Проектирование режущих инструментов



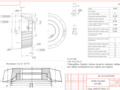
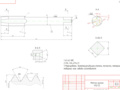
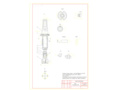
- Добавлен: 24.01.2023
- Размер: 406 KB
- Закачек: 0
Описание
Состав проекта
![]() |
![]() ![]() ![]() |
![]() ![]() ![]() |
![]() ![]() ![]() ![]() |
![]() ![]() ![]() |
![]() ![]() ![]() ![]() |
![]() ![]() ![]() ![]() |
![]() ![]() ![]() |
![]() ![]() ![]() |
Дополнительная информация
Спецификация1.doc
Винт M6- 6q x 8.56.05
Винт M10- 6q x 8.68.05
Гайка Tr28 x 2-7H.055
Проверка долбяка.doc
Станочный угол зацепления долбяка и нарезаемого колеса
Межосевое расстояние долбяка и нарезаемого колеса
Диаметр окружности впадин зубьев колеса после нарезания долбяком
Должно быть колеса внешнего зацепления. Условие выполняется.
Торцовый угол зацепления нарезаемого и сопряжённого с ним колёс в зубчатой передачи.
Радиус кривизны профиля зубьев колеса в точке начала активной части.
Радиус кривизны профиля зубьев колеса после нарезания долбяком в точке начала обработки.
Должно быть . Условие выполняется
Метчик.dwg

ДВУ 433.00.00.000 Д1
Схема функциональная
Графики напряжений в контрольных точках
Сталь У11 ГОСТ1435-90
±IT142 3 Маркировать: диаметр
товарный знак завода-изготовителя
Моя ЗАПИСКА.doc
Производительность и эффективность работы металлообрабатывающего оборудования качество и точность получаемых деталей машин во многом зависят от того как функционируют системы связанные с режущим инструментом. Использование более совершенных методов изготовления машин требует применения прогрессивных конструкций высокопроизводительного инструмента позволяющего снижать затраты на производство. Поэтому проектирование режущего инструмента является одной из основных дисциплин при подготовке грамотного инженера в области машиностроения.
Проектирование зуборезного долбяка
Введение к зуборезному долбяку
Зуборезные долбяки применяют для нарезания зубчатых колёс с наружными и внутренними с прямыми винтовыми и с наружными шевронными зубьями. Долбяки имеют вид зубчатого колеса с изменяющимся по длине зуба смещением исходного контура (высотной коррекцией); контур торца зубчатого венца является режущей кромкой. Долбяки работают по принципу обката. Изменение высотной коррекции по длине зубьев долбяка обеспечивает образование задних углов на лезвиях зубьев. Долбяки образуют зубья колеса методом огибания; профиль их зубьев(образующий инструментальную поверхность) является сопряжённым к профилю зубьев нарезаемого колёса; для обработки колёс с эвольвентными зубьями он тоже имеет эвольвентную форму.
Долбяк дисковый. Обрабатываемый материал – Сталь 25Н; ; ; ; угол наклона зубьев – 10º; степень точности колес – 6.
Проектный расчёт долбяка выполняем в соответствии с рекомендациями [1] .
Для проектного расчёта долбяка необходимо предварительно найти дополнительные технологические параметры зубчатых колёс.
Торцовый профильный угол и модуль колеса:
Действительный угол зацепления в передаче:
где А12 – заданное межосевое расстояние в зубчатой передаче.
Диаметры основных окружностей колёс:
Наименьший радиус кривизны профиля зуба нарезаемого колеса:
Радиус кривизны в точке начала активной части профиля зуба нарезаемого колеса:
где и - наружная и основная окружности сопряжённого колеса.
Проектный расчёт долбяка.
Определение исходных данных
Число зубьев долбяка:
где - номинальный диаметр делительной окружности принимаемый по таблице 2 [1] .
Диаметр делительной окружности:
Теоретический диаметр основной окружности:
Боковой задний угол в плоскости параллельной оси долбяка:
Определение параметров долбяка в исходном сечении
Диаметр наружной окружности долбяка в исходном сечении:
где - диаметр окружности впадин зубьев колеса.
Толщина зуба на делительной окружности по нормали в исходном сечении:
Угол давления на головке зуба:
Толщина зуба на вершине в исходном сечении:
Определение исходных расстояний
Станочный угол зацепления переточенного долбяка гарантирующий отсутствие среза и неполной обработки вершины зубьев колеса неэвольвентной частью профиля зуба долбяка:
где - наименьший допустимый радиус кривизны профиля зуба долбяка принимаемый равным 5 мм при .
Станочный угол зацепления переточенного долбяка определяющий начало подреза ножки зуба колеса не производится т. к. .
Вспомогательная величина:
Максимальное отрицательное исходное расстояние предельно сточенного долбяка:
где - наибольший из углов найденных в пп. 9 и 10.
Станочный угол зацепления нового долбяка определяющий полную обработку рабочей части профиля зуба колеса:
Положительное исходное расстояние определяющее полную обработку рабочей части профиля зуба колеса:
Расчётный задний угол по верху долбяка:
Исходное расстояние лимитируемое заострением зуба долбяка:
где - задаваемая толщина зуба долбяка на вершине берётся по таблице 2[1].
Максимально возможная величина стачивания долбяка вдоль его оси:
где - наименьшая из и найденных в пп. 14 и16.
Принимаемое положительное исходное расстояние(рекомендуемое):
Определение чертёжных размеров долбяка по передней поверхности
Станочный угол зацепления нового долбяка:
Наружный диаметр нового долбяка:
Станочный угол зацепления предельно сточенного долбяка:
Уточненный (чертёжный) задний угол по верху:
Принимаемая высота долбяка:
где b берётся по таблице 2[1].
Толщина зуба на делительной окружности нормали:
Высота головки зуба долбяка по передней поверхности:
Полная высота зуба долбяка:
где h – высота зуба долбяка.
Корректированный торцовый профильный угол долбяка для уменьшения искажения профиля колеса от наличия переднего и заднего углов:
а) для “острой” (позитивной) стороны зуба
б) для “тупой” (негативной) стороны зуба
Диаметры основных окружностей долбяка при шлифовании его профиля:
а) для “острой” стороны зуба
б) для “тупой” стороны зуба
3 Проверочный расчёт долбяка
Станочный угол зацепления долбяка и нарезаемого колеса:
Межосевое расстояние долбяка и нарезаемого колеса:
Диаметр окружности впадин зубьев колеса после нарезания долбяком:
Должно быть колеса внешнего зацепления. Условие выполняется.
Торцовый угол зацепления нарезаемого и сопряжённого с ним колёс в зубчатой передачи:
Радиус кривизны профиля зубьев колеса в точке начала активной части:
Радиус кривизны профиля зубьев колеса после нарезания долбяком в точке начала обработки:
Должно быть . Условие выполняется.
4 Технические требования на изготовление долбяка
Твёрдость режущей части 61-63 HRC.
На всех поверхностях долбяка не должно быть трещин забоин выкрошенных мест заусенцев и следов коррозии.
Шероховатость передней и задней поверхности зубьев Rz=16 опорной поверхности Rа=016 посадочной поверхности Rа=016 внутренней опорной поверхности Rа=016 остальные поверхности Rа=25.
5 Термическая обработка долбяка
Зуборезный долбяк подвергают закалке и многократному отпуску.
Закалку долбяка ведут в следующем режиме: первый – подогрев в соляной ванне при температуре 800–8500С 10–15 мин во избежание образования трещин при нагреве до температуры 12300С после чего охлаждают в масле
После закалки долбяк подвергают трехкратному отпуску: в соляных ваннах его нагревают до температуры 550–5600С и выдерживают в течении 1–15 часов.
Проектирование метчика
Метчики служат для изготовления резьбы в отверстиях. Метчик как инструмент получатся из винта путём прорезания в нём стружечных канавок образования заборного конуса и затылования зубьев для создания положительного заднего угла. Канавки образуют переднюю поверхность режущие кромки и пространство для размещения и удаления стружки. Исходный винт должен быть изготовлен из инструментальной стали и после указанных операций пройти соответствующую термическую обработку.
Метчик. Обрабатываемый материал – М1; резьба – М12; разновидность метчика – ручной; длина отверстия – 30мм отверстие - сквозное.
Для изготовления ручного метчика по рекомендации стр.221[2] выбираем материал режущей части: углеродистая инструментальная сталь У11.
Число зубьев метчика по табл.7.2 [2] в зависимости от диаметра принимаем равным 3.
Для ручного метчика длина заборной части находится по следующей формуле из [3](т.к. отверстие сквозное):
Для ручного метчика длина калибрующей части находится по следующей формуле из [3]:
где d – диаметр метчика.
Длина рабочей части находится как сумма заборной и калибрующей частей:
Калибрующая часть не является строго цилиндрической. Для снижения сил трения и уменьшения величины разбивки отверстия калибрующая часть имеет небольшую обратную конусность т.е. по направлению к хвостовику наружный средний и внутренний диаметры несколько уменьшаются. По рекомендациям табл.7.7 стр.225 [2] назначаем обратную конусность 008 мм на 100 мм длины.
Для распределения работы резания на несколько режущих зубьев режущая часть выполняется в виде усечённого конуса с наклоном его образующей к оси метчика под углом j. Находим tgj по следующей формуле из [4]:
Находим толщину среза снимаемого одним режущим элементом метчика по следующей формуле из [3]:
Передний угол g назначаем в зависимости от обрабатываемого материала по табл.7.9 [2]: принимаем g=10°. Передний угол на режущей и калибрующей частях принимают одинаковым.
Задний угол a назначаем в зависимости от вида отверстия (сквозное) по табл.7.10 [2]: принимаем a=4°.
На длине режущей части метчик затачивают по задней поверхности с углом конуса j. Форму кривой затылования метчика выбирают в зависимости от типа и размеров метчика условий работы. Наиболее распространённой формой кривой затылования является архимедова спираль. Величину затылования находим по следующей формуле из [4]:
В любой другой точке на конусе режущей части задний угол определяют по формуле из[4]:
где di – диаметр окружности соответствующего сечения конуса.
Допускаемые отклонения элементов профиля резьбы метчика выбираем согласно рекомендаций [5].
Предельные отклонения квадрата хвостовика выбираем в соответствии с рекомендациями [2].
3 Технические требования на изготовление метчика
Маркировать: диаметр резьба шаг степень точности материал товарный знак завода изготовителя.
Проектирование зенкера
Зенкеры – осевой режущий инструмент предназначенный для повышения точности формы отверстия полученных после сверления отливки ковки штамповки а также для обработки торцовых поверхностей на выступах корпусных деталей (бобышек приливах т.п.) и др.
В целях экономии инструментальных материалов зенкеры больших диаметров делают насадными цельными и насадными сборными.
Зенкер. Обрабатываемый материал – Сталь20. Диаметр отверстия – 45Н11. Длина отверстия – 50 мм. Вид отверстия – глухое. Вид зенкера – насадной. Хвостовик – цилиндрический.
2 Проектный расчет зенкера
Схема расчета полей допусков и диаметров зенкера
Выбор числа зубьев: по рекомендации стр. 118 [4] принимаем количество 4 ножа.
Выбор материала режущей части и корпуса зенкера: в зависимости от обрабатываемого материала выбираем ножи для зенкера из быстрорежущей стали. По ГОСТу 16858-71 выбираем нож 0-22-8. Для корпуса зенкера принимаем Сталь 40Х.
Для крепления ножей на корпусе делают косые пазы наклоненные к оси под углом =10(по рекомендации стр.120 [4]). Ножи имеют клиновидную форму с углом клина 5 их крепят в корпусе при помощи клина.
Определение геометрических и конструктивных параметров режущей части .
Определение углов заточки:
по рекомендации стр. 45 [3] главный задний угол . Главный угол в плане Передний угол .
По рекомендации стр. 45 [3] находим ширину цилиндрической ленточки по следующей формуле:
где D – диаметр зенкера.
Все виды насадных зенкеров имеют обратную конусность 004-01 мм на длине зуба. Обратную конусность по длине ножа принимаем равным 005 мм.
Расстояние от оси зенкера до дна паза под нож:
- припуск на полирование
Размеры профиля винтовых канавок:
Для крепления насадного зенкера в хвостовике инструмента выбираем для него оправку по ГОСТ 13044-85.
Цилиндрический хвостовик оправки выбираем в соответствии С ГОСТ 26540-85.
Хвостовик инструмента конусностью 7:24 выбираем по ГОСТ 25827-83.
3 Технические требования на изготовление зенкера
Материал корпуса зенкера – сталь 40Х. Твёрдость 61-63 HRC.
Ножи из быстрорежущей стали по ГОСТ 16858-71.
Маркировать: диаметр номер зенкера по точности материал режущей части товарный знак завода изготовителя.
4 Расчет инструментального блока на точность позиционирования и податливость
Согласно схеме сборки можно выделить следующие составляющие погрешности:
Биение конического отверстия шпинделя станка:
Допускаемый перекос:
Биение базового агрегата от перехода в соединении конусности 7:24
Биение оправки от зазора в цилиндрическом соединении:
Биение посадочного отверстия базисного агрегата относительно конуса
Биение оправки от перекоса в цилиндрическом соединении:
Биение цилиндрической поверхности:
Биение конической поверхности конусности 1:30 относительно наружной цилиндрической поверхности:
Величина первичного отклонения вершины инструмента от номинального положения
где - передаточное отношение
- коэффициент относительного рассеивания
- перенос или параллельное смещение оси;
- вылет на котором нормируется величина перекоса;
- коэффициент относительного рассеивания замыкающего звена ;
Коэффициент рассеивания :
для цилиндрических поверхностей -;
для конической поверхности 1:30 - ;
Передаточные отношения:
Допускаемое биение зенкера диаметром 50мм – 0062мм по стр.37[6]
Расчет инструментального блока на податливость:
Согласно схеме сборки перемещения крепления оправки определим как суммарное смещение режущей кромки в точке приложения нагружающей силы (P = 1kH) с учетом контактной податливости в соединениях инструмента:
где - длинна i - го элемента вспомогательного инструмента
- осевой момент инерции сечения i - го элемента
- модуль продольной упругости ()
- податливость i - го элемента
- диаметр i - го элемента
- податливость в конусе с конусностью 7:24
- податливость в цилиндрическом соединении с боковым зажимным винтом =00016
- податливость в конусе 1:30 = 00014
Жесткость инструментального блока:
Податливость инструментального блока:
Для зенкеров-разверток диаметром до 80 мм допускается податливость 0115 =115 .
5 Термическая обработка корпуса зенкера
По рекомендации стр. 126[7] для корпуса зенкера-развертки изготовленного из стали 40Х выполнить:
При нагреве под закалку предварительно нагреть зенкера-развертку до температуры 300 – 500 ºС.
Нагрев под закалку – в расплаве солей пр.
Закалка: основная производится в закалочной среде
заменяющая закалка производится в закалочной среде
Отпуск закаленного инструмента производится в жидкой среде или воздушной среде.
Список использованной литературы
Романов В.Ф. Расчеты зуборезных инструментов – М: Машиностроение 1969 – 255 с.
Фельдштейн Е.Э. Курсовое и дипломное проектирование – Мн: Дизайн ПРО 1997 - 384 с.
Иноземцев Г.Г. Проектирование металлорежущих инструментов – М: Машиностроение 1984. – 272 с.
Сахаров Г.Н. Металлорежущие инструменты - М: Машиностроение 1989. – 328 с.
Ординарцев И.А. Справочник инструментальщика – М.: Машиностроение 1987. – 846 с.
Кирсанов Г.Н. Руководство по курсовому проектированию металлорежущих инструментов – М.: Машиностроение 1986. – 288с.
Кузнецов Ю.И. Оснастка для станков с ЧПУ. Справочник . – М: Машиностроение 1990. – 510 с.
Долбяк.dwg

ДВУ 433.00.00.000 Д1
Схема функциональная
Графики напряжений в контрольных точках
Долбяк дисковый косозубй
Число зубьев долбяка
Номинальный делительный диаметр
Фактический угол зацепления
Диаметр основной окружности
Толщина зубьев по делительной окруж- ости в исходном сечении
Высота головки зуба в исходном сечении
Высота ножки зуба в исходном сечении
Степень точности долбяка по ГОСТ9323-79
Отклонение от параллельности опорных поверхностей
Торцовое биение передней поверхности
Биение окружности вершин зубьев
Разность соседних окружных шагов
Накопленная погрешность окружного шага
Радиальное биение зубчатого венца
±IT142 3 Маркировать: диаметр
товарный знак завода-изготовителя
Сталь Р6M5ГОСТ19265-73
Исполнение 2 по АС 1127713
Зенкер.dwg

Материал корпуса зенкера - сталь40Х.Твёрдость 61-63 HRC 2 Ножи из быстрорежущей стали по ГОСТ 16858-71 3 Н14
±IT142 4 Маркировать: номинальный диаметр
номер зенкера по точности
материал режущей части
товарный знак завода-изготовителя
Содержание.doc
Введение к зуборезному долбяку
2 Проектный расчет долбяка
3 Проверочный расчёт долбяка
4 Технические требования на изготовление долбяка 1.5 Термическая обработка долбяка
Проектирование метчика
3 Технические требования на изготовление метчика
Проектирование зенкера
2 Проектный расчет зенкера
3 Технические требования на изготовление зенкера
4 Расчет инструментального блока на точность и податливость
5 Термическая обработка корпуса зенкера
Список использованной литературы