Разработка конструкции привода подач вертикально-сверлильного станка 2Б118




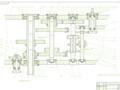
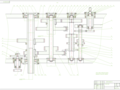
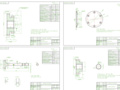
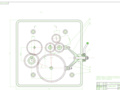
- Добавлен: 25.01.2023
- Размер: 662 KB
- Закачек: 0
Описание
Состав проекта
![]() |
![]() ![]() ![]() |
![]() ![]() ![]() ![]() |
![]() ![]() ![]() ![]() |
![]() ![]() ![]() ![]() |
![]() ![]() ![]() ![]() |
![]() ![]() ![]() |
![]() ![]() ![]() ![]() |
![]() ![]() ![]() ![]() |
![]() ![]() ![]() ![]() |
![]() ![]() ![]() ![]() |
Дополнительная информация
Vlad4.doc
Министерство образования Российской Федерации
ГОСУДАРСТВЕННОЕ УЧРЕЖДЕНИЕ ВЫСШЕГО
ПРОФЕССИОНАЛЬНОГО ОБРАЗОВАНИЯ
БЕЛОРУССКО–РОССИЙСКИЙ УНИВЕРСИТЕТ
Кафедра «Металлорежущие станки и инструменты»
по дисциплине «Конструирование и расчёт металлорежущих станков»
«Разработка конструкции привода подач вертикально-сверлильного станка 2Б118»
Расчет режимов резания
Кинематический расчёт
1 Прочностной расчёт зубчатых колёс ..
2 Расчёт зубчатых колёс на усталостную прочность
3 Расчёт геометрических параметров зубчатых колёс ..
4 Определение степени точности зубчатых колёс .
Проектный и проверочный расчёт валов ..
1 Ориентировочный расчёт валов
2 Прочностной расчёт валов
3 Расчёт вала на выносливость
Подбор подшипников ..
Расчёт шлицевого соединения
1 Расчёт шлицевого соединения на прочность ..
2 Расчёт шлицевого соединения на износ ..
3 Расчёт шлицевого соединения на безизносную работу .
Расчёт шпоночного соединения .
Индивидуальное задание
Мероприятия по технике безопасности и охране окружающей среды
Список используемых источников
В качестве базового задания по курсовой работе определен радиально-сверлильный станок модели 2Б118.
На станках можно производить сверление в сплошном материале рассверливание зенкерование развёртывание подрезку торцев нарезку резьбы метчиками и другие подобные операции.
Базовая модель станка снабжена 9-ти ступенчатой коробкой подач. Разрабатываемая коробка имеет 10 ступеней подач.
Благодаря своей универсальности станок находит применение везде где требуется обработка отверстий от ремонтного цеха до крупносерийного производства.
Применение приспособлений и специального инструмента значительно повышает производительность станков и расширяет круг возможных операций позволяя производить на них выточку внутренних канавок вырезку круглых пластин из листа и т.д. При соответствующей оснастке на станке можно выполнять многие операции характерные для расточных станков.
Техническая характеристика (основные параметры и размеры согласно ГОСТ 1222-71):
Класс точности - Н (по ГОСТ 8-82)
Наибольший условный диаметр сверления (в стали 45 по ГОСТ 1050-88) 35мм
Вылет шпинделя от образующей колонны 250 мм;
Расстояние от торца шпинделя до плиты
- наибольшее 1060 мм;
Количество ступеней скоростей шпинделя 12
Пределы скоростей шпинделя от 45 до 2000 обмин
Количество ступеней механических подач шпинделя 9
Пределы подач шпинделя от 015 до 33 ммоб
Наибольшая эффективная мощность на шпинделе 22 кВт
Наибольшее усилие подачи 2000 Н
Габаритные размеры станка
Масса станка 1020 кг.
Расчет режимов резания
Согласно паспорту станка модели 2Б118 наибольший диаметр сверления на станке – 35 мм. В качестве обрабатываемого материала принимаем сталь 40Х с твёрдостью 160 240 НВ =750 МПа.
Определяем скорость резания для сверления:
где - коэффициент на обрабатываемый материал;
- коэффициент на инструментальный материал =1
- коэффициент учитывающий глубину сверления =06
= 98; q = 04; y = 0.5; m = 0.2; T =110 мин; s = 1.008 обмин.
Определим крутящий момент:
= 00345; q = 20; y = 08.
=10*0.0345**1 = 4253 Н*м
Определим эффективную мощность:
где n – частота вращения шпинделя
Принимаем = 90 тогда
По данной мощности для привода при условии подбираем электродвигатель серии 4А132S4У3 с=75 кВт и синхронной частотой вращения n =1500.
Кинематический расчёт
Составляем структурную формулу привода. По заданию z = 10 φ =158.
По структурной формуле строим структурную сетку (рис. 1).
Строим график частот вращения. Так как в последней групповой передаче необходимо обеспечить максимальную редукцию частот вращения определим максимально возможный угол наклона луча передачи. При этом учитываем рекомендации по ограничению передаточного отношения передач .
Определим частоту вращения выходного вала а также частоты вращения для всех значений s расположенных по геометрическому ряду.
Строим график частот вращения:( рис.2 ).
Определим передаточные отношения:
где - знаменатель геометрического ряда ;
s – число интервалов.
Используя передаточные отношения определим числа зубьев единичных и групповых передач аналитическим методом:
Определим сумму зубьев :
Определим числа зубьев остальных передач:
Аналогично расчитав для остальных зубчатых колёс передачи получим следующие значения чисел зубьев: = 56; = 88; = 64; = 80; = 64; = 80; = 30; =114; = 30; =114; = 104;.
Определим крутящие моменты на валах
Определяем межосевое расстояние.
-модуль упругости =21*МПа;
- крутящий момент на валу;
где - предел выносливости = 2НВ+70 = 570 МПа;
- коэффициент долговечности =1;
- коэффициент безопасности =11
Из стандартного ряда принимаем = 160 мм.
Из стандартного ряда принимаем = 100 мм.
Определяем модули зубчатых колёс в соответствующих передачах.
По стандартному ряду принимаем = 2.
Уточняем межосевое расстояние = = 146 мм.
Уточняем межосевое расстояние =146 мм.
По стандартному ряду принимаем = 25.
Уточняем межосевое расстояние = 1045 мм.
1 Прочностной расчёт зубчатых колёс
Для получения сравнительно небольших габаритов и невысокой стоимости привода подач изготовим колёса 1 и 2 ступеней (16 17 18 19) из сравнительно недорогой легированной стали 40Х.
Для шестерен 19 и 16 зададим термообработку – закалка 830 850 и отпуск 500 до твёрдости 260 280 НВ.
= 950 МПа = 700 МПа.
= 2НВ+70 = 2*280+70 = 630 МПа;
Для зубчатых колёс 17 18 термообработка – закалка 830 850 отпуск 540 580 до твёрдости 230 260 НВ.
= 250*2+70 = 570 МПа;
= 115*116 = 133 (20)
= 02*100 = 20 мм. (22)
- прочность обеспечена.
Так как колёса 3-5 ступеней предназначены для передачи достаточно большого крутящего момента и кроме того конструкция выдвижной шпонки подразумевает вращение колёс блока не входящих в зацепление то материал таких колёс должен обладать высокой прочностью и износостойкостью. Поэтому для колёс 3–5 ступеней (9 – 11) в качестве материала выберем сталь 45 удовлетворяющую данным требованиям.
Термообработка – закалка при температуре 820 840 отпуск 520 530.
= 850 МПа = 580 МПа.
С учётом допустимого запаса 4% принимаем т.е. условие прочности выполняется.
2 Расчёт зубчатых колёс на усталостную прочность
Выполним расчёт для 1 и 2 ступеней:
где - предел выносливости зубьев по напряжениям изгиба;
- коэффициент безопасности = 175;
- коэффициент учитывающий влияние двустороннего приложения нагрузки = 1;
- коэффициент долговечности = 18.
= 18НВ = 18*240 = 432 МПа
где - коэффициент расчётной нагрузки = 15 ;= 142.
- усталостная прочность обеспечена.
Выполним расчёт для 3 – 5 ступеней:
= 18НВ = 18*280 = 504 МПа
= 14*142 = 198; (29)
С учётом допустимого запаса 4% принимаем т.е. условие усталостной прочности выполняется.
3 Расчёт геометрических параметров зубчатых колёс
= = 2*30 = 60 мм; (30)
=+ 2*m = 60 + 2*2 = 64 мм; (31)
=+ 2*m = 48 + 2*2 = 52 мм;
= - 2.5*m = 60 – 2.5*2 = 55 мм; (32)
= - 2.5*m = 48 – 2.5*2 = 43 мм.
Аналогично производим расчёт остальных пар зубчатых колёс. Результат вычислений сведём в таблицу.
Таблица 1 – Геометрические характеристики зубчатых колёс
Делительный диаметр d мм
4 Определение степени точности зубчатых колёс
Для определения степени точности зубчатых колёс найдём окружные скорости вращения данных колёс по формуле:
где d – делительный диаметр колеса;
n – частота вращения вала на котором сидит колесо.
Степень точности определим по прил.19 [3]. Результаты занесём в таблицу.
Таблица 2 Степень точности зубчатых колёс
Окружная скорость Vмс
Проектный и проверочный расчёт валов
1 Ориентировочный расчёт валов
где - крутящий момент на валу;
- допустимое напряжение на кручение = 15МПа.
Принимаем = 16 мм диаметр вала под подшипник = 16 мм.
Принимаем = 20 мм диаметр вала под подшипник = 20 мм.
Принимаем = 45мм диаметр вала под подшипник = 40мм.
Принимаем = 50 мм диаметр вала под подшипник = 40 мм.
2 Прочностной расчёт валов
Рассчитаем вал X как самый нагруженный (= 42530 Н*м).
В качестве материала вала примем сталь 45 термообработка – закалка с нагревом ТВЧ до твёрдости HRC 54 60.
= 750 МПа = 450 МПа.
Так как в конструкции блока зубчатых колёс 9-111819 предусмотрена выдвижная шпонка то вал изготавливаем из трубы наружным диаметром d =44 мм.
Определяем силы в зацеплении :
Силы взаимодействующие между звеньями раскладываются на две взаимно перпендикулярные составляющие: - окружную силу и - радиальную силу.
где d – диаметр шестерни.
где - угол зацепления = .
= 87525*0364 = 31856 Н.
Определим реакции в опорах и построим эпюры моментов.
Горизонтальные составляющие:
Вертикальные составляющие:
Строим эпюру моментов для горизонтальных сил(рис3):
= 40637*150 = 60956 Н*м;
Строим эпюру моментов для вертикальных сил:
= 14790*150 = 22185 Н*м;
Статическая прочность вала оценивается по эквивалентному напряжению которое рассчитывается по 3 и 4 критериям прочности.
где d – диаметр вала d = = 30 мм;
- условие статической прочности выполняется.
3 Расчёт вала на выносливость
Расчёт вала на выносливость для опасного сечения производится с целью предотвращения усталостного разрушения вала.
Выносливость вала оценивается по формуле:
где S - расчётный коэффициент запаса прочности;
- требуемый коэффициент для обеспечения запаса прочности = 13 15;
- коэффициент запаса прочности по нормальным напряжениям;
- коэффициент запаса прочности по касательным напряжениям;
где - амплитуда переменных составляющих циклов напряжений;
- постоянные составляющие.
= 04*750 = 300 МПа; (44)
= 02*750 = 150 МПа. (45)
и - эффективные коэффициенты концентрации напряжений при изгибе и кручении = 17 = 17;
и - масштабный фактор и фактор шероховатости = 082 = 09;
и - коэффициенты корректирующие влияние постоянной составляющей цикла напряжений на сопротивление усталости = 01 = 005.
= 05*= 05*4201 = 2101 МПа;
- условие выполняется.
Рассчитаем параметры геометрического сечения вала используя условие кручения бруса.
= 42530 Н*м ; = 15 МПа.
Чтобы не допустить работы вала на предельных значениях произведём коррекцию внутреннего диаметра. Принимаем d = 20 мм.
Определим прогиб в вертикальной плоскости от силы :
Е = 21* МПа ; = 31856 Н.
Прогиб в горизонтальной плоскости:
- условие прогиба выполняется.
Подбор подшипников произведём для вала X как самого нагруженного.
Диаметр вала в месте посадки подшипника = 35 мм частота вращения вала = 1162 . Номинальная долговечность = 20000 ч; режим нагрузки – нормальный (Н); реакции опор согласно предыдущему расчёту:
По диаметру = 35 мм предварительно принимаем радиальный шарикоподшипник средней серии №308 по ГОСТ 8338 – 75 со следующими характеристиками: D =80 мм С = 332 кН = 180 кН.
Определяем эквивалентную динамическую нагрузку.
Радиальная нагрузка:
где - коэффициент учитывающий динамичность внешней нагрузки = 12;
- коэффициент учитывающий влияние температуры подшипникового узла = 1;
V – скорость при вращающемся внутреннем кольце V=1 мс.
Для определения коэффициентов X и Y найдём отношение :
Для данного подшипника эксцентриситет е = 030
= 0 е следовательно X=1 и Y=0.
где L – ресурс млн. об.;
р – показатель степени р = 3 (для шарикоподшипников);
- коэффициент надёжности = 1;
- обобщённый коэффициент совместного влияния качества металла и условий эксплуатации = 1.
где - эквивалентная долговечность.
- коэффициент режима нагрузки = 025.
= 025*20000 = 5000 ч
Так как превышает С предварительно выбранного подшипника то для данного диаметра вала принимаем роликовый конический однорядный подшипник серии 42508 с С = 561 кН = 350 кН удовлетворяющий условию .
Проверим подшипник на статическую грузоподъёмность по формуле:
где - коэффициенты радиальной и осевой статических нагрузок соответственно = 05 = 022*ctgα = 1.035.
=05*31856+1035*0 = 15928 Н
Необходимое условие выполняется так как 15928 47500.
Расчёт шлицевого соединения
Рассчитаем шлицевое соединение используемое для передачи крутящего момента на валу . IX.
Так как расчётный диаметр вала. IX под шлицевое соединение = 25мм то по ГОСТ 1139-80 выбираем шлицевое прямобочное соединение 6×18×25 средней серии.
1 Расчёт шлицевого соединения на прочность
где Т – номинальный крутящий момент Т = = 33562 Н*м;
- коэффициент неравномерности нагрузки по зубьям = 075;
- число зубьев шлица = 6;
- рабочая длина зубьев = 190 мм;
- рабочая высота зубьев;
- средний диаметр соединения.
D – наружный диаметр шлица D = 25 мм;
- внутренний диаметр шлица = 18 мм;
= 05*(25-18) - 2*04 = 52 мм
= (25+18)*05 = 22 мм (60)
2 Расчёт шлицевого соединения на износ
Расчёт выполняют по условию:
- допустимое напряжение по износу.
где - допускаемое условное давление при числе циклов и постоянном режиме нагружения = 110 МПа;
- коэффициент неравномерности нагрузки и различного скольжения на зубьях при расчёте на износ = 22;
- коэффициент продольной концентрации нагрузки = 15;
- коэффициент переменности нагрузки = 057;
- коэффициент числа циклов микросдвигов в соединении за полный срок службы
N = 60* t * n = 60*5000*1162 = 3.49* об. (64)
- коэффициент условий смазки = 1;
- коэффициент осевой подвижности в соединении = 125.
= 482 МПа - условие прочности выполняется.
3 Расчёт шлицевого соединения на безызносную работу
- допускаемое давление на рабочих поверхностях зубьев по условию безызносной работы.
= 0032*НВ = 0032*260 = 832 МПа.
- срок службы соединения больше 5000 ч но ограничен.
Расчёт шпоночного соединения
Запишем условия прочности шпоночного соединения на смятие и на срез:
Так как расчётный диаметр вала VIIIпод шестерню = 22 мм то выбранная шпонка по ГОСТ 23360-78 будет иметь следующие размеры (b×h×L): 10 ×8×22 мм.
- условие прочности выполняется.
Индивидуальное задание
Повысить общую технологичность привода можно путём повышения технологичности отдельных его элементов.
В ходе курсового проекта были разработаны следующие решения:
Для обеспечения требуемого числа передач в конструкции привода был применён механизм переключения с выдвижной шпонкой. Данный механизм подразумевает использование в качестве вала трубы. Это привело к повышению технологичности ввиду малой инерционности трубы и возможности расположения конструкции выдвижной шпонки во внутренней полости.
Повышение технологичности привода обеспечивается упрощением конструкции зубчатых колёс так как переключение подач обеспечивается механизмом с выдвижной шпонкой и одним блоком зубчатых колёс.
Была упрощена конструкция валов. Они стали технологичны и обеспечивают надёжное крепление зубчатых колёс и работу передачи а также имеют требуемую прочность и жёсткость.
Усовершенствована конструкция корпуса коробки подач что позволило усовершенствовать конструкцию подшипниковых узлов.
Для наилучшего зацепления и контакта при переключении передач соударяемые торцы зубьев рекомендуется выполнять бочкообразной формы (по нормали станкостроения Н22-1). Термообработка таких зубьев – сквозная закалка с нагревом ТВЧ.
Передвижение блоков зубчатых колес осуществляется вилкой 26 которая набрасывается на венец зубчатого блока. Передвижение вилки осуществляется рычагом 27 который получает вращение от рукоятки управления 38 через ось. Связь рычага и вилки осуществляется секторно-реечным зубчатым колесом. Фиксация положения блока на валу осуществляется фиксирующим механизмом (шарик и пружина).
При перемещении блока на валу фиксирующий механизм находящийся в вилке перемещается вместе с ней. В определенном положении шарик фиксирующего механизма замыкается в проточку на направляющей скалке и блок не имеет возможности перемещаться без приложения дополнительного усилия (поворота рукоятки). Перемещение вилки по направляющей скалке ограничивается упорами расположенными по обеим сторонам от вилки переключения зубчатого блока.
Управление выдвижной шпонкой осуществляется при помощи реечного колеса 20. Реечное колесо входит в зацепление со шток-рейкой 21 на которой закреплена выдвижная шпонка. Для фиксации положения зубчатой рейки предусмотрен фиксирующий механизм.
Чтобы не допустить прогиба вала данного фиксирующего механизма он закреплён в подшипниковых опорах.
Систематическая и своевременная смазка механизмов применение масел надлежащего качества и постоянное наблюдение за правильным функционированием смазочных устройств обеспечивают длительную сохранность станка. Смазка подвижных узлов станка снижает потери на трение повышает КПД уменьшает износ увеличивает долговечность сохраняет точность станка что способствует его плавной работе и получению заданной шероховатости обрабатываемых поверхностей.
Резервуар для масла находится в нижней части корпуса коробки скоростей откуда с помощью шестерёнчатого насоса через трубку масло подаётся в верхнюю часть коробки скоростей обеспечивая автоматическую смазку ее подвижных частей и узлов. Излишнее масло
поступает в коллектор откуда расходуется на смазку подшипников и охлаждение.
Нижние подшипники шпинделя смазываются солидолом через пресс-маслёнки прилагаемые к станку. Смазка верхних подшипников и пиноли шпинделя производится фитильным способом из ванны верхнего гнезда подшипников коробки скоростей.
Перед началом работы на станке сразу после его включения необходимо проверить работу насоса при нормальной работе насоса спустя 2-3 мин. после пуска станка за смотровым глазком станка должна появиться струйка масла.
Марка масла заливаемого в резервуар – «Индустриальное-20» по ГОСТ 20799-75. Полная замена масла производится один раз в три месяца.
Мероприятия по технике безопасности и охране окружающей среды
При работе на сверлильных станках основным источником травм являются: шпиндель с вращающимся инструментом ток в электросети отлетающая стружка неправильное закрепление заготовки.
Для исключения захвата вращающимся инструментом одежды сверловщика он обязан иметь спецодежду застегнутую на все пуговицы; длинные волосы должны быть убраны под головной убор. Все приводные механизмы коробки скоростей и всего станка должны быть убраны в закрытые корпуса.
Особое внимание со стороны работающего следует уделять отлетающей стружке. При обработке вязких металлов когда сливная стружка завивается вокруг сверла следует периодически удалять ее специальным захватом. При этом также периодически нужно останавливать станок.
Несчастные случаи могут происходить из-за слабого закрепления заготовок или инструмента. За всем этим станочник и мастер участка обязаны постоянно следить. Что касается опасности поражения электрическим током для ее предотвращения следует держать в исправном состоянии системы блокировки заземление ограждения станка.
Загрязнение окружающей среды при работе на сверлильном станке может произойти при обработке неметаллических материалов имеющих вредные составляющие: свинец бериллий асбест пластмассы. В этих случаях надо своевременно удалять стружку или устанавливать отсасывающие устройства аналогичные тем что применяются для отсоса абразива на шлифовальных станках.
Список используемых источников
Справочник технолога-машиностроителя. Том 2. Под. ред. А.Г. Косиловой Р.К. Мещерякова – 4-е изд. перераб. и доп. – М.: Машиностроение 1985. 496 с. ил.
Детали машин в примерах и задачах (учеб. пособие Д38) С.Н. Ничипорчик М.И. Корженцевский В.Д. Калачев и др. Под общ. ред. С.Н. Ничипорчика – 2-е изд. – Мн.: Выш. школа 1981.-432 с. ил.
Свищерский Ю.И. Макейчик Н.Н. «Расчет и конструирование коробок скоростей и подач.». Минск Выш. школа” 1976-592 с. ил.
Иванов М.Н. «Детали машин».- 5-е изд. перераб.- Мн.: Выш. шк.1991.-383 с.: ил.
Решетов Д.Н. «Детали и механизмы металлорежущих станков». Т.2. М. «Машиностроение» 1972 стр.520.
Кочергин А.И. «Конструирование и расчёт металлорежущих станков и станочных комплексов. Курсовое проектирование»: Учеб. пособие для вузов.- Мн.: Выш. шк.1991- 382 с.: ил.
Тайц Б.А. «Производство зубчатых колёс». Изд.2-е перераб. и доп. М. «Машиностроения» 1975-708 с. ил.
Методические указания по выполнению курсового проекта по КИРС.: Могилёв 1991.
Технический паспорт радиально-сверлильного станка 2М55.
Vladlist1(kompo).frw

Коэффициент смещения
Допуск колебания дли-
Предельное отклонения
Диаметр делительной
Направление линии зуба
Vladlist4(krugi).dwg

перед сборкой покрыть уплотнительной
пастой типа Герметик
Vladlist4(krugi).frw

перед сборкой покрыть уплотнительной
пастой типа Герметик
Vladlist1(kompo).dwg

Коэффициент смещения
Допуск колебания дли-
Предельное отклонения
Диаметр делительной
Направление линии зуба
Vladspec.doc
ВинтМ8х20.58ГОСТ1478-93
ВинтМ6х10ГОСТ1478-93
Кольцо1А15ГОСТ13942-86
Кольцо1А20ГОСТ13942-86
Кольцо1А30ГОСТ13942-86
Кольцо1А40ГОСТ13942-86
Подшипник212ГОСТ8338-75
Подшипник309ГОСТ8338-75
Подшипник310ГОСТ8338-75
Подшипник311ГОСТ8338-75
Подшипник312ГОСТ8338-75
Шпонка8х7х30ГОСТ23360-78
Шпонка20х14х100ГОСТ23360-78
Vladlist3(stanok).dwg

вертикально-сверлильного
Кинематическая схема
Vladlist2(korobka).dwg

вращаться от руки без заеданий.
Vladlist2(korobka).frw

вращаться от руки без заеданий.
Vladlist3(stanok).frw

вертикально-сверлильного
Кинематическая схема
Рекомендуемые чертежи
- 07.06.2021