Нормирование точности и технические измерения Курсовой проект Эскиз №12 позиция 2



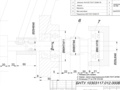
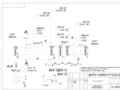

- Добавлен: 25.10.2022
- Размер: 3 MB
- Закачек: 0
Описание
Состав проекта
![]() |
![]() |
![]() ![]() ![]() ![]() |
![]() ![]() |
![]() ![]() ![]() |
![]() ![]() |
![]() ![]() ![]() ![]() |
![]() ![]() ![]() ![]() |
![]() ![]() |
Дополнительная информация
Вал-шестерня.dwg

остальных поверхностей 200 240HB
Точность зубчатого венца по ГОСТ 1643-81.
Общие допуски по ГОСТ 30893.1-2002.
БНТУ.10303117.012.001
Курсовая работа.doc
Расчет допусков и посадок гладких цилиндрических сопряжений7
Выбор методик измерительного контроля геометрических параметров детали12
Рисунок 3.6 – Общая схема расположений контрольных сечений и направлений14
Расчет посадок подшипника качения15
Расчет норм точности резьбовых соединений20
Рисунок 5.1 - Схема расположения полей допусков резьбового сопряжения М90-8H8h21
Расчет норм точности шпоночного соединения22
Выбор контрольного комплекса для зубчатого колеса26
Технические нормативные правовые акты38
Современное машиностроительное производство может быть высокопроизводительным и обеспечить требуемое качество выпускаемых изделий при их серийном и массовом выпуске только при его организации на основе принципа взаимозаменяемости.
Принципом взаимозаменяемости называется комплекс научно-технических исходных положений выполнение которых при конструировании производстве и эксплуатации обеспечивает взаимозаменяемость деталей сборочных единиц и изделий.
Для того чтобы выделить основные элементы взаимозаменяемости изделий рассмотрим общую схему производственного процесса в машиностроении (рисунок 1).
Рисунок 1 – Общая схема производственного процесса в машиностроении
Таким образом к основным элементам обеспечения взаимозаменяемости изделий можно отнести:
Нормирование параметров;
Контроль соответствия действительных значений параметров установленных стандартизированными требованиями.
Причем выделенные элементы относятся как к продукции на различных этапах ее преобразования так и к технологическим процессам преобразующим продукцию.
Назначение и анализ норм точности геометрических параметров деталей
По исходному чертежу узла сложного изделия необходимо дать краткое описание его состава и работы. С учетом исходных данных об узле необходимо выбрать посадки гладких цилиндрических поверхностей включая посадки подшипников качения на вал и в корпус. Выбрать посадки для шпоночных и шлицевых соединений резьбовую посадку а также нормы точности зубчатой передачи. Дать краткое описание каждого выбранного стандартного соединения со ссылкой на соответствующий документ или другой источник информации. Оформить чертеж общего вида узла в соответствии в соответствии с требованиями общих стандартов ЕСКД. Выполнить рабочие чертежи вала и зубчатого колеса с указанием всех необходимых норм точности. Дать краткое обоснование выбранных норм точности. При выполнении зубчатого колеса особое внимание следует обратить на таблицу параметров зубчатого колеса.
Исходные данные: Эскиз №12 позиция 2.
Редуктор (рисунок 1.1) предназначен для повышения тяговой способности приводного вала и уменьшения частоты его вращения на котором установлен поворотный стол станка. Состоит из ведущего вала-шестерни. Вал опирается на два шариковых радиальных подшипника зафиксированных втулками. Ведущая шестерня входит в зацепление с зубчатыми колесами установленными на ведомых валах редуктора через призматические шпонки. Ведомый вал опирается на два шариковых радиальных подшипника. На выходном конце вала имеется шпоночный паз для установки призматической шпонки передающей крутящий момент на круглый стол станка.
Производим выбор посадок соединений узла №2 пользуясь рекомендациями [4].
Для соединений «крышка-корпус» выбираем посадку H7d9 которая обеспечит зазор в соединениях.
Выбор посадок подшипников качения на вал и отверстие корпуса осуществляют в соответствии с требованиями к точности и необходимой плотности соединения колец с посадочными поверхностями. На внутреннее кольцо подшипника назначаем посадки L6k6 а на наружное – H7l0 т.к. подшипник имеет нормальную степень точности.
Зубчатое колесо установлено на валу переходной посадкой Н7k6.
Расчет допусков и посадок гладких цилиндрических сопряжений
Для двух заданных гладких цилиндрических соединений дать краткую характеристику посадок (вид предпочтительность принадлежность к системе рекомендации по использованию). Построить схему распределения полей допусков рассчитать предельные размеры сопрягаемых деталей зазоры(натяги) табличные и вероятные а также допуски посадок. Для переходных посадок определить вероятности получения зазоров и натягов. Построить диаграмму распределения зазоров (натягов) партии соединения.
1 Расчет посадки с зазором
H10f9 – посадка с зазором в системе основного отверстия.
Данная посадка с наибольшей вероятностью зазора.
Посадки с наименьшим гарантированным зазором («движения») используют для обеспечения точного вращения деталей с небольшой скоростью.
Посадки с зазором предназначены для образования подвижных соединений как правило разъемных. Относительная подвижность деталей таких сопряжений обеспечивается за счет гарантированных зазоров. Примерами применения посадок с зазором являются соединения крышек и фланцев с корпусами машин втулок и валов.
Данная посадка с гарантированным зазором.
Рассчитываем предельные размеры отверстия 56 H10:
по ГОСТ 25346-89 определяем величину допуска IT=120 мкм;
по ГОСТ 25346-89 определяем нижнее отклонение EI= 0.
Верхнее отклонение ES = EI + IT = 0+120 = +120 мкм.
Предельные размеры отверстия:
Dmax = Dном + ES = 56 +0120 = 56120 мм.
Расчет среднего диаметра отверстия Dm:
Рассчитываем предельные размеры вала 56 f9:
по ГОСТ 25346-89 определяем величину допуска IT = 74 мкм;
Верхнее отклонение es = -30 мкм.
Нижнее отклонение ei = es – IT = -30 – 74 = -104 мкм.
Предельные размеры вала:
dmax = dном + es = 56 + (-0030) = 55970 мм.
Средний диаметр вала dm:
Оформим результаты в виде таблицы.
Строим схему расположения полей допусков сопрягаемых деталей.
Рисунок 2.1 - Схема расположения полей допусков сопрягаемых деталей
Расчет предельных табличных зазоров.
Smin = Dmin – dmax = 56000– 55970 = 0030 мм.
Расчет допуска посадки
T(S) = IT(D) + IT(d) = 0120 + 0074 = 0194 мм.
Расчет среднеквадратичного отклонения зазоров
Принимаем нормальный закон распределения погрешностей и рассчитываем предельные значения вероятностных зазоров.
Расчет предельных вероятностных значений зазора:
-расчет наибольшего вероятностного зазора
- расчет наименьшего вероятностного зазора
Smin.вер.= Scp - 3s(S) = 127 - 3*235= 565 мкм
Рисунок 2.2 - Распределение вероятностных зазоров
2 Расчет переходной посадки
H5m5 – переходная посадка в системе основного вала.
Для отверстия 17H5 определяем предельные отклонения и размеры:
Допуск на отверстие IT = 8 мкм
Нижнее отклонение EI= 0 мкм
Верхнее отклонение ES = 0+8= 8 мкм
Наибольший предельный диаметр отверстия Dmax = D + ES = 17-0008 =
Наименьший предельный диаметр отверстия Dmin =D + EI =17+0000 =
Для вала 17m5 определяем предельные отклонения и размеры:
Допуск на вал IT = 63 мкм
Верхнее отклонение es = 15мкм
Нижнее отклонение ei= es-IT = 15 - 8 = 7 мкм
Наибольший предельный диаметр вала dmax = d + es =17+0015= 17015 мм
Наименьший предельный диаметр вала dmin = d + ei =17+0007 =17007 мм
Строим схему расположения полей допусков переходного сопряжения17H5m5
Рисунок 2.3 – Схема расположения полей допусков переходной посадки сопрягаемых деталей
Определяем предельные зазор и натяг:
Smax = Dmax – dmin = 17008 –17007= 0001 мм
Nmax = dmax – Dmin = 17015–17000 = -0015 мм
2.5. Определяем допуск посадки:
T(SN) = ITD+ITd = 8 + 8 = 16 мкм.
Определяем величину математического ожидания появления зазоров (натягов):
M(SN) = Dср – dср = (Smax – Nmax)2 = (1-15)2 = -7 мкм так как M(SN)0 то в посадке преобладает натяг.
Определяем величину вероятных натягов посадки:
где – среднее квадратичное отклонение вала (отверстия);
Nmax вер. = Bср + 3B = M(SN) + 3SN = 7+3·189 = 1267 мкм
Nmin вер. = Sср – 3S = M(SN) – 3SN = 7-3·189 = 133 мкм
Определяем вероятность получения натяга:
P(N) = 05 + Ф(x) = 05+049 = 099 = 99%
P(S) = 05 – Ф(x) = 05-049= 001 = 1%
x = M(SN)SN =7189 = 37
Строим кривую распределения вероятных натягов
Рисунок 2.4 – Схема распределения зазоров и натягов
Выбор методик измерительного контроля геометрических параметров детали
Для заданного гладкого цилиндрического соединения выбрать и обосновать универсальные средства измерения с указанием их основных метрологических характеристик и условий использования при приемочном контроле сопрягаемых деталей по диаметрам. Привести схемы измерений и дать краткое описание реализуемых измерительных процедур.
Исходные данные: 55Н10f9.
Для заданного сопряжения 55Н10f9 необходимо подобрать средства измерения. Для этого используем РД 50-98-86 «Методические указания. Выбор универсальных средств измерений линейных размеров до 500 мм».
Для контроля вала 55f9 выбираем:
[Δ] = 10 мкм – допускаемая погрешность
IT = 74 мкм – допуск
а – микрометры рычажные (МК) с ценой деления 0002 мм при натсройке на нуль по установочной мере.
Предельная погрешность измерения Δ = 7 мкм
мкм 10 мкм – данное средство измерения подходит.
Рисунок 3.1 – Микрометр гладкий
Годность детали определяется по результатам шести измерений в трех сечениях: по длине детали 1-1 2-2 3-3 и в двух взаимно-перпендикулярных направлениях А-А и Б-Б. Схема измерения приведена на рисунке 3.2.
Рисунок 3.2 – Схема измерения
Основным недостатком измерения наружных линейных размеров деталей с использованием накладных измерительных приборов является невозможность выявления размера описанного цилиндра.
в – индикатор часового типа с ценой деления 001 мм класс точности 0.
Предельная погрешность Δ = 10 мкм.
Рисунок 3.3 – Индикатор часового типа
Т.к. Δ= 10 мкм = [Δ] = 10 мкм то данное средство измерения подходит.
2 Для контроля отверстия 55Н10 выбираем
[Δ] = 12 мкм – допускаемая погрешность
IT = 120 мкм – допуск
б - Нутромеры индикаторные (НИ) с ценой деления отсчетного устройства 001 мм.
Предельная погрешность измерения Δ = 10 мкм
мкм 12 мкм – выбранное средство измерения подходит.
Рисунок 3.4 - Нутромер индикаторный
Рисунок 3.5 - Схема настройки нутромера
Рисунок 3.6 – Общая схема расположений контрольных сечений и направлений
Расчет посадок подшипника качения
Исходя из заданных характеристик и условий работы подшипникового узла дать полную расшифровку обозначения подшипника качения выбрать его посадки на вал и в корпус. Для выбранных посадок построить схемы расположения полей допусков рассчитать предельные размеры сопрягаемых деталей а также табличные зазоры (натяги). Произвести проверку наличия радиального зазора в подшипнике качения после установки его на вал и в корпус.
Определить необходимый и достаточный набор требований к точности геометрических параметров элементов деталей сопрягаемых с подшипниками качения и обозначить их на эскизах соответствующих деталей.
Исходные данные: подшипник 307. Вид нагружения колец: внутреннее – циркуляционное наружное – местное. Режим работы тяжелый.
(первая и вторая позиции) – условное обозначение диаметра подшипника качения. Диаметр подшипника качения равен 07*5=35 мм.
(третья позиция) – тяжелая серия по диаметру
(четвертая позиция) – шариковый радиальный
(пятая и шестая позиции) - основного конструктивного исполнения
(седьмая позиция) – узкой серии ширин подшипников
– класс точности подшипника качения нормальный.
По ГОСТ 8338-81 определяем основные размеры:
d = 35 мм – внутренний диаметр
D = 80 мм – наружный диаметр
r= 25 мм - радиус закругления кольца
Категория подшипника – А.
C=33200 динамическая грузоподъемность
C0=18000 статическая грузоподъемность
m=0447 кг масса подшипника.
Выбираем посадки внутреннего кольца подшипника на вал и наружного кольца в корпус.
Вращающимся элементом в узле является вал поэтому внутреннее кольцо подшипника нагружено циркуляционно и во избежание проскальзывания кольца относительно вала необходимо выбрать посадку с натягом.
Наружное кольцо подшипника установлено в корпус неподвижно испытывает местное нагружение и поэтому необходимо выбрать посадку с зазором.
Расчетная долговечность соответствующая режимам работы: нормальный — от 5000 до 10000 ч.;
По ГОСТ 3325-85 выбираем рекомендуемую посадку вала сопряжённой с подшипником качения. Для циркуляционного вида нагрузки внутреннего кольца при тяжёлом режиме рекомендуются посадки L0js6 и L0k6 Выбираем посадку L0k6.
Выбираем поле допуска отверстия корпуса. Для местного вида нагрузки внутреннего кольца и при нормальном режиме работы подшипника рекомендуютя посадки Js7l0 и Jsl6. Выбираем Js7l0.
Определяем предельные отклонения среднего диаметра отверстия.
Верхнее отклонение ES = 0
Нижнее отклонение EI = -10 мкм;
Наибольший предельный диаметр вала
L0max = L0 + ES = 35+0 = 35000 мм
Наименьший предельный диаметр вала
L0min = L0 + EI = 35+(-0010)= 34990 мм.
Верхнее отклонение es = +15
Наибольший предельный диаметр отверстия
l0max = l0 + es = 80+0015 =80015 мм
Наименьший предельный диаметр отверстия
l0min = l0 + ei = 80+(-0015) =79985 мм.
Определяем предельные отклонения и размеры вала 35k6:
Допуск на вал IT = 16 мкм
Нижнее отклонение ei = +2 мкм
Верхнее отклонение es = IT + e
Наибольший предельный диаметр вала dmax = d + es = 35+0018 = 35018 мм
Наименьший предельный диаметр вала dmin = d + ei = 35+0002 = 35002 мм.
Строим схему расположения полей допусков сопряжения 35 L0k6
Рисунок 4.1 – Схема расположения полей допусков сопряжения 35 L0k6
Определяем предельные натяги в посадке:
Nmax = dmax – L0min = 35018-34990 = 0028 мм
Nmin = dmin – L0max = 35002-35000 = 0002 мм
Nср. = (Nmax – Nmin)2 = (0028+0002)2 = 0015 мм.
T(N) = IT(D) + IT(d) = 0010 + 0016= 0026 мм.
Т(N)= Nmax –Nmin=0.028-0.002=0.026 мм
Определяем предельные отклонения и размеры отверстия 80Js7:
Нижнее отклонение EI = -15
Верхнее отклонение ES = +15 мкм;
Dmax = D + ES = 80+0015 = 80015 мм
Dmin = D + EI = 80+(-0015) = 79985 мм.
Строим схему расположения полей допусков сопряжения 80 Js7l0.
Рисунок 4.2 – Схема расположения полей допусков сопряжения 80 Js7l0
Опредедяем предельные зазоры в посадке:
Smax = Dmax – l0min = 80.015-79987 = 0028 мм
Smin = Dmin – l0max = 79985-80000 = -0015
Sср. = (Smax + Smin)2 = (0028+(-0015))2 = 00065 мм.
T(S) = IT(D) + IT(d) = 0030+ 0016 = 0046 мм.
Т(S)= Smax –Smin=0.028-(-0015)=0.043 мм
Расчёт на заклинивание:
Для этого проводят расчёт эффективного натяга для кольца которое испытывает циркуляционное нагружение:
Nэф. =085·Nср. =085·0015=00128 мм
Затем определяем диаметральную деформацию беговой дорожки кольца
d1 = Nэф.(dd0) =00128 (35464) = 000965 мм
Приведенный внутренний диаметр кольца
d0 =d+(D-d)4 = 35+(80-35)4 =464 мм
Тогда зазор в подшипнике Grпос после посадки с натягом
Gпос = Gr ср. - d1 = 125 – 965 = 285 мкм
Среднее значение предельного зазора
Gr ср. = (Gr min+ Gr max)2 = (5+20)2 =125
Минимальное значение предельного зазора Gr min =5 мкм
Максимальное значение предельного зазора Gr max =20 мкм
Gпос = 285 мкм Grmax = 20 мкм следовательно заклинивания не произойдет.
Требования проставляемые на посадочную поверхность подшипника:
Шероховатость поверхности:
- посадочной поверхности вала под кольцо подшипника Ra=063 мкм;
- торцовой поверхности корпуса заплечиков Ra=25 мкм и заплечиков вала Ra=25 мкм;
- посадочной поверхности корпуса под кольцо подшипника Ra=125 мкм
Допуск круглости посадочной поверхности вала под кольцо подшипника – 4 мкм;
Допуск профиля продольного сечения посадочной поверхности вала под кольцо подшипника – 4 мкм;
Допуск круглости посадочной поверхности корпуса под кольцо подшипника – 7.5 мкм;
Допуск профиля продольного сечения посадочной поверхности корпуса под кольцо подшипника – 7.5 мкм.
Допуск торцевого биения заплечиков вала – 25 мкм;
Допуск торцевого биения заплечиков корпуса – 46 мкм.
Допуск соосности – 8 мкм.
Рисунок 4.3 – Эскизы вала и корпуса в местах установки подшипников качения
Расчет норм точности резьбовых соединений
Дана резьбовая посадка М90-8H8h:
M – резьба метрическая
– номинальный диаметр сопряжения
– шаг резьбы крупный
H8h – резьбовая посадка с зазором
где 8H – поле допуска внутренней резьбы (гайки) по среднему и внутреннему диаметрам;
h – поле допуска наружной резьбы (болта) по среднему и наружному диаметрам.
Определяем номинальные размеры резьбы:
Определяем предельные отклонения и размеры внутренней резьбы М90-8H:
Dmin = D + EI = 90000+0 = 90000 мм
D2 max = D2 + ES = 86103+0600 = 86.703 мм
D2 min = D2 + EI = 86103+0 = 86103 мм
D1 max = D1 + ES = 83505+1250 = 84755 мм
D1 min = D1 + EI = 83505+0 = 83505 мм
Определяем предельные отклонения и размеры наружной резьбы
dmax = d + es = 90000+0 = 90000 мм
dmin = d + ei = 90000+(-0950) = 89050 мм
d2 max = d2 + es = 86103+0 = 86103 мм
d2 min = d2 + ei = 86103+(-0450) = 85653 мм
d1 max = d1 + es = 83.505+0 = 83505 мм
Строим схему расположения полей допусков резьбового сопряжения
Рисунок 5.1 - Схема расположения полей допусков резьбового сопряжения М90-8H8h
Расчет норм точности шпоночного соединения
Для данного вида шпоночного соединения определить посадки на вал и во втулку. Построить для них схемы расположения полей допусков рассчитать предельные размеры сопрягаемых деталей табличные зазоры (натяги). Исходные данные d=85 мм l=30 мм вид соединения –свободное.
В зависимости от диаметра вала определяем основные параметры шпоночного соединения по ГОСТ 23360-78:
Рисунок 6.1 – Схема шпоночного соединения
Ширина шпонки b = 22 мм
Высота шпонки h = 14 мм
Глубина впадины вала t1 = 9 мм
Глубина впадины детали t2 = 54 мм
Диаметр вала d = 22 мм.
Исходя из выбранных параметров рассчитываем шпонку:
Шпонка 22×14×30 ГОСТ 23360-78
Расчёт шпоночного соединения по ширине шпонки:
Ширина шпонки b = 22h9
IT = 52 мкм es = 0 ei = -52 мкм
bmax = b + es = 22+0 = 22000 мм
bmin = b + ei = 22+(-0052) = 21.948 мм
Ширина паза вала B1 = 22H9
ES = 52 EI = 0 мкм IT = 52 мкм
B1 max = B1 + ES = 22+0 = 22000 мм
B1 min = B1 + EI = 22+0052= 22052 мм
Ширина паза втулки B2 = 22D10
ES = +149 мкм EI = +65 мкм IT = 84 мкм
B2 max = B2 + ES = 22+0149 = 22.149 мм
B2 min = B2 + EI = 22+0065= 22.065 мм
Строим схему расположения полей допусков шпоночного соединения по ширине шпонки.
Рисунок 6.2 – Схема расположения полей допусков шпоночного соединения по ширине шпонки
Определяем предельные зазоры в посадке:
S1 max = B1 max – bmin = 22052-21948 = 0104 мм
S1 min = bmax – B1 min = 22000-22000 = 0
S2 max = B2max – bmin =22149-21946= 0201 мм
N2 max = B2min – bmax =22065-22.000= 0065 мм
Расчёт шпоночного соединения по высоте шпонки:
Высота шпонки h = 14h11
es = 0 ei = -110 мкм IT =110 мкм
hmax = h + es = 14000+0 = 14000 мм
hmin = h + ei = 14000+(-0110) = 13890мм
Глубина паза вала t1 = 90 мм
t1 max = t1 + ES = 90+02 = 92 мм
t1 min = t1 + EI = 90+0 = 90 мм
Глубина паза втулки t2 = 54 мм
EI = 0 ES = +0.2 мм
t2 max = t2 + ES = 54+02 = 56 мм
t2 min = t2 + EI = 54+0 = 54 мм
Определяем предельные зазоры в соединении:
Smax = (t1 max + t2 max) – hmin = (92+56)-13.890 = 0910 мм
Smin = (t1 min + t2 min) – hmax = (9.0+54)-14.00 = 0.400 мм
Расчёт шпоночного соединения по длине шпонки
Длина шпонки l = 70h14
ei = es – IT = 0-074 = -074 мм
lmax = l + es = 70+0 = 7000 мм
lmin = l + ei = 70+(-074) = 69260 мм
Длина паза вала L = 70H15
ES = EI + IT = 0+12 = +12 мм
L max = L + ES =70+12 = 71200 мм
L min = L + EI = 70+0 = 7000 мм
Строим схему расположения полей допусков шпоночного соединения по длине шпонки.
Рисунок 6.3 – Схема расположения полей допусков шпоночного соединения по длине шпонки
Smax = L max – lmin = 71.200-69260 = 1940 мм
Smin = L min – lmax = 70000-70000 = 0 мм
Определяем допуск посадки:
Ts = ITD+ITd = 1200+740 = 1940 мкм.
Выбор контрольного комплекса для зубчатого колеса
Для заданной зубчатой передачи расшифровать обозначение и дать её краткую характеристику (тип условия работы область применения). Выбрать и обосновать показатели контрольного комплекса дать определение каждому показателю с приведением необходимой графической его интерпретации определить допуски и предельные отклонения выбранных контрольных показателей. Выбрать универсальные средства измерений для контроля выделенных показателей и привести их метрологические схемы дать краткие описания соответствующих измерительных процедур.
Выбор показателей контрольного комплекса зубчатого колеса
m = 25 мм; z = 42; 8-7-6-D ГОСТ 1643 – 81
m – модуль зубчатой передачи;
z – число зубьев колеса;
– степень точности по нормам кинематической точности;
– степень точности по нормам плавности работы;
– степень точности по нормам контакта зубьев в зацеплении;
Передача относится к передачам общего назначения т.к. не имеет явно выраженного эксплуатационного характера (передача не требует высокой точности передаточного отношения работает при небольших скоростях и передает средние крутящие моменты) к такой передаче не предъявляют повышенных требований по точности используют как правило для обеспечения вспомогательных функций механизмов машин (например передача ручного привода в автоматизированном оборудовании) и сельскохозяйственных машинах.
Выбор и обоснование показателей контрольного комплекса.
Для выбора показателей контрольного комплекса необходимо рассчитать делительный диаметр зубчатого колеса:
dm= m·z = 25·42 = 105мм
Для оценки метрологических параметров зубчатых колёс необходимо обеспечить их контроль по всем нормам точности (показателям кинематической точности плавности работы контакта зубьев и по боковому зазору в передаче). Стандартом регламентированы контрольные комплексы показателей обеспечивающие проверку соответствия зубчатого колеса всем установленным нормам.
Показатели точности подлежащие контролю по ГОСТ 1643-81 «Передачи зубчатые цилиндрические. Допуски»:
По нормам кинематической точности для 8 степени точности выбран частный контрольный комплекс который использует такие показатели как:
- колебания измерительного межосевого расстояния за оборот колеса;
-радиальное биение зубчатого венца.
По нормам плавности работы для 7 степени точности выбран контрольный комплекс который использует такие показатели как:
-колебания измерительного межосевого расстояния на одном зубе;
- отклонение шага зацепления;
- дискретное значение кинематической погрешности зубчатого колеса при его повороте на один номинальный угловой шаг.
По нормам полноты контакта зубьев для 6 степени точности выбран контрольный комплекс который использует такие показатели как:
- погрешность направления зуба;
- суммарная погрешность контактной линии.
По основным показателям бокового зазора между нерабочими боковыми поверхностями зубьев колес могут быть использованы:
–межосевое расстояние определяемое размерами зуба при комплексном контроле в без зазорном зацеплении с измерительным колесом;
–толщина зуба по хорде на заданном расстоянии от окружности выступов;
–длина общей нормали значение которой зависит от толщины зуба;
–размер по роликам М определяемый смещением исходного контура.
По основным показателям бокового зазора между нерабочими боковыми поверхностями зубьев колес выбран контрольный комплекс который использует такой показатель как:
W - длина общей нормали и - отклонение длины общей нормали.
Термины обозначения и определения показателей контрольных комплексов.
Колебания измерительного межосевого расстояния за оборот колеса- это разность между наибольшим и наименьшим действительными межосевыми расстояниями при двухпрофильном зацеплении измерительного колеса с контролируемым зубчатым колесом при повороте последнего на полный оборот.
Графическая интерпретация колебания измерительного межосевого расстояния за оборот колеса показана на рисунке 1.6.1.
Рисунок 1.6.1 -Диаграмма колебания измерительного межосевого расстояния:
- один угловой шаг; 2 - кривая изменения измерительного межосевого расстояния; 3 - один оборот зубчатого колеса
Радиальное биение зубчатого венца – это разность действительных предельных положений исходного контура в пределах зубчатого колеса.
Колебания измерительного межосевого расстояния на одном зубе – это разность между наибольшим и наименьшим действительными межосевыми расстояниями при двухпрофильном зацеплении измерительного колеса с контролируемым зубчатым колесом при повороте последнего на один угловой шаг.
Графическая интерпретация колебания измерительного межосевого расстояния на одном зубе показана на рисунке 1.6.1.
Отклонение шага зацепления - разность между действительным и номинальным шагами зацепления. Под действительным шагом зацепления понимают расстояние между параллельными плоскостями касательными к двум одноименным активным боковым поверхностям соседних зубьев зубчатого колеса.
Графическая интерпретация отклонения шага зацепления показана на рисунке 1.6.2.
Отклонение шага - дискретное значение кинематической погрешности зубчатого колеса при его повороте на один номинальный угловой шаг.
Графическая интерпретация отклонения шага показана на рисунке 1.6.3.
Рисунок 1.6.2 - Графическая интерпретация отклонения шага зацепления:
I – номинальный шаг зацепления; II – действительный профиль зуба;
III – номинальный профиль зуба; IV – действительный шаг зацепления.
Рисунок 1.6.3 - Графическая интерпретация отклонения шага:
–действительный угол поворота зубчатого колеса; z - число зубьев зубчатого колеса; k – число целых угловых шагов (k = 1);
r – радиус делительной окружности зубчатого колеса
Погрешность направления зуба - это расстояние между двумя ближайшими друг к другу номинальными делительными линиями зуба в торцовом сечении между которыми размещается действительная делительная линия зуба соответствующая рабочей ширине зубчатого венца или шеврона.
Графическая интерпретация погрешности направления зуба показана на рисунке 1.6.3.
Рисунок 1.6.4 - Графическая интерпретация погрешности направления зуба
Суммарная погрешность контактной линии - расстояние по нормали между двумя ближайшими друг к другу номинальными контактными линиями условно заложенными на плоскость (поверхность) зацепления между которыми размещается действительная контактная линия на активной боковой поверхности.
Графическая интерпретация суммарной погрешности контактной линии показана на рисунке 1.6.5.
Рисунок 1.6.5 - Графическая интерпретация суммарной погрешности контактной линии:
I – направление рабочей оси вращения колеса; II– номинальные контактные линии; III– действительная контактная линия; IV – границы активной поверхности зуба
Номинальная длина общей нормали W - расчётная длина общей нормали соответствующая номинальному положению исходного контура.
Отклонение длины общей нормали – разность значений действительной и номинальной длины общей нормали.
Допуски и предельные отклонения выбранных контрольных показателей.
Допуск на колебание измерительного межосевого расстояния за оборот колеса т.к. степень точности по нормам кинематической точности – 8 m =25 мм dm = 105 мм.
Допуск на радиальное биения зубчатого венца = 25 мкм т.к. степень точности по нормам кинематической точности – 8 m =25 мм dm = 105мм.
Допуск на колебание измерительного межосевого расстояния на одном зубе мкмт.к. степень точности по нормам плавности работы – 7 m =25мм dm=105 мм.
Допуск на предельные отклонения шага зацепления :
нижнее = - 17 мкм т.к. степень точности по нормам плавности работы – 8 m =4 мм dm = 104 мм.
Допуск на предельные отклонения шага :
нижнее = – 18 мкм т.к. степень точности по нормам плавности работы – 7m = 25мм dm = 105 мм.
Допуск на направление зуба = 8 мкм т.к. степень точности по нормам полноты контакта зубьев в зацеплении –6 m =25 мм длина контактной линии – до 18 мм.
Допуск на суммарную погрешность контактной линии = 18 мкм т.к. степень точности по нормам полноты контакта зубьев в зацеплении – 6 m =25 мм длина контактной линии – до 18 мм.
Наименьшее отклонение длины общей нормали (наименьшее предписанное отклонение длины общей нормали осуществляемое с целью обеспечения в передаче гарантированного бокового зазора):
– = – 85 мкм т.к. степень точности по нормам плавности – 7 вид сопряжения – D dm = 105 мм.
Допуск на длину общей нормали = 40 мкм т.к. вид сопряжения – D вид допуска – b допуск на радиальное биения зубчатого венца = 45 мкм.
Выбор универсальных средств измерений для контроля выделенных показателей.
Для контроля предельного отклонения межосевого расстояния а также для проверки колебания этого расстояния при двухпрофильном зацеплении мелкомодульных зубчатых цилиндрических колес (насадных и валковых) конических колес можно использовать прибор КДП-150 рисунок 1.6.6.
Рисунок 1.6.6 -Метрологическая схема прибора КДП-150:
- станина;2 - направляющие корпуса; 3 - маховичок крепления оправки; 4 - рукоятка; 56 - оправки; 7 - измерительная каретка; 8 - эксцентриковый валик; 9 - установочные салазки; 10 - маховичок для установки салазок; 11 - маховичок перемещения измерительной каретки
На установочных салазках (9) смонтирована на шариках измерительная каретка (7) которая несет на себе оправку (6). Измерительная каретка перемещается при помощи маховичка (1)1 в пределах 3 мм. При проверке колебания межосевого расстояния на оправку 6 измерительной каретки устанавливается измерительное эталонное колесо а на оправки или центры сменных кронштейнов установленных на направляющих станины (1) в зависимости от типа передачи - проверяемое колесо.Измерительная каретка (7) под действием пружины находящейся внутри каретки прижимает измерительное эталонное колесо к проверяемому создавая плотное зацепление.Величина колебания межосевого расстояния фиксируется индикатором с ценой деления 0001 мм. Наконечник индикатора установленного на измерительной каретке (7) упирается в планку жестко связанную с установочными салазками (9).
Для контроля радиального биения зубчатого венца можно использовать приборы типа 25003 БВ05015 БВ-5050 БВ-5060 БВ-5061.
Одиночный зуб 1 эвольвентной рейки (исходного контура) занимает определенное положение во впадине зубчатого колеса 2 (рисунок 1.6.7 показано сплошными линиями). Положение зуба рейки в следующей впадине (показано пунктиром) при наличии радиального биения зубчатого венца будет отличаться от предыдущего.
Рисунок 1.6.7 -Схема измерения:
- зуб эвольвентой рейки; 2 - зубчатое колесо
Рассмотрим прибор для контроля радиального биения зубчатого венца биениемер Б-10 рисунок 1.6.8.
На станине (1) прибора имеются взаимно перпендикулярные направляющие для измерительной (2) и установочных (4) и (7) бабок. В установочных бабках расположены центры для установки измеряемого колеса. Центр левой бабки (4) неподвижен а центр правой бабки (7) может отводиться рукояткой (8) и возвращаться в исходное положение под действием пружины скрытой в корпусе бабки. Положение бабок (4) и (7) на станине фиксируется рукоятками (3).Измерительная бабка (2) несет на себе каретку (14) с измерительным механизмом (10). Перемещение бабки (2) по станине производится вручную а ее крепление - рукояткой (15).При вращении маховика (18) каретка (14) может перемещаться относительно измерительной бабки (2) параллельно оси центров прибора. Крепится каретка (14) винтом (6).
Рисунок 1.6.8 – Общий вид биениметра Б -10:
– станина; 2 – измерительная бабка; 3 – рукоятка фиксации;4 - установочная бабка; 5 – рукоятка премещения штока;6 - винт крепления каретки; 7 – правая бабка;8 – рукояткалевойбабки; 9 – измерительный наконечник;
– измерительный механизм;11- винт фиксации наконечника; 12 – рукоятка фиксацииизмерительного механизма;13 – рукоятка фиксации угла поворота;
– каретка;15 – рукоятка крепления бабки; 16 – упор;17 – маховичок;
– маховик перемещения каретки; 19 – винт крепления индикатора; 20 –шкала.
В корпусе измерительного механизма (10) расположен подвижный шток с цанговым зажимом для закрепления измерительного наконечника (9) и с упором (16) для индикатора. Перемещение штока осуществляется поворотом рукоятки (5) на себя. Для закрепления измерительного наконечника (9) в крайнем отведенном положении рукоятки (5) поворачивается на себя до отказа и поворотом винта (11) фиксируется в таком положении. При вращении маховичка (17) измерительный механизм (10) может перемещаться в направлении движения измерительного наконечника (9). Фиксация измерительного механизма (10) относительно каретки (14) производится рукояткой (12). Для измерения радиального биения конических зубчатых колес измерительный механизм (10) имеет возможность поворачиваться на необходимый угол вокруг вертикальной оси. Установка механизма (10) ведется по шкале (20). После установки необходимого угла поворота измерительный механизм (10) крепится рукояткой (13).
Контроль шага зацепления производится на приборах типа 21802 21702 21703 БВ-5070 и др.
Рисунок 1.6.9- Схема эвольвентамера (тип БВ-5062)
Погрешность профиля выявляют на эвольвентомерах рисунок 1.6.9 сопоставляя теоретическую эвольвенту воспроизводимую прибором с реальной эвольвентой контролируемого зуба. В приборе типа БВ-5062 теоретическая эвольвента воспроизводится образцовым сектором 1 расположенным на одной оси с контролируемым колесом. В качестве линейки обката служит каретка 3 которая связана с сектором с помощью охватывающих его с двух сторон лент 2. Радиус основной окружности меняют при настройке путем изменения положения упора 4 находящегося на измерительной каретке 5. Микроскоп 6 служит для настройки прибора на требуемый радиус основной окружности.
Для контроля направления зуба цилиндрических колес применяют прибор БВ–5034 рисунок 1.6.10. Прибор имеет 2 центровые бабки между центрами которых закрепляется оправка с контролируемым колесом. Измерительная каретка несущая измерительный наконечник и отсчетное устройство с ценой деления 005 мм перемещается по направляющим параллельно оси центров. Измерительный наконечник находится в осевой горизонтальной плоскости и касается боковой поверхности зуба. Отклонение поверхности зуба вызывает смещение наконечника в плоскости касательной к цилиндру соосному колесу и фиксируется отсчетным устройством.
Рисунок 1.6.10 – Схематический вид ходомера БВ–5034:
- продольный стол; 2 – поперечная каретка; 3 – передняя бабка; 4 – зубчатое колесо; 5 – задняя бабка; 8 – микроскоп; 9 – лимб;
Для измерения длины общей нормали используют нормалемер рисунок 1.6.11.
Рисунок 1.6.11– Нормалемер
Нормалемер представляет собой трубку 7 на которой установлена разрезная втулка 6 с неподвижной измерительной губкой 4 и корпус 1 с подвижной измерительной губкой 3. Перемещения губки 3 передаются на индикаторчерез рычаг с i = 2 : 1 что обеспечивает цену деления прибора 0005 мм.
Рисунок 1.6.12– Схема измерения длины общей нормали нормалимером
Распространен шагометр с тангенциальными наконечниками. Измерительный наконечник подвешен на плоских пружинах; его перемещения фиксируются отсчетным устройством с ценой деления 0001 мм. Второй измерительный наконечник можно устанавливать в нужном положении винтом. Опорный наконечник поддерживает прибор при измерении и обеспечивает расположение линии измерения по нормали к профилям. Наконечники со стороны измерительных поверхностей армированы твердым сплавом.
Шагометр настраивают по блоку концевых мер размер которых равен номинальному значению основного шага.
Разность окружных шагов проверяют либо с помощью угломерных приборов одновременно с контролем накопленной погрешности окружного шага либо с помощью накладных шагомеров для окружного шага.
Рисунок 1.6.13 – Шагомер для контроля окружного шага.
В этом шагомере два измерительных наконечника 1 и 2 устанавливаются с помощью двух специальных упоров 3 на одинаковом расстоянии от оси. Один наконечник неподвижный а другой связан с индикатором. Прибор настраивают на нуль по произвольной паре зубьев колеса 4 а потом этот размер сравнивают с размерами на остальных парах зубьев.
В результате проделанной работы был изучен теоретический материал а также выполнены практические задания по темам:
Допуски и посадки гладких цилиндрических соединений.
Выбор измерительных средств.
Нормирование точности соединений с подшипниками качения.
Нормирование точности шпоночных соединений.
Нормирование точности зубчатого колеса.
В результате выполнения заданий научился работать со стандартами овладел методиками нормирования точности соединения различных типов.
Знание основ нормирования точности является обязательным требованием для всех специалистов работающих в любой области машиностроения и приборостроения.
Выполнение курсовой работы по дисциплине «Нормирование точности и технические измерения» способствует развитию у студентов практических навыков самостоятельной работы с нормативно-технической документацией стандартами справочной технической литературой.
Курсовая работа состоит из ряда независимых друг от друга частей каждая из которых имеет отдельный набор исходных данных. Каждая из частей посвящена вопросам нормирования точности определенного вида соединений из числа тех что находят наиболее широкое применение в современном машиностроении и приборостроении.
Выполнение данной курсовой работы было невозможно без использования справочной литературы. В тексте курсовой работы даются подробные ссылки на соответствующие таблицы из нормативных документов.
Дунаев И.Ф. Леликов О.П. Ворламова Л.П. «Допуски и посадки. Обоснование выбора.» Учебное пособие. – Мн.: Выш. шк. 1984.
Мягков В.Д. «Допуски и посадки» I и II том Справочник. –М.: Выш. шк. 1983.
Соломахо В.Л. и другие «Справочник конструктора - приборостроителя.» -Мн.:Выш. шк. 1988.
Корвацкий А.М. и другие «Взаимозаменяемость стандартизация и технические измерения. Методическое пособие к курсовой работе для студентов заочных факультетов.» 1992.
Технические нормативные правовые акты
ГОСТ 2.104-58 Единая система конструкторской документации. Основные надписи
ГОСТ 2 109-73 Единая система конструкторской документации. Основные требования к чертежам
ГОСТ 2.308-79 Единая система конструкторской документации. Указание на чертежах допусков формы и расположения поверхностей ГОСТ 2.309-73 «Единая система конструкторской документации. Обозначения шероховатости поверхностей»
ГОСТ 2.402-68 .Единая система конструкторской документации. Условные изображения зубчатых колес реек червяков звездочек цепных передач
ГОСТ 2.403-75 Единая система конструкторской документации. Правила выполнения чертежей цилиндрических зубчатых колес.
ГОСТ 2.409-74 Единая система конструкторской документации Правила выполнения чертежей зубчатых (шлицевых) соединений
ГОСТ 8.010-99 Государственная система обеспечения единства измерений. Методики выполнения измерений. Основные положения
ГОСТ 8.050-73 Государственная система обеспечения единства измерений. Нормальные условия выполнения линейных и угловых измерений
ГОСТ S 051-81 Государственная система обеспечения единства измерений. Погрешности допускаемые при измерении линейных размеров до 500 мм
ГОСТ 520-2002 Подшипники качения Общие технические условия
ГОСТ 1643-81 Основные нормы взаимозаменяемости. Передачи зубчатые цилиндрические. Допуски
ГОСТ 3189-89 Подшипники шариковые и роликовые. Система условных обозначений
ГОСТ 3325-85 Подшипники качения. Поля допусков и технические требования к посадочным поверхностям валов и корпусов Посадки
ГОСТ 20226-82 Подшипники качения. Заплечики для установки подшипников качения. Размеры
ГОСТ 23360-78 Основные нормы взаимозаменяемости. Соединения шпоночные с призматическими шпонками Размеры шпонок и сечений пазов. Допуски и посадки
ГОСТ 24642-81 Основные нормы взаимозаменяемости. Допуски формы и расположения поверхностей. Основные термины и определения ГОСТ 24643-81 Основные нормы взаимозаменяемости. Допуски формы и расположения поверхностей. Числовые значения
ГОСТ 24810-81 Подшипники качения. Зазоры
ГОСТ 308931-2002 (ИСО 2768-1-89) Основные нормы взаимозаменяемости. Общие допуски. Предельные склонения линейных и угловых размеров с неуказанными допусками.
Зубчатое колесо.dwg

остальных поверхностей 269 312 НВ.
*. Размеры обеспеч. инстр.
Точность зубчатого колеса в соответствии с ГОСТ 1643-81.
Общие допуски по ГОСТ 30893.1-2002.
Неуказанные радиусы 2 4 мм.
Коэффициент смещения
Нормальный исходный
Длина общей нормали
БНТУ.10303117.012.002
Узел редуктора.dwg

Подшипник 405 ГОСТ 8338-75
Шпонка 15х7х32 ГОСТ 23360-78
Размеры для справок.
Остальные ТТ по СТБ 1014-95.
Смазка - масло индустриальное И-30А ГОСТ 20799-78.
БНТУ.10303117.012.000ВО
Сталь 40Х ГОСТ 4543-71
Сталь 08кп ГОСТ 1050-88
Сталь 45 ГОСТ 1050-88
Рекомендуемые чертежи
Свободное скачивание на сегодня
Другие проекты
- 29.08.2014