![]() ![]() |
![]() ![]() ![]() ![]() |
![]() ![]() ![]() |
![]() ![]() ![]() |
![]() ![]() ![]() |
![]() ![]() ![]() |
![]() ![]() ![]() |
Дополнительная информация
Skoba .dwg
Скоба 8113-0149 s6 ГОСТ 18362-73
Задание 34 вариант 4
Курсовая работа по ВСиТИ
Цементировать 59-63 2.Покрытие нерабочих поверхностей-Хим.Ок. 3.Другие ТТ по ГОСТ2015-84 4.Полный износ Р-ПРизн=70
Posadka podshupnikov.dwg
Схема расположения полей допусков посадк подшипников
Задание 34 вариант 4
Курсовая работа по ВСиТИ
Rezb6a.dwg

Задание 34 вариант 4
Теоретический профиль и схема расположение полей допусков резьбового соединения
Курсовая работа по ВСиТИ
Perexodna9 posadka.dwg
Схема расположения полей допусков переходной посадки
Задание 34 вариант 4
Курсовая работа по ВСиТИ
Posadka s nat9gom.dwg
Схема расположения полей допусков посадки с натягом
Задание 34 вариант 4
Курсовая работа по ВСиТИ
ShlicbI.dwg
Схема расположения полей допусков шлицевого соединения
Задание 34 вариант 4
Курсовая работа по ВСиТИ
Kalibr probka neproxodna9 .dwg
Калибр-пробка (НЕ)8133-1109 H6 ГОСТ 14813-69
Задание 34 вариант 4
Курсовая работа по ВСиТИ
Цементировать 59-63 2.Покрытие нерабочих поверхностей-Хим.Ок. 3.Другие ТТ по ГОСТ2015-84
Uzel.dwg

Курсовая работа по ВСиТИ
Задание 34 вариант 4
Kalibr Kontrkalibr.dwg
Схема расположения полей допусков калибров и контркалибров
Задание 34 вариант 4
Курсовая работа по ВСиТИ
Shestern9 A4.dwg
Сталь 45 ГОСТ1050-74
Курсовая работа по ВСиТИ
Закалка HRC40-45 2. ISO 2768-mk
Данные для контроля взаимного расположения разноименных профилей зубьев
Нормативный выходной контур
Размер постоянной хорды
Высота до постоянной хорды
Posadka s zazorom.dwg
Схема расположения полей допусков посадки с зазором
Задание 34 вариант 4
Курсовая работа по ВСиТИ
Kalibr probka proxodna9 .dwg
Калибр-пробка (ПР)8133-1109 H6 ГОСТ 14812-69
Задание 34 вариант 4
Курсовая работа по ВСиТИ
Цементировать 59-63 2.Покрытие нерабочих поверхностей-Хим.Ок. 3.Другие ТТ по ГОСТ2015-84 4.Полный износ Р-ПРизн=69
Курсовой.docx
молодежи и спорта Украины
Запорожский Национальный Технический Университет
Кафедра : Металлорежущие станки
Курсовая работа по дисциплине :
Взаимозаменяемость Стандартизация и технические измерения
студент гр. М-719 М.С. Мокиенко
ст.преподователь В.С. Штанкевич
ПЗ: с.46 2 таблицы 8 источников.
Цель проекта – укрепить и расширить изученный материал по дисциплине ВС и ТИ; приобрести навыки проектирования и расчета разных типов соединений по принципу функциональной взаимозаменяемости; научится работать со справочной литературой и нормативно-технической документацией.
Метод исследования – расчетно-аналитический с использованием стандартных пакетов: Math Cad AutoCAD Word.
Задачей курсового проекта является выбор и обоснование допусков и посадок на соединенных поверхностях деталей соответственно их функционального назначения; расчет и проектирование калибров и контркалибров; определение размерных взаимосвязей между отдельными поверхностями; выбор и обоснование параметров зубчатого колеса которые контролируются; выполнение рабочего чертежа узла.
ДОПУСК ПОСАДКА КАЛИБР КОНТРКАЛИБР ОТКЛОНЕНИЕ НАТЯГ ЗАЗОР НОМИНАЛЬНЫЙ ДИАМЕТР ПОДШИПНИК ВАЛ ОТВЕРСТИЕ КВАЛИТЕТ СТЕПЕНЬ ТОЧНОСТИ.
Описание конструкции5
Гладкие цилиндрические соединения6
1 Расчет и выбор посадок с зазором6
2 Расчет и выбор посадки с натягом.8
3 Расчет и выбор переходной посадки13
4 Расчет и проетирование калибров и контркалибров.15
Расчет посадок подшипников качения19
Расчет резьбового соединения23
Расчет шлицевого соединения26
Выбор параметров характеризующих зубчатое колесо30
Машины и механизмы состоят из деталей которые в процессе работы должны совершать относительные движения или находится в относительном покое. В большинстве случаев детали машин представляют собой определенные комбинации геометрических тел ограниченных поверхностями простейших форм. Две детали элементы которых входят друг в друга образуют соединение. В соединении элементов двух деталей один из них является внутренним (охватывающим) а другой наружным (охватываемым). В системе допусков и посадок гладких соединений наружный элемент называется валом а внутренний – отверстием. Разность размеров отверстия и вала до сборки определяет характер соединения деталей или посадку.
При проектировании деталей машин их геометрические параметры задаются размерами элементов а также формой и взаимным расположением их поверхностей. При изготовлении возникают отступления геометрических параметров реальных деталей от идеальных значений.
Вследствие колебания размеров деталей при изготовлении значения зазоров и натягов при сборке деталей также будут колебаться.
При построении системы допусков и посадок выполнении чертежей и измерениях размеров как правило удобнее выражать не в абсолютной форме – полным числовым значением – а с помощью отклонения его от номинального размера. Стандартизация систем допусков и посадок и их применение при проектировании изготовлении эксплуатации и ремонте машин и приборов дает большой технико-экономический эффект. Применение специальных допусков и посадок должно быть технически и экономически обосновано.
ОПИСАНИЕ КОНСТРУКЦИИ
Данный узел представляет собой конструкцию машины или механизма в которой вал 4 вращается в подшипниках качения 3 которые установлены в корпусе 2. На валу установлены маслоразбрызгивающие кольца 5 и зубчатое колесо. Крутящий момент передается от шкива 1 через шлицы вала 4 на ступицу 6 зубчатого колеса 7. Шкив 1 на шлицах удерживается гайкой 8.
Между валом 4 и подшипниками 3 дана посадка с натягом. Крутящий момент зубчатого колеса Мкр= 210 Hм. Между ступицей 6 и зубчатым колесом 7. Переходная посадка на шпоночном соединении между валом 4 и зубчатым колесом 7.
Исходные данные к курсовой работе представлены в таблице 1.1.
Таблица 1.1 – Исходные данные
ГЛАДКОЕ ЦИЛИНДРИЧЕСКОЕ СОЕДИНЕНИЕ
1 Расчёт и выбор посадки с зазором
Зазор – это разность размеров отверстия и вала если размер отверстия больше размера вала.
Посадки с зазором предназначены для подвижных и неподвижных соединений деталей. В подвижных соединениях зазор служит для обеспечения свободного перемещения размещения слоя смазки и прочего. В неподвижных соединениях посадки с зазором применяются для обеспечения беспрепятственной сборки деталей (в особенности сменных).
Рассчитаем допуски на зазор для соединения ø30
Предельные размеры и допуски на отверстие ø30Е9
Предельные размеры отверстия равны:
D max = D + ES = 30 + 0092 = 30092 ( мм) (2.1)
D min = D + EI = 30 + 004 = 3004 (мм) (2.2)
Допуск на изготовление отверстия составляет:
TА = D max – D min = ES – EI = 0092 – 004 = 0052 (мм) (2.3)
Исполнительный размер отверстия равен:
Предельные размеры и допуски для вала ø30k6
Предельные размеры вала равны:
d max = d + es = 30 + 0015 = 30015 (мм) (2.5)
d min = d + ei = 30 + 0002 = 30002 (мм) (2.6)
Допуск на изготовление вала составляет:
TB = d max – d min = es – ei = 0015 – 0002 = 0013 (мм) (2.7)
Исполнительный размер вала равен:
Зазор соединения ø30
Smin = Dmin – d max = 3004 - 30015 = 0025 (мм) (2.9)
Smax = D max – d min = 30092 - 30002 = 009 (мм) (2.10)
TS = TA + TB = 0052 + 0013 = 0065 (мм) (2.11)
По полученным данным строим схему расположения полей допусков и предельных размеров соединения.
2 Расчёт и выбор посадок с натягом
Натяг – это разность размеров вала и отверстия если размер вала больше размера отверстия
Посадка с натягом – это посадка в которой образуется натяг в соединении. Посадки с натягом используются для неподвижных неразъемных соединений деталей. Иногда для повешения надежности соединений устанавливают шпонку или штифт. Расчет посадки с натягом выполняют исходя и функционального назначения в целях обеспечения прочности соединений при передаче деталей которые касаются крутящего момента или осевого усилия.
Посадка с натягом будет пригодна к эксплуатации если при минимальном натяге обеспечиваться неподвижность соединения то есть передаваться заданный крутящий момент или осевое усилие. По максимальному натягу рассчитывают наиболее слабую деталь на прочность.
По заданному значению Мкр = 210 Нм рассчитываем требуемое минимальное удельное давление между сопрягаемыми поверхностями.
где l – длина соединения. l = 10 мм = 1010-3 м.
D – номинальный диаметр соединения. D = 70 мм = 7010-3 м.
F – коэффициент трения. f = 01 (из таблицы 3.5).
Получив результат минимального удельного давления между сопрягаемыми поверхностями можем определить минимальный натяг в соединении.
где Е1 Е2 – модуль упругости. Е = 21011
С1 С2 – коэффициент Лямэ. Определяется
где – коэффициент Пуассона = 03
Таким образом минимальный натяг в соединении по формуле (2.13) составляет:
Рассчитанный минимальный натяг необходимо увеличить с учётом поправки Um которая учитывает смятие неровностей контактируемых поверхностей. Um рассчитывают по формуле:
Um =2К(RZA+RZB) = 2(1610-3 + 1.610-3) = 00096 (мм)=64(мкм) (2.16)
где К – коэффициент учитывающий смятия неровностей; К = 1
RZB – высота неровностей.
RaA=0.8 RZA=4* RaA=0.8*4=3.2
RaB=0.4 RZB=4* RaB=0.4*4=1.6
Таким образом минимальный натяг в соединении будет составлять
Nmin = Nmin расч + Um = 332+64=396 (мкм) (2.17)
Для определения максимального допустимого натяга в соединении необходимо определить наибольшее допустимое давление Pmax на сопрягаемых поверхностях.
В расчётах принимаем меньшее из значений Pmax A и Pmax B
Для отверстия максимальное давление составляет:
Для вала максимальное давление составляет:
Таким образом расчётный максимальный натяг составляет:
Определяем максимальный натяг с учётом поправки учитывающей смятие неровностей контактирующих поверхностей Um.
Nmax = Nmax расч · γуд+Um = 1515 ·05+022 = 8535 (мкм) (2.21)
Принимая во внимание что:
Nmin т = dmin – Dmax = ei – ES (2.22)
Nmax т = dmax – Dmin = es – EI (2.23)
А также учитывая что номинальный диаметр отверстия равен 70 мм и выполнено оно по шестой степени точности для которой ES = +0019 мм а EI = 0000 мм можем рассчитать теоретическое предельное верхнее и нижнее отклонение для вала
еiт = Nmin + ES = 396+19=586 (мкм) (2.24)
еsт = Nmax + EI = 8535+0 = 8535 (мкм) (2.25)
Таким образом по ГОСТ 8809 – 71 выбираем для вала поле допуска по седьмому квалитету точности принимая во внимание что:
Тогда ei принимаем равным 0059 мм а es принимаем равным 0078 мм что соответствует ø70s6. Таким образом:
Предельные размеры и допуски на отверстие ø70Н6
D max = Dн + ES = 70 + 0030 = 70019 (мм) (2.26)
D min = Dн + EI = 70 + 0 = 70 (мм) (2.27)
TA = D max – Dmin = ES – EI = 0019 – 0 = 0019 (мм) (2.28)
DA исп =Dmin+Ta = 70+0.019 (мм) (2.29)
Предельные размеры и допуски для вала ø70s6
d max = dн + es = 70 + 0078 = 70078 (мм) (2.30)
d min = dн + ei = 70 + 0059 = 70059 (мм) (2.31)
TB = d max – d min = es – ei = 0078 – 0059 = 0019 (мм) (2.32)
d исп =dmax-TB = 70078-0019 (мм) (2.33)
В результате действительный максимальный и минимальный натяг в соединении ø70 будет
Nmin = ei – ES = 0059 – 0019 = 004 (мм) (2.34)
Nmax = es – EI = 0078 – 0 = 0078 (мм) (2.35)
TN=Nmax-Nmin=0078-004=0038
По полученным данным строим схему расположения полей допусков и предельных размеров соединения с натягом.
3 Расчёт и выбор переходной посадки
Переходную посадку выбирают в зависимости от точности центрирования и условий сборки и разборки деталей. Из ГОСТ 1643-81 при заданной степени точности находим значение радиального биения в зависимости от заданного диаметра вала. По выбранному значению рассчитываем наибольший допустимый зазор в соединении:
где Fr – по ГОСТ1643 – 81.
Предельные размеры и допуски на отверстие ø28Н7
D max = Dн + ES = 28 + 0021 = 28021 (мм) (2.37)
D min = Dн + EI = 28 + 0 = 28 (мм) (2.38)
TA = D max – D min = ES – EI = 0021 – 0 = 0021 (мм) (2.39)
DA исп = 28+0021 (мм) (2.40)
Предельные размеры и допуски для вала 28
eip=ES-Smax=21-18 = 3 (мкм) - соответствует m6
d max = dн + es = 28 + 0021 = 28021 (мм) (2.41)
d min = dн + ei = 28 + 0008 = 28008 (мм) (2.42)
TB = d max – d min = es – ei = 0021 – 0008 = 0013 (мм) (2.43)
dB исп = 28021 -0013 (мм) (2.44)
Таким образом выбрав поля допусков для отверстия и вала можем рассчитать переходную посадку для соединения ø28.
Nmax = es - EI = 0021 - 0= 0021 (мм) (2.45)
Smax = ES - ei = 0021 – 0008 = 0013 (мм) (2.46)
ТП =ТА + ТВ = 0021- 0013 = 0008 (мм) (2.47)
Так как Smax [Smax] то переходная посадка выбрана верно
4 Расчёт и проектирование калибров и контркалибров
Калибры – это измерительные инструменты предназначенные для проверки и контроля точности изготовления изделия. Калибры подразделяют на калибры-пробки для контроля диаметров отверстий и на калибры-скобы для контроля наружных диаметров валов.
Z = 00025 (мм) Z1 = 0004 (мм)
У = 0002 (мм) У1 = 0003 (мм)
Н = 0003 (мм) Н1 = 0005 (мм)
4.1 Расчёт калибров-пробок для отверстия ø70Н6
D max = Dн + ES = 70 + 0019 = 70019 (мм) (2.47)
D min = Dн + EI = 70 + 0 = 70 (мм) (2.48)
Определяем размеры рабочего проходного калибра.
Р-ПРmax = D min + Z + H2 = 70 + 00025 + 00032 = 70004 (мм) (2.49)
Р-ПРmin = D min + Z – H2 = 70 + 00025 – 00032 = 70001 (мм) (2.50)
Р-ПРизн = D min – У = 70 – 0002 = 69998 (мм) (2.51)
IT = Р-ПРmax – Р-ПРmіn = 70004 – 70001 = 0003 (мм) (2.52)
Исполнительный размер калибра:
Р-ПРисп =Р-ПРmax-Н= 70004-0003 (мм) (2.53)
Определяем размеры рабочего непроходного калибра.
Р-НЕmax = D max + H2 = 70019 + 00032 = 700205 (мм) (2.54)
Р-НЕmin = D max – H2 = 70019 – 00032 = 700175(мм) (2.55)
IP = Р-НЕmax – Р-НЕmіn = 700205 – 700175 = 0003 (мм) (2.56)
Р-НЕисп = = 700205 -0003 (мм) (2.57)
4.2 Расчёт калибров-скоб для вала ø70s6
d max = dн + es = 70 + 0078 = 70078 (мм) (2.58)
d min = dн + ei = 70 + 0059 = 70059 (мм) (2.59)
Р-ПРmax = d max – Z1 + H12 =
=70078 – 0004 + 00052 = 700765 (мм) (2.60)
Р-ПРmin = d max – Z1 – H12 =
= 70078 – 0004 - 00052 = 700715 (мм) (2.61)
Р-ПРизн = d max + У1 = 70078 + 0003 = 70081 (мм) (2.62)
IT = Р-ПРmax – Р-ПРmіn = 700765 – 700715= 0005 (мм) (2.63)
Р-ПРисп = = 700715+0005(мм) (2.64)
Р-НЕmax = d min + H12 = 70059 + 00052 = 700615 (мм) (2.65)
Р-НЕmin = d min – H12 = 70059 – 00052 = 700565 (мм) (2.66)
IT = Р-НЕmax – Р-НЕmіn = 700615 – 700565 = 0005 (мм) (2.67)
Р-НЕисп = = 700565 +0005 (мм) (2.68)
4.3 Контрольный калибр рабочего проходного калибра.
Предельные размеры контрольного калибра рабочего проходного калибра.
К-РПmax = d max – Z1 + Hр2 =
= 70078 – 0004 + 00022 = 70075 (мм) (2.69)
К-РПmin = d max – Z1 – Hр2 =
= 70078 – 0004 - 00022 = 70073 (мм) (2.70)
IT = К-РПmax – К–РПmіn = 70075 – 70073 = 0002 (мм) (2.71)
К-РПисп = = 70075-0002 (мм) (2.72)
Контрольный калибр износа рабочего проходного калибра
К-Иmax = d max + У1– 1 + Hр2 =
= 70078 + 0003 – 0 + 00022 = 70082 (мм) (2.73)
К-Иmin = d max + У1– 1 – Hр2 =
= 70078 + 0003 – 0 – 00022 = 7008 (мм) (2.74)
IT = К-Иmax – К-Иmіn = 70082 – 7008 = 0002 (мм) (2.75)
К-Иисп = = 70082-0002 (мм) (2.76)
4.4 Контрольный калибр рабочего непроходного калибра.
К-НЕmax = d min + 1 + Hр2 =
= 70059 + 0 + 00022 =7006 (мм) (2.77)
К-НЕmin = d min + 1 – Hр2 =
= 70059 + 0 – 00022 = 70058 (мм) (2.78)
IT = К-НЕmax – К-НЕmіn = 7006 – 70058 = 0002 (мм) (2.79)
К-НЕисп = = 7006-0002 (мм) (2.80)
РАСЧЁТ ПОСАДОК ПОДШИПНИКОВ КАЧЕНИЯ
Подшипники качения применяются в машиностроении в качестве опор узлов а также для передачи крутящего момента и восприятия осевой нагрузки.
Для определения и назначения посадок для наружной и внутренней обоймы подшипника необходимо рассчитать радиальную реакцию.
k1 – динамический коэффициент посадки; k1 = 18.
k2 – коэффициент учитывающий ослабление посадочного натяга
k3 – коэффициент неравномерности распределения нагрузки; k3 = 1
R – радиальная реакция опоры на подшипник; R = 0429 кН
b – ширина посадочного места кольца; b = 0015
Исходя из значения радиальной нагрузки и согласно таблицы 4.92 назначаем посадку для внутреннего и наружного колец подшипника. Для наружного кольца назначаем посадку с зазором а для внутреннего кольца назначаем посадку с натягом.
Предельные размеры и допуски на отверстие ø72H7
D max = Dн + ES = 72 + 003 = 7203 (мм) (3.2)
D min = Dн + EI = 72 + 0 = 72(мм) (3.3)
TD = D max – D min = ES – EI = 003– 0 = 003 (мм) (3.4)
D исп = = 72+0030 (мм) (3.5)
Предельные размеры и допуски для вала øl 0
d max = dн + es = 72 + 0 = 72 (мм) (3.6)
d min = dн + ei = 72 + (- 0013) = 71987 (м) (3.7)
Зазор соединения ø72
Smin = D min – d max = 72 – 72 = 0 (мм) (3.8)
Smax = D max – dmin = 72.03 – 71.987 = 0043 (мм) (3.9)
TS = TD + Td = 003 + 0013 = 0043(мм) (3.10)
Рассчитаем допуски для соединения ø30
Предельные размеры и допуски на отверстие ø30L0
D max = Dн + ES = 30 + 0 = 30 (мм) (3.11)
D min = Dн + EI = 30 + (-0008) = 29992 (мм) (3.12)
TD = D max – D min = ES – EI = 0 – (- 0008) = 0008 (мм) (3.13)
D исп = = 29992+0008 (мм) (3.14)
d max = dн + es = 30 + 0015 = 30015 (мм) (3.15)
dB min = dн + ei = 30 + 0002= 30002 (мм) (3.16)
Td = d max – d min = es – ei = 0015 – 0002 = 0013 (мм) (3.17)
d исп =dmax-Tb = 30015 -0013 (мм) (3.18)
Nmax = es - Е = 0015 – (-0008) = 0023 (мм) (3.19)
Nmin = ei - ES = 0002 – 0 = 0002 (мм) (3.20)
TS (TN) = TD + Td = 0013 + 0008 = 0021 (мм) (3.21)
РАСЧЁТ РЕЗЬБОВОГО СОЕДИНЕНИЯ
Резьбовое соединение – это соединение предназначенное для соединения деталей при помощи навинчивания гайки на болт по винтовой линии именуемой резьбой.
Резьбы обеспечивают необходимую прочность соединения обеспечивают простоту сборки и разборки узлов и агрегатов.
Из ГОСТа 24705 – 81 выбираем значения наружного среднего и внутреннего диаметров для резьбы М8×1 мм.
Для отверстия М8×1 из ГОСТ 16093 – 81 выбираем поле допуска на резьбу равным 7Н.
EI (D1 D2 D) = 0 (мм)
Dmin = D + EI (D) = 8000 + 0 = 8 (мм) (4.1)
D2 max = D2 + ES (D2) = 7.35 + 019 = 754 (мм) (4.2)
D2 min = D2 + EI (D2) = 735 + 0 = 735 (мм) (4.3)
D1 max = D1 + ES (D1) = 6917 + 03 = 7217 (мм) (4.4)
D1 min = D1 + EI (D1) = 6917 + 0 = 6917 (мм) (4.5)
Допуск на изготовление составляет:
TD2 = ES (D2) – EI (D1) = 019 – 0 = 019 (мм) (4.6)
TD1 = ES (D1) – EI (D2) = 03 – 0 = 03 (мм) (4.7)
Исполнительный размер резьбы составляет:
D2 исп = = 735+019 (мм) (4.8)
D1 исп = = 6917+03 (мм) (4.9)
Для винта М8×1 из ГОСТ 16093 – 81 выбираем поле допуска на резьбу равным 8g.
es (d1 d2 d) = -0026 (мм)
ei (d2) = - 0206 (мм)
ei (d) = - 0306 (мм)
dmax = d + es (d) = 8000 + (- 0026) = 7974 (мм) (4.10)
dmin = d + ei (d) = 8000 + (- 0306) = 7694 (мм) (4.11)
d2 max = d2 + es (d2) = 735 + (- 0026) = 7324 (мм) (4.12)
d2 min = d2 + ei (d2) = 735 + (- 0206) = 7144 (мм) (4.13)
d1 max = d1 + es (d1) = 6917 + (- 0026) = 6891 (мм) ( 4.14)
Td = es (d) – ei (d) = - 0026 – (- 0306) = 028 (мм) (4.15)
Td2 = es (d2) – ei (d2) = - 0026 – (- 0206) = 018 (мм) (4.16)
d исп = = 7974 -028 (мм) (4.17)
d 2 исп = = 7324 -018 (мм) (4.18)
Зазор для резьбы М8×1-
Smax = ES (D2) – ei (d2) = 019 – (- 0206) = 0396 (мм) (4.19)
Smin = EI (D2) – es (d2) = 0 – (- 0026) = 0026 (мм) (4.20)
Таблица 5.1 – Предельные размеры резьбового соединения.
По полученным данным строим схему расположения полей допусков и предельных размеров резьбового соединения.
РАСЧЁТ ШЛИЦЕВОГО СОЕДИНЕНИЯ
Шлицевое соединение предназначено для обеспечения соосности деталей и передачи крутящего момента через эти детали.
Шлицы обеспечивают центровку по внутреннему диаметру (наиболее точное центрирование) по наружному диаметру и центрирование по боковым поверхностям шлицев.
Поскольку деталь посаженная на вал по шлицам должна перемещаться в осевом направлении то необходимо применить центровку по внутреннему диаметру шлицев.
D max = Dн + ES = 23 + 0021 = 23021 (мм) (5.1)
D min = Dн + EI = 23 + 0 = 23 (мм) (5.2)
TD = ES – EI = 0021 – 0 = 0021(мм) (5.3)
Исполнительный размер составляет:
D исп = = 23+0021 (мм) (5.4)
d max = dн +es=23-0.02=22.98 (мм) (5.5)
d min =dн +ei=23-0.041=22.959 (мм) (5.6)
Td = dmax -dmin= 22.98 – 22.959 = 0.021 (мм) (5.7)
d исп = = 22.98-0.021 (мм) (5.8)
Smax = Dmax -dmin= 23.021 – 22.959 = 0.062 (мм) (5.9)
Smin = Dmin -dmax= 23-22.98=0.02 (мм) (5.10)
Tn = TD + Td = 0.021 + 0.021 = 0.042 (мм) (5.11)
TS = Smax – Smin = 0.062 – 0.02= 0.042 (мм) (5.12)
D max = Dн + ES = 28 + 0210 = 28210 (мм) (5.13)
D min = Dн + EI = 28 + 0 = 28 (мм) (5.14)
TD = ES – EI = 0210 – 0 = 0210 (мм) (5.15)
D исп = = 28+0210 (мм) (5.16)
d max = dн + es = 28 + (- 03) = 277 (мм) (5.17)
d min = dн + ei = 28 + (- 043) = 2757 (мм) (5.18)
Td = es – ei = - 03 – (- 043) = 013 (мм) (5.19)
d исп = = 277-013 (мм) (5.20)
Smax = ES – ei = 0210 – (- 043) = 064 (мм) (5.21)
Smin = EI – es = 0 – (- 03) = 03 (мм) (5.22)
Tn = TD + Td = 021 + 013 = 034 (мм) (5.23)
TS = Smax – Smin = 064– 03 = 034 (мм) (5.24)
Bmax =B+ES=6+0.047=6.047 (мм) (5.25)
Bmin=B+EI=6+0.25=6.025 (мм) (5.26)
TD = ES – EI = 0047 – 0025 = 0022 (мм) (5.27)
Bисп =Bmin+TD= 6.025+0022 (мм) (5.28)
bmax=b+es=6-0.013=5.987 (5.29)
bmin=b+ei=6-0.028=5.972 (5.30)
Td = es – ei = - 0013 – (- 0028) = 0015 (мм) (5.31)
bисп =bmax-TD = 5.987-0015 (мм) (5.32)
Smax= Bmax- Bmin=6.047-5.972=0.075 (мм) (5.33)
Smin=Bmin-bmax=6.025-5.987=0.038(мм) (5.34)
Tn = TD + Td = 0021 + 0015= 0037 (мм) (5.35)
TS = Smax – Smin = 0075– 0038 = 0037(мм) (5.36)
По полученным данным строим схему расположения полей допусков и
предельных размеров соединения.
ВЫБОР ПАРАМЕТРОВ ХАРАКТЕРИЗУЮЩИХ ЗУБЧАТОЕ КОЛЕСО
Принятие параметров точности зубчатого колеса
Зубчатое цилиндрическое колесо z=35 ; m=25 мм.
Профиль эвольвентный по ГОСТ 13755-81.
Цилиндрическая зубчатая передача 9 степени по нормам кинематической точности 9 степени по нормам плавности 9 степени по нормам контакта зубьев.
Согласно ГОСТу 1643-81 устанавливаем вид бокового зазора В и вид сопряжения в так как зубчатое зацепление не ответственно.
Согласно ГОСТу 1643-81 устанавливаем контролируемые нормы кинематической точности и допуски на них.
Контролируем по показателю .
Согласно ГОСТ 1643-81 устанавливаем контролируемые нормы плавности работы и допуски на них.
Контролируем по показателю предельное отклонение шага зацепления.
Согласное гост 1643-81 устанавливаем контролируемые нормы контакта зубьев и допуски на них.
Контролируем по показателю
Допуск параллельности осей:
Допуск на перенос осей:
Согласно госту 1643-81 устанавливаем нормы и допуски бокового зазора.
где W1= 780048 устанавливается согласно госту 2403-75;
Контролируемы параметры: W
В ходе выполнения курсовой работы был произведен выбор и обоснование допусков и посадок на соединенных поверхностях деталей соответственно их функционального назначения.
Была выбрана и рассчитана посадка с зазором 30 рассчитана посадка с натягом 70 переходная посадка в месте шпоночного соединения 28. Был произведен расчет и проектирование калибров и контркалибров для посадки с натягом. Выбраны и рассчитаны посадки на внутренний и на внешний диаметры подшипника. Была выбрана и обоснована посадка с зазором для резьбового соединения М8x1-. Произведен расчет шлицевого соединения по внутреннему диаметру и боковым граням. Был произведен выбор и обоснование контролируемых параметров зубчатого колеса.
Выполнена графическая часть проекта с помощью стандартного пакета AutoCAD.
Мягкова В.И. Допуски и посадки. Справочник : У 2–х ч. Л.: Машиностроение 1982. – Ч. I. – 543с.
Мягкова В.И. Допуски и посадки. Справочник : У 2–х ч. Л.: Машиностроение 1982. – Ч. I. – 446с.
Методические указания к курсовой работе по дисциплине. Взаимозаменяемость стандартизация и технические измерения : г.Запорожье ЗНТУ 2001. - 104с.
Болонкина И.И. Кутай А.К..Точность и производственный контроль в машиностроении. Справочник : – Л.: Машиностроение 1983. – 348 с.
ГОСТ 25347-82 Единая система допусков и посадок. введ. 2002–07–01. – Минск : Межгос. совет по стандартизации метрологии и сертификации ; М. : Изд-во стандартов cop. 2002. – 3 с. – (Система стандартов по информации библиотечному и издательскому делу).
ГОСТ 18362-73 Калибры-скобы односторонние двупредельные для диаметров свыше 10 до 100 мм. введ. 2002–07–01. – Минск : Межгос. совет по стандартизации метрологии и сертификации ; М. : Изд-во стандартов cop. 2002. – 3 с. – (Система стандартов по информации библиотечному и издательскому делу).
ГОСТ 14810-69 Калибры-пробки двусторонние со вставками диаметром свыше 3 до 50 мм. введ. 2002–07–01. – Минск : Межгос. совет по стандартизации метрологии и сертификации ; М. : Изд-во стандартов cop. 2002. – 3 с. – (Система стандартов по информации библиотечному и издательскому делу).
ГОСТ 1643-81 Передачи зубчатые цилиндрические допуски. введ. 2002–07–01. – Минск : Межгос. совет по стандартизации метрологии и сертификации ; М. : Изд-во стандартов cop. 2002. – 3 с. – (Система стандартов по информации библиотечному и издательскому делу).
Рекомендуемые чертежи
- 01.07.2014