Проектирование инструментальной наладки и режущих инструментов




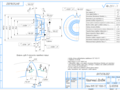
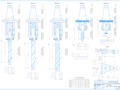
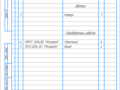
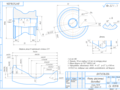
- Добавлен: 24.01.2023
- Размер: 2 MB
- Закачек: 0
Описание
Состав проекта
![]() |
![]() |
![]() ![]() ![]() |
![]() ![]() ![]() |
![]() ![]() ![]() ![]() |
![]() ![]() ![]() ![]() |
![]() ![]() ![]() ![]() |
![]() ![]() |
Дополнительная информация
наладка моя окончательная.cdw

5-2301 ОСТ 2И20-2-80
1836033 ТУ 2-035-768-80
1113040 ТУ 2-035-986-85
5-2220 ОСТ 2И62-2-75
52-0052 ГОСТ 10673-75
Инструментальная наладка
Таблица режимов резания
МОЯ ПОЛНОЯ МОЯ ЗАПИСКА.doc
БЕЛОРУССКИЙ НАЦИОНАЛЬНЫЙ ТЕХНИЧЕСКИЙ УНИВЕРСИТЕТ
Факультет Машиностроительный
Кафедра «Металлорежущие станки и инструменты»
ПОЯСНИТЕЛЬНАЯ ЗАПИСКА
по дисциплине «Инструментальные системы»
на тему «Проектирование инструментальной наладки и режущих инструментов»
Специальность: «Технологическое оборудование машиностроительного производства»
Специализация: «Металлорежущие станки»
Исполнитель: студент
группы 103516 Кухлевский С.А.
Руководитель проекта Романюк С.И.
Разработка инструментальной наладки7
1. Разработка маршрутной технологии обработки заданной детали7
2 Выбор режущих и вспомогательных инструментов9
3 Расчёт режимов резания13
4 Описание настройки инструмента вне станка14
Разработка конструкции чашечного долбяка для нарезания зубьев прямозубых цилиндрических колес18
1 Назначение типы описание конструкции и работы долбяков18
2 Расчёт геометрических и конструктивных параметров23
Разработка конструкции концевой фрезы с МНП29
1 Назначение типы описание конструкции фрез общего назначения29
2 Расчёт геометрических и конструктивных параметров концевой фрезы с МНП31
Разработка конструкции круглого фасонного резца33
1 Назначение типы описание конструкции и работы фасонного резца33
2 Расчет геометрических и конструктивных параметров37
Большинство деталей машин из различных материалов приобретает окончательную форму и размеры в результате механической обработки. Важная роль в этом принадлежит обработке материалов резанием особенно в случаях когда требуется получить детали с высокой точностью и малой шероховатостью обработанных поверхностей. Для того чтобы такая обработка была производительной экономичной и обеспечивала высокое качество изготовленных деталей необходимо знать основные закономерности процесса резания на основании которых можно сознательно управлять процессами протекающими в его зоне. Поскольку обработка может выполняться различными режущими инструментами из разнообразных инструментальных материалов и с различными геометрическими параметрами изучение закономерностей процесса резания следует проводить неотрывно от установления основных путей совершенствования режущего инструмента.
Развитие машиностроения тесно связано с совершенствованием конструкций технологических машин металлорежущих станков и в частности режущего инструмента.
От качества надёжности и работоспособности режущих инструментов применяемых в машиностроении в значительной степени зависит качество и точность детали её шероховатость производительность и эффективность процесса обработки в особенности в наше время при использовании инструмента в автоматизированном производстве в условиях гибких производственных систем.
Данный курсовой проект включает в себя разделы по разработке инструментальной наладки детали расчёты режимов резания выбора режущего инструмента проектирование режущего инструмента.
Графическая часть проекта состоит из рабочего чертежа инструментальной наладки рабочих чертежей спроектированных инструментов.
Разработка инструментальной наладки
1 Разработка маршрутной технологии обработки
Рисунок 1.1—Эскиз детали
Для обработки данной детали применяем многоцелевой станок сверлильно-фрезерно-расточной группы модели 2204ВМФ4.
Техническая характеристика
Размеры рабочей поверхности стола мм 400 х 500
Наибольшие программируемые перемещения мм:
продольное по оси Х 500
вертикальное по оси Y 500
поперечное по оси Z 500
Конус шпинделя (*-по заказу) 50АТ4 (*40АТ4)
Частота вращения шпинделя обмин 20 5000
Пределы рабочих подач по осям X Y Z мммин 01 10000
Скорость быстрых перемещений
по осям X Y Z мммин 12000
Количество инструментов в магазине 30 (*45)
Мощность главного привода кВт 10
Габариты станка мм 4280х3840х2926
Масса станка кг 6500
Переход 1. Сверлить отверстие 20 мм. Глубина сверления t=10 мм.
Переход 1. Сверлить отверстие 25 мм. Глубина сверления t=125 мм.
Переход 2. Зенкеровать отверстие 30 мм глубиной t=25 мм.
Переход 4. Фрезеровать отверстие и паз.
Переход 5. Фрезеровать паз. Глубина фрезерования t=3 мм.
2 Выбор режущих и вспомогательных инструментов
Используем литературу [1].
Переход 1. Для сверления отверстия 20 мм принимаем сверло спиральное с коническим хвостовиком 035-2301-1060 ОСТ 2И20-2-80 (с. 226 табл.74). Материал сверла – сталь Р6М5. В качестве вспомогательного инструмента принимаем державку для регулируемых втулок ТУ 2-035-763-80 191112041 (с. 332 табл. 37) и втулку регулируемую с внутренним конусом Морзе ТУ 2-035-768-80 191836032 (с. 332 табл.39)
Рисунок 1.2. Державка втулка и сверло
Переход 2. Для сверления отверстия 25 мм принимаем сверло спиральное с коническим хвостовиком 035-2301-1081 ОСТ 2И20-2-80 (с. 226 табл.74). Материал сверла – сталь Р6М5. В качестве вспомогательного инструмента принимаем державку для регулируемых втулок ТУ 2-035-763-80 191112041 (с. 332 табл. 37) и втулку регулируемую с внутренним конусом Морзе ТУ 2-035-768-80 191836033 (с. 332 табл.39)
Переход 3. Для зенкерования отверстия 25 мм в 30 мм принимаем зенкер цельный быстрорежущий с числом зубьев z=3 с коническим хвостовиком 035-2320-0026 ТУ 2-035-926-83 (с. 239 табл. 82). В качестве вспомогательного инструмента принимаем патрон цанговый с ТУ 2-035-986-85 191113040 (с. 330 табл. 33).В качестве вспомогательного инструмента принимаем державку для регулируемых втулок ТУ 2-035-763-80 191112041 (с. 332 табл. 37) и втулку регулируемую с внутренним конусом Морзе ТУ 2-035-768-80 191836033 (с. 332 табл.39)
Рисунок 1.3. Державка втулка и зенкер
Переход 4. Для фрезерования отверстия из 30 мм в 50 мм принимаем и фрезерования паза принимаем фрезу концевую цельную быстрорежущую с цилиндрическим хвостовиком 035-2220-0105 ОСТ 2И62-2-75 (с. 206 табл. 53). В качестве вспомогательного инструмента принимаем патрон цанговый с ТУ 2-035-986-85 191113040 (с. 330 табл. 33).
Рисунок 1.4. Фреза концевая и цанговый патрон
Переход 5. Для фрезерования паза принимаем фрезу Т-образную с цилиндрическим хвостовиком быстрорежущую по ГОСТ 7063-72 с 125 мм и b=6 ммчислом зубьев z=6 (с. 179 табл.75). В качестве вспомогательного инструмента принимаем патрон цанговый с ТУ 2-035-986-85 191113040 (с. 330 табл. 33).
Рисунок 1.5. Фреза Т-образная и цанговый патрон
3 Расчет режимов резания
Расчет режима выполнил по методике [4].
Расчет режимов резания при сверлении отверстия 15 мм.
Материал заготовки: сталь 40Х ГОСТ 4543-71 с НВ=269в=600 МПа. Инструмент – сверло спиральное из быстрорежущей стали Р6М5 диаметром D=20 мм.
) Глубина резания t.
t = 05 D = 05 x 20 = 10 мм.
По табл. 25 с. 277 принимаем подачу Sотабл..= 025 ммоб. т.к. l3D то коэффициент Кls = 1.
где по табл. 28 с.278 – Cv=98; q=04; y=05; m=02 а по табл. 30 с. 27 стойкость инструмента T=45 мин. тогда
Общий поправочный коэффициент на скорость резания
где по табл. 2 с. 262 Kг=1; nv=09
по табл. 6 с. 263 Kиv=1 а по табл. 31 с. 280 Klv=1
) Частота вращения шпинделя:
где по табл. 32 с. 281 См = 00345: q = 2; y = 08.
Коэффициент учитывающий фактические условия обработки
Принимаем режимы резания по таблицам [5] для перехода 2 (сверление D=25мм).
) Глубина резания t=125 мм.
) Подача на оборот S=045 ммоб.
) Скорость резания V=21 ммин.
) Мощность резания N=35 кВт.
) Минутная подача мммин.
) Машинное время мин.
4. Описание настройки инструмента вне станка
Для размерной настройки инструмента вне станка применяем оптический прибор предназначенный для станков сверлильной расточной и фрезерной групп модели БВ-2015.
Прибор состоит из литого основания 1 в котором размещены шпиндель 4 и механизм грубого 11 и точного 12 перемещений вертикальной каретки. Фиксатор 3 исключает поворот шпинделя 4 во время затяжки инструмента маховиком 2. На верхней плоскости основания крепится стойка 9 с вертикальной 10 и горизонтальной 8 каретками. Вертикальная каретка перемещается по прямоугольным направляющим посредством ходового винта с шагом 4 мм. На вертикальной каретке находятся также прямоугольные направляющие по которым перемещается горизонтальная каретка. Горизонтальная каретка предназначена для проверки и установки размера по диаметру. На горизонтальной каретке закреплено визирное устройство с микроскопом М-125 предназначенное для фиксации положения настраиваемого инструмента на заданный размер как по диаметру так и по вылету. Шкала горизонтального размера визирующего устройства также закреплена на горизонтальной каретке и снабжена индикатором 1-МИГ. Перемещение горизонтальной каретки осуществляется маховиком 14 посредством ходового винта с шагом 2 мм.
Настройка прибора осуществляется следующим образом. Маховиком грубого перемещения 11 перемещают вертикальную каретку до отметки 100 ориентируясь по шкале линейки 13. Устанавливают лимб микроскопа 6 поворачивая его против риски-указателя с отметкой “0”. Линия находящаяся на подвижной шкале микроскопа должна при этом занять положение между двумя параллельными линиями видимыми в окуляр микроскопа. Маховиком 14 перемещают горизонтальную каретку положение когда отметка с цифрой 0 шкалы 0-10 микроскопа 7 модели МОС-21 совместится с цифрой 0 шкалы линейки горизонтального отсчета. Поворачивая лимб микроскопа МОС-21 устанавливают подвижную шкалу микроскопа отметкой 0 против риски указателя. Отметки с цифрами от 0 до 10 шкалы 0-10 микроскопа МОС-21 должны находиться в промежутке между двумя дуговыми концентричными линиями видимыми в окуляр микроскопа.
Действительный размер вылета инструмента считывают со шкалы линейки 13 и лимба микроскопа МО-В. Установка прибора на заданный размер по диаметру включает два режима: установка прибора на заданный размер по диаметру; определение диаметра инструмента.
Для определения диаметра инструмента предварительно перемещают вертикальную каретку на размер вылета инструмента вставляя оправку с инструментом в шпиндель ослабляют фиксатор. Поворачивая шпиндель с помощью микроскопа М-12 добиваются наиболее резкого изображения режущей кромки инструмента. Вращая маховик перемещения горизонтальной каретки добиваются совпадения вертикальной линии нанесенной на шкале микроскопа М-12 с линией режущей кромки инструмента. Вращая лимб микроскопа подстраивают прибор. Полученный размер читают по микроскопу МОС-21. Это радиус инструмента. Для получения диаметра инструмента полученный размер удваивают.
Установка прибора на заданные координаты по вылету включает два режима: установка прибора на заданный размер по вылету; измерение действительного вылета инструмента.
Установка прибора на заданный размер по вылету осуществляется следующим образом. Маховиком грубого перемещения 11 устанавливают предварительный размер пользуясь шкалой линейки 13. Затем с помощью маховика точного перемещения 12 точно устанавливают требуемый размер пользуясь отсчетным устройством.
Рисунок 1.12. - Прибор оптический модели БВ-2015.
Измерение действительного вылета инструмента осуществляется следующим образом. Маховиком грубого перемещения 11 перемещают вертикальную каретку на размер приблизительно равный размеру вылета исследуемого инструмента. Вертикальная каретка в этом случае не мешает вставлять оправку с инструментом в шпиндель. После этого ослабляют фиксатор 3. Пользуясь микроскопом М-12 визирного устройства 5 и поворачивая шпиндель 4 добиваются такого положения инструмента когда изображение режущей кромки инструмента видимое в окуляр микроскопа будет наиболее четким а края режущей кромки будут видны наиболее резко. В этом положении наиболее резкого изображения фиксатором стопорят шпиндель. Маховиком 2 зажимают инструмент а маховиком 12 точного перемещения вертикальной каретки добиваются совмещения горизонтальной линии видимой в окуляр микроскопа М-12 с линией режущей кромки инструмента. Поворачивая лимб микроскопа М-13 из положения “0” по часовой стрелке добиваются положения когда перемещающиеся две горизонтальные и параллельные линии заключат в пространство между собой горизонтальную линию находящуюся на шкале микроскопа.
Разработка конструкции чашечного долбяка для нарезания зубьев прямозубых цилиндрических колес
1 Патенто-информационый поиск. Назначение типы описание конструкции долбяков
№2152855 Зуборезный долбяк
Изобретение относится к машиностроению проектированию изготовлению и эксплуатации зуборезных долбяков. Зуборезный долбяк имеет ступицу с посадочным отверстием и переднюю поверхность на режущих зубьях. Для повышения эффективности долбяка при эксплуатации за счет снижения трудоемкости заточки и расхода абразивных и алмазных кругов ширина передней поверхности определена по приведенной формуле в зависимости от диаметров вершин и впадин зубьев и модуля долбяка. 1 ил.
Зуборезный долбяк имеющий ступицу с посадочным отверстием и переднюю поверхность на режущих зубьях отличающийся тем что ширина передней поверхности определена по формуле:
где В - ширина передней поверхности; dao - диаметр окружности вершин зубьев; df - диаметр окружности впадин зубьев; m - модуль долбяка.
№2254966 Прямозубый долбяк
Изобретение относится к области металлообработки чистовой обработке эвольвентных зубчатых колес. Долбяк имеет выполненные коническими передние и задние поверхности вершин зубьев и задние боковые поверхности зубьев. Для исключения погрешности профиля при назначении любых по величине оптимальных передних и задних углов боковые задние поверхности зубьев определены приведенными уравнениями. 2 ил.
Прямозубый долбяк имеющий выполненные коническими передние и задние поверхности вершин зубьев и задние боковые поверхности зубьев отличающийся тем что задние боковые поверхности зубьев определены уравнениями
Назначение типы описание конструкции долбяков
Зуборезные долбяки предназначены для обработки прямозубых косозубых и шевронных колес наружного и внутреннего зацепления на специальных зубодолбежных станках. По производительности уступают червячным фрезам а по точности обработки превосходят их. Внешний долбяк представляет собой шестерню которая своей начальной окружностью обкатывается по начальной окружности нарезаемого колеса. Это согласованное взаимное вращение долбяка и заготовки – движение обкатки которое является одновременно и движением круговой подачи. Для обеспечения резания долбяк совершает возвратно-поступательные движения: длвижение вниз – главное движение со скоростью резания и движение вверх – холостой ход во время которого заготовка отводится от долбяка в радиальном направлении для устранения трения его задних поверхностей о заготовку. Перед началом рабочего хода заготовка опять подводится к долбяку. Кроме того в начальный период процесса долбяку сообщают радиальную подачу врезания на полную глубину межзубьей впадины нарезаемого колеса.
Передний и задний углы получают шлифованием передней и задней поверхностей на конус. Боковые поверхности зуба долбяка образуются путем непрерывного увеличения смещения исходного контура рейки к оси долбяка при перемещении от переднего к заднему торцу. Это создает задние боковые углы и сохраняет профиль зуба долбяка при его переточках по передней поверхности. Боковые стороны зубьев долбяка в этом случае не только эвольвентные но и винтовые левые для правой стороны зуба и правые для левой если смотреть со стороны передней поверхности. Сам долбяк таким образом можно представить как совокупность элементарных корригированных колес с бесконечно тонкой шириной обода с переменной величиной смещения исходного контура рейки. Положительное смещение ( от оси долбяка) у переднего торца непрерывно переходит в отрицательное у заднего торца. В некотором сечении перпендикулярном к оси долбяка смещение исходного контура рейки равно нулю. Это сечение называют исходным или расчетным. В нем – расчетное значение делительного диаметра долбяка а параметры зуба долбяка соответствуют параметрам впадины нарезаемого колеса. Для удобства измерения все параметры долбяка пересчитывают на переднюю плоскость кроме диаметра основной и делительной окружностей которые постоянны по всей высоте долбяка.
По типу нарезаемых колес различают прямозубые и косозубые долбяки для нарезания прямозубых и косозубых колес соответственно. По конструкции присоединительной части долбяки разделяют на дисковые чашечные втулочные и хвостовые. Наиболее экономичные из них – дисковые долбяки. Чашечные долбяки используются для нарезания колес в упор когда оправка выступающая за переднюю поверхность дискового долбяка мешает работе. Втулочные и хвостовые долбяки – это долбяки малых диаметров применяемые для нарезания мелкомодульных колес и колес внутреннего зацепления малого диаметра. В зависимости от точности долбяки бывают АА А В классов точности.
Для повышения экономичности долбяки крупных модулей делают сборными а для повышения производительности – комбинированными с черновыми и чистовыми зубьями для обработки одного или нескольких колес одновременно оснащают твердыми сплавами.
Рисунок 2.1 Профиль долбяка и его геометрические параметры
Долбяк бывают 5 типов (Рисунок 2.2). Долбяки: а — тип 1 (дисковые прямозубые с диаметрами 75 100 125 160 и 220 мм); б — тип 2 (дисковые косозубые с диаметром 100 мм); в — тип 3 (чашечные прямозубые с диаметрами 50 75 100 и 125 мм); г — тип 4 (хвостовые прямозубые с диаметрами 25 38 мм); д — тип 5 (хвостовые косозубые с диаметром 38 мм и углами наклона 15° и 23°).
Рисунок 2.2 Типы долбяков
Долбяк делятся на три класса: АА предназначается для обработки зубчатых колёс 6-й степени точности А — 7-й и Б — 8-й. При нарезании зубьев Долбяк и обрабатываемая заготовка обкатываются по начальным окружностям без скольжения. Кроме вращения Долбяк движется возвратно-поступательно вдоль оси заготовки а также поступательно в радиальном направлении на величину высоты зуба (или её части) нарезаемого колеса. Срезание стружки происходит при движении Долбяк вниз (рабочий ход); обратный ход холостой.Нарезание зубьев цилиндрических зубчатых колес на зубодолбежных станках производится двумя методами: обкатыванием — круглыми долбяками или зубчатой рейкой и копированием — специальной резцовой головкой. Наибольшее применение в промышленности получил метод обкатывания круглыми долбяками. Обработку производят на зубодолбежных станках с одним вертикальным инструментальным шпинделем или на станках с двумя противоположно расположенными горизонтальными шпинделями. Метод обкатывания круглым долбяком более универсален его технологические возможности значительно шире чем при зубофрезеровании червячными фрезами.
На зубодолбежных станках методом обкатывания круглыми долбяками можно нарезать зубчатые колеса внешнего (Рисунок 2.3 а) и внутреннего (б) зацеплений с прямыми и косыми зубьями с бочкообразной (в) и конической (г) формами зуба.
Некоторые типы зубчатых колес могут быть нарезаны только долбяками к ним относятся блочные зубчатые колеса с близко расположенными венцами (д) колеса цилиндроконических передач (е) зубчатые рейки (ж) шевронные колеса без канавки между зубьями (з) и с канавками короткие шлицевые валы а также копиры со сложной формой зубьев.
Рисунок 2.3 – Нарезание зубчатых колес круглыми долбяками на зубодолбежных станках.
Зубодолбление широко применяют не только там где вследствие геометрии колеса нельзя использовать зубофрезерование но и для нарезания стандартных зубчатых колес высокого качества. Степень точности изготовления зубчатых колес круглыми долбяками: при применении долбяков класса АА - 6-я класса А -7-я и класса В - 8-я (по ГОСТ 1643-81). Шероховатость поверхности профилей зубьев Ra = 08 -16 мкм.
Принципы образования зубьев и методы зубодолбления
Нарезание зубчатых колес круглыми долбяками по методу обкатывания основано на воспроизведении зацепления пары зубчатых колес. Одним элементом является нарезаемое колесо другим - круглый долбяк 2 (Рисунок 2.4 а). Если червячную фрезу можно сравнить с производящей рейкой то долбяк сравнивают с зубчатым колесом имеющим такое же число зубьев.
Долбяк нарезает зубья строганием при возвратно-поступательном движении причем снятие стружки производится по всей ширине зуба и только в процессе рабочего хода 3. При обратном ходе 1 снятие металла не происходит инструмент отводится от заготовки (или заготовка отводится от инструмента) чтобы исключить повреждение режущих кромок при трении.
В процессе резания колесо 6 и долбяк 1 вращаются согласованно вокруг своих осей совершая движения обкатки 7 и 4 относительно друг друга для придания эвольвентного профиля зубьям нарезаемого колеса одновременно долбяк совершает возвратно-поступательное движение вдоль оси. Поворот долбяка на один зуб соответствует повороту заготовки также на один зуб.
В начале обработки долбяк 2 быстро подводится к заготовке не доходя до ее наружной поверхности примерно 05 100 мм. По традиционному методу обработки первоначально долбяк 2 осуществляет врезание с определенной радиальной подачей 5. При достижении полной высоты зуба (если обработку производят за один проход) врезание прекращается автоматически включается круговая подача начинается взаимная обкатка в результате движения резания происходит формирование профиля зубьев колеса. Обкатывание продолжается до тех пор пока заготовка после врезания не совершит один полный оборот т.е. все зубья колеса будут полностью обработаны. После чего станок автоматически выключается заготовка возвращается в исходное положение.
На зубодолбежных станках с ЧПУ врезание долбяка может также осуществляться с меньшей радиальной подачей при одновременной взаимной обкатке.
Рисунок 2.4 - Схема нарезания круглыми долбяками цилиндрических колес:
а - прямозубых; б - косозубых (с помощью винтового копира (в))
Прямозубые чашечные долбяки применяют для изготовления прямозубых колес внешнего и внутреннего зацепления. Чашка долбяка которая отличает его от других типов долбяка предназначена для закрепления долбяка в патрон станка.
Рисунок 2.5 - Прямозубый чашечный долбяк.
2 Расчет геометрических и конструктивных параметров
Расчет ведем по методике [3].
Необходимо спроектировать и дать рабочий чертёж чашечного долбяка для нарезания зубьев прямозубых цилиндрических колёс с закрытым венцом по следующим исходным данным:
Угол профиля нарезаемого колеса α= 20°;
Модуль колеса m=35 мм;
Номинальный делительный диаметр d=75 мм;
Число зубьев нарезаемого колеса Z1=32;
Число зубьев сопряжённого колеса Z2=64.
Обозначения геометрических параметров долбяка и профиля его зуба представлены на рисунках 2.1 2.2.
Число зубьев долбяка с учетом заданного номинального делительного диаметра долбяка равно и округляется до целого числа.
Уточняется делительный диаметр долбяка
Передний угол для черновых долбяков принимается
Задний угол на вершине рекомендует равным 9.
Фактический угол профиля долбяка с точностью до 1 определяется по формуле:
Боковой задний угол в сечении по делительному цилиндру :
Задний угол на боковых сторонах зубьев в нормальном сечении к профилю:
На угол поворачивается шлифовальная бабка станка при шлифовании зубьев долбяка поэтому указанный угол обязательно проставляется на чертеже.
Основной диаметр долбяка:
Определение размеров зубьев долбяка в исходном сечении.
Толщина зуба долбяка по делительной окружности:
- для черновых долбяков
где - утоньшение зуба долбяка для образования припуска на зубьях нарезаемого колеса под последующую обработку:
- величина утолщения зубьев долбяка для образования бокового зазора при чистовой обработке нарезаемых колес. Значения и допуск на толщину зуба долбяка принимаем по.
Высота головки зуба где - высота ножки зуба нарезаемых шестерни и колеса;
где если и если - высота головки зуба нарезаемых шестерни и колеса.
Диаметр окружности выступов долбяка в исходном сечении:
Минимально допустимая по условию механической прочности толщина зуба нового долбяка на наружном диаметре:
Толщина зуба долбяка на наружном диаметре в исходном сечении:
где α – угол в радианах;
Величина исходного расстояния А обеспечивающая заданную толщину зуба на вершине:
Величина исходного расстояния принимается равной расчетной если расчетная и если расчетная где B – высота долбяка по ГОСТ 9323-79. Для данного долбяка ;
Проверка долбяка с выбранным исходным расстоянием на отсутствие интерференции с переходными кривыми у нарезаемых им колес выполняется только для шестерни.
Интерференция отсутствует если выполняется условие где - радиус кривизны активного профиля зуба шестерни в нижней начальной контактной точке при внешнем зацеплении ее с колесом; - радиус кривизны эвольвентного профиля зуба шестерни в точке начала переходной кривой при нарезании ее с долбяком (рис.2.6).
Рисунок 2.6 Определение радиусов кривизны профиля зуба шестерни
где - радиус основной окружности колеса
Межосевое расстояние в зубчатой передаче определяется по формуле:
где - коэффициенты смещения шестерни и колеса соответственно. Так как данное зацепление без смещения то
Угол профиля зуба долбяка в точке на окружности выступов определяется из соотношения:
где - радиус делительной окружности колеса; - радиус окружности вершин колеса.
- радиус основной окружности долбяка.
Межосевое расстояние в станочном зацеплении шестерни с долбяком определяется по формуле:
Угол зацепления в станочном зацеплении определяется из соотношения:
где и - коэффициенты смещения соответственно для шестерни и долбяка.
При проверке нового долбяка принимают:
поэтому интерференция отсутствует.
Определение размеров зубьев долбяка на передней поверхности.
Окружная толщина зуба:
Высота головки зуба долбяка:
Высота ножки зуба долбяка:
Диаметр вершин зубьев долбяка:
Диаметр впадин зубьев долбяка:
Наибольшая допустимая величина стачивания долбяка ΔВ ограничивается прочностью зуба сточенного долбяка и отсутствием подрезания зубьев нарезаемых им колес: где - длина зуба окончательно сточенного долбяка; рекомендуется В – длина зуба нового долбяка (принимается по ГОСТ 9323-79).
При работе окончательно сточенным долбяком может происходить подрезание ножки зуба шестерни и колеса. Подрезание отсутствует если выполняется условие (для шестерни) и (для колеса). Расчет и ведут по формулам приведенным в п. 14 принимая :
На отсутствие срезания головки зуба колеса окончательно сточенного долбяком проверка производится по формуле:
В этой формуле значения компонентов вычисляются следующим образом:
где - коэффициент смещения;
Остальные элементы конструкции долбяка выбираем по ГОСТ 9323-79 или из конструктивных соображений.
По ГОСТ 9323-79 определяются допуски на все элементы долбяка и технические требования к его изготовлению.
Выполняется рабочий чертеж долбяка с учетом всех требований к рабочему чертежу.
Разработка конструкции концевой фрезы с МНП.
1 Патентно-информационный поиск. Назначение типы описание конструкции фрез общего назначения
№2147492 Концевая фреза
Концевая фреза включающая хвостовик и рабочую часть имеющую винтовые режущие зубья с пилообразными выступами со скругленными вершинами на передней поверхности расположенными на цилиндрической части фрезы асимметрично отличающаяся тем что радиус скругления вершин упомянутых пилообразных выступов определен из выражения:
где S - подача на зуб ммзуб;
Н - требуемая высота шероховатости мкм;
R - радиус округления пилообразного выступа мм.
№2243066 Концевая фреза
Концевая фреза содержащая на корпусе режущей части непрерывные зубья одного направления и угла наклона к оси фрезы и чередующиеся с ними участки корпуса этого же направления и угла наклона со ступенчатыми зубьями другого направления и другого угла наклона отличающаяся тем что угол наклона ступенчатых зубьев равен нулю и участки корпуса выполнены шириной равной ширине непрерывного зуба и одинаковыми по форме поперечного сечения с непрерывным зубом а шаг ступенчатых зубьев выбран таким чтобы их режущие кромки перекрывали друг друга в направлении резания.
Назначение типы описание конструкции фрез общего назначения
Фрезерование является одним из наиболее распространенных методов обработки. По уровню производительности фрезерование превосходит строгание и в условиях крупносерийного производства уступает лишь наружному протягиванию. Кинематика процесса фрезерования характеризуется быстрым вращением инструмента вокруг его оси и медленным движением подачи. Движение подачи при фрезеровании может быть прямолинейно-поступательным вращательным либо винтовым. При прямолинейном движении подачи фрезами производится обработка всевозможных цилиндрических поверхностей: плоскостей всевозможных пазов и канавок фасонных цилиндрических поверхностей (рисунок 3.1).
При вращательном движении подачи фрезерованием обрабатываются поверхности вращения а при винтовом движении подачи — всевозможные винтовые поверхности например стружечные канавки инструментов впадины косозубых колес и т. п.
Фреза представляет собой исходное тело вращения которое в процессе обработки касается поверхности детали и на поверхности которого образованы режущие зубья. Форма исходного тела вращения зависит от формы обработанной поверхности и расположения оси фрезы относительно детали. Меняя положение оси инструмента относительно обработанной поверхности можно спроектировать различные типы фрез предназначенных для изготовления заданной детали.
Рисунок 3.1. - Схемы фрезерования
Основные части фрез и элементы их режущей части показаны на рисунок 3.2
Рисунок 3.2. - Элементы фрез
Многообразие операций выполняемых на фрезерных станках обусловило разнообразность типов форм и размеров фрез.
Разновидностью концевых фрез являются шпоночные двухзубые фрезы (рисунок 3.3). Рассматриваемые шпоночные фрезы подобно сверлу могут углубляться в материал заготовки при осевом движении подачи и высверливать отверстие а затем двигаться вдоль канавки. В момент осевой подачи основную работу резания выполняют торцовые кромки. Одна из них должна доходить до оси фрезы чтобы обеспечить сверление отверстия.
Переточка таких фрез производится по задним поверхностям торцовых кромок поэтому при переточках их диаметр сохраняется неизменным.
Рисунок 3.3. - Шпоночные фрезы
Фрезы для обработки Т-образных пазов
Для обработки Т-образных пазов часто встречающихся в станкостроении применяют Т-образные фрезы (рисунок 3.4).
Рисунок 3.4. - Фреза для обработки Т-образных пазов
Они работают в тяжелых условиях и часто ломаются что объясняется затрудненным отводом стружки. Каждый зуб работает два раза за один оборот фрезы. Такие фрезы делаются с разнонаправленными зубьями и имеют поднутрения с углом Ф1 = 1°30'÷2* на обоих торцах. С целью улучшения условий размещения стружки производят заточку фасок на зубьях то с одного то с другого торца под углом 30° и шириной 05мм.
Фрезы со смеными неперетачиваемыми пластинами из твердосплавного материала.
Фрезы с механическим креплением сменных неперетачиваемых пластин широко применяются для обработки различных материалов. Их преимущество по сравнению с фрезами с напайными пластинами и вставными ножами состоит в повышении стойкости в 2 раза и сокращению до 3 раз количесва фрез находящихся в обращении. Исключение операций пайки и заточки ножей снижает брак при изготовлении фрез позволяет использовать новые виды инструментальных материалов.
Рисунок 3.5 Фрезы концевые с механическим креплением многогранных твердосплавных пластин. Основные размеры. ГОСТ 28435-90
Рисунок 3.6 Фрезы торцовые концевые с механическим креплением круглых твердосплавных пластин. Конструкция и размеры. ГОСТ 22088-76
Расчет ведем по методике [2].
Фреза концевая с ромбическими МНП;
Выбор инструментального материала:
по ГОСТ 28437-90 выбираем материал корпуса фрезы сталь 40Х ГОСТ 14959;
по каталогу Mitsubishi выбираем пластину MPMT 120408.
Выбираем геометрические параметры фрезы:
γ=11° =0o φ=90° φ1=4° λ=0°α=11o.
Рассчитаем гнёзда под режущие пластины.
Передняя поверхность пластины имеет собственную геометрию и требуется расчет бокового и радиального смещения пластин.
Подсчитываем боковое и радиальное смещение.
E=D2=275 т.к. φ=90o и кромка идет по диаметру.
Разработка конструкции круглого фасонного резца
1 Патентно-информационный поиск. Назначение типы описание конструкции фасонного резца
№1103952 Сборный фасонный резец
Неподвижность элементов и жесткость всей конструкции обеспечивается посредством того что возникающий вследствие действия сил резания вращающий момент приложенный к дисковому резцу 1 и стремящийся повернуть его относительно оси воспринимается резьбовым соединением дискового резца 1 с осью 2. Сопрягаемая поверхность резьбы обуславливает возникновение крутящего момента на оси 2 и осевой силы действующей- вдоль нее. Для уменьшения величины этой силы действующей на ось 2 резьба делается многозаходной. Осевая сила стремится переместить дисковый фасонный резец 1 вдоль оси 2. Этому препятствуют боковые поверхности державки 3 жесткость которых обеспечивается осью 2 стягиваемой крепежными элементами 4. Крутящий момент передается с оси 2 на державку 3 через квадратные опоры чем исключается возможность вращения дискового фасонного резца вместе с осью 2.
№1219265 Фасонный резец
Фасонный резец по авт. св. № 837568 отличающийся тем что с целью расширения технологических возможностей боковые стороны пластин режущие кромки которых образуют участки перегиба профиля выполнены с уклоном направленным к центру кривизны этого участка профиля.
Назначение типы описание конструкции фасонного резца
Резцы с фасонной режущей кромкой применяют для обработки поверхностей вращения цилиндрических и винтовых поверхностей на токарных и револьверных станках автоматах и полуавтоматах. Схема обработки поверхности вращения фасонным резцом показана на Рис. 4.1. В процессе обработки заготовка быстро вращается вокруг своей оси а резец совершает движение подачи. Наиболее часто движение подачи является поступательным. Оно может осуществляться в радиальном направлении. Резцы с таким направлением подачи называют радиальными (Рис. 4.1 а). В процессе обработки направления движения подачи одной или нескольких точек режущей кромки такого резца пересекает ось детали.
Фасонные резцы с осевой подачей применяют при обработке односторонних профилей не имеющих кольцевых канавок или выступов а также при обработке торцовых фасонных поверхностей (Рис. 4.1б). По сравнению с радиальными резцами при обработке ступенчатых деталей рассматриваемые резцы срезают меньшие сечения а силы резания будут меньшими. Это позволяет обрабатывать менее жесткие детали.
Рисунок 4.1. Схемы обработки поверхности вращения фасонным резцами
Направление подачи различных точек режущей кромки фасонного резца может касаться обработанной поверхности детали. Фасонные резцы с таким направлением подачи называют тангенциальными фасонными резцами (Рис. 4.1 в). Произвольная точка режущей кромки такого резца начинает резание в точке А а заканчивает работу в точке В При дальнейшем движении подачи резец металла не снимает поэтому детали получаются идентичными по размерам независимо от того в какой момент времени выключено движение подачи.
Фасонные резцы можно разделить на следующие группы:
) по форме — круглые (рис. 4.2 а-в е) призматические (рис. 4.2 г и д) и стержневые (рис. 4.2 ж);
) по установке относительно детали призматические резцы делятся на резцы с радиально расположенной режущей кромкой (рис. 4.2 г) и тангенциальные (рис. 4.2 д);
) по расположению оси — с параллельным расположением оси относительно оси детали (рис. 4.2 а—в) и с наклонным расположением оси или базы крепления (рис. 4.2 е);
) по форме образующей поверхности — круглые резцы с кольцевыми образующими (рис. 4.2 а и б) круглые с винтовыми образующими (рис. 4.2 в) призматические с плоскими образующими (рис. 4.2 г и д). Резцы с наклонным расположением оси или базы (рис. 4.2 е) ввиду их сложности применяют редко в случае когда форма детали (например на участке аб) не позволяет применить резцы с параллельным расположением оси.
Фасонные резцы изготовляют в основном из быстрорежущей стали но все более широкое применение находит и твердый сплав. Пластифицированный твердый сплав легко обрабатывается обычным твердосплавным резцом. Полученные после токарной обработки и разрезки профильные (еще «сырые») пластинки имеют размеры на 25—30% больше по сравнению с окончательными размерами профиля резца.
Такие пластинки-заготовки подвергаются затем окончательному спеканию после чего припаиваются (или крепятся механически) к корпусу фасонного резца. Применение твердосплавных фасонных пластин для резцов способствует повышению производительности труда на 30—40% (по сравнению с быстрорежущими фасонными резцами). Фасонный резец должен иметь соответствующие задние и передние углы чтобы стружка снималась при достаточно выгодных условиях. Задний угол α режущей кромки резца зависит от типа фасонного резца. У круглых фасонных резцов α = 10-12° у призматических фасонных резцов а = 12 - 15°; у резцов предназначенных для затылования фасонных фрез задний угол α может приниматься до 25—30°; его приходится брать большим потому что угол наклона траектории относительного движения достигает 10—15°.
Рисунок 4.2- Типы фасонных резцов:
а - круглый резец с передним углом равным нулю; б - круглый резец с передним углом больше нуля; в - круглый винтовой резец;
г - призматический резец с радиально расположенной режущей кромкой;
д - тангенциальный резец; е - резец с наклонным расположением оси;
ж - стержневой фасонный резец.
Рисунок 4.3 - Фасонный резец оснащённый твёрдым сплавом:
– корпус; 2 – профильные пластины; 3 – упор.
Чтобы получить положительные задние углы на участках режущих кромок перпендикулярных оси детали применяют круглые фасонные резцы с наклонным расположением оси под углом φ по отношению к оси детали и призматические фасонные резцы с наклонным расположением базы крепления (Рис. 4.4 а).
Рисунок 4.4 Фасонные резцы с наклонной установкой и винтовой задней
В необходимых случаях при наклонной подаче рассматриваемых резцов становится возможным обработка «поднутрений» на детали. С целью получения положительных задних углов у круглых резцов может создаваться также винтовая задняя поверхность (Рис. 4.4 б). Такие резцы особенно пригодны для расточки ступенчатых каналов с осевой подачей. Они могут изготовляться с хвостовиком служащим для их крепления. Передняя поверхность фасонных резцов в большинстве случаев является плоскостью. Передняя плоскость может располагаться под определенным передним углом γ параллельно оси детали (Рис. 4.5 а). В общем же случае фасонные резцы имеют двойной наклон передней плоскости когда ее положение характеризуется не только передним углом γ по и углом наклона режущей кромки λ (Рис. 4.5 б).
Рисунок 4.5 Положение передней плоскости резца
Такие резцы используются при повышенных требованиях в отношении соблюдения формы и точности обработки конических участков поверхностей деталей.4.2 Расчет геометрических и конструктивных параметров
2 Расчет геометрических и конструкционых параметров
Рисунок 4.5. Эскиз детали.
d1 = 15 мм r1 = 75 мм
d2 = 35 мм r2 = 175 мм
d3 = 44 мм r3 = 22 мм
d4 = 50 мм r4 = 25 мм
d5 = 44 мм r5 = 22 мм
d6 = 35 мм r6 = 175 мм
d7 = 35 мм r7 = 175 мм
Точность – 11-й квалитет материал детали – чугун СЧ18 (HB=170 МПа)
Определение углов режущей части.
Выбираем передний угол резца =12° задний угол =12°.
Коррекционный расчет призматического резца.
Из-за наличия заднего и переднего углов профиль резца в осевом сечении и сечении перпендикулярном образующим призмы не совпадает с профилем детали.
Цель корректировочного расчёта – определение высотных размеров профиля фасонных лезвий измеренных в направлении перпендикулярном базе резца.
Определяем положение центра
A1 = r1·cos(g) = 75·cos(12) = 7336 мм.
A2 = r2·cos(g2) =175·cos(5111) =1743 мм;
A3 = r3·cos(g3) =22·cos(4064) =21945 мм;
A4 = r4·cos(g4) =25·cos(3575) =24951 мм;
A2 = A6 = A7 =1743 мм;
С2 = A2 – A1 = 1743-7336 = 10094 мм;
С3 = A3 – A1 = 21945-7336 = 14609 мм;
С4 = A4 – A1 = 24951-7336 = 17615 мм;
С2 = С6 = С7 = 10094 мм;
H=48 sin(12+12)= 19523 мм.
B1= 48 cos(12+12)=4385 мм;
B2= B1 – C2=43850 – 10094=33756 мм;
B3= B1 – C3=43850 – 14609=29241 мм;
B4= B1 – C4=43850 – 17615=26235 мм;
B2= B6= B7= 33756 мм;
=arctg(HB2)=arctg(1952333756)=30043o;
=arctg(HB3)=arctg(1952329241)=33729o;
=arctg(HB24)=arctg(1952326235)=36655o;
R2= R6= R7=38968 мм;
Rсф=(R1+R2)2=(48+38968)2=43484 мм;
CсфM= Rсфcos сф=43484cos 2668=38854 мм;
KCсф=5121-38854=12356 мм;
rcт=(75+175)2=125 мм;
Δ=125-12454=0046 мм.
Рисунок 4.6 Схема к коррекционному расчету.
Расчет допусков на размеры профиля.
Допуски на диаметр Di:
Допуски на радиус dRi:
Высота профиля детали hi:
Высота профиля резца Pi:
Высота точки профиля Pi’:
Допуск на высоту профиля hi hi:
dh1 = dR1 - dRб = 0035 мм;
dh4 = dR4 - dRб = 0025 мм;
Допуск на заточку dhЗ.у.i = 0.5·dmin·Pi’P’dmin:
Допуск на неточность выполнения профиля hp:
Допуск на высоту профиля Pi’:
Верхнее(+) и нижнее(-) отклонение высоты профиля:
Расчитал и сделал рабочие чертежи чашечный долбек концевую фрезу с МНП и фасонный круглый резц.
ДОЛБЯК ОКОНЧАТЕЛЬНЫЙ МОЙ.cdw

Номинальный делительный диаметр
Фактический угол зацепления
Диаметр основной окружности
Толщина зубьев по дилетельной окружности в исходном сечении
Высота головки зуба в исходном сечении
Степень точности долбяка
Отклонение от параллельности опорных поверхностей
Торцевле биение передней поверхности
Биение окружности вершин зубьев
Разность соседних окружных шагов
Накопленная погрешность окружного шага
Радиальное биение зубчатого венца
Профиль зуба в плоскости переднего торца
Долбяки должны удовлетворять требованиям ГОСТ 9323-79
Общие допуски по ГОСТ 30893
номинальный делительный диаметр
класс точности долбяка
год выпуск и товарный знак завода-изготовителя
На всех поверхностях долбяков не должно бытьт трещин
заусенцев и следов коррозии
Сталь Р6М5 ГОСТ 19265-73
Спецификация 123456.spw

Резец фасонный дисковый правильный.cdw

Общие допуски по ГОСТ 30893.2-mK.
Маркировать: обозначение; Р6М5;
3 мм; товарный знак завода-изготовителя; год выпуска.
Профиль резца в нормальном сечении (2:1)
Рекомендуемые чертежи
- 14.03.2022