Проектирование сверлильного приспособления для детали шестерня



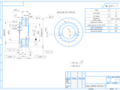
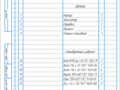
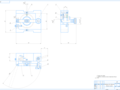
- Добавлен: 25.01.2023
- Размер: 283 KB
- Закачек: 1
Описание
Проектирование сверлильного приспособления для детали шестерня
Состав проекта
![]() |
![]() |
![]() ![]() ![]() ![]() |
![]() ![]() ![]() |
![]() ![]() ![]() ![]() |
![]() ![]() ![]() ![]() |
Дополнительная информация
При.cdw

Размеры для справок.
Предельно изношенный размер кондукторной втулки
Приспособ_сверл.doc
1. Техническое задание
2. Последовательность и этапы при проектировании станочных приспособлений
Выбор способа установки заготовки в станочном приспособлении
1 Выбор схемы базирования и описание работы приспособления
2 Методика расчета приспособления на точность
Силовой расчёт приспособления
1 Составление расчетной схемы и исходного уравнения для расчета зажимного усилия
2. Расчет коэффициента надежности закрепления К.
3 Составление расчетной схемы и исходного уравнения для расчета исходного усилия Ри
Прочность деталей приспособлений
чертеж приспособления со спецификацией (формат А1)
Интенсификация производства в машиностроении неразрывно связана с техническим перевооружением и модернизацией средств производства на базе применения новейших достижений науки и техники. Техническое перевооружение подготовка производства новых видов продукции машиностроения и модернизация средств производства неизбежно включают процессы проектирования средств технологического оснащения и их изготовления.
В общем объеме средств технологического оснащения примерно 50% составляют станочные приспособления. Применение станочных приспособлений позволяет:
надежно базировать и закреплять обрабатываемую деталь с сохранением ее жесткости в процессе обработки;
стабильно обеспечивать высокое качество обрабатываемых деталей при минимальной зависимости качества от квалификации рабочего;
повысить производительность и облегчить условия труда рабочего в результате механизации приспособлений;
расширить технологические возможности используемого оборудования.
В зависимости от вида производства технический уровень и структура станочных приспособлений различны. Для массового и крупносерийного производства в большинстве случаев применяют специальные станочные приспособления. Специальные станочные приспособления имеют одноцелевое назначение для выполнения определенных операций механической обработки конкретной детали. Эти приспособления наиболее трудоемки и дороги при исполнении. В условиях единичного и мелкосерийного производства широкое распространение получила система универсально-сборных приспособлений (УСП) основанная на использовании стандартных деталей и узлов. Этот вид приспособлений более мобилен в части подготовки производства и не требует значительных затрат.
Создание любого вида станочных приспособлений отвечающих требованиям производства неизбежно сопряжено с применением квалифицированного труда. В последнее время в области проектирования станочных приспособлений достигнуты значительные успехи. Разработаны методики расчета точности обработки деталей в станочных приспособлениях созданы прецизионные патроны и оправки улучшены зажимные механизмы и усовершенствована методика их расчета разработаны различные приводы с элементами повысившими их эксплуатационную надежность.1. Проектирование станочного приспособления
Спроектировать установочно-зажимное приспособление под детали типа "Шестерня" для операции сверление отверстия на вертикально-сверлильном станке модели 2Н135 в условиях серийного производства;
-геометрические параметры:
-Точность выполняемой операции в мм:
диаметр отверстия 3H14 глубина 25 (напроход) отклонение от соосности 1 мм.
-Способ обеспечения заданной точности по предварительной настройке станка
-Годовая программа выпуска всех типоразмеров Nг = 5000шт
2. Последовательность и этапы при проектировании станочных приспособлений.
Техническое задание на проектирование станочного приспособления
Анализ исходных данных для разработки технического проекта
Выбор и обоснование системы станочного приспособления
Критерий выбора - зона рентабельности применения системы станочного приспособления
Выбор баз и способа установки заготовки на разрабатываемой операции
Определение и анализ погрешности базирования Eб
Определение погрешности закрепления – Ез
Анализ и оптимизация теоретических схем базирования
Схема силового замыкания детали
Определение погрешности
базирования (Еб) для выбранной схемы установки
Выбор точки приложения и направления зажимных сил
Анализ возможных схем установки детали на операции
Выбор конструкции и расположения опорных (установочных) элементов приспособления.
Анализ размерных связей при различных схемах базирования
Расчет погрешности закрепления Ез = С1 * q0.5 * (C2 + kRa)
Оптимизация схемы базирования. Расчет Еб
Выбор способа установки приспособления на станке
Осуществляется привязка станочного приспособления к системе координат станка
Оценка (расчетная) погрешности установки Е = E12 + E22
Оценка (расчетная) допуска на исполнительный размер [бp] [бт]
Выбор направляющих элементов для инструмента
Разработка компоновочной схемы приспособления
Расчетная часть проекта
Выбор способа установки заготовки в станочном приспособлении.
1. Выбор схемы базирования и описание работы приспособления.
Анализируя техническое задание эскиз детали под выполняемую операцию из ГОСТ 21495-76 выбираем теоретическую схему базирования и из ГОСТ3.1107-81 возможные схемы практической реализации.
Практическая схема базирования детали "Шестерня" для операции ''Сверление''.
Кондуктор предназначен для сверления отверстия диаметром 3 мм в шестерне.
В отверстии корпуса 1 установлен фиксатор 2 закреплённый винтами 10.
Обрабатываемую деталь устанавливают до упора в торец. Правильное положение детали относительно оси вращения регулируют упорным винтом 9. Деталь закрепляют прижимом 4 шарнирно закреплённым на откидной планке 5 при навинчивании гайки 12 на откидной болт 8.
При сверлении отверстия кондуктор устанавливают стойками 13 и 14 на столе вертикально-сверлильного станка.
Приспособление спроектировано для серийного производства.
На рассматриваемой операции выдерживаются 2 размера - 3+03; 22±026.
Выявим составляющие погрешности:
- dс=0 так как ею можно пренебречь;
- dрп и dн определяются одной и той же величиной – зазором между кондукторной втулкой и сверлом так как положение на столе станка кондуктору придаётся при настройке путём совмещения оси сверла с осью кондукторной втулки.
Определим smax между втулкой и сверлом. Для получения отверстия диаметром 3Н14 осуществляют сверление сверлом 3-0036.
Диаметр кондукторной втулке принят 3F7=3+0.01+0.022. Отсюда максимальный зазор между отверстием втулки и сверлом будет равен:
smax=0022+0036=0058(мм).
Следовательно dн=0058(мм).
Погрешность dп.о.=0; dб.и.б равна максимальному зазору между отверстием заготовки и пальцем. Отверстие заготовки к моменту данной операции имеет базовый диаметр 435+002 а диаметр пальца принят 435g6=435-009-0025. Следовательно:
smax=002+009=011(мм).
Погрешность dб.и.б=011(мм).
Погрешность dз=001(мм) (принята без расчёта).
Погрешность dп.н. для кондуктора с запрессованной втулкой определяется совокупностью двух величин:
- погрешность dвт=2eвт – эксцентриситет втулки. dвт=2eвт=2001=002(мм);
- погрешность dв=smax – максимальный зазор при посадке втулки в корпус.
Примем посадку втулки в корпус 6Н7р6. Отсюда максимальный зазор равен:
smax=0.015+0.024=0.039(мм).
Погрешность dв=0039 (мм).
Погрешностью dД пренебрегаем.
Суммирование составляющих погрешностей рассчитаем по формуле:
Результирующая погрешность 013 меньше допуска 052. Кондуктор обеспечит требуемую точность.
Силовой расчёт приспособления.
1 Составление расчетной схемы и исходного уравнения для расчета зажимного усилия Рз
Величину необходимого зажимного усилия определяют на основе решения задачи статики рассматривая равновесие заготовки под действием приложенных к ней сил. Для этого необходимо составить расчетную схему то есть изобразить на схеме базирования заготовки все действующие на нее силы: силы и моменты резания зажимные усилия реакции опор и силы трения в местах контакта заготовки с опорными и зажимными элементами.
Расчетную схему следует составлять для наиболее неблагоприятного местоположения режущего инструмента по длине обрабатываемой поверхности.
По расчетной схеме необходимо установить направления возможного перемещения или поворота заготовки под действием сил и моментов резания определить величину проекций всех сил на направление перемещения и составить уравнения сил и моментов:
Назначаем режимы резания при сверлении.
По таблицам справочника при 3 определяем s=02 ммоб
V=12.5 ммин n=200 обмин.
Сила резании при сверлении определяется по формуле:
Хр=086; yр=074; zр=100; qp=-086; D=3мм; B=20мм.
Крутящий момент Мкр определяется по формуле:
где См=39 безразмерный поправочный коэффициент;
s=0.2 ммоб - подача при сверлении;
Введем коэффициент надежности закрепления К:
Заготовка может переместиться лишь под действием крутящего момента Мкр.
При расчёте усилия зажима не учитываем закрепление заготовки на оправке т.е. рассматриваем «худший» вариант закрепления.
2 Расчет коэффициента надежности закрепления К.
Так как в производственных условиях могут иметь место отступления от тех условий применительно к которым рассчитывались по нормативам силы и моменты резания возможное увеличение их следует учесть путем введения коэффициента надежности (запаса) закрепления К и умножения на него сил и моментов входящих в составленные уравнения статики.
Значение коэффициента надежности К следует выбирать дифференцированно в зависимости от конкретных условий выполнения операции и способа закрепления заготовки. Его величину можно представить как произведение частных коэффициентов каждый из которых отражает влияние определенного фактора:
К0 – гарантированный коэффициент запаса надежности закрепления К0 = 15;
К1 – коэффициент учитывающий увеличение силы резания из-за случайных неровностей на заготовках;
К1 = 12 – для черновой обработки;
К1 = 10 – для чистовой обработки;
К2 – коэффициент учитывающий увеличение силы резания вследствие затупления инструмента (табл. 5.2);
К3 – коэффициент учитывающий увеличение силы резания при прерывистом резании К3 = 12;
К4 – учитывает непостоянство зажимного усилия;
К4 = 13 – для ручных зажимов;
К4 = 10 – для пневматических и гидравлических зажимов;
Таблица 5.2 Значение коэффициента К2
К5 – учитывает степень удобства расположения рукояток в ручных зажимах;
К5 = 12 – при диапазоне угла отклонения рукоятки 900;
К5 = 10 – при удобном расположении и малой длине рукоятки;
К6 – учитывает неопределенность из-за неровностей места контакта заготовки с опорными элементами имеющими большую опорную поверхность (учитывается только при наличии крутящего момента стремящегося повернуть заготовку);
К6 = 10 – для опорного элемента имеющего ограниченную поверхность контакта с заготовкой;
К6 = 15 – для опорного элемента с большой площадью контакта.
Величина К может колебаться в пределах 15 80. Если К 25 то при расчете надежности закрепления ее следует принять равной К = 25 (согласно ГОСТ 12.2.029-77).
Таким образом К=11151213115=27.
Окончательно принимаем К=27.
Силовые механизмы обычно выполняют роль усилителя. Его основной характеристикой является коэффициент усиления i (передаточное отношение сил)
Наряду с изменением величины исходного усилия силовой механизм может также изменять его направление разлагать на составляющие и совместно с контактными элементами обеспечивать приложение зажимного усилия к заданной точке. Иногда силовые механизмы выполняют роль самотормозящего элемента препятствуя раскреплению заготовки при внезапном выходе из строя привода.
Силовые механизмы делятся на простые и комбинированные. Простые состоят из одного элементарного механизма – винтового эксцентрикового клинового рычажного.
Комбинированные представляют собой комбинацию нескольких простых: рычажного и винтового рычажного и эксцентрикового рычажного и клинового и т.д.
Силовые механизмы используются в приспособлениях с зажимными устройствами как первой так и второй групп. Для приспособлений с зажимными устройствами первой группы силовой механизм следует выбирать совместно с приводом чтобы можно было рационально согласовать силовые возможности механизма (коэффициент усиления i) с силовыми данными привода.
Выбор конструктивной схемы силового механизма производится также с учетом конкретных условий компоновки приспособления.
Для выбранного силового механизма необходимо определить коэффициент усиления i и исходное усилие Ри которое должно быть приложено к силовому механизму приводом или рабочим.
Расчетная формула для нахождения Ри может быть получена на основе решения задачи статики – рассмотрения равновесия силового механизма под действием приложенных к нему сил.
Дано: Wз =986Н l=18мм d=10мм.
Н составляет примерно 5 кг усилия при зажиме что допустимо при ручных операциях.
Прочность — одно из основных требований предъявляемых к деталям и приспособлениям в целом. Прочность деталей может рассматриваться по коэффициентам запаса или по номинальным допускаемым напряжениям. Расчеты по номинальным допускаемым напряжениям менее точны и прогрессивны но значительно проще.
С помощью расчета деталей (элементов) приспособлений на прочность можно решать две задачи: а) проверку на прочность уже существующих деталей с определенными размерами сечений путем сравнения фактических напряжений) (моментов сил) с допускаемыми — проверочный расчет; б) определение размеров сечений деталей — предварительный проектный расчет.
Расчет на прочность (задача а) детали в виде стержня круглого сечения нагруженного осевой силой по допускаемым напряжениям растяжения (сжатия) осуществляется по формуле
где — фактическое напряжение растяжения (сжатия) МПа; Р — расчетная осевая сила Н; d — диаметр опасного сечения (для резьбового стержня — внутренний диаметр резьбы) мм; [] — допускаемое напряжение растяжения (сжатия) МПа.
Определение необходимого размера опасного сечения (задача б) для подобного случая можно производить по формуле
Полученное значение округляется в сторону увеличения до целого или ближайшего стандартного значения.
Наиболее нагруженной деталью является ось диаметром 6мм (поз.15).
Расчеты на прочность валов и осей с целью определения их размеров (задача б) можно производить по формулам: на изгиб (детали круглого сечения)
Изгибающий момент Миз равен усилию зажима (Н) умноженное на плечо (м):
Округляем полученное значение в большую сторону и примем d=6мм.
А.Г. Косилова и Р.К.Мещерякова "Справочник технолога-машиностроителя" в 2-х томах изд. Москва "Машиностроение" 1986г.
Б.Г.Зайцев "Справочник молодого токаря'" изд. Москва "Высшая школа" 1977г.
М.А.Ансеров "Приспособление для металлорежущих станков'' изд. Москва ' 'Машиностроение'' 1975г.
Б.Н.Вардашкин и А.А.Шапилова "Станочные приспособления "в 2-х томах изд. Москва "Машиностроение 1984г.
В.В.Данилевский "Технология машиностроения" изд. Москва "Высшая школа" 1984г.
Н.Ф.Мельников "Технология машиностроения" изд. Москва "Машиностроение" 1977г.
А.А.Маталин "Технология машиностроения" изд. Москва "Машиностроение" 1985г.
Спецификация.frw

Болт B.М10-6g х 65 ГОСТ 3033-79
Винт М6 х 25 ГОСТ 1483-84
Винт М6 х 16 ГОСТ 1491-80
Втулка 7501-4587 ГОСТ 15362-73
Гайка 7003-0257 ГОСТ 14726-69
Ось 1-6 х 20 ГОСТ 9650-80
Шестерня.cdw

Степень точности по ГОСТ 1643-81
Допуск на радиальное
биение зубчатого венца
Сталь 20ХН3А ГОСТ4543-71
Рекомендуемые чертежи
- 23.10.2015