По дисциплине Нормирование точности и технические измерения




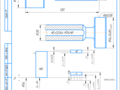
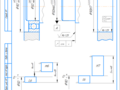
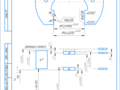
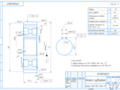
- Добавлен: 24.01.2023
- Размер: 3 MB
- Закачек: 0
Описание
Состав проекта
![]() |
![]() |
![]() |
![]() |
![]() |
![]() ![]() ![]() ![]() |
![]() ![]() ![]() |
![]() |
![]() ![]() ![]() ![]() |
![]() |
![]() ![]() ![]() ![]() |
![]() ![]() ![]() ![]() |
![]() ![]() ![]() ![]() |
![]() |
![]() ![]() ![]() |
![]() ![]() ![]() ![]() |
![]() |
![]() |
Дополнительная информация
3(final-A4).cdw

Записка(final).doc
С помощью стандартов Государственная Система стандартизации способствует:
- улучшению качества работы качества продукции и обеспечению его оптимального уровня;
- обеспечению условий для развития специализации в области проектирования и производства продукции снижению ее трудоемкости металлоемкости и улучшению других показателей;
- обеспечению условия для широкого развития экспорта товаров высокого качества отвечающих требованиям мирового рынка;
- обеспечению увязки требований к продукции с потребностями обороны страны;
- рациональному использованию производственных фондов и экономии материальных и трудовых ресурсов;
- развитию международного экономического и технического сотрудничества.
Для получения поставленных целей стандарты постоянно обновляют на основе достижений науки техники и производства с учетом комплексности и системности решений задач стандартизации.
Допуски цилиндрических зубчатых колес
Число зубьев большего колесаZ1 = 18
Число зубьев малого колесаZ2 = 36
Окружная скоростьV = 19 мс
Ширина зубчатого венца В = 45 мм.
Диаметр посадочного отверстия зубчатого колеса d =54 мм.
2 Расчет геометрических параметров зубчатой передачи
- делительный диаметр малого колеса
- делительный диаметр большего колеса
- межосевое расстояние
3 Назначение степеней точности зубчатой передачи
Система допусков цилиндрических зубчатых передач (ГОСТ 1643-81) устанавливает 12 степеней точности зубчатых колес.
Степень точности проектируемого колеса устанавливается в зависимости от окружной скорости колеса. Согласно рекомендациям [1] степень точности зубчатой передачи по норме плавности назначаем 9 в зависимости от окружной скорости V=19 мс. По рекомендациям ГОСТ 1643-81 применив комбинирование норм точности назначаем по кинематической норме точности степень такую же как по плавности - 9 а полноте контакта на одну точнее т.е. 8.
4 Выбор вида сопряжения по боковому зазору
Вид сопряжения передачи выбирается по величине гарантированного бокового зазора.
Боковой зазор это зазор между нерабочими профилями зубьев который необходим для размещения смазки компенсации погрешностей изготовления при сборке и для компенсации изменения размеров от температурных деформаций.
Величину бокового зазора необходимого для размещения слоя смазки для тихоходной передачи (Vокр. до 3 мс) ориентировочно можно определить по зависимости
jn.min.расч = 001 × m
jn.min.расч = 001 45 = 0045мм =45мкм.
По рассчитанной величине jn min расч равной 45 мкм в зависимости от межосевого расстояния aw=1215 мм из таблицы 13 (ГОСТ 1643-81) выбираем вид сопряжения причем выполняется условие
jn.min.табл. ³ jn.min.расч .
Данному условию соответствует вид сопряжения С для которого
jn.min.табл. = 87 мкм > jn.min.расч = 45мкм.
Таким образом точность зубчатой передачи будет 9 - 9 - 8 С ГОСТ 1643-81.
5 Назначение комплексов показателей для контроля зубчатого колеса
Выбор показателей для контроля зубчатого колеса (z2 =36) проводится согласно рекомендациям ГОСТ 1643-81 по таблицам 2 3 5 а по таблицам 6 8 12 22 этого же ГОСТ назначаем на них допуски.
Средства для контроля показателей выбираем по [6]результаты выбора показателей допусков на них и средств и средств контроля сводим в таблицу 1.
Таблица 1 - Показатели и приборы для контроля зубчатого колеса
Наименование и условное обозначение контролируемого показателя
Условное обозначение и численное значение допуска мкм
-колебание измерительного межосевого расстояния за 1 оборот колеса
-колебание измерительного межосевого расстояния на 1 зуб
-погрешность направления зуба
Еаs Еаi - предельные отклонения измерительного межосевого расстояния
Тн – допуск на смещение исходного контура
Рассчитываем длину общей нормали по формуле
где W1 – длина общей нормали для зубчатого колеса при m =1 мм [3].
Наименьшее отклонение длины общей нормали определяем по таблице 16 ГОСТ 1643-81 = -100мкм.
Наибольшее отклонение длины общей нормали определяем по выражению
= - = -100–140= -240 мкм
где - допуск на длину общей нормали определяемый по таблице 19 ГОСТ 1643-81 в зависимости от величины радиального биения зубчатого венца (таблица 6 ГОСТ 1643-81) =140 мкм.
Допуски на размеры и расположения базовых поверхностей колеса назначаем с учетом выбранных показателей контроля зубчатого венца. Требования к точности заготовки определяются допусками на диаметры выступов da радиальным и торцовым биениями.
Так как наружная поверхность зубчатого колеса не используется в качестве базовой поверхности (измерительной и установочной) допуск на наружный диаметр Тda назначаем как для несопрягаемых размеров – h14 а радиальное биение наружной поверхности определяем по формуле [3]:
Fda = 01 45 =045 мм.
Допуск на торцовое биение базового торца определим по формуле [3]:
где Fb - допуск на погрешность направления зуба по степени нормы полноты контакта мм выбираем по таблице 11 ГОСТ 1643-81в зависимости от ширины зубчатого венца Fb = 0025 мм;
В – ширина зубчатого венца мм;
d – диаметр на котором определяется биение.
где z1 – число зубьев большего колеса.
d = (36– 24) 45 =1512 мм.
Шероховатость боковой поверхности зубьев при 9-ой степени точности зубчатого колеса по плавности работы составляет Ra63 мкм. Точность размера посадочного диаметра колеса выбирается в зависимости от степени точности колеса – Н8.
Расчет и выбор переходной посадки неподвижного соединения с дополнительным креплением
Точность зубчатого колеса 9 - 9 - 8 - С ГОСТ 1643-81
Номинальный диаметр соединения d =54 мм
Допуск на радиальное биение зубчатого венца Fr =100 мкм
Соединение зубчатого колеса с валом редуктора с дополнительным креплением при помощи шпонки является разъемным неподвижным соединением образованным переходной посадкой. Расчет разъемных соединений образованных переходными посадками производится исходя из условий:
- обеспечение высокой точности центрирования зубчатого колеса на валу;
- обеспечение легкой сборки и разборки соединения.
Сочетание этих двух условий возможно лишь при небольших натягах или зазорах в соединении.
Хорошее центрирование зубчатого колеса на валу необходимо для обеспечения высокой кинематической точности передачи ограничения динамических нагрузок. Для обеспечения неподвижности зубчатых колес с валом применяются шпонки. Наибольшее применение получили призматические шпонки отличающиеся простотой изготовления.
Параметры шпонки пазов на валу и на зубчатом колесе выбираем исходя из диаметра посадочной поверхности колеса (d =54 мм) по ГОСТ 23360-78:
- ширина шпонки (паза) b =16 мм;
- глубина паза на валу t1 =6 +02 мм;
- глубина паза на колесе t2 = 43+02 мм;
Известно что наличие зазора в сопряжении за счет односторонних смещений вала в отверстии вызывает появление радиального биения зубчатого венца колеса определяющего кинематическую точность.
В этом случае наибольший допустимый зазор обеспечивающий первое условие может быть определен по формуле:
где Kt коэффициент запаса точности (Kt = 2 5) принимаем Kt = 2.
Fr допуск на радиальное биение зубчатого венца (Fr =100 мкм).
Smax ≤100 2 =50 мкм.
Возможный наибольший натяг в соединении рассчитываем по формуле
Nmax = Smax (3 - z) (3 + z)
где z аргумент функции Лапласа который определяется по ее значению
где P вероятность получения зазора в соединении. Задаемся P = 03 для 9 степени точности колеса тогда
Фо(zo) = 03 – 05= - 0.2.
По таблице приложения 11 [1] находим значение z = - 053
Nmax =50 (3 + 053) (3 - 053) =71 мкм.
По номинальному диаметру соединения d =54 мм и Nmax p=71 мкм
Smax p =50 мкм по ГОСТ 25347-82 выбираем переходную посадку H8k7 параметры выбранной посадки не превышают расчетной т. е
Smax таб = 44 Smax p =50 мкм
Nmax таб =32 Nmax p =71 мкм.
Причем выполняются требования по соответствующей степени точности зубчатого колеса точности отверстия (таблица 2.2 [3]).
Шпонка является стандартным изделием и изготавливается независимо от посадок по которым она будет устанавливаться в паз вала и в паз колеса. Работоспособность шпоночного соединения определяется точностью посадки по ширине шпонки (паза) . ГОСТ 23360-78 предусматривает посадки образующие нормальное плотное и свободное соединение шпонок с пазами вала и колеса (втулки) в системе основного вала.
Принимаем свободный тип соединения. Для свободного типа соединения установлены поля допусков ширины для паза на валу H9 и для паза во втулке D10.
Предельные отклонения указанных полей допусков соответствуют ГОСТ 25347-82 шпонка как основной вал имеет поле допуска .
В этом случае посадка в соединении со шпоночным пазом вала будет 16 и с пазом втулки 16.
В серийном и массовом производстве для контроля точности размеров используют калибры. Калибры для контроля отверстий называются пробками для контроля валов - скобами. Калибры изготовляются комплектом из проходного (ПР) и непроходного (НЕ) калибра. При контроле детали калибрами она (деталь) признается годной если проходной калибр проходит а непроходной не проходит через проверяемую поверхность.
Если проходной калибр не проходит то в этом случае имеет место исправимый брак. Если непроходной калибр проходит то в этом случае имеет место неисправимый брак.
1 Расчет калибров пробок
Контролируемое отверстие 54Н8(+00 46 )
При расчете предельных и исполнительных размеров пробок за номинальный размер для проходного калибра принимается минимальный предельный размер контролируемого отверстия а для непроходного калибра - максимальный предельный размер контролируемого отверстия.
Максимальный предельный диаметр контролируемого отверстия
Dmax = D + ES = 54+ 0046= 54046 мм.
Минимальный предельный диаметр контролируемого отверстия
Dmin = D + EI =54 + 0 = 54 мм.
Допуски на изготовление калибров нормируются по ГОСТ 24853-81.
Для определения предельных и исполнительных размеров пробок из таблицы указанного стандарта выписываем численные значения параметров Н Z y
где Н - допуск на изготовление калибра
Z - координата середины поля допуска проходной пробки
y - координата определяющая границу износа проходной пробки
Н =5 мкм = 0005 мм; y =5 мкм = 0005 мм; Z = 7мкм = 0007мм;
Определяем предельные и исполнительные размеры пробок ПР и НЕ по формулам из ГОСТ 24853-81 .
DПР изн = D min – y = 54- 0005 =53995 мм.
Исполнительный размер проходной пробки
DПР исп = DПР max -Н =540095 -0005 мм .
Исполнительный размер непроходной пробки
DНЕ исп = DНЕ max -Н =540485-0005 мм .
2 Расчет калибров скоб
Контролируемый вал 54k7.
При расчете предельных и исполнительных размеров скоб за номинальный размер для проходной стороны калибра принимается максимальный предельный размер контролируемого вала а для непроходного калибра - минимальный предельный размер контролируемого вала.
Максимальный предельный диаметр вала
dmax = d + es = 54 + 0032 =54032 мм.
Минимальный предельный диаметр вала
dmin = d + ei =54+ 0002 =54002 мм.
Для определения предельных и исполнительных размеров скобы из таблицы ГОСТ 24853-81 выписываем допуски: Н1 z1 y1Hр;
Н1 =5 мкм = 0005 мм; z1 =4 мкм =0004 мм;
y1 = 3 мкм = 0003 мм; Нр =2 мкм = 0002 мм;
где Нр - допуск на изготовление контрольных калибров.
Определяем предельные размеров скобы ПР и НЕ:
dПР изн = dmax + y1 =54032 + 0003 =54035 мм.
Исполнительные размеры скобы
dПР исп = dПРmin = 540255+0005 мм
dНЕ исп = dНЕmin = 539995 +0005 мм.
Шероховатость рабочих поверхностей калибров пробок и скоб в соответствии с квалитетом точности контролируемых размеров 7-ой и 8-ой составляет Rа 008 мкм.
Выбор универсальных измерительных средств
В единичном и мелкосерийном производстве для контроля точности размеров используют универсальные измерительные средства.
контролируемое отверстия - 54H8(+0046) .
контролируемый вал - 54.
Для обеспечения точности измерения при выборе измерительных средств для проверяемых деталей необходимо чтобы допускаемая погрешность измерения ±d которая регламентируется ГОСТ 8.04-81 и зависит от допуска контролируемого размера была больше или равна предельной погрешности измерительного средства ±D которая указывается в технической характеристике на него.
Результаты выбора измерительных средств для проверяемых деталей сводим в таблицу 2.
Таблица 2 - Выбранные средства измерения (В микрометрах)
Допускаемая погрешность измерения
Наименование средства измерения модель ГОСТ
Цена деления отсчетного устройства
Предельная погрешность
измерительного средства
С измерительными головками
Расчет и выбор посадок подшипников качения
радиальная нагрузка R =725Н;
класс точности подшипника –6;
вал вращается вал сплошной корпус толстостенный;
нагрузка умеренная перегрузки не превышают 150%.
Исходя из диаметра посадочного отверстия зубчатого колеса (d =54 мм) принимаем подшипник легкой серии №210. Из таблицы стандарта по номеру подшипника выписываем его параметры D =90 мм d =50 мм В =20 мм r =2 мм.
1 Расчет и выбор посадок подшипников качения на вал и корпус
Посадка внутреннего кольца с валом всегда осуществляется в системе основного отверстия а наружного кольца в корпус в системе основного вала.
Выбор посадок для подшипников качения зависит от характера нагружения колец. В подшипниковых узлах редукторов кольца испытывают циркуляционное и местное нагружение. Внутреннее кольцо подшипника является циркуляционно нагруженным при котором результирующая радиальная нагрузка воспринимается последовательно всей окружностью его дорожки качения и передает ее всей посадочной поверхности вала.
Наружное кольцо подшипника испытывает местное нагружение при котором постоянная по направлению результирующая радиальная нагрузка воспринимается лишь ограниченным участком окружности дорожки качения и передает ее соответствующему ограниченному участку посадочной поверхности корпуса.
Так как в изделии вращается вал внутреннее кольцо подшипника является циркуляционно нагруженным наружное кольцо соединятся с неподвижным корпусом испытывает местное нагружение следовательно внутреннее кольцо должно соединяться с валом по посадке с натягом наружное с отверстием в корпусе с небольшим зазором.
Посадку внутреннего кольца подшипника на вал определяем по минимальному расчетному натягу между внутренним кольцом и посадочной поверхностью вала который рассчитывается по формуле
где коэффициент (для подшипников легкой серии N =28);
радиальная нагрузка;
r - радиус скругления фаски кольца подшипника.
Квалитет точности для отверстия и вала устанавливается в зависимости от класса точности подшипника при 0 и 6-ом классе точности вал обрабатывается по 6 а отверстие по 7-му квалитету точности. По ГОСТ 3325-85 выбираем поле допуска для посадочной поверхности вала соблюдая условие:
где табличное значение минимального натяга.
Посадка внутреннего кольца на вал - 50.
Предельные отклонения для колец подшипника выбираем по ГОСТ 520-89.
Прочность внутреннего кольца проверяем по допустимому натягу
где [] - допускаемое напряжение материала кольца при растяжении (для подшипниковой стали = 400 МПа = 400 106 Па);
d - номинальный диаметр кольца подшипника (d=50 мм).
Прочность кольца гарантируется так как
Наружное кольцо подшипника испытывает местное нагружение. По таблице 3.9[2] выбираем для посадочной поверхности отверстия корпуса поле допуска H .
Посадка по наружному кольцу – 90.
3 Определение требований к посадочным поверхностям вала и отверстия в корпусе
Требование к посадочным поверхностям вала и отверстия определяется по ГОСТ 3325-85.
Шероховатость поверхности выбирается по таблице 3. Для вала ; отверстия в корпусе торца вала
Допуски круглости и профиля продольного сечения по таблице 4. Для вала для отверстия
Допуск торцового биения опорного торца вала по таблице 5
Расчет размерной цепи методом регулирования
Для обеспечения зазора между подшипником и крышкой устанавливаемых на промежуточный вал-шестерню в пределах S = 0 074 мм который является замыкающим (исходным) звеном в сборочном узле предусмотрен компенсатор. Роль такого звена (детали) обычно выполняют втулки кольца планки плиты прокладки и т.п. специально предусмотренные в конструкции машины детали.
Задачу целесообразно решать методом регулирования. Точность замыкающего звена (ВΔ) достигается изменением компенсирующего звена которым является кольцо(втулка прокладка) – неподвижный компенсатор.
Собираемые детали в этом случае изготавливаются с расширенными экономически целесообразными производственными допусками.
По сборочному чертежу вала выявляем все звенья размерной цепи В (В1 В6) участвующие в решении поставленной задачи. Вычерчиваем отдельно размерную цепь (рисунок 1).
Рисунок 1 - Схема размерной цепи В
Расчет ведем согласно рекомендациям [1].
Записываем параметры замыкающего звена в удобном для дальнейшего расчета виде:
предельные отклонения ESВΔ = + 074 мм; EIВΔ = + 0мм
допуск замыкающего звена
ТВD = + 074 – 0 = 074 мм
координата середины поля допуска исходного звена
Выявляем увеличивающие и уменьшающие звенья:
увеличивающие - В8 В9
уменьшающие - В1 В2 В3 В4 В5 В6 В7 В10
Конструктивно по сборочному чертежу определяем номинальные значения составляющих звеньев:
В1 =20мм; В2 =6 мм; В3 = 45 мм; В4 = 6 мм; В5 =20мм; В6 = 2 мм;
В7 =5 мм; В9 = 2 мм; В10 = 10мм; В8 =112 мм.
Размеры звеньев В1 и В5 (ширина кольца подшипника B) выбираем по номеру подшипника № 210.
Проверяем правильность определения номинальных значений составляющих звеньев:
ВΔ = В8 + В9– (В1+ В2 + В3 + В4 + В5 + В6 + В7 + B10);
ВΔ = 112+2- (20 + 6 + 45 + 6 + 20 + 2 + 5+10) = 0
По ГОСТ 25347–82 устанавливаем экономически целесообразные допуски и предельные отклонения составляющих звеньев за исключением компенсирующего В9 и подшипников В1 В5:
ТВ2 = 030 мм (14 квалитет); ТВ6 = 010 мм (12 квалитет); ТВ3 = 025 мм (12 квалитет); ТВ7 = 030 мм (14 квалитет); ТВ4 = 030 мм (14 квалитет). ТВ8 = 0350 мм (12 квалитет);
ТВ10 = 036 мм (14 квалитет);
Для звеньев В1 В5 допуски выбираем из таблицы стандарта для подшипников ГОСТ 520-71 на ширину колец подшипника в зависимости от внутреннего диаметра и класса точности ТВ1 = ТВ5 = 012 мм.
Задаем расположение допусков составляющих звеньев и записываем их предельные отклонения кроме компенсирующего звена. Для звеньев определяющих размеры охватывающих поверхностей ESВ EIВ
В1 = 20-012 мм; В2 = 6-03 мм; В3 = 45-025 мм;
В4 = 6-03 мм; В5 = 20-012 мм; В6 = 2-01 мм;
В7 = 5 ± 0.15мм; В8 = 112-035 мм; В10 = 10 ± 0.18мм мм;
Определяем координаты середин полей допусков составляющих звеньев кроме компенсирующего звена:
ЕсВ1 = - 006 мм; ЕсВ2 = - 015мм; ЕсВ3 = - 0125 мм;
ЕсВ4 = - 0150 мм; ЕсВ5 = - 006 мм; ЕсВ6 = - 005 мм;
ЕсВ7 = - 015 мм; ЕсВ8 = - 0175 мм; ЕсВ10 = - 018 мм
Определяем производственный допуск замыкающего звена путем суммирования производственных допусков составляющих звеньев кроме замыкающего и компенсирующего звена
где m – общее число звеньев в цепи включая замыкающее звено m = 11
2 + 03 + 025 + 03 + 012 + 01 + 03 + 035 +036 = 22 мм
Определяем величину компенсации:
где Тмк – допуск на изготовление компенсатора (звено В9) принимаем по 10-му квалитету точности 004 мм.
Тк = 22 - 074 + 004 =15 мм.
Определяем координату середины производственного допуска замыкающего звена:
ЕсВΔ = +(- 0175) - (-006-015-0125 -015-006- 005- 015- 018)= + 075 мм.
Определяем величину компенсации координаты седины поля производственного допуска замыкающего звена:
Знак «плюс» ставится в том случае если компенсатор является увеличивающим звеном а знак «минус» - уменьшающим звеном.
Определяем предельные значения величины необходимой компенсации
Так как EIk 0 то изменяем координату середины поля допуска одного из составляющих звеньев (ЕсВ8) на величину ЕсВ8 = ЕсВ8 - EIk (для увеличивающих звеньев);
ЕсВ8 = - 0175 - (- 037) = + 0195 мм.
Определяем новые предельные отклонения для измененного звена
Устанавливаем толщину одной прокладки
Определяем число прокладок
Принимаем 2 прокладки.
Курсовое проектирование по курсу «Нормирование точности и технические измерения». Методические указания. В 2-х ч. - Могилев: БРУ 2007.
Лукашенко В.А. Расчет точности механизмов: учеб. пособие по курсу «Взаимозаменяемость стандартизация и технические измерения» для студентов машиностроительных специальностей В.А. Лукашенко Р.Н. Шадуро. - Могилев: МГТУ 1992.
Мягков В.Д. Допуски и посадки: справочник в 2 т. Под ред. В.Д.Мягкова. - 6-е изд. перераб. и доп. - Л.: Машиностроение 1982. – Т. 1 - 543 с.
Мягков В.Д. Допуски и посадки: справочник в 2 т.. Под ред. В.Д.Мягкова. - 6-е изд. перераб. и доп. - Л.: Машиностроение 1983. - Т.2. - 448 с.
Якушев А.И. Взаимозаменяемость стандартизация и технические измерения А.И.Якушев Л.Н.Воронцов Н.М.Федотов. - 6-е изд. перераб. и доп. - М.: Машиностроение 1987. - 352 с.
Марков А.Л. Измерение зубчатых колес А.Л. Марков. – Л.: Машиностроение 1977. – 275 с.
6(final-A3).cdw

5(final-A4).cdw

1(final-A3).cdw

Сталь 40Х ГОСТ 4543-71
Коэффициент стещения
Остальные технические требования по СТБ 1014-95
4(final-A4).cdw

Содержание, титульный.doc
Кафедра «Технология машиностроения»
«Нормирование точности и технические измерения»
Допуски цилиндрических зубчатых колес ..
1 Исходные данные .
2 Расчет геометрических параметров зубчатой передачи
3 Назначение степеней точности зубчатой передачи .
4 Выбор вида сопряжения по боковому зазору
5 Назначение комплексов показателей для контроля зубчатого колеса
Расчет и выбор переходной посадки неподвижного соединения с дополнительным креплением
1 Расчет калибров пробок
2 Расчет калибров скоб .
Выбор универсальных измерительных средств ..
Расчет и выбор посадок подшипников качения
1 Расчет и выбор посадок подшипников качения на вал и в корпус .
Расчет размерной цепи методом регулировани .
2(final-A3).cdw

Рекомендуемые чертежи
- 20.12.2023
Свободное скачивание на сегодня
Другие проекты
- 22.08.2014