Проектирование конструкции приспособления для сверлильного станка




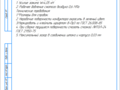
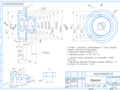
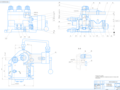
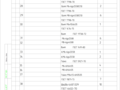
- Добавлен: 25.01.2023
- Размер: 667 KB
- Закачек: 0
Описание
Состав проекта
![]() |
![]() |
![]() |
![]() |
![]() |
![]() ![]() ![]() ![]() |
![]() |
![]() ![]() ![]() ![]() |
![]() ![]() ![]() ![]() |
![]() ![]() ![]() ![]() |
![]() ![]() ![]() ![]() |
![]() ![]() ![]() |
![]() ![]() ![]() ![]() |
Дополнительная информация
Кондуктор скальчатый _ 1510.13.528.0.0 СБ.cdw

Нерабочие поверхности кондуктора окрасить в зеленый цвет.
Спецификация 3л..frw

Спецификация 1л..frw

Спецификация 2л..frw

тт.cdw

Техническая характеристика:
Рабочее давление сжатого воздуха 0
Технические требования:
*Размеры для справок.
Нерабочие поверхности кондуктора окрасить в зеленый цвет.
Маркировать и клеймить шрифтом 8-Пр3 по ГОСТ 26.008-85
При сборке трущиеся поверхности смазать смазкой ЛИТОЛ-24
Максимальный зазор в соединении штока и корпуса 0
ПЗ Головачёв.doc
Технологическая оснастка
на тему "Проектирование конструкции приспособления
для сверлильного станка
Головачёв С.Ю. Разработка комплекта конструкторской документации для приспособления сверлильного станка – Трехгорный: ТТИ НИЯУ МИФИ ТМ 2013 27 л. Библиография: литературы – 7 наименований 1 лист чертежей формата А1 1 лист чертежей формата3 листа спецификации.
В данном курсовом проекте рассматривается вопрос разработки комплекта конструкторской документации на приспособление для детали типа крышка на технологической операции 060.
В данной работе разработана принципиальная схема приспособления рассчитаны силы зажима и место их приложения на основе расчета по усилиям резания. Определена необходимость применения вспомогательных устройств выбор их конструкций исходя из массы заготовки и выполняемой операции при необходимой точности обработки.
Вычислена погрешность установки заготовки на приспособлении. Описана технология сборки приспособления его установки и настройки на станке последовательность действий при эксплуатации.
Анализ исходных данных
Уточнение схемы базирования
1 Выбор установочных элементов приспособления
Определение места приложения сил закрепления и их величины
Выбор типа зажимного устройства
1 Описание схемы привода
2 Расчет основных размеров зажимного устройства
Необходимость вспомогательных устройств исходя из массы детали
Определение погрешности приспособления и расчет на точность
Определение технических требований на приспособление
Описание сборки приспособления его установки на станке наладка
последовательность действий при эксплуатации
2 Установка приспособления на столе и его наладка
3 Последовательность действий при эксплуатации
)Графическая часть на 2 листах формата А1 и А3;
)Спецификация на 3 листах.
Приспособлениями в машиностроении называют вспомогательные устройства используемые при механической обработке сборки и контроля изделий. Приспособления рабочие и контрольные инструменты вместе взятые называют технологической оснасткой причем приспособления являются наиболее сложной и трудоемкой ее частью. Наиболее значительная их доля составляет приспособления применяемые для установки и закрепления обрабатываемых заготовок. Использование приспособлений способствует повышению производительности и точности обработки сборки и контроля облегчению условий труда сокращению количества и снижению необходимой квалификации рабочих строгой регламентации длительности выполняемых операций расширению технологических возможностей оборудования повышению безопасности работы и снижению аварийности.
Производительность при использовании приспособлений повышается устранением разметки заготовок и сокращением штучного времени по всем остальным технологическим операциям. Использование приспособлений снижает себестоимость продукции. Однако в каждом конкретном случае целесообразность применения приспособлений должна подтверждаться экономическим расчётам. Применение быстродействующих и автоматизированных приспособлений совместно с управляющими и транспортирующими устройствами является одним из эффективных направлений автоматизации универсального технологического оборудования способствующих внедрению многостаночного обслуживания и высвобождению рабочих.
Приспособления должны быть удобными и безопасными в работе быстродействующими достаточно жесткими для обеспечения заданной точности обработки удобными для быстрой установки на станок что особенно важно при периодической смене приспособлений в серийном производстве простыми и дешевыми в изготовлении доступными для ремонта и замены изношенных деталей.
Деталь типа Крышка имеет ступенчатую цилиндрическую форму со сквозным ступенчатым отверстием.
Деталь типа Крышка изготавливается из сплава СЧ 20 ГОСТ 1412 - 85 его химический состав приведен в таблице 1.1.
Таблица 1.1 – Химический состав СЧ 20
Серый чугун технологичный материал обладает хорошей жидкотекучестью малой склонностью к образованию усадочных дефектов по сравнению с чугуном других типов. Из него можно изготовлять отливки самой сложной конфигурации с толщиной стенок от 2 до 500мм.
В основу стандартизации серого чугуна (СЧ) заложены принципы регламентирования минимально допустимого значения временного сопротивления разрыву при растяжении.
Механические свойства серого чугуна по ГОСТ 1412-85 ИСО 185 и национальным стандартам некоторых стран приведены в табл. 1.2
Таблица 1.2 – Механические свойства СЧ 20
Марка чугуна по СТ СЭВ 4560-84
Временное сопротивление при растяжении МПА (кгсмм2) не менее
Модульупругостипри растяжении Е.10-2 МПА
Удельнаятеплоемкостьпритемпературе20-200 С Дж (кг.К)
Коэффициент линейного расширения при температуре 20-200
Теплопроводность при 20 Вт(м.К)
По ГОСТ 1412-85 марка серого чугуна определяется показателем временного сопротивления чугуна при растяжении. Условное обозначение марки включает буквы СЧ - серый чугун и цифровое обозначение величины минимального временного сопротивления при растяжении в МПа × 10-1.
Механические свойства серого чугуна обеспечиваются в литом состоянии или после термической обработки. Поскольку значения прочности чугуна данной марки в отливке зависят от скорости охлаждения определяемой толщиной стенки (диаметром) отливки в стандартах приводятся минимальные значения вв отдельно отлитых пробных заготовках других диаметров или сечений из СЧ каждой марки.
Классификация серого литейного чугуна по международному стандарту ИСО 185 включает шесть классов устанавливаемых на основании результатов механических испытаний на растяжение образцов вырезанных из различных литейных проб.
Характерным показателем определяющим марку чугуна является временное сопротивление при растяжении в образцов из отдельно отлитых цилиндрических проб диаметром 30мм.
По стандарту Германии DIN1691 в заказе на отливки должно быть однозначно указано: является ли характерным свойством временное сопротивление при растяжении или твердость по Бринеллю. В зависимости от этого маркировка чугунов обозначается по разному. Например:
Чугун DIN 1691-GG-25
Чугун DIN 1691-GG-210HB
Данные о временном сопротивлении при растяжении являются гарантированными в отливках. Связь между толщиной стенки (25 - 80мм) и твердостью отливки из различных марок СЧ представлена в DIN1691 в регламентированном виде что позволяет правильно и точно устанавливать твердость для заданного интервала толщин стенок отливок.
Деталь типа Крышка является вполне технологичной. Недостатком будет являться легкая деформация материала детали что будет затруднять её обработку. Для этого потребуется разработка и использование специальных приспособлений и оснастки.
Анализ исходных данных
К исходным данным относятся маршрутный технологический процесс обработки детали программа выпуска деталей – 2000используемые оборудования и инструмент режимы резания. На основании программы выпуска следует применять механизированный зажим-отжим заготовки в данном случае он будет пневматический. Маршрутный технологический процесс для обработки детали Основание приведен в таблице 2.1.
Таблица 2.1 – Маршрутный технологический процесс
Наименование операции
Согласно заданию следует разработать приспособление для выполнения операции 070 Фрезерно-сверлильной ЧПУ.
После операции 060 заготовка имеет вид операционный эскиз которой показан на рисунке 1.
Рисунок 1 – Операционный эскиз на операцию 060
Согласно операционному эскизу на операцию 060 деталь имеет все необходимые габаритные размеры. Таким образом нет необходимости специально подготавливать опорную базовую поверхность при установке и закреплении детали в проектируемом приспособлении. В качестве базовых поверхностей используем цилиндрическую поверхность 48H11(+016).Их шероховатость равна Rа 63.
На операции 070 операционный эскиз которой показан на рисунке 2 необходимо просверлить отверстие.
Рисунок 2 – Операционный эскиз на операцию 070
Приспособление на данной операции используется стационарно то есть оно устанавливается на станок на время обработки данной партии деталей. Приспособление должно обеспечить надежное закрепление заготовки предотвращающее возможность поворота заготовки при фрезеровании и сверлении.
Схема базирования детали на операции 070 приведена на рисунке 3.
Рисунок 3 – Схема базирования на операцию 070
Проектируемое приспособление для данной детали будет крепиться на столе станка вертикально положение определяется с помощью двух установочных цилиндрических пальцев и фиксируется болтами устанавливается на квадратном столе станка габаритами 300х300.
Так же к исходным данным относится программа выпуска деталей которая равна 2000 штук и режим работы участка – двусменный. На основании этих данных следует применять не ручной а механизированный привод закрепления детали. В нашем случае в качестве привода используется пневмоцилиндр встроенный в корпус приспособления.
Цилиндрическая заготовка закреплена в призме с углом α и находится под
действием момента обработки Мкр и осевой силы Р0. Создаваемые силы и моменты трения противодействуют сдвигу вдоль оси и повороту заготовки. Тогда расчетная формула имеет вид:
где Мкр- крутящий момент на сверле Н·м. Мкр=81Н·м;
К-коэффициент запаса К=252;
f- коэффициент трения на рабочих поверхностях зажимов f=016;
d- диаметр заготовки мм.
В качестве силового механизма выступает кондукторная плита с установленными в нее прижимными опорами и пневмоцилиндр.
Фактическая сила зажима развиваемая пневмоцилиндром определяется по формуле:
где р- давление в пневмосистеме предприятия Р=04-16 МПа.
- КПД пневмоцилиндра =095.
Данный зажим вполне удовлетворяет всем требованиям и
обеспечивает необходимую зажимную силу которая превосходит силы резания.
Приспособление устанавливается на стол станка при помощи двух цилиндрических пальцев которые предотвращают поворот приспособления относительно стола станка. В столе станка выполнены пазы размером 14Н7 (+0018) а размер установочного пальца принимаем 14h6 (-0014). Таким образом установка приспособления на столе станка будет производится по посадке с зазором 14 мм.
Запрессовка установочных пальцев в приспособление будет производиться по посадке с натягом 8мм
Определяем максимальный зазор между установочными пальцами и пазами стола станка
где максимальный зазор мм;
нижнее отклонение установочного пальца мм;
верхнее отклонение отверстия мм.
Определяем действительный угол поворота приспособления относительно стола станка
где действительный угол поворота град.;
расстояние между установочными пальцами мм.
Геометрические параметры установочных пальцев показаны на рисунке 5.
Рисунок 5 – Геометрические размеры установочного цилиндрического пальца
После выбора способа установки (базирования) детали и разместив установочные элементы в приспособлении определяем величину место приложения и направления сил для зажима обрабатываемой детали.
Величину силы зажима и ее направление определяем в зависимости от сил резания и их моментов действующих на обрабатываемую деталь.
На обрабатываемую деталь действуют силы резания от сверления а также их моменты..
Для силового расчета необходимо назначить станок и инструмент для сверления и рассчитать режимы резания.
Сверление будет производиться на вертикально-сверлильном станке 2Н125.
Сверлятся 1 отверстие 10 мм выдерживая размер от торца детали 1525+- 001 мм.
При обработке используется спиральное сверло из быстрорежущей стали 10 мм с коническим хвостовиком ГОСТ 10903 – 77.
Диаметр сверла D=10 мм
Длина сверла L=168 мм
Длина рабочей части l=87 мм
Геометрические параметры:
α=12º ; = 40º ; 2φ = 118º .
Расчет режимов резания.
Глубину резания t принимаем равной половине диаметра отверстия:
Подачу принимаем в соответствии с рекомендациями в [1 табл. 35] в зависимости от диаметра сверла и твердости обрабатываемого материала:
Скорость резания рассчитываем по эмпирической формуле:
где Т – среднее значение стойкости инструмента мин.;
D – диаметр сверла мм;
Kv – коэффициент учитывающий условия обработки.
Значения коэффициентов Cv показателей степени q y и m принимаем из [1 табл. 38]: Cv=70 q=04 y=07 и m=02.
Коэффициент Kv представляет собой:
Kиv – коэффициент учитывающий материал инструмента Kиv=1 [1 табл. 6];
Kмv – коэффициент учитывающий влияние материала заготовки:
где nv=09 [1 табл. 2];
Тогда скорость резания по формуле:
Частоту вращения шпинделя определим по формуле:
Для вертикально-сверлильного станка принимаем частоту вращения шпинделя равную nпр=650 мин-1.
Крутящий момент и осевую силу рассчитаем по формулам:
где Kp – поправочный коэффициент:
Поправочный коэффициент Kмр:
Значения коэффициентов Cм показателей степени q и y принимаем из [1 табл. 32]: Cм=00345 q=2 y=08.
Значения коэффициентов Cр показателей степени q и y принимаем из [1 табл. 42]: Cр=68 q=10 y=07.
Основное время на обработку:
где – длина обрабатываемой поверхности мм;
– величина врезания инструмента мм;
- величина перебега инструмента мм.
Принимаем величину перебега мм.
При конструировании нового станочного приспособления силу закрепления находят из условия равновесия заготовки под действием сил резания тяжести инерции трения реакции в опорах и собственно силы закрепления. Полученное значение силы закрепления проверяют из условия точности выполнения операции. В случае необходимости изменяют схему установки режимы резания и другие условия выполнения операций. При расчетах силы закрепления учитывают упругую характеристику зажимного механизма.
Силовой расчет учитывает коэффициент запаса - К поскольку при обработке заготовки возникают неизбежные колебания сил и моментов резания. В общем случае величина этого коэффициента находится в пределах от 2 35 в зависимости от конкретных условий обработки.
Значение коэффициента надежности К следует выбирать дифференцированно в зависимости от конкретных условий выполнения операции и способа закрепления заготовки. Его величину можно представить как произведение частных коэффициентов каждый из которых отражает влияние определенного фактора:
- гарантированный коэффициент запаса надежности закрепления ;
- коэффициент учитывающий наличие случайных неровностей на заготовке;
- для предварительно обработанных;
- коэффициент учитывающий увеличение силы резания при пригрессирующем затуплении инструмента в зависимости от метода обработки;
- в зависимости от обрабатываемого материала и метода обработки;
- коэффициент учитывающий увеличение силы резания при прерывистой обработке
- коэффициент учитывающий изменение зажимного усилия прикладываемого к заготовке;
- для пневматического зажимов;
- коэффициент учитывающий степень удобства расположения рукояток в ручных зажимах;
- при удобном расположении и малой длине рукоятки;
- коэффициент учитывающий наличие момента стремящегося повернуть заготовку на опорах.
- для опорного элемента имеющего ограниченную поверхность контакта с заготовкой;
Величину необходимого зажимного усилия определяют на основе решения задачи статики рассматривая равновесие заготовки под действием приложенных к ней сил. Для этого необходимо составить расчетную схему то есть изобразить на схеме базирования заготовки все действующие на нее силы: силы и моменты резания зажимные усилия реакции опор и силы трения в местах контакта заготовки с опорными и зажимными элементами.
По расчетной схеме необходимо установить направления возможного перемещения или поворота заготовки под действием сил и моментов резания определить величину проекций всех сил на направление перемещения и составить уравнения сил и моментов:
Рисунок 6 - Схема установки детали. Расчетная схема сверлильного приспособления.
Зажимные устройства приспособлений служат для зажима (закрепления) и разжима (раскрепления) деталей обрабатываемых на станках.
Зажимные устройства приспособлений должны удовлетворять определенным требованиям:
) при зажиме не изменять первоначально заданное положение обрабатываемой детали в приспособлении;
) сила зажима должна обеспечить надежное закрепление детали и не допускать сдвига поворота или вибраций детали при обработке на станке:
Зажимные устройства приспособлений подразделяются на простые (элементарные) и комбинированные. В зависимости от источника силы требуемой для зажима детали зажимные устройства делятся на ручные механизированные и автоматизированные. Ручные зажимные устройства приводит в действие непосредственно рабочий за счет мускульной силы. Механизированные зажимные устройства работают от пневматического гидравлического или другого привода. Автоматизированные устройства перемещаются от движущихся узлов станка. При этом зажим и разжим детали производится без участия человека ([3] с. 37).
Для зажима детали принимаем комбинированное механическое зажимное устройство которое состоит из призмы на которую устанавливается деталь и кондукторной плиты которая установлена на штоке приводимый в движение пневматическим устройством что позволяет надежно закрепить деталь.
1 Описание схемы пневмопривода
В качестве источника энергии для нашего приспособления выбираем пневмокамеру одностороннего действия встроенную в корпус приспособления.
Эти меры позволяют уменьшить габариты приспособления упростить его изготовление а следовательно уменьшить его стоимость.
Пневмокамера состоит из корпуса и крышки между которыми зажата диафрагма тарельчатой формы. Сжатый воздух поступает через штуцер давит на диафрагму и перемещает диск шток опускается вниз. Так шток воздействует на зажимной механизм приспособления закрепляя деталь.
Так как пневмокамера одностороннего действия то разжим осуществляется с помощью пружины которая давит на диафрагму через опорную шайбу и перемещает шток в обратную сторону. Так осуществляется разжим детали.
Схема пневмопривода показана на рисунке 7.
Рисунок 7 – Схема пневмопривода.
Сжатый воздух под давлением p0 подает в фильтр – отстойник. Затем через редукционный клапан и обратный клапан поступает в пневмораспределитель и в пневмопривод.
Функциональное назначение элементов привода входящих в схему:
)обратный клапан предотвращает быструю утечку воздуха из рабочей полости пневмокамеры;
)фильтр – отстойник предназначен для отделения воды масла и механических частиц;
)редукционный клапан предназначен для снижения давления воздуха и автоматического поддержания его на заданном уровне перед поступлением его из пневмолинии к потребителю;
Расчет диафрагменного привода основывается величинами: силой на штоке (сила необходимая для сжатия пружины) Q = 1567Н и длиной рабочего хода штока.
Рациональная длина хода штока при котором сила Q изменяется незначительно зависит от расчетного диаметра D диафрагмы ее толщины t материала формы и от диаметра d опорного диска диафрагмы.
Для проектируемой пневмокамеры выбираем тарельчатую резинотканевую диафрагму так как требуется ход 15 мм и эта диафрагма обеспечивает наибольшую прочность чем резиновая.
Определяем геометрические параметры и характеристику пневмокамеры.
Приближенная сила зажима при подаче сжатого воздуха в нагнетательную полость в исходном положении штока определяется по формуле:
где D – диаметр диафрагмы мм;
d – диаметр опорной шайбы( d = 07D) мм;
p – давление сжатого воздуха p = 630 кПа;
P – сила возвратной пружины (Р = 0).
Отсюда находим диаметр диафрагмы.
Получаем D = 662 мм. Внутренний диаметр диафрагмы Dд (диаметр в “свету”) принимаем равным 70 мм наружный диаметр Dд1= 98 диаметр опорной шайбы для резинотканевых диафрагм d = 49 мм. Толщину диафрагмы принимаем равной h = 4 мм.
Полученные характеристики пневмокамеры позволяют осуществить полноценный зажим и разжим детали то есть полученная пневмокамера полностью удовлетворяет нашим требованиям.
Вследствие того что устанавливаемая деталь в приспособлении имеет сравнительно небольшую массу (m = 076 кг) и габаритные размеры то во вспомогательных устройствах нет необходимости. Деталь устанавливается в приспособлении и снимается с него вручную.
Особенностью обработки отверстий на сверлильных станках является наличие в конструкции приспособлений элементов для направления режущих элементов (кондукторных втулок) направление и ориентация инструментов осуществляется непосредственно по режущей части.
Погрешность обработки заготовок на кондукторах во многом зависит от погрешности положения направляющих элементов относительно установочных элементов приспособления. В то же время погрешности связанные с установкой кондуктора на станке не оказывают влияния на точность координатного расположения обрабатываемых отверстий. Элементы для ориентации приспособления на станке в большинстве случаев отсутствуют положение кондуктора определяется свободным вхождением инструмента в направляющий элемент т.е. начало координат таких технологических систем материализуются в элементах для направления инструмента.
Погрешность настройки инструмента равна наибольшему возможному смещению оси обрабатываемого отверстия вызванному перекосом инструмента во втулке. Возможность такого перекоса обусловлена зазором между инструментом и отверстием кондукторной втулки. Причинами перекоса инструмента относительно номинального положения могут быть:
- биение режущей части при вращении;
- несимметричность заточки;
- неоднородность материала заготовки (пятнистая структура);
- неравномерности поверхности в месте входа инструмента с осью отверстия направляющего инструмента.
При расчете приспособлений на точность суммарная погрешность при обработке детали не должна превышать величину допуска Т размера .
Суммарная погрешность зависит от ряда факторов и в общем случае может быть представлена выражением
где - погрешность установки детали в приспособлении;
– погрешность обработки детали;
– расчетная погрешность приспособления.
Погрешность установки представляет собой отклонение фактического положения закрепленной детали в приспособлении от требуемого теоретического. Погрешность установки включает погрешности: базирования закрепления и положения детали в приспособлении :
Погрешность положения п детали в приспособлении состоит из погрешностей: изготовления приспособления по выбранному параметру 'пр установки приспособления на станке у и положения детали из-за износа элементов приспособления и:
Для расчета точности приспособления используем упрощенную формулу:
где Т – допуск выполняемого размера 10+043;
– соответственно погрешности: базирования закрепления установки приспособления на станке положения детали из-за износа установочных элементов приспособления и от перекоса инструмента; – экономическая точность обработки kт=1 12 – коэффициент учитывающий отклонение рассеяния значений составляющих величин от закона нормального распределения; kт1=08 085 – коэффициент учитывающий уменьшение предельного значения погрешности базирования при работе на настроенных станках; kт2=06 08 – коэффициент учитывающий долю погрешности обработки в суммарной погрешности вызываемой факторами не зависящими от приспособления.
Погрешность базирования рассчитаем по формуле [1 с.152 табл.74]:
где =0 – угол обработки отверстия к оси симметрии призмы;
α=902=45°- угол призмы;
ТD- допуск по диаметру 50мм по Н14 ТD =074мм.
Погрешность закрепления [1 с.165 табл.76]:
мм для закрепления в призме пневматическим зажимом по предварительно обработанной поверхности.
Погрешность мм так как обеспечен надежный контакт приспособления со столом станка а обработка производится без переустановок приспособления.
Погрешность положения детали из-за износа элементов приспособления определяем по следующей формуле [1 с.186 табл.80]:
где U – значение приближенного износа установочных элементов;
где – средний износ установочных элементов для чугунной заготовки при усилии зажима Р0=10 кН и базовом числе установок N=100000; U0=0115 – для призмы из стали 40Х [1с.169 табл.81];
- соответственно коэффициенты учитывающие влияние материала заготовки оборудования условий обработки и числа установок заготовки отличающиеся от принятых при определении U0 [1 с.176 табл.82].
при обработке незакаленных сталей;
для обработки на универсальном станке;
для сверления стали с охлаждением;
Экономическая точность обработки для сверления по кондуктору по 4 классу точности.
При применении подвижной кондукторной плиты суммарная погрешность смещения инструмента относительно обрабатываемой детали определяется по формуле:
где – погрешность смещения инструмента от зазоров в направляющих элементах кондукторной плиты;
– погрешность смещения инструмента от погрешностей установки кондукторной плиты относительно приспособления.
где h – расстояние от поверхности заготовки до кондукторной втулки; m=5мм;
s – максимальный диаметральный зазор между кондукторной втулкой и инструментом.
где - максимальный зазор между кондукторной втулкой и сверлом;
- максимальный зазор между кондукторной втулкой и кондукторной плитой.
Рисунок 8 -Увод сверла
Исполнительный диаметр сверла зависит от установочного допуска на обрабатываемое отверстие и определяется с учетом разделения этого допуска запасом на износ. Обычно принимают:
где – номинальный диаметр обрабатываемого отверстия.
Рисунок 9 – Кондукторная втулка
Назначив допуск на сверло по посадке h6 получим исполнительный размер сверла 1005-009.
Назначив допуск для кондукторной втулки F7 получим исполнительный размер кондукторной втулки .
Назначив посадку кондукторной втулки в кондукторную плиту и приняв посадочный диаметр равным 15 получим .
Тогда Σsmax=0124+0029=0153.
где – допуск на координаты расположения направляющих скалок 110±001 определяющих положение кондукторной плиты относительно приспособления;
- сумма максимальных зазоров в сопряжении:
- направляющих скалок с приспособлением при посадке направляющей скалки 25 во втулку корпуса по посадке максимальный зазор будет равен 0063 для двух скалок ;
- штока пневмоцилиндра с приспособлением при посадке штока 25 во втулку корпуса по посадке максимальный зазор будет равен 012мм.
Допустимая погрешность изготовления приспособления:
То есть допустимая не параллельность кондукторной плиты основанию скальчатого кондуктора не более 004мм.
К любому приспособлению или изделию предъявляются технические требования которые должны выполняться.
К проектированию приспособления предъявляются следующие технические требования:
)Требования по технике безопасности станочных приспособлений ГОСТ 12.2.029-77;
)Требования по технике безопасности к пневмосистеме ГОСТ 12.3.001-85;
)Остальные технические требования ОСТ 26016-80;
Описание сборки приспособления его установки на станке наладка последовательность действий при эксплуатации
Собираем приспособление следующим образом:
–запрессовать в корпус (поз. 1) втулки (поз. 3);
–запрессовать в корпус (поз. 1) 2 пальца (поз. 16);
–закрепить мембрану (поз. 6) на корпусе (поз.1) винтами (поз. 12);
–поставить кольцо (поз. 7);
–установить пружину (поз. 17) прижать ее упором (поз. 8);
–упор прикрепить к корпусу винтами (поз. 13);
–вставить шток (поз.4) в корпус закрепить его гайками;
–одеть на штоки прижим (поз. 5) и закрепить гайками (поз. 15).
Приспособление в собранном виде устанавливаем на стол станка установочными пальцами в пазы. Выверку приспособления производим совмещением центрального отверстия стола и приспособления. Затем закрепляем приспособление к столу двумя болтами.
Эксплуатация данного приспособление при установке детали в приспособление:
–включить с помощью распределительного крана пневмопривод;
–установить заготовку на призму до упора 12 ;
–выключить с помощью распределительного крана пневмопривод
После чего включается станок и ведется обработка детали.
Снятие обработанной детали с приспособления:
–снять деталь с приспособления.
При сборке и эксплуатации приспособления нужно соблюдать технику безопасности установленную ГОСТ или отделом техники безопасности данного предприятия. Так как зажим заготовки ведется с помощью пневмопривода то общие требования безопасности труда для пневмоприводов изложены в ГОСТ 12.3.001—85 (СТ СЭВ 3274—81) «Пневмоприводы. Общие требования безопасности».
Ансеров М.А. Приспособления для металлорежущих станков – М.: Машиностроение 1964. 652с.
Анурьев В.И. Справочник конструктора – машиностроителя: В 3-х т. Т.1 – 5-е изд. перераб. и доп. – М.: Машиностроение 1979. 240с.
Белоусов А. П. Проектирование станочных приспособлений: Учеб. Пособие для учащихся техникумов. – 3-е изд. перераб. и доп. – М.: Высшая школа 1980. 240с.
Справочник технолога машиностроителя. В 2-х Т. Под. ред. канд. техн. наук А. Г. Касилова и Р. К. Мещерикова - М.: Машиностроение 1985. 496с.
Станочные приспособления. Справочник. В 2-х Т. Под. ред. Б. Н. Вардашкина и А. А. Шатилова. Т.1. – М.: Машиностроение 1984. 592 с.
Толстов М. А. Пневматические и пневмогидравлические приспособления. – 3-е изд. перераб. и доп. – Сврдловск Государственное научно – техническое издательство машиностроительной литературы 1961. 271с.
Устюгов И. И. Детали машин: Учеб. Пособие для техникумов. – 2-е изд. перераб. и доп. – М.: Высшая школа 1981. 399с.
крышка.cdw

трещины и пористость не допускаются.
Неуказанные литейные радиусы 3 5 мм
Формовочные уклоны - по ГОСТ 3212 - 92.
выполненных из алюминиевых сплавов -
Неуказанные предельные отклонения размеров: отверстий - по
остальных - по js14.